ABSTRACT
Natural soil can play an important role in the production of geopolymer due to having required aluminosilicate precursors and abundant availability. Numerous aluminosilicate materials have been used in the past for the production of geopolymers but they have some limitations like various ashes can be toxic during handling and processing due to presence of harmful components. The major purpose of this study was to develop geopolymers via cheap and easily available aluminosilicate material like loam type of natural soil. Geopolymer specimens were prepared by mixing natural soil and other required precursors such as sodium silicate and sodium hydroxide through ball milling. After the preparation of mortars via subsequent hydrothermal treatment for 24 hours at 60⁰C, the physical and mechanical properties were evaluated. FTIR analysis showed that geopolymerization reaction occurred in soil-based geopolymer mortars. This was confirmed by detecting some zeolitic phases like Albite/Anorthite in geopolymers. X-ray diffraction analysis also confirmed the presence of these zeolitic phases. The maximum compression strength of 22.70 MPa was achieved for A-75 composition which proved to be an optimum composition in this study which is somehow comparable to the compressive strength of ordinary Portland cement (OPC) mortars.
1. Introduction
Cement-based concretes are widely used construction materials and their demand is increasing day by day but, the release of extensive amount of CO2 worldwide during production of these materials is a major environmental problem (Ozer and Soyer-Uzun Citation2015; Zhang et al. Citation2014; Nazari and Ghafouri Safarnejad Citation2013; Duxson et al. Citation2007a, Citation2007b). According to recent researches (Zaidi et al. Citation2017; Papadopoulos and Giama Citation2007) 0.66 to 0.83 tons CO2 is released in the atmosphere due to producing one ton of ordinary Portland cement; on the other hand, one ton of geopolymer emits only 0.19 to 0.24 ton CO2 and shows minor contribution towards global warming.
Geopolymer mortars have potential to be used as ecofriendly materials due to low emission of CO2 during their production. The geopolymers are amorphous to crystalline structured materials and they are formed as a result of reaction between the aluminosilicate precursor and an alkali silicate or alkali hydroxide solution, giving Si-O-Si/Si-O-Al network. These reactions occur in hydrothermal condition and at low temperature (mainly at 60⁰C) (Ozer and Soyer-Uzun Citation2015; Xie and Ozbakkaloglu Citation2015). There are various terms used for geopolymers like “low-temperature aluminosilicate glass”, “geo cement”, “alkali bonded ceramics”, and “hydro ceramic” (Ozer and Soyer-Uzun Citation2015).
Loam natural soil is composed of different types of clays mixtures, silts, and sands. The clays and silts both are aluminosilicates, silt being relatively greater in particle size. The compositions vary according the source and land of the region in various parts of the world (Tümsavaş et al. Citation2019). Clays and silt naturally contain higher amounts of alumina and silica which can be used as precursor required for geopolymerization (Cai, Liu, and Zheng Citation2019). Geopolymerization reaction occurs in four steps: (i) the oxides of Al and Si are dissolved from the raw material of aluminosilicates by the attack of strong alkaline solution, (ii) oligomers are formed when Si-O-Al and Si-O-Si bonds polymerize, (iii) the formed oligomers at second step undergo polycondensation to give a three-dimensional network, (iv) and finally the remaining particles of the solid filler material make bond with the network of aluminosilicates resulting in a further stable and strong structure (Ul Haq, Padmanabhan, and Licciulli Citation2014; Thakur, Thakur, and Ghosh Citation2009; Izquierdo et al. Citation2009). For the geopolymerization reaction, the ingredients of soil like silts and clays are activated as they are the source of silica and alumina while sand could be proved as reinforcement. Luckily all these ingredients are available in a greatly abundant natural matter such as loam soil (Cai, Liu, and Zheng Citation2019).
There is still room for investigating the production of geopolymer mortars from some types of natural soil-based raw materials, e.g. loam natural soil. Although some researchers have tried to make geopolymers using soil as a basic raw material but they used red soil as the raw material and also the properties reported by them are very low like strength approaching to ~7 MPa maximum (Uddin and Saraswathy Citation2018; Uddin, Velu, and Elumalai Citation2015). The reason for the lower properties seems to be that they have not tried for the optimum combinations of the raw ingredients including sodium silicate, sodium hydroxide and natural soil. They merely have mixed a single combination of these ingredients and found these very properties. These studies were also lacking in explanation based on X-ray diffraction (the crystalline nature of the raw soil and geopolymers), Fourier transform infrared spectroscopy (the bonding behaviour of the geopolymers), thermogravimetric analysis (to study weight loss with temperature) through which it could be expected that the explanation and reasoning would be fruitful.
