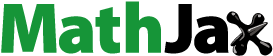
ABSTRACT
Nowadays, when the zero-waste strategy is an inevitable component of the circular economy, the reuse of waste, including dredged sludges, has drawn the attention of many researchers. This study evaluated four kinds of bio-wastes (corn core powder, rice husk powder, sugarcane bagasse powder, and peanut shell powders) and two kinds of construction wastes (autoclaved aerated concrete-AAC and pavement stone) in enhancing the dewaterability of dredged sludge from the lake, in which the sludges would then be reused for brick production. The results showed that the moisture contents decreased from 62 ± 0.14% to 57 ± 1.89% after mixing and then to 35 ± 8.31% after compressing for the construction waste-blended sludge. Among the bio-wastes, the sugarcane bagasse additive performed the best at a mixing ratio of 1:3 by weight and rice husk powder worked best at a mixing ratio of 1:5 by weight. The organic matter was increased up to 80% when the bio-wastes were added, while it was decreased to 5% for the case of construction wastes. The optimum percentage of sludge in the mixture to meet all the oxide contents in the brick and energy saving shall be about 30%. The results have revealed a potentially green route for brick production with lake sediment and bio-waste/construction wastes.
Implications: It is the first time the reuse of agro-wastes/construction waste was evaluated to mix with lake sediment to partly replace clay for brick production; Among the bio-wastes, the sugarcane bagasse additive performed the best at a mixing ratio of 1:3 by weight; Moisture contents decreased from 62 ± 0.14% to 57 ± 1.89% after mixing and then to 35 ± 8.31% after compressing for the blended sludge; The optimum percentage of mixed sludge, possibly replaced the clay in brick production, considering oxide contents and energy saving shall be up to 30%.
Introduction
Urban sludge has been a worldwide issue, particularly in developing countries. There are three main kinds of urban sludges: (i) dredged sludge from sewers, canals, and lakes; (ii) sewage sludges from wastewater treatment plants, and (iii) fecal sludges from on-site septic tanks. In many countries, these sludges are often dumped in landfills as this is the cheapest way of handling sludge (Hoang and Nguyen Citation2017; Tyagi and Lo Citation2013; Yang, Zhang, and Wang Citation2015). Nevertheless, the landfill space for urban sludge becomes limited. Recycling of sludges, therefore, would not only reduce pressure on land use but also conserve our natural resources and serve for sustainable environment protection.
Reused sludge for agricultural purposes has been applied in some countries including the USA, Australia, China, and some European countries, but not in the others like Poland, Austria, Germany, etc. where more stringent quality is required for sludge reuse for fertilization (Mininni et al. Citation2015). More attention has been paid to the reused sludge for construction materials recently. In Japan, 48% of total sewage sludge generation was reused for construction materials. The sludge after drying can be considered as material sources for cement production (Xu et al. Citation2014), coarse aggregates (Beddaa et al. Citation2020), lightweight aggregates or supplementary cementitious materials (Świerczek, Cieślik, and Konieczka Citation2018), brick production (Chiang et al. Citation2009), or concrete blocks (Chen et al. Citation2019; Nakic Citation2018).
One of the pre-treatment processes for sludges before the production of construction materials (i.e., bricks) is dewatering (Ramachandra and Devatha Citation2020; Rashvanlou et al. Citation2020). This step is vital, as it was proved by some previous studies that if they use high moisture content sludge, the compressive strength decreased noticeably by 40% (Hamood, Khatib, and Williams Citation2017; Liang et al. Citation2015). The dredged sludge without any pretreatment may not be suitable to be used directly as additive material or fine aggregates in cement (Chang et al. Citation2020). For brick production, the moisture of reused material should be as low as possible (Hoang and Nguyen Citation2017) while the dredged sludge from the lake could have moisture content up to 98%. The dewatering can be implemented by using thickening, dehydration or hydrothermal process (Zhu et al. Citation2013). The dehydration process will be carried out by natural drying or mechanical dewatering and be enhanced by using chemicals or blending with the sludge (Cai et al. Citation2019; Dai et al. Citation2018; Liu Citation2018; Tao et al. Citation2019; Xin, Chai, and Zhao Citation2014). When adding chemicals such as NaCl, CaCl2, Ca(OH)2, and FeCl3 to dredged sludge and then compressing at different pressures, Yan et al. (Citation2016). found that the addition of CaCl2 and FeCl3 showed a better reduction of sludge’s moisture content than Ca(OH)2, NaCl at low compression. With bio-waste such as walnut shell further added, the moisture content of the dewatered sludge cake conditioned with Ca(ClO)2/ferric coagulant/walnut shell was reduced from 96% to below 50% (Liang et al. Citation2018). Bio-waste has been considered to be blended with sludge for dewatering enhancement in many studies within the last decade. Different kinds of bio-wastes including rice stover (Guo et al. Citation2016), corn core powder (Guo et al. Citation2019), rice husk (Liu Citation2018), rice straw (Guo, Jiang, and Pang Citation2019), etc., have been employed to lower the moisture content by up to 50%. Moreover, construction wastes were not tried before and shall be employed in this study with the lake sediment for dewatering enhancement for brick production. The construction waste was selected as they are quite abundant in Vietnam (Hanoi Drainage and Sewerage Company HSDC Citation2019) and its characteristics have been proven a high potential for making fired clay bricks (Reis et al. Citation2020).
