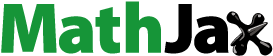
ABSTRACT
Ammonia, as an essential and economical fuel, is a key intermediate for the production of innumerable nitrogen-based compounds. Such compounds have found vast applications in the agricultural world, biological world (amino acids, proteins, and DNA), and various other chemical transformations. However, unlike other compounds, the decomposition of ammonia is widely recognized as an important step towards a safe and sustainable environment. Ammonia has been popularly recommended as a viable candidate for chemical storage because of its high hydrogen content. Although ruthenium (Ru) is considered an excellent catalyst for ammonia oxidation; however, its high cost and low abundance demand the utilization of cheaper, robust, and earth abundant catalyst. The present review article underlines the various ammonia decomposition methods with emphasis on the use of non-noble metals, such as iron, nickel, cobalt, molybdenum, and several other carbides as well as nitride species. In this review, we have highlighted various advances in ammonia decomposition catalysts. The major challenges that persist in designing such catalysts and the future developments in the production of efficient materials for ammonia decomposition are also discussed.
IMPACT STATEMENT
In this dynamic area, ammonia degradation to hydrogen fuel provides a valuable contribution in the carbon neutral economy. Ammonia has been used extensively in several industries and is considered an ideal candidate for hydrogen generation and storage due to its high hydrogen content. Consequently, the ammonia decomposition to yield green hydrogen has become a hot topic in research. Although numerous studies on ammonia decomposition have been conducted over the last few decades, still very few review articles on the most recent advances in this field of catalysis have been published. Through this review, systematic information on the types of decomposition catalysts including both noble (Ru) and non-noble earth abundant metals such as iron, nickel, cobalt, molybdenum, their carbides and nitrides, catalytic routes, as well as the reactivity and mechanism can be comprehended. The literature on newly discovered catalysts, specifically from the last five years, is well documented and explained in this review article. Furthermore, the effect of catalyst supports, their reaction kinetics and mechanistic insights have also been discussed. The challenges and opportunities associated with the decomposition catalysts are comprehensively explicated in the end.
HIGHLIGHTS
Ammonia decomposition reaction (ADR) is a viable method for hydrogen storage in the form of chemical bonds.
Catalysts composed of noble, non-noble metals, amides, imides, carbides, nitrides, and their combinations have been widely explored towards the ADR.
Challenges and opportunities in the ammonia oxidation are pointed out.
1. Introduction
Owing to the rising demand for energy and depleting fuel reserves, the consumption of valuable fossil feedstocks has become inevitable. Fossil fuels form an important source of a variety of hydrocarbons and energy carrier in the world [Citation1,Citation2]. However, the widely increasing population and excess industrialization have made them a huge polluter [Citation3]. Despite the known damaging effects of fossil fuels, their excellent applications are undeniable. Fossil fuels such as coal, petroleum, and natural gas meet around 90% of the world’s total energy demand [Citation4]. However, their utilization involves the burning process which liberates a significant amount of carbon dioxide to the environment [Citation5]. The achievement of carbon neutrality, in which CO2 released into the atmosphere is balanced by an equivalent amount removed, is far too important for a sustainable environment [Citation6,Citation7]. Therefore, there is a serious need to replace fossil fuels with an alternate fuel that must be convenient and as effective. Ammonia is one of the key components released by the combustion of fossil fuels. Globally, more than 70% of ammonia is generated by the burning of fossil fuels [Citation8]. However, it emerges as a key solution towards the clean energy requirement of the world. Ammonia is involved as an important building block for the manufacture of a range of chemicals such as from fertilizers to fuels [Citation9]. According to the reports published by the Royal Society in 2020, ammonia has been regarded as a zero-carbon fertilizer, fuel, and energy store. The average energy density of ammonia is about 3 kWh/litre, which is less than fossil fuels but still comparable in terms of its energy storage properties () [Citation10]. Moreover, the power conservation capacity of ammonia (20.1 MJ/kg) is the same as that of methane (18.6 MJ/kg). The sole difference lies in the oxidation process, while latter releases CO2, the former releases N2 gas into the atmosphere. The global data estimated that the rise in annual ammonia production from 235 million meter in 2019 up to 290 million metric tons by the end of the year 2030 (). This significant rise is due to the enormous population growth and vast growth in the industrialization. Ammonia is considered as a zero-carbon energy vector for the future generation. However, it is not economically viable to store and transport hydrogen on a massive scale in its pure form. In contrast, the use of ammonia as a hydrogen-based synthetic fuel or as a hydrogen template appears to be extremely favourable.
Figure 1. (a) Energy density of a range of chemical fuels. (b) Estimated rise in annual ammonia production.
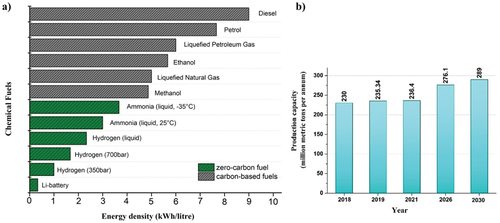
Over the past few decades, ammonia is the world’s second most produced chemical after sulfuric acid (globally over 200 million tons per annum). With expanding potential applications like its utilization in the feed stock and agriculture sector, its world production could rise by several orders of the magnitude. The primary benefit of ammonia is that it contains 40% more hydrogen than methanol and can be produced from renewable hydrogen and nitrogen without the utilization of any carbon-based species [Citation11]. However, the utilization of ammonia for their application in various power technologies offers certain challenges and requirements as provided below () [Citation12].
Table 1. Fuel-associated ammonia technologies.
Ammonia is regarded as the most significant option in terms of developing green energy production techniques and simultaneously satisfying the need for sustainable production of chemical fuels or building block chemicals. Moreover, ammonia decomposition reaction (ADR) is regarded as the most environmentally benign, energy efficient, and economically viable step in achieving sustainable future goals. Although ecological awareness has led to the usage of solar energy, geo thermal energy, and hydro energy as a replacement of fossil fuels, their restricted operating conditions limit their practices and hence their execution at individual level will still take time. Considering all these points, the reliable answer is hydrogen which again is directly linked with the production as well as degradation of ammonia gas. As per existing electrolysers technique, the production of 1 kg of H2 from fuel combustion causes an amount of 8.8 kg of CO2 emission [Citation13]. In contrast to this, the only by-product ammonia degradation generated in addition to H2 would be nitrogen gas (N2). As a result, no additional handling of greenhouse emissions (GHE) is required [Citation14]. The International Energy Agency (IEA) has proposed a roadmap guide for net zero energy goals by the year 2050 (). That means that there would be a huge decline in the use of fossil fuels and the energy sectors would be based on the supply of renewable sources only [Citation15].
Figure 2. Estimated net zero carbon energy goals from 2020 till the end of the year 2050 (citation: 2020, International Energy Agency (IEA)).
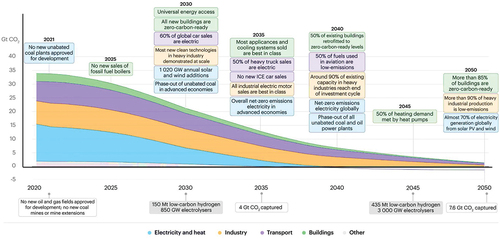
The concept of using ammonia as a source of hydrogen is not recent, and the process of cracking or more profoundly called as ammonia decomposition to produce forming gas (H2 + N2) has long been employed on a vast scale in industries [Citation16]. Breaking of nitrogen-hydrogen bonds in ammonia (NH3) results in a net energy gain that affects in the production of nitrogen and hydrogen together with oxygen [Citation17]. Significantly, this indicates that green hydrogen could be produced sustainably using only selective catalyst, assuming sustainable energy is employed to power the operation. For a wide range of applications, hydrogen and nitrogen have the potential to be cost-effective net-zero energy sources and carriers. To more precisely assess this potential, development, demonstration, and deployment are essential.
In this perspective review article, the clean ammonia as a prospective to achieve zero-carbon solution is explored. Furthermore, different types of catalysts which show promising results to achieve hydrogen production are discussed. Considering the fact that a review which covers all types of ammonia degradation catalysts is yet to be reported, the present review article discusses all classes of effective catalysts with their activities and properties.
2. Ammonia as carrier for sustainable hydrogen production
Hydrogen, as an energy carrier, is becoming increasingly important in achieving a transition to a low carbon of hard-to-abate sectors. Industries, including refining, fertilizers, and steel industries, emit large amount of carbon dioxide and, therefore, carbon-free hydrogen will be essential to allowing deep emissions reductions. Hydrogen is one of the major options being studied with the potential to be the preferred alternative for many applications. Hydrogen can be produced using a number of methods. Different organic as well as inorganic materials such as fossil fuels, biomass, or water release hydrogen gas upon treatment [Citation18]. Some microbial and bacterial species even produce hydrogen through different biochemical ways ().
Natural gas reforming, or more commonly known as steam reforming or hydrocarbon reforming process, is one of the most widely used processes by industries on a larger scale for H2 production. Here, high-temperature steam, 700–1000°C, is passed through methane gas to produce syngas (CO + H2), further through water gas shift reaction, carbon monoxide is converted to carbon dioxide with simultaneous production of large amount of heat [Citation19]. Apart from this, coal gasification and hydrocarbon pyrolysis are other ways of producing hydrogen through fossil fuel combustion [Citation20,Citation21]. An overview of various hydrogen production methods using non-renewable energy sources is provided in .
Table 2. Summary of the basic conditions for H2 production through non-renewable sources.
However, the other way is to produce hydrogen through the energy provided by renewable sources. In this category, water electrolysis as well as ammonia decomposition are widely recognized processes [Citation22,Citation23]. Low-carbon-footprint hydrogen can minimize CO2 emissions and thus limit the global temperature to 2°C. Different technologies based on electro-, photo-, and bio-oxidation for hydrogen production have been provided in .
Table 3. Different hydrogen production technologies from a renewable source of water.
Probably, the water splitting from ammonia is considered the most promising way to obtain H2 with simultaneous oxygen production. In an overall reaction, two reactions take place in each electrode, the anode and the cathode to convert electrical energy into chemical energy that is released in the form of hydrogen and oxygen as a by-product, EquationEquations (1)(1)
(1) –(Equation3
(3)
(3) ).