Some other researchers successfully used fly ash-based geopolymers to improve clay soil (Cristelo, Glendinning, and Teixeira Pinto Citation2011; Phetchuay et al. Citation2014; Zhang et al. Citation2013; Tang et al. Citation2015). However, most of these studies report the curing of the samples at ambient temperature for longer periods of time, up to one year in some cases, while some studies used high temperatures curing to reduce the time. Zhang et al. (Zhang et al. Citation2013) evaluated the feasibility of metakaolin-based geopolymers as next-generation soil stabilizer. So, geopolymers have been produced by using many aluminosilicate precursors like bottom ash and fly ash (Ul Haq, Padmanabhan, and Licciulli Citation2014; Temuujin, van Riessen, and MacKenzie Citation2010; Xu et al. Citation2010; Khan et al. Citation2016; Freidin Citation2007; Shehab, Eisa, and Wahba Citation2016), metakaolin (Yuan et al. Citation2016; He et al. Citation2016), various clays (Longhi et al. Citation2016; Diffo et al. Citation2015; Burciaga-Diaz, Escalante-Garcia, and Gorokhovsky Citation2012), natural soil (Zaidi et al. Citation2017), glass waste, volcanic ashes and metallurgical slags (Kastiukas, Zhou, and Castro-Gomes Citation2016; Huseien et al. Citation2016; Sore et al. Citation2016; Zarwah et al. Citation2016; El-Naggar and El-Dessouky Citation2017). The precursors are mixed and activated by using NaOH/Na2SiO3 or KOH/K2SiO3 (Duxson et al. Citation2007a; Wang et al. Citation2007; Singh et al. Citation2015; Lemougna et al. Citation2016). But, these precursors have some limitations like various ashes can be toxic during handling and processing due to the presence of some harmful components such as Pb and Cd (Dietel et al. Citation2017; Duxson and Provis Citation2008; Galán and Ferrell Citation2013). Hence, the major purpose of this study was to develop geopolymers via cheap, nontoxic and easily available aluminosilicate precursor material like loam type of natural soil. A few researches have been done on natural soil (Zaidi et al. Citation2017; Nadeem et al. Citation2015) to make geopolymer foam; but geopolymer mortar has not been synthesized by using loam natural soil. Hence, the aim of this research is to produce the geopolymers from natural soil which is abundantly available in most parts of the world hence minimizing the costs of transportation and logistics, especially in remote and undeveloped areas. Therefore, this research explores a somewhat novel idea to make in-situ sustainable geopolymer mortar from loam natural soil.
The prepared geopolymer material specimens were characterized in terms of their morphology, structure and composition by scanning electron microscopy (SEM), X-ray diffraction (XRD), Fourier transform infrared (FTIR) spectroscopy and X-ray fluorescence (XRF) analysis, respectively. The degradation characteristics were studied with the help of thermogravimetric analyzer (TGA) and compression strengths were evaluated by universal mechanical testing machine.
2. Experimental work
2.1. Materials
The loam natural soil, the major ingredient used in this study, was obtained from the local source in South Punjab, Pakistan. and present the properties and composition of soil, respectively. The soil was dried in an oven to remove any moisture contents and subsequently was ground with the help of ball mill using alumina balls as grinding media. The particle size was reduced down to 74 μm (200 mesh) by this milling process to achieve the high surface area for better reactivity because more reactivity can be obtained by using finer particle size (Nadeem et al. Citation2015). Besides soil, other raw materials used were sodium silicate (66% H2O, 9% Na2O, and 25% SiO2 with specific gravity 1.52 g/cm3). 14.0 M sodium hydroxide solution (Zaidi et al. Citation2017) was prepared by mixing pellets of sodium hydroxide in water and it was used as the activating solution for the soil particles to initiate the polycondensation reaction during geopolymerization. 14 M solution is mostly preferred as activation solution for the production of geopolymers due to better outcome (Zaidi et al. Citation2017; Ul Haq, Padmanabhan, and Licciulli Citation2014).
Table 1. Properties of soil
Table 2. Composition of soil as determined by XRF analysis (Mass %)
2.2. Mortar preparation
The composition of mortars prepared in this study is given in . The suffix “A” indicates the amount of soil used. For example in the material system A-71, there is 71% of soil while the balance percentage is of liquid.
Table 3. Material system IDs and their respective compositions
Sodium hydroxide (NaOH), sodium silicate (Na2SiO3), natural soil and water; all mixed in fixed proportions in a ceramic jar for the preparation of mortars. While the ratio of sodium silicate to sodium hydroxide was kept to 4.4:1 as suggested in the literature (Ul Haq, Padmanabhan, and Licciulli Citation2014). The mixture was milled in a planetary ball mill (Pulverisette 5) for 15 minutes with the help of alumina grinding balls of different diameters (Zaidi et al. Citation2017; Ul Haq, Padmanabhan, and Licciulli Citation2014; Haq, Padmanabhan, and Licciulli Citation2019). In this way, a homogenized slurry was obtained. Only a little amount of extra water can be added during mixing due to the reason that excess quantity of water might degrade the properties of geopolymers (Zaidi et al. Citation2017). This extra water enhances the cast ability and plasticity of the mixture. Only a little amount of water is required because silica glass (sodium silicate) already contains 66% water. After mixing, the slurry was then poured into the high-density polyethylene (HDPE) cylindrical mold of 3.12 cm diameter having 4.6 cm of length (height to diameter ratio = 1.5 approx.). The lid of the molds was closed to suppress the loss of moisture during curing. Then, the samples were heated at 60⁰C for 24 h. shows the representative samples after heating at 60⁰C for 24 hours. After this, samples were de-molded and cured at ambient temperature for 24–48 h to further remove the moisture. Then, the compositions were subjected to post heat treatment at 150⁰C for 2 h. The samples after this post heat treatment were 2.8 cm in diameter and 3.6 cm in height. Samples lag the mold height by 1 cm because molds were not filled completely and also the top and bottom sides of the samples were polished to get even surface for good compression test. Finally, the geopolymer mortars were characterized to evaluate their physical as well as the mechanical properties.
