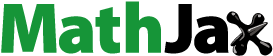
ABSTRACT
In this work, graphene was used as a filler for banyan aerial root fibers reinforced epoxy composites at various compositions. The synergetic effect of graphene and banyan fibers, on the physical and mechanical characteristics of the epoxy thermoset, was studied. The mechanical tests, hardness, water absorption behavior and morphology of the composites were studied. Significant improvement in tensile strength, flexural strength, shore D hardness and substantial reduction in the percentage of water absorption was observed. This paper also discusses the ideal proportion of banyan fibers with graphene powder for the development of the improved epoxy composites. The optimum concentration of the composites was observed at 4% of graphene powder in the 40% banyan fiber-reinforced hybrid epoxy composites. From the results, it is proved that graphene combined with 40% banyan fiber-reinforced epoxy hybrid composites will efficiently improve the strength of the composites.
摘要
本文以石墨烯为填料,制备了不同组成的榕树气生根纤维增强环氧树脂复合材料. 研究了石墨烯与榕树纤维对环氧热固性树脂物理力学性能的协同作用. 研究了复合材料的力学性能、硬度、吸水性能和形貌. 观察到拉伸强度、抗弯强度、肖氏硬度和吸水率显著降低的显著改善. 本文还讨论了榕树纤维与石墨烯粉的理想配比,以期开发出性能优良的环氧树脂基复合材料. 在40%榕纤维增强混杂环氧树脂复合材料中,石墨烯粉体的最佳浓度为4%. 结果表明,石墨烯与40%榕树纤维增强环氧混杂复合材料复合,能有效地提高复合材料的强度.
Introduction
Natural fibers have high strength, biodegradability, low cost, and lightweight is an alternative for synthetic fibers. Natural fibers are suitable as reinforcement materials for making polymer composites that could be employed for different lightweight applications such as automotive parts, aeroplane seats, and racing sailboat, etc. (Binoj et al. Citation2016; Faruk et al. Citation2012; Pickering, Aruan Efendy, and Le Citation2016; Rangappa and Siengchin Citation2018; Sanjay et al. Citation2016, Citation2018, Citation2018).
Anbukarasi and Kalaiselvam investigated the effect of dimension (mat fiber, short fiber, and particle), surface treatment and volume fraction of luffa fibers on the mechanical properties, thermal stability, and water absorption behavior of the composites. The treated mat fiber-reinforced epoxy composites show the maximum tensile strength, flexural strength, and impact strength when compared with short fiber, or particle-reinforced composites. However, water absorption is more for mat fiber-reinforced epoxy composites (Anbukarasi and Kalaiselvam Citation2015). Sathishkumar et al. treated snake grass fibers with various chemical reagents, such as alkali, benzoyl peroxide, benzoyl chloride, potassium permanganate, and stearic acid. These treated fibers were then used for the preparation of polyester composites. The results reveal that the mechanical properties of the treated fiber-reinforced polyester composites are higher than that of the untreated fiber composites (Sathishkumar et al. Citation2013). Athith et al. studied the mechanical and tribological properties of jute/sisal/E glass fabrics reinforced rubber/epoxy composites filled with a different proportion of tungsten carbide powder (WC). The authors observed a significant increase in tensile strength, flexural strength, impact strength and wear resistance for the composites containing WC. (Athith et al. Citation2018). Sathish et al. prepared hybrid epoxy composites and studied the water absorption behavior and mechanical properties by varying the percentage of flax and bamboo fibers by compression molding techniques. The composites with 40% flax show the best results (Sathish et al. Citation2017). Arpitha et al., incorporated sisal and E-glass fibers with epoxy matrix and added silicon carbide filler. The results show that E-glass-reinforced composites have fewer voids and hence delivers better mechanical properties compared to other composites (Arpitha et al. Citation2017). Ganesan et al., studied the mechanical properties of polyester matrix nanocomposites reinforced by the NaOH-treated jute cloth mat (NJM) and the untreated jute cloth mat (UJM). In addition, the effects of eggshell powder (ESP) and nanoclay (NC) have also been studied. The incorporation of NC (1.5% by weight) and ESP (1.5% by weight) with NJM generated good tensile and flexural strength (Ganesan et al. Citation2018). Jeyakumar et al. prepared the glass fiber-reinforced epoxy composites filled with cloisite clay. The authors observed significant improvement in mechanical properties by the addition of nanoclay in the glass fiber-reinforced epoxy composites (Jeyakumar et al. Citation2017).