This study aimed to evaluate the effect of using four bio-wastes as organic additives (rice husk powder, corn core powder, peanut shell powder, sugarcane bagasse powder, and two construction wastes as inorganic additives (autoclaved aerated concrete, stone powder) during the mechanical dewatering of lake sediment. The results from this study may reveal which factors impact the concentration of organic matter, heavy metals or moisture contents in the reused sludges for brick production to create a green route for sustainable waste management and energy-saving brick production.
Materials and methods
Sludge for testing
The dredged sludge was taken from Yen Son Lake, the biggest regulation reservoir in Hanoi, Vietnam. It was settled for several hours. The settled dredged sludges were screened using 2.5-mm sieves to remove gravels, debris, grits, leaves or cloths, then stored at 4°C before use (hereafter called “DSL”). The settled sludge and its supernatant were sent for analysis including physical (moisture content, pH, composition) and chemical (heavy metals, thermal energy, organic matters, etc.) characteristics. Details of analytical methods are presented in .
Table 1. Sample analytical methods.
To assess the alternation of sludges after mixing with additives, the mixed samples were sent for Scanning Electron Microscope (SEM) and X-Ray Diffraction (XRD). The SEM was implemented using the Tabletop Microscope (TM4000plus, Hitachi, Japan) while XRD was conducted using the X-ray machine (Miniflex600, Rigaku, USA). The oxide components were detected using X-ray Fluorescence Spectrometer XRF (JSX 1000S, Jeol, Japan). The total organic matters of sludge samples (thickened sludge) were analyzed using a method for soil analysis employing K2Cr2O7 solution (national standard TCVN 7376:2004).
Preparation of additives
Four types of agro-wastes (corn core, rice husk, sugarcane bagasse and peanut shell) were collected dry from nearby farms and ground to a size of 100 mesh (i.e., 150 μm) (). These additives were hydrolyzed by soaking individually in 2 M NaOH solution >98% purity (CAS: 1310-73-2, Sigma Aldrich) for 60 min at room temperature, then washed with distilled water until free of foams and put in the oven at 105°C until completely dry. The hydrolyzation with alkaline (NaOH solution) was proved to breakdown the lignin structure, and increase the internal surface area (Yan et al. Citation2016). Since they were attached together during the hydrolyzation and drying processes, the additives were then ground again into powder and sieved to particle size diameters <150 μm. Finally, they were stored in sealed bottles and named as corn core powder (CCP), rice husk powder (RHP), sugarcane bagasse powder (SBP), and peanut shell powder (PSP).
Figure 1. Image of testing Additives: (a) rice husk powder_RHP; (b) corn core powder_CCP; (c) peanut shell powder_PSP; (d) sugarcane bagasse powder_SBP; (e) autoclaved aerated concrete_AAC and (f) stone powder_SP.
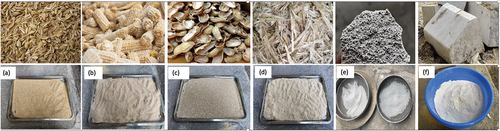
In addition, the autoclaved aerated concrete waste and stones were gathered from a demolishing site to the lab. Stones were from broken sidewalk near the site of commercial structure and the AAC was from broken wall panels and floor panels. They were placed separately. In the lab, they were ground and sieved to particle size diameters <150 μm; and were stored in separated boxes and named as autoclaved aerated concrete (AAC) and stone powder (SP).
Sludge dewatering test
The dredged sludges, after being screened, were mixed with studied additive: sludge ratio of 1:3; 1:5, and 1:7 by weight; each sample was 100 grams. The dredged sludge and studied additives were mixed for 15 min at 100 rpm. After that, the mixture was compressed by a hydraulic compression machine (60T, 267/56/21, Leipzig, Germany) with a compression load of 400 kG, with a compression time of 15 min. The selection of the dewatering test’s conditions was referred from previous studies with some modifications to fit with the dredged sludges (Guo et al. Citation2019; Liang et al. Citation2018). All the tests were conducted in duplicate. The whole process was presented in .
Data analysis
A statistical analysis was also conducted to evaluate the impact of additive types or mixing ratios on the decrease in moisture content. This step was performed by using a two-way analysis of variance (ANOVA) in which the variables were the additive types and mixing ratio of the moisture content. The level of significance was α = 0.05 in all cases. The software StatPlus:mac LE v7.3.31 (Analyst Soft Inc., USA) was used for this statistical analysis.