2.3. Sample analysis
An XRF spectrometer (The X-5000: Innov-X Canada) was used to evaluate the chemical composition of natural soil. ATR spectrometer (Attenuated Total Reflectance; Jasco FT/IR-4100) was used with 4 cm−1 resolution and 2 mm/s scan rate in order to perform Fourier transform infrared spectroscopy (FTIR) analysis. An X-ray diffractometer (Panalytical X’Pert Pro, with Cu Kα1 radiations generated at 45kV and 45 mA) was used for phase analysis. Whereas the compressive mechanical strength of the cured specimens was evaluated with the help of a universal testing machine by METRO COM s.p.a Italy.
3. Results and discussion
3.1. Soil analysis
gives the physico-chemical properties of the soil. It was observed as slightly basic in nature with ingredients of sand, clays and silt in a proportion of loam soil. The loss on ignition could mainly be attributed to the organic matter present in the soil. The chemical composition of natural soil as evaluated by XRF analysis is given in . Natural soil contained SiO2, Al2O3, Fe2O3, TiO2 etc. The maximum percentage of soil was composed of SiO2 as given in . Fe2O3 was found in the form of nontronite which is iron-rich smectite clay mineral. Besides Fe2O3, traces of some other compounds were also found like CaCO3 (Calcite), etc., as revealed by the XRD spectra.
3.2. XRD analysis of soil and mortars
XRD analysis of soil and its respective geopolymers were carried out in order to identify different phases present. For soil, X-ray diffraction spectrum is shown in . While for geopolymers, it is given in . An iron-rich phase was identified in both soil and geopolymer which is nontronite a smectite clay mineral (Gainey et al. Citation2014). Besides nontronite, other phases present in soil and its respective geopolymers were quartz (JCPDS 5–0490), albite (JPCPDS 20–0554), and anorthite (JCPDS 89–1462). Compound of iron was found in rich amount in the soil as shown in .
Figure 3. XRD analysis of soil-based geopolymers (N = Nontronite, Q = Quartz, C = Calcite, A = Albite/Anorthite)
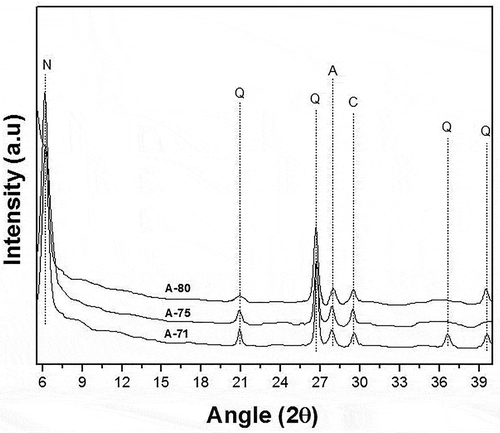
Albite and anorthite are already present in the natural soil. The peak with increased intensity, in mortars, is due to the formation of new albite/anorthite via geopolymerization reaction and due to increase in the relative amounts of the soil. Haq et al. (Ul Haq, Padmanabhan, and Licciulli Citation2014) described the presence of albite/anorthite in aluminosilicate source and also in the product after geopolymerization reaction. Albite and anorthite are plagioclase feldspar members which were actually present in the soil due to the hydrothermal history of the soil (Hunt, Mineralogical Society of America, and Kleppa Citation1994). These are zeolitic phases found in nature hence in natural soils (Itskos et al. Citation2014). Quartz is the indication of sand, which is present in the soil naturally. Besides these phases, XRD pattern of soil and its respective geopolymers also indicate calcite phase (JCPDS 86–2334) (Ul Haq, Padmanabhan, and Licciulli Citation2014).
In the present work, the soil used may be termed as crystalline in nature because XRD results show the crystalline peaks for quartz (SiO2), nontronite (rich in Fe2O3 and Al2O3), etc. And the presence of these minerals is also quantitatively confirmed by the XRF results which show that major proportion of the soil is consisting of these crystalline compounds (65.1% SiO2, 15.7% Fe2O3, 16.8% Al2O3 etc.). It was important to cure the mortar samples developed out of crystalline soil first at 60⁰C for geopolymerization and then at elevated temperature for the development of a 3D network of Si-O-T (T = Si/Al) by dehydroxylation to make the mortars water-insoluble (Haq et al. Citation2016).
