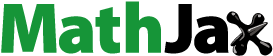
ABSTRACT
Owing to the generation of waste during mining and processing, granite stone causes great damage to the environment. In this study, the broken granite waste and the stone powder were used as concrete coarse aggregate and “admixture” to make granite waste concrete hollow blocks, which could meet the requirements of compressive strength, durability and economy. The influence of the water-binder ratio, cement dosage, and powder-slag ratio on the compressive strength and freeze-thaw properties of the block were analyzed. Subsequently, the optimal mix ratio was determined based on range analysis. The effect of granite waste on the compressive strength and durability of the blocks was also analyzed. In addition, the economic effects of the granite waste concrete hollow block were analyzed. The results show that granite waste concrete hollow blocks with a water-binder ratio of 0.55, powder slag ratio of 15%, and cement dosages of 340 kg/m3 and 320 kg/m3 can meet the strength requirements of MU10 grade and the requirements of freeze-thaw properties. The strength and frost resistance of the granite concrete hollow blocks were enhanced because the granite powder filled the aggregate gaps. In addition, the price of granite concrete hollow blocks was reduced by approximately 50%. The small hollow block of granite concrete is environmentally friendly and worth promoting.
1. Introduction
Granite is hard, dense, and corrosion-resistant, has low water absorption and beautiful color, and can be preserved for hundreds of years. Granite is often used as a decorative material (Gencel et al. Citation2012). However, in granite mining and processing, a large amount of scraps and dust are generated owing to sawing, polishing, and other processes (Vijayalakshmi, Sekar, and Prabhu Citation2013). Dust with a small particle size and light weight generated by cutting will seriously harm the safety of residents and crops if they cover nearby villages and paddy fields (Rajgor and Pitroda Citation2012). Another part of weathered granite and cut waste material will be piled on both sides of the river, around the mine, or even in wasteland, which results in the waste of land resources (Aarthi and Arunachalam Citation2018; Taji et al. Citation2019).
To protect the ecological environment, the disposal of granite waste is necessary. At present, a series of studies on the feasibility of reusing granite waste have been conducted. Krzysztof Ostrowski et al. (Ostrowski et al. Citation2020) described the morphological characteristics of granite using indoor microscale tests and introduced a treatment process for granite waste. This study provided a theoretical basis for the reuse of granite waste. Granite has also been used as a substitute for raw ceramic materials in the preparation of ceramic products to conserve natural resources. The test results show that adding an appropriate amount of granite waste promotes the performance of ceramic products without changing the original process conditions of ceramic tile production (Menezes et al. Citation2005; Torres et al. Citation2003; Vidak, Nevenka, and Zagorka Citation2022).
The main component of granite waste is silicon dioxide, which is a popular additive in concrete and can improve its strength and durability (Alqamish and AlTamimi Citation2021; S et al. Citation2021). Abhishek Jain et al (Jain, Gupta, and Chaudhary Citation2020). added granite waste and fly ash to dense concrete instead of fine aggregates and cement. The results show that granite waste and fly ash can significantly improve the hardening performance of the fresh mix without adversely affecting its strength. At present, granite waste has been applied in high-performance concrete, pavement base materials, and wall materials, all of which have good performance (Akbulut and Gürer Citation2006; Jain, Gupta, and Chaudhary Citation2020). Therefore, granite has a great potential as a building material.
In rural China, 70% of building materials are wall materials, of which clay brick accounts for the largest proportion (approximately 90%). However, the production of clay bricks requires a large amount of arable land (Riaz, Khitab, and Ahmed Citation2019). Currently, autoclaved fly ash blocks are used to replace clay bricks, but they have inadequate strength and poor durability. Compared with autoclaved fly ash blocks, concrete hollow blocks have better strength and durability, which is also energy savings, environmental protection, simple production, and light weight. However, the cost of the hollow concrete block is slightly high. Therefore, it is necessary to research and develop new wall materials that can reuse waste, save soil, meet the requirements of strength and durability, and reduce cost (Bewket, Lemma, and Getahun Citation2022; Fraile-Garcia et al. Citation2016; Hong et al. Citation2021; Jiao et al. Citation2018; Li et al. Citation2021; Liu et al. Citation2019; Pawar Citation2021).
Granite waste is inexpensive and not environmentally friendly. Realizing the application of granite waste in concrete hollow blocks can not only protect farmland and the environment but also realize waste utilization. At the same time, the application of waste can reduce costs.
In this study, a method for preparing granite waste concrete hollow blocks was explored by using granite waste to completely replace natural coarse aggregate, which can meet the requirements of compressive strength, durability, and economy. The effects of the water-cement ratio, cement dosage, and powder-slag ratio on the strength and freeze-thaw properties of granite waste concrete hollow blocks were investigated. The mix ratio of the granite waste concrete hollow block with the highest strength and frost resistance was determined. In addition, the economic effects of the prepared granite waste concrete hollow blocks were analyzed.
This study can reduce the pollution caused by granite waste, save resources, and reduce the cost of blocks, which are conducive to the development of society and the economy. This study can also provide a new type of wall material that is economical and can satisfy load-bearing requirements.
