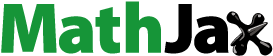
ABSTRACT
To achieve a more sustainable waste-to-energy (WTE) process, the recycling of solid waste incineration (MSWI) bottom ash (BA) has received large attention nowadays. This study investigated how WTE BA form is changed after the hydration and the impacts of WTE BA hydration on its leaching characteristics by using geometrical and leaching tests when incorporated in cement matrix for the recycling. The material composition and characteristics of anhydrous BA, hydrated BA, cement paste, Portland cement concrete (PCC), and BA-combined PCC were evaluated through scanning electron microscopy, X-ray spectroscopy and X-ray diffraction analyses. The results confirmed that the WTE BA newly formed a complex phase of hydration products in a cement matrix. Synthetic precipitation leaching procedure (SPLP) test was also conducted to investigate the leaching behaviors of alkaline components and metals of BA in the crushed BA-PCC samples. Through the leaching study, the leachability of crushed BA-combined concrete was rigorously evaluated when recycled as construction materials (e.g. base, subbase, subdrainage, etc.), which is the worst–case scenario. The results revealed that the release of highly alkaline elements increases with increasing BA content. However, the release of trace metals was reduced by 20-30% significantly when mixed properly with Portland cement concrete (PCC), which is due to both physical and chemical binding in cement hydration products. In addition, the thresholds of water regulations, set by the World Health Organization (WHO) and the Environmental Protection Agency (EPA) of the United States, were assessed as the basis for evaluating the extent of the risk of the leaching of toxic materials.
Implications: This study investigated how waste to energy (WTE) bottom ash (BA) form is changed after the hydration and the impacts of WTE BA hydration on its environmental leaching characteristics by using geometrical and leaching tests when incorporated in cement matrix for the recycling. Incorporating of WTE BA in cement mixture can form new mineralogical phases of hydration products in cement matrices such as Copper Hydrogen Arsenate Hydrate and Jahnsite. A significant reduction of alkaline elements (Si, Al, and K) from crushed PCC mixed with WTE BA due to the hydration. The lowest concentrations of major alkaline elements leached from the crushed PCC containing either 10% or 20% of BA contents. The averaged leaching concentration of detected elements is substantially below the water quality guidelines (provided by U.S. EPA and WHO) except Al.
Introduction
In 2017, municipal solid waste (MSW) was being produced at the rate of 267.8 million tons per year in the U.S. and disposal included 52.1% by landfilling, 35.2% by recycling and composting, and 12.7% by incineration (U. S. EPA Citation2016). Among the management of MSW, an incineration has been an area of increasing focus since it does not only reduce the principal method of disposal (i.e. landfilling) but can also be a means of energy production. The term, Waste-to-Energy (WTE) or Energy-from–Waste, is the energy recovery process of generating heat, thus electricity, heat from the burning of municipal solid wastes and other industrial, agricultural, and forestry residues (WTERT). Through the process, the total volume of MSW by more than 80% is reduced as well as a way to generate energy is provided (Chandler et al. Citation1997), which is beneficial environmentally and economically. However, even though energy production and a reduction of MSW are expected from the WTE process due to the incineration, there remains a by product known as municipal solid waste incineration (MSWI) after the process, such as WTE fly ash and bottom ash. Thus, finding ways to achieve a more sustainable WTE process and to consume MSWI ashes have received large attention nowadays (Silva et al. Citation2019; Yang et al. Citation2018).
The WTE process primarily has two types of incineration products that are bottom ash (BA) and fly ash (FA). Both products can be considered as possible replacements for a portion of the fine or coarse aggregate used in the production of cementitious and bituminous materials such as Portland cement concrete (PCC) and asphalt concrete (AC), respectively. BA and FA have been known to contain hazardous and toxic materials. However, BA is more practical for use than FA for two reasons: 1. BA represents approximately 80-90% of the total MSW WTE process product (Chandler et al. Citation1997; U. S. EPA Citation2016), and 2. BA has relatively low amounts of hazardous or toxic material components compared to FA, which means BA has more potential to be recycled safely. FA material usually is found to have considerable amounts of toxic material, heavy metals, chlorides and alkaline salts, including Pb, Zn, Cr, Ni, Cu, Cl, Na, K, Ca, and others (Kida, Noma, and Imada Citation1996; Quina, Bordado, and Quinta-Ferreira Citation2011).
However, there has been still concern and latent issues about the environmental safety of using BA as a construction material (Forteza et al. Citation2004; Gao et al. Citation2017; Li et al. Citation2012; Silva et al. Citation2019). The use of the BA as a recycled aggregate with PCC for a base in pavement systems can significantly affect the surrounding environment and its leachate can transport to groundwater (Kim et al. Citation2016, Citation2015; Li et al. Citation2012; Silva et al. Citation2019). Even though many studies have been performed to investigate the leaching behaviors of the ash-cement composites, the interaction between a variety of substance in BA and cement during the cement hydration process is still unknown. With regard to chemical reactions, even though BA has relatively low amounts of hazardous or toxic material components compared to FA, a relatively large amount of the toxic alkaline substance and heavy metals might be generated from the final cement-composite material in comparison with environmental regulations such as regulations given by U.S. EPA or the World Health Organization (WHO) (An et al. Citation2014; Chandler et al. Citation1997; EPA, Citation1988, Citation2008, Citation2009; Vehlow Citation2012; WHO Citation2004; Wiles and Shepherd Citation1999). This final matrix of cement composite forms as the result of a complicated process involving many variables, including the materials present, temperature, the pH of the cementitious solution, curing time, etc. The addition of BA in cement composite changes the materials in the mixture, therefore it changes the source of crystallization of cement hydration products. The difference source of cement hydration can change the reaction temperature and the pH of the cementitious pore solution. As a result, the presence of the additional BA can cause the series of changes of the cement hydration process and lead to a new formation of cement hydrates involving the alkaline substances and heavy metals in BA. (Al Muhit, An, and Nam Citation2015; An et al. Citation2015; Chen et al. Citation2008; Dubey and Townsend Citation2007; Kim et al. Citation2015; Tang et al. Citation2015; Xue et al. Citation2009).
The objective of this study is to investigate the new formation of hydrates involving the alkaline substances and metals in the WTE BA by comparing the anhydrous materials prior to cement production and the resulting hydrated materials. The study utilized multiple materials characterization tools including Scanning electron microscopy (SEM), Energy-dispersive X-ray spectroscopy (EDS), and X-ray diffraction (XRD). EDS and XRD analyses assessed the material composition and characteristics of anhydrous BA, PCC, hydrated BA, cement paste, and BA-combined-cement-composite paste. The data were collected before and after the cement hydration process. Data were also collected using the synthetic precipitation leaching procedure test to further investigate leaching behaviors of the toxic materials in the cement-composite as the result of including the recycled WTE BA as a partial replacement of the aggregate in the cement product. The Synthetic Precipitation Leaching Procedure (SPLP) test utilized crushed PCC with BA test materials in order to simulate a worst-case scenario for leaching risks. Thresholds of water regulations, set by the World Health Organization (WHO) and the Environmental Protection Agency (EPA) of the United States, were used as the basis for evaluating the extent of the risk of the leaching of toxic materials.