Similarly, solar water splitting, or photolytic, processes the breakdown of water into hydrogen and oxygen using light energy [Citation24]. While still in varied early stages of development, these procedures have the potential to produce sustainable hydrogen in the future with minimal impact on the environment. However, the effectiveness of production is heavily dependent on the geographic setting, i.e. periods of maximum prolonged wind and/or high solar irradiation, and as a result, the produced H2 must be stored or carried over extremely long distances to the consumers. Moreover, the storage and transportation of hydrogen faces a number of inherent challenges [Citation25]. H2 is frequently liquefied at very low temperatures and under high pressure. Due to the lower density of H2 and the relatively huge weight of the carrying vessel, H2 still has a low energy density, even at high pressure [Citation26]. Additionally, compression requires 10–13% of the hydrogen’s net energy, making it an energy-intensive process. Hydrogen may be carried as a liquid by cooling it to below 20 K [Citation27]; however, the energy required to liquefy reduces the net energy content (consume approximately by 40%). Additionally, the high combustible range of H2 (5–75%) demands extra care while transporting, storage, and use [Citation28]. Hence, considering all such limitations, ADR represents an extremely interesting and promising way for H2 production since only N2 is generated as a by-product and it can be easily liquified at ambient pressure (8–10 bar). ADR process operates endothermically at slightly high temperature and low pressure, according to EquationEquation (4)(4)
(4) [Citation29].
Compared with the water splitting, ammonia decomposition requires substantially less energy to take place since it may spontaneously combine with oxygen to form N2O and produce a lot of heat, which powers water splitting [Citation12]. Simultaneous N2O breakdown happens when exposed to light. As a result, ammonia may be able to generate hydrogen by utilizing oxygen to promote the breakdown of water.
A catalytic pathway influences ammonia degradation via endothermic reactions and the reverse process of ammonia synthesis. Furthermore, this reaction mechanism entails the entire dehydrogenation process in a stepwise manner, with hydrogen and nitrogen desorption occurring at the end of the reaction. Considering the choice of catalyst which significantly promotes the modification of the strong basic components induces the potential active species and accelerates the nitrogen desorption step via the electron transfer mechanism. In this paper, we reviewed a number of research trends that were carried out by utilising various classes of proficient catalysts for highly efficient ammonia decomposition.
3. Ammonia decomposition catalysts
In recent years, researchers have used different materials such as noble metal, non-noble metal, single-atom, and defect materials to obtain higher NH3 yield rates and better Faradaic efficiency. Since the decomposition of ammonia is the inverse reaction of the Haber-Bosch process for the synthesis of ammonia, initially the same catalysts which are used for the synthesis, i.e. Ru and Fe, were considered for the thermal decomposition of ammonia assuming the principle of micro reversibility in heterogeneous catalysis [Citation30]. Afterward, Cu-based catalysts were studied as well as other metals [Citation31,Citation32], including Ni [Citation33,Citation34], Ir [Citation35,Citation36], Mo [Citation37], Co [Citation14,Citation38,Citation39], Pt [Citation40], Pd [Citation41], Ru [Citation42,Citation43] and Rh [Citation44] and different combinations of metals and non-metals [Citation45]. The effect of alkaline earth metals (Mg, Ca, Sr, and Ba) over Ni/Y2O3 catalysts for ammonia decomposition has been studied, with remarkable results achieved for Sr and Ba modification and no significant results obtained with Mg and Ca [Citation45]. The catalytic performance was improved upon reaching at 500°C, their physical characterization, percentage conversion, and stability test of prominent catalyst have been shown in .
Figure 4. Catalytic activity for ammonia decomposition over alkaline earth metals modified Ni/Y2O3; (a) TEM images, (b) particle size distribution, (c) NH3 conversion percentage, and (d) stability performance of SrO-Ni/Y2O3 (5:40 wt%), (copyright @ 2016 RSC Advances).
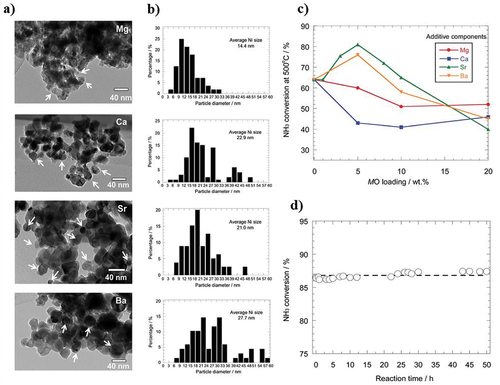
Ruthenium supported on various oxides or structured and unstructured carbon has been reported to have the highest catalytic activity for the breakdown of ammonia among the catalysts investigated in the literature, with deactivation being the main issue. Ruthenium, however, is a rare, expensive noble metal that is rare in nature. This is why inexpensive catalytic compositions with catalytic activity similar to ruthenium’s have been aggressively sought after.
3.1. Noble metals as ammonia decomposition catalysts
The resistance of the noble metals to oxidation and corrosion is used to classify them. Although there is no clear definition for them, Ru, Rh, Pd, Ag, Re, Os, Ir, Pt, and Au are frequently taken into consideration [Citation46]. However, ruthenium is a noble metal that has been the focus of most research as a catalyst for ammonia oxidation.
3.1.1. Ruthenium (Ru)
The catalyst Ru/CNTs (ruthenium supported on carbon nanotubes) promoted with Cs (20 weight percent) was described by Hill and Torrente-Murciano as the one thought to be the most active to date in the decomposition of ammonia [Citation47]. In a subsequent investigation, they prepared the same catalysts with the carbon nanotubes graphitized and with a reduced Cs concentration (4 wt%). Under the same reaction conditions, they obtained a considerable increase in conversion compared to the catalyst with the support without graphitization. It is important to note that nitrogen doping modifies the characteristics of carbon and further boosts the catalyst’s catalytic activity [Citation48]. Comparing Ru supported on ordered mesoporous carbon (OMC) doped with nitrogen to other types of carbon (CNTs, activated carbon, or undoped OMC), the former showed a high catalytic activity [Citation49]. Generally speaking, carbon nanofibers are shown to be the best support for Ru, showing comparable catalytic activity to Ru/CNTs [Citation50]. In this work, the conversion of NH3 increases noticeably (from 45% to 95%) at 450°C, when the membrane is used. A schematic bimodal and monomodal catalytic membrane, catalytic activities, and their morphologies have been represented in .
Figure 5. Incorporation of catalytic membrane for ADR process. (a) Schematic catalytic membrane reactor, (b) catalytic activities, (c) TEM image of bimodal, (d) TEM image of monomodal, and e) SEM image of bimodal catalytic membrane (copyright @ 2011 Elsevier). (f) Mechanistic interaction of Ru doping in LaxCe1-xOy composites and (g) catalytic performance by varying different temperature for NH3 conversion (copyright @ 2021 Elsevier).
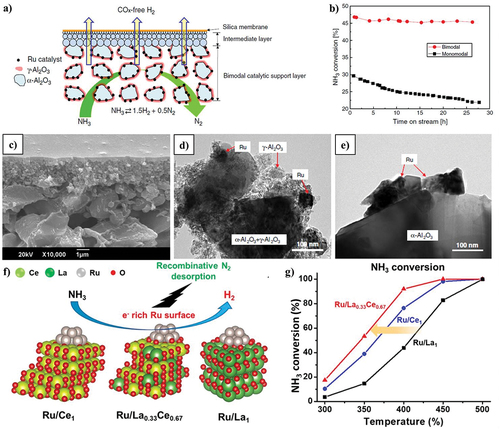
Ru-based catalyst’s simplicity has been shown to be crucial. Bajus et al. investigated to see if Ru/Al2O3 could be promoted using the same alkali metals that exhibited a promoting effect on Ru supported on carbon [Citation51]. The three metals Li, Na, and Cs are said to be able to help the catalyst, according to their report. The turn-over frequency (TOF) quantifies the activity of the catalytic centre by utilizing the number of molecular reaction or catalytic cycles occurring at the centre per unit time. The TOF for Na and Cs was around double that of the unpromoted catalyst, with Li showing the greatest increase (0.26 vs 0.05 s−1 at 350°C). Sayas et al. found that CaO, the most fundamental support of the materials utilised, produced the best catalytic activity when comparing catalysts based on Ru promoted with K supported on different materials (CNTs, MgO, and CaO) [Citation33]. In comparison to two extensively used supports in the literature, carbon nanotubes and SiO2, the Ru supported on a layered oxide consisting of Ca and Al (CaAlOx) had a higher conversion (78 vs 21 and 62% at 450°C, respectively) [Citation52]. Similar to this, Hayashi et al. compared the outcomes with conventional catalysts of Ru supported on CaO, Al2O3, and MgO and evaluated electride, [Ca24Al28O64]4+(O2-)2, and mayenite oxide as supports [Citation53]. They also made catalysts for Ru/MgO and Ru/C stimulated by K and Cs, respectively. The catalyst supported on [Ca24Al28O64]4+(e−)4 demonstrated the best conversion at comparatively low temperatures (400°C). When added to an alumina support, barium has also demonstrated its ability to promote catalytic activity. For instance, compared to conventional supports such as MgO, Al2O3, and CNTs, Ru supported on barium hexaaluminate (BHA) has enhanced catalytic activity that is approximately 4 times higher than MgO and more than double that of carbon nanotubes. Pure ammonia at 450°C was used and reported to have extremely good stability for 60 h [Citation54]. Nagaoka et al. conducted a thorough investigation of the catalytic activities of Ru supported on Pr6O11. The promoted Pr6O11 underwent ammonia conversion in the order Cs2O > Rb2O > K2O > Na2O, where Cs2O is the most fundamental oxide [Citation55]. The ammonia conversion of Ru/Pr6O11 enhanced by Cs2O was extremely high. They found that the non-promoted Ru/Pr6O11 catalyst has comparable catalytic activity to Ru supported on other oxides, such as Ru/La2O3. Recently, Thien An Le et al. reported a co-precipitated procedure for synthesising a noble catalyst for the low-temperature decomposition of ammonia by doping Ru in LaxCe1-xOy () [Citation56]. The results show that the prepared Ru composite demonstrated the best catalytic performance at temperatures below 400°C () by maintaining its stability performance for more than 100 h.
In addition to it, iridium, palladium, platinum, and rhodium are other noble metals that have been examined in the nitrification of ammonia [Citation57–60]. For instance, Maeda et al. demonstrated higher catalytic activity utilising Rh/SiO2 boosted with niobium (Nb) compared to a catalyst made of Rh supported on Nb2O5 [Citation61]. Richardson et al. examined platinum supported on alumina and found limited catalytic activity [Citation62]. lists some catalysts based on ruthenium and other noble metals with their catalytic performances towards ammonia decomposition.