2. Experimental program
2.1. Material properties
The granite was obtained from the waste of Baotianman Stone Co., Ltd., China. The waste (as shown in was repeatedly broken and screened because the maximum particle size of the coarse aggregate should not be greater than 10 mm. After screening, small gravel with a diameter between 5 mm and 10 mm (as shown in was selected as the coarse aggregate to replace the natural coarse aggregate in concrete, whose physical properties are listed in . Granite powder (as shown in formed during the sawing, polishing, and crushing processes of the granite scraps was added to the concrete as an admixture.
Figure 1. The different types of granite waste: (a) the granite waste of Baotianman Stone Co., LTD.;(b) the small gravel with a diameter between 5mm to 10mm;(c) granite powder.
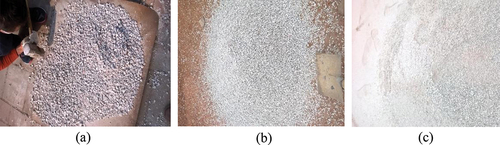
Table 1. Physical property index of coarse aggregates of granite waste.
River sand with a fineness modulus is 3.0. Lignosulfonate was used as a water-reducing agent, which greatly reduces water consumption and inhibits slump loss. Ordinary Portland cement of 32.5 grade was used in the test, produced by Xinxing Cement Factory, was used in the test.
2.2. The design of mix ratio
To determine the best mix ratio of the granite waste hollow block, the best mix ratio of concrete needs to be determined first, because there is a linear relationship with a positive correlation between the strength of concrete and the strength of the hollow block. Therefore, the effects of different factors on the compressive, freeze-thaw properties, and economic benefits of concrete with granite waste were studied first through an orthogonal test. Based on the results of the orthogonal test, the best two mix ratios of granite concrete could be selected, which could meet the requirements of compressive, freeze-thaw properties, and economic benefits. The two best mix ratios were also used for the preparation of granite waste hollow blocks for further use.
The water-binder ratio, cement dosage, and powder-slag ratio are important for the compressive and freeze-thaw properties of concrete. Therefore, the effects of the three factors on the compressive and freeze-thaw properties were studied. To improve the efficiency of the experiment, it was designed according to the L9(34) orthogonal table. The orthogonal test table, experimental arrangement and sample number are listed in .
Table 2. Orthogonal test factor levels.
Table 3. The experiment arrangement according to L9(34) orthogonal table.
2.3. Sample preparation
2.3.1. Granite concrete specimens
According to , nine types of granite concrete specimens with dimensions of 100 × 100 × 100 were prepared. Nine specimens were prepared for each type of sample. Among the nine specimens, three were used for the compressive test and the other six specimens were used for the freeze-thaw test. Three of the six specimens for the freeze-thaw test were used as the comparison group.
During the test, 9 groups of test blocks are placed on the lower pressure plate of the pressure testing machine according to the group number, and the forming top surface of the test block is perpendicular to the pressure surface when the test block is placed. Start the testing machine, load evenly at a speed of 5KN/s until the test block is broken, record the maximum failure load, and the compression process of the concrete test block is shown in .
2.3.2. Granite concrete hollow block
A granite concrete hollow block with a size of 390 mm × 190 mm × 190 mm was prepared by a laboratory method. The block cavity rate was 46.1%. According to the Chinese specifications, the external wall and rib thicknesses were designed to be 35 mm, and the hole angle was designed as an arc with a radius of 15 mm. In addition, the compressive strength of the granite concrete hollow block needs to be above MU10, and the number of freeze-thaw cycles of the granite concrete hollow block must be no less than 25.
According to the design index of the granite concrete hollow block, the dimensions of each component and the position of the drill hole of the steel die were accurately drawn using the software, as shown in . A set of steel dies is composed of five parts: a bottom plate, horizontal plate, side plate, inner column, and press bar. Each part is connected using bolts. The dimensions of the main components of the steel dies are presented in .
Figure 3. Dimensions of the main components of the steel mold: (a) Horizontal plate; (b) Side plate; (c) Angle yards; (d) Angle yards; (e) Drill location of bottom plate; (f) Overall model of steel die.
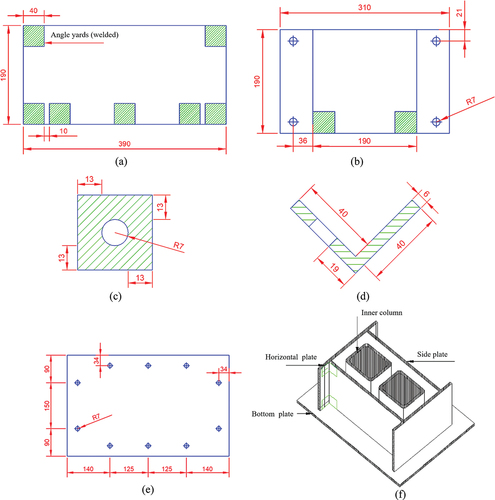
Table 4. Dimensions of the main components of the steel mold.
Based on the two best mix ratios, the concrete paste was prepared and poured into the steel mold three times. First, fix the bottom bolt, and evenly apply oil-based release agent (silicone oil) to the inner column wall, side plate and horizontal plate with a brush. With each pour, the steel mold vibrated once. The last vibration did not stop until the slurry was removed. The steel mold was then immediately moved to flat ground. All bolts of the bottom plate were removed. Subsequently, the steel mold was reversed on the ground, and the bottom plate was slowly separated. The horizontal and side plates were separated after the paste solidified slightly.The process of making granite hollow blocks is shown in .
