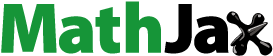
ABSTRACT
Droplet charging is an effective method to enhance dust removal efficiency using an electrostatic spray scrubber (ESS). However, effects of the materials and dimensions of different electrodes on droplet charging efficiency have not been studied systematically. In this study, ring-shaped electrodes were selected to test effects of three types of electrode materials (copper, stainless steel, and graphite) with various dimensions on droplet charging efficiency. A Faraday pail charge measurement device was used to measure the droplet charge generated by the electrodes. A reduced factorial design with four factors was used in this study to investigate the charging efficiency affected by the factors. The four factors tested were electrode material, electrode diameter, nozzle height, and applied voltage. A 304L stainless steel electrode was found to achieve higher droplet charge-to-mass ratio (CMR) values than identically shaped electrodes made from either copper or graphite. The optimal stainless steel electrode inner diameter was 100 mm. The 304L stainless-steel electrode with this optimal diameter and a height of 45 mm achieved the highest mean CMR of 0.435 ± 0.002 mC kg−1 at an applied voltage of −11 kV with the bottom of the nozzle tip positioned 15 mm below the top of the electrode.
Implications Currently, the low removal efficiency of submicron particles cannot meet the environmental control requirements of industrial applications that may have significant concentrations of particulate matter (PM) in this size range. As stricter environmental regulations are increasingly enforced, there is an urgent need to efficiently remove submicron dust particles from the air. Experiments show that the dust capture process is improved by charging droplets in the spray separator and reducing the secondary escape of dust particles in the electrostatic precipitator
Although high-voltage charging of droplets has been investigated in many studies, the effect of electrode material and size on droplet CMR is still not fully understood. The purpose of this study was to (1) quantify the performance of 304L stainless steel (304L SS), copper, and high-purity graphite electrodes for spray droplet CMR, (2) evaluate effects of the applied voltage, nozzle height, electrode material and dimension on CMR, and (3) optimize the specific values of key design factors and operating parameters that lead to the highest CMR. The results of this study aim to optimize electrostatic spray scrubbers to achieve high droplet CMR values.
Introduction
Dust is a significant problem in mining, agricultural food production, building construction, and other industrial operations. Dust emissions negatively affect human and animal health as well as environmental quality (Ru, Zhao, and Hadlocon et al. Citation2017; Xiao et al. Citation2019; Xiaochuan et al. Citation2019). A variety of dust capture and removal methods and equipment with different working mechanisms have been invented for different industrial processes, such as filters, wet scrubbers, and electrostatic precipitators. However, the removal efficiencies of conventional gas cleaning systems, such as inertial scrubbers, bag filters, and electrostatic precipitators (Balachandran, Jaworek, and Krupa et al. Citation2003; Guo and Xue Citation2021; Huang and Chen Citation2002), rapidly decrease for fine particles with diameters smaller than 1 µm, known as submicron particles. The low removal efficiency for submicron particles cannot satisfy the environmental control requirements for industrial applications that can have significant concentrations of particulate matter (PM) in this size range. In addition, dust particles smaller than 2.5 microns pose a greater threat to human health. As more stringent environmental regulations are increasingly being implemented, there is an urgent need for a method to effectively remove fine dust particles from the air.
Research has been conducted to improve the dust capture process through charging droplets in an ESS (Jaworek et al. Citation2006a, Citation2013; Wang et al. Citation2020, Citation2019) and reducing secondary escape of dust particles from the electrostatic precipitators (Chenghang, Dawei, and Qianyun et al. Citation2019; Gaunt et al. Citation2003; Jaworek et al. Citation2006b; Lee et al. Citation2019). Electrostatic spraying in a dusty air stream is an effective method to enhance fine particle removal using electrostatic forces. Industrial dust tends to carry charges and can be more effectively controlled using an ESS. (Almuhanna et al. Citation2008; Almuhanna, Amer Eissa, and Alghannam et al. Citation2012, Di Natale, Carotenuto, and D’Addio et al. Citation2015, Ru, Zhao, and Hadlocon et al. Citation2017) all indicated that ESS is a promising technology to effectively capture submicron particles.
Droplet charging is an important process for effective operation of an ESS. There are many factors that can affect droplet charging. Electrode voltage has a significant effect on the charge-to-mass ratio (CMR), which is estimated as the ratio of electric current to the mass flow rate of the droplets, of spray droplets and higher voltages, up to a limit, generally result in higher CMRs (Almekinders et al., Citation1992; John Carroz and Keller Citation1978; Tessum and Raynor Citation2021). Electrode materials and dimensions are the other significant factors. Some electrode materials may enhance the chargeability of water droplets. At present, copper, stainless steel, and brass are the most common materials used for electrodes in electrostatic nozzles (Almuhanna, Amer Eissa, and Alghannam et al. Citation2012; Chen et al. Citation2019; Marchewicz et al. Citation2019). Nickel and aluminum have also been used to make electrodes for high voltage applications with different dimensions and shapes (Kumar Patel et al. Citation2016; Manoj Kumar Patel and Kapur Citation2013; Teng and Li Citation2020).
