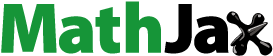
ABSTRACT
Activated carbonaceous were prepared from high-carbon, abandoned straw biomass. With hydrogen sulfide gas as the target pollutant, single factor experiments were employed to assess the effects of activator type, activation temperature, activation time, and liquid-material ratio on the adsorption performance of the prepared carbonaceous adsorbent. The materials were characterized using elemental analysis, SEM, FTIR, and BET. The results showed -OH, -CH-, and -C = O groups exist on the surface of the prepared adsorbent, specific surface area can reach 1104.84 m2•g−1, total pore volume can reach 0.261 cm3•g−1 and, where the pore volume is greater than 80%, well-developed pore structures were present that facilitated adsorption. The experimental results showed the adsorption time could reach 198 min with optimal ZnCl2 activator concentration (30%), carbonization temperature (550°C), and liquid-to-material ratio (3:1). Compared with the existing activated carbon adsorbents, the adsorption effects and preparation cost of this absorbent are advantageous, and the absorbent has prospects for broad market application.
Implications
Activated carbons were prepared from high-carbon, abandoned straw biomass. With hydrogen sulfide gas as the target pollutant, single factor experiments were employed to assess the effects of activator type, activation temperature, activation time, and liquid-material ratio on the adsorption performance of the prepared carbonaceous adsorbent. The materials were characterized using elemental analysis, SEM, FTIR, and BET. Compared with the existing activated carbon adsorbents, the adsorption effects and preparation cost of this absorbent are advantageous, and the absorbent has prospects for broad market application.
Introduction
Hydrogen sulfide is a gas with a strong, pungent odor that is present in various toxic and harmful gas mixtures, such as waste gas from waste treatment plants, sulfur-containing natural gas and gas, waste gas from the food industry, and sludge treatment plant emissions (Liu, Zhou, and Wu Citation2016). It can pose a serious threat to human physical and mental health. Adsorption technology is the main tool for controlling this environmental pollutant. However, this technology has been limited by the high price of traditional adsorption materials. Therefore, researchers have spent many years developing higher-quality, environmentally-friendly, low price adsorption products. Since biomass waste materials are cheap and readily available, they have been favored by researchers in recent years. There have been many studies on the use of biomass waste to prepare pollutant adsorbents in different fields (Bagreev et al. Citation2001). Erdem et al. studied the squeezing of discarded oil bean cakes to prepare activated carbonaceous materials to treat wastewater (Erdem et al. Citation2013). Cronje and Mohanty prepared activated carbonaceous from bagasse and coconut shell, respectively (Cronje et al. Citation2011; Mohanty et al. Citation2005). The Cr6+ adsorption rate increased to 87% for leather wastewater. Hameed and Rahman used activated carbonaceous prepared from rattan sawdust to remove phenol from water, with the adsorption capacity reaching 149.25 mg/g (Hameed and Rahman Citation2008). In terms of air treatment, Kante et al. used a carbonaceous adsorbent prepared from the ground powder of waste coffee beans to adsorb H2S (Kante et al. Citation2012). It was found that a nitrogen-containing functional group in the prepared adsorbent played a catalytic role in hydrogen sulfide adsorption. Bandosz studied the absorption of hydrogen sulfide gas with activated carbonaceous prepared from various biomass materials, such as bituminous coal, wood, coconut shell, and peat (Bandosz Citation2002). It was found that the carbonaceous surface pre-absorbed a sufficient amount of water to promote dissociation, which played an important role in H2S adsorption and oxidation processes. Therefore, the use of biomass straw as a raw material to prepare a carbonaceous adsorbent with better adsorption performance would reduce production costs and solve the problem of processing large straw yields.
