ABSTRACT
Although the modular construction method is safer than traditional onsite construction methods, accidents still occur; therefore, modular projects have characteristic safety risks. This study investigated accident cases related to modular construction and identified the safety risk factors. The study evaluated accident cases related to modular construction that occurred in the United States from 2000 to 2018 and analyzed safety risk factors, such as the types and causes of accidents in these cases. In the process of analysis, the causal map was developed and it was used to identify the causes of accidents. The results of the analyses showed the major accident causes and types that occurred in these activities. Second, this study conducted a comparative analysis to identify differences between accidents in modular and general constructions. Furthermore, suggestions are proposed to prevent safety accidents and to develop management schemes based on the analyzed outcomes. This study contributes to the body of knowledge as a basic modular construction safety management study; it presents safety risk factors by identifying safety accidents in modular construction projects and helps safety managers frame appropriate measures when making decisions.
Graphical abstract
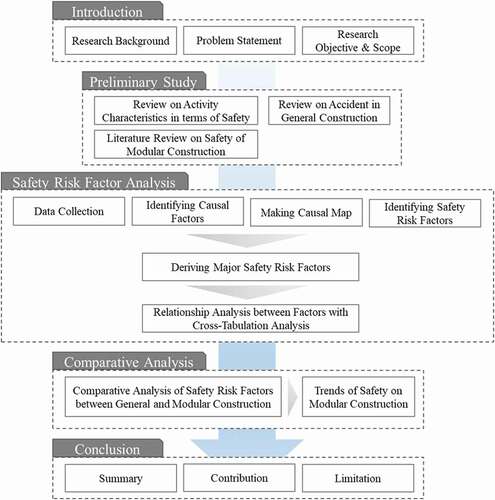
1. Introduction
Modular construction has been recently attracting increased interest. Many construction companies are attempting to build based on the use of the modular construction technique (Innella, Arashpour, and Bai Citation2019). According to the report by the Modular Building Institute (Citation2019), the global market size of modular construction in 2018 was valued at USD 112.3 billion; the market is expected to continue to grow during the forecasted period. Specifically, modular construction has been used in a variety of applications, such as dormitory and hotel constructions; it has also been applied to residential facilities as a solution to urban housing shortages (Smith Citation2011). Modular construction is developing because it has advantages in various areas compared with the general construction method. It is less affected by the external environment, with 70–80% of the work completed in the manufacturing plant (Fard et al. Citation2017; Smith Citation2011). Given that most of the work performed onsite is conducted at the manufacturing factory, it can ameliorate the shortcomings of the construction industry and take advantage of the good features of the manufacturing industry. Modular construction can also reduce the input of field workers, shorten construction duration, save energy, and improve the quality of buildings (Gibb Citation1999). Thus, modular construction is considered a sustainable construction method that leads to a sustained market growth (Lee et al. Citation2019). There is also an opportunity to reduce safety accidents because it is not profoundly affected by external environmental factors, such as rainfall and wind. Workers can become familiar with the workspace and work because they perform repetitive tasks in manufacturing factories (O’Connor, O’Brien, and Choi Citation2015). Additionally, as the amount of onsite work decreases, there are fewer workers required, and it is comparatively easy to manage them (Smith Citation2011). Modular construction is generally regarded as a safer method than traditional construction methods (Becker, Fullen, and Takacs Citation2003) because of these advantages. Many research studies reported that the adoption of modular construction methods can reduce safety risks and prevent the occurrence of safety accidents (Braverman, Morante, and Hofmayer Citation1997). However, accidents still occur in modular construction projects. The characteristics of the work are different from those in general constructions. Therefore, to ensure the safety of workers, the potential risk of safety accidents should not be ignored.
Contrary to the general perception that modular construction is comparatively safe, the United States (US) Bureau of Labor Statistics reported that accident rates in modular and prefabricated buildings are much higher than in the general construction and manufacturing industries (Bureau of Labor Statistics Citation2017). shows the incident rate, which represents the number of injuries and illnesses per 100 full-time workers for all industries, and the construction, manufacturing, and prefabricated wood building manufacturing industries in the US from 2002 to 2018. Furthermore, from a survey on modular construction workers, McGraw found that there were no significant changes in safety (McGraw Citation2011). These results raised doubts about the general perception of safety in relation to modular construction accidents.
Figure 1. Incident rates in all industries, construction, manufacturing, and prefabricated wood building manufacturing (the incidence rates represent the number of injuries per 100 full-time equivalent workers).
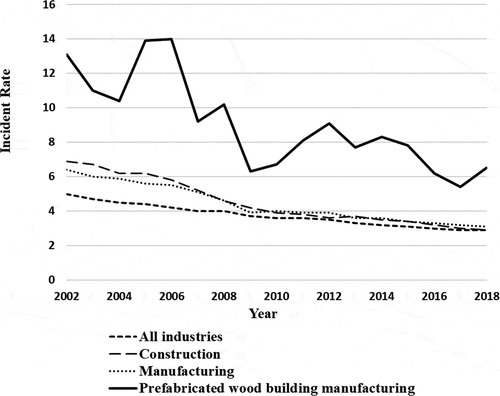
As modular construction projects increase, more trained workers and skilled managers, who are familiar with safety risks, are needed to complete the projects successfully (Fard et al. Citation2017). Existing construction companies, managers, and employees, who are working on general constructions, are also participating in modular construction projects. Additionally, there is a lack of capable contractors who have adopted modular construction processes (Blismas, Pasquire, and Gibb Citation2006). Therefore, safety management is being applied to modular construction projects in a similar manner to that of general construction projects without consideration of the differences between the two methods (Becker, Fullen, and Takacs Citation2003)
The application of safety management for general constructions to modular constructions is limited because there are different activities from those in general constructions (Ikuma, Nahmens, and James Citation2011). Furthermore, given that modular construction is associated with a large proportion of manufacturing processes, project participants should understand both the management aspects of manufacturing processes (offsite) and construction processes (onsite). Therefore, there is a clear need to reflect the characteristics of modular construction in safety management; this requires a detailed analysis of safety risk factors in modular construction. This construction method would thus provide an opportunity to understand and improve the safety management of modular construction by comparing its differences from the risk factors associated with general construction. The determination of the differences could ensure the primary targets of modular construction in terms of safety and accident occurrences.
