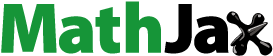
ABSTRACT
Although being rather similar in appearance, forwarders have gone through substantial development during the more than half a century they have been used in forestry. The aim was to describe the development in Sweden, by a combination of historical narratives and data. The latter consists of technical parameters of forwarders sold on the Swedish market from 1962 to 2012, together with sales figures from 1975 to 2017. Data were collected from the original specifications from manufacturers; advertisements in old forestry magazines; Internet forums; and from the literature. In total, 51 forwarder manufacturing companies were identified, all located in Sweden or Finland, which produced over that time 361 models in total. The weight and load capacity has increased over time, as well as engine power and torque per tonne total weight. Load index has decreased over time. Ground pressure decreased from 1962 to 1985, but then remained stable. In Sweden, 12,602 forwarders were sold from 1975 to 2012. The trend for annual sales decreased until 1993 but since 2005 has increased to between 300 and 400 forwarders per year. Since 1995 annual sales in Sweden have been between four and six forwarders per million m3 harvested industrial wood. Corresponding values for the years 1975–1984 were double that. Why the first Swedish forwarder was developed from a farm tractor rather than importing an already existing, purpose-built forwarder from Canada is discussed, as well as the probable direction of future developments in forwarder design and construction. New forwarder size-classes are suggested. Soil damage issues are predicted to be of increased importance.
Introduction
It has been estimated that the global annual harvest of roundwood is about 1.32 billion m3 (UN Citation2015), and that 35% of this volume was harvested with the fully mechanized Cut-To-Length (CTL) technique, 37% with the fully mechanized full tree or tree length technique and that the remaining 29% was harvested with less sophisticated or not ground-based equipment. The corresponding value for Sweden is close to 100% CTL technique (Lundbäck et al. Citation2018).
Most mechanized CTL harvesting is currently performed by a harvester and a forwarder. The harvester that fells and processes trees into logs is usually a purpose-built machine, but a harvester-head mounted onto, e.g. an excavator is also common practice, for instance in plantation forestry (Drushka and Konttinen Citation1997). However, the forwarder that carries and transports logs to the roadside is almost exclusively a purpose-built machine.
At present in Sweden, forwarders are used to extract almost all industrial wood (sawlogs and pulpwood). One important driving force for the development of forwarders has been the steadily increasing volume of harvested industrial wood. The total annual harvested volume in Sweden between 1942 and 2017 has been in the range of 34–75 million m3 of merchantable stem volume without bark (m3sub), with 2005 being an exceptional year with 98 million m3 sub due to the large volume of wind-felled trees during the storm “Gudrun” (Anon Citation2014, Citation2017). The proportion of this volume that comprised industrial wood ranged from 41 to 70% during the 1940s, and from 68 to 83% during the 1950s. Between 1980 and 2017 the proportion of industrial wood stabilized with an average of 91% (Anon Citation2014, Citation2017). The overall pattern of the industrial wood harvest was characterized by a rapid increase in production from 1942 to 1970, then a rapid decrease from 1974 to 1978, followed by a slow but stable increase, except for the peak caused by the storm in 2005, up to a level that since 2002 has been, on average, higher than the earlier peak years of 1970–1974 ().
Figure 1. Harvested industrial wood volume (m3 merchantable stem volume without bark) of sawlogs and pulpwood in Sweden between 1942 and 2017 (after Anon Citation2014, Citation2017).
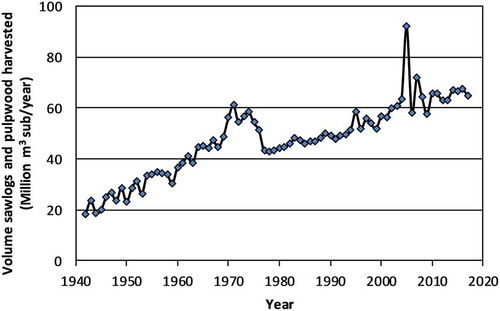
At present, the forwarders used in Sweden are almost exclusively produced in either Sweden or Finland. The forest machine manufacturing companies began the production and sale of a few units locally, gradually growing into bigger concerns, or, more often, being sold to or merged with other forest machine manufacturers (Östberg Citation1990; Drushka and Konttinen Citation1997; Adelhult Citation2014). In 2014, among the seven brands on the market (Johnsen Citation2015), 65% of forwarders sold in Sweden were manufactured by Komatsu (Sweden) or John Deere (Finland); 25% by Ponsse (Finland) or Rottne (Sweden); most of the remaining 10% being manufactured in Sweden by Ecolog, Gremo, and Tiger Cat.
The term “Forwarder” was first used with its meaning of a load carrying machine with articulated steering for extraction of logs by McColl (Citation1958) at the Pulp and Paper Research Institute of Canada. An almost identical definition was given in Sweden by Sundberg (Citation1967) who defined it as a single axle tractor connected to a load carrying unit as a rear chassis part. In reality this also means that it has articulated frame steering, and that the front and rear chassis parts are held rigidly in the vertical plane. The importance of this is that there is no need for each of the chassis parts to be longitudinally stable, and a single axle, with or without bogie, can be used under each chassis part. However, 2 years later the term was redefined for inclusion in the first specific Swedish glossary of forest terms by a refereeing process among Swedish stakeholders. The new definition mentioned nothing about “single axle tractor,” meaning that a machine that was capable of vertical movements between its front and rear chassis parts could also be classified as a forwarder (Selander Citation1969). However, all forwarders introduced on the Swedish market after about 1970 were designed and constructed following the original Swedish definition of Sundberg (Citation1967) (cf. Östberg Citation1990). Other criteria have since been included in the definition of forwarders as used in present day operational forestry.
In the present study, the term forwarder is only used with respect to an off-road log transportation vehicle that has articulated frame steering and is rigid in the vertical plane between front and rear chassis parts; is all-wheel driven; and has a grapple loader. The term “forest tractor” is used for a vehicle that fulfills most of the above criteria, except the front and rear chassis parts being rigid in the vertical plane (cf. ). In the past “forest tractor,” and other similar terms, have also sometimes been used to distinguish this type of machine from forwarders (Nilsson and Svensson Citation1971).
Figure 2. (Above). A schematic forest tractor with a vertical movement between the front and rear parts of the machine when passing obstacles. (Below). A silhouette of the first Swedish forwarder (Brunett 350 Boxer), rigid in the vertical plane between front and rear chassis parts (after Staaf Citation1983).
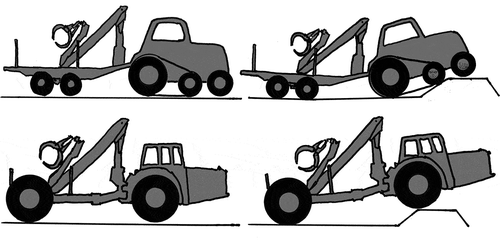
An old, but commonly-used size classification of forwarders is that the maximum load of small forwarders is less than 10 tonnes (t), for mid-sized forwarders it is between 10 t and 12 t, and that large forwarders have a maximum load of more than 12 t (Athanassiadis et al. Citation1999).