The electrode diameter, which affects the distance between the electrode and the nozzle, is another factor affecting the droplet charging (Ahmed, Soban, and Ohyama Citation2014). As the distance decreases, the CMR increases because the electric field becomes stronger at the breakup points of the water film. However, when this distance reaches a certain limit, saturation of CMR can be noticed (Krupa, Jaworek, and Sobczyk et al. Citation2013; Xiang and Colbeck Citation1997). A shorter distance between the electrode and the spray nozzle can lead to charging instability, as some of the charged droplets may deposit on the electrode, causing charge transfer to the electrode along with localized disruptions to the generated electric field (Penney Citation1944; Teng and Li Citation2021). Additionally, water flow rate, droplet size, droplet distribution, and water conductivity are also factors that have been found to affect the chargeability of spray droplets (Hao and Pratim Citation2021; Maski and Durairaj Citation2010; Mohammad-Reza and Jose Carlos Citation2021; Rubio et al. Citation2021).
Although high-voltage charging of droplets has been investigated in many studies, the effects of electrode materials and dimensions on droplet CMR are still not fully understood. The objectives of this study are to (1) quantify performances of various 304L stainless steel (304L SS), copper, and high-purity graphite electrodes in terms of spray droplet CMR, (2) quantify and model the combined effects of applied voltage, nozzle height, electrode material, and electrode diameter on CMR, and (3) Optimize the values of design factors and operating parameters to maximize CMR. The results of this study were intended to develop an electrostatic spray scrubber with high CMR values for potential high dust removal efficiency.
Materials and methods
Experimental setup
The experimental spraying system consisted of an 80° hollow cone spray nozzle (TX-VK6, TeeJet Technologies, Glendale Heights, IL), a pressure regulator, and a diaphragm pump (model SFDP1-013-100-22, Seaflo, Xiamen, China). A high voltage power supply (model AU-60R5-LC, Matsusada Precision, Kusatsu, Japan) was used to hold each electrode at negative voltages. An electrometer (model 6514, Keithley Instruments, Solon, OH) was connected via alligator clips to the wire mesh stretched across the top of the inner vat in the custom-built Faraday pail, while the outer vat was kept electrically grounded, electrically isolated from the inner vat, and separately connected to the electrometer, allowing the electrometer to measure the electric current passing between the inner vat collecting charged spray droplets and the grounded outer vat. The spray nozzle pressure was set to 0.3 MPa while the water mass flow rate ranged from 0.3843 to 0.4113 kg min−1, where the average flow rate was 0.4021 kg min−1. The error values were −4.21% to 2.52%, which can be considered as measurement deviation. Droplet size distribution data provided by the manufacturer suggested a volumetric median diameter (VMD) of 141 µm. A schematic diagram of the spraying system is shown in .
The electrode was positioned right underneath the spray nozzle aligned with the central vertical axis of the electrode. The vertical position of the nozzle could be adjusted up and down. The nozzle height (h) was defined as the vertical distance between the nozzle tip and the upper end face of the electrode (). Zero height was defined where the bottom of the nozzle tip coincided with the upper edge of electrode. The direction upwards from the nozzle was defined as the positive direction, and downwards as the negative direction.
Description of electrodes
To explore the effects of electrode material on droplet CMR, three different materials, namely 304L SS, copper, and graphite, were selected. Physical properties of the electrode materials are shown in . The density of graphite is about 1/4 of those of the metal materials, and its electrical resistivity is 13.7 and 571.4 times that of 304L SS and copper, respectively.
Table 1. Physical properties of the electrode materials.
To test the different dimensions of the electrodes, ring-shaped electrodes were designed with various thicknesses depending on mechanical properties of the electrode materials in order to maintain strength, rigidity, and stability throughout testing. The electrode shape might affect the performance of the electrode. Due to consideration of the symmetric pattern of a sprayer, electrodes with a ring shape were used to provide more uniform charges to all the droplets generated by the sprayer. Effects of the electrode diameter and position relative to the spray nozzle (i.e. nozzle height) on droplet charge were studied. The electrodes were assigned names that included the material from which the electrode was made. The dimensions of the tested electrodes, including inner electrode diameter (D) and electrode height (EH, the vertical distance from the bottom of the nozzle to the top of the electrode), are listed in , while a photograph of the ring electrodes is shown in . Droplet spray patterns and nozzle height affect the electrode diameter and height. The principles are to have strong electrical fields with smaller electrode diameters, prevent spray droplets impacting on to the electrode, and have a tall enough electrode to increase the droplet charge time without blocking the spray droplet expansion. For this study, we have conducted some preliminary experiments to determine the electrode diameter and height based on above principles for the selected nozzle, an 80° hollow cone spray nozzle (TX-VK6, TeeJet Technologies, Glendale Heights, IL), which can produce droplets with optimum sizes of 100–150 μm in terms of Sauter mean diameter identified in previous research for capturing poultry dust particles.
Table 2. The dimensions of the experimental electrodes.
