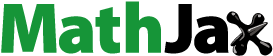
ABSTRACT
Ligno-cellulosic natural fiber like Banana can be acclimated to manufacture hybrid or union fabric with mostly used jute fiber which can get colossal popularity as a wearable product because of the health and hygiene issues. Banana fibers, extracted from the sheath, can be utilized for manufacturing fiber, can diminish the pressure on the jute fiber. It will be very frugal, and ineluctably it will be a great opportunity to blend it with the other natural fiber. In this study, a Jute-Banana hybrid fabric (JBHF) was developed by using Jute yarn (12 Ne, in warp) and Banana yarn (18 Ne, in weft). In order to evaluate physico- mechanical properties of naturally dyed Jute-Banana hybrid fabric, different tests like Stiffness, Thickness, Tensile strength, Tear strength, Drape and Crease recovery were conducted which provided satisfactory results. Colorfastness to wash, water, rubbing and perspiration of naturally dyed Jute-Banana hybrid fabrics (JBHF) also provided acceptable outcomes. FTIR test also provided the confirmation of this two fibers and Spectrophotometer was used to illustrate the dyeing quality. It was an endeavor to minimize the dependency on a single quality fiber and find an alternative way to prepare the hybrid fabric by blending two different quality natural fibers.
摘要
像香蕉这样的木质纤维素天然纤维可以适应,利用主要使用的黄麻纤维制造混合或联合织物。由于健康和卫生问题,黄麻纤维作为一种可穿戴产品非常受欢迎. 香蕉纤维,从鞘中提取,可用于制造纤维,可减少对黄麻纤维的压力. 这将是非常节俭的,不可避免地,这将是一个很好的机会,将它与其他天然纤维混合. 本研究以黄麻纱(经向12ne)和香蕉纱(纬向18ne)为原料,开发了黄麻-香蕉混纺织物(JBHF). 为了评价天然染色黄麻-香蕉混纺织物的物理力学性能,进行了刚度、厚度、拉伸强度、撕裂强度、悬垂性和折皱回复性等试验,取得了满意的结果. 天然染色黄麻-香蕉混合织物(JBHF)的耐洗、耐水、耐摩擦和耐汗渍色牢度也提供了可接受的结果. FTIR测试也证实了这两种纤维,并使用分光光度计来说明染色质量. 这是一项努力,以尽量减少对单一质量纤维的依赖,并找到一种替代方法,通过混合两种不同质量的天然纤维来制备混合织物.
Introduction
Banana (Musa paradisiacal) is one of the most huge and oldest cultivated fruit flora grown nearly anywhere in Bangladesh round the year. Presently, the banana pseudo-stem is unsafe waste in Bangladesh whilst it has been utilized in numerous international locations to make fertilizer, fish feed, bio-chemical materials, paper, handicrafts etc. It is found that a colossal part of banana vegetation is just dumped as waste causing the surrounding environment dirty and imbalance. Currently, plenty and thousands of tons of banana pseudo-stem are dumped in our Bangladesh as waste and maximum farmers are going through big issues in disposing of the accumulated banana pseudo-stem which was mentioned by Eyerer and Gettwert (Citation2010). All sorts of banana pseudo-stem can be utilized for fiber extraction which can also be used as textile fiber which was mentioned by Subagyo and Chafidz (Citation2018). Banana fiber had been culled to manufacture woven fabric as it is a natural fiber. Ligno-cellulosic natural fiber like Banana can be acclimated to manufacture hybrid or blended fabric with mostly used jute fiber which can get immensely colossal popularity as a wearable product because of the health and hygiene issues. This was an endeavor to minimize the dependency on the single fiber & find an alternative way to prepare the hybrid fabric by blending two different quality natural fibers. However, banana fiber has better fineness and spin ability. It has a bright appearance depending upon the extraction and spinning approach. Banks‐Lee and Pegram (Citation2011) identified that banana fiber absorbed and released moisture without any issues. Koohestani et al. (Citation2019) described that; it may be spun by well-accepted techniques like ring spinning, open-end spinning, bast fiber spinning, and semi-worsted spinning. It is bio-degradable and has no horrific effect on surroundings and hence may be categorized as eco-friendly fiber, mentioned by Kumar et al. (Citation2008). According to Ghorpade and Balasubramanya (Citation2013), banana fiber is significantly used for mixing and blending fiber in various international locations like the Philippines, Malaysia, Japan and Korea. It may be mixed up without trouble with