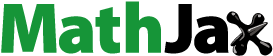
ABSTRACT
Many researchers are interested in using natural fibres to treat due to recent advancements in polymer characteristics. The mechanical properties of three types of bars are studied in this paper: Cotton Fibre-Reinforced Polymer bars, Cotton/Carbon Fibre-Reinforced Polymer bars, and Cotton/Glass Fibre-Reinforced Polymer bars. The goal of the paper was to create low-cost bars with comparable mechanical performance and corrosion resistance to steel reinforcement. The bars were made using two methods: fibres immersed in polymer and fibres coated with polymer by repeated tension and relaxation of fibres. The second method produced better results in terms of the tensile strength of Cot.CFRP, Cot.GFRP, and Cot.FRP bars, which were 688, 477, and 284 MPa, respectively, and the stress–strain curve revealed brittle behaviour for all bars and modulus of elasticity of 43, 31 and 22 GPa. When sand was put on the bar’s surface, the bars demonstrated a good connection with the concrete. It also showed good resistance to moisture, alkaline solutions and acids, as well as heat resistance at temperatures below 200°C.
Introduction
In recent years, the use of Fibre-Reinforced Polymer (FRP) bars haves been commonly used in many construction projects, the reason behind that is the durability of the FRP bars compared to conventional reinforcing steel bars (Ottosson Citation2021). FRP bars are also a lightweight material, Where the weight of GFRP bars is 25% of the weight of the reinforcing steel and its tensile strength is twice that of the reinforcing steel thus reduce the loads on the structure, especially when using lightweight concrete, By comparing lightweight foamed concrete reinforced with GFRP bars to normal concrete beams it was found that the increase in the load capacity for lightweight foamed concrete is 3.6% of the load capacity for normal concrete beams (Abd and Ghalib Citation2018).
The FRP bars are more durable than the conventional reinforcing steel bars when structures are exposed to an aggressive environment, such as, high humidity and high salts concentration (Ahmed et al. Citation2020). The FRP bars are used in basins and water treatment plants for chemical industries, sewage, and facilities that required magnetic isolation such as magnetic resonance imaging centres (Almusallam et al. Citation2013). In terms of the mechanical properties, the FRP bars have a higher tensile strength compared to the conventional reinforcing steel bars (Al-Attar et al. Citation2021).
The types of fibre and resin used in the production of the FRP bars have a significant effect on the mechanical properties of FRP bars, which are made of glass fibres, CFRP carbon fibres, BFRP basalt fibres and AFRP aramids (Tanks, Harris, and Sharp Citation2016; Hassan et al. Citation2016). In addition, the quality of the resin material is of great importance in showing improvements in the mechanical properties of the resulting composite material (shear resistance and flexibility) and on the durability for the FRP bars (resistance to salts, acids, and moisture) (Wang and Yang Citation2021). The strength of the bars is also affected by the amount of voids and the homogeneity of the composite material, which depends on the method of forming the fibres and the amount of their saturation with the resin (Spagnuolo et al. Citation2021).
The corrosion of steel cables in bridges has been studied and compared with FRP bars in terms of tensile strength and durability issues, such as the effect of temperature, salt, humidity, and UV rays. The experimental work was achieved based on rapid procedure to simulate the exposure for long term. The results show that FRP cables have the feasibility to be used in long-span cable-supported bridges from the mechanical properties (Wang and Yang Citation2021).
The researchers were attempted to enhance the bond between the FRP bars and concrete by adding fine sand to the outer surface of the FRP bars after the saturation by the resin In addition, it was found that adding sand to the resin improved the toughness, tensile, fracture and shear resistance, reduced the reaction temperature between the polymer and the hardener, and increased the curing time (Abdulla et al. Citation2016).
In an attempt to manufacture FRP bars Use different types of fibres (hybrid fibres) to improve the properties of FRP bars and reduce the manufacturing cost. where was mixed natural fibres with vinyl ester in a 7:3 ratio, replacing the natural fibres with volumetric proportions of glass fibres, 0%, 30%, 50%, 70% and 100%. The tensile load and displacement curve showed almost linear elastic behaviour when adding 50% natural fibres, but was partially non-linear in 70%. The tensile strength decreased with the increase in the volume addition of natural fibres because the tensile strength of natural fibres is much lower than that of glass fibres (about 1:8.65). Because of the lower density of natural fibres is half the density of glass fibre (Han et al. Citation2015).
