ABSTRACT
The current research investigates the combustion characteristics of bioslurry fuel derived from the products of agricultural waste pyrolysis. The bioslurry fuel was prepared by mixing biochar and pyrolysis oil. The combustion characteristics of a suspended single droplet of the bioslurry were analysed. The results indicate that an increase in pyrolysis temperature (400–600°C) lead to higher concentrations of fixed carbon (56–60%), increased ash content (16–18%), and higher calorific values (25–32 MJkg−1). As the pyrolysis temperature rises, the biochar surface becomes more porous, lower volatile matter content and particle size. As biochar content increases, the bioslurry’s density, viscosity, and caloric value increase but stability index decreases. Higher biochar content in the bioslurry increases the ignition delay and burnout time while reducing the burning rate. The bioslurry fuel contained 30% biochar achieved a calorific value of 28 MJkg−1 and a viscosity of 600 cP, comparative to conventional fossil fuels.
Up to 30% BC can be added to pyrolysis oil to produce SF.
Pyrolysis temperature increased FC, ash, and calorific value of biochar.
Biochar surface appears more porous with increasing pyrolysis temperature.
Biochar content affects bioslurry combustion characteristics.
Highlights
1. Introduction
The utilisation of fossil fuels is fraught with several challenges, including the depletion of reserves, escalating fuel prices, environmental degradation, and global warming. These issues underscore the unsustainability of our current energy systems and highlight the necessity for renewable, eco-friendly alternatives like biomass energy. Biomass sources are abundant, particularly in tropical regions. Indonesia, for instance, generates an estimated 146.7 million tons of biomass annually, translating to roughly 470 GJ/year (Rhofita et al. Citation2022). This biomass predominantly comes from agricultural residues such as rubber, sugar, palm oil, and plywood mill waste, as well as from coconut residues, rice husk, and corncob (Rhofita et al. Citation2022). These materials, often with high calorific values, are by-products of both biomass and industrial processes. However, directly combusting such wastes for heat and electricity generation can pose environmental hazards.
Pyrolysis is a prevalent method for biomass conversion, yielding three main products: pyrolysis oil, gas, and biochar (Liu et al. Citation2022; Citation2023; Vuppaladadiyam et al. Citation2022). Biochar is renowned for enhancing soil fertility and serving as an eco-friendly adsorbent for water purification, but it also boasts a high carbon content, considerable calorific value of approximately 30 MJkg−1 (Yang et al. Citation2017), and variable surface area (Saghir et al. Citation2022), making it a promising fuel alternative, particularly in the form of slurry fuel.
Slurry fuel, a suspension of finely ground solids in liquids such as water or oil, has been effectively used with coal for decades (Nunes Citation2020). Coal-based slurry fuel rivals petroleum in handling and operational costs, offering substantial savings in transportation, storage, and drying. Its combustion efficiency is increased, producing fewer emissions and reducing costs associated with combustion components (Kuznetsov et al. Citation2021).
Bioslurry fuels, derived from biomass pyrolysis and mixed with water to form a slurry-like consistency, offer a promising renewable energy solution with distinct properties and combustion characteristics. These fuels typically have a high calorific value and low moisture content, ensuring efficient combustion processes while reducing emissions of pollutants such as sulphur dioxide and particulate matter. Their viscosity and pumpability facilitate transportation and handling, while their flexibility in feedstock selection – from agricultural residues to organic waste – enhances sustainability and mitigates waste management challenges. As ongoing research focuses on optimisation and scaling, bioslurry fuels stand poised as an environmentally sound and economically viable alternative to conventional fossil fuels, promising a greener energy future.
Integrating biomass biochar into fossil fuel-based slurry can increase the energy per unit of fossil fuel compared to a solely fossil-based power system (Liu et al. Citation2017). The increased calorific value with added carbon makes biochar slurry fuel (BSF) an attractive option. The existing research on utilising biochar as slurry fuel in the literature mainly recorded the properties of the slurry fuel (Liu et al. Citation2017; Zepeda et al. Citation2023). The rheological behaviour and slurry fuel stability were investigated (Yan et al. Citation2023). Nonetheless, the use of biomass, especially agricultural waste, in BSF has yet to be extensively explored. The BSF can be easily modified to increase the properties (Nunes Citation2020).
The present research aimed to investigate the properties and combustion characteristics of BSF made of biochar and its respective pyrolysis oil from selected biomass. Incorporating pyrolysis oil for BSF will reduce the waste by utilising both products of biomass pyrolysis. The ignition and combustion of biochar mixed with water and other waste, such as glycerol, were explored (Nunes Citation2020). The absorption of pyrolysis oil as water replacement for slurry fuel production was investigated (Yan et al. Citation2023). However, the combustion characteristics of slurry fuel using pyrolysis oil as a solvent remain unexplored.