Calculation of droplet charge and water characteristics
The CMRs of the charged droplets were calculated based on the current carried by droplets and the mass flow rate using EquationEquation 1(1)
(1) .
where CMR is the droplet charge-to-mass ratio (mC kg−1), m is the mass flow rate of sprayed droplets (kg min−1), and I is the measured current (µA).
For current measurement, each data sample lasted for 3 seconds, include at least 30 values of data. The average measurement within 3 seconds was taken as the display value. Six groups of data were recorded continuously, and the averages and errors were calculated.
The water flow rate, conductivity, and density were measured prior to starting each test. The water flow rate was calculated by measuring the amount of water ejected from the nozzle within 1 minute. Water conductivity was adjusted by starting with distilled water and adding NaCl until the water conductivity reached 0.05 S m−1, to simulate the electrical conductivity achieved by ordinary industrial water. The water conductivity was measured by a portable conductivity meter (Orion 3 Star Plus, Thermo Scientific, Waltham, MA). The conductivity of the liquid was measured at the beginning and end of the experiment to ensure the accuracy of the experiment. The mean water temperature was 18 ± 2°C and water density ranged from 1000.74 to 1006.13 kg m−3.
The achieved CMR values can be compared to the theoretical Rayleigh limit, which signifies the maximum possible amount of charge that a droplet can acquire before the electrical forces overcome surface tension, resulting in droplet breakup. EquationEquations 2(2)
(2) , Equation3
(3)
(3) , and Equation4
(4)
(4) were derived from Post and Roten (Citation2018) and define the theoretical Rayleigh limit, the associated theoretical maximum CMR, and the fraction of the Rayleigh limit that was achieved, respectively (Post and Roten Citation2018).
where qmax is the theoretical Rayleigh limit (C), ε0 is the vacuum permittivity constant (8.845 × 10−12 C2 s2 kg−1 m−3), σ is the surface tension of water against air (0.0730 kg s−2), d is the diameter of an individual droplet (m), m is the mass of an individual droplet (kg), ρ is the density of sprayed water (1003.4 kg m−3), FR is the achieved fraction of the Rayleigh limit in decimal form, CMR is the observed mean charge-to-mass ratio (C kg−1), and VMD is the volume median diameter of the sprayed droplets (m).
Experimental design
A reduced factorial design with four factors was used in this study to investigate how the CMR was affected by these factors. The four factors tested were electrode material, electrode diameter, nozzle height, and applied voltage (V). Electrode material was treated as a blocking factor in the experimental design and the water flow rate was treated as a known and uncontrollable nuisance factor, as the exact value of the water flow rate was not held constant to allow for natural variability. It is worth mentioning that, since the spray flow pattern of the nozzle is a hollow cone, the designed height of each ring electrode was chosen to meet the requirement that the spray droplets did not hit the bottom of the electrode and the effective installation height of the nozzle was not obstructed by the top of the electrode. The electrode height was thus considered a known and controllable potential nuisance factor. The upper ends of the applied voltage ranges for each electrode were each chosen to be the highest integer voltage at which neither sparkover nor flashover occurred. The testing conditions in the experimental design are listed in .
Table 3. The values of each factor tested in the experiment for each of the electrodes.
Statistical analysis
Data analysis was performed using JMP 13.1.0 software (SAS Institute, Cary, NC). All statistical tests, including Student’s t-tests and Tukey–Kramer tests, were completed using a significance level of 0.05. A standard least squares linear regression approach was used to develop a linear regression model to predict CMR from the applied voltage and nozzle height for the specific electrode exhibiting the greatest CMRs. The final linear regression model was loaded into the optimization module within JMP to determine the optimal values of these key parameters, i.e. the values of nozzle height and applied voltage that resulted in the highest predicted CMR. It should be noted that the primary purpose of the linear regression model is optimization of key parameter values to maximize CMR, not prediction of CMR values from given input parameter values.
Results and discussions
Effects of electrode material on CMR
To determine the effects of electrode material on observed CMR values, three electrodes, one each made of 304L SS, copper, and graphite, each with a height of 45 mm and an inner diameter of 100 mm, were tested across their respective ranges of applied voltages and nozzle heights. The reason why the graphite was be chose as the electrode, we found in experiments that copper and other metal materials are more prone to oxidation under the action condition of high voltage. Graphite is a nonmetallic material, with more stable chemical properties, so we take graphite as an object of study. The mean CMR values observed for the 304L SS, copper, and graphite electrodes were 0.268 ± 0.099, 0.255 ± 0.068, and 0.234 ± 0.117 mC kg−1, respectively (). From EquationEquations 2(2)
(2) and Equation3
(3)
(3) , it was found that the theoretical Rayleigh limit was 1.196 × 10−8 mC and the theoretical maximum CMR was 8.12 mC kg−1. Thus, the 304L SS, copper, and graphite electrodes achieved mean Rayleigh limit fractions of 3.30%, 3.14%, and 2.88%. However, as noted by Post and Roten (Citation2018), the achieved Rayleigh limit fractions rarely exceed 10% (Ahmed, Soban, and Ohyama Citation2014). Overall, the 304L SS electrode achieved a significantly greater (p < .05) CMR than either the copper or graphite electrodes.
