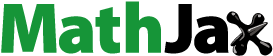
ABSTRACT
Modern people spend more and more time in cars in their daily lives, and the pollution of formaldehyde in the car may directly affect people’s health. Thermal catalytic oxidation technology by solar light is a potential way to purify formaldehyde in cars. MnOx-CeO2 was prepared by the modified co-precipitation method as the main catalyst, and the basic characteristic (SEM, N2 adsorption, H2-TPR, UV-visible absorbance) were also analyzed in detail. The experimental study was set up to simulate the solar photothermal catalysis of formaldehyde in-car environment. The results showed that the higher the temperature in the experimental box (56.7 ± 0.2°C, 62.6 ± 0.2°C, 68.2 ± 0.2°C), the better the formaldehyde degradation by catalytic effect (formaldehyde degradation percentage: 76.2, 78.3
, 82.1
). With increase of the initial formaldehyde concentration (200
, 500
, 1000
), the catalytic effect first increased and then decreased (formaldehyde degradation percentage: 63
, 78.3
, 70.6
). The catalytic effect risen gradually with the increase of load ratio (10
, 20
, and 40
), and the formaldehyde degradation percentages were 62.8
, 78.3
, and 81.1
, respectively. According to the expressions of the Eley-Rideal (ER) model, the Langmuir-Hinshelwood (LH) model, and the Mars-Van Krevelen (MVK) model, the experimental results were fitted and verified, and it was found that the ER model had a high degree of fit. It is more suitable to explain the catalytic mechanism of formaldehyde by MnOx-CeO2 catalyst in the experimental cabin, where formaldehyde is in the adsorption state and oxygen is in the gas phase.
Implications: Judging from the current research status, vehicles have become an indispensable mode of travel for people, and the air quality in the vehicle is not optimistic. Most vehicles generally have the phenomenon of excessive formaldehyde. The characteristic of formaldehyde in the car is the continuous release, especially in the hot summer, the temperature inside the car rises sharply under the sun radiation. At this time, the formaldehyde concentration exceeds the standard by 4 to 5 times, which can cause great damage to the health of the passengers. In order to improve the air quality in the car, it is necessary to adopt the correct purification technology to degrade formaldehyde. The problem brought by this situation is how to effectively use solar radiation and high temperature in the car to degrade formaldehyde in the car. Therefore, this study uses the thermal catalytic oxidation technology to catalyze the degradation of formaldehyde in the high temperature environment of the car in summer. The selected catalyst is MnOx-CeO2, mainly because manganese oxide (MnOx) itself is the most effective catalyst for volatile organic compounds (TCO) among transition metal oxides, and CeO2 has excellent oxygen storage and release capacity and Oxidation activity, which helps to improve the activity of MnOx. Finally, the effects of temperature, initial concentration of formaldehyde and catalyst loading on the experiment were explored, and the kinetic model of thermal catalytic oxidation of formaldehyde with MnOx-CeO2 catalyst was analyzed to provide technical support for the future application of this research in practice.
Introduction
Nowadays, vehicles have become an indispensable way for people to travel, and most of the air quality problems in cars are poor. Among them, formaldehyde pollution in cars cannot be ignored. Formaldehyde is a toxic air pollutant and is known to cause cancer (Kumar, Rattan, and Prasad Citation2015). China’s national standard stipulates that the formaldehyde in the car should not exceed 0.1 (Ministry of Ecology and Environment of the People’s Republic of China, Citation2011). While the formaldehyde concentration is in the range of 0.06
~ 0.07
, infants may develop mild asthma (Hao et al. Citation2021; Tang et al. Citation2009; Ye et al. Citation2007). Numerous studies have shown that long-term exposure to high concentrations of formaldehyde can cause serious pathological effects on human health, including skin and mucous membrane irritation, nasal tumors, chronic bronchitis, respiratory dysfunction, hepatotoxic damage, and even cancer (Jiang et al. Citation2017; Hu et al. Citation2020; Zhu et al. Citation2018). Lower concentrations of formaldehyde can also irritate the eyes and airways of humans (Chen et al. Citation2015; Guo et al. Citation2018; Kumar, Rattan, and Prasad Citation2015).
Formaldehyde solvents are widely used in chemical adhesives for construction, decoration industries, and automotive interior furniture products. As a typical volatile organic compound (VOCs), it is easy to be continuously released into the environment (Guo et al. Citation2018; Zhu et al. Citation2020). The temperature has a great influence on the release of formaldehyde. The formaldehyde concentration increases synchronously with the increase in temperature and decreases synchronously with the decrease in temperature, and there is a strong positive correlation (Chen et al. Citation2019). The indoor air formaldehyde concentration and indoor temperature basically conform to the exponential relationship (Chen et al. Citation2019; Deng, Yang, and Zhang Citation2009; Zhang et al. Citation2007; Huang, Xiong, and Zhang Citation2015). Therefore, in hot summer, due to solar radiation, the temperature inside the car rises sharply, the average temperature can reach 53°C, and the maximum temperature can reach more than 70°C, which can accelerate the release of formaldehyde in the car (Hou Citation2017).
To solve the problem of air pollution caused by formaldehyde, a large number of researchers have studied the purification of formaldehyde from both experimental and theoretical aspects. At present, the most popular experimental formaldehyde purification technologies are adsorption, plasma, photocatalytic oxidation (PCO), and thermal catalytic oxidation (TCO) (Hu et al. Citation2020). Adsorption can remove most of the volatile organic compounds in the environment, but there are disadvantages such as limited adsorption capacity, easy desorption to form secondary pollution, and difficult regeneration and formaldehyde cannot be satisfactorily removed by pure adsorbent media (Pei and Zhang Citation2011); plasma formaldehyde oxidation technology has poor performance at low concentrations and may produce harmful by-products, which has great limitations (Xing et al. Citation2011); photocatalytic oxidation technology can directly use sunlight as an activation catalyst and drive redox reactions, which is an ideal with low energy consumption technology (Armaroli and Balzani Citation2007). TiO2 is currently the most widely studied photocatalyst for VOCs treatment, but its band gap is wide, and it only responds to ultraviolet light, which limits the use of sunlight to a large extent (Yu et al. Citation2020; Yu et al. Citation2019); thermal catalytic oxidation technology is to supply energy through heating The method relies on the catalyst to oxidize and decompose formaldehyde, so that the gas is purified, and has the advantages of low operating temperature and no harmful by-products (Xu et al. Citation2017). Among them, the room temperature catalytic oxidation method is a kind of thermal catalytic oxidation method, which can realize the catalytic degradation of formaldehyde at room temperature, with low energy consumption and good application prospects (Liu and Huang Citation2020).