2. Experimental
The corncob and rice husks were obtained from a farmer at Landungsari village, Indonesia. The bagasse was obtained from Malang, Indonesia's sugar factory (PT Kebon Agung). The physical and chemical properties of the biomasses are as seen on .
Table 1. The physical and chemical characteristics of the selected biomass.
The pyrolysis equipment was a lab scale, an 80 cm vertical fixed-bed quartz reactor powered by a 3500 W furnace to create a heating area of up to 800°C. The biochar was prepared by pyrolysis of each rice husk, corncob, and bagasse as the raw material separately. Each material weighed 500 g was placed in the middle of the quartz reactor and pyrolysed under a certain temperature for 2 h in a nitrogen atmosphere. The rate of nitrogen (N2) used as a pyrolysis sweeping gas was 100 mLmin−1. The pyrolysis gas was cooled at 5°C through a condenser, and the pyrolysis oil was collected. The solid, after pyrolysis, was cooled to ambient temperature and then collected as biochar. The pyrolysis temperatures tested were 400°C, 500°C, and 600°C, respectively. The heating rates for the pyrolysis experiments were set at 10°C min−1 up to the desired temperatures of 400°C, 500°C, and 600°C, respectively. Each biochar sample was ground with a ball mill for 15 min and sieved at 300 mesh (biochar particle size is ≤ 50 µm), following the particle size requirements for slurry fuel materials, which is less than 88 µm (Hammerton, Li, and Ross Citation2020). The pyrolysis oil was collected for slurry fuel production.
The properties of the biochar are characterised. The proximate analysis was performed using a Shimadzu DTG60 Series thermogravimetric analyser, and the ultimate analysis was conducted using a Shimadzu AA7800 elemental analyser. The particle size was analysed using Shimadzu PSA SALD-7500nano. ASTM-D 4442 was used to measure the moisture content, ASTM-E 872 for volatile matter, ASTM-E 1755 for ash in biomass, and ASTM-E 711 for the gross calorific value with a Parr 6400 Bomb Calorimeter. The stability index is approached by allowing a mixture to sit for 3–7 days. A glass rod is inserted into the mixture at specific time intervals ranging from one to four hours. The rod weighs approximately 20 grams and has a length equivalent to the height of the container containing the mixture (Liu et al. Citation2017).
The slurry fuel was produced by adding each biochar to its respective pyrolysis oil. Biochar and the pyrolysis oil were homogenised using an IKA™ ULTRA-TURRAX™ T 18 Digital homogeniser at 11,000 rpm for 2 min. The higher the rotation speed, the quicker the contact between particles, resulting in the emulsion forming more quickly and becoming stable (Namira, Paramita, and Kusumayanti Citation2021). In this study, 1% of Tween 80 was added, acting as a surfactant to increase solubility and as a wetting agent in liquid preparations containing fine solids. The concentration of biochar was between 15 and 30% of the mixture. Above 30%, the slurry's viscosity was too thick to create a fuel droplet.
The slurry fuels were subjected to single droplet combustion tests utilising the experimental equipment illustrated in (Setyawan et al. Citation2015; Setyawan et al. Citation2017a; Citation2017b). The testing apparatus included a horizontal tube furnace (600 mm long and 40 mm in diameter) with temperature control to create a hot air environment, a droplet suspension system, a step motor to deliver the droplet into the furnace, and a charge-coupled device (CCD) camera to assess combustion characteristics. A slurry droplet was ignited and burned in the tube furnace after it had reached the desired temperature. The air rate used in the slurry combustion was 150 mLmin−1 to ensure sufficient air for complete combustion of the slurry fuel. A quartz rod was used to suspend the droplet from the tip of a silicon carbide fibre with 0.142 mm in diameter.
Figure 1. A schematic diagram and photo of the apparatus for experimentation of single droplet combustion.
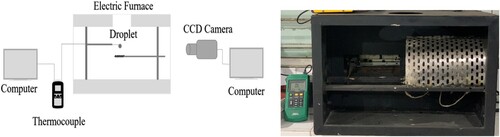
A stated droplet size in the current experiment referred to a sphere-equivalent value calculated as the cubic root of the product of the droplet width squared and the droplet length. The actual shape of the suspended droplet in the experiment was elliptical. The entire process, from when the droplet entered the furnace until it burned out, was photographed using a high-speed CCD camera (Basler PIA-210gc) with an exposure time of 200 ms. A 50W halogen lamp was used to backlight the burning droplet, and the CCD camera captured it to measure the changing droplet size during combustion – a computer-controlled the CCD camera and step motor. In the current study, the furnace temperatures were set at 650°C, and the initial droplet diameter ranged from 0.5 to 1.0 mm. The CCD camera's optical images were used to calculate the burning droplet's ignition delay period and flame duration. The ignition was said to have occurred when the first discernible flame appeared. The interval between the droplet's entry into the furnace and when ignition occurred is known as the ignition delay time. As soon as the spark ignited, a flame engulfed the droplet. The flame duration was determined as the total time the flame was visible. The morphology of some of the slurry particle samples was examined. With the help of the step motor, the formed slurry particles were quickly removed from the furnace's centre at the time of flame extinguishment.
