ABSTRACT
The key feature of diffusion brazing, also referred to as transient liquid phase bonding, is isothermal solidification which precludes the formation of intermetallic in the joint centreline. Analysing the available data published in the literature showed that the composition of the nickel-based superalloys plays a strong role in determining the required time for obtaining intermetallic-free joint during diffusion brazing. This effect is not predictable by the standard conventional models. It is proposed that increasing the boride-forming elements in the base superalloy which promotes in situ boride precipitation at the diffusion-affected zone can accelerate the diffusion flux of the boron into the base superalloy, leading to faster isothermal solidification. The higher the Cr + Mo + Nb + Ta + W content in base superalloy, the shorter the isothermal solidification time.
Introduction
The nickel-based superalloys play a key role in the development of aircraft and power-generation turbines. Their exceptional combinations of high temperature strength, toughness, crack-growth resistance and resistance to degradation in corrosive or oxidising environments are achieved via sophisticated microstructure design through complex multiple stages processing [Citation1,Citation2]. The joining/repairing processes are vital for manufacturing/service life extension of the superalloys which are used in safety-critical applications. One of the key microstructural requirements of a high performance joint/repair is the absence of any undesired intermetallic phase. Diffusion brazing, also known as transient liquid phase (TLP) bonding, which utilises diffusion-induced isothermal solidification provides an intriguing approach to preclude formation of the intermetallic phases during re-solidification of the liquid phase [Citation3–14].
A typical microstructure of diffusion-brazed Ni-based superalloys, with a boron-containing filler metal (FM), after partial isothermal solidification consists of three distinct microstructural zones (see ) [Citation6,Citation15,Citation16]:
Isothermal solidification zone (ISZ): The microstructure of this zone is free from boron-containing intermetallic and consists of a solid solution phase. Induced compositional changes, by interdiffusion between the base metal and FM during holding at a constant bonding temperature, are the driving force for isothermal solidification.
Athermal solidification zone (ASZ): This zone is formed during cooling of the residual liquid in the joint centreline via a eutectic transformation reaction, which is a characteristic of the Ni-based/B-bearing FM system. The microstructure of this zone composes eutectic-type solidification reaction products consisting of hard and brittle borides’ intermetallic compounds.
Diffusion-affected zone (DAZ): The microstructure of this zone is influenced by B diffusion into the base superalloy and low solubility of B in Ni-based superalloys which lead to in situ precipitation of borides in the substrate region.
Figure 1. Schematic microstructure of a TLP-bonded nickel-based superalloy using a B-bearing interlayer after partial isothermal solidification along with overall boron concentration gradient across the bond region: ASZ, ISZ, DAZ and BM indicate ASZ, ISZ and diffusion-affected zone and base metal, respectively. CS is B solubility at solid/liquid interface and is B solubility in the base metal.
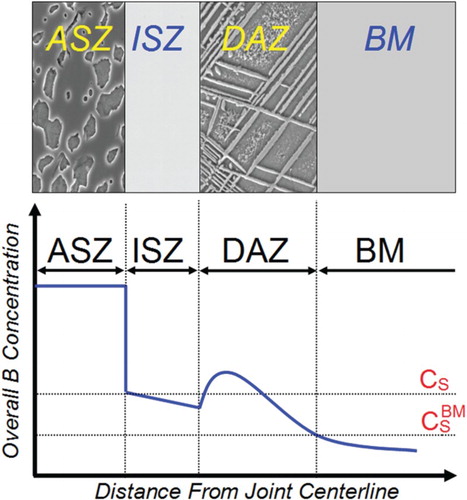
It is shown that in situation where the isothermal solidification is not accomplished completely, the stress concentration associated with hard and brittle eutectic microconstituents plays a key role in determining joint strength [Citation14]. An inverse relation between the ASZ size and shear strength of the diffusion-brazed joints has been reported [Citation6,Citation14]. It seems that precipitates in DAZ have less detrimental effect on the joint shear strength due to their non-continuously distributed fashion along the joint/base metal interface [Citation14]. Therefore, to ensure reliability of the diffusion-brazed nickel-based alloys during service, process parameters should be adjusted so that the completion of isothermal solidification is guaranteed (i.e. no liquid experiences eutectic-type solidification during cooling). It is shown that there is a critical bonding time (tIS) which beyond that the isothermal solidification of the liquid phase is ensured [Citation3–14]. Therefore, the kinetics of isothermal solidification is a key issue in fabricating eutectic-free robust joint/repair. Since the isothermal solidification is controlled by solid-state diffusion of melting point depressant (MPD) element into the base metal, the process is slow especially when the gap size is large (more than 100 μm, for example in the case of repairing of the cracks). The time required for solidification is, therefore, of primary interest when deciding whether any particular system is suitable for diffusion brazing.