Experimental methods
Materials
The experimental material was straw abandoned after grain harvest in Northeast China. The water content after drying was about 4.61%. Therefore, its carbonaceous content and hydrogen content were significantly higher than other types of waste, indicating it was an excellent raw material for preparing carbonaceous adsorbents (Tzu-Hsing, Hsin, and Lung-Kai Citation2005). During the H2S adsorption process, the glucose group in the cellulose chain, present in a large variety of straw, has a highly polar alcoholic hydroxyl group that self-interacts with oxygen atoms to form hydrogen bonds, which firmly lock the S2 + ion in H2S (Neal and Loehr Citation2000). There are many choices for activators, including ZnCl2, H3PO4, H2SO4, and KOH, but after examining the literature, the chemical activation by ZnCl2 was found to be outstanding. Rozada, Jeyaseelan, and others have used ZnCl2 as the activator to prepare adsorbents (Jeyaseelan and Qing Citation1996; Rozada et al. Citation2005). Therefore, ZnCl2 was the activator used in this study. In addition, ZnCl2 can be used to form zinc oxides during high-temperature carbonization. During the adsorption process, a small amount of water and gas can liquefy part of the H2S. The liquefied H2S reacts with Zn2+, which is beneficial for the adsorption of H2S. After passing hydrogen sulfide gas, sulfides are formed in a gas-solid reaction at low temperature. The main reaction is as follows:
The collected waste straw was washed to remove dust and surface impurities. After cleaning, it was dried in a 80–100°C oven. Dried straw was crushed in a small grinder, passed through a 20-mesh sieve, and placed in a beaker for use. Different concentrations of activator solution were mixed at different proportions with the sieved straw, and the mixture was stirred with a glass rod to ensure that straw was immersed in the solution. The beaker containing the mixture was sealed with parafilm, put in a thermostatic water bath set to 40–45°C, and soaked for 18–24 hr. After impregnation, the mixture was dried in an oven, placed in a resistance furnace, and carbonized in a N2 atmosphere at 300°C, 400°C, and 500°C. After carbonization, the final carbonaceous adsorbent was cooled to room temperature under the protection of N2.
Methods
Evaluation of H2S breakthrough capacity
In order to determine the breakthrough capacities of the produced carbonaceous adsorbent, dynamic breakthrough tests were performed at room temperature. The prepared carbonaceous adsorbent was pulverized with a mortar and sieved to collect 40 to 60 mesh particles. Each sample (0.2 ± 0.05) g was weighed in a glass tube that was 450 mm in length and had a 9 mm inner diameter. The port was filled with 1002 ppm H2S at 20 mL•min−1. The outlet was connected to the H2S concentration detector and exhaust gas absorption bottle with a three-way pipe. The outlet gas concentration was detected. Immediately after the adsorbent failed, the experiment was ended. The yield of the experimental product was the ratio of the mass of the carbonaceous adsorbent obtained after the high temperature treatment to the mass of the raw materials used. Activation of the raw materials resulted in a rich pore structure that increased the specific surface area and can increase the number of oxygen-containing functional groups. The good adsorption performance of the biomass raw material ensured that substantial activator was adsorbed. The activator’s role was to limit the formation of tar at the initial stage of high-temperature carbonization and aromatize the raw material. At the end of carbonization, activator molecules were deposited on the carbonaceous skeleton to form a pore structure. After the activator type was selected, this optimal activator was used at different concentrations in adsorption experiments to determine the optimal activator concentration.
FT-IR spectroscopy
Fourier transform infrared (FT-IR) spectroscopy was carried out using a T60SXBFTIR spectrometer produced by American NICOLE company. To assess functional groups and other structures with infrared scanning, powdered sample was thoroughly mixed with KBr powder, and tablets were pressed. The scanning range was 400–4000 m−1, and the resolution was 1 cm−1.
X-ray diffraction analysis
The X’Pert Powder type multifunctional powder X-ray diffractometer produced by the Dutch company Parnak was used with the three-dimensional high-precision positioning function. The structural crystal state of the prepared carbonaceous adsorbent was measured at room temperature. Using CuKa radiation, the wavelength λ was 1.540598 deg, the range was 0–90°, the tube voltage was 45 kV, the current was 50 mA, and the scanning step was 0.02°.
Scanning electron microscope
The FEI sirion scanning electron microscope produced by the Dutch company Philips was used to analyze the surface morphology differences of various carbonaceous adsorbent samples. The test technical indicators were 1.5 nm when the resolution was more than 10 kV, 2.5 nm at 1 kV, and 3.5 nm at 500 kV; and the acceleration voltage was 200–300 kV.