3. Results and discussion
3.1. Characteristics of agricultural waste
shows the characteristics of the bagasse, corncob and rice husk. Overall, cellulose is a dominant feature in biomass, except for corncob. Plants comprise about 25% lignin and 75% sugars or carbohydrates (Li et al. Citation2022). The sugar molecules that make up the carbohydrate fraction are linked together in long chains or polymers. The distinction is between the two categories of cellulose and hemicellulose. The non-sugar-type molecules that make up the lignin fraction are a glue to hold the cellulose fibres together.
The other feature that might affect biomass as an energy source is the moisture content, which accounted for 8–12% of all materials. Ash content is also significantly higher in rice husk than in the other biomass. The ultimate analysis of the selected biomass shows that the properties are relatively similar, apart from rice husk, which contains the lowest carbon content. The calorific value reflects the composition of the biomass. The calorific value of bagasse was the lowest due to the high moisture in the material (Komilis, Kissas, and Symeonidis Citation2014).
3.2. Characteristics of biochar samples derived from agricultural waste
shows the effect of pyrolysis temperature on the physical and chemical properties of the biochar produced from the selected agroindustry wastes. Overall, the particle size of the biochar was between 20 and 60 µm, and the particle size decreased with increasing pyrolysis temperature. The internal porosity of biochar is influenced by feedstock type, pyrolysis temperature, and pyrolysis residence time (Setyawan et al. Citation2023). More porous biochar is produced when pyrolysis temperatures are higher (Setyawan et al. Citation2023). Therefore, increasing temperature promotes smaller particle sizes due to the collapse of the biochar structure.
Table 2. The characteristics of the selected biochar.
Overall, there was no significant difference in the water content for all feedstocks. However, with increasing temperature, the biochar's water content varied. This is because the smaller particle size produced during high pyrolysis temperature increases the capability of the biochar to absorb moisture from the air (Werdin et al. Citation2021).
The fixed carbon concentration increased with increasing pyrolysis temperature. Corncob, as indicated in the raw material composition in , has the highest carbon content, followed by bagasse and rice husk. It is noted that before the pyrolysis, the carbon content was under 20%, but it dramatically increased after pyrolysis. As the pyrolysis temperature increases, many volatile substances and materials with low boiling points are released. When the temperature reached 500°C and above, volatile substances with higher boiling points started breaking down gradually, leaving more carbon in the biochar. Corncob and bagasse had higher lignin contents than rice husk, which was the cause of the difference in fixed C content between the biochar. In air-limited pyrolysis, lignin with a more condensed aromatic structure had weaker reactive activity than hemicellulose, particularly at low temperatures (Chen et al. Citation2019).
The increasing temperatures also increased the ash content. The ash content of all the feedstock was 12–22%, much higher than that of the raw material, excluding the rice husk. The ash contents in biochar produced in CO2 and N2 were significantly lower than those produced in air-limited at each pyrolysis temperature (Yousef et al. Citation2021). As mentioned in , the ash content of rice husk raw material is over 20%. After the pyrolysis, the ash content in the rice husk remained the highest among the selected biomass waste. The raw materials of bagasse and corncob have similar ash content (3–5%). After pyrolysis, the ash content was increased to approximately 12–16%, showing that even if the ash was not participating during combustion, it was a significant part of the biochar proportion. The higher the ratio of ash in biochar, the lower the carbon content and calorific value (Tabakaev et al. Citation2020).
Regardless of the types of feedstocks, the volatile matter content slightly decreased with increasing temperature for each pyrolysis temperature. A combination of aromatisation reactions and removing aliphatic and alicyclic groups account for decreased volatile matter at higher temperatures. Aliphatic structures can be destroyed during heating through reactions known as cracking, which are promoted by branched structures (Jiménez et al. Citation1999). An increase in aromatisation is also brought on by hydroaromatic structure dehydrogenating or by forming an alkyl group ring and subsequent dehydrogenation (Jiménez et al. Citation1999).
