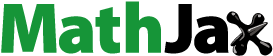
ABSTRACT
This study investigates the effect of super absorbent polymers (SAPs) and glass fiber (GF) additions on the properties of lightweight concrete. The SAPs act as a pore-forming agent, with the addition of various GF contents (0.1–1.0% by weight of dry ingredients). The results indicate that the use of SAPs at 7% by weight of OPC produces a product with similar properties to conventional lightweight concretes which meet the ASTM C332–17 standard. The addition of GF to the mixture tends to reduce the dry density and compressive strength, but increases the porosity and flexural strength. The results indicate that the use of SAPs at 7% by weight of OPC produces a product with similar properties to conventional lightweight concretes which meet the ASTM C332–17 standard. The 28-day compressive strengths decreased from 7.04 ± 0.07 for control sample to 4.59 ± 0.11 MPa, while the flexural strengths increased from 3.89 ± 0.04 for control sample to 6.72 ± 0.06 MPa. High-porosity lightweight concrete prepared from SAPs and GF shows reduced thermal conductivity and an increased sorption rate. The initial rate of water absorption gradually increases from 2.48 × 10−1 mm/sec0.5 in the sample without GF up to 5.45 × 10−1 mm/sec0.5 in the sample containing 1.0 wt.% GF. Comparison with the literature indicates that the use of SAPs as pore-forming agents in conjunction with GF has the potential to produce fiber-reinforced lightweight concrete with improved properties.
HIGHLIGHTS
High SAP content (7 wt. % of OPC) acts as a pore-forming agent.
SAPs show potential for the production of lightweight concrete.
The addition of GF directly influences the physical and mechanical properties.
The high porosity of mixtures containing SAPs and GF increases the sorptivity.
1. Introduction
Super absorbent polymers (SAPs), classified as hydrogels, are water-insoluble three-dimensional crosslinked polymer network structures that have the ability to absorb and retain large amounts of liquids within their structures, even under pressure (Tally and Atassi Citation2015). These properties of SAPs make them useful in a number of applications, including agriculture (Beiranvandi et al. Citation2022; Fernando et al. Citation2017; Ji et al. Citation2022), wastewater treatment (Thakur, Pandey, and Arotiba Citation2016; Wang, Wang, and Wang Citation2013), tissue engineering (Wang et al. Citation2010), and drug delivery systems (Merino et al. Citation2015). Recently, SAPs have also been used in cement and concrete for various applications, especially for internal curing (Farzanian et al. Citation2016; Senff et al. Citation2015; Yao, Zhu, and Yang Citation2012) and crack healing (Hu et al. Citation2019; Park and Choi Citation2018; Wang et al. Citation2014). The utilization of SAPs in cementitious materials can affect their fresh and hardened properties. Nodehi and Nodehi (Citation2021) concluded that the addition of SAPs can increase the workability of ultra-high performance concrete (UHPC). Previous reports also show that SAPs can improve the flowability of fresh concrete and reduce the total shrinkage of hardened concrete due to enhanced internal curing by the SAPs (AzariJafari et al. Citation2016). Similarly, Liu et al. (Citation2021) proposed that the high shrinkage (450 με) of a reference mixture of UHPC could be reduced by the incorporation of SAPs. An addition of 0.7% SAPs by mass of binder decreased the shrinkage by approximately 72%, compared with the reference mixture. The high water storage capacity of SAPs can be exploited to supply water to the surrounding cement matrix to assist the formation of hydration products, providing denser structures and enhancing the compressive strength of cementitious materials. Justs et al. (Citation2015) reported that the introduction of SAPs (0.3% by mass of cement) into cement mixtures produced a 28-day compressive strength of almost 150 MPa. Liu, Farzadnia, and Shi (Citation2021) also noted that the density of calcium silicate hydrate (C-S-H) can be transformed from low-density to high-density or ultra-high-density with the addition of 0.6% SAPs.
A limiting factor in the use of SAPs in cementitious materials is a decrease in the mechanical properties by as much as 30%–40% when the amount of SAPs is increased (depending on the mix proportions) (Beushausen, Gillmer, and Alexander Citation2014; Pourjavadi et al. Citation2013). Jensen and Hansen (Citation2002) reported that the compressive strength of concrete (without SAPs) was reduced from 134 MPa to 109 MPa (calculated as −18%) after the addition of 0.6% SAPs. This result is consistent with another study in which the incorporation of 1.5% SAPs by mass of binder resulted in a reduction of the compressive strength of self-consolidated lightweight concrete by 13%–27% by comparison with corresponding reference mixtures (AzariJafari et al. Citation2016). This result was ascribed to the creation of air voids upon drying of the SAPs; however, this limitation can be exploited to form porous materials. Rutkevičius et al. (Citation2012) noted that lightweight porous materials produced from hydrogels showed a good potential for building industry products such as heat and sound insulation panels and as alternatives to conventional materials, including aerated concrete, lightweight building blocks, porous rubber substitutes, and foam shock absorbers. Thompson et al. (Citation2018) also suggested that the use of hydrogel-based lightweight materials can reduce the thermal conductivity and improve the economic use of the matrix material. AzariJafari et al. (Citation2016) introduced SAPs into self-consolidating lightweight concrete, thereby improving its static stability and reducing its total shrinkage by up to 50%. Although these studies have utilized SAPs or hydrogels for the production of lightweight materials, there remains a need for further comprehensive development of their application as lightweight materials for the building industry, especially in terms of reinforced-lightweight materials or concrete.