In addition, researchers at home and abroad have also proposed photothermal catalytic treatment technology, which uses solar energy storage and conversion to drive reactions to achieve low-energy VOCs treatment (Li et al. Citation2020). But it is basically still in the experimental research stage, and the main scientific problem currently facing is how to achieve the maximum utilization of sunlight. Studies have shown that loading precious metals can effectively improve the utilization of sunlight because precious metals have excellent local plasmon resonance thermal effects and high catalytic activity (Cai et al. Citation2018; Meng et al. Citation2016); noble metal nanoparticles also have strong light-matter interaction characteristics (Li et al. Citation2016; Li et al. Citation2010). But precious metals are expensive, and large loads will increase investment costs. From the perspective of economic benefits, transition metal oxides are a good choice. Manganese oxides can exhibit efficient catalytic activity under sunlight, in addition to following the sunlight-driven thermos catalysis mechanism, there is also the existence of a photoactivation effect (Yang et al. Citation2017; Yang et al. Citation2018). In addition, manganese oxide (MnOx) itself is the most effective catalyst for the volatile organic compound TCO among transition metal oxides and is widely used in the oxidation of HCHO (Wei et al. Citation2019; Xu et al. Citation2017). But MnOx usually requires higher temperatures to fully decompose formaldehyde (Pei and Zhang Citation2011). So the researchers tried to increase the activity of the catalyst through elemental incorporation. CeO2 is often used as the active component or carrier of catalysts due to its excellent oxygen storage and release capacity and oxidation activity. It helps to improve the activity of MnOx and reduce its complete catalytic temperature (Wang, Yeung, and Banares Citation2020). Tang et al found that MnOx-CeO2 prepared by a modified co-precipitation method can completely convert 580 formaldehyde at 100°C. If promoted by Pt, MnOx-CeO2 catalyst can completely convert formaldehyde to CO2 and H2O at 25°C (Tang et al. Citation2008; Tang et al. Citation2006). Later, Zhu et al. prepared a cerium-modified hydrated birnessite-type manganese oxide, and completely converted HCHO (190
) at 100°C (Zhu et al. Citation2017). Based on the above research and based on factors such as temperature and light intensity in the car in summer, it is very suitable to use MnOx-CeO2 to purify formaldehyde in the car. Therefore, the improved co-precipitation method was used in this study to prepare the MnOx-CeO2 catalyst for experimental study (Tang et al. Citation2008). The UV-visible absorbance test (UV-visible absorbance), H2 temperature programmed reduction (H2-TPR), SEM, and N2 adsorption were carried out on MnOx-CeO2 to analyze the light absorption capacity, structure, and redox properties of the catalyst.
The idea of this study is to use solar energy as the energy source and use the thermal catalytic oxidation technology to catalyze the degradation of formaldehyde in the high-temperature environment in summer vehicles. Its advantages lie in purifying formaldehyde on the premise of reducing energy consumption, reducing costs, producing no secondary pollution, and sustainable purification. Therefore, we also need to consider the influence of environmental factors on the catalytic effect of formaldehyde. The main environmental factors involved are temperature, concentration, humidity, and speed (wind speed). For the effect of temperature, researchers have basically agreed that the higher the temperature, the higher the conversion efficiency of formaldehyde (Chuang, Zhou, and Tong Citation1994; Peng and Wang Citation2007); for the concentration, Peng et al. (Citation2007) studied the formaldehyde concentration at three levels of 100, 240
and 400
The conversion rates at room temperature were 41.5
, 33.1
and 22.7
, respectively. It can be seen that the conversion rate is higher at low concentrations (Peng et al. Citation2007). Xu et al. also obtained similar conclusions (Xu et al. Citation2011), which are different from our experimental results. It may be caused by the different experimental environments and concentration selection. Due to the limitation of experimental equipment, we did not do experiments on speed and humidity, but we studied the effect of catalyst loading on the catalytic effect of formaldehyde and found that with the increase of loading, the catalytic effect became better and better, but the improvement was not significant.
In addition, exploring the reaction mechanism of formaldehyde catalytic oxidation can provide a deeper understanding of the performance of MnOx-CeO2 catalysts in the catalytic oxidation of formaldehyde in vehicles. Three models can generally describe the current mechanism of catalyst oxidation of VOCs: Langmuir-Hinshelwood (L-H) model, Eley-Rideal (E-R) model, and Mars-Van Krevelen (MVK) model. For L-H model, formaldehyde molecules and oxygen molecules compete for adsorption at the active points on the surface of the catalyst, and the adsorption or desorption rate is much higher than the reaction rate, and the surface reaction may dominate the adsorption process. For E-R model, monatomic state is involved in the reaction process. One of the formaldehyde or oxygen is adsorbed to form a solid solution with the catalyst, and then reacts with the other molecule in the gas state. As for MVK model, when the temperature rises to a certain extent, the adsorbed formaldehyde molecules react with the lattice oxygen on the catalyst to generate carbon dioxide and water, and the oxygen in the air is supplemented by the lattice oxygen in the catalyst, so the cycle reaction (Pei, Zu, and Yi Citation2015; Pei and Zhang Citation2011; Xu et al. Citation2017). Xu et al. believed that the bimolecular L-H model could better describe the decomposition of formaldehyde by Pt/MnOx-CeO2 catalysts (Xu et al. Citation2011); Wang et al. believed that the catalytic oxidation of formaldehyde generally conforms to the MVK model (Wang et al. Citation2015). Therefore, the effectiveness of each mechanism depends to a large extent on the properties of the catalysts (active metals and supports) and the properties of the VOCs molecules, and it is difficult to generalize (Xu et al. 2015).
In this study, the experimental results were fitted with the mechanism model of catalytic oxidation of VOCs and a suitable mechanism model for the MnOx-CeO2 catalyst to catalyze the oxidation of formaldehyde in the vehicle was found. It provides theoretical support for the practical application of formaldehyde purification in vehicles in the future.
Experimental materials, devices, and methods
Preparation of catalyst
Tang found that a MnOx-CeO2 catalyst prepared by modified co-precipitation showed the highest catalytic activity in catalytic formaldehyde oxidation, its manganese ions had a higher valence state, and it had more lattice oxygen species (Tang Citation2006). In this study, we prepared a certain amount of KMnO4 solution (analytical reagent, molecular weight 158.3, Tianjin Chemical Reagent Supply and Marketing Company), Mn(NO3)3-6 H2O solution (molecular weight 287.4, Afaisha (China) Chemical Co., Ltd.) and Ce(NH4)2(NO3)6 solution (index 99%, molecular weight 548.22, Shanghai Minrell) in a molar ratio of 3:2:5, respectively. and the three solutions were fully mixed. During the stirring process, 2 potassium KOH solution(Analytical Reagent, molecular weight 56.11, Tianjin Yuanli Chemical Co., LTD.) was gradually dropped into the solution until the pH was 10.5. The temperature of the mixed solution was controlled at 50°C, and the brown precipitate was stirred and aged for 2
with a constant temperature heating agitator (DF-101S, Stirring speed: stepless speed regulation 0–2600 rpm, temperature control range: room-400°C, manufacturer: Shanghai Lichen Bangxi Instrument Technology Co., Ltd., China). After filtering and washing, the brown precipitate was placed in an air-blowing drying oven (101–2, drying temperature: 30–250°C, manufacturer: Beijing Beifang Lihui Test Equipment Co., Ltd., China), where it was dried at 110°C for 12
to remove moisture. Finally, the brown precipitate was placed in a muffle furnace (YTH-2.5-10, heating temperature: room-1000°C, manufacturer: Huawei Ketron (Wuhan) Technology Co., Ltd., China) and calcined at 500°C for 6
to obtain a black solid MnOx-CeO2 catalyst.
Experimental devices
MnOx-CeO2 was characterized by a Quanta FEG 250 field emission scanning electron microscope (SEM) (acceleration voltage: 200–30
, beam: max. 200
and continuously adjustable, magnification: 14
–1,000,000
, manufacturer: American FEI), McAsap2460 (pressure range: 0–1000
test range: 0.35–500
, manufacturer: Micromeritics Instruments Corp. American), UV-3600 Plus (wavelength range: 190–2600
, manufacturer: Shimadzu, Japan) and McAutochem II 2920 (maximum temperature of heating electric furnace 1200°C, online mass spectrometry: mass number range 1–200
, manufacturer: Micromeritics Instruments Corp. American).