Figure 3. Mean CMR values for electrodes (D = 100 mm, EH = 45 mm) of the three materials tested across their respective ranges of applied voltage and nozzle height, with the error bars denoting one standard deviation.
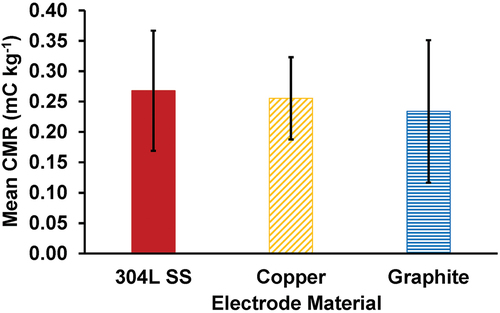
Of the three tested electrode materials, graphite was the least electrically conductive, likely contributing to the significantly lower observed CMR values for this material as compared to the more conductive materials of 304L SS and copper. Additionally, the inner surface of the graphite electrode was noticeably rougher than the other two electrodes, which may have also led to lower electric field strengths, due to the increased surface roughness lowering the corona onset voltage for the graphite electrode. Interestingly, although copper was more conductive than 304L SS, the 304L SS electrode exhibited a higher mean CMR than the copper electrode. This result differs from a previous study that reported copper electrodes achieving higher CMR values than stainless steel electrodes (Tessum and Raynor Citation2021). However, one possible explanation is the greater corrosion resistance of the 304L SS electrode compared to the copper electrode. The copper electrode was found to corrode easily () when sprayed water droplets landed on the inner surface of the electrode under high voltage loading, weakening the generated electric field (Shinato, Zewde, and Jin Citation2020). These findings suggest that of the three tested electrode materials, the best-performing and most practical material to achieve the highest CMR values is 304L SS.
Effects of electrode diameter on CMR
The designed height of each ring electrode was chosen to meet the requirement that the spray droplets did not hit the bottom of the electrode and the effective installation height of the nozzle was not obstructed by the top of the electrode. The effect of electrode height was preliminary tested only using the electrode with a diameter of 100 mm and no significant difference in CMR was detected with different electrode height. Therefore, electrodes with other sizes of diameters were only tested with one electrode height. The mean CMR values for the 304L SS electrodes of each tested inner electrode diameter are shown in . It should be noted that although 304L SS electrodes with diameters of 53.1, 150, and 200 mm were only tested at a single electrode height, two 304L SS electrodes with different electrode heights (10 and 45 mm) were tested with an inner diameter of 100 mm. The highest mean CMR (0.261 ± 0.088 mC kg−1) occurred at an electrode diameter of 100 mm, while the electrode diameter of 200 mm resulted in the lowest mean CMR (0.162 ± 0.044 mC kg−1). The electrodes with diameters of 53.1 and 150 mm exhibited mean CMR values of 0.232 ± 0.126 and 0.183 ± 0.051 mC kg−1, respectively.
Figure 5. Mean CMR values for 304L SS electrodes at each tested electrode diameter, with the error bars representing standard deviation.
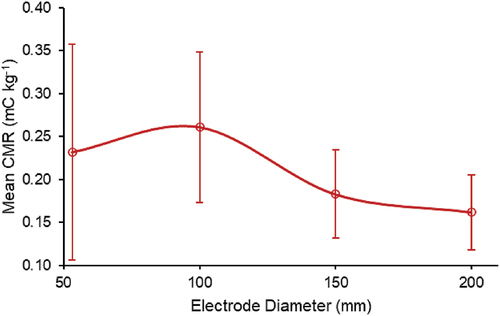
The mean CMR values achieved by the electrodes with diameters of 150 and 200 mm were not significantly different (p > .05), while the mean CMR achieved at an electrode diameter of 100 mm was significantly greater than at all other tested diameters (include the electrode with diameters of 53.1 mm) (p < .05). The 53.1 mm electrode is small in diameter and high in height, resulting in a stronger electric field. In comparison, 100 mm, 150 mm and 200 mm diameter electrodes generate electric fields with relatively low intensity and result in relatively weaker charging capacity. The 304L SS electrodes with a diameter of 100 mm and electrode heights of 10 and 45 mm exhibited mean CMR values of 0.255 ± 0.075 and 0.268 ± 0.099 mC kg−1, respectively, which were not significantly different (p > .05). The possible reason for this insignificance is that the small variation of the height (10–45 mm) limited by the nozzle spray pattern could not result in significant difference in droplet charging time considering the high speed of droplets, and then in turn could not cause significant difference in CMR. It can be seen from the data of CMR that, the difference of electric field formed by electrodes with different heights is small, indicating that the influence of electrode height within a range of 10–45 mm on CMR value was not significant. The standard deviations of CMR values decreased with increasing electrode diameter, suggesting that droplet charging stability was inversely related to electrode diameter. One possible explanation for this trend is the increased likelihood of sprayed droplets landing on the inner surface of smaller diameter electrodes, which would cause local disruptions to the electric field, adversely affecting the ability to impart charge to droplets (Almekinders et al., Citation1992; Gaunt et al. Citation2003).
