ABSTRACT
Plastic waste is considered a global environmental disaster due to its extensive negative impacts on ecosystems, human health, and the overall well-being of the planet. Approximately 91% of plastic waste, including multi-layer plastic (MLP), is yet to be recycled and ends up in the landfill, incinerated or in the environment. MLP can be used as a construction material since it exhibits the necessary characteristics. This study evaluated the mechanical properties of multilayer plastic (MLP) composite blocks as a wall material. Two types of composite plastic blocks were tested: one made entirely of MLP and the other composed of MLP (80%) and mixed material (20%). The mixed material included sawdust powder, stone dust, and cement mixed with sand. Tests were conducted to measure the compressive strength, water absorption, and fire resistance of the blocks. The MLP composite block mixed with cement and sand in a ratio of 1:5 exhibited the highest compressive strength at 9.43 MPa, while the 100% MLP block had the lowest compressive strength at 2.73 MPa. The MLP composite block mixed with sawdust showed the highest water absorption at 11.35%, while the 100% MLP block had the lowest water absorption at 0.96%. The 100% MLP composite block ignited and melted within 2 minutes during the fire test, while the MLP composite block mixed with cement and sand did not ignite during 10 minutes of burning. It was concluded that the composite blocks containing 100% MLP do not meet the requirements for wall construction. This study also found that 80% MLP mixed with 20% cement and sand in a ratio of 1:5 exhibits the best mechanical properties among all blocks. MLP content with a considerable portion of each plastic composite block product will help reduce plastic waste in the environment.
1. Introduction
Indonesia generates approximately 7.8 million tons of plastic waste annually. 4.9 million tons of plastic waste is mismanaged––i.e., uncollected, disposed of in open dumpsites or leaked from improperly managed landfills (Ministry of Environment and Forestry Ministry of Environment and Forestry Republic of Indonesia Citation2020). Plastic can last hundreds to thousands of years, but plastic tends to persist longer in deep seas and non-surface polar environments (Barnes et al. Citation2009). The most common type of plastic waste on earth is present in the form of plastic packaging. Plastic packaging is generally made from thermoplastic resin, namely Polyethylene Terephthalate (PET) (known as type 1); High-Density Polyethylene (HDPE) (known as type 2); Polyvinyl Chloride (PVC) (known as type 3); Low-Density Polyethylene (LDPE) (known as type 4); Polypropylene (PP) (known as type 5); Polystyrene (PS) (known as type 6); and others (known as type 7). The last category includes multi-layered plastic (MLP), which is generally not collected for recycling (Hahladakis and Iacovidou Citation2018).Improper plastic use and poor waste management cause significant environmental and human health problems. Therefore, reducing plastic production and usage and ensuring proper plastic waste management is essential.
Recycling is one of the best strategies recommended for managing plastic waste (d’Ambrières, Citation2019; Ferdous et al. Citation2021; Huysman et al. Citation2015; Kumar et al. Citation2021) . Recycling plastic waste can significantly reduce the amount of plastic waste generated, create job opportunities, and boost the economy. Research has shown that recycling 10,000 tons of waste can create 9.2 jobs, compared to only 2.8 if the waste is disposed of in a landfill (Ferdous et al., Citation2021). Using recycled plastic waste for construction will significantly improve environmental sustainability. This process will provide a reliable source of materials (Chauhan et al. Citation2021; Naderi Kalali et al. Citation2023; Ogundairo et al. Citation2021). Due to rapid development, there has been an increasing demand for bricks, and the need to preserve the environment has driven various waste materials to replace cement, clay, or sand in brickmaking, including plastic waste. Plastic waste pollution poses serious environmental problems. At the same time, the cement industry is one of the largest sources of CO2 emissions, posing other ecological challenges. This makes plastic sand bricks an attractive alternative to concrete blocks and conventional bricks. Currently, research and practice on the use of plastic waste for brickmaking have been rapidly progressing. Generally, the types of plastic used to make certain building materials and infrastructures are HDPE, PET, LDPE, and PP, which are mixed with various materials and compositions such as sand, cement, sawdust, rice husk, fly ash, and stone dust (Kanchidurai et al. Citation2018; Sahani et al. Citation2022). Plastic brick products are made in various ways, including shredding or melting plastic waste, burning it to produce plastic dust, which is then mixed with other materials, or simply filling plastic beverage bottles with plastic waste or sand and making eco-brick (Dadzie et al. Citation2020; Edike et al. Citation2022; Haque & Islam, Citation2021; Idrees et al. Citation2023). Studies on the use of various types of plastic waste for conventional brickmaking have revealed that plastic bricks perform better than conventional bricks. These studies recommend using plastic bricks as a sustainable construction material (Adiyanto, Mohamad, and Abd Razak Citation2022; Lamba et al. Citation2022; Mohan, Jayanarayanan, and Mini Citation2021).