Results and discussion
Characteristics of DSL sample
The characteristics of the sludge’s sediment and supernatant were given in , respectively. The moisture content was quite low at 62%, instead of ~ 90% due to initially dredged and pumped from the lake into the trucks. The pH had neutral conditions because the Yen So lake received mostly rainwater, treated domestic wastewater and some treated industrial wastewater. The sand accounts for the majority in the composition (45.7%) followed by Limon (32.5%) and then clay (21.8%) in the DSL. Accordingly, the SiO2 concentration was as high as 41%, significantly higher than sewage sludge of 10% (Reis et al. Citation2020). It was the runoff water from the road surface surrounding the lake that contributes to this high SiO2 concentration. The high percentage of sand and clay would make DSL a great potential material source for brick production.
Table 2. Characteristic of DSL sludge’s sediment.
Table 3. Characteristic of DSL sludge’s supernatant.
In addition, there was evidence that contamination of heavy metals, i.e., As, Zn, Cr and Pb in the dredged sludge from the lake, was due to the discharge of improperly treated wastewater into the lake. High concentrations of heavy metals were a problem of sewage sludges as well (Świerczek, Cieślik, and Konieczka Citation2018). In their review, they found heavy metal issues in many sewage sludges from municipal WWTPs in the USA, Turkey, UK, China, etc. Nevertheless, the heavy metals concentration would probably be reduced after blending with clay and other additives during brick production. In terms of total organic matter (OM), the OM concentration in DSL was 20%, which is lower than that from the sewage sludge of 20–60% (Palermo and Hays Citation2013).
In comparison with the dredged sludge from sewers that was also characterized by our research group, the DSL had a lower sand component (45.7% vs 70%) but higher organic matter (20% vs 10%). The heat value of DSL was, therefore, a bit higher (1800 kCal/kg vs 1250 kCal/kg). It should be noted that the heat value indicates the amount of heat required to change the temperature of a mass unit of a substance by one degree. High heat value indicates the promising potential of reuse for calcined brick production as less coal or fuel materials would be added during the firing of calcined bricks.
In this study, the characteristic of the untreated supernatant was evaluated in (). In general, its quality did not meet the requirement of domestic wastewater effluent, in particular in terms of suspended solids, organic matter and microorganisms. However, it showed evidence that the heavy metals were not present in the supernatant, but all settled in the sediment. For brick production, the supernatant can be reused to mix the materials. This was consistent with some previous studies elsewhere (Chang et al. Citation2020; Hoang and Nguyen Citation2017).
Effect of mixing ratio additives on organic matter concentration
As mentioned above, organic matters as well as the thermal energy/heating values shall be considered after blending with additives since these characteristics are related directly to the brick production process.
It can be seen clearly in the difference in the impact of bio-mass waste and construction waste (separated by the vertical green line). As the bio-mass wastes are rich in organic matters, the addition of them increased the organic matter in the mixture up to 80%, and most of them were above the horizontal green line. The organic matters were quite proportional to the mixing ratio but not in the case of the rice husk additive. Just a slight amount of rice husk blended with the DSL (sludge: additive ratio of 1:7) can increase the organic matters to almost 80%, and it kept the same no matter how much rice husk was further added. The high content of organic matters can be considered potential fuel with its high calorific value (Bożym and Siemiątkowski Citation2018), which would be valued during the incineration for producing calcined bricks.
Figure 3. Organic matters in the DSL with and without additives (DSS: dredged sludge from sewers; CCP: corn core powder, RHP: rice husk powder, SBP: sugarcane bagasse powder, and PSP: peanut shell powders; AAC: autoclaved aerated concrete and SP: stone powder).
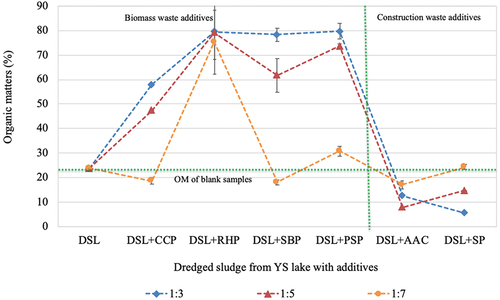
renders the strong correlation between organic matter and heat values of the dredged sludges (R2 = 0.999). According to this linear relationship, the heat values increased from 1800 kCal/kg to 3250 kCal/kg when the OM increased from 20 to 35%. If the organic matter of sludge is 80% after adding the biomass waste additives as in , the heat value can be much higher than 4000 kCal/kg. It should be noted that the heat value was measured when the moisture content of samples was less than 10%.
Assuming this sludge is mixed with raw materials (i.e., clay and additives) for the brick production. The normal heat value of the mixture required for making the brick (ER) is about 1200 kCal/kg. Depending on the mixing ratio of sludge with raw materials, the heat value of the mixture (Em) was determined.