Forwarders in Sweden have, over time, become more reliable, more productive, and have been designed and constructed to higher levels of technical performance (Nordfjell et al. Citation2010). Between 1985 and 1989 most forwarders had hydrodynamic-mechanical transmissions (converters), six wheels, and hydraulics with a maximum pressure of 15–19 MPa. By 2010, the hydrostatic-mechanical transmission totally dominated the field, with the eight-wheeled machine (with a bogie on both chassis parts) being the most common, and the hydraulics having a maximum pressure of 22 MPa, 24 MPa, or in some cases even 26 MPa. The boom lifting torque in relation to the weight of the forwarder increased over the same period. The mechanical availability of forwarders increased on average by between 80 and 88% from 1985 to 2008, and the productivity in logging (harvesting and forwarding) increased more than two-fold at the forest company SCA over the same period (Nordfjell et al. Citation2010). The change in prices of forest machines over time was highly correlated with changes in the market for forestry products, i.e. Swedish market prices for industrial round-wood (Nordfjell et al. Citation2010).
Many forwarder models have been developed and used in Sweden since the mechanization of harvesting began. Forwarders in Sweden have an important forerunner in their Canadian counterpart (Silversides Citation1988). However, the history of the development of forwarders in Sweden and the progressive advances in their technical parameters has only been fragmentarily described, and mostly in the Swedish language. The aim of the present study was therefore threefold: (1) to summarize the history of the development of Swedish forwarders and their Canadian forerunners, (2) to describe and analyze the development over time of the main technical parameters of forwarders sold on the Swedish market from 1962 to 2012, and (3) to describe the pattern of sales of new forwarders in Sweden from 1975 to 2017, and to set this in relation to the harvested volume of industrial wood over the same time period. The study intended to include all forwarder brands and models with a curb weight over 5 t marketed in Sweden from 1962 to 2012. The earlier forest tractors, mentioned above, are not included.
Materials and methods
A literature survey was done of the history of forwarder development in the usual literature databases. Additionally, some older internal research institute reports and other documents not widely available were found in library storerooms, or in a private library collected by one of the co-authors (BA) during his academic working life that began in the late 1950s.
Technical data on forwarders and the year of introduction to the Swedish market were mostly collected from the specifications published by the manufacturers directly, but also material such as advertisements in old forestry magazines and on internet forums (e.g. Johnsen Citation2015) was used. In many cases, there were several different options for components like tires and loaders. In such cases, the most common alternative was chosen.
The load index for forwarders was calculated as the maximum load weight divided by the curb weight (Malmberg and Granström Citation1981), (Equation 1).
Max L = Maximum permitted load (kg), Curb W = Curb weight (kg).
The ground pressure of the machines was calculated as “mean ground pressure” (Malmberg and Granström Citation1981) separately for the front and rear axle (Equation 2). Input data for this model are the number of wheels, their dimensions, and the machine weight plus load on the front and rear axles. Two outlier ground pressure values have been removed from the dataset. These related to two early versions of forwarder models introduced before 1980 with a calculated ground pressure above 250 kPa. The reason for removing them was that their tire widths were unrealistically narrow, and were apparently meant to be covered with steel tracks.
Al = Axle load (kg), g = constant 9.82 m/s2 (acceleration due to gravity), n = number of wheels on the axle, r = radius of an unloaded wheel (m), w = width of an unloaded wheel (m).
For most machines, it was possible to find data concerning curb weights and maximum permitted loads, but it was only possible to source data on the weight distribution between front and rear axles for 57 models. These data were used to estimate the average weight distribution of unloaded and loaded forwarders, which then was applied to all other forwarders. The distribution of curb weight was 56% on the front axle and 44% on the rear axle for unloaded forwarders, and 39 and 61% of the total weight (curb weight plus maximum load) on front and rear axles respectively for loaded forwarders.
A main forwarder model can be configured with different number of bogies (zero, one or two) and consequently with different numbers of wheels (four, six or eight). In such cases, all different configurations were categorized as individual forwarder models.
All forwarders are registered in Sweden (Transportstyrelsen Citation2015). However, this register is only valid for a few years after which old data are deleted. Thus, data for the most recent years were collected from the register directly, whereas earlier data had to be gathered differently. Forest magazines (e.g. Davner Citation2002), the Swedish Forest Research Institute Skogforsk (eg. Myhrman Citation1993, Citation1995, Citation1997, Citation1999) and internet sites (e.g. Johnsen Citation2015, Citation2019) have published, on a more or less regular basis, the annual sales figures from this register over the course of a series of years. Thus, by combining sources a complete dataset on the number of forwarders sold in Sweden from 1975 to 2017 was created.
Statistical analyses of how technical parameters have changed over time were performed by using regression analysis of data relevant to lengthy time periods, or with t-tests between mean values calculated over shorter time periods. The critical probability for a significant difference between samples was set to p ≤ 0.05.
Results
Early developments in Canada
The first steps in the mechanization of short-wood extraction from harvest site to roadside were taken around 1940 with the use of small crawler tractors (Silversides and Rajala Citation1997). Silversides also reports that half-tracks on farm tractors appeared at the end of the 1940s. They had an extra wheel on each side between the front and rear axle, and a steel track covering the powered rear wheel and the extra wheel.
In the winter of 1947–48 a mechanized solution, based on military surplus stock, was developed for loading by winch and transporting bundles of 1.31 m wood pieces (4 foot) that were piled by the cutters along the strip roads. In 1951 the Canadian Pulp and Paper Association hired Bonnard Equipment to improve and further develop this concept. The result was the Mark I prototype based on a Ferguson TE-A20 farm tractor with a wheeled carriage. Bundles of 1.31 m wood were loaded by winch, transported to the roadside and dumped. The improvements seen in the Mark II, also appearing in 1951, were gained by removing the front wheels of the farm tractor and introducing articulated frame steering between the tractor chassis and the carriage. Experiments with the Mark II prompted further improvements to its specifications e.g. increased tire load carrying capacity, tractive force and ground clearance. The result was the Mark III, developed in 1953 (Silversides Citation1988). The final version of this system was the all-wheel driven Mark IV, appearing in 1955. It was produced commercially and tested by four Canadian forest companies (Silversides and Rajala Citation1997). A theoretical analysis, including all processes from cutting to truck transportation, showed 20–27% cost reductions when a system including a Mark IV equipped with a boom-mounted hydraulic grapple loader was used rather than a conventional system with horse extraction (McColl Citation1958). In the winter of 1958–59 a successful trial was conducted with a Mark IV equipped with a grapple loader for loading and unloading 2.62 m lengths of wood (8 foot) (Ager Citation1961). The use of a grapple loader permitted the loggers to produce wood in small bunches that could be located almost anywhere. The switch from cut-and-pile to cut-and-bunch increased the productivity of loggers by at least 30% (Silversides and Rajala Citation1997). In 1959, the Canadian International Paper Company agreed with Dowty Equipment of Canada Limited to design, develop and manufacture a forwarder according to the basic concept that is still used for forwarders: two axles with big, fully powered wheels; articulated frame steering; rigidity in the vertical plane between the front and rear chassis parts; and fitted with a hydraulic grapple loader. The Dowty forwarder was commercially produced in six versions in 1961 (Ager Citation1961; Silversides and Rajala Citation1997), with the following main characteristics: a 74 kW diesel engine; hydrodynamic-mechanical transmission (converter); a 13.6 t curb weight; a load capacity of about 10 t; and a boom reach of 4.2 m. It could be driven equally well in both forward and reverse gears () (Ager Citation1961; V. Bergen Citation1961).