In this study, different percentage of graphene powder is used a filler for banyan aerial root fibers reinforced epoxy composites. The main objective of the study is to determine the mechanical properties and water absorption behavior of the modified epoxy composites.
Materials and methods
Matrix preparation
Epoxy resin (Araldite LY 556) of density 1.2 g/cc and hardener (Aradur HY 951) of density 0.98 g/cc were purchased from Chemicote Engineers, Bangalore, India. For the preparation of the matrix system, the epoxy and hardener were mixed in a ratio of 10:1.
Fibers preparation
Banyan is also called Ficus benghalensis and is the national tree of India. The banyan fibers were extracted and collected from the Coimbatore region, Tamilnadu. The long fiber was soaked in 5% NaOH solution for 2 h (Madhu et al. Citation2018; Sanjay et al. Citation2018) and then washed with tap water until the complete removal of NaOH from the surface of the fibers. Later the fibers were dried in an air oven at a temperature of 75°C for 24 h. After the moisture content is removed from the fiber, it is cut down into short fiber of 15 mm in length.
Graphene powder
The graphene powder with 99% purity was purchased from United Nanotech Innovations PVT. LTD. The average thickness of each graphene nanoplatelets is 5 to 10 nm, diameter 1 to 5 μm, bulk density 0.35 g/cc, and with a high aspect ratio of ca. 1000.
Fabrication procedure
The epoxy resins have high viscosity formulations. The high viscosity provides better adhesion properties and performance characteristics. Due to the high viscosity of epoxy resins, the graphene powder cannot disperse properly and may result in poor performance of the fabricated composite material. To achieve proper mixing, the graphene powder was sonicated with acetone for 30 min. The mixture was then poured to the epoxy resin and continued mixing for another 30 min at 70°C to achieve better dispersion of graphene in the epoxy matrix and to remove the acetone present in the epoxy mixture.
For making banyan fiber-reinforced composites, the chopped banyan fibers were placed inside the mold die and the required epoxy resin was poured over it. The banyan fiber-reinforced composites S1, S2 were prepared using 30% banyan fiber with 70% epoxy resin and 40% banyan fiber with 60% epoxy resin, respectively. The weighed fiber was placed inside the mold die, later the weighed epoxy resin was poured over it. The mold was closed and placed in a compression molding machine. The samples were then cured for 30 min at 140°C at a pressure of 45 Kg/cm2. After curing, samples were cooled slowly to room temperature. The wax was used to release the samples from the mold after the completion of the process. The size of the composite laminates was 270 × 270 × 3 mm3. Similarly, hybrid composites containing graphene powder were also prepared. The composites with 2, 4, 6, 8, and 10 wt% of graphene were prepared and are designated as S3, S4, S5, S6, and S7, respectively. presents the type and composition of the composites prepared.
Table 1. Type and composition of the composites prepared
Characterization
Tensile test
The tensile test was carried out using a universal testing machine, model DTRX-30 KN. For each composite, five measurements were taken and the average value was taken as tensile strength according to ASTM 3039 standard. Dimension of the sample was 250 × 25 × 3 mm3. The test was carried out under a load cell of 5 kN. The cross-head speed of 3 mm/min and a gauge length of 80 mm were used for the test.