According to the existing models [Citation17,Citation18] for isothermal solidification during diffusion brazing, for a given superalloy-/B-containing FM combinations with a certain joint gap, tIS depends on diffusivity of boron into the base superalloys. The effect of base metal composition on the isothermal solidification kinetics is not predictable based on the standard models. However, as will be discussed below, the superalloy chemical composition has strong influence on the kinetics of the isothermal solidification. Analysing the effect of base metal chemical composition on the isothermal solidification kinetics during diffusion brazing of superalloys is instrumental in extending the general understating of the process to develop more reliable and effective models for real base metal/FM multicomponent systems.
Isothermal solidification parameters during diffusion brazing of Ni-based superalloys
Theoretically, the isothermal solidification is completed when the boron concentration at the joint centreline reaches boron solid solubility [Citation15,Citation16]. Practically, during TLP bonding of superalloys, tIS is the minimum bonding time required to obtain an eutectic-free joint centreline (i.e. when ASZ completely disappears). Isothermal solidification times (tIS) during diffusion brazing for various commercial nickel-based superalloy are collected from the literature () [Citation7,Citation19–24]. The isothermal solidification times () are based on experimental data at temperature of 1373 K. According to the analytical models for predicting tIS [Citation19], to account for differences in initial gap size (W0) and boron content of the FM (CFM), tIS were normalised using the following formula:
(1)
Table 1. Isothermal solidification time during diffusion brazing of various superalloys.
shows the normalised tIS of various Ni-based superalloys. As can be seen, the base metal composition has significant influence on the tIS. For example, the normalised tIS for CMSX-2 single crystal superalloy is 16 times longer than that for IN718 superalloy. Therefore, it can be concluded that the isothermal solidification rate of CMSX-2 is significantly slower than that of IN718. At the first sight, it can be attributed to the absence of grain boundaries in the single crystal superalloy and lack of contribution of grain boundary diffusion to the MPD mass transport flux into the base superalloy. However, the contribution of the grain boundary diffusion at temperature higher than 0.75 Tm (where Tm is the equilibrium melting temperature in K) is less pronounced [Citation25]. Therefore, considering the fact that bonding temperature during diffusion brazing of Ni-base superalloys is typically higher than 0.75 Tm, and the absence of grain boundary cannot explain the slow isothermal solidification rate of single crystal superalloys compared to the polycrystalline ones.
Figure 2. Normalised isothermal solidification time (tIS) for some commercial Ni-based superalloys including IN738 [Citation6], cast IN718-cast [Citation19], IN600, IN713 [Citation20], CMSX-2 [Citation21], GTD-111 [Citation22], Waspaloy [Citation23] and Haynes282 [Citation24].
![Figure 2. Normalised isothermal solidification time (tIS) for some commercial Ni-based superalloys including IN738 [Citation6], cast IN718-cast [Citation19], IN600, IN713 [Citation20], CMSX-2 [Citation21], GTD-111 [Citation22], Waspaloy [Citation23] and Haynes282 [Citation24].](/cms/asset/5ed3f454-ce17-4199-81d0-0d108ec2e039/ystw_a_1327934_f0002_c.jpg)
The kinetics of the isothermal solidification which is proportional to the rate of solid/liquid interface movement (dX/dt) is governed by diffusion flux of the MPD into the base metal (JMPD). The mass balance at solid/liquid interface gives the following Equation [Citation17,Citation18]:
(2)
where DMPD is the diffusivity of MPD, CL is the MPD concentration in the liquid phase, CS is the solubility of MPD in the solid at the solid/liquid interface and dC/dX is the concentration gradient (from liquid/solid interface to the base metal). Therefore, the interface velocity can be written as follows:
(3)
According to Equation (3), the isothermal solidification rate is controlled by MPD diffusivity, and MPD concentration in the liquid phase (CL) and MPD solubility of in the solid at the solid/liquid interface (CS). According to the standard models for diffusion brazing, the concentration gradient is influenced by CS and MPD concentration in the BM (CBM). However, an ignored important factor which can affect the concentration gradient is the formation of the in situ boride precipitation (see ). summarises the type and composition of boride precipitation observed in DAZ of diffusion-brazed Ni-based superalloys [Citation14–16,Citation26–30]. As can be seen in , all boride types are rich in strong boride formers elements such as Mo, W, Cr, Ta and Nb. Indeed, the presence of strong boride former elements coupled with the diffusion of B, during isothermal solidification, explains the precipitation of borides. Gale and Wallach [Citation31] provided some evidence indicating that boride precipitates in this region are formed during holding at the bonding temperature (i.e. in situ precipitation), not during the cooling to room temperature.