Developments in Sweden
The mechanized extraction of wood in Sweden started in the 1920s with long-distance extraction using relatively large crawler tractors towing a train of up to about 10 sledges over frozen lakes or frozen flat terrain. But it was some years into the 1930s that this was first done on a practical commercial scale, and then only on prepared ice roads (cf. Kinnman Citation1930). It was only at the end of the 1940s that the important move of exchanging horses for mechanical power in the first extraction of wood within and from the forest stand was first attempted (Sundberg Citation1978). These early developments generally followed the same pattern in Canada, even though a greater variety of machinery was already available there (Brown Citation1949).
In Sweden, the development of farm tractors into forwarders began in 1952 when the first farm tractor to be equipped with half–tracks was sold on the Swedish market. During the following years further developments of the farm tractor chassis were undertaken as it was transformed for forestry work (Östberg Citation1990; Drushka and Konttinen Citation1997). Other trials were also undertaken in Sweden in which small crawler tractors, and in 1954, rubber-wheeled crawler tractors (three rubber wheels on each side covered with steel tracks) were developed and introduced. In parallel with the development on tractors there were, in the late 1950s, further development of sledges as well as trailers, with or without powered wheels, and with or without loading equipment that could be attached to the tractor unit (Nilsson et al. Citation1961). Several of those equipment manufacturers would later develop into forwarder producers. In 1956 forest tractors were built on a farm tractor chassis with steel tracks covering all three wheels on each side with a purpose equipped wire rope crane, winch, and rollover protection. It was commonly used with a sledge as a rear load-carrying chassis part, but some of them also had powered wheels at the rear end (Embertsén Citation1976; Östberg Citation1990; Drushka and Konttinen Citation1997). From 1961 they were usually equipped with a hydraulic grapple loader. The steering was often through the front wheels (half-tracks) or by the track braking steering principle, or a combination of both; but by the late 1950s many of them had this combined with an early version of articulated steering (Embertsén Citation1976; Östberg Citation1990).
However, in 1960 horses were still being used to extract at least 80% of the industrial round-wood in Sweden (Sundberg Citation1978); but mechanization was coming fast. In 1966 it was estimated that 37% of the total industrial round-wood harvest in Sweden was extracted with ordinary tractors (most often half-track farm tractors with a wire rope crane), 30% with horses, 24% with forwarders or forest tractors, and the remaining 9% with skidders (Malmberg Citation1967). Three years later in 1969, it was estimated that as much as 67% of the total industrial round-wood harvest in Sweden was transported with forwarders or forest tractors, 16% with ordinary tractors and 10% with skidders, and only 6% was extracted with horses (Nilsson Citation1970). Skidders were used in Sweden between about 1960 and 1975, but they never extracted more than about 10% of the industrial wood volume annually, even during the peak years at the end of the 1960s (Anon Citation1988; Nordansjö Citation2011). In total 5240 forest tractors or forwarders were sold in Sweden between 1968 and 1974, with the peak year being 1971 in which 905 units were sold (Boström Citation1976; Andersson Citation1982).
The first forwarder in Sweden (Brunett 350 Boxer) was developed by Lars Bruun at Värmlands Skogsarbetsstudier (VSA) and was demonstrated as a prototype version in 1962. VSA was an organization focusing on studies and developments in the area of forest operations that, in 1964, merged into Forskningsstiftelsen Skogsarbeten and then in 1992 merged into the Swedish Forest Research Institute Skogforsk (Holmberg Citation2005). The Brunett was built on a standard farm tractor with a 41 kW engine, clutch and 10 gears. The front axle was removed and a rear load carrying chassis part with single axle wheels was attached. A hydraulic grapple loader, originally designed for trucks, was attached. An articulated steering system was mounted between the two chassis parts. The rear wheels were powered with a hydraulic motor that was engaged when needed. It had a curb weight of 7.7 t (Staaf Citation1983; Öhman Citation2013). After some technical improvements it was commercially produced in 12 versions in 1963 (Staaf Citation1983) (cf. ). The original name of this forwarder was Brunett (Ager Citation2017), but in 1968 when its manufacture was taken over by a traditional Swedish machine manufacturing company (Kockums) the spelling of the name was changed to Bruunett (Drushka and Konttinen Citation1997; Adelhult Citation2014).
Until about the late 1960s there was stiff competition in the Swedish market between forwarders and forest tractors. The breakthrough for forwarders can be considered to have occurred in 1965 when four manufacturers were selling five forwarder models on the Swedish market (Öhman Citation2013). One probable reason for forwarders winning this competition was that they generally had better trafficability than forest tractors, especially uphill (Embertsén Citation1976), due to their having powered wheels also on the rear chassis part, while forest tractors mostly did not. Another reason was that forest tractors did not have the same longitudinal stability as forwarders, since they were not rigid in the vertical plane between front and rear chassis parts. They could even tip over forwards, and then overturn sideways, when negotiating steep downhill slopes (Back et al. Citation2000).
In 1967 there were still many more forest tractors than forwarders in operational use (Malmberg Citation1968). However, in 1971, 780 forwarders were sold on the Swedish market, divided among five manufacturers and seven models. Only 125 forest tractors were sold in the same year (Myhrman Citation1971; Andersson Citation1982). Ager (Citation2017) concludes that the forwarder had become the dominant forest machine for extraction in 1971, even if many old forest tractors continued to be used much later than that. The total number of extraction machines working in large-scale forestry in Sweden (mainly forest companies and the state forestry) in 1971 was 2900 forwarders, 700 forest tractors, 300 ordinary tractors and 600 skidders. At that time, 400 horses were also still being used in large-scale forestry for wood extraction (Nilsson and Svensson Citation1971). In 1973, although only 94 new forest tractors were sold in Sweden (Myhrman Citation1974), it indicated that it would still take some time until only forwarders would be used in large-scale wood extraction.
Sale and technical parameters of forwarders in Sweden
Overall, 51 forwarder-manufacturing companies were identified, all located in Sweden or Finland. The period during which the greatest number (10–15) of different manufacturing companies were producing forwarders at the same time was between 1980 and 1987. In total, 299 main forwarder models were identified, many of which could be equipped with different numbers of wheels, so giving in total 361 individual forwarder model configurations.
Forwarders have become significantly heavier over time (p ˂ 0.001, ). Before 1970, the curb weight was in general between 8 and 14 t with an average of 9.2 t (SD 1.72). Since 2010 the curb weight has in general been between 11 and 23 t with an average of 17.3 t (SD 3.31) ().