Table 4. Catalysts based on noble metals utilization to decompose ammonia.
3.2. Non-noble metals as ammonia decomposition catalysts
Nickel is the non-noble metal that has received the most attention among those utilized as catalysts for the breakdown of ammonia because of its extraordinary activity. Once more, the catalytic performance is significantly impacted by the type of support. When comparing the transition metals Ni, Fe, and Co distributed in an alumina matrix, Gu et al. found that the cobalt catalyst had the highest catalytic activity, followed by the Ni catalyst [Citation83], while the Fe/Al2O3 catalyst had the lowest catalytic activity. After more than 70 h, all three catalysts demonstrated high stability for the degradation reaction. The catalysts supported on MgO modified with La and on CNTs produced the same order of catalytic activity. Similar to this, Yan et al. found that the Co catalyst has a higher activity (85 vs. 30% conversion at 500°C) when comparing the breakdown of ammonia in the presence of Fe and Co catalysts [Citation84]. On the other hand, both catalysts displayed a decline in activity following a second reaction cycle, despite the fact that the addition of lanthanum to the catalyst improved both catalysts’ stability. When comparing the catalytic outcomes of several low-ordered carbon types with and without the addition of Fe or Ca, Xu et al. demonstrated that adding Fe to the catalyst can boost conversion while adding Ca has a negative impact on the reaction.
3.2.1. Monometallic catalysts
There have been numerous monometallic catalysts; however, few of them such as nickel, iron, cobalt, and molybdenum have been widely utilized in their active phase for ammonia decomposition reaction [Citation14].
3.2.1.1. Nickel (Ni)
As was already indicated, the industrial ammonia crackers use commercially available catalysts that are largely made of nickel supported on alumina. According to the research given by Zhang et al., the best TOF with Ni/Al2O3 catalysts is produced with metallic Ni particles ranging in size from 1.8 to 2.9 nm [Citation85], and doping alumina with lanthanum boosts the catalytic activity. In this study, La could partially reduce the particle size of Ni0 and thus influence the kinetic results of Ni/Al2O3 and Ni/La-Al2O3 catalysts at 733–813 K. In this regard, Yan et al. developed a porous microsphere catalyst made of Ni, Ni0.5Ce0.5Ox, Ni0.5Al0.5Ox, or Ni0.5Ce0.1Al0.4Ox, and concluded that the catalyst made of nickel and cerium performed better than Ni0.5Al0.5Ox, while Ni0.5Ce0.1Al0.4Ox increased the stability of the catalyst [Citation84]. Rare earth promoters seem to have a good impact on Ni’s catalytic activity. Okura et al. discovered that the promoting effect on the Ni/Al2O3 catalyst followed the path La > Pr > Nd > Y > Sm > Eu Gd > Ce [Citation86].
Silica has also been studied as a support for nickel catalysts in a variety of forms, including SiO2, mesoporous frameworks, and as a natural mineral [Citation87]. Choudhary et al. examined a variety of Ni supported on different silica and zeolite types (HY and H-ZSM-5) as well as a catalyst based on a silica and alumina combination, resulting in the following catalytic activity rankings: Al2O3-SiO2 > SiO2~HY > H-ZSM-5. At temperatures below 650°C, it was discovered that the catalyst with the lowest pore diameter (7.7 nm) displayed the maximum activity, however at higher temperatures, the conversion was higher with wider pores as a result of internal mass transfer problems. Zirconium-based supports are another class of substances that have been tested as Ni supports. When ZrO2 was evaluated as a dopant for an alumina support, for instance, Henpraserttae et al. found that the catalyst’s ammonia conversion increased by 11% at 500°C compared to the catalyst supported exclusively on alumina. When compared to a catalyst that had the promoter supplied directly to the active Ni phase, the catalyst supported on the oxide mixture demonstrated greater catalytic activity. A larger dispersion of Ni and an increase in basic sites are credited with the Zr-doped sample’s improved activity [Citation88,Citation89].
3.2.1.2. Iron (Fe)
A natural iron mineral with impurities of TiO2, CaO, Al2O3, K2O, SiO2, and Mn made up a catalyst that had strong activity but was unstable over time, with a quick decline in a 3 h test. An exclusively made of Fe2O3 reference catalyst produced the same behaviour. Tseng et al. asserted through in-situ studies that the active form of catalysts made of Fe is Fe3Nx, while FeNx is generated at high temperatures (>675°C), which has a detrimental effect on the conversion of ammonia [Citation90]. At 500°C, a Fe2O3 catalyst based on SBA-15 mesoporous silica has higher catalytic activity than iron oxide alone (18 vs. 4%). Fe nanoparticles encased in silica are significantly more active (conversion of 9 vs 27% at 500°C), according to research by Li et al. It has been shown that Fe is substantially more stable for the reaction when it is encapsulated in SiO2. Li et al. found that adding Cs to this catalyst increased the ammonia conversion at 450°C by about twofold compared to the catalyst without promoting [Citation91]. Additionally, under the same reaction conditions, the catalytic activity increased when Fe nanoparticles were enclosed in Al2O3 (9 vs. 4% at 450°C). Cui et al. evaluated the activities of iron oxide alone and iron oxide modified with cerium or titanium oxide, finding that the composite catalysts produced a higher and more stable conversion over time [Citation92]. In this study, iron-based nanostructured composites were utilized for NH3 decomposition in a fixed-bed continuous-flow quartz reactor by varying different catalytic temperatures (400–650°C) (). The composite catalyst has high stability when heated by ramping the temperature to 600°C for 60 h, shown in (). Their morphologies of fresh and used Fe3O4/composites show spherical shapes with average particle sizes of 100 nm. It is important to note that the modification using ceria was the most successful. Compared to nickel, Fe and carbon-based supports work better together. In comparison to Ni/Al2O3 and Fe supported on a mixture of carbon and SBA-15, supported on ordered mesoporous carbon CMK-5, Fe demonstrated better catalytic activity (74 vs. 32 and 29% at 600°C, respectively). When graphitized carbon (GC) is employed as a support for Fe, great activity and stability can also be attained. Furthermore, when potassium (K) is introduced to Fe catalyst supported on GC, the rate of ammonia decomposition increases [Citation93]. It has been concluded that the study based on ceria, which has rich oxygen vacancies, and its oxides based supported metal composites has a positive impact on the reduction, dispersion, and stabilisation in NH3 decomposition, as demonstrated by the various catalytic performance shown in the () [Citation70,Citation94,Citation95].
Figure 6. Varying different temperature for NH3 conversion over iron-based nanostructured composites (a) 1st catalytic performance, (b) 2nd catalytic performance, and (c) stability performance (copyright @ 2015 Elsevier). Varying different temperature for NH3 conversion over ceria-based oxide supported nickel composites (d) catalytic performance, (e) Arrhenius plot, and (f) stability performance (copyright @ 2020 Elsevier). (g) Varying different temperature for NH3 conversion over ceria-based oxide supported Ni, Ru, and Ni-Ru composites (copyright @ 2019 Elsevier), varying different temperature for NH3 conversion over ceria-based oxide supported Ru/Al2O3 composites. (h) Comparative study with literature reports and (i) catalytic performance (copyright @ 2023 Elsevier).
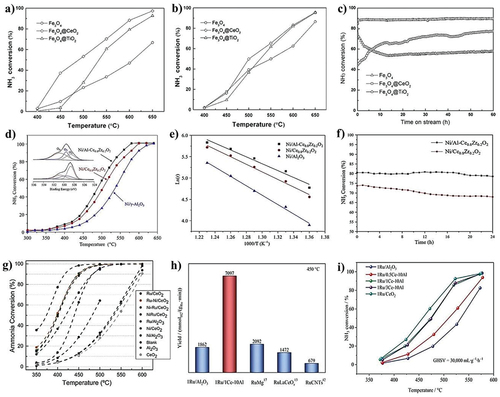
3.2.1.3. Cobalt (Co)
Despite being less active than iron and nickel, cobalt has little effect on ammonia decomposition. The composite with alumina, on the other hand, increases the catalytic activity [Citation96]. In this work, Co3O4-Al2O3 demonstrated excellent catalytic performance towards NH3 decomposition, achieving 100% conversion at 600°C and remaining its stability for 72 h. Al, Ca, and K oxides were added as promoters by Czekajlo and Lendzion-Bieluń to boost the conversion [Citation97]. Promoter oxides are thought to stabilise the catalyst’s surface area when they are added. Consequently, by incorporating alumina (10 wt %) into cobalt oxide, the conversion of ammonia was greatly boosted. Gu et al. also achieved a similar outcome using a catalyst of the same composition; the conversion increased by around 20% in comparison to pure cobalt oxide [Citation98].
Co was also investigated and demonstrated good catalytic activity when supported on carbon nanotubes. Multi-walled carbon nanotubes (MWCNTs) outperformed activated carbon (AC), reduced graphene oxide (rGO) and single-walled carbon nanotubes (SWCNTs) in contrast to other carbon supports for Co [Citation99]. Boosting impact of Na on a cobalt catalyst supported on titania nanotubes was demonstrated by Lara-Garcia et al. They found that the catalyst with Co particles of 15 nm had the best catalytic results, which is consistent with literature that claims that Co nanoparticles between 10 and 20 nm in size exhibit the highest activity [Citation100]. In this study, cobalt-supported titanate nanotubes were used as a catalyst for ammonia decomposition followed by different approaches, where the catalytic activity increased as the cobalt particle size decreased (). Similarly, the boosting impact of La on the activity of Co supported on MgO was also confirmed by Hu et al. At 400°C, the conversion of pure ammonia increases by 12% compared to the catalyst. Hu et al. also evaluated a Co catalyst supported on SiO2 [Citation101]. When silicates are utilised as a support, Co exhibits good activity. In this regard, the ammonia conversion was significantly boosted by the incorporation of cobalt into a structured mesoporous silicate. Cobalt included in a sodium silicate structure also exhibited strong activity [Citation39].
Figure 7. NH3 decomposition by (a) ion exchange method, (b) NaOH deposition method, (c) TEM images of 1. 10CoTi-NT 2. 10CoNaTi-NT (copyright @ 2019 Elsevier). (d) Synthesis scheme of MoS2 catalysts, (e) catalytic activity of MoS2 composites, and (f) stability performance (copyright @ 2020 Elsevier).
