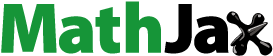
ABSTRACT
Dioxins are a kind of persistent organic pollutants (POPs) with extremely toxic. Municipal solid waste incineration (MSWI) process has become one of the most dominant discharge sources of dioxins. A comprehensive discussion about dioxin formation mechanisms was reviewed in this paper, and the mechanisms of high-temperature gas-phase reaction and “de novo” synthesis were systematically illustrated in the form of diagrams. What’s more, the effects of various influencing factors on the formation of PCDD/Fs were briefly analyzed in the form of a table. We believed that temperature, catalyst, chlorine source, carbon source, oxygen concentration and moisture were necessary factors for PCDD/Fs formation. Control technologies of dioxins in MSWI process were summarized subsequently from three stages: pre-combustion, in-combustion and post-combustion, and a device for synergistic removal of dioxins based on multi-field force coupling and technical routes for controlling dioxin emissions were proposed, so as to provide mechanisms and methods for effectively reducing the emission concentration of dioxins. An introduction was also conducted of dioxin control technologies in municipal solid waste incineration fly ash (MSWI-FA) in this paper, and their mechanisms, advantages, disadvantages and technical maturity were illustrated in the form of diagrams, which can provide theory and reference for in-depth research of follow-up scholars and industrial application of dioxin control technologies. Finally, current research hotspots, challenges and future research directions were proposed.
Implications: In this paper, the main research contents and achievements are as follows: With the emphasis placed on the formation mechanism of dioxins and effects of various influencing factors on the formation of PCDD/Fs. The control technology of dioxins in MSWI process is summarized subsequently from three stages: pre-combustion, in-combustion and post-combustion.A device for synergistic removal of dioxins based on multi-field force coupling and technical routes for controlling dioxin emissions are proposed.A systematic review is conducted of the research progress on control technologies of dioxins in MSWI fly ash in the most recent years.The mechanisms, advantages, disadvantages and technical maturity of PCDD/Fs degradation technologies in MSWI fly ash are illustrated in the form of diagrams.Current research hotspots, challenges and future research directions are proposed.
Introduction
With the substantial increase of urban population, the amount of municipal solid waste (MSW) generated is increasing day by day. With MSW generated by 337 cities in China amounts to approximately 343 million tons in 2019 (National Bureau of Statistics of China Citation2020), the problem of how to utilize and disposal MSW is imminent. According to People’s Republic of China Solid Waste Pollution Prevention and Control Law, the clearance volume of MSW is 235 million tons in 2020, and the harmless disposal rate is as high as 99.7%. At present, landfill, composting and incineration are known as the main harmless disposal of MSW at home and abroad (Liu, Liu, and Huang Citation2016). Although MSW landfill has the competitive advantages of simple operation and management, large capacity, low investment and operating costs and so on, a large amount of land resources will be permanently occupied by landfill and the soil or groundwater will be contaminated if the permeate is used improperly (Faitli et al. Citation2019). The prospect of MSW composting is limited due to the lower disposal capacity and unsuitability for disposing large amounts of mixed waste (Zurbrugg et al. Citation2004). As revealed by the data in (National Bureau of Statistics of China Citation2020), the disposal capacity of MSW incineration increases obviously and is nearly equivalent to that of MSW landfill in 2019. Not only can MSWI reduce the volume of waste by more than 90% (Fang and Li Citation2019), but also the heat generated by incineration can be utilized for the purpose of power generation and resource recycling. With the promotion of the “dual carbon” goal, MSWI industry shows a bright future. However, the flue gas and fly ash generated in MSWI process contain an extremely toxic organic pollutant: dioxins, and the prevention and control of dioxin Pollution have become one of the most important challenges faced by MSWI industry.
The commonly referred to dioxins are a generic term for polychlorinated dibenzo-p-dioxins (PCDDs), polychlorinated dibenzofurans (PCDFs) and polychlorinated biphenyls (PCBs) (Shi Citation2009). Two benzene rings linked by two oxygen atom are PCDFs and two benzene rings linked by one oxygen atom are PCDFs, whose molecular structures are shown in . Owing to each benzene ring can be replaced by 0–4 chlorine atoms, there are 75 isomers of PCDDs and 135 isomers of PCDFs, and these 210 isomers are collectively referred to as dioxins.
All dioxins are in solid state at room temperature and have a high melting and boiling point. In terms of solubility, dioxins are extremely insoluble in water and easily soluble in organic solvents and fats. In terms of volatility, dioxins are not easy to volatilize in the environment due to the low vapor pressure (Sun Citation2012). In terms of stability, The chemical stability of dioxins is high due to the asymmetry of structure, but dioxins can be decomposed at high temperatures of 700 ~ 800°C and resynthesized once cooled (Liu Citation2020).In terms of harmfulness, dioxins are known as “the most toxic poison on earth”, and tens of thousands of people can be killed by 1 g of dioxins. The most toxic is 2,3,7,8-TCDD, which is 900 times more toxic than arsenic and 1,000 times more toxic than potassium cyanide (KCN). Therefore, it is of great significance for economic development and environmental protection to study the formation mechanism of dioxins and put forward corresponding control measures to effectively reduce the emission concentration of dioxins.
In this paper, an introduction was conducted of the formation mechanisms and effects of various influencing factors on PCDD/Fs formation during MSWI process. We discussed the issues that remain controversial in the current academic community. With the emphasis placed on dioxin control technologies during MSWI process from the aspects of flue gas and fly ash. We analyzed the technical bottlenecks of the current control technologies. Finally, current research hotspots, challenges and future research directions were proposed to provide theory and reference for further research by subsequent scholars.
Formation mechanisms and influencing factors of dioxins in MSWI process
Due to the formation mechanism of dioxins is very complicated in MSWI process, a universally accepted result, which can fully reveal the formation of dioxins, has yet to be obtained. So far, the formation pathways have been proved to be divided into the inherent dioxins in primary waste, high-temperature gas-phase reaction, “de novo” synthesis and precursor synthesis four categories.
Formation mechanisms of dioxins in MSWI process
The inherent dioxins in primary waste
Dioxins generated by MSWI process are partially derived from primary waste. During MSWI process, dioxins released from the waste are not completely decomposed and still exist in flue gas and fly ash. Some scholars calculated that the content of dioxins in the incinerator-fed waste is 5 ~ 57 ng TEQ/kg (Abad et al. Citation2000), among which the content of dioxins in textiles, medical supplies and plastic products is higher (El-Shahawi et al. Citation2010; Pariatamby and Kee Citation2016).
For the whole MSWI system, the inherent dioxins in the waste are not the main source of dioxins, which can be decomposed by optimizing combustion conditions.
High-temperature gas-phase reaction mechanism
High-temperature gas-phase reaction occurs mainly at heat exchange zone of waste incinerator chamber (Liu et al. Citation2010), and 500 ~ 850°C is the optimum temperature for high-temperature gas-phase reaction to form dioxins (Stanmore Citation2004). Water in the waste evaporates rapidly when waste is fed into the incinerator, and a local oxygen-deficient area and products of incomplete combustion (PIC) may be formed at this point. Most chlorine elements in the waste will be issued in the form of HCl and some of HCl will be subsequently converted into Cl2 and H2O (Kanters et al. Citation1996). PIC will be chlorinated by Cl2 at high temperature to generate precursors such as chlorobenzene, chlorophenol and PCBs, and then PCDD/Fs are formed by polymerization reaction (Zhang, Zhang, and Liu Citation2020). Studies have found that Cl2 atmosphere is more conducive to PCDD/Fs formation than HCl atmosphere, possibly because HCl will not directly form PCDD/Fs from precursors at high temperature, but rather will promote the formation of more dioxin precursors (Akki, Citation1998).
Studies have shown that dioxins can be formed by precursors in high-temperature gas-phase. For example, PCDD/Fs can be formed rapidly under aerobic condition by PCBs at 500 ~ 700°C (Kong et al. Citation2012), and PCDD/Fs can be formed by gas-phase reactions of chlorophenols under O2 atmosphere above 340°C (Lu Citation2004). Ritter and Bozzelli (Citation1994) proposed the theory that short-chain chlorinated hydrocarbons were first formed precursors in high-temperature gas-phase, and then PCDFs were formed through OH substitution and dechlorination reaction. shows our summary of the formation pathway of high-temperature gas-phase reaction for PCDFs based on the study of Ritter and Bozzelli (Citation1994).
Many scholars made calculations and revisions based on the piston flow model (S-T model). It was finally concluded that high-temperature gas-phase formation contributes to the emission of total dioxins and that heterogeneous catalytic reaction is the main source of PCDD/Fs (Babushok and Tsang Citation2003; Ficarella and Laforgia Citation2000; Huang and Buskens Citation1999).
“De novo” synthesis mechanism
Stieglitz and Vogg were the first to propose the synthesis mechanism of “de novo”. “De novo” synthesis takes place mainly at low-temperature zone of the incinerator (optimal reaction temperature of 300°C). Dioxins are formed from hydrogen, oxygen and chlorine elements adsorbed to the surface of fly ash and unburned carbon through pre-oxidation and post-condensation reaction in the presence of catalyst (mainly Cu2+ in fly ash) (Tuppurainen et al. Citation1998). shows our summary of this reaction process based on previous studies.
Pre-oxidation reaction
Oxygen is a necessary condition for the gasification reaction of granular carbon and “de novo” reaction, the carbon matrix must be destroyed through oxidation reactions of chlorine-containing carbon molecules on the granular carbon to form dioxin precursors.
“De novo” reaction formula:
(2) Post-condensation reaction
Catalyzed by transition metal cations or activated carbon-like structures, the hydroxyl groups on the benzene ring can undergo condensation reaction to provide the structure of two aromatic hydroxyl groups for PCDD/Fs formation, and then the chlorobenzene and chlorophenol generated by the oxidation reaction are condensed to dioxins.