Figure 4. The curb weight of forwarders sold in Sweden as a function of year of introduction to the Swedish market.
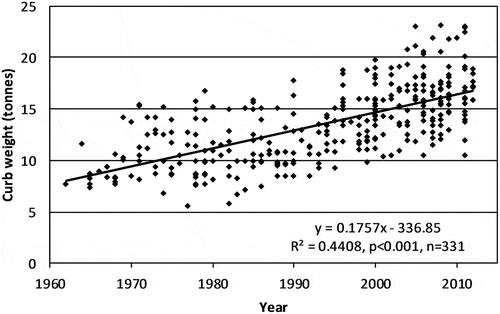
The maximum load has also increased over time, but not as much as the curb weight. Before 1970 the maximum load was on average 11.5 t (SD 2.93) which was significantly lower than the 2010 average of 14.5 t (SD 3.07) (p = 0.001, t-test). As a result, the total mass (curb weight plus maximum load) has increased significantly over time (p ˂ 0.001, ). Before 1970 the total mass was on average 20.4 t (SD 3.73) and since 2010 it has been on average 31.8 t (SD 6.21) ().
Figure 5. The total mass (curb weight plus maximum load) of forwarders sold in Sweden as a function of year of introduction to the Swedish market.
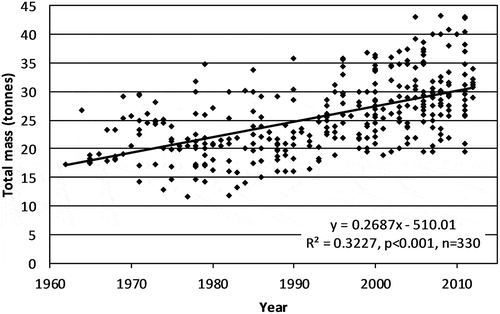
Because of the curb weight increasing over time more than the maximum load, the average load index has decreased significantly over the same period (p ˂ 0.001, ). Before 1970 the load index was on average 1.22 (SD 0.28) and since 2010 it has been on average 0.84 (SD 0.08). The variation in load index was larger before than after 1985 ().
Figure 6. Load index of forwarders sold in Sweden as a function of year of introduction to the Swedish market.
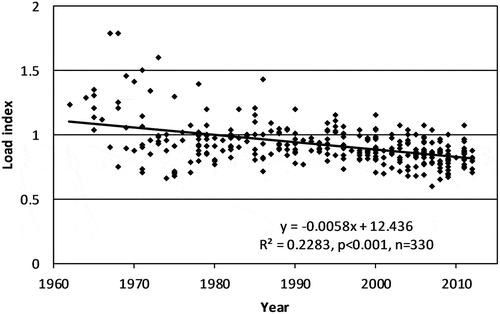
The engine capacity (power and torque) on forwarders has increased significantly over time. Before 1970, the engine power was on average 71.6 kW (SD 24.9), which was significantly lower than the 2010 average of 158.6 kW (SD 35.2) (p ˂ 0.001, t-test). Before 1970 the engine torque was on average 318 Nm (SD 72) which was significantly lower than the 2010 average of 907 Nm (SD 211) (p ˂ 0.001, t-test). This increase in engine capacity has more than compensated for the reported increase in total mass (p ˂ 0.001, and ). Before 1970 the ratio between engine power and total mass was on average 3.44 kW/t (SD 0.94) and since 2010 it has been on average 5.00 kW/t (SD 0.72), meaning an increase of 45% (). Before 1970 the ratio between engine torque and total mass was on average 15.0 Nm/t (SD 2.2) and since 2010 it has been on average 29.3 Nm/t (SD 2.7), meaning an increase of 95% ().
Figure 7. Engine power as a ratio of total mass of forwarders sold in Sweden as a function of year of introduction to the Swedish market.
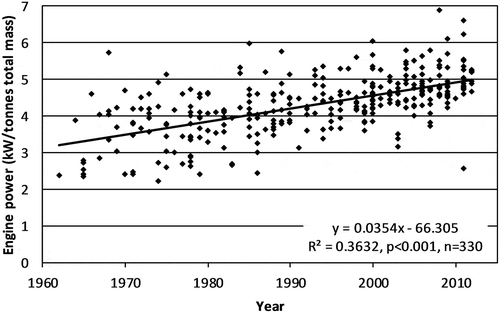
Figure 8. Engine torque as a ratio of total mass of forwarders sold in Sweden as a function of year of introduction to the Swedish market.
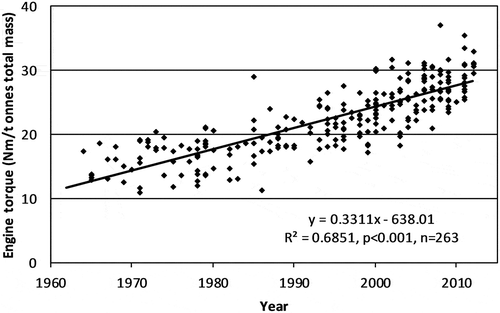
For an unloaded forwarder, the ground pressure is higher on the front than on the rear axle. For a fully loaded forwarder the situation is opposite with a higher ground pressure on rear axle. Both with and without a load, the mean ground pressure on forwarders has decreased if comparing the periods before and after 1985. Before 1985 the ground pressure without load on the front axle was on average 73.7 kPa (SD 19.6) which was significantly higher than the after 1985 average of 59.5 kPa (SD 15.6) (p ˂ 0.001). Before 1985 the ground pressure with full load on the rear axle was on average 116.5 kPa (SD 28.9) which was significantly higher than the after 1985 average of 99.9 kPa (SD 18.4) (p ˂ 0.001) (). Since 1985 there has been no significant change in ground pressure on either front or rear axles (p ˃ 0.1).
Figure 9. Ground pressure of forwarders sold in Sweden, plotted against the year of introduction to the Swedish market. Circles indicate front axle on unloaded forwarders; filled triangles indicate rear axle on fully loaded forwarders.
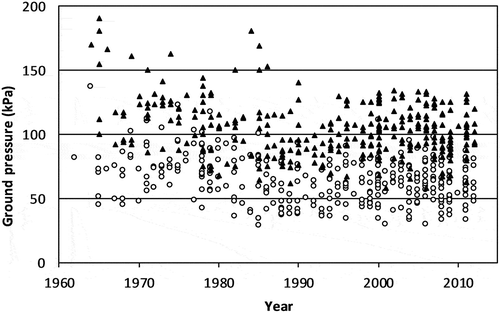
The reason for decreased or constant ground pressure over time () in spite of heavily increased total mass () is that the contact area between wheels and ground has increased on the rear axle. The main reason for this is that wheel width has increased significantly, as has the average wheel diameter (data not shown). The range of standard tire widths before 1970 was 330–600 mm, and since 2010 it has been 600–750 mm, meaning that 600 mm defined the widest tires before 1970 and the narrowest tires since 2010.
