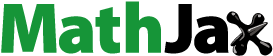
ABSTRACT
Traditional bonded dust suppressants have high viscosity, insufficient fluidity and poor permeability problems, which is adverse to the formation of a continuous and stable solidified layer of dust suppressant solution on the surface of a dust pile. Gemini surfactant has efficient wetting performance and environmental protection performance, it is introduced as a wetting component to improve the flow and penetration performance of bonded dust suppressant solution, polymer absorbent resin (SAP) and sodium carboxymethyl starch (CMS) were selected as the main components of dust suppressant. A proportioning optimization model was constructed based on response surface methodology (RSM), and the concentration of each dust suppression component was selected as the independent variable, water loss rate, moisture retention rate, wind erosion rate and solution viscosity were chosen as the dependent variables in this model. The optimal formulation of the improved bonded dust suppressant was obtained by analyzing the laboratory experiments and field tests data. The results show that the effective time (≥15d) of the newly developed dust suppressant is 45 times longer than that of pure water (≈1/3d), and 1.875 times longer than that of the comparative dust suppressant (8d), the comprehensive cost is 27.36% lower than that of the similar dust suppressant product for mining enterprises.
Implications: This paper presents the research idea of optimizing the bonded dust suppressant based on the improvement of wetting performance. And the paper used response surface method to obtain a wetting and bonding composite dust suppressant formulation. The field test shows that the dust suppressant has good dust suppression performance and economic benefits. This study laid the foundation for the development of new and efficient dust suppressants, and had important theoretical and application values for reducing dust environmental hazards and preventing occupational diseases.
Introduction
Large amounts of mineral dust are produced during mining, processing and transportation for open pit mines, which causes serious harm to operators, equipment and the surrounding environment (Chen et al. Citation2013; Ding et al. Citation2020; Liang et al. Citation2018; Liu et al. Citation2021). The commonly used technologies for dust control include ventilation and dust removal, water mist dust removal, dust collector and chemical dust suppression (Cai et al. Citation2019; Li et al. Citation2021; Peng et al. Citation2019). As one of the safe and efficient dust control techniques, chemical dust suppression has been widely studied and applied in many mines in recent years (Shi et al. Citation2022; Song et al. Citation2021; Yan et al. Citation2020).
At the present, dust suppressants can be classified as either wetting type or bonding type, depending on the mechanism of dust suppression (Zhao et al. Citation2021). Many researchers have conducted research on dust suppressants in order to meet the needs in different fields, trades and application situations (Lu, Lei, and Zafar Citation2021; Shi et al. Citation2019; Wang et al. Citation2019, Citation2021; Zhou et al. Citation2018; S. Zhu et al. Citation2021; Y. Zhu et al. Citation2021). For the road dust pollution of the open-pit mine, most of the dust suppressant components are developed from the perspective of the bonding type (Zhang et al. Citation2018; Y. Zhu et al. Citation2021). Bonded dust suppressants mainly form a solid or bonded layer on the surface of the dust layer to lock the dust and prevent the secondary dust pollution caused by wind erosion. Among this, Medeiros, Leite, and Lago (Citation2012) utilized glycerol, a biodiesel by-product, to generate an excellent dust suppressant with good bonding properties, but the preparation procedure is complicated. Jin et al. (Citation2020) developed a composite dust suppressant with a wind erosion rate of 20.62% at a 5 wt% concentration, however, the dust suppression rate was lower than that of a high-efficiency bonded dust suppressant. Fan, Zhou, and Wang (Citation2018) prepared a composite dust suppressant with a strong bonding effect, but the solid film is only formed on the surface of the dust pile because of its poor permeability (Wang et al. Citation2020), and the effective time of dust suppression may be shortened under the effect of continuous wind erosion.
In order to improve the performance of resistance to wind erosion of bonded dust suppression, it is very important to enhance the strength and compactness of the bonded layer created by the dust suppressant solution on the surface of the dust pile. However, the general bonded dust suppression solution has limitations with its high viscosity, poor fluidity, and weak permeability (Bao et al. Citation2019), which makes it difficult to form a continuous, complete and uniform bonded layer on the surface of the dust pile, it is easy to be cracked and destroyed by the continuous action of wind erosion and resulting in secondary dust pollution. The wetting dust suppressant can increase the contact area between the dust suppressant solution and the dust pile, improve the flow performance and the permeability of the bonding dust suppressant solution. As a result, a new development idea of bonded dust suppression was proposed, that is, the wetting component was used to improve the wetting performance of the general bonded dust suppression solution.