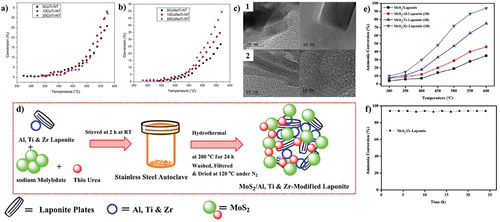
3.2.1.4. Molybdenum (Mo)
Mo is another non-noble metal that has been investigated for its ability for various environmental remediation activities such as sulfur removal, hydrogen production, and ammonia degradation [Citation102–105]. Testing catalysts with MoS2 as the active phase supported on laponite and laponite modified with Al, Ti, and Zr, Krishnan et al. found that the support changed with Zr produced the best results, achieving a conversion of 94% at 600°C (). They arrived at the conclusion that adding heteroatoms to the support allows for an improvement in the catalyst’s basicity and MoS2 dispersion [Citation106]. Mo2C was optimized and catalytically examined by Zheng et al. When using pure ammonia at a high temperature (600°C), the catalyst tended to produce MoN, which resulted in a considerable decrease in specific surface area [Citation107]. Nevertheless, the catalyst had lower activity than Ru supported on graphite. Similar to this, Li et al. evaluated catalysts made of MoO2 and Mo2C nanoparticles dispersed in a porous carbon matrix, noting that they quickly produced MoN during reaction, which ended up being the active phase [Citation108]. A list of non-noble ammonia-decomposition catalysts as the active phase along with their catalytic performances is provided in .
Table 5. Efficiency of reported non-noble metal catalysts for ammonia-decomposition.
3.2.1.5. Other metal amides, imides, carbides, and nitrides
Choi et al. investigated different vanadium carbide forms and compared their activity to that of Mo2C and found that while it was consistently lower than that of the molybdenum catalyst, it was significantly higher than a catalyst made of platinum supported on carbon. In a different study, Choi et al. contrasted the vanadium and molybdenum carbides and their equivalent nitrides, VN and MoN, activities [Citation136]. The outcomes demonstrated that the two element carbides are more effective at causing ammonia to break down.
Alkali metal amides, such as LiNH2, KNH2, and NaNH2, have emerged as promising compounds for the decomposition of ammonia, providing conversion rates that are on par with or better than those of ruthenium-based catalysts [Citation140]. For instance, compared to the Ru/Al2O3 and Ni/SiO2Al2O3 catalysts under the same catalytic conditions, lithium amide had a significantly higher activity [Citation141]. It was discovered that the active phase of amide catalysts varies depending on the reaction circumstances and the alkali metal of choice. The imide form, NH, of Li amides is the active phase in this scenario. Lithium imide was synthesised by Makepeace et al., adjusted with Ca and Mg, and the outcomes were compared to a lithium amide-imide mixture [Citation142,Citation143]. In comparison to the unmodified catalyst, they noticed that the changed forms exhibit a higher conversion at low temperatures. Additionally, Wood and Makepeace examined the compatibility of the lithium amide-imide catalyst with a number of support materials, including silicon dioxide (SiO2), aluminium oxide (Al2O3), magnesium oxide (MgO), and activated carbon [Citation143]. In contrast to the unsupported lithium amide-imide, there was no improvement in the catalytic performance for any of the configurations [Citation144]. The catalytic activity of LiNH2 alone versus supported by carbon was studied by Bramwell et al. Due to the production of Li2NCN, no activity was seen with the assisted catalyst. However, the reaction can be delayed until 450°C by adding Ni to the supported catalyst [Citation145]. As a result, compared to LiNH2, the catalytic activity of the LiNH2/Ni/C catalyst was greater. These results show a 26% greater conversion to LiNH2/Ni/C at 400°C under the reaction conditions examined as compared to those achieved using a Ru catalyst supported on alumina. Guo et al. investigated the catalytic activity of MnN mixed with the imide Li2NH in this context and contrasted the results with a Ru/CNTs catalyst, getting a greater activity with the MnN-Li2NH catalyst under the identical reaction conditions [Citation130]. When combined with the imide CaNH, the nitride Mn6N5, which is nearly inactive in the degradation of ammonia, demonstrated rather strong catalytic activity. By combining amides with ruthenium, several kinds of catalysts have been synthesized, often utilising mechanochemical processes. Examples include the amides of the alkaline earth metals Ba, Ca, and Mg. A thorough investigation into the catalytic activity of catalysts made of lithium imides and transition metal nitrides (TMN) was conducted by creating a number of catalysts from the corresponding transition metal chlorides and LiNH2, then nitriding them one after the other using NH3. In comparison to Fe2N, Li2NH, and Fe supported on CNTs, the Li2NH-Fe2N catalyst showed a greater ammonia decomposition rate [Citation146]. A list of different metal-based amides, imides, carbides, and nitrides is provided in for their catalytic activity in the degradation of ammonia.
Table 6. Catalytic activity of metallic amides, imides, carbides, and nitrides.
3.2.2. Bimetallic and multimetallic systems
Permutations of the metals Co, Mo, Ni, Fe, Pt, Cu, Ir, Cr, Mn, Mg, Cu, Sn, Zn, Li, and Pd have been examined as bimetallic and multimetallic catalysts for the ammonia decomposition reaction [Citation151,Citation152]. Additionally, studies of combinations of Ru with Fe, Sr, Bi, Pb, Sn, In, Cd, Zn, Au, Ag, Cu, Pt, Pd, Ni, Ir, and Rh have been established [Citation153]. However, because of its outstanding catalytic activity, the cobalt and molybdenum combination is one of the most explored bimetallic catalysts. Duan et al. confirmed that Co3Mo3N was the active phase of the bimetallic catalyst by evaluating an unsupported Co-Mo catalyst [Citation154]. Compared to the monometallic form, Mo2N, the bimetallic Co3Mo3N catalyst, demonstrated greater conversion. Additionally, the monometallic nitride, Mo2N [Citation155,Citation156], was outperformed by a catalyst made of Fe3Mo3N, which was synthesized by nitriding FeMoO4. Following up on the earlier findings, Srifa et al. [Citation157] evaluated bimetallic catalysts made by nitriding the appropriate oxides with NH3 at 350°C utilising Mo coupled with Co, Ni, and Fe. They listed the catalyst activity in the following order: Co3Mo3N, Ni3Mo3N, Fe3Mo3N, and Mo2N.
Bimetallic catalysts have been tested to boost their catalytic activity and to be able to minimise their presence in the catalyst in addition to replacing ruthenium or other noble metals. In this regard, McCullough et al. used a high-throughput technique to test more than 100 bimetallic catalysts based on Ru metal K supported on Al2O3 for the low-temperature decomposition of ammonia [Citation153]. Similar to this, Dasireddy and Likozar created a bimetallic catalyst made of Cu and Zn supported on alumina and showed that it had better catalytic activity than the corresponding monometallic catalysts [Citation158].
Xie et al. tested the usage of carbon nanofibers (CNFs) as supports. The catalytic activity of the nanofiber in combination with a Co-Mo-Fe-Ni-Cu alloy was compared to that of Ru and a Co-Mo bimetallic catalyst utilizing the same support [Citation46]. By adjusting the proportions of Co and Mo in the composition, they were able to achieve a TOF that was 20 times higher than that obtained with Ru and an even greater increase in TOF when compared to the traditional Co-Mo catalyst. In a 50 h test at 500°C, this multimetallic formulation demonstrated good stability. The catalytic activity of many bimetallic formulations has also been tested using various ceramic supports. For instance, on various oxide substrates, Huang et al. compared the catalytic activity of bimetallic catalysts Ce0.6Zr0.3Y0.1O2 (CZY) solid solutions supported with Ni and Co [Citation126]. The NiCo9/CZY morphologies, corresponding elemental mapping, and SAED pattern have been shown in , whereas the XPS spectra of the reduced Ni1Co9/CZY shown in . The physical characterization reveals that the lattice spacing of 0.303 nm corresponds to the (422) planes of Co3O4. In this study, a steady-state reaction was carried out using Ni- and Co-based catalysts, with Ni/CeO2, Ni/Y2O3, Co/CeO2, Co/Y2O3, Ni/CZY, and Co/CZY showing similar catalytic activity while Ni/ZrO2 and Co/ZrO2 show lower activity than others, as shown in . The supports catalytic activity was obtained in the series Ce0.6Zr0.3Y0.1O2 > CeO2 > Y2O3> ZrO2.
Figure 8. Ammonia decomposition over bimetallic Ni- and Co-based catalyst (copyright @ 2019 Elsevier).
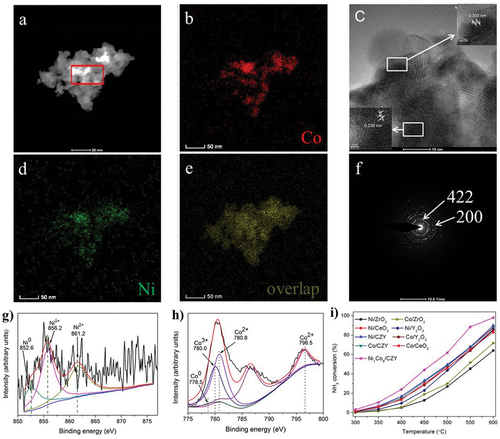
There is currently widespread commercial use of ammonia decomposition, but storing the by-products still poses significant difficulties for the development of a sustainable hydrogen economy. Due to several drawbacks that have hampered the development of hydrogen storage, researchers believe that much more work is required to reach a satisfactory level for commercialization. Although several technologies have been investigated for hydrogen storage, fuel cell transformation is an alternative to utilising hydrogen that directly produces electric energy by combining the electrochemical reaction of hydrogen and oxygen. Since the catalytic route to completely decompose ammonia into hydrogen is quite limited, Miyaoka et al. reports on the reduction of ammonia concentration during decomposition using a polymer electrolyte membrane (polymer electrolyte membrane) fuel cell equipped with Li-exchange X-type zeolite (Li-X) as adsorbent [Citation159]. In this study, the ammonia decomposition reaction was carried out at 773–823 K and 0.1 MPa had to be reduced to less than 0.1 ppm on specially designed apparatus (PICCARO G2103) outfitted with an agate mortar, as shown in ().
