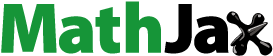
ABSTRACT
This paper reports the corrosion inhibition effect of the realkalization and corrosion inhibitors combination treatment on steel rebars. First, the corrosion was studied in simulated carbonated concrete and simulated realkalized concrete environments and then compared with the corrosion, while realkalization-corrosion inhibitor treatment was applied. The corrosion inhibitors studied are monoethanolamine (MEA), dimethylethanolamine (DEMA) and triethylenetetramine (TETA). Through the electrochemical measurement; the potential of steel rebars in realkalized environment containing MEA and DMEA shifted in positive direction by 84 mV and 66 mV; the current destiny of each group decreased by 3.76 and 2.33 μA/cm2, respectively. Unlike the addition of TETA shifted the potential in negative direction by 281 mV and increased the current density by 27.72 μA/cm2. Comparing steel rebars surfaces, the realkalization-corrosion inhibitors groups showed a better inhibition effect than the two control groups (simulated carbonated concrete and simulated realkalized environments). Among the corrosion inhibitors used, MEA has the best corrosion inhibition effect in the electrochemical realkalized concrete environment, it can form a protective film on the steel rebars through physical and chemical adsorption, which can effectively inhibit the corrosion of steel rebars. The result confirms that, by the combination of MEA and electrochemical realkalization, the corrosion inhibition in carbonated reinforced concrete can improve significantly.
1. Introduction
The corrosion of steel rebars caused by concrete carbonation has always been one of the main problems affecting the durability of reinforced concrete building structures (Réus and Medeiros Citation2020; Zhang et al. Citation2013; Bertolini, Spagnolo, and Redaelli Citation2012; Alaskar, Alqrni, and Alfalah et al. Citation2020; Alabduljabbar et al. Citation2020). Various technologies have been used to alleviate the concrete carbonation, prevent further corrosion of steel rebars and improve the life cycle of the structures. Electrochemical realkalization, concrete coating, corrosion inhibitors, etc., are some of the effective repair technologies. Electrochemical realkalization as a non-destructive concrete carbonation reparation technology reached extensive recognition and application (Yeih and Chang Citation2005; Andrade et al. Citation1999), but according to some scholars, the reparation effect slowly decrease. The marginal effect is 3–4 years, after that the corrosion of steel rebar become active again; the reparation effect on durability is still questionable (Al-Otaibi et al. Citation2014, Tong et al., Citation2011-1671; Mietz Citation2015). Corrosion inhibitors are widely used because they are low cost, easy to operate and have perfect anti-corrosion effect. Corrosion inhibitors are inorganic and organic. In reinforced concrete structures, the inorganics have negative effect and are toxic, but the organics are environmental protector, non-toxic and harmless (Ma, Ammar, and Kumar et al. Citation2022). Nowadays, organic corrosion inhibitors are the most applied in engineering. They are mainly fatty acids, amines, alcohols and esters. They don’t only have good corrosion inhibition performance, but also show efficient migration performance. They can migrate from the concrete surface to the steel rebar without changing the concrete structure and be adsorbed to form passivation film on the steel rebar to prevent corrosion development. To protect efficiently the steel rebar from corrosion, researchers attempted to introduce corrosion inhibitors while using electrochemical realkalization in reinforced concrete. The combination of the two reparation methods such as quickly migration of corrosion inhibitors from the surface to the internal of the reinforced concrete, while the restauration of the concrete internal alkalinity through the electric field action greatly improved the reparation (Junichiro, Tanaka, and Christopher et al. Citation2013).