Where: Er: Required heat value for making the brick, according to the heat consumption of similar brick production, Er = 1200 kcal/kg; Em: Heat value of mixture (sludge and additive); Ei: Heat value of material in the mixture; fi: Ratio of material
in the mixture and m: sum of ratio
The additional energy supplement (kCal/kg) ES - the difference of ER and Em, shall be calculated as in . For instance, if the mixing ratio is 1S:1 R (S: sludge, R: raw materials), the heat supplement shall be about 150 kCal/kg providing that the heat value of dry sludge is about 1800 kCal/kg () and heat value of raw materials is approximately 300–400 kCal/kg (Hoang and Nguyen Citation2017). Ideally one would expect to supply as less energy for heating as possible for energy saving. Thus, it is acceptable with the mixing ratios of 1S:1 R (50% sludge) or 1S:2 R (33% sludge) (the two lowest energy supplies) for brick production. One thing should be noted that calculated for sludge without any modification and the OM content is 20%. Thus, for the modified one with higher OM content, the energy supplement could even be less.
Although the presence of organic matters helps enhance the combustion capability, it may lead to more μm-scale pores and large macro defects on the surface of brick after the organic matters are burned. It was claimed that the high content of organic matter in raw sludge caused a decrease in mechanical strength and a delay in the hydration process (Chang et al. Citation2020). Despite these defects, the properties of all brick samples such as compressive strength, water absorption and freeze-thawing resistance still met the standard requirement of brick products (Zabaniotou and Theofilou Citation2008). Furthermore, a high percentage of organic matters would help produce lightweight bricks (Chiang et al. Citation2009), a trend in making brick industry lately. They found that with an increased amount of rice husks added up to 20%, the open porosity of bricks increased from 5% to 38% which led to an increase in water absorption and decrease in bulk density and thermal conductivity property.
For the case of blending construction wastes which contain mostly inorganic matters (on the right side of the vertical green line), their organic matter of the mixtures was almost below the organic matter of blank samples. The organic matter decreased from 20% to 5% for the case of using SP with a ratio of 1:3 (See for detail). The impact of the mixing ratio, however, did not show clearly in the case of blending with construction wastes.
Thus, it was evident from these results that the content of organic matters would vary depending on the types of additives. Should the final products be non-calcined bricks that had minimum organic matter to reduce the smell during production, inorganic additives such as construction waste can be used. Should the final products be calcined bricks which require high potential fuel in the materials, or for lightweight brick development, organic additives such as bio-mass waste can be applied, however, maximum of 50% of sludge can be added to the material mixture for brick production due to energy saving as found in .
Effect of additives on dewaterability
presents the effect of additive types and additive-sludge mixing ratio on the reduction of moisture contents of the testing sludges.
Figure 6. Moisture contents of testing DSL with mixing ratio: (A) 1:3, (B) 1:5 and (C) 1:7 (DSS: dredged sludge from sewers; CCP: corn core powder, RHP: rice husk powder, SBP: sugarcane bagasse powder, and PSP: peanut shell powders; AAC: autoclaved aerated concrete and SP: stone powder).
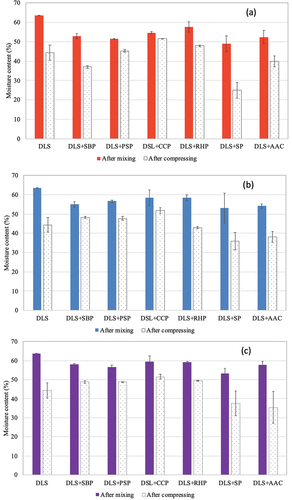
While the different types of additives (bio-wastes and construction wastes) showed a clear impact on organic matter in the DSL, they showed almost no distinctive trend in the moisture content after mixing (). However, upon compression, the construction waste additive showed more influence on the moisture content reduction, i.e., moisture content decreased from 62 ± 0.14% to 57 ± 1.89% after mixing with construction waste and then to 35 ± 8.31 after compressing. This led to a total reduction of up to 30% with a standard deviation.
Among the organic additives, the moisture content reduction was only significant with the mixing ratio of 1:3 and 1:5 by weight. More specifically, the sugarcane bagasse additive performed the best at a mixing ratio of 1:3 by weight (i.e., moisture content reduced from 62% to 53 ± 1.26% after mixing and 37 ± 0.67% after compression), and rice husk powder showed best at the mixing ratio of 1:5 with moisture content reduction from 62% to 58 ± 1.47% after mixing and 43 ± 0.65% after compression. As it can be seen that the organic and inorganic additives have distinctive impacts on the removal of water from sludges. It proved the different bind and release mechanisms of water molecules from sludges. The organic additive utilized in this study were rich in cellulose and partly hemicelluloses and lignin; which were claimed to be skeleton builders and made the sludge more porous after mixing, thus they formed channels for the outflow of the bound water from sludges (Liang et al. Citation2018). While the construction waste contains mostly inorganic minerals including quartz (a hard, crystalline mineral composed of silica), tobermorite Ca5Si6O16(OH)2.4 H2O and calcium silicate hydrate (C-S-H). The physical characteristic makes AAC quite hydrophilic which has high adsorption to water. Once contact with the highly moisturized sludge, it would absorb quickly the water and release water only under the compression pressure. To further understand the water binding, we have checked the SEM images of the testing sludges ().