Wetting component optimal selection
The special double-chain amphiphilic structure of Gemini surfactant makes it have higher surface activity, which can significantly reduce the surface tension and improve the wettability of dust suppressants solution (Mondal et al. Citation2015; Su et al. Citation2011). As a common raw material of daily chemicals, it is nontoxic, nonirritating and biodegradable (Cheng et al. Citation2019; Kamal Citation2016).
The wetting process of Gemini surfactant solution is shown in . The space between the ion head groups with charged will increase because of the existence of the intermediate bond, then produce the strong interaction between hydrocarbon chains and higher surface activity compared to monomer of Gemini surfactant, such as lower surface tension and critical micelle concentration (Sakai, Sakai, and Abe Citation2011; Xing et al. Citation2014), as show in .
The wetting process of dust is that the air on the dust surface is replaced by the dust suppressant solution. The Gemini hydrophobic group changes the structure of water molecules, and forms a tightly arranged Gemini molecular layer on the surface of water molecules when Gemini is dissolved in water, as show in , the hydrophobic group approach toward the air. In general, the surface of metal dust usually exhibits the strong hydrophobic properties because the dust surface contains hydrophobic group. Gemini solution and the hydrophobic groups on the surface of the dust interact, making it easier for the dust suppressant solution to effectively combine with the dust and increase wetting ability, as show in .
The quaternary ammonium cationic Gemini surfactant (Dodecanol) was selected as the wetting component of the bonded dust suppressant on the basis of the data analysis of the comparative test for several Gemini surfactants on the market. The dust sample was collected from the road dust of an open-pit iron mine in Guangxi Province, China, it is primarily made up of hematite, which was sieved and dried for laboratory experiment, shows the size distribution of the dust sample.
Because it is difficult to achieve synergism between cationic surfactants and similar surfactants (Geng et al. Citation2017), the preliminary experiment was carried out. It was found that the wettability of Gemini solution could be further improved by adding cocoamidopropyl betaine (CAB), alcohol ethoxylate (AEO) and sodium alcohol ether sulfate (AES), to simplify the description, the Gemini solution described later is a mixture of the above four materials. In order to further confirm the stability of the optimized ratio of Gemini solution, Fourier transform infrared spectrometer (FTIR) analysis was used, and the result is shown in . The unsaturated C-H stretching vibration peak at 3393.05 cm−1, the antisymmetric bending vibration peak of CH3 was at 1463.92 cm−1, and the stretching vibration peak of organic halide C-Cl was at 656.98 cm−1. It shows that the functional groups of Gemini solution are simpler and more stable than that of single Gemini surfactant.
The concentration ranges for each component of dust suppressant
Besides the Gemini solution was determinated as the wetting component, polymer absorbent resin (SAP) and sodium carboxymethyl starch (CMS) were selected as the functional components of the composite dust suppressant from the viewpoint of bonding and moisturizing properties.
In order to obtain reasonable concentration intervals for each functional component, the data of the sedimentation time of dust, water loss rate and wind erosion rate at different components and concentrations were compared and analyzed from the evaluation indexes of wetting, moisture retention and bonding performance. Due to space limitations, the reasonable concentration range of Gemini solution determined was 1.0–2.0% without further details. According to the literature research (Ai et al. Citation2021; Bhandari and Hanna Citation2011), the CMS concentration range was determined to be 1.0% ~ 2.5% and the SAP concentration range was 0.05% ~ 0.2%.
Optimization of the ratio of the composite dust suppressant
Box-Behnken method was used to design the experimental scheme (Hu et al. Citation2014; Jie, Zi-Wen, and Xiao-Ling Citation2007; Vinayagamoorthy Citation2017), CMS concentration, SAP concentration, Gemini solution concentration were selected as the independent variables, the water loss rate (Y1), moisture retention rate (Y2), wind erosion rate (Y3) and solution viscosity (Y4) were taken as the dependent variables. The response surface method was conducted to get the optimal ratio of the composite dust suppressant based on the Box-Behnken design, the results are shown in .
