ABSTRACT
The two-stage technology of porous carbonaceous material obtained via pyrolysis in inert medium with subsequent activation by steam is well known. While steam could be a suitable substance for pyrolysis as well, single-staged technology for waste tire recycling is yet to be developed. A comparative analysis of the characteristics of the carbonaceous materials obtained by the single-staged steam pyrolysis of waste tires was carried out, which could provide a theoretical background for the development of such technology. The steam pyrolysis was performed in a tubular reactor in an overheated steam medium (500°C with 5 kg/h mass flow rate). The technical characteristics of the obtained samples were evaluated in the context of their potential for further application as absorbent and raw material for rubber production according to Chemical Abstracts Service No. 1333–86-4. The composition and physico-chemical properties of the obtained samples were studied using BET and thermogravimetric analysis, atomic emission, transmission and scanning electron microscopies, Raman, X-ray diffraction, and photoelectron spectroscopies. The results revealed that the structure and properties of all obtained carbonaceous material samples were similar. The samples consisted of amorphous carbon (with a disordered graphite lattice) and contained a significant amount of metal oxides. According to experimental data, zinc was present in the form of ZnO with a binding energy of 1022.4 eV, while sulfur was observed in the form of sulfide and oxysulfide with binding energies of 161.8 and 163.2 eV, respectively. According to electron microscopy, the morphology of samples was represented by a set of spherical agglomerates comprising nanosized particles. According to the BET analysis of the samples, the specific surface area varied in the range between 52.0 and 66.0 m2/g and the pore volume values were within a range of 0.53–0.87 cm3/g, while the average pore size varied from 412 to 527 Å.
Implications: Our paper presents original research in the field of characterization of solid material obtained by single-staged steam gasification of waste tires, which were produced and exploited in conditions of Russia. Modern technology allows thermal utilization of waste tires by obtaining powders of carbonaceous material, which could be used as fuel, adsorbent, etc., but this process usually consists of two stages – pyrolysis in inert medium and activation in steam or carbon dioxide. One of the most promising directions of technological development is simplifying this process into single step, ensuring that the obtained material could be used as carbon black or adsorbent for gas steam cleansing. No data on suitability of carbonaceous material obtained by single-step steam pyrolysis of all-season waste tires to be adsorbent and/or carbon black is present in the literature. In order to evaluate the suitability of the obtained material to be adsorbent, the high specific surface area should be determined, while CAS technical standards specify many chemical and physical properties of industrial carbon black.
The aim of the current article is to study the properties of carbonaceous material obtained during single-staged steam gasification of four different all-season tires (due to their widespread application worldwide) and evaluate its fitness as industrial-scale carbon black or adsorbent. The additional problem addressed was the evaluation of the variation in characteristics of carbonaceous material obtained due to different origins of tires. Experiments were conducted in a tubular lab reactor in order to simplify the experimental procedure while ensuring the applicability of the obtained results to practical conditions.
The obtained results could be used for the development of the technology for closed-cycle tire processing (because black carbon is used for tire production) and adsorbent production. The characteristics of the materials obtained allow us to choose optimal parameters for such treatment and develop special policies and programs, which will integrate and regulate waste tire utilization via steam gasification.
Introduction
The annual global growth of produced automobiles leads to an increase in the number of waste tires. According to statistics (global demand for car and light commercial vehicle tires from 2012 to 2018, Statista, Citation2019), in 2018, 1.624 million car tires were produced worldwide. A significant share of the total number of tires goes out of exploitation and ultimately becomes unsuitable for further use.
It should be noted that the storage of rubber waste (RW) is prohibited by the requirements for the industrial waste management (Mmereki, Machola, and Mokokwe Citation2019) and corresponding directives on the waste disposal and incineration (Kenzhin et al. Citation2019). This is connected to the high hazard class of such waste and high flammability (Li et al. Citation2005). It is known that the combustion of RW produces toxic substances that pollute the atmosphere, soil, and water (Labaki and Jeguirim Citation2017). Besides, tire dumps create favorable conditions for the reproduction of mosquitoes and other insects (Jang et al. Citation1998; Mui, Ko, and McKay Citation2004). In turn, this type of waste has a significant logistical advantage related to the possibility of organized collection and sorting of used tires at automobile service stations (Kyari, Cunliffe, and Williams Citation2005).
Modern approaches to RW disposal are based on thermal (conversion to energy and valuable raw materials for the industry) or mechanical processing (production of a crumb rubber). The latter option seems to be a very effective solution for ensuring the secondary use of RW in various fields because crumb or granular rubber is attractive material for the playgrounds, some sport surfaces, and rubber-modified asphalt (Shu and Huang Citation2014). At the same time, the volume of market for the abovementioned products is quite limited, which does not allow us to apply it for continuous sustainable RW utilization due to the much higher amount of waste tire generation.
The simplest way of RW disposal is their direct combustion at energy facilities. At the same time, this method can cause serious harm to the environment due to the intense release of ash, soot, heavy metals, and sulfur dioxide into the environment and some super-toxic compounds, like, dioxins or polyaromatic hydrocarbons (Jimoda et al. Citation2018). In turn, pyrolysis of RW does not cause such negative consequences, making it one of the most environmentally friendly solutions for RW thermal conversion into useful products compared to other utilization methods (Xu et al. Citation2020,12,13; Policella et al. Citation2019). This method allows us to obtain activated carbon (33–38 wt%), valuable oils (38–55 wt%), and gas-phase products (10–30 wt%) (Helleur et al. Citation2001). Pyrolysis gas has a high calorific value and can be used as a fuel to partially or completely compensate the energy consumption of pyrolysis unit and nearby infrastructure (Elbaba, Wu, and Williams Citation2010,17; Barbooti et al. Citation2004). The liquid hydrocarbon fraction obtained during pyrolysis has characteristics very similar to fuel oil. It could be used as heating fuel or a source of valuable substances such as limonene, benzene, toluene, and xylene (Helleur et al. Citation2001). The liquid fraction has also proven to be feasible alternative raw material for enterprises involved in oil processing into automotive fuels (Aranda et al., Citation2007). The carbon residue could be returned to the rubber production cycle, which increases the economic potential and market demand of product obtained (Martínez et al. Citation2019). However, in order to successfully introduce this material into existing industrial process with reasonable modification of equipment, it will be necessary for product characteristics to partially or completely comply with the requirements of CAS (Chemical Abstracts Service) No. 1333–86-4. Among them, the specific surface area, pore volume, ash, and the sulfur content are of most significance (López et al. Citation2009).
Improving carbon characteristics could be done by chemical or physical methods. The chemical method involves the use of an agent (KOH), which ensures the sufficient activation of the carbon-containing material obtained under the conditions of classic pyrolysis (Sun et al. Citation1997). Physical methods of improving the obtained carbon characteristics involve the application of carbon dioxide and superheated steam (López et al. Citation2009). Moreover, the latter is more effective due to the smaller size of water molecules, which allows ensuring their more effective diffusion into the pores of carbon particles. It also promotes the increase of the particles' specific surface area due to pore expansion (Cunliffe and Williams Citation1999; González et al. Citation2006; Mui, Ko, and McKay Citation2004). It is also worth noting that the use of steam instead of carbon dioxide allows moderating or even completely eliminating the carbonization of carbon formed during the thermal decomposition of RW.
