ABSTRACT
The precast concrete (PC) method is preferable in construction activities for its short construction time, guaranteed quality, and cost-effectiveness. Most researchers and engineers believe that these benefits are maximized if the PC components are produced at manufacturing plants. However, under similar production conditions, the in-situ production of PC components can save production costs while providing quality equal to or better than in-plant production. Several studies have described the benefits for the cost reduction effects of in-situ production. However, the verification by using case studies was not conducted. The purpose of this study is to analyze the cost reduction effects of the in-situ production of PC elements. For this study, a case project was selected to establish an in-situ production plan and PC columns were produced on site. Then, the cost reduction effects were analyzed using the actual data of the case project. The results of this study will be used as a core for the development of algorithms for in-situ production of PC components.
1. Introduction
The precast concrete (PC) method has been preferred (Kim et al. Citation2013; Hong et al. Citation2017; Lee et al. Citation2015) over traditional methods because it shortens the construction time (Kang Citation2008; Badir, Kadir, and Hashim Citation2002; Chan and Hu Citation2002), guarantees high-quality products (Eastman and Sacks Citation2008; Kale and Arditi Citation2006), and is cost-effective (Polat Citation2008; Yee and Eng Citation2001; Lim, Lee, and Kim Citation2015; Lee, Lim, and Kim Citation2016). Most researchers and engineers believe that these advantages are gained only when the PC components are produced at plants.
However, based on several studies on the in-situ production of PC components, this method is fairly competitive in terms of time management (Jung and Lee Citation1992; Li and Love Citation2000), quality (Lim et al. Citation2011; Lee et al. Citation2011a), and cost (Osman, Georgy, and Ibrahim Citation2003; Ning, Lam, and Lam Citation2010; Abdul-Rahman, Wang, and Eng Citation2011). Although these studies have been theoretically verified, they have not been tested in actual field production of PC members. Therefore, practical verification of these studies is essential.
This study study aims to analyze the cost reduction effects of in-situ PC production. Based on research by Hong et al. (Citation2017) and Lim (Citation2016), we hypothesize that in-situ PC production would be more cost-effective than in-plant PC production. In the building-construction project used in our case study, most of the PC components were supplied from the PC plant, whereas some columns were produced on-site. This study is limited to the long span of heavily loaded buildings, which include a large floor area (≥10,000 m2), a floor height of approximately 10 m or more, and a unit structure with a size of 10 tons or more.
The study proceeds through the following five stages:
Establishment of an in-situ production plan for PC column components subsequent to the selection of a case site.
Implementation of in-situ production of PC columns.
Cost estimation of the in-situ and in-plant production.
Comparison and analysis of the construction costs of in-situ and in-plant production.
Discussion on the quality considerations based on the analysis performed.
2. Literature review
The in-situ production of PC components is more cost-effective than off-site production (Lee et al. Citation2011b; Lee Citation2012; Hong et al. Citation2014; Lim Citation2016), and also improves the product quality (Oh Citation2017). The quality of PC components is determined by the quality of their form, vibration, and curing. The lower quality of in-plant PCs than in-situ PCs (Lim et al. Citation2015; Won et al. Citation2013; Hong et al. Citation2014) might be attributed to their erection immediately after on-site production. In contrast, in-plant PCs can be damaged by the in-yard stocking process, loading, transportation, and unloading at the new site. From this viewpoint, several studies have demonstrated that under the same production conditions, the quality of in-situ PC elements is at least equal to that of in-plant PC elements (Lee et al. Citation2011b; Lee Citation2012; Son, Lim, and Kim Citation2018; Lim Citation2018).
Hong et al. (Citation2014) reported that on-site production can reduce the construction cost by 14.5–21.6%, relative to in-plant production. Moreover, under the same production conditions, the quality of in-situ production can exceed that of in-plant production. Lim (Citation2016) deduced that the construction cost of in-situ production can be reduced by 18.1% from that of in-plant production.
However, most of these studies simulated the results of on-site or in-situ production by computational processes such as system dynamics and genetic algorithms. Although their results were theoretically verified, a physical verification is necessary for assessing the benefits on on-site production in practice.
To clarify, on-site production means the production of PC components in and/or around the site, whereas in-situ production defines production within the working radius of a tower crane, or within the range of a mobile crane without horizontal transportation of the components.