The calorific value of the biochar was between 20 and 30 MJkg−1, showing the potential of the biochar for fuel. Overall, the calorific value increased with increasing pyrolysis temperature. The corncob and bagasse biochar had slightly higher calorific values due to the biochar’s low water and ash content. The increasing carbon content consequently increases calorific value. The number of carbon atoms in the biochar will affect its calorific value; the more carbon atoms there are, the more calorific value is produced because carbon is the fuel (Jiang et al. Citation2018). The compound that produces the most carbon atoms is lignin, while hemicellulose produces the least amount, according to the number of atoms owned by cellulose, hemicellulose, and lignin. Because lignin can decompose at temperatures between 300°C and 500°C, the higher the pyrolysis temperature, the more completely lignin will decompose.
In most cases, a lower calorific value (LHV) is affected by the heat of the water formed from the hydrogen in the material and the moisture evaporating. The fuel's chemical characteristics affect how the calorific values differ. The moisture content, which affects the fuel's energy content, is the most crucial aspect of biomass feedstocks concerning combustion and other thermo-chemical processes.
shows the SEM images of effect of pyrolysis temperature on biochar at 400–600°C. The biochar surface appears more porous overall as the pyrolysis temperature rises. The pore structure was present at 400°C but diminished as the temperature increased. The pore of biochar collapses at 600°C. When biochar is heated at a high temperature, the pores will open, and their diameter will increase, releasing complex compounds, particularly those trapped inside the pores (Yang, Liu, and Lu Citation2021).
The properties of pyrolysis oil depend on the pyrolysis temperature and material. shows that the typical colour of pyrolysis temperature is a yellowish liquid, containing water as its main component. The water content of the pyrolysis oil for bagasse is 95–96%, rice husk 95–98% and corncob 92–95%. Addition of 5–8% pyrolysis oil can enhance the properties of the slurry fuel.
3.3. The effect of pyrolysis temperature on water content of biochar samples
Production of slurry fuel mimics the convenience of liquid fuel by utilising the pyrolysis product, both pyrolysis oil and biochar. The present research mixed the pyrolysis oil and the biochar, producing the biochar slurry fuel. In this research, the highest biochar loading was 30%. Above 30%, the slurry fuel density was too high compared to the standard. shows the effect of biochar loading on the viscosity and density of slurry fuel. Biochar, as a solid substance, can increase the viscosity of the slurry fuel. Greater amounts of dissolved substance (biochar) per unit volume indicate higher solution concentration. Friction between particles will be greater if there are more dissolved substances. This is what causes an increase in viscosity if the amount of solid substance is larger (Romanov et al. Citation2024). The density of the slurry fuel generally increases with higher percentages of biochar loading across all biomass types. However, the degree of increase and the pattern of density change are unique to each biomass. Bagasse demonstrates a consistent moderate rise in density with increasing biochar content, whereas corncob exhibits a more inconsistent pattern, with some data points at higher biochar percentages showing notably greater densities. In contrast, rice husk displays a more subtle increase and greater scatter in the data, indicating a less consistent effect of biochar loading on density.
shows that increasing biochar loading increases the caloric value of the slurry fuel. The caloric value of the slurry fuels tends to increase with an increase in the percentage of biochar loading (Mitianiec Citation2023). Bagasse’s slurry fuel shows a noticeable increment in caloric value at higher biochar loadings. Corncob’s slurry fuel also demonstrates a rise in caloric value, but rice husk’s slurry fuel seems to exhibit a lower increase in caloric value with biochar loading compared to the other two biomasses. The caloric value of the slurry fuel varies depending on the biochar feedstock and pyrolysis oil. The caloric value of biochar pyrolyzed at 500°C, such as bagasse, is 30.2 MJkg−1, corncob is 32.1 MJkg−1, and rice husk is 18.3 MJkg−1. However, compared to the biochar, the caloric value of the pyrolysis oil is very low. The caloric value of the pyrolysis oil of bagasse is 0.015 MJkg−1, corncob is 0.018 MJkg−1, and rice husk is 0.009 MJ-kg−1. The caloric value of the pyrolysis oil is low due to the high-water content, which is over 95% for the three biomasses.
shows the stability index of the slurry fuel over time as a measure of how well the slurry maintains its uniformity without phase separation. The stability index of biochar-slurry fuel from all biomasses appears to decrease both with increasing biochar loading and with longer time lapses (Bergvall et al. Citation2024). The higher percentages of biochar loading are associated with a lower stability index. Adding high biochar loading to slurry fuel may not benefit the fuel's stability over extended periods. The decreasing trend in stability with increasing biochar content suggests that while biochar may contribute positively to specific fuel characteristics, such as caloric value or initial viscosity, it may adversely affect the long-term homogeneity of the mixture. This could be due to various factors, such as the physical characteristics of the biochar particles, their interaction with the liquid phase of the slurry, or the chemical composition altering the slurry's ability to remain in a stable emulsion. Furthermore, the time-dependent decrease in stability, shown by the lower stability indices at 48 and 72 h, could indicate the dynamics within the slurry mixture. Over time, heavier components, potentially the larger biochar particles, might settle. With the progression of time, the stability index was observed to diminish. After 24 h, the index was relatively higher across all levels of biochar loading, but as time extends to 48 and 72 h, the index drops, implying a decline in stability. This suggests that the fuel's resistance to separation or degradation lessens over time, which could be a concern for the long-term storage or consistency of the fuel quality.