Despite the abovementioned research works, there have been only few studies that have utilised multi-layered plastic (MLP). Multi-layered plastic is a type of plastic composed of several layers of different materials, which form flexible packaging such as bags, pouches, and other flexible products, or rigid packaging such as cups, containers, and other rigid plastic sheets (Wagner Citation2016)
Additionally, the recycling process of multilayered plastic requires more complex and expensive technology and techniques than those of other plastic types (Huysman et al. Citation2015, Mulakkal et al. Citation2021, Soares et al. Citation2022). Therefore, several facilities that perform plastic waste treatment do not accept these types of plastic waste, leading to accumulation in landfills or the environment. The durable, lightweight, and elastic nature of MLP can be utilised to make stronger, lighter, and more affordable bricks. Currently, several efforts have been made at the grassroots level to recycle MLP plastic waste for making bricks or paving blocks. However, some publications must provide complete data on the composition of the materials used and the extent to which the resulting brick products meet the requirements for use as wall construction materials. One example of an MLP plastic brick product made in Indonesia that has been tested and sold in the market is Rebrick (Rebricks.id Citation2022). The percentage of MLP plastic waste used in Rebrick bricks is only 20%, with the rest of the material comprising a mixture of cement and sand. To significantly reduce MLP plastic waste, the percentage of MLP plastic waste used in bricks should be higher than the percentage of the mixture of other materials. This study aims to determine the mechanical properties of bricks made of MLP plastic mixed with other materials at a ratio of 80:20. The test results will be compared with the mechanical properties of plastic bricks made of 100% MLP to determine the amount of MLP plastic that can be used in an alternative brick material, in addition to PET plastic, HDPE, and other types that have been widely studied previously. Considering that many similar studies use other types of plastic, such as PET or LDPE, this research has the novelty of using MLP waste as the main raw material for the plastic bricks. In addition, the use of MLP for plastic bricks in a much larger percentage compared to existing products can contribute to a significant reduction in the amount of MLP waste. Widely studied previously. Considering that many similar studies use other types of plastic, such as PET or LDPE, this research has the novelty of using MLP waste as the main raw material for the plastic bricks. In addition, the use of MLP for plastic bricks in a much larger percentage compared to existing products can contribute to a significant reduction in the amount of MLP waste.
2. Method
This study uses a research and development (R&D) approach; the usage of this approach provides a hope that new products can be found and tested that are useful for human life, institutions, and society (Weyant, Citation2022). The sample in this study is an interlocking plastic composites block measuring 60 cm in length, 10 cm in width, and 20 cm in height, which is inspired by a similar interlocking brick product that is also made of a plastics mixture from Conceptos Plasticos, Columbia (Conceptos Plasticos Citation2022). The interlocking plastic composite blocks are made from multi-layer plastic (MLP) waste that is shredded and melted with a mixed material. In this study, four types of plastic composite block samples were used. The first type is made from 100% MLP, and the other three types were made from 80% MLP and 20% mixed material, consisting of sawdust, stone dust, cement, and sand (1:5) (). The proportions used in each of the three samples are shown in . in each of the three samples are shown in .
Table 1. The proportion in each of the samples.
The plastic composite samples were manually prepared in Padalarang, West Bandung Regency. The instruments used for the fabrication of the plastic composites were a shredder machine to shred multilayer plastics into tiny particles, a griddle, and a stove to melt the multilayer plastic particles and mould to melt multilayer plastics. The sample-making is performed according to the step-by-step method described below. This method is also illustrated in the flowchart below ().
The multilayer plastics were separated from the other materials collected in the Sukamaju Waste Bank, Padalarang, West Bandung Regency.
After being separated, the multilayer plastic was shredded into some tiny particles.
The tiny particles from multilayer plastic wastes were melted in a griddle with the heat from the stove. The shredded multilayer plastics were mixed until melted. The product looks like a paste.
After the multilayer plastic paste is formed, it is moulded with a mould made of an iron plate into a desired shape. The multilayer plastic paste must be wholly set for at least 15 - 30 minutes to be completely moulded.
After waiting for the paste to be moulded, the mould can be dismantled, and the plastic composite block is ready to be smoothed on the surface with sandpaper or a grinding machine. If the desired results are obtained, the composite plastic blocks can be directly used for construction by connecting to other composite plastic blocks, such as assembling Lego toys with interlocking shapes.
Figure 2. Step-by-step of interlocking plastic composite block making.