An environmental test chamber method was adopted as shown in , which is mainly composed of formaldehyde generator (FSQ-JQ-003 intelligent gas generator, flow range: 1–5, preheating temperature 60–80°C, formaldehyde cracking temperature 160°C, manufacturer: Suzhou Shengyuan Purification Equipment Co., Ltd., China), experimental chamber (5 mm thick transparent tempered glass, SUS304 stainless steel material with 2
thickness for the rest of the wall, length, width and height dimensions are
), formaldehyde detector (InterScan 4160 formaldehyde analyzer, range: 0 ~ 1000
, delay time: <1
, manufacturer: Interscan corporation, American), solar radiation meter (TBQ-2-SL, measurement range: 0 ~ 2500
, resolution: 1
, manufacturer: Shanghai Minyi electronics Co., Ltd, China), HOBO U12-012 temperature sensor (measuring range: −20 ~ 70°C, humidity 5
–95
RH, manufacturer: Onset, USA), solar radiation simulation system (Osram ULTRA-VITALUX light source lamp, power: 300W; quartz discharge tube; tungsten wire), and other components.
Figure 1. Experimental system diagram for formaldehyde purification performance testing 1. Formaldehyde generator; 2. Three-way valve; 3. Solar simulator; 4. Experimental cabin; 5. Stirring fan; 6. Catalyst carrier; 7. Catalyst; 8. Glass wall surface; 9. Formaldehyde detector; 10. Temperature sensor; 11. Vacuum pump; 12. Detection.
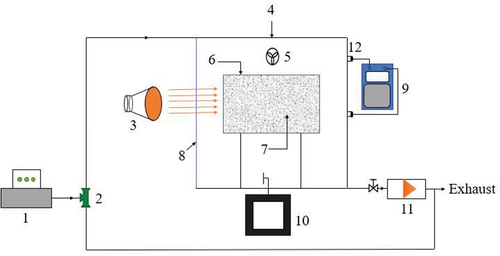
The test was conducted as following process: (1) Preparation of the catalyst film, the glutinous rice glue was first evenly coated on a square stainless steel sheet plate of 0.25 m2, and the powder of catalyst was uniformly sprayed onto the plate, after that dried the plate at 50°C for 1 hour. (2) Setup of test chamber, the pump was turned on for 30 minutes to clean the chamber, and the catalyst film was fixed up in the center of the experimental chamber. Use the temperature control system to control the ambient temperature at about 18°C. Turned on the solar radiation simulator and set the radiation intensity required for the experimental conditions. Make light radiation on the catalyst on the carrier surface, and the temperature change in the chamber was recorded. (3) Generation of formaldehyde, Start the formaldehyde generator generation function, and open the stirring fan for a short time so that the target concentration of formaldehyde is in the experimental chamber after closing the formaldehyde generator. (4) Detection of formaldehyde, after the temperature in the experimental chamber reached in a stable state, the formaldehyde detector was connected to the gas detection port in the experimental chamber, and the concentration of formaldehyde was recorded in every 10 minutes.
The solar simulation system consists of OSRAM ULTRA-VITALUX UV special light source lamps with built-in reflectors (simulate sunlight), quartz discharge tubes, and tungsten filaments to generate mixed radiation. The lamps were arranged in the array of three by three, and the range interval is 200 mm. The effective radiation area can reach up to 3.24 m2 (1.8 m X 1.8 m), and the radiation intensity per unit area is controllable at 50–1200w/m2. shows the spectral radiant power distribution of the ULTRA-VITALUX lamp.
Test data analysis method
Introduction to experimental methods
Formaldehyde degradation percentage
In the experimental process of formaldehyde catalysis, the influence of the self-decay rate of formaldehyde on the experimental results should be considered. The measured decay of formaldehyde can be used in the modified formula for calculating the degradation percentage.
In the process of the self-attenuation experiment, the change in formaldehyde concentration over time conforms to the trend of an exponential function, which is expressed in the form of EquationFormula (1)(1)
(1) :
where : formaldehyde concentration in the experimental chamber at time
,
;
: initial concentration of formaldehyde in the experimental chamber at time 0,
;
: attenuation constant,
; and
: time,
.
Taking the logarithmic transformation of both sides of EquationFormula (1)(1)
(1) , its logarithmic equation is:
Supposing that the volume of the laboratory chamber is ; then, the decay amount of formaldehyde is:
The formaldehyde degradation percentage is adopted as the index, and the degradation percentage is modified according to the natural decay amount of formaldehyde in the self-attenuation experiment, as shown in EquationEquations (4)(4)
(4) :
: formaldehyde degradation percentage;
: formaldehyde concentration at the initial time,
;
: formaldehyde concentration at time t,
;
: formaldehyde self-attenuating concentration,
.
The average reaction rate of formaldehyde
In this paper, a ten-minute time step is used as a reaction period, and the average reaction rate of formaldehyde in different periods is calculated, and the formula is:
In the formula, : average reaction rate per unit of BET specific surface area,
;
: volume in the experimental chamber, m3;
: difference in formaldehyde concentration, ppb;
: catalyst mass, g;
: reaction time, s;
: the specific surface area of the catalyst per unit mass m2/g (from the BET results, the specific surface area of the catalyst is about: 3.4 m2/g).
Introduction to model analysis methods
In the formulation of catalytic reaction theory, kinetic calculations must be performed as the ultimate goal. Formaldehyde is a kind of VOC, and some scholars have found that the greater the molecular weight of VOCs, the less easily they are oxidized (Xu et al. Citation2017). Rui et al. found that at a certain reaction temperature, when a catalyst is used to catalyze the oxidation of some organic matter, the main products are CO2 and H2O, and much heat is released (Rui and Ji Citation2018). The reaction process conforms to EquationFormula (6)(6)
(6) below:
At present, there are three widely used gas-solid interaction models for volatile organic compounds, namely, the ER model, LH model, and MVK model.
(1) MVK model
The reaction mechanism of the MVK model is that when the temperature rises to a certain level, the adsorbed reactant molecules react with the lattice oxygen on the catalyst to generate carbon dioxide and water, and the oxygen in the air is supplemented by the catalyst to form lattice oxygen (Pei and Zhang Citation2011). The expression for the reaction rate r is as follows:
Combining oxygen concentration into
, a simple model can be obtained:
Where is the formaldehyde concentration at different moments,
;
is the reaction rate constant,
;
is the constant of MVK model,
.
After simplifying the above integral:
(2) LH model
The reaction mechanism of the LH model is that two gas-phase reactants in the adsorbed state react chemically on the surface of the catalyst. In the kinetic study of the thermal catalytic oxidation of formaldehyde, the bimolecular competitive reaction is the main research object (Li Citation2007). The reaction rate equation is (Pei, Xu, and Yi Citation2015):
In practical experiments, the oxygen concentration and oxygen adsorption constant
in the above equation are constants, and these two constants are combined into the other parameters to obtain a simplified model:
where is the apparent rate constant,
;
is the apparent formaldehyde adsorption equilibrium constant,
;
is the formaldehyde concentration at different moments,
.