2.4. Test methods
2.4.1. Compressive strength
Compressive testing was performed in the laboratory of Zhengzhou University, with a maximum measuring range of 2000 kN.
The concrete specimens were removed after curing for 28 d and then cleaned with a brush. Compressive testing was performed in the laboratory of Zhengzhou University, with a maximum measuring range of 2000 kN. The machine was uniformly loaded at a speed of 5 kN/s until the specimen broke. The maximum failure load, P0 was recorded.
A compression test was carried out for the granite concrete hollow block after the specimens were cured for 24 h. The test machine was a microcomputer-controlled electro-hydraulic servo pressure testing machine (YAW6596) provided by Jinke Co., Ltd. The maximum measurement range was 5000kN. The specimens were placed on a press plate, and the opening direction was ensured to be consistent with the pressure direction. According to the specifications, the machine was uniformly loaded at a speed of 4 kN/s until the specimens broke. The maximum failure load (P0)was then recorded.
According to the Chinese standard (GB/T4111–2013), the compressive strength of hollow concrete blocks should be calculated according to Eq. (1).
where fc is the compressive strength of the hollow concrete block (MPa), P0 is the failure load of the concrete specimen (N), L is the length of the bearing surface of the specimen (mm), B is the width of the bearing surface of the specimen (mm).
2.4.2. Freeze-thaw cycle test
The strength loss rate and quality loss rate were evaluated using the freeze-thaw test. A press machine from the laboratory of Jinke Co., Ltd. was used in the test. The freeze-thawing test was performed using a freeze-thawing testing machine (TDS-300) produced by Donghua Test Instrument Co., Ltd.
For the concrete specimens and granite concrete hollow blocks, the 28-days specimens were weighed and recorded as m1. The specimens were then soaked for 4 days. The specimens were removed and wiped with a wet towel. The weight was recorded as m2, which also represented the mass of the specimen before freezing and thawing. The weighed blocks were placed in a freeze-thaw machine. The spacing between the blocks and that between the blocks and the inner wall of the freeze-thaw machine was ensured to be greater than 20 mm. Subsequently, the number of freeze-thaw cycles of the freeze-thaw machine was set to 25. After every five freeze-thaw cycles, the block was checked to record the damage condition. After freezing and thawing, the specimens were removed and wiped using a wet towel. The weight was recorded in m3.
Subsequently, all concrete specimens and granite concrete hollow blocks were loaded evenly at speeds of 5 kN/s and 4 kN/s, respectively. The maximum failure load (P0) was then recorded.
The strength loss rate of a single block and the average strength loss rate of the blocks were calculated using Eq. (2) and Eq. (3), respectively:
where Ki is the strength loss rate of a single block, %; ff is the average compressive strength of three specimens, which is not frozen and thawed (MPa); fi is the compressive strength of a single freeze-thaw specimen, MPa; KR is the average strength loss rate of the specimen, %; fR is the average compressive strength of three freeze-thaw specimens (MPa).
The mass loss rate of the granite concrete hollow block was calculated using Eqs. (4).
where KM is the mass loss rate of the specimen (%), m2 is the mass of the specimen before freezing and thawing (kg), m3 is the mass of the specimen after freezing and thawing (kg).
3. Results and discussion
3.1. The selection of optimal mix ratio
The optimum mix ratio was obtained by analyzing the influence of the water-binder ratio, cement dosage, and powder-slag ratio on the compressive strength, strength loss rate, and mass loss rate using the range analysis method.
3.1.1. The effect rules of different factors on compressive strength
The effects of the water-binder ratio, cement content, and powder-slag ratio on the compressive strength of the concrete are shown in .
Figure 5. The effects of different factors on the compressive strength of concrete:(a) Water-binder ratio; (b) Cement content; (c) Powder-slag ratio.
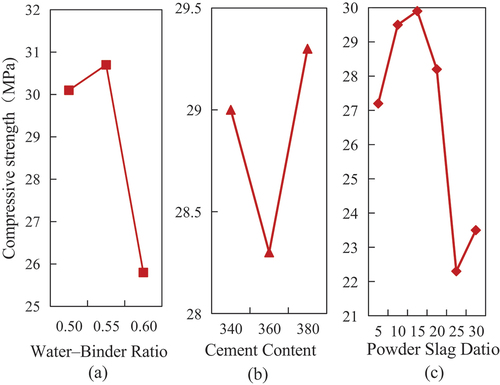
As shown in , there was an inflection point. The compressive strength of concrete increases with an increase in the water-binder ratio when the water-binder ratio is between 0.5 and 0.55. However, the compressive strength decreases with an increase in the water-binder ratio when the water-binder ratio is larger than 0.55. When the water-binder ratio was less than 0.55, the water used for the hydration of cement was insufficient. The hydration degree increased as the water-binder ratio increased. Therefore, the compressive strength of concrete increases with an increase in the water-binder ratio when the water-binder ratio is less than 0.55 (Meng et al. Citation2023). When the water-binder ratio is greater than 0.55, the water used for the hydration of cement is sufficient and surplus. Excess water creates pores in concrete, which results in a loss of compressive strength (Lijuan et al. Citation2022; Wang and Park Citation2017; Zhang, Song, and Ding Citation2022).