Hydration of OPC with WTE BA
The hydration of OPC is quite a complex process that includes dissolution of anhydrous compounds and precipitation of hydration products (Bullard et al. Citation2011; Scrivener, Juilland, and Monteiro Citation2015; Thomas and Hamlin Citation2009). Tricalcium silicate (C3S), which is Alite, and Dicalcium silicate (C2S), which is Belite, are the major compounds of OPC and dominate the development of properties of calcium silicate hydrate (C-S-H) which is the primary binding compound in cement paste that provides a strength to concrete. OPC is composed of approximately 50 ~ 70% of C3S, 10 ~ 20% of C2S and 5 ~ 10% of C3A. The overall hydration of C3S (Ca3SiO5), C2S (Ca2SiO4) and C3A (Ca3Al2O6) can be described as follows (Bullard et al. Citation2011; Scrivener, Juilland, and Monteiro Citation2015):
where H is water (H2O), CH is calcium hydroxide (Ca(OH)2) and C1.7-S-Hx is calcium silicate hydrate. The variable x in EquationEquations (1(1)
(1) ) and (Equation2
(2)
(2) ) represents the associated water in calcium silicate hydrate. In addition, the ratio of moles of calcium to silicon is varied and depending on the concentration of calcium and silicon ions in cement pore solution (Bullard et al. Citation2011; Scrivener, Juilland, and Monteiro Citation2015). shows the fundamental process of cement hydration. describes the process of the dissolution of a cement grain in water at the initial stage of hydrolysis. describes the nucleation of C-S-H and the crystallization of CH.
Figure 1. Fundamental process of cement hydration with WTE BA (a) the dissolution of cement grain in water at the initial stage, (b) the nucleation of C-S-H and the crystallization of CH, (c) the dissolution of cement grain and WTE BA in water at the initial stage, and (d) the nucleation of C-S-H and the crystallization of CH and the new formation of hydrates (NFH)
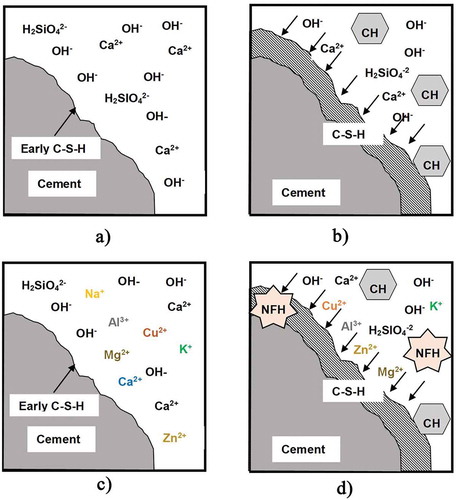
When ordinary Portland cement (OPC) is mixed with WTE BA, both materials may react simultaneously to be influenced. Therefore, to investigate the effects of WTE BA on cement hydration, it is important to know hydration of WTE BA as well as that of cement compounds in terms of the chemical process at ordinary temperature. Since WTE BA is a relatively reactive material compared to fine and coarse aggregates that are regarded as inert materials in the cement matrix composite, it can result in another formation of hydrates. conceptually shows the hydration process of OPC with WTE BA. portrays the dissolution of cement grain and WTE BA in water at the initial stage of hydrolysis. illustrates the nucleation of C-S-H, the crystallization of CH, and the new formation of hydrates (NFH) due to the chemical compounds of WTE BA. When OPC dissolves in water it creates an alkaline environment, with a solution pH of approximately 12. In this high alkaline condition, many alkaline and metal materials also can be dissolved and activated.
Many studies on the cement hydration process with alkaline and heavy metal materials present, which exists in WTE BA, have been investigated. Ataie et al. (Citation2015) compared the retarding mechanisms of zinc oxide (ZnO) and sucrose (C12H22O11) on cement hydration (Ataie et al. Citation2015). The chemical and mechanical behaviors of magnesium oxide (MgO) in concrete were reviewed by Yan and Chen (Citation2015). Beaudoin, Ramachandran, and Feldman (Citation1990) reported the interaction between chloride (Cl¯) and C-S-H (Beaudoin, Ramachandran, and Feldman Citation1990). Chappex and Scrivener (Citation2012) demonstrated the effect of aluminum (Al) in cementitious materials (Chappex and Scrivener Citation2012). Due to the complexity of WTE BA containing different types of alkaline and metal elements, each of the BA compounds may affect cement hydration differently. As shown in , different types of alkaline elements (such as Al, Ca, K, Na and Si) and metal elements (such as Cu, Fe, Mg, Ti, and Zn) can be dissolved from WTE BA and precipitated as a new formation of hydrates (NFH). In this study, XRD, EDS and SPLP data of the anhydrous WTE BA, OPC, cement paste, and the BA-combined paste were used to investigate possible cement hydration processes with the BA compounds.
Materials
Sample preparation of cement paste and PCC containing BA
The test specimens for the leaching tests are the crushed cement paste and BA-mixed concrete in order to evaluate the feasibility of recycling of the crushed BA-mixed concrete as unbound aggregate. The WTE BA used in this study was obtained from a refuse-delivered fuel (RDF) waste to energy facilities in Florida, USA. It is known that RDF facility can effectively sort out metallic materials; thus, the recovery of ferrous and some of the nonferrous metals can be considerably increased (Sarc and Lorber Citation2013). Scanning electron microscopy (SEM) was used for the microstructural morphology of the WTE BA (). For comparison, other SEM images of supplementary cementitious materials (SCMs) () are also presented (Association, Citation2009). As can be seen in , the difference in shape, size and surface texture between the WTE BA and other SCMs are clearly shown. Unlike other SCMs, which exhibit a round-shape ( (Association Citation2009)), there is no distinguishable pattern to the WTE BA () due to having an amorphous phase. In addition, the WTE BA shows high porosity which results in the low specific gravity and high absorption capacity (An, Kim, and Nam Citation2017).
Figure 2. SEM image of (a) anhydrous WTE BA (1,000 X magnification) and other supplementary cementitious materials (b) coal fly ash and (c) silica fume
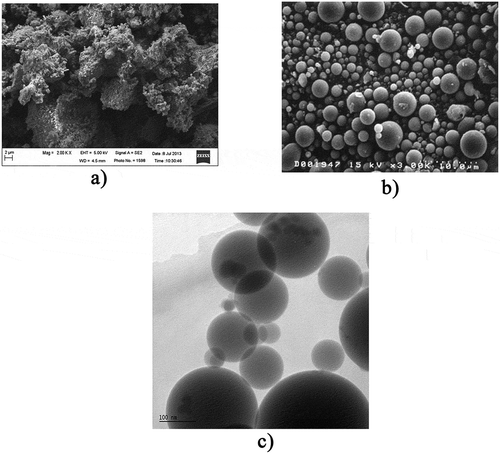
The BA was oven-dried to remove any residual moisture from a quench process performed at the RDF incineration plant, then screened to a particle size finer than 75 µm for the replacement of Portland cement in the cement paste and BA was sieved and screened between 75 µm and 4.75 mm sieves to meet the ASTM standard of fine aggregate. BA-combined cement paste is used for investigating the effect of BA on the cement hydration and PCC containing BA is used for assessing the leaching behavior of BA from PCC. Fine aggregate through which sand particle passed 4.75 mm was used. Limestone which has the nominal maximum size of 19 mm was utilized as coarse aggregate. Ordinary Portland cement (OPC) Type I, which is conformed to ASTM C150, was used in this study. Based on ASTM C305, five different sets of cement paste specimens (cubic specimens 50 × 50 × 50 mm3) with a water-to-cement (w/c) ratio of 0.5 were casted using 0%, 10%, 20%, 30%, or 50% BA, replacement of OPC. Moreover, five different sets of concrete specimens (cylindrical specimens 100 × 200 mm2) were casted and cured with w/c ratio of 0.5. For the cylinder concrete specimens, the varied proportion of BA (0%, 10%, 20%, 30%, or 50%) was employed as the replacement of the fine aggregate. Cement paste and concrete mix designs are presented in . For instance, P and C stand for the control cement paste and concrete, respectively. BP10 and B10 indicate cement paste and concrete containing 10% of BA as a substitute for OPC and fine aggregate, respectively. All specimens were air-cured in order to avoid creating pre-leachate from wet curing.