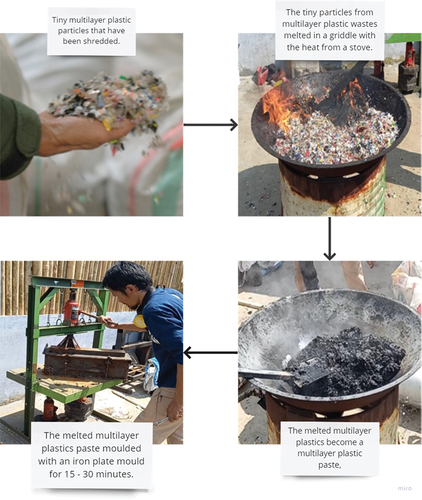
The samples were tested to determine their mechanical properties. An analysis was conducted to determine the factors that influence the mechanical properties of each composite plastic block. Mechanical property testing refers to SNI 15–2094–2000 related to the quality standards of solid bricks in Indonesia (Standar Nasional Indonesia Citation2000), which include compressive strength and water absorption capacity. The testing was conducted in the laboratory with testing procedures and equipment used according to ASTM C109 standards for compressive strength testing on cube specimens of size 50 × 50 mm (ASTM International Citation2020) and SNI 03–6433–2016 for testing of water absorption capacity (Standar Nasional Indonesia Citation2016). Compressive strength refers to the material’s ability to withstand compressive loads without breaking or changing shape. In the case of composite plastic blocks, the compressive strength represents the pressure that can be endured by the composite plastic blocks before cracking or breaking. For compressive strength testing, cube-shaped samples of plastic composite blocks measuring 10 cm x 10 cm x 10 cm were made and then tested for compression using a Universal Testing Machine (UTM) with a capacity of 200 kN and loading rate of 1 kN/s (). and loading rate of 1 kN/s ().
Figure 3. The compression test process uses a Universal testing machine (UTM).
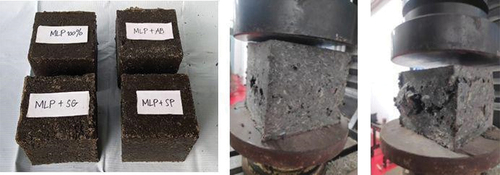
illustrates the essential compression test process conducted using a Universal Testing Machine (UTM). The UTM applies controlled vertical forces to the multilayer plastic (MLP) composite blocks in order to evaluate their compressive strength. The process involves gradually increasing the load on the block until failure occurs, allowing for the measurement of the maximum force sustained by the block before it collapses. This test assesses the structural integrity and load-bearing capacity of the composite blocks, providing valuable insights into their suitability as construction materials. The data obtained from this test informs decisions regarding material selection and design for sustainable architectural applications. The use of a UTM ensures accurate and standardised testing conditions, facilitating the consistent evaluation of different composite block formulations and their mechanical properties.
Water absorption capacity refers to a material’s ability to absorb water when immersed in it and represents its water-holding capacity. The water absorption capacity is the ratio of the weight of water absorbed by a material in a saturated state to the weight of the dry material (Li et al. Citation2011). This test refers to SNI 15–2094–2000 on the quality standards of solid bricks in Indonesia, in which it is stated that water absorption should not exceed 20% (Standar Nasional Indonesia Citation2000).
In addition to the testing of mechanical properties, a non-standard fire test was carried out with a blowtorch. This test aims to detect a sample that exhibits the property of burning without melting rapidly and igniting. Through this manner, one can identify the type of material and mixture proportion having the best fire resistance that can be used in composite plastic blocks. The fire test conducted in this study is only a preliminary test where the results will be used to determine the type of sample that can be developed as a wall component in subsequent research works. The test was conducted by exposing the sample to a torch flame at a temperature of 800–1300℃ by maintaining 10 cm for 10 minutes. Each sample was burned for 10 minutes. Intervals of 2 minutes were used for recording the physical changes in the sample during burning and for allowing the plastic composite surface to ignite (). An illustration of the preliminary fire test configuration process using a blowtorch can be seen in .
3. Result
The results of the compressive strength test conducted on the multilayer plastic composites are listed in .
Table 2. The result of the compressive strength test.
Based on the results of the compressive strength test, it is revealed that the composite plastic blocks made from MLP mixed with cement and sand exhibit the highest compressive strength. In contrast, it is observed that the composite plastic blocks made from only MLP have the lowest compressive strength. The MLP + AB and MLP + SG composite plastic blocks have higher compressive strengths than the plastic composite block made of 100% MLP. The plastic composite blocks made of 100% MLP, MLP + SG, and MLP + AB have lower compressive strengths than the plastic composite block made of MLP + SP.
