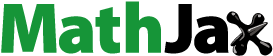
ABSTRACT
An experimental investigation was conducted to explore the flexural behaviour of reinforced beam made with dune sand (DS) from Gurbantunggut desert in northwest China’s Xinjiang province. In order to study the influence of DS replacement levels on the engineering properties of dune sand concrete (DSC) beam, the mechanical properties of DSC and the flexural behaviour of DSC beam were examined with the DS replacement levels ranged from 0% to 80%. Based on the test results, the equations for DSC were proposed to describe the effect of DS replacement levels on mechanical properties of DSC. Meanwhile, the crack pattern and failure modes of DSC beams were investigated, the formula to calculate flexural strength of DSC beam was established, and the concrete strain, strains in reinforcement and load–deflection curve of beams were discussed.
1. Introduction
Due to the scarcity of aggregates in the areas where aggregate resources are in short supply for environmental reasons, there has been a growing interest in utilization of dune sand (DS) in the production of concrete in structural engineering (Zhang et al. Citation2006; Al-Harthy et al. Citation2007; Bouziani, Bederina, and Hadjoudja Citation2012; Zaitri et al. Citation2014; Belferrag, Kriker, and Khenfer Citation2013; Abu Seif et al. Citation2016; Alhozaimy et al. Citation2014; Alawad et al. Citation2015; Jiang et al. Citation2016; Luo et al. Citation2013; Lee, Park, and Kim Citation2016). The Xinjiang province is located in the northwest of China, and nearly a quarter of Xinjiang is covered with DS due to dry continental climatic conditions (Wang, Xiao, and Li Citation2007), and the region of Xinjiang is characterized by a lack of fine natural aggregate resources. Therefore, using DS as a fine aggregate resource will provide an alternative solution to the problem.
So far, numerous studies have been done on ordinary concrete and its components (Sallam Citation2010; Sallam et al. Citation2010; Abou El-Mal, Sherbini, and Sallam Citation2015; Hawileh et al. Citation2015; Abdalla et al. Citation2016; Abou El-Mal, Sherbini, and Sallam Citation2018). However, the utilization of DS in concrete would improve the mechanical properties of concrete (Zhang et al. Citation2006). Therefore, several researches on the various properties of DSC were carried out. The early research on concrete made with DS was carried out by Zhang et al. (Citation2006) in China’s Inner Mongolia province, and it concluded that the properties of DSC were different when the DS came from different desert regions. Al-Harthy et al. (Citation2007) studied the mechanical properties and workability of concrete made with DS in Oman, and tests found that the mechanical strength of dune sand concrete (DSC) was similar to that of conventional natural aggregate concretes (NAC), when the concrete mixes were designed properly. Bouziani, Bederina, and Hadjoudja (Citation2012) researched the usage of DSC in construction in Saharan regions of Algeria, and an optimal content of DS was obtained. Zaitri et al. (Citation2014) optimized the composition of a high-performance concrete and developed high-performance concrete mixed with grinded DS and limestone rock in Algeria. Belferrag, Kriker, and Khenfer (Citation2013) used waste metal fibres to improve the compressive strength of DSC and cement mortar. Abu Seif et al. (Citation2016) studied the mortar and concrete made with DS in the area of Saudi Arabia, and tests indicated that the workability and compressive strength of the DSC and cement mortar were both suitable when the volume of sand did not exceed 50% of the total fine aggregate. Alhozaimy et al. (Citation2014), Alawad et al. (Citation2015) and Jiang et al. (Citation2016) analysed the microstructure of DSC by XRD and SEM, and tests revealed the correlation between the compressive strength and the CaO/SiO2. Luo et al. (Citation2013) studied on the properties of concrete made with DS from Australian deserts, and results showed that the performance of DSC would vary according to the S/C ratio. Lee, Park, and Kim (Citation2016) investigated the drying shrinkage cracking of DSC and revealed the correlation between compressive strength and DS/FA.
