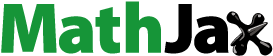
Abstract
Specimens of iron-based binary Fe–Si alloy and ternary Fe–Me–Si alloys (with Me = Ti, Cr and V) were nitrided at 580 °C in a NH3/H2-gas mixture applying a nitriding potential of 0.1 atm−1/2 until nitrogen saturation in the specimens was attained. In contrast with recent observations in other Fe–Me 1–Me 2 alloys, no “mixed” (Me 1, Me 2) nitrides developed in Fe–Me–Si alloys upon nitriding: first, all Me precipitates as MeN; and thereafter, all Si precipitates as Si3N4. The MeN precipitates as crystalline, finely dispersed, nanosized platelets, obeying a Baker–Nutting orientation relationship (OR) with respect to the ferrite matrix. The Si3N4 precipitates as cubically, amorphous particles; the incoherent (part of the) MeN/α-Fe interface acts as heterogeneous nucleation site for Si3N4. The Si3N4-precipitation rate was found to be strongly dependent on the degree of coherency of the first precipitating MeN. The different, even opposite, kinetic effects observed for the various Fe–Me–Si alloys could be ascribed to the different time dependences of the coherent → incoherent transitions of the MeN particles in the different Fe–Me–Si alloys.
1. Introduction
Gas nitriding is applied to ferritic iron-based alloys to improve their mechanical and chemical properties [Citation1–3]. The dissociation of gaseous NH3 on the surface of the component releases free nitrogen atoms which can be absorbed and diffused inwardly via the octahedral interstitial-lattice sites of the ferrite matrix. Nitriding steels are usually alloyed with elements (e.g. Al, Ti, V and Cr [Citation4–23]) having a strong affinity to nitrogen leading upon nitriding to the precipitation of nanosized alloying-element nitride particles in the ferrite matrix.
A parameter which characterizes the strength of the interaction of nitrogen and alloying element can be defined as the ratio of the energy gained upon nitride formation (i.e. chemical Gibbs energy) and the energy spent to form nitride precipitates in the ferrite matrix (i.e. interfacial and misfit-strain energies) [Citation24,25]. The larger the interaction parameter for a certain alloying element, the larger is the tendency for precipitation of the corresponding alloying-element nitride. On this basis, two extremes of nitride-precipitation behaviour can be distinguished [Citation26]:
Strong interaction: In the nitrided surface region (case) all alloying-element atoms precipitate more or less instantaneously as nitrides. Consequently, a sharp case/core boundary migrates to larger depths with increasing nitriding time. In this case, the nitriding kinetics is rate controlled, at constant temperature, by the diffusion of nitrogen through the nitrided case.
Weak interaction: Prior to the nitride precipitation, the iron matrix gets saturated with nitrogen throughout the specimen. Then, the nitride precipitation occurs at the same rate at each depth below the specimen surface. In this case, the nitriding rate depends on the rate of precipitation kinetics that can be controlled by (a combination of) nucleation, growth and impingement mechanisms [Citation27].
Experimental results obtained for the kinetics of precipitation, in binary iron-based alloys upon nitriding, of TiN [Citation28–30] and VN [Citation31–33] have shown that Ti and V exhibit a strong interaction with (inwardly diffusing) nitrogen. Cr shows a strong (for high Cr contents) to an intermediate (for relatively small Cr contents) interaction behaviour [Citation34–37]. Weak interaction behaviour is observed in the cases of Si [Citation38–40] and Al [Citation26,41,42], for nitride precipitation in a defect (dislocation) free/poor ferrite matrix.
Recently, the nitriding behaviour of ternary iron-based Fe–V–Si alloy was investigated for the first time [Citation43]. It was shown that VN and Si3N4 precipitate not only separately but moreover successively: first, all V precipitates as VN; and thereafter, Si3N4 precipitation takes place. Further, as compared to the precipitation rate of Si3N4 in binary Fe–Si alloy, the precipitation rate of Si3N4 in the ternary Fe–V–Si alloy was found to be much lower.
TiN, CrN and VN have the same cubic, rock-salt type crystal structure and precipitate in ferrite on the same habit plane () and with the same orientation relationship (OR) (Baker–Nutting:
). However, as indicated by their lattice parameters, their (coherency-) strain fields induced by the misfitting nitride platelets in the ferrite matrix are of distinctively different magnitude: the coherency strains are highest for TiN, lower for CrN and lowest for VN.
The present project is focused on investigation of the effect of the magnitude of the coherency strains, caused by prior precipitation of MeN (with Me = Ti, Cr and V) on the subsequently developing Si3N4 particles. Thereby, insight into mechanisms of precipitation in a matrix exhibiting locally fluctuating (coherency) strains is obtained.
2. Experimental procedures
2.1. Specimen preparation
The iron-based ternary Fe–Me–Si alloys and the binary Fe–Si alloy were produced by melting granules of Fe (purity 99.98 wt.%), Si (purity 99.999 wt.%), Ti (purity 99.999 wt.%), V (purity 99.9 wt.%) and Cr (purity 99.999 wt.%) under protective Ar atmosphere and cast to rods. The cast rods, with a length of 100 mm and a diameter of 10 mm, were ground to remove a possible surface-oxide layer. Afterwards, the cast-rods were subjected to cold rolling to prepare sheets with a thickness of approximately 1 mm. Specimens, with a rectangular shape and dimensions (15 × 10 × 1) mm, were cut from these sheets and subsequently ground, polished (final step with 1 μm diamond paste) and ultrasonically cleaned in ethanol. Next, the specimens were annealed, after having put them into a quartz tube filled with protective Ar gas, at 800 °C for 20 min to recrystallize the deformed microstructure. The recrystallized specimens were polished (1 μm diamond paste) again, to remove a possible surface-oxide layer formed during the recrystallization treatment and ultrasonically cleaned in ethanol.
The chemical composition of the Fe–Si and Fe–Me–Si specimens was determined by inductively coupled plasma optical emission spectroscopy (for the alloying-metal contents: Si, Ti, Cr and V), carrier gas hot extraction (for O and N) and combustion methods (for C and S). Results of the chemical analysis are shown in Table .
Table 1. Alloying-element contents and light element impurity contents in the binary iron-based Fe–Si alloy and the ternary Fe–Me–Si alloys prepared and employed in the present work.
2.2. Nitriding
The Fe–2.0Si and Fe–Me–2.0Si alloy specimens were gas nitrided by suspending them, with a quartz fiber, in a vertical multizone quartz-tube furnace equipped with gas mass-flow (flow variation ± 2.5 ml/min) and temperature (temperature variation ± 1 °C) controllers (see Ref. [Citation44] for detailed description of the nitriding facility). Nitriding experiments were performed at 580 °C with a gas flux of NH3 (purity 99.998 vol.%) adjusted to 45 ml/min and a gas flux of H2 (purity 99.999 vol.%) adjusted to 455 ml/min. This set of gas fluxes corresponds to a nitriding potential of (the nitriding potential [Citation1,45] is defined as
, where p denotes partial pressure). Using this set of nitriding parameters, a 1 mm thick pure iron specimen is through nitrided after 20 hours [Citation1]. For the employed nitriding potential at 580 °C, iron nitrides (ε-Fe3N1+x
or γ′-Fe4N1-y
) cannot form upon nitriding pure iron [Citation46], and no iron nitrides were found upon nitriding the Fe–2.0Si and Fe–Me–2.0Si alloys. The nitriding treatments were terminated by quenching the specimens into distilled water purged with N2 gas (purging water with N2 gas minimizes the O content dissolved in water).
2.3. Weighing
Every specimen was weighed before and after nitriding with a comparator balance (Mettler XP56). For weight determination, five such weighing measurements were carried out. From the mean values and their standard deviations, before and after nitriding, the nitrogen uptake and its standard deviation were calculated. The latter standard deviation is smaller than the size of the data points in Figure .
Figure 1. (colour online) (a) Nitrogen content as a function of nitriding time for the binary Fe–2.0Si alloy and the ternary Fe–Me–2.0Si alloy (with Me = Ti, Cr and V) specimens nitrided at 580 °C with r
N = 0.1 atm−1/2. The “theoretical nitrogen contents” as indicated with dashed lines, pertain to (pure) ferrite saturation with nitrogen and all alloying-element atoms precipitated as stoichiometric MeN and Si3N4. (b) For nitriding times shorter than 30 h the nitrogen–content curves attain, except of the nitrided ternary Fe-0.2/0.5Ti–2.0Si alloy specimens, a practically constant nitrogen level. The dashed lines indicate the nitrogen levels in nitrided Fe–Me–2.0Si alloys for (pure) ferrite saturation ( = 0.29 at.%; according to [Citation50]) and all Me (= Ti, Cr and V) precipitated as stoichiometric MeN. The dotted lines in (a) and (b) are connecting the experimentally obtained data points.