In reviewing the previous literature, it was noted that there is a gap a Sufficiently investigation of produce hybrid FBR bars from natural and synthetic fibres that meet structural requirements, are economically feasible, and are a good alternative to concrete rebar (Han et al. Citation2015). In this paper, the mechanical properties, the effect of alkaline solutions, acids, moisture, heat effect, and bonding with concrete was studied. The bars were manufactured from cotton fibre treated with epoxy reinforced with 50% volume of glass fibre or carbon fibre and were investigated in this paper to determine whether these bars could be a viable alternative to concrete reinforcement.
Experimental works
The practical program included the manufacture of two types of FRP bars with a diameter of 12 mm, one of which was of cotton fibres treated with epoxy and the other of cotton fibres reinforced with carbon fibres or glass fibres treated with epoxy.
Initially, two forms of fibres were chosen, the first strands of cotton fibres twisted together in the form of a cotton rope, and the second threads of separate cotton fibres extended longitudinally in parallel, and the latter was approved to fulfil the requirements of the mechanical properties of FRP bars.
Two methods were chosen to treat the fibres with epoxy, one by immersion in a pan containing epoxy and the other by repeated coating by soft brush with continuous relaxation and tension of the fibres during coating. The second method was adopted to achieve fibre saturation and homogeneity as a uniform matrix in the produced composite material, It will also be explained in the paragraph 2.2.1.
Materials
It is critical to select materials that meet the needs of specified standards in order to achieve realistic results. As a result, the type of cotton fibres used in the current study was chosen based on visual testing in the first-phase cleanliness and continuity of cotton fibres as well as the mechanical test like tensile, and density tests. The epoxy resin was selected as the bonding material for fibres. The viscosity and evolved heat during mixing can determine the quality of epoxy resins, with low viscosity and minimal generated heat yielding the best results. Sikadur 52 polymer is mixed with fine sand, Add fine sand of 50% by volume of epoxy (Abdulla et al. Citation2016), and then resin is added. When used the fine sand in this study by the same ratio, a decrease in the temperature generated during mixing was observed where the fine sand has the potential to reduce the amount of heat released by up to 50%, but the viscosity was raised, causing difficulty and delay in the mixing process. In addition, when the viscosity increased, the fibre’s absorption of epoxy decreased. While when using the epoxy (PrimeTM 20LV) did not result in a reduction in fibre absorption Due to the low viscosity In addition, no heat emission was observed during mixing. Therefore, the epoxy (PrimeTM 20LV) was chosen as a fibre adhesive because it has a low viscosity, does not emit heat during mixing, and has a good hardening period, in addition to its high tensile resistance. The specifications of (PrimeTM 20LV) as are follows:
Low viscosity at 30°C for resin (390-410)
and hardener (10-12))
.
Infusion times that can be adjusted
The exotherm is quite low, particularly in dense areas.
Carbon, Glass, and Cotton fibres are readily available on the local market, with specifications and shapes indicated in and , respectively.
Table 1. Mechanical properties of carbon, Cotton, fibre and matrix resin.
Polymer cotton bars reinforced by carbon/glass fibre
Sample manufacturing process
Following the selection of materials, they were prepared in two groups, the first group of cotton ropes braids was twisted together, and the second group of cotton longitudinal separated bundles. were used two methods to treat fibres with epoxy by immersion and coating. when immersion of the twisted fibre ropes together in the pot containing epoxy and after hardening The outer surface of the fibres was smooth, and there was not enough saturation of the fibres due to the Stacking of the twisted fibres together in the braids, as well as when coating them with a soft brush, the fibres were not well saturated with the epoxy. When testing the tensile strength of the twisted braid bars, we note that there is an early failure and a loss of 60% of the tensile strength Because of the torsional torque of the twisted braids
While the results of tensile strength in the second group of samples in which repeated coating was used with epoxy with sequential tension and release of longitudinally separated bundles of cotton fibres were better than samples that were immersed in epoxy because of the equal distribution of epoxy in the coated samples and the complete saturation obtained so that the cotton fibres act as a uniform matrix with the epoxy and obtaining more homogeneity ().
All bars were made from continuous linear fibres using a tension-release fibres method during continuous coating by volume fraction 50%, which ensured that the fibres were saturated with epoxy and that micro-bubbles were expelled, ensuring that the surface roughness was maintained when the sand for the bar’s surface was added (See ).