4. Conclusion and future outlook
Ammonia is utilised for a variety of industrial purposes, including plastics, explosives, and synthetic fibres, accounting for around 70% of its use in fertilisers. Ammonia as a fuel offers promise in the context of sustainable energy transitions, however this application is still in its infancy. The focus of this current emphasis is primarily on ammonia’s current use in agriculture and industry. While improvements have been made to existing technologies and new alternatives to fossil fuels have been added over time, a fundamental shift in the energy system, the so-called ‘energy shift’ has yet not occurred. The steep drop in the price of energy storage technologies, as well as solar and wind technologies, is a major driving force behind the planned fundamental change in the energy transition toward a new clean and efficient system. Building on existing initiatives, international collaboration, including on infrastructure, can assist improve the results provided here. Numerous investigations have concentrated on identifying the decomposition reaction’s limiting step utilising various types of catalysts. Although at first it was suggested that the limiting step was the desorption of nitrogen from the catalyst’s surface and that, consequently, the binding energy with nitrogen could determine the activity of the catalyst, it was later discovered that the limiting step was different for different types of catalysts. The reaction is significantly influenced by the active phase, the support, and the promoters. According to conventional wisdom, a catalyst support for NH3 decomposition should have a high basicity, high conductivity, low concentration of electron-withdrawing groups, high thermal stability, and high surface area. Numerous studies have specifically linked basicity to catalyst activity, and this relationship has been noted for a variety of active phases including Ru, Ni, Fe, Co, and Mo. Research should be combined with international collaboration to spur further development. For an accurate design of catalytic devices as well as for a better understanding of the reaction process, kinetic studies, and reactor modelling are helpful and essential methods.
Author contributions
ZZ: Visualization, Investigation, Data curation, Writing – original draft. YG: Investigation, Writing – original draft, Formal Analysis. K, SS, MG: Visualization, Formal Analysis. AS: Conceptualization, Funding acquisition, Supervision, Review & Editing,
Acknowledgments
The authors would like to acknowledge the financial assistance, funded by R&D Projects of CSIR-Council of Scientific & Industrial Research (Grant no. HCP-044), Government of India.
Disclosure statement
The authors declare no conflicts of interest or financial relationships.
Additional information
Funding
References
- Litvinenko V. The role of hydrocarbons in the global energy agenda: the focus on liquefied natural gas. Resources. 2020;9(5):59. doi: 10.3390/resources9050059
- Abas N, Kalair A, Khan N. Review of fossil fuels and future energy technologies. Futures. 2015 May 1;69:31–20. doi: 10.1016/j.futures.2015.03.003
- Perera F. Pollution from fossil-fuel combustion is the leading environmental threat to global pediatric health and equity: solutions exist. Int J Environ Res Public Health. 2017 Dec 23;15(1). doi: 10.3390/ijerph15010016; PubMed PMID: 29295510; PubMed Central PMCID: PMCPMC5800116. eng.
- Welsby D, Price J, Pye S, et al. Unextractable fossil fuels in a 1.5 °C world. Nature. 2021 Sep 9;597(7875):230–234. doi: 10.1038/s41586-021-03821-8
- Lelieveld J, Klingmüller K, Pozzer A, et al. Effects of fossil fuel and total anthropogenic emission removal on public health and climate. Proc Nat Acad Sci. 2019;116(15):7192–7197. doi: 10.1073/pnas.1819989116
- Fukushima T, Kitano S, Hata S, et al. Carbon-neutral energy cycles using alcohols. Sci Technol Adv Mater. 2018;19(1):142–152. doi: 10.1080/14686996.2018.1426340; PubMed PMID: 29511392; PubMed Central PMCID: PMCPMC5827732. eng.
- Chapman A, Ertekin E, Kubota M, et al. Achieving a carbon neutral future through advanced functional materials and technologies. Bull Chem Soc Jpn. 2022 Jan 15;95(1):73–103. doi: 10.1246/bcsj.20210323
- Yüzbaşıoğlu AE, Avşar C, Gezerman AO. The current situation in the use of ammonia as a sustainable energy source and its industrial potential. Curr Res Green Sustain Chem. 2022 Jan 1;5:100307. doi: 10.1016/j.crgsc.2022.100307
- Erdemir D, Dincer I. A perspective on the use of ammonia as a clean fuel: challenges and solutions. Int J Energy Res. 2021;45(4):4827–4834. doi: 10.1002/er.6232
- Xin G, Ji C, Wang S, et al. Experimental study on the effect of hydrogen substitution rate on combustion and emission characteristics of ammonia internal combustion engine under different excess air ratio. Fuel. 2023 Jul 1;343:127992.
- Blanco EC, Sánchez A, Martín M, et al. Methanol and ammonia as emerging green fuels: evaluation of a new power generation paradigm. Renew Sust Energ Rev. 2023 Apr 1;175:113195.
- Valera-Medina A, Xiao H, Owen-Jones M, et al. Ammonia for power. Prog Energ Combust Sci. 2018 Nov 1;69:63–102.
- Bareiß K, de la Rua C, Möckl M, et al. Life cycle assessment of hydrogen from proton exchange membrane water electrolysis in future energy systems. Appl Energy. 2019 Mar 1;237:862–872.
- Bell TE, Torrente-Murciano L. H2 production via ammonia decomposition using non-noble metal catalysts: a review. Top Catal. 2016 Sep 1;59(15):1438–1457.
- IEA. 2022. WEO, IEA, Paris, License: CC BY 4.0 (report); CC BY NC SA 4.0 (Annex A). Available from: https://www.iea.org/reports/world-energy-outlook-2022
- Aziz M, Wijayanta AT, Nandiyanto ABD. Ammonia as effective hydrogen storage: a review on production, storage and utilization. Energies. 2020;13(12):3062. doi: 10.3390/en13123062; PubMed PMID: doi:10.3390/en13123062.
- Krishnamoorthy A, Nomura K-I, Baradwaj N, et al. Hydrogen bonding in liquid ammonia. J Phys Chem Lett. 2022 Aug 4;13(30):7051–7057. doi: 10.1021/acs.jpclett.2c01608
- Megía PJ, Vizcaíno AJ, Calles JA, et al. Hydrogen production technologies: from fossil fuels toward renewable sources. A mini review. Energy Fuels. 2021 Oct 21;35(20):16403–16415. doi: 10.1021/acs.energyfuels.1c02501
- Fowles M, Carlsson M. Steam reforming of hydrocarbons for synthesis gas production. Top Catal. 2021 Dec 1;64(17):856–875.
- Bakhtyari A, Makarem MA, Rahimpour MR. Hydrogen production through pyrolysis. In: Meyers R, editor. Encyclopedia of sustainability science and technology. New York, NY: Springer New York; 2017. p. 1–28.
- Schneider S, Bajohr S, Graf F, et al. State of the art of hydrogen production via pyrolysis of natural gas. ChemBioeng Rev. 2020 Oct 1;7(5):150–158. doi: 10.1002/cben.202000014
- Li G, Kanezashi M, Tsuru T. Catalytic ammonia decomposition over high-performance Ru/Graphene nanocomposites for efficient COx-free hydrogen production. Catalysts. 2017;7(12):23. doi: 10.3390/catal7010023
- Ponikvar Ž, Likozar B, Gyergyek S. Electrification of catalytic ammonia production and decomposition reactions: from resistance, induction, and dielectric reactor heating to electrolysis. ACS Appl Energy Mater. 2022 May 23;5(5):5457–5472.
- Engge Y, Maulana F, Nurhuda M, et al. Dissociation of water into hydrogen and oxygen through a combination of electrolysis and photocatalyst. IOP Conf Ser Earth Environ Sci. 2021 May 1;743:012054.
- Li H, Cao X, Liu Y, et al. Safety of hydrogen storage and transportation: an overview on mechanisms, techniques, and challenges. Energy Rep. 2022 Nov 1;8:6258–6269.
- Andersson J, Grönkvist S. Large-scale storage of hydrogen. Int J Hydrogen Energy. 2019 May 3;44(23):11901–11919.
- Aziz M. Liquid hydrogen: a review on liquefaction, storage, transportation, and safety. Energies. 2021;14(18):5917. doi: 10.3390/en14185917
- Abohamzeh E, Salehi F, Sheikholeslami M, et al. Review of hydrogen safety during storage, transmission, and applications processes. J Loss Prevent Process Indust. 2021 Jun 1;72:104569.
- Valera-Medina A, Amer-Hatem F, Azad AK, et al. Review on ammonia as a potential fuel: from synthesis to economics. Energy Fuels. 2021 May 6;35(9):6964–7029. doi: 10.1021/acs.energyfuels.0c03685
- Wang K, Smith D, Zheng Y. Electron-driven heterogeneous catalytic synthesis of ammonia: current states and perspective. Carbon Resour Convers. 2018 Apr 1;1(1):2–31.
- Peng C, Chai L, Tang C, et al. Study on the mechanism of copper–ammonia complex decomposition in struvite formation process and enhanced ammonia and copper removal. J Environ Sci. 2017 Jan 1;51:222–233.
- Bao JL, Carter EA. Surface-plasmon-induced ammonia decomposition on copper: excited-state reaction pathways revealed by embedded correlated wavefunction theory. ACS Nano. 2019;13(9):9944–9957.
- Im Y, Muroyama H, Matsui T, et al. Ammonia decomposition over nickel catalysts supported on alkaline earth metal aluminate for H2 production. Int J Hydrog Energy. 2020 Oct 16;45(51):26979–26988. doi: 10.1016/j.ijhydene.2020.07.014
- McCabe RW. Kinetics of ammonia decomposition on nickel. J Catal. 1983 Feb 1;79(2):445–450.
- Chen W, Ermanoski I, Madey TE. Decomposition of ammonia and hydrogen on Ir surfaces: structure sensitivity and nanometer-scale size effects. J Am Chem Soc. 2005 Apr 1;127(14):5014–5015.
- Amirsardari Z, Dourani A, Amirifar MA, et al. Development of novel supported iridium nanocatalysts for special catalytic beds. J Nanostruct Chem. 2020 Mar 1;10(1):47–53. doi: 10.1007/s40097-019-00327-8
- Zhao J, Cui C, Wang H, et al. Insights into the mechanism of ammonia decomposition on molybdenum nitrides based on DFT studies. J Phys Chem C. 2019 Jan 1;123(1):554–564. doi: 10.1021/acs.jpcc.8b10101
- Morlanes N, Sayas S, Genrikh S, et al. Development of a Ba–CoCe catalyst for the efficient and stable decomposition of ammonia. Catal Sci Technol. 2021 Jan 1;11:3014–3024.
- Lendzion-Bielun Z, Narkiewicz U, Arabczyk W. Cobalt-based catalysts for ammonia decomposition. Materials. 2013;6(6):2400–2409. doi: 10.3390/ma6062400; PubMed PMID.