other fibers like cotton, jute, PALF etc. This Ligno-cellulosic fiber is also appropriate for making technical textiles, suggested by Das et al. (Citation2010). Madhu et al. (Citation2020) identified that when banana fibers were treated with different chemicals like alkali and peroxide, during the removable of bark and other impurities, considerable weight loss was observed. The fineness of representative raw banana fibers was determined by using USTER HVI 1000 and the collected raw banana fibers were very coarse (about 140 Denier) before chemical treatments. Jute, the natural golden fiber and cheapest fiber of Bangladesh, is a long, soft, silky shine vegetable as well as bast fiber that can be spun into coarse, strong threads. Jute fibers are formed mostly of the plant materials cellulose and lignin, mentioned by Sisti et al. (Citation2018). Jute is a harsh fiber due to the presence of significant amounts of lignin and low wax content, observed by Sudhakara et al. (Citation2013). Jute fiber is entirely bio-degradable and recyclable and thus environmentally altruistic as well as friendly. Jute can be blended with other fibers, both synthetic and natural and it can be dyed with cellulosic dye classes such as natural, basic, vat, sulfur, reactive, and pigment dyes. As a curiosity for natural comfort fibers increases, consumption of jute and other natural fibers that can be blended with jute will increase which was described by Mohiuddin et al. (Citation2014). Fabrics made from banana fiber and jute are carbon dioxide neutral and naturally decomposable. Extraction of dye from henna leaves & turmeric was done and then dyeing was accomplished. Different tests(such as Stiffness, Thickness, Tensile Strength, Tearing Strength, Drape, Crease recovery and Colorfastness Tests) were carried out after the preparation of naturally dyed jute-banana hybrid fabrics (JBHF). The qualitative physico-mechanical properties of the prepared JBHF were satisfactory. FTIR test also provided the confirmation of this used two fibers & Spectrophotometer was used to illustrate the copacetic dyeing quality.
Materials and methods
Treating banana fibers with chemicals
This is a reduction of the total mass of the banana fibers due to a mean loss of fluid, bark, hemicelluloses, lignin etc., by treated the fibers with NaOH (concentration of 2.5%, 5%, 10% & 15%). The fiber weight loss can be calculated by using the formula given below. Combinedly, 4% H2O2 and 2% NaOH were also used to reduce the fineness of the banana fiber. In every case, we kept a 1:20 material liquor ratio (MLR) and the immersion period was 30 minutes. The temperature was 95°C in every time.
Weight loss % = [(IW – AW) /IW] x 100
Where IW- Mass of materials before chemical treatments (g), AW- Mass of materials after chemical treatments (g).
When banana fibers were treated with different chemicals like alkali and peroxide, during the removable of bark and other impurities, considerable weight loss was observed. Treatment leads to the irreversible alkalization effect, which increases the magnitude of amorphous cellulose at the expense of crystalline cellulose. Crystalline reduction is achieved by the removal of lignin, hemicelluloses and other residues from the surface of the fibers. As the results are shown in the weight of the banana fiber was decreased with increased concentration of the alkali.
Table 1. Weight losses of alkali treated banana fibers
Banana fiber fineness reduction& yarn formation
The fineness of representative raw banana fibers was determined by using USTER HVI 1000. Banana Fiber Fineness was reduced by using different chemicals like NaOH & H2O2. The result was mentioned in Tex, which ultimately helped to determine the weight loss % due to chemical treatment.
Spinnable properties like length, strength, fineness, tenacity, color, and elongation at break etc., are essential for yarn manufacturing. It is revealed that Banana shows similar spinnable properties like jute fiber.