The longitudinal parallel cotton fibres were tied and supported on a steel structure frame and tied the second end on movable support which helped the bundle cotton fibres to relax and tensile during the process of coating fibres, the bundle cotton fibres are dried by hot air before coating process to get rid of moisture. where coating the fibres with epoxy must be sure the fibres are saturated evenly, the core bundle carbon or glass fibres are placed within cotton fibres it’s surrounding. Then a thin cotton rope is wrapped in an opposite manner around the fibres bundle, where be the composite material like a uniform matrix, then fine and dry sand is sprayed on the fibres bundle surface Randomly 60 g/m approximately so as to ensure that the sand is evenly distributed over the surface of bundle to increase the roughness for FRP bars and bond with concrete () (Abdulla et al. Citation2016; Ali et al. Citation2019; Arias, Vazquez, and Escobar Citation2012; Dong, Wu, and Xu Citation2016; Hassan et al. Citation2016).
Prepare samples for testing
End by treating the cotton and carbon/glass hybrid fibres with epoxy and stringing them in the steel frame for 24 h at 50°C under treated circumstances. When preparing the specimen for testing, both ends must be fixed with epoxy sikadur 330 in a steel grip 50 × 300 mm and grooves made on the tube surface to prevent specimen slippage or fibre failure in the clamping tensile machine, and the clamps must not slip during testing. A strain gauge must also be installed in the middle of the specimens to measure the strain (See ) (American Society for Testing and Materials Citation2012; Han et al. Citation2015; Matrix Citation2010; Saeed et al. Citation2020; Standard Citation2015).
Other Cot.FRP, Cot.CFRP, and Cot.GFRP bar samples were also made for bonding tests with concrete (Al-khafaji Citation2021), where bars were inserted vertically 150 mm Anchorage bond depth (Development length as in the Equations 1,2,3) in the concrete using standard cylinders (300 × 150 mm) and sprayed with a sika Antisol WB curing compound to moisten the concrete without need to cure with water.
Where:
Zbd = bond stress
P = ultimate load at failure
d = diameter of specimen
Lb = lengths of bonding (Rahim et al. Citation2020)
The other end of the specimen was fixed with epoxy sikadur 330 in a steel grip 50 undefined mm (Diameter height) and grooves were made on the tube surface to prevent specimen slippage. The specimens were tested for 28 days using a universal tensile test device to determine the bonding strength of the bars with concrete, which is an important property of FRP bars (See ).
Results and discussion
Mechanical properties
Tensile properties
The tensile strength of FRP bars is one of the most important mechanical properties governing the acceptance of its use as an alternative to steel bars. the two ends of the sample were fixed in a universal testing machine, loading capacity (250 kN).The speed of testing shall be set to constant strain rate. where produce failure within 1 to 10 minutes from the beginning of force application, and the standard strain rate can be adjusted to 0.01 min.-1. If strain control is available on the testing machine (D7205/d7205m Citation2016) as shown in Equations (4–6)
During the tensile test, displacement of 5 mm/minute in displacement control mode, as display in EquationEquations 4(4)
(4) –Equation6
(6)
(6) , the two ends of the sample were fastened, (). Several samples of Seel, Cot.FRP, Cot.CFRP, and Cot.GFRP bars with a diameter of 12 mm were evaluated (Saeed et al. Citation2020; Biswas et al. Citation2015), After getting the data, it was discovered that the tensile behaviour of the stress-strain curve for Cot.CFRP, Cot.GFRP, and Cot.FRP is linear till failure in the elastic limit only, and the yield stress of CFRP bars (688) MPa is similar to that of steel bars (624) MPa. The tensile strength of the Cot.FRP and Cot.GFRP bars was lower, with findings of (477,284) MPa While when comparing the results of the tensile strength of CotGFRB and CotCFRP bars with the results of the tensile strength of composite strips of epoxy and cotton by researchers (115) MPa, this is due to the low tensile strength of the resin and hardener, as well as its high viscosity, which reduces the saturation of the fibres of those strips with epoxy (P. Sharma, Pandey, and Srivastava Citation2017). the modulus of elasticity was lower for Cot.CFRP, Cot.GFRP, and Cot.FRP (55,42,31)GPa, respectively, compared to a modulus of elasticity for steel bars (218) GPa (, ). While when comparing it with the results of the GFRP bars, we note the convergence of the results () (Al-khafaji Citation2021)
Table 2. Tensile properties of Seel, Cot.FRP,Cot.CFRP, and Cot.GFRP bars.