Geopolymers are amorphous in nature and are generally produced easily from amorphous precursor materials but, they can also be produced from crystalline powders with high surface energy. Because the surface of crystalline materials is associated with relatively high surface-free energy (than the bulk), which is analogous to amorphousness in nature; hence, the surface shows reactivity for the geopolymerization reaction to occur. However, in these cases, the geopolymer structure is formed only on the surface while the inside materials still remain crystalline. So the XRD patterns of the geopolymer specimens still showed crystalline peaks due to inner crystalline material, and because during the activation process only surface is activated and the inner particles remain undissolved.
3.3. Thermogravimetric analysis
Thermogravimetric analysis showed variable weight loss trends in the soil and its respective geopolymers as shown in .
Low water contents were observed in natural soil compared to resultant geopolymer mortars because moisture was absorbed by resultant geopolymer during handling and transportation. Additionally, extra water was added for the preparation of slurry to make natural soil-based geopolymer mortar. There is observed a gradual decrease in weight of soil up to 100°C which is, in fact, due to the removal of physically adherent water. Water was also removed at 220°C because of dehydroxylation of geopolymer, which was chemically held in the molecules of geopolymers. While from 100°C onward up to 600°C, the weight of the soil decreases gradually due to the removal of volatile organic compounds and oxidation of carbon from organic matter. In addition, the sodium carbonate present in sodium silicate is also reduced to CO2 and sodium oxide at higher temperatures. This sodium carbonate is formed due to the absorbance of CO2 from the atmosphere as a result of handling and transportation of sodium silicate (Haq, Padmanabhan, and Licciulli Citation2013).
3.4. FTIR analysis
FTIR analysis was carried out on representative compositions to evaluate the geopolymerization in soil-based geopolymer mortars, and functional groups present in soil and its respective geopolymers. For such geopolymer mortars the –OH bending and –OH stretching bands were observed at 1636 cm−1 and 3620 cm−1, respectively, due to water as shown in .
The small band of –OH bending was observed in the soil which indicates the presence of little amounts of water which is also justified by the data in . In geopolymers, the peak of – OH stretching becomes shallower as we move from A-71 to A-80. Since the amount of soil increases from A-71 composition to A-80, so in order to increase the cast ability and plasticity more water was added in samples with A-75, and A-80 compositions with respect to the samples having A-71 composition. No peak of –OH stretching was observed for soil because soil contained very less amount of water (0.3%) as indicated in . The band around 1440 cm−1 indicates the presence of sodium carbonate (Na2CO3) which is formed by the reaction between NaOH and CaCO3 (Abdel-Gawwad and Abo-El-Enein Citation2015). A chemical reaction between Na2SiO3 and CO2 can also form the sodium carbonate (Na2CO3) (Haq, Padmanabhan, and Licciulli Citation2013).
For geopolymer mortars, the band at around 1000 cm−1 becomes deeper and slimmer when compared with the band of natural soil which is due to geopolymerization reaction (Haq, Padmanabhan, and Licciulli Citation2019; Heah Citation2010). The band around 1000 cm−1 indicates the stretching vibrations in Si-O-T (T = Si or Al) and area under this band Si-O-T is again a sign of geopolymerization reaction as per already published literature (Ul Haq, Padmanabhan, and Licciulli Citation2014). But as the solid contents are increased, there is observed a decreasing trend of geopolymerization reaction which is because of decrease in the binding liquid and activation content which is presented in (Haq, Padmanabhan, and Licciulli Citation2019).
A band at around 771 cm−1 corresponds to Si-O-Al stretching vibrations in both soil and geopolymers. In soil, this is due to the presence of zeolitic phases (albite, anorthite) while in geopolymers it is due to the geopolymerization reaction. At around 695 cm−1 the band indicates the Si-O stretching vibrations which is an indication of the Si-O-Si network in geopolymers while this indicates the natural occurrence of quartz (sand) in the soil as revealed in XRD spectrum too (Ekosse Citation2005).
3.5. SEM analysis
SEM (scanning electron microscopy) analysis was performed to the selected compositions to evaluate the morphology of the soil and its respective geopolymers as shown in . SEM microstructures of soil represented an irregular particle size distribution. These microstructures show a uniform morphology in case of soil specimens whereas the morphology of geopolymers specimens is non-uniform. The white phase in the microstructure of geopolymer represents the dendrites of sodium silicate which is formed after the geopolymerization reaction. Actually, the purpose of sodium silicate was like an activating agent and it gets the dendritic character during the geopolymerization reaction of the soil and its dendrites are present between the particles of the formed product which cause an increase in the mechanical strength. Dendrites actually cause entanglement between the particles of resultant product, which also play a vital role to increase the strength of the final product at optimum composition which is in accordance with the already published data (Nadeem et al. Citation2015). Furthermore, silica particles in natural soil also played an important role in geopolymerization. Besides optimum composition, the interactions of natural soil with the dendrites of sodium silicate became successively negligible while the integrity of particles remained unchanged, which resulted in a situation where no load was transferred from one grain to its vicinity and the mechanical strength is lowered beyond optimum composition.