3. In-situ production planning
To confirm the cost reduction effect of the on-site production of PC components, an in-situ production plan was established for the case project (a heavily loaded warehouse building). The contents of the case project are outlined in . In essence, the case project consisted of a reinforced concrete core and a steel roof with a main PC structure of four aboveground stories. The building was loaded at 2.4 ton/m2, and its floor height, long-span width and maximum long-span width were 10 m, 12 m and 24 m, respectively.
Table 1. Construction overview of the building in the case project.
The PC components in the case project were assumed to be wholly supplied by the production plant. To investigate the effect of cost reduction by in-situ production, the initial plans were adjusted so that some of the PC columns were produced on-site. Primarily, the in-situ production of the columns is expected to save costs by preventing failure, as hypothesized in Section 1. The cost-saving effect was confirmed even when the local production quantity was limited. Moreover, if the in-situ production of complicated columns is allowed, simple girders can be applied. Finally, the lead time to produce the girder is increased by the delayed decision-making on the in-situ production experiments, which results in optimum time management.
For efficient in-situ production, this study first analyzes the production cycle of the PC components. The molds were designed to minimize the cost while maximizing the construction time. Second, the PC components were produced and installed within the working radius of the mobile crane. Third, the production site was moved with the erection of the PC components over the specified range.
outlines the planning stages of the in-situ production plant for PC columns. After selecting the feasible PC columns from drawings, the number of molds and the production area were estimated by considering the erection and lead times. Next, the production site of the PC components within the working radius of the mobile crane was decided by reviewing the crane’s specifications and drawings. In this stage, alternative numbers of molds were calculated considering the available areas and lead times. Finally, the cost considerations and erection schedule were determined at the time of establishing the rebar processing plant.
The details of the in-situ production plan are given below.
3.1. Selection of PC columns
In this study, the in-situ production was decided after launching the erection process. Therefore, the number of PC components for in-plant production was already ordered with the necessary adjustments, and the established PC installation schedule was reviewed. The first floor had been installed at the time of planning the in-situ production. The second and third floors required 123 and 117 columns respectively (240 columns in total; see ). Meanwhile, columns of dimensions 0.8 m × 0.8 m × 9 m, each with a concrete volume of 5.76 m3, were selected for the steel molds. To better resolve potential problems during the in-situ production and to increase the cost-saving effect, the column sizes and reinforcement bars were selected to be similar, allowing for the reusability of the molds. When the PC components have different cross sections, the cost-saving effect is largely negated by the small number of productions per mold, as occurs during in-plant production.
3.2. Decisions on production molds and areas
The mold material in the case project was the steel mold used at the PC plant. The initial cost of the steel mold was considerably reduced to the unit formwork cost as the molds were repeatedly reused. Therefore, the minimum number of molds was calculated while considering the construction cost. Based on the PC installation schedule and lead time, an estimated eight molds were required to produce the 240 PC columns in the present work.
The production area of a single production module is usually estimated from the quantity of locally produced PC components meeting the erection plan, a time analysis of the module production method, and the stacking space of the in-situ production plan of the PC components (Lim et al. Citation2016). In this study, the production modules for PC components are assumed to be two cases as shown in . As shown in , the required area included the areas of the steam curing boiler, curing cover, and the stacked columns. For safe and smooth passage by workers, a 0.5-m space was allocated between each production module. As a reference, the boiler’s capacity was determined by PC columns produced in the first instance, and the produced components were stacked into two stories. Under these conditions, the area requirement for producing two columns per module was 117 m2, versus 91 m2 for one column per module. The planned mold layouts of modules A and B are displayed in panels (a) and (b) of , respectively.
3.3. Planning of the in-situ production location
For small buildings, the in-situ production site of PC components is predetermined within the working radius of the crane. However, in the present case project and other large-scale building sites, the PC components are produced at sites of easy erection. For a large precast concrete structure with a wider floor area, the in-situ production plan must ensure a safe working path considering the crane’s productivity. In the case project, the PCs were erected by three mobile cranes: one 450-ton crane and two 550-ton cranes. Therefore, a production plan was established within the working radius generated along the paths of these cranes. The working radii of the 450- and 550-ton cranes deployed at the worksite, with total lengths of 86 m and 90 m respectively when using the boom and jib, were 66 m and 74 m, respectively. As shown in , the PC components were produced within the working radii of the paths generated by the cranes, so no work was expended in horizontally transporting the PC components ()), and no transportation costs were incurred.