Table 1. The results of Box-Behnken design and response surface design.
According to the analysis process of response surface method (Nair, Velmurugan, and Sukumaran Citation2020; Wei et al. Citation2016; Yolmeh and Jafari Citation2017) and the experimental data in , the relationships between different values of the dependent variables (water loss rate, moisture absorption rate, wind erosion rate, viscosity) and independent variables (each component concentration) were established, and the corresponding quadratic polynomial regression equations were obtained and ANOVA was performed. The results show that the correlation coefficient R2 of each regression equation is close to 1, indicating that these calculation results have high reliability.
Based on the analysis result of each regression equation, the optimal proportion of the composite dust suppressant was obtained by using response surface method, that is 2.50% CMS, 0.10% SAP and 1.55% Gemini solution.
Verification test for optimal ratio of the composite dust suppressant
In order to verify the actual performance of the optimal ratio of the composite dust suppressant, the anti-evaporation and wind erosion resistance tests (Huang et al. Citation2021; Omane, Liu, and Pourrahimian Citation2018) were used to evaluate the performance of dust suppressant, and pure water was selected as the comparative group.
The variation of water loss rate versus test time was obtained by anti-evaporation test, and the results are shown in . After drying at 50°C for 60 min, the surface of the dust sample treated with Gemini dust suppressant still shows a bright and humid state, while the surface of the dust sample treated with water has shown a dry state. It shows that the Gemini dust suppressant has a certain water locking effect, which can prevent the rapid loss of water at high temperature. After drying for 240 min, the surface of dust sample treated with Gemini dust suppressant was dry and hard, with few floating particles, while there was a lot of dust floating particles on the surface of dust sample treated with water. It shows that after a long time of high temperature drying, the dust suppressant can still adhere to the dust well to prevent its loose floating and cause secondary dust. The maximum evaporation of dust samples treated with dust suppressant and water is 5 g and 9 g respectively, and the maximum water retention is 80% higher than that of water.
The relationship between the moisture content and test time was obtained by the anti-evaporation experiment, the results are shown in . The moisture content of the dust sample tested by the Gemini dust suppressant decreased at an early stage, it remained basically unchanged after 25 h, and maintained at about 3.80%, but the water-treated dust samples converged to 0 after 40 h. This shows that the Gemini dust suppressant has good moisture retention effect, and can effectively slow down water evaporation.
Through wind erosion resistance test, the relationship between the wind erosion rate and test time is obtained, the results as shown in . Overall, the growth of wind erosion rate is slower than that of water with increase of wind erosion time. When the wind erosion time is 60 min, the wind erosion rate of Gemini dust suppressant is 3.60%. At this time, the wind erosion rate of the dust sample treated with water reached 10.80%, which is three times the former rate, indicating that the Gemini dust suppressant has good wind erosion resistance.
Field application test in open pit mine
Comparative analysis of dust suppression performance
Field application test was carried out on the transportation road of a metal mine in Guangxi Province, China. The test site was divided into three areas A, B and C, area A is sprayed with Gemini dust suppressant, area B is sprayed with water, and area C is not treated, some pictures of the test are shown in . During the experiment, the temperature was 9 ~ 12°C, the humidity was 60 ~ 78%, and the wind speed was 0.3 ~ 3.0 m/s. Dust sampling instrument and laser dust concentration meter were used to continuously observe the change of dust concentration in the downwind direction of the test area. Regular sampling and photographing were taken every day to record the change of road dust.
The surface color of area A is darker and deeper, and there is an obvious consolidation layer from the photos in , area B road surface slightly white, there are fine dust particles on the surface, area C road surface orange, the dust on the road surface is loose. The 7th to 9th days of the test were cloudy days, the surface color of area A deepened and brightened, and the surface of area B and C became white. It shows that the dust surface in area A has good water retention capacity and bond performance, after Gemini dust suppressant treatment. Due to wind erosion effect, it makes water evaporation is easy and causes secondary dust pollution in area B and C.
The test data of dust sampler and laser dust concentration meter within 5 days of the test were selected for analysis, and the results are shown in . The images show the microscopic analysis of the sampled filter membranes at different times and dust suppressant measures, allowing visualization of the changes in dust mass concentration and quantity concentration.