Effects of applied voltage on CMR
The applied voltage is an important factor affecting the CMR. According to the literature, the CMR generally increases first and then decreases with the increase of the applied voltage, up to a certain point (Jaworek et al. Citation2006a). This same trend was observed in testing the two 304L SS electrodes with an inner diameter of 100 mm. For the electrode with a height of 10 mm, the mean CMR increased from 0.162 ± 0.048 mC kg−1 at an applied voltage of −5 kV to 0.307 ± 0.062 mC kg−1 at −13 kV. Beyond this voltage, the mean CMR values decreased, falling to 0.263 ± 0.048 mC kg−1 at −15 kV. For the electrode with a height of 45 mm, the mean CMR at −5 kV was 0.189 ± 0.078 mC kg−1, which increased up to a maximum observed value of 0.315 ± 0.099 mC kg−1 at −11 kV, then decreased down to 0.237 ± 0.069 mC kg−1 at −15 kV ().
Figure 6. Mean CMR values across the range of tested applied voltages for 304L SS electrodes (D = 100 mm) at two different electrode heights.
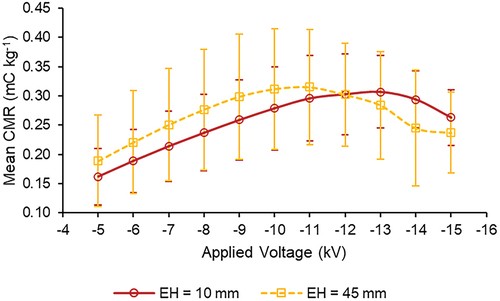
The reason for the increase of CMR with voltage was that as the voltage increased, the electric field intensity of the space where the electrode was located increased. As a result, the charge polarization of the Taylor cone and spray jet (before separation into distinct charged water droplets) was enhanced with increasing voltage, and the charge carried by the droplets then increased. As the voltage further increased, the air began to ionize due to the strengthened electric field intensity, forming corona, which exhibited a shielding effect via space charge, causing the droplets to become less charged. For the electrode with a height of 45 mm, the peak CMR occurred at an applied voltage of −11 kV, which means that the optimal applied voltage to maximize droplet charging for this electrode was around −11 kV. For the electrode with a height of 10 mm, the peak value of CMR occurred at −13 kV. This indicates that the electrode height can improve the electric field intensity between electrode and nozzle to a certain extent, which can reduce the peak voltage of CMR. Large electrode height enhances droplet charging process and therefore help to reach peak CMR with a relative low voltage.
Effects of nozzle height on CMR
Changing the applied voltage of the electrode can change the electric field intensity between the electrode and nozzle. However, the relative position of the electrode and nozzle, that is the installation height of the nozzle, is also an important factor affecting the electric field intensity between them.
The electric field intensity around the nozzle could be changed by changing the h value, which further influenced the droplet charge during spraying. As shown in , the nozzle and electrode served as the two poles of a capacitor, between which an electric field with intensity E was formed. Changing h values was done to change the distance between the two poles. The larger the distance, the smaller the charge Q of the capacitor and the smaller the charge density q of the electrode. As a result, the electric field intensity E around the nozzle would be smaller.
Figure 7. Graphic demonstration of the spray nozzle, electrode, nozzle height h, and continuous jet length L: (a) a photograph, and (b) a schematic.
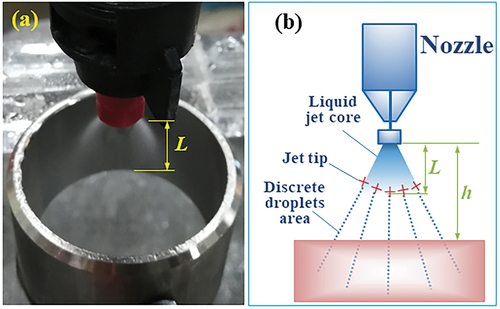
It was noticed that the initial segment of jet from the nozzle existed in the form of continuous jet (known as liquid jet core area, the length of continuous jet is defined as L shown in ). When this part of jet was exposed to the electric field, a large amount of positive charges would accumulate on the continuous jet tip (). When the continuous jet at the positively charged tip was separated into discrete droplets, the droplets would acquire a certain amount of positive charges. This is the basic principle of induction charging. Since the continuous jet had a certain length, higher CMR could be obtained if the continuous jet tip were placed where the electric field intensity was the highest.