Figure 4. Mold operation plan (a) and installation of PC components within the working range of the cranes deployed at the worksite (b).
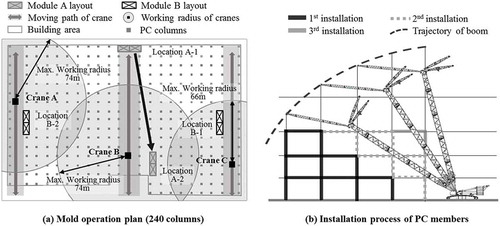
Under the above-mentioned conditions and after reviewing the drawing and erection schedule, it was confirmed that the PC components could be produced within the working radii of the cranes (see ). Four in-situ PC production sites within these short moving distances were selected. In the plan that accommodated the molds and their areas (), 52 and 54 PC components could be produced using module A in locations A-1 and A-2 of ), respectively. Similarly, 58 and 76 components could be produced using module B in locations B-1 and B-2 of ), respectively. When deploying crane B, the production location moved from A-1 to A-2 as the PC components were erected, as shown in .
When the components had already been installed, the PC component furthest from the crane was difficult to install because the upper and lower trajectories of the crane boom were interfered by the already installed components. This problem was solved by a step-like process consisting of three stages, as shown in .
3.4. Planning of rebar work
In the present case project, the PC components were produced on-site from reinforced bars delivered to the site after in-plant prefabrication. As shown in , the concrete was cast and cured after installing the reinforced steel mold bars. The design strength was secured to exceed 70% after stacking the PC components for erection. The rebar work was relegated to the plant for two reasons: (1) the difficulty of performing rebar work in a limited site area, and (2) the shorter working time of in-plant production. In other words, this procedure was intended to reduce the critical path by supplying the in-plant produced rebar in advance (see ).
4. In-situ production of PC elements
The production plan of the PC columns was established considering the conditions of the case site. However, owing to delays in the decision-making process, it was necessary to review the site conditions and the established plans. When reviewing the situation, some of the PC columns on the second floor were already being produced at the plant. Therefore, the lead time of the production must be sufficient for on-schedule installation of the PC components. Because a considerable number of the PC columns planned for in-situ production were being produced at the plant, the production plan of 240 PC columns was reduced to 72 pieces. Considering the lead time of in-situ production, 18 PC columns on the second floor and 54 PC columns on the third floor () were selected for in-situ production.
After reducing the number of in-situ production columns, the production layout plan of was changed and the number of steel molds was reduced to two modules as depicted in . The production lead time that satisfied the PC erection time was considered when calculating the number of steel molds. The selected location of in-situ production accounted for the produced and lifted PC components (). In (a), production was planned inside the building where crane operation was possible, but in the modified plan of , the production occurred outside the building because the smaller number of PC components reduced the required area of the production.
The in-situ production of the PC components proceeded as follows. Once the rebars were installed, the concrete was poured, cured, and stacked as shown in . The rebar installation and concrete pouring was performed to the same level as the plant, and the fresh concrete was made at the site. At the plant, the columns were cured in a steel-frame room, but the on-site curing was aided by plastic fabrics which created an untidy look, as shown in . Therefore, a temporary curing box was devised at the plant, which was lightweight and easy to close and open. After the PC columns were stacked and quality-checked, final touch-ups were performed on columns with partial defects on their surfaces.
The PC components were erected on-site by a sequential process of shacking, lifting, positioning and propping, and unshackling (see ). For reference, the average, minimum and maximum times of erecting one PC column weighing 37.4 tons, determined from 15 time measurements, were 31.8, 20.8 and 46.7 minutes, respectively. The time expended in this process was similar to that of factory-produced PC columns. With the erection time of the PC components included in its operation schedule, one crane can install up to 15 PC columns in an eight-hour working day. As the production site was selected for erection of the PC components, no movement was required during the preparation of lifting, so no preparation time was incurred.