It can be seen from that the initial dust concentration in area A, B and C are consistent, and the dust concentration decrease in area A is significantly greater than those in area B and C. From the second day, the dust concentration in area A steadily fluctuated at a low level, and the total dust inhibition rate reached 75%. The total dust concentration in areas B and C fluctuated greatly and was always higher than that of area A. The sudden increase of total dust concentration in areas B and C on the second day was caused by the sudden increase of wind speed during test, but it has a little effect on area A. Combined with the distribution of dust particles on the surface of sampling filter, it is found that the consolidation effect of water on dust pile is very weak, and the water retention capacity and bonding performance of Gemini dust suppressant are excellent, because it formed consolidation layer which can effectively prevent the secondary dust on the road.
Comparative analysis of economic benefits
The open-pit mine transport road was selected as an example where the field experiment was carried out. The metal mine runs for 300 days throughout the year, the transport road is 5 km long and 15 m wide. The amount of dust suppressant solution or water solution is about 2 kg·m−2, then 150t Gemini dust suppressant is required for a full spraying for once. The cost of one ton Gemini dust suppressant is RMB 590 Yuan, and the single effective time is 15 days. The comparison group is billed at 3 Yuan per ton of water based on sprinkling 3 times per day. The results of use cost are shown in .
Table 2. The comparison results of use cost.
The mine application test shows that the use cost of the Gemini dust suppressant was 39.50% higher than that of water, but the effective time of dust suppressant was 45 times that of water. According to the data of a multi-functional dust suppressant (Li et al. Citation2020), the use cost of Gemini dust suppressant is 27.36% lower than that of the same type dust suppressant, and the effective time of dust suppression is 1.875 times of the same type of dust suppressant. Therefore, it can be considered that Gemini dust suppressant has good economic application value.
Conclusion
The wetting mechanism of Gemini surfactant on dust is analyzed theoretically. The special double-chain amphiphilic structure of Gemini surfactant with excellent wetting performance and wetting efficiency had been investigated. The combination of Gemini surfactant and bonded dust suppressant can improve the fluidity and wettability of bonded dust suppressant, which is conducive to improving the solidification performance of bonded dust suppressant.
The optimal ratio of Gemini dust suppressant was obtained by using response surface method. From the perspective of improving the wetting and moisturizing performance of the bonded dust suppressant, CMS and SAP were selected as the components of the composite dust suppressant, and the optimal ratio of the Gemini dust suppressant was obtained using the response surface method.
The field application effect and economic benefit of the Gemini dust suppressant are remarkable. The mine application test shows that the use cost of the Gemini dust suppressant was 39.50% higher than that of water, but the effective time of dust suppressant was 45 times that of water. And it is 27.36% lower than the cost of the same type of dust suppressant, and the effective time of dust suppression is 1.875 times of the same type of dust suppressant.
Disclosure statement
No potential conflict of interest was reported by the authors.
Data availability statement
All data generated or analyzed during this study are included in this published article.
Additional information
Funding
Notes on contributors
Ming Li
Ming Li is an associate professor in Central South University, Changsha, China. His research activities focus on dust control technology and theory, mine safety and environmental protection.
Wanjie Yin
Wanjie Yin is an MS in Resources and Safety Engineering school at Central South University, Changsha, China.
Jiao Tang
Jiao Tang is an MS in Resources and Safety Engineering school at Central South University, Changsha, China.
Linling Qiu
Linling Qiu was an MS in Central South University, Changsha, China.
Xudong Fei
Xudong Fei was an MS in Central South University, Changsha, China.
Huaizhen Yang
Huaizhen Yang is an MS in Resources and Safety Engineering school at Central South University, Changsha, China.
Zhenhong Tang
Zhenhong Tang is a project leader of Guangxi Liuzhou Steel Group Co., Ltd, China.
Fashun Chen
Fashun Chen is a project manager for Guangxi Liuzhou Steel Group Co., Ltd, China.
Xingbo Qin
Xingbo Qin is a staff member of Guangxi Liuzhou Steel Group Co., Ltd, China.
Gang Li
Gang Li is a professorate senior engineer at Sinosteel Maanshan General Institute of Mining Research Co., Ltd, China. He has long been engaged in scientific research in the direction of occupational health engineering protection in non-coal mines.