As is the case with all concrete, lightweight concrete shows a lower tensile and flexural strength than compressive strength. Various natural and synthetic fibers, including hemp fibers (Gencel et al. Citation2021), wood fibers (He et al. Citation2019; Xu et al. Citation2019), cellulose (Bencardino et al. Citation2019; Zhang et al. Citation2022), basalt fibers (Gencel et al. Citation2022; Jiang et al. Citation2022; Kim, Kim, and Song Citation2020), steel fibers (Centonze, Leone, and Aiello Citation2012; Samarakoon et al. Citation2019) and glass fibers (Cong et al. Citation2022; Pehlivanlı et al. Citation2016), have been used to reinforce and enhance both the tensile and flexural strengths of lightweight concrete. Gencel et al. (Citation2022) reinforced foamed concrete containing silica fume with basalt fibers. This study showed that the flexural strength of the concrete could be increased by 88% when the basalt fiber content was increased from 0 to 3% by mass of cement. Another study by Gencel et al. (Citation2021) reported that the incorporation of 3% hemp fiber in foamed concrete containing fly ash could be attributed to the enhancement of the flexural strength by approximately 240.54%, 354.05%, and 395.94% after aging for 7, 28, and 91 days, respectively, by comparison with the reference samples. In a study of autoclaved aerated concrete (AAC), Xu et al. (Citation2019) incorporated wood fiber waste to reinforce the AAC. These workers found that increasing the wood fiber waste content from 0.1% to 0.4% by the total weight of the dry mix increased the flexural strength from 9% to 43%. An investigation by Cunha, Sampaio, and Martinelli (Citation2021) compared various types of fibers on the properties of lightweight concrete, and found that enhancement of the flexural strength by the fibers depended on their elastic modulus and tensile strength, in addition to the fiber content and the distribution of the fibers in the mixture.
Of these fibers, the use of glass fibers (GF) to reinforce cementitious materials has attracted attention for many years, due to their low specific gravity, low water absorption, high elasticity modulus, and high tensile strength (Chen et al. Citation2021; Fenu, Forni, and Cadoni Citation2016). Mirza and Soroushian (Citation2002) used glass fibers to reinforce lightweight concrete and showed these to be highly effective in controlling the restrained shrinkage cracking of the lightweight concrete. The addition of these fibers also improved the flexural strength and ductility of the concrete. In that study, the use of 1% mass glass fiber content (0.25% volume fraction) was found to be effective in enhancing the material properties of lightweight concrete mixtures. Similarly, Chen et al. (Citation2021) concluded that the incorporation of glass fibers in a mortar mixture produced an extreme enhancement of the mechanical properties of mortars, especially the flexural strength. They also reported that the 40% autogenous shrinkage and 50% drying shrinkage in their samples were eliminated when 5% glass fiber was incorporated in the mortars. In a study of the thermal properties of concretes, Małek et al. (Citation2021) reported that concrete containing glass fiber exhibited relatively low thermal conductivity values compared with concrete containing polypropylene fibers and steel fibers. The lowest thermal conductivity was found to occur with a 1% addition of glass fiber (by mass of cement); this conductivity was lower than a reference sample by approximately 12%. (Nagy, Nehme, and Szagri Citation2015) also reported that a 0.3% addition of glass fiber to a concrete mixture could result in a 5.6% decrease in the thermal conductivity of the material from 2.83 to 2.67 W/m-K. In addition, recent research has shown the potential of GF-reinforced concrete for reducing the seismic impact associated with earthquake disasters (Dai et al. Citation2023). This could be applied as another method for reducing the impact of earthquakes on the structure of buildings, as tuned mass dampers (TMDs) (Wang, Shi, and Zhou Citation2022; Wang, Zhou, and Shi Citation2023; Wang et al. Citation2020, Citation2022). These properties suggest that they could be an excellent material for reinforcement lightweight concrete.
However, less is known about the behavior of lightweight concrete containing both SAPs and GF fibers. Thus, the aim of the present study is to investigate the combined effect of SAPs and GF on the properties of lightweight concrete. The content of SAPs used in this study (7% by weight of OPC) acts as the pore-forming agent in the lightweight concrete, and GF additions of 0.1%–1.0% by weight of the dry ingredients were used. The physical and mechanical properties, sorptivity, thermal conductivity, and microstructure of the resulting samples were determined.
2. Methodology
2.1. Materials
The materials used in this study were ordinary Portland cement (OPC) (SG = 3.13, chemical composition ), river sand (particle size of 150–300 μm, specific gravity 2.73), super absorbent polymer (SAP, polyacrylamide type, swelling capacity of 354 g/g), and Alkali Resistant (AR) glass fiber (GF, 14–16 μm dia., 12 mm length, density 2.60 g/cm3).
Table 1. Chemical composition of the OPC used in this study.
2.2. Experimental methods
2.2.1. Specimen preparation
shows the composition of the mixes used in this study. The OPC-to-sand ratio was 1:1, and the water-to-OPC ratio was 1.18. In preliminary experiments, SAPs contents of 1–9 wt % were used, as illustrated in . The water-to-OPC in this preliminary experiment was determined by a flow table method in order to maintain a similar workability as the mixture without SAPs. The compressive strength and density could be reduced with increasing SAPs contents due to porous structure obtained from SAPs particles after drying. These experiments indicated that the optimum SAPs content to meet the ASTM C332–17 standard (American Society for Testing Materials Citation2017) was 7 wt.%. Thus, further experiments were carried out with a fixed SAPs content of 7% by weight of OPC, with GF added at levels of 0.1%, 0.2%, 0.3%, 0.4%, 0.5%, and 1.0% by weight of the dry ingredients (OPC + sand). The OPC, sand, and GF were mixed in a Hobart mixer for 1 min before the addition of the SAPs and water, followed by further mixing for 1.5 min. The resulting slurries were poured into 50 × 50 × 50 mm3 molds for measurement of compressive strength, dry density, porosity, and sorptivity, while the size of the specimens for flexural strength testing was 40 × 40 × 160 mm3 and the specimen size for the thermal conductivity determinations was 50 × 300 × 300 mm3. After hardening for 24 h, the samples were demolded and wrapped in plastic until testing.
Table 2. Mix proportions per m3 for the samples in this study.
2.2.2. Test methods
The compressive and flexural strengths of the samples were determined according to ASTM C109 (American Society for Testing Materials Citation2020a) and ASTM C348 (American Society for Testing Materials Citation2020c), respectively, after 7, 14, and 28 days. Six sample compressive strengths are reported as the average of six samples, determined on six replicates using a compressive strength testing machine. The compressive strengths were calculated using EquationEq. 1(1)
(1) .
where σc is the compressive strength, F is the maximum load, and A is the cross-section area of the cube.
For the flexural strength determinations, a set of three samples was used. The flexural strengths were determined by the three-point-loading method (Wang, Wang, and Shi Citation2021; Wang et al. Citation2021, Citation2023), as given in and calculated by EquationEq. 2(2)
(2) .
where Rf is the flexural strength (MPa), Ff is the applied load to the destruction of the specimen (N), L is the distance between the two supporting points (mm), b is the edge length of a prismatic section perpendicular to the applied longitudinal force (mm) and h is the length of an edge parallel to the longitudinal force applied at the interface of the prism (mm).