Beam is one of the important components of the structure, so numerous studies have been carried out in previously literatures (Sallam Citation2010; Sallam et al. Citation2010; Meraj, Pandey, and Rao Citation2014; Abou El-Mal, Sherbini, and Sallam Citation2015; Bhashya et al. Citation2015; Gopinath, Murthy, and Iyer Citation2015; Hawileh et al. Citation2015; Abdalla et al. Citation2016; Evangelista and de Brito Citation2017; Abou El-Mal, Sherbini, and Sallam Citation2018; Balaji and Thirugnanam Citation2018; Prusty, Patro, and Mohanty Citation2018; Sunayana and Barai Citation2018). However, comparably rare research on the flexural behaviour DSC beams has been carried out.
Therefore, the primary objective of this study was to study the effect of DS replacement levels on mechanical properties of DSC beam. The mechanical properties of DSC and the flexural behaviour of DSC beam were examined with the DS replacement levels ranged from 0% to 80%. Furthermore, a formula was proposed to calculate the flexural strength of DSC beam.
2. Materials and experimental methods
2.1. Concrete mixtures and properties
In this study, ordinary Portland cement with grade 42.5 and the fly ash with grade I were used for all the concrete mixtures according to Chinese specification (GB50081) (Citation2002). The fine and coarse aggregates used were river natural sand taken from Manas River in China’s Xinjiang province. The size of fine aggregates ranged from 0.4 to 2.5 mm, and the size of coarse aggregates ranged from 5 to 20 mm. The DS was taken from Gurbantunggut desert in Xinjiang province. presents the chemical compositions of this DS. Superplasticizer was used in all the mixtures, and the superplasticizer used was HSC (see ). The water used was tap water.
Table 1. The chemical composition of dune sand (Gurbantunggut desert).
Table 2. Superplasticizer properties (HSC).
In order to investigate the effort of DS replacement levels on the engineering properties of DSC, five types of concrete mixtures were designed (see ). The codified names of specimens included two parts. The first part “DSC” was the abbreviation of DSC. The second part “0-80” reflected DS added as a replacement for fine aggregates.
Table 3. The mix proportion of dune sand concrete.
The dimensions and tested methods of all concrete specimens were based on Chinese specification (GB50081) (Citation2002). The dimensions that measured the compressive strength and splitting strength were designed 150 mm in length, 150 mm in width and 150 mm in height, and the dimensions that measured the elasticity modulus and axial compressive strength were designed 150 mm in length, 150 mm in width and 300 mm in height. The dimensions that measured the flexural strength were designed 550 mm in length, 150 mm in width and 150 mm in height, while the length of the span of the specimens was 450 mm.
2.2. Description of beam specimens
A total of five longitudinally reinforced beams made of DSC were cast to carry out mechanical properties tests, as shown in . All the tested beams were designed 1600 mm in length, 150 mm in width and 300 mm in height. The length of the span of all beams was 1300 mm, and the shear span-to-depth ratio () of all beams was kept equal to 1.56.
Table 4. Parameters of specimens.
All the beams were defined by the reinforcement ratios (2aaaaaaa16). The codified names of beams included two parts. The first part “DSCB” was the abbreviation of DSC beam. The second part “0-80” reflected DS added as a replacement for fine aggregates.
The properties of longitudinal reinforcement and stirrup are shown in .
Table 5. Properties longitudinal reinforcement and stirrup.
2.3. Test set-up and instrumentation
All the concrete specimens were tested based on Chinese specification (GB50081) (Citation2002), and three specimens were tested for each mechanical property, and the mechanical properties of all the concrete specimens were evaluated at 28 days age.
The engineering properties of all concrete specimens were tested by the servo-controlled universal testing machine. The set-up for compressive strength test is shown in ). The diagram for splitting strength test is shown in ). The set-up for axial compressive strength and elasticity modulus test is shown in ). The diagram for flexural strength test is shown in ).
Figure 1. Concrete test setup. (a) Setup for compressive strength test, (b) Diagram for splitting strength test, (c) Setup for axial compressive strength and elasticity modulus test, (d) Diagram for flexural strength test.