References
- Ai, F., X. Yin, R. Hu, H. Ma, and W. Liu. 2021. Research into the super-absorbent polymers on agricultural water. Agric. Water Manag. 245 (February):106513. doi:10.1016/j.agwat.2020.106513.
- Bao, Q., W. Nie, C. Liu, Y. Liu, H. Zhang, H. Wang, and H. Jin. 2019. Preparation and characterization of a binary-graft-based, water-absorbing dust suppressant for coal transportation. J. Appl. Polym. Sci. 136 (7):WOS:000453845100012. doi:10.1002/app.47065.
- Bhandari, P.N., and M.A. Hanna. 2011. Continuous solventless extrusion process for producing sodium carboxymethyl starch suitable for disintegrant applications in solid dosage forms. Ind. Eng. Chem. Res. 50 (22):12784–12789. doi:10.1021/ie200311w.
- Cai, P., W. Nie, D. Chen, S. Yang, and Z. Liu. 2019. Effect of air flowrate on pollutant dispersion pattern of coal dust particles at fully mechanized mining face based on numerical simulation. Fuel 239 (March):623–35. doi:10.1016/j.fuel.2018.11.030.
- Chen, H., Q. Feng, R. Long, and H. Qi. 2013. Focusing on coal miners’ occupational disease issues: A comparative analysis between China and the United States. Saf. Sci. 51 (1):217–22. doi:10.1016/j.ssci.2012.06.025.
- Cheng, Y., Y. Yang, C. Niu, Z. Feng, W. Zhao, and S. Lu. 2019. Progress in synthesis and application of zwitterionic Gemini surfactants. Front. Mater. Sci. 13 (3):242–57. doi:10.1007/s11706-019-0473-0.
- Ding, J., G. Zhou, D. Liu, W. Jiang, Z. Wei, and X. Dong. 2020. Synthesis and performance of a novel high-efficiency coal dust suppressant based on self-healing gel. Environ. Sci. Technol. 54 (13):7992–8000. doi:10.1021/acs.est.0c00613.
- Fan, T., G. Zhou, and J. Wang. 2018. Preparation and characterization of a wetting-agglomeration-based hybrid coal dust suppressant. Process Saf. Environ. Prot. 113 (January):282–91. WOS:000424854400027. doi:10.1016/j.psep.2017.10.023.
- Geng, T., C. Zhang, Y. Jiang, H. Ju, and Y. Wang. 2017. Synergistic effect of binary mixtures contained newly cationic surfactant: Interaction, aggregation behaviors and application properties. J. Mol. Liq. 232 (April):36–44. doi:10.1016/j.molliq.2017.02.055.
- Hu, J., J. Li, P. Feng, X. Zhang, and M. Zhong. 2014. Optimization of enzymatic extraction of polysaccharide from dendrobium officinale by Box-Behnken design and response surface methodology. Zhong Yao Cai = Zhongyaocai = J. Chin. Med. Mater. 37 (1):130–33. MEDLINE:25090717.
- Huang, Z., Y. Huang, Z. Yang, J. Zhang, Y. Zhang, Y. Gao, Z. Shao, and L. Zhang. 2021. Study on the physicochemical characteristics and dust suppression performance of new type chemical dust suppressant for copper mine pavement. Environ. Sci. Pollut. Res 28 (42):59640–51. Heidelberg: Springer Heidelberg. doi:10.1007/s11356-021-14917-z.
- Jie, G., H. Zi-Wen, and F. Xiao-Ling. 2007. Optimization of epirubicin liposome formulation using Box-Behnken experimental design. Fudan Xuebao (Yixueban) 34 (6):816–20. BCI:BCI200800132028.
- Jin, H., Y. Zhang, K. Chen, K. Niu, G. Wu, X. Wei, and H. Wang. 2020. Preparation and characterization of a composite dust suppressant for coal mines. Polymers 12 (12):2942. doi:10.3390/polym12122942.
- Kamal, M. S. 2016. A review of Gemini surfactants: Potential application in enhanced oil recovery. J. Surfact. Deterg. 19 (2):223–36. doi:10.1007/s11743-015-1776-5.