3.6. Mechanical strength
The mechanical properties of geopolymer mortar compositions were evaluated through compression tests. These compression tests were performed on three samples of each composition and the average results for all compositions are reported in . Minimum compressive strength was 13 MPa in A-71 specimen due to high percentage of activating solution. Higher the percentage of sodium silicate in the slurry results in the creation of more porosity and decrease in the compressive strength due to increased porosity percentage as there is an inverse relation between mechanical strength and porosity (Nadeem et al. Citation2015). The maximum compression strength 22.70 MPa was achieved for A-75 composition which proved to be an optimum composition in this study. This achieved strength is somehow comparable to the compressive strength of ordinary Portland cement mortars (Tang et al. Citation2015). Initially, the strength was lower and gradually increased to maximum owing to lower relative contents of solid soil precursors which are actually activated and load-bearing species of the concoction. Later strength decreased (specimens A-77.5 and A-80) due to the effect of gradual lowering of the liquid binding contents of the mixture, e.g. activating agents. Hence, A-75 composition was found to be best and optimized for the construction purposes.
compares the strength of soil-based geopolymer mortars prepared in this study with the strengths of other materials reported in published literature. The comparisons show that the strength of soil-based geopolymer mortars is close to the OPC mortar. The mechanical properties of these geopolymers can further be enhanced by proper mixing of the slurry and thoroughly activating the soil through other available techniques. Overall, this scenario suggests that OPC-based mortars can be replaced with soil-based geopolymer mortars. The elastic moduli of the prepared compositions were also measured to be almost in a close range of 2.5 GPa on the average which are in close tolerance to already reported results in the literature (Ul Haq, Padmanabhan, and Licciulli Citation2014).
Table 4. Comparison of compressive strength of soil-based geopolymer mortars with other materials
4. Conclusions
Geopolymer mortars have been prepared using natural soil as well as sodium silicate and sodium hydroxide by varying their quantity. Better physical and mechanical properties have been achieved in this study which exhibited that natural soil can be used as main precursor for the production of geopolymer mortar because it has all required aluminosilicate precursors like alumina and silica. XRD analysis showed the required phase for geopolymerization such as albite in geopolymer mortars. FTIR analysis also confirmed the geopolymerization in the natural soil-based geopolymer mortar samples by showing the stretching vibrations in Si-O-T (T = Si or Al) band. SEM analysis showed the microscopic confirmation of geopolymer structure where strands of silica are seen. The mechanical compressive strength was increased up to an optimum value of 22.70 MPa observed for A-75 composition which is closer to the strength of ordinary Portland cement. The use of natural soil in this study has been proved to be economical and eminently available required raw material for the synthesis of geopolymer mortar.
Acknowledgment
The authors extend their acknowledgement to Higher Education Commission (HEC) of Pakistan for funding this work via Project No: 10493/KPK/NRPU/R&D/HEC/2017 under its National Research Program for Universities (NRPU). Authors also pay their gratitude to the University of Engineering and Technology, Lahore, GIK Institute of Engineering Sciences and Technology, Topi and University of Education, Lahore, Pakistan for their financial support to carryout this work.
Disclosure statement
No potential conflict of interest was reported by the authors.
References
- Abdel-Gawwad, H. A., and S. A. Abo-El-Enein. 2015. “A Novel Method to Produce Dry Geopolymer Cement Powder.” HBRC Journal 74 (1): 13–24. doi:10.1016/j.hbrcj.2014.06.008.
- Burciaga-Diaz, O., J. I. Escalante-Garcia, and A. Gorokhovsky. 2012. “Geopolymers Based on a Coarse Low-purity Kaolin Mineral: Mechanical Strength as a Function of the Chemical Composition and Temperature.” Cement and Concrete Composites 34 (1): 18–24. doi:10.1016/j.cemconcomp.2011.08.001.
- Cai, G.-H., S.-Y. Liu, and X. Zheng. 2019. “Influence of Drying-wetting Cycles on Engineering Properties of Carbonated Silt Admixed with Reactive MgO.” Construction and Building Materials 204 (April): 84–93. doi:10.1016/j.conbuildmat.2019.01.125.
- Cristelo, N., S. Glendinning, and A. Teixeira Pinto. 2011. “Deep Soft Soil Improvement by Alkaline Activation.” Proceedings of the Institution of Civil Engineers-Ground Improvement 164 (2): 73–82, May.