Previous research studies had been conducted to identify safety risks in modular construction. However, only a few of them have derived safety risk factors based on accident cases that occurred in modular construction projects. Accordingly, suggestions that consider characteristics of activities in modular construction are lacking. Therefore, this study investigates safety risk factors by analyzing accident cases in modular construction and discusses several findings to understand the characteristics of safety accidents that occur during modular projects. This study first analyzes the major accident factors with accident cases recorded by the Occupational Safety and Health Administration (OSHA) in the US. To investigate the various characteristics of accidents, the study first collects modular construction-related accident cases using web crawling and analyze all the cases including the types and causes of accidents, and the activities in which the accidents occurred. Second, the study compares the safety risk factors and characteristics of accidents in general and modular construction. These include accident rates, project cost, fall location, and fall height. With the results of comparative analysis, the study identifies the characteristics of safety accidents and discuss the differences that may have been disregarded in the safety management of modular construction.
This study deals with safety accidents that occur in activities during the manufacturing (offsite) and construction processes (onsite) in modular construction projects. For construction processes, several onsite activities, such as unit transportation, module unit lifting, unit installation, and finishing activities are targeted because these activities characterize the modular project. Foundation and temporary work are excluded from the scope of this study because they are similar to that in general construction, and it is difficult to distinguish the project types when collecting data. The accident cases used in this study are related to modular constructions recorded by the OSHA from 2000 to 2018. The analyzed results of the study can constitute the basis of research outcomes for the formulation of safety management guidelines in modular construction. Furthermore, it will also assist safety managers to understand and make prompt safety decisions by presenting major risk factors for each activity of the modular construction process. Comparative analysis is conducted by comparing some of the safety risk factors analyzed in the study of Kang et al. (Citation2017). Kang et al. compiled the trend of construction accidents, especially falls, with data from OSHA’s database related to constructions in the US from 1997 to 2012. By comparing the risk factors analyzed based on accident cases in modular constructions with the research of Kang et al. (Citation2017), it is possible to assess whether the trend of accidents in modular constructions differs from that for general constructions. Specifically, the factors investigated included the accident ratio, project cost, fall height, and fall location.
2. Preliminary study
2.1. Research studies on safety management in modular constructions
Many studies have identified accident types based on the investigation of accident cases to establish a safety management system; they have classified how and why these accidents occur (Fullman Citation1984). Some works have focused on the management of the safety of modular construction. Becker, Fullen, and Takacs (Citation2003) conducted a survey to identify possible hazards to workers when modular units were installed onsite. Based on the survey results, major risk tasks and accident types were analyzed in modular construction sites. This research only focused on onsite activities. McGraw Hill Construction (Citation2013) conducted a survey to determine the three primary reasons why modular construction is deemed safe. Based on the results, modular construction is safe because (a) complex work is executed on the ground and offsite, (b) there are fewer workers on the field, and (c) works conducted at increased heights are reduced (McGraw Hill Construction Citation2013). James et al. (Citation2012) conducted a research study on the application of the lean construction method to some of the operations in the modular manufacturing plant and showed that the lean method could reduce the risk exposure of workers. Fard et al. (Citation2017) investigated the accident cases that occurred at the modular and prefabricated construction stage as documented in OSHA. They assessed recorded case data in terms of injury types, accident causes, and types of equipment involved, and discussed approaches to reduce accidents in modular projects. Based on this review of the literature, this study concludes that there are previous research studies related to the safety management of modular construction, but most of them were conducted only for the empirical identification of some hazardous factors based on surveys. Additionally, most of them focused only on onsite construction work. The accident rate at offsite plants is also high, and accidents occur frequently during the manufacturing process (James et al. Citation2012). Therefore, for the safety management of modular construction, it is necessary to study the construction process and the accidents that occur during the manufacturing process.
Specifically, only a few research studies have discussed the safety risk factors related to activities in modular construction. Given that the activities have different characteristics from those of general construction, an in-depth investigation of activities is necessary. Safety management that fully considers the characteristics of activities in modular construction can be of great help in the planning and execution of modular projects. To establish a safety management plan, this study aims to analyze accident cases that occur in modular construction projects to derive safety risk factors. By utilizing the safety risk factors, this study then conducts a comparative analysis with accidents in general construction cases to identify relevant characteristics.