Table 1. Mix proportions of cement paste and concrete specimens (kg/m3)
The hardened concrete specimens were then crushed to obtain particle sizes ranging from 10 to 30 mm. These crushed BA contained concretes are used for SPLP test to simulate a worst-case scenario for leaching risks.
Experimental methods
Elemental and mineralogical analyses of WTE BA, OPC, and BA-combined cement paste
Elemental and mineralogical analyses of the BA were carried out using EDS and XRD, respectively. Average chemical compositions (elemental and oxide form) of BA are listed in . BA, in general, contains Silicon (Si), Calcium (Ca), Aluminum (Al), Sodium (Na), Potassium (K), and Iron (Fe) at major concentrations and Titanium (Ti), Magnesium (Mg), Copper (Cu), Chromium (Cr), and Zinc (Zn) at minor concentrations. The EDS results show that the major alkaline elements of the BA are Ca, Si, Al, Na, S, and K, the minor elements are Mg and Fe with metal contents of Ti, Cu, and Zn (see ). The oxide forms of the BA were calculated from the EDS data based on the assumption that most of the chemical elements were properly incinerated since MSW is combusted at a temperature of approximately 1,000°C (1,832℉) (An, Kim, and Nam Citation2017).
Table 2. Average chemical compositions of anhydrous BA and OPC (% by weight)
XRD was employed for the characterization of crystal structures of the BA, OPC, and BA-combined cement paste before and after hydration. The BP30 specimen which replaces 30% of OPC with BA in cement paste was chosen to present the XRD data because it was found in this study that the release of Cu, Mg, and alkaline (Al, Si, and K, etc.) was significantly reduced in 20-30% BA-combined concrete. For the XRD measurement, diffraction angles were kept 2θ = 5 until 80 degrees with Cu Ka radiation and 0.05 was chosen for step size to obtain appropriate phases. Mineralogical compositions were identified by a manual search of the Joint Committee on Powder Diffraction Standards (JCPDS) database.
SPLP batch test
According to the standard EPA method 1312 (EPA, Citation1994), SPLP batch tests were conducted to evaluate the leaching behavior of crushed PCC containing WTE BA. To consider realistic cases of exposure to stormwater infiltration, synthetic stormwater simulated in the east of the Mississippi River was prepared by mixing sulfuric and nitric acids in a solution with a pH of 4.2. The solid-to-liquid ratio was 1:20. The crushed PCC and extraction fluid were put into 2-L High-Density Polyethylene (HDPE) batch bottles and rotated in an agitator at 30 rpm for 24 hours. All SPLP extractions using zero-headspace extractor (ZHE) were then performed with a 0.25-μm filter paper under 350 kPa pressure, preserved with nitric acid at a pH of less than 2, and stored at 4°C. All SPLP leaching tests were performed in triplicate.
The SPLP batch test was performed over 72 hours (3 days) to investigate the effect of elapsed time on the leaching characteristic of the crushed PCC containing BA. For this case, the sample was collected every 24 hours, three times total. To evaluate the leaching characteristic of the crushed PCC containing WTE BA, Al, Ca, K, Na and Si (major alkaline elements) and Cu, Fe, Mg, Ti, and Zn (minor metals) were analyzed through inductively coupled plasma optical emission spectrometry (ICP-OES). Other toxic metals such as As, Cr, Cd, Hg, and Pb were under the detection limits of ICP-OES. When the concentrations of some solutions were too high, those elements such as Al, Ca, Na, K and Si were selectively diluted at a ratio of 1:50 and reanalyzed. The crushed PCC containing 10%, 20%, 30%, and 50% of WTE BA were used to simulate a scenario when PCC specimens are reused as a fine aggregate replacement. WTE BA “as is” specimens were tested as a control in comparison to the leaching potential of WTE BA in PCC specimens.
The concentration and pH of leached synthetic stormwater solution were measured after 24 hours. The average pH of each leached solution from BA contained PCC was 12.05 (0% BA), 11.18 (10% BA), 11.50 (20% BA), 12.17 (30% BA), and 11.98 (50% BA), respectively. The pH of BA itself was 11.62. In general, the pH of the leachate from PCC is higher than stormwater due to the presence of carbonates and hydroxides in PCC which increase its alkalinity (Dabo et al. Citation2009; De Windt et al. Citation2011; François and Pierson Citation2009; Izquierdo et al. Citation2008).
Results and discussions
Mineralogical analyses of anhydrous WTE BA and OPC
For a better understanding of the behavior of BA in cement hydration, crystal structures of anhydrous WTE BA and OPC were compared. As shown in , XRD data of anhydrous WTE BA and OPC are presented. The XRD pattern exhibits major crystalline phases in the anhydrous WTE BA, such as portlandite (Ca(OH)2), silica (SiO2), calcium oxide (CaO) and calcite (CaCO3) and minor compounds are calcium aluminate hydrate (Ca2Al(OH)7∙5H2O), jaffeite (Ca6(Si2O7)∙(OH)6), and tricalcium aluminate (Ca3Al2O6) as shown in . XRD results are found to be in agreement with EDS analysis (see ). According to , the major oxide compounds found in WTE BA are calcium oxide (CaO), silica (SiO2), and Sulfuric anhydride (SO3).
In the result of XRD of anhydrous BA, two oxide compounds of BA, which are calcium oxide (CaO) and silica (SiO2) are found noticeably. These oxide compounds are major oxide compounds of OPC (see ). These data present that WTE BA could be a feeder material to provide either Ca2+, CaOH+, or H2SiO42− for cement hydration. It is also interesting to note that several hydration products in WTE BA such as portlandite (Ca(OH)2), gibbsite (Al(OH)2) and jaffeite (Ca6Si2O7(OH)6) are found even though BA is one of the byproducts of WTE incineration process. The presence of these hydration products is due to a quench process in the post-combustion zone of the WTE incineration plant. The collected BA was quenched with water after the combustion and the moisture level in BA is approximately between 20% and 25% (Florida Department of Environmental Protection, Citation2010). Although BA appears to contain less soluble compounds due to this quenching process, exposure to acidic stormwater may lead to potential leaching of elements when incorporated into PCC. In addition, there are several metal elements in anhydrous BA based on the EDS data () such as Mg, Cu, Zn and Fe. A large part of these metals was properly incinerated (oxidized) due to the incineration process. The XRD result of anhydrous BA also shows magnesium oxide (MgO) which is a metal oxide. In the meantime, some metals were found in metallic form, even though the intensity of XRD data is relatively low, based on the XRD data ( and ) such as Mg, Cu, Zn and Fe. Because some metals might not be fully incinerated due to the size of metals.
Table 3. XRD peak profile of metallic solid (JCPDS)
The XRD data of OPC are also in good agreement with the EDS data (), as shown in . The major crystalline phases in anhydrous OPC are tricalcium silicate (C3S)/alite, dicalcium silicate (C2S)/belite and Tricalcium aluminate (C2A)/aluminate which are mostly the combination of CaO and SiO2.