Elshami (Elshami, Ahmed Bonnet, and Khelidj Citation2020) and Lee (Lee et al. Citation2015) found that, compared with traditional nitrite inhibitors, ethanolamines inhibitors had a more efficient corrosion inhibition effect, even at low concentrations. Rakanta (Rakanta, Zafeiropoulou, and Batis Citation2013), Ryu (Ryu et al. Citation2016) and Raffaini (Raffaini et al. Citation2021) showed that monoethanolamine (MEA), dimethylethanolamine (DMEA) and triethylenetetramine (TETA) have good corrosion inhibition performance and can compete with Cl− in the Chloride environment by forming a protective layer on the steel rebars and inhibit corrosion. In addition to high corrosion inhibition performance, corrosion inhibitors have migration properties, which are suitable for the reparation of carbonated reinforced concrete (Kubo et al. Citation2007) (Liu, Miao, and Zhou et al. Citation2008). However, most research focus on effect of the organic corrosion inhibitors in concrete, acid environment and in chloride ions environment. Few studies have investigated the corrosion inhibition performance of MEA, DMEA and TETA corrosion inhibitors in environment after electrochemical realkalization treatment. In this paper, the three corrosion inhibitors were screened according to migration performance, ionization properties stability; their corrosion inhibition performances were tested and evaluated in simulated concrete pore solution after electrochemical realkalization treatment.
2. Materials and methods
2.1. Sample preparation
2.1.1. Steel rebars
The steel rebars used for this study were HPB235 smooth steel rebars of 10 mm diameter, which were cut into cylindrical specimens (length = 40 mm) by using a steel rebar cutter. The elemental composition of rebar is shown in .
Table 1. Elemental composition of steel rebars.
The surface of each steel rebar was polished with abrasive paper to remove the surface oxide layer and other impurities, then cleaned with absolute alcohol. Once the steel rebar samples had dried in a laboratory environment, a wire was welded to the upper surface of each specimen. Epoxy was used to seal the top and bottom surfaces of the cylindrical steel rebar specimens (but not the side surfaces), as shown in The effective working area of each sample was 12.5 cm2.
2.1.2. Artificial accelerated corrosion
The accelerated corrosion method using an applied anodic current was used to simulate the corrosion of the rebars (Zhang, Zhang, and Xi Citation2012). The applied current density was 100 μA/cm2, which means that the current passing through each steel rebar was 1.25 mA, and the duration of experiment was 72 h (Caré and Raharinaivo Citation2007). After that 3 days, corrosion products formed on the surface of the steel rebars, and according to Faraday’s law, the corrosion rate of the steel rebars following the accelerated corrosion reached 0.39% (Tian et al. Citation2020).
The mass loss was calculated from:
Where M is the molar mass of iron; I(A) is the corrosion current intensity; t(s) is the accelerated corrosion test piece; Z is the number of electrons lost by the reactive electrode and F is the Faraday constant.
The corrosion rate was calculated from:
Where ∆m (g) is the mass loss after three days and m (g) is the initial mass of the steel rebar.
2.1.3. Depolarization of rebars
The steel rebars were in a polarized state after accelerated corrosion; the potentials of the steel rebars were extremely unstable (Otani et al. Citation2017); therefore, the accelerated corrosion steel rebars was conducted in simulated concrete pore solution to depolarize. The potential of the steel rebar gradually increased during the depolarization process, which was completed after 7 days, as shown in .
Table 2. Depolarization of steel rebars.
2.2. Simulated realkalized concrete solutions
Concrete pore solution can be treated using electrochemical realkalization, which generally increases the internal alkalinity of the concrete, but can’t restore its original highly-alkaline state. Therefore, the pH of the saturated Ca(OH)2 solution was adjusted to 10.5 by adding NaHCO3 to simulate the internal environment of concrete under realkalization conditions. Similarly, the pH value was adjusted to 9 to simulate a severely carbonated concrete environment.
2.3. Ethanolamines corrosion inhibitors
Ethanolamines is one type of representative and efficient organic corrosion inhibitors. Considering the stability, solubility, toxicity and ionization properties of various ethanolamines corrosion inhibitors (Singh and Yadav Citation2008), three ethanolamines corrosion inhibitors were selected: monoethanolamine (MEA), dimethylethanolamine (DMEA) and triethylenetetramine (TETA). Their chemical structures are as follow().