2.2. Characteristics of activities in modular construction
Modular construction differs from general construction and manufacturing in various ways (Smith Citation2011). There are differences in production methods; differences also occur owing to various characteristics, such as scheduling, work, quality, and risk of modular construction projects. According to the study of Smith(Citation2011), characteristics of modular construction could also affect safety management. Among these characteristics, this study selects some significant characteristics that could affect safety. It investigates some factors, such as workplace, workers, works at increased heights, and lifting work that could have a significant impact on safety. shows the characteristics that could affect safety in modular construction.
Table 1. Characteristics of modular construction
The first characteristic is the workspace. In modular construction, workers could have a better understanding of space to perform repetitive tasks in the same workspace even if the project changes (Smith Citation2011). In addition, because external environmental factors cannot serve as variables in terms of a fixed indoor environment, the change in the workspace itself is small (Isabelina and Laura Citation2012). From the aspect of the manufacturing process, conveyor systems and a production process have been introduced in general manufacturing plants; however, in modular unit production, there is considerable additional work that needs to be done by workers who move around (Bae et al. Citation2012). This increases the frequency with which work positions are not fixed, thus resulting in complex workflows and worker exposure to risks.
The second characteristic relates to the workers themselves. Modular construction has relatively few inputs owing to its introduction of automation and its simplicity and repeatability (Smith Citation2011). Therefore, safety management can be more efficient with comparatively few objects. Conversely, the number of workers who have experience is small owing to the low numbers of modular constructions and construction cases. Additionally, there is a lack of experts who can instruct other workers (Joshua Citation2016). There is also a limit to the operator’s ability to identify and recognize hazards that may arise from the work. Thus, it is necessary to improve capabilities based on prior safety education.
The third characteristic is work at increased heights. By converting the vertical working form of the general construction project into the horizontal working form of the production line of the fabrication plant, the construction work of the building is conducted on the ground. However, works still exist at heights where workers could fall, such as the installation and roofing of modular units, and the finishes of the exterior parts (Lawson and Ogden Citation2010). Although the proportion of falls is relatively small in general manufacturing tasks, it is possible that these may occur during the modular unit production phase owing to the use of unit structures, ladders, or mobile scaffolding (Fard et al. Citation2017). Therefore, a management system is needed to prevent falls during work.
The last characteristic is lifting work. Modular construction requires a high-performance crane to lift and install module units of approximately 20,000 kg; it also uses additional equipment to prevent damages and distortions when the unit is lifted (Lawson and Ogden Citation2010). In addition, when the unit is suspended from a crane, the worker below it may adjust the unit’s position or perform operations, such as jointing work. Therefore, it is important to plan cranes and secure the safety of workers to operate management systems, such as securing work lines and workspaces.
This study demonstrates that the characteristics of safety-related factors in modular construction, such as workspaces, workers, work at increased heights, and lifting work, are different from those in general construction and general manufacturing. Although there are characteristics that can be advantageous regarding their capacities to reduce accidents, there are additional management targets that need to be considered during modular construction. These characteristic differences have a direct effect on the actions of the workers and can cause safety accidents (Oliver Citation1986). Therefore, this study analyzes the characteristics of accidents based on modular construction accident cases and identifies the relationships with the activity characteristics. The results can also be used for comparative analyses with accidents in general constructions.
3. Safety risk factor analysis in modular construction
3.1. Data acquisition
To investigate accidents in modular construction, this study uses OSHA’s database. The accident information of the entire US industry is recorded in OSHA; OSHA provides summaries and detailed information for each accident case. Accident data in OSHA can be classified using standard industrial classification (SIC) or North American industry classification system (NAICS) codes. However, accident data are not usually separated among sectors associated with modular construction; hence, there is a limit to the capacity to search for accidents related to modular construction based on SIC and NAICS codes. In this study, data collection was conducted with web crawling using Python 3.6 to extract only the desired accident data. By coding with Python, accident data – including specific keywords related to modular construction – were extracted. The keywords used in this study include modular, prefabricated, and mobile homes. This research focuses on accidents that occurred from 2000 to 2018 in the US. There were 63 cases with the keyword “mobile homes,” 75 with “prefabricated,” and 102 with “mobile homes.” Thus, a total of 236 accident cases were collected with the exception of three overlapping cases. Although the aforementioned keywords were included, some accident samples were collected that did not correspond to the modular manufacturing and construction processes related to the scope of this research. For example, some accident cases include the word “modular,” but these accidents were caused by modular boilers, modular conveyor belts, modular pipes, etc. Furthermore, samples also included accidents caused by fire after the completion of the construction. Therefore, the cases needed to be resorted to be used for analysis. The resorting is conditional based on the inclusion of several keywords related to modular construction work, such as the installing and lifting processes, assembly, panel, and unit. Among them, 107 cases of accidents that occurred during the manufacturing and construction processes were selected as the final data and used for the analysis of the study. The contents of the accidents and the descriptions were used in this study.
3.2. Identification of casual factors
Prior to the analysis of the risk factors of each accident, it was necessary to identify the causal factors for modular construction. To identify the causal factors of the accident, this study lists and identifies the related causes of accidents in construction projects and modular constructions registered in the OHSA (Citation2015), Health and Safety Commission (Hide et al. Citation2003), Korean Occupational Safety and Health Agency (KOSHA Citation2014), and the Construction Safety Management Information System (COSMIS Citation2019). The causal factors were categorized into cause type, detailed cause type, and causal factors. shows the casual factors for modular construction.