Mineralogical analysis of anhydrous WTE BA and hydrated WTE BA
Mineralogical analyses of anhydrous WTE BA and hydrated WTE BA were also carried out using XRD. In a comparison of crystal structures of anhydrous WTE BA to those of hydrated WTE BA, possible chemical reactions can be explained during hydration. As expected, there are several hydration products in hydrated WTE BA such as thaumasite, kamaishilite, and reinhardbraunsite which are calcareous- and siliceous-based hydration products as compared with anhydrous WTE BA (see ). As shown in , the major chemical elements of anhydrous WTE BA are calcium and silicon.
Moreover, ettringite (Ca6Al2(SO4)3(OH)12 · 26H2O) and gypsum (CaSO4∙2H2O) were found. The presence of ettringite in hydrated WTE BA could be explained by the balance between aluminate and sulfate in the anhydrous WTE BA (see EquationEquation (4))(4)
(4) . During BA-water interactions, supersaturated mixture with respect to relatively high calcium, sulfate ions, and a low concentration of aluminate ions may lead to the quick formation of large crystals of ettringite which might be considered fail set (An, Kim, and Nam Citation2017). The existence of gypsum in hydrated WTE BA is due to the hydration of basanite (CaSO4·½ H2O) which is known as plaster of paris in anhydrous WTE BA (see EquationEquation (5)
(5)
(5) and ).
In addition, gibbsite (Al(OH)3) which is aluminum hydroxide is found from the hydrated WTE BA. During cement hydration, the pH of cement mix rises over 12 rapidly because of the release of alkaline hydroxide (OH−) ions. This particular environment can lead to the dissolution of metals in anhydrous WTE BA. Metallic aluminum in WTE BA can be reacted and precipitated as gibbsite (Al(OH)3). EquationEquation (6)(6)
(6) shows the possible chemical reaction of metallic aluminum in cement mix during hydration.
Mineralogical analyses of cement paste and BA-combined cement paste
Mineralogical compositions of BA-combined cement paste were also determined by XRD analysis and compared with the control cement paste (see Figure). With the comparison of XRD data between the control cement paste and BA-combined cement paste, the effect of BA on the cement hydration can be observed and accounted for. From the XRD data of the control cement paste, typical cement hydration products were found. Portlandite and ettringite which are the typical cement hydration products are exhibited in . Some unhydrated minerals of cement powder are also detected in the XRD data such as C3S and C2S. Because C-S-H which is the most important cement hydration product is amorphous, C-S-H is not exhibited in the XRD data. However, some crystalline C-S-H can be detected in the XRD data such as jennite (see ).
The XRD data of BA-combined cement paste show more a complex XRD pattern when compared to the control cement paste (see ). Although typical cement hydration productions such as portlandite and ettringite are found from BA-combined cement paste, the new formation of hydrates (NFH) is likewise found from the XRD data. As mentioned in the previous section, during cement hydration, the pH of cement mix rises over 12 rapidly because of the release of alkaline hydroxide (OH−) ions. This highly alkaline environment can lead the dissolution of metals in anhydrous WTE BA. Some of the dissolved metal ions in cement mix could be reacted and precipitated with dissolved cement compounds. shows the list of NFH found from the XRD data of BA-combined cement paste.
Table 4. List of the new formation of hydrates (NFH) in BA-combined cement paste
There are several possible stabilizations of toxic elements in cement hydration products during hydration of the BA-combined cement mix. The new formation of hydrates in are good examples to identify toxic waste stabilization in BA-combined cement paste (see and ). Cationic substitutions may replace the cement hydration products when Mg2+, Zn2+, and Fe2+ can replace Ca2+ in the crystal lattice (Day Citation1992). The other examples of toxic waste stabilization in the BA-combined cement paste are geminite (Cu(AsO3OH)(H2O)) and connellite (Cu19Cl4(SO4)(OH)323H2O) which can be found from XRD data in . Some of the copper ions (Cu2+) from the copper-bearing waste in WTE BA may react with cement components. Moreover, cement binder could precipitate the binding of ionized alkaline substances and metals from supersaturated aqueous substances in the cement-water mix (Day Citation1992; Li et al. Citation2012).
Leaching characteristics of alkaline substances
In , the relative concentrations of all major alkaline elements (i.e., Si, Al, K, Ca, and Na) and metals obtained from SPLP batch test were presented. The results are to realistically evaluate the leaching characteristics from crushed PCC samples containing different percentages of BA. To effectively compare the leaching characteristics of all alkaline substances, the relative concentration was used, which is the leaching concentration of PCC containing different BA contents over that of pure BA. The relative concentrations increased with adding the BA content in the PCC specimens. However, depending on the alkaline elements, two trends of the relative concentrations were observed. At low BA contents (10%-30%), one group including Si, Al, and K shows low increasing rate of the concentrations. The concentrations of PCC containing low BA contents ranged from 10% to 30% became lower than those for high BA content (50%). In particular, the concentrations of Al and Si were considerably low, which are less than 10%, for the PCC specimens with the low BA contents. However, the other group which includes Ca and Na shows high increasing rate of concentrations at low BA contents.
Table 5. Relative concentration (%) of major alkaline and metals in leaching from SPLP batch test
In , the release concentrations of alkaline elements including Si, Al and K with different amounts of BA contents are presented. The concentration of the elements except K remained less than 10% of concentrations when BA content ranged from 10% to 30% in comparison to pure BA specimen. Moreover, the concentration of 50% BA is less than 20% compared to that of pure BA.
Figure 6. Release concentration of (a) Si, (b) Al, and (c) K from PCC containing 10%, 20%, 30%, and 50% MSWI BA contents
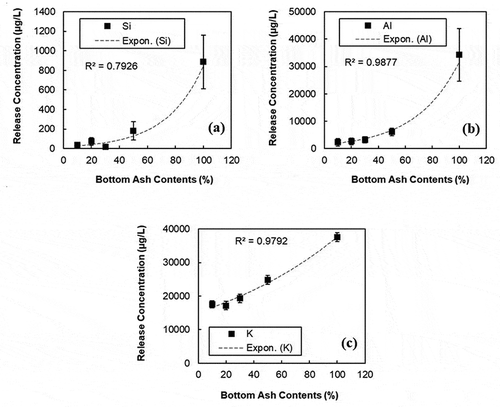
The hydration process in BA and PCC might affect this rapid reduction of the concentrations. To take an instance from Al, even though Al is abundant in the cement and BA (Dabo et al. Citation2009; De Windt et al. Citation2011; Kirkelund et al. Citation2012), it is easy to dissolve into the solution during the process. As ionized elements (e.g., aluminum and potassium ions) increase, pH of the solution increases even more. At high pH levels, Al can form oxyanions that has high solubility. In this high pH condition, Al+ can be consumed through hydration as follows:
Aluminum compounds in the cement and BA induce several reactions with ionized oxygens and hydroxyl groups (-OH). In accordance with the Pourbaix diagram of aluminum (Dabo et al. Citation2009; De Windt et al. Citation2011; Kirkelund et al. Citation2012), the aluminum is transformed to anionic AlO2¯ or a stable form such as Al2O3 when the pH of the solution is higher than 8.5. Thus, the released concentration of Al becomes low in the solution because Al might be consumed by either hydration or oxidation. Even though the released concentration of Al gradually increased with increasing the BA contents, the concentration of Al is much lower in the solution compared to that of the pure BA sample ().