Specific surface area and pore size distribution test
The specific surface area and pore size distribution of the samples were determined using the ASAP2020 specific surface and pore analyzer produced by American micromechanics. Using the volumetric method, N2 was used as the adsorbent, and adsorption was performed at the temperature of liquid nitrogen (77 K). The specific surface area was obtained by the BET method [12], and the pore size distribution was calculated by the BJH method [13]
X-ray photoelectron spectroscopy
A PHI 5400 ESCASystem type X-ray photoelectron spectrometer produced by American Physical Electronics Corporation, a hemispherical precision electronic energy analyzer, was used to irradiate the sample with Al K-ray (hv = 1486.6 eV) to excite the photoelectron. XPS was used to judge the change of surface chemical composition after sample adsorption and explain the final adsorption process and principle.
Elemental analysis
A Vario EL cube elemental analyzer manufactured by Elementar was used to assess the sample’s elemental content. The instrument uses a dynamic combustion method. The sample was placed in a combustion tube and decomposed by instantaneous combustion under high temperature and oxygen-rich conditions. The analysis temperature was 950–1200°C, and the standard deviation was no more than 0.1% of the absolute error.
Results and discussion
Effect of activator concentration on adsorption performance of a straw-based carbonaceous adsorbent
With the liquid to material ratio set to 1: 1 and a fixed carbonization temperature set to 500°C, effects of activator concentration were assessed at wt. 10% (SC10), wt. 15% (SC15), wt. 20% (SC20), wt. 25% (SC25), wt. 30% (SC30), and wt. 35% (SC35). The results are shown in .
Figure 1. Adsorption time curves of straw-based carbon adsorbent with different concentrations of activator.
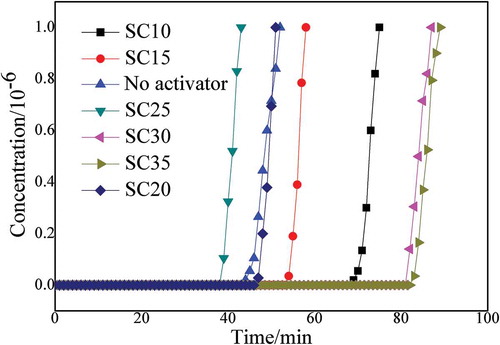
As can be seen in , when the activator concentration was SC10, the adsorption time was about 75 min. With increasing activator concentration, the adsorption time showed a significant downward trend in the range of 15%–25% activator, with an adsorption time of only about 40 minutes for SC25. At SC30, the adsorption time increased significantly, reaching 86 min. The adsorption effect of SC35 improved only slightly. The yields of SC10, SC15, SC20, SC25, SC30, and SC35 were 57.66%, 54.35%, 53.89%, 60.67%, 79.71%, and 58.93%, respectively. In addition, compared with the adsorption effect of the sample without activator added to the raw materials in the figure, the effect of adding activator is much better than the raw materials .Because the concentration of the activator was too large to corrode the straw material itself, the internal structure collapsed, and the yield was significantly reduced after the activator was washed away. When the concentration of the activator exceeded 30%, the concentration was too high and particles would be precipitated in the impregnating solution. Considering the preparation cost and the immersion effect of the activator, the optimal concentration of the activator was determined to be 30%.
Effect of the liquid-material ratio on the adsorption performance of the straw-based carbonaceous adsorbent
The activator concentration of the prepared straw-based biomass charcoal adsorbent was set to 30% to determine the optimal liquid-material ratio. Results of experiments with the liquid-to-material ratio set to 1:1 (SC30-1), 1:2 (SC30-2), 1:3 (SC30-3), and 1:4 (SC30-4) are shown in . shows that when the liquid-to-material ratio was increased from 1:1 to 2:1, the deodorization performance was reduced. When the liquid-to-material ratio was increased to 3:1 and 4:1, the deodorization performance at 3:1 was more stable than at 4:1. In view of the complexity and cost of the preparation process, a material ratio of 3:1 was selected as optimal for obtaining improved deodorization performance.