Table 2. Casual factors for modular construction
According to Heinrich’s domino theory (Heinrich, Citation1941), unsafe conditions and unsafe acts are the fundamental factors related to accidents. Therefore, safety management should be enforced to eliminate them. However, the content and description of the accident cases used in this study were not specific and did not contain all the information. To uncover an unsafe act, the study needed to determine the exact background of the accident, such as information about workers, educational status, management conditions, and other related data (Baldissone et al. Citation2019). Accident cases from OSHA rarely contain detailed information to identify unsafe acts in an exact manner. In other words, determining the cause of an accident can be inaccurate because it has a risk that involves the subjective views of the researcher during the identification of the cause of an accident as an unsafe action with an indirect cause. Therefore, this study limited its scope to causes of accidents by unsafe conditions only; this factor can be objectively identified. The cause types are selected based on the major categories used in the construction industry: material/equipment, safety protection devices, personal protection equipment (PPE), site layout/spaces, and workplaces.
Detailed cause types for material/equipment are slippery/pointed materials, improper use of equipment, and defective material/equipment. They also include no safety devices, non-operating safety devices, and a lack of risk indications for safety protection devices. PPE cause type is classified into (a) no-PPE and (b) defective-PPE types. Detailed cause types for the site layout/space are the improper arrangement of the workplace, insufficient workplace, congested work areas, and unstable work areas/platforms. Regarding the workplace, detailed types of causes are poor illumination/ventilation, excessive noise, unpredictable weather, and poor housekeeping. Based on the derived causal factors, the causes of the accidents for the various cases were analyzed.
3.3. Identifying accident causes
To use the causal factor table presented in the previous section, this study created a causal map that can visually represent the causal factor. A causal map in a tree form is one of the most common methods used to describe the process of a problem and its causes and to analyze the cause of an accident (Abdelhamid and Everett Citation2000). In the causal map, the decision for one accident is made by switching from the upper category to the lower category. The cause of the lowest level is then determined. By creating and using this causal map, this study can make decisions at the stage of determining the cause of an accident in the initial modular construction process.
The causal map for modular construction is first classified into the manufacturing and onsite construction processes; the accident types based on the work activities for each process are then presented. In the lower part, the causal factors of accidents derived previously are expressed in tree form. shows the causal map for modular construction. Using the causal map, based on the accident case information in the database, the study identifies the cause of the accident by selecting each factor from the upper category to the lowest cause. To identify the cause of the accident, the study adheres to the following procedure: the manufacturing and construction process, unit work activity, accident type, cause type, detailed cause type, and finally the causal factor. Each identified outcome is re-entered in the database that stored modular construction accident cases and produced results. shows the results of the analysis of causes according to the modular construction activities. It contains the number of accident cases in all activities and causes. Activities in the manufacturing process (offsite) are divided into material imports and load (M1), cutting (M2), lifting (M3), unit assembly (M4), interior finishing (M5), exterior finishing (M6), and packing (M7). Activities in the construction process (onsite) are divided into unit transport (C1), unit lifting (C2), unit installation (C3), roof finishing (C4), interior finishing (C5), and exterior finishing (C6)
Table 3. Cause analysis results in modular construction
4. Results of accident analysis
After identifying the accident cases, the results were analyzed are categorized. A total of 107 accident cases were used to analyze the causes of the accidents. There were 26 accidents during the manufacturing process and 81 accidents during the construction process. In this section, the study summarizes the main factors based on the analysis of the accident cases in the previous section. By analyzing the accident cases, major hazardous activities, accident types, and accident causes were derived. First, the activities based on which the accident occurred were classified in detail, and major hazardous activities in the manufacturing and construction processes were identified. Second, the types of accidents were classified into the following categories: falls, struck-by falling object, crush/crash, and caught in. Finally, the major accident causes were derived from the results of the cause analysis conducted in the previous section.
4.1. Hazardous activities
shows the types of accidents by activities, and it indicates the number of cases. As the table indicates, in the manufacturing process, 31% of the accidents occur during the material import and loading activities, and 16% are at the time of unit assembly and interior finishes. Cutting and exterior finishing processes account for 12% each. Conversely, during the construction process, unit installation activity is the most hazardous activity with over 50% of all accidents. Roof finishing is second at 20%, and unit lifting and exterior finishing are third with 7%.
Table 4. Types of accidents in manufacturing and construction processes
4.2. Accident types
also lists the types of accidents in the manufacturing and construction processes. As this table indicates, accidents caused by falls and struck-by falling objects are the major types of accidents during the manufacturing process at a rate of 31%. Moreover, there are few accidents caused by caught-in and cuts at the rate of 15% each. In the case of the construction process, falls account for 35%, which is the highest percentage overall, wherein 27% of accidents were attributed to crushes/crashes, and 23% to falling objects. In the entire modular construction process, fall accidents are the major accident types followed by the struck-by falling objects and crush/crash categories.
4.3. Accident causes
Accidents occurred owing to various causes in modular construction. Thus, this section mentions only a few of the major causes of accidents. In the manufacturing process, unstable work areas/platforms yielded a maximum frequency rate of 35%. Defective material/equipment (15%) and improper arrangements of workplaces (12%) also yielded high rates compared with the other causes. There were also accidents caused by the improper use of equipment (8%) and the lack of use of PPE (8%). During the construction process, defective material/equipment accounted for 32% and constituted the major accident cause. Unstable work area/platforms constituted the second highest cause at 23%. The categories no PPE and improper arrangement of workplace accounted for 20%.