Huang and Buekens (Citation2001). found that the addition of reactive group initiator in the reaction was able to increase the number of PCDD/Fs by 5 ~ 15 times. Apparently the reactive group plays a very important role in de novo reaction. They concluded that the necessary conditions for PCDD/Fs formation were summarized as follows: (1) suitable temperature (200 ~ 500°C); (2) precursors (mainly organic compounds containing benzene rings); (3) presence of inorganic carbon; (4) presence of oxygen; (5) presence of chlorine sources; (6) presence of transition metal cation catalysts, mainly Cu2+.
Precursor synthesis mechanism
Synthesis reaction of precursors are mainly divided into homogeneous catalytic reaction of precursors and heterogeneous catalytic reaction of precursors (Sun Citation2012). The following precursors of PCDD/Fs have been confirmed: (1) organic compounds with similar chemical structures to PCDD/Fs, such as chlorophenol and chlorobenzene; (2) chlorine-free organic compounds with dissimilar molecular structures, such as aliphatic compounds (e.g. propylene, acetylene), aromatic compounds (e.g. benzene, toluene, phenol), and other short-chain hydrocarbons (Addink, Espourteille, and Altwicker Citation1998; Chen Citation2006; Vermeulen, Van Caneghem, and Vandecasteele Citation2013).
In brief, homogeneous catalytic reaction of precursors refers to the process of formation, desorption, dechlorination and decomposition between dioxin precursors (e.g. chlorobenzene, chlorophenol, aliphatic compounds) adsorbed on fly ash under the action of catalyst. Heterogeneous catalytic reaction of precursors refers to the catalytic formation of dioxins between gaseous precursors (e.g. PVC, chlorobenzene, chlorophenols) formed by insufficient combustion of waste and dioxin precursors adsorbed on fly ash, with the temperature of 200 ~ 500°C. Representative models for homogeneous and heterogeneous catalytic reaction are shown in (Ficarella and Laforgia Citation2000), and the two reaction constants are roughly the same except for the formation process.
Table 1. Representative models for homogeneous and heterogeneous catalytic reactions. (Ficarella and Laforgia Citation2000)
Some scholars have carried out quantum chemical calculations on the formation process of PCDD/Fs by 4,4’-DCB using the Gaussian 09 suite program to confirm the synthesis mechanism of precursors (Hou et al. Citation2019). Fernandez Pulido et al. (Citation2016). illustrated the mechanism of 2-CP condensation to form PCDD catalyzed by CuCl. The hydroxyl group of 2-CP was destroyed by Cu+ to promote the removal of HCl, which in turn formed a oxygen bridge, followed by the formation of PCDD after the C-Cl bond was broken and CuCl molecule was removed.
Studies have demonstrated that synthesis reaction of precursors mainly forms PCDDs, and “de novo” reaction mainly forms PCDFs. In this regard, some scholars have been proposed that the ratio of PCDDs/PCDFs can be compared to judge which mechanism plays a major role. Precursor synthesis mechanism dominates if the ratio of PCDD/PCDFs is greater than 1. “De novo” synthesis mechanism is dominant if the ratio of PCDD/PCDFs is less than 1. Some scholars have also concluded that the formation mechanism of dioxins in actual MSWI process is mainly “de novo” synthesis through analysis and calculation (Huang and Buskens Citation1999).
So far, which mechanism plays a major role for dioxin formation, the interconnection between the three mechanisms, the role of catalysts, and so on have remained controversial in academia. The following is our discussion.
the inherent dioxins in the waste are not the main source of dioxins, which can be decomposed by optimizing combustion conditions. At lower temperatures (200 ~ 400°C), the dominant role is played by the precursor synthesis mechanism and the de novo synthesis mechanism. For the precursor synthesis mechanism, the amount of synthesized PCDD/Fs is mainly restricted by that of the precursors. In the case of sufficient combustion, the amount of precursor formed is greatly reduced and the synthesis of PCDD/Fs is inhibited, at which time the de novo synthesis mechanism dominates. While in the case of insufficient combustion, a large amount of precursors are generated, and the conversion rate of these precursors into PCDD/Fs is much faster than that of the de novo synthesis mechanism, at which time the precursor synthesis mechanism dominates. The high-temperature gas-phase mechanism can play a dominant role on PCDD/Fs formation only if the amount of precursors is higher and the temperature is sufficiently high.
A large amount of CPh and CBz are formed by the high-temperature gas-phase reaction, which provides sufficient precursors for PCDD/Fs synthesis at low-temperature zone. Intermediates formed by de novo synthesis can also be used as precursor synthesis reactants.
The role of catalysts can be roughly divided into three categories: metal catalysts can promote deacon reaction and precursor synthesis; Activated carbon can promote the catalytic dechlorination and condensation of PCDDs; Fly ash can significantly promote chlorophenol reaction.
Influencing factors
From the above formation mechanisms, it can be seen that the influencing factors of dioxin formation in MSWI process are complex and multifaceted. The effects of temperature, catalyst, chlorine source, carbon source, oxygen concentration and moisture on PCDD/Fs formation are briefly analyzed in .
Table 2. Effects of various influencing factors on the formation of PCDD/Fs.
Control technologies of dioxins in MSWI process
In 2014, China promulgated the Pollution Control Standard for municipal solid waste (GB18485-2014). The emission limit of dioxins in MSWI flue gas was reduced to 0.1 ng TEQ/m3, which not only regulates dioxin emissions, but also places higher demands on control technologies. In this chapter, an introduction was conducted of dioxin control technologies from three perspectives as follows: pre-combustion control, in-combustion control and post-combustion control. Finally, technical routes for controlling dioxin emissions in MSWI flue gas were proposed.
Pre-combustion control technologies
The composition of China’s waste is complex, with high water content and organic matter, and too many dioxins will be formed if incinerated directly. In order to reduce the formation and emission of dioxins, the most important thing should be the pretreatment of waste and the front-end of waste classification before entering the incinerator.
The classification and pretreatment methods of waste should be adapt to China’s national conditions. At the front-end, we should coordinately promote the construction of MSW classification and drop-off points in residential areas, and enhance the environmental awareness of public. At the middle-end, we should build a classification and transportation system and improve the current garbage trucks. At the end, we should promote the construction of disposal facilities and realize the industrialization of waste recycling. Fully build the whole chain of waste classification system of “front-end classification and drop-off + middle-end classification and transportation + end classification and disposal”. Technical routes of waste classification and pretreatment is shown in . Mixed waste is divided into three categories: kitchen waste, dry waste and hazardous waste after the front-end of classification. The kitchen waste is sent to MSWI plant after compression and dehydration, and then the heap fermentation reaction is carried out in the storage pit, which can reduce the water content of kitchen waste and improve the calorific value (Shang et al. Citation2012); The dry waste first passes through a non-ferrous metal separator to separate out the recyclable Cu, Fe and other scrap metals. Subsequently, through manual sorting, the recyclable waste paper, glass, plastics, textiles, and so on, are sorted out. The recyclable part of dry waste is sent to the waste utilization plant for recycling, while the non-recyclable part and the treated kitchen waste are crushed and compressed into RDF (Refuse derived fuel). The waste is crushed before entering the incinerator, which can increase the contact area with oxygen and make the combustion more sufficient. Combustion with RDF has been proven to reduce dioxin emissions.
After the classification and pretreatment of waste, the carbon sources, chlorine sources and metal catalysts are greatly reduced, which can effectively control the formation of dioxins during the incineration process. Shi (Citation2009) applied the new waste classification and pretreatment system to the pretreatment of MSW, and the results showed that the concentration of dioxins in MSWI flue gas was reduced by more than 30% and the concentration of various PAHs in MSWI ash was reduced by 20%-60% after classification and pretreatment of MSW.
Studies have shown that co-firing waste with high-sulfur coal can effectively inhibit the formation of dioxins. However, this method has been applied in a few MSWI plants only and co-firing waste with coal is inconsistent with the dual carbon policy of China.
In-combustion control technologies
Optimization of the combustion process
Reasonable and good combustion process in incinerator is the key to control dioxin formation. The formation of PCDD/Fs can be reduced by optimizing the furnace and grate structure. Various parameters of the combustion process, such as temperature, oxygen, and flue gas residence time, have a greater impact on PCDD/Fs formation. The parameters and performance indexes shall meet the international “3 T + E” principle. That is, the flue gas temperature at furnace exit is not less than 850°C during the combustion process; reasonable control of air flow, O2 concentration and injection position; entering the secondary air at high-temperature zone and mixing thoroughly to enhance the turbulence intensity; the residence time of the gas at high-temperature zone (>2s). The combustion conditions are optimized so that MSW and volatile soot can be burned adequately, thus inhibiting the formation of PCDD/Fs (Chang and Huang Citation2000; Chen Citation2006).
CO concentration in incinerator is negatively correlated with combustion efficiency. Studies have shown that the formation of PCDD/Fs can be inhibited and burned under low CO condition, the ideal CO concentration in flue gas is less than 60 mg/Nm3 (Chen et al. Citation2004). Therefore, improving combustion efficiency to reduce CO concentration is an important factor affecting PCDD/Fs formation.
Addition of inhibitors on dioxin formation
The formation of dioxins can be reduced by adding inhibitors in MSWI process. At present, inhibitors are mainly divided into three categories: the first category of sulfur-containing inhibitors include sulfur-containing compounds such as ammonium sulfate, pyrite, and sodium thiosulfate (Hunsinger, Seifert, and Jay Citation2007; Wu et al. Citation2012; Yan et al. Citation2006). Many scholars have shown that CuCl2 catalyst with high activity can be converted to the low active CuSO4 by sulfur-containing compounds, thus reducing the formation rate of PCDD/Fs (Chang, Cheng, and Chi Citation2006; Ke et al. Citation2010). Some scholars have also believed that the conversion of Cl2 to HCl by SO2 is the main mechanism of the inhibition process (Griffin Citation1986). Samaras et al. (Citation2000). investigated the inhibitory ability of different sulfur-containing compounds on PCDD/Fs. The results showed that PCDD/Fs were significantly inhibited by inorganic sulfur-compounds and the I-TEQ reduction rate was as high as 98%. The inhibition rate of PCDD/Fs formation by pyrite reached 98.3%, and with the increase of concentration, the concentration of PCDD/Fs decreased to about 0.1 ng I-TEQ/Nm3, EU emission standard was met.