(3) ER model
The ER model mechanism is a reaction between a substance in an adsorbed state and another substance in a gaseous state. Assuming that the formaldehyde molecules adsorbed on the surface of the catalyst react with oxygen in the gaseous phase, the chemical reaction rate r is expressed as (Bedia et al. 2009):
Since the reaction rate formula involves the concentration of oxygen, the oxygen content in the air is basically unchanged in the actual experiment, which can be regarded as a constant. By combining its into k, a simplified model that only considers the single parameter of formaldehyde concentration can be obtained:
where is the apparent rate constant of the formaldehyde thermal catalytic reaction,
;
is the Langmuir adsorption constant,
;
is the formaldehyde concentration at different times,
Integrate and simplify the above equation to get:
Result analysis
Characterization results and analysis of catalyst
UV-visible light absorbance test
A (absorbance) is an important parameter to measure the ability of a solution or solid to absorb light. Its formula is A = lg(1/T), 1 represents the incident light intensity, and T represents the projected light intensity. In the formula, only T cannot be greater than 1, and it has nothing to do with A. When the absorbance exceeds 1, it means that more than 90% of the light intensity is absorbed by the sample. Overall, the absorbance of 1 is a critical value. It can be seen from that the MnOx-CeO2 catalyst has a very high absorbance in the wavelength range of 200–1000 nm. In the wavelength range of 1000–1500 nm, the absorbance showed a decreasing trend, but even at 1500 nm, the absorbance was still greater than 0.5. At 1800 nm, there is a serious fluctuation in the data, which is due to switch the light source for the near-infrared light during the test. In addition, the MnOx-CeO2 catalyst exhibits good light absorption characteristics in the wavelength range of 200–2500 nm (the radiation wavelength received on the ground is mainly concentrated in the range of 0.295–2.5 μm), and the average absorbance is about 0.8. Therefore, the catalyst has an ideal light absorption capacity, and the catalyst surface can reach a higher catalytic temperature under the action of solar radiation when purifying formaldehyde, thereby stimulating the catalytic activity, and maintaining a high formaldehyde catalytic efficiency.
Hydrogen temperature-programmed reduction (H2-TPR) test
It can be seen from that there are a weak reduction peak around 420°C and a strong reduction peak at 480°C. The low-temperature reduction peak indicates that Mn2O3 or MnO2 is reduced to Mn3O4, and the high-temperature reduction peak indicates the reduction of Mn3O4 to MnO and the reduction of surface Ce4+/Ce3+ (Kapteijn et al. Citation1994; Tang et al. Citation2008; Tang et al. Citation2006). Pure CeO2 generally has two reduction peaks in the process of H2 reduction, which are the high-temperature reduction peak at 820°C and the low-temperature reduction peak at 500°C. The H2-TPR spectrum of pure MnOx has two overlapping strong reduction peaks between 360°C and 570°C, representing a typical two-step reduction process. Comparing to CeO2 and MnOx, it can be seen that the reduction peak temperature of MnOx-CeO2 is lower, which is because there is a strong interaction between CeO2 and MnOx during the preparation process of the catalyst. CeO2 can store oxygen and can provide oxygen to MnOx to improve the oxidation state of manganese ions. The valence of manganese ions plays a crucial role in the catalytic activity of the MnOx-CeO2 catalyst. The higher the valence, the stronger the redox ability and the better the catalytic formaldehyde effect. For the MnOx-CeO2 catalyst in this experiment, the valence of manganese ions is generally greater than +3, and has a strong redox ability.
SEM characterization results
is a scanning electron microscope image of the MnOx-CeO2 catalyst magnified 20,000 times and 50,000 times. As seen from the figure, the catalyst presents a massive coral-type structure with irregular size and shape, and obvious textural phenomena can be observed. In addition, its structure is relatively loose, and a good pore structure is formed between the active particles. However, it should be noted that we did not find abundant microporous structures in the SEM images, which may result in the catalyst not having a high specific surface area, which may be related to the grinding process of the catalyst powder.
BET characterization results analysis
is the nitrogen adsorption and desorption isotherm curve of the MnOx-CeO2 catalyst at a temperature of 77.2°C. It can be seen from the figure that with the increase of the relative pressure, the adsorption and desorption of nitrogen gas gradually increased. There is an obvious hysteresis loop between the relative pressures of 0.5–0.98, caused by capillary condensation during the adsorption process in part of the mesoporous structure.
shows the results of the BET-specific surface area, pore volume, and average pore size of the MnOx-CeO2 catalyst. It can be seen that the specific surface area is small, and the pore structure is not developed, which is related to the preparation method of the catalyst and the grinding degree of its powder. Unlike activated carbon, the more developed the pore structure is, the stronger the physical adsorption effect is, the formaldehyde thermos-catalyst is chemically catalytic, so the physical structure of the catalyst is not a decisive factor in the catalytic performance of formaldehyde.
Table 1. Specific surface area, pore volume, and average pore diameter of the MnOx-CeO2 catalyst.
Influence of various factors on the thermal catalytic oxidation of formaldehyde
Experimental conditions
We measured the temperature inside the car in Tianjin in July, August, September, and October, and found that the highest temperature reached 78.6°C, 70.2°C, 62.97°C, 55.1°C, and the strongest radiation intensity was 602.56 w/m2, 574.84 w/m2, 560.23 w/m2 and 473.31 w/m2. Therefore, the solar radiation intensities we set are 450 w/m2, 550 w/m2, and 650 w/m2, respectively, and the corresponding temperatures are 56.7 ± 0.2°C, 62.6 ± 0.2°C, and 68.2 ± 0.2°C. According to the survey, the common formaldehyde concentration that exceeds the standard is generally 5–6 times the national standard value (0.1 mg/m3). To be closer to the actual formaldehyde concentration in the car, this paper uses three different concentrations of 200 ppb, 500 ppb, and 1000 ppb for experimental research. Since the 0.5 × 0.5 m stainless steel was used as the carrier in this study, if the catalyst loading is too small, the catalytic efficiency of formaldehyde will not be ideal, and if it is too large, the catalyst will easily fall off. After testing, 10 g/m2, 20 g/m2, and 40 g/m2 are the most suitable loads in this experiment.
In this study, a ten-minute step was used as a reaction cycle, with a total of 30 cycles, and the formaldehyde degradation percentage and average reaction rate in different cycles were calculated. The test conditions are shown in .
Table 2. Experimental condition table.
Analysis of experimental results
It can be seen from that the formaldehyde catalytic effect of the MnOx-CeO2 catalyst is significantly affected by the temperature, and the formaldehyde catalytic effect is gradually enhanced with the increase in temperature. After 5 hours of the experiment under the conditions of initial formaldehyde concentration of 500 ± 5 ppb and catalyst loading of 20 g, the degradation percentages of formaldehyde at 68.2 ± 0.2°C, 62.6 ± 0.2°C and 56.7 ± 0.2°C were 82.1%, 78.3%, and 76.2%, respectively. In the experiment of 68.2 ± 0.2°C, formaldehyde concentration finally stabilized at about 70 ppb, has been lower than the national standard GB/T 27630-2011 standard value of 0.1 mg/m3. In addition, the concentration of formaldehyde at 62.6 ± 0.2°C and 56.7 ± 0.2°C finally stabilized at about 90 ppb and 99 ppb. It is not difficult to see that with the increase in catalytic temperature, the degradation percentage of formaldehyde gradually increased, and the residual concentration of formaldehyde after degradation gradually decreased. Huang et al. (Citation2018) used potassium permanganate and cerium nitrate as raw materials and prepared Mn-Ce-O materials with different Mn/Ce molar ratios at 500°C. The environmental chamber method was used, the initial concentration of formaldehyde was 1 mg/m3, and the formaldehyde was catalyzed at room temperature for 48 hours. It was found that when the Mn/Ce molar ratio was 1:4 and 4:1, the formaldehyde conversion was 92.1% and 91.2%, respectively (Dave, Sirach, and Deshpande Citation2022; Huang et al. Citation2018). Overall, the MnOx-CeO2 catalyst indicates good performance in the purification of formaldehyde in the high-temperature environment in summer vehicles.