![Figure 1. (colour online) (a) Nitrogen content as a function of nitriding time for the binary Fe–2.0Si alloy and the ternary Fe–Me–2.0Si alloy (with Me = Ti, Cr and V) specimens nitrided at 580 °C with r N = 0.1 atm−1/2. The “theoretical nitrogen contents” as indicated with dashed lines, pertain to (pure) ferrite saturation with nitrogen and all alloying-element atoms precipitated as stoichiometric MeN and Si3N4. (b) For nitriding times shorter than 30 h the nitrogen–content curves attain, except of the nitrided ternary Fe-0.2/0.5Ti–2.0Si alloy specimens, a practically constant nitrogen level. The dashed lines indicate the nitrogen levels in nitrided Fe–Me–2.0Si alloys for (pure) ferrite saturation ([N]α0 = 0.29 at.%; according to [Citation50]) and all Me (= Ti, Cr and V) precipitated as stoichiometric MeN. The dotted lines in (a) and (b) are connecting the experimentally obtained data points.](/cms/asset/9a146bc3-cb84-4fd2-99e1-332ef156dea4/tphm_a_952258_f0001_oc.gif)
2.4. X-ray diffraction
A PANalytic X’Pert multipurpose diffractometer (MPD) employing Co-Ka radiation (λ = 1.7902 Å) and Bragg–Brentano geometry was used to record X-ray diffraction (XRD) patterns. This MPD is equipped with a graphite monochromator in the diffracted beam and an X’Celerator detector from PANalytic. The recorded diffractograms were analysed by the software X’Pert Highscore and the occurring phases were identified from peak positions in the diffractograms using the data base from the International Centre for Diffraction Data (ICDD) [Citation47]. Recognizing that the specimens are homogeneously (through) nitrided after 20 h at 580 °C and r N = 0.1 atm−1/2 (see Section 2.2) no residual stress-depth profile occurs in the specimen. However, the misfit-strain fields surrounding the precipitated particles invoke a macroscopic, hydrostatic component of strain/stress (independent of depth) [Citation48], leading to diffraction-peak shifts as a consequence of a change of the ferrite-lattice parameter. To trace the change of the ferrite-lattice parameter, the 200α-Fe peaks were fitted with an asymmetric (split) pseudo-Voigt function for both the Kα1 component and the Kα2 component [Citation49], in the diffraction-angle range (70°–85°) 2θ using the software Topas 3.0 from Bruker AXS. The instrumental offset for the utilized diffractometer was determined by making measurements on a pure iron specimen, prepared according to the procedure described in Section 2.1 (adopting the lattice parameter of pure iron 2.8664 Å [Citation47]). From the obtained fit functions, the peak position, (and thereby the ferrite-lattice parameter) and the full width at half maximum (FWHM) of the Kα1 component were determined adopting 1/5 of the step size (0.033° 2θ) as the error in peak position. Thus, the error in the ferrite-lattice parameter values in Table is ±0.0002 Å and the error for the lattice-parameter difference values in Table is ±0.0004 Å. The error in the FWHM values in Table is taken as two times 1/5 of the step size (see above) and thus is ±0.013° 2θ.
Table 2. Predicted and measured ferrite-lattice parameters of the binary Fe–2.0Si alloy and the ternary Fe–Me–2.0Si alloys in the unnitrided state (stage 1).
Table 3. FWHM (in ° 2θ) of the 200α-Fe-ferrite peak (Kα1 component) of the binary Fe–2.0Si alloy and the ternary Fe–Me–2.0Si alloys in the unnitrided state (stage 1), after all Me has precipitated as MeN (stage 2) and after also all Si has precipitated as Si3N4 additionally to MeN (stage 3). The error in the FWHM values is ±0.013° 2θ (see Section 2.4).
2.5. Transmission electron microscopy
Electron transparent foils were prepared from nitrided specimens at a depth below the surface of 100 μm (only in one case the depth was 500 μm as explicitly mentioned in the corresponding figure caption). To this end, discs with a diameter of 3 mm were cut out of the nitrided specimens. The thickness of the discs was reduced by grinding in such a way that the desired depth is in the middle of the remaining specimen; the final thinning involved either electropolishing or ion milling. In case of electropolishing, the discs were (mechanically) polished and then electropolished (electrolyte: 85 vol.% acetic acid and 15 vol.% perchloric acid) with a Struers Tenupol-5 apparatus. In case of ion milling, the discs were dimpled and then ion-milled using the apparatus Model 1010 from Fischione. A Philips CM 200 transmission electron microscope was used. The instrument is equipped with a Gatan CCD camera to record the bright-field (BF), dark-field (DF) images and selected area diffraction patterns (SADP). Ferrite-matrix diffraction spots, corresponding with known lattice spacings, d, were used for calibration of the camera constant of the microscope. In order to index diffraction spots in the SADPs, the software Digital Micrograph Diffpack from Gatan was used to determine the distances, R, of diffraction spots from the centre in the SADPs and to calculate the corresponding d values. These d values were then compared with the lattice-parameter data provided by the ICDD data base [Citation47].
3. Results and evaluation
3.1. Nitride-precipitation kinetics
Specimens of the ternary Fe–Me–2.0Si alloys (with Me = Ti, Cr and V) and the binary Fe–2.0Si alloy (see Table for composition of the alloys) were nitrided for different times at 580 °C with r
N = 0.1 atm−1/2. The nitrogen uptakes as a function of nitriding time for these nitrided alloys are shown in Figure . The levels of nitrogen content expected, for precipitation of all Me as MeN, plus precipitation of all Si as Si3N4 and plus the establishment of the equilibrium-nitrogen solubility of an unstrained ferrite matrix, (here 0.29 at.% N for the employed nitriding conditions [Citation50]), for all the nitrided alloys have been indicated in Figure (a) with dashed lines. These levels of nitrogen content are called the “theoretical” nitrogen contents (
).
All alloy specimens were nitrided for sufficiently long time to reach the theoretical nitrogen content (at least; see what follows for uptake of “excess nitrogen”). Establishment of the theoretical nitrogen content for the different nitrided alloys is compatible with the development of separate MeN and Si3N4 precipitates, which are in agreement with the evidence from transmission electron microscopy investigation (cf. Section 3.2). The nitrogen taken up beyond the theoretical nitrogen level, as observed for especially the Fe-0.5/0.2Ti–2.0Si alloys, is called “excess nitrogen”.Footnote1
The rate of increase of the nitrogen content in case of the ternary Fe–0.3V–2.0Si alloy is significantly smaller as that of the binary Fe–2.0Si alloy, the ternary Fe–2.0Cr–2.0Si and Fe–0.2/0.5Ti–2.0Si alloys: For example, the nitriding times needed to attain a constant, saturation level of nitrogen are 650 h for the binary Fe–2.0Si alloy, 200/520 h for the ternary Fe–0.5/0.2Ti–2.0Si alloys, 500 h for the ternary Fe–2.0Cr–2.0Si alloy and 1500 h for the ternary Fe–0.3V–2.0Si alloy (see Figure (a)).
For nitriding times less than about 30 h, and except for the nitrided ternary Fe–0.5/0.2Ti–2.0Si alloys, all other alloys show (more or less) a plateau in the nitrogen content vs. time curves (Figure (b)). The levels of nitrogen content expected for equilibrium saturation of the ferrite matrix with nitrogen, and with all Ti precipitated as TiN (for the Fe–Ti–Si alloys), with all Cr precipitated as CrN (for the Fe–Cr–Si alloy) and with all V precipitated as VN (for the Fe–V–Si alloy), have been indicated in Figure (b) with dashed horizontal lines. These levels of nitrogen content are called the “normal nitrogen content upon MeN development” ().
The initial (at nitriding time <30 h) plateau level of nitrogen content of the ternary Fe–0.3V–2.0Si alloy specimen is nearly at the expected level (Figure (b)), suggesting that at this stage, all V has precipitated as stoichiometric VN and that no significant precipitation of Si3N4 has occurred. The initial plateau level of nitrogen content of the ternary Fe–2.0Cr–2.0Si alloy specimen is lower than the expected
level. This discrepancy, despite the expectation of an even higher nitrogen content due to precipitation of a small amount of Si3N4 at this stage (as revealed by TEM; cf. Section 3.2) and excess nitrogen uptake, which is expected in connection with precipitated CrN [Citation52,53] can be attributed to dissolved Si in ferrite lowering the nitrogen solubility [Citation54].
Absence of an initial plateau for the nitrided Fe–Ti–Si alloys suggests overlapping in time of the TiN precipitation and Si3N4 precipitation processes, i.e. some part of Si precipitates, as Si3N4, simultaneously with the precipitation of Ti as TiN (see what follows and Section 3.2. where supporting TEM evidence is presented).
In case of the nitrided binary Fe–2.0Si alloy specimen the initial plateau level of nitrogen content is 0.20 at.%. This value is smaller than the expected nitrogen solubility of pure iron (0.29 at.%; according to Ref. [Citation50]) for the same nitriding conditions, suggesting that, at this stage of nitriding, no significant Si3N4 precipitation has taken place. The slightly lower nitrogen level in the Fe–2.0Si alloy as compared to the expected nitrogen solubility of pure iron can be attributed to the presence of dissolved Si in ferrite that lowers (significantly) the nitrogen solubility [Citation54].