Effect of carbonization temperature on the adsorption performance of straw-based carbonaceous adsorbent
After comparing activator concentrations and liquid-material ratios, the best adsorbent was determined to be SC30-3. shows the experimental results for tests at carbonization temperature of 400°C (SC30-3-400), 450°C (SC30-3-450), 500°C (SC30-3-500), 550°C (SC30-3-550), and 600°C (SC30- 3-600). shows that when the carbonization temperature was increased from 400°C to 600°C, the adsorption time fluctuated within the range of 90 min to 125 min. When the carbonization temperature was increased from 400°C to 500°C, the deodorization performance was enhanced. When the carbonization temperature was continuously increased to 600°C, the adsorption effect was significantly reduced. When the carbonization temperature was 550°C, the deodorization performance was significantly better than at other carbonization temperatures. When the carbonization temperatures are too high, the internal structure collapses and results in excessively volatile carbonaceous matter adsorption performance degradation. However, when the carbonization temperature is too low, the carbonization degree is too low, which will also reduce adsorption performance. Compared to other process conditions, the carbonization temperature had the greatest effect on deodorization performance. The difference between the longest adsorption time and the shortest adsorption time at different carbonization temperatures was about 100 min.
Figure 3. Breakthrough time curves of carbon adsorbent from straw at different carbonization temperatures.
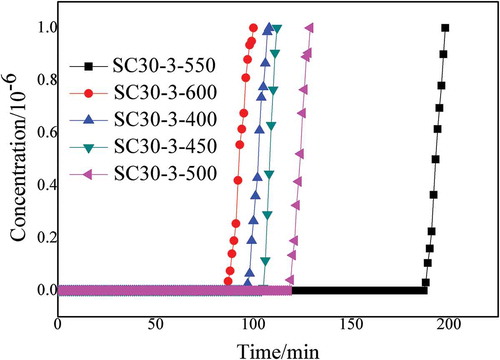
When the carbonization temperatures were 400°C, 450°C, 500°C, 550°C, and 600°C, the yields corresponded to 55.68%, 53.50%, 54.89%, 54.20%, and 46.56%, respectively. This shows that the impact of carbonization temperature on yield, concentrated at about 54%, was not very large at these low carbonization temperatures (below 600°C). Therefore, combining the assessed effects of carbonization temperature on the deodorizing properties of the absorbent, the optimal conditions were a carbonization temperature of 550°C and combined sample conditions of SC30-3-550.
Effect of surface structure on adsorption performance
is a scanning electron microscope photograph of raw straw at 1000× magnification. As seen in the figure, the surface of the straw raw material was uneven and an obvious pore structure appeared in the cross section. The dried pore structure of the straw raw material was still shaped as an elongated tube, which is beneficial to activator deposition. shows the straw charcoal adsorbent prepared under optimal process conditions at different magnifications. Compared to untreated straw, the carbon adsorbent had a rougher surface and more prominent grooves. The cross section of the pore structure showed an increased pore size, indicating that the reduction of volatile substances after carbonization treatment changes the pore size to allow superior adsorption performance for the adsorbent.
X-ray diffraction analysis
Earlier studies found that carbonization temperature has the greatest effect on deodorization performance, so XRD analysis was performed for straw charcoal adsorbents produced at different carbonization temperatures, as shown in . Samples prepared at 250°C and 350°C produced no obvious diffraction peaks. With the carbonization temperature increased to 450°C and 550°C, two distinct diffraction peaks appeared near 23° and 25°, which are the characteristic peaks of crystalline silicon oxide and random layer graphite structure (002) planes, respectively. It is generally believed that the Scherrer formula is applicable when the grain size is less than 100 nm because the stress-induced broadening is negligible compared with the grain-size widening, so this formula can be used to calculate the microcrystalline scale La parallel to the base and microcrystalline scale Lc perpendicular to the basal plane. At this time β is the half-peak width of the diffraction peak, so the value of k is 0.89. If the result shows that the calculated grain size of each crystal plane is similar, then there is no micro-strain and the grains are basically spherical.
According to the parameters obtained from the experiment, when the carbonization temperature was too low (250°C, 350°C), a shaped crystal form was not produced, which explains why the adsorption performance decreased as the carbonization temperature decreased. When the carbonization temperature was sufficiently high, the crystalline size La between crystal planes parallel to the base plane increased from 0.3684 nm to 0.5791 nm, and the Lc increased from 0.1782 nm to 0.2801 nm. This indicates that the microcrystalline were in fewer layers, had increased surface atomic activity, and more readily formed microporous structures [14].