Figure 7. Reaction rate of MnOx-CeO2-catalyzed formaldehyde at different temperatures, concentrations and loadings.
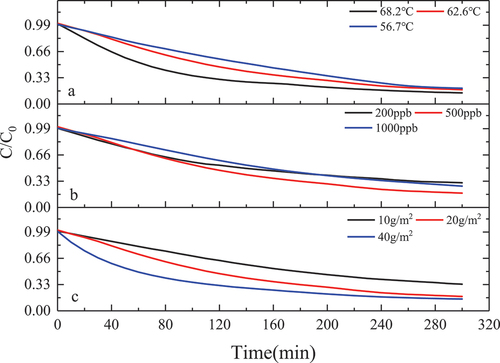
It can be seen from that in the experiments with initial concentrations of 200 ppb, 500 ppb, and 1000 ppb, the formaldehyde degradation percentages were 63%, 78.3%, and 70.6% after the experiment was performed for 5 hours under the conditions of solar radiation intensity of 550w/m2, stable temperature of 62.6 ± 0.2°C in the experimental chamber, and catalyst loading of 20 g. With the increase of the initial concentration, the degradation percentage of formaldehyde first increased and then decreased, mainly because when the initial concentration of formaldehyde was 200 ppb, the adsorption of formaldehyde molecules on the catalyst surface was limited, resulting in a poor catalytic reaction effect. When the initial concentration increased to 500 ppb, more formaldehyde molecules participated in the redox reaction on the catalyst surface, which increased the formaldehyde degradation percentage. However, when the initial concentration increased to 1000 ppb, the degradation percentage of formaldehyde decreased, which is because oxygen was continuously consumed, and the oxygen in the air could not be replenished to the catalyst in time to form lattice oxygen, resulting in a decrease in the degradation percentage. Or because in the experiment of 1000 ppb, the reaction rate is large, the formaldehyde adsorbed on the surface of the catalyst is oxidized to formaldehyde salt by the oxygen-containing group, and formate species on the surface of the catalyst can’t be decomposed in time, covering the active point on the surface of the catalyst, resulting in the loss of activity of the catalyst, the degradation percentage of formaldehyde is reduced.
It can be seen from that with the increase of the loading, the catalytic effect is getting better and better. When the catalyst load is 10 g/m2, 20 g/m2, and 40 g/m2, after 5 h of catalysis under the conditions of solar radiation intensity of 550w/m2, a stable temperature of 62.6 ± 0.2°C in the experimental chamber, and initial concentration of formaldehyde of 500 ± 5 ppb. formaldehyde degradation percentage is 62.8%, 78.3%, 81.1%, respectively. This is because the active point sites on the catalyst surface increase with the increase of the catalyst load and providing more reaction sites so that more formaldehyde molecules participate in the catalytic reaction. However, the catalytic effect increases slowly, which might be the following two reasons: (1) The weight of the catalyst load increases the thickness of the catalyst coating, formaldehyde molecules in the process of moving to the catalyst coating inside there is a large resistance, at the same time the catalyst temperature inside the coating is lower than the surface catalyst temperature; (2) Catalyzed formaldehyde reaction products within the coating also have greater movement resistance in the process of desorption.
It can be seen from that the reaction rates of formaldehyde at three different temperatures (68.2 ± 0.2°C, 62.6 ± 0.2°C, and 56.7 ± 0.2°C) all continued to decrease with the progress of the experiment. The average reaction rates of formaldehyde in the initial cycle were 1.76 × 10−3 ppb·m·s−1, 9.4 × 10−4 ppb·m·s−1, and 7.8 × 10−4 ppb·m·s−1, respectively. The average reaction rates of formaldehyde in the terminal cycle were 7.8 × 10−5 ppb·m·s−1, 1.17 × 10−4 ppb·m·s−1, and 7.8 × 10−5 ppb·m·s−1, respectively. This is because of the following two reason: (1)In the initial stage of the experiment, the reaction rate is mainly affected by the temperature. The higher the temperature, the higher the activity of formaldehyde molecules and the more intense the molecular motion, which is conducive to its adsorption to the catalyst surface and increases the chance of contacting the oxidizing active substances on the catalyst surface. At the same time, the desorption of CO2 and H2O molecules produced by the reaction on the catalyst surface is accelerated. (2) The increase in the reaction temperature is favorable for the cerium ion to provide oxygen element to the manganese ion, which increases the valence of the manganese ion, thereby enhancing the redox ability of the manganese oxide. In addition, after the lattice oxygen in the catalyst reacts with formaldehyde, oxygen vacancies are formed on the surface of the catalyst. The higher reaction temperature may promote the formation of various types of oxygen species on the surface of the catalyst by oxygen molecules in the air, which can supplement the oxygen vacancies quickly and effectively (Cui, Wang, and Tan Citation2020; Dave, Sirach, Chaturvedi et al. Citation2022; Dave, Sirach, and Thakkar Citation2022; Dave, Sirach, Thakkar, et al. Citation2022). It can be seen that the catalytic activity of the MnOx-CeO2 catalyst for formaldehyde is significantly affected by the reaction temperature. With the progress of the experiment, concentration will gradually become the main influencing factor. At this time, the experimental reaction rate with high temperature may not be the fastest, which can also be reflected in the figure.
In the three groups of experiments with different initial concentrations of formaldehyde, the reaction rate was the highest in the initial period and gradually decreased with the progress of the experiment. It is worth noting that in the experiment of 1000 ppb, the average reaction rate of formaldehyde in the end cycle is 4.2 × 10−4 ppb·m·s−1. At this time, the reaction rate of formaldehyde is still relatively considerable. Therefore, we extended the experiment to seven hours and found that the degradation percentage of formaldehyde reached 82.1%, an increase of 11.5%.
In the three groups of experiments with different catalyst loadings, the average reaction rate of formaldehyde gradually decreased with the progress of the experiment, and the larger the loading, the faster the average reaction rate of formaldehyde decreased. This is because the index to measure the reaction speed of formaldehyde in this study is the average reaction rate per BET-specific surface area. Therefore, theoretically speaking, increasing the catalyst load can only accelerate the concentration decline rate in the experimental chamber under the same experimental conditions but cannot improve the reaction rate. Therefore, with the progress of the experiment, the formaldehyde concentration in the experiment with large catalyst loading will also decrease faster, resulting in a gradual increase in the effect of formaldehyde concentration on the reaction rate. This can be clearly observed in the experiment with a loading capacity of 40 g/m2. As can be seen from , the reaction rate decreased rapidly in the first 8 cycles due to the rapid decrease of formaldehyde concentration, and then the reaction gradually stabilized with the decrease of formaldehyde concentration.
Formaldehyde catalytic model analysis
In this paper, several common kinetic model expressions were derived in Section 2.3.2, and the fitting parameters and fitting degree of MVK, LH and ER models were obtained by fitting them with the data of the formaldehyde catalytic effect at different temperatures and concentrations, as shown in and . Under the experimental conditions of 56.7 ± 0.2°C temperature and 500 ± 10
formaldehyde concentration, the fitting effects of these three models are good, and
are greater than 0.88. On the whole, the expression with the highest average fitting degree is the ER model regardless of temperature or concentration, indicating that the ER model best describes the reaction process of the MnOx-CeO2 catalyst to formaldehyde catalytic oxidation at different temperatures or concentrations. To better reflect the fitting degree, the first five data points and the last four data points in each group of experiments were excluded (excluding the factor that formaldehyde concentration was unstable at the beginning of the experiment), and then the ER model was fitted to obtain
(see ), indicating that the fitting degree was significantly improved. It also shows that in the process of thermal catalytic oxidation, formaldehyde is in the adsorbed state, and oxygen is in the gas state.