For instance, reported in González et al. Citation2006 are the characteristics of the formed carbon after two-stage heat treatment in an N2 medium at a temperature of 800°C and subsequent activation by steam and carbon dioxide at various temperatures. The application of steam (at a temperature of 900°C) as a heating medium, in contrast to CO2, facilitated an increase in the specific surface of the particles and a number of micropores formed. Steam activation of carbon also reduced the sulfur content in material obtained (Lopez et al. Citation2012; López et al. Citation2009), which is strictly regulated by CAS No. 1333–86-4 for industrial applications. Additionally, by means of high-temperature steam activation, the ash content could also be reduced due to the removal of organometallic components (Helleur et al. Citation2001). However, the use of high-temperature steam led to a decrease in the amount of carbon produced, while the energy consumption was increased. As it was reported in (Kalitko Citation2010), in order to meet the requirements of CAS No. 1333–86-4, the characteristics of the carbon produced in industrial-scale conditions (while ensuring the uniform distribution of heat supplied to the feed) the lower temperatures of superheated steam supplied to the reactor (400–500°C) are recommended. The advantages of using superheated steam as an agent additionally include high heat capacity, explosion safety, and the possibility of smooth regulation of the thermal conversion process while simultaneously neutralizing environmentally hazardous compounds. Adjusting the steam flow rate allows us to control the total pressure in the system and overall reaction rate. The steam activation of the obtained chas allows us to utilize it as an adsorbent for different toxic and dangerous substances like mercury (Park and Lee Citation2018) or organic compounds (Hsi et al. Citation2011). This is why the application of steam for waste tire processing carries out the possibility to simplify the corresponding process into a single stage, thus allowing the reduction of the cost of the obtained material.
Apart from operating conditions, the type and origin of the waste tires have a noticeable effect on the carbon production process and characteristics of material obtained. They, in turn, depend on the technological features of their production and later exploitation (Kandasamy and Gökalp Citation2015). According to Kyari, Cunliffe, and Williams Citation2005, the specific surface area values and the sulfur content in the obtained solid products by the classical pyrolysis of the waste car tires of different types varied in a wide range (±17% and ±47%, respectively).
This paper presents a comparative analysis of the characteristics of carbonaceous material samples obtained by single-staged steam pyrolysis of waste car tires of the widely used types. The obtained samples were studied by a set of physicochemical analysis methods including X-ray diffraction (XRD) analysis, X-ray photoelectron spectroscopy (XPS) analysis, Raman spectroscopy, scanning electron microscopies (SEM), BET analysis, elemental analysis, transmission electron microscopy (TEM), atomic emission spectroscopy (AEM), etc. The consistency of the obtained carbonaceous material with requirements for industrial carbon black and gas adsorbent was evaluated.
Materials and methods
Materials
Four samples of waste all-season type tires of passenger cars were used as initial materials. This type of tire was chosen for the current study because it is widespread all over the world due to the all-weather character of exploitation (especially in countries without constant snow and ice during the cold season).
Tires were cut via a cutting tool into rectangular chips with simultaneous removal of the metal cord and textile before undergoing steam pyrolysis. The size of the samples (width × height × length) was 7 x 1 x 7 cm with the deviation of not more than 1 cm for both the width and the length. The obtained samples of initial RW were designated as 1/RW, 2/RW, 3/RW, and 4/RW. Technical characteristics and elemental composition of RW samples are presented in .
Table 1. Physico-chemical characteristics of the waste tire samples
Experimental setup
The principle scheme of the experimental setup for the single-staged RW steam pyrolysis is presented in .
The double-walled tubular steam pyrolysis reactor (with length l = 0.8 m and diameter d = 0.15 m) utilized the batch operation principle (in the case of processed material) with continuous steam purging through the system. At first, 0.5 kg of RW sample was loaded into a container made of a metal mesh, which was tightly fixed inside the reaction chamber. Then, the reactor was sealed, and the steam flow regulator was opened to ensure constant purging of the system with steam and reliable removal of the gases released during RW pyrolysis. Steam was produced in the steam generator, and then it was passed through the first stage of the superheater and an additional heat exchanger, where it was further superheated to the required temperature. The steam flow rate was set using a needle-type regulator and controlled using a flow rate meter, which was installed before the steam generator.
To reduce the error during the operation of the setup associated with the slow heating of the system, steam was supplied to the reaction chamber of the reactor after reaching a predetermined temperature. Following the introduction of steam into the reactor, additional heat was indirectly supplied to its annular space. The heat source was heated by air to a predetermined temperature using a thermoregulated air heater LHS 61 L Premium (Leister, Switzerland) with a power of 16 kW (maximum heating temperature 600°C). Air was supplied to the thermal heater using an Airpack high-pressure fan (Leister, Switzerland).
The gas-phase products formed during the RW steam pyrolysis were condensed in a tubular condenser. The liquid-phase products (water and liquid hydrocarbons) were discharged and accumulated into a storage tank. Temperature control inside the reactor and in the annular purge gap was carried out continuously using installed thermocouples (T1 and T2) connected to a multi-channel thermocouple recorder.
The steam pyrolysis of the studied waste tire samples was carried out at a temperature of 500°C and a steam flow rate of 5 kg/h for 1 h. After this time, the purging of the reactor chamber was stopped and its cooling with the cold air had been started. The reactor had been opened, and carbonaceous material (CM) had been retrieved after its temperature had dropped to 30°C.
Characterization of carbonaceous material
The choice of the studied characteristics was based on the requirements mentioned in CAS No. 1333–86-4. These requirements were applied to the standard carbon black, which is used as a reinforcing component during the production of rubber products for various purposes. Before the analysis, the CM samples obtained via steam pyrolysis (which were designated as 1/C-4/C) were subjected to mechanical grinding followed by fractionation using sieves with a mesh size of 80 μm.
Technical characteristics of carbonaceous material
The moisture and ash content of the initial RW samples were determined according to the ISO 589:2008 and ISO 1171–97 methods, respectively. The moisture and ash content as well as iodine number of the obtained CM samples were determined using standard procedures described in ISO 589:2008, ISO 1125:2015, and ISO 1304:2006, respectively. The pH value of the aqueous suspension was determined using a Mettler Toledo S220-kit pH meter with a glass electrode according to the ASTM E70 – 19 method.
Elemental composition of carbonaceous material
The content of carbon, hydrogen, nitrogen, and sulfur in the initial RW and obtained CM samples was determined using a Flash 2000 CHNS analyzer (Thermo Fisher Scientific, USA). The analysis was carried out using tin crucibles with V2O5. The technical and elemental composition of the obtained samples is essential to determine their suitability for many applications.