- Dave, N., A. K. Misra, A. Srivastava, and S. K. Kaushik. 2016. “Experimental Analysis of Strength and Durability Properties of Quaternary Cement Binder and Mortar.” Construction and Building Materials 107: 117–124. doi:10.1016/j.conbuildmat.2015.12.195.
- Dietel, J., L. N. Warr, M. Bertmer, A. Steudel, G. H. Grathoff, and K. Emmerich. 2017. The Importance of Specific Surface Area in the Geopolymerization of Heated Illitic Clay.” Applied Clay Science 139: 99-107.
- Diffo, B. B. K., A. Elimbi, M. Cyr, J. D. Manga, and H. T. Kouamo. 2015. “Effect of the Rate of Calcination of Kaolin on the Properties of Metakaolin-based Geopolymers.” Journal of Asian Ceramic Societies 3 (1): 130–138. doi:10.1016/j.jascer.2014.12.003.
- Duxson, P., A. Fernández-Jiménez, J. L. Provis, G. C. Lukey, A. Palomo, and J. S. J. van Deventer. 2007a. “Geopolymer Technology: The Current State of the Art.” Journal of Materials Science 42 (9): 2917–2933, May. doi:10.1007/s10853-006-0637-z.
- Duxson, P., and J. L. Provis. 2008. “Designing Precursors for Geopolymer Cements.” Journal of the American Ceramic Society 91 (12): 3864–3869. doi:10.1111/j.1551-2916.2008.02787.x.
- Duxson, P., J. L. Provis, G. C. Lukey, and J. S. J. van Deventer. 2007b. “The Role of Inorganic Polymer Technology in the Development of ‘Green Concrete’.” Cement and Concrete Research 37 (12, December): 1590–1597. doi:10.1016/j.cemconres.2007.08.018.
- Ekosse, G.-I. E. 2005. “Fourier Transform Infrared Spectrophotometry and X-ray Powder Diffractometry as Complementary Techniques in Characterizing Clay Size Fraction of Kaolin.” The Journal of Applied Sciences & Environmental Management 9 (2): 43–48, November.
- El-Naggar, M. R., and M. I. El-Dessouky. 2017. “Re-use of Waste Glass in Improving Properties of Metakaolin-based Geopolymers: Mechanical and Microstructure Examinations.” Construction and Building Materials 132: 543–555. doi:10.1016/j.conbuildmat.2016.12.023.
- Freidin, C. 2007. “Cementless Pressed Blocks from Waste Products of Coal-firing Power Station.” Construction and Building Materials 21 (1): 12–18. doi:10.1016/j.conbuildmat.2005.08.002.
- Gainey, S. R., E. M. Hausrath, J. A. Hurowitz, and R. E. Milliken. 2014. “Nontronite Dissolution Rates and Implications for Mars.” Geochimica et Cosmochimica Acta 126 (February): 192–211. doi:10.1016/j.gca.2013.10.055.
- Galán, E., and R. E. Ferrell. 2013. “Chapter 3 - Genesis of Clay Minerals.” In Handbook of Clay Science, edited by F. Bergaya and C. S. Lagaly, Vol. 5, no. Supplement C, 83–126. Elsevier.
- Haq, E. U., S. K. Padmanabhan, and A. Licciulli. 2013. “In-situ Carbonation of Alkali Activated Fly Ash Geopolymer.” Construction and Building Materials 47: 781–786. doi:10.1016/j.conbuildmat.2014.06.012.
- Haq, E. U., S. K. Padmanabhan, and A. Licciulli. 2019. “Microwave Synthesis of Thermal Insulating Foams from Coal Derived Bottom Ash.” Fuel Processing Technology 204: 263–267. doi:10.1016/j.fuproc.2014.10.017.
- Haq, E. U., S. K. Padmanabhan, M. R. A. Karim, and A. Licciulli. 2016. “Setting and Curing of Mortars Obtained by Alkali Activation and Inorganic Polymerization from Sodium Silicate and Silica Aggregate.” Construction and Building Materials 105: 291–296. doi:10.1016/j.conbuildmat.2015.12.064.
- He, P., M. Wang, S. Fu, D. Jia, S. Yan, J. Yuan, J. Xu, et al. 2016. “Effects of Si/Al Ratio on the Structure and Properties of Metakaolin Based Geopolymer.” Ceramics International 42 (13): 14416–14422. doi:10.1016/j.ceramint.2016.06.033.
- Heah, C. Y. 2010. “Et Al, “Study on Solids-to-liquid and Alkaline Activator Ratios on Kaolin-based Geopolymers.” Construction and Building Materials 175: 912–922. doi:10.1016/j.conbuildmat.2012.04.102.
- Huseien, G. F., J. Mirza, M. Ismail, and M. W. Hussin. 2016. “Influence of Different Curing Temperatures and Alkali Activators on Properties of GBFS Geopolymer Mortars Containing Fly Ash and Palm-oil Fuel Ash.” Construction and Building Materials 125: 1229–1240. doi:10.1016/j.conbuildmat.2016.08.153.