Figure 7. SEM images (magnification of 1000X) of raw and blended dredged sludge from lake. DSL: Dredged sludge from lake (A), DSL + AAC: autoclaved aerated concrete 1:7 (B); DSL + SP: stone powder 1:3 (C) and DSL + PSP: peanut shell powders 1:7 (D).
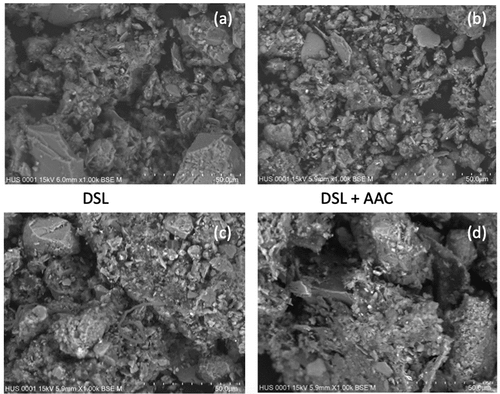
Figure 8. Acceptable mixing ratio for DSL in terms of oxides (red line: the standard values for corresponding oxide contents in the brick).
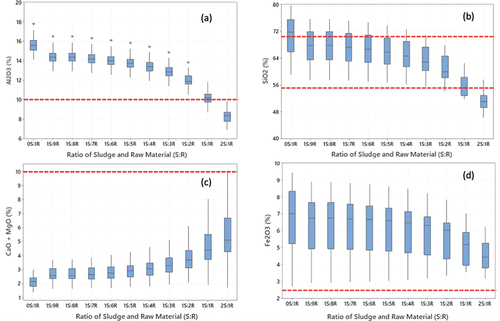
It can be seen from that with the same magnification of 1000 times, there are some noticeable differences between DSL before and after blending with additives, and differentiation between the ones blended with bio-waste () and ones with construction waste (). For the original sludge (), the materials showed some macro pores and holes on the surface. Upon blending with agro-waste like peanut shell powder, many big aggregates were formed, leaving more pores on the surface. It was similar to the previous findings (Guo et al. Citation2019; Xiong et al. Citation2017). The porous surface formed channels for the outflow of the bound water from sludge (Guo, Jiang, and Pang Citation2019). In contrast, the constructed waste, which includes mostly inorganic matters, seemed to be discrete and did not attach to the sludge to form bigger aggregates, but adhered to every porous surface of the sludge. There were lots of tiny particles, which seemed to be inorganic ones, presenting on the surface. Thus, fewer pores were seen in . Due to the different ways of contacting sludge particles, organic and inorganic additives have an impact differently with the bound water of the sludge solids. One thing can be sure that inorganic additives help release water better after compression in all mixing ratios () as their bound water with sludge might be more ready to break and release than the bound water of sludge and organic additives. The moisture content reduction really depended on the water affinity and release of the additives.
Chemical characteristics of the testing sludges
As found in the above results, the construction waste had much better impact on the moisture reduction for the DSL, they were selected for further chemical examination. This was to evaluate the impact of various additives on the sludge characteristics as materials for brick production.
The oxide components did not alter that much, except for the case of adding stone powder (M2) (see ). As the main component of stone powder is CaO, it enriched the blended sludge samples with CaO concentration increasing from 6.25 to 21.65% by wt. It is noted that blending with stone powder helped lower the heavy metal concentrations, up to 78.6%, 63.12%, 78.34% and 20.35% for Cr, Co, Ni and Pb, respectively. While many heavy metal concentrations were increased upon mixing with AAC. It seems that the stone powder had a better sorption capacity to heavy metals than that of AAC powder possibility due to the enriched CaO component in the stone powder. The heavy metal adsorption abilities when blending waste with sludge were also found in a previous study by Liu (Citation2018). It is the adsorption capability of stone powder that makes it a better choice for sludge dewatering enhancement for brick production compared to AAC material. In comparison with the national standard for sediment quality, the presence of some heavy metals, such as As, Zn, was still higher than the accepted values.
Table 4. Chemical characteristics of samples.
One attempt was made to theoretically calculate the optimum mixing ratio of DSL and raw materials for brick production that still maintains the best quality of the bricks (). As regulated in the technical standard for the calcined bricks in Vietnam, the acceptable percentage of Al2O3 in the brick is from 10–25%, of SiO2 is from 55–70%, of CaO and MgO is less than 10% and of Fe2O3 is from 2.5–10%. According to , the suitable mixing percentage of DSL sludge would be <33% for Al2O3, 20–33% for SiO2, 0–100% for CaO and MgO and Fe2O3. Overall, the optimum percentage of sludge in the mixture to meet all the oxide contents in the brick shall be 20–33%. This is consistent with the finding of Hoang and Nguyen (Citation2017), when mixing with clay to produce calcined bricks that the maximum of urban dredge sludge was 30% by weight. In combination with the optimum sludge percent for energy saving of 30–50% (), the best sludge percent used for calcined brick production would be about 30%.