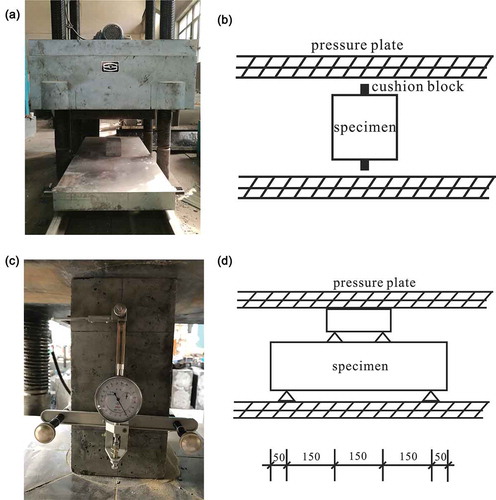
All the beams were tested at 28–30 days age, with a symmetrical two-point force control system applied at the third points of the beam span, as shown in . The supports were placed to allow for deflection, 150 mm from each end of the beam. Loading protocol was based on Chinese specification (GB50152) (Citation2012). All the beams were loaded until failure.
3. Results and discussion
3.1. Mechanical properties of DSC
In this paper, setting the ordinary concrete as the control specimen, the compressive strength, splitting strength, flexural strength, elastic modulus and axial compressive strength of DSC were compared with those of control specimen.
3.1.1. Compressive strength
The measured compressive strength of all the concrete specimens is shown in . Test results indicate that the compressive strength decreases with replacement of DS increasing when the replacement level is low, and this trend is consistent with previous literatures (Zhang et al. Citation2006; Al-Harthy et al. Citation2007; Zaitri et al. Citation2014; Belferrag, Kriker, and Khenfer Citation2013; Abu Seif et al. Citation2016; Alawad et al. Citation2015; Jiang et al. Citation2016; Luo et al. Citation2013). Also, notably, higher replacement of DS aggregates (60%, 80%) causes increasing compressive strength, and this increase is due to absorption of DS which could reduce the water–cement ratio of cement gel. In order to explore the compressive strength of DSC with DS replacement levels, the empirical expression was proposed by the regression analysis of the test results, as shown in the following equation:
Table 6. Summary of experimental results of DSC.
where and
are the compressive strength of DSC and NAC, respectively; and
is the DS replacement level (%).
3.1.2. Splitting strength
The splitting strength of all the concrete specimens is given in . Test results indicate that, compared with compressive strength of DSC, the tendency of splitting strength of DSC is similar to that of compressive strength, and the splitting strength increases with compressive strength increasing.
The functional relationship between the splitting strength and the compressive strength of DSC could be obtained by the tests results, as shown in the following equation:
where and
are the splitting strength and compressive strength, respectively.
3.1.3. Flexural strength
The measured flexural strength of all the concrete specimens are shown . The functional relationship between the flexural strength and the compressive strength for DSC could be obtained by the tests results, as shown in the following equation:
where is the flexural strength and
is the compressive strength.
3.1.4. Elasticity modulus
The results indicate that the elastic modulus () (see ) increases first and then decreases with increasing replacement of DS. The functional relationship between the elasticity modulus and the compressive strength for DSC could be obtained by the test results, as shown in the following equation:
where is the compressive strength.
3.1.5. Axial compressive strength
The axial compressive strength is the most important factor for the structural calculation and design (Xiao et al. Citation2014). The measured prisms’ axial compressive strength of all the concrete specimens are shown in . The functional relationship between the axial compressive strength and the compressive strength was linear for conventional natural aggregate concrete.
The relationships between the axial compressive strength and the compressive strength for DSC could be obtained by the tests results, as shown in the following equation:
where is the prisms axial compressive strength and
is the compressive strength.
3.2. Mechanical properties of DSC beam
3.2.1. Crack pattern and failure modes
The experimentally obtained crack patterns of all beams are plotted in . It is clear that the flexural cracks are evident, as are flexure-shear cracks, and the crack patterns of the ordinary beam are similar to those of DSC beams. The first crack was recorded at around 80 kN () in the central flexural zone, and it could be concluded that the presence of DS might delay the first crack. At a load around 130 kN, the shear cracks emanated in both shear spans near the supports, but the diffusion of shear cracks in shear spans was different. At a load around 280 kN, all beams failed in flexure shear, and the eventual failure occurred at the load point for concrete crushing in the compression zone (). The failure load of all beams is presented in , and it can be concluded that the presence of DS might reduce the failure load of beams. Although the first crack, failure load and shear cracks were different, the leading shear crack path and failure modes were almost identical.