Particle size distribution of carbonaceous material
The particle size distribution of carbonaceous material is an important characteristic for its application as carbon black or sorbent. For the obtained CM samples it was determined using a SALD-7101 laser diffraction particle analyzer (Shimadzu, Japan). The samples were dispersed in a liquid medium (water) at a temperature of 23°C. Then, the samples were subjected to an ultrasound treatment via a dispersant UZDN-A (Russia) for 1 minute. For each sample, at least 4 parallel measurements were performed and the results were averaged.
Ash residue elemental analysis
The ash composition affects many features of carbonaceous material due to its possible catalytic properties, energy applications, etc. This is determined by the chemical and elemental composition of ash.
Microwave-assisted acid digestion
Before acid digestion, RW and carbonaceous material samples were calcined in a muffle furnace at 600°C using Al2O3 crucibles. The mass of each studied sample was 5 g. Then, the obtained ash samples were cooled and dispersed into acid. The samples were treated with acid in a MARS-5 microwave reactor (CEM, USA). The powder ash samples (0.1 g) were processed in a mixture of HNO3 (9 ml), HCl (3 ml), and HF (1 ml), heated to 180°C, and exposed at this temperature for 10 min. After hydrolysis, the solutions were filtered through 0.45 μm syringe filters (PTFE) and placed in 50 ml volumetric flasks.
ICP-OES chemical analysis method
The chemical composition of the ash samples was analyzed by the ICP-OES (Inductively Coupled Plasma Optical Emission Spectroscopy) method using an iCAP 6300 Duo instrument (Thermo Fisher Scientific, USA). The concentrations of the following metals were determined: Al, Ba, Ca, Cd, Co, Cr, Cu, Fe, K, La, Li, Mg, Mn, Mo, Na, Nb, Ni, Pb, Sc, Si, Sr, Ti, V, Y Zn, and Zr. A multi-element mother liquor (SKAT, Russia) was used to prepare a standard solution. At least three repetitive measurements were performed for each sample.
XRD-analysis
The phase composition of the carbonaceous material samples was analyzed using a Shimadzu XRD7000s X-ray diffractometer (CuKα radiation, graphite monochromator). The experiments were performed with the following parameters: scanning speed – 1º/min; scanning step – 0.02º; and 2Θ angle range – 10-90º. The processing of the X-ray diffraction analysis results was performed using the PDF4+ database (2019 release) and standard software for the X-ray diffractometer (PC Suit XRD-6100/7000 Ver. 7.00: main). The “XRD: Crystallinity” program was also used to analyze the degree of the sample’s crystallinity. It allows us to better understand the reactivity and chemical properties of samples.
Differential thermal analysis
In order to study the reactivity of the obtained samples, the thermal decomposition of the obtained carbonaceous material samples was studied using a Netzsch STA 449 F3 Jupiter differential thermal analyzer (Netzsch, Germany). The analysis was realized at a heating rate of 10°C/min in a corundum crucible with a perforated lid in the temperature range of 50–1000°C in order to ensure the complete conversion of the sample. An ~ 20 mg sample was distributed evenly over the bottom of the crucible and placed in a flow of an oxidizing (air) or inert (argon) medium. The gas flow rate was 150 ml/min. All experiments were performed at atmospheric pressure. A comparative assessment of the thermal conversion characteristics of the carbonaceous material samples in different media was carried out using physical parameters (temperature, time, and reaction rate), which were determined graphically using experimental thermogravimetric (TG), differential thermogravimetric (DTG), and differential scanning calorimetry (DSC) curves (Larionov and Gromov Citation2019).
Raman spectroscopy
To study the phase composition of carbon in samples, the Raman spectra of carbonaceous material samples were obtained using a Horiba Jobin Yvon LabRAM HR UV-VIS-NIR Evolution Raman spectrometer (Horiba, France) equipped with an Olympus BX41 microscope (Olympus, Japan) and a 514.5-nm line Ar ion laser. The power of light focused in a spot with a diameter of ∼2 mm was less than 0.8 mW to avoid thermal decomposition of the sample.
XPS analysis
XPS analysis of carbon samples was performed using a SPECS photoelectron spectrometer (Germany) using nonmonochromatized AlKα radiation (hν = 1486.6 eV, 150 W) in order to suppose the form of major chemical elements' existence. To determine the ratio of atomic concentrations of elements on the sample surface, the S2p, C1s, O1s, and Zn2p regions were studied. The binding energies of all peaks were calibrated using the position of the C1s photoelectron line (284.5 eV). The integral intensities of lines were measured by the areas of the corresponding regions (S2p, C1s, O1s, and Zn2p). The determination of the relative content of elements on the surface of the samples and the ratio of their atomic concentrations was carried out úsing the integral intensities of photoelectric lines, which were corrected using the corresponding coefficients of atomic sensitivity.
Scanning electron microscopy
The morphological characteristics of the carbonaceous material samples were studied using an JSM-6460LV scanning electron microscope (JEOL, Japan) at different magnification (× 3000 – ×30000).
Transmission electron microscopy
The carbonaceous material samples were analyzed using a JEOL JEM2100F (JEOL, Japan) transmission electron microscope with an energy-dispersive analysis attachment to study the distribution of elements around the obtained samples. For analysis, the sample was dispersed in alcohol by treatment in an ultrasonic bath to disintegrate agglomerates and isolate a nanoscale fraction on the surface of the alcohol. The resulting alcohol suspension was deposited on an amorphous carbon substrate on a standard copper grid.
Specific surface area and pore size
The specific surface area, volume, and size of pores of the carbonaceous material samples were determined by a low-temperature nitrogen adsorption method (BET) using an ASAP 2400 specific surface analyzer (Micromeritics, USA). Prior to analysis, the samples were vacuumed for 2 h at 150°C. Together with the phase composition of main elements of the sample, this is the one of the main properties of the carbonaceous material.
Results and discussion
After the steam pyrolysis of the waste car tire samples, the amount of carbon obtained (regarding the initial mass) is as follows: 1/C – 31.3; 2/C – 32.9; 3/C – 34.1; and 4/C – 33.6 wt%. Unlike the samples obtained by tire pyrolysis in an oxygen-free medium (Aranda et al., Citation2007; Kaminsky and Mennerich Citation2001; Li et al. Citation2005), the amount of carbon residue in the case of steam pyrolysis was found to be slightly lower (by 1.5–3.0 wt%). This could be explained by the fact that in the presence of steam, the intense carbonization of aromatic compounds released during the sublimation of volatile substances was excluded (Helleur et al. Citation2001).
Physico-chemical characteristics of waste tires, carbonaceous material, and ash residue
The physico-chemical characteristics of the initial RW and obtained CM samples obtained after the steam pyrolysis of RW are summarized in .