When the components were produced at the plant, the operation efficiency of the PC erection by cranes was lowered by the delay of PC member delivery, waiting for preparation and erection, and interference with other work tasks. Therefore, to deploy the erection crane for in-situ production, the waiting and delay times of the crane were carefully examined and a production schedule was prepared. A layout plan for PC column production was then established within the working radius that required no movement of crane A (). Here, the crane was required to install the rebars, install and remove the side molds, and stack the PC columns. The required work times were eight minutes for the rebar installation (stage ①), 35 minutes for processing the side molds (stage ②) and three minutes for stacking (stage ③). Hence, the total work time was 46 minutes (①+②+③). In this study, the total time of the crane deployment was 92 minutes (46 minutes for each component in the two B modules, completed over two days; see and ). During the in-situ production, the erection crew was additionally tasked with supporting the erection crane; however, this task was not problematic over the 92 minutes of PC column production in two days. In other words, it was confirmed that in-situ production can be fully supported or can use the otherwise unused waiting time of the installation crane.
5. Analysis of cost reduction effects
The costs of in-situ production of the PC components were analyzed and compared with those of in-plant production. The materials, labor, equipment and transport costs, along with the overhead and profit (O&P), were determined for 72 PC column components and are listed in . In this study, the PC cost of in-situ production was based on the actual cost paid on-site, and the in-plant production costs were based on the contract cost with a PC production company. That is, the costs in were not estimated from RS Means or other data. The total costs of the in-plant and in-situ productions were estimated at 200,648 USD and 160,544 USD, respectively. In conclusion, the in-situ production costs were approximately 40,104 USD (20.0%) lower than the in-plant production costs.
Table 2. Total cost analysis of the in-plant and in-situ productions.
In , the material costs in the in-plant and in-situ productions were assumed equal because both productions process the steel molds, concrete, and rebars in the same manner. However, the cost portions differed, being 50.1% and 62.7% in the in-plant and in-situ productions, respectively. The significantly higher proportional cost in the in-situ production can be explained by the O&P of suppliers and transportation in the in-plant production, which is avoided in in-situ production.
The labor cost of in-situ production was 59,756 USD, 9,319 USD higher than that of in-plant production. The additional cost was attributed to the manpower required during the pilot production, which utilizes not common labor, but a field engineer with a high wage rate. A crew of five field engineers directly participated in the rebar, steel mold installation, and concreting and curing work. In this endeavor, they identified the problems of in-situ production and established themselves as the core managers of future in-situ production.
To study the cost reduction effect of in-situ PC production, the engineers trained as multifunctional workers for two weeks, performing production work directly in the PC plant. The pilot production phase of the research confirmed that after 2–3 weeks of training, common laborers could accomplish in-situ production. This finding validates the use of common laborers on most of the production activities at PC plants. However, to secure the quality of in-situ produced PC components, five or six common laborers per crew should be well trained in the in-situ production process for two or three weeks. Nevertheless, the labor cost of in-situ production was expected to be similar to that of in-plant production.
The in-plant production used overhead and gantry cranes installed at the plant, whereas the in-situ production used idle equipment. Therefore, the calculated fuel cost of in-plant production was 3,150 USD, including the electricity and depreciation costs of the crane usage. In contrast, the fuel cost of in-situ production was only 699 USD; that is, the in-situ production reduced the fuel costs by 2,451 USD. Using the idling crane for erecting PCs on-site also saves the equipment costs, as confirmed in this study.
The in-situ production removed the transportation costs and the O&P costs to the manufacturers who supplied the PC components (). Accordingly, the cost of the PC components was greatly reduced in the in-situ production.
As shown in , the in-situ production of 72 PC columns reduced the production cost by 20% per column, relative to in-plant production. The in-plant and in- situ production costs were estimated as 2,787 USD and 2,320 USD per column, respectively. Under the existing plan, the in-situ production of 240 PC columns lowered the construction cost by 39.4% from the factory supply price (see ).
Costs were reduced by the reusability property of the steel molds. In addition, the costs of transporting the PC components and the O&P of the PC suppliers were greatly reduced or even eliminated by the in-situ production, as shown in . To analyze the cost reduction effect of in-situ production, the break-even point (BEP) was computed for 36 pieces of PC components produced in two steel molds. The results are shown in . When the productivity is fewer than 36 PC columns, the in-situ production is cost-ineffective because the production cost exceeds the in-plant production cost. However, when the number of reusable molds is increased to 40 units and beyond, the in-situ production becomes economically viable. The original plan with a productivity of 240 units can save a maximum of 39.4% in production costs.