Based on the results of the absorption testing in , it is observed that the MLP + CS composite plastic blocks have the lowest average absorption capacity. In contrast, the MLP + SD composite plastic blocks, a mixture of MLP and sawdust, have the highest absorption capacity. Plastic composite blocks of 100% MLP have a slightly higher absorption capacity than the MLP + CS composite plastic blocks, which have a higher absorption capacity than composite plastic blocks of MLP + SA. However, the average absorption capacities of the four types of plastic composite blocks tested are lower than the standard for maximum absorption capacity of bricks according to SNI 15–2094–2000 related to the quality standards of solid bricks in Indonesia, which is 20%.
presents a series of visualisations depicting the behaviour of various plastic composite block samples when exposed to a blowtorch flame at 8-minute intervals. From left to right, the samples include: 100% MLP (Multilayer Plastic), MLP+SD (MLP with Sawdust), MLP+SA (MLP with Stone Ash), and MLP+SP (MLP with Sand and Cement). The sequence of images captures the evolving response of each sample as it interacts with the applied heat.
Figure 6. The visualisation of plastic composite block samples while being fired by the blowtorch at eight minutes time intervals. Left to right: 100% MLP, MLP+ SG, MLP+ AB, and MLP + SP.
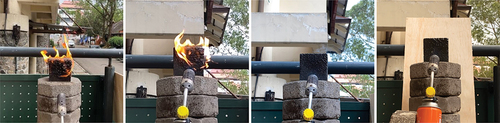
provides a visual representation of the composite plastic block samples after undergoing blowtorch exposure. The images reveal the effects of the fire test on each sample’s physical integrity and appearance, offering valuable insights into their fire resistance and structural performance. The composite plastic blocks are arranged from left to right, corresponding to the following formulations: 100% MLP (Multilayer Plastic), MLP+SD (MLP with Sawdust), MLP+SA (MLP with Stone Ash), and MLP+SP (MLP with Sand and Cement). Upon examination, it becomes evident that each formulation responds differently to fire exposure.
Figure 7. The visualisation of composite plastic block samples after being fired by the blowtorch.
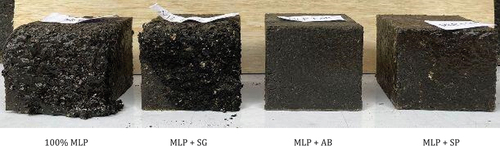
Based on the results of the simple fire resistance test in , it is observed that the MLP + SA plastic composite blocks, which contain multilayer plastic mixed with stone dust, have the highest fire resistance. Up to 10 minutes of burning, this type of composite plastic block did not undergo any physical changes and did not burn. Meanwhile, although not ignited, the MLP + CS plastic composite blocks, which contain multilayer plastic mixed with cement and sand, had a slightly melted surface. The plastic composite block with 100% MLP had the lowest fire resistance, as this block melted and produced flames within a range of 6 minutes, which is the shortest time taken as compared to the times taken by the other types of bricks. The MLP + SG plastic composite blocks, which contain multilayer plastic mixed with sawdust, also have a low level of fire resistance. However, this resistance is slightly higher than that of the plastic composite blocks with 100% MLP. This is because the flame was observed only after 8 minutes, and the flame only partially melted the surface of the plastic composite blocks. The detailed physical changes on both plastic composite samples during fire testing can be seen in .
Table 3. The result of the absorption test.
Table 4. The result of fire testing.
4. Discussion
Based on the results of the compressive strength tests, it is observed that the composite plastic blocks made of 80% MLP mixed with other materials have a higher compressive strength than the plastic blocks made of 100% MLP. This suggests that MLP should be combined with other materials to achieve the maximum compressive strength for plastic composite blocks. This is in line with the results of previous studies, which revealed that increasing the proportion of plastic will decrease the compressive strength of the composite plastic block (Akinyele and Oyelakin Citation2021; Al-Sinan and Bubshait Citation2022; Thorneycroft et al. Citation2018). This study found that cement and sand are the most suitable materials that can be mixed with MLP plastic with a proportion of 80% MLP and 20% cement and sand (1:5 ratio). This indicates that the presence of cement and sand will significantly affect the strength of composite plastic blocks even though they are present in tiny amounts. However, adding cement and sand with a much more significant portion of sand as compared to the MLP content is not recommended because excessive sand content will reduce the strength of the plastic block. The ideal ratio between plastic and sand is 30:70 or 1:4 (Aneke and Shabangu Citation2021; Lamba et al. Citation2022).
The addition of sawdust and brick dust can increase the strength of MLP plastic bricks, although their compressive strength is lower than that of the MLP bricks mixed with cement and sand. In this study, the brick dust that was used as a mixture in the plastic brick was waste produced from mountain stone mining, and the amount used was 20% of brick dust and 80% of MLP. However, to obtain optimum results, the proportion of brick dust to plastic should be 1:2) (Akinyele and Oyelakin Citation2021; Arnandha et al., Citation2020; Haque & Islam, Citation2021) Moreover, the addition of sawdust also has a positive effect on the compressive strength of the bricks. Sawdust can provide additional strength by increasing the porosity of the bricks and reducing their weight, which can affect their mechanical properties (Alabduljabbar et al. Citation2021; Batool et al. Citation2021). The combination of plastic brick materials in this study, including MLP, brick dust, cement, sand, and organic materials such as sawdust, serves as a filler and strengthens, helping to fill the voids in the bricks. Strengthens, helping to fill the voids in the bricks.