Flexural test
Flexural test was conducted according to ASTM 790 using a universal testing machine model DTRX-30 KN. The size of the specimen was 127 × 12 × 3 mm3 and the span-depth ratio of all sample was 32:1. The load cell used was 5 kN and a crosshead speed of 3 mm/min was used for the test. For each composite, five measurements were taken and the avearge value was taken as the flexural strength.
Hardness test
The Shore D Hardness test was carried out to study the withstand capacity of the composites against the conical indentation. The test was carried out according to ASTM 2240–15 hardness standard-D type scale. The digital type shore D Durometer machine with a range 0 to 100HD and an accuracy of 0.5HD was used for testing the composites.
Water absorption test
The water absorption test was carried according to the ASTM D 570 standard. The specimen size of the samples used for testing is 64 × 12.7 x 3 mm3. The distilled water was used to find the water absorption behavior of the composites.
The percentage of water absorption in the composites is calculated using Equationequation (1)(1)
(1)
Morphological analysis
A field emission scanning electron microscope (FESEM) model ZEISS SIGMA was used to examine the fracture surface of the epoxy composites. The accelerating voltage of 5 kV was used to examine the samples. The samples were sputtered with gold before analysis.
Results and discussion
The fiber composites with different volume fraction of banyan fiber and graphene nanoplatelets modified banyan fiber-reinforced hybrid composites were prepared by the compression molding process. The mechanical properties of banyan fiber modified epoxy composites are given in and . The tensile strength increases by ca. 10% for 40% banyan fiber-reinforced epoxy composites in comparison with 30% banyan fiber-reinforced epoxy composites. Since the best result is obtained for S2 composite, graphene-based hybrid composites are prepared with S2 composite as the base material. The variations in tensile strength with respect to the concentration of the graphene powder are shown in and .
Table 2. Mechanical and water absorption behavior of epoxy composites
The result shows a significant increase in tensile strength with the addition of 4% graphene powder, the value is higher than S2 and S3 samples by ca. 63% and 45%, respectively. After 4% graphene concentration the tensile strength gradually decreases (S5, S6, S7) because of the increased filler content, which tends to agglomerate at higher loadings leading to poor tensile strength. It should be noted that the banyan fiber may also play a vital role in the high performance of the composite material and hence a synergetic increase in tensile strength is observed.
The variations in flexural strength with respect to banyan fiber loading are shown in and . The flexural strength is better for 40% banyan fiber-reinforced composites when compared with 30% banyan fiber-reinforced composites. With increasing banyan fiber content, the short length fiber forms better interlocking or chemical bonding with the epoxy matrix and is the main cause for the increase in the flexural strength. With the incorporation of graphene powder, the hybrid composites show a reasonable increase in flexural strength and a maximum value is obtained for 4 wt% filler content, this is followed by a decrease in flexural strength at higher graphene content (). As stated earlier, at higher concentrations, the graphene powder tends to agglomerate that initiate cracks at lower loadings.
The shore D Hardness is measured for unfilled and filled graphene hybrid composites. The test was conducted on 10 different areas of the same sample and the average is calculated. shows the average values of the hardness of the composites studied. From the results, the sample S1 has the lowest value and the hardness value increases for S2 sample with higher fiber content (40%). Further, the incorporation of graphene in S2 increases the hardness and the maximum value was obtained for S5 samples, this is followed by a marginal decrease.
The water absorption test is carried out according to ASTM D 570 standards. Individual samples were kept in a beaker filled with distilled water at room temperature for 120 h, later the samples are taken out from the beaker and wiped out completely and weighed using an Auto calibration machine (MH-200) whose accuracy is 0.01 g. and show that the percentage of water absorbed in the composites studied. The maximum water absorption is observed for S1 and S2 samples with 30% and 40% banyan fiber content. This is because of the hydrophilic nature of the fibers. The fibers contain free hydroxyl groups which can interact with water molecules via hydrogen bonding and also the hollow tubular structure of the fibers allows the diffusion of water molecules into composites. It is important to mention that the voids or defects present in the matrix and at the interface of the fiber and matrix may also contribute to the penetration of water molecules into the composites. On the other hand, the percentage of water absorption reduced drastically with the addition of graphene. This is due to the hydrophobic nature of the graphene nanoplatelets. Also, the presence of graphene powder reduces the void content. Thus, graphene nanoplatelets may physically hinder the penetration of the water molecules reducing the water absorption.