Table 3. MVK kinetic model parameters of thermal catalytic oxidation of formaldehyde.
Table 4. LH kinetic model parameters of thermal catalytic oxidation of formaldehyde.
Table 5. ER kinetic model parameters of thermal catalytic oxidation of formaldehyde.
As seen from , the reaction rate constants of formaldehyde thermal catalysis at temperatures of 56.7 ± 0.2°C, 62.6 ± 0.2°C and 68.2 ± 0.2°C were 4.095 , 6.9759
and 2.875
, respectively. With increasing reaction temperature, the reaction rate constant first increased and then decreased because when the temperature was high, the reaction rate of formaldehyde in the early stage of the experiment was more quick, leading to a rapid decline in formaldehyde concentration. The formaldehyde in the experimental chamber was in a state of low concentration for most of the time, and the reaction rate of formaldehyde was low. The reaction rate constants of formaldehyde thermal catalysis at formaldehyde concentrations of 200 ± 4
, 500 ± 10
and 1000 ± 20
were 0.8125
, 6.9759
and 11.6
, respectively, which also increased first and then decreased because in the middle and late stages of high-concentration formaldehyde catalysis, the intermediate products formaldehyde salt and CO2 occupy the active sites on the catalyst surface so the catalytic rate decreases.
Discussion and limitations
Dave, Sirach, and Chaturvedi (Citation2022), Han (Citation2014), and Yu (Citation2018) found that the catalytic mechanism of formaldehyde was in line with the LH bimolecular competitive adsorption model by using a single-channel test in thermal catalysis experiment. However, it was concluded that formaldehyde photocatalysis conforms to the ER model by using laboratory chamber tests in photocatalysis experiment (Li 2017; Yu and Huang Citation2010). The main difference between the single-channel test and laboratory chamber test is that the former can ensure a constant concentration of formaldehyde during the experimental process, formaldehyde, and oxygen pass through the catalyst under the same external pressure, and both have the same adsorption opportunities at the active points on the catalyst surface. In the laboratory chamber, the concentration of formaldehyde continues to decline, and an important point is that formaldehyde and oxygen freely diffuse to the surface of the catalyst in the chamber. In this study, three models were used to analyze and verify the experimental results of formaldehyde catalysis, and the results showed that the reaction mechanism of the ER model was more consistent with the study of formaldehyde thermal catalytic reactions using a laboratory chamber.
is a diagram of the formaldehyde purification system in the car, which can provide theoretical support for the application of the content of this study in practice. As shown in the figure, the formaldehyde adsorption plate with the MnOx-CeO2 catalyst attached is installed at the skylight (it can also be installed at the front windshield), the purpose is to effectively use the solar energy to heat up the catalyst and the heated catalyst has a higher activity. Install a small fan on the side of the formaldehyde adsorption board, which can speed up the airflow on the surface of the board, and at the same time, can drive the air circulation in the car so that the formaldehyde in the car can be more fully contacted with the catalyst, to improve the degradation percentage of formaldehyde.
This study also has some limitations: (1) The experiment was not conducted in a real car; (2)After the experiment, the catalyst was not characterized to analyze the changes before and after use; (3) Due to the limitations of the experimental equipment, the influencing factor of humidity is not considered in this study. In future research, emphasis should be placed on establishing a multiparameter model based on the single-parameter concentration ER model.
Conclusion
In this study, the thermal catalyst MnOx-CeO2 was prepared by the modified co-precipitate method, and thermal catalytic oxidation technology was used to purify formaldehyde in cars. An experimental platform was built to simulate the car environment, and a series of thermal catalytic oxidation experiment was carried out. MnOx-CeO2 was characterized, the experimental results were fitted, and the following conclusions were obtained:
The characterization results showed that the average absorbance of MnOx-CeO2 was around 0.8 in the wavelength range of 200-2500 nm, with good absorbance and strong redox ability, and good pore structure was formed between the active particles, but the pore size was sparse, and no abundant microporous structure was found.
The intensity of solar radiation has an important effect on the catalytic effect of formaldehyde; the higher the intensity of radiation and the higher the temperature in the experimental chamber, the better the catalytic effect of formaldehyde. This is because the increase in temperature facilitates the supply of oxygen from cerium ions to manganese ions, which enhances the redox ability of manganese oxides and also promotes the desorption of products.
With increasing initial formaldehyde concentration, the formaldehyde degradation percentage first increased and then decreased. In the experiments with 200 ± 4
, 500 ± 10
and 1000 ± 20
of formaldehyde, the degradation percentage at 200 ± 4
was the lowest, and the degradation percentage at 500 ± 10
was the highest, followed by that at 1000 ± 20
, but the residual formaldehyde concentration at 200 ± 4
was the lowest;
With the increase of catalyst loading, the formaldehyde degradation percentage gradually increased, however, when the loading amount increased to 40 g/m2, compared with 20 g/m2, the formaldehyde degradation percentage only increased by 2.9%, and the catalytic effect was not significantly improved. Excessive loading does not necessarily improve the purification rate, and the optimal loading is determined according to the actual situation.
In the environmental chamber, the process of using solar thermal catalytic oxidation of formaldehyde is more consistent with the reaction mechanism of the ER model, and the
of 5 of the 6 data groups was above 0.98. It is more suitable to explain the catalytic mechanism of formaldehyde in the experimental cabin, that is, when formaldehyde is catalyzed, formaldehyde is in an adsorbed state, and oxygen is in a gaseous state.
Acknowledgment
The work presented in this paper is supported by the Natural Science Foundation of China through grant No. 52278121.
Disclosure statement
No potential conflict of interest was reported by the authors.
Data availability statement
The authors confirm that the data supporting the findings of this study are available within the article.
Additional information
Funding
Notes on contributors
Zhiqiang Wang
Zhiqiang Wang, Ph.D., is an Associate Professor, in the School of Mechanical Engineering, Tianjin University of Commerce, Tianjin, China, studying indoor air quality.
Wei Xiao
Wei Xiao, Tianjin University of Commerce, Tianjin, China, holds a master’s degree and studies indoor air quality.
Fangzhu Zhang
Fangzhu Zhang, Tianjin University of Commerce, Tianjin, China, holds a master’s degree and studies indoor air quality.
Shimin Zhang
Shimin Zhang, Tianjin University of Commerce, Tianjin, China, holds a master’s degree and studies indoor air quality.
Wufeng Jin
Wufeng Jin, Ph.D., is an Associate Professor, in the School of Mechanical Engineering, Tianjin University of Commerce, Tianjin, China, studying building environments, HVAC systems, and energy saving optimization control.
References
- Armaroli, N., and V. Balzani. 2007. The future of energy supply: Challenges and opportunities. Angew. Chem. Int. Ed. 46 (1–2):52–66. doi:10.1002/anie.200602373.
- Cai, S.-C., J.-J. Li, E.-Q. Yu, X. Chen, J. Chen, and H.-P. Jia. 2018. Strong photothermal effect of plasmonic Pt nanoparticles for efficient degradation of volatile organic compounds under solar light irradiation. Acs Appl. Nano Mater. 1 (11):6368–77. doi:10.1021/acsanm.8b01578.