The deflection of the 28-day flexural strength specimens was also determined.
The broken pieces of the 28-day compressive strength samples were soaked in acetone to stop further hydration reactions and gold-coated for scanning electron microscopy (SEM, Merlin compact, Zeiss).
The remaining tests were also carried out on samples cured for 28 days. The dry density and porosity were determined on a set of six samples according to ASTM C20 (American Society for Testing Materials Citation2022). The duplicate samples were used for thermal conductivity testing, determined according to ASTM C518 (American Society for Testing Materials Citation2021). The rate of water absorption by the samples (sorptivity) was determined by an adaption of ASTM method C1585 (American Society for Testing Materials Citation2020b) (). In this modified test method, the set of three specimens of each mix composition was dried at 55°C to constant weight, sealed to provide unidirectional capillary suction, then placed in a container with 2 ± 1 mm of their lower surface in contact with water. The sorptivity (I) was determined from the increase in sample weight after 1, 5, 10, 20, 30, 60, 120, 240, and 1440 min, calculated by EquationEq. 3(3)
(3) and plotted as a function of time0.5 (sec).
Where I is the water absorption (mm), mt is the change in the specimen mass (g), a is the area of the specimen (mm2), and d is the density of water (g/mm3)
3. Results
3.1. Mechanical properties
The compressive and flexural strengths of the lightweight concrete samples are shown in , respectively. The compressive strength of sample LCF0 containing 7 wt.% SAPs gained compressive strengths of 5.53 ± 0.04, 6.38 ± 0.12, and 7.04 ± 0.07 MPa after 7, 14, and 28 days, respectively, with a 28-day dry density of 1181 ± 1.7 kg/m3. The compressive strength of lightweight concrete is related to factors such as its void content, density, composition of the materials, and the forming method. A previous study of foamed concrete with a dry density of 1200 kg/m3 (Newman and Owens Citation2003) reported a 28-day compressive strength of 4.5–5.5 MPa, by comparison with ̴7.5 MPa for autoclaved aerated concrete (AAC) with a dry density of 750 kg/m3 (Newman and Owens Citation2003). Thus, the literature suggests that the present lightweight concretes prepared from SAPs have similar properties to foamed concrete and AAC.
Figure 5. Flexural strength of lightweight concrete prepared using SAPs and GF. (a) flexural strength, (b) deflection in 28-day samples.
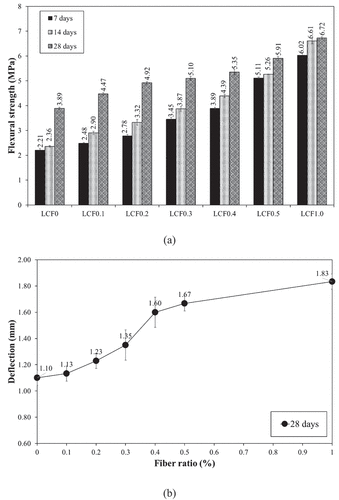
The addition of GF to the present lightweight concretes prepared using SAPs gradually decreased the compressive strength at all curing times; the incorporation of 0.1–1% GF by weight of dry ingredients resulted in a decrease in the compressive strength of the 28-day samples by 4–35% compared to the LCF0 control sample. This was due to the limited degree of compaction resulting from the addition of the fibers and may also reflect the non-uniform dispersion of the comparatively high fiber volumes (Cunha, Sampaio, and Martinelli Citation2021; Liu et al. Citation2019). This finding is in line with the study of Cunha, Sampaio, and Martinelli (Citation2021), who reported a decrease in the compressive strength of approximately 13% upon the addition of glass fibers into their material. In the present study, the development of compressive strengths from 7 days to 28 days were calculated to be 26–44% for all mix proportions. In the previous study, the internal curing behavior of the SAPs enhanced the compressive strength by 22–24% when the curing time was increased from 7 to 28 days by contrast with the increase in compressive strength of about 18–20% in the samples without SAPs (Justs et al. Citation2015). This may be the reason for the positive effect of SAPs as pore-forming agents in lightweight concrete production. The Thai Industrial Standard (TIS) no. 2601–2556: “cellular lightweight concrete blocks using preformed foam” specifies that materials with a density of 901–1200 kg/m3 should show compressive strength values greater than 2.5 MPa (Thai Industrial Standards Institute Citation2013). Comparison of this standard with the results obtained in this study shows that sample LCF1.0 meets this standard. This suggests that the LCF1.0 mixture would be suitable for fiber-reinforced lightweight concrete production. However, the workability of this fiber-reinforced lightweight concrete in its fresh state would need to be determined and taken into account.
shows the flexural strengths of the samples cured for 7, 14 and 28 days. As expected, increasing the content of GF increased the flexural strength at all curing times. A comparison with the 28-day LCF0 sample showed an increase in the flexural strengths of approximately 14%, 26%, 31%, 37%, 51%, and 72% in samples LCF0.1, LCF0.2, LCF0.3, LCF0.4, LCF0.5 and LCF1.0, respectively. This result is similar to one previously reported (Cunha, Sampaio, and Martinelli Citation2021), that the average flexural strength of a lightweight concrete containing 0.2–0.6% GF by volume of concrete was enhanced by 28% compared to a reference sample. The addition of GF to a lightweight concrete can inhibit fracture development under a high test load (Barluenga and Hernández-Olivares Citation2007; Chen et al. Citation2021), as can be seen in . Here, the deflection is increased by 3–66% with increasing GF content, compared to the control sample LCF0. The effect of the GF on the rupture plane of specimens results in an increase in the ratio of flexural to compressive strength from 0.44 in sample LCF0 to 1.08 in sample LCF1.0. This suggests that the LCF1.0 mixture could be used for the production of fiber-reinforced lightweight concrete. However, the workability of fresh fiber-reinforced lightweight concrete should be determined and taken into account in any practical application.