In view of the results during the manufacturing process, one of the interesting features was the high percentage of falls. There was a risk of falls when workers built or finished modular unit structures using ladders or when they worked above the structure. According to the National Safety and Health Agency’s industrial disaster statistics, 70% of falls occur at a low height of less than 3 m (KOSHA Citation2016). Considering that the height of the unit is less than 3 m, it is obvious that a hazard exists. Premeasures can be identified to prevent falls. Conversely, from the aspect of the construction process, the characteristics of safety accidents refer to their large numbers of lifting and installation of modular units. The components that made up the modular units also acted as a factor that caused the accidents. In particular, various types of accidents occurred during the installation activity because (a) the worker movements and available spaces were not sufficiently considered and (b) the number of fall prevention devices was not adequate.
5. Comparative analysis with general construction
Modular construction projects were executed by existing construction companies, and the same safety management system for general construction was applied to modular construction (Blismas, Pasquire, and Gibb Citation2006). It is necessary to compare the trends and characteristics of safety accidents between modular construction and general construction to see if existing safety management schemes can be applied. If there are differences, the cause should be identified and reflected in the safety management of modular construction. This process can allow the establishment of safety management for modular construction.
Comparative analysis requires an analysis of general construction in a similar manner as conducted for modular construction in this study. Kang et al. (Citation2017) collected 20,997 accident cases that occurred in the construction industry that were recorded in OSHA and identified various safety risk factors for different accident cases. In particular, the same authors presented a detailed analysis of the trend of falls in the US construction industry. According to the results of this study, the main type of accidents that occurred in modular construction projects was falls. This is judged to be suitable for comparison with the results of this study because of the similar scope of the analyzed results and the intensive analysis on falls. For this reason, this study conducted comparative analyses with those conducted by Kang et al. (Citation2017) that identified the trends of modular construction accidents.
This study selected four components, namely the accident type ratios, project costs, fall heights, and fall locations, and conducted a comparative analysis on these factors. The modular construction accident cases collected from OSHA have different information in each case. For example, some cases included information about fall protection, but most did not. Therefore, this study selected the four components that were mainly available for many accident cases. The study examined the frequency of accidents in modular construction, classified them into four components, and compared their frequencies with those obtained from general constructions.
5.1. Accident type ratio
lists the ratio of accident types between the result of this study for modular and general construction. The accident data from KOSHA are presented together to compare the accident type ratio in the manufacturing industry. Both general and modular constructions account for the highest percentage of falls. The characteristic part pertained to the percentage of falls during the manufacturing process, which was also high. In the modular construction process, work was divided into manufacturing processes (offsite) and construction processes (onsite). Furthermore, the manufacturing rate was approximately in the range of 70–80% (Florida Citation2004). Despite the reduced vertical work, falls accounted for the highest percentage in modular construction. A review of the manufacturing process indicated that most of the work was done using ladders, scaffolding or building structures, except for floor concrete placement and flat paneling (Lawson and Ogden Citation2010; Fard et al. Citation2017).
Table 5. Ratio of accident type in modular and general construction
5.2. Project cost
shows the ratio of accident by project cost in modular and general constructions. Project costs refer to the scale of the project. This study compared the accident rate by the project scale and checked whether the accidents that occurred in modular construction were affected by the scale of the project. Small companies are vulnerable to safety accidents because they have less manpower and resources available for training (Dong et al. Citation2009). Although much research is being conducted for safety management in small construction projects, many disasters still occur (Navon and Kolton Citation2007). The number of experienced workers is small, and there is also a shortage of experts who can transfer skills (Joshua Citation2016). Not many large-scale modular projects have been conducted at home and abroad.
Table 6. Accidents by project cost in modular and general construction
5.3. Fall location
According to the accident analysis results of this study, falls were the major types of accidents and account for more than 30% of each process. Falls were also the main accident types in the general construction industry and a detailed comparative analysis was necessary. shows the ratio of falls according to location in the modular and general constructions. Both general and modular constructions are associated with the most frequent falls on the roof, followed by structures and ladders. Critical works in the modular project were the lifting module units. Depending on the number of loads per day, the entire construction duration was affected (Lawson and Ogden Citation2010). Continuous lifting and installation of the unit required a minimum number of obstacles in the lifting radius and careful planning of the worker’s layout. Given that the lifting and installation of the module unit are ongoing, the safety net system and scaffold may not be installed for the efficiency of work and shortening of the construction duration. If the external finishing rate was low and the finishing work occurred onsite, the scaffold was installed after the completion of the unit lifting and installation (Kamali and Hewage Citation2016).
Table 7. Classification of falls based on location in modular and general construction
5.4. Fall height
lists the ratio of falls by height in modular and general constructions. In general constructions, more than 80% of accidents occur below 9 m. The safety net system and safety barriers may not be installed at low-rise construction sites. Moreover, according to the standard for the installation of a safety net, the first stage is to be installed at a position in the range 7–10 m from the ground (Hinze and Gambatese Citation2004). In addition, the project types of accident data in the US are associated with high percentages of housing and dwellings (Kang et al. Citation2017). The fall height in modular construction is related to the unit height. The average module unit is approximately 3 m in height. Falls from ladders and structures during the manufacturing process and falls in residential modular construction affected this result.