- Chen, F.N., H.M. Zhang, W.H. Liang, Yang, X.D, and X.D. Yang. Analysis of the influence of temperature on material pollution emission and formaldehyde concentration in indoor air. Build. Sci. 2019 (6):5. doi:10.13614/j.cnki.11-1962/tu.2019.06.03.
- Chen, Y.C., K.I. Katsumata, Y.H. Chiu, K. Okada, N. Matsushita, and Y.-J. Hsu. 2015. ZnO–graphene composites as practical photocatalysts for gaseous acetaldehyde degradation and electrolytic water oxidation. Appl. Catal. A Gen. 490:1–9. doi:10.1016/j.apcata.2014.10.055.
- Chuang, K.T., B. Zhou, and S. Tong. 1994. Kinetics and mechanism of catalytic oxidation of formaldehyde over hydrophobic catalysts. Ind. Eng. Chem. Res. (United States) 33 (7):1680–86. doi:10.1021/ie00031a007.
- Cui, W.Y., X.Y. Wang, and N.D. Tan. 2020. Research progress on the mechanism of catalytic oxidation of formaldehyde. Fine Chem. 37 (10):1977–85.
- Dave, P.N., R. Sirach, S. Chaturvedi, R. Thakkar, and M. P. Deshpande. 2022. The catalytic effect of CoCuZnF on the thermal decomposition of 3-nitro-2,4-dihydro-1,2,4-triazol-5-one (NTO) and nanosize NTO. Mater. Lett. X 15:100159. doi:10.1016/j.mlblux.2022.100159.
- Dave, P.N., R. Sirach, and S. Chaturvedi. 2022. Kinetics of the thermolysis of 3-nitro-2,4-dihydro-3H-1,2,4-triazol-5-one (NTO) and nanosize NTO the presence of nickel-zinc-cobalt ferrite. Int. J. Chem. Kinet. 1–10. doi:10.1002/kin.21603.
- Dave, P.N., R. Sirach, and M.P. Deshpande. 2022. Evaluating the effect of nanosized CoCuFe2O4 for thermal decomposition of nitrotriazolone high energetic material. Chem. Sel. 7 (32):e202202071. doi:10.1002/slct.202202071.
- Dave, P.N., R. Sirach, and R. Thakkar. 2022. Thermal decomposition and kinetic investigation of AP and AP based composite solid propellant in the presence of nickel ferrite additive. J. Mater. Res. Technol. 19:4183–96. doi:10.1016/j.jmrt.2022.06.123.
- Dave, P., R. Sirach, R. Thakkar, M.P. Deshpande, and D.M. Badgujar. 2022. Cobalt copper zinc ferrite: an efficient catalyst for the thermal decomposition of ammonium perchlorate. Combust. Sci. Technol. 1–18. doi:10.1080/00102202.2022.2040997.
- Deng, Q., X. Yang, and J. S. Zhang. 2009. Study on a new correlation between diffusion coefficient and temperature in porous building materials. Atmos. Environ. 43 (12):2080–83. doi:10.1016/j.atmosenv.2008.12.052.
- Guo, R.H., H.L. Sun, F. Hu, Y.D. Huang, and Y.Y. Song. Automotive interior materials and interior air pollution. Auto Parts 2018 (11):6.
- Han, X. 2014. Study on the performance and kinetic model of removing indoor formaldehyde by thermal catalytic oxidation. Tianjin University.
- Hao, H., Y. Zhang, H. Zhang, and X. Song. 2021. Study on the distribution characteristics and purification effect of formaldehyde in decorated indoors under different ventilation methods. IOP Conf. Ser.: Earth Environ. Sci. 680 (1):012101 (5pp). doi:10.1088/1755-1315/680/1/012101.
- Hou, S.L. 2017. Analysis of temperature change characteristics of vehicles parked in open air in summer. J. Beijing Polytech. Coll. 16 (1):17–21.
- Huang, H., Y. Xu, Q. Feng, and D.Y.C. Leung. 2015. Low temperature catalytic oxidation of volatile organic compounds: A review. Catal. Sci. Technol. doi:10.1039/C4CY01733A.
- Huang, Q., M.T. Bai, C. Ren, G.H. Wang, T. Tao, Y.X. Zhao, and M. D. Chen. 2018. Catalytic oxidation of formaldehyde with Mn-based metal oxide catalysts at room temperature. Chin. Environ. Sci. 38 (1):103–11.
- Huang, S., J. Xiong, and Y. Zhang. 2015. Impact of temperature on the ratio of initial emittable concentration to total concentration for formaldehyde in building materials: Theoretical correlation and validation. Environ. Sci. Technol. 49 (3):1537–44. doi:10.1021/es5051875.
- Hu, X., C. Li, Z. Sun, J. Song, and S. Zheng. 2020. Enhanced photocatalytic removal of indoor formaldehyde by ternary heterogeneous BiOCl/TiO2/sepiolite composite under solar and visible light. Build. Environ. 168:168. doi:10.1016/j.buildenv.2019.106481.
- Jiang, C., D. Li, P. Zhang, J. Li, J. Wang, and J. Yu. 2017. Formaldehyde and volatile organic compound (VOC) emissions from particleboard: Identification of odorous compounds and effects of heat treatment. Build. Environ. 117 (May):118–26. doi:10.1016/j.buildenv.2017.03.004.
- Kapteijn, F., L. Singoredjo, A. Andreini, and J.A. Moulijn. 1994. Activity and selectivity of pure manganese oxides in the selective catalytic reduction of nitric oxides with ammonia. Appl. Catal. B 33 (2–3):173–89. Cheminform. doi:10.1016/0926-3373(93)E0034-9.
- Kumar, M., G. Rattan, and R. Prasad. 2015. Catalytic abatement of methane emission from CNG vehicles: An overview. 3:381–409. doi:10.13179/canchemtrans.2015.03.04.0227.
- Li, J.J., M. Zhang, S.C. Cai, E. Q. Yu, J. Chen, H.P, Jia. 2020. Research progress of photothermal catalytic oxidation of VOCs. Environ. Eng. 38(1):8. doi:10.13205/j.hjgc.202001002.
- Li, Y., M. Mao, H. Lv, J. Hou, M. Zeng, L. Ren, H. Huang, and X. Zhao. 2016. Efficient UV-vis-IR light-driven thermocatalytic purification of benzene on a Pt/CeO2 nanocomposite significantly promoted by hot electron-induced photoactivation. Environ. Sci.: Nano 4 (2):373–84. doi:10.1039/C6EN00472E.
- Li, Y.H. 2007. Degradation of formaldehyde in indoor air by photocatalytic oxidation and numerical simulation. Harbin Institute of Technology.
- Li, Y.Z., J.C. Huang, T. Peng, J. Xu, and X. Zhao. 2010. Photothermocatalytic synergetic effect leads to high efficient detoxification of benzene on TiO2 and Pt/TiO2 nanocomposite. Chemcatchem 2 (9):1082–87. doi:10.1002/cctc.201000085.
- Liu, Y.R., and Y. Huang. 2020. Progress in catalytic degradation of formaldehyde by MnO2 - based materials at room temperature. J. Earth Environ. 11 (1):17.
- Meng, X.G., L.Q. Liu, S. Ouyang, H. Xu, D. Wang, N. Zhao, and J. Ye. 2016. Nanometals for solar-to-chemical energy conversion: From semiconductor-based photocatalysis to plasmon-mediated photocatalysis and photo-thermocatalysis. Adv. Mater. 28 (32):6781–803. doi:10.1002/adma.201600305.