Table 3. Mechanical and physical properties of GFRP rebars(al-khafaji Citation2021).
The Cotton polymer fibres that surround the bundle of carbon fibres or glass fibres worked to contain them during the test, and did not burst diffusely upon failure, but stayed inside the Cotton polymer fibre even after surface cracks developed ().
In general, the FRP bars had a linear elastic activity with no plastic behaviour and a brittle failure characteristic. This is due to the difference in modulus elasticity of carbon fibres or glass fibres (160, 81) GPa compared to the modulus elasticity of Cotton fibres (11.7)GPa, as well as a difference in density between glass fibres and Cotton fibres (2.8, 1.5) gm/cm3, where glass fibres volume decreases when compared to Cotton fibres volume. These bars, on the other hand, functioned as a homogeneous matrix of carbon or glass fibres encircled by cotton fibres submerged in a hardened polymer.
Flexural properties
Flexural strength testing is a critical feature of FRP bars. Under laboratory settings (temperature 25°C, humidity 55%), samples were manufactured and tested according to ASTM D4476 requirements (ASTM Citation2014; A specimen with a length of 500 mm was supported simply at the span length (20 diameter of the sample) and using a bending test lever, and the load was applied by a load cell controlled computerised universal testing machine with a capacity of 250 kN and a rate of displacement of 3 mm/minute, and the flexural strength was calculated using the EquationEquation (7)(7)
(7) .
where = stress in the outer fibres at midspan, N/m2, P = load at a given point on the load-deflection curve (N), L = support span, m, I = moment of inertia (m4), C = distance from centroid to extremities (m)
where E = flexural modulus of elasticity in bending (N/mm2), Y = middle-span deflection at load P (mm).
When comparing the bendability of Cot.CFRP bars to Cot.GFRP and Cot.FRP bars during the test, the bending angles before the bars failed from the bottom side were (38o,29o,26o) respectively, compared to steel bars (450) ().
Transverse-Shear strength
The bonding test between FRP bars and concrete used the direct pull-out test method, in which the samples were inserted in a universal test machine at a displacement rate of a displacement of 3 mm/minute, as illustrated in () (). The bonding strength was then estimated using the EquationEquation (8)(8)
(8) . [(ASTM D7914 Citation2021)]:
Table 4. Mechanical Properties of the Cot.FRP, Cot.CFRP, and Cot.GFRP bars.
where = transverse-shear strength (MPa), Ps = failure load (N),A = cross-sectional area of the FRP bar (mm2).
Bond behaviour for Cot.FRP, Cot.CFRP, and Cot.GFRP bars with concrete
The bonding test between FRP bars and concreteIt is as important in FRP bars as it is in steel reinforcing bars, especially at high temperatures (Zhu et al. Citation2021), used the direct pull-out test method, in which the samples were inserted in a universal test machine at a displacement rate of 3 mm/min, (see . After that, can use the equation to compute bonding strength.:
where = bond strength of the FRP bent bar (MPa),
= ultimate force measured in the bend test (N), A = standard cross-sectional area of single leg of the FRP bent bar as described in section (mm2)
Due to the increased friction for the sand addition effect on the bars surface, the results revealed a good bonding between CotCFRP, Cot.GFRP, and Cot.FRP bars and concrete. Where the sand is made up of rounded particles and contains 98% silica, and where the surface roughness was used to increase the surface area between the bars and the concrete, As a result, the rough surface area of the carbon or glass fibre bundle has risen due to the cotton fibres generated with the polymer and sand as a matrix When comparing the results of the bonding of CotGFRB and CotCFRP bars with concrete, (see ) GFRB and CFRB bars in previous studies, we note the convergence of the results in achieving high bonding with concrete due to the surface roughness and formed grooves. (Al-khafaji Citation2021; Biswas et al. Citation2015).