As shown in , when the cement dosage was less than 360 kg/m3, the compressive strength of concrete increased with increasing cement content is less than 360 kg/m3. A cement dosage of 360 kg/m3 was the turning point. The increase in cement dosage leads to an increase in water consumption when the water-binder ratio is the same. However, a large amount of water will lead to collapse and deformation, whereas a small amount of water will lead to difficulty in the vibration molding of concrete. The highest compressive strength is reached when the amount of water meets the requirement of sufficient cement hydration. In addition, the cost of the block mainly comes from the cement because of the low cost of the granite waste aggregate. The reduction in cement is beneficial for the cost control of the block. Therefore, the most reasonable amount of cement can not only meet the requirements of compressive strength, but also achieve maximum economic benefits.
As shown in , the compressive strength of concrete increases with an increase in the powder-slag ratio when the powder-slag ratio is between 5% and 15%. However, the compressive strength decreases with an increase in the water-binder ratio when the powder-slag ratio is larger than 15%. Therefore, 15% was the best powder-slag ratio.
3.1.2. The effect rules of different factors on freeze-thaw properties
The results of freeze-thaw test of concrete are shown in .
As shown in , the strength loss rate and mass loss rate of concrete increase with an increase in the water-binder ratio when the water-binder ratio is between 0.5 and 0.55. However, the strength loss rate and mass loss rate decreased with an increase in the water-binder ratio when the water-binder ratio was larger than 0.55. The rules are similar to those for the compressive strength. When the water-binder ratio was less than 0.55, the water used for the hydration of cement was insufficient. The hydration degree increased as the water-binder ratio increased. The freeze-thaw resistance and hydration degree are positively correlated (An, Wang, and Yu Citation2019). Therefore, the strength loss rate and mass loss rate increase with an increase in the water-binder ratio. When the water-binder ratio is greater than 0.55, the water used for the hydration of cement is sufficient and surplus. The excess water creates pores in the concrete, which is harmful to freeze – thaw resistance.
Figure 7. The effects of different factors on the strength loss rate:(a) Water-binder ratio; (b) Cement content; (c) Powder-slag ratio.
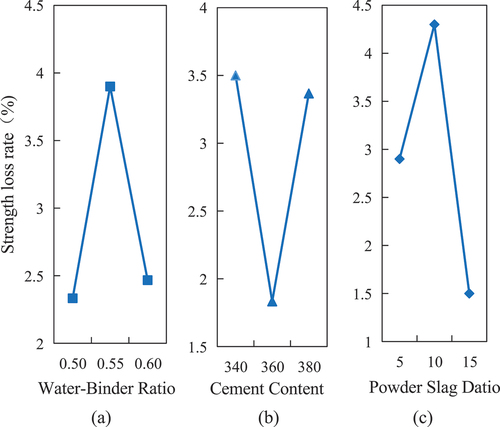
Figure 8. The effects of different factors on the mass loss rate:(a) water-binder ratio; (b) cement content; (c) powder-slag ratio.
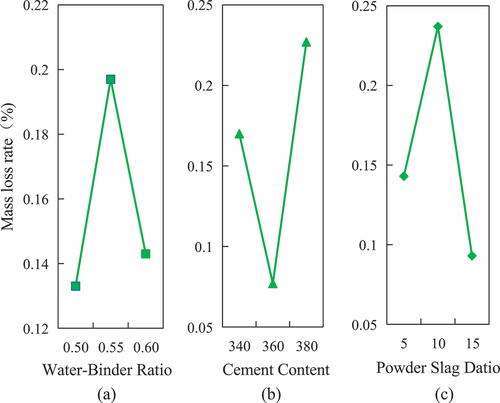
As shown in , the strength loss rate and mass loss rate increase with increasing cement content. A cement dosage of 360 kg/m3 is a turning point, which has the best freeze-thaw resistance. When the cement dosage is less than 360 kg/m3 , the aggregate cannot be wrapped tightly by cement paste, which is harmful to the internal structure of the concrete. Therefore, the freeze-thaw resistance of concrete is low. When the cement dosage is greater than 360 kg/m3, the decrease in the ability of the concrete to freeze – thaw resistance is due to the cracking and shrinkage of concrete caused by excessive paste.
As shown in , the strength loss rate and mass loss rate of concrete increase with an increase in the powder-slag ratio when the powder-slag ratio is between 5% and 10%. However, the strength loss rate and mass loss rate decreased with an increase in the powder-slag ratio when the powder-slag ratio was larger than 10%. The rate of decrease is larger when the powder-slag ratio is more than 10%. This is because the granite powder can fill the gaps between the aggregates and lubricate the aggregate surface. The filling can dense the internal structure of concrete, which is beneficial for freeze-thaw resistance.
3.1.3. The determine of optimum mix ratio by range analysis method
Orthogonal arrangement table L9(34) has evenly distributed the test conditions to different parts, so the test results have a good representative. Therefore, the best combination in the nine groups of tests will also be a good ratio in the whole combination. However, the total combination is much more than nine combinations and the optimal combination may not be among the nine groups, so further analysis is needed. At the same time, the function of polar deviation folding of orthogonal test was utilized to distinguish the importance of each factor and predict the better level combination, which provides an effective basis for further tests.
According to the judgment rule of range analysis, the larger the range of a column, the greater the impact on the test index when the factors corresponding to the column change within the range of the test level. Based on the range analysis function of the orthogonal experimental design assistant, the range of each factor is shown in .
Table 5. The range analysis of compressive strength.
Table 6. The range analysis of strength loss rate.