- Antunes R, Steiner R, Marot L, et al. Decomposition studies of NH3 and ND3 in presence of H2 and D2 with Pt/Al2O3 and Ru/Al2O3 catalysts. Int J Hydrog Energy. 2022 Apr 8;47(30):14130–14140. doi: 10.1016/j.ijhydene.2022.02.155
- Cechetto V, Di Felice L, Medrano JA, et al. H2 production via ammonia decomposition in a catalytic membrane reactor. Fuel Process Technol. 2021 Jun 1;216:106772.
- Pinzón M, Ruiz-López E, Romero A, et al. Electrochemical activation of Ru catalyst with alkaline ion conductors for the catalytic decomposition of ammonia. Mol Catal. 2021 Jul 1;511:111721.
- Kim A-R, Cha J, Kim JS, et al. Hydrogen production from ammonia decomposition over Ru-rich surface on La2O2CO3-Al2O3 catalyst beads. CatalToday. 2023 Mar 1;411-412:113867.
- Sittichompoo S, Nozari H, Herreros JM, et al. Exhaust energy recovery via catalytic ammonia decomposition to hydrogen for low carbon clean vehicles. Fuel. 2021 Feb 1;285:119111.
- Okura K, Okanishi T, Muroyama H, et al. Additive effect of alkaline earth metals on ammonia decomposition reaction over Ni/Y2O3 catalysts. RSC Adv. 2016;6(88):85142–85148. doi: 10.1039/C6RA19005G
- Xie P, Yao Y, Huang Z, et al. Highly efficient decomposition of ammonia using high-entropy alloy catalysts. Nat Commun. 2019 Sep 5;10(1):4011. doi: 10.1038/s41467-019-11848-9
- Hill AK, Torrente-Murciano L. Low temperature H2 production from ammonia using ruthenium-based catalysts: synergetic effect of promoter and support. Appl Catal B Environ. 2015 Aug 1;172–173:129–135. doi: 10.1016/j.apcatb.2015.02.011
- Bell TE, Zhan G, Wu K, et al. Modification of ammonia decomposition activity of ruthenium nanoparticles by N-Doping of CNT supports. Top Catal. 2017 Sep 1;60(15):1251–1259. doi: 10.1007/s11244-017-0806-0
- Sebastián D, Nieto-Monge MJ, Pérez-Rodríguez S, et al. Nitrogen doped ordered mesoporous carbon as support of PtRu nanoparticles for methanol electro-oxidation. Energies. 2018;11(4):831. doi: 10.3390/en11040831
- Nishi M, Chen S-Y, Tateno H, et al. A super-growth carbon nanotubes-supported, Cs-promoted Ru catalyst for 0.1–8 MPaG ammonia synthesis. J Catal. 2022 Sep 1;413:623–635.
- Bajus S, Agel F, Kusche M, et al. Alkali hydroxide-modified Ru/γ-Al2O3 catalysts for ammonia decomposition. Appl Catal A Gen. 2016 Jan 25;510:189–195.
- Zhao J, Xu S, Wu H, et al. Metal–support interactions on Ru/CaAlOx catalysts derived from structural reconstruction of Ca–Al layered double hydroxides for ammonia decomposition. Chem Commun. 2019;55(96):14410–14413. doi: 10.1039/C9CC05706D
- Hayashi F, Toda Y, Kanie Y, et al. Ammonia decomposition by ruthenium nanoparticles loaded on inorganic electride C12A7: e. Chem Sci. 2013;4(8):3124–3130. doi: 10.1039/C3SC50794G
- Wang Z, Cai Z, Wei Z. Highly active ruthenium catalyst supported on barium hexaaluminate for ammonia decomposition to COx-free hydrogen. ACS Sustain Chem Eng. 2019 Mar 6;7(9):8226–8235.
- Nagaoka K, Eboshi T, Abe N, et al. Influence of basic dopants on the activity of Ru/Pr6O11 for hydrogen production by ammonia decomposition. Int J Hydrog Energy. 2014 Dec 3;39(35):20731–20735. doi: 10.1016/j.ijhydene.2014.07.142
- Le TA, Kim Y, Kim HW, et al. Ru-supported lanthania-ceria composite as an efficient catalyst for COx-free H2 production from ammonia decomposition. Appl Catal B Environ. 2021 Mar 15;285:119831.
- Han X, Chu W, Ni P, et al. Promoting effects of iridium on nickel based catalyst in ammonia decomposition. J Fuel Chem Technol. 2007 Dec 1;35(6):691–695. doi: 10.1016/S1872-5813(08)60004-3
- Itoh N, Oshima A, Suga E, et al. Kinetic enhancement of ammonia decomposition as a chemical hydrogen carrier in palladium membrane reactor. CatalToday. 2014 Nov 1;236:70–76.
- Wallace SW, McCrum IT, Janik MJ. Ammonia electro-oxidation mechanism on the platinum (100) surface. CatalToday. 2021 Jul 1;371:50–57. doi: 10.1016/j.cattod.2020.09.024
- Pura J, Kwasniak P, Wiecinski P, et al. Investigation of the degradation mechanism of platinum-rhodium catalytic wires during oxidation of ammonia process. Solid State Phenom. 2015 Jan 1;227:229–232. doi: 10.4028/www.scientific.net/SSP.227.229
- Maeda A, Hu Z, Kunimori K, et al. Effect of high-temperature reduction on ammonia decomposition over niobia-supported and niobia-promoted rhodium catalysts. Catal Lett. 1988;1(5):155–157. doi: 10.1007/BF00765898
- Richardson DJ, Hellgardt K, Russell P, et al. Flux response analysis: a study of ammonia decomposition over Pt/Alumina. Chem Eng Res Des. 2004 Oct 1;82:1397–1403. doi: 10.1205/cerd.82.10.1397.46741
- Yao L, Shi T, Li Y, et al. Core–shell structured nickel and ruthenium nanoparticles: very active and stable catalysts for the generation of CO x -free hydrogen via ammonia decomposition. CatalToday. 2011 Apr 1;164:112–118. doi: 10.1016/j.cattod.2010.10.056
- Lorenzut B, Montini T, Pavel CC, et al. Embedded Ru@ZrO2 catalysts for H2 production by ammonia decomposition. ChemCatchem. 2010 Sep 17;2(9):1096–1106. doi: 10.1002/cctc.201000097
- Varisli D, Elverisli EE. Synthesizing hydrogen from ammonia over Ru incorporated SiO2 type nanocomposite catalysts. Int J Hydrogen Energy. 2014 Jul 3;39(20):10399–10408.
- García-García FR, Gallegos-Suarez E, Fernández-García M, et al. Understanding the role of oxygen surface groups: the key for a smart ruthenium-based carbon-supported heterogeneous catalyst design and synthesis. Appl Catal A Gen. 2017 Aug 25;544:66–76.
- Chung D, Kim H, Jeon M, et al. Enhanced ammonia dehydrogenation over Ru/La(x)-Al2O3 (x = 0–50 mol%): structural and electronic effects of La doping. Int J Hydrogen Energy. 2016 Aug 28;42:1639–1647.
- Hu X-C, Fu X-P, Wang W-W, et al. Ceria-supported ruthenium clusters transforming from isolated single atoms for hydrogen production via decomposition of ammonia. Appl Catal B Environ. 2020 Jul 5;268:118424.
- Nagaoka K, Honda K, Ibuki M, et al. Highly active Cs2O/Ru/Pr6O11 as a catalyst for ammonia decomposition. Chem Lett. 2010;39(9):918–919. doi: 10.1246/cl.2010.918
- Lucentini I, Casanovas A, Llorca J. Catalytic ammonia decomposition for hydrogen production on Ni, Ru and Ni Ru supported on CeO2. Int J Hydrogen Energy. 2019 Feb 1;44:12693–12707. doi: 10.1016/j.ijhydene.2019.01.154
- Sayas S, Morlanés N, Katikaneni SP, et al. High pressure ammonia decomposition on Ru–K/CaO catalysts. Catal Sci Technol. 2020;10(15):5027–5035. doi: 10.1039/D0CY00686F
- Yin S-F, Xu B-Q, Ng C-F, et al. Nano Ru/CNTs: a highly active and stable catalyst for the generation of COx-free hydrogen in ammonia decomposition. Appl Catal B Environ. 2004 Apr 8;48(4):237–241. doi: 10.1016/j.apcatb.2003.10.013
- Guo J, Chen Z, Wu A, et al. Electronic promoter or reacting species? The role of LiNH2 on Ru in catalyzing NH3 decomposition. Chem Commun. 2015;51(82):15161–15164. doi: 10.1039/C5CC04645A
- Tan H, Kun L, Sioud S, et al. Synthesis of Ru nanoparticles confined in magnesium oxide-modified mesoporous alumina and their enhanced catalytic performance during ammonia decomposition. Catal Commun. 2012 Sep 5;26:248–252. doi: 10.1016/j.catcom.2012.06.007
- Li J, Wang W, Chen W, et al. Sub-nm ruthenium cluster as an efficient and robust catalyst for decomposition and synthesis of ammonia: break the “size shackles”. Nano Res. 2018 Sep 1;11(9):4774–4785. doi: 10.1007/s12274-018-2062-4
- Su Q, Gu L, Zhong AH, et al. Layered double hydroxide derived Mg2Al-LDO supported and K-Modified ru catalyst for hydrogen production via ammonia decomposition. Catal Lett. 2018;148(3):894–903. doi: 10.1007/s10562-017-2195-1
- Marco Y, Roldán L, Armenise S, et al. Support-induced oxidation state of catalytic Ru nanoparticles on carbon nanofibers that were doped with heteroatoms (O, N) for the decomposition of NH3. ChemCatchem. 2013 Dec 1;5(12):3829–3834. doi: 10.1002/cctc.201300455
- Ren S, Huang F, Zheng J, et al. Ruthenium supported on nitrogen-doped ordered mesoporous carbon as highly active catalyst for NH3 decomposition to H2. Int J Hydrog Energy. 2017 Feb 23;42(8):5105–5113. doi: 10.1016/j.ijhydene.2016.11.010
- Ganley JC, Thomas FS, Seebauer E, et al. A priori catalytic activity correlations: the difficult case of hydrogen production from ammonia. Catal Lett. 2004 Jul 1;96:117–122. doi: 10.1023/B:CATL.0000030108.50691.d4
- Choudhary TV, Sivadinarayana C, Goodman DW. Catalytic ammonia decomposition: COx-free hydrogen production for fuel cell applications. Catal Lett. 2001 Apr 1;72(3):197–201. doi: 10.1023/A:1009023825549
- Polanski J, Bartczak P, Ambrozkiewicz W, et al. Ni-supported Pd nanoparticles with Ca Promoter: a new catalyst for low-temperature ammonia cracking. PLoS One. 2015;10(8):e0136805. doi: 10.1371/journal.pone.0136805; PubMed PMID: 26308929; PubMed Central PMCID: PMCPMC4550460. eng.