In the same manner as aluminum that silicon compounds in the cement and BA can be consumed through the cement hydration when the silicon component is dissolved in the solution as silicon ions (Si4+). As discussed in the section “Hydration of OPC with WTE BA,” the silicon ion can be controlled by EquationEquations (1(1)
(1) ) and (Equation2
(2)
(2) ) during cement hydration. The concentration of potassium (K) (17,180.7 µg/L) released from the 20% BA−PCC specimen was considerably lower than that of the control (37,570.5 µg/L). The potassium ions (K2+) can be consumed by hydration as well. For the three elements (Al, Si and K), it was found that an optimized BA content for PCC is ranged between 20% and 30%. When the BA contents in PCC are higher beyond this range, the reaction might exceed the limit to capture these elements, which attributes to an increase in the released concentration.
On the contrary, the relative concentrations of Ca and Na were increased (see ). The major components of cement paste (calcium silicate hydrate (C-S-H), portlandite (Ca(OH)2), alumina-ferric oxide-trisulfate (Aft), alumina-ferric oxide-monosulfate (Afm), and ettringite) have the potential for alkaline leaching, especially Ca (Choi and Yang Citation2013). Calcium can also be released from calcium oxide (CaO), calcium sulfate (CaSO4), and portlandite (Ca(OH)2) which are contained in the cement and BA (). Hence, both PCC and BA result in the high percentage release of calcium (approx. 50,000 µg/L). Chen et al. (Li et al. Citation2012) report the high pH alkaline leaching behavior. However, depending on the amount of BA content, the leaching of Ca varies. For 10% BA, the concentration of Ca is low because free calcium ions can be either reacted or consumed by other ions in the supersaturated solution. However, for more than 20% replacement of BA with cement, the concentration of Ca ions may markedly increase when reacting with water to generate portlandite (Ca(OH)2). Because the pozzolanic component is a siliceous element it is proportionally reduced with the replacement of BA, adding more BA will result in more free calcium ions becoming available to generate portlandite instead of C-S-H. This is known that calcium hydroxide is soluble in an acid solution (SPLP leaching condition). Although free calcium ions react with other ionic compounds such as hydroxides, aluminum ions, and sulfates (EquationEquations (7(7)
(7) ) and (Equation8
(8)
(8) )), profuse free calcium ions can produce ettringite with sulfate and aluminum hydroxide (EquationEquation (9))
(9)
(9) .
Furthermore, thaumasite [Ca3Si(OH)6(CO3)(SO4)H2O] is a result of a transformation from C-S-H to C-S-S-H. This transformation is caused by the presence of sulfate (SO42¯) in the supersaturated cement solution (Rahman and Bassuoni Citation2014). This reaction can result in the loss of binding since C-S-H is denser than C-S-S-H (Rahman and Bassuoni Citation2014). Therefore, even though the concentration of BA is low, the leaching Ca is active in the leaching test solution and the concentration is high.
Leaching characteristics of metals
In , the relative concentrations of minor metals (i.e., Cu, Mg, Zn, Fe, and Ti) obtained from SPLP batch test were presented to investigate the leaching characteristics with the BA contents. Some metals might be physically encapsulated by the cement matrix as well as transformed into either stable or insoluble compounds through chemical reactions. Therefore, the concentration of metals decreased (Tang et al. Citation2015; Xue et al. Citation2009) when the PCC is mixed with the BA. Depending on the metals, two trends of the relative concentrations were observed. At low BA contents (10–30%), one group including Cu and Mg shows significantly the low concentrations (). This phenomenon is similar to what was noticed with the select alkaline ions (Si, Al, and K). Another group including Zn, Fe, and Ti shows high concentration but does not have any clear trend associated with the BA contents (). In , the release concentrations of Cu and Mg with different amounts of BA contents are presented. However, the release concentrations of Zn, Fe, and Ti are not presented because there is no clear trend associated with the BA contents.
Figure 7. Release concentration of (a) Cu and (b) Mg from PCC containing 10%, 20%, 30%, and 50% MSWI BA contents
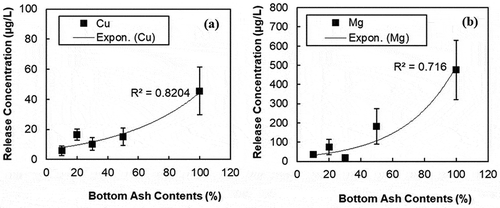
Based on the results of the SPLP test, the optimum addition of BA to capture metal elements in the cement matrix could be between 10-30% of BA (see ). Most of the copper or copper compounds will be physically encapsulated in the cement matrix. Metallic copper could be oxidized through the combustion process. Based on Pourbaix diagram for copper, most of copper oxides remain in oxidized form with the high pH condition. Thus, copper may not react with other hydrates in a cement matrix. In other words, most of copper oxides physically embedded in hardened concrete. However, there is still the possibility that a small amount of copper ions (Cu2+) from copper oxide may react with cement components. During cement hydration which can cause a pH over 12, high concentrations of chloride and sulfate can result in
In case of Magnesium (Mg), possible stable phases of magnesium compound are either Mg, MgO or Mg(OH)2 in the solution with pH higher than 8.5 on the basis of Poubaix diagram in electrochemistry. It is well known that pH of cement pore solution is usually higher than 11. Thus, magnesium compounds in cement matrix are Mg, MgO or Mg(OH)2. Moreover, these Mg or MgO can undergo phase changes through cement hydration process (see EquationEquations (11(11)
(11) ) and (Equation12))
(12)
(12) .
In other words, most of magnesium compounds are possibly stabilized in the cement matrix or react with other ionic compounds such as silicate (SiO4⁴¯) or oxyhydroxides (-O, -OH). Based on the result of XRD presented in , jahnsite (CaMg2MnFe(PO4)4(OH)28H2O) and ferrierite (NaMg(Si15Al3)O369H2O) are the evidence of magnesium phase change. Either stabilization or phase change of magnesium could lead to the reduction of the release concentration of magnesium from PCC. As can be seen in , 50% replacement of BA in PCC released 181.3 µg/L of the release concentration which is 38% of the release concentration of BA.
Zn release, however, appears not to have decreased significantly (varied between 0.6 and 1.5 µg/L) between the PCC containing BA and the BA due to its amphoteric high leaching behavior at high pH condition (Al-Abed et al. Citation2008). After the incineration process, most of the zinc or zinc compounds may be oxidized. These zinc oxides can be dissolved in supersaturated basic solution during cement hydration. Free zinc ions may be consumed by cement hydration and act as a retarder. Free zinc ions may react with free calcium ion to produce new phase as follows (see ):
It is interesting to note that the BA-PCC specimen which replaces 10% of sand with BA shows the highest relative concentration of Zn compared to other BA-PCC specimens (20%, 30%, and 50%) even though triplicate tests were performed (see ). This is because one of the 10% BA-PCC specimens produced a very high relative concentration in comparison with the other two specimens. This result shows that crushed PCC specimens may expose a chunk of metal on the surface which can result in an increased concentration of leaching value.
The released concentration of Fe had oscillated between 4.9 and 12.2 µg/L. Leaching behavior of Fe is insensitive to BA content. However, PCC contained 50% BA replacement indicates noticeable increment of leaching results for most of the metals. This may be attributed to the higher BA loading that introduces interfering elements (e.g., S) which can hinder the incorporation of metals into the Ca bearing mineral phases in PCC. Some of metals such as Pb and Cr were considered for leaching behavior; however, those metals were not detectable. Ti fluctuated between 0.1 µg/L for PCC with BA to 0.3 µg/L for the BA. The Ti can be negligible because the concentration of Ti is lower than the detection limit.