Table 2. Physico-chemical characteristics of the initial rubber waste and carbonaceous material samples
The ash content in the obtained carbonaceous material samples varied from 6.9 to 9.1 wt%, which was slightly lower compared to the values presented in other studies (López et al. Citation2013,33; Aylón et al. Citation2008) for both initial RW and CM samples. This was caused by the fact that in the current work, the all-season tires of passenger vehicles were used, which were characterized by a lower content of metal oxides (in particular, ZnO, SiO2, etc.) (Kaminsky and Mennerich Citation2001). It is also worth mentioning that external moisture appeared, despite the sealed storage of the samples, due to the high adsorption capacity of the activated carbon (Lin et al. Citation2008). In the ash residue, the content of elements such as aluminum, silicon, calcium, potassium, titanium, iron, and zinc was predominant because they are used for the manufacturing of car tires (Supplementary Information 1) (Kandasamy and Gökalp Citation2015).
The elemental analysis results of the obtained carbonaceous material samples () showed a nearly complete absence of hydrogen, which was caused by its removal in the form of H2 and CxHy (Karatas, Olgun, and Akgun Citation2012) formed during the steam pyrolysis of the waste tires. For RW samples, the hydrogen content was higher and varied from 6.9 to 7.2 wt%. Despite the interaction of carbon with steam and its subsequent oxidation to CO and CO2, there was a slight increase in the amount of carbon (from 2.7 to 5.1 wt%) in contrast to the initial sample (). At the same time, an increase in the amount of carbon did not directly correlate with the initial physico-chemical characteristics of the RW samples. It is also important to note that the increase in the sulfur content of the samples (from 0.4 to 0.7 wt%) was due to the lower rate of sulfur removal compared to carbon and volatile matter of samples. In this case, part of sulfur was removed in the form of COS and H2S during the steam pyrolysis of RW (Karatas, Olgun, and Akgun Citation2012).
The obtained values of the iodine number, as a characteristic of carbon activity (Kumar Singh et al. Citation2018), were varied from 144 to 165 mg/g. They were higher than the CAS No. 1333–86-4 requirements, but, on average, by 1.8 times lower than the values presented in Helleur et al. Citation2001. A high iodine number value indicated a high degree of activation and developed porosity of the material (Kumar Singh et al. Citation2018).
It should be noted that the obtained samples were slightly alkaline (pH>7). In this case, carbon samples 1/C, 2/C, and 3/C, unlike 4/C, had higher pH values (), which may be caused by the active participation of the formed alkali metal oxides in the process of RW steam pyrolysis (Chan, Cheung, and McKay Citation2011). In Fu et al. Citation2013, the increased pH value was explained by the presence hydroxyl groups at high concentrations in the activated carbon.
The particle size distribution has a monomodal form, with an average value in the range of 108–196 nm, which is quite typical for such a material (Robertson et al. Citation2008).
The results of AEM of the ash residue obtained from the initial RW samples and the obtained carbonaceous material are presented in Supplementary Information 1. The carbonaceous material obtained by the RW steam treatment had a lower content of the following metals in its ash residue (compared with the initial RW samples): Ba, Cd, Cr, Cu, Fe, K, Li, Mn, Mo, Na, Nb, Pb Si, Ti, V, Y, Zn, and Zr. No obvious pattern was found in the concentration changes: Al, Ca, La, Mg, Ni, Sr, and Sc. A significant increase in the concentration was observed only for Co. These changes could be explained by complex multi-step reactions occurring under the pyrolysis conditions (at a steam temperature of 500°C, a flow rate of 5 kg/h, and a gauge pressure of 1 atm).
The metals contained in carbonaceous material samples could be recovered using electromagnetic purification or demineralization methods (Iraola-Arregui, Van Der Gryp, and Görgens Citation2018; Martínez et al. Citation2019; Zhang et al. Citation2018).
XRD-analysis results
The results of the X-ray diffraction analysis of the studied carbonaceous material samples are presented in . The general image of the X-ray diffraction patterns was typical for the products obtained by the steam pyrolysis of the waste car tires. In all the diffraction patterns, a characteristic halo was identified, as well as a series of individual reflexes corresponding to the oxides of metals and nonmetals, which are usually added to rubber during automobile tire production.
Figure 2. X-ray diffraction patterns for the carbonaceous material samples obtained by the steam pyrolysis of RW. The diffraction peaks corresponding to the main oxides contained in the ash residue are given at the bottom of the figure.

All the diffraction patterns contained a diffusive maximum, indicating the presence of an X-ray amorphous carbon fraction. The diffusive maxima in the range of ~18 to ~30 degrees could correspond to the reflections of the (002) planes of a graphite-like structure, characterized by a short-range order with the absence of a long-range order. Similarly, diffusive maxima in the 2Θ range from ~42 to ~52 degrees corresponded to reflections in the (100) and (101) planes of the same phase. The degree of the sample crystallinity varied from 35.5 to 46.3%. The content of the X-ray amorphous fraction (which was identified as a graphite-like structure with short-range order and the absence of long-range order) was varied from 53.7 to 64.5%. Regarding the identification of crystalline phases, it should be noted that many chemical elements were present in the obtained materials due to the complex chemical reactions occurring upon heating of sample’s organic matter, which additionally complicated the unambiguous identification of all diffraction peaks. Nevertheless, the main reflexes in the diffraction patterns could be attributed to the compounds of chemical elements that form the basis of the crystalline phase in the ash residue. Thus, the peaks corresponding to the following oxides could be identified in the diffraction patterns: Al2O3 (cubic phase), SiO2 (hexagonal phase), CaO2 (tetragonal phase), TiO2 (tetragonal phase), MnO2 (tetragonal phase), Fe2O3 (orthorhombic phase), and ZnO (hexagonal phase). The obtained results are in accordance with the data on the elemental composition of the obtained materials ( and Supplementary Information 1). The presence of individual diffraction peaks of metal (iron oxide) and nonmetal oxides (zinc oxide) in the diffraction patterns as well as strongly broadened maxima corresponding to a graphite-like structure with a short-range order was typical for the powders obtained by the RW steam pyrolysis (Heidari and Younesi Citation2020; Seng-eiad and Jitkarnka Citation2016).
Thermal analysis results
The results of thermal analysis of the carbonaceous material samples performed in oxidizing and inert media are presented in Supplementary Information 2 and (the DTG curve is built using absolute values), respectively. The values of the calculated parameters are given in Supplementary Information 3.
Figure 3. TG (a) and DTG (b) data of the thermal conversion of the carbon samples in an inert medium. The flow rate of argon – 150 ml/min, the heating rate – 10°C/min, the sample weight ~15 mg.
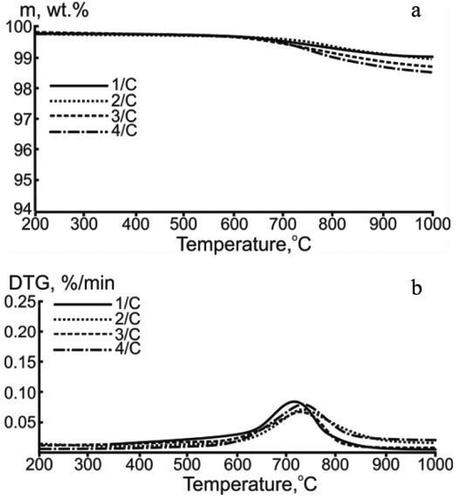
Comparing the obtained results (Supplementary Information 2), it could be noted that the shape of the TG-curves characterizing the oxidation process had a similar character for all the studied samples and close values of oxidation initiation temperature Ti (516–525°C). This was connected to the fact that the samples had similar morphology, particle size, and other physico-chemical characteristics ().