The second category of nitrogen-containing inhibitors include ethanolamine, monoethanolamine, urea, ammonia, triethanolamine, thiourea, NaSCN, and other nitrogen-containing compounds (Ren et al. Citation2021; Tuppurainen et al. Citation1999). Studies have shown that the formation of dioxins can be inhibited by nitrogen-containing compounds with more than 95% inhibition rate. Thiourea is commonly used as an inhibitor of dioxins due to its high content of S and N (Lin et al. Citation2015). Luna et al. (Citation2000) studied the inhibition mechanism of this process. Thiourea reacted with the metal catalyst to form nitrogen-containing metal complexes with strong bonding, which led to irreversible deactivation of the catalytic site, and then the chlorination reaction in the formation of dioxins was inhibited. (Ren et al. Citation2021). studied and compared the inhibitory effects of NaSCN and thiourea on dioxin emissions in MSWI system. The results showed that NaSCN had better effect on dioxin emissions reduction than thiourea, and NaSCN showed excellent application prospects in controlling dioxin emissions.
The third category of alkaline dechlorinators include alkaline compounds such as CaO, CaCO3 and NaOH (Lei Citation2017). Alkaline dechlorinators react with volatile chlorine-containing substances and most of the chlorine in the gas phase is transferred to the solid phase residue, thereby reducing the in-furnace reformation and post-furnace resynthesis of dioxins. Wen et al (Liu et al. Citation2005). found that the conversion of dioxin precursors to dioxins can be effectively inhibited by CaO. The inhibition rate of 5% CaO on the conversion of PCP, PCB and 2,3,4,5-T4CP to dioxins were 99%, 89.8% and 84.3% respectively. Ma et al. (Citation2018). comparatively investigated the effects of CaO and S on PCDD/Fs congeners formation in MSWI process. The results showed that the inhibition on HxCDD/Fs formation by CaO was the most significant, and with an inhibition rate of 85.1%. The inhibition on HpCDD/Fs formation by S was more obvious than CaO, and the inhibition rate was about 88.1%. Furthermore, addition of dioxin formation inhibitors in MSWI process is more economical than by using extra air pollution control devices (APCDs) or removal processes.
Flue gas quench technology
Flue gas quench technology is based on the change of temperature field to cause homogeneous or heterogeneous condensation of gaseous precursors of PCDD/Fs, the formed liquid or solid particles are adsorbed on the fly ash under the action of thermophoresis force, and then captured by the dust removal device. Kunshan MSWI power plant changed the structural type of flue gas air preheater and economizer at the tail flue of waste heat boiler to all economizers, so that the flue gas temperature can be quickly reduced from 450°C to 195°C. The test results showed that the emission concentration of dioxins was basically controlled below 0.1 ng I-TEQ/m3 (Zhu and Cai Citation2011). In addition, the residence time of the flue gas in the range of 200 ~ 400°C can also be reduced by flue gas quench technology, so as to avoid the temperature interval for PCDD/Fs re-synthesis.
Post-combustion control technologies
New purification process
Activated carbon injection and bag filter (ACI+BF) have been proved to be the most effective combined process for the purification of dioxins in MSWI flue gas. The main mechanism of bag filter for removing dioxins from flue gas is to remove dioxins adsorbed on fly ash, but the effect on gaseous suspended dioxins is very poor. The activated carbon after adsorption can not be recycled and regenerated, and can only be disposed by landfill or solidification as solid waste or even hazardous waste. Although the efficiency of ordinary electrostatic precipitator (ESP) is as high as 99%, the operating temperature (150 ~ 300°C) is exactly the temperature range for PCDD/Fs re-formation, which is extremely detrimental to the control of dioxin emissions. Dioxins are a typical condensable particulate matter (CPM) (Du et al. Citation2018), and the most common method for the capture and removal of CPM is condensation. Lu et al (Lu, Liu, and Zhang Citation2020). invented a new type of ESP, the cold electrode electrostatic precipitator (CE-ESP). That is, on the basis of the condensation method, the tubular circulation cooling tubes are laid on the anode plate to reduce the corrosion of electrode plate. The coupling of electric field force, diffusiophoresis force and thermophoretic force synergistically promotes the coagulation, agglomeration and trapping of PCDD/Fs to achieve their efficient removal. The proposal of CE-ESP has great research value and practical significance, and its potential application capability in removing dioxins is waiting to be explored and utilized.
Selective catalytic reduction (SCR) technology
Selective catalytic reduction technology (SCR) is commonly used for NOx removal in coal-fired power plants. Studies have shown that the decomposition of PCDD/Fs can be effectively facilitated by SCR technology using NH3-SCR catalyst (V2O5-WO3/TiO2) without hindering the normal operation of incinerator (Chang et al. Citation2009; Dvo?Ák et al. Citation2010; Lu et al. Citation2013). At present, most of the new MSWI power plants in China are equipped with SCR reserved space to cope the possible demand for dioxin standards upgrading in the future.
Vermeulen et al. (Citation2014). made a detailed study for the whole process of V2O5-WO3/TiO2 catalyst inhibiting the formation of dioxins. First of all, the outlet temperature of bag filter is generally 150°C, and catalytic reduction cannot be carried out at this temperature. Therefore, the flue gas discharged from incinerator needs to be reheated in a gas heat exchanger to heat the gas from 125 ~ 130°C to 219 ~ 229°C. The heated flue gas is then decomposed at 300°C after entering the SCR reactor, and 300°C is the temperature with the highest catalytic efficiency of V2O5-WO3/TiO2 catalyst. The main mechanism of this process is that PCDD/Fs were oxidized by V2O5-WO3/TiO2 catalyst, nontoxic substances such as H2O, CO2 and HCl were generated in the SCR reactor at 300°C, and then the purified gas was discharged through the internal blower (Dvo?Ák et al. Citation2010). Higher temperature favored catalytic oxidation, and the removal efficiency of dioxins was as high as 97.24%, while low-temperature led to catalyst deactivation and promoted the formation of PCDD/Fs. Dvo?Ák et al. (Citation2010). conducted an experimental study on the removal of NOx in this process and found that the removal efficiency of NOx reached 90.3% at 300°C. This study provided a theoretical basis for the co-processing of dioxins and NOx.
So far, SCR technology has not been applied in incinerators of China. One important reason is that the synergistic removal of multiple pollutants from actual flue gas is not studied in sufficient depth. In addition, the presence of trace amounts of heavy metal elements in the waste can easily poison the catalyst in SCR reactor. Therefore, SCR reactor is generally installed after scrubber and bag filter in industrial application, but the temperature condition often fail to meet the requirements, and a heating device needs to be installed. This leads to the high operation cost of SCR process, so catalysts with high activity at low-temperature have high research value.
Electron beam radiation technology
Electron beam radiation can treat a large amount of exhaust gas, especially when the temperature of exhaust gas is low (Jin et al. Citation2013), the combination of electron beam radiation and slaked lime can simultaneously remove HCl, SO2, NOx and chlorine-containing compounds from the exhaust gas (Osada et al. Citation1995). Paur et al. (Citation1991). demonstrated for the first time the feasibility of electron beam degradation of gaseous PCDD/Fs. Researchers from Japan Atomic Energy Research Institute, using the method of electron beam decomposition tested in a waste dump, and found that PCDD/Fs were significantly removed. First of all, 1000 m3 exhaust gas was generated by burning waste per hour, and then imposed electron beam (current 40 mA, bandwidth 45 cm) generated by 300KV voltage. The results showed that the decomposition rate of PCDD/Fs was above 90% (Ma et al. Citation2012).
Electron beam degradation of PCDD/Fs has the advantages of no secondary pollution, moderate energy consumption and simple process, and can be directly installed on the existing incinerator, so it has a broad development prospect.
Other new technologies
Currently, scholar Chen (Citation2006) used UV/O3 oxidation technology to degrade dioxins in flue gas, and the results showed that UV/O3 oxidation technology was effective in degrading gaseous dioxins. Scholars Hung et al. (Citation2010). used low-temperature plasma technology to degrade dioxins in flue gas and conducted experiments and studies. However, the above researchs are still in the laboratory stage and have not yet been put into industrial application.
Technical routes for controlling dioxin emissions in MSWI process
In summary, the control of dioxins in MSWI process must adopt a full range of control technologies. Technical routes for controlling dioxin emissions in MSWI process is shown in . Firstly, try to remove chlorine and catalyst sources from the source, secondly inhibit the formation of dioxins from the combustion process, and finally realize the comprehensive control of dioxins through terminal purification technologies.
Control technologies of dioxins in MSWI-FA
Studies have shown that dioxins are mainly condensed and adsorbed on fly ash in MSWI process. The content of PCDD/Fs in fly ash accounts for 65 ~ 70% of the total emissions of PCDD/Fs (Chang and Chung Citation1998; Tang, Huang, and Yang Citation2013), the toxic equivalent of PCDD/Fs in fly ash accounts for more than 80% of the total toxic equivalent (Shin and Chang Citation1999), so MSWI-FA must be recycled or landfilled after harmless disposal. In this chapter, a highlight introduction was conducted of dioxin control technologies in MSWI-FA, and the mechanism of each control technology was briefly analyzed. Finally, the advantages and shortcomings of each control technology were compared and analyzed.
Thermal treatment technologies
In recent years, many scholars have conducted in-depth research on thermal treatment technologies, which can be divided into high-temperature melting technology, low-temperature heat treatment technology and hydrothermal treatment technology three categories.
High-temperature melting technology
High-temperature melt treatment can completely decompose PCDD/Fs from fly ash in a relatively short time. The mass and volume of treated fly ash are reduced by more than 1/3 and 2/3 respectively (Wang et al. Citation2020), and the slag can be used as construction materials to achieve effective utilization of resources. However, the toxic equivalence of PCDD/Fs only begins to decrease when the temperature is higher than 650°C (Huber et al. Citation2018), and dioxin emissions can be effectively controlled when the temperature reaches about 1200 ~ 1400°C. Therefore, high-temperature melting technology has high energy consumption and investment cost, and the secondary fly ash generated in heat treatment process will be resynthesized into PCDD/Fs (Li Citation2016; Zhu et al. Citation2021).