As shown in , the in-plant production cost was proportional to the number of columns because the contract price was constant. For the above-mentioned reasons, the unit price of in-situ production decreased with increasing number of columns. In this case project, the BEPs of the in-plant and in-situ productions were 100,332 USD and 100,265 USD, respectively, and the analyzed unit prices were 2,787 USD and 2,785 USD, respectively.
For 72 production units, the in-plant and in-situ production costs were 200,664 USD and 160,560 USD, respectively; for 240 production units, they increased to 668,880 USD and 405,360 USD, respectively. In other words, the production costs of 72 and 240 units were 20% and 39.4% lower in the in-situ production than in the in-plant production.
6. Discussion
A checklist for ensuring the quality of PC components produced on-site was established in accordance with the production and installation guidelines of PCs by the Korea Concrete Institute (KCI). To guarantee the quality of PC components produced on-site, the products must be examined for cracks, breakages, and size- and strength-related anomalies. The inspection items were selected following the PC production and installation guidelines of the KCI, and the standards and inspection methods were prepared. The in-plant and in-situ productions of the PC columns employed the same steel mold and concrete pouring equipment, and their curing systems delivered the same performance. The concrete was cured by heat application at 1000 °C·h for 20 hours, following the curing algorithm proposed by Won et al. (Citation2013), which guarantees high energy efficiency and curing quality. The curing cycle consisted of pre-curing, isothermal curing, and post-curing steps (see ). The PC components produced in-situ by Won et al.’s algorithm were free of cracks and breakages, and met the quality criteria of size and strength. On the other hand, 20 of the in-plant PCs were rejected due to cracks, breakage, and size mismatches, and needed to be replaced. After several studies under the same production conditions, it was concluded that the quality of in-situ produced PCs at least matches that of in-plant produced PCs.
Interviews with PC plant officials confirmed that plant owners do not contract because they cannot cover the overhead of plant operation unless the profits exceed 20% of the production cost (Lim, 2018). In previous researches of in-situ production, the costs were reduced by 14.5–21.6% from those of supply after in-plant production, largely because the in-situ production reduces the transportation cost and O&P of the plant (Lee et al. Citation2011b; Lee Citation2012; Hong et al. Citation2014; Son, Lim, and Kim Citation2018; Lim, 2018). In the present case project, the in-situ production reduced the production cost of 72 columns by 20.0%. For 240 columns, the expected cost reduction is 39.4%. As the number of columns increases, the cost should be further reduced by the higher reuses of the expensive steel molds, and by the lower curing cost and price of mass-produced PC parts.
As respecting the construction time is mandatory, the available area at the site must be reviewed to determine the appropriate number of in-situ production components; the remainder must be produced at the plant (Lim, 2018). If the available area is insufficient, the molds for the PC components should be moved off-site to maintain the erection schedule. In heavily loaded long-span buildings, the components of large floor areas are erected sequentially, so the molds can be moved to sites with no PC components. In other words, the PC components can be simultaneously produced and installed in different places of the worksite. Once the PC components are installed, and the slab concrete poured and cured, the molds can be moved to the upper floor for PC production.
In this test production process, the in-situ production of PC components was feasible both inside and outside the building. During the in-situ production, the design load conditions of most floors of the building were relatively larger than the generated loads. For example, large warehouses like that of the present study have a designed load condition of 2 tons/m2 or more, but the load generated during the production of the PC components was around 1 ton/m2. However, to guarantee the stability of the structure under construction, one must closely examine the production–installation process; in some cases, partial reinforcement of the structures is necessary.
In this study, the in-situ production was limited to the PC columns, but is extendible to PC girders. That is, slender components such as columns and beams can be produced wholly on-site. However, owing to the large space requirement of producing PC slabs such as rib-plus-slab and double-T slabs, in-plant production of these components is usually more advantageous than production within the small space of the worksite.
Finally, to increase the productivity and achieve successful in-situ production, close communication and cooperation between the site engineers are essential. The uninterested and uncooperative behavior of the site engineers was the most difficult part of this test production study. This situation slowed all decisions and resulted in fewer PC columns than originally planned. Nevertheless, the study confirmed that on-site production of PC components such as columns and girders can considerably save the production costs while ensuring a quality at least as high as that of in-plant production.
Most site engineers have negative perceptions about the quality of in-situ produced PC members. Other concerns are interference with erection work, increased number of tasks, and the application of new methods. For this reason, most companies rejected the current proposal of in-situ production. However, one local construction company approved the research team’s persuasion, and drafted a detailed preliminary production plan confirming the large cost reduction effect without sacrificing quality. As the present study verified the effectiveness of in-situ production, it should encourage more application case studies in the future.