Table 8. Classification of falls based on height in modular and general construction
6. Discussion
6.1. Trends of accidents in modular construction
Using the accident data of OSHA, this study analyzed the accident cases in modular constructions, derived the major hazardous activities, and the types and causes of accidents. The analyzed results were compared with accidents in general constructions to identify the characteristics of safety accidents in modular constructions. There are notable findings based on the analyzed results. In the entire process of modular construction, falls accounted for 35%, struck-by falling objects accounted for 25%, crushes/crashes accounted for 22%, caught-in account for 7%, and others accounted for 10% of the accidents. Falls accounted for the highest percentage in both manufacturing and construction processes. Although the activities during which falls occurred decreased, the risk of falls still existed in other activities, such as unit installations, and roof and exterior finishes. In addition, during the manufacturing process, falls were the major accident type owing to the extensive use of ladders to assemble components and to finish unit interiors or exteriors. In terms of accident causes, approximately 50% of the accidents were caused by unstable work area/platform and defective material/equipment. Accidents occurred owing to a lack of preplanning based on considerations of the worker movements and workspace, and a lack of pre-inspection and equipment management. Additionally, accidents can occur at modular construction project sites because PPE is missing or not worn.
Through comparative analyses with accident trends in general constructions, several characteristics of accidents in modular constructions were identified. Similar to general constructions, safety accidents in modular constructions usually occurred in small projects. In addition, the frequencies of fall accidents based on height were maximized for heights in the range of 3–6 m. Most of the projects which adopted modular construction in the US were residential, low-rise commercial buildings, and medical and educational facilities. From the aspect of fall location, falls were most common on the roof. Poor management regarding the proper use of PPE and the insufficient number of safety devices for the prevention of falls cause fall accidents from the roof. By analyzing the modular accident trends, it is possible to see how modular construction differs from general construction and which risks should be managed more intensively.
6.2. Suggestions of safety management for modular construction
As a result of the analysis, it is considered that intensive safety management is required for unit installations with the highest accident rate during the construction process. The main causes of falls during unit installations are the absence of personal safety equipment and unstable workspaces. Given that prebuilt units are installed in the field in a short period of time in modular constructions, installations of safety devices, such as fall-prevention nets, are not performed as thoroughly as in general construction projects for the sake of the efficiency of work. In particular, personal safety devices may be neglected in consideration of workability, as the work of settling and joining units takes time. Therefore, prior safety education should be conducted to alert workers to falls on the educational side, and safety measures should be taken into account to increase work efficiency on the technical side at the same time. In addition, in organizational terms, movements of workers should be planned in advance for works associated with falling risks. Correspondingly, the safety managers’ ability to manage the site is important.
When installing the unit, there is a high risk of accidents from falling objects; the modular unit itself is unstable or defective. In general, accidents caused by struck-by falling objects are caused by crane defects or poor driving by crane drivers; in modular constructions, there were also many cases in which the unit itself was defective. This may be attributed to improper welding or bonding during the unit’s manufacturing process, or damage due to impact during transport to the site, or damage to the component due to distortions during crane lifting. Thus, from an organizational point of view, a systematic procedure is needed for the verification of confidentiality in the manufacturing of modular unit structures. The manager’s role is important to check and evaluate whether the manufacturing has been conducted in accordance with the design. On the technical side, technologies, such as vibration control systems, should be installed to reduce impact during transportation, which will minimize the shaking on the vehicle.
Many accidents have been caused by falls and falling objects in the modular manufacturing process, and safety management should also be considered for this purpose. When assembling the structure of the modular unit, accidents caused by falls and falling objects have occurred. Modular manufacturing plants are mainly responsible for handling heavy loads, and all the components and modular units are conducted with an overhead crane. In addition, work was conducted on the unit structure by using a ladder or movable scaffolding. In general manufacturing, work at locations at increased heights is rarely conducted. Additionally, there is an insufficient number of devices for the prevention of falls at manufacturing plants. Conversely, considering the height of the modulator unit, safety measures for preventing falls are insufficient, even though there is sufficient room for falls. Therefore, it is necessary to thoroughly conduct prior safety training on the handling of heavy objects and on the use of cranes in the construction of structures. On the technical side, fall prevention ropes and devices should be installed on the structure itself or on the production line to prevent falls.
It is certain that modular construction has many advantages in terms of safety by introducing manufacturing characteristics and performing most of the work in manufacturing plants. It is also obvious that safety accidents can be reduced and workability at construction sites can be improved. However, as the results of this study showed, safety accidents still occur, and the characteristics of modular construction activity cause different types of accidents with different causes than those of the general construction and manufacturing industries. It is also confirmed that various accidents occur not only during the modular construction process but also during the manufacturing process because of the activities needed to manufacture modular units. In other words, modular construction had different work characteristics from existing construction projects. Thus, the types and causes of accidents are different, and accident prevention measures are thus needed.
7. Conclusion
Modular construction has various advantages in terms of safety and has been extensively applied recently. Although there have been studies related to modular safety management, accident cases have rarely been analyzed and their characteristics have not been identified. In addition, the focus of previous studies was on the work onsite, and the unit manufacturing process was rarely considered. Therefore, this study investigated the accident cases of modular constructions and analyzed safety risk factors, such as major accident types and the cause of accidents. In addition, this study conducted a comparative analysis between modular construction and general construction to identify differences in characteristics and trends of safety accidents in modular construction. Nevertheless, the number of accident cases was small in the selection of major accident types and causes. If more accident cases could be collected and analyzed, the cause of accidents can be identified more accurately, and it may help in the establishment of safety management measures. Therefore, it is necessary to secure cases of safety accidents in modular construction and to analyze more detailed activity levels.