The highest water absorption rate was observed in MLP + SG. This observation can be attributed to the fact that sawdust is a dry organic material that absorbs water, thereby increasing the porosity of the composite plastic blocks. The consistent high water absorption capacity of the plastic composite blocks containing sawdust has been demonstrated in studies using other types of plastic besides MLP, such as Wood Plastic Panels made from PET plastic and sawdust and similar studies that incorporate sawdust (Clement et al. Citation2019; Mohan et al. Citation2021; Turgut and Algin Citation2007). The lowest water absorption rate was observed in MLP +SP. Cement and sand are materials with low water absorption capacity, and this property affects the water absorption rate of the plastic composite blocks containing either or both these materials (Al-Sinan and Bubshait Citation2022; Sahani et al. Citation2022). The presence of voids in plastic bricks with 100% MLP causes water absorption. Cement and sand fill these voids and create strong bonds between the brick composites, making the resulting brick more water-resistant (Edike, Ameh, and Dada Citation2023; Ozcelik & Ozguven, Citation2014). Generally, the average water absorption capacity of the four types of plastic composite blocks tested is below the standard water absorption capacity of clay bricks, which is having a maximum value of 20%. Therefore, the tested plastic composite blocks can last long. Based on the combustion tests, it is observed that composite plastic blocks with 100% MLP would burn within 90 seconds, while MLP plastic composite blocks mixed with sawdust ignite within 6 minutes. MLP plastic composite blocks mixed with cement and sand and those mixed with stone dust do not ignite after being burned for 10 minutes. This observation indicates that composite plastic blocks with 100% MLP are highly hazardous when burned as they produce flames quickly.
Based on the physical and mechanical properties shown in the results of this study, plastic composite blocks have excellent potential to be developed as components for strengthening building structures against shocks caused by earthquakes. In recent years, many vibration controls, such as the Tuned Mass Damper (TMD), have been proposed (Koutsoloukas, Nikitas, and Aristidou Citation2022). Dampers are large concrete beams or steel bodies installed in skyscrapers or other structures. Numerous engineering practices and experimental tests have proven that the TMD system is effective in protecting structures from major damage during earthquakes. However, TMDs have some inherent limitations, such as a narrow effective frequency range, poor durability, and deterioration over time. Hence, some researchers have developed new passive control devices to overcome the shortcomings of conventional TMD systems (Lu et al. Citation2022; Wang et al. Citation2022, Citation2023; Wang, Zhou, and Shi Citation2023). In the future study, the structural control device and energy dissipation damper will be investigated for plastic composite blocks made from MLP mixed with various materials.
In general, the higher proportion of multilayer plastic waste in the plastic composite blocks mixture did not decrease the capacity of the plastic composite blocks. It still fulfilled the mechanical property requirements as a wall construction material. However, plastic composite blocks made entirely of multilayer plastic waste have limitations compared to plastic composite blocks mixed with other materials. Bricks made of 100% MLP tend to be hollow in the middle, which makes them risky to be used as a wall material since they are highly flammable. For resolving this, in addition to adding proven fire-resistant materials to multilayer composite plastic blocks (MLP), other measures can be taken, such as installing fire-resistant coverings.
5. Conclusion
The mechanical properties of plastic composite blocks made from multi-layer plastic (MLP) mixed with various materials and compositions have been tested to determine the amount of MLP waste that can be utilised as a building material. This study found that plastic composite blocks using MLP are suitable for wall-building materials when they are prepared with a mixture of 20% of cement and sand in a ratio of 1:5, which significantly increase the compressive strength and fire resistance of the plastic composite block. This also implies that MLP can be utilised as a building material in addition to other plastic types that have been widely studied previously. This research work has yet to fully assess the potential of MLP waste as a building material. To address the research gap in case of MLP waste, it is advisable to further utilise various combinations of MLP with other materials, to develop the potential of MLP as a building material. There are several potential avenues for future research in this area, such as optimisation of formulations, long-term durability, innovative additives, structural application, life cycle assessment, regulatory and standardisation, local material sourcing, comparative studies, architectural design, and social acceptance and perception.
Acknowledgements
We would like to thank ITB for the financial support through the Flagship Research Program that has made this study possible. Further acknowledgement is also given to Toni Permana as the coordinator of Sukamaju Sejahtera Waste Bank in West Bandung Regency, where the research samples were produced.
Disclosure statement
No potential conflict of interest was reported by the author(s).