Relationship between elapsed time and leaching characteristics
shows the released concentration of select alkaline elements (i.e., Na, Al, Ca, K) and metals (i.e., Cu, Fe) from PCC containing different percentages of BA contents with time. The sampling was conducted at 1, 2, and 3 days into the test. Typically, the concentration increased with time due to increasing time exposed to the solution and leachate from cement and BA (Tasneem, Eun, and Nam Citation2017). Also, the concentration from PCC with higher BA content is higher than those with lower BA contents. However, the concentration of some of the selected substances had a gradual reduction in the rate of increase and approached the state of equilibrium within three days. For example, after the third day of leaching, Ca and K from PCC with 50% BA contents showed a peak concentration of approximate 55,000 µg/L and 29,000 µg/L, respectively. And, the released concentrations of Ca and K from PCC with 30% BA content appear to be stable after the third day of elapsed time (approximately 53,000 and 28,000 µg/L, respectively). The leaching of Ca and K increased less with increasing BA contents compared to other alkaline substances (i.e., Na, Al) (). For instance, as BA content increases from 10% to 50%, the released concentration of Ca increased by only 22%, while the concentration of Al increased by 260%. The effect of BA contents on leaching Ca and K is not significant compared to other alkaline substances. The concentration of Ca and K approached the steady state condition in the solution for the elapsed time (3 days).
Figure 8. Release concentration from PCC containing 10%, 30%, and 50% MSWI BA contents with time for alkaline substances (Na, Al, Ca, K) and metals (Fe, Cu): (a) Na, (b) Al (c) Ca, (d) K, (e) Cu and (f) Fe
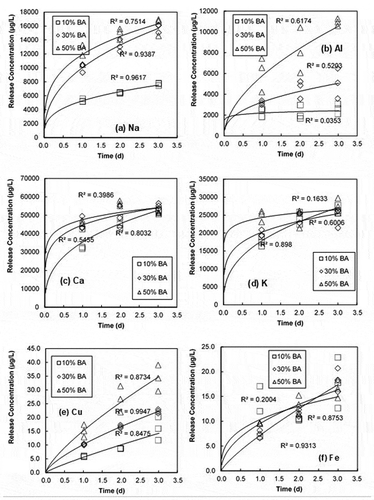
In case of metals (i.e., Cu and Fe), show the rising trend of the release concentration as the elapsed time increases. Although the release concentration of Cu and Fe increase in process of time, however, the levels of leached Cu and Fe are relatively very small in comparison with other alkaline elements (i.e., Ca and Al). For instance, the release concentration of Al after 3-day () is almost 280 times higher than the release concentration of Cu from 50% replacement of BA-PCC sample. This result may indicate that metals of BA in PCC might react with other ionic compounds or be stabilized in the cement matrix.
Comparison of leaching concentration with selected water quality guidelines
To evaluate the acceptance of the released concentration of select alkaline and metals (Cu, Fe, Zn, and Al) from BA-combined PCC and to check the risk of the leaching of toxic materials, the results of the leaching test were compared to the thresholds of water regulations given by U.S. EPA and the World Health Organization (WHO) (EPA Citation1988, Citation2008, Citation2009; WHO Citation2004). Maximum Contaminants Level (MCL), Secondary Maximum Contaminants Level (SMCL), and Drinking Water Quality Guidelines (DWQG) were chosen as the drinking water standard and Multi-Sector General Permit (MSGP) was used for the stormwater discharges standards. Three of these standards (MCL, SMCL, and MSGP) are regulated by U.S. EPA and DWQG is controlled by WHO. MCL is a legally enforceable standard for the public health while SMCL are non-enforceable guidelines. The purpose of DWQG is to protect public health by providing guideline values of constituents within water. MSGP is for the stormwater discharges associated with industrial activity. shows the drinking water standards for elements of interest (Cu, Fe, Zn and Al).
Table 6. Drinking water standards for elements of interest (μg/L) (U.S. EPA and WHO)
shows the comparison of leaching results for selected water quality guidelines. Each mark indicates the average released concentration of selected elements (Cu, Fe, Zn and Al) with different percentages of BA content as well as elapsed time. The dotted lines with notes represent each water standard guideline (SMCL, DWQG, and MSGP) for elements of interest. Since MCL only provides the guideline for Cu among elements of interest and is comparable to SMCL (1,300 μg/L of MCL and 1,000 μg/L of SMCL), MCL is substituted with SMCL.
Figure 9. Release concentration of selected elements (a) Cu, (b) Fe, (c) Zn and (d) Al from PCC containing 10%, 20%, 30%, and 50% WTE BA contents with water quality guidelines (SMCL, MSGP and DWQG)
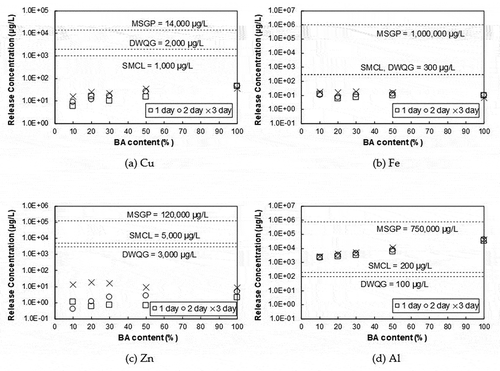
The averaged release concentration of all elements of interest is substantially below the water quality guidelines except for Al. As expected in case of Cu, the maximum concentration of Cu was measured with the BA-only control specimen, ranging from 70.1 to 22.9 μg/L. For the release concentration of Fe, there was not much difference between BA-only control specimen and BA-combined PCC specimen. This result could be predicted since the bottom ash was from a refused-delivered fuel (RDF) incineration plant. RDF facility can effectively sort out ferrous metals.
The leaching result of Zn shows a different pattern when compared to other elements of interest. The maximum release concentration of Zn at 1 day was measured with BA “as is” control specimen. However, the release concentration of BA-combined PCC specimens increased in process of time as compared with BA “as is” control specimen. This phenomenon may indicate that not only physically bonded Zn components but chemically bonded Zn components in cement matrix were leached out in acidic condition. Since the solubility of Zn in acid is high, there is a possibility that both physically and chemically bonded Zn components with the cement hydration products were dissolved in the acidic solution.
Al is the only exception that exceeds some of the water quality guidelines (SMCL and DWQG). This result might be due to the limitation of nonferrous metal screening at the RDF facility. Even though RDF facilities may provide separation procedures such as flail mill, disc screens, air knife, magnetic separation, and secondary shredding, some of the nonferrous metals such as Al and Ni (nickel) are not properly sorted out. Thus, those residuals could be leached out more during the leaching test when compared to other metallic materials.
Conclusion
In this study, the elemental and mineralogical characteristics and leaching behavior of the BA-combined concrete (as crushed aggregate) were investigated to evaluate the feasibility of the recycling of crushed PCC containing WTE BA when incorporated in cement matrix for the recycling. Elemental and mineralogical analysis of WTE BA and crushed PCC containing BA were conducted by using petrographic analysis tools such as SEM, EDS, and XRD. In addition, the SPLP test was conducted to investigate the leaching behaviors of alkaline components and metals of BA in the crushed BA-PCC samples. Moreover, the leaching results of BA-PCC samples were compared with thresholds of water regulations (WHO and U.S. EPA) for evaluating the extent of the risk of the leaching of toxic materials. On the basis of the experimental results, the following conclusions were made:
Incorporating WTE BA into cement mixtures can form new mineralogical phases of hydration products in cement matrices such as connellite (Cu19Cl4(SO4)(OH)32 · 3H2O) and jahnsite (CaMg2MnFe(PO4)4(OH)28H2O). This result of XRD testing indicates that some of the metals might potentially be encapsulated in the cement matrix by chemical bonds.