In total, 12,602 forwarders were sold in Sweden between 1975 and 2012. In general, the annual sales of forwarders in Sweden decreased from 1975 to 1993. Sales peaked in 1976, 1983 and 1989 but overall showed a decrease from 580 to 406 forwarders per year, equivalent to a decrease of 30% during the 13-year period. In 1993 sales hit a minimum with only 98 forwarders sold, after which sales increased to another peak in 2011 with 398 forwarders sold ().
Combining the data on annual harvested industrial wood volume () with the annual sales of forwarders () gives the number of forwarders sold in Sweden per million m3 harvested per year. In general, the annual sales of forwarders per million m3 harvested in Sweden decreased between 1975 and 1993. The peak years of sales in 1976, 1983 and 1989 showed a decrease from 11.6 to 8.2 forwarders sold per million m3 industrial wood harvested, and in 1993 only 2.0 forwarders per million m3 industrial wood were sold (). Until 1993, this is the same pattern as shown in concerning the total annual sale of forwarders. However, the increase in numbers of forwarders sold per million m3 harvested after 1993 is less clear than the annual sales in absolute numbers (cf. and ). In fact, a regression analysis of the data from 1996 to 2017 shows a significant (p = 0.029) increase in sales, but a similar analysis of the number of forwarders sold per million m3 harvested shows no significant increase (p = 0.68).
Discussion
The term forwarder was defined rather late in Sweden (Sundberg Citation1967; Selander Citation1969), and the definitions given by Sundberg (Citation1967) and Selander (Citation1969) differed somewhat, meaning that there has been a confusion in older publications about the type of machine being referenced (cf. Nilsson Citation1970). The intention in the present study has been to categorize all machines as either forwarders or forest tractors. However, the data sources concerning machines sold before 1971 might rarely have led to an incorrect classification.
Changes in the sales price of forest machines are highly correlated with changes in Swedish market prices for industrial round-wood (Nordfjell et al. Citation2010). A comparison of the annual sales () with forwarder sales prices in Nordfjell et al. (Citation2010) showed that those years in which forwarder sales peaked were also years in which forwarders sold at relatively high prices, and when market prices of industrial round-wood in Sweden were high. In other words: the machine manufacturers have been able to command a higher price for their products, and achieve more sales, when the forest companies have had good years. The opposite situation has been the case when forest companies have had less productive years. The outcome of this must have been rather extreme variations in the profitability for forest machine manufacturing companies. This has probably been one important reason for the common selling and/or merging of forest machine manufacturing companies in the past (cf. Östberg Citation1990; Drushka and Konttinen Citation1997; Adelhult Citation2014).
The measure of the number of forwarders sold per million m3 industrial wood harvested in a certain year gives an indication of how large the volumes are that, on average, a forwarder transports during its life time. This measure is not totally correct since a forwarder will transport logs for several years after it is purchased. The data concerning harvested volumes is lagging behind the respective data concerning the sales of those forwarders that extracted the harvest. However, when comparing values over relatively long time spans, the lag effect should be less important, especially if the time span is longer than the average working lifetime of a forwarder. During the period 1975 to 1990 the sales of forwarders ranged from 7 to 12 per million m3 industrial wood harvested (). If all this volume was extracted with forwarders it indicates an average between 83,000 m3 and 143,000 m3 extracted during the lifetime of a forwarder, with the highest value at the end of this time period. During the period 1996 to 2017 the sales of forwarders ranged from 4 to 6 per million m3 industrial wood harvested (). If all this volume was extracted with forwarders it indicates an average of between 167,000 m3 and 250,000 m3 extracted during the lifetime of a forwarder, with the highest value again at the end of this time period. These numbers indicate that forwarders extracted almost twice as much wood in their lifetime after 1996 than before 1990. However, not all the industrial wood volume harvested () was extracted with forwarders, meaning that the volume of wood extracted with a forwarder during its lifetime likely is overestimated. Some of the total volume would have been transported by private wood-lot owners who may have used horses and farm tractors, as well as forwarders and other machines smaller than 5 t. However, the amount of wood extracted by means other than an ordinary forwarder, and then delivered to industries, has decreased over time. This means that the relative difference in volumes extracted during the lifetime of a forwarder is somewhat higher than the above estimate.
The decrease in load index over time () might at first thought be considered as a step backwards in technical development and efficiency, (Löfroth and Hallonborg Citation1998; Brunberg et al. Citation2000). There are however several logical reasons for there to have been an increased weight of forwarders, without a respective increase in maximum load. The boom lifting capacity has increased over time (Nordfjell et al. Citation2010), indicating larger and heavier booms. In the past there have been examples of data on forwarder weight provided by manufacturers that have been too low. However, the quality of provided weight data seems to have improved over time, suggesting that the load indexes of earlier years may have been overestimated for some forwarder models. This is also supported by the fact that the load index varied over a wider range before 1985 than after that year (). There are also many more models of forwarders with a bogie at the front end (eight-wheeled forwarders) after 2000 than before (Öhman Citation2013); this adds a considerable weight without increasing the load capacity. After 2006 adjustable load-bunks became common on many forwarder models. Furthermore, after 2009 tilting or rotatable cabins were often fitted (Öhman Citation2013), which also adds weight without increasing the load capacity. The gradual increase in wood volume transported by a forwarder during its lifetime shows that forwarders have also become more durable. One reason for this might be that the load index of older forwarder models was too high causing excessive wear and tear.
The fact that the smallest forwarder on the market in 2012 has the same curb weight as the average forwarder in the late 1970s () has opened a possibility for new manufacturers with smaller forwarders to enter the market. Some private forest owners have created a demand for forest contactors with smaller forwarders to undertake first thinning operations (Gustavsson Citation2017). At the time of writing (2018) there are three new manufacturers that market, in total, four small conventional forwarders on the Swedish market. Three of them have a maximum load of 5–5.5 t and the fourth has a maximum load of 7.5 t. It was also one of the already established manufacturers (Gremo) that in 2017 introduced a small forwarder with a maximum load of 8.5 t. The future will tell if the market for such small forwarders is big enough to sustain a profitable production, either in Sweden or elsewhere.
The data on maximum load show that the old definition of forwarder size-classes (Athanassiadis et al. Citation1999) i.e. < 10 t, 10–12 t, and > 12 t, doesn’t correspond very well with the current range of forwarders on the market. About 60% of the forwarders in the present study that have been introduced into the Swedish market since 2000 fall into the largest size-class according to this definition. It is also now common practice for forwarder manufacturers to divide the class above 12 t into two groups. The authors suggest therefore that the definitions of forwarder size-classes should be updated to reflect the current structure of the forwarder market in Sweden. The recommendation is to use 3 t size-classes, and also to include classes for the smallest and largest forwarders in the system. The largest forwarder models in the present study have a maximum load capacity of 20 t, so this size and above would define the largest size-class. If the future reveals a need to include yet larger forwarders, it will be simple to add and name an extra size class ().
Table 1. Suggested new definitions of forwarders based on forwarder size-classes. Maximum load capacity (tonnes).
By following the size-classes suggested in , 8% of the forwarders in the present study introduced after 2009 would be categorized as Small, 33% as Medium, 29% as Large, 21% as XL and 8% as XXL.