FT-IR spectroscopy
The main functional groups in straw are hydroxyls, ethers, and carbonyls. The presence of lignin indicates a high degree of aromatic substance polymerization. The activation process caused defects and unsaturated valences in the basic structure, such that oxygen and other atoms were adsorbed onto these defects, thereby forming various surface functional groups to enhance the adsorption performance. The functional groups on the surface of the carbonaceous adsorbents are mainly oxygen-containing, such as carboxylic acids (-COOH), hydroxyls (-OH), and carbonyls (-C = O), basic group carboxyls -CH2 or – CHR, and, perhaps, neutral quinone carbonyls.
In show the infrared spectra before and after adsorption, respectively. The stretching vibration peaks were mainly concentrated at the wave numbers 3400 cm−1, 1600 cm−1, 1380 cm−1, 1150 cm−1, and 750 cm−1. The broad and strong absorption peak that appeared around 3300–3350 cm−1 indicated the stretching vibration peak of hydroxyl groups O-H. From the intensity of O-H before and after adsorption, it can be seen that the hydroxyl content decreased after adsorption, which indicates that the hydroxyl oxygen played a catalytic role and OH • and O2- were produced by the reaction with acidic H2 S gas. The absorption peak at a wave number of 1600 cm-1 was assigned as the C = O stretching vibration of quinone or benzoquinone, showing that the straw contained quinones. The absorption peak between 1200–1300 cm−1 was assigned as the stretching vibration of phenolic hydroxyl groups. The characteristic stretching vibration peak at 800 cm−1 indicated the existence of Si-O, which shows that the straw contained silicon, consistent with matching XRD results.
Specific surface area and pore structure analysis
) shows adsorption isotherms before and after adsorption of H2 S by straw charcoal prepared under optimal process conditions. is the pore diamater and pore volume distribution ratio before and after adsorption.The figure show that sample adsorption increased sharply with increasing N2 equilibrium pressure and reached the highest point when the relative pressure P/P0 = 0.3, before decreasing as the equilibrium pressure was further increased. It can be seen from the curve that the phase of the adsorption platform was almost horizontal, typical of I adsorption lines according to IUPAC classification. It shows that the prepared adsorbent had the adsorption performance of a micro-mesopore adsorbent. The shapes of the two adsorption and desorption curves were basically the same. However, the adsorption capacity before adsorption was higher than that after adsorption, indicating that the former had more pore structure than the latter. As shown in the specific surface area and pore size distribution , the specific surface area, reaching 1104.84 m2• g−1 before adsorption, was reduced to 904.60 m2• g−1 after adsorption, and the pore volume decreased from 0.261 cm2• g−1 before adsorption to 0.214 cm2• g−1 after adsorption. It can be seen in the figure (b) that the pore size and pore volume are significantly reduced after adsorption.The carbonaceous adsorbent underwent a chemical reaction after it adsorbed H2S gas, generating S containing substances that may block the pore structure. Therefore, in addition to physical adsorption, the carbonaceous adsorbent produced a multi-layer chemical adsorption process.
Table 1. Pore area and volume distribution data.
Carbonaceous adsorbent before and after adsorption
The pore size distribution data before and after adsorption are provided in . In combination with (b) in , it can be seen that most of the pore diameters before and after adsorption were concentrated in the range of 2 to 5 nm and accounted for more than 70% of the total pore volume. And the pore volume is reduced by about 60.8% before and after adsorption.This shows that the pore size distribution of the prepared carbonaceous adsorbent was relatively uniform, with predominant mesoporous structures, which are excellent adsorption products.