The dependence of nitrogen content on nitriding time for the different alloys can be fitted well (for nitriding times beyond the initial stage, i.e. for nitriding times >30 h; see above) with a sigmoidal Boltzmann function (see Figure (a)). The derivative of these functions with respect to nitriding time provides the nitriding rates as a function of nitriding time (Figure (b)). Evidently, the highest maximum nitriding rate occurs for the ternary Fe–0.5Ti–2.0Si and Fe–0.2Ti–2.0Si alloys, followed by the ternary Fe–2.0Cr–2.0Si alloy, the binary Fe–2.0Si alloy and the ternary Fe–0.3V–2.0Si alloy, in that order. The kinetic data show that, as compared to the Si3N4-precipitation rate in the binary Fe–2.0Si alloy, pronounced acceleration of the Si3N4-precipitation rate occurs in the ternary Fe-0.2/0.5Ti–2.0Si alloys, whereas a strong deceleration is observed in the ternary Fe–0.3V–2.0Si alloy. In this respect, the Fe–2.0Cr–2.0Si alloy takes an intermediate position.
Figure 2. (colour online) (a) Nitrogen content as a function of nitriding time for binary Fe-2.0Si alloy and ternary Fe–Me–2.0Si alloy (with Me = Ti, Cr and V) specimens nitrided at 580 °C with r N = 0.1 atm−1/2. The experimentally obtained data points were numerically fitted with a sigmoidal Boltzmann function (continuous lines). (b) The corresponding nitrogen-uptake rates as a function of nitriding time (derivatives of the continuous lines in (a)).
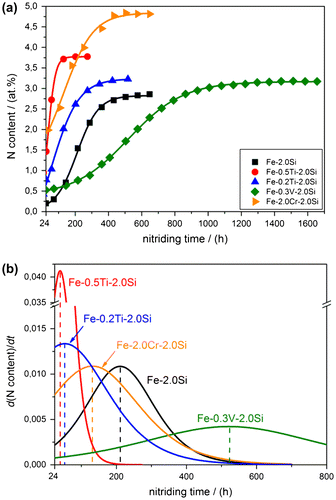
3.2. Structure and morphology of precipitated nitrides
TEM investigations were performed to reveal the structure and morphology of precipitated nitrides (i) after relatively short nitriding times (but mostly after 24 h, because this nitriding time is sufficient to nitride a 1 mm thick specimen homogenously; cf. Section 2.2) and (ii) after the nitriding time at which (in addition to MeN) nearly all Si3N4 has precipitated.
TEM images, recorded from the ternary Fe–0.2Ti–2.0Si alloy specimen, from the ternary Fe–2.0Cr–2.0Si alloy specimen and from the ternary Fe–0.3V–2.0Si alloy specimen after short-time nitriding, are shown in Figure . In these nitrided alloys, finely dispersed, nanosized MeN precipitates have developed. These precipitates exhibit a platelet-like morphology (thickness of only 1–2 atomic layers) with a length around 4 nm in case of TiN, a length around 23 nm in case of CrN and a length around 5 nm case of VN. The (semi-) coherency of these nitride platelets with the ferrite matrix is illustrated by the coffee-bean like contrast [Citation55] surrounding the platelets in the BF images (cf. magnified insets in Figure (a1), (b1) and (c)). The corresponding SADPs, recorded in [0 0 1]α-Fe-zone axis, show diffraction spots from the ferrite matrix and in case of the Fe–2.0Cr–2.0Si and Fe–0.3V–2.0Si alloys streaks of intensity along [1 0 0] α-Fe and [0 1 0] α-Fe directions with intensity maxima at positions corresponding to diffraction spots of CrN/VN of rock-salt crystal structure type oriented in Baker–Nutting OR () [Citation56] with respect to the ferrite matrix. These streaks of intensities are a consequence of strain broadening due to the development of (semi-) coherent nitride platelets on
-habit planes (the maximal misfit strain occurs in
directions perpendicular to the nitride platelets) and the very thin nature of the MeN platelets. Note that these streaks of intensity are less well observable in case of the Fe–0.2Ti–2.0Si alloy and are most pronounced in case of the Fe–0.3V–2.0Si alloy. Both the Fe–0.2Ti–2.0Si and the Fe–2.0Cr–2.0Si alloy specimens additionally show, in contrast with the Fe–0.3V–2.0Si alloy specimen, relatively small cubically shaped precipitate particles (Figure (a2) and (b2)); small as compared to their size after longer nitriding times (see Figures ). These observations suggest that these particles are amorphous Si3N4 (for direct evidence see discussion of Figures , as reported before for nitrided binary Fe–Si [Citation39,40,57], an effect likely due to control by interface thermodynamics [Citation58,59].
Figure 3. (colour online) TEM images recorded from ternary Fe–Me–Si alloy (with Me = Ti, Cr and V) specimens after nitriding at 580 °C with r
N = 0.1 atm−1/2 for 10 h in case of the Fe–0.2Ti–2.0Si alloy and for 24 h in case of the Fe–2.0Cr–2.0Si and Fe–0.3V–2.0Si alloys. The specimens show the development of nanosized MeN platelets (BF images (a1), (b1) and (c)). These platelets are associated with a coffee-bean-like contrast due to their (semi-) coherency with the surrounding ferrite matrix. The corresponding SADPs ([0 0 1]α-Fe-zone axis) show diffraction spots belonging to the ferrite matrix, iron oxide (-diffraction spots at the location of the forbidden 1 0 0α-Fe diffraction spot due to a surface-oxide layer which unavoidable develops upon TEM specimen preparation; see also Section 2.5 in Ref. [Citation70]) and in case of the Fe–2.0Cr–2.0Si and Fe–0.3V–2.0Si alloy specimens streaking along [1 0 0]α and [0 1 0]α directions. Further, in the SADP of the Fe–2.0Cr–2.0Si alloy specimen intensity maxima at the position of rock-salt type CrN diffraction spots, in compliance with a Baker–Nutting OR with respect to the ferrite matrix, are visible. Both, the BF images of the Fe–0.2Ti–2.0Si alloy specimen and the Fe–2.0Cr–2.0Si alloy specimen show, in addition to TiN/CrN platelets, cubical Si3N4 particles (see BF images (a2) and (b2)) in the ferrite matrix. The BF image of the Fe–0.2Ti–2.0Si alloy specimen (b2) shows additionally a ferrite-grain boundary covered with a band of amorphous Si3N4 (black line from top to bottom).
![Figure 3. (colour online) TEM images recorded from ternary Fe–Me–Si alloy (with Me = Ti, Cr and V) specimens after nitriding at 580 °C with r N = 0.1 atm−1/2 for 10 h in case of the Fe–0.2Ti–2.0Si alloy and for 24 h in case of the Fe–2.0Cr–2.0Si and Fe–0.3V–2.0Si alloys. The specimens show the development of nanosized MeN platelets (BF images (a1), (b1) and (c)). These platelets are associated with a coffee-bean-like contrast due to their (semi-) coherency with the surrounding ferrite matrix. The corresponding SADPs ([0 0 1]α-Fe-zone axis) show diffraction spots belonging to the ferrite matrix, iron oxide (220Fe3O4-diffraction spots at the location of the forbidden 1 0 0α-Fe diffraction spot due to a surface-oxide layer which unavoidable develops upon TEM specimen preparation; see also Section 2.5 in Ref. [Citation70]) and in case of the Fe–2.0Cr–2.0Si and Fe–0.3V–2.0Si alloy specimens streaking along [1 0 0]α and [0 1 0]α directions. Further, in the SADP of the Fe–2.0Cr–2.0Si alloy specimen intensity maxima at the position of rock-salt type CrN diffraction spots, in compliance with a Baker–Nutting OR with respect to the ferrite matrix, are visible. Both, the BF images of the Fe–0.2Ti–2.0Si alloy specimen and the Fe–2.0Cr–2.0Si alloy specimen show, in addition to TiN/CrN platelets, cubical Si3N4 particles (see BF images (a2) and (b2)) in the ferrite matrix. The BF image of the Fe–0.2Ti–2.0Si alloy specimen (b2) shows additionally a ferrite-grain boundary covered with a band of amorphous Si3N4 (black line from top to bottom).](/cms/asset/069c25a6-4a86-432f-b813-e979deeeff95/tphm_a_952258_f0003_oc.gif)
Figure 4. TEM images recorded from the ternary Fe–0.5Ti–2.0Si alloy specimen after nitriding at 580 °C with r
N = 0.1 atm−1/2 for 77 h (after this nitriding time all TiN and nearly all Si3N4 have precipitated). (a) BF image showing two cubical Si3N4 particles at the edge of the TEM foil; tiny (TiN) platelets can be discerned within these Si3N4 particles. (b) The corresponding SADP ([0 0 1] α-Fe-zone axis) with diffraction spots of the ferrite matrix (α), iron oxide (see caption of Figure ) and very weak streaks of intensities along [1 0 0]α and [0 1 0]α directions. (c) DF image recorded using the (weak) intensity of a streak (location of the aperture (at the position of the possible, but not observable, -diffraction spot) has been indicated with a dashed circle in the SADP) exhibits crystalline (TiN) platelets with a pronounced bright contrast in the ferrite matrix and within the cubical Si3N4 particles. The cubical Si3N4 particles appear also brighter than the surrounding matrix due to the diffuse intensity resulting from electron scattering by the amorphous Si3N4 particles. (d) DF image, recorded using the diffuse intensity, showing the Si3N4 particles by bright contrast with the matrix. Note the high Si3N4-particle density at this practically end stage of the precipitation process.