Table 7. The range analysis of mass loss rate.
As shown in , A, B, and C represent the water-binder ratio, cement dosage, and powder-slag ratio, respectively. The water – binder ratio, cement content, and powder-slag ratio have different effects on the compressive strength, strength loss rate, and mass loss rate of concrete.
As shown in , the results of the range analysis show that the influence of the water-binder ratio on the compressive strength is greater than that of the powder-slag ratio, which is greater than that of the cement content. The optimum combination of AIIBIIICIII was obtained by comparing the range values corresponding to each level of the same factor.
As shown in , the results of the range analysis show that the influence of the P/L ratio on the compressive strength is greater than that of the cement content, which is greater than that of the water-binder ratio. The optimum combination of AIBIICIII was obtained by comparing the range values corresponding to each level of the same factor.
As shown in , the ranges of the water-binder ratio, cement content, and powder-slag ratio were all small. The results indicate that the influence of the water-binder ratio, cement content, and powder-slag ratio on the compressive strength is small.
The results of the range analysis show that the optimum combination differs when the compressive strength, strength loss rate, and mass loss rate are considered. Therefore, a reasonable choice should be made based on the purpose and economy. Considering the purpose of this study, the compressive strength should be prioritized. Therefore, a water-binder ratio of 0.55 was chosen. Considering the economic benefit and mechanical performance, lower cement contents of 340 kg/m3 and 320 kg/m3 were chosen. Considering the cost and environmental awareness, the highest powder-slag ratio of 15% was chosen.
3.2. Mechanical properties and freeze-thaw properties of granite concrete hollow block
Two different mix ratios selected by range analysis were used in the preparation of the granite concrete hollow blocks. The mechanical properties and freeze-thaw properties of granite concrete hollow blocks with two mix ratios were explored.
3.2.1. Mechanical properties of granite concrete hollow block
The compressive strength of the granite concrete hollow blocks are shown in , which meets the requirement of grade MU10. This grade is commonly used in the blocks. The results showed that the block with a cement content of 340 kg/m3 had a relatively stable strength, and its appearance was dense. The block with a cement content of 320 kg/m3 had a poorer stable strength and an uncompacted appearance. However, a cement content of 320 kg/m3 is more economical. In addition, pressure pressing is required for factory production. Therefore, in the case of factory production, a cement content of 320 kg/m3 is preferred for making MU10 blocks.
As shown in and , at present, the compressive strength of most hollow blocks is low due to the material properties. They can only be used in non-load walls (Ali et al. Citation2020; Lasco, Madlangbayan, and Sundo Citation2017; Olofinnade et al. Citation2023; Wu et al. Citation2018; Xie et al. Citation2021; Zheng and Guangxiu Citation2018). In contrast, granite waste hollow block has higher compressive strength, which has great application prospects in load-bearing wall materials.
Table 8. Compressive strength of new hollow blocks.
3.2.2. Freeze-thaw properties of granite concrete hollow block
The freeze-thaw properties of the granite concrete hollow blocks are listed in . In the table, 320DNi is the freeze-thaw group with a cement content of 320 kg/m3 and 320DBNi is the comparison group with a cement content of 320 kg/m3. In addition, the mass-loss rate is replaced by zero when it is negative.
Table 9. Strength loss rate and mass loss rate of granite concrete hollow block.
The frost resistance index of the concrete block is shown in . For the mass loss rate, the maximum value of single mass loss rate of the test block is 0.1% and the average value of mass loss rate is 0.03%, which are far less than the standard value. At the same time, for the strength loss rate, the maximum value of single strength loss rate of the test block is 29%, which is less than the specification requirement of 30%. The average value of strength loss rate was 18%, which is also less than the specification requirement of 20%. Therefore, the freeze-thaw properties of the granite concrete hollow block can meet the index of the frost resistance index.
Table 10. Frost resistance index of concrete block.
3.3. Economic benefit analysis of granite concrete hollow block
Granite of small hollow concrete block as a kind of new wall materials, energy saving, environmental protection, recycling, not only the characteristics of low carbon and light, at the same time has good strength and durability, to meet the basic requirement of load-bearing wall using.However, whether it can be vigorously promoted also depends on its economy.
The cost of the granite concrete hollow block includes the costs of concrete and production. The cost and selling price of two different mix ratios of the granite concrete hollow blocks are listed in .
Table 11. The price of granite concrete hollow block.
lists the prices of various types of block bricks. As shown in , the price per cubic meter of granite concrete hollow block is only 42.6% of the highest price of 236, which means that granite concrete hollow block has better market competitiveness.
Table 12. Prices of various types of block bricks.
The application of granite waste will reduce the burden of granite ore plant waste treatment and provide an effective method for solving granite waste pollution. The hollow ratio of the granite concrete hollow block was 46.1%, and its density was only 1200 kg/m3. Therefore, the self-weight of the block wall and transportation cost of the block can be significantly reduced. In addition, the load bearing of the foundation and the foundation cost can be reduced. Granite concrete hollow blocks are also non-fired bricks, which can save considerable coal resources.
As granite hollow block has high compressive strength, it can be used in all kinds of building walls in areas with seismic design intensity of 8 degrees and below, including high-rise and large-span buildings, with good anti-seismic performance. At the same time, with the use of FM mass damper, it has a great application prospect in the seismic wall, which can well reduce the damage of earthquake and protect people’s property safety (Wang et al. Citation2019, Citation2020, Citation2020, Citation2020, Citation2022, Citation2023; Wang, Shi, and Zhou Citation2019; Wang, Wang, and Shi Citation2021; Wang, Wang, and Zhou Citation2022).