Table 7. First crack loads and failure loads.
3.2.2. Concrete strain
shows the concrete strains along depth of beam’s midspan section with increasing loading. It is obvious that the change of measured concrete strains for DSC beams is similar to that of ordinary beam, and the strain distribution of all beams varies almost linearly along the height of the beam. This means that the contribution of DS is negligible in both tension and compression. The concrete strains of all beams were almost the same with Xiao’s research (Citation2014); hence, it could be concluded that the plane cross-section assumption could be used for DSC beam, and the theoretical formula of Chinese code (GB50010) (Citation2010) could be applied for DSC beam.
3.2.3. Strains in reinforcement
The relations between load and reinforcement strains in the midspan are shown in . It is clear that the trend of measured reinforcement strains for DSC beams is similar to that of ordinary beam. Initially relations between load and reinforcement strains of all beams showed linear behaviour. However, once cracking occurred at around 80 kN, the reinforcement strains increased rapidly. At a higher load level, the reinforcement strains for DSC beams were larger than that of ordinary beam.
3.2.4. Load–deflection curve
The experimentally obtained load–midspan deflection curves of the beams are plotted in . It can be seen that for all beams, they show linear behaviour of load–deflection before cracking. After appearance of first cracks, before yielding of steel reinforcement, the overall slope of the curve at ascending stage is in accordance with the ordinary beam. However, there is a big difference in the descending stage; the larger the DS replacement levels, the greater the deflection capacity. It can be concluded that the DS could increase the ductility of beams.
3.2.5. Flexural strength
Since no formula could be used as standard method to calculate the flexural strength of DSC beam, the empirical formula was adopted according to Chinese code (GB50010) (Citation2010), as shown in in the following equation:
where is the equivalent coefficient of concrete;
and
are shown in and ;
is depth of concrete compression zone;
and
are the effective depth of the section and the width of beam, respectively;
is the area of longitudinal reinforcement; and
is the ultimate moment of beam.
The is one of the parameters of concrete, and it varies with the load. To simplify the calculation, the
could be expressed as in the following equation (Xiao et al. Citation2014):
So was a function of concrete, and the flexural strength of DSC beam could be calculated by EquationEquation (7)
(7)
(7) .
The test values and calculated values by EquationEquation (7)(7)
(7) are shown in . It can be seen that test values of flexural strength are larger than that of theoretical calculation of code. It was feasible to calculate flexural strength of DSC by Chinese code, but it was not economical. Meanwhile, EquationEquation (7)
(7)
(7) did not take into account the replacement levels of DS. Therefore, the correction factor of concrete considering the replacement levels of DS was introduced to improve the EquationEquation (7)
(7)
(7) , as shown in the following equation:
Table 8. Comparison of test values, calculated values by code and proposed formula MuT.
where is the correction factor of concrete.
The was determined by the method of regression analysis (see ). Hence, the modified formula of flexural strength of DSC beam could be expressed by EquationEquation (9)
(9)
(9) . Here,
was DS replacement level, as shown in .
As shown in , it can be seen that the calculated values by proposed formula are in agreement with the test values. It was more reasonable to calculate flexural strength of DSC beam by proposed formula.
4. Conclusions
The following conclusions are drawn from this study:
The equations were proposed to describe the effect of DS replacement levels on the compressive strength, splitting strength, flexural strength, elastic modulus and axial compressive strength of DSC.
The crack pattern and failure modes of DSC beams were similar to that of ordinary beam, and the concrete strains satisfied the plane cross-section assumption. Therefore, the theoretical formula of Chinese code (GB50010) could be applied for DSC beam.
The strains in reinforcement and load–midspan deflection curve of DSC were lager than those of ordinary concrete beam, proving that the DS could increase the ductility of beams.
The proposed formula to calculate flexural strength of DSC beam could be applied to predict the flexural strength of DSC beams in the area of northwest China’s Xinjiang province.
Disclosure statement
No potential conflict of interest was reported by the authors.
Additional information
Funding
References
- Abdalla, J. A., F. H. Hraib, R. A. Hawileh, and A. M. Mirghani. 2016. “Experimental Investigation of Bond-slip Behaviour of Aluminum Plates Adhesively Bonded to Concrete.” Journal of Adhesion Science and Technology 2016: 1–18. doi:10.1080/01694243.2016.1204741.