Statistical analysis
This section will analyze the impact of types of additives (corn core, rice husk, peanut shell, sugarcane bagasse, stone powder and AAC) and mixing ratio of sludge and additives (1:3, 1:5 and 1:7) in the reduction of moisture contents after mixing and then after compression. The two-way ANOVA and t-test from the software StatPlus:mac LE v7.3.31 (AnalystSoft Inc., USA) were conducted for this purpose. presents the correlation matrix of the variables, while shows the two-way ANOVA results (p-value, n = 36).
Table 5. Correlation matrix.
Table 6. Two-way ANOVA results (p value, n = 36) showing the impact on moisture content by different additives and mixing ratio, based on Turkey Kramer approach.
It was clearly shown in the that the type of additives had significant impacts on moisture content either after mixing or after compression while the mixing ratio had a substantial influence on moisture content after mixing only. This was revealed better in the detailed interaction for individual additives with more cases having p-values less than 0.05.
Conclusion
It is the first-time dredged sludge from lake (lake sediment) was evaluated in terms of mechanical dewaterability upon mixing with four different bio-wastes, including rice husk, corn core, sugarcane bagasse and peanut shell and two kinds of construction waste (AAC and stone waste).
The results showed that blending with stone powder helped reduce the moisture content by up to 5% and up to 30% after mechanical compression. Due to the adsorption capacity, the stone powder also lowered the heavy metal (Pb, Cr) concentrations in the sludges to meet the standard for soil quality. Organic matters in the construction waste-blended sludges decreased from 20% to only 5%. Among the bio-wastes, the optimum mixing ratio for sugarcane bagasse and rice husk additives were 1:3 and 1:5 by weight, respectively, with moisture content reduction up to 10% after mixing and 25% after compression. The organic matters in the sludge increased from 20% up to 80% when adding the bio-wastes. Depending on whether calcined bricks or non-calcined bricks are developed, the selection of waste type (bio-waste or construction waste) will be implemented. Should this sludge be used for calcined brick, the optimum percent of sludge in the mixture is about 30% for energy saving and chemical quality control.
Statistical analysis revealed that the type of additives had significant impacts on moisture content reduction either after mixing or after compression while the mixing ratio had a substantial influence on moisture content after mixing only.
Currently, when the source of clay has become limited, the partial replacement of clay with other sources such as dredged sludge and construction wastes could be tremendously vital. In the next step of brick production with blended dredged sludge and corresponding wastes, it is necessary to understand the optimal percentage of sludge, waste and clay to obtain the bricks with acceptable compressive strength and shrinkage. This practical research and application could definitely help to boost sustainable development and circular economy during the manufacturing process of construction materials.
Acknowledgment
The authors would like to express high acknowledgment to Science and Technology Program: Environment and Resources (Research project Grant No 01C-09/-2019-3) from the Hanoi Department of Science and Technology, Ministry of Science and Technology, Vietnam. We kindly thank Hanoi Sewerage and Drainage Limited Company for sludge sampling during the project. The support in the lab of student’s scientific research group from Hanoi University of Civil Engineering (co-research group) was also appreciated.
Disclosure statement
No potential conflict of interest was reported by the author(s).
Data availability statement
The data that support the findings of this study are available from the corresponding author, upon reasonable request.
Additional information
Notes on contributors
Huyen T.T. Dang
Huyen T.T. Dang is an Associate Professor at Faculty of Environmental Engineering, Hanoi University of Civil Engineering (HUCE). She received a bachelor’s degree in Environmental Engineering from HUCE in 2002. She did her post graduate study at University of Ottawa (Canada) and obtained her Doctoral Degree in 2009. Her research fields of interest are membrane technology, water and waste reuse, sustainable drainage and green building.
Lan T.N. Pham
Lan T.N. Pham is an Associate Professor at Faculty of Chemistry and Environment, Thuy Loi University. She received a bachelor’s degree in Hydrology and Environment from Thuy Loi University in 1993. She did her post-graduate study and achieved the Degree of Master of Science in Soil and Water Engineering at Karlsruhe University in 1996. She did her PhD study at Thuy loi University and obtained her Doctoral Degree in 2012. She is interested in doing research in some areas including water quality management; water and wastewater treatment; solid waste recycle and sustainable drainage.
Thuy T. Pham
Thuy T. Pham is an Associate Professor at Faculty of Environmental Sciences, University of Science, Vietnam National University (VNU). She received a bachelor’s degree in Environmental Engineering from Hanoi University of Civil Engineering in 2003. She did her post graduate study at Katholieke Universiteit Leuven (Belgium) and obtained her Doctoral Degree in 2012. Her research fields of interest are water and waste treatment, waste utilization toward circular economy.
Huan X. Nguyen
Huan X. Nguyen is a doctor and researcher at Faculty of Environmental Sciences, University of Science (HUS), Vietnam National University (VNU) since 2006. He received a bachelor’s degree in Soil science from VNU in 2002 and a master’s degree in Environmental of Sciences in 2012. He gained his Doctoral degree from VNU in 2020. He is interested in analysis of elements and materials in the Chemistry lab for environment-related research projects.
