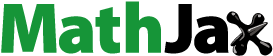
Abstract
Wax-based additives can be added to crumb rubber modified bitumen (CRMB) at different stages to enhance the workability. This study aims to optimize the preparation procedure by investigating the effects of the preparation procedure on the rheological properties of CRMB containing wax-based additives and the interaction mechanism. Rubber swelling tests under various conditions were conducted to examine the effects of temperature and additives on the interaction process. Rheological and thermal characterizations were performed on the CRMB binder and its liquid phase. Results show that reducing the bitumen viscosity by adding wax-based additives can promote the bitumen-rubber interaction and achieve similar swelling results at a lower temperature. However, a significant proportion of wax-based additives were found to penetrate rubber particles for the warm-produced CRMB. Although warm-produced CRMB may save energies compared to hot-produced CRMB, it is not recommended to replace the traditional hot-produced CRMB procedure.
1. Introduction
Bitumen modification using crumb rubber from scrap tires has been increasingly popular in the context of circular economy (Nanjegowda & Biligiri, Citation2020). Although crumb rubber modified bitumen (CRMB) has been reported to improve the rheological and mechanical properties of binders, its high viscosity has caused some concerns. Warm mix asphalt (WMA) technologies are often combined with CRMB technology to solve the high-viscosity related issues, such as high construction temperatures, high energy consumption and greenhouse gas emissions, etc. (Wang et al., Citation2018b). A 10–90°C temperature reduction can be achieved by using different WMA additives. There are generally two types of WMA additives widely used in paving practices, organic additives (in most cases, wax-based additives) and chemical additives. Wax-based additives decrease the viscosity of the mix at temperatures above their melting point and increase the stiffness by solidification into microscopic and uniformly distributed particles when the mixture cools down. In contrast to organic additives, chemical additives do not rely on viscosity reduction to achieve lower mixing and compaction temperatures. Chemical additives usually contain surfactants, polymers or different additives, which can achieve improved coating properties, better mixture workability, and more effective compaction at lower temperatures (Cheraghian et al., Citation2020; Rubio et al., Citation2012). Among various types of WMA additives, wax-based additives have been reported to be effective in improving the rubberised asphalt’s workability without compromising its mechanical properties (Kataware & Singh, Citation2019; Yu et al., Citation2018).
Previous studies have successfully incorporated non-foaming WMA additives into rubberised bituminous materials (Rodríguez-Alloza et al., Citation2017; Yu et al., Citation2016b). The most commonly used procedure is to prepare CRMB binder first, and then add the WMA additive into CRMB during the mixing of CRMB and aggregate. However, there is also a direct mixing method by directly mixing rubber, base binder and additives together. This direct mixing method may lead to further energy savings since the earlier incorporation of additives may reduce the required interaction temperature of bitumen and rubber (Yu et al., Citation2017). The different preparation procedures also lead to different interactions between rubber, bitumen and additives, thus affecting the rheological and mechanical properties of final CRMB binders.
The objective of this study is to investigate the effects of preparation procedure on the rheological properties of CRMB containing wax-based additives and the interaction mechanism. To achieve this objective, rubber swelling tests in bitumen were first conducted to investigate the effects of wax-based additives on the bitumen-rubber interaction process. Then, a series of rheological and thermal characterisation were performed on both CRMB binders and their liquid phases.
2. Materials and methods
2.1. Materials
Penetration grade 70/100 bitumen (Nynas) and fine rubber particles from scrap truck tires (ambient grounding, size ranging from 0 to 0.5 mm) were used to prepare CRMB binders. High shear mixer was applied to mix the blend of base bitumen and rubber (22% by mass of base bitumen) for 30 min at 180°C according to the mixing procedure developed in a previous study (Wang et al., Citation2020b), resulting in binder CRMB-22. Wax-based additive (W), which is a synthetic hard wax free of sulphur and other impurities, was added to base bitumen and CRMB-22. The wax-based additives are greyish-white prills with a melting point of 105–115°C. Based on the manufacturers’ recommendation, the dosage of wax-based additive W was 2.0% for both base bitumen and CRMB binders.