Low-temperature thermal treatment technology
Low-temperature thermal treatment technology refers to the degradation of PCDD/Fs in an inert atmosphere with a temperature much lower than that of high-temperature melting technology, the main degradation pathway of PCDD/Fs at low-temperature is the dechlorination reaction. At present, the studies on low-temperature thermal treatment of fly ash at home and abroad mainly focus on the thermal treatment parameters. Stieglitz and Vogg (Citation1987). demonstrated that dioxins in fly ash can also be decomposed at low-temperature. The degradation rate of dioxins was up to 95% when the fly ash was heated at 600°C for two hours in an oxygen atmosphere, but dioxins were re-synthesis at low-temperature. When the fly ash was heated in an inert atmosphere of 300°C for two hours, the degradation rate of dioxins reached 90% and the re-synthesis rate was low (Huang Citation1998). Huang (Citation2005) investigated the removal efficiency of dioxins from fly ash under various conditions. The experimental results showed that the most cost-effective experimental conditions for low-temperature removal of dioxins from fly ash were: nitrogen atmosphere, temperature at 400°C, and heating for 60 min.
Compared with high-temperature melting technology, low-temperature thermal treatment technology can not only reduce energy consumption, but also solve the re-synthesis problem of dioxins at low-temperature zone effectively. However, this technique must be carried out in an oxidizing or inert atmosphere, which makes it difficult to operate in practice (Peng et al. Citation2020).
Hydrothermal treatment technology
Hydrothermal treatment technology is a late-model and effective method to degrade dioxins in fly ash (Hu et al. Citation2012; CitationMa; Xie Citation2010). The solubility of dioxins is extremely low at normal temperature and pressure. However, the solvent is in a (sub) critical state in the physical environment of high temperature and pressure provided by reactor. The solubility of dioxins in this state is substantially improved, and dioxins in fly ash can be dissolved into solvent and effectively degraded (Liu Citation2019).
Yamaguchi et al. (Citation1996). first utilized hydrothermal treatment technology to degrade dioxins in fly ash. They found that the hydrothermal treatment technology can effectively degrade dioxins in fly ash, and the degradation rate of dioxins was as high as 99.9% after adding alkali and methanol. However, methanol is highly toxic and can easily cause secondary contamination. Hu et al. (Citation2012). found that low-polluting, low-cost ferric sulfate and ferrous sulfate can effectively promote the degradation of dioxins during hydrothermal treatment and that temperature was the most critical factor in the hydrothermal degradation process of dioxins. Domestic scholars Ma et al. studied the degradation efficiency of dioxins in fly ash under aerobic and anaerobic conditions, and the results showed that the degradation efficiency of dioxins reached 93.08% and the toxicity equivalent decreased by 95.72% after hydrothermal treatment under anaerobic condition for 12 h. The efficiency of hydrothermal degradation on dioxins increased with the increase of temperature, and 250°C was the optimal temperature for hydrothermal treatment and the degradation efficiency of dioxins was as high as 99.93%. Significant reactions such as hydrodechlorination, interconversion of PCDDs and PCDFs occurred during hydrothermal treatment (Jin et al. Citation2013).
Not only can hydrothermal treatment technology degrade dioxins efficiently, but also the heavy metals in fly ash can be stabilized. Compared with low-temperature thermal treatment technology, the energy consumption of hydrothermal treatment is lower, and the treated fly ash can be used in the cement industry (Ma and Brown Citation1997). However, the industrial application of hydrothermal treatment technology is also facing great challenges: the wastewater generated by the treatment process is highly corrosive and can cause more harm to the environment if disposed of improperly (Peng et al. Citation2020).
Photodegradation technology
Photodegradation of dioxins is a cost-effective method of degradation, and PCDD/Fs can be oxidized and decomposed by absorbing near-ultraviolet rays. In the most recent years, most reports on photodegradation technology have focused on how to improve the degradation efficiency of dioxins in fly ash, and oxidizing atmosphere and semiconductor catalyst have been proved to promote the photodegradation rate (Chen Citation2006; Huang Citation2005; Zhang, Zhang, and Liu Citation2020).
Sommer et al. (Citation1996). compared the photodegradation rates of PCDD/Fs in fly ash under the oxidizing (O2/O3) and reducing (N2/NH3) atmospheres. The tests showed that the oxidizing atmosphere was more favorable for the photodegradation PCDD/Fs, and the degradation rate of PCDD/Fs reached 70%. Koester and Hites (Citation1992). found that the presence of ozone promoted the photodegradation of PCDD/Fs, which increased from 35% to 50% with the increase of light duration.
When the semiconductor catalyst is illuminated by light with energy greater than the width of forbidden band, conduction band electrons (e−) and holes (h+) with high redox electrode potential will be formed on the surface. They are capable of redox reactions with H2O and O2 adsorbed on the surface of semiconductor catalyst under the action of electric field or through diffusion, thus reactive groups such as hydroxyl radical and superoxide radical are generated to degrade PCDD/Fs into CO2, H2O, etc (Pelaez et al. Citation2012). The semiconductor photocatalytic degradation process of PCDD/Fs is shown in . Among the catalysts used for photocatalysis, N-type semiconductor TiO2 is widely used owing to its superior performance. Li et al. (Citation2011). prepared N-F doped TiO2 photocatalyst using NH4F as N source and F source, and the degradation of 4-chlorophenol reached 75.84% under the visible light irradiation for 5 h. Binh et al. (Citation2014). conducted UV degradation test of 2,3,7,8-TCDD in soil using anatase nano titanium dioxide and the degradation rate of 2,3,7,8-TCDD was as high as 79.6%.
In conclusion, photodegradation technology can quickly and effectively degrade PCDD/Fs in fly ash with low cost, but there are also shortcomings such as incomplete degradation and secondary pollution of degradation products. How to prepare a more efficient catalyst combined with UV light is the key to its industrial application.
Plasma technology
Plasma technology has been proved to effectively degrade dioxins in MSWI-FA (Agon et al. Citation2016; Hung et al. Citation2010; Zhou et al. Citation2003). The process of degrading dioxins in fly ash by plasma technology is shown in . Collisions and reactions occur between a large number of high-energy electrons, various reactive radicals generated by plasma furnace and PCDD/Fs, chemical bonds such as C-H, C-Cl and C-O are destroyed, and than PCDD/Fs is decomposed into nontoxic and harmless CO2, HCl and H2O (Zhang, Zhang, and Liu Citation2020).
The literature (Koester and Hites Citation1992) reported that the treatment of MSWI-FA by DC plasma melting. The results showed that the volume of fly ash was reduced by 78%, and the degradation rate of PCDD/Fs was as high as 98.57%. Katou et al. (Citation2001). applied the plasma melting furnace with graphite electrode for the detoxification of MSWI-FA. The results showed that the decomposition rate of PCDD/Fs was up to 99% at 1400 ~ 1500°C.The fly ash treated with plasma technology will be vitrified to form microcrystalline glass, which can be used as raw materials for cement, insulation materials, and other construction materials (Yang et al. Citation2014).
Plasma technology is an emerging technology in recent years, which can achieve the goals of fly ash reduction, harmlessness and resource utilization. However, this technology is still not mature enough and there are some unresolved problems: (1) While the plasma generates active particles conducive to the decomposition of dioxins, some unfavorable by-products will be generated; (2) The plasma generator has low service life and high cost, and the development of a plasma generator with high service life and low cost is the focus of current researchs.
Biodegradation technology
Biodegradation technology refers to the mineralization of PCDD/Fs into inorganic substances such as H2O and CO2 through the biochemical action of microorganisms (algae, bacteria and fungi, etc.), which is more complex than the above three technologies. The microbial mineralization process of PCDD/Fs is shown in . Firstly, high-chlorinated PCDD/Fs are dechlorinated by anaerobic microorganisms under anaerobic condition, and then low-chlorinated PCDD/Fs are oxidized to CO2 and H2O by aerobic microorganisms under aerobic condition.
In recent years, an increasing number of studies have been reported on biodegradation technology, which show great potential in degrading PCDD/Fs. summarizes the biodegradation of POPs. Compared with conventional methods, biodegradation technology requires low equipment and labor costs and is an environment-friendly and sustainable technology for the degradation of PCDD/Fs (Megharaj et al. Citation2011; Perelo Citation2010). The biodegradation mechanism still needs to be further improved due to the long degradation cycle and low efficiency, and the toxicity of heavy metals in fly ash to microorganisms needs to be urgently addressed (Zhu et al. Citation2021).
Table 3. Summary for biodegradable POPs.
Water-washing coupled cement kiln co-processing technology
Cement kiln co-processing of fly ash refers to the utilization of MSWI-FA as a raw material added to the cement production process to replace part of cement raw materials. At high-temperature zone, dioxins can be completely oxidized and decomposed into harmless substances such as small molecules, which can effectively degrade dioxins in fly ash and realize resource disposal of fly ash at the same time, so it is a win-win technology. When the replacement ratio of MSWI-FA is within a certain range, it will not affect the compressive strength of clinker (Shi, Chang, and Chiang Citation2003). However, high concentrations of chlorine salts in fly ash can reduce the quality of cement, corrode the wall of cement kiln (Dontriros, Likitlersuang, and Janjaroen Citation2020), and may promote the re-synthesis of dioxins at low-temperature zone. The Technical Specification for Environmental Protection of Cement Kiln Co-processing of Solid Waste (HJ662-2013) also stipulated that the content of chlorine element in the material entering the kiln should not be greater than 0.04%. Therefore, the fly ash needs to be dechlorinated by water-washing before entering the kiln. Schematic diagram of water-washing coupled cement kiln Co-processing process is shown in . Water-washing can improve the effect of cement kiln co-processing and guarantee the quality of cement, and the wastewater generated by water-washing process can be recycled after treatment.