The effect of nozzle height on observed CMR values was examined for the 304L SS electrode (D = 100 mm, EH = 45 mm) at the best-performing applied voltage of −11 kV and the nearby applied voltages of −10 and −12 kV (). As the nozzle height of −85 mm moved to −15 mm, CMR values increased, although the observed CMR values decreased as the nozzle height moved from −15 mm to 0 mm, level with the top of the electrode. The same trend occurred at all three of the applied voltages shown in . The lowest mean CMR values for −10, −11, and −12 kV all occurred at a nozzle height of −85 mm (0.147 ± 0.011, 0.158 ± 0.010, and 0.170 ± 0.012 mC kg−1, respectively). At a nozzle height of −15 mm, each voltage exhibited its highest mean CMR, with −12 kV achieving 0.419 ± 0.002 mC kg−1, −10 kV reaching 0.425 ± 0.004 mC kg−1, and −11 kV resulting in the highest observed mean CMR of 0.435 ± 0.002 mC kg−1, significantly greater (p < .05) than the CMR values observed for the other two applied voltages at the same nozzle height. These results suggest that for the 304L SS electrode with an inner diameter of 100 mm and an electrode height of 45 mm, the combination of an applied voltage of −11 kV and a nozzle height of −15 mm (i.e. positioning the tip of the nozzle 15 mm below the top of the electrode) resulted in the most effective spray droplet charging. These results are similar to those of a prior study (Post and Roten Citation2018).
Linear regression model and optimization for CMR
Observations of the testing data showed that the 304L SS electrode with an inner diameter of 100 mm and a height of 45 mm was able to achieve the highest CMR values. A more general linear regression model was developed using the data from all tested electrodes, regardless of material. However, this regression model was not presented in this study due to a low R2 value (0.12). This suggested that the electrode material played such an important role in determining the observed CMR values that linear regression models specific to each material should be developed. Therefore, a linear regression model was developed using a standard least squares approach to predict the CMR achieved by the 304L SS electrode with an inner diameter of 100 mm and a height of 45 mm. It should be noted that the linear regression model cannot be reliably applied to any 304L SS electrode with different dimensions than the one tested here. The reason for only including the linear regression model for the best-performing electrode in this study is that one of the main objectives of the study is to optimize the spray charging process to achieve the highest CMR values. If other variables (such as electrode material, electrode diameter, and electrode height) were to be included, the predictive power of the linear regression model would significantly decrease, which would be counterproductive to the optimization process.
A full factorial combination of these factors and their squares were included in the initial model, and all five terms were found to be statistically significant (p < .001). The linear regression model had an R2 value of 0.734 and a root mean square error of 0.0520, suggesting good correlation with observed CMR values. The final linear regression model is shown as EquationEquation 5(5)
(5) , while the dimensionless parameter estimates obtained through multivariate analysis of variance are shown in .
Table 4. Dimensionless parameter estimates and their standard errors from multivariate analysis of variance performed for the terms included in the linear regression model for CMR.
where CMR is the droplet charge-to-mass ratio (mC kg−1), h is the nozzle height (mm), and V is the applied voltage (kV).
The term with the largest effect on predicted CMR was the square of applied voltage, while the term with the second largest effect on CMR was the cross-effect between nozzle height and applied voltage. As applied voltages became increasingly negative, the predicted CMR values generally increased. However, as nozzle heights became more negative, the predicted CMR values showed a more complicated trend, as the effects of h caused the predicted CMR values to decrease while the effects of h2 caused the predicted CMR values to increase, suggesting that some optimal nozzle height exists to cause the effects of these terms to give higher predicted CMR values.
Optimization of the linear regression model suggested that a maximum predicted CMR of 0.360 mC kg−1 occurred at an applied voltage of −9.6 kV and a nozzle height of −19.5 mm. The closest combination of applied voltage and nozzle height tested for the modeled electrode was −10 kV and −22.5 mm, which resulted in an observed mean CMR of 0.412 ± 0.002 mC kg−1. However, the highest observed mean CMR of 0.435 ± 0.002 mC kg−1 actually occurred at an applied voltage of −11 kV and a nozzle height of −15 mm, still close to the predicted optimal set of parameters. Thus, despite the projected optimal combination of applied voltage and nozzle height from optimization of the linear regression model, it is recommended that the 304L SS electrode with an inner diameter of 100 mm and a height of 45 mm be operated at an applied voltage of −11 kV and a nozzle height of −15 mm to achieve a maximum CMR of 0.435 mC kg−1, representing an achieved Rayleigh limit fraction of 5.36% (Post and Roten Citation2018).
Conclusion
Among the three electrode materials tested, the 304L SS electrode achieved the highest mean CMR (0.268 ± 0.099 mC kg−1), while copper and graphite resulted in respective mean CMR values of 0.255 ± 0.068 and 0.234 ± 0.117 mC kg−1. Electrode diameter is an important factor affecting CMR. For the tested 304L SS electrodes, an inner diameter of 100 mm resulted in the highest mean CMR (0.261 ± 0.088 mC kg−1). The observed CMR values increased with electrode diameter from 53.1 to 100 mm, but decreased as the electrode diameters increased from 100 to 200 mm. Nozzle height significantly affects droplet CMR. The maximum mean CMR of 0.435 ± 0.002 mC kg−1 was achieved at a nozzle height of −15 mm for 304L SS electrode with an inner diameter of 100 mm and a height of 45 mm operated at the best-performing applied voltage of −11 kV.