A uniform rubber slice of 2 mm thickness was cut from the truck tire tread (metal fibre free) using the water jet cutting technology. Then, laser cutting was applied on the slice to obtain the rubber cylinders with a diameter of 8 mm. These cylindrical rubber samples (2 mm-thickness and 8 mm-diameter) were subjected to swelling tests in both neat bitumen and wax-additive modified bitumen.
2.2. Preparation procedure of CRMB with wax-based additives
For the base bitumen, wax additives were manually blended with hot bitumen at 140°C for 10 min (designated as 70/100-W). For the CRMB, warm-mix additives were normally added into the hot CRMB at 160°C due to its higher viscosity and manually mixed for 10 min. Considering the viscosity-reduction effect of warm-mix additives, one question emerges: Is it possible to add warm-mix additives to bitumen prior to mixing with rubber to prepare CRMB at lower mixing temperatures (warm-produced) without compromising the rheological properties comparing to the hot blended CRMB (at 180 °C)? The earlier incorporation of warm-mix additives may reduce the required mixing temperature for CRMB and hence save more energy (Leng et al., Citation2017; Yu et al., Citation2017). In contrast to chemical-based liquid additive with volatile components, wax-based additive can keep its effectiveness even being heated several times under certain temperatures. To investigate the effects of preparation procedure, the following procedures were used:
Hot-produced CRMB (H-CRMB). Bitumen and rubber were first mixed at 180°C for 30 min to prepare CRMB. Then wax-based additive was added to the prepared CRMB at 160°C and manually blended for 10 min.
Warm-produced CRMB (W-CRMB). Bitumen, rubber and wax-based additive were blended and mixed at 160°C for 30 min.
To have a further understanding of the interaction mechanism among the components (i.e. bitumen, rubber and wax-based additive), the liquid phases of H-CRMB and W-CRMB were extracted by removing the insoluble CRM particles from the bitumen matrix as shown in Figure (Wang et al., Citation2018a). To allow for a fast and uniform filtration, the heated CRMB samples were manually flattened on the mesh before the drainage. The residual (drained) binders designated as H-CRMB-LP and W-CRMB-LP were collected on an aluminium pan. The extracted liquid phase was stored in the refrigerator immediately to prevent any unwanted aging or reaction.
2.3. Test methods
2.3.1 Rubber swelling tests in bitumen
To examine the effects of wax-based additives on the bitumen-rubber interaction process, rubber swelling tests were conducted in both base bitumen and wax-additive modified bitumen. The reason for using rubber pieces instead of rubber particles for the swelling tests is because loose rubber particles are difficult to trace and collect to investigate their mass or mechanical property changes. To simulate the real CRMB preparation procedures, cylindrical rubber samples were soaked in based bitumen 70/100 at 160°C, 180°C and modified bitumen 70/100-W at 160°C respectively for different time durations (1, 4, 8, 12, 18, 24, 36 h). Gravimetric method (weight gain experiments) was used to monitor the mass uptake of rubber samples after interacting with bitumen. The mechanical properties of rubber samples after swelling were measured by a Dynamic Shear Rheometer (DSR) using frequency sweep tests. The detailed sample preparation and testing procedures as illustrated in Figure can be found in (Wang et al., Citation2020a).
2.3.2 Rotational viscosity (RV)
To examine the effect of preparation procedure on the viscosity of binder, the Brookfield viscometer was used to measure the rotational viscosities of different binders at a constant rotational speed of 20 rpm using the #27 cylindrical spindle. Viscosity tests were conducted at various temperatures, 135, 160, 177 and 190°C, which cover the temperature range of production, transport, and construction (Zhang et al., Citation2015).
2.3.3 Multiple stress creep and recovery (MSCR)
MSCR tests were conducted on CRMB and liquid phase binders to compare their nonlinear viscoelastic properties. MSCR tests were performed at 64°C according to the standard procedure. The two chosen stress levels (0.1 and 3.2 kPa) can characterise both linear and nonlinear responses of binders. The test protocol includes 10 creep (1 s) – recovery (9 s) cycles at each stress level.