Additional information
Funding
Notes on contributors
Lily Tambunan
Lily Tambunan is a researcher and lecturer at the School of Architecture, Planning, and Policy Development, Institute Technology Bandung. Her research focuses on disaster resiliency topics in architectural design including fire safety and environmentally friendly materials.
Chibhatul Mufrida
Chibhatul Mufrida is a former postgraduate student at the School of Architecture, Planning, and Policy Development, Institute Technology Bandung.
Dewi Larasati
Dewi Larasati is an Associate Professor at the Department of Architecture, Institute Technology Bandung. Her research focuses on building technology, green building, sustainable design and construction, and sustainable procurement.
References
- Adiyanto, O., E. Mohamad, and J. Abd Razak. 2022. “Systematic Review of Plastic Waste as Eco-Friendly Aggregate for Sustainable Construction.” International Journal of Sustainable Construction Engineering and Technology 13 (2): 243–257. https://doi.org/10.30880/ijscet.2022.13.02.022.
- Akinyele, J. O., and S. K. Oyelakin. 2021. “Assessment of the Properties of Bricks Made from Stone Dust and Molten Plastic for Building and Pedestrian Pavement.” International Journal of Pavement Research and Technology 14 (6): 771–777. https://doi.org/10.1007/s42947-020-1268-5.
- Alabduljabbar, H., O. Benjeddou, C. Soussi, M. A. Khadimallah, and R. Alyousef. 2021. “Effects of Incorporating Wood Sawdust on the Firing Program and the Physical and Mechanical Properties of Fired Clay Bricks.” Journal of Building Engineering 35: 102106. https://doi.org/10.1016/j.jobe.2020.102106.
- Al-Sinan, M. A., and A. A. Bubshait. 2022. “Using Plastic Sand as a Construction Material Toward a Circular Economy: A Review.” Sustainability 14 (11): 6446. https://doi.org/10.3390/su14116446.
- Aneke, F. I., and C. Shabangu. 2021. “Green-Efficient Masonry Bricks Produced from Scrap Plastic Waste and Foundry Sand.” Case Studies in Construction Materials 14: e00515. https://doi.org/10.1016/J.CSCM.2021.E00515.
- Arnandha, Y., A. Rakhmawati, and H. H. Ali. 2020. “Study of Utilizations of Recycled LDPE Plastic and Stone Ash Waste from Remaining Split Stone Fragments for Block Paving Application.” Journal of Physics. Conference Series 1625 (1): 012017. https://doi.org/10.1088/1742-6596/1625/1/012017.
- ASTM International. 2020. Standard Test Method for Compressive Strength of Hydraulic Cement Mortars (Using 2-In. or [50 Mm] Cube Specimens) (Patent C109/C109M−20b). ASTM Intenational. https://www.astm.org/.
- Barnes, D. K. A., F. Galgani, R. C. Thompson, and M. Barlaz. 2009. “Accumulation and Fragmentation of Plastic Debris in Global Environments.” Philosophical Transactions of the Royal Society B: Biological Sciences 364 (1526): 1985–1998. https://doi.org/10.1098/rstb.2008.0205.
- Batool, F., K. Islam, C. Cakiroglu, and A. Shahriar. 2021. “Effectiveness of Wood Waste Sawdust to Produce Medium- to Low-Strength Concrete Materials.” Journal of Building Engineering 44: 103237. https://doi.org/10.1016/J.JOBE.2021.103237.
- Chauhan, S. S., J. K. Singh, H. Singh, S. Mavi, V. Singh, and M. I. Khan. 2021. “An Overview on Recycling Plastic Wastes in Bricks.” Materials Today: Proceedings 47: 4067–4073. https://doi.org/10.1016/j.matpr.2021.05.697.
- Clement, M., P. Krishnakumar, M. Athipathy, and M. Vijayakumar. 2019. “An Experimental Study on Brick Manufactured Using M-Sand, Sawdust, and Recycled Plastic.” International Journal of Advance Research in Engineering and Technology 10: 171–178 https://iaeme.com/Home/article_id/IJARET_10_04_021.
- Conceptos Plasticos. 2022. From Wate to Shelter. Conceptos Plasticos. https://conceptosplasticos.com/content/brick-and-blocks.html.
- Dadzie, D. K., A. K. Kaliluthin, and D. R. Kumar. 2020. “Exploration of Waste Plastic Bottles Use in Construction.” Civil Engineering Journal 6 (11): 2262–2272. https://doi.org/10.28991/cej-2020-03091616.
- d’Ambrières, W. 2019. “Plastics Recycling Worldwide: Current Overview and Desirable Changes. Field Actions Science Reports.” The Journal of Field Actions 19: 12–21.
- Edike, U. E., O. Aina, and A. B. Adeoye. 2022. “Adoption of Eco-Bricks for Housing: The Case of Yelwa, Nigeria.” African Journal of Science, Technology, Innovation & Development 14 (3): 801–812. https://doi.org/10.1080/20421338.2021.1903735.