7. Conclusion
Whether PC components should be produced in-situ is determined by various conditions, such as the site conditions, compliance with the erection time, number of PC components, and the available area for production and stock yard. This study demonstrated that heavily loaded long-span buildings meet most of these conditions. Three management concepts are proposed for the successful in-situ production of long-span and heavily loaded buildings: (1) an appropriate mold layout that enhances the productivity, (2) the production and installation of PC components within the working radius of the cranes, and (3) movement of the production place to satisfy the previous two rules. After selecting the case study project, these concepts were verified in the production plan of PC columns. The cost reduction and high quality validated the established plans of in-situ production. The following conclusions were drawn from the study.
First, the costs of the in-plant and in-situ productions of 72 columns at the case study site were calculated as 200,664 USD and 160,560 USD, respectively, and those of 240 columns were 668,880 USD and 405,360 USD respectively. In other words, the production costs of 72 and 240 columns were 20% and 39.4% lower, respectively, in the in-situ production than in the in-plant production. This result proves the hypothesis mentioned in the Introduction. Furthermore, the cost reduction ratio increased with increasing quantity of the columns produced in-situ.
Second, 240 PC columns were originally planned for the on-site production, but only 72 columns were actually produced due to delayed decisions at the beginning of the project. Therefore, decision-making affects the production lead time of the PC components and compromises the cost reduction.
Third, many engineers are concerned about the quality of PC components produced in-situ. To verify that the quality is maintained during in-situ production, the in-situ and in-plant produced PC members were inspected for strength, cracks, breakages, shape, and size. All columns produced at the site met the required quality; however, 20 columns produced at the plant were rejected because of to quality problems. Therefore, the quality of the in-situ PC components actually exceeded that of the in-plant components. The present experimental results corroborate the descriptions of previous studies.
The results of this study will contribute to the algorithm development of production of PC components. In practice, a generalized in-situ production might reduce the construction cost. The cost reduction effect can be confirmed more accurately by increasing the number of PC columns produced in-situ. The present study was conducted on a long-span heavily loaded building, but is extendible to regular-size projects or general buildings. Additional case studies on in-situ production would provide a statistical validation and should be attempted in future work.
Disclosure Statement
No potential conflict of interest was reported by the authors.
Additional information
Funding
Notes on contributors
Jeeyoung Lim
Jeeyoung Lim BSc, MSc, PhD studied Construction Engineering and Management at the department of architectural engineering, Kyunghee University in South Korea. She had joined three Korean construction firms, Iksungtech Co., Ltd, Kunwon Architects & Engineers Corp., Universe Top Engineering Architects, for 5 years. She has concentrated on the research such as development of sustainable construction technology and management, production technology of free-form concrete panels, cost management of precast concrete, simulation, optimization, and risk management. Jeeyoung Lim is serving as now a lecturer at California State University Long Beach in USA.
Kwangheon Park
Kwangheon Park BSc, MSc, PhD, Professor studied Nuclear Engineering and received B.S. at the department of nuclear engineering, Seoul National University. He had received M.S. and Ph.D in U.C.Berkely majoring Nuclear Engineering. He have joined as a faculty member in the department of nuclear engineering, Kyung Hee University since 1989. Professor Park was the Head of the Center of Research Facilities, Kyung Hee Univ. (2007-2013), Vice-Dean of the College of Engineering, Kyung Hee Univ. (2009-2013), Dean of Academic Affairs, Global campus, Kyung Hee Univ. (2013-2018). He has been the Head of Future Nuclear Research Center funded by National Research Foundation of Korea since 2019. Park has concentrated on the research such as decontamination using supercritical fluids, analysis of nuclear fuel materials, regulations related to dry storage of used nuclear fuels, and quantitative analysis of engineering issues.
Seunghyun Son
Seunghyun Son BSc, MSc is studying in architectural engineering from Kyung Hee University, as a student of doctoral course, and is currently a lecturer at University of Ulsan in South Korea. In the field of construction project management and construction engineering, he is actively conducting research on simulation, optimization, and risk management of building projects and qualitative analysis using machine learning technique. In addition, he has participated in the development of reinforcement method against seismic impact and free-form concrete panel production technology for about five years.