4. Conclusion
In this study, the effects of the water-cement ratio, cement content, and powder-slag ratio on the strength and freeze-thaw properties of granite waste concrete hollow blocks were investigated. The mix ratio of the granite waste concrete hollow block with the highest strength and frost resistance was determined. In addition, the economic effects of the prepared granite waste concrete hollow blocks were analyzed. The results are as follows:
The strength and freeze-thaw properties of the granite concrete were enhanced because the granite powder filled the aggregate gap.
The water-cement ratio has a significant influence on the strength of granite concrete, which is the main influencing factor. When the water glue ratio was 0.55, the compressive strength of the concrete was at its maximum, and the freezing resistance was satisfied. The cement content has a significant influence on freeze-thaw properties. When the amount of cement was 360 kg/m3, the freezing resistance was the highest, but the compressive strength was the lowest. The optimal mixing amount of granite powder was 15%.
The compressive strength of granite concrete hollow blocks with a water-binder ratio of 0.55, powder slag ratio of 15%, and cement content of 340 kg/m3 or 320 kg/m3 can meet the strength requirements of MU10 grade and freeze-thaw properties. Meanwhile, compared with other new hollow blocks, granite concrete hollow blocks have higher compressive strength and can be used in load-bearing walls.
The unit price per cubic meter of granite concrete hollow blocks was reduced by approximately 50%. Granite concrete hollow blocks with a cement content of 320 kg/m3 were more economical.
This study can reduce the pollution caused by granite waste, save resources, and reduce the cost of blocks, which are conducive to the development of society and the economy. This study can also provide a new type of wall material, which is economical and can meet the load-bearing requirements.
Author contributions
Gengqi Zhao: Conceptualization, Methodology, Validation, Formal analysis, data curation, and writing of the original draft. Xiaogang Gao and Xiaoxing Huang: Investigation, validation, and writing – original draft. Xiaohang Zhang: Writing the original draft, formal analysis, Resources, Project administration, and funding acquisition.
All authors have read and agreed to the published version of the manuscript.
Acknowledgements
This research was supported by the China Postdoctoral Science Foundation. The Grant Number is (2022M710044).
Disclosure statement
No potential conflict of interest was reported by the author(s).
Additional information
Funding
Notes on contributors
Gengqi Zhao
Gengqi zhao, Ph.D., Professor, post-graduate student advisor, Class 1 Registered Constructor. Research fields: construction building materials, structural reinforcement.
Xiaogang Gao
Xiaogang Gao, Master, Student. Research fields: construction building materials, structural reinforcement.
Xiaohang Zhang
Xiaohang Zhang, Ph.D., Post-doctor. Research fields: self-healing concrete, cement hydration, bio-cement.
Xiaoxing Huang
Xiaoxing Huang, Master. Research fields: construction building materials, structural reinforcement.
References
- Aarthi, K., and K. Arunachalam. 2018. “Durability Studies on Fibre Reinforced Self Compacting Concrete with Sustainable Wastes.” Journal of Cleaner Production 174:274–255. https://doi.org/10.1016/j.jclepro.2017.10.270.
- Akbulut, H., and C. Gürer. 2006. “Use of Aggregates Produced from Marble Quarry Waste in Asphalt Pavements.” Building & Environment 42 (5): 1921–1930. https://doi.org/10.1016/j.buildenv.2006.03.012.
- Ali, Y. A. Y., E. H. A. Fahmy, M. N. AbouZeid, Y. B. I. Shaheen, and M. N. A. Mooty. 2020. “Use of Expanded Polystyrene Wastes in Developing Hollow Block Masonry Units, Constr.” Construction and Building Materials 241:118149. https://doi.org/10.1016/j.conbuildmat.2020.118149.
- Alqamish, H. H., and A. K. AlTamimi. 2021. “Development and Evaluation of Nano-Silica Sustainable Concrete.” Applied Science 11:3041. https://doi.org/10.3390/APP11073041.
- An, M., Y. Wang, and Z. Yu. 2019. “Damage Mechanisms of Ultra-High-Performance Concrete Under Freeze–Thaw Cycling in Salt Solution Considering the Effect of Rehydration.” Construction and Building Materials 198:546–552. https://doi.org/10.1016/j.conbuildmat.2018.11.175.
- Bewket, B. M., Y. A. Lemma, and S. R. Getahun. 2022. “Utilization of Basaltic Quarry Dust as a Partial Replacement of Cement for Hollow Concrete Block Production.” International Journal of Concrete Structures and Materials 16 (1): 55. https://doi.org/10.1186/S40069-022-00546-4.
- Fraile-Garcia, E., J. Ferreiro-Cabello, B. Defez, and G. Peris-Fajanes. 2016. “Acoustic Behavior of Hollow Blocks and Bricks Made of Concrete Doped with Waste-Tire Rubber.” Materials 9 (12): 962. https://doi.org/10.3390/ma9120962.
- Gencel, O., C. Ozel, F. Koksal, E. Erdogmus, G. Martínez-Barrera, and W. Brostow. 2012. “Properties of Concrete Paving Blocks Made with Waste Marble.” Journal of Cleaner Production 21 (1): 62–70. https://doi.org/10.1016/j.jclepro.2011.08.023.