Table 2. Composition of observed boride precipitation in the DAZ of the diffusion-brazed nickel-based superalloys.
Role of boride precipitation on isothermal solidification time
The question is how boride precipitation can affect MPD concentration gradient? In situ precipitation of borides in the DAZ requires short-range diffusion of boron and boride-forming elements from the adjacent matrix creating a boron-depleted zone surrounding the precipitates (i.e. the boron of the matrix is consumed by precipitation). B-content of the matrix surrounding the boride precipitates is lower than the boron content of the base metal. This B-depleted zone can act as a sink for B atoms in the liquid phase to enter in the base metal. Therefore, the boride precipitation increases the MPD concentration gradient (dC/dX) enhancing the boron diffusion flux into the base metal [Citation32,Citation33]. It can be concluded that the boride precipitation at the bonding temperature helps to faster completion of isothermal solidification.
Regarding the role of boride precipitates in the DAZ on the isothermal solidification kinetics, some further effects should be considered.
(i) Diffusivity through boride particles: The intermetallic phases such as borides typically exhibited low diffusion coefficient. Therefore, it is expected that effective diffusivity through γ-matrix+Boride is reduced. However, considering the low volume fraction of the boride phases in DAZ (typically less than 50vol.-%), this factor is not expected to play dominant role in diffusion behaviour of the MPD.
(ii) Influence of boride-forming elements of the base superalloy on the solid solubility at liquid/solid interface (): According to the analytical models for tIS [Citation18,Citation19],
is an important factor in determining the MPD flux during isothermal solidification which is governed by the chemical composition of the ISZ. The presence of boride-forming elements in the ISZ can reduce
which in turn decelerate the kinesis of isothermal solidification. The composition of ISZ is mainly determined by the composition of the filler alloy. Moreover, the base metal chemistry can influence composition of the ISZ via BM dissolution and solid-state interdiffusion between isothermally solidified layer and BM during bonding process. However, owing to slow diffusion rate of boride-forming element with large atomic radius compared to Ni and small contribution of dissolution process (at standard bonding temperatures), the influence of boride-forming elements in the base metal on the
can be neglected. Therefore, the net effect of increasing the Cr + Mo + W + Nb in the base metal chemistry is accelerating the diffusion flux via promoting the in situ precipitation.
Role of superalloy composition on isothermal solidification time
According to the proceeding discussion, it can be concluded that increasing the potential for in situ boride precipitation in DAZ amplifies the sinking action of B-depleted zones which leads to enhanced diffusion flux of B and hence faster completion of isothermal solidification. The ‘boride-precipitation potential’ during diffusion brazing a superalloy using a given FM at certain temperature is determined by the content of the strong boride-forming elements (i.e. Cr, Mo, Nb, Ta and W) [Citation32]. Therefore, increasing boride-forming elements in the base superalloy can accelerate the kinetics of isothermal solidification via increasing the potential for in situ precipitation during diffusion brazing. To experimentally investigate the effect of base metal composition on boride precipitation, diffusion brazing was carried out between two distinct nickel-based superalloys: wrought IN718 (18.23 wt-% Cr, 3.1 wt-% Mo, 4.85 wt-% Nb) and cast IN738 (16 wt-% Cr, 1.7 wt-% Mo, 2.64 wt-% W, 0.7 wt-% Nb). The bonding was performed using a 50 μm thick Ni–15Cr–4B interlayer at the bonding temperature of 1373 K for 30 min. shows the DAZ microstructures at both superalloys. SEM-EDS analysis showed that (not shown here) that the boride precipitates in IN718 and IN738 are rich in Cr–Mo–Nb and Cr–Mo–W, respectively. As can be seen, IN718 exhibited wider DAZ with higher volume fraction of borides compared with the IN738. This confirms that IN718 alloy displays a high capability for accommodating B atoms, which are diffusing from liquid to the base metal during isothermal solidification. This can be attributed to the higher amount of boride-forming elements in IN718 compared to the IN738. The higher boride-precipitation potential of the IN718 can explain why the normalised tIS for IN718 is much shorter than that of the IN738 ().