Many of the parameters reported in the present study show a more or less linear trend, which increases or decreases over time (, , and ). It might be tempting trying to predict the future development by just extrapolating those trends. There are several reasons why this would be wrong. Currently the largest forwarders are already so large that any further increase in size would make it difficult to transport them on public roads between harvesting sites due to Swedish traffic regulations concerning the width and height of vehicles. The assumption is, then, that traffic regulations rather than the forest operations per se will define the limit for dimensions that in turn limit the curb weight and total mass.
Many of the parameters tested by regression analysis in the present study range rather widely over time. For parameters like curb weight, total mass and engine size, this is to be expected since the data cover the entire range of forwarder size-classes (). In general, the size-class Small includes forwarders only used in thinning, while size-classes XL and XXL are occupied by forwarders only used in final fellings. However, the range of values in variables like engine power, or torque per t total mass ( and ) are more difficult to understand. The spread of those variables may well decrease over time as the designs of new forwarders are optimized and unified. Why this has not yet occurred is, perhaps, simply because machine manufacturers try to standardize the use of components as much as they can. The engine and many expensive transmission components are used in several models of machines (and not only in forestry machines) and will therefore not be optimal for all forwarders. Compared to most other work machines (farm tractors, excavators, loaders etc.) forest machines are produced in very low numbers (Drushka and Konttinen Citation1997), and in order to keep development costs down it is necessary to be able to use standardized components as much as possible.
It is difficult to understand why Canadian expertise and their well-designed prototype Bonnard Logger in 1958–59, and the 1961 commercially produced Dowty forwarder (), did not influence forwarder development in Sweden at that time. It begs the question of why, in Sweden in 1962, it was decided to develop from scratch a machine based on a farm tractor chassis instead of using the purpose-built Dowty forwarder (cf. and ). To test the Dowty forwarder concept it would have been simple to import just one unit, and to study and test its abilities under Swedish conditions. Ager (Citation2017) discusses this matter, as well as asking why it took so long for the forwarder concept to be accepted in Sweden; he comes to a number of likely reasons as follows. (1) There was a commonly held belief within a number of major Swedish forest companies at that time, that mechanization of harvesting would lead to tree length harvesting, and skidding to roadside. They were therefore much more interested in skidders; in fact the Garrett Tree Farmer skidder was first imported in 1961, and was later even manufactured in Sweden under licence. (2) The Dowty forwarder, with its 13 t curb weight, was much bigger than most Swedish experts of that time considered as being suitable, or its use even possible, for transporting logs in the terrain of Swedish forestry. Some prominent Swedish experts saw the Dowty forwarder more as a kind of truck for transporting logs on bad forest roads. The first forwarders developed in Sweden had a curb weight below 8 t and a rather small engine. It took until the end of the 1960s before any forwarder in Sweden was of a comparable size to the Dowty forwarder (Öhman Citation2013). (3) The pioneering development of a forwarder in Sweden was done in a region (Värmland) where a lot of effort had been spent on developing and improving the tools and work methods employed in motor-manual cutting and log transportation with horses. The use of a forwarder required a more advanced way of directional felling and log-piling within reach of a loader. Consequently there was a lot of resistance to the introduction of forwarders among forest companies close to where it was being developed. (4) The inventor who developed the first Swedish forwarder (Lars Bruun) did this as an employee at one of the Swedish forestry study organizations at that time (VSA). There was, however, an increasing level of general distrust towards VSA from many forest companies, and when VSA and Lars Bruun promoted the forwarder concept in 1962 it was only a few forest professionals in a few forest companies that had any faith in the new concept. It was one of those companies, Iggesunds bruk (whose manager for forest technology Gösta Bruun was Lars Bruun’s brother!) that, in 1963, bought seven of the first 12 commercially produced Brunett forwarders. They evaluated the Brunett forwarders thoroughly and gave the manufacturer feedback with recommendations for improvements.
Figure 3. The Canadian Dowty forwarder with steering wheels in both directions (Photo Bengt Ager Citation1961).
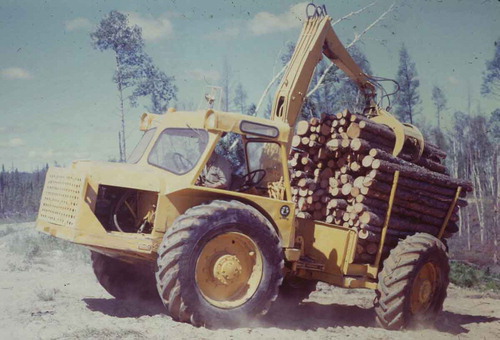
Vanclay (Citation2011) hazarded some predictions concerning the technological advances that might come about in forest machines over the course of the following 25 years (by 2036). He thought that “new sensing technology will allow harvesting machines to better optimise both vehicle movements and handling of harvested material, and to provide a comprehensive inventory of the residual stand and of soil data to assist the management of the residual forest.” Some aspects of this forecast have already come to fruition, e.g. information concerning the spatial distribution and assortment of specific log volumes can now be used to find the most efficient number and proportion of assortments to combine in the various loads requiring forwarding from a given stand (Manner et al. Citation2013). There have also been forecasts concerning the future automation or semi-automation of forwarder work. This is not new: it has been a topic at several scientific meetings and workshops since 1974, but few products have reached the market so far (Lindroos et al. Citation2017). However, studies have shown that an autonomous forwarder is able to follow a previously specified path with a high level of accuracy (Ringdahl et al. Citation2011). Häggström and Lindroos (Citation2016) point out that technical developments in the area of automation and semi-automation will be important in improving the safety and productivity of harvesters and forwarders. The cooperation between harvester and forwarder work can also be further improved when the work is automated or semi-automated. According to Lindroos et al. (Citation2015) the automation of forwarder cranes would reduce an operator’s mental fatigue by automating the crane’s movements. It would also improve efficiency since computers are better than people at optimizing combinations of factors like speed of work, fuel consumption and energy usage. Lindroos et al. (Citation2015) further states that “additionally, this [crane automation] technology also offers the possibility to improve operator and machine safety by applying virtual restrictions to harmful crane movements.”
But, even with the use of all kinds of sensor technology and an optimized course for a forwarder to take in relation to assortments and distance, and a fully automated forwarding process, it is still a matter of hundreds or thousands of tonnes of timber that have to be extracted from a harvesting site to the roadside. Currently, the only other known ways to avoid tonnes of logs being extracted over the ground is the use of cable systems, helicopter logging, or other types of aircraft like balloons (Guimier and Wellburn Citation1984; Chung et al. Citation2004; Roberts et al. Citation2004). However, the majority of wood extraction everywhere in the world, from flat or moderately steep terrain, will still be executed with ground-based machines, at least in the near future, because of a combination of economy and energy consumption. Damage to soils has been identified as one of the most important factors affecting the sustainability of future forestry (Marchi et al. Citation2018). It is therefore easy to forecast that soil damage and machines for wood extraction will be even more important issues in the future (Abbas et al. Citation2018; Lindroos et al. Citation2017). From a machine design perspective, it includes among other things optimized ground contact devices with low ground pressure, slip control, an even load distribution, improved load index, and control of vertical dynamic forces.