Count& tensile strength determination of yarn
Yarn can be considered as a long continuous length of interlocked fibers, which is used in textile weaving, knitting, sewing etc. Tensile strength is the capability of a material to withstand a pulling (tensile) force (Dwivedi et al., Citation2016). The tensile strength of yarn was tested according to ASTM E-4. Here UTM(Testometric) was used to calculate the tensile strength. The twist per inch of yarn was measured by a mechanical Shirley twist tester. Different physical properties of Banana yarn are provided here in the . The count of the yarn was measured using the indirect English Count (Ne) by following the formula below:
Table 2. Testing result of yarn (banana)
Fabric specification & composition % of the sample in hybrid fabric
Generally, fabric means a thin, flexible sheet of material with ample strength and tear resistance (especially when wet) for habiliments, interior fabrics, and other protective, utilizable, and decorative functions. Woven cloth is composed of the interlacement of two sets of threads, namely, warp and weft threads. These threads are interlaced with one another according to the type of weave or design.
Weave plan
Construction of the fabric: 3 up – 2 down
EPI (Ends per inch) = 20 (for jute); PPI (Picks per inch) = 16(for banana)
Warp count = 12 Ne (jute); Weft count = 18 Ne (banana)
Fabric width (in inches) = 10 inches
Banana in overall fabric = 40%; Jute in overall fabric = 60%
GSM determination
Gram per square meter or GSM is a very important factor in order to specify the bulkiness of a fabric. In order to determine the GSM of a fabric, a 100 cm2 circular-shaped fabric sample was cut by using the GSM cutter. The weight of those sample fabrics was then determined by using an electric balance. By using the following formula, the GSM of the sample fabrics was then determined.
The GSM of the fabric sample was determined as 184 gm/m2.
Dyeing of banana, jute blended fabric
Natural ingredients like henna leaves & turmeric were used. Extraction of dyes were done from natural ingredients by following the procedure, mentioned by Pujari, Ramakrishna, and Kumar (Citation2014). Firstly, the required ingredients were collected and cleaned properly by using water. Ingredients were blended and turned into paste form. These pastes were boiled at a certain temperature. After boiling, the exudates were filtrated. At first, pretreatment like scouring & bleaching was carried out to remove oil, wax, natural impurities from Banana, jute blended fabrics as well as to remove the natural color & to impart a pure, permanent and basic white effect on the fabrics. This treatment was done at 100°C for 50 minutes. After this treatment, at first hot wash was done & then cold wash. Neutralization was carried out at 60°C by using acetic acid. For the pretreatment process, detergent was used at the quantity of 0.8 g/L with 0.50 g/L wetting agent and 1.50 g/L sequestering agent. In order to overcome the creasing and foaming problems, 0.70 g/L anti-creasing agent and 0.3 g/L anti-foaming agents were used. Sodium Hydroxide (NaOH) and Hydrogen Peroxide (H2O2) were used at the quantity of 3 g/L and 5 g/L respectively.
After the pretreatment process, dyeing of hybrid fabric was done. At first, the dye bath was set at 60°C. Chemicals like leveling agent, sequestering agent were entered into the dye bath nozzle. It was then kept for 30 minutes. After that, the natural turmeric sap was transferred to the dye bath nozzle. Another 30 minutes was kept to the nozzle at 60°C. Another natural sap like henna was entered into the dye bath nozzle & was kept for another 30 minutes. The dyed fabric samples were washed properly to remove the unfixed surface color. Firstly, a cold wash was done and after that hot wash was carried out. Then soaping chemical like detergent was used to wash for obtaining good fastness result. Again, the fabric was rinsed properly to make it clear. The porcess curve of Dye extraction technique is showed in and the fabric Dyeing curve is showed in the .
Color shade was found when the dyed samples were checked under a light box. The used light source was D65. All the samples were viewed keeping at 45°angle in the lightbox.