2.3.4 Frequency sweep (FS)
FS tests of CRMB and liquid phase binder samples were carried out with a parallel-plate geometry (25 mm diameter and 1 mm gap) from 0.1 to 100 rad/s at temperatures of 10, 30, 50 and 70°C. All the measurements were carried out at a strain level of 0.1% under strain-controlled mode.
FS tests of rubber samples were performed from 0.1 to 100 rad/s over a temperature range of −10∼130°C with an increment of 20°C. According to the previous study (Wang et al., Citation2020a), the measurements were carried out at a strain level of 1% under strain-controlled mode. The viscoelastic parameters (complex modulus and phase angle) of each sample were collected and analysed.
2.3.5 Differential scanning calorimetry (DSC)
To perform the DSC tests, approximately 15 mg of bitumen sample is placed in a DSC cup. The cup is sealed with a lid using a special tool to ensure proper contact between the sample and the bottom surface. The cup containing testing materials was placed in the apparatus and conditioned at 25°C for 5 min. Then the temperature was decreased from 25°C to −60°C. The measurement started after the isothermal conditioning at −60°C for 5 min, with temperature ramping from −60°C to 140°C at a rate of 20°C /min (Soenen et al., Citation2014). The heat flows of test samples were monitored and compared to those of the reference sample (an empty aluminium pan) for further derivations. It is reported the reproducibility on the enthalpies from heating scans is generally better than those from cooling scans. For each binder, three replicates were tested.
3. Results and discussion
3.1. Rubber swelling test
The swelling index (Q), which reflects the process of rubber absorbing bitumen, is defined as follows:
(1)
(1) where
is the mass of original/dry rubber sample, and
is the mass of swollen rubber sample.
The swelling behaviours of rubber samples in different binders were monitored and are presented in Figure in a plot of swelling index versus interaction time. Each data point is an average value of three replicated samples. It can be found that regardless of the bitumen type and temperature, bitumen components were initially absorbed by rubber rapidly and then slowed down. In general, the swelling index increases with swelling time along the logarithmic trend line. Besides, increasing temperature from 160°C to 180°C accelerates the diffusion of bitumen into rubber and hence the swelling of rubber. It is noteworthy that when wax additives were added to the base bitumen, even at 160°C, rubber samples achieve similar swelling degrees comparing to that immersed in base bitumen at 180°C. This indicates that wax additives can promote the interaction between bitumen and rubber, which could compensate the effects of decreasing temperature.
During the rubber swelling test process, it was found the swollen rubber sample became soft and viscous due to the absorption of bitumen components, forming a gel-like structure (Wang et al., Citation2020b; Xu et al., Citation2012). The mechanical properties of swollen rubber samples after 36 h interaction with bitumen were also measured using FS tests to examine the effects of temperature and additives on the interaction process. Since the swollen rubber is not a rheologically simple material, the master curves were established using a generalised logistic function in Equation (Equation2(2)
(2) ) (Rowe et al., Citation2009) and the Williams-Landel-Ferry (WLF) equation for shift factors fitting to form smooth curves.
(2)
(2) where A is either complex shear modulus or phase angle. δ is the lower asymptote; α is the difference between the values of upper and lower asymptote; λ, β and γ define the shape between the asymptotes and the location of the inflection point.
The master curves of complex modulus and phase angle of rubber samples after swelling in different binders at a reference temperature of 30°C were built in Figure . It can be seen that swollen rubber samples exhibit obvious viscoelasticity because of the absorption of viscous bitumen components. When increasing the interaction temperature from 160°C to180°C, rubber polymer chain absorbs more bitumen molecules, resulting in a higher swelling degree and looser networks. This is revealed by the decreased complex modulus and increased phase angle over the frequency range. However, after the addition of wax-based additives into base bitumen, the viscoelastic master curves of rubber samples interacting at 160°C are quite close to that interacting at 180°C. This demonstrates that wax additives can offset the negative influence of reduced temperature on the bitumen-rubber interaction process.