Crushed BA-mixed PCC demonstrated a significant reduction of alkaline elements (Si, Al, and K). Leaching of all major alkaline elements mostly showed the lowest concentrations when the crushed PCC contained either 10% or 20% of BA contents. The result of SPLP shows that some of the alkaline elements in BA might be consumed by cement hydration (e.g. Si and Ca) and hydration (e.g. Al and K).
The crushed PCC including BA appeared to be less promising to encapsulate Fe and Ti. When the crushed BA-combined PCC was leached out by the stormwater, leaching behavior of Fe and Ti is not sensitive to the BA content. Ineffectiveness to capture those metals into PCC matrix can be attributed to the dissolution of cement hydration products (e.g. Ca(OH)2) due to an acidic environment.
The concentrations of most major alkaline elements (e.g. Ca, Si, and Na, except Al) from the BA-combined PCC reached steady state with increasing elapsed time due to the availability of possible leachable elements. However, leaching of minor metals (e.g. Cu and Fe) showed an unclear pattern. Cu and Fe seem mainly physically (not chemically) encapsulated in a cement matrix; thus, they can be exposed to stormwater and get leached out.
The leaching results show that the averaged release concentration of all elements of interest is substantially below the water quality guidelines (provided by U.S. EPA and WHO) except for Al. Al is the only exception that exceeds some of the water quality guidelines (SMCL and DWQG). This result might be due to the limitation of nonferrous metal screening at RDF facility.
Disclosure statement
No potential conflict of interest was reported by the authors.
Additional information
Notes on contributors
Jinwoo An
Jinwoo An is currently an Assistant Professor at the School of Engineering (Civil Engineering) at the University of Mount Union. He received his Ph.D. in Civil Engineering from the University of Central Florida in 2015. His research field can be classified into three categories: 1) Characterization of recyclable materials for sustainability in construction and civil engineering, 2) Utilization of new advanced nanomaterials in cement and concrete composites to develop multifunctional construction materials, and 3) Investigation on the relationship between sustainable materials and the environment.
Boo Hyun Nam
Boo Hyun Nam is currently Associate Professor of Department of Civil, Environmental, and Construction Engineering (ECE) at University of Central Florida (UCF). His research includes the areas of characterization of multiple civil engineering materials (i.e., cement/concrete, aggregate, soil, solid waste, etc.), nano-engineered cementitious composites, and mechanical characterization of cement/concrete. Dr. Nam serves multiple technical committees of ASCE Geotechnical-Institute (GI) and Transportation Research Board (TRB). He is a current faculty advisor of ASCE-UCF student chapter advisor.
Byoung Hooi Cho
Byoung Hooi Cho is currently an Assistant Professor of the Department of Civil Engineering at Sangmyung University, Republic of Korea. After his Ph.D. at The University of Texas at Austin, he worked as an engineering manager in Samsung C&T and then as Postdoctoral researcher at University of Central Florida. His research areas include use of nanotechnology (e.g., graphene, carbon nanotube) in concrete, characterization of cement-based materials, and polymer-based concrete structures (e.g., Latex-modified concrete, waterproofing concrete systems, etc.).
Jongwan Eun
Jongwan Eun is an Assistant Professor in the Department of Civil and Environmental Engineering at the University of Nebraska-Lincoln. Dr. Eun received an M.S. from the University of Texas at Austin, and received his Ph.D. degree from the University of Wisconsin-Madison focused on Geoenvironmental Engineering. Dr. Eun has over 15 years of professional and academic experience in Geotechnical and Geoenvironmental engineering. His research interest is focused on waste containment system, GHG emission controls, and radioactive material disposal. Dr. Eun is a member of three technical committees (geosynthetics, and unsaturated soil mechanics) of Geo-Institute, ASCE.
References
- A. C. A. Association. 2009. Fly ash facts for highway engineers.
- Al Muhit, B. A., J. An, and B. H. Nam 2015. Recycling of Municipal Solid Waste Incineration (MSWI) ash as aggregate replacement in concrete. IFCEE 2015. San Antonio, Texas.
- Al-Abed, S. R., G. Jegadeesan, J. Purandare, and D. Allen. 2008. Leaching behavior of mineral processing waste: Comparison of batch and column investigations. J. Hazard. Mater. 153 (3):1088–92. doi:10.1016/j.jhazmat.2007.09.063.
- An, J., B. Golestani, B. H. Nam, and J. L. Lee. 2015. Sustainable utilization of MSWI bottom ash as road construction materials, part I: Physical and mechanical evaluation. Airfield Highway Pavements 2015: 225–235.
- An, J., J. Kim, B. Golestani, K. Tasneem, B. Al Muhit, B. H. Nam, and A. Behzadan 2014. Evaluating the use of waste-to-energy bottom ash as road construction materials. Report No. BDK78-977-20, Florida Department of Transportation, Tallahassee.
- An, J.-W., J.-Y. Kim, and B.-H. Nam. 2017. Investigation on impacts of municipal solid waste incineration bottom ash on cement hydration. ACI Mater. J. 114 (5). doi:10.14359/51689712.
- Ataie, F. F., M. C. Juenger, S. C. Taylor-Lange, and K. Riding. 2015. Comparison of the retarding mechanisms of zinc oxide and sucrose on cement hydration and interactions with supplementary cementitious materials. Cem. Concr. Res. 72:128–36. doi:10.1016/j.cemconres.2015.02.023.
- Beaudoin, J. J., V. S. Ramachandran, and R. F. Feldman. 1990. Interaction of chloride and C S H. Cem. Concr. Res. 20 (6):875–83. doi:10.1016/0008-8846(90)90049-4.
- Bullard, J. W., H. M. Jennings, R. A. Livingston, A. Nonat, G. W. Scherer, J. S. Schweitzer, K. L. Scrivener, and J. J. Thomas. 2011. Mechanisms of cement hydration. Cem. Concr. Res. 41 (12):1208–23. doi:10.1016/j.cemconres.2010.09.011.
- Chandler, A. J., T. T. Eighmy, O. Hjelmar, D. S. Kosson, S. E. Sawell, J. Vehlow, H. A. van der Sloot, and J. Hartlén. 1997. Municipal solid waste incinerator residues. Amsterdam, Netherlands: Elsevier Sci.
- Chappex, T., and K. L. Scrivener. 2012. The influence of aluminium on the dissolution of amorphous silica and its relation to alkali silica reaction. Cem. Concr. Res. 42 (12):1645–49. doi:10.1016/j.cemconres.2012.09.009.
- Chen, J. S., P. Y. Chu, J. E. Chang, H. C. Lu, Z. H. Wu, and K. Y. Lin. 2008. Engineering and environmental characterization of municipal solid waste bottom ash as an aggregate substitute utilized for asphalt concrete. J. Mater. Civ. Eng. 20:432–39. doi:10.1061/(ASCE)0899-1561(2008)20:6(432).
- Choi, Y. S., and E. I. Yang. 2013. Effect of calcium leaching on the pore structure, strength, and chloride penetration resistance in concrete specimens. Nucl. Eng. Des. 259 (Supplement C):126–36. doi:10.1016/j.nucengdes.2013.02.049.
- Dabo, D., R. Badreddine, L. De Windt, and I. Drouadaine. 2009. Ten-year chemical evolution of leachate and municipal solid waste incineration bottom ash used in a test road site. J. Hazard. Mater. 172 (2–3):904–13. doi:10.1016/j.jhazmat.2009.07.083.
- Day, R. L. 1992. The effect of secondary ettringite formation on the durability of concrete: A literature analysis. Skokie, IL: Portland Cement Association.