![Figure 4. TEM images recorded from the ternary Fe–0.5Ti–2.0Si alloy specimen after nitriding at 580 °C with r N = 0.1 atm−1/2 for 77 h (after this nitriding time all TiN and nearly all Si3N4 have precipitated). (a) BF image showing two cubical Si3N4 particles at the edge of the TEM foil; tiny (TiN) platelets can be discerned within these Si3N4 particles. (b) The corresponding SADP ([0 0 1] α-Fe-zone axis) with diffraction spots of the ferrite matrix (α), iron oxide (see caption of Figure 3) and very weak streaks of intensities along [1 0 0]α and [0 1 0]α directions. (c) DF image recorded using the (weak) intensity of a streak (location of the aperture (at the position of the possible, but not observable, 002¯TiN-diffraction spot) has been indicated with a dashed circle in the SADP) exhibits crystalline (TiN) platelets with a pronounced bright contrast in the ferrite matrix and within the cubical Si3N4 particles. The cubical Si3N4 particles appear also brighter than the surrounding matrix due to the diffuse intensity resulting from electron scattering by the amorphous Si3N4 particles. (d) DF image, recorded using the diffuse intensity, showing the Si3N4 particles by bright contrast with the matrix. Note the high Si3N4-particle density at this practically end stage of the precipitation process.](/cms/asset/65565600-f679-49d5-bde6-b7ae33c14d58/tphm_a_952258_f0004_b.gif)
Figure 5. TEM images recorded from the ternary Fe–2.0Cr–2.0Si alloy specimen after nitriding at 580 °C with r N = 0.1 atm−1/2 for 648 h (after this nitriding time all CrN and all Si3N4 have precipitated). In contrast with the electron transparent foils pertaining to the TEM analysis shown in Figures , and , this TEM foil was prepared from the core region (around 500 μm below the surface). (a) The BF image shows two cubical Si3N4 particles intersected by significantly coarsened (as compared to the initial stage: see Figure (b1)) CrN precipitates. (b) The corresponding SADP (with [0 0 1]α-Fe-zone axis) shows diffraction spots of the ferrite matrix (α), iron oxide (see caption of Figure ) and CrN of rock-salt crystal-structure type, satisfying a Baker–Nutting OR with respect to the ferritic matrix. (c) DF image, recorded using the diffuse intensity and a weak diffraction spot of CrN (see the large dashed circle in (b)), shows Si3N4 particles and CrN platelets with a pronounced bright contrast. (d) BF image showing two Si3N4 particles apparently nucleated at the tip of coarsened CrN platelets. (e) BF image showing Si3N4 particles grown along the faces of CrN platelets.
![Figure 5. TEM images recorded from the ternary Fe–2.0Cr–2.0Si alloy specimen after nitriding at 580 °C with r N = 0.1 atm−1/2 for 648 h (after this nitriding time all CrN and all Si3N4 have precipitated). In contrast with the electron transparent foils pertaining to the TEM analysis shown in Figures 3, 4 and 6, this TEM foil was prepared from the core region (around 500 μm below the surface). (a) The BF image shows two cubical Si3N4 particles intersected by significantly coarsened (as compared to the initial stage: see Figure 3(b1)) CrN precipitates. (b) The corresponding SADP (with [0 0 1]α-Fe-zone axis) shows diffraction spots of the ferrite matrix (α), iron oxide (see caption of Figure 3) and CrN of rock-salt crystal-structure type, satisfying a Baker–Nutting OR with respect to the ferritic matrix. (c) DF image, recorded using the diffuse intensity and a weak diffraction spot of CrN (see the large dashed circle in (b)), shows Si3N4 particles and CrN platelets with a pronounced bright contrast. (d) BF image showing two Si3N4 particles apparently nucleated at the tip of coarsened CrN platelets. (e) BF image showing Si3N4 particles grown along the faces of CrN platelets.](/cms/asset/c8be3920-bc53-4654-b29f-733407e570ba/tphm_a_952258_f0005_b.gif)
Figure 6. TEM images recorded from the ternary Fe–0.3V–2.0Si alloy specimen after nitriding at 580 °C with r N = 0.1 atm−1/2 for 1656 h (after this nitriding time all VN and all Si3N4 have precipitated). (a) BF image showing a cut through an octapod-shaped Si3N4 precipitate, with cross-over distance from tip to tip of approximately 350 nm; note the VN platelets within the Si3N4 particle. (b) The corresponding SADP ([0 1 1]α-Fe-zone axis) shows diffraction spots belonging to the ferrite matrix and VN and a diffuse intensity (“halo”) around the primary electron beam due to electron scattering by the amorphous Si3N4 precipitates. (c) DF image, recorded using the intensity of the 002VN-diffraction spot, exhibiting crystalline (VN) platelets with a pronounced bright contrast in the ferrite matrix and within the cubical Si3N4 particle. The cubical Si3N4 particles appear also brighter than the surrounding matrix due to the diffuse intensity resulting from electron scattering by the amorphous Si3N4 particle. (d) DF image, recorded using the diffuse intensity, showing multiple illuminated Si3N4 particles by bright contrast with the matrix.
![Figure 6. TEM images recorded from the ternary Fe–0.3V–2.0Si alloy specimen after nitriding at 580 °C with r N = 0.1 atm−1/2 for 1656 h (after this nitriding time all VN and all Si3N4 have precipitated). (a) BF image showing a cut through an octapod-shaped Si3N4 precipitate, with cross-over distance from tip to tip of approximately 350 nm; note the VN platelets within the Si3N4 particle. (b) The corresponding SADP ([0 1 1]α-Fe-zone axis) shows diffraction spots belonging to the ferrite matrix and VN and a diffuse intensity (“halo”) around the primary electron beam due to electron scattering by the amorphous Si3N4 precipitates. (c) DF image, recorded using the intensity of the 002VN-diffraction spot, exhibiting crystalline (VN) platelets with a pronounced bright contrast in the ferrite matrix and within the cubical Si3N4 particle. The cubical Si3N4 particles appear also brighter than the surrounding matrix due to the diffuse intensity resulting from electron scattering by the amorphous Si3N4 particle. (d) DF image, recorded using the diffuse intensity, showing multiple illuminated Si3N4 particles by bright contrast with the matrix.](/cms/asset/1e9de908-9144-4072-a765-672bfda70839/tphm_a_952258_f0006_b.gif)
TEM images recorded from a Fe–0.5Ti–2.0Si alloy specimen nitrided for 77 h (after this nitriding time all Ti and nearly all Si have precipitated as TiN and Si3N4, respectively; cf. Figure (a)) are shown in Figure . The BF image (Figure (a)) reveals two cubical Si3N4 precipitates which remained upon electropolishing at the edge of the TEM foil due to selective dissolution of the ferrite matrix. The edge length of the cubes is approximately 30 nm and the cube faces are parallel to -lattice planes. The corresponding SADP (Figure (b)), recorded in [0 0 1]α-Fe-zone axis, shows diffraction spots from the ferrite matrix together with an extremely weak streaking in [0 1 0] α-Fe and [1 0 0] α-Fe directions. A DF image (Figure (c)) recorded using the weak intensity of a streak at the location of the expected 002TiN-diffraction spot (indicated with a circle in the SADP in Figure (b)) shows, by bright appearance, TiN platelets in both the ferrite matrix and the amorphous Si3N4 particles. In the DF image, the cubical Si3N4 particles also appear with bright contrast indicating their amorphous nature: the diffuse halo of intensity generated by electron scattering by the amorphous Si3N4 particles at the location of 002TiN-diffraction spot implies illumination of both the amorphous particles and crystalline TiN platelets in the DF image (see Figure (c)); the DF image formed by placing the SADP aperture at a location of diffuse intensity, where no TiN spot occurs, leads to bright appearance of only the amorphous Si3N4 particles in the corresponding DF image (Figure (d)).
Both the presence of much smaller TiN platelets (length around 4 nm) within relatively large Si3N4 particles and the recognition that these TiN platelets have the same orientation as the TiN particles in the ferrite matrix suggest that the TiN platelets within the Si3N4 particles have precipitated first in the ferrite matrix, in accordance with a Baker–Nutting OR, and were incorporated later into (overgrown by) growing Si3N4 particles.