- Hong, N., X. Zhe, L. Ying-Lei, L. Li, F. Liu, D. Su, Y. Zhou, Z. Zhang, and J. Lu. 2021. “Feasibility of a Novel Prefabricated Concrete Wall System for Masonry Structures.” Structures 32:1907–1920. https://doi.org/10.1016/J.ISTRUC.2021.04.005.
- Jain, A., R. Gupta, and S. Chaudhary. 2020. “Sustainable Development of Self-Compacting Concrete by Using Granite Waste and Fly Ash.” Construction and Building Materials 262:120516. https://doi.org/10.1016/j.conbuildmat.2020.120516.
- Jiao, Z., Y. Wang, W. Zheng, W. Huang, and X. Zhou. 2018. “Use of Industrial Waste Slag in Alkali-Activated Slag Ceramsite Concrete Hollow Blocks.” Applied Science 8 (12): 2358. https://doi.org/10.3390/app8122358.
- Lasco, J. D., M. Madlangbayan, and M. B. Sundo. 3 2017. “Compressive Strength and Bulk Density of Concrete Hollow Blocks (CHB) with Polypropylene (PP) Pellets as Partial Replacement for Sand.” Civil Engineering Journal 3 (10): 821. https://doi.org/10.28991/cej-030917.
- Li, J., H. Zhou, W. W. Chen, and Z. Chen. 2021. “Mechanical Properties of a New Type Recycled Aggregate Concrete Interlocking Hollow Block Masonry.” Sustainability 13 (2): 745. https://doi.org/10.3390/SU13020745.
- Lijuan, Z., D. Dong, Z. Jun, G. Zhou, and Z. Wang. 2022. “Mixture Design and Mechanical Properties of Recycled Mortar and Fully Recycled Aggregate Concrete Incorporated with Fly Ash.” Materials 15 (22): 8143. https://doi.org/10.3390/MA15228143.
- Liu, C., C. Zhu, G. Bai, Z. Quan, and J. Wu. 2019. “Experimental Investigation on Compressive Properties and Carbon Emission Assessment of Concrete Hollow Block Masonry Incorporating Recycled Concrete Aggregates.” Applied Science 9 (22): 4870. https://doi.org/10.3390/app9224870.
- Menezes, R. R., H. S. Ferreira b, G. A. Neves, H. C. Ferreira, and H. C. Ferreira. 2005. “Use of Granite Sawing Wastes in the Production of Ceramic Bricks and Tiles.” Journal of the European Ceramic Society 25 (7): 1149–1158. https://doi.org/10.1016/j.jeurceramsoc.2004.04.020.
- Meng, T., X. F. Yang, H. D. Wei, R. Meng, and W. Zhou. 2023. “Study of the Relationship Between the Water Binder Ratio and Strength of Mixed Recycled Aggregate Concrete Based on Brick Content.” Construction and Building Materials 394:132148. https://doi.org/10.1016/J.CONBUILDMAT.2023.132148.
- Olofinnade, O. M., J. U. Anwulidiunor, K. E. Ogundipe, and D. A. Ajimalofin. 2023. “Recycling of Periwinkle Shell Waste as Partial Substitute for Sand and Stone Dust in Lightweight Hollow Sandcrete Blocks Towards Environmental Sustainability.” Materials 5 (5): 16051853. https://doi.org/10.3390/ma16051853.
- Ostrowski, K., D. Stefaniuk, Ł. Sadowski, K. Krzywiński, M. Gicala, and M. Różańska. 2020. “Potential Use of Granite Waste Sourced from Rock Processing for the Application as Coarse Aggregate in High-Performance Self-Compacting Concrete.” Construction and Building Materials 238:117794. https://doi.org/10.1016/j.conbuildmat.2019.117794.
- Pawar, A. D. A Critical Study to Assess the Hurdles in Adoption of Sustainable Walling Materials in Construction Industry. International Conference on Sustainable Energy, Environment and Green Technologies, Jaipur, India, March 5-6, 2021. https://doi.org/10.1088/1755-1315/795/1/012007.
- Rajgor, M. B., and J. Pitroda. 2012. “A Study of Utilization Aspect of Stone Waste in Indian Context.Glob.” Global Journal for Research Analysis 2 (1): 50–53. https://doi.org/10.15373/22778160/january2013/67.
- Riaz, M. H., A. Khitab, and S. Ahmed. 2019. “Evaluation of Sustainable Clay Bricks Incorporating Brick Kiln Dust.” Journal of Building Engineering 24:100725. https://doi.org/10.1016/j.jobe.2019.02.017.
- S, A. M., S. I, M. S. Z, and M. Mahgoub. 2021. “Effect of Nano-Silica on the Properties of Concrete and Its Interaction with Slag.” Transportation Research Record: Journal of the Transportation Research Board 2675 (9): 47–55. https://doi.org/10.1177/0361198120943196.
- Taji, I., S. Ghorbani, D. J. Brito, V. W. Y. Tam, S. Sharifi, A. Davoodi, M. Tavakkolizadeh. et al. 2019. “Application of Statistical Analysis to Evaluate the Corrosion Resistance of Steel Rebars Embedded in Concrete with Marble and Granite Waste Dust.” Journal of Cleaner Production 210:837–846. https://doi.org/10.1016/j.jclepro.2018.11.091.