Figure 2. Chemical structures of MEA, DMEA, TETA.

The experimental setup involved five sample groups, as shown in . The two control groups that didn’t contain corrosion inhibitors were simulated by the internal conditions of carbonated concrete (pH = 9) and internal condition of concrete after realkalization (pH = 10.5) (Bastidas, Cobo, and Otero Citation2008). The selected ethanolamines were added to the simulated internal environment of concrete under realkalization condition to form three other experimental groups to verify their applicability in concrete environments. Three steel rebars were added to each solution, and the experiments were conducted at ambient laboratory temperature (25°C). The potentials and current densities of each set of steel rebars were measured.
Table 3. Simulation experimental groups.
2.4. Electrochemical measurements
All the steel rebars were put in the solutions. The potential and polarization resistance were measured before immersion and during immersion at 1, 3, 7 and 14 days using the Shanghai Huachen electrochemical workstation and the corrosion current density was calculated (Melara, Mendes, and Andreczevecz Citation2020).
The electrochemical system was composed of three electrodes: the working electrode was the steel rebars, the reference electrode was a saturated calomel electrode (E vs NHE = +242), and the counter electrode was a titanium/platinum-based grid.
2.4.1. Open-circuit potential measurement
Open-circuit potential provides information on the tendency of metals towards reactivity and corrosivity.
The open circuit potential (OCP) test function of the electrochemical workstation was used to determine the potential of each steel rebar specimen. The scanning time was set to 600 s, and the recording interval was set at 0.1 s. The potentials were obtained once the data stabilized.
2.4.2. Current density
The corrosion of steel rebars can be quantified according to their current density (Icorr) values (Faritov, Rozhdestvenskii, and Yamshchikova Citation2016; Rocchini Citation1997). Using the linear sweep voltammetry (LSV) technique, the sweep rate was set at 2.5 mV/min and the range of the free potential ±10 mV, the current versus the voltage was recorded. The polarisation resistance of the steel rebar, Rp(Ω), was determined and the current density Icorr(μA/cm2) of the steel rebars were calculated according to Stern-Geary equation.
Where B is a constant (26 mV; the value when the steel bar is active), and S is the area of the polarized steel rebar (12.5 cm2 in this study).
2.5. Corrosion microscopic analysis
Hitachi TM3000 scanning electron microscope (SEM) was used to visualise the specimens’ surfaces. Large areas of corrosion could be easily observed without the microscope, when the corrosion is inactive, it is difficult to evaluate the degree of rust, for example when only pitting corrosion occurs. The observation condition mode 15 kV was applied. By comparing the development and trend of corrosion between the groups, each corrosion inhibitors effects can be evaluated in this specific environment.
3. Results
3.1. Corrosion potential
The potential of each group of steel rebars before immersion and during immersion at 1, 3, 7 and 14 days is presented in .
Table 4. Corrosion potential of steel rebars.
The potentials of the steel rebars in each group were between –230 and –300 mV before immersion; according to standard ASTMC876 (ASTM C876-09 Standard Test Method for Corrosion Potentials of Uncoated Reinforcing Steel in Concrete Citation0000), the steel rebars had intermediate probability of corrosion and the corrosion was active.
In the control group 1, simulated environment after carbonation, corrosion potential of the steel rebars decreased from −232 mV and reached −260 mV at 14 days. In the realkalization environment (control group 2), the potential slightly increased from −241 mV and reached −215 mV at 14 days.
In the MEA and DMEA groups, the corrosion of the steel rebars was mitigated significantly after 14 days. The presence of MEA and DMEA increased the potential of steel rebar by 84 mV and 66 mV, respectively. However, the corrosion inhibition effect of TETA wasn’t justified. Unexpectedly, the potential highly decreased by 325 mV at 14 days and reached −514 mV.