The Fe–2.0Cr–2.0Si alloy specimen nitrided for 648 h (at this stage all Cr and all Si have precipitated as CrN and Si3N4, respectively) exhibits cubical Si3N4 particles (edge length around 40 nm) which incorporate parts of significantly coarsened CrN platelets (platelet length up to 80 nm; cf. Figure (a)). Due to the significant coarsening of the CrN precipitates diffraction spots belonging to CrN are (now) visible in the corresponding SADP (see the SADP in Figure (b) and compare it with that in Figure (b1)). The DF image shown in Figure (c) was recorded using the diffuse intensity around the primary electron beam and a weak diffraction spot of CrN. Similar to the observations for the Fe–Ti–Si alloy, the Si3N4 particles and CrN platelets show a bright contrast and thus the Si3N4 particles are amorphous. The BF images suggest that small (as compared to the CrN platelet length; see above) Si3N4 particles heterogeneously nucleate at the incoherent CrN/α-Fe interface perpendicular to the platelet faces (Figure (d)) and grow along the (initially) coherent CrN/α-Fe interface of the platelet faces with the matrix (Figure (e)).
Nitriding of a Fe–0.3V–2.0Si alloy specimen for 1656 h leads to coarsening of crystalline VN precipitates and to the development of large amorphous Si3N4 particles with a presumably octopod-shapeFootnote2 (Figure ). Further, crystalline VN platelets have become incorporated, by overgrowth, into the amorphous and much larger Si3N4 particles. Corresponding SADP (Figure (b)) shows diffraction spots belonging to the ferrite matrix and to VN. The DF image shown in Figure (c) was recorded using the intensity of a VN-diffraction spot and as a consequence the VN precipitates show a distinctively bright contrast. Note the similar orientation of VN platelets in the Si3N4 particle and in the matrix (see above discussion for the Fe–0.5Ti–2.0Si alloy). The DF image recorded by placing the SADP aperture at a location of diffuse intensity, where no VN spot occurs, leads to bright appearance of the octapod-shaped amorphous Si3N4 particles (Figure (d)).
3.3. Ferrite-lattice parameter changes as a function of nitriding time; macrostrain and microstrain
The diffractograms recorded from the surface of the nitrided specimens show only reflections from the ferrite matrix. A comparison of the -reflections of the binary Fe–2.0Si alloy and the ternary Fe–Me–2.0Si alloys, before nitriding (stage 1), and after nitriding for times (i) at which the ferrite matrix is saturated with dissolved nitrogen and all Me, in case of the Fe–Me–2.0Si alloys, has precipitated as MeN (at around 24–26 h; stage 2), and (ii) at which, additionally (for the Fe–Me–2.0Si alloys), all Si has precipitated as Si3N4 (stage 3), is provided by Figure . Again (cf. Section 2.4), note that, for the homogenously nitrided specimens considered here, no (macro)stress-depth profiles occur, thereby allowing an interpretation of ferrite-lattice parameter changes as caused only by possible changes of solute contents and (homogeneous) hydrostatic (macro)stress. Thus, upon nitriding, ferrite-peak shifts pertaining to the times/conditions (i) and (ii), indicated above, can be due to a change of the ferrite-lattice parameter associated with (a) the change in the contents of interstitially dissolved nitrogen and substitutionally dissolved Me and Si in the ferrite matrix, upon precipitation of internal nitrides, and (b) the establishment of a macroscopic, tensile, hydrostatic component of stress as a consequence of the elastic accommodation of the MeN-particle/α-Fe matrix misfit; such change of the matrix-lattice parameter upon nitriding was demonstrated for the first time for precipitation of Si in supersaturated Al–Si alloys in Ref. [Citation48]. On this basis ((a) + (b)), the measured ferrite-lattice parameter changes as a function of nitriding time is interpreted in the following as reflecting the different stages of nitride precipitation.
Figure 7. (colour online) X-ray diffractograms (normalized with respect to integrated intensity) in the diffraction-angle range of the 200α-Fe reflection recorded from the surface of the binary Fe–2.0Si alloy specimen and the ternary Fe–Me–Si alloy (with Me = Ti, Cr and V) specimens before nitriding and after nitriding at 580 °C with a nitriding potential of 0.1 atm%1/2 for times (i) after the 1 mm thick specimens have been (homogenously) through nitrided (cf. Section 2.2) and (ii) after in addition to MeN, practically all Si3N4 has precipitated. In the diffractograms only reflections belonging to ferrite are observed. The intensity data (circles) were fitted with asymmetrical (split) pseudo-Voigt functions for the Kα1 and Kα2 components (continuous lines; cf. Section 2.4).
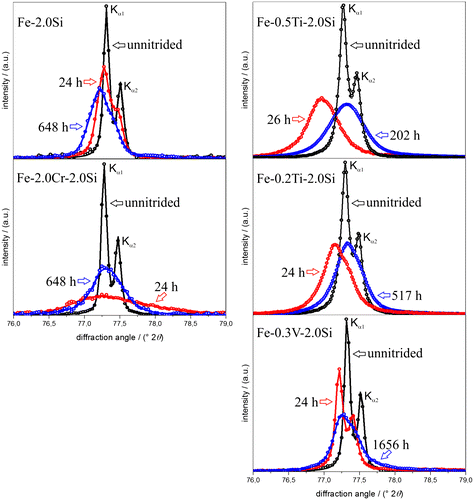
The ferrite-lattice parameters of unnitrided (stage 1), 24–26 h nitrided (stage 2) and homogeneously through nitrided (stage 3) specimens of the Fe–2.0Si alloy and the Fe–Me–2.0Si alloys were determined, applying Bragg’s law, from the measured positions of -ferrite (XRD) Kα1 peaks, corrected for the instrumental offset (cf. Section 2.4). The measured changes in the lattice parameter of ferrite for a particular stage of nitriding, with respect to its value in the preceding stage, are presented in Table (the last two columns). The measured lattice-parameter values of the unnitrided alloys and the corresponding values as predicted by using the lattice-parameter data for the different binary iron-based alloys as presented in Ref. [Citation61], by interpolation adopting “Végard’s law” even in the present case of ternary instead of binary iron-based alloys, are also presented in Table .
A fair agreement between measured and predicted lattice parameter values of the unnitrided Fe–Me–Si alloys occurs (Table ; first two columns), recognizing the experimental accuracy (about ±0.0002 Å; cf. Section 2.4). Moreover, the possible discrepancies may be ascribed to the non-validated assumption of a Végard-like dependence of the lattice parameter on content of solutes even in the present case of ternary alloys.
The small, positive change of the ferrite-lattice parameter in case of the binary Fe–2.0Si alloy after nitriding for 24 h (stage 2) is in agreement with the lattice parameter increase expected due to the dissolution of 0.2 at.% of nitrogen in ferrite (see Section 3.1; according to Ref. [Citation62], an increase of 0.0014 Å of the lattice parameter of ferrite is expected upon dissolution of 0.2 at.% nitrogen). This suggests that at this stage, all Si remains in dissolved state, i.e. no Si3N4 precipitation occurs (cf. Section. 3.1). A further increase in the ferrite-lattice parameter occurs in stage 3, which is compatible with the expectation that upon precipitation of Si, in stage 3, the lattice parameter of the ferrite matrix increases further [Citation40,54]. A depletion of 2 at.% of Si solute in ferrite results in an increase of the ferrite-lattice parameter of the order 0.0013 Å [Citation61]. Further, the removal of 2 at.% Si from the ferrite matrix leads to an increased equilibrium nitrogen solubility (plus 0.09 at.% nitrogen; see Section 3.1) and thus to a further increase of the ferrite-lattice parameter of 0.0006 Å [Citation62]. The good agreement of the thus predicted, total (0.0019 Å) and measured (0.0022 Å) lattice parameter changes for stage 3 is compatible with the absence of any possible hydrostatic tensile misfit stress due to misfitting Si3N4 precipitates. As indicated in Section 3.1, the precipitation of Si3N4 in a ferritic matrix is associated with such a large volume misfit (>100%) that it is entirely accommodated plastically by dislocation generation (as shown in Ref. [Citation60]).
Considering stage 2 and as compared to the binary Fe–Si alloy, for all ternary Fe–Me–Si alloys a much larger, positive change in the ferrite-lattice parameter occurs (Table ). Note that the removal of dissolved Me from the solid solution, upon MeN development, leads to a decrease in the ferrite lattice parameter (opposite to an increase as induced by Si depletion (see above discussion), which depletion does not occur in stage 2 (see Sections 3.1 and 3.2)). Hence, the occurrence of the large, positive change in the lattice parameter in stage 2 for the Fe–Me–Si alloys is direct evidence for the development of a hydrostatic tensile misfit strain, as expected according to Ref. [Citation48], upon elastic accommodation of the MeN-particle/α-Fe volume misfit.
Considering stage 3, and as compared to stage 2, for all ternary Fe–Me–Si alloys an opposite (i.e. negative) change of the ferrite-lattice parameter occurs. Upon only precipitation of Si in stage 3 in the Fe–Me–Si alloys, the ferrite-lattice parameter increases (see above). Hence, the occurrence of an, in absolute sense, much larger and negative ferrite-lattice parameter change for the Fe–Me–Si alloys in stage 3, is ascribed to the relaxation of the tensile hydrostatic component of misfit stress, induced in stage 2, upon the continued nitriding (aging) in stage 3. This is compatible with the observations reported in Sections 3.1 and 3.2: In stage 3, the MeN particles, which (largely) all developed in stage 2, grow and become incoherent with the surrounding ferrite matrix, leading to the relaxation of the misfit stresses.