3.2. Rational viscosity test
Figure shows the rotational viscosities of CRMB binders with different preparation procedures at various temperatures. It is obvious that binder viscosity decreases with the increase of testing temperature. CRMB-22 is the rubberised binder without warm-mix additives. Even at 190°C, the rotational viscosity of CRMB-22 has exceeded 4000 mPa·s. Excessively high viscosities of CRMB will impede its application in asphalt production and construction. Based on the recommended specification for rubberised bitumen in California (State of California Department of Transportation, Citation2003), the apparent viscosity of CRMB at 190°C should be in the range of 1500–4000 mPa·s to ensure the proper plant production. Either with hot-produced procedure or warm-produced procedure, the viscosity of CRMB-22 was reduced after the addition of wax-based additives. The viscosity of H-CRMB has reduced to lower than 4000 mPa·s at 190°C, which satisfies the specifications for rubberised bitumen as proposed by Caltrans (California Department of Transportation). By contrast, the viscosity of W-CRMB is still higher than 4000 mPa·s at 190°C, which might cause workability issues when producing asphalt mixtures. Based on a previous study (Leng et al., Citation2017) in which the workability of asphalt mixture samples produced with both H-CRMB and W-CRMB was compared, asphalt mixtures prepared with H-CRMB can achieve the desired mixture density with less compaction efforts at the same mixing and compaction temperatures than W-CRMB does, which indicates a better workability.
3.3. MSCR test
MSCR tests were conducted on CRMB and liquid phase binders to compare their rheological properties. The MSCR test results summarised in Table show that of W-CRMB is slightly lower than that of H-CRMB, indicating higher resistance to permanent deformation. In addition, W-CRMB has a higher elastic recovery than H-CRMB at 3.2 kPa, which implies that different polymer networks and rubber structures may exist within the binder. To further investigate the effect of wax-based additive on the bitumen-rubber interaction process, the liquid phases of these two CRMB binders were also compared in Table .
Table 1. MSCR test results of CRMB and liquid phase binders.
The liquid phase of hot-produced CRMB (H-CRMB-LP) has a very small . Two reasons contribute to this result. First, the light fractions of bitumen were absorbed by rubber particles and therefore, the liquid phase became stiffer because of a large proportion of asphaltenes. Second, the wax-based additives can be completely dissolved into bitumen and remained in the liquid phase after extraction, hence stiffening the binder. Similar explanations are also applicable to the small
value of W-CRMB-LP. However, its
is larger than that of H-CRMB-LP. Results in the previous section have demonstrated that reducing the bitumen viscosity by adding wax-based additives has a similar effect on rubber swelling as increasing the interaction temperature. It was actually shown in a previous study (Wang et al., Citation2021) that the viscosity of neat bitumen at 180°C is very close the viscosity of neat bitumen with wax-based additive at 160°C. If assuming similar bitumen-rubber interactions occurred for both H-CRMB and W-CRMB, the reason for the difference in the non-recoverable compliance is because of the different wax contents in each liquid phase (Yu et al., Citation2016a). This inference will be verified in the following sections.
3.4. Frequency sweep test
A modified Christensen-Anderson-Marasteanu (CAM) model together with the WLF equation was used to develop complex modulus and phase angle master curves for binders based on the frequency sweep test results (Bahia et al., Citation2001). The complex modulus and phase angle master curves of H-CRMB and W-CRMB at a reference temperature of 30°C are shown in Figure (a).
Figure 6. Complex modulus and phase angle master curves of (a) H-CRMB and W-CRMB; (b) the liquid phases of H-CRMB and W-CRMB.