According to the data of Supplementary Information 2, it was clear that the DTG curves characterizing the 1/C and 2/C samples had a bimodal shape with the characteristic shoulders and low-intensity peaks. In the temperature range from 25 to 100°C, physically adsorbed moisture was removed (∆m = 0.9–2.0 wt%, which was in good correspondence with the moisture content from ). In the temperature range of 100–700°C, no change in the mass of carbonaceous samples was observed. In turn, at temperatures above 500°C, a significant change in the sample mass was observed (∆m was about 91.0 wt%), which was associated with the oxidation of the carbon matrix (Zabuga et al. Citation2018).
It is also worth mentioning that for the 1/C and 2/C samples, additional small peaks and characteristic shoulders could be associated with non-uniform oxidation of the surface of particles and their agglomerates (). In this case, the peaks corresponding to the oxidation of the carbon matrix were characterized by the same width and different reaction rates wmax = 1.4–2.9 wt%/min (Supplementary Information 3). The characteristics of both TG and DTG curves for the oxidation process of the studied carbonaceous material samples, as well as the observed characteristic temperatures, were consistent with the results presented earlier in Zabuga et al. Citation2018.
The position of exothermic peaks on the DSC curves (Supplementary Information 2) practically coincides with those on the DTG curves corresponding to the maximum oxidation rate of the carbon matrix. The observed exothermic effects on the DSC curves (Supplementary Information 2) were associated with the release of heat at the different stages of carbon matrix oxidation. Moreover, for the experimentally obtained carbonaceous material samples 2/С-4/С, the integrand area of the DSC curve was 32–44% larger than that for sample1/С.
illustrates that the total mass loss of the studied samples was about 1.5 wt%. In this case, the initial decomposition temperature Td values for the studied samples were obtained in the temperature range 600–650°C.
According to DTG data (), the maximum reaction rate wmax did not exceed 0.07 wt%/min at a temperature of Tmax ≈ 750°C (Supplementary Information 3). The observed change in the mass of the studied samples in the high-temperature region (600–1000°C) could be associated with the decomposition of carboxyl groups and subsequent release of CO2. This was additionally proved by the results of mass spectrometry (Supplementary Information 4). Most likely, the oxidation of carboxyl groups with CO2 formation in the high-temperature region occurred as a result of the interaction of carbon with structural oxygen contained in the carbonaceous material (). The obtained results of the thermal decomposition of the studied carbonaceous material samples were in good correlation with earlier published data (Jakab and Omastová Citation2005).
Raman analysis results
The Raman spectra of the first order for all samples were characterized by two main lines D and G attributed to amorphous carbon (). The first one was the disorder-induced D-line at ~1357 cm−1 (HWNM ~210 cm−1), which was assigned to the activated A1g mode due to the finite crystal size (Ferrari and Robertson Citation2000). The second one was the G-line at ~1590 cm−1 (HWNM ~80 cm−1) corresponding to allowed vibrations E2g within the graphitic hexagons (Nemanich and Solin Citation1979). There were also D3 (~1500 cm−1) and D4 (~1200 cm−1) lines attributed to amorphous carbon with a disordered graphitic lattice (A1g symmetry) or polyenes (Sadezky et al. Citation2005), which are typical for soot and related carbonaceous materials. For the studied samples, the average ratios of corresponding intensities were calculated to be ID3/G = 0.09 and ID4/G = 0.11. As it is seen in the diagram in (on the right), there was a somewhat decrease in the ID/IG ratio from 0.88 to 0.85, which implied an insignificant increase in the extent of graphite disordering. Based on the known correlation ID/IG~Cl·La2 (Ferrari and Robertson Citation2000), it was possible to estimate the cluster diameter in the studied samples (La), which varied from 12.2 to 12.6 Å.
SEM-analysis results
presents the typical microphotographs of carbonaceous material samples (on the example of sample 2/C) obtained by SEM.
Particles of the studied carbonaceous material samples were characterized by an array of spherical agglomerates with a size less than 20 µm. These agglomerates, in turn, consisted of a large number of smaller particles, the size of which correlated with the values from .
According to (Wu et al. Citation2002), the formation of agglomerates was associated with the occurring van der Waals forces since the particles of the studied carbonaceous material samples were smaller than 1 μm. According to (Miguel et al. Citation2002) the formation of agglomerates could be associated with the continuous oxidation of the main components of rubber (the rubber itself and other resin-like products formed during steam pyrolysis), which acted as a binder during vulcanization.
In general, the surface structure of the agglomerates was characterized by a large number of sites having interparticle voids, which indicated a high heterogeneity and porosity of the samples (). The SEM results for the carbon samples were comparable with the data presented in (Ariyadejwanich et al. Citation2003; Helleur et al. Citation2001; López et al. Citation2013), where the steam treatment led to the formation of more amorphous and porous carbonaceous materials.
Table 3. Specific surface area, average size, and volume of pores of carbonaceous material samples obtained as a result of steam pyrolysis of waste tires
XPS analysis results
According to the observed spectra, the lines were characteristic for sulfur, carbon, oxygen, and zinc. No other lines were observed within the sensitivity of the XPS method. The S2p and Zn2p spectra are presented in the Supplementary Information 5.
The sulfur was observed in two forms with binding energies of the S2p line: ~161.8 eV for the sulfur in the form of sulfide and ~163.2 eV for the sulfur in the form of oxysulfide (). In this case, the shares of S2- and SOx contributing to the S2p line were 41.4 and 58.6%, respectively. The spectrum of Zn2p illustrated one state with a binding energy of ~1022.4 eV, which corresponded to the charge state of Zn2+ in ZnO () (Mashkovsky et al. Citation2017).
Figure 6. Results of transmission electron microscopy (on the example of sample 2/C): a) typical overview image of the product; b) SAED; c) dark-field image; d) picture in direct resolution mode; e) picture in scanning-transmission electron microscopy mode; f-l) mapping of the chemical elements’ distribution.

The atomic concentrations of sulfur (SS) and zinc (SZn) on the surface of the studied sample particles were 1145.8 and 565.9 (). For carbon SC, it was 183808.9.
TEM analysis results
The results of high-resolution transmission electron microscopy (2/C sample) are presented in . According to a series of typical bright-field images, the product contained a carbon matrix, in which denser particles were included. According to the typical SAED diffraction pattern (), the structure of the material corresponded to four highly diffusive rings, as well as a series of individual low-intensity maxima. The interpretation of the diffraction patterns showed that the radius of the washed-out rings corresponded to interplanar spacing of ~3.85 Å, ~2.17 Å, ~2.71 Å, and ~1.27 Å. This result indicated the presence of a graphite-like structure in the material. Individual diffraction peaks corresponded to the reflections of families of planes with interplanar spacings of ~2.00 Å, ~2.30 Å, ~2.90 Å, and ~3.25 Å. These reflections (within the limits of the possible error) could correspond to the oxides of metals and nonmetals, which were previously identified in the samples by X-ray diffraction analysis ().