shows the SEM images of the samples broken after the tensile test. ) shows the SEM micrographs of 40% banyan fiber-reinforced epoxy composites. The micrographs reveal the presence of banyan fibers in the brittle epoxy composites, which exist as fiber bundles. It is observed that the fibers are wetted uniformly by the epoxy resin. The better strength of the banyan fiber-reinforced composites is due to the excellent wetting. River like patterns in the composites in the fracture surface confirms the ductile nature of the composites. Similar SEM micrographs are observed for the hybrid composites with 4% graphene content ()). On the other hand, the composites containing 10% of the graphene show agglomeration of the graphene powder in the epoxy banyan fiber-reinforced composites ()). Fiber breakage and fiber pullout are also observed in the micrograph. Some of the fibers are delaminated from the epoxy matrix by the application of the applied load. It clearly shows that the adhesion between the fiber and epoxy are influenced by the presence of graphene resulting in the fiber pull-out and fiber debonding. Thus, the poor mechanical properties of hybrid composites at higher graphene content are due to the fiber breakage and agglomeration of the graphene powder.
Conclusion
This present investigation is carried out on banyan fiber-reinforced epoxy composites containing graphene powder. The unfilled composite obtained the tensile strength of 27.93 MPa and flexural strength of 155.51 MPa. The hybrid composites containing 4% of graphene have the highest tensile strength (40.6 MPa) and flexural strength (163.23 MPa). On the other hand, the composites containing 10% of graphene give the lowest tensile strength (19.87 MPa) and flexural strength (133.55 MPa) because of the agglomeration tendency of the filler that deteriorates the matrix properties. The shore D Hardness value of the composites gradually increases by the addition of graphene powder and maximum value was observed at 6% of graphene powder and the values are reduced with the further addition of filler. Short fibers provide better fiber matrix blending and good fiber to matrix wettability. Usually, natural fiber has the property of absorbing moisture content hence with the usage of graphene reduces the moisture content. The water absorption of the composites reduced drastically with the incorporation of even a small amount of graphene powder. The hybrid composites with 4% graphene powder show excellent wetting of the fibers with epoxy resin. River like patterns of these composites in the fracture surface confirms the ductile nature of the composites. On the other hand, composites with 10% of graphene powder show matrix crack, fiber and matrix debonding, fiber pull-out defects of the composite, etc., and hence poor mechanical properties for these composites. In summary, an ideal proportion of banyan fibers with graphene powder in epoxy matrix can generate hybrid composites with interesting properties suitable for structural applications.
References
- Anbukarasi, K., and S. Kalaiselvam. 2015. Study of effect of fibre volume and dimension on mechanical, thermal, and water absorption behaviour of luffa reinforced epoxy composites. Materials and Design 66 (PA):321–30. doi:10.1016/j.matdes.2014.10.078.
- Arpitha, G. R., M. R. Sanjay, P. Senthamaraikannan, C. Barile, and B. Yogesha. 2017. Hybridization effect of sisal/glass/epoxy/filler based woven fabric reinforced composites. Experimental Techniques 41:6. doi:10.1007/s40799-017-0203-4.
- Athith, D., M. R. Sanjay, T. G. Yashas Gowda, P. Madhu, G. R. Arpitha, B. Yogesha, and M. A. Omri. 2018. Effect of tungsten carbide on mechanical and tribological properties of jute/Sisal/E-glass fabrics reinforced natural rubber/epoxy composites. Journal of Industrial Textiles 48 (4):713–37. doi:10.1177/1528083717740765.