- Itskos, G., A. Koutsianos, N. Koukouzas, and C. Vasilatos. 2014. “Zeolite Development from Fly Ash and Utilization in Lignite Mine-water Treatment.” International Journal of Mineral Processing 40 (June): 43–50. doi:10.1016/j.minpro.2015.04.011.
- Izquierdo, M., X. Querol, J. Davidovits, D. Antenucci, H. Nugteren, and C. Fernández-Pereira. 2009. “Coal Fly Ash-slag-based Geopolymers: Microstructure and Metal Leaching.” Journal of Hazardous Materials 166 (1): 561–566. doi:10.1016/j.jhazmat.2008.11.063.
- Kastiukas, G., X. Zhou, and J. Castro-Gomes. 2016. “Development and Optimisation of Phase Change Material-impregnated Lightweight Aggregates for Geopolymer Composites Made from Aluminosilicate Rich Mud and Milled Glass Powder.” Construction and Building Materials 110: 201–210. doi:10.1016/j.conbuildmat.2016.02.029.
- Khan, M. Z. N., F. Uddin Ahmed Shaikh, Y. Hao, and H. Hao. 2016. “Synthesis of High Strength Ambient Cured Geopolymer Composite by Using Low Calcium Fly Ash.” Construction and Building Materials 125: 809–820. doi:10.1016/j.conbuildmat.2016.08.097.
- Lemougna, P. N., K. Wang, Q. Tang, U. C. Melo, and X. Cui. 2016. “Recent Developments on Inorganic Polymers Synthesis and Applications.” Ceramics International 42 (14): 15142–15159. doi:10.1016/j.ceramint.2016.07.027.
- Longhi, M. A., E. D. Rodríguez, S. A. Bernal, J. L. Provis, and A. P. Kirchheim. 2016. “Valorisation of a Kaolin Mining Waste for the Production of Geopolymers.” Journal of Cleaner Production 115: 265–272. doi:10.1016/j.jclepro.2015.12.011.
- Nadeem, M., E. U. Haq, F. Ahmed, M. A. Rafiq, G. H. Awan, M. Zain-ul-Abdein, T. Xie, and T. Ozbakkaloglu. 2015. “Effect of Microwave Curing on the Construction Properties of Natural Soil Based Geopolymer Foam.” Construction and Building Materials 41: 117074. doi:10.1016/j.conbuildmat.2019.117074.
- Nazari, A., and M. Ghafouri Safarnejad. 2013. “Prediction Early Age Compressive Strength of OPC-based Geopolymers with Different Alkali Activators and Seashell Powder by Gene Expression Programming.” Ceramics International 39 (2, March): 1433–1442. doi:10.1016/j.ceramint.2012.07.086.
- Ozer, I., and S. Soyer-Uzun. 2015. “Relations between the Structural Characteristics and Compressive Strength in Metakaolin Based Geopolymers with Different Molar Si/Al Ratios.” Ceramics International 41 (8, September): 10192–10198. doi:10.1016/j.ceramint.2015.04.125.
- Papadopoulos, A. M., and E. Giama. 2007. “Environmental Performance Evaluation of Thermal Insulation Materials and Its Impact on the Building.” Building and Environment 42 (5): 2178–2187. doi:10.1016/j.buildenv.2006.04.012.
- Phetchuay, C., S. Horpibulsuk, C. Suksiripattanapong, A. Chinkulkijniwat, A. Arulrajah, and M. M. Disfani. 2014. “Calcium Carbide Residue: Alkaline Activator for Clay–fly Ash Geopolymer.” Construction and Building Materials 69 (October): 285–294. doi:10.1016/j.conbuildmat.2014.07.018.
- Sengul, O., S. Azizi, F. Karaosmanoglu, and M. A. Tasdemir. 2016. “Effect of Expanded Perlite on the Mechanical Properties and Thermal Conductivity of Lightweight Concrete.” Energy and Buildings 126 (2): 671–676. doi:10.1016/j.enbuild.2010.11.008.
- Shehab, H. K., A. S. Eisa, and A. M. Wahba. 2016. “Mechanical Properties of Fly Ash Based Geopolymer Concrete with Full and Partial Cement Replacement.” Construction and Building Materials 126: 560–565. doi:10.1016/j.conbuildmat.2016.09.059.
- Singh, B., G. Ishwarya, M. Gupta, and S. K. Bhattacharyya. 2015. “Geopolymer Concrete: A Review of Some Recent Developments.” Construction and Building Materials 85: 78–90. doi:10.1016/j.conbuildmat.2015.03.036.
- Sore, S. O., A. Messan, E. Prud’homme, G. Escadeillas, and F. Tsobnang. 2016. “Synthesis and Characterization of Geopolymer Binders Based on Local Materials from Burkina Faso – Metakaolin and Rice Husk Ash.” Construction and Building Materials 124: 301–311. doi:10.1016/j.conbuildmat.2016.07.102.