- Li, G., J. Wu, L. Jin, and J. Guo. 2021. Study status and prospect of dust control technology for metal mines in China. Metal Mine (1):154–67. doi:10.19614/j.cnki.jsks.202101011.
- Li, J., Y. Yuan, J. Cao, K. Wang, H. Gao, Y. Hao, and Z. Leng. 2020. Application of multi-functional dust-depressor in open-pit mine parement. Mod. Min. 36 (7):209–11+256.
- Liang, Y., J. Zhang, T. Ren, Z. Wang, and S. Song. 2018. Application of ventilation simulation to spontaneous combustion control in underground coal mine: A case study from bulianta colliery. Int. J. Min. Sci. Technol. 28 (2):231–42. doi:10.1016/j.ijmst.2017.12.005.
- Liu, X., W. Nie, Y. Hua, C. Liu, L. Guo, and W. Ma. 2021. Behavior of diesel particulate matter transport from subsidiary transportation vehicle in mine. Environ. Pollut. 270 (February):116264. doi:10.1016/j.envpol.2020.116264.
- Lu, Z., Z. Lei, and M.N. Zafar. 2021. Synthesis and performance characterization of an efficient environmental-friendly sapindus mukorossi saponins based hybrid coal dust suppressant. J. Clean. Prod. 306 (July):127261. doi:10.1016/j.jclepro.2021.127261.
- Medeiros, M., C. Leite, and R. Lago. 2012. Use of glycerol by-product of biodiesel to produce an efficient dust suppressant. Chem. Eng. J. 180 (January):364–69. WOS:000300475900046. doi:10.1016/j.cej.2011.11.056.
- Mondal, M.H., S. Malik, A. Roy, R. Saha, and B. Saha. 2015. Modernization of surfactant chemistry in the age of Gemini and bio-surfactants: A review. RSC Adv 5 (112):92707–18. doi:10.1039/C5RA18462B.
- Nair, K.S., R. Velmurugan, and S.K. Sukumaran. 2020. Formulation and optimization of ansamycin-loaded polymeric nanoparticles using response surface methodology for bacterial meningitis. Bionanoscience 10 (1):279–91. WOS:000527918000026. doi:10.1007/s12668-019-00713-0.
- Omane, D., W. Liu, and Y. Pourrahimian. 2018. Comparison of chemical suppressants under different atmospheric temperatures for the control of fugitive dust emission on mine hauls roads. Atmos. Pollut. Res. 9 (3):561–68. WOS:000437043500017. doi:10.1016/j.apr.2017.12.005.
- Peng, H., W. Nie, P. Cai, Q. Liu, Z. Liu, and S. Yang. 2019. Development of a novel wind-assisted centralized spraying dedusting device for dust suppression in a fully mechanized mining face. Environ. Sci. Pollut. Res. 26 (4):3292–307. WOS:000457726700015. doi:10.1007/s11356-018-3264-8.
- Sakai, K., H. Sakai, and M. Abe. 2011. Recent advances in Gemini surfactants: Oleic acid-based Gemini surfactants and polymerizable Gemini surfactants. J. Oleo Sci. 60 (4):159. doi:10.5650/jos.60.159.
- Shi, G.-Q., C. Han, Y. Wang, and H.-T. Wang. 2019. Experimental study on synergistic wetting of a coal dust with dust suppressant compounded with noncationic surfactants and its mechanism analysis. Powder Technol. 356 (November):1077–86. WOS:000504777100100. doi:10.1016/j.powtec.2019.09.040.
- Shi, G., J. Qi, G. Teng, Y. Wang, and H. Shen. 2022. Influence of coal properties on dust suppression effect of biological dust suppressant. Adv. Powder Technol. 33 (1):103352. doi:10.1016/j.apt.2021.11.004.
- Song, C., Y. Zhao, W. Cheng, X. Hu, S. Zhu, M. Wu, Y. Fan, W. Liu, and M. Zhang. 2021. Preparation of microbial dust suppressant and its application in coal dust suppression. Adv. Powder Technol. 32 (12):4509–21. doi:10.1016/j.apt.2021.10.001.
- Su, X., B. Wang, Z. Lu, L. Wei, and Y. Feng. 2011. A new cationic Gemini surfmer: Synthesis and surface activities. J. Surfact. Deterg. 14 (1):73–76. doi:10.1007/s11743-010-1211-x.