The three corrosion inhibitors groups showed an increase of potential at early age of immersion (), the electrochemical potential reached the pick at 1 day for MEA and DMEA groups with −298 and −309 mV, respectively, and at 3 days for TETA group with −615 mV. Some reactions may occur because of the corrosion inhibitors.
3.2. Corrosion current density
The current density of each group of steel rebars before immersion and during immersion at 1, 3, 7 and 14 days was measured; the evolution are presented in and .
Figure 4. Corrosion current densities of sample groups simulating reinforced steel under various conditions.
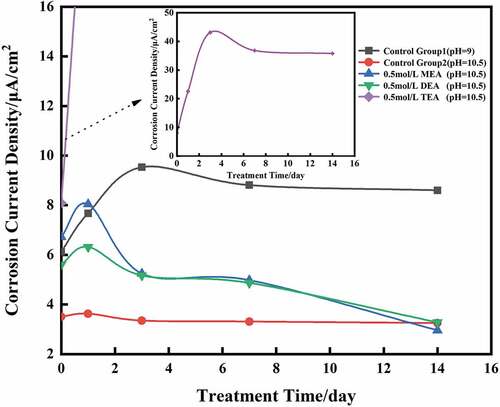
Table 5. Current density of steel rebars.
The current density of control group 1 rise rapidly in few days, stabilize and finally reached 8.60 μA/cm2 at 14 days, but the corrosion current density in control group 2 decreased slightly, by 0.26 μA/cm2.
The change of current density was consistent with potential changes in the three groups containing corrosion inhibitor. The presence of MEA caused the most significant reduction of the current density, which dropped by 3.76 μA/cm2 at 14 days, DMEA also induced a good corrosion inhibition effect, causing the decreased of the steel rebars corrosion current density by 2.33 μA/cm2 at the same age. Unlikely TETA increased significantly the current density, which reaching 35.77 μA/cm2.
Meanwhile, like the potential, the steels rebars current density of MEA, DMEA and TETA groups showed an increase of current density at early age of immersion. The steel rebars current density of MEA and DMEA increased from 6.72 μA/cm2 and 5.61 μA/cm2 to 8.04 μA/cm2 and 6.32 μA/cm2 respectively at 1 days, then decreased gradually. TETA groups showed the same variation, but the pick was reached at 3 days by increasing of 35.02 μA/cm2.
3.3. Surface analysis
Observation by SEM after 14 days immersion showed obvious differences on the surface of each group of steel rebars. Comparing all the groups, the steels rebars of the two control groups (groups without corrosion inhibitors) had a large amount of corrosion products on their surfaces (). The increase of SEM magnification showed densely distribution corrosion products on the control group 1 steel rebars of pH = 9. In the realkalization concrete environment (control group2), the passivation film of the steel rebar was conditionally restored to a certain extent; therefore, the corrosion activity was alleviated and the corrosion products was reduced compare to control group 1 steel rebars.
Figure 5. SEM microscopic analysis of two control groups.
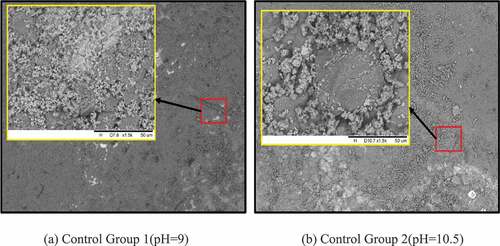
As shown in , the surface of the steel rebars of MEA and DMEA were relatively clean and smooth, only few amounts of corrosion occurred and mainly existed as pitting corrosion. The surface analysis showed that the two inhibitors can effectively exert their anti-corrosion effect in the realkalized concrete environment by reducing the corrosion activity and corrosion rate, protecting and improving the durability of the steel rebars. On TETA group steel rebars, the corrosion products were not much like the two control groups but important compare to the two other corrosion inhibitor groups.