- Ministry of Ecology and Environment of the People’s Republic of China. 2011. GB/T 27630—2011 Guide for air Quality assessment in Passenger vehicles. China.
- Pei, J., H. Xu, and L. Yi. 2015. Performance and kinetics of catalytic oxidation of formaldehyde over copper manganese oxide catalyst. Build. Environ. 84:134–41. doi:10.1016/j.buildenv.2014.11.002.
- Pei, J., and J.S. Zhang. 2011. Critical review of catalytic oxidization and chemisorption methods for indoor formaldehyde removal. HvaC&R Res. 17 (4):476–503. doi:10.1080/10789669.2011.587587.
- Peng, J., and S. Wang. 2007. Performance and characterization of supported metal catalysts for complete oxidation of formaldehyde at low temperatures. Appl. Catal. B 73 (3–4):282–91. doi:10.1016/j.apcatb.2006.12.012.
- Rui, Z.B., and H.B. Ji. 2018. Multiscale effects and catalyst design in catalytic combustion of organic waste gas. J. Chem. Eng. 69 (1):317–26.
- Tang, X., Y. Bai, A. Duong, M.T. Smith, L. Li, and L. Zhang. 2009. Formaldehyde in China: Production, consumption, exposure levels, and health effects. Environ. Int. 36 (8):1210–24. doi:10.1016/j.envint.2009.06.002.
- Tang, X., J. Chen, X. Huang, Y. Xu, and W. Shen. 2008. Pt/MnOx–CeO2 catalysts for the complete oxidation of formaldehyde at ambient temperature. Appl. Catal. B 81 (1):115–21. doi:10.1016/j.apcatb.2007.12.007.
- Tang, X., Y. Li, X. Huang, Y. Xu, H. Zhu, J. Wang, and W. Shen. 2006. MnOx–CeO2 mixed oxide catalysts for complete oxidation of formaldehyde: Effect of preparation method and calcination temperature. Appl. Catal. B 62 (3–4):265–73. doi:10.1016/j.apcatb.2005.08.004.
- Tang, X.F. 2006. Study on complete oxidation of formaldehyde over manganese - Cerium solid solution catalyst. Graduate School of Chinese Academy of Sciences.
- Wang, J., R. Yunus, J. Li, P. Li, P. Zhang, and J. Kim. 2015. In situ synthesis of manganese oxides on polyester fiber for formaldehyde decomposition at room temperature. Appl. Surf. Sci. 357 (DEC.1PT.A):787–94. doi:10.1016/j.apsusc.2015.09.109.
- Wang, Q.Y., K.L. Yeung, and M.A. Bañares. 2020. Ceria and its related materials for VOC catalytic combustion: A review. Catal. Today 356:141–54. doi:10.1016/j.cattod.2019.05.016.
- Wei, G., P. Liu, D. Chen, T. Chen, X. Liang, and H. Chen. 2019. Activity of manganese oxides supported on halloysite towards the thermal catalytic oxidation of formaldehyde: Constraint from the manganese precursor. Appl. Clay Sci. 182:105280. doi:10.1016/j.clay.2019.105280.
- Xing, F., T. Zhu, Y. Sun, and X. Yan. 2011. The roles of various plasma species in the plasma and plasma-catalytic removal of low-concentration formaldehyde in air. J. Hazard. Mater. 196:380–85. doi:10.1016/j.jhazmat.2011.09.044.
- Xu, H., N. Yan, Z. Qu, W. Liu, J. Mei, W. Huang, and S. Zhao. 2017. Gaseous heterogeneous catalytic reactions over Mn-based oxides for environmental applications: A critical review. Environ. Sci. Technol. 51 (16):8879. doi:10.1021/acs.est.6b06079.
- Xu, Q.J., Y.P. Zhang, J.H. Mo, and X. Li. 2011. Indoor formaldehyde removal by thermal catalyst: Kinetic characteristics, key parameters, and temperature influence. Environ. Sci. Technol. 45 (13):5754–60. doi:10.1021/es2009902.
- Yang, Y., Y. Li, M. Mao, M. Zeng, and X. Zhao. 2017. Uv–visible–infrared light driven thermocatalysis for environmental purification on ramsdellite MnO2 hollow spheres considerably promoted by a novel photoactivation. ACS Appl. Mater. Interfaces 9 (3):2350–57. doi:10.1021/acsami.6b12819.
- Yang, Y., Y.Z. Li, Q. Zhang, M. Zeng, S. Wu, L. Lan, and X. Zhao. 2018. Novel photoactivation and solar-light-driven thermocatalysis on ε-MnO2 nanosheets lead to highly efficient catalytic abatement of ethyl acetate without acetaldehyde as unfavorable by-product. J. Mater. Chem. Mater. Energy Sustain. 6 (29):14195–206. doi:10.1039/C8TA04274H.
- Ye, X.L., X.J Guo, H.Y Shi, Lin, S.T, Cen, Z. H, et al. 2007. Analysis of formaldehyde pollution in automobile air and its influencing factors. Environ. Pollut. Prev. 29 (4):4.
- Yu, B.D. 2018. Experimental and numerical study of a novel Trombe wall system with solar photothermal catalysis. University of Science and Technology of China.
- Yu, B.D., D. Zhong, J.X. Liu, and X. Niu. 2020. A novel solar PV/T driven air purification system based on heterogeneous photocatalytic reaction principles: A short review and preliminary investigation. Energy Convers. Manage. 210:210. doi:10.1016/j.enconman.2020.112697.
- Yu, E., J. Li, J. Chen, J. Chen, Z. Hong, and H. Jia. 2019. Enhanced photothermal catalytic degradation of toluene by loading Pt nanoparticles on manganese oxide: Photoactivation of lattice oxygen. J. Hazard. Mater. 388:121800. doi:10.1016/j.jhazmat.2019.121800.
- Yu, Z.J., and S.P. Huang. 2010. Study on photocatalytic degradation of formaldehyde by gas phase. J. Xianyang Norm. Univ. 25 (04):35–38.
- Zhang, Y., X. Luo, X. Wang, K. Qian, and R. Zhao. 2007. Influence of temperature on formaldehyde emission parameters of dry building materials. Atmos. Environ. 41 (15):3203–16. doi:10.1016/j.atmosenv.2006.10.081.
- Zhu, C., B. Li, W. Yu, H. Wang, T. Zhang, J. Xiong, and Z. Bu. 2018. Risk assessment of inhalation exposure to VOCs in dwellings in Chongqing, China. Toxicol. Res. (Camb.). doi:10.1039/c7tx00191f.
- Zhu, G., J. Wang, Y. Muhammad, Y. Zhang, S.J. Shah, Y. Hu, Z. Chu, Z. Zhao, and Z. Zhao. 2020. Enhanced moisture-resistance and excellent photocatalytic performance of synchronous N/Zn-decorated MIL-125(Ti) for vaporous acetaldehyde degradation. Chem. Eng. J. 388:124389. doi:10.1016/j.cej.2020.124389
- Zhu, L., Wang, J. Rong, S. Rong, H. Wang, and P. Zhang. 2017. Cerium modified birnessite-type MnO2 for gaseous formaldehyde oxidation at low temperature. Appl. Catal., B. Environ.: Int. J. Devoted Catal. Sci. Appl. 211:212–21. doi:10.1016/j.apcatb.2017.04.025.