As compared to VN, TiN exhibits a larger misfit with the ferrite matrix. With a view to the above discussion, then a larger hydrostatic, tensile macrostress in the ferrite matrix is expected, leading, for the same amount of alloying element, to a larger increase of the ferrite-lattice parameter. This expectation is compatible with the experimental results for the lattice parameter change after 24–26 h of nitriding (cf. results for Fe–V–Si and Fe–Ti–Si for stage 2 in Table ). Also note that the increase of the ferrite-lattice parameter is larger for the alloy with the higher Ti content, which is in agreement with the given interpretation. In view of the misfit of TiN with the ferrite matrix being larger than for VN, it can be expected that upon continued nitriding (aging), at identical conditions, TiN will lose coherency with the ferrite matrix sooner than VN. Indeed, whereas for the Fe–V–Si alloy in stage 3, i.e. after all Si3N4 has precipitated, the relaxation of the (coherency) macrostrain in the ferrite matrix has not been completed, for the Fe–Ti–Si alloys, this relaxation appears to be fully realized (cf. corresponding results in the last two columns of Table ).
As compared to VN and TiN, CrN takes an intermediate position regarding its misfit with the ferrite matrix. An in this sense modified discussion as above can be given for the macrostrain changes (ferrite-lattice parameter changes) for the Fe–Cr–Si alloy. Doing so, it should be recognized that the amount of alloying-element Me is much larger in the Fe–Cr–Si alloy than in the Fe–V–Si and Fe–Ti–Si alloys.
The diffraction-line broadening data support the above interpretation. The FWHM of the 200α-Fe Kα1 peak increases for all Fe–Me–Si alloys upon nitriding for 24–26 h (stage 2) and the increase is the more pronounced the larger the misfit between MeN and the ferrite matrix and the higher the Me content (Table ).These observations strongly suggest that the nitriding induced diffraction-line broadening at this stage 2 reflects the development of microstrain (i.e. localized variation in strain due to the misfit-strain fields surrounding the (semi-)coherent MeN precipitates as reported in Ref. [Citation63]. The semi-coherent MeN (with Me = Ti, Cr and V) platelets developing along lattice planes of the matrix, according to the Baker–Nutting OR, induce tensile and compressive misfit stresses parallel and perpendicular to the faces of the platelets, respectively. Thereby, a locally varying, tetragonal distortion of the platelet surrounding ferrite matrix occurs, which contributes to a large extent to the (asymmetry of the) diffraction-line broadening especially observed for the 200α-Fe reflex [Citation63]. Upon continued nitriding until nitrogen saturation, i.e. Si3N4 has precipitated in addition to MeN (stage 3), the FWHM of the 200α-Fe peak has decreased as compared to the FWHM after 24 h of nitriding (stage (2)) due to relaxation of the MeN/α-Fe misfit, relatively most pronouncedly for the Fe–Ti–Si alloys and least for the Fe–V–Si alloy, which is fully compatible with the above interpretation of the (average) ferrite-lattice parameter change.
4. General discussion
4.1. Separate precipitations of binary nitrides, MeN and Si3N4
In the nitrided ternary Fe–Me–Si (with Me = Ti, Cr and V) alloys, precipitation of separate binary, crystalline cubic rock-salt crystal-structure type Me-nitride (MeN) and binary, amorphous Si-nitride (Si3N4) occurs, as indicated by the mass-uptake and TEM data (Sections 3.1 and 3.2). This contrasts with the nitriding behaviour of other ternary iron-based alloys: in Fe–Cr–Al and Fe–Cr–Ti alloys mixed ternary nitrides, Me a(1−x) Me b(x)N, develop [Citation64–68]. The occurrence of the one or the other nitride-precipitation process can be understood as follows.
The values of the so-called interaction parameter, as defined in Ref. [Citation24], for MeN (with Me = Ti, Cr and V) development in ferrite compared to the value of the interaction parameter for SiN1.33 (Si3N4) development in ferrite (cf. Table and Section 1) are largely different, and thus suggest the improbability of formation of ternary mixed nitrides upon nitriding Fe–Me–Si alloys. As compared to crystalline Si3N4, MeN has a distinctly different crystal structure and Me–N bonding character [Citation69].
Table 4. Interaction parameter, I, defined as the ratio of the change of the chemical Gibbs energy upon precipitation of Me (with Me = Al, Ti, Cr, V and Si) and N, both dissolved in α-Fe (ferrite), as MeN
n
, at 773 K. 
, where 
is the Gibbs energy of formation for one mole MeNn and 
is the Gibbs energy of dissolution of 1 mole nitrogen in ferrite (Fe–Me interaction is ignored). 
is the misfit-strain energy developing upon precipitation of MeN
n
in ferrite, where 
is the shear modulus of ferrite, C is given by 3
/(3
+ 4
), with 
as the bulk modulus of MeN, ε is the linear misfit parameter and 
is the molar volume of the nitride. The misfit-strain energy was calculated according to Ref. [Citation24] for the case of full elastic accommodation of the misfit.
In the case of ternary iron-based alloys which contain two different alloying-elements (Me a , Me b ), which both can form nitrides of identical crystal structure, precipitation of mixed ternary nitrides is more likely. This explains the development of metastable, cubic rock-salt crystal-structure type, mixed ternary nitrides Cr x Al1−x N and Cr x Ti1−x N in nitrided ternary Fe–Cr–Al [Citation64–66] and Fe–Cr–Ti [Citation67,68] alloys. The development of mixed nitrides in the case of Fe–Cr–Al and Fe–Cr–Ti alloys is moreover favoured due to the decrease of precipitate/matrix misfit as compared to the development of the stable binary nitrides in the ferrite matrix [Citation64,68]: Incorporation of Al into CrN decreases the misfit of CrN and ferrite; incorporation of Cr into TiN decreases the misfit of TiN and ferrite.
4.2. Influence of coherency strain on the Si3N4-precipitation kinetics
The ternary Fe–Me–Si alloys (with Me = Ti, Cr and V) show distinctively different rates of Si3N4 precipitation as reflected by the nitriding rates (Section 3.1). The rate of Si3N4 precipitation upon nitriding is highest in the Fe–Ti–Si alloys, followed by the Fe–Cr–Si alloy, and slowest in the Fe–V–Si alloy (cf. Section 3.1). As compared to the rate of Si3N4 precipitation in binary Fe–Si alloy, the additional presence of Ti and Cr appears to have an accelerating effect, whereas the additional presence of V retards the precipitation of Si3N4. These effects on the Si3N4-precipiation kinetics can be ascribed to the varying degree of coherency, strain-field development, associated with the preceding practically fully (Me = Cr, V)) or largely (Me = Ti) precipitation of (semi-) coherent cubic rock-salt crystal-structure type MeN, as follows.
The presence of coherency, misfit-strain fields in the ferritic matrix, arisen by the (preceding) precipitation of MeN particles, is an obstacle for dislocation mobility, and thus obstructs the development of Si3N4: Si3N4 has a large volume misfit with the ferrite matrix such that plastic accommodation associated with dislocation generation accompanies the precipitation of Si3N4 ([Citation60]; cf. discussion of ferrite-lattice parameter changes for the Fe–Si alloy upon nitriding in Section 3.3). It may thus be expected that the precipitation of Si3N4 is hindered most severely if the misfit-strain fields around the MeN precipitates are most pronounced. As follows from the results presented in Sections 3.2 and 3.3, in case of the Fe–V–Si alloy, the degree of coherency is larger (e.g. see Figure (c): SADP with distinct streaks) and upon prolonged long-time nitriding (involving aging/coarsening of the VN precipitates) this coherency is only partly lost (see Table and Figure ; discussed in Section 3.3). Both effects (degree of coherency and its perseverance) are much less pronounced for the Fe–Ti–Si alloys (see Sections 3.2 and 3.3). On this basis, it can be understood that pronounced retardation of the Si3N4 precipitation, as compared to the rate of Si3N4 precipitation in the binary Fe–Si alloy, occurs for the Fe–V–Si alloy.
Evidently, the TiN precipitates can realize/maintain their coherency and elastic accommodation of their misfit with the ferrite matrix much less well than the VN precipitates (the misfit with the ferritic matrix decreases in the order TiN → CrN → VN). As a matter of fact, whereas for the Fe–V–Si and Fe–Cr–Si alloys, the Si3N4 precipitation effectively occurs after full MeN precipitation (see plateaus in Figure (b) after 24 h of nitriding), partial overlap with the subsequent Si3N4 precipitation occurs in case of the Fe–Ti–Si alloys (no plateau in Figure (b) after 24 h of nitriding).