4. Discussion
Potential and current density are two important parameters, which connect the fundamental electrochemical and the practical corrosion behavior of steel rebars. They indicate, respectively, the state of a corroding steel and the instantaneous corrosion rate at the time of measurement. In the carbonated environment, the decrease of the steel rebars potential and increase of current density are due to its environment as well as the low variation of potential and current density in the control group 2 (Tong et al. Citation2012). By examination of the corrosion as a function of pH as shown in , steel rebars in the control group 1 formed Fe 2+, which in presence of oxygen easily form corrosion product Fe(OH)2 and Fe(OH)3 due to the pH = 9 of the environment. Those corrosion products covered almost all the surface on the steels rebars. The potential and current density variations of control group 2 steel rebars are unsignificant. According to Pourbaix gram of Fe-H2O system (), when pH > 10, the rebar might be in passive state (Pourbaix Citation1973); therefore, the immersion in alkaline environment with pH = 10.5 enable a passivation film to protect the rebar from corrosion. The film are composed of various hydroxides such as -FeO(OH),
-FeO(OH),
-FeO(OH), Fe(OH)2, Fe(OH)3 and oxides as FeO, Fe2O3 and Fe3O4(Zhang, Chen, and Luo Citation2019; Fei et al. Citation2014; Matějovsk et al. Citation2019). The passivation film stability depends on the structure nature, the adherence and the thickness. In the Alkaline solution without corrosion inhibitors, the film on steel rebars is very unstable, it can easily be broken and caused corrosion on some area of the steel rebars like observed on SEM image.
The corrosion inhibitors reacted positively in the alkaline environment, on the SEM images only pitting corrosion occurred. The increased of corrosion activity at early age is due to the possible reaction between the corrosion inhibitors and water during passivation process to form hydroxyl which in contact with ion Fe2+ can form corrosion products (Jevremovi and Stankovi Citation2012). For MEA and DMEA groups, the steel rebars corrosion activities decreased after 1 days. It due to the passivation film which can block the released of ion Fe2+ and destroyed the corrosion system of Fe-H2O. At later age (14 days), the increase of potential and the decrease of current density are higher than these of the realkalized simulated environment steel rebars, which proved that the steel rebars passivation film are better corrosion activity reducer when MEA and DMEA are added. Comparing the both, MEA is the best inhibitors, it is due to its chemical structure.
The polar functional groups in MEA, -NH2 and -OH form coordination bonds with Fe2+ on the surface of the steel bar and MEA chain structure forms a chelate similar to the five-membered ring through the two ends -NH2 and -OH. Jiang (Jiang and Zhang Citation1994) pointed out that hydrogen bonds between various chelates can form a complete and dense protective layer. In DMEA chain structure, there is only one polar group -OH, so the chemical connection with Fe2+ on the steel rebar surface can only be completed by -OH, and the non-polar section is far away from the steel rebar to form a hydrophobic layer ().
Figure 8. MEA and DMEA protection of steel bar.
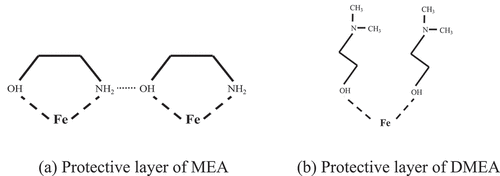
The pitting corrosion on TETA group steel rebars were important compare to the two other corrosion inhibitor group but less than the control group 2 steel rebars. TETA inhibit corrosion even though the effect is not better as MEA and DMEA. According to the chemical structure of TETA, it can chelate with iron through multiple -NH2, and the SEM figure also proved that it reduces the corrosion activity of rebar, no large amount of rust products are found, indicating that TETA eventually form a protective layer on the surface of the steel rebar to inhibit corrosion (Kumar Citation2013). Unexpectedly, the decrease of potential to more negative value and the higher current density of the steel rebars are due to the continuous TETA absorption on the steel rebars during the passive film formation. The analysis of solution chemical components is recommended to clarify the results.
5. Conclusions
From above results, the following conclusions can be drawn:
(1) In carbonated concrete environment, the steel rebars corrosion is rapid. the limited alkalinity of the simulated environment doesn’t allow the formation of the passive film which should protect the steel from corrosion.