Conclusion
In this paper, a carbonaceous adsorbent was prepared using waste straw biomass, which is difficult to handle, as the raw material, and its adsorption performance with H2S as the target pollutant was studied. Elemental analysis of the straw raw material showed the major elemental composition was C, 36.27%; N, 0.56%; H, 7.29%; O, 0.104%.The best conditions for preparing straw-based carbonaceous adsorbent were with 30% ZnCl2 activator concentration, a carbonization temperature of 550°C, and a liquid-to-material ratio of 3:1. For the carbonaceous adsorbent H2 S prepared under these conditions, the useful absorption time was extended to 198 min. XRD, FT-IR, SEM, and specific surface area tests were performed on the straw-based carbonaceous adsorbents. The results show that increased carbonization temperatures increased the interplanar spacing, which makes it easier to form microporous structures that facilitate adsorption. There are -OH, -CH-, and -C = O groups on the surface, and the hydroxyl content was reduced after carbonization. The specific surface area can reach 1104.84 m2• g−1, and the total pore volume can reach 0.261 cm3• g−1, of which more than 80% is mesopore volume. The void structure is well developed.
Additional information
Notes on contributors
L. Li
L. Li is a teaching assistant at Northeast Electric Power University, Jilin City, Jilin Province, China.
F. Li
F. Li is a professor at Harbin University of Science and Technology, Heilongjiang Province, China.
References
- Bagreev, A., S. Bashkova, D. C. Locke, and T. J. Bandosz. 2001. Sewage sludge-derived materials as efficient adsorbents for removal of hydrogen sulfide[J]. Environ. Sci. Technol. 35 (7):1537–43. doi:10.1021/es001678h.
- Bandosz, T. J. 2002. On the adsorption/oxidation of hydrogen sulfide on activated carbons at ambient temperatures[J]. J. Colloid Interface Sci. 246 (1):1–20. doi:10.1006/jcis.2001.7952.
- Cronje, K. J., K. Chetty, M. Carsky, J. N. Sahu, and B. C. Meikap. 2011. Optimization of chromium (VI) sorption potential using developed activated carbon from sugarcane bagasse with chemical activation by zinc chloride[J]. Desalination. 275 (1–3):276–84. doi:10.1016/j.desal.2011.03.019.
- Erdem, M., S. Ucar, S. Karagöz, and T. Tay. 2013. Removal of lead (II) ions from aqueous solutions onto activated carbon derived from waste biomass. Sci. World J. 1–7. doi:10.1155/2013/146092.
- Hameed, B. H., and A. A. Rahman. 2008. Removal of phenol from aqueous solutions by adsorption onto activated carbon prepared from biomass material[J]. J. Hazard. Mater. 160 (2–3):576–81. doi:10.1016/j.jhazmat.2008.03.028.
- Jeyaseelan, S., and L. G. Qing. 1996. Development of adsorbent/catalyst from municipal wastewater sludge[J]. Water Sci. Technol. 34 (3–4):499–505. doi:10.2166/wst.1996.0469.
- Kante, K., C. Nieto-Delgado, J. R. Rangel-Mendez, and T. J. Bandosz. 2012. Spent coffee-based activated carbon: Specific surface features and their importance for H2S separation process[J]. J. Hazard. Mater. 201:141–47. doi:10.1016/j.jhazmat.2011.11.053.
- Liu, D., W. Zhou, and J. Wu. 2016. CeO2–MnOx/ZSM-5 sorbents for H2S removal at high temperature. Chem. Eng. J. 284:862–71. doi:10.1016/j.cej.2015.09.028.
- Mohanty, K., M. Jha, B. C. Meikap, and M. N. Biswas. 2005. Removal of chromium (VI) from dilute aqueous solutions by activated carbon developed from Terminalia arjuna nuts activated with zinc chloride[J]. Chem. Eng. Sci. 60 (11):3049–59. doi:10.1016/j.ces.2004.12.049.
- Neal, A. B., and R. C. Loehr. 2000. Use of biofilters and suspended-growth reactors to treat VOCs[J]. Waste Manage. 20 (1):59–68. doi:10.1016/S0956-053X(99)00297-4.
- Rozada, F., M. Otero, A. Moran, and A. Garcia. 2005. Activated carbons from sewage sludge and discarded tyres: Production and optimization[J]. J. Hazard. Mater. 124 (1–3):181–91. doi:10.1016/j.jhazmat.2005.05.002.
- Tzu-Hsing, K., C. Hsin, and C. Lung-Kai. 2005. The sorption of hydrogen sulfide from hot syngasby metal oxides over supports[J]. Chemosphere. 58:467–74.