In recent years, many domestic and foreign scholars have evaluated emission and distribution of dioxins in cement kiln co-processing fly ash and found that cement kiln co-processing technology is feasible. For example, Yan et al. (Citation2018). found that the co-processing of MSWI-FA by water-washing coupled cement kiln had not impact negatively on the formation of PCDD/Fs and the total destruction rate for PCDD/Fs in MSWI-FA was 82.6%. Liu et al. (Citation2015). collected and analyzed PCDD/Fs in stack gas and particulate matter generated by cement kiln co-processing MSWI-FA. The results showed that stack emissions of PCDD/Fs were below the European Union limit for cement kilns (0.1 ng-TEQ/m3). Xiao et al. (Citation2018). also studied the effect of cement kiln co-processing fly ash on clinker, and the results showed that the concentration of dioxins in clinker and fly ash is much lower than the national standards.
Water-washing coupled cement kiln co-processing technology and standards are relatively mature, and with the advantages of large treatment capacity, saving cement raw materials, effective degradation of dioxins and solidification of heavy metals. However, there are also technical bottlenecks, such as high energy consumption, high cost of water-washing pretreatment, and difficulty in treating the salt generated by evaporation and crystallization of water-washing waste liquid.
Iron ore sintering process co-processing technology
Min et al. (Citation2017). first proposed a new method of co-processing MSWI-FA by utilizing the iron ore sintering process. The iron ore sintering process is one of the most important procedures of iron and steel production. During this process, an appropriate amount of fuels and fluxes are added to the various powdered iron-bearing raw materials, and then the mixture is agglomerated into finished sinter at high temperature. The sintering process has an environment similar to that of high-temperature melting, A high temperature (>1300°C) generated during the process were conductive to the degradation of dioxins and the volatilization of heavy metals when co-processing MSWI-FA. Therefore, the sintering process has the prerequisite to solve the difficult problems such as dioxins and heavy metals in fly ash. The main chemical composition of fly ash is CaO and SiO2, which can be used as fluxes in the sintering process and inhibitors of dioxin formation. Min et al. (Citation2018). evaluated the effect of MSWI-FA addition on the formation and emission of PCDD/Fs through sintering pot tests. The results showed that most of the PCDD/F congeners in MSWI-FA were destroyed and the mass emission of PCDD/Fs decreased. However, the amount of fly ash added should be controlled according to the bearing capacity of the sintering process when co-processing MSWI-FA. Studies have shown that the impact on sinter composition, sintering process, physical properties, metallurgical properties and flue gas emissions is small when the proportion of fly ash added is less than 1%, and the addition of MSWI-FA can be accepted up to 2% as far as the sinter strength and yield maintain (Min et al. Citation2017; Qin Citation2017).
Iron ore sintering process has higher chlorine resistance than cement kiln co-processing without water-washing pretreatment. However, the content of dioxins in flue gas after the addition of fly ash sintering is uncertainty, and dioxins may be re-synthesized at low-temperature zone, whether the fly ash is water-washed or not. Therefore, it is of great significance to reduce the negative impacts on dioxin emissions caused by adding MSWI-FA. Gan et al. (Citation2020). proposed that the degradation of dioxins was enhanced by the pretreatment of MSWI-FA pelletizing. Compared with the addition of fly ash powder, the degradation rate of dioxins in fly ash increased by 3% and the concentration of dioxin emissions in flue gas decreased by 20.5%. He et al. (Citation2022). studied the inhibition behaviors of PCDD/Fs by adjusting the proportion of sintering raw mixture (calcined lime (CaO) and limestone (CaCO3)). Experimental results indicated that a slight increase in the proportion of CaO or CaCO3 in the sintered raw mixture within the normal range is effective in reducing the international total toxicity equivalent concentration of dioxins.
Compared with other high-temperature treatment technologies, iron ore sintering process has simple operating conditions and lower costs. However, the treatment process will generate heavy metal-containing flue gas and secondary fly ash. The technology and standards for co-processing MSWI-FA through iron ore sintering process are still not quite mature, the related researchs are still at pilot stage and have not yet been put into industrial application. From the process point of view, co-processing MSWI-FA through iron ore sintering process is feasible, which can be further studied and analyzed theoretically.
Comparative analysis of PCDD/Fs degradation technologies in fly ash
At present, there are still many shortcomings in degradation technologies of PCDD/Fs in fly ash, and future research will mainly focus on promoting its industrial application. The comparative analysis of the advantages, disadvantages and technical maturity of the above degradation technologies is shown in .
Table 4. Advantages, disadvantages and technical maturity of PCDD/Fs degradation technologies in MSWI fly ash.
Current research hotspots, challenges and future directions
Based on the summary and further consideration of relevant studies, Some research hotspots, challenges and future research directions are generalized and put forward in the aspects of dioxin formation and control.
Dioxin formation aspect
(1) The control technologies of dioxins mostly depend on the understanding of dioxin formation mechanisms. Therefore, further clarification of dioxin formation mechanisms in the incineration process is needed in the future, so as to provide theoretical guidance for the development of control technologies;
(2) In addition to dioxins, there are also PBDD/Fs, PFDD/Fs and other dioxin-like pollutants with similar structure and toxicity generated during waste incineration. The knowledge of their formation mechanisms will facilitate the development of synergistic control strategies for dioxins and other dioxin-like POPs;
(3) Dioxins are unintentionally generated during various industrial thermal processes, many cement and steel industries are also facing enormous challenges, which is a future research direction.
Flue gas control aspect
(1) Although the application of inhibitors achieved a significant inhibition of dioxin formation, traditional sulfur-based or nitrogen-based inhibitors would increase the concentration of SO2 or NOx. Therefore, the development of new, economical and environment-friendly inhibitors is a current research hotspot;
(2) Most of the existing technologies for dioxin control are single, heavy metals and NOx generated by MSWI are also important pollutants. The synergistic removal of multiple pollutants has a strong application potential, and improving additives to achieve matching of operating parameters will be a key point of research for this technology.
(3) Under the background of “dual carbon”, waste classification and renewable resources utilization will be further deepened. Meanwhile, the pretreatment of waste and the front-end of waste classification are the most important measures to reduce the formation and emission of dioxins;
(4) Through modification to enhance the dioxin adsorption capacity of activated carbon, the development of SCR catalysts with high activity at low temperature, and the application of flue gas quench technology are all current research hotspots;
(5) In the “dual carbon” situation, the control standards for dioxins are becoming increasingly stringent. Given that it is difficult to break through the existing control technologies in a short time, some waste power generation enterprises have to meet the emission standards by increasing energy consumption, which is contrary to the original intentions of energy conservation and carbon reduction.The development or improvement of low-energy and efficient pollutant control devices is the trend in the future.
Fly ash disposal aspect
(1) Although thermal treatment technologies can effectively dispose dioxins and heavy metals in MSWI-FA, all thermal treatment technologies have the shortcoming of high energy consumption. Compared with other thermal treatment technologies, hydrothermal treatment is a new and effective technology with lower energy consumption, which is a current research hotspot;
(2) About the control technologies of dioxins in MSWI-FA, most studies have focused on the establishment of the independent treating system, while synergistic treatment utilizing other industrial processes is also an important direction, which is the more promising process that the harmless treatment and resource utilization of MSWI-FA can be achieved synergistically, and can be further studied and analyzed theoretically;
(3) The disposal and utilization technologies of fly ash in line with environment-friendly and cost-controllable still need to be further studied, especially the technologies of resource utilization based on water-washing pretreatment and the purification and utilization of fly ash water-washing crystalline salt should be paid more attention.
Disclosure statement
The authors declare that they have no known competing financial interests or personal relationships that could have appeared to influence the work reported in this paper.
Data availability statement
The data that support the findings of this study are openly available in [China Statistical Yearbook] at [http://www.stats.gov.cn/].
Additional information
Funding
Notes on contributors
Bowen Zhao
Bowen Zhao, Ma. Eng., is a member of the Hebei Key Laboratory of Power Plant Flue Gas Multi-Pollutants Control, China, and focus on relevant research on air pollution control.
Xiude Hu
Xiude Hu, Ma. Eng., is an inaugural Distinguished Member of the State Key Laboratory of High-efficiency Utilization of Coal and Green Chemical Engineering, China, and focus on coal / coke chemical chain gasification, gasification filter cake decarbonization and resource utilization.
Jianyi Lu
Jianyi Lu, Ph.D., is an inaugural Distinguished Member of the Hebei Key Laboratory of Power Plant Flue Gas Multi-Pollutants Control, and long-term commitment to the research of the coupling enrichment law and removal technology of heavy metals in particulate matter during combustion.
References
- Abad, E., M. A. Adrados, J. Caixach, B. Fabrellas, and J. Rivera. 2000. Dioxin mass balance in a municipal waste incinerator[J]. Chemosphere 40 (9–11):1143–47. doi:10.1016/S0045-6535(99)00363-X.
- Addink, R., F. Espourteille, and E. R. Altwicker. 1998. Role of inorganic chlorine in the formation of polychlorinated dibenzo-p-dioxins/dibenzofurans from residual carbon on incinerator fly ash[J]. Environ. Sci. Technol 32 (21):3356–59. doi:10.1021/es971080i.
- Agon, N., M. Hrabovsky, O. Chumak, M. Hlina, V. Kopecky, A. Maslani, A. Bosmans, L. Helsen, S. Skoblja, and G. V. Oost. 2016. Plasma gasification of refuse derived fuel in a single-stage system using different gasifying agents[J]. Waste Manag 47. doi:10.1016/j.wasman.2015.07.014.
- Akki, U. 1998. Gas phase formation pathways and mechanisms of polychlorinated dibenzo-p-dioxins and dibenzofurans[J]. Atlanta: Georgia institute of technology.
- Anasonye, F., E. Winquist, B. Kluczek-Turpeinen, M. Raesaenen, K. Salonen, K. T. Steffen, and M. Tuomela. 2014. Fungal enzyme production and biodegradation of polychlorinated dibenzo-p-dioxins and dibenzofurans in contaminated sawmill soil[J]. Chemosphere 110:85–90. doi:10.1016/j.chemosphere.2014.03.079.