Normally synthetic dyes are used for normal dyeing in the textile field. Different shades were achieved here by dyeing with natural dyes & natural mordants. If similar shades on 100% jute fabric were achieved by synthetic dyes, reactive dyes would be used. Here Remazol Red RR, Remazol Blue RR, Remazol Yellow RR can be used to achieve similar shades of natural dyeing. Dye bath PH should be adjusted slightly acidic condition before start dyeing. Then electrolyte (glubar salt) was transferred to the dye bath to reduce electronegativity. After 20–25 minutes of hold time, linear color dosing should be carried out to the dye bath for 35–40 minutes. After that 30 min hold time was carried out for the uniform distribution of the dyes to the fabric. Then (progressive −3) soda dosing was done to the dye bath for 30–35 minutes for fixation of the synthetic dyes with the fabric. During the fixation period, the pH should be kept at 10.5 for light shade & around 10.8 for a medium shade. After shade checking, neutralization should be carried out at 60°C with 1 g/L acetic acid. Finally, hot washing with soaping chemicals should be used to remove unfixed dyes. Additional time was required to raise, lower the temperature for required operation & also for washing purposes. The full dyeing process of pretreated bleached fabric was around 4 hours up to unloading from the dyeing machine & the cost of 1 kg fabric dyeing was 1500–2000 taka considering the cost of the dyes & chemicals. But comparing with this natural dyeing which was carried out here in this article, the full dyeing process was carried out at 60°C. After the addition of natural dyes, 30 minutes hold time was carried out. Then natural mordant was applied. Here full dyeing process was carried out for 1 hr −1.30 hr with natural ingredients & the cost of dyeing was a maximum of 400–500 taka. Natural dyes & natural mordants were collected freely from the environment. The main cost was the utility purpose to raise, lower the temperature & also the use of nonionic detergent to remove unfixed dyes. The quality of the natural dyed fabric shade was good without any levelness, dye spots, crease mark & colorfastness properties were good in rating. The water after the natural dyeing was not harmful and the amount of BOD & COD was less as no synthetic dyes & chemicals were used. But these amounts are normally high for dyeing with synthetic dyes, chemicals. Dyeing textile fabric with natural dyes is environmentally friendly. So, in comparison of this natural dyeing with conventional synthetic dyeing, the dyeing cost & time are less consumed for natural dyeing as well as the good quality of the dyed fabric. Natural dyes along with natural mordants are convenient to use & also productive to get good quality in dyeing, financial and environmental point of view. Appearance of the fabric before dyeing and after dyeing are shown in the and respectively.
Results & discussion
Different tests were carried out after the preparation of jute-banana hybrid fabric & its dyeing utilized fully natural ingredients. Physical properties were evaluated to ensure the quality of the fabric. Different fastness properties were checked to confirm the dyeing quality. FTIR test was done, which illustrated the presence of the two fibers used in the hybrid fabric. Spectrophotometer readings were also measured to check out the dyeing performance as well as the wavelength in the visible spectrum.
Measurement of stiffness and thickness of hybrid fabric
Stiffness is the extent to which an object hinders deformation in response to an applied force. Here Stiffness test was performed according to ASTM D4032. Fabric thickness affects air permeability and moisture absorbency and also has a great influence on abrasion resistance. The thickness test was performed according to ASTM D1777.
The stiffness test results for the three samples are shown in . From the test results, it can be seen that sample 2 has the most stiffness among all the samples which is 4.2 N. The stiffness value of sample 1 and sample 3 were 4.0 N and 4.1 N respectively. However, the thickness test results which are shown in , indicate that sample1 has the highest thickness value of 0.56 mm. The thickness value of Sample 2 and sample 3 were 0.54 mm and 0.52 mm respectively. So it can be clearly understood that in spite of having the biggest thickness value, sample 1 has more flexibility than all other samples.