- Binoj, J. S., R. Edwin Raj, V. S. Sreenivasan, G. Rexin, and Thusnavis. 2016. Morphological, physical, mechanical, chemical and thermal characterization of sustainable indian areca fruit husk fibers (Areca Catechu L.) as potential alternate for hazardous synthetic fibers. Journal of Bionic Engineering 13 (1):156–65. doi:10.1016/S1672-6529(14)60170-0.
- Faruk, O., A. K. Bledzki, H. P. Fink, and M. Sain. 2012. Biocomposites reinforced with natural fibers: 2000–2010. Progress in Polymer Science 37 (11):1552–96. doi:10.1016/j.progpolymsci.2012.04.003.
- Ganesan, K., C. Kailasanathan, M. R. Sanjay, P. Senthamaraikannan, and S. S. Saravanakumar. 2018. A new assessment on mechanical properties of jute fiber mat with egg shell powder/nanoclay-reinforced polyester matrix composites. Journal of Natural Fibers 1–9. doi:10.1080/15440478.2018.1500340.
- Jeyakumar, R., P. S. Sampath, R. Ramamoorthi, and T. Ramakrishnan. 2017. Structural, morphological and mechanical behaviour of glass fibre reinforced epoxy nanoclay composites. International Journal of Advanced Manufacturing Technology 93 (1–4):527–35. doi:10.1007/s00170-017-0565-x.
- Madhu, P., M. R. Sanjay, P. Senthamaraikannan, S. Pradeep, S. S. Saravanakumar, and B. Yogesha. 2018. A review on synthesis and characterization of commercially available natural fibers: Part-I. Journal of Natural Fibers 1–13. doi:10.1080/15440478.2018.1453433.
- Sanjay, M R., S. Siengchin, J. Parameswaranpillai, M. Jawaid, C. I. Pruncu, and A. Khan. 2018. A comprehensive review of techniques for natural fibers as reinforcement in composites: Preparation, processing and characterization. Carbohydrate Polymers. doi:10.1016/j.carbpol.2018.11.083.
- Pickering, K. L., M. G. Aruan Efendy, and T. M. Le. 2016. A review of recent development in natural fibre composites and their mechanical properties. Composites: Part A 83:98–112. Elsevier Ltd. https://ac.els-cdn.com/S1359835X15003115/1-s2.0-S1359835X15003115-main.pdf?_tid=f5b19772-ebbf-11e7-b2c7-00000aab0f02&acdnat=1514459715_26980301747c113e1bddde94468b1642. doi:10.1016/j.compositesa.2015.08.038.
- Rangappa, S. M., and S. Siengchin. 2018. Natural fibers as perspective materials. KMUTNB International Journal of Applied Science and Technology 11 (4):2018. doi:10.14416/j.ijast.2018.09.001.
- Sanjay, M. R., G. R. Arpitha, L. Laxmana Naik, K. Gopalakrishna, and B. Yogesha. 2016. Applications of natural fibers and its composites: An overview. Natural Resources 07 (03):108–14. doi:10.4236/nr.2016.73011.
- Sanjay, M. R., P. Madhu, P. Mohammad Jawaid, S. S. Senthil, and S. Pradeep. 2018. Characterization and properties of natural fiber polymer composites: A comprehensive review. Journal of Cleaner Production 172:566–81. doi:10.1016/j.jclepro.2017.10.101.
- Sathish, S., K. Kumaresan, L. Prabhu, and N. Vigneshkumar. 2017. Experimental investigation on volume fraction of mechanical and physical properties of flax and bamboo fibers reinforced hybrid epoxy composites. Polymers and Polymer Composites 25 (3):229–36. doi:10.1177/096739111702500309.
- Sathishkumar, T. P., P. Navaneethakrishnan, S. Shankar, and R. Rajasekar. 2013. Investigation of chemically treated longitudinally oriented snake grass fiber-reinforced isophthallic polyester composites. Journal of Reinforced Plastics and Composites 32 (22):1698–714. doi:10.1177/0731684413495321.