The creation of biochar slurry fuel, an innovative approach to emulate liquid fuels, brings forth challenges in optimising biochar loading for desirable fuel properties like viscosity, density, and calorific value. A key finding is that higher biochar content enhances viscosity and calorific value but compromises the stability of the slurry, indicating a need for a careful balance of these properties. Furthermore, the stability and combustion characteristics of biochar slurry fuel are crucial for its practical application.
3.4. Combustion characteristics of single droplets of the slurry fuels
shows the typical droplet burning of the slurry fuel. The image sequence illustrates the stages of droplet combustion over time, highlighting key phases of the process. Initially, at 0 s, the droplet is stable, possibly pre-heating. By 3 s, ignition begins, evidenced by the onset of visible flames or a glow around the droplet, indicating that the temperature has reached the ignition point. At 10 s, combustion is more pronounced as the droplet decreases in size due to active evaporation and reaction with the surrounding oxidiser, producing heat and light. By 15 s, the combustion process is fully developed, with the droplet continuing to shrink as fuel is consumed. At 25 s, the droplet is significantly smaller, and the flame intensity may vary as combustion nears completion. Finally, at 45 s, the droplet is almost entirely burned out, with the flame likely subsiding, indicating that most of the fuel has been consumed.
Figure 7. Typical of droplet burning of the slurry fuel from various biochar sources at 15% addition.
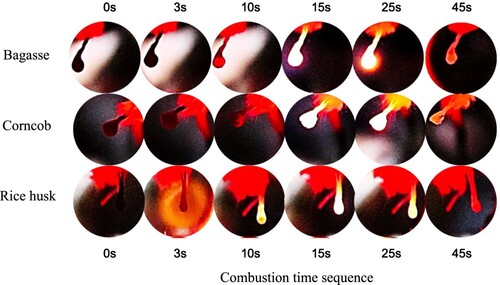
captures the dynamic changes in the normalised droplet diameter squared ((d/d0)²) for slurry fuel droplets containing varying amounts of biochar and biochar concentrations post-ignition. The trend shows a linear decrease in droplet size over time, aligning with the d²-law of combustion (Law Citation2006). Notably, the droplet sizes exhibited occasional variations due to the disparate boiling points of biochar and pyrolysis oil, which cause pyrolysis oil molecules within the droplet to expand and alter the droplet's size and shape. At the combustion's end, the remaining solid residue is comparably large. This possibly due to the remaining minerals in the ash that did not participate in the combustion but exist in high proportion within the biochar.
Figure 8. Temporal variations of the square of the normalised droplet diameters of slurry fuels added with different biochar concentrations.
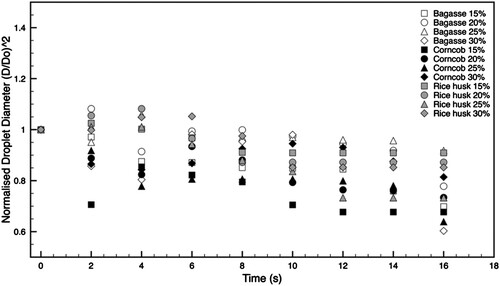
details how biochar integration affects the ignition delay in slurry fuel droplets, revealing a direct correlation between increased biochar content and longer ignition delays. These delays are a product of processes like droplet heating, evaporation, molecular diffusion, and the chemical reactions between fuel and oxygen in the gas phase (Law Citation2006). Pyrolysis oil, which has a lower boiling point than biochar, evaporates first, leading to an expedited ignition delay. Notably, the shortest delay is observed in slurry fuel with bagasse biochar, with rice husk and corncob following suit.
Figure 9. Effect of the biochar addition on (a) ignition delay time; (b) burnout time; and (c) burning rate of slurry fuels.