- Babushok, V. I., and W. Tsang. 2003. Gas-phase mechanism for dioxin formation[J]. Chemosphere 51 (10):1023–29. doi:10.1016/S0045-6535(02)00716-6.
- Binh, N. D., N. Oanh, and P. Parisian. 2014. Photodegradation of dioxin in contaminated soil in the presence of solvents and nanoscale TiO 2 particles. Environ Technol 35 (9):1121–32. doi:10.1080/09593330.2013.861873.
- Chang, M. B., and Y. T. Chung. 1998. Dioxin contents in fly ashes of MSW incineration in Taiwan[J]. Chemosphere 36 (9):1959–68. doi:10.1016/S0045-6535(97)10080-7.
- Chang, M. B., and T. F. Huang. 2000. The effects of temperature and oxygen content on the PCDD/PCDFs formation in MSW fly ash[J]. Chemosphere 40 (2):159–64. doi:10.1016/S0045-6535(99)00227-1.
- Chang, M. B., Y. C. Cheng, and K. H. Chi. 2006. Reducing PCDD/F formation by adding sulfur as inhibitor in waste incineration processes[J]. Sci. Total Environ 366 (2–3):456–65. doi:10.1016/j.scitotenv.2005.04.047.
- Chang, Y. M., C. Y. Hung, J. H. Chen, C. T. Chang, and C. H. Chen. 2009. Minimum feeding rate of activated carbon to control dioxin emissions from a large-scale municipal solid waste incinerator[J]. J. Hazard. Mater 161 (2–3):1436–43. doi:10.1016/j.jhazmat.2008.04.128.
- Chen, T., X. Dong, J. Yan, S. Lu, Y. Jin, and K. Cen. 2004. Distribution characteristics of dioxins in fly ash of waste incinerator[J]. J. Fuel Chem 32 (1):59–64. CNKI:SUN:RLHX.0.2004-01-012.
- Chen, T. 2006. Study on formation mechanism and control technology of dioxins in municipal solid waste incineration process[D]. City: Zhejiang university.
- Chen, T., J. Yan, S. Lu, X. Li, K. Qiu, and K. Cen. 2007. Characteristics of fly ash and effect of chlorine on de novo synthesis mechanism of dioxins[J]. Proc. CSEE 27 (11):27–32. doi:10.3321/j.0258-8013.2007.11.006.
- Dontriros, S., S. Likitlersuang, and D. Janjaroen. 2020. Mechanisms of chloride and sulfate removal from municipal-solid-waste-incineration fly ash (MSWI FA): Effect of acid-base solutions[J]. Waste Manag 101:44–53. doi:10.1016/j.wasman.2019.09.033.
- Du, Q., H. Dong, D. Lv, L. Su, J. Gao, Z. Zhao, and M. Wang. 2018. Field measurements on the generation and emission characteristics of PM2.5 generated by utility pulverized coal boiler[J]. J. Energy Inst 91 (6):1009–20. doi:10.1016/j.joei.2017.07.007.
- Dvo?Ák, R., P. Chlápek, D. Jecha, R. Puchy, and P. Stehlík. 2010. New approach to common removal of dioxins and NOx as a contribution to environmental protection[J]. J. Clean. Prod 18 (9):881–88. doi:10.1016/j.jclepro.2010.01.024.
- El-Shahawi, M. S., A. Hamza, A. S. Bashammakh, and W. T. Al-Saggaf. 2010. An overview on the accumulation, distribution, transformations, toxicity and analytical methods for the monitoring of persistent organic pollutants[J]. Talanta 80 (5):1587–97. doi:10.1016/j.talanta.2009.09.055.
- Faitli, J., S. Nagy, R. Romenda, I. Gombkoto, L. Bokanyi, and L. Barna. 2019. Assessment of a residual municipal solid waste landfill for prospective ‘landfill mining’[J]. Waste Manag Res 37 (12):1229–39. doi:10.1177/0734242X19881197.
- Fang, D., and K. Li. 2019. Progress of municipal solid waste incineration power generation technology at home and abroad[J]. Power Gener. Technol 40 (4):10. doi:10.12096/j.2096-4528.pgt.18234.
- Fernandez Pulido, Y., E. Suarez, R. Lopez, and M. I. Menendez. 2016. The role of CuCl on the mechanism of dibenzo-p-dioxin formation from poly-chlorophenol precursors: A computational study[J]. Chemosphere 145:77–82. doi:10.1016/j.chemosphere.2015.11.042.
- Ficarella, A., and D. Laforgia. 2000. Numerical simulation of flow-field and dioxins chemistry for incineration plants and experimental investigation[J]. Waste Manag 20 (1):27–49. doi:10.1016/S0956-053X(99)00301-3.
- Gan, M., G. Wong, X. Fan, Z. Ji, and Z. Wang. 2020. Enhancing the degradation of dioxins during the process of iron ore sintering co-disposing municipal solid waste incineration fly ash[J]. J. Clean. Prod 291 (3). doi: 10.1016/j.jclepro.2020.125286.
- Griffin, R. D. 1986. A new theory of dioxin formation in municipal solid waste combustion[J]. Chemosphere 23:1491–500. doi:10.1016/0045-6535(86)90498-4.
- He, H., X. Guo, L. Jin, Y. Peng, M. Tang, and S. Lu. 2022. The effect of adjusting sinter raw mix on dioxins from iron ore co-sintering with municipal solid waste incineration fly ash. Energies 15 (3):1136. doi:10.3390/en15031136.
- Hong, H. B., I. H. Nam, K. Murugesan, Y. M. Kim, and Y. S. Chang. 2004. Biodegradation of dibenzo-p-dioxin, dibenzofuran, and chlorodibenzo-p-dioxins by Pseudomonas veronii PH-03[J]. Biodegradation 15 (5):303. doi:10.1023/B:BIOD.0000042185.04905.0d.
- Hou, S., M. Altarawneh, E. M. Kennedy, J. C. Mackie, R. Weber, and B. Z. Dlugogorski. 2019. Formation of polychlorinated dibenzo-p-dioxins and dibenzofurans (PCDD/F) from oxidation of 4,4′-dichlorobiphenyl (4,4′-DCB)[J]. Proc. Combust. Inst 37 (1):1075–82. doi:10.1016/j.proci.2018.05.045.
- Hu, Y., P. zhang, D. chen, B. zhou, J. Li, and X. W. Li. 2012. Hydrothermal treatment of municipal solid waste incineration fly ash for dioxin decomposition[J]. J. Hazard. Mater 207-208 (15):79–85. doi:10.1016/j.jhazmat.2011.05.068.
- Huang, A. B. 1998. Comparative evaluation of techniques for controlling the formation and emission of chlorinated dioxins/furans in municipal waste incineration[J]. J. Hazard. Mater doi:10.1016/S0304-3894(98)00153-8.
- Huang, H., and A. Buskens. 1999. Comparison of dioxin formation levels in laboratory gas-phase flow reactors with those calculated using the Shaub-Tsang mechanism[J]. Chemosphere 38 (7):1595–602. doi:10.1016/S0045-6535(98)00386-5.
- Huang, H., and A. Buekens. 2001. Chemical kinetic modeling of de novo synthesis of PCDD/F in municipal waste incinerators[J]. Chemosphere 44 (6):1505–10. doi:10.1016/S0045-6535(00)00365-9.
- Huang, L. 2005. Experimental study on low temperature heat treatment and ULTRAVIOLET photolysis of dioxins in municiple solid waste incineration process[D]. City: Zhejiang university.
- Huang, W. Y., H. H. Ngo, C. Lin, C. T. Vu, A. Kaewlaoyoong, T. Boonsong, H. T. Tran, X. T. Bui, T. Vo, and J. Chen. 2019. Aerobic co-composting degradation of highly PCDD/F-contaminated field soil. A study of bacterial community[J]. Sci. Total Environ 660 (10):595–602. doi:10.1016/j.scitotenv.2018.12.312.
- Huber, F., H. Herzel, C. Adam, O. Mallow, D. Blasenbauer, and J. Fellner. 2018. Combined disc pelletisation and thermal treatment of MSWI fly ash[J]. Waste Manag 73:381–91. doi:10.1016/j.wasman.2017.12.020.
- Hung, P. C., H. C. Shu, H. C. Kai, and M. B. Chang. 2010. Degradation of gaseous dioxin-like compounds with dielectric barrier discharges[J]. J. Hazard. Mater 182 (1–3):246–51. doi:10.1016/j.jhazmat.2010.06.021.
- Hunsinger, H., H. Seifert, and K. Jay. 2007. Reduction of PCDD/F formation in MSWI by a process-integrated SO2 cycle[J]. Environ. Eng. Sci 24 (8):1145–59. doi:10.1089/ees.2007.0108.
- Jiao, S., Y. Qiu, P. Ding, P. Peng, H. Yang, and L. Li. 2017. Conjugative transfer of dioxin-catabolic megaplasmids and bioaugmentation prospects of a rhodococcus sp[J]. Environ. Sci. Technol 51 (11):6298–307. doi:10.1021/acs.est.7b00188.
- Jin, Y., H. Tian, and Y. Nie. 2003. Formation mechanism and influencing factors of dioxins in waste incineration system[J]. Chongqing Environ. Sci 25 (4):4. doi:10.3969/j.1674-2842.2003.04.005.
- Jin, Y. Q., X. J. Ma, X. G. Jiang, H. M. Liu, X. D. Li, and J. H. Yan. 2013. Hydrothermal degradation of polychlorinated Dibenzo- p -dioxins and polychlorinated dibenzofurans in fly ash from municipal solid waste incineration under non-oxidative and oxidative conditions. Energy Fuels 27 (1):414–20. doi:10.1021/ef301325f.
- Kanters, M. J., R. V. Nispen, R. Louw, and P. Mulder. 1996. Chlorine input and chlorophenol emission in the lab-scale combustion of municipal solid waste[J]. Environ. Sci. Technol 30 (7):2121–26. doi:10.1021/es950579e.