Nga T.H. Tran
Nga T.H. Tran is a doctor and researcher at at Faculty of Environmental Sciences, University of Science (HUS), Vietnam National University (VNU) since 2004. She received her bachelor’s degree in Biology from VNU in 2004 and her doctoral degree in Biochemistry from VNU in 2010. Her research of interest is biochemistry technologies and environmental microorganism.
Khai M. Nguyen
Khai M. Nguyen is an Associate Professor at Faculty of Environmental Sciences, University of Science, Vietnam National University, Hanoi (VNU). He received a bachelor’s degree in Biology from VNU University of Science in 1996. He did her post graduate study at Swedish University of Agricultural Science and obtained his Doctoral Degree in 2007. He is interested in environment, green technology and waste utilization.
References
- Beddaa, H., I. Ouazi, A. Ben Fraj, F. Lavergne, and J.-M. Torrenti. 2020. Reuse potential of dredged river sediments in concrete: Effect of sediment variability. J. Clean. Prod. 265:121665. doi:10.1016/j.jclepro.2020.121665.
- Bożym, M., and G. Siemiątkowski. 2018. Characterization of composted sewage sludge during the maturation process: A pilot scale study. Environ. Sci. Pollut. Res. 25 (34):34332–42. doi:10.1007/s11356-018-3335-x.
- Cai, M., Q. Wang, G. Wells, D.D. Dionysiou, Z. Song, M. Jin, J. Hu, S.-H. Ho, R. Xiao, Z. Wei, et al. 2019. Improving dewaterability and filterability of waste activated sludge by electrochemical Fenton pretreatment. Chem. Eng. J. 362:525–36. doi:10.1016/j.cej.2019.01.047.
- Chang, Z., G. Long, J.L. Zhou, and C. Ma. 2020. Valorization of sewage sludge in the fabrication of construction and building materials: A review. Resour. Conserv. Recycl. 154:104606. doi:10.1016/j.resconrec.2019.104606.
- Chen, D., Y. Dou, Q. Tang, Y. Huang, M. Song, J. Zhou, and L. Fu. 2019. New insight on the combined effects of hydrothermal treatment and FeSO4/Ca(ClO)2 oxidation for sludge dewaterability improvement: From experimental to theoretical investigation. Fuel Proc. Technol. 197:106196. doi:10.1016/j.fuproc.2019.106196.
- Chiang, K.Y., P.H. Chou, C.R. Hua, K.-L. Chien, and C. Cheeseman. 2009. Lightweight bricks manufactured from water treatment sludge and rice husks. J. Hazard. Mater. 171 (1–3):76–82. doi:10.1016/j.jhazmat.2009.05.144.
- Dai, Q., N. Ren, L. Ma, P. Ning, G. Qu, Z. Guo, and L. Xie. 2018. Research on dewaterability and properties of sewage sludge under modified phosphogypsum and acetic acid pretreatments. Biores. Technol. 264:268–76. doi:10.1016/j.biortech.2018.05.078.
- Guo, J., J. Du, P. Chen, X. Tan, X. Huang, P. Gan, and L. Fu. 2016. Enhanced efficiencies of sludge dewatering and domestic wastewater treatment by using the bioflocculant from rice stover. Water Environ. J. 31 (1):120–26. doi:10.1111/wej.12221.
- Guo, J., S. Jiang, and Y. Pang. 2019. Rice straw biochar modified by aluminum chloride enhances the dewatering of the sludge from municipal sewage treatment plant. Sci. Total Environ. 654:338–44. doi:10.1016/j.scitotenv.2018.10.429.
- Guo, Z., L. Ma, Q. Dai, J. Yang, R. Ao, and L. Wang. 2019. Dewatering performance of sewage sludge under pretreatment with modified corn-core powder. Sci. Total Environ. 684:402–12. doi:10.1016/j.scitotenv.2019.05.366.
- Hamood, A., J.M. Khatib, and C. Williams. 2017. The effectiveness of using Raw Sewage Sludge (RSS) as a water replacement in cement mortar mixes containing Unprocessed Fly Ash (u-FA). Constr. Build. Mater. 147:27–34. doi:10.1016/j.conbuildmat.2017.04.159.
- Hanoi Drainage and Sewerage Company (HSDC). 2019. Annual production report. Hanoi, HN: Construction Publisher (in Vietnamese).
- Hoang, V.L., and D.B. Nguyen. 2017. Study on utilization of urban canal sediment to produce fired bricks. Vietnam J. Constr. 38–42. (in Vietnamese).
- Liang, J., J. Huang, S. Zhang, X. Yang, S. Huang, L. Zheng, M. Ye, and S. Sun. 2018. A highly efficient conditioning process to improve sludge dewaterability by combining calcium hypochlorite oxidation, ferric coagulant re-flocculation, and walnut shell skeleton construction. Chem. Eng. J. 361:1462–78. doi:10.1016/j.cej.2018.10.143.
- Liang, J., S. Huang, Y. Dai, Li, L., Sun, S. 2015. Dewaterability of five sewage sludges in Guangzhou conditioned with Fenton’s reagent/lime and pilot-scale experiments using ultrahigh pressure filtration system. Water Res. 84:243–54. doi:10.1016/j.watres.2015.07.041.