3.2. Dry density and porosity
The dry density of lightweight concrete is generally related to the void content, mix proportions, and raw materials. The SAPs pore-forming agent used in this study (7% by weight of OPC) produced a lightweight concrete with a dry density of 1181 ± 1.7 kg/m3 and a porosity of 31% (). The high porosity of LCF0 is probably due to the presence of pores produced by the SAPs particles after drying (AzariJafari et al. Citation2016). Mechtcherine, Dudziak, and Hempel (Citation2009) reported that the total porosity of concrete could be reduced by 2% of total volume when 0.6% SAPs (by mass of cement) was added, compared to a mixture containing 0.3% SAPs. A similar result was reported by Ouattara Coumoin et al. (Citation2019) who showed that the addition of 0.3% SAPs (by mass of cement) to high-performance concrete could increase the porosity over that of the high-performance concrete without SAPs.
The addition of GF to the mixtures decreased their dry density and increased their porosity. This result is consistent with previous reports that the porosity of concrete mixtures is influenced by the addition of fibers (Liu et al. Citation2019). Cunha, Sampaio, and Martinelli (Citation2021) reported that the density behavior of their samples was related to high void contents resulting from the introduction of lightweight fibers. In that study, the densities of mixtures containing fibers were 7–12% less than reference samples without fibers. A similar study by Gencel et al. (Citation2021) reported that the density was decreased with increasing amounts of pore-forming agent and fibers. In the case of glass fibers, it was reported (Małek et al. Citation2021) that a 7.2% increase in the porosity of concrete could be obtained by the addition of 1% glass fiber (by mass of cement), compared to the corresponding reference sample (Małek et al. Citation2021). This result is similar to that of another study (Söylev and Özturan Citation2014) which reported a 5.0% increase in the porosity of concrete modified by the incorporation of 0.1% glass fiber (by volume of concrete). In the present study, the dry densities and porosities of mixtures containing GF (samples LCF0.1–LCF1.0) were in the range 968–1145 kg/m3 and 32–44%, respectively.
3.3. Thermal conductivity
shows that the thermal conductivity of the 28-day lightweight concrete samples containing SAPs and GF decreases with increasing GF content. The thermal conductivity of lightweight concrete depends on factors such as the density, porosity, pore size distribution, moisture content, and thermal conductivity of the added materials (Pehlivanlı et al. Citation2016; Xu et al. Citation2019). The relatively high porosity of the mixtures containing GF () is the cause of the decrease in thermal conductivity from 0.4 W/m-K for LCF0 to 0.285 W/m-K for LCF1.0. Similarly, Gencel et al. (Citation2022) reported a 2% reduction in the thermal conductivity of foam concrete containing 3% basalt fiber. These authors also pointed to a direct relationship between the density and the thermal conductivity of their samples. In addition, the thermal conductivity of the added fibers can also affect the thermal conductivity values of lightweight concrete. A study by Pehlivanlı et al. (Citation2016) showed that the high thermal conductivity value of carbon fiber (1.74–1.80 W/m-K) resulted in the highest thermal conductivity value of their materials into which they had incorporated a number of different fibers, whereas the lowest thermal conductivity value of the materials in this study came from the incorporation of basalt fibers (thermal conductivity 0.031–0.038 W/m-K). The thermal conductivity value of glass fiber used in this study was 0.034–0.40 W/m-K, which was found to reduce the thermal conductivity value of this lightweight concrete. A previous report (Małek et al. Citation2021) showed that the thermal conductivity of concrete containing glass fiber decreased with increasing glass fiber content (from 0.5% to 1.0% by mass of cement) by about 9–12% compared with the reference sample. This finding is also consistent with the results of this study. Furthermore, the values of dry density and thermal conductivity of the present samples fall within the limits quoted in ASTM C 332 (American Society for Testing Materials Citation2017; maximum dry density 1440 kg/m3 and maximum thermal conductivity 0.43 W/m-K). Thus, the present lightweight concretes prepared from SAPs and GF conform to the ASTM specifications for insulating concrete.
3.4. Sorptivity
Sorptivity is the ability of a material to transport water by capillarity action and is very strongly related to the porosity of the material (Gencel et al. Citation2022). Since SAPs are extremely susceptible to contact with water, and this property, in addition to the high porosity of sample (LCF0), produces a high degree of water absorption (I > 2 mm within the first 60 sec (8 sec0.5) and I = 11.9 mm within 1 h (60 sec0.5), as given in . A similar result was reported by Gencel et al. (Citation2022) who showed that mixtures containing 100 kg/m3 foam content produced a sorptivity three times higher than a mixture containing foam content of 50 kg/m3; they attributed this to a lower solid matrix content and higher capillary porosity. A study by AzariJafari et al. (Citation2016) reported that a self-consolidated lightweight concrete containing SAPs can absorb ~18% of water by mass of concrete within 30 min, but only ~1% in self-consolidated lightweight concrete without SAPs. This observation is consistent with our present study.
shows that the initial slope of water absorption increases with increasing GF ratios. The highest initial slope, shown by sample LCF1.0, then changes only slightly and becomes stable within 20 min (35 sec0.5). The slopes of the curves at this point were used to determine the initial rate of water absorption (). The initial rate of water absorption gradually increased from 2.48 × 10−1 mm/sec0.5 for sample LCF0 to 5.45 × 10−1 mm/sec0.5 for sample LCF1.0. Previous researchers have reported that relatively high sorptivity values indicated either a larger volume of capillary pores or a more connected network (Alnahhal et al. Citation2022; Panesar Citation2013). This finding is consistent with the dry densities and porosities of the present samples.
Table 3. Initial rate of water absorption at t = 35 sec0.5 of lightweight concrete prepared using SAPs and GF.
3.5. Scanning electron microscopy
shows the SEM micrographs of lightweight concrete prepared using SAPs and GF after 28 days. In sample LCF0 at 1000X magnification, the hydration product calcium silicate hydrate (C-S-H) occurs in a needle-like crystalline form on the surface of the sample (). The addition of GF to the mixture has no effect on the crystalline C-S-H hydration product (). To investigate the behavior of the GF and mortar matrix, a 30X magnification was used (). This figure shows that in the sample containing both the SAPs matrix and GF, there is good adhesion between the GF. This feature is beneficial for the enhancement of the flexural strength of concrete containing SAPs and GF.