By the displacement of the aperture diaphragm to the region marked in , a dark-field image of с was obtained. The individual particles with sizes up to ~30–40 nm could be seen to glow on a black background. In this dark-field photograph, these luminous objects could be a series of metal and nonmetal oxides previously identified by the XRD. Using the image in direct resolution mode, it was possible to determine the presence of a short-range order with individual-ordered regions with an interplanar distance of ~3.8 Å.
shows an image obtained in a scanning transmission electron microscopy (STEM) mode, and shows the corresponding maps of the distribution of the chemical elements. In general, energy-dispersive analysis illustrated the presence of carbon (up to 93.3 wt%), oxygen (up to 4.1 wt%), zinc (up to 1.3 wt%), as well as magnesium, aluminum, silicon, sulfur, potassium, calcium, titanium, chromium, and iron (with a total content of 1.3 wt%). The most illustrative maps of the chemical element distribution are presented in f-l. These maps confirmed the fact that the inclusions in the carbon matrix were oxides of metals and nonmetals in the solid-phase product of RW steam pyrolysis.
Specific surface area and pore sizes of the particles
The isotherms of low-temperature nitrogen adsorption-desorption and the pore volume distribution curves for the obtained carbonaceous material samples are presented in Supplementary Information 6. The obtained isotherms (Supplementary Information 6) were very similar for all samples; they were assigned to Type III, according to the IUPAC classification.
The obtained values of the specific surface area for the carbonaceous material samples () were varied from 52 to 66 m2/g, which was consistent with the published data (Kaminsky and Mennerich Citation2001). The specific surface area values were directly dependent on the sample particle size (). It is important to note that the measured SBET values met the requirements of CAS No. 1333–86-4 and corresponded to a carbon grade N330. According to (González et al. Citation2006; Martínez et al. Citation2019), the specific surface area of the pyrolytic residue depended on the technology of tire production, the characteristics of the initial material as well as the method of supplying the activating agent (design of the reaction chamber).
The mean volume and size of pores of carbonaceous material particles were 0.53–0.87 cm3/g and 412–527 Å, respectively (). Despite close values of the specific surface area of carbonaceous material samples obtained by the steam pyrolysis and classic pyrolysis methods (Kaminsky and Mennerich Citation2001), the volume and size of pores of these materials were significantly different. Thus, carbon particles obtained as a result of the RW steam pyrolysis had a significantly larger pore volume, in contrast to the materials produced by the classic pyrolysis at the same temperatures (Li et al. Citation2005). This fact may be associated with more intensive removal of volatile substances and ultrafine carbon particles from the porous structure of the sample, which led to increase in its volume. The large pore volume could also be explained by the high content of volatile substances in the initial RW material, the removal of which in an oxygen-free regime led to the formation of a large number of channels and the appearance of a well-developed porous structure. While the obtained carbonaceous material has a relatively high specific surface area, these values are still inferior to characteristics of biochar-derived carbon powders activated at higher steam temperatures (Hsi et al. Citation2011). Thus, the application of the steam with higher temperatures into single-staged waste tire processing should be studied.
Conclusion
A comparative analysis of the characteristics of carbonaceous material obtained by the steam pyrolysis of all-seasonal waste tires of passenger cars was carried out. Based on the research results, the following main conclusions were made.
The steam pyrolysis was found to produce carbonaceous material close to CAS No. 1333–86-4 carbon black, which likely could be used as fuel or absorbent.
The elemental composition and technical characteristics had insignificant differences in the content of carbon (С = 86.0–90.0 wt%), sulfur (S = 1.9–2.4 wt%), ash residue (6.9–9.1 wt%), and pH (7.8–10.3). The average particle size varied from 108 to 196 nm. The obtained iodine number values varied from 144 to 165 mg/g, which were higher compared to the requirements of CAS No. 1333–86-4.
According to the XPS analysis data, it was found that sulfur on the surface of the carbonaceous material was present in two forms – sulfide and oxysulfide with binding energies of 161.8 and 163.2 eV, respectively.
XRD patterns for all obtained samples were characterized by a wide reflex in the region 2Θ = 26°, which indicated the presence of an X-ray amorphous carbon phase. The degree of crystallinity of the samples varied from 35.5 to 46.3%. The amorphous structure of carbon with an unambiguous structure was also proved by Raman analysis data.
The specific surface area of the samples was in direct correlation with the average particle size and varied from 52.0 to 66.0 m2/g, which corresponded to the requirements of CAS No. 1333–86-4 for the carbon black grade N330. The average volume and size of pores of carbonaceous material particles varied from 0.53 cm3/g and 412 Å to 0.87 cm3/g and 527 Å, respectively.
Supplemental_File.docx
Download MS Word (2.4 MB)Disclosure statement
No potential conflict of interest was reported by the author(s).
Supplementary material
Supplemental data for this paper can be accessed on the publisher’s website
Additional information
Funding
Notes on contributors
Kirill B. Larionov
Kirill B. Larionov, PhD, head of the laboratory of catalysis and conversion of carbonaceous materials to obtain useful products of Gorbachev Kuzbass State Technical University, assistant professor of School of Energy & Power Engineering of Tomsk Polytechnic University.
Konstantin V. Slyusarskiy
Konstantin V. Slyusarskiy, assistant professor of School of Energy & Power Engineering of Tomsk Polytechnic University.
Aleksey A. Ivanov
Aleksey A. Ivanov, researcher of Research School of Chemistry & Applied Biomedical Sciences of Tomsk Polytechnic University.
Ilya V. Mishakov
Ilya V. Mishakov, PhD, specialist in the field of catalysis, senior researcher at the Boreskov Institute of Catalysis SB RAS.
Alexander Y. Pak
Alexander Y. Pak, assistant professor of School of Energy & Power Engineering of Tomsk Polytechnic University.
Stanislav A. Jankovsky
Stanislav A. Jankovsky, assistant professor of School of Energy & Power Engineering of Tomsk Polytechnic University.
Vladimir O. Stoyanovskii
Vladimir O. Stoyanovskii, PhD, specialist in the field of catalysis, researcher at the Boreskov Institute of Catalysis SB RAS.
Aleksey A. Vedyagin
Aleksey A. Vedyagin, PhD, Doctor of Chemical Sciences, specialist in the field of catalysis, deputy director of the the Boreskov Institute of Catalysis SB RAS.
Vladimir E. Gubin
Vladimir E. Gubin, assistant professor of School of Energy & Power Engineering of Tomsk Polytechnic University.
References
- Aranda, A., R. Murillo, T. García, M. S. Callén, and A. M. Mastral. 2007. Steam activation of tyre pyrolytic carbon black: Kinetic study in a thermobalance. Chem. Eng. J. 126 (2–3):79–85. doi:https://doi.org/10.1016/j.cej.2006.08.031.