Heterogeneous precipitation of Si3N4 can be accelerated over homogeneous precipitation if sufficient favourable nucleation sites exist in the ferrite matrix. As soon as upon coarsening/aging of the MeN platelets incoherency occurs at the MeN/α-Fe interface such nucleation sites are produced (note the finely dispersed nature of the MeN precipitates). Considering the state of (coherency) stress around the MeN platelets, coherency is best realized and maintained along the faces of the MeN platelets, where -planes of the ferrite matrix are parallel to
-planes of MeN, whereas incoherency is expected first at the narrow surface/rim of the platelets, where
-planes of the ferrite matrix are parallel to
-planes of MeN (see the schematic Figure ). Recognizing that the interfacial energy of an incoherent interface is distinctively larger than that of a coherent interface [Citation27], heterogeneous nucleation of Si3N4 is expected at such incoherent interfaces. This has been observed indeed in this study (see Figure (d)). Again, upon continued nitriding (i.e. aging) incoherency for the MeN/α-Fe interface is observed first for the TiN precipitates and latest for the VN precipitates (see results presented in Sections 3.2 and 3.3 and the above discussion), in accordance with the (volume) misfit for TiN being largest. As a consequence the provision of nucleation sites for Si3N4 at (the high density of) MeN/α-Fe interfaces leads to an acceleration of the Si3N4 precipitation in the Fe–Ti–Si and, to a much lesser degree, in the Fe–Cr–Si alloys, as compared to the Si3N4 precipitation in the binary Fe–Si alloy.
Figure 8. Schematic drawing of a (semi-) coherent MeN platelet in the ferrite matrix. Due to the (semi-)coherency of the misfitting MeN platelet, the ferrite matrix surrounding the platelet is tetragonally distorted: (i) Two principal tensile stresses act parallel to the platelet; and (ii) a principal compressive stress acts normal to the platelet.
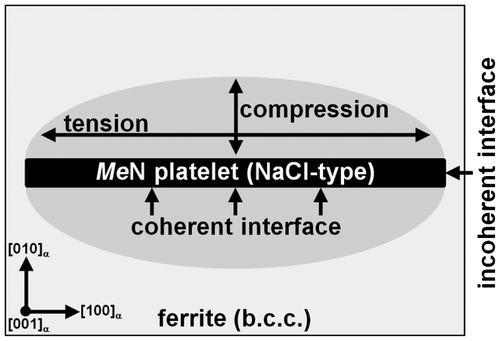
5. Conclusions
In contrast with the formation of “mixed” nitrides, Me a(1−x) Me b(x)N, in Fe–Al–Cr and Fe–Cr–Ti alloys upon nitriding, nitriding of Fe–Me–Si alloys (with Me = Ti, Cr and V) leads to the precipitation of MeN and Si3N4 nitrides, separately and successively: first, all MeN precipitate as finely dispersed, nanosized and crystalline platelets. The MeN platelets have the rock-salt type crystal structure and maintain the Baker–Nutting OR with the surrounding ferrite matrix. Subsequently, all Si precipitates as larger, amorphous, cubically Si3N4 particles with the cube faces parallel to
planes. The formation of separate MeN and Si3N4 nitrides, and not a mixed nitride, can be ascribed to the large difference of the Me–N and Si–N interactions.
The precipitation rate of Si3N4 differs strongly for the different Fe–Me–Si alloys; the Si3N4 precipitation is pronouncedly retarded in the Fe–V–Si alloy and accelerated in the Fe–Ti–Si and Fe–Cr–Si alloys, as compared to the binary Fe–Si alloy. On the basis of transmission electron microscopy and diffraction data, and XRD-line shift and broadening data, these striking differences in nitriding kinetics could be ascribed to subtle differences in the development and relaxation of coherency strains:
A strongly retarded Si3N4 precipitation is observed in the Fe–V–Si alloy, as a consequence of the highest degree of coherency of MeN precipitate and ferrite matrix occurring for VN (as compared to TiN and CrN) and of preservation of this coherency for a distinct part upon prolonged nitriding.
An accelerated Si3N4 precipitation is observed for the Fe–Ti–Si and Fe–Cr–Si alloys due to a rapidly occurring coherent → incoherent transition for the TiN/α-Fe, CrN/α-Fe interfaces. Subsequent heterogeneous nucleation of Si3N4 at these incoherent interfaces takes place. The larger the alloying element, Ti, content in the Fe–Ti–Si alloy, the higher the TiN-particle density and the faster the Si3N4 precipitation (more nucleation sites).
The Si3N4 precipitation occurs in the Fe–Cr–Si alloy, and in particular in the Fe–V–Si alloy, largely separated in time, after the MeN precipitation, whereas a partial overlap occurs in the Fe–Ti–Si alloys. This phenomenon is consistent with a coherent → incoherent transition of the CrN/α-Fe and VN/α-Fe interfaces after completed CrN/VN precipitation, and a partial coherent → incoherent transition of the TiN/α-Fe interface before completed TiN precipitation.
Acknowledgements
The authors thank Mr Dipl.-Ing. (FH) P. Kress and Mr W. Engelhardt for assistance with the nitriding experiments and Prof Dr van Aken for providing access to the TEM (all are with the Max Planck Institute for Intelligent Systems, Stuttgart).
Notes
1. Excess nitrogen denotes the part of the nitrogen uptake (after saturation) above that expected for only precipitation of MeN and realization of the equilibrium solubility of unstrained ferrite. This extra nitrogen can be (i) adsorbed at the MeN/α-Fe interface, (ii) dissolved in the ferrite matrix due to the strain field surrounding (semi-) coherent MeN precipitates and (iii) trapped at dislocations [Citation24,51].
2. A change of morphology happens upon Si3N4 precipitation in the long-time nitrided Fe–0.3V–2.0Si alloy specimen. At the beginning (216 h) of Si3N4 precipitation, the Si3N4 particles are cubical, whereas after completion of the precipitation process (1656 h), the particles have become octapod-shaped (see Ref. [Citation43]). Comparably, long nitriding/ageing times were not applied to the other alloy specimens of this work. A similar change in Si3N4 precipitate morphology upon nitriding a binary Fe–4.5Si alloy for long times at 650 °C (923 K) was observed and discussed in Ref. [Citation60].
References
- E.J. Mittemeijer , Fundamentals of nitriding and nitrocarburizing , in ASM Handbook , Vol. 4A, J.I. Dossett and G.E. Totten , eds., ASM International, Ohio, 2013, p.619.
- D. Liedtke , U. Baudis , J. Boßlet , U. Huchel , H. Klümper-Westkamp , W. Lerche and H.-J. Spies , Wärmebehandlung von Eisenwerkstoffen – Nitrieren und Nitrocarburieren , 3rd ed., Expert-Verlag, Renningen-Malmsheim, 2006.
- P.M. Unterweiser and A.G. Gray (eds.), Source Book on Nitriding , ASM, Metals Park, OH , 1977.
- E. Menthe , K.T. Rie , J.W. Schultze and S. Simson , Surf. Coat. Technol. 74–75 (1995) p.412.10.1016/0257-8972(95)08246-8
- B. Larisch , U. Brusky and H.J. Spies , Surf. Coat. Technol. 116–119 (1999) p.205.10.1016/S0257-8972(99)00084-5
- Y. Tomio , S. Kitsuya , K. Oh-Ishi , K. Hono , G. Miyamoto and T. Furuhara , Metall. Mater. Trans. A 45 (2014) p.239.10.1007/s11661-013-1991-5
- Y. Lin , J. Wang , D. Zeng , R. Huang and H. Fan , J. Mater. Eng. Perform. 22 (2013) p.2567.10.1007/s11665-013-0545-8
- H. Selg , S.R. Meka , M. Kachel , R.E. Schacherl , T. Waldenmaier and E.J. Mittemeijer , J. Mater. Sci. 48 (2013) p.4321.10.1007/s10853-013-7248-2
- A.R. Mashreghi , S.M.Y. Soleimani and S. Saberifar , Mater. Des. 46 (2013) p.532.10.1016/j.matdes.2012.10.046
- G. Park , G. Bae , K. Moon and C. Lee , J. Therm. Spray Technol. 22 (2013) p.1366.10.1007/s11666-013-0035-4
- S.A. Nikulin , S.O. Rogachev , V.M. Khatkevich and A.B. Rozhnov , Met. Sci. Heat Treat. 55 (2013) p.351.10.1007/s11041-013-9633-5
- C.E. Pinedo , L.B. Varela and A.P. Tschiptschin , Surf. Coat. Technol. 232 (2013) p.839.10.1016/j.surfcoat.2013.06.109
- L.B. Winck , J.L.A. Ferreira , J.A. Araujo , M.D. Manfrinato and C.R.M. da Silva , Surf. Coat. Technol. 232 (2013) p.844.10.1016/j.surfcoat.2013.06.110
- F.J. da Silva , R.R. Marinho , M.T.P. Paes and S.D. Franco , Wear 304 (2013) p.183.10.1016/j.wear.2013.04.025
- L.N. Tang and M.F. Yan , J. Mater. Eng. Perform. 22 (2013) p.2121.10.1007/s11665-013-0488-0
- A. Nakonieczny and G. Monka , Mater. Sci. 48 (2013) p.715.10.1007/s11003-013-9559-5
- F. Kahraman , G.M. Gencer and S. Karadeniz , J. Fac. Eng. Archit. Gazi Univ. 28 (2013) p.7.