In conclusion, the forwarder concept was invented in Canada, but later mainly manufactured in Sweden or Finland. Forwarders are specialized vehicles produced in few numbers. They have become larger and more powerful over time, and extract over time larger volumes during their lifespan. Soil damage issues are predicted to be of increased importance for further development of forwarders.
Acknowledgements
Some months before this paper was submitted for review, Professor emeritus Bengt Ager sadly passed away at the age of 89 years. The forwarder concept was introduced in the early part of Ager’s long career as researcher (which yielded three (!) PhD titles), and he personally knew many of the inventors and researchers involved in the development of forwarders, both in Canada and Sweden. Thus, his contribution was invaluable for this paper, and especially for the description of the early stages of the forwarder development.
An earlier and summarized version of parts of this article was presented at the 5th Forest Engineering- Formec Conference in Gerardmer, France, in September 23–26, 2014.
Freja, Vidar and Sara Lindroos are thanked for their contributions with the drawing of .
Disclosure statement
No potential conflict of interest was reported by the authors.
Additional information
Funding
References
- Abbas D, Di Fulvio F, Spinelli R. 2018. European and United States perspectives on forest operations in environmentally sensitive areas. Scand J For Res. 33(2): 188–201. doi:10.1080/02827581.2017.1338355.
- Adelhult S. 2014. En norrländsk teknikhistoria. In: Björkman A, editor. Att skörda en skog. Västerbotten 1. 2014. Sweden: Västerbottens museum, Västerbottens läns hembygdsförbund. (In Swedish).
- Ager B. 1961. Motoriserad terrängtransport i Nordamerika. Norrlands Skogsvårdsförbunds Tidskrift. Vol. 4. Forskningsstiftelsen SDA. Meddelande nr. 74. Stockholm. (In Swedish).
- Ager B. 2017. Nedslag i skogsbrukets teknikhistoria. Umeå (Sweden): Institutionen för skogens biomaterial och teknologi, SLU. Rapport 11/2017. (In Swedish).
- Andersson S. 1982. Ny teknik i skogen. Sekretariatet för framtidsstudier. Liber Förlag. (In Swedish).
- Anon. 1988. 50 years of forest technology R&D in Sweden. Kista (Sweden): Forskningsstiftelsen Skogsarbeten. Redogörelse nr. 6, 1988. (In Swedish).
- Anon. 2014. Swedish statistical yearbook of forestry 2014. Jönköping (Sweden): Official Statistics of Sweden. Swedish Forest Agency.
- Anon. 2017. Gross felling in 2017, preliminary statistics. Sveriges officiella statistic, statistiska meddelanden JO0312 SM 1801. Swedish Forest Agency, Jönköping (In Swedish).
- Athanassiadis D, Lidestav G, Wästerlund I. 1999. Fuel, hydraulic oil and lubricant consumption in swedish mechanized harvesting operations, 1996. J For Eng. 10(1):59–66.
- Back S, Rasch L, Johansson L, Lejman M, eds. 2000. Från yxa till skördare – en berättelse om skogens arbetare och dess förbund. Stockholm (Sweden): Skogs- och träfacket. (In Swedish).
- Boström C. 1976. Progress in rationalization and the current machinery situation. The rationalization conference 1976. Redogörelse nr. 3, 1976. Forskningsstiftelsen Skogsarbeten. Stockholm, Sweden. (In Swedish).
- Brown N C. 1949. Logging – the principles and methods of harvesting timber in United States and Canada. New York: John Wiley & sons, Inc.
- Brunberg T, Eriksson G, Granlund P, Löfgren B, Löfroth C, Nordén B. 2000. Skärpning! Mellanskotarna håller inte måttet. Uppsala (Sweden): Skogforsk. Resultat 2000:20. (In Swedish).
- Chung W, Sessions J, Heinimann HR. 2004. An application of a heuristic network algorithm to cable logging layout design. Int J for Eng. 15(1):11–24.
- Davner L. 2002. 612 skogsmaskiner såldes ifjol, eller? Skogen nr. 6–7; p. 12–13. (In Swedish).
- Drushka K, Konttinen H. 1997. Tracks in the forest. Helsinki (Finland): Timberjack Group; p. 1–254.
- Embertsén S. 1976. Logging and transport in the Kramfors forests of SCA 1911–1965. Stud For Suec. (134): 59–65. (In Swedish).
- Guimier D-Y, Wellburn G-V. 1984. Logging with heavy-lift airships. Forest Engineering Research Institute of Canada, FERIC. Technical Report No. TR-58.
- Gustavsson H. 2017. Time study and quality monitoring when comparing of small and conventional harvesters and forwarders in the first thinning. Umeå (Sweden): Sveriges lantbruksuniversitet, Institutionen för skogens biomaterial och teknologi. Arbetsrapport nr. 5/2017. (In Swedish).
- Häggström C, Lindroos O. 2016. Human, technology, organization and environment – a human factors perspective on performance in forest harvesting. Int J for Eng. 27(2):67–88.
- Holmberg L-E. 2005. Skogshistoria år från år 1177–2005 – skogspolitiska beslut och andra viktiga händelser i omvärlden som påverkat skogsvårdsorganisationens arbete. Jönköping (Sweden): Skogsstyrelsen. Rapport 5/2005. (In Swedish).
- Johnsen T. 2015. Skotarkartan. [ accessed 2015 Mar 24]. http://skotarkartan.se/. (In Swedish).
- Johnsen T. 2019. Skogsforum. [ accessed 2019 Jan 10]. https://skogsforum.se/. (In Swedish).
- Kinnman G. 1930. Skogsteknologi – teknisk och ekonomisk handledning vid skogens avverkning, transport och förädling. In: Sederholm,G., Sonesson, N., Leufvén, G.,Nilsson-Ehle, H. & Sjöström, A. Stockholm. Svenska jordbrukets bok – illustrerad handbok för jordbruket och dess binäringar. Albert Bonniers förlag. (In Swedish).
- Lindroos O, Häggström C, La Hera P. 2017. Drivers of advances in mechanized timber harvesting – a selective review of technological innovation. Croat J For Eng. 38(2):243–258.
- Lindroos O, Ringdahl O, La Hera P, Hohnloser P, Hellström T. 2015. Estimating the position of the harvester head – a key step towards the precision forestry of the future? Croat J For Eng. 36(2):147–164.
- Löfroth C, Hallonborg U 1998. Skotartest 98. Uppsala (Sweden): Skogforsk. Resultat 1998:26. (In Swedish).
- Lundbäck M, Häggström C, Nordfjell T 2018. Worldwide trends in the methods and systems for harvesting, extraction and transportation of roundwood. 6th International Forest Engineering Conference; 2018 Apr 16–19. Rotorua, New Zealand.