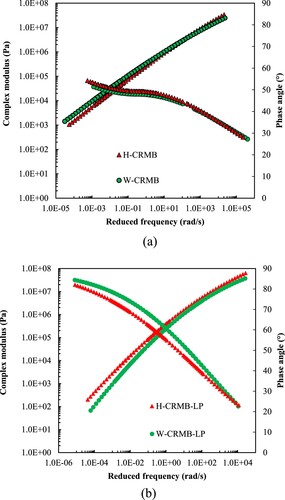
It can be found that the complex modulus and phase angle curves of these two binders are close to each other. The plateaus indicate the presence of rubber networks within the binder. The peculiar feature of phase angle plateau at intermediate frequencies was also observed. W-CRMB is slightly stiffer (higher modulus) and more elastic (lower phase angle) than H-CRMB. In general, the mixing procedure does not significantly influence the bitumen-rubber interaction and hence the binder’s linear viscoelasticity. As stated earlier, the existence of wax-based additive may affect the interaction between bitumen and rubber. In this regard, the viscoelastic master curves of liquid phases of H-CRMB and W-CRMB are compared in Figure (b).
It is obvious that W-CRMB-LP is softer (lower modulus) and more viscous (higher phase angle) than H-CRMB-LP. Since rubber particles were removed from the liquid phase, their contributions to binder viscoelasticity were assumed to be neglected. Again, if assuming similar bitumen-rubber interactions occurred for both H-CRMB and W-CRMB, the difference in rheological properties of these two liquid phases may stem from the wax-based additives. It is reported from previous studies (Wang et al., Citation2018c) that the addition of wax into bitumen can improve the viscoelastic response by increasing the modulus and decreasing the phase angle. Therefore, it is speculated that H-CRMB-LP may have a higher wax content than W-CRMB-LP. This speculation will be further investigated by DSC tests on the liquid phases.
3.5 Differential scanning calorimetry test
To verify the assumption that the higher and lower complex modulus of binder W-CRMB-LP comparing to H-CRMB-LP is because of the less wax content in the liquid phase of the binder, DSC tests were performed on the liquid phases to determine the wax content. Previous studies have demonstrated the applicability and validity of using DSC to determine the wax content in crude oils, residues and bitumens (Lu et al., Citation2008). As described before, wax-based additive W is a synthetic microcrystalline wax which will show a melting peak during the heating process and a crystallisation peak during cooling process in a DSC test (Jamshidi et al., Citation2013). Figure shows a DSC curve of a typical waxy bitumen having a melting peak temperature of 103.7°C during a heating process.
The melting enthalpy, the area underneath the melting peak, is of particular interest because it reflects the total thermal effect of the precipitated wax in the sample. With a known value of melting enthalpy for wax, the wax content in the sample can be estimated using Equation (Equation3(3)
(3) ) (Soenen et al. Citation2014):
(3)
(3) where
is the wax content;
is the melting enthalpy of the bitumen sample;
is the melting enthalpy of wax, which is chosen as 121 J/g for natural wax and 250 J/g for synthetic wax.
For comparison, Figure shows the DSC curves of 70/100, 70/100-W, liquid phases of both H-CRMB and W-CRMB during the heating scan. For clarity, only curves close to the melting region are shown. It is clear that neat bitumen shows no melting signal, which means it is wax free. For the other three binders, they all show a melting peak because of the addition of wax-based additives. The melting peak temperatures of three binders are around 104 °C. However, the respective melting enthalpy is different from each other. The average melting enthalpies for 70/100-W, H-CRMB-LP and W-CRMB-LP are 4.27, 4.01 and 2.34 J/g respectively. According to Equation (1), melting enthalpy of 250 J/g for synthetic wax was used to estimate the wax content of each binder. The estimated wax contents of 70/100-W, H-CRMB-LP, W-CRMB-LP are respectively 1.71%, 1.60% and 0.94%. The estimated wax contents of 70/100-W is close to the dosage of additive W. The estimated wax content of H-CRMB-LP is lower than that of 70/100-W, which is probably because some additives were remained on/in the rubber particles after the extraction process. W-CRMB-LP shows the lowest wax content of 0.94%, indicating a large portion of the wax-based additives penetrated into rubber particles (Yu et al., Citation2016a).