- L.F. Zagonel , J. Bettini , R.L.O. Basso , P. Paredez , H. Pinto , C.M. Lepienski and F. Alvarez , Surf. Coat. Technol. 207 (2012) p.72.10.1016/j.surfcoat.2012.05.081
- S.M.Y. Soleimani , A.R. Mashreghi , S.S. Ghasemi and M. Moshrefifar , Mater. Des. 35 (2012) p.87.10.1016/j.matdes.2011.09.067
- C. Nouveau , P. Steyer , K.R.M. Rao and D. Lagadrillere , Surf. Coat. Technol. 205 (2011) p.4514.10.1016/j.surfcoat.2011.03.087
- Z.-H. Jiang , X.-J. Tong , F. Sun , G.-S. Wang , and Z. Li , J. Aeronaut. Mater. 31 (2011) p.40.
- J.H. Kong , D.J. Lee , H.Y. On , S.J. Park , S.K. Kim , C.Y. Kang , J.H. Sung and H.W. Lee , Met. Mater. Int. 16 (2010) p.857.
- A. Akbari , R. Mohammadzadeh , C. Templier and J.P. Riviere , Surf. Coat. Technol. 204 (2010) p.4114.10.1016/j.surfcoat.2010.05.042
- M.A.J. Somers , R.M. Lankreijer and E.J. Mittemeijer , Philos. Mag. A 59 (1989) p.353.10.1080/01418618908205064
- J. Hartford , Phys. Rev. B 61 (2000) p.2221.10.1103/PhysRevB.61.2221
- M.H. Biglari , C.M. Brakman , M.A.J. Somers , W.G. Sloof and E.J. Mittemeijer , Z. Metallk. 84 (1993) p.124.
- E.J. Mittemeijer , Fundamentals of Materials Science , Ch. 9, Springer, Heidelberg, 2011.10.1007/978-3-642-10500-5
- H.H. Podgurski and F.N. Davis , Acta Metall. Mater. 29 (1981) p.1.10.1016/0001-6160(81)90081-X
- D.S. Rickerby , S. Henderson , A. Hendry and K.H. Jack , Acta Metall. Mater. 34 (1986) p.1687.10.1016/0001-6160(86)90116-1
- D.H. Kirkwood , O.E. Atasoy and S.R. Keown , Met. Sci. 8 (1974) p.49.10.1179/msc.1974.8.1.49
- S.S. Hosmani , R.E. Schacherl and E.J. Mittemeijer , Metall. Mater. Trans. A-Phys. Metall. Mater. Sci. 38A (2007) p.7.
- M.M. Yang and A.D. Krawitz , Metall. Trans. A 15 (1984) p.1545.10.1007/BF02657793
- J.D. Kamminga and G. Janssen , Surf. Coat. Technol. 200 (2005) p.909.10.1016/j.surfcoat.2005.01.066
- P.M. Hekker , H.C.F. Rozendaal and E.J. Mittemeijer , J. Mater. Sci. 20 (1985) p.718.10.1007/BF01026547
- P.C. van Wiggen , H.C.F. Rozendaal and E.J. Mittemeijer , J. Mater. Sci. 20 (1985) p.4561.10.1007/BF00559347
- R.E. Schacherl , P.C.J. Graat and E.J. Mittemeijer , Modelling the nitriding kinetics of iron-chromium alloys , in Thermec’2003, Pts 1–5 , T. Chandra , J.M. Torralba and T. Sakai , eds., Trans Tech Publications Ltd, Zurich-Uetikon , 2003, p.1047.
- S.S. Hosmani , R.E. Schacherl and E.J. Mittemeijer , Mater. Sci. Technol. 21 (2005) p.113.10.1179/174328405X16289
- R.M. Lankreijer , M.A.J. Somers and E.J. Mittemeijer , in Proceedings of the International Conference on High Nitrogen Steels , J. Foct and A. Hendry , eds., Lille, France, 18–20 May 1988, The Institute of Metals, London , 1989.
- E.J. Mittemeijer , M.H. Biglari , A.J. Bottger , N.M. van der Pers , W.G. Sloof and F.D. Tichelaar , Scr. Mater. 41 (1999) p.625.10.1016/S1359-6462(99)00143-8
- S.R. Meka , K.S. Jung , E. Bischoff and E.J. Mittemeijer , Philos. Mag. 92 (2012) p.1435.10.1080/14786435.2011.648226
- H.H. Podgurski and H.E. Knechtel , Trans. Metall. Soc. AIME 245 (1969) p.1595.
- M.H. Biglari , C.M. Brakman , E.J. Mittemeijer and S. van der Zwaag , Metall. Mater. Trans. A-Phys. Metall. Mater. Sci. 26 (1995) p.765.
- B. Schwarz , S.R. Meka , E. Bischoff , R.E. Schacherl and E.J. Mittemeijer , Acta Mater. 76 (2014) p.394.
- A. Leineweber , T. Gressmann and E.J. Mittemeijer , Surf. Coat. Technol. 206 (2012) p.2780.10.1016/j.surfcoat.2011.11.035
- E.J. Mittemeijer and J.T. Slycke , Surf. Eng. 12 (1996) p.152.10.1179/sur.1996.12.2.152
- E. Lehrer , Z. Elektrochem. 36 (1930) p.383.
- JCPDS, PDF-2 Database , Version 2.1. International Center for Diffraction Data. Version 2.1 , 2002.
- E.J. Mittemeijer , P. van Mourik and T.H. de Keijser , Philos. Mag. A 43 (1981) p.1157.10.1080/01418618108236149
- R. Delhez and E.J. Mittemeijer , J. Appl. Crystallogr. 8 (1975) p.609.10.1107/S0021889875011466
- J. Stein , R.E. Schacherl , M. Jung , S.R. Meka , B. Rheingans and E.J. Mittemeijer , Int. J. Mater. Res. 104 (2013) p.1053.
- M.H. Biglari , C.M. Brakman , E.J. Mittemeijer and S. van der Zwaag , Philos. Mag. A 72 (1995) p.931.10.1080/01418619508239945
- S.S. Hosmani , R.E. Schacherl and E.J. Mittemeijer , J. Mater. Sci. 43 (2008) p.2618.10.1007/s10853-008-2473-9
- S.S. Hosmani , R.E. Schacherl , L. Litynska-Dobrzynska and E.J. Mittemeijer , Philos. Mag. 88 (2008) p.2411.10.1080/14786430802345660
- J. Kunze and P.O.K. Friedrich , J. Mater. Sci. Lett. 5 (1986) p.815.10.1007/BF01730101
- T.C. Bor , A.T.W. Kempen , F.D. Tichelaar , E.J. Mittemeijer and E. Van der Giessen , Philos. Mag. A-Phys. Condens. Matter Struct. Defect Mech. Prop. 82 (2002) p.971.
- E.C. Bain , Trans. Am. Inst. Min. Met. Eng. 70 (1924) p.25.
- H.P. van Landeghem , M. Goune and A. Redjaimia , Steel Res. Int. 83 (2012) p.590.10.1002/srin.v83.6
- L.P.H. Jeurgens , Z.M. Wang and E.J. Mittemeijer , Int. J. Mater. Res. 100 (2009) p.1281.
- R. Benedictus , A. Böttger and E.J. Mittemeijer , Phys. Rev. B 54 (1996) p.9109.10.1103/PhysRevB.54.9109
- S.R. Meka , E. Bischoff , B. Rheingans and E.J. Mittemeijer , Philos. Mag. Lett. 93 (2013) p.238.10.1080/09500839.2012.762465
- W.D. Pearson , A Handbook of Lattice Spacing and Structures of Metals and Alloys , Vols. 1 and 2, Pergamon Press, New York , 1958.
- P. Ferguson and K.H. Jack , J. Met. 35 (1982) p.A73.
- N.E.V. Diaz , S.S. Hosmani , R.E. Schacherl and E.J. Mittemeijer , Acta Mater. 56 (2008) p.4137.10.1016/j.actamat.2008.04.041
- A.R. Clauss , E. Bischoff , S.S. Hosmani , R.E. Schacherl and E.J. Mittemeijer , Metall. Mater. Trans. A-Phys. Metall. Mater. Sci. 40A (2009) p.1923.
- A.R. Clauss , E. Bischoff , R.E. Schacherl and E.J. Mittemeijer , Philos. Mag. 89 (2009) p.565.10.1080/14786430802709105
- A.R. Clauss , E. Bischoff , R.E. Schacherl and E.J. Mittemeijer , Mater. Sci. Technol. 26 (2010) p.297.10.1179/174328409X422266
- K.S. Jung , R.E. Schacherl , E. Bischoff and E.J. Mittemeijer , Metall. Mater. Trans. A-Phys. Metall. Mater. Sci. 43A (2012) p.763.
- K.S. Jung , S.R. Meka , R.E. Schacherl , E. Bischoff and E.J. Mittemeijer , Metall. Mater. Trans. A-Phys. Metall. Mater. Sci. 43A (2012) p.934.
- V.K. Sarin , D. Mari , L. Llanes and C.E. Nebel , Comprehensive Hard Materials , Vols. 1–3, Elsevier Books, Philadelphia, 2014.
- M.H. Biglari , C.M. Brakman and E.J. Mittemeijer , Philos. Mag. A-Phys. Condens. Matter Struct. Defect Mech. Prop. 72 (1995) p.1281.