- Varisli D, Rona T. Cox free hydrogen production from ammonia decomposition over platinum based siliceous materials. Int J Chem React Eng. 2012;10(1). doi: 10.1515/1542-6580.3058
- Gu Y-Q, Jin Z, Zhang H, et al. Transition metal nanoparticles dispersed in an alumina matrix as active and stable catalysts for CO x -free hydrogen production from ammonia. J Mater Chem A. 2015;3(33):17172–17180. doi: 10.1039/C5TA04179A
- Yan H, Xu Y-J, Gu Y-Q, et al. Promoted multimetal oxide catalysts for the generation of hydrogen via ammonia decomposition. J Phys Chem C. 2016 Apr 14;120(14):7685–7696. doi: 10.1021/acs.jpcc.6b01595
- Zhang J, Xu H, Li W. Kinetic study of NH3 decomposition over Ni nanoparticles: the role of La promoter, structure sensitivity and compensation effect. Appl Catal A Gen. 2005 Dec 12;296(2):257–267.
- Okura K, Okanishi T, Muroyama H, et al. Ammonia decomposition over nickel catalysts supported on rare-earth oxides for the on-site generation of hydrogen. ChemCatchem. 2016 21;8(18):2988–2995. doi: 10.1002/cctc.201600610
- Munnik P, de Jongh PE, de Jong KP. Recent developments in the synthesis of supported catalysts. Chem Rev. 2015 Jul 22;115(14):6687–6718.
- Henpraserttae S, Charojrochkul S, Lawtrakul L, et al. Ni-based catalysts for hydrogen production from ammonia decomposition: effect of dopants and urine application. ChemistrySelect. 2018 Nov 15;3(42):11842–11850. doi: 10.1002/slct.201802975
- Henpraserttae S, Charojrochkul S, Klysubun W, et al. Reduced temperature ammonia decomposition using Ni/Zr-doped Al2O3 catalyst. Catal Lett. 2018 Jun 1;148:1775–1783.
- Tseng J-C, Gu D, Pistidda C, et al. Tracking the active catalyst for iron-based ammonia decomposition by in situ synchrotron diffraction studies. ChemCatchem. 2018 Oct 9;10(19):4465–4472. doi: 10.1002/cctc.201800398
- Li Y, Yao L, Liu S, et al. Cs-modified iron nanoparticles encapsulated in microporous and mesoporous SiO2 for COx-free H2 production via ammonia decomposition. CatalToday. 2011 Feb 2;160(1):79–86. doi: 10.1016/j.cattod.2010.02.066
- Cui H-Z, Gu Y-Q, He X-X, et al. Iron-based composite nanostructure catalysts used to produce COx-free hydrogen from ammonia. Sci Bull. 2016 Feb 1;61(3):220–226. doi: 10.1007/s11434-015-0991-9
- Jedynak A, Kowalczyk Z, Szmigiel D, et al. Ammonia decomposition over the carbon-based iron catalyst promoted with potassium. Appl Catal A Gen. 2002 Nov 1;237(1):223–226. doi: 10.1016/S0926-860X(02)00330-7
- Sima D, Wu H, Tian K, et al. Enhanced low temperature catalytic activity of Ni/Al–Ce0.8Zr0.2O2 for hydrogen production from ammonia decomposition. Int J Hydrogen Energy. 2020 Feb 1;45:9342–9352.
- Meng Q, Liu H, Xu K, et al. CeO2‒x modified Ru/γ-Al2O3 catalysts for ammonia decomposition reaction. J Rare Earths. 2023 Jun 1;41(6):801–809. doi: 10.1016/j.jre.2023.01.017
- Zhang Z-S, Fu X-P, Wang W-W, et al. Promoted porous Co3O4-Al2O3 catalysts for ammonia decomposition. Sci China Chem. 2018 Jul 25;61:1389–1398.
- Czekajło Ł, Lendzion-Bieluń Z. Effect of preparation conditions and promoters on the structure and activity of the ammonia decomposition reaction catalyst based on nanocrystalline cobalt. Chem Eng J. 2016 Apr 1;289:254–260. doi: 10.1016/j.cej.2015.12.093
- Gu Y-Q, Fu X-P, Du P-P, et al. In situ X-ray diffraction study of Co–Al Nanocomposites as catalysts for ammonia decomposition. J Phys Chem C. 2015 Jul 30;119(30):17102–17110. doi: 10.1021/acs.jpcc.5b02932
- Zhang H, Alhamed YA, Chu W, et al. Controlling Co-support interaction in Co/MWCNTs catalysts and catalytic performance for hydrogen production via NH3 decomposition. Appl Catal A Gen. 2013 Apr 15;464-465:156–164.
- Lara-García HA, Mendoza-Nieto JA, Pfeiffer H, et al. Cox-free hydrogen production from ammonia on novel cobalt catalysts supported on 1D titanate nanotubes. Int J Hydrog Energy. 2019 Nov 15;44(57):30062–30074. doi: 10.1016/j.ijhydene.2019.09.120
- Hu X-C, Wang W-W, Gu Y-Q, et al. Co-SiO2 nanocomposite catalysts for COx-free hydrogen production by ammonia decomposition. ChemPluschem. 2017 Mar 1;82(3):368–375. doi: 10.1002/cplu.201600444
- Gupta Y, Zaidi Z, Mehta S, et al. Assembly of a coordination polymer with sulphate-capped pentamolybdate units and copper: synthesis, structure, magnetic and catalytic studies. Dalton Trans. 2022;51(18):7255–7267. doi: 10.1039/D2DT00816E
- Zaidi Z, Gupta Y, Sorokhaibam LG. Semiconducting nanomaterials for photocatalytic desulfurization of liquid fuel under sunlight irradiation. Int J Chem React Eng. 2021 Sep 6;20:501–509. doi: 10.1515/ijcre-2021-0081
- Gupta Y, Zaidi Z, Sorokhaibam LG, et al. Molybdenum chalcogenides for photo-oxidative desulfurization of liquid fuels under ambient conditions: process optimization, kinetics, and recyclability studies. Catal Lett. 2023 Mar 1;153(3):643–658. doi: 10.1007/s10562-022-04015-1
- Pichaimuthu K, Chen C-J, Chen C-H, et al. Boosting Solar hydrogen production of molybdenum tungsten sulfide-modified Si micropyramids by introducing phosphate. ACS Appl Mater Interfaces. 2020 Sep 16;12(37):41515–41526. doi: 10.1021/acsami.0c11538
- Santhana Krishnan P, Neelaveni M, Tamizhdurai P, et al. COx-free hydrogen generation via decomposition of ammonia over al, Ti and Zr−Laponite supported MoS2 catalysts. Int J Hydrog Energy. 2020 Mar 18;45(15):8568–8583. doi: 10.1016/j.ijhydene.2020.01.062
- Zheng W, Cotter TP, Kaghazchi P, et al. Experimental and theoretical investigation of molybdenum carbide and nitride as catalysts for ammonia decomposition. J Am Chem Soc. 2013 Mar 6;135(9):3458–3464. doi: 10.1021/ja309734u
- Li L, Chu W, Ding C, et al. Embedded MoN@C nanocomposites as an advanced catalyst for ammonia decomposition to COx-free hydrogen. Int J Hydrog Energy. 2017 Dec 28;42(52):30630–30638. doi: 10.1016/j.ijhydene.2017.10.174
- Zhang L-F, Li M, Ren T-Z, et al. Ce-modified Ni nanoparticles encapsulated in SiO2 for COx-free hydrogen production via ammonia decomposition. Int J Hydrog Energy. 2015 Feb 19;40(6):2648–2656. doi: 10.1016/j.ijhydene.2014.12.079
- Meng T, Xu Q-Q, Li Y-T, et al. Nickle nanoparticles highly dispersed on reduced graphene oxide for ammonia decomposition to hydrogen. J Ind Eng Chem. 2015 Dec 25;32:373–379.
- Donald J, Xu C, Hashimoto H, et al. Novel carbon-based Ni/Fe catalysts derived from peat for hot gas ammonia decomposition in an inert helium atmosphere. Appl Catal A Gen. 2010 Feb 26;375(1):124–133. doi: 10.1016/j.apcata.2009.12.030
- Zhang J, Xu H, Jin X, et al. Characterizations and activities of the nano-sized Ni/Al2O3 and Ni/La–Al2O3 catalysts for NH3 decomposition. Appl Catal A Gen. 2005 Aug 18;290(1):87–96. doi: 10.1016/j.apcata.2005.05.020
- Lu A-H, Nitz J-J, Comotti M, et al. Spatially and size selective synthesis of Fe-based nanoparticles on ordered mesoporous supports as highly active and stable catalysts for ammonia decomposition. J Am Chem Soc. 2010 Oct 13;132(40):14152–14162. doi: 10.1021/ja105308e
- Tüysüz H, Schüth F, Zhi L, et al. Ammonia decomposition over iron phthalocyanine-based materials. ChemCatchem. 2015 May 4;7(9):1453–1459. doi: 10.1002/cctc.201500024
- Okura K, Okanishi T, Muroyama H, et al. Promotion effect of rare-earth elements on the catalytic decomposition of ammonia over Ni/Al2O3 catalyst. Appl Catal A Gen. 2015 Sep 25;505:77–85.
- Li L, Chen F, Shao J, et al. Attapulgite clay supported Ni nanoparticles encapsulated by porous silica: thermally stable catalysts for ammonia decomposition to COx free hydrogen. Int J Hydrogen Energy. 2016 Dec 14;41(46):21157–21165. doi: 10.1016/j.ijhydene.2016.08.156
- Yao LH, Li YX, Zhao J, et al. Core–shell structured nanoparticles (M@SiO2, Al2O3, MgO; M=Fe, Co, Ni, Ru) and their application in COx-free H2 production via NH3 decomposition. CatalToday. 2010 Dec 22;158(3):401–408. doi: 10.1016/j.cattod.2010.05.009
- Simonsen SB, Chakraborty D, Chorkendorff I, et al. Alloyed Ni-Fe nanoparticles as catalysts for NH3 decomposition. Appl Catal A Gen. 2012 Dec 7;447-448:22–31.