Nevertheless, this study is meaningful academically in that the safety management of modular construction was extended beyond the construction process to the manufacturing process, whereby safety accident cases were analyzed for each of the activities executed at each studied process. This study also presented a causal map for accidents in modular construction. The causal map can be used to make a decision on the cause of the accident. In addition, by comparing the accident trends in general construction, the characteristics of modular construction were identified in detail. This can prove the need for specialized safety management in modular constructions.
Findings in this study could contribute to the diagnosis of the current state of accident factors in the modular construction industry in the US. This can be used to predict the probability of accidents offsite and onsite, and to develop a strategy to reduce the number of accidents in modular construction projects. The outcomes will assist safety managers to understand safety risk factors and to make prompt safety decisions. They can also prioritize risk factors and control unsafe conditions in various working sites.
Acknowledgments
This research was supported by Gant No. 21RERP–B082884-08 from Housing Environment Research Program funded by the Ministry of Land, Infrastructure and Transport of Korean government.
Data availability statements
Some or all data generated or analyzed during the study are available from the corresponding author by request.
Disclosure statement
No potential conflict of interest was reported by the authors.
Additional information
Funding
Notes on contributors
Gilsu Jeong
Gilsu Jeong is a Ph. D candidate at the Department of Architecture of Seoul National University. He received a bachelor’s degree from SNU in 2018. In 2020, he graduated master’s course for construction management at SNU. His main research area is construction engineering and management including safety management and modular construction. Recently, he has studied workers’ unsafe behavior and unstable balance of body which can cause accidents in construction sites. Also, he has participated in projects that make a roadmap for intelligent house for the future housing.
Hyunsoo Kim
Hyunsoo Kim received a bachelor's degree in 2008, a master's degree in 2010 and a doctorate degree in 2015 at the Department of Architectural Engineering of Seoul National University. Since 2019 he has been working as an assitant professor at the Department of Architectural Engineering of Dankook University. Currently, his major research topics include wearable sensing based activity recognition and safety management.
Hyun-Soo Lee
Hyun-Soo Lee received bachelor’s degree in 1983 and master’s degree in 1985 at the Department of Architecture of Seoul National University. He has studied Construction Engineering & Management at the University of Michigan since 1988 and finished doctor’s degree in 1992. And he worked for the Dept. of Architecture Engineering in Inha University as a professor. Since 1997, he has been working as a professor at the Department of Architecture and Architectural Engineering of Seoul National University. His major research area is Construction Engineering and Management.
Moonseo Park
Moonseo Park got into Department of Architecture of Seoul National University in 1985, completed the courses for a bachelor’s degree in 1989, and graduated master’s course for City Planning at SNU in 1992. In 1998-2001, he received master’s degree and doctor’s degree for Project Management in MIT. After graduation, he worked for the Dept. of Building in National University of Singapore as an assistant professor. Since 2005 he has been working as a professor at the Department of Architectural Engineering of Seoul National University. Currently, his major research area is systematic approach for construction, knowledge-based construction etc.
Hosang Hyun
Hosang Hyun received a doctorate degree at Seoul National University in 2019, and he has been dedicated to research at Seoul Housing & Communities Corporation as a senior researcher. His main research area is construction management and off-site construction.
References
- Abdelhamid, T., and J. Everett. 2000. “Identifying Root Causes of Construction Accidents.” Journal of Construction Engineering and Management 126 (1): 52–60. doi:https://doi.org/10.1061/(ASCE)0733-9364(2000)126:1(52).
- Bae, B., K. Kim, H. Cha, and D. Shin. 2012. “To Improve Production Process of the Modular Using the Conveyor System.” Korean Journal of Construction Engineering and Management 13 (5): 103–112. doi:https://doi.org/10.6106/KJCEM.2012.13.5.103.
- Baldissone, G., L. Comberti, S. Bosca, and S. Murè. 2019. “The Analysis and Management of Unsafe Acts and Unsafe Conditions. Data Collection and Analysis.” Safety Science 119: 240–251. doi:https://doi.org/10.1016/j.ssci.2018.10.006.
- Becker, P., M. Fullen, and B. Takacs. 2003. Safety Hazards to Workers in Modular Home Construction. Silver Spring, MD: Center to Protect Workers’ Rights.
- Blismas, N., C. Pasquire, and A. Gibb. 2006. “Benefit Evaluation for Off-site Production in Construction.” Construction Management and Economics 24 (2): 121–130. doi:https://doi.org/10.1080/01446190500184444.
- Braverman, J., R. Morante, and C. Hofmayer. 1997. Assessment of Modular Construction for Safety-related Structures at Advanced Nuclear Power Plants (No. NUREG/CR–6486). Nuclear Regulatory Commission.
- Bureau of Labor Statistics. 2017. “Number and Rate of Nonfatal Occupational Injuries and Illnesses by Selected Industry.” Accessed 27 March 2019. http://www.bls.gov/iif/oshsum.htm
- COSMIS. 2019. “Accident Occurrence Status by Accident Cause.” Accessed 9 March 2019. https://www.cosmis.or.kr/
- Dong, X. S., A. Fujimoto, K. Ringen, and Y. Men. 2009. “Fatal Falls among Hispanic Construction Workers.” Accident Analysis & Prevention 41 (5): 1047–1052. doi:https://doi.org/10.1016/j.aap.2009.06.012.