- Edike, U. E., O. J. Ameh, and M. O. Dada. 2023. “Performance of Polymer Bricks Produced with Plastic Waste.” Innovative Infrastructure Solutions 8 (1): 1–14. https://doi.org/10.1007/s41062-022-01021-5.
- Ferdous, W., A. Manalo, R. Siddique, P. Mendis, Y. Zhuge, H. S. Wong, W. Lokuge, T. Aravinthan, and P. Schubel. 2021. “Recycling of Landfill Wastes (Tyres, Plastics and Glass) in Construction–A Review on Global Waste Generation, Performance, Application and Future Opportunities.” Resources Conservation & Recycling 173: 105745. https://doi.org/10.1016/j.resconrec.2021.105745.
- Hahladakis, J. N., and E. Iacovidou. 2018. “Closing the Loop on Plastic Packaging Materials: What is Quality and How Does It Affect Their Circularity?” Science of the Total Environment 630: 1394–1400. https://doi.org/10.1016/J.SCITOTENV.2018.02.330.
- Haque, M. S., and S. Islam. 2021. “Effectiveness of Waste Plastic Bottles as Construction Material in Rohingya Displacement Camps.” Cleaner Engineering and Technology 3: 100110. https://doi.org/10.1016/j.clet.2021.100110.
- Huysman, S., S. Debaveye, T. Schaubroeck, S. De Meester, F. Ardente, F. Mathieux, and J. Dewulf. 2015. “The Recyclability Benefit Rate of Closed-Loop and Open-Loop Systems: A Case Study on Plastic Recycling in Flanders.” Resources, Conservation and Recycling 101: 53–60. https://doi.org/10.1016/j.resconrec.2015.05.014.
- Idrees, M., A. Akbar, F. Saeed, M. Gull, and S. M. Eldin. 2023. “Sustainable Production of Low-Shrinkage Fired Clay Bricks by Utilizing Waste Plastic Dust.” Alexandria Engineering Journal 68: 405–416. https://doi.org/10.1016/j.aej.2023.01.040.
- Kanchidurai, D., K. S. R. Mohan, S. Vivek, M. Sivateja, and V. Ravindhirran. 2018. “Comparison of Effectiveness of Fly Ash Bricks with Addition of Plastic Waste.” International Journal of Civil Engineering and Technology (IJCIET) 9 (3): 914–919.
- Koutsoloukas, L., N. Nikitas, and P. Aristidou. 2022. “Passive, Semi-Active, Active and Hybrid Mass Dampers: A Literature Review with Associated Applications on Building-Like Structures.” Developments in the Built Environment 12: 100094. https://doi.org/10.1016/J.DIBE.2022.100094.
- Kumar, R., A. Verma, A. Shome, R. Sinha, S. Sinha, P. K. Jha, and R. Kumar. (2021). Impacts of Plastic Pollution on Ecosystem Services, Sustainable Development Goals, and Need to Focus on Circular Economy and Policy Interventions. In Sustainability 13 (17). https://doi.org/10.3390/su13179963
- Lamba, P., D. P. Kaur, S. Raj, and J. Sorout. 2022. “Recycling/Reuse of Plastic Waste as Construction Material for Sustainable Development: A Review.” Environmental Science and Pollution Research 29 (57): 86156–86179. https://doi.org/10.1007/s11356-021-16980-y.
- Li, Y., S. Ren, Y. Zhou, and H. Liu. 2011. Building Decorative Materials. edited by Y. Li & S. Ren. 1st ed. Vol. 1. Woodhead Publishing. https://www.sciencedirect.com/book/9780857092571/building-decorative-materials#book-description.
- Lu, Z., X. Liu, N. Ma, and M. Zhou. 2022. “Multi-Objective Optimization and Seismic Performance Verification of Multiple Tuned Impact Dampers for Nonlinear Benchmark Building.” Structures 41: 1672–1686. https://doi.org/10.1016/J.ISTRUC.2022.05.101.
- Ministry of Environment and Forestry Ministry of Environment and Forestry Republic of Indonesia. 2020. National Plastic Waste Reduction Strategic Actions for Indonesia, Republic of Indonesia. https://wedocs.unep.org/bitstream/handle/20.500.11822/32898/NPWRSI.pdf?sequence=1&isAllowed=y.
- Mohan, H. T., K. Jayanarayanan, and K. M. Mini. 2021. “Recent Trends in Utilization of Plastics Waste Composites as Construction Materials.” Construction and Building Materials 271: 121520. https://doi.org/10.1016/j.conbuildmat.2020.121520.
- Mohan, H. T., F. Whitaker, R. Mini, K. M. Mohan, and K. M. Mini. 2021. “Performance Assessment of Recycled LDPE with Sand Fillers.” Materials Today: Proceedings 42: 1526–1530. https://doi.org/10.1016/j.matpr.2021.02.285.