- Abou El-Mal, H. S. S., A. S. Sherbini, and H. E. M. Sallam. 2015. “Locating the Site of Diagonal Tension Crack Initiation and Path in Reinforced Concrete Beams.” Ain Shams Engineering Journal 6: 17–24. doi:10.1016/j.asej.2014.10.006.
- Abou El-Mal, H. S. S., A. S. Sherbini, and H. E. M. Sallam. 2018. “Structural Behaviour of RC Beams Containing a Pre- Diagonal Tension Crack.” Latin American Journal of Solids and Structures 15 (7): e82. doi:10.1590/1679-78254701.
- Abu Seif, E. S., A. R. Sonbul, B. A. H. Hakami, and E. K. El-Sawy. 2016. “Experimental Study on the Utilization of Dune Sands as a Construction Material in the Area between Jeddah and Mecca, Western Saudi Arabia.” Bulletin of Engineering Geology and the Environment 75 (3): 1007–1022. doi:10.1007/s10064-016-0855-9.
- Alawad, O. A., A. Alhozaimy, M. S. Jaafar, F. N. A. Aziz, and A. Al-Negheimish. 2015. “Effect of Autoclave Curing on the Microstructure of Blended Cement Mixture Incorporating Ground Dune Sand and Ground Granulated Blast Furnace Slag.” International Journal of Concrete Structures and Materials 9 (3): 381–390. doi:10.1007/s40069-015-0104-9.
- Al-Harthy, A. S., M. A. Halim, R. Taha, and K. S. Al-Jabri. 2007. “The Properties of Concrete Made with Fine Dune Sand.” Construction and Building Materials 21 (8): 1803–1808. doi:10.1016/j.conbuildmat.2006.05.053.
- Alhozaimy, A., O. A. Alawad, M. S. Jaafar, A. Al-Negheimish, and J. Noorzaei. 2014. “Use of Fine Ground Dune Sand as a Supplementary Cementing Material.” Journal of Civil Engineering and Management 20 (1): 32–37. doi:10.3846/13923730.2013.768541.
- Balaji, S., and G. S. Thirugnanam. 2018. “Behaviour of Reinforced Concrete Beams with SIFCON at Various Locations in the Beam.” KSCE Journal of Civil Engineering 22 (1): 161–166. doi:10.1007/s12205-017-0498-9.
- Belferrag, A., A. Kriker, and M. E. Khenfer. 2013. “Improvement of the Compressive Strength of Mortar in the Arid Climates by Valorization of Dune Sand and Pneumatic Waste Metal Fibers.” Construction and Building Materials 40: 847–853. doi:10.1016/j.conbuildmat.2012.11.079.
- Bhashya, V., S. S. Kumar, G. Ramesh, B. H. Bharatkumar, T. S. Krishnamoorthy, and N. R. Iyer. 2015. “Long Term Studies on FRP Strengthened Concrete Specimens.” Indian Journal of Engineering and Materials Sciences 22 (4): 465–472.
- Bouziani, T., M. Bederina, and M. Hadjoudja. 2012. “Effect of Dune Sand on the Properties of Flowing Sand-concrete (FSC).” International Journal of Concrete Structures and Materials 6 (1): 59–64. doi:10.1007/s40069-012-0006-z.
- Evangelista, L., and J. de Brito. 2017. “Flexural Behaviour of Reinforced Concrete Beams Made with Fine Recycled Concrete Aggregates.” KSCE Journal of Civil Engineering 21 (1): 353–363. doi:10.1007/s12205-016-0653-8.
- GB50010. 2010. Code for Design of Concrete Structures. Chinese Standard. GB 50010-2010. Beijing: Chinese Standard Institution.
- GB50081. 2002. Standard Test Method for Mechanical Properties of Ordinary Concrete. Chinese Standard. GB 50081-2002. Beijing: Chinese Standard Institution.
- GB50152. 2012. Standard Test Method for Concrete Structures. Chinese Standard. GB 50152-2012. Beijing: Chinese Standard Institution.