Figure 3. Diffusion brazing of IN718/Ni–15Cr–4B/IN738 at the bonding temperature of 1373 K for 30 min showing diffusion-affected zone (DAZ) microstructure at (a) IN718 side and (b) IN738 side. Arrows indicate the boride precipitates. The volume fraction of the boride precipitates in DAZ of IN718 is significantly higher than that of in IN738 side confirming the higher ‘boride-precipitation potential’ of the IN718 compared to the lN738.
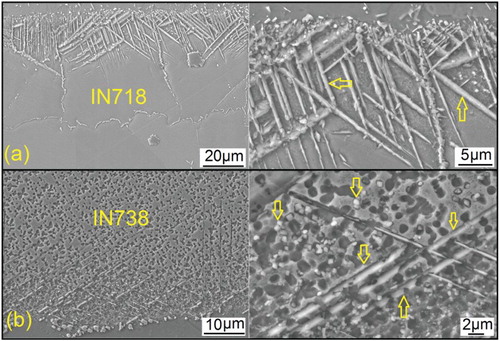
Considering the influence of boride precipitation on the kinetics of isothermal solidification during diffusion brazing, finding an index to reflect the role of superalloy composition on boride precipitation potential is useful. Here the sum of boride-forming elements (Cr + Mo + Nb + Ta + W) is used as a simplified index for ‘boride-precipitation potential’ of the base superalloy. To verify this point, the correlation between Cr + Mo + Nb + Ta + W and normalised isothermal solidification time (tIS) was investigated using experimental data in the literature. According to , there is an inverse relationship between Cr + Mo + Nb + Ta + W content of the base superalloy and normalised tIS confirming that superalloy chemical composition has a pronounced effect on the isothermal solidification behaviour. Therefore, for example, the fast isothermal solidification process in IN718 compared with CMSX-2 single crystal superalloys can be explained by their different boride precipitation potentials. The sum of the boride-forming elements (Cr + Mo + Nb + Ta + W) for IN718 and CMSX-2 alloys is 25 and 15 at.-%, respectively.
Figure 4. Effect of Cr + Mo + Nb + Ta + W contents of the base superalloy, as an index for boride-precipitation potential, on normalised isothermal solidification time for various superalloys including IN738 [Citation6], cast IN718-cast [Citation19], IN600, IN713 [Citation20], CMSX-2 [Citation21], GTD-111 [Citation22], Waspaloy [Citation23] and Haynes282 [Citation24].
![Figure 4. Effect of Cr + Mo + Nb + Ta + W contents of the base superalloy, as an index for boride-precipitation potential, on normalised isothermal solidification time for various superalloys including IN738 [Citation6], cast IN718-cast [Citation19], IN600, IN713 [Citation20], CMSX-2 [Citation21], GTD-111 [Citation22], Waspaloy [Citation23] and Haynes282 [Citation24].](/cms/asset/20eb09b5-dec5-415a-880b-5fbef6bd6b3e/ystw_a_1327934_f0004_c.jpg)
It should be noted that the affinity of Cr, Mo, W and Nb element to boron is not identical. This can be inferred from their different heat of formation [Citation34]. However, owing to the possibility of formation of various types of borides (), determination of the relative affinities of boride-forming elements in multi-component systems to B is difficult. It should be noted that most of the research on the isothermal solidification phenomenon during TLP bonding has been conducted on multi-component superalloy that can confound the determination of any systematic solute effect. The present work provides a basis for understanding the role of in situ boride precipitation and superalloy composition in determining the isothermal solidification kinetics during diffusion brazing. However, there is a clear need for systematic investigations on the effect of base metals composition (particularly boride-forming elements) on the microstructural development mechanism during isothermal solidification. Owing to the different affinity of boride-forming elements to B, individual effect of each element should be determined. Systematic experimentation coupled with computational thermodynamic/kinetics modelling is needed to develop a fundamental knowledge regarding the role of base alloys’ composition of isothermal solidification kinetics. This provides a basis to move towards design superalloys specifically tailored for diffusion brazing.