4. Conclusions and recommendations
A two-stage study was conducted to investigate the effects of preparation procedure on the rheological properties of CRMB containing wax-based additives and the interaction mechanism. Rubber swelling tests under various conditions were conducted to examine the effects of temperature and additives on the interaction process. Reducing the bitumen viscosity by adding wax-based additives can promote the bitumen-rubber interaction and achieve similar swelling results at a lower temperature. The influence of preparation procedure on CRMB containing warm-mix additives was also investigated from both rheological and thermal characteristics. In general, warm-produced CRMB (mixing bitumen, rubber and additives together at a lower temperature) slightly improved the rheological properties by increasing the modulus and elasticity compared to hot-produced CRMB. However, it was found that a significant proportion of wax-based additives penetrated rubber particles for the warm-produced CRMB procedure. This may cause workability issues when producing asphalt mixtures with W-CRMB. This is mainly because the absorbed wax-additives in rubber particles cannot effectively reduce the binder viscosity and function as a lubricator to improve the workability. From this perspective, although warm-produced CRMB may save energies compared to hot-produced CRMB, it is not recommended to replace the traditional hot-produced CRMB procedure.
The above findings are based on limited material combinations, other types of WMA additives will be investigated to generalise the findings in the current study. Effects of preparation procedures on the performance of warm rubberised mixtures as well as the quantitative estimation of energy saving for the purpose of life cycle assessment should be investigated in the future study.
Disclosure statement
No potential conflict of interest was reported by the author(s).
Additional information
Funding
References
- Bahia, H. U., Hanson, D. I., Zeng, M., Zhai, H., Khatri, M. A., & Anderson, R. M. (2001). Characterization of modified asphalt binders in superpave mix design. Transportation Research Board.
- Cheraghian, G., Cannone Falchetto, A., You, Z., Chen, S., Kim, Y. S., Westerhoff, J., Moon, K. H., & Wistuba, M. P. (2020). Warm mix asphalt technology: An up to date review. Journal of Cleaner Production, 268. https://doi.org/10.1016/j.jclepro.2020.122128
- Jamshidi, A., Hamzah, M. O., & You, Z. (2013). Performance of warm mix asphalt containing sasobit®: State-of-the-art. Construction and Building Materials, 38, 530–553. https://doi.org/10.1016/j.conbuildmat.2012.08.015
- Kataware, A. V., & Singh, D. (2019). Dynamic mechanical analysis of crumb rubber modified asphalt binder containing warm mix additives. International Journal of Pavement Engineering, 20(9), 1044–1054. https://doi.org/10.1080/10298436.2017.1380806
- Leng, Z., Yu, H., Zhang, Z., & Tan, Z. (2017). Optimizing the mixing procedure of warm asphalt rubber with wax-based additives through mechanism investigation and performance characterization. Construction and Building Materials, 144, 291–299. https://doi.org/10.1016/j.conbuildmat.2017.03.208
- Lu, X., Kalman, B., & Redelius, P. (2008). A new test method for determination of wax content in crude oils, residues and bitumens. Fuel, 87(8-9), 1543–1551. https://doi.org/10.1016/j.fuel.2007.08.019
- Nanjegowda, V. H., & Biligiri, K. P. (2020). Recyclability of rubber in asphalt roadway systems: A review of applied research and advancement in technology. Resources, Conservation and Recycling, 155. https://doi.org/10.1016/j.resconrec.2019.104655
- Rodríguez-Alloza, A. M., Gallego, J., & Giuliani, F. (2017). Complex shear modulus and phase angle of crumb rubber modified binders containing organic warm mix asphalt additives. Materials and Structures, 50(1), 77. https://doi.org/10.1617/s11527-016-0950-1
- Rowe, G., Baumgardner, G., & Sharrock, M. (2009). Functional forms for master curve analysis of bituminous materials. Advanced Testing and Characterisation of Bituminous Materials, 1 and 2, 81-+. Available from: <Go to ISI>://WOS:000280392100009
- Rubio, M. C., Martínez, G., Baena, L., & Moreno, F. (2012). Warm mix asphalt: An overview. Journal of Cleaner Production, 24, 76–84. https://doi.org/10.1016/j.jclepro.2011.11.053
- Soenen, H., Besamusca, J., Fischer, H. R., Poulikakos, L. D., Planche, J.-P., Das, P. K., Kringos, N., Grenfell, J. R. A., Lu, X., & Chailleux, E. (2014). Laboratory investigation of bitumen based on round Robin DSC and AFM tests. Materials and Structures, 47(7), 1205–1220. https://doi.org/10.1617/s11527-013-0123-4
- State of California department of transportation. (2003). Asphalt rubber usage guide. Caltrans.