- Gopinath, S., A. R. C. Murthy, and N. R. Iyer. 2015. “Monotonic and Low Cycle Fatigue Behaviour of Concrete Beams Strengthened with Textile Reinforced Concrete U-wrap.” Indian Journal of Engineering and Materials Sciences 22 (3): 331–338.
- Hawileh, R. A., W. Nawaz, J. A. Abdalla, and E. I. Saqan. 2015. “Effect of Flexural CFRP Sheets on Shear Resistance of Reinforced Concrete Beams.” Composite Structures 122: 468–476. doi:10.1016/j.compstruct.2014.12.010.
- Jiang, C. H., X. B. Zhou, G. L. Tao, and D. Chen. 2016. “Experimental Study on the Performance and Microstructure of Cementitious Materials Made with Dune Sand.” Advances in Materials Science and Engineering 2016: 1–8. doi:10.1155/2016/2158706.
- Lee, E., S. Park, and Y. Kim. 2016. “Drying Shrinkage Cracking of Concrete Using Dune Sand and Crushed Sand.” Construction and Building Materials 126: 517–526. doi:10.1016/j.conbuildmat.2016.08.141.
- Luo, F. J., L. He, Z. Pan, W. H. Duan, X. L. Zhao, and F. Collins. 2013. “Effect of Very Fine Particles on Workability and Strength of Concrete Made with Dune Sand.” Construction and Building Materials 47: 131–137. doi:10.1016/j.conbuildmat.2013.05.005.
- Meraj, T., A. K. Pandey, and B. K. Rao. 2014. “Flexural Behaviour of Latex Modified Steel Fiber Reinforced Concrete.” Indian Journal of Engineering and Materials Sciences 21 (2): 219–226.
- Prusty, J. K., S. K. Patro, and T. Mohanty. 2018. “Structural Behaviour of Reinforced Concrete Beams Made with Ferrochrome Slag as Coarse Aggregate.” KSCE Journal of Civil Engineering 22 (2): 696–707. doi:10.1007/s12205-017-1294-2.
- Sallam, H. E. M. 2010. “Discussion of ‘Flexural Strengthening of Steel Bridges with High Modulus CFRP Strips’ by David Schnerch and Sami Rizkalla.” Journal of Bridge Engineering 15: 117. doi:10.1061/(ASCE)BE.1943-5592.72.
- Sallam, H. E. M., A. A. M. Badawy, A. M. Saba, and F. A. Mikhail. 2010. “Flexural Behaviour of Strengthened Steel–concrete Composite Beams by Various Plating Methods.” Journal of Constructional Steel Research 66: 1081–1087. doi:10.1016/j.jcsr.2010.03.005.
- Sunayana, S., and S. V. Barai. 2018. “Flexural Performance and Tension-stiffening Evaluation of Reinforced Concrete Beam Incorporating Recycled Aggregate and Fly Ash.” Construction and Building Materials 174: 210–223. doi:10.1016/j.conbuildmat.2018.04.072.
- Wang, Y. G., D. N. Xiao, and Y. Li. 2007. “Temporal-spatial Change in Soil Degradation and Its Relationship with Landscape Types in A Desert-oasis Ecotone: A Case Study in the Fubei Region of Xinjiang Province, China.” Environmental Geology 51 (6): 1019–1028. doi:10.1007/s00254-006-0371-5.
- Xiao, J. Z., T. L. Pham, P. J. Wang, and G. Gao. 2014. “Behaviors of Semi-precast Beam Made of Recycled Aggregate Concrete.” Structural Design of Tall and Special Buildings 23: 692–712. doi:10.1002/tal.1071.
- Zaitri, R., M. Bederina, T. Bouziani, Z. Makhloufi, and M. Hadjoudja. 2014. “Development of High Performances Concrete Based on the Addition of Grinded Dune Sand and Limestone Rock Using the Mixture Design Modelling Approach.” Construction and Building Materials 60: 8–16. doi:10.1016/j.conbuildmat.2014.02.062.
- Zhang, G. X., J. X. Song, J. S. Yang, and X. Liu. 2006. “Performance of Mortar and Concrete Made with a Fine Aggregate of Desert Sand.” Building and Environment 41: 1478–1481. doi:10.1016/j.buildenv.2005.05.033.