- De Windt, L., D. Dabo, S. Lidelöw, R. Badreddine, and A. Lagerkvist. 2011. Mswi bottom ash used as basement at two pilot-scale roads: Comparison of leachate chemistry and reactive transport modeling. Waste Manage. 31 (2):267–80. doi:10.1016/j.wasman.2010.06.002.
- Dubey, B., and T. Townsend. 2007. Leaching of milled asphalt pavement amended with waste to energy ash. Int. J. Environ. Waste Manage. 1 (2/3):145–58. doi:10.1504/IJEWM.2007.013629.
- Florida Department of Environmental Protection, F. D. 2010. Technical evaluation & preliminary determination. DEP File No. 0990234-017-AC (PSD-FL-413), Palm Beach Renewable Energy Facility No. 2.
- Forteza, R., M. Far, C. Seguı́, and V. Cerdá. 2004. Characterization of bottom ash in municipal solid waste incinerators for its use in road base. Waste Manage. 24 (9):899–909. doi:10.1016/j.wasman.2004.07.004.
- François, D., and K. Pierson. 2009. Environmental assessment of a road site built with MSWI residue. Sci. Total Environ. 407 (23):5949–60. doi:10.1016/j.scitotenv.2009.08.007.
- Gao, X., B. Yuan, Q. L. Yu, and H. J. H. Brouwers. 2017. Characterization and application of municipal solid waste incineration (MSWI) bottom ash and waste granite powder in alkali activated slag. J. Clean. Prod. 164 (Supplement C):410–19. doi:10.1016/j.jclepro.2017.06.218.
- Izquierdo, M., X. Querol, A. Josa, E. Vazquez, and A. López-Soler. 2008. Comparison between laboratory and field leachability of MSWI bottom ash as a road material. Sci. Total Environ. 389 (1):10–19. doi:10.1016/j.scitotenv.2007.08.020.
- Kida, A., Y. Noma, and T. Imada. 1996. Chemical speciation and leaching properties of elements in municipal incinerator ashes. Waste Manage. 16 (5–6):527–36. doi:10.1016/S0956-053X(96)00094-3.
- Kim, J., J. An, B. H. Nam, and K. M. Tasneem. 2016. Investigation on the side effects of municipal solid waste incineration ashes when used as mineral addition in cement-based material. Road Mater. Pavement Des. 17 (2):345–64. doi:10.1080/14680629.2015.1083463.
- Kim, J., B. H. Nam, B. A. A. Muhit, K. M. Tasneem, and J. An. 2015. Effect of chemical treatment of MSWI bottom ash for its use in concrete. Mag. Concr. Res. 67 (4):179–86. doi:10.1680/macr.14.00170.
- Kirkelund, G. M., A. S. Joergensen, T. Ingeman-Nielsen, and A. Villumsen 2012. Characterization of MSWI bottom ash for potential use as subbase in greenlandic road construction. Paper presented at the 4th International Conference on Engineering for Waste and Biomass Valorisation, Porto, Portugal.
- Li, X.-G., Y. Lv, B.-G. Ma, Q.-B. Chen, X.-B. Yin, and S.-W. Jian. 2012. Utilization of municipal solid waste incineration bottom ash in blended cement. J. Clean. Prod. 32 (Supplement C):96–100. doi:10.1016/j.jclepro.2012.03.038.
- Quina, M. J., J. C. M. Bordado, and R. M. Quinta-Ferreira. 2011. Percolation and batch leaching tests to assess release of inorganic pollutants from municipal solid waste incinerator residues. Waste Manage. 31 (2):236–45. doi:10.1016/j.wasman.2010.10.015.
- Rahman, M. M., and M. T. Bassuoni. 2014. Thaumasite sulfate attack on concrete: Mechanisms, influential factors and mitigation. Constr. Build. Mater. 73 (Supplement C):652–62. doi:10.1016/j.conbuildmat.2014.09.034.
- Sarc, R., and K. E. Lorber. 2013. Production, quality and quality assurance of Refuse Derived Fuels (RDFs). Waste Manage. 33 (9):1825–34. doi:10.1016/j.wasman.2013.05.004.
- Scrivener, K. L., P. Juilland, and P. J. M. Monteiro. 2015. Advances in understanding hydration of Portland cement. Cem. Concr. Res. 78 (Part A):38–56. doi:10.1016/j.cemconres.2015.05.025.
- Silva, R. V., J. De Brito, C. J. Lynn, and R. K. Dhir. 2019. Environmental impacts of the use of bottom ashes from municipal solid waste incineration: A review. Resour. Conserv. Recycl. 140:23–35. doi:10.1016/j.resconrec.2018.09.011.
- Tang, P., M. V. A. Florea, P. Spiesz, and H. J. H. Brouwers. 2015. Characteristics and application potential of municipal solid waste incineration (MSWI) bottom ashes from two waste-to-energy plants. Constr. Build. Mater. 83 (Supplement C):77–94. doi:10.1016/j.conbuildmat.2015.02.033.
- Tasneem, K. M., J. Eun, and B. Nam. 2017. Leaching behaviour of municipal solid waste incineration bottom ash mixed with Hot-Mix Asphalt and Portland cement concrete used as road construction materials. Road Mater. Pavement Des. 18 (3):687–712. doi:10.1080/14680629.2016.1186108.
- Thomas, J. J. A. J., and M. Hamlin 2009. Materials of cement science primer: The science of concrete. Final Report, the U.S. Department of Transportation, University Transportation Centers Program.
- U. S. EPA. 1988. National secondary drinking water regulations. https://www.epa.gov/sites/production/files/2015-11/documents/howeparegulates_cfr-2003-title40-vol20-part143.pdf
- U. S. EPA. 1994. SW-846 test method 1312: Synthetic precipitation leaching procedure.
- U. S. EPA. 2008. Multi-sector general permit for stormwater discharges associated with industrial activity (MSGP). https://www3.epa.gov/npdes/pubs/msgp2008_finalpermit.pdf
- U. S. EPA. 2009. Drinking water contaminants. (EPA 816-F-09-0004). http://www.nrc.gov/docs/ML1307/ML13078A040.pdf
- U.S. EPA. 2016. Municipal solid waste generation, recycling, and disposal in the United States: Facts and figures for 2014. https://www.epa.gov/sites/production/files/2016-2011/documents/2014_smmfactsheet_2508.pdf
- Vehlow, J. 2012. aste-to-energy ash management in Europe encyclopedia of sustainability science and technology, 11720–36. New York: Springer.
- WHO. 2004. Guidelines for drinking-water quality. Third edition volume 1: Recommendations. Geneva: World Health Organisation.
- Wiles, C., and P. Shepherd. 1999. Beneficial use and recycling of municipal waste combustion residues– A comprehensive resource document. Boulder, CO: National Renewable Energy Lab.
- Xue, Y., H. Hou, S. Zhu, and J. Zha. 2009. Utilization of municipal solid waste incineration ash in stone mastic asphalt mixture: Pavement performance and environmental impact. Constr. Build. Mater. 23 (2):989–96. doi:10.1016/j.conbuildmat.2008.05.009.
- Yan, S. L., and C. L. Chen. 2015. Influence of specimen size on autogenous volume deformation of concrete with magnesium oxide. IOP Conf. Ser. Mater. Sci. Eng. 103 (1):012001. doi:10.1088/1757-899X/103/1/012001.
- Yang, Z., R. Ji, L. Liu, X. Wang, and Z. Zhang. 2018. Recycling of municipal solid waste incineration by-product for cement composites preparation. Constr. Build. Mater. 162:794–801. doi:10.1016/j.conbuildmat.2017.12.081.