- Tang, S. W., E. Chen, H. Y. Shao, and Z. J. Li. 2015. “A Fractal Approach to Determine Thermal Conductivity in Cement Pastes.” Construction and Building Materials 74 (January): 73–82. doi:10.1016/j.conbuildmat.2014.10.016.
- Temuujin, J., A. van Riessen, and K. J. D. MacKenzie. 2010. “Preparation and Characterisation of Fly Ash Based Geopolymer Mortars.” Construction and Building Materials 24 (10): 1906–1910. doi:10.1016/j.conbuildmat.2010.04.012.
- Thakur, R. N., R. N. Thakur, and S. Ghosh. 2009. “Effect of Mix Composition on Compressive Strength and Microstructure of Fly Ash Based Geopolymer Composites.” ARPN Journal of Engineering and Applied Sciences 4 (4): 68–74.
- Tümsavaş, Z., Y. Tekin, Y. Ulusoy, and A. M. Mouazen. 2019. “Prediction and Mapping of Soil Clay and Sand Contents Using Visible and Near-infrared Spectroscopy.” Biosystems Engineering 177 (January): 90–100. doi:10.1016/j.biosystemseng.2018.06.008.
- Uddin, M. N., S. Velu, and P. Elumalai. 2015. “An Experimental Investigation of Red Soil Based Geopolymer Mortar without Portland Cement.” International Journal of Scientific & Engineering Research 6 (5): 1722–1732.
- Uddin, M. N., and V. Saraswathy. 2018. “A Comparative Study on Clay and Red Soil Based Geopolymer Mortar.” Civil Engineering and Architecture 6 (1, January): 34–39. doi:10.13189/cea.2018.060104.
- Ul Haq, E., S. K. Padmanabhan, and A. Licciulli. 2014. “Synthesis and Characteristics of Fly Ash and Bottom Ash Based geopolymers – A Comparative Study.” Ceramics International 40 (2): 2965–2971. doi:10.1016/j.ceramint.2013.10.012.
- Wang, K., Y. He, X. Song, and X. Cui. 2007. “Effects of the Metakaolin-based Geopolymer on High-temperature Performances of geopolymer/PVC Composite Materials.” Applied Clay Science 42: 586–592. doi:10.1016/j.clay.2015.07.008.
- Xie, T., and T. Ozbakkaloglu. 2015. “Behavior of Low-calcium Fly and Bottom Ash-based Geopolymer Concrete Cured at Ambient Temperature.” Ceramics International 41 (4): 5945–5958, May. doi:10.1016/j.ceramint.2015.01.031.
- Xu, H., Q. Li, L. Shen, W. Wang, and J. Zhai. 2010. “Synthesis of Thermostable Geopolymer from Circulating Fluidized Bed Combustion (CFBC) Bottom Ashes.” Journal of Hazardous Materials 175 (1–3): 198–204. doi:10.1016/j.jhazmat.2009.09.149.
- Yuan, J., P. He, D. Jia, C. Yang, S. Yan, Z. Yang, and Y. Zhou. 2016. “Effect of Curing Temperature and SiO2/K2O Molar Ratio on the Performance of Metakaolin-based Geopolymers.” Ceramics International 42 (14): 16184–16190. doi:10.1016/j.ceramint.2016.07.139.
- Zaidi, S. F. A., E. U. Haq, K. Nur, N. Ejaz, M. Anis-ur-Rehman, M. Zubair, and M. Naveed. 2017. “Synthesis & Characterization of Natural Soil Based Inorganic Polymer Foam for Thermal Insulations”. Construction and Building Materials 157: 994–1000. doi:10.1016/j.conbuildmat.2017.09.112.
- Zarwah, M. F., Gado, R. A., Feltin, N, and Ducourtieux, S. 2016. “Recycling and Utilization Assessment of Waste Fired Clay Bricks (Grog) with Granulated Blast-furnace Slag for Geopolymer Production.” Process Safety and Environmental Protection 103 (A): 237-251.
- Zhang, M., H. Guo, T. El-Korchi, G. Zhang, and M. Tao. 2013. “Experimental Feasibility Study of Geopolymer as the Next-generation Soil Stabilizer.” Construction and Building Materials 47 (October): 1468–1478. doi:10.1016/j.conbuildmat.2013.06.017.
- Zhang, Z., J. L. Provis, A. Reid, and H. Wang. 2014. “Geopolymer Foam Concrete: An Emerging Material for Sustainable Construction.” Construction and Building Materials 56: 113–127. doi:10.1016/j.conbuildmat.2014.01.081.
- Zhu, H., Newton, R. C., Kleppa, O. J., 1994. Enthalpy of Formation of Wollastonite (CaSiO3) and Anorthite (CaAl2Si2O8) by Experimental Phase Equilibrium Measurements and High-temperature Solution Calorimetry, American Mineralogist 79: 134-144.