- Ariyadejwanich, P., W. Tanthapanichakoon, K. Nakagawa, S. Mukai, and H. Tamon. 2003. Preparation and characterization of mesoporous activated carbon from waste tires. Carbon N. Y. 41 (1):157–64. doi:https://doi.org/10.1016/S0008-6223(02)00267-1.
- Aylón, E., A. Fernández-Colino, M. V. Navarro, R. Murillo, T. García, and A. M. Mastral. 2008. Waste tire pyrolysis: comparison between fixed bed reactor and moving bed reactor. Ind. Eng. Chem. Res. 47 (12):4029–33. doi:https://doi.org/10.1021/ie071573o.
- Barbooti, M. M., T. J. Mohamed, A. A. Hussain, and F. O. Abas. 2004. Optimization of pyrolysis conditions of scrap tires under inert gas atmosphere. J. Anal. Appl. Pyrolysis. 72 (1):165–70. doi:https://doi.org/10.1016/j.jaap.2004.05.001.
- Chan, O. S., W. H. Cheung, and G. McKay. 2011. Preparation and characterisation of demineralised tyre derived activated carbon. Carbon N. Y. 49 (14):4674–87. doi:https://doi.org/10.1016/j.carbon.2011.06.065.
- Cunliffe, A. M., and P. T. Williams. 1999. Influence of process conditions on the rate of activation of chars derived from pyrolysis of used tires. Energy & Fuels. 13 (1):166–75. doi:https://doi.org/10.1021/ef9801524.
- Elbaba, I. F., C. Wu, and P. T. Williams. 2010. Catalytic pyrolysis-gasification of waste tire and tire elastomers for hydrogen production. Energy & Fuels. 24 (7):3928–35. doi:https://doi.org/10.1021/ef100317b.
- Ferrari, A. C., and J. Robertson. 2000. Interpretation of Raman spectra of disordered and amorphous carbon. Phys. Rev. B. 61 (20):14095. doi:https://doi.org/10.1103/PhysRevB.61.14095.
- Fu, K., Q. Yue, B. Gao, Y. Sun, and L. Zhu. 2013. Preparation, characterization and application of lignin-based activated carbon from black liquor lignin by steam activation. Chem. Eng. J. 228:1074–82. doi:https://doi.org/10.1016/j.cej.2013.05.028.
- Global demand for car and light commercial vehicle tires from 2012 to 2018, Statista. 2019. https://www.statista.com/statistics/792209/global-tire-demand/
- González, J. F., J. M. Encinar, C. M. González-García, E. Sabio, A. Ramiro, J. L. Canito, and J. Gañán. 2006. Preparation of activated carbons from used tyres by gasification with steam and carbon dioxide. Appl. Surf. Sci. 252 (17):5999–6004. doi:https://doi.org/10.1016/j.apsusc.2005.11.029.
- Heidari, A., and H. Younesi. 2020. Synthesis, characterization and life cycle assessment of carbon nanospheres from waste tires pyrolysis over ferrocene catalyst. J. Environ. Chem. Eng. 8 (2):103669. doi:https://doi.org/10.1016/j.jece.2020.103669.
- Helleur, R., N. Popovic, M. Ikura, M. Stanciulescu, and D. Liu. 2001. Characterization and potential applications of pyrolytic char from ablative pyrolysis of used tires. J. Anal. Appl. Pyrolysis. 58-59:813–24. doi:https://doi.org/10.1016/S0165-2370(00)00207-2.
- Hsi, H.-C., R. S. Horng, T.-A. Pan, and S.-K. Lee. 2011. Preparation of activated carbons from raw and biotreated agricultural residues for removal of volatile organic compounds. J. Air Waste Manag. Assoc. 61 (5):543–51. doi:https://doi.org/10.3155/1047-3289.61.5.543.
- Iraola-Arregui, I., P. Van Der Gryp, and J. F. Görgens. 2018. A review on the demineralisation of pre- and post-pyrolysis biomass and tyre wastes. Waste Manag. 79:667–88. doi:https://doi.org/10.1016/j.wasman.2018.08.034.
- Jakab, E., and M. Omastová. 2005. Thermal decomposition of polyolefin/carbon black composites. J. Anal. Appl. Pyrolysis. 74 (1–2):204–14. doi:https://doi.org/10.1016/j.jaap.2005.02.001.
- Jang, J.-W., T.-S. Yoo, J.-H. Oh, and I. Iwasaki. 1998. Discarded tire recycling practices in the United States, Japan and Korea. Resour. Conserv. Recycl. 22 (1–2):1–14. doi:https://doi.org/10.1016/S0921-3449(97)00041-4.
- Jimoda, L. A., I. D. Sulaymon, A. O. Alade, and G. A. Adebayo. 2018. Assessment of environmental impact of open burning of scrap tyres on ambient air quality. Int. J. Environ. Sci. Technol. 15 (6):1323–30. doi:https://doi.org/10.1007/s13762-017-1498-5.
- Kalitko, V. A. 2010. Steam thermolysis of tire shreds: Modernization in afterburning of accompanying gas with waste steam. J. Eng. Phys. Thermophys. 83 (1):179–87. doi:https://doi.org/10.1007/s10891-010-0333-3.
- Kaminsky, W., and C. Mennerich. 2001. Pyrolysis of synthetic tire rubber in a fluidised-bed reactor to yield 1,3-butadiene, styrene and carbon black. Journal of Analytical and Applied Pyrolysis. 58-59:803–11. doi:https://doi.org/10.1016/S0165-2370(00)00129-7.
- Kandasamy, J., and I. Gökalp. 2015. Pyrolysis, combustion, and steam gasification of various types of scrap tires for energy recovery. Energy & Fuels. 29 (1):346–54. doi:https://doi.org/10.1021/ef502283s.
- Karatas, H., H. Olgun, and F. Akgun. 2012. Experimental results of gasification of waste tire with air&CO2, air&steam and steam in a bubbling fluidized bed gasifier. Fuel Process. Technol. 102:166–74. doi:https://doi.org/10.1016/j.fuproc.2012.04.013.
- Kenzhin, R. M., Y. I. Bauman, I. V. Mishakov, I. V. Zibareva, and A. A. Vedyagin. 2019. Conversion of polymer and resin wastes into the valuable products. 5, 555660.1-7.
- Kumar Singh, R., B. Ruj, A. Jana, S. Mondal, B. Jana, A. Kumar Sadhukhan, and P. Gupta. 2018. Pyrolysis of three different categories of automotive tyre wastes: product yield analysis and characterization. J. Anal. Appl. Pyrolysis. 135:379–89. doi:https://doi.org/10.1016/j.jaap.2018.08.011.
- Kyari, M., A. Cunliffe, and P. T. Williams. 2005. Characterization of oils, gases, and char in relation to the pyrolysis of different brands of scrap automotive tires. Energy & Fuels 19 (3):1165–73. doi:https://doi.org/10.1021/ef049686x.
- Labaki, M., and M. Jeguirim. 2017. Thermochemical conversion of waste tyres—a review. Environ. Sci. Pollut. Res. 24 (11):9962–92. doi:https://doi.org/10.1007/s11356-016-7780-0.