3.6. Comparison of performance obtained from lightweight concrete prepared using SAPs and GF with literatures
shows the comparison of results obtained in this study with the literature for samples cured for 28 days (excluding autoclaved aerated concrete, AAC). The literature shows similar trends in the relationship between density and compressive strength. Samples with relatively low density have reduced compressive strengths due to the porous structure of lightweight concrete. In the case of fiber-reinforced lightweight concrete, all the literature, including the results of the present study, indicates that the flexural strength can be improved by the addition of both natural and synthetic fibers. Thus, the present study indicates that the use of SAPs as a pore-forming agent, together with GF has a good potential for the preparation of fiber-reinforced lightweight concrete.
Table 4. Comparison of results obtained in this study with literature.
4. Conclusion
In this work, SAPs were used as pore-forming agents for the production of GF-reinforced lightweight concrete. The effect of various GF contents on the mechanical and physical properties, sorptivity, thermal conductivity, and microstructure of the lightweight concretes prepared using SAPs were investigated, with the following conclusions:
Using SAPs at 7% by weight of OPC for the production of lightweight concrete resulted in materials with dry densities and thermal conductivities that meet the requirements of ASTM C332-17 for insulating concrete.
The compressive strengths and dry densities of lightweight concretes containing both SAPs and GF were directly related to the GF ratios; the 28-day compressive strengths decreased by 4%–35% and the dry densities decreased by 3%–18% compared to the reference sample. The addition of GF to the samples enhanced their 28-day flexural strength by 14%–72% compared to the reference sample.
The thermal conductivity of the lightweight concrete containing SAPs and GF decreased with increasing GF content, in the range 0.364 W/m-K in sample LCF0.1 to 0.285 W/m-K in sample LCF1.0.
The high porosity of lightweight concrete containing SAPs and GF directly affected the sorptivity rate. The initial rate of water absorption gradually increased from 2.48 × 10−1 mm/sec0.5 in sample LCF0 to 5.45 × 10−1 mm/sec0.5 in sample LCF1.0.
SEM microscopy shows good adhesion between the GF fibers and the lightweight SAPs-containing concrete, explaining the observed enhancement of the flexural strength. In future, this result could be more comprehensively studied by examining the microstructure of the fracture surface and the fiber–matrix interface of the flexural strength test samples.
Thus, this work demonstrates an alternative method for producing lightweight concrete using SAPs as pore-forming agent, but further investigations are required, including shrinkage, fire resistance, freeze-thaw behavior, as well as a comparison of the production costs with traditional techniques. In addition, an environmental assessment of this material after use should be made. In view of the large amount of industrial wastes containing glass fiber that is presently produced, current and future waste management policies and environmental legislation will require all engineering materials to be properly recovered and recycled to reduce both landfill and environmental impacts.
Acknowledgements
This research was supported by the National Science, Research and Innovation Fund (NSRF) and the Prince of Songkla University (Grant No ENG6601060S).
Disclosure statement
No potential conflict of interest was reported by the author(s).
Additional information
Funding
Notes on contributors
Kittipong Kunchariyakun
Kittipong Kunchariyakun is an associate professor in the School of Engineering and Technology, Walailak University, Nakhonsithammarat, Thailand. His main research field is the green and smart construction materials.
Suthatip Sinyoung
Suthatip Sinyoung is an assistant professor in the Department of Civil and Environmental Engineering, Faculty of Engineering, Prince of Songkla University, Songkhla, Thailand. Her main research field is wastes and hazardous wastes management.
Kenneth J. D. MacKenzie
Kenneth J.D. MacKenzie is a professor in the MacDiarmid Institute for Advanced Materials and Nanotechnology, School of Chemical and Physical Science, Victoria University of Wellington, Wellington, New Zealand. His main research field is ceramic materials, including traditional clay-based ceramics, cements, glasses, electronic ceramics, engineering and aerospace ceramics, bioceramics, and environmentally friendly materials (inorganic polymers and materials with structures mimicking nature).
Wongsatorn Boonyung
Wongsatorn Boonyung is a bachelor's degree student in School of Engineering and Technology, Walailak University. His research interest is lightweight construction materials.
Chanchira Suwannaphong
Chanchira Suwannaphong is a bachelor's degree student in School of Engineering and Technology, Walailak University. Her research interest is lightweight construction materials.
Kraisorn Pantong
Kraisorn Pantong is a bachelor's degree student in School of Engineering and Technology, Walailak University. His research interest is lightweight construction materials.
Piyawan Dungsang
Piyawan Dungsang is a bachelor's degree student in School of Engineering and Technology, Walailak University. Her research interest is lightweight construction materials.
References
- Alnahhal, A. M., U. J. Alengaram, S. Yusoff, P. Darvish, K. Srinivas, and M. Sumesh. 2022. “Engineering Performance of Sustainable Geopolymer Foamed and Non-Foamed Concretes.” Construction and Building Materials 316:125601. https://doi.org/10.1016/j.conbuildmat.2021.125601.
- American Society for Testing Materials. 2017. ASTM C332-17: Standard Specification for Lightweight Aggregates for Insulating Concrete. Philadephia PA.
- American Society for Testing Materials. 2020a. ASTM C109/C109M-20b: Standard Test Method for Compressive Strength of Hydraulic Cement Mortars (Using 2-In. or [50 Mm] Cube Specimens). Philadephia PA.
- American Society for Testing Materials. 2020b. ASTM C1585: Standard Test Method for Measurement of Rate of Absorption of Water by Hydraulic-Cement Concretes. Philadephia PA.
- American Society for Testing Materials. 2020c. ASTM C348 - 20: Standard Test Method for Flexural Strength of Hydraulic-Cement Mortars. Philadephia PA.
- American Society for Testing Materials. 2021. ASTM C518 - 21: Standard Test Methods for Steady-State Thermal Transmission Properties by Means of the Heat Flow Meter Apparatus. Philadephia PA.
- American Society for Testing Materials. 2022. ASTM C20-00: Standard Specification for Apparent Porosity, Water Absorption, Apparent Specific Gravity, and Bulk Density of Burned Refractory Brick and Shapes by Boiling Water. Philadephia PA.
- AzariJafari, H., A. Kazemian, M. Rahimi, and A. Yahia. 2016. “Effects of Pre-Soaked Super Absorbent Polymers on Fresh and Hardened Properties of Self-Consolidating Lightweight Concrete.” Construction and Building Materials 113:215–220. https://doi.org/10.1016/j.conbuildmat.2016.03.010.