A linear regression model for the best-performing electrode was developed to optimize the parameter values that would maximize CMR values. Optimization of the model suggested that a maximum CMR of 0.360 mC kg−1 would have occurred at an applied voltage of −9.6 kV and a nozzle height of −19.5 mm. However, this electrode exhibited its highest CMR of 0.435 mC kg−1 at an applied voltage of −11 kV and a nozzle height of −15 mm, suggesting these values as the optimal parameters. Given that the maximum theoretical CMR as determined by the Rayleigh limit would have been 8.12 mC kg−1, the CMR of 0.435 mC kg−1 observed using the optimal electrode configuration represents an achieved Rayleigh limit fraction of 5.36%.
Disclosure statement
No potential conflict of interest was reported by the author(s).
Data availability statement
The data that support the findings of this study are available from the corresponding author and can be shared upon reasonable request.
Additional information
Funding
References
- Ahmed, A., T. Soban, and R.-I. Ohyama. 2014. Experimental studies on influence of different conductivities on water mist charging with electrostatic induction. Annual Report Conference on Electrical Insulation and Dielectric Phenomena.
- Almekinders, H., H. E. Ozkan, D. L. Reichard, T. G. Carpenter, and R. D. Brazee. 1992. Spray deposit patterns of an electrostatic atomizer. Trans. ASAE 35 (5):1361–67. doi:10.13031/2013.28741.
- Almuhanna, E. A., R.G. Maghirang, J.P. Murphy, and L.E. Erickson. 2008. Effectiveness of electrostatically charged water spray in reducing dust concentration in enclosed spaces. Trans. ASABE. 51 (1):279–86. doi:10.13031/2013.24221.
- Almuhanna, E. A., A. H. Amer Eissa, A. O. Alghannam and A.M. Al-Amri. 2012. Optimization of dust removal in poultry houses using electrostatic wet scrubber. Res. J. Appl. Sci. 8 (12):5651–60.
- Balachandran, W., A. Jaworek, A. Krupa, J. Kulon and M. Lackowski. 2003. Efficiency of smoke removal by charged water droplets. J. Electrost. 58 (3–4):209–20. doi:10.1016/S0304-3886(03)00049-4.
- Chen, F., H. Chen, L. Zhang, S. Yin, S. Huang, G. Zhang, and Q. Tang. 2019. Controllable distribution of ultrafine diamond particles by electrostatic spray deposition. Powder Technol. 345:267–73. doi:10.1016/j.powtec.2019.01.019.
- Chenghang, Z., D. Dawei, C. Qianyun, S. Liu, Z. Yang, X. Liu, W. Weng and X. Gao.2019. Experiments on enhancing the particle charging performance of an electrostatic precipitator. Aerosol. Air Qual. Res. 19 (6):1411–20. doi:10.4209/aaqr.2018.11.0400.
- Di Natale, F., C. Carotenuto, L. D’Addio, A. Jaworek, A. Krupa, M. Szudyga and A. Lancia. 2015. Capture of fine and ultrafine particles in a wet electrostatic scrubber. J. Environ. Chem. Eng. 3:349–56.
- Gaunt, L. F., J.F. Hughes and N.M Harrison. 2003. Removal of domestic airborne dust particles by naturally charged liquid sprays. J. Electrost. 58 (3–4):159–69. doi:10.1016/S0304-3886(03)00044-5.
- Guo, S., and H. Xue. 2021. The enhancement of droplet collision by electric charges and atmospheric electric field, Atmos. Chem. Phys. 21:69–85.
- Hao, Z., and B. Pratim. 2021. The prediction of size and charge of particles formed from evaporation of charged droplets generated in an electrospray system. Chem. Eng. Sc.i 232:116237.
- Huang, S. H., and C. C. Chen. 2002. Ultrafine aerosol penetration through electrostatic preciptators. Environ. Sci. Technol. 36 (21):4625–32.
- Jaworek, A., W. Balachandran, M. Lackowski, J. Kulon, and A. Krupa. 2006a. Multi-nozzle electrospray system for gas cleaning processes. J. Electrost. 64 (3–4):194–202. doi:10.1016/j.elstat.2005.05.006.
- Jaworek, A., W. Balachandran, A. Krupa, J. Kulon, and M. Lackowski. 2006b. Wet electroscrubbers for state of the art gas cleaning. Environ. Sci. Technol. 40 (20):6197–207. doi:10.1021/es0605927.
- Jaworek, A., A. Krupa, A.T. Sobczyk, A. Marchewicz, M. Szudyga, T. Antes, W. Balachandran, F. Di Natale, and C. Carotenuto. 2013. Submicron particles removal by charged sprays. Fundamentals. J. Electrostat. 71 (3):345–50. doi:10.1016/j.elstat.2012.11.028.
- John Carroz, W., and N. Keller. 1978. Electrostatic induction parameters to attain maximum spray charge. Trans. ASAE 21 (1):63–69. doi:10.13031/2013.35251.