(2) The realkalization treatment increase the alkaline and improve the steel rebars corrosion resistance to a certain extent by forming the passivation film. But the film is unstable and provide weak protection.
(3) Addition of monoethanolamine (MEA), dimethylethanolamine (DMEA) and triethylenetetramine (TETA) in realkalization treated environment highly improved the corrosion inhibitions. Their absorption on the steel rebars form a strong passivation film and provide efficient protection. Among the three corrosion inhibitors, MEA has the best inhibition effect follow by DMEA.
In this study, MEA has been proved to have the most efficient corrosion inhibition ability in the realkalization environment. Non-toxic, economic and due to its good migration performance, MEA can combine with non-destructive electrochemical realkalization treatment, to give good, easy and efficient reparation of corroded steel rebars in reinforced concrete. Because of the limit method to study the passive film structure on the steel rebars, the analysis of the simulated pore solution components should give better understanding of the different potential and current density variation. Further studies should focus on the chemical analysis of the pore solution.
Disclosure statement
No potential conflict of interest was reported by the author(s).
Data Availability Statement
Data is contained within the article.
Additional information
Funding
References
- Al-Otaibi, M. S., A. M. Al-Mayouf, M. Khan, A. A. Mousa, S. A. Al-Mazroa, and H. Z. Alkhathlan. 2014. “Corrosion Inhibitory Action of Some Plant Extracts on the Corrosion of Mild Steel in Acidic Media.” Arabian Journal of Chemistry 7 (3): 340–346. doi:10.1016/j.arabjc.2012.01.015.
- Alabduljabbar, H., R. Alyousef, H. Mohammadhosseini, and T. Topper . 2020. “Bond Behavior of Cleaned Corroded Lap Spliced Beams Repaired with Carbon Fiber Reinforced Polymer Sheets and Partial Depth Repairs.” Crystals 10 (11): 1014. DOI:10.3390/cryst10111014.
- Alaskar, A., A. Alqrni, G. Alfalah, El-Sayed, A., Mohammadhosseini, H., and Alyousef, R. . 2020. “Performance Evaluation of Reinforced Concrete Beams with Corroded Web Reinforcement: Experimental and Theoretical Study.” Journal of Building Engineering 35: 102038.
- Andrade, C., M. Castellote, J. Sarría, and C. Alonso. 1999. “Evolution of Pore Solution Chemistry, Electro-osmosis and Rebar Corrosion Rate Induced by Realkalisation.” Materials and Structures 32 (6): 427–436. doi:10.1007/BF02482714.
- ASTM C876-09 Standard Test Method for Corrosion Potentials of Uncoated Reinforcing Steel in Concrete, “ASTM C876-09 Standard Test Method for Corrosion Potentials of Uncoated Reinforcing Steel in Concrete.”
- Bastidas, D. M., A. Cobo, and E. Otero. 2008. “Electrochemical Rehabilitation Methods for Reinforced Concrete Structures: Advantages and Pitfalls.” British Corrosion Journal 43: 248–255.
- Bertolini, L., L. S. Spagnolo, and E. Redaelli. 2012. “Electrochemical Realkalization as a Conservation Technique for Reinforced Concrete.” International Journal of Architectural Heritage 6 (2): 214–227. doi:10.1080/15583058.2010.528147.
- Caré, S., and A. Raharinaivo. 2007. “Influence of Impressed Current on the Initiation of Damage in Reinforced Mortar Due to Corrosion of Embedded Steel.” Cement and Concrete Research 37 (12): 1598–1612. doi:10.1016/j.cemconres.2007.08.022.
- Elshami, A., S. Ahmed Bonnet, and A. Khelidj. 2020. “Effectiveness of Corrosion Inhibitors in Simulated Concrete Pore Solution.” European Journal of Environmental and Civil Engineering 24 (13): 2130–2150.