- Katou, K., T. Asou, Y. Kurauchi, and R. Sameshima. 2001. Melting municipal solid waste incineration residue by plasma melting furnace with a graphite electrode[J]. Thin Solid Films 386 (2):183–88. doi:10.1016/S0040-6090(00)01640-0.
- Kawamoto, K. 2009. Potential formation of PCDD/Fs and related bromine-substituted compounds from heating processes for ashes[J]. J. Hazard. Mater 168 (2–3):641–48. doi:10.1016/j.jhazmat.2009.02.068.
- Ke, S., J. Yan, X. Li, S. Lu, Y. Wei, and M. Fu. 2010. Inhibition of de novo synthesis of PCDD/Fs by SO2 in a model system[J]. Chemosphere 78 (10):1230–35. doi:10.1016/j.chemosphere.2009.12.043.
- Koester, C. J., and R. A. Hites. 1992. Photodegradation of polychlorinated dioxins and dibenzofurans adsorbed to fly ash[J]. Environscitechnol 26 (3):502–07. doi:10.1021/es00027a008.
- Kong, S., H. Liu, H. Zeng, and Y. Liu. 2012. Formation mechanism and influencing factors of dioxin pollutants in waste incineration process[J]. Environ. Eng 2:7. CNKI:SUN:HJGC.0.2012-S2-070.
- Lechner, B. U. 2001. Regiospecific dechlorination of spiked tetra- and trichlorodibenzo-p-dioxins by anaerobic bacteria from PCDD/F-contaminated Spittelwasser sediments[J]. Chemosphere. doi:10.1016/S0045-6535(00)00420-3.
- Lei, M. 2017. Emission characteristics and control of dioxins and heavy metals from small rural household garbage heat treatment furnace[D]. City: South China University of Technology.
- Li, X., H. Zhang, X. Zheng, Z. Yin, and W. Le. 2011. Visible light responsive N-F-codoped TiO2 photocatalysts for the degradation of 4-chlorophenol[J]. J. Environ. Sci 23 (11):1919–24. doi:10.1016/S1001-0742(10)60656-0.
- Li, J. 2016. Harmless dispoal technologies of fly ash from waste incineration[J]. Enterp. Technol. Dev 35 (7):2. CNKI:SUN:QYJK.0.2016-20-002.
- Lin, X., A. Dai, F. Jianying, L. Xiaodong, and L. Shengyong. 2015. Simultaneous suppression of PCDD/F and NOx during municipal solid waste incineration[J]. Chemosphere Environ. Toxicol. Risk Assess 126:60–66. doi:10.1016/j.chemosphere.2015.02.005.
- Liu, W., M. Zheng, Z. Bing, Y. Qian, X. Ma, and W. Liu. 2005. Inhibition of PCDD/Fs formation from dioxin precursors by calcium oxide[J]. Chemosphere 60 (6):785–90. doi:10.1016/j.chemosphere.2005.04.020.
- Liu, F., H. Yu, D. Zhang, R. Wei, and Y. Zhang. 2010. Study on formation mechanism and control of dioxins in waste incineration process[J]. Sol. Energy 8:4. doi:10.3969/j.1003-0417.2010.08.016.
- Liu, G., J. Zhan, M. Zheng, L. Li, C. Li, X. Jiang, M. Wang, Y. Zhao, and R. Jin. 2015. Field pilot study on emissions, formations and distributions of PCDD/Fs from cement kiln co-processing fly ash from municipal solid waste incinerations[J]. J. Hazard. Mater 299 (1):471–78. doi:10.1016/j.jhazmat.2015.07.052.
- Liu, W., S. Liu, and G. Huang. 2016. Research on the sorting reclaim system of municipal solid waste based on the concept of “cradle to cradle”[J]. Procedia Environ. Sci 31:482–90. doi:10.1016/j.proenv.2016.02.057.
- Liu, L. 2019. Study on hydrothermal degradation of dioxins in municipal solid waste incineration fly ash[D]. City: China University of Mining and Technology (Jiangsu).
- Liu, L. 2020. Formation mechanisms and control measures of dioxins in municipal solid waste incineration[J]. Resour. conserv. Environ. Prot 5:2. CNKI:SUN:ZYJH.0.2020-05-090.
- Lu, S. 2004. Study on the formation, emission and control mechanism of dioxins during garbage and coal combustion[D]. City: Zhejiang University.
- Lu, S., Y. Ji, A. Buekens, Z. Ma, Y. Jin, X. Li, and J. Yan. 2013. Activated carbon treatment of municipal solid waste incineration flue gas[J]. Waste Manag. Res 31 (2):1263–71. doi:10.1177/0734242X12462282.
- Lu, J., W. Liu, and S. Zhang. 2020. The utility model relates to a cold electrode electric dust collector for agglomeration and collecting condensable particles. CN210449518U[P].
- Luna, A., B. Amekraz, J. P. Morizur, J. Tortajada, M. O, and M. Yá?Ez. 2000. Reactions of Urea with Cu + in the Gas Phase: An Experimental and Theoretical Study[J]. J. Phys. Chem. A 104 (14):3132–41. doi:10.1021/jp9934634.
- Ma, X. Study on the treatment of heavy metals and dioxins from municiple solid waste incineration fly ash by hydrothermal method[D]. City: Zhejiang university.
- Ma, W., and P. W. Brown. 1997. Hydrothermal reactions of fly ash with Ca(OH)2 and CaSO4•2H2O[J]. Cem. Concr. Res 27 (8):1237–48. doi:10.1016/S0008-8846(97)00116-6.
- Ma, X. C., X. P. Zeng, J. T. Liu, K. K. You, and J. X. Ren. 2012. Technology to Control PCDD/Fs from MSW incineration processes[J]. Adv. Mater. Res 610-613:2621–26. doi:10.4028/AMR.610-613.2621http://www.scientific.net/.
- Ma, H., N. Du, X. Lin, C. Liu, J. Zhang, and Z. Miao. 2018. Inhibition of element sulfur and calcium oxide on the formation of PCDD/Fs during co-combustion experiment of municipal solid waste[J]. Sci. Total Environ 633:1263–71. doi:10.1016/j.scitotenv.2018.03.282.
- Megharaj, M., B. Ramakrishnan, K. Venkateswarlu, N. Sethunathan, and R. Naidu. 2011. Bioremediation approaches for organic pollutants: A critical perspective[J]. Environ Int 37 (8):1362–75. doi:10.1016/j.envint.2011.06.003.
- Min, Y., C. Qin, P. Shi, C. Liu, Y. Feng, and B. Liu. 2017. Effect of municipal solid waste incineration fly ash addition on the iron ore sintering process, mineral phase and metallurgical properties of iron ore sinter[J]. ISIJ Int 57 (11):1955–61. doi:10.2355/isijinternational.ISIJINT-2017-310.
- Min, Y., C. Liu, P. Shi, C. Qin, Y. Peng, and B. Liu. 2018. Effects of the addition of municipal solid waste incineration fly ash on the behavior of polychlorinated dibenzo-p-dioxins and furans in the iron ore sintering process[J]. Waste Manag 77:287–93. doi:10.1016/j.wasman.2018.04.011.
- Nam, I. H., Y. M. Kim, S. Schmidt, and Y. S. Chang. 2006. Biotransformation of 1,2,3-Tri- and 1,2,3,4,7,8-Hexachlorodibenzo-p- dioxin by sphingomonas wittichii strain RW1[J]. Appl. Environ. Microbiol 72 (1):112–16. doi:10.1128/AEM.72.1.112-116.2006.
- National Bureau of Statistics of China. 2020. China Statistical Yearbook[J]. Accessed June 19, 2020. http://www.stats.gov.cn/.
- Olivier, P., C. And, A. Rafin, and V. Etienne. 2004. Bioremediation of an aged polycyclic aromatic hydrocarbons (PAHs)-contaminated soil by filamentous fungi isolated from the soil[J]. Int. Biodeterior. Biodegradation. doi:10.1016/j.ibiod.2004.01.003.
- Osada, Y., K. Hirota, M. Sudo, S. Baba, E. Shibuya, T. Doi, M. Nakajima, M. Komiya, K. Miyajima, and T. Miyata. 1995. Pilot-scale test on electron beam treatment of municipal solid waste flue gas with spraying slaked-lime slurry[J]. Radiat. Phys. Chem 45 (6):1021–27. doi:10.1016/0969-806X(94)00158-G.
- Pariatamby, A., and Y. L. Kee. 2016. Persistent organic pollutants management and remediation[J]. Procedia Environ. Sci 31:842–48. doi:10.1016/j.proenv.2016.02.093.
- Paur, H. R., H. Mtzing, and W. Schikarski. 1991. Removal of chlorinated dioxins and furans from simulated incinerator flue gas by electron beam[C]. 4th World Congress of Chemical Engineering, Karlsruhe, Germany.
- Pelaez, M., N. T. Nolan, S. C. Pillai, M. K. Seery, P. Falaras, A. G. Kontos, P. S. M. Dunlop, J. W. J. Hamilton, J. A. Byrne, and K. O’Shea. 2012. A review on the visible light active titanium dioxide photocatalysts for environmental applications[J]. Appl Catal B 125. doi:10.1016/j.apcatb.2012.05.036.
- Peng, Y., S. Lu, X. Li, J. Yan, and K. F. Cen. 2020. Measurement, and control of dioxins from the incineration of municipal solid wastes: Recent advances and perspectives[J]. Energy Fuels 34 (11):13247–67. doi:10.1021/acs.energyfuels.0c02446.
- Perelo, L. W. 2010. Review: In situ and bioremediation of organic pollutants in aquatic sediments[J]. J. Hazard. Mater 177 (1–3):81–89. doi:10.1016/j.jhazmat.2009.12.090.
- Qin, C. 2017. Experimental study on the treatment of waste incineration fly ash by sintering process [D]. City: Northeast University.