Sunkuk Kim
Sunkuk Kim BSc, MSc, PhD, PE, Professor studied Construction Engineering and Management at the department of architectural engineering, Seoul National University. He had joined three Korean construction firms, Dealim Industrial Co., Ltd., Deadong Coporation Co., Ltd. and Seoktop Construction Co., Ltd., for 12 years. As a visiting scholar, he researched about the construction management & organization at the department of civil engineering, Stanford University from 1994 to 1995. Since September, 1995, he has served at Kyung Hee University as a professor. Kim served as a dean of the Graduate School of Technology Management from 2015 to 2018. In addition, he was an organization chair in three international conferences including ICCEPM (2009) and MOC (2015). He was also a vice president of Korea Institute of Ecological Architecture and Environment and Korean Council on Tall Buildings and Urban Habitat (K-CTBUH). He also served as a guest editor for two special issues of Modular & Offsite Construction (2017) and Global Convergence in Construction (2011), Automation in Construction and special issue of Global Convergence in Construction (2010), International Journal of Strategic Property Management. Currently he is the guest editor for special issue of Technology and Management for Sustainable Buildings and Infrastructures, Sustainability. Kim has concentrated on the research such as health performance evaluation of buildings, development of sustainable construction technology and management, simulation, optimization and risk management, construction information technology. Especially, for about a decade, he has participated in the development of SMART frame, a sustainable structural system, and production technology of free-form concrete panels.
References
- Abdul-Rahman, H., C. Wang, and K. S. Eng. 2011. “Repertory Grid Technique in the Development of Tacit-Based Decision Support System (TDSS) for Sustainable Site Layout Planning.” Automation in Construction 20 (7): 818–829. doi:10.1016/j.autcon.2011.02.004.
- Badir, Y. F., M. A. Kadir, and A. H. Hashim. 2002. “Industrialized Building Systems Construction in Malaysia.” Journal of Architectural Engineering 8 (1): 19–23. doi:10.1061/(ASCE)1076-0431(2002)8:1(19).
- Chan, W. T., and H. Hu. 2002. “Constraint Programming Approach to Precast Production Scheduling.” Journal of Construction Engineering and Management 128 (6): 513–521. doi:10.1061/(ASCE)0733-9364(2002)128:6(513).
- Eastman, C. M., and R. Sacks. 2008. “Relative Productivity in the AEC Industries in the United States for On-Site and Off-Site Activities.” Journal of Construction Engineering and Management 134 (7): 517–526. doi:10.1061/(ASCE)0733-9364(2008)134:7(517).
- Hong, W. K., G. Kim, C. Lim, and S. Kim. 2017. “Development of a Steel-Guide Connection Method for Composite Precast Concrete Components.” Journal of Civil Engineering and Management 23 (1): 59–66. doi:10.3846/13923730.2014.975740.
- Hong, W. K., G. Lee, S. Lee, and S. Kim. 2014. “Algorithms for In-Situ Production Layout of Composite Precast Concrete Members.” Automation in Construction 41: 50–59. doi:10.1016/j.autcon.2014.02.005.
- Jung, H. T., and M. S. Lee. 1992. “A Study on the Site-Production Possibility of Prefabricated PC Components.” Proceeding of the 1992 Autumn Annual Conference of the Architectural Institute of Korea 12 (2): 629–636.
- Kale, S., and D. Arditi. 2006. “Diffusion of ISO 9000 Certification in the Precast Concrete Industry.” Construction Management and Economics 24 (5): 485–495. doi:10.1080/01446190600601594.
- Kang, H. J. 2008. “A Study of Ship Design Process Optimization in A Concurrent Engineering Environment.” Master’s diss., Seoul National University, Republic of Korea.
- Kim, S., W. K. Hong, J. H. Kim, and J. T. Kim. 2013. “The Development of Modularized Construction of Enhanced Precast Composite Structural Systems (Smart Green Frame) and Its Embedded Energy Efficiency.” Energy and Buildings 66: 16–21. doi:10.1016/j.enbuild.2013.07.023.
- Lee, D., C. Lim, and S. Kim. 2016. “CO2 Emission Reduction Effects of an Innovative Composite Precast Concrete Structure Applied to Heavy Loaded and Long Span Buildings.” Energy and Buildings 126: 36–43. doi:10.1016/j.enbuild.2016.05.022.