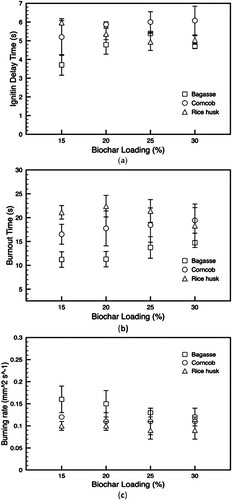
In the same figure, the burnout times for droplets doped with biochar are presented, showing an extension with higher biochar ratios. This elongation results from decreased burning rates in the slurry fuel droplets. The burning rates for different biochar and concentrations are also mapped, indicating that biochar addition generally slows down the burning process. This is consistent with biochar's inherently lower burning rate compared to pyrolysis oil. Droplet combustion theory suggests that a fuel's burning rate is inversely proportional to its evaporation latent heat, boiling point, and density (Law Citation2006). Consequently, the integration of biochar into pyrolysis oil, which raises the boiling point, heat of evaporation, and density, results in a decreased burning rate as the biochar concentration increases.
Additionally, the combustion characteristics, such as ignition delay and burnout times, are influenced by biochar content, suggesting less efficient combustion with higher concentrations. The use of agricultural waste in this manner offers an environmentally friendly approach to waste management and energy generation, but it necessitates a thorough evaluation of the environmental impacts, fuel efficiency, and economic viability of the process.
Future studies aimed to optimise pyrolysis conditions, enhance biochar slurry fuel's stability and combustion efficiency, and explore this technology's broader environmental and economic implications. The potential uses of biochar, beyond energy production, in areas like soil amendment or carbon sequestration, also merit further exploration. Transforming agricultural waste into biochar and biochar slurry fuel is a promising avenue for bioenergy, yet it is beset with challenges related to biomass variability, pyrolysis optimisation, and fuel property balancing. Addressing these issues is crucial for this technology's practical and sustainable deployment.
4. Conclusions
The present study examined the characteristics and combustion behaviour of slurry fuels made from biochar derived from rice husk, bagasse, and corncob. The investigation focused on the properties of biochar produced at various pyrolysis temperatures and the subsequent blending with pyrolysis oil to form bioslurry fuels. The findings revealed that increasing the pyrolysis temperature significantly altered the biochar’s properties across all feedstocks. Higher pyrolysis temperatures resulted in higher fixed carbon content, increased ash content, and greater calorific values. For instance, bagasse biochar pyrolysed at 400°C compared to 600°C exhibited a fixed carbon content increase from 56 to 60%, an ash content rise from 16 to 18%, and a calorific value 25–32 MJkg−1. Additionally, the biochar surface became more porous with increasing temperature, although the volatile matter content and particle size decreased. Pyrolysis oil properties were influenced by the feedstock and pyrolysis conditions, with water content remaining high across all samples.
Higher biochar content increased the density, viscosity and caloric value of the bioslurry but reduce the stability index. The optimal bioslurry fuel composition was found with 30% biochar, achieving a calorific value of 28 MJkg−1 and a viscosity of 600 cP. Combustion characteristics indicated that increasing content of biochar in the bioslurry increased the ignition delay and burnout time while reducing the burning rate, due to the higher boiling point and heat of evaporation of biochar compared to pyrolysis oil.
This study’s novel contributions include demonstrating the impact of varying pyrolysis temperatures and biochar concentrations on both the physical properties and combustion behaviour of bioslurry fuels. It highlighted the trade-offs between increasing biochar content for higher calorific value and the resultant decrease in slurry stability and combustion efficiency. For future work, optimising pyrolysis conditions to maximise fixed carbon content and calorific value while minimising undesirable traits such as excessive ash content and high moisture retention in pyrolysis oil is recommended. Investigating additives or processing techniques that can enhance the long-term stability of bioslurry fuels without compromising their combustion efficiency is also needed. By addressing these areas, future research can help overcome the challenges related to biomass variability, pyrolysis optimisation, and fuel property balancing, making the production and use of biochar-based slurry fuels a viable and sustainable alternative to conventional fossil fuels.
Data availability statement
The data that support the findings of this study are available in cloud at https://s.ub.ac.id/bioslurrydata. These data were derived from the following resources available in the public domain: [https://s.ub.ac.id/bioslurrydata].
Disclosure statement
No potential conflict of interest was reported by the author(s).
Additional information
Funding
References
- Bergvall, N., Y.W. Cheah, C. Bernlind, A. Bernlind, L. Olsson, D. Creaser, L. Sandström, and O.G.W. Öhrman. 2024. “Upgrading of Fast Pyrolysis Bio-oils to Renewable Hydrocarbons Using Slurry- and Fixed Bed Hydroprocessing.” Fuel Processing Technology 253:108009. https://doi.org/10.1016/j.fuproc.2023.108009.
- Chen, W.-H., C.-W. Wang, H.C. Ong, P.L. Show, and T.-H. Hsieh. 2019. “Torrefaction, Pyrolysis and Two-stage Thermodegradation of Hemicellulose, Cellulose and Lignin.” Fuel 258:116168. https://doi.org/10.1016/j.fuel.2019.116168.