- Krupa, A., A. Jaworek, A. T. Sobczyk, A. Marchewicz, M. Szudyga, and T. Antes. 2013. Charged spray generation for gas cleaning applications. J. Electrost. 71 (3):260–64. doi:10.1016/j.elstat.2012.11.022.
- Kumar Patel, M., M. Kundu, H. Kumar Sahoo, and M. Kumar Nayak. 2016. Enhanced performance of an air-assisted electrostatic nozzle: Role of electrode material and its dimensional considerations in spray charging. Eng. Agric. Environ. Food 9 (4):332–38. doi:10.1016/j.eaef.2016.05.002.
- Lee, K., K.I. Lee, S.Y. Jeon, and S. Kim. 2019. Preparation of monodisperse charged droplets via electrohydrodynamic device for the removal of fine dust particles smaller than 10 mu m. Adv. Powder Technol. 30 (1):190–98. doi:10.1016/j.apt.2018.10.022.
- Manoj Kumar Patel, C. G., and P. Kapur. 2013. Characterization of electrode material for electrostatic spray charging: Theoretical and engineering practices. J. Electrost. 71 (1):55–60. doi:10.1016/j.elstat.2012.11.019.
- Marchewicz, A., A. T. Sobczyk, A. Krupa, and A. Jaworek. 2019. Induction charging of water spray produced by pressure atomizer. Int. J. Heat Mass Transf. 135:631–48. doi:10.1016/j.ijheatmasstransfer.2019.02.013.
- Maski, D., and D. Durairaj. 2010. Effects of electrode voltage, liquid flow rate, and liquid properties on spray chargeability of an air-assisted electrostatic-induction spray-charging system. J. Electrost. 68 (2):152–58. doi:10.1016/j.elstat.2009.12.001.
- Mohammad-Reza, P., and P. Jose Carlos. 2021. Numerical analysis of charged droplets size distribution in the electrostatic coating process: Effect of different operational conditions. Phys. Fluids 33 (3):033317. doi:10.1063/5.0041021.
- Penney, G. 1944. Electrostatic liquid spray precipitator. US. Patent No. 2357 354.
- Post, S. L., and R. L. Roten. 2018. A review of the effects of droplet size and flow rate on the chargeability of spray droplets in electrostatic agricultural sprays. Trans. ASABE 61 (4):1243–48. doi:10.13031/trans.12516.
- Ru, Y., L. Zhao, L. J. S. Hadlocon, H. Zhu, and S.K. Ramdon.2017. Laboratory evaluation of electrostatic spray wet scrubber to control particulate matter emissions from poultry facilities. Environ. Technol. 38 (1):23–33. doi:10.1080/09593330.2016.1184319.
- Rubio, M., S. H. Sadek, A. M. Ganan-Calvo, and J. M. Montanero. 2021. Diameter and charge of the first droplet emitted in electrospray. Phys. Fluids 33 (3):032002. doi:10.1063/5.0041428.
- Shinato, K. W., A. A. Zewde, and Y. Jin. 2020. Corrosion protection of copper and copper alloys in different corrosive medium using environmentally friendly corrosion inhibitors. Corros. Rev. 38 (2):101–09. doi:10.1515/corrrev-2019-0105.
- Teng, C., and J. Li. 2020. Experimental study on particle removal of a wet electrostatic precipitator with atomization of charged water drops. Energy & Fuels 34 (6):7257–68. doi:10.1021/acs.energyfuels.0c00646.
- Teng, C., and J. Li. 2021. Performance of reduction on particle emission by combining the charged water drop atomization and electric field in wet electrostatic precipitator. Process Saf. Environ. Prot. 155:543–54. doi:10.1016/j.psep.2021.09.035.
- Tessum, M. W., and P. C. Raynor. 2021. Measuring electrostatic charge on pneumatically generated spray drops. J. Aerosol. Sci. 151:105691. doi:10.1016/j.jaerosci.2020.105691.
- Wang, B., H. Liu, Z. Chunlai, H. Huo, K. Dong, and Y. Jiang. 2020. Enhancing the collection efficiency of a gas cyclone with atomization and electrostatic charging. Powder Technol. 364:562–71.
- Wang, J., Y. Sun, M. S. M. Xiaodan Gao, and B. Wilhite. 2019. Experimental study of electrostatic hazard inside scrubber column using response surface methodology. Chem. Eng. Sci. 200:46–68. doi:10.1016/j.ces.2018.12.060.
- Xiang, X. D., and I. Colbeck. 1997. Charged water drops and smoke dissipation. Fire Saf. J. 28 (3):227–32. doi:10.1016/S0379-7112(96)00080-X.
- Xiao, D., X. Li, W. Yan, and Z. Fang. 2019. Experimental investigation and numerical simulation of small-volume transverse-flow air curtain performances. Powder Technol. 352:262–72.
- Xiaochuan, L., X. Xinhao, M. Zhang, and Y. Jiao. 2019. Column dust scrubber based on the orifice plate to intensify the gas-liquid mixing. Chem. Eng. Technol. 42 (11):2302–09. doi:10.1002/ceat.201800685.