- Liu, C. 2018. Enhancement of dewaterability and heavy metals solubilization of waste activated sludge conditioned by natural vanadium-titanium magnetite-activated peroxymonosulfate oxidation with rice husk. Chem. Eng. J. 359:217–24. doi:10.1016/j.cej.2018.11.139.
- Mininni, G., A. Blanch, F. Lucena, et al. 2015. EU policy on sewage sludge utilization and perspectives on new approaches of sludge management. Environ. Sci. Pollut. Res. 22 (10):7361–74. doi:10.1007/s11356-014-3132-0.
- Nakic, D. 2018. Environmental evaluation of concrete with sewage sludge ash based on LCA. Sustain. Prod. Consum. 16:193–201. doi:10.1016/j.spc.2018.08.003.
- Palermo, M., and D.F. Hays. 2013. Processes, assessment and remediation of contaminated sediments. Sediment dredging, treatment and disposal. 365–91. New York, NY: Springer. doi:10.1007/978-1-4614-6726-7_13.
- Ramachandra, R.H., and C.P. Devatha. 2020. Experimental investigation on sludge dewatering using granulated blast furnace slag as skeleton material. Environ. Sci. Pollut. Res. 27 (11):11870–81. doi:10.1007/s11356-020-07614-w.
- Rashvanlou, B.R., H. Pasalari, A.A. Moserzadeh, and M. Farzadkia. 2020. A combined ultrasonic and chemical conditioning process for upgrading the sludge dewaterability. Inter. J. Environ. Anal. Chem. 1–14. doi:10.1080/03067319.2020.1739668.
- Reis, G.S., B.G. Cazacliu, A. Cothenet, P. Poullain, M. Wilhelm, C.H. Sampaio, E.C. Lima, W. Ambros, and J.-M. Torrenti. 2020. Fabrication, microstructure, and properties of fired clay bricks using construction and demolition waste sludge as the main additive. J. Clean. Prod. 258:120733. doi:10.1016/j.jclepro.2020.120733.
- Świerczek, L., B.M. Cieślik, and P. Konieczka. 2018. The potential of raw sewage sludge in construction industry–a review. J. Clean. Prod. 200:342–56. doi:10.1016/j.jclepro.2018.07.188.
- Tao, S., J. Yang, H. Hou, S. Liang, K. Xiao, J. Qiu, J. Hu, B. Liu, W. Yu, H. Deng, et al. 2019. Enhanced sludge dewatering via homogeneous and heterogeneous Fenton reactions initiated by Fe-rich biochar derived from sludge. Chem. Eng. J. 372:966–77. doi:10.1016/j.cej.2019.05.002.
- Tyagi, V.K., and S.L. Lo. 2013. Sludge: A waste or renewable source for energy and resource recovery? Renew. Sustain. Energy Rev. 25:708–28. doi:10.1016/j.rser.2013.05.029.
- Xin, D., X. Chai, and W. Zhao. 2014. Hybrid cement-assisted dewatering, solidification and stabilization of sewage sludge with high organic content. J. Mater. Cycles Waste Manage. 18 (2):356–65. doi:10.1007/s10163-014-0337-8.
- Xiong, Q., M. Zhou, H. Yang, M. Liu, T. Wang, Y. Dong, and H. Hou. 2017. Improving the dewaterability of sewage sludge using rice husk and Fe2+-sodium persulfate oxidation. ACS Sustainable. Chem. Eng. 6 (1):872–81. doi:10.1021/acssuschemeng.7b03227.
- Xu, W., J. Xu, J. Liu, H. Li, B. Cao, X. Huang, G. and Li. 2014. The utilization of lime-dried sludge as resource for producing cement. J. Clean. Prod. 83:286–93. doi:10.1016/j.jclepro.2014.07.070.
- Yan, M., B. Prabowo, L. He, Z. Fang, Z. Xu, and Y. Hu. 2016. Effect of inorganic coagulant addition under hydrothermal treatment on the dewatering performance of excess sludge with various dewatering conditions. J. Mater. Cycles Waste Manage. 19 (3):1279–87. doi:10.1007/s10163-016-0522-z.
- Yang, G., G. Zhang, and H. Wang. 2015. Current state of sludge production, management, treatment and disposal in China. Water Res. 78:60–73. doi:10.1016/j.watres.2015.04.002.
- Zabaniotou, A., and C. Theofilou. 2008. Green energy at cement kiln in Cyprus-Use of sewage sludge as a conventional fuel substitute. Renew. Sustain. Energy Rev. 12 (2):531–41. doi:10.1016/j.rser.2006.07.017.
- Zhu, Y., Z. Han, X. Liu, J. Li, F. Liu, and S. Feng. 2013. Study on the effect and mechanism of hydrothermal pretreatment of dewatered sewage sludge cake for dewaterability. J. Air Waste Manage. Assoc. 63 (8):997–1002. doi:10.1080/10962247.2013.788458.