- Mulakkal, M. C., A. C. Castillo, A. C. Taylor, B. R. K. Blackman, D. S. Balint, S. Pimenta, and M. N. Charalambides. 2021. “Advancing Mechanical Recycling of Multilayer Plastics Through Finite Element Modelling and Environmental Policy.” Resources, Conservation and Recycling 166: 105371. https://doi.org/10.1016/j.resconrec.2020.105371.
- Naderi Kalali, E., S. Lotfian, M. Entezar Shabestari, S. Khayatzadeh, C. Zhao, and H. Yazdani Nezhad. 2023. “A Critical Review of the Current Progress of Plastic Waste Recycling Technology in Structural Materials.” Current Opinion in Green and Sustainable Chemistry 40: 100763. https://doi.org/10.1016/J.COGSC.2023.100763.
- Ogundairo, T. O., D. O. Olukanni, I. I. Akinwumi, and D. D. Adegoke. 2021. “A Review on Plastic Waste as Sustainable Resource in Civil Engineering Applications.” IOP Conference Series: Materials Science & Engineering 1036 (1): 012019. https://doi.org/10.1088/1757-899X/1036/1/012019
- Ozcelik, Y., and A. Ozguven. (2014). “Water Absorption and Drying Features of Different Natural Building Stones.” Construction and Building Materials 63: 257–270. https://doi.org/10.1016/j.conbuildmat.2014.04.030.
- Rebricks.id. 2022. Eco Building Materials - Rebricks. https://rebricks.id/.
- Sahani, K., B. R. Joshi, K. Khatri, A. T. Magar, S. Chapagain, N. Karmacharya, and P. Smarzewski. 2022. “Mechanical Properties of Plastic Sand Brick Containing Plastic Waste.” Advances in Civil Engineering 2022: 1–10. https://doi.org/10.1155/2022/8305670.
- Soares, C. T. D. M., M. Ek, E. Östmark, M. Gällstedt, and S. Karlsson. 2022. “Recycling of Multi-Material Multilayer Plastic Packaging: Current Trends and Future Scenarios.” Resources, Conservation and Recycling 176: 105905. https://doi.org/10.1016/j.resconrec.2021.105905.
- Standar Nasional Indonesia. 2000. SNI-15-2094-2000 Bata merah pejal untuk pasangan dinding (Patent SNI 15-2094-2000). Badan Standardisasi Nasional (BSN). https://pesta.bsn.go.id/produk/detail/2449-sni15-2094-2000.
- Standar Nasional Indonesia. 2016. Metode uji densitas, penyerapan, dan rongga dalam beton keras (ASTM C642 - 13, MOD) (Patent SNI 6433: 2016). Badan Standardisasi Nasional (BSN). https://pesta.bsn.go.id/produk/detail/10956-sni64332016.
- Thorneycroft, J., J. Orr, P. Savoikar, and R. J. Ball. 2018. “Performance of Structural Concrete with Recycled Plastic Waste as a Partial Replacement for Sand.” Construction and Building Materials 161: 63–69. https://doi.org/10.1016/J.CONBUILDMAT.2017.11.127.
- Turgut, P., and H. M. Algin. 2007. “Limestone Dust and Wood Sawdust as Brick Material.” Building and Environment 42 (9): 3399–3403. https://doi.org/10.1016/j.buildenv.2006.08.012.
- Wagner, J. R., Jr. 2016. Multilayer Flexible Packaging. 2nd ed. William Andrew. https://doi.org/10.1016/C2014-0-02918-8.
- Wang, L., S. Nagarajaiah, W. Shi, and Y. Zhou. 2022. “Seismic Performance Improvement of Base-Isolated Structures Using a Semi-Active Tuned Mass Damper.” Engineering Structures 271: 114963. https://doi.org/10.1016/J.ENGSTRUCT.2022.114963.
- Wang, L., S. Nagarajaiah, Y. Zhou, and W. Shi. 2023. “Experimental Study on Adaptive-Passive Tuned Mass Damper with Variable Stiffness for Vertical Human-Induced Vibration Control.” Engineering Structures 280: 115714. https://doi.org/10.1016/J.ENGSTRUCT.2023.115714.
- Wang, L., Y. Zhou, and W. Shi. 2023. “Seismic Control of a Smart Structure with Semiactive Tuned Mass Damper and Adaptive Stiffness Property.” Earthquake Engineering and Resilience 2 (1): 74–93. https://doi.org/10.1002/EER2.38.
- Weyant, E. (2022). Research Design: Qualitative, Quantitative, and Mixed Methods Approaches. 5th Ed. 19(1–2): 54–55. https://doi.org/10.1080/15424065.2022.2046231.