- Wang, D., Li, D., Yan, J., Leng, Z., Wu, Y., Yu, J., & Yu, H. (2018). Rheological and chemical characteristic of warm asphalt rubber binders and their liquid phases. Construction and Building Materials, 193, 547–556. https://doi.org/10.1016/j.conbuildmat.2018.10.199
- Wang, H., Liu, X., Apostolidis, P., Erkens, S., & Skarpas, A. (2020a). Experimental investigation of rubber swelling in bitumen. Transportation Research Record: Journal of the Transportation Research Board, 2674(2), 203–212. https://doi.org/10.1177/0361198120906423
- Wang, H., Liu, X., Apostolidis, P., & Scarpas, T. (2018a). Review of warm mix rubberized asphalt concrete: Towards a sustainable paving technology. Journal of Cleaner Production, 177, 302–314. https://doi.org/10.1016/j.jclepro.2017.12.245
- Wang, H., Liu, X., Apostolidis, P., & Scarpas, T. (2018b). Rheological behavior and its chemical interpretation of crumb rubber modified asphalt containing warm-mix additives. Transportation Research Record: Journal of the Transportation Research Board, 2672(28), 337–348. https://doi.org/10.1177/0361198118781376
- Wang, H., Liu, X., Apostolidis, P., Wang, D., Leng, Z., Lu, G., Erkens, S., & Skarpas, A. (2021). Investigating the high- and low-temperature performance of warm crumb rubber–modified bituminous binders using rheological tests. Journal of Transportation Engineering, Part B: Pavements, 147(4). https://doi.org/10.1061/JPEODX.0000326
- Wang, H., Liu, X., Zhang, H., Apostolidis, P., Scarpas, T., & Erkens, S. (2020b). Asphalt-rubber interaction and performance evaluation of rubberised asphalt binders containing non-foaming warm-mix additives. Road Materials and Pavement Design, 21(6), 1612–1633. https://doi.org/10.1080/14680629.2018.1561380
- Xu, B., Di, X., & Mckenna, G. B. (2012). Swelling behavior of cross-linked rubber: Explanation of the elusive peak in the swelling activity parameter (dilational modulus). Macromolecules, 45(5), 2402–2410. https://doi.org/10.1021/ma202631u
- Yu, H., Leng, Z., Dong, Z., Tan, Z., Guo, F., & Yan, J. (2018). Workability and mechanical property characterization of asphalt rubber mixtures modified with various warm mix asphalt additives. Construction and Building Materials, 175, 392–401. https://doi.org/10.1016/j.conbuildmat.2018.04.218
- Yu, H., Leng, Z., & Gao, Z. (2016a). Thermal analysis on the component interaction of asphalt binders modified with crumb rubber and warm mix additives. Construction and Building Materials, 125, 168–174. https://doi.org/10.1016/j.conbuildmat.2016.08.032
- Yu, H., Leng, Z., Xiao, F., & Gao, Z. (2016b). Rheological and chemical characteristics of rubberized binders with non-foaming warm mix additives. Construction and Building Materials, 111, 671–678. https://doi.org/10.1016/j.conbuildmat.2016.02.066
- Yu, H., Leng, Z., Zhou, Z., Shih, K., Xiao, F., & Gao, Z. (2017). Optimization of preparation procedure of liquid warm mix additive modified asphalt rubber. Journal of Cleaner Production, 141, 336–345. https://doi.org/10.1016/j.jclepro.2016.09.043
- Zhang, J. P., Yang, F. H., Pei, J. Z., Xu, S. C., & An, F. W. (2015). Viscosity-temperature characteristics of warm mix asphalt binder with Sasobit®. Construction and Building Materials, 78, 34–39. Available from: <Go to ISI>://WOS:000350929900005. https://doi.org/10.1016/j.conbuildmat.2014.12.123