- Faritov, A. T., Y. G. Rozhdestvenskii, and S. A. Yamshchikova. 2016. “Improvement of the linear polarization resistance method for testing steel corrosion inhibitors.“ In Russ. Metall 2016: 1035–1041.
- Fei, F., J. Hu, J. Wei, Q. Yu, and Z. Chen . 2014. “Corrosion Performance of Steel Reinforcement in Simulated Concrete Pore Solutions in the Presence of Imidazoline Quaternary Ammonium Salt Corrosion Inhibitor”. Construction and Building Materials 70: 43–53. DOI: 10.1016/j.conbuildmat.2014.07.082.
- Jevremovi, I., and V. Stankovi. 2012. “The Inhibitive Effect of Ethanolamine on Corrosion Behavior of Aluminium in NaCl Solution Saturated with CO2.” Metallurgical and Materials Engineering 18: 4.
- Jiang, F., and P. Zhang. 1994. “Corrosion Inhibition Properties and Molecular Structure of Alcohol-amines.” Corrosion and Protection 15 (5): 232–234.
- Junichiro, K., Y. Tanaka, L. Christopher, and Mary, M. 2013. “Application of Electrochemical Organic Corrosion Inhibitor Injection to a Carbonated Reinforced Concrete Railway Viaduct.” In Construction and Building Materials 39: 2–8.
- Kubo, J., S. Sawada, C. Page, and M. Page. 2007. “Electrochemical Injection of Organic Corrosion Inhibitors into Carbonated Cementitious Materials: Part 2.” Mathematical Modelling. Corrosion Science 49 (3): 1205–1227. DOI:10.1016/j.corsci.2006.06.015.
- Kumar, S. 2013. “Substituted Amines as Corrosion Inhibitors for N80 Steel in 15%HCL.” Journal of Materials and Environmental Science 4 (5): 691.
- Lee, H., H. Ryu, W. Park, and M. Ismail . 2015. “Comparative Study on Corrosion Protection of Reinforcing Steel by Using Amino Alcohol and Lithium Nitrite Inhibitors.” Materials 83390 (1): 251–269. DOI:10.3390/ma8010251.
- Liu, Z., C. Miao, W. Zhou, and Liu, J. 2008. “Maintenance and Improvement of Durability of Reinforced Concrete Using Migrating Corrosion Inhibitors.” Journal of the Chinese Ceramic Society 36 (10): 1494–1500.
- Ma, I., S. Ammar, S. Kumar, Ramesh, K., and Ramesh, S. 2022. “A Concise Review on Corrosion Inhibitors: Types, Mechanisms and Electrochemical Evaluation Studies.” Journal of Coatings Technology and Research and Electrochemical Evaluation Studies 19: 241–268.
- Matějovsk, L., J. Macák, O. Pleyer, P. Straka, and M. Staš. 2019. “Efficiency of Steel Corrosion Inhibitors in an Environment of Ethanol–gasoline Blends.” ACS Omega 4 (5): 8650–8660. doi:10.1021/acsomega.8b03686.
- Melara, K. E., Z. A. Mendes, C. N. Andreczevecz, Bragança, O.M., and Medeiros-Junior, A.R. 2020. In Construction and Building Materials 242: 118001.
- Mietz, D. 2015. “Electrochemical Realkalisation for Rehabilitation of Reinforced Concrete Structures.” Materials and Corrosion/Werkstoffe und Korrosion 46 (9): 527–533. doi:10.1002/maco.19950460904.
- Otani, S., M. A. Caronge, D. Yamamoto, and H. Hamada. 2017. “Fundamental Study on Depolarization Value and Protection Effects of Steel in Concrete under Cathodic Protection.” Concrete Research and Technology 28 25–33. doi:10.3151/crt.28.25.
- Pourbaix, M. 1973. “Lecture on Electrochemical Corrosion.” In NewYork: Pleum Press, 29–183.