The results of this study assist in judicious selection of proper superalloy for diffusion brazing when fast isothermal solidification is required for economical considerations. In situation where long isothermal solidification is envisaged, for example in repairing wide cracks or brazing of cellular architecture structures with gap size of several hundred micrometres, one can deliberately choose a superalloy with high content of boride-forming elements. Finally, it should be noted that despite the beneficial effect of in situ boride precipitation on the isothermal solidification rate, they can deteriorate joint properties in terms of corrosion resistance and mechanical properties. They also affect the aging response of a precipitation-hardened nickel-based superalloy. Therefore, there is a need to design a proper post-bond heat treatment to reduce/eliminate boride precipitation in DAZ via a break-up and dissolution process.
Conclusion
The kinetics of isothermal solidification during TLP diffusion brazing not only is determined by diffusivity of boron and solid solubility of MPD solid/liquid interface, but is significantly influenced by in situ boride precipitation which in turn is influenced by the composition of the base metal. The Cr + Mo + W + Nb + Ta content of the base metal can be considered as an index for expressing the influence of the superalloy chemistry on the isothermal solidification time. Existing standard models for diffusion brazing do not account borides’ precipitations. Therefore, fundamental understanding of in situ boride precipitation in diffusion-affected zone and its effect on boron flux during bonding process is necessary to develop more precise mathematical models for predicting isothermal solidification kinetics during diffusion brazing of superalloys.
Disclosure statement
No potential conflict of interest was reported by the authors.
ORCID
M. Pouranvari http://orcid.org/0000-0002-9603-447X
References
- Pollock TM, Tin S. Nickel-based superalloys for advanced turbine engines: chemistry, microstructure and properties. J Propul Power. 2006;22:361–374. doi: 10.2514/1.18239
- Pollock TM. Alloy design for aircraft engines. Nat Mater. 2016;15:809–815. doi: 10.1038/nmat4709
- Duvall DS, Owczarski WA, Paulonis DF. TLP bonding: a new method for joining heat resistant alloys. Weld J. 1974;53:203–214.
- Gale WF, Butts DA. Transient liquid phase bonding. Sci Technol Weld Join. 2004;9:283–300. doi: 10.1179/136217104225021724
- Rabinkin S. Brazing with (NiCoCr)-B-Si amorphous brazing filler metals: alloys, processing, joint structure, properties, applications. Sci Technol Weld Join. 2004;9:181–199. doi: 10.1179/136217104225012300
- Pouranvari M, Ekrami A, Kokabi AH. Diffusion brazing metallurgy of IN718/Ni-Cr-Si-B-Fe/IN718. Weld J. 2014;93:60s–68s.
- Ojo OA, Richards NL, Chaturvedi MC. Isothermal solidification during transient liquid phase bonding of Inconel 738 superalloy. Technol Weld Join. 2004;9:532–540. doi: 10.1179/174329304X8702
- Ojo OA, Richards NL, Charturvedi MC. Effect of gap size and process parameters on diffusion brazing of Inconel 738. Sci Technol Weld Join. 2004;9:209–220. doi: 10.1179/136217104225012175
- Nishimoto K, Saida K, Shinohara Y. Computer aided alloy design of insert metal for transient liquid phase bonding of γ/γ'/β type high aluminium nickel base superalloy. Sci Technol Weld Join. 2003;8:29–38. doi: 10.1179/136217103225008946
- Liu JD, Jin T, Zhao NR, et al. Bonding behaviour of nickel base single crystal to polycrystal superalloys by transient liquid phase method. Sci Technol Weld Join. 2010;15:194–198. doi: 10.1179/136217109X12518083193513
- Pouranvari M, Ekrami A, Kokabi AH. Aging response of transient liquid phase bonded wrought IN718 superalloy: influence of post-bond heat treatment. Sci Technol Weld Join. 2014;19:105–110. doi: 10.1179/1362171813Y.0000000170
- Riggs B, Alexandrov B, Benatar A, et al. Thermodynamic and kinetic simulations of high temperature brazing: microstructure evolution in CMSX-4 joints. Sci Technol Weld Join. 2017;22:428–437. doi: 10.1080/13621718.2016.1250432
- Riggs B, Alexandrov B, Benatar A, et al. Metallurgical characterisations of CMSX-4 vacuum-brazed with BNi-2 and BNi-9. Sci Technol Weld Join. 2017;22:227–235. doi: 10.1080/13621718.2016.1218415
- Pouranvari M, Ekrami A, Kokabi AH. TLP bonding of cast IN718 nickel based superalloy: process–microstructure–strength characteristics. Mater Sci Eng A. 2013;568:76–82. doi: 10.1016/j.msea.2013.01.029
- Pouranvari M, Ekrami A, Kokabi AH. Phase transformation during diffusion brazing of IN718/Ni-Cr-B/IN718. Mater Sci Technol. 2013;29:980–984. doi: 10.1179/1743284713Y.0000000238
- Pouranvari M, Ekrami A, Kokabi AH. Solidification and solid state phenomena during TLP bonding of IN718 superalloy using Ni–Si–B ternary filler alloy. J Alloys Compd. 2013;563:143–149. doi: 10.1016/j.jallcom.2013.02.100
- Zhou Y, Gale WF, North TH. Modeling of transient liquid phase bonding. Int Mater Rev. 1995;40:181–196. doi: 10.1179/imr.1995.40.5.181
- Tuah-Poku I, Dollar M, Massalaski TB. Study of transient liquid phase bonding process applied to a Ag/Cu/Ag sandwich joint. Metall Mater Trans A. 1998;19A:675–685.