- Torres, P., H. Fernandes, S. Agathopoulos, D. U. Tulyaganov, and J. M. F. Ferreira. 2003. “Incorporation of Granite Cutting Sludge in Industrial Porcelain Tile Formulations.” Journal of the European Ceramic Society 24 (10–11): 3177–3185. https://doi.org/10.1016/j.jeurceramsoc.2003.10.039.
- Vidak, M. V., M. Nevenka, and R. Zagorka. 2022. “Aplitic Granite Waste as Raw Material for the Production of Outdoor Ceramic Floor Tiles.” Materials 15 (9): 3145. https://doi.org/10.3390/MA15093145.
- Vijayalakshmi, M., A. Sekar, and G. G. Prabhu. 2013. “Strength and Durability Properties of Concrete Made with Granite Industry Waste.” Construction and Building Materials 46:1–7. https://doi.org/10.1016/j.conbuildmat.2013.04.018.
- Wang, L., S. Nagarajaiah, W. Shi, and Y. Zhou. 2020. “Study on Adaptive-Passive Eddy Current Pendulum Tuned Mass Damper for Wind-Induced Vibration Control.” The Structural Design of Tall & Special Buildings 29 (15): e1793. https://doi.org/10.1002/tal.1793.
- Wang, L., S. Nagarajaiah, W. Shi, and Y. Zhou. 2022. “Seismic Performance Improvement of Base-Isolated Structures Using a Semi-Active Tuned Mass Damper.” Engineering Structures 271:114963. https://doi.org/10.1016/j.engstruct.2022.114963.
- Wang, L., S. Nagarajaiah, Y. Zhou, and W. Shi. 2023. “Experimental Study on Adaptive-Passive Tuned Mass Damper with Variable Stiffness for Vertical Human-Induced Vibration Control.” Engineering Structures 280:115714. https://doi.org/10.1016/j.engstruct.2023.115714.
- Wang, L., W. Shi, X. Li, Q. Zhang, and Y. Zhou. 2019. “An Adaptive-Passive Retuning Device for a Pendulum Tuned Mass Damper Considering Mass Uncertainty and Optimum Frequency.” Structural Control & Health Monitoring 26 (7): e2377. https://doi.org/10.1002/stc.2377.
- Wang, L., W. Shi, Y. Zhang,and Y. Zhou. 2020. “Q.Study on Adaptive-Passive Multiple Tuned Mass Damper with Variable Mass for a Large-Span Floor Structure.” Engineering Structures 209:110010. https://doi.org/10.1016/j.engstruct.2019.110010.
- Wang, L., W. Shi, and Y. Zhou. 2019. “Study on Self-Adjustable Variable Pendulum Tuned Mass Damper.Tall. Spec.” The Structural Design of Tall & Special Buildings 28 (1): e1561. https://doi.org/10.1002/tal.1561.
- Wang, L., W. Shi, Y. Zhou, and Zhang. 2020. “Q.Semi-Active Eddy Current Pendulum Tuned Mass Damper with Variable Frequency and Damping.” Smart Structures and Systems 25:65–80. https://doi.org/10.12989/sss.2020.25.1.065.
- Wang, L., L. Wang, and W. Shi. 2021. “Two-Dimensional Air Spring Based Semi-Active TMD for Vertical and Lateral Walking and Wind-Induced Vibration Control.” Structural Engineering and Mechanics 80:377–390. https://doi.org/10.12989/sem.2021.80.4.377.
- Wang, L., L. Wang, and Y. Zhou. 2022. “Adaptive-Passive Tuned Mass Damper for Structural Aseismic Protection Including Soil–Structure Interaction.” Soil Dynamics and Earthquake Engineering 158:107298. https://doi.org/10.1016/j.soildyn.2022.107298.
- Wang, X., and K. Park. 2017. “Analysis of the Compressive Strength Development of Concrete Considering the Interactions Between Hydration and Drying.” Cement and Concrete Research 102:1–15. https://doi.org/10.1016/j.cemconres.2017.08.010.
- Wu, J., G. L. Bai, P. Wang, and Y. Liu. 2018. “Mechanical Properties of a New Type of Block Made from Shale and Coal Gangue.” Construction and Building Materials 190:190 796–804. https://doi.org/10.1016/j.conbuildmat.2018.09.130.
- Xie, J. H., J. B. Zhao, J. J. Wang, P. Y. Huang, and J. F. Liu. 2021. “Investigation of the High-Temperature Resistance of Sludge Ceramsite Concrete with Recycled Fine Aggregates and GGBS and Its Application in Hollow Blocks.” Journal of Building Engineering 34:101954. https://doi.org/10.1016/j.jobe.2020.101954.
- Zhang, X. H., Z. J. Song, and Y. G. Ding. 2022. “Predicting Compressive Strength of Cement-Based Materials Containing Water-Absorbent Polymers Considering the Internal-Curing Region.” Construction and Building Materials 360:129594. https://doi.org/10.1016/J.CONBUILDMAT.2022.129594.
- Zheng, W., and F. Guangxiu. Nov 23-25, 2018. “Experimental Study on Compressive Strength of New Type Volcanic Slag Lightweight Aggregate Concrete and Its Hollow Block.Iop.” Conference Series: Earth and Environmental Science Qingdao China 189 (6): 032063. https://doi.org/10.1088/1755-1315/189/3/032063.