- Barluenga, G., and F. Hernández-Olivares. 2007. “Cracking Control of Concretes Modified with Short AR-Glass Fibers at Early Age. Experimental Results on Standard Concrete and SCC.” Cement and Concrete Research 37 (12): 1624–1638. https://doi.org/10.1016/j.cemconres.2007.08.019.
- Beiranvandi, M., N. Akbari, A. Ahmadi, H. Mumivand, and F. Nazarian. 2022. “Biochar and Super Absorbent Polymer Improved Growth, Yield, and Phytochemical Characteristics of Satureja Rechingeri Jamzad in Water-Deficiency Conditions.” Industrial Crops and Products 183:114959. https://doi.org/10.1016/j.indcrop.2022.114959.
- Bencardino, F., A. Cecchi, M. Franceschi, M. Nisticò, L. Ombres, and S. Verre. 2019. “Structural Behavior of Small-Scale Masonry Panel with Fiber Reinforced Mortar Under Compressive Load.” Key Engineering Materials 817:472–477. https://doi.org/10.4028/www.scientific.net/KEM.817.472.
- Beushausen, H., M. Gillmer, and M. Alexander. 2014. “The Influence of Superabsorbent Polymers on Strength and Durability Properties of Blended Cement Mortars.” Cement and Concrete Composites 52:73–80. https://doi.org/10.1016/j.cemconcomp.2014.03.008.
- Centonze, G., M. Leone, and M. A. Aiello. 2012. “Steel Fibers from Waste Tires as Reinforcement in Concrete: A Mechanical Characterization.” Construction and Building Materials 36:46–57. https://doi.org/10.1016/j.conbuildmat.2012.04.088.
- Chen, H., P. Wang, J. Pan, A. S. Lawi, and Y. Zhu. 2021. “Effect of Alkali-Resistant Glass Fiber and Silica Fume on Mechanical and Shrinkage Properties of Cement-Based Mortars.” Construction and Building Materials 307:125054. https://doi.org/10.1016/j.conbuildmat.2021.125054.
- Cong, X., T. Qiu, J. Xu, X. Liu, L. Wang, Y. Wang, C. Chen, L. Zhao, C. Xing, and Y. Tan. 2022. “Study on the Effectiveness of Fibre Reinforcement on the Engineering Performance of Foamed Concrete.” Case Studies in Construction Materials 16:e01015. https://doi.org/10.1016/j.cscm.2022.e01015.
- Cunha, F. G., Z. L. M. Sampaio, and A. E. Martinelli. 2021. “Fiber-Reinforced Lightweight Concrete Formulated Using Multiple Residues.” Construction and Building Materials 308:125035. https://doi.org/10.1016/j.conbuildmat.2021.125035.
- Dai, L., Z. Zhu, C. Zhang, and D. Zhu. 2023. “Experimental Study on the Influence of Glass Fiber Reinforced Concrete Isolation Layer on the Seismic Dynamic Response of Tunnels.” Case Studies in Construction Materials 19:e02303. https://doi.org/10.1016/j.cscm.2023.e02303.
- Farzanian, K., K. Pimenta Teixeira, I. Perdigão Rocha, L. De Sa Carneiro, and A. Ghahremaninezhad. 2016. “The Mechanical Strength, Degree of Hydration, and Electrical Resistivity of Cement Pastes Modified with Superabsorbent Polymers.” Construction and Building Materials 109:156–165. https://doi.org/10.1016/j.conbuildmat.2015.12.082.
- Fenu, L., D. Forni, and E. Cadoni. 2016. “Dynamic Behaviour of Cement Mortars Reinforced with Glass and Basalt Fibres, Composites Part B.” Composites Part B Engineering 92:142–150. https://doi.org/10.1016/j.compositesb.2016.02.035.
- Fernando, T. N., S. A. Ariadurai, C. K. Disanayaka, S. Kulathunge, and A. G. B. Aruggoda. 2017. “Development of Radiation Grafted Super Absorbent Polymers for Agricultural Applications.” Energy Procedia 127:163–177. https://doi.org/10.1016/j.egypro.2017.08.106.
- Gencel, O., M. Nodehi, O. Yavuz Bayraktar, G. Kaplan, A. Benli, A. Gholampour, and T. Ozbakkaloglu. 2022. “Basalt Fiber-Reinforced Foam Concrete Containing Silica Fume: An Experimental Study.” Construction and Building Materials 326:126861. https://doi.org/10.1016/j.conbuildmat.2022.126861.
- Gencel, O., O. Yavuz Bayraktar, G. Kaplan, O. Arslan, M. Nodehi, A. Benli, A. Gholampour, and T. Ozbakkaloglu. 2022. “Lightweight Foam Concrete Containing Expanded Perlite and Glass Sand: Physico-Mechanical, Durability, and Insulation Properties.” Construction and Building Materials 320:126187. https://doi.org/10.1016/j.conbuildmat.2021.126187.
- Gencel, O., O. Yavuz Bayraktar, G. Kaplan, A. Benli, G. Martínez-Barrera, W. Brostow, M. Tek, and B. Bodur. 2021. “Characteristics of Hemp Fibre Reinforced Foam Concretes with Fly Ash and Taguchi Optimization.” Construction and Building Materials 294:123607. https://doi.org/10.1016/j.conbuildmat.2021.123607.
- He, T., R. Xu, Y. Da, R. Yang, C. Chen, and Y. Liu. 2019. “Experimental Study of High-Performance Autoclaved Aerated Concrete Produced with Recycled Wood Fibre and Rubber Powder.” Journal of Cleaner Production 234:559–567. https://doi.org/10.1016/j.jclepro.2019.06.276.
- Hu, M., J. Guo, J. Du, Z. Liu, P. Li, X. Ren, and Y. Feng. 2019. “Development of Ca2+-based, Ion-Responsive Superabsorbent Hydrogel for Cement Applications: Self-Healing and Compressive Strength.” Journal of Colloid and Interface Science 538:397–403. https://doi.org/10.1016/j.jcis.2018.12.004.
- Jensen, O. M., and P. F. Hansen. 2002. “Water-Entrained Cement-Based Materials: II.” Experimental Observations, Cement and Concrete Research 32 (6): 973–978. https://doi.org/10.1016/S0008-8846(02)00737-8.