- Pouranvari M, Ekrami A, Kokabi AH. Diffusion induced isothermal solidification during transient liquid phase bonding of cast IN718 superalloy. Can Metall Q. 2014;53:38–46. doi: 10.1179/1879139513Y.0000000076
- Nakao Y, Nishimoto K, Shnizokai K, et al. Theoretical research on transient liquid insert metal diffusion bonding of nickel base superalloy. Trans Jpn Weld Soc. 1989;20:60–65.
- Nishimoto K, Saida K, Kim D, et al. Transient liquid phase bonding of Ni-base single crystal superalloy, CMSX-2. ISIJ Int. 1995;35(10):1298–1306. doi: 10.2355/isijinternational.35.1298
- Pouranvari M, Ekrami S, Kokabi AH. Microstructure-properties relationship of TLP-bonded GTD-111 nickel-base superalloy. Mater Sci Eng A. 2008;490:229–234. doi: 10.1016/j.msea.2008.01.032
- Wikstrom NP, Egbewande AT, Ojo OA. High temperature diffusion induced liquid phase joining of a heat resistant alloy. J Alloys Compd. 2008;460:379–385. doi: 10.1016/j.jallcom.2007.06.066
- Ghoneim A, Ojo OA. Microstructure and mechanical response of transient liquid phase joint in Haynes 282 superalloy. Mater Charact. 2011;62:1–7. doi: 10.1016/j.matchar.2010.09.011
- Porter DA, Easterling KE, Sherif M. Phase transformations in metals and alloys. CRC Press, Boca Raton, Florida; 2009.
- Idowu OA, Ojo OA, Chaturvedi MC. Microstructural study of transient liquid phase bonded cast INCONEL 738LC superalloy. Metall Mater Trans A. 2006;37:2787–2796. doi: 10.1007/BF02586111
- Sheng N, Hu X, Liu J, et al. M3b2 and M5B3 formation in diffusion-affected zone during transient liquid phase bonding single-crystal superalloys. Metall Mater Trans A. 2015;46:1670–1677. doi: 10.1007/s11661-014-2733-z
- Liu J, Jin T, Zhao N, et al. Microstructural study of transient liquid phase bonded DD98 and K465 superalloys at high temperature. Mater Charact. 2011;62:545–553. doi: 10.1016/j.matchar.2011.03.012
- Steuer S, Singer RF. Boride zone formation in transient liquid phase bonding of pairings of parent superalloy materials with different compositions and grain structures. Metall Mater Trans A. 2013;44:2226–2232. doi: 10.1007/s11661-012-1597-3
- Zhang B, Sheng G, Jiao Y, et al. Precipitation and evolution of boride in diffusion affected zone of TLP joint of Mar-M247 superalloy. J Alloys Compd. February 2017;695(25):3202–3210. doi: 10.1016/j.jallcom.2016.11.306
- Gale WF, Wallach ER. Microstructural development in transient liquid-phase bonding. Metall Trans A. 1991;22:2451–2457. doi: 10.1007/BF02665011
- Schnell A. A study of the diffusion brazing process applied to the single crystal superalloy CMSX-4 [PhD thesis]. EPFL, Institut des matériaux; 2004.
- LeBlanc A, Mevrel R. High Temperature Materials for Power Engineering Conference; Liege, Belgium; 1990, p. 1451–1460.
- Heats of formation of metallic borides by fluorine bomb calorimetry. Ohio: Air Force Aero Propulsion Laboratory, Research and Technology Division, Air Force Systems Command; 1964. (Technical documentary report No. APL-TDR-64-39).