Thermogravimetric analysis of Cot.FRP, Cot.CFRP, and Cot.GFRP bars
By exposing samples to different temperatures (100,200,300,400,500). During a 1–24 hour heat exposure period while recording the change in sample weight, thermogravimetric analysis was utilised to investigate the heat behaviour of Cot.FRP, Cot.CFRP, and Cot.GFRP bars (Arias, Vazquez, and Escobar Citation2012). At (100, 200°C), the weight-temperature curve indicated no effect on weight, but after 250°C, the weight of the samples decreased till full burning at 500°C, () . That depends on the type of epoxy and the heat period; when fibres are saturated, heat resistance increases, preserving the fibres. Do not allow air bubbles to form between the fibres, as this reduces the thermal resistance of FRP bars When comparing the results with GFRP and CFRP bars, we notice a greater decrease in weight during exposure to heat, due to the presence of cotton fibres that decompose more quickly than glass and carbon () (Rahman et al. Citation2015).
Chemical properties
To determine the extent of sample resistance to moisture, acid, and alkaline solutions, samples were divided into four groups: the first group was immersed in an alkaline solution PH (12–13) by preparing the following chemical compound (Spagnuolo et al. Citation2021), and the second group was immersed in an acid solution PH(12–13) by preparing the following chemical compound:
(118.5 g of Ca(OH)2 + 0.9 g of NaOH +4.2 g of KOH +1 litre of tap water) (Anon Citationn.d.; ASTM D7914 Citation2021)
The third and fourth groups, on the other hand, were immersed in sulphuric acid at concentrations of 5% and 10%, respectively. The immersion continued for six months. Weighing the samples on a regular basis allowed us to track changes in their form, colour, and weight. .
Figure 15. Resistance test to moisture, alkaline solutions, and acid for for Cot.FRP, Cot.CFRP, and Cot.GFRP bars.
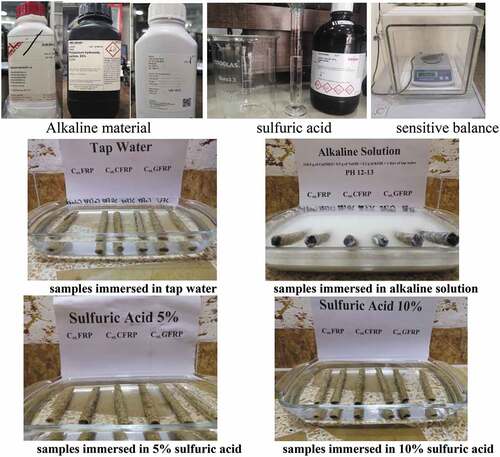
When samples were taken, Water, alkaline solution, and sulphuric acid at 5% and 10% concentrations had no influence on Cot.CFRP and Cot.GFRP bars during the immersion duration. After 50 and 90 days, swelling and cracks were seen in Cot.FRP bars immersed in 10% and 5% sulphuric acid, respectively, and the swelling and crack expansion continued in the samples, changing colour to black after 6 months as a result of the fibres degradation ( (Saurabh Citation2014).
The amount of polymer applied to all bars is the same, and GFRP bars’ high absorption, in contrast to carbon and glass fibres, resulted in cavities and acid degradation of the fibres.
Conclusions
Cotton fibres treated with a low viscosity polymer are reinforced by carbon fibre or glass fibre bundles. where the tensile strength of composite material Cot.CFRP and Cot.GFRP bars (688,488) MPa respectively, and these results encourage more research on FRP hybrid bars to improve some properties such as brittleness and modulus of elasticity to be a successful alternative to steel reinforcement.
Compared to steel, CFRP, and GFRP rebar, Cot.FRP, Cot.CFRP, and Cot.GFRP bars are light weight and have densities of (1.33,1.42,1.7) g/cm3 and (7.45,2.22,2.45) g/cm3 correspondingly.
Compared to steel rebar, Cot.CFRP and Cot.GFRP bars have acceptable tensile strength, but they are 40-50% less expensive than CFRP and GFRB bars.
Adding sand to the surface of the bars increased the bonding between the Cot.FRP,
Moisture, alkaline solutions, and acids were not a problem for the Cot.CFRP and Cot.GFRP bars, as the polymer acted to preserve the fibres.
The heat resistance of the Cot.FRP, Cot.CFRP, and Cot.GFRP bars was up to 300°C.
• After being immersed in water, alkaline solutions, and acids during the exposure time, FRP bars must be tested for mechanical characteristics on a regular basis.
Data available within the article or its supplementary materials
The authors confirm that the data supporting the findings of this study are available within the article [and/or] its supplementary materials.