- Hammerton, J.M., H. Li, and A.B. Ross. 2020. “Char-diesel Slurry Fuels for Microgeneration: Emission Characteristics and Engine Performance.” Energy 207:118225. https://doi.org/10.1016/j.energy.2020.118225.
- Jiang, K.-M., C.-G. Cheng, M. Ran, Y.-G. Lu, and Q.-L. Wu. 2018. “Preparation of a Biochar with a High Calorific Value from Chestnut Shells.” New Carbon Materials 33 (2): 183–187. https://doi.org/10.1016/S1872-5805(18)60333-6.
- Jiménez, A., M.J. Iglesias, F. Laggoun-Defarge, and I. Suárez-Ruiz. 1999. “Effect of the Increase in Temperature on the Evolution of the Physical and Chemical Structure of Vitrinite.” Journal of Analytical and Applied Pyrolysis 50 (2): 117–148. https://doi.org/10.1016/S0165-2370(99)00027-3.
- Komilis, D., K. Kissas, and A. Symeonidis. 2014. “Effect of Organic Matter and Moisture on the Calorific Value of Solid Wastes: An Update of the Tanner Diagram.” Waste Management 34 (2): 249–255. https://doi.org/10.1016/j.wasman.2013.09.023.
- Kuznetsov, G.V., D.S. Romanov, K.Y. Vershinina, and P.A. Strizhak. 2021. “Rheological Characteristics and Stability of Fuel Slurries Based on Coal Processing Waste, Biomass and Used Oil.” Fuel 302:121203. https://doi.org/10.1016/j.fuel.2021.121203.
- Law, C.K. 2006. Combustion Physics, Vol. 1. New York, USA: Cambridge University Press, 214–217.
- Li, H., X. Li, D. Li, J. Zhang, H. Nawaz, T. You, and F. Xu. 2022. “Highly-efficient Pretreatment Using Alkaline Enhanced Aqueous Deep Eutectic Solvent to Unlock Poplar for High Yield of Fermentable Sugars: Synergistic Removal of Lignin and Mannan.” Bioresource Technology 351:126993. https://doi.org/10.1016/j.biortech.2022.126993.
- Liu, J., X. Chen, W. Chen, M. Xia, Y. Chen, H. Chen, K. Zeng, and H. Yang. 2023. “Biomass Pyrolysis Mechanism for Carbon-Based High-value Products.” Proceedings of the Combustion Institute 39 (3): 3157–3181. https://doi.org/10.1016/j.proci.2022.09.063.
- Liu, P., M. Zhu, Z. Zhang, Y.-K. Leong, Y. Zhang, and D. Zhang. 2017. “Rheological Behaviour and Stability Characteristics of Biochar-water Slurry Fuels: Effect of Biochar Particle Size and Size Distribution.” Fuel Processing Technology 156:27–32. https://doi.org/10.1016/j.fuproc.2016.09.030.
- Liu, P., H. Zhuang, Y. Qian, J. Yang, Y. Pan, Z. Zhou, L. Jia, and F. Qi. 2022. “Recent Advances in Mass Spectrometric Studies on the Reaction Process of Biomass Pyrolysis.” Fuel Processing Technology 237:107473. https://doi.org/10.1016/j.fuproc.2022.107473.
- Mitianiec, W. 2023. “Study of Increasing Thermodynamic Efficiency and Hydrogen Amount in the Process of Solid Fuels and Biomass Gasification.” International Journal of Hydrogen Energy 48 (31): 11709–11726. https://doi.org/10.1016/j.ijhydene.2022.03.191.
- Namira, Z.R., V. Paramita, and H. Kusumayanti. 2021. “The Effect of Rotational Speed of Homogenization on Emulsion Results Obtained Using soy Lecithin Emulsifier.” Journal of Vocational Studies on Applied Research 3 (1): 14–17. https://doi.org/10.14710/jvsar.v3i1.10916.
- Nunes, L.J.R. 2020. “Potential of Coal–Water Slurries as an Alternative Fuel Source During the Transition Period for the Decarbonization of Energy Production: A Review.” Applied Sciences 10:2470. https://doi.org/10.3390/app10072470.
- Rhofita, E.I., R. Rachmat, M. Meyer, and L. Montastruc. 2022. “Mapping Analysis of Biomass Residue Valorization as the Future Green Energy Generation in Indonesia.” Journal of Cleaner Production 354:131667. https://doi.org/10.1016/j.jclepro.2022.131667.
- Romanov, D.S., V.V. Dorokhov, K.Y. Vershinina, and P.A. Strizhak. 2024. “Stabilized Fuel Slurries Based on Fine Coal Slime: Rheology, Combustion and Feasibility Study.” Fuel 356:129560. https://doi.org/10.1016/j.fuel.2023.129560.