Measurement of tensile strength and tearing strength of fabric
The tensile strength of the fabric was tested according to ASTM D-638. Here UTM (Testometric) was used to calculate the tensile strength. Tear strength is the resistance of the fabric against tearing or force necessary to propagate the tear once it is initiated. The tear strength of fabric was tested according to ASTM Standard D1424 and the results are shown in the below:
Table 3. Strength test and tearing test
From these results, it can be concluded that sample 3 showed the best tensile properties among all samples. However, the result of tearing strength also showed that sample 3 had the highest tearing strength value which was 65 N. Sample 1 and sample 3 had the tearing strength of 61 N and 63 N respectively. So, the overall tensile properties of sample 3 were much higher than the other samples, where the average tear strength of the samples was 62 N.
Drape& crease recovery determination of fabric
The drape is the term that is used to depict the way a fabric hangs under its own weight. The drape of fabric was measured in the laboratory by following the standard ASTM D-3691.
Crease recovery exhibits the capability of fabric to go back to its initial state after creasing. It is specified quantitatively in terms of crease recovery angle. The test was carried out according to AATCC TM 66 in the laboratory. The test results of Drape & Crease recovery of the fabrics are shown in below:
Table 4. Drape& crease recovery test results
The average static drape coefficient for the samples was 48.56. The average dynamic drape coefficient for the samples was 53.60. Among those samples, sample 2 had the highest static drape coefficient, and sample 1 has the highest dynamic drape coefficient. So, the crease recovery of the JBHF was moderate. Among those samples, sample 3showed the highest warp and highest weft recovery angle. Moreover, the samples had a larger warp recovery angle than their weft recovery angle.
Colorfastness test
Different tests were carried out to check the fastness properties& dyeing accuracy. All the samples were tested in third-party testing company A-ONE POLAR Limited which is a sister concern of Micro Fiber group. Test name & results of different tests are provided below:
Colorfastness to washing (ISO-105-C06)
The colorfastness to wash test was according to the ISO-105-C06 method. The colorfastness to washing rating for the sample was 4.
Colorfastness to water (ISO-105-E01)
The colorfastness to water test of all the samples was carried out by the ISO-105-E01 method. A gyro wash machine was used for this purpose. Multi-fiber fabric shows that the result is good. The fastness rating for the sample was 4–5. This means the fastness rating for the sample is satisfactory.
Color fastness to rubbing (ISO-105-X12)
Colorfastness to rubbing of all the samples was carried out by the ISO-105-X12 method.
Colorfastness to perspiration (ISO-105-E04)
The colorfastness to perspiration test of the sample was tested & the test was carried out by ISO-105-E04 method. The fastness rating for the sample was 4, both in acidic & alkaline conditions. The dyed fabric was tested separately. After testing, the change in color of multi-fiber fabric for different tests for colorfastness to rubbing, perspiration, water, water test are given below, as well as the grayscale which was used to measure the fastness rating:
The multi-fiber fabric of different tests that change in color is not so much significant as the test rating was not below 3. The average colorfastness rating of all the samples is given below in :
Table 5. Fastness (wash, water, perspiration) rating of sample
From it can be seen that the colorfastness to washing and water of the dyed sample fabrics were 4 and 5 respectively. The colorfastness to perspiration using the Alkali media was 4, where the colorfastness to perspiration using the Acidic media was 4 also. The colorfastness to dry rubbing and wet rubbing was 5 and 4 respectively. All the color fastness results were within 4 − 5. So, it can be concluded that the color fastness of the fabric was good.
FTIR test
FTIR Spectroscopy is a nondestructive method for studying the physico-chemical properties of Fibrous materials. The FTIR spectrum of banana jute blended fabric is shown below. The FTIR spectrum of banana jute blended sample shows peaks at 3373–3422 cm−1 can be assigned to C-H stretching. The broad shoulder around 3950 cm−1can supports the existence of C-H stretching. FTIR spectrum shows pick at 1036–1382 cm−1 can be assigned to the existence of C-O bond. The broad shoulder around 1113 cm−1 for the sample can support the existence of the C-O bond. In the samples, FTIR spectrum picks at 1052 cm−1 can be assigned to the vibration of C-O in the alcohol hydroxyl group. FTIR spectrum shows peaks at 3854–3950 cm−1 can be assigned to the presence of O-H stretching vibration. In the sample, the FTIR spectrum peak at 3874 cm−1 which strongly indicates the presence of O-H stretching vibration& as well as the hydroxyl group & these are the functional groups of cellulose. The peaks near 1599 cm−1 and 1462 cm−1 are shown in the spectrum; they show the functional groups of lignin. The FTIR test result is shown in the .