Disclosure statement
No potential conflict of interest was reported by the author(s).
Correction Statement
This article has been republished with minor changes. These changes do not impact the academic content of the article.
Additional information
Funding
References
- D4476D4476M-14. Standard Test Method For Flexural Properties of Fiber Reinforced Pultruded Plastic Rods.
- Abd, Suhad M., and Dhamyaa Ghalib. 2018. “Flexural Behaviour of Lightweight Foamed Concrete Beams Reinforced with GFRP Bars.” Civil Engineering Journal 4 (2): 278. doi:10.28991/cej-030991.
- Abdulla, Aziz I., Hashim Abdul Razak, Yassen Ali Salih, and Muataz Ibrahim Ali. 2016. “Mechanical Properties of Sand Modified Resins Used for Bonding CFRP to Concrete Substrates.” International Journal of Sustainable Built Environment 5 (2): 517–525. doi:10.1016/j.ijsbe.2016.06.001.
- Ahmed, Azzam, Shuaicheng Guo, Zuhua Zhang, Caijun Shi, and Deju Zhu. 2020. “A Review on Durability of Fiber Reinforced Polymer (FRP) Bars Reinforced Seawater Sea Sand Concrete.” Construction and Building Materials: 256.
- Al-Attar, Alya’a A., Mazin B. Abdulrahman, Eethar Thanon Dawood, Aziz I. Abdulla, Muyasser M. Juma’Ah, and Hashim A. Rzazk. 2021. “Physicochemical Properties of Modified Epoxy Used for Reinforcing Concrete by Carbon Fiber Reinforced Polymer.” IOP Conference Series: Materials Science and Engineering 1058 (1): 012054. doi:10.1088/1757-899x/1058/1/012054.
- Ali, Ahmed H., Hamdy M. Mohamed, Brahim Benmokrane, Adel ElSafty, and Omar Chaallal. 2019. “Durability Performance and Long-Term Prediction Models of Sand-Coated Basalt FRP Bars.” Composites Part B: Engineering 157: 248–258. doi:10.1016/j.compositesb.2018.08.065.
- Al-khafaji, Ali Fadhil. 2021. “Scholars ’ Mine Fiber Reinforced Polymer Bar Investigation : Long-Term in-Situ Durability and Bond Strength Assessment in Conventional and Sustainable Concrete.” 50–59.
- Almusallam, Tarek H., Yousef A. Al-Salloum, Saleh H. Alsayed, Sherif El-Gamal, and Mohammed Aqel. 2013. “Tensile Properties Degradation of Glass Fiber-Reinforced Polymer Bars Embedded in Concrete Under Severe Laboratory and Field Environmental Conditions.” Journal of Composite Materials 47 (4): 393–407. doi:10.1177/0021998312440473.
- American Society for Testing and Materials. 2012. ”Standard Test Method for Tensile Creep Rupture of Fiber Reinforced Polymer Matrix Composite Bars.” i: 3–8. 10.1520/D7337.
- Anon. n.d. Standard Test Method for Alkali Resistance of Fiber Reinforced Polymer (FRP) Matrix Composite Bars Used in Concrete Construction 1. doi:10.1520/D7705_D7705M-12.
- Arias, Juan Pablo Morales, Analía Vazquez, and Mariano M. Escobar. 2012. “Use of Sand Coating to Improve Bonding Between GFRP Bars and Concrete.” Journal of Composite Materials 46 (18): 2271–2278. doi:10.1177/0021998311431994.
- ASTM D7914. 2021. ”Standard Test Method for Strength of Fiber Reinforced Polymer (FRP) Bent Bars in Bend Locations.” ASTM International December: 1–7. doi:10.1520/D7914.
- Biswas S, Shahinur S, Hasan M and Ahsan Q. 2015. Physical, Mechanical and Thermal Properties of Jute and Bamboo Fiber Reinforced Unidirectional Epoxy Composites. Procedia Engineering 105: 933–939. doi: 10.1016/j.proeng.2015.05.118.
- ASTM D7205/d7205m. 2016. “Standard Standard Test Method for Tensile Properties of Fiber Reinforced Polymer Matrix Composite Bars.” ASTM International. doi:10.1520/D7205.