- Larionov, K. B., and A. A. Gromov. 2019. Non-isothermal oxidation of coal with Ce(NO3)3 and Cu(NO3)2 additives. Int. J. Coal Sci. Technol. 6 (1):37–50. doi:https://doi.org/10.1007/s40789-018-0229-y.
- Li, S.-Q., Q. Yao, S.-E. Wen, Y. Chi, and J.-H. Yan. 2005. Properties of pyrolytic chars and activated carbons derived from pilot-scale pyrolysis of used tires. J. Air Waste Manage. Assoc. 55 (9):1315–26. doi:https://doi.org/10.1080/10473289.2005.10464728.
- Lin, H.-Y., W.-C. Chen, C.-S. Yuan, and C.-H. Hung. 2008. Surface functional characteristics (C, O, S) of waste tire-derived carbon black before and after steam activation. J. Air Waste Manage. Assoc. 58 (1):78–84. doi:https://doi.org/10.3155/1047-3289.58.1.78.
- López, F. A., T. A. Centeno, O. Rodríguez, and F. J. Alguacil. 2013. Preparation and characterization of activated carbon from the char produced in the thermolysis of granulated scrap tyres. J. Air Waste Manage. Assoc. 63 (5):534–44. doi:https://doi.org/10.1080/10962247.2013.763870.
- Lopez, G., M. Artetxe, M. Amutio, A. Erkiaga, J. Alvarez, I. Barbarias, and M. Olazar. 2012. Preparation of adsorbents derived from waste tires. Chem. Eng. Trans. 29:811–16. doi:https://doi.org/10.3303/CET1229136.
- López, G., M. Olazar, M. Artetxe, M. Amutio, G. Elordi, and J. Bilbao. 2009. Steam activation of pyrolytic tyre char at different temperatures. J. Anal. Appl. Pyrolysis. 85 (1–2):539–43. doi:https://doi.org/10.1016/j.jaap.2008.11.002.
- Martínez, J. D., N. Cardona-Uribe, R. Murillo, T. García, and J. M. López. 2019. Carbon black recovery from waste tire pyrolysis by demineralization: Production and application in rubber compounding. Waste Manag. 85:574–84. doi:https://doi.org/10.1016/j.wasman.2019.01.016.
- Mashkovsky, I. S., P. V. Markov, G. O. Bragina, G. N. Baeva, A. V. Bukhtiyarov, I. P. Prosvirin, V. I. Bukhtiyarov, and A. Y. Stakheev. 2017. Formation of supported intermetallic nanoparticles in the Pd–Zn/α-Al2O3 catalyst. Kinet. Catal. 58 (4):471–79. doi:https://doi.org/10.1134/S0023158417040127.
- Miguel, G. S., G. D. Fowler, M. Dall’Orso, and C. J. Sollars. 2002. Porosity and surface characteristics of activated carbons produced from waste tyre rubber. J. Chem. Technol. Biotechnol. 77 (1):1–8. doi:https://doi.org/10.1002/jctb.518.
- Mmereki, D., B. Machola, and K. Mokokwe. 2019. Status of waste tires and management practice in Botswana. J. Air Waste Manag. Assoc. 69 (10):1230–46. doi:https://doi.org/10.1080/10962247.2017.1279696.
- Mui, E. L. K., D. C. K. Ko, and G. McKay. 2004. Production of active carbons from waste tyres––a review. Carbon N. Y. 42 (14):2789–805. doi:https://doi.org/10.1016/j.carbon.2004.06.023.
- Nemanich, R. J., and S. A. Solin. 1979. First- and second-order Raman scattering from finite-size crystals of graphite. Phys. Rev. B. 20 (2):392. doi:https://doi.org/10.1103/PhysRevB.20.392.
- Park, J., and -S.-S. Lee. 2018. Adsorption of mercury by activated carbon prepared from dried sewage sludge in simulated flue gas. J. Air Waste Manag. Assoc. 68 (10):1077–84. doi:https://doi.org/10.1080/10962247.2018.1468364.
- Policella, M., Z. Wang, K. G. Burra, and A. K. Gupta. 2019. Characteristics of syngas from pyrolysis and CO2-assisted gasification of waste tires. Appl. Energy. 254:113678. doi:https://doi.org/10.1016/j.apenergy.2019.113678.
- Robertson, C. G., C. J. Lin, M. Rackaitis, and C. M. Roland. 2008. Influence of particle size and polymer−filler coupling on viscoelastic glass transition of particle-reinforced polymers. Macromolecules. 41 (7):2727–31. doi:https://doi.org/10.1021/ma7022364.
- Sadezky, A., H. Muckenhuber, H. Grothe, R. Niessner, and U. Pöschl. 2005. Raman microspectroscopy of soot and related carbonaceous materials: spectral analysis and structural information. Carbon N. Y. 43 (8):1731–42. doi:https://doi.org/10.1016/j.carbon.2005.02.018.
- Seng-eiad, S., and S. Jitkarnka. 2016. Untreated and HNO3-treated pyrolysis char as catalysts for pyrolysis of waste tire: In-depth analysis of tire-derived products and char characterization. J. Anal. Appl. Pyrolysis. 122:151–59. doi:https://doi.org/10.1016/j.jaap.2016.10.004.
- Shu, X., and B. Huang. 2014. Recycling of waste tire rubber in asphalt and Portland cement concrete: an overview. Constr. Build. Mater. 67:217–24. doi:https://doi.org/10.1016/j.conbuildmat.2013.11.027.
- Sun, J., T. A. Brady, M. J. Rood, C. M. Lehmann, M. Rostam-Abadi, and A. A. Lizzio. 1997. Adsorbed natural gas storage with activated carbons made from Illinois coals and scrap tires. Energy & Fuels. 11 (2):316–22. doi:https://doi.org/10.1021/ef960201h.
- Wu, G., S. Asai, M. Sumita, and H. Yui. 2002. Entropy penalty-induced self-assembly in carbon black or carbon fiber filled polymer blends. Macromolecules. 35 (3):945–51. doi:https://doi.org/10.1021/ma0104940.
- Xu, J., J. Yu, J. Xu, C. Sun, W. He, J. Huang, and G. Li. 2020. High-value utilization of waste tires: A review with focus on modified carbon black from pyrolysis. Sci Total Environ. 742:140235. doi:https://doi.org/10.1016/j.scitotenv.2020.140235.
- Zabuga, V. Y., O. O. Bochechka, G. G. Tsapyuk, V. E. Diyuk, T. O. Kurylyak, and V. V. Lisnyak. 2018. Kinetic analysis of nanodiamonds oxidation. Mol. Cryst. Liq. Cryst. 673 (1):89–96. doi:https://doi.org/10.1080/15421406.2019.1578497.
- Zhang, X., H. Li, Q. Cao, L. Jin, and F. Wang. 2018. Upgrading pyrolytic residue from waste tires to commercial carbon black. Waste Manag. Res. J. A Sustain. Circ. Econ. 36:436–44. doi:https://doi.org/10.1177/0734242X18764292.