- Ren, M., H. Zhang, Y. Fan, H. Zhou, R. Cao, Y. Gao, and J. Chen. 2021. Suppressing the formation of chlorinated aromatics by inhibitor sodium thiocyanate in solid waste incineration process[J]. Sci. Total Environ 798:149154. doi:10.1016/j.scitotenv.2021.149154.
- Ritter, E. R., and J. W. Bozzelli. 1994. Pathways to chlorinated dibenzodioxins and dibenzofurans from partial oxidation of chlorinated aromatics by oh radical: Thermodynamic and kinetic insights[J]. Combust. Sci. Technol 101 (1–6):153–69. doi:10.1080/00102209408951870.
- Samaras, P., M. Blumenstock, D. Lenoir, K. W. Schramm, and A. Kettrup. 2000. PCDD/F prevention by novel inhibitors: Addition of inorganic s- and n-compounds in the fuel before combustion[J]. Environ. Sci. Technol 34 (24):5092–96. doi:10.1021/es0001207.
- Shang, P., R. Li, J. Hao, B. Liu, and J. Tang. 2012. Research progress of heap fermentation dehydration before municipal solid waste incineration[J]. Environ. Sanit. Eng 20 (1):5–8. doi:10.3969/j.1005-8206.2012.01.002.
- Shi, P. H., J. E. Chang, and L. C. Chiang. 2003. Replacement of raw mix in cement production by municipal solid waste incineration ash[J]. Cem. Concr. Res 33 (11):1831–36. doi:10.1016/s0008-8846(03)00206-0.
- Shi, D. 2009. Study on pollutant control and mechanism of municipal solid waste incineration process based on new classified collection system[D]. City: Zhejiang University.
- Shin, K. J., and Y. S. Chang. 1999. Characterization of polychlorinated dibenzo-p-dioxins, dibenzofurans, biphenyls, and heavy metals in fly ash produced from Korean municipal solid waste incinerators[J]. Chemosphere 38 (11):2655–66. doi:10.1016/S0045-6535(98)00473-1.
- Sommer, S., R. Kamps, and K. Kleinermanns. 1996. Photooxidation of exhaust pollutants—V. Photooxidation and photoreduction of polychlorinated dibenzo-p-dioxins and dibenzofurans on fly-ash[J]. Chemosphere 33 (11):2221–27. doi:10.1016/0045-6535(96)00330-X.
- Song, H. G. 1999. Comparison of pyrene biodegradation by white rot fungi[J]. World J. Microbiol. Biotechnol 15 (6):669–72. doi:10.1023/A:1008927424034.
- Stanmore, B. R. 2004. The formation of dioxins in combustion systems[J]. Combust. Flame 136 (3):398–427. doi:10.1016/j.combustflame.2003.11.004.
- Stieglitz, L., and H. Vogg. 1987. On formation conditions of PCDD/PCDF in fly ash from municipal waste incinerators[J]. Chemosphere 16 (8–9):1917–22. doi:10.1016/0045-6535(87)90188-3.
- Sun, J. 2012. Experimental study on synthesis mechanism and preparation method of dioxins in municipal solid waste incineration process[D]. City: Tianjin University.
- Tang, Z., Q. Huang, and Y. Yang. 2013. PCDD/Fs in fly ash from waste incineration in China: A need for effective risk management[J]. Environ. Sci. Technol 47 (11):5520–21. doi:10.1021/es401463s.
- Tuppurainen, K., I. Halonen, P. Ruokojrvi, J. Tarhanen, and J. Ruuskanen. 1998. Formation of PCDDs and PCDFs in municipal waste incineration and its inhibition mechanisms: A review[J]. Chemosphere 36 (7):1493–511. doi:10.1016/S0045-6535(97)10048-0.
- Tuppurainen, K., M. Aatamila, P. Ruokojärvi, I. Halonen, and J. Ruuskanen. 1999. Effect of liquid inhibitors on PCDD/F formation. Prediction of particle-phase PCDD/F concentrations using PLS modelling with gas-phase chlorophenol concentrations as independent variables[J]. Chemosphere 38 (10):2205. doi:10.1016/S0045-6535(98)00439-1.
- Vermeulen, I., J. Van Caneghem, and C. Vandecasteele. 2013. Indication of PCDD/F formation through precursor condensation in a full-scale hazardous waste incinerator[J]. J. Mater. Cycles Waste Manag 16 (1):167–71. doi:10.1007/s10163-013-0160-7.
- Vermeulen, I., J. V. Caneghem, and C. Vandecasteele. 2014. Indication of PCDD/F formation through precursor condensation in a full-scale hazardous waste incinerator[J]. J. Mater. Cycles Waste Manag 16 (1):167–71. doi:10.1007/s10163-013-0160-7.
- Vogg, H., M. Metzger, and L. Stieglitz. 1987. Recent findings on the formation and decomposition of PCDD/PCDF in municipal solid waste incineration[J]. Waste Manag. Res 5 (1):285–94. doi:10.1016/0734-242X(87)90080-2.
- Wang, C., L.-Z. Chen, Z.-J. Liu, Y. Li, Y.-Z. Wang, and K.-X. Jiao. 2020. A new technology for treating waste incineration fly ash by shaft furnace[J]. J. Iron. Steel Res. Int 28 (7):773–84. doi:10.1007/s42243-020-00453-6.
- Wikström, E., S. Ryan, A. Touati, M. Telfer, and B. K. Gullett. 2003. Importance of chlorine speciation on de novo formation of polychlorinated dibenzo-p-dioxins and polychlorinated dibenzofurans[J]. Environ. Sci. Technol 37 (6):1108. doi:10.1021/es026262d.
- Wu, H. L., S. Y. Lu, X. D. Li, X. G. Jiang, J. H. Yan, M. S. Zhou, and W. Hua. 2012. Inhibition of PCDD/F by adding sulphur compounds to the feed of a hazardous waste incinerator[J]. Chemosphere 86 (4):361–67. doi:10.1016/j.chemosphere.2011.10.016.
- Xiao, H., R. Yu, Z. Peng, D. Yan, L. Li, K. K. Helge, W. Ning, and Q. Huang. 2018. Destruction and formation of polychlorinated dibenzo-p-dioxins and dibenzofurans during pretreatment and co-processing of municipal solid waste incineration fly ash in a cement kiln[J]. Chemosphere 210:779–88. doi:10.1016/j.chemosphere.2018.07.058.
- Xie, J. 2010. Hydrothermal treatment of MSWI fly ash for simultaneous dioxins decomposition and heavy metal stabilization[J]. Acad. Abstr. Chin. Univ. • Environ. Sci. Eng 4 (1):108–15. doi:10.1007/s11783-010-0013-8.
- Yamaguchi, H., E. Shibuya, Y. Kanamaru, K. Uyama, M. Nishioka, and N. Yamasaki. 1996. Hydrothermal decomposition of PCDDs/PCDFs in MSWI fly ash[J]. Chemosphere 32 (1):203–08. doi:10.1016/0045-6535(94)00247-9.
- Yan, J. H., T. Chen, X. D. Li, J. Zhang, S. Y. Lu, M. J. Ni, and K. F. Cen. 2006. Evaluation of PCDD/Fs emission from fluidized bed incinerators co-firing MSW with coal in China[J]. J. Hazard. Mater 135 (1–3):47–51. doi:10.1016/j.jhazmat.2005.12.007.
- Yan, M., L. Xiaodong, S. Chen, L. Jianhua, and K. Yan. 2010. Effect of temperature and oxygen on the formation of chlorobenzene as the indicator of PCDD/Fs[J]. J. Environ. Sci 10:6. CNKI:SUN:HJKB.0.2010-10-025.
- Yan, D., Z. Peng, L. Yu, Y. Sun, R. Yong, and K. Karstensen. 2018. Characterization of heavy metals and PCDD/Fs from water-washing pretreatment and a cement kiln co-processing municipal solid waste incinerator fly ash[J]. Waste Manage 76:106–16. doi:10.1016/j.wasman.2018.03.006.
- Yang, S. F., W. T. Chiu, T. M. Wang, C. T. Chen, and C. C. Tzeng. 2014. Porous materials produced from incineration ash using thermal plasma technology[J]. Waste Manag 34 (6):1079–84. doi:10.1016/j.wasman.2013.07.022.
- Zeng, X., Z. Hao, W. Pan, X. Ma, and J. Ren. 2011. Formation and control technology of dioxins in municipal solid waste incineration process[J]. Energy Environ 4:112–14. doi:10.3969/j.1672-9064.2011.04.049.
- Zhang, J. 2020. Study on enhanced removal of dioxins from soil by erythrococci degradation plasmids[D]. City: Shandong university.
- Zhang, J., S. Zhang, and B. Liu. 2020. Degradation technologies and mechanisms of dioxins in municipal solid waste incineration fly ash: A review[J]. J. Clean. Prod 250. doi:10.1016/j.jclepro.2019.119507.
- Zheng, Y., and G. Qi. 2008. Formation mechanism and control technology of solid waste incineration dioxins[J]. Environ. Prot. Sci 34 (3):4. doi:10.3969/j.1004-6216.2008.03.005.
- Zhou, Y. X., P. Yan, Z. X. Cheng, M. Nifuku, X. D. Liang, and Z. C. Guan. 2003. Application of non-thermal plasmas on toxic removal of dioxin-contained fly ash[J]. Powder Technol 135-136:345–53. doi:10.1016/S0032-5910(03)00168-2.
- Zhu, G., and Y. Cai. 2011. Abatement measures of dioxins in waste incineration - to meet eu standards[J]. China Sci. Technol. Expo 1:1.
- Zhu, W., Q. Gou, T. He, and L. He. 2021. Research progress of dioxins control technology in municiple solid waste fly ash[C]. China Society for Environmental Science annual Conference 2021 – Environmental Engineering Technology Innovation and Application Sub-venue, Tianjin, China.
- Zurbrugg, C., S. Drescher, A. Patel, and H. C. Sharatchandra. 2004. Decentralised composting of urban waste–an overview of community and private initiatives in Indian cities[J]. Waste Manag 24 (7):655–62. doi:10.1016/j.wasman.2004.01.003.