- Dong, Zhiqiang, Gang Wu, and Yiqian Xu. 2016. “Experimental Study on the Bond Durability Between Steel-FRP Composite Bars (SFCBs) and Sea Sand Concrete in Ocean Environment.” Construction and Building Materials 115: 277–284. doi:10.1016/j.conbuildmat.2016.04.052.
- Han, J. W., S. K. Lee, K. W. Kim, and C. G. Park. 2015. “Tensile Properties of Glass/natural Jute Fibre-Reinforced Polymer Bars for Concrete Reinforcement.” in IOP Conference Series: Materials Science and Engineering, 3–6 August 2015, IOP Publishing Ltd. Vol. 103. Institute of Physics Publishing.
- Hassan, Mohamed, Brahim Benmokrane, Adel ElSafty, and Amir Fam. 2016. “Bond Durability of Basalt-Fiber-Reinforced-Polymer (BFRP) Bars Embedded in Concrete in Aggressive Environments.” Composites Part B: Engineering 106: 262–272. doi:10.1016/j.compositesb.2016.09.039.
- Matrix, Polymer, Composite Materials, Glass-fiber-reinforced Plastic Rod, Compressive Axial, and Force Application. 2010. “Standard Test Method for Tensile Properties of Fiber Reinforced Polymer Matrix Composite Bars 1.” :1–12. doi: 10.1520/D7205.
- Ottosson, David. 2021. Concrete Reinforced with FRP Rebars. Luleå University of Technology, Department of Civil. Civil Engineering, Master’s Level 2021.
- Rahim, N. L., N. M. Ibrahim, S. Salehuddin, S. A. Mohammed, and M. Z. Othman. 2020. “Investigation of Bamboo as Concrete Reinforcement in the Construction for Low-Cost Housing Industry.” IOP Conference Series: Earth and Environmental Science 476 (1). doi:10.1088/1755-1315/476/1/012058.
- Rahman, Md Mizanur, Md Rezaur Rahman, Sinin Hamdan, Md Faruk Hossen, Josephine Chang Hui Lai, and Fui Kiew Liew. 2015. “Synthesis of Cotton from Tossa Jute Fiber and Comparison with Original Cotton.” International Journal of Polymer Science 2015: 1–4. doi:10.1155/2015/470928.
- Saeed, Yasir M., Salam M. Al-Obaidi, Ehab G. Al-Hasany, and Franz N. Rad. 2020. “Evaluation of a New Bond-Type Anchorage System with Expansive Grout for a Single FRP Rod.” Construction and Building Materials 261: 120004. doi:10.1016/j.conbuildmat.2020.120004.
- Saurabh, A. Jaiswal Darji, and A.R. 2014. “To Study Effect of Cotton Fiber on Strength and Durability of Concrete Using Mineral Admixture IJSRD (International Journal for Scientific Research and Development).” 2 (10): 36–38. online:36–38.
- Sharma, P. Arun Pandey, and Aashish Srivastava. 2017. Tensile and Impact Strength Analysis of Cotton Fiber Reinforced Polymer Composites. Arimpie, ELK Asia Pacific Journals.
- Spagnuolo, S, Z Rinaldi, J Donnini, and A Nanni. (2021). Physical, Mechanical and Durability Properties of GFRP Bars with Modified Acrylic Resin (Modar) Matrix. Composite Structures, 262: 113557. doi: 10.1016/j.compstruct.2021.113557.
- Standard, daneshlinkco. ACI 440. 6. 082015Specification for Carbon and Glass Fiber-Reinforced Polymer Bar Materials for Concrete Reinforcement
- Tanks, Jonathon D., Devin K. Harris, and Stephen R. Sharp. 2016. “Mechanical Response of Unidirectional Composite Bars Loaded in Transverse Compression.” Composites Part B: Engineering 97: 18–25. doi:10.1016/j.compositesb.2016.04.051.
- Wang, Meng, and Yaqiang Yang. 2021. “Study on Aging Properties and Degradation Mechanism of FRP Bars.” E3S Web of Conferences 261:1–4. doi: 10.1051/e3sconf/202126102079.
- Zhu B, Liu H, Liu G, Hussain A, Zhang X and Wang X. 2021. Bond Behavior between BFRP Bars and Hybrid Fiber Recycled Aggregate Concrete after High Temperature. Journal of Renewable Materials 9(3): 507–521. doi:10.32604/jrm.2021.013580.