From the aforementioned discussion, it is exhibited that there are significant resembles in physico-chemical structure of these two fibers.
Color quality checking using spectrophotometer
The Spectrophotometer is an optical instrument for quantifying the intensity of light relative to wavelength. Electromagnetic energy, amassed from the sample, enters the contrivance through the aperture and is dissevered into its component wavelengths by the holographic grating. The test result is given below in .
Uses of jute banana hybrid fabric
Jute- A banana hybrid fabric that we have made is a woven fabric. After dyeing with natural dye, it will play a vital role in green technology. Fiber sourcing was done from nature and dyeing was accomplished with natural dye. The fabric was made eco-friendly and biodegradable. This can be used as curtains, table cloths, bedsheets, floor mats, school bags and normal bags. It can additionally be used as wearable clothes and wearable sheets for the winter season. In the field of interior designing, sheets of this type of fabric are a blessing for eco-friendly decoration. Even baby shoes can be made from it. In agro textile, inside the greenhouse it can be used as covering and fencing materials but we have to keep it aloof from water without water-repellant coating. The feasibility of using the fabric was forecasted in the indoor environment only and our further plan is to check about the aforementioned items in the outdoor environment as well.
Conclusion
The banana fibers were found to be coarser, whiter, and more effulgent and contain low lignin. It was an endeavor to minimize the fineness of banana fiber, keeping copacetic spinnable properties which is a great achievement. Wastes turned to an asset for utilizing banana fiber as a textile fiber. Mundane prevailing spinning systems like Ring spinning and Rotor spinning can be acclimated to manufacture banana yarn. After blending with 100% jute yarn, all the specimens were dyed with natural dyes. The present study revealed that Jute-Banana hybrid fabric(JBHF) has copacetic physico-mechanical properties. Shade obtained from Banana jute hybrid fabric utilizing natural dyes was even in tone. The spectrophotometer test provided an illustration of the digital color measurement feature which was also satisfactory.FTIR test was done for corroboration of the presence of these two fibers in the blended fabric. In Madhu et al. (Citation2020), they reduced the hydrophilicity and obtained superior and improved physicochemical and mechanical properties in their jute composite by using chemical treatment techniques. However, in this study the hydrophilicity and colorfastness of the jute-banana hybrid fabric (JBHF) were improved by diminishing lignin, fats and wax contents. Besides, the physico-mechanical properties were also enhanced through manufacturing hybrid fabrics and chemical treatment processes.
Highlights
Banana fibre has been culled as it is a natural fibre. Ligno-cellulosic natural fibre like banana can be acclimated to manufacture union or blended fabric with mostly used jute fiber which can get immensely colossal popularity as wearable product because of the health and hygiene issues. This was an endeavor to minimize the dependency on the single fiber & find an alternative way to prepare union fabric by blending two different quality natural fibers.
Banana fibres, extracted from the sheath which can be utilized for manufacturing fiber, can diminish the pressure on the jute fibre and the availability of banana fibre is quite copacetic and it will be very frugal and ineluctably it will be a great opportunity to blend it with the other costly natural fibre like jute.
When banana fibers were treated with different chemicals like alkali and peroxide, during the removable of bark and other impurities, considerable weight loss was observed. The fineness of representative raw banana fibers was determined by using USTER HVI 1000. Spinnable properties like length, strength, fineness, tenacity, color, and elongation at break etc. were found for yarn manufacturing and a suitable method was found to manufacture yarn.