- Lee, G. J. 2012. “A Study of In-Situ Production Management Model of Composite Precast Concrete Members.” PhD diss., Kyung Hee University, Republic of Korea.
- Lee, G. J., J. K. Joo, S. H. Lee, and S. K. Kim. 2011b. “A Basic Study on the Arrangement of In-Situ Production Module of the Composite PC Members.” Proceeding of the 2011 Autumn Annual Conference of the Korea Institute of Building Construction 11 (2): 29–30.
- Lee, G. J., S. H. Lee, J. K. Joo, and S. K. Kim. 2011a. “A Basic Study of In-Situ Production Process of PC Members.”.” Proceeding of the 2011 Autumn Annual Conference of the Architectural Institute of Korea 31 (2): 263–264.
- Lee, S., W. K. Hong, C. Lim, and S. Kim. 2015. “A Dynamic Erection Simulation Model of Column-Beam Structures Using Composite Precast Concrete Components.” Journal of Intelligent & Robotic Systems 79 (3): 537–547. doi:10.1007/s10846-014-0115-9.
- Li, H., and P. E. Love. 2000. “Genetic Search for Solving Construction Site-Level Unequal-Area Facility Layout Problems.” Automation in Construction 9 (2): 217–226. doi:10.1016/S0926-5805(99)00006-0.
- Lim, C. 2016. “Construction Planning Model for In-Situ Production and Installation of Composite Precast Concrete Frame.” PhD diss., Kyung Hee University, Republic of Korea.
- Lim, C., S. Lee, and S. Kim. 2015. “Embodied Energy and CO2 Emission Reduction of a Column-Beam Structure with Enhanced Composite Precast Concrete Members.” Journal of Asian Architecture and Building Engineering 14 (3): 593–600. doi:10.3130/jaabe.14.593.
- Lim, C. Y., J. K. Joo, G. J. Lee, and S. K. Kim. 2011. “In-Situ Production Analysis of Composite Precast Concrete Members of Green Frame.” Journal of the Korea Institute of Building Construction 11 (5): 501–514. doi:10.5345/JKIBC.2011.11.5.501.
- Lim, J., W. Cho, T. O. Lee, and S. Kim. 2016. “A Basic Study of Process and Layout for In-Situ Production of Precast Concrete Members.” Proceeding of the 2016 Autumn Annual Conference of the Architectural Institute of Korea, Architectural Institute of Korea 36 (2): 945–946.
- Lim, Jeeyoung 2018. “A risk Management Model for In-situ Production of Precast Concrete Members Focused on Time and Cost Using System Dynamics, PhD diss., Kyung Hee University, Republic of Korea.
- Ning, X., K. C. Lam, and M. C. K. Lam. 2010. “Dynamic Construction Site Layout Planning Using Max-Min Ant System.” Automation in Construction 19 (1): 55–65. doi:10.1016/j.autcon.2009.09.002.
- Oh, O. 2017. “A Model for Production and Erection Integration Management (PEIM) of Large Scale PC Structures Using System Dynamics.” PhD diss., Kyung Hee University, Republic of Korea.
- Osman, H. M., M. E. Georgy, and M. E. Ibrahim. 2003. “A Hybrid CAD-Based Construction Site Layout Planning System Using Genetic Algorithms.” Automation in Construction 12 (6): 749–764. doi:10.1016/S0926-5805(03)00058-X.
- Polat, G. 2008. “Factors Affecting the Use of Precast Concrete Systems in the United States.” Journal of Construction Engineering and Management 134 (3): 169–178. doi:10.1061/(ASCE)0733-9364(2008)134:3(169).
- Son, S., J. Lim, and S. Kim. 2018. “Planning Algorithms for In-situ Production of Free-form Concrete Panels.” Automation in Construction 91: 83–91. doi:10.1016/j.autcon.2018.03.006.
- Won, I., Y. Na, J. T. Kim, and S. Kim. 2013. “Energy-Efficient Algorithms of the Steam Curing for the in Situ Production of Precast Concrete Members.” Energy and Buildings 64: 275–284. doi:10.1016/j.enbuild.2013.05.019.
- Yee, A. A., and P. H. D. Eng. 2001. “Structural and Economic Benefits of Precast/Prestressed Concrete Construction.” PCI Journal 46 (4): 34–43. doi:10.15554/pcij.07012001.34.42.