- Malmberg C-E. 1967. Mekaniseringsläget hösten 1966. In: Anon 1967, editor. Föredrag vid skogschefskonferensen i Jönköping 9–10 november 1966. Del 1. Redogörelse nr. 1; p. 9–15. 1967. Stockholm (Sweden): Forskningsstiftelsen Skogsarbeten. (In Swedish).
- Malmberg C-E. 1968. Den tekniska utvecklingen – nuläge och aktuella tendenser. In: Anon 1968, editor. The lectures given at the rationalization conference in Sundsvall. 1968 Mar 27–28. Redogörelse nr. 6; p. 10–15. 1968. Stockholm (Sweden): Forskningsstiftelsen Skogsarbeten. (In Swedish).
- Malmberg C-E, Granström L, eds. 1981. Terrängmaskinen Del 2. Stockholm (Sweden): Forskningsstiftelsen Skogsarbeten. (In Swedish).
- Manner J, Nordfjell T, Lindroos O. 2013. Effects of the number of assortments and log concentration on time consumption for forwarding. Silva Fennica. 47(4):Article id 1030.
- Marchi E, Chung W, Visser R, Abbas D, Nordfjell T, Mederski P, Brink M, Laschi A. 2018. Sustainable Forest Operations (SFO): a new paradigm in a changing world and climate. Sci Total Environ. 634(2018):1385–1397.
- McColl B J 1958, March. The ”Forwarder” concept. To maintaining member companies. Technical Report No. 78. Pulp and paper research institute of Canada.
- Myhrman D. 1971. Technical development. In: Anon, editor. Introduction of highly mechanized methods. Papers given at the rationalization conference held in Saltsjöbaden November 10–11, 1971. Redogörelse nr. 9, 1971. Stockholm (Sweden): Forskningsstiftelsen Skogsarbeten. (In Swedish).
- Myhrman D. 1974. The current situation regarding machinery. In: Anon, editor. Continued mechanization – economy, raw materials, working environment? Papers given at the rationalization conference held in Lidingö March 13–14, 1974. Redogörelse nr. 2, 1974. Stockholm (Sweden): Forskningsstiftelsen Skogsarbeten. (In Swedish).
- Myhrman D. 1993. Nya skotare. Skogforsk Nytt, Aktualiteter från SkogForsk. nr. 1/1993. (In Swedish).
- Myhrman D. 1995. 166 nya skotare 1994. Skogforsk Nytt, Aktualiteter från SkogForsk. nr. 1/1995. (In Swedish).
- Myhrman D. 1997. Uppåt för skotare och virkesbilar. Skogforsk Nytt, Nyheter från SkogForsk. nr. 1/1997. (In Swedish).
- Myhrman D. 1999. Något färre nya skotare 1998. Skogforsk Nytt, Nyheter från SkogForsk. nr. 1/1999. (In Swedish).
- Nilsson B. 1970. Skogsbrukets rationalisering under 1960 talet. In: Anon, editor. Papers given at the rationalization conference held in Karlstad. 1969 Dec 4–5. Redogörelse nr. 2, 1970. Stockholm (Sweden): Forskningsstiftelsen Skogsarbeten. (In Swedish).
- Nilsson B, Svensson SA. 1971. The present situation and trends in forestry rationalization. In: Anon, editor. Introduction of highly mechanized methods. Papers given at the rationalization conference held in Saltsjöbaden November 10–11, 1971. Redogörelse nr. 9, 1971. Stockholm (Sweden): Forskningsstiftelsen Skogsarbeten. (In Swedish).
- Nilsson N, Söderlund J, Nilsson L-E. 1961. Tillverkning inom Sverige av lastfordon för vintertransport av virke med traktor – en sammanfattande inventering utförd 1959–1960. Stockholm (Sweden): SDA Redogörelse nr. 5. (In Swedish).
- Nordansjö I. 2011. Technical advances in forestry. In: Jansson U, editor. Agriculture and forestry in Sweden since 1900. Stockholm (Sweden): National Atlas of Sweden. The Royal Swedish Academy of Agriculture and Forestry. Norstedts förlagsgrupp.
- Östberg M. 1990. En smedjas förvandling – ÖSAs historia [The transformation of a blacksmith’s workshop - The history of ÖSA]. Bollnäs (Sweden): Nyströms tryckeri AB. (In Swedish).
- Öhman E. 2013. The wheel forwarders technical development. SLU (Umeå, Sweden): Institutionen för skoglig resurshushållning. Arbetsrapport 395/2013. (In Swedish).
- Nordfjell T, Björheden R, Thor M, Wästerlund I. 2010. Changes in technical performance, mechanical availability and prices of machines used in forest operations in Sweden from 1985 to 2010. Scand J For Res. 25(4):382–389.
- Ringdahl O, Lindroos O, Hellström T, Bergström D, Athanassiadis D, Nordfjell T. 2011. Path tracking in forest terrain by an autonomous forwarder. Scand J For Res. 26(4):350–359.
- Roberts B, Ward B, Rollerson T. 2004. A comparison of landslide rates following helicopter and conventional cable-based clear-cut logging operations in the Southwest Coast Mountains of British Columbia. Geomorphology. 61:337–346.
- Selander E, ed. 1969. Glossary of forest terms: Swedish-English. Stockholm (Sweden): Swedish centre of techhnical terminology publications. No. 43.
- Silversides C R. 1988. The impact of forest operations and techniques upon forest mechanization in eastern Canada. Commun Norw For Res Inst. 41(16):233–250. Ås, Norway.
- Silversides C R, Rajala RA. 1997. From broadaxe to flying shear. The mechanization of forest harvesting east of the Rockies. Ottawa (Canada): National Museum of Science and Technology.
- Staaf A. 1983. En skogsteknisk historik – med anknytning till Värmlands skogsarbetsstudier. Institutionen för skogsteknik, SLU, stencil nr 251. Garpenberg (In Swedish).
- Sundberg U. 1967. Lunnare och skotare – nya skogstekniska termer. In: Delin BH, editor. (In Swedish). Stockholm (Sweden): Skogen nr 16; p. 410–411.
- Sundberg U. 1978. Teknik i skogen. In: Fries J, Zimmerman J, editors. Skogshögskolan 150 år. Problem och idéer i svenskt skogsbruk 1828–1978. Uppsala (Sweden): Allmänna skrifter nr 2; p. 127–144. Sveriges lantbruksuniversitet. (In Swedish).
- Transportstyrelsen. 2015. [ accessed 2015 Mar 24]. http://transportstyrelsen.se/sv/Vag/Fordon/Vagtrafikregistret. (In Swedish).
- UN. 2015. Statistics yearbook Forest products. Rome: FAO Statistics yearbook. accessed 2017 Oct 15. http://www.fao.org/3/a-i7304m.pdf.
- V. Bergen L 1961. Nyare drivningsformer – redogörelse för vissa metoder och maskiner vilka är föremål för försök i USA, Kanada, Ryssland och Sverige. Stockholm. SDA-redogörelse nr 7, 1961. (In Swedish).
- Vanclay J-K. 2011. Future harvest: what might forest harvesting entail 25 years hence? Scand J For Res. 26(2):183–186.