Natural ingredients like hena leaves & turmeric were used. Extraction of dye was done first from natural ingredients. Different tests(such as Stiffness, Thickness, Tensile Strength, Tearing Strength, Drape, Crease recovery and Colorfastness Tests) were carried out after the preparation of jute-banana union fabric & its dyeing was done with fully natural ingredients. FTIR test also provided the confirmation of these used two fibres & spectrophotometer was used to illustrate the dyeing quality.
If banana fibre can be acclimated to manufacture yarn and fabric so that sizably voluminous quantity of natural fibre can be amassed from nature which can be blended with jute fibre. It was an endeavor to minimize the fineness of banana fibre keeping copacetic spinnable properties which is a great achievement. It will truncate pressure on the cultivation and availability of jute fibre withal.
References
- Banks‐Lee, P., and J. Pegram. 2011. Kirk‐Othmer Encyclopedia of Chemical Technology. 5th ed. New Jersey: John Wiley & Sons, Inc.
- Das, P. K., D. Nag, S. Debnath, and L. K. Nayak. 2010. Machinery for extraction and traditional spinning of plant fibers. Indian Journal of Traditional Knowledge 9:386–93.
- Dwivedi, A. K., M. W. Dalzell, S. A. Fossey, K. A. Slusarski, L. R. Long, and E. D. Wetzel. 2016. Low velocity ballistic behavior of continuous filament knit aramid. International Journal of Impact Engineering, 96(1): 23–34
- Eyerer, P., and V. Gettwert. 2010. Polymers-Opportunities and Risks I. 1st ed. Berlin: Springer.
- Ghorpade, R., and R. H. Balasubramanya. 2013. Microbial retting of banana pseudostem for extracting textile grade fibers and its applications. Man-Made Textiles in India 41 (5):149–53.
- Koohestani, B. A. B. A. K., A. K. Darban, P. Mokhtari, E. R. O. L. Yilmaz, and E. S. M. A. E. E. L. Darezereshki. 2019. Comparison of different natural fiber treatments: A literature review. International Journal of Environmental Science and Technology 16 (1):629–42. doi:10.1007/s13762-018-1890-9.
- Kumar, R., V. Choudhary, S. Mishra, and I. K. Varma. 2008. Banana fiber-reinforced biodegradable soy protein composites. Frontiers of Chemistry in China 3 (3):243–50. doi:10.1007/s11458-008-0069-1.
- Madhu, P., M. R. Sanjay, P. Senthamaraikannan, S. Pradeep, S. Siengchin, M. Jawaid, and M. Kathiresan. 2020. Effect of various chemical treatments of prosopis juliflora fibers as composite reinforcement: Physicochemical, thermal, mechanical, and morphological properties. Journal of Natural Fibers 17 (6):833–44. doi:10.1080/15440478.2018.1534191.
- Mohiuddin, A. K. M., M. K. Saha, M. S. Hossian, and A. Ferdoushi. 2014. Usefulness of Banana (Musa paradisiaca) wastes in manufacturing of bio-products: A review. The Agriculturists 12 (1):148–58. doi:10.3329/agric.v12i1.19870.
- Pujari, S., A. Ramakrishna, and M. S. Kumar. 2014. Comparison of jute and banana fiber composites: A review. International Journal of Current Engineering and Technology 2 (2):121–26. doi:10.14741/ijcet/spl.2.2014.22.
- Sisti, L., G. Totaro, M. Vannini, and A. Celli. 2018. Lignocellulosic composite materials. 1st ed. Cham: Springer.
- Subagyo, A., and A. Chafidz. 2018. Banana nutrition-function and processing kinetics. 1st ed. London: IntechOpen.
- Sudhakara, P., D. Jagadeesh, Y. Wang, C. V. Prasad, A. K. Devi, G. Balakrishnan, and J. I. Song. 2013. Fabrication of Borassus fruit lignocellulose fiber/PP composites and comparison with jute, sisal and coir fibers. Carbohydrate Polymers 98 (1):1002–10. doi:10.1016/j.carbpol.2013.06.080.