- Ji, B.-Y., C.-P. Zhao, Y. Wu, W. Han, J.-Q. Song, and B. Wen-Bo. 2022. “Effects of Different Concentrations of Super-Absorbent Polymer on Soil Structure and Hydro-Physical Properties Following Continuous Wetting and Drying Cycles.” Journal of Integrative Agriculture 21 (11): 3368–3381. https://doi.org/10.1016/j.jia.2022.08.065.
- Jiang, T., Y. Wang, S. Shi, N. Yuan, X. Wu, D. Shi, K. Sun, Y. Zhao, W. Li, and J. Yu. 2022. “Study on Compressive Strength of Lightweight Concrete Filled with Cement-Reinforced Epoxy Macrospheres and Basalt Fibers.” Structures 44:1347–1355. https://doi.org/10.1016/j.istruc.2022.08.056.
- Justs, J., M. Wyrzykowski, D. Bajare, and P. Lura. 2015. “Internal Curing by Superabsorbent Polymers in Ultra-High Performance Concrete.” Cement and Concrete Research 76:82–90. https://doi.org/10.1016/j.cemconres.2015.05.005.
- Kim, E., K. Kim, and O. Song. 2020. “Properties of Basalt-Fiber Reinforced Foam Glass.” Journal of Asian Ceramic Societies 8 (1): 170–175. https://doi.org/10.1080/21870764.2020.1718858.
- Liu, J., N. Farzadnia, K. H. Khayat, and C. Shi. 2021. “Effects of SAP Characteristics on Internal Curing of UHPC Matrix.” Construction and Building Materials 280:122530. https://doi.org/10.1016/j.conbuildmat.2021.122530.
- Liu, J., N. Farzadnia, and C. Shi. 2021. “Microstructural and Micromechanical Characteristics of Ultra-High Performance Concrete with Superabsorbent Polymer (SAP.” Cement and Concrete Research 149:106560. https://doi.org/10.1016/j.cemconres.2021.106560.
- Liu, P., Z. Wu, X. Ge, and X. Yang. 2019. “Hydrothermal Synthesis and Microwave-Assisted Activation of Starch-Derived Carbons as an Effective Adsorbent for Naphthalene Removal.” RSC Advances 9 (21): 11696–11706. https://doi.org/10.1039/C9RA01386E.
- Małek, M., M. Jackowski, W. Łasica, and M. Kadela. 2021. “Influence of Polypropylene, Glass and Steel Fiber on the Thermal Properties of Concrete.” Materials 14 (8): 1888. https://doi.org/10.3390/ma14081888.
- Mechtcherine, V.; D. Dudziak; S. Hempel, 2009. “Mitigating Early Age Shrinkage of Concrete by Using Super Absorbent Polymers.” In 8th International Conference on Creep, shrinkage and durability mechanics of concrete and concrete structures-CONCREEP-8, Japan.
- Merino, S., C. Martín, K. Kostarelos, M. Prato, and E. Vázquez. 2015. “Nanocomposite Hydrogels: 3D Polymer–Nanoparticle Synergies for On-Demand Drug Delivery.” Agricultural Science & Technology Nano 9 (5): 4686–4697. https://doi.org/10.1021/acsnano.5b01433.
- Mirza, F. A., and P. Soroushian. 2002. “Effects of Alkali-Resistant Glass Fiber Reinforcement on Crack and Temperature Resistance of Lightweight Concrete.” Cement and Concrete Composites 24 (2): 223–227. https://doi.org/10.1016/S0958-9465(01)00038-5.
- Nagy, B., S. G. Nehme, and D. Szagri. 2015. “Thermal Properties and Modeling of Fiber Reinforced Concretes.” Energy Procedia 78:2742–2747. https://doi.org/10.1016/j.egypro.2015.11.616.
- Newman, J., and P. Owens. 2003. “Properties of Lightweight Concrete.” In Advanced Concrete Technology, edited by J. Newman and B. S. Choo, 3–29. Oxford: Butterworth-Heinemann. https://doi.org/10.1016/B978-075065686-3/50288-3.
- Nodehi, M., and S. E. Nodehi. 2021. “Ultra High Performance Concrete (UHPC): Reactive Powder Concrete, Slurry Infiltrated Fiber Concrete and Superabsorbent Polymer Concrete.” Innovative Infrastructure Solutions 7 (1): 39. https://doi.org/10.1007/s41062-021-00641-7.
- Ouattara Coumoin, C., F. Wang, J. Yang, and Z. Liu. 2019. “Effect of SAP on Properties of High Performance Concrete Under Marine Wetting and Drying Cycles.” Journal Wuhan University of Technology, Materials Science Edition 34 (5): 1136–1142. https://doi.org/10.1007/s11595-019-2170-3.
- Panesar, D. K. 2013. “Cellular Concrete Properties and the Effect of Synthetic and Protein Foaming Agents.” Construction and Building Materials 44:575–584. https://doi.org/10.1016/j.conbuildmat.2013.03.024.
- Park, B., and Y. C. Choi. 2018. “Self-Healing Capability of Cementitious Materials with Crystalline Admixtures and Super Absorbent Polymers (SAPs).” Construction and Building Materials 189:1054–1066. https://doi.org/10.1016/j.conbuildmat.2018.09.061.
- Pehlivanlı, Z. O., İ. Uzun, Z. P. Yücel, and İ. Demir. 2016. “The Effect of Different Fiber Reinforcement on the Thermal and Mechanical Properties of Autoclaved Aerated Concrete.” Construction and Building Materials 112:325–330. https://doi.org/10.1016/j.conbuildmat.2016.02.223.
- Pourjavadi, A., S. M. Fakoorpoor, P. Hosseini, and A. Khaloo. 2013. “Interactions Between Superabsorbent Polymers and Cement-Based Composites Incorporating Colloidal Silica Nanoparticles.” Cement and Concrete Composites 37:196–204. https://doi.org/10.1016/j.cemconcomp.2012.10.005.
- Rutkevičius, M., S. K. Munusami, Z. Watson, A. D. Field, M. Salt, S. D. Stoyanov, J. Petkov, G. H. Mehl, and V. N. Paunov. 2012. “Fabrication of Novel Lightweight Composites by a Hydrogel Templating Technique.” Materials Research Bulletin 47 (4): 980–986. https://doi.org/10.1016/j.materresbull.2012.01.014.