- Saghir, S., C. Pu, E. Fu, Y. Wang, and Z. Xiao. 2022. “Synthesis of High Surface Area Porous Biochar Obtained from Pistachio Shells for the Efficient Adsorption of Organic Dyes from Polluted Water.” Surfaces and Interfaces 34:102357. https://doi.org/10.1016/j.surfin.2022.102357.
- Setyawan, H.Y., L. Safira, A.R. Mulyarto, S. Wijana, and D. Pranowo. 2023. “The Effect of Pyrolysis Temperature and Ball-milling Duration on Characteristics of Micro Bio-char Derived from Oil Palm Empty Fruit Bunches.” Sustainable Environment 9 (1), https://doi.org/10.1080/27658511.2023.2173041.
- Setyawan, H.Y., M. Zhu, Z. Zhang, and D. Zhang. 2015. “An Experimental Study of Effect of Water on Ignition and Combustion Characteristics of Single Droplets of Glycerol.” Energy Procedia 75:578–583. https://doi.org/10.1016/j.egypro.2015.07.459.
- Setyawan, H.Y., M. Zhu, Z. Zhang, and D. Zhang. 2017a. “An Experimental Investigation into the Effect of Soap on Ignition and Combustion Characteristics of Single Droplets of Glycerol.” Combustion Science and Technology 189 (9): 1540–1550. https://doi.org/10.1080/00102202.2017.1308356.
- Setyawan, H.Y., M. Zhu, Z. Zhang, and D. Zhang. 2017b. “An Experimental Study of the Effect of Biodiesel on the Ignition and Combustion Characteristics of Single Droplets of Glycerol.” In 11th Asia-Pacific Conference on Combustion, edited by M. Dunn, E.R.H., A.R. Masri, M. Cleary, A. Kourmatzis, Q.N. Chan, and S. Kook. Sydney, Australia: Combustion Institute.
- Tabakaev, R., K. Ibraeva, V. Kan, Y. Dubinin, M. Rudmin, N. Yazykov, and A. Zavorin. 2020. “The Effect of Co-combustion of Waste from Flour Milling and Highly Mineralized Peat on Sintering of the ash Residue.” Energy 196:117157. https://doi.org/10.1016/j.energy.2020.117157.
- Vuppaladadiyam, A.K., S.S.V. Vuppaladadiyam, A. Awasthi, A. Sahoo, S. Rehman, K.K. Pant, S. Murugavelh, et al. 2022. “Biomass Pyrolysis: A Review on Recent Advancements and Green Hydrogen Production.” Bioresource Technology 364:128087. https://doi.org/10.1016/j.biortech.2022.128087.
- Werdin, J., R. Conn, T.D. Fletcher, J.P. Rayner, N.S.G. Williams, and C. Farrell. 2021. “Biochar Particle Size and Amendment Rate are More Important for Water Retention and Weight of Green Roof Substrates Than Differences in Feedstock Type.” Ecological Engineering 171:106391. https://doi.org/10.1016/j.ecoleng.2021.106391.
- Yan, S., H. Chen, H. Zhu, Z. Lin, G. Wu, W. Gao, H. Zhang, et al. 2023. “Enhanced Adsorption of Bio-oil on Activated Biochar in Slurry Fuels and the Adsorption Selectivity.” Fuel 338:127224. https://doi.org/10.1016/j.fuel.2022.127224.
- Yang, C., J. Liu, and S. Lu. 2021. “Pyrolysis Temperature Affects Pore Characteristics of Rice Straw and Canola Stalk Biochars and Biochar-Amended Soils.” Geoderma 397:115097. https://doi.org/10.1016/j.geoderma.2021.115097.
- Yang, X., H. Wang, P.J. Strong, S. Xu, S. Liu, K. Lu, K. Sheng, et al. 2017. “Thermal Properties of Biochars Derived from Waste Biomass Generated by Agricultural and Forestry Sectors.” Energies 10:469. https://doi.org/10.3390/en10040469.
- Yousef, S., J. Eimontas, N. Striūgas, and M.A. Abdelnaby. 2021. “Pyrolysis and Gasification Kinetic Behavior of Mango Seed Shells Using TG-FTIR-GC–MS System Under N2 and CO2 Atmospheres.” Renewable Energy 173:733–749. https://doi.org/10.1016/j.renene.2021.04.034.
- Zepeda, L.C., G. Griffin, K. Shah, S. Bhargava, and R. Parthasarathy. 2023. “A Study of Biochar Physiochemistry and Particle Size Distribution Influencing the Properties of Water-Based Slurry Fuels.” Environmental Research 236:116578. https://doi.org/10.1016/j.envres.2023.116578.