- Fard, M., S. Terouhid, C. Kibert, and H. Hakim. 2017. “Safety Concerns Related to Modular/prefabricated Building Construction.” International Journal of Injury Control and Safety Promotion 24 (1): 10–23. doi:https://doi.org/10.1080/17457300.2015.1047865.
- Florida, R. 2004. The Rise of the Creative Class. New York, NY: Basic Books.
- Fullman, J. 1984. Construction Safety, Security, and Loss Prevention. New York, NY: Wiley-Interscience.
- Gibb, A. 1999. Off-site Fabrication: Prefabrication, Pre-assembly and Modularization. Caithness, UK: John Wiley & Sons.
- Heinrich, H. W. 1941. Industrial Accident Prevention. New York, NY: McGraw Hill.
- Hide, S., S. Atkinson, T. Pavitt, R. Haslam, A. Gibb, and D. Gyi. 2003. Causal Factors in Construction Accidents. HSE research report 156. London: Health and Safety Executive.
- Hinze, J., and J. Gambatese. 2004. “Factors that Influence Safety Performance of Specialty Contractors.” Journal of Construction Engineering and Management 10: 1061.
- Ikuma, L. H., I. Nahmens, and J. James. 2011. “Use of Safety and Lean Integrated Kaizen to Improve Performance in Modular Homebuilding.” Journal of Construction Engineering and Management 137 (7): 551–560. doi:https://doi.org/10.1061/(ASCE)CO.1943-7862.0000330.
- Innella, F., M. Arashpour, and Y. Bai. 2019. “Lean Methodologies and Techniques for Modular Construction: Chronological and Critical Review.” Journal of Construction Engineering and Management 145 (12): 04019076. doi:https://doi.org/10.1061/(ASCE)CO.1943-7862.0001712.
- Isabelina, N., and H. I. Laura. 2012. “Effects on Lean Construction on Sustainability of Modular Homebuilding.” Journal of Architectural Engineering 18 (20): 155–163. doi:https://doi.org/10.1061/(ASCE)AE.1943-5568.0000054.
- James, J., L. Ikuma, I. Nahmens, and F. Aghazadeh. 2012. “Influence of Lean on Safety Risk Exposure in Modular Home-building.” In IIE Annual Conference. Proceedings(p.1), Institute of Industrial and Systems Engineers.
- Joshua, S. 2016. Smart Construction: How Offsite Manufacturing Can Transform Our Industry. KPMG, Technical Report CRT059791.
- Kamali, M., and K. Hewage. 2016. “Life Cycle Performance of Modular Buildings: A Critical Review.” Renewable and Sustainable Energy Reviews 62: 1171–1183. doi:https://doi.org/10.1016/j.rser.2016.05.031.
- Kang, Y., S. Siddiqui, S. J. Suk, S. Chi, and C. Kim. 2017. “Trends of Fall Accidents in the U.S. Construction Industry.” Journal of Construction Engineering and Management 143 (8): 04017043. doi:https://doi.org/10.1061/(ASCE)CO.1943-7862.0001332.
- KOSHA. 2014. Industrial Accident Cause Survey in 2014. KOSHA
- KOSHA. 2016. Technical Specification for Root Cause Analysis, KOSHA GUIDE P-151-2016. KOSHA
- Lawson, R. M., and R. G. Ogden. 2010. „Sustainability and Process Benefits of Modular construction.„ In Proceedings of 18th CIB World Building Congress, TG57-Industrialization in Construction (pp. 38–51).
- Lee, J.-H., J.-S. Kim, H.-J. Lee, Y.-M. Lee, and H.-G. Kim. 2019. “Small-scale Public Rental Housing Development Using Modular construction—Lessons Learned from Case Studies in Seoul, Korea.” Sustainability 11 (4): 1120. doi:https://doi.org/10.3390/su11041120.
- McGraw Hill Construction. 2011. Prefabrication and Modularization: Increasing Productivity in the Construction Industry. Bedford, MA: McGraw Hill Construction.
- McGraw Hill Construction. 2013. Safety Management in the Construction Industry: Identifying Risks and Reducing Accidents to Improve Site Productivity and Project ROI. Bedford, MA: McGraw Hill Construction.
- Modular Building Institute. 2019. 2019 Permanent Modular Construction Report. MBI
- Navon, R., and O. Kolton. 2007. “Algorithms for Automated Monitoring and Control of Fall Hazards.” Journal of Computing in Civil Engineering 21 (1): 21–28. doi:https://doi.org/10.1061/(ASCE)0887-3801(2007)21:1(21).
- O’Connor, J. T., W. J. O’Brien, and J. O. Choi. 2015. “Standardization Strategy for Modular Industrial Plants.” Journal of Construction Engineering and Management 141 (9): 04015026. doi:https://doi.org/10.1061/(ASCE)CO.1943-7862.0001001.
- Occupational Health and Safety Administration. 2015. Incident (Accident) Investigations: A Guide for Employers. Washington, DC: U.S. Dept. of Labor.
- Oliver, C. 1986. Relationship of Accident Type to Occupant Injuries. University of Michigan, Transportation Research Institute Report UMTRI-86-15.
- Smith, R. 2011. Prefab Architecture: A Guide to Modular Design and Construction. Hoboken, NJ: John Wiley & Sons.