- Vinayagamoorthy, R. 2017. Parametric optimization studies on drilling of sandwich composites using the Box-Behnken design. Mater. Manuf. Processes 32 (6):645–53. WOS:000396020900008. doi:10.1080/10426914.2016.1232811.
- Wang, H., W. Xuan, Z. Zhang, and B. Qin. 2019. Experimental investigation of the properties of dust suppressants after magnetic-field treatment and mechanism exploration. Powder Technol. 342 (January):149–55. WOS:000454375100015. doi:10.1016/j.powtec.2018.09.099.
- Wang, Y., G. Zhou, C. Xu, W. Jiang, and Z. Zhang. 2020. Synthesis and characteristics of a novel dust suppressant with good weatherability for controlling dust in open coal yards. Environ. Sci. Pollut. Res 27 (16):19327–39. doi:10.1007/s11356-020-08309-y.
- Wang, Z., X. Meng, K. Yan, Z. Li, Q. Xiao, X. Ma, and J. Wang. 2021. Study on the inhibition of Al-Mg alloy dust explosion by modified Mg(OH)(2). Powder Technol. 384 (May):284–96. WOS:000634262000008. doi:10.1016/j.powtec.2021.02.037.
- Wei, Y.-C., M. Yan, J. Yang, J.-C. Liu, H.-M. Yin, Y. Wu, Y.-C. Sun, and W. Xiao. 2016. Optimization of flash-type extraction technology of Alisol B 23-Acetate from Alismatis Rhizoma by response surface methodology. Zhongguo Zhong Yao Za Zhi = Zhongguo Zhongyao Zazhi = China J Chin. Materia. Medica. 41 (3):438–42. MEDLINE:28868860. doi:10.4268/cjcmm20160313.
- Xing, F., Y. Gao, Q. Xu, X. Li, L. Wang, J. Meng, and P. Wang. 2014. The effects of the organic groups attached at the silicone atoms of the organosilane-based Gemini nonionic surfactants on their surface activities. J. Surfactants Deterg. 17 (4):739–45. doi:10.1007/s11743-013-1545-2.
- Yan, J., W. Nie, H. Zhang, Z. Xiu, Q. Bao, H. Wang, H. Jin, and W. Zhou. 2020. Synthesis and performance measurement of a modified polymer dust suppressant. Advanced Powder Technol. 31 (2):792–803. doi:10.1016/j.apt.2019.11.033.
- Yolmeh, M., and S.M. Jafari. 2017. Applications of response surface methodology in the food industry processes. Food Bioprocess Technol. 10 (3):413–33. WOS:000394285200001. doi:10.1007/s11947-016-1855-2.
- Zhang, H., W. Nie, Y. Liu, H. Wang, H. Jin, and Q. Bao. 2018. Synthesis and performance measurement of environment-friendly solidified dust suppressant for open pit coalmine. J. Appl. Polym. Sci. 135 (29):46505. doi:10.1002/app.46505.
- Zhao, Z., Y. Zhao, X. Hu, W. Cheng, J. Hou, and C. Song. 2021. Preparation and performance analysis of enteromorpha-based environmentally friendly dust suppressant. Powder Technol. 393 (November):323–32. doi:10.1016/j.powtec.2021.07.071.
- Zhou, Q., B. Qin, J. Wang, H. Wang, and F. Wang. 2018. Effects of preparation parameters on the wetting features of surfactant-magnetized water for dust control in Luwa Mine, China. Powder Technol. 326 (February):7–15. doi:10.1016/j.powtec.2017.12.002.
- Zhu, Y., Y. Cui, Z. Shan, R. Dai, L. Shi, and H. Chen. 2021. Fabrication and characterization of a multi-functional and environmentally-friendly starch/organo-bentonite composite liquid dust suppressant. Powder Technol. 391 (October):532–43. doi:10.1016/j.powtec.2021.06.050.
- Zhu, S., Y. Zhao, X. Hu, M. Wu, W. Cheng, Y. Fan, C. Song, and X. Tang. 2021. Study on preparation and properties of mineral surfactant – Microbial dust suppressant. Powder Technol. 383 (May):233–43. doi:10.1016/j.powtec.2021.01.053.