- Raffaini, G., M. Catauro, F. Ganazzoli, F. Bolzoni, and M. Ormellese . 2021. “Organic Inhibitors to Prevent Chloride Induced Corrosion in Concrete: Atomistic Simulations of Triethylenetetramine Based Inhibitor Film.” Macromolecular Symposia 395 (1): 2000231. DOI:10.1002/masy.202000231.
- Rakanta, E., T. Zafeiropoulou, and G. Batis. 2013. “Corrosion Protection of Steel with DMEA-based Organic Inhibitor.” Construction and Building Materials 44: 507–513. doi:10.1016/j.conbuildmat.2013.03.030.
- Réus, G. C., and H. F. Medeiros. 2020. “Chemical Realkalization for Carbonated Concrete Treatment: Alkaline Solutions and Application Methods.” Construction and Building Materials 262: 120880. doi:10.1016/j.conbuildmat.2020.120880.
- Rocchini, G. 1997. “Experimental Verification of the Validity of the Linear Polarization Method.” Corrosion Science 39 (5): 877–891. doi:10.1016/S0010-938X(97)81155-9.
- Ryu, H.-S., K. J. Singh, H.-M. Yang, H.-S. Lee, and M. A. Ismail 2016. “Evaluation of Corrosion Resistance Properties of N, N′-Dimethyl Ethanolamine Corrosion Inhibitor in Saturated Ca(OH)2 Solution with Different Concentrations of Chloride Ions by Electrochemical Experiments - ScienceDirect.” Construction and Building Materials 114 (114): 223–231. DOI:10.1016/j.conbuildmat.2016.03.174.
- Singh, D., and S. Yadav. 2008. “Role of Tannic Acid Based Rust Converter on Formation of Passive Film on Zinc Rich Coating Exposed in Simulated Concrete Pore Solution.” Surface & Coatings Technology 202 (8): 1526–1542. doi:10.1016/j.surfcoat.2007.07.013.
- Tian, Y., J. Liu, H. Xiao, Y. Zhang, Q. Mo, J. Shen, and J. Shi. 2020. “Experimental Study on Bond Performance and Damage Detection of Corroded Reinforced Concrete Specimens.” Advances in Civil Engineering 2020: 1–15. doi:10.1155/2020/7658623.
- Tong, Y., V. Bouteiller, and E. Marie. 2011. “Durability Investigation of Realkalization Treatment Using Impressed Current.” Journal of Zhejiang University 2011 (45): 1664–1670.
- Tong, Y., V. Bouteiller, E. Marie, and S. Joiret . 2012. “Efficiency Investigations of Electrochemical Realkalisation Treatment Applied to Carbonated Reinforced Concrete - Part 1 Sacrificial Anode Process.” Cement and Concrete Research 42 (1): 84–94. DOI:10.1016/j.cemconres.2011.08.008.
- Yeih, W., and J. Chang. 2005. “A Study on the Efficiency of Electrochemical Realkalisation of Carbonated Concrete.” Construction and Building Materials 19 (7): 516–524. doi:10.1016/j.conbuildmat.2005.01.006.
- Zhang, W., J. Chen, and X. Luo. 2019. “Effects of Impressed Current Density on Corrosion Induced Cracking of Concrete Cover.” Construction and Building Materials 204 (20): 213–223. doi:10.1016/j.conbuildmat.2019.01.230.
- Zhang, J., J. Jiang, L. Yan, J.-L. Lu, S.-J. Qian, K. Wang, and W.-J. Qu. 2013. “Electrochemical Realkalisation and Combined Corrosion Inhibition of Deeply Carbonated Historic Reinforced Concrete.” Corrosion Engineering Science and Technology 48 (1): 28–35. doi:10.1179/1743278212Y.0000000039.
- Zhang, W., R. Zhang, and L. Xi. 2012. “Corrosion of Reinforced Concrete in Accelerated Tests.” Advanced Materials Research 610-613: 485–489. 1 0.4028/w–ww.scientific.net/A–MR.610-613.485.