- Xu C, Tsubouchi N, Hashimoto H, et al. Catalytic decomposition of ammonia gas with metal cations present naturally in low rank coals. Fuel. 2005 Oct 1;84(14):1957–1967. doi: 10.1016/j.fuel.2005.03.019
- Duan X, Qian G, Zhou X, et al. Tuning the size and shape of Fe nanoparticles on carbon nanofibers for catalytic ammonia decomposition. Appl Catal B Environ. 2011 Jan 14;101(3):189–196. doi: 10.1016/j.apcatb.2010.09.017
- Zhang H, Alhamed YA, Al-Zahrani A, et al. Tuning catalytic performances of cobalt catalysts for clean hydrogen generation via variation of the type of carbon support and catalyst post-treatment temperature. Int J Hydrogen Energy. 2014 Dec 22;39(31):17573–17582. doi: 10.1016/j.ijhydene.2014.07.183
- Torrente-Murciano L, Hill AK, Bell TE. Ammonia decomposition over cobalt/carbon catalysts—effect of carbon support and electron donating promoter on activity. CatalToday. 2017 May 15;286:131–140. doi: 10.1016/j.cattod.2016.05.041
- Ji J, Duan X, Qian G, et al. Towards an efficient CoMo/γ-Al2O3 catalyst using metal amine metallate as an active phase precursor: enhanced hydrogen production by ammonia decomposition. Int J Hydrogen Energy. 2014 Aug 13;39(24):12490–12498. doi: 10.1016/j.ijhydene.2014.06.081
- Zhang Z-S, Fu X-P, Wang W-W, et al. Promoted porous Co3O4-Al2O3 catalysts for ammonia decomposition. Sci China Chem. 2018 Nov 1;61(11):1389–1398. doi: 10.1007/s11426-018-9261-5
- Torrente-Murciano L, Hill A, Bell T. Ammonia decomposition over cobalt/carbon catalysts—effect of carbon support and electron donating promoter on activity. CatalToday. 2016 Jun 1;286:131–140. doi: 10.1016/j.cattod.2016.05.041
- Huang C, Li H, Yang J, et al. Ce0.6Zr0.3Y0.1O2 solid solutions-supported NiCo bimetal nanocatalysts for NH3 decomposition. Appl Surface Sci. 2019 Jun 1;478:708–716.
- Zhang J, Comotti M, Schüth F, et al. Commercial Fe- or co-containing carbon nanotubes as catalysts for NH3 decomposition. Chem Commun (Camb). 2007 Jun 1;38:1916–1918. doi: 10.1039/B700969K
- Zhang H, Alhamed Y, Kojima Y, et al. Cobalt supported on carbon nanotubes. An efficient catalyst for ammonia decomposition. Proc Bulg Acad Sci. 2013 Jan 1;66. doi: 10.7546/CR-2013-66-4-13101331-7
- Zhang J, Müller J-O, Zheng W, et al. Individual Fe−Co alloy nanoparticles on carbon nanotubes: structural and catalytic properties. Nano Lett. 2008 Sep 10;8(9):2738–2743. doi: 10.1021/nl8011984
- Guo J, Peikun W, Wu G, et al. Lithium imide synergy with 3d transition-metal nitrides leading to unprecedented catalytic activities for ammonia decomposition. Angew Chem. 2015 Jan 21;127:2993–2997.
- Melchionna M, Fornasiero P. The role of ceria-based nanostructured materials in energy applications. Mater Today. 2014 Sep 1;17(7):349–357.
- Duan X, Qian G, Zhou X, et al. MCM-41 supported CoMo bimetallic catalysts for enhanced hydrogen production by ammonia decomposition. Chem Eng J. 2012 Oct 1;207-208:103–108.
- Lorenzut B, Montini T, Bevilacqua M, et al. FeMo-based catalysts for H2 production by NH3 decomposition. Appl Catal B Environ. 2012 Aug 1;125:409–417.
- Liu H, Wang H, Shen J, et al. Preparation and evaluation of ammonia decomposition catalysts by high-throughput technique. React Kinet Catal Lett. 2008 Jan 1;93(1):11–17. doi: 10.1007/s11144-008-5155-3
- Liang C, Li W, Wei Z, et al. Catalytic decomposition of ammonia over nitrided MoNx/α-Al2O3 and NiMoNy/α-Al2O3 catalysts. Ind Eng Chem Res. 2000;39(10):3694–3697. doi: 10.1021/ie990931n
- Choi J-G. Ammonia decomposition over vanadium carbide catalysts. J Catal. 1999 Feb 15;182(1):104–116.
- Xu J, Yan H, Jin Z, et al. Facile synthesis of stable MO2N nanobelts with high catalytic activity for ammonia decomposition. Chin J Chem. 2019 Apr 1;37(4):364–372. doi: 10.1002/cjoc.201900016
- Wise RS, Markel EJ. Catalytic NH3 decomposition by topotactic molybdenum oxides and Nitrides: effect on temperature programmed γ-Mo2N synthesis. J Catal. 1994 Feb 1;145(2):335–343.
- Tagliazucca V, Leoni M, Weidenthaler C. Crystal structure and microstructural changes of molybdenum nitrides traced during catalytic reaction by in situ X-ray diffraction studies. Phys Chem Chem Phys. 2014;16(13):6182–6188. doi: 10.1039/C3CP54578D
- Chang F, Wu H, Pluijm RVD, et al. Effect of pore confinement of NaNH2 and KNH2 on hydrogen generation from Ammonia. J Phys Chem C. 2019 Sep 5;123(35):21487–21496. doi: 10.1021/acs.jpcc.9b03878
- Guo J, Fei C, Peikun W, et al. Highly active MnN–Li 2 NH composite catalyst for producing CO x-free hydrogen. ACS Catal. 2015 May 1;5:2708–2713.
- Makepeace JW, Hunter HMA, Wood TJ, et al. Ammonia decomposition catalysis using lithium–calcium imide. Faraday Discuss. 2016;188:525–544. doi: 10.1039/C5FD00179J
- Makepeace JW, Wood TJ, Marks PL, et al. Bulk phase behavior of lithium imide–metal nitride ammonia decomposition catalysts. Phys Chem Chem Phys. 2018;20(35):22689–22697. doi: 10.1039/C8CP02824A
- Wood TJ, Makepeace JW, David WIF. Neutron diffraction and gravimetric study of the manganese nitriding reaction under ammonia decomposition conditions. Phys Chem Chem Phys. 2018;20(13):8547–8553. doi: 10.1039/C7CP07613D
- Bramwell PL, Lentink S, Ngene P, et al. Effect of pore confinement of LiNH2 on ammonia decomposition catalysis and the storage of hydrogen and ammonia. J Phys Chem C. 2016 Dec 8;120(48):27212–27220. doi: 10.1021/acs.jpcc.6b10688
- Makepeace J, Wood T, Marks P, et al. Bulk phase behavior of lithium imide–metal nitride ammonia decomposition catalysts. Phys Chem Chem Phys. 2018 Aug 23;20:22689–22697.
- Wang P, Guo J, Xiong Z, et al. The interactions of Li3FeN2 with H2 and NH3. Int J Hydrog Energy. 2016 Aug 24;41(32):14171–14177. doi: 10.1016/j.ijhydene.2016.05.108
- Kraupner A, Markus A, Palkovits R, et al. Mesoporous Fe3C sponges as magnetic supports and as heterogeneous catalyst. J Mater Chem. 2010;20(29):6019–6022. doi: 10.1039/C0JM00774A
- Cao H, Guo J, Chang F, et al. Transition and alkali metal complex ternary amides for ammonia synthesis and decomposition. Chemistry. 2017 Jul 21;23(41): 9766–9771. 10.1002/chem.201702728; PubMed PMID: 28627715; eng.
- Yu P, Guo J, Liu L, et al. Effects of alkaline earth metal amides on Ru in catalytic ammonia decomposition. J Phys Chem C. 2016 Feb 11;120(5):2822–2828. doi: 10.1021/acs.jpcc.5b11768
- Crawley JWM, Gow IE, Lawes N, et al. Heterogeneous trimetallic nanoparticles as catalysts. Chem Rev. 2022 Mar 23;122(6):6795–6849. doi: 10.1021/acs.chemrev.1c00493
- Ma X-L, Liu J-C, Xiao H, et al. Surface single-cluster catalyst for N2-to-NH3 thermal conversion. J Am Chem Soc. 2018 Jan 10;140(1):46–49. doi: 10.1021/jacs.7b10354
- McCullough K, Chiang PH, Jimenez JD, et al. Material discovery and high throughput exploration of Ru based catalysts for low temperature ammonia decomposition. Materials. 2020 Apr 16;13(8): 1869. 10.3390/ma13081869; PubMed PMID: 32316302; PubMed Central PMCID: PMCPMC7215519. eng.
- Duan X, Ji J, Yan X, et al. Understanding Co-Mo catalyzed ammonia decomposition: influence of calcination atmosphere and identification of active phase. ChemCatchem. 2016 Mar 7;8(5):938–945. doi: 10.1002/cctc.201501275
- Podila S, Zaman SF, Driss H, et al. Hydrogen production by ammonia decomposition using high surface area Mo2N and Co3Mo3N catalysts. Catal Sci Technol. 2016;6(5):1496–1506. doi: 10.1039/C5CY00871A
- Zaman SF, Jolaoso LA, Podila S, et al. Ammonia decomposition over citric acid chelated γ-Mo2N and Ni2Mo3N catalysts. Int J Hydrog Energy. 2018 Sep 6;43(36):17252–17258. doi: 10.1016/j.ijhydene.2018.07.085
- Srifa A, Okura K, Okanishi T, et al. CO x -free hydrogen production via ammonia decomposition over molybdenum nitride-based catalysts. Catal Sci Technol. 2016 Oct 10;6:7495–7504.
- Dasireddy V, Likozar B. CO -free hydrogen generation via decomposition of ammonia over copper and zinc-based catalysts. Fuel. 2017 Mar 1;196:325–335. doi: 10.1016/j.fuel.2017.01.117
- Miyaoka H, Miyaoka H, Ichikawa T, et al. Highly purified hydrogen production from ammonia for PEM fuel cell. Int J Hydrog Energy. 2018 Aug 2;43(31):14486–14492. doi: 10.1016/j.ijhydene.2018.06.065