- Samarakoon, S. M. S. M. K., P. Ruben, J. Wie Pedersen, and L. Evangelista. 2019. “Mechanical Performance of Concrete Made of Steel Fibers from Tire Waste.” Case Studies in Construction Materials 11:e00259. https://doi.org/10.1016/j.cscm.2019.e00259.
- Senff, L., R. C. E. Modolo, G. Ascensão, D. Hotza, V. M. Ferreira, and J. A. Labrincha. 2015. “Development of Mortars Containing Superabsorbent Polymer.” Construction and Building Materials 95:575–584. https://doi.org/10.1016/j.conbuildmat.2015.07.173.
- Söylev, T. A., and T. Özturan. 2014. “Durability, Physical and Mechanical Properties of Fiber-Reinforced Concretes at Low-Volume Fraction.” Construction and Building Materials 73:67–75. https://doi.org/10.1016/j.conbuildmat.2014.09.058.
- Tally, M., and Y. Atassi. 2015. “Optimized Synthesis and Swelling Properties of a pH-Sensitive Semi-IPN Superabsorbent Polymer Based on Sodium Alginate-G-Poly(acrylic Acid-Co-Acrylamide) and Polyvinylpyrrolidone and Obtained via Microwave Irradiation.” Journal of Polymer Research 22 (9): 181. https://doi.org/10.1007/s10965-015-0822-3.
- Thai Industrial Standards Institute. 2013. TIS No. 2601-2556: Cellular Lightweight Concrete Blocks. Bangkok.
- Thakur, S., S. Pandey, and O. A. Arotiba. 2016. “Development of a Sodium Alginate-Based Organic/Inorganic Superabsorbent Composite Hydrogel for Adsorption of Methylene Blue.” Carbohydrate Polymers 153:34–46. https://doi.org/10.1016/j.carbpol.2016.06.104.
- Thompson, B. R., T. S. Horozov, S. D. Stoyanov, and V. N. Paunov. 2018. “Hierarchically Porous Composites Fabricated by Hydrogel Templating and Viscous Trapping Techniques.” Materials & Design 137:384–393. https://doi.org/10.1016/j.matdes.2017.10.046.
- Wang, J. Y., D. Snoeck, S. Van Vlierberghe, W. Verstraete, and N. De Belie. 2014. “Application of Hydrogel Encapsulated Carbonate Precipitating Bacteria for Approaching a Realistic Self-Healing in Concrete.” Construction and Building Materials 68:110–119. https://doi.org/10.1016/j.conbuildmat.2014.06.018.
- Wang, L., S. Nagarajaiah, W. Shi, and Y. Zhou. 2020. “Study on Adaptive-Passive Eddy Current Pendulum Tuned Mass Damper for Wind-Induced Vibration Control.” The Structural Design of Tall & Special Buildings 29 (15): e1793. https://doi.org/10.1002/tal.1793.
- Wang, L., S. Nagarajaiah, W. Shi, and Y. Zhou. 2021. “Semi-Active Control of Walking-Induced Vibrations in Bridges Using Adaptive Tuned Mass Damper Considering Human-Structure-Interaction.” Engineering Structures 244:112743. https://doi.org/10.1016/j.engstruct.2021.112743.
- Wang, L., S. Nagarajaiah, W. Shi, and Y. Zhou. 2022. “Seismic Performance Improvement of Base-Isolated Structures Using a Semi-Active Tuned Mass Damper.” Engineering Structures 271:114963. https://doi.org/10.1016/j.engstruct.2022.114963.
- Wang, L., S. Nagarajaiah, Y. Zhou, and W. Shi. 2023. “Experimental Study on Adaptive-Passive Tuned Mass Damper with Variable Stiffness for Vertical Human-Induced Vibration Control.” Engineering Structures 280:115714. https://doi.org/10.1016/j.engstruct.2023.115714.
- Wang, L., W. Shi, and Y. Zhou. 2022. “Adaptive-Passive Tuned Mass Damper for Structural Aseismic Protection Including Soil–Structure Interaction.” Soil Dynamics and Earthquake Engineering 158:107298. https://doi.org/10.1016/j.soildyn.2022.107298.
- Wang, L., Y. Zhou, and W. Shi. 2023. “Seismic Control of a Smart Structure with Semiactive Tuned Mass Damper and Adaptive Stiffness Property.” Earthquake Engineering and Resilience 2 (1): 74–93. https://doi.org/10.1002/eer2.38.
- Wang, X., S. P. Strand, Y. Du, and K. M. Vårum. 2010. “Chitosan–DNA–Rectorite Nanocomposites: Effect of Chitosan Chain Length and Glycosylation.” Carbohydrate Polymers 79 (3): 590–596. https://doi.org/10.1016/j.carbpol.2009.09.012.
- Wang, Y., L. Wang, and W. Shi. 2021. “Two-Dimensional Air Spring Based Semi-Active TMD for Vertical and Lateral Walking and Wind-Induced Vibration Control.” Structural Engineering and Mechanics 80 (4): 377–390.
- Wang, Y., W. Wang, and A. Wang. 2013. “Efficient Adsorption of Methylene Blue on an Alginate-Based Nanocomposite Hydrogel Enhanced by Organo-Illite/smectite Clay.” Chemical Engineering Journal 228:132–139. https://doi.org/10.1016/j.cej.2013.04.090.
- Xu, R., T. He, Y. Da, Y. Liu, J. Li, and C. Chen. 2019. “Utilizing Wood Fiber Produced with Wood Waste to Reinforce Autoclaved Aerated Concrete.” Construction and Building Materials 208:242–249. https://doi.org/10.1016/j.conbuildmat.2019.03.030.
- Yao, Y., Y. Zhu, and Y. Yang. 2012. “Incorporation Superabsorbent Polymer (SAP) Particles as Controlling Pre-Existing Flaws to Improve the Performance of Engineered Cementitious Composites (ECC).” Construction and Building Materials 28 (1): 139–145. https://doi.org/10.1016/j.conbuildmat.2011.08.032.
- Zhang, J., F. Huang, Y. Wu, T. Fu, B. Huang, W. Liu, and R. Qiu. 2022. “Mechanical Properties and Interface Improvement of Bamboo Cellulose Nanofibers Reinforced Autoclaved Aerated Concrete.” Cement and Concrete Composites 134:104760. https://doi.org/10.1016/j.cemconcomp.2022.104760.