ABSTRACT
Cochineal is employed in the field of cosmetics, food, textile, and flavors. The use of cochineal in textile goes back an ancient times in Mexico. These dyes have been used in different natural fibers. After the first quarter of the sixteenth century, cochineal was brought from Mexico to Europe and Asia. Since this date, it has been used very quickly and widely in Europe and Asia. The dye is used as a natural dye all over the world nowadays. Today, the dye is usually dyed with traditional methods. Cochineal is an important natural dye resource for red colors. The use of cochineal has come to importance in the textile industry for the red color in recent years. Cochineal has not been used as an economical, sustainable, and mass production in the textile industry up to now. This study has provided economical, sustainable, and industrial-scale production in the cotton textile industries. Cochineal dyeing recipes were created on industrial-scale samples by the jet dyeing machines. Color change, washing, rubbing fastness 4–5, and lightfastness found 4–5. The optimum conditions were determined for dyeing by the jet dyeing machine. According to the optimum dyeing recipe, cotton fabric was dyed with cochineal.
摘要
胭脂虫油应用于化妆品、食品、纺织品和香料领域。胭脂虫在纺织品中的使用可以追溯到远古时期的墨西哥. 这些染料已用于不同的天然纤维中. 16世纪前25年后, 胭脂虫从墨西哥传入欧洲和亚洲. 自那时以来, 它在欧洲和亚洲得到了迅速和广泛的应用. 这种染料现在在世界各地都被用作天然染料. 今天, 染料通常用传统方法染色. 胭脂虫是一种重要的红色天然染料资源. 近年来, 胭脂虫因其红色在纺织工业中的应用变得非常重要. 到目前为止, 胭脂虫还没有作为一种经济、可持续和大规模生产的药物在纺织工业中使用. 本研究为棉纺织行业提供了经济、可持续和工业规模的生产. 胭脂虫染色配方是通过喷射染色机在工业规模的样品上创建的. 变色、洗涤、摩擦牢度4-5, 以及发现的耐光性4-5. 确定了喷射染色机染色的最佳条件. 根据最佳染色配方, 用胭脂虫对棉织物进行染色.
Introduction
Cochineal was derived from the dried bodies of females of the Dactylopius coccus Costa insects and used for the coloration of textile fibers as a red dye. This natural dye presents good light stability. Its color varies from orange to red, depending on the pH (Blyskal Citation2015; Borges et al. Citation2012). Natural dye sources used different fibers (Benli, Citation2020; Deveoğlu et al. Citation2013; Kyung-Hee et al. Citation2014). Over 700 dye plants can be used for natural dyeings in the World (Karadag Citation2021). The dye source of them is cochineal.
There are many works about protein fibers (silk, wool, etc.) dyed with cochineal or carminic acid. Wool fabric was dyed with cochineal extract by microwave irradiation (Adeel et al. Citation2019). Microwave-assisted extraction of colorant from cochineal for dyeing of bio-mordanted silk has been carried out (Amin et al. Citation2020). Silk fabrics were dyed with cochineal and gall oak (Şahinbaşkan, Karadag, and Torgan Citation2018) for red and purple colors. Cochineal and chitosan were used in the cotton fabric dyeing.
Cochineal had been used in the dyeing of many historical textiles for red and purple colors (Kahraman and Karadag Citation2017; Karadag et al. Citation2015; Karapanagiotis and Karadag Citation2015; Karapanagiotis et al. Citation2008; Katarzyna et al. Citation2015).
In this study, bleached cotton is dyed with cochineal, gall oak bio mordant, calcium mordant, and alum mordant as sustainable industrial-scale production. Different mordant matters (alum, calcium and gall oak) and dye concentration were applied in these dyings by the just-in-time extraction, complex formation dyeing, and fixing method.
Material and method
Material
Dye plant and chemicals
Cochineal and guar gum (C10H14N5Na2O12P3) were provided from Natural Dyes Doğal Boya Hammaddeleri San.ve Dış Tic. Ltd. Şti. Turkey. Turkey. Coloring compounds reference standards and chemicals were provided by DATU Cultural Heritage Preservation and Natural Dyes Laboratory in Istanbul, Turkey. Knitting cotton fabric was used and the weight of the fabric was 230 g/m2. The following coloring compounds standards were used as references: Carminic acid from Carl Roth (Karlsruhe, Germany). Additionally, alum [KAl(SO4)2.12H2O], hydrochloric acid (HCl), methanol (CH3OH), acetonitrile (CH3CN), and trifluoroacetic acid (CF3COOH) from Merck, flavokermesic acid was provided by Prof. Mohammad S. Mubarak in the INCO CT 2005 015406 MEDCOLOUR-TECH Project, H2O2, Ca(NO3)2.2H2O, NaOH, citric acid, and Na2CO3, from Balmumcu Kimya San. Tic. Ltd. Şti. Turkey was used.
Bleaching
A standard bleaching process was used. Desized and scoured cotton fabrics were immersed in their bleaching solutions. Each bleaching solution contained a nonionic wetting agent (1 g/L), 30% H2O2 (5 g/L), and an alkali [(NaOH) (2 g/L)]. The process took place at 70 degrees and 60 minutes. At the end of the bleaching process duration, the bleached samples were washed thoroughly with hot water and then cold water then dried (Karadag Citation2021). Bleaching imparts cationic and hydrophilic properties to the fabric. The dyestuff is dyeing more efficiently and strong bound in the cationic fabric.
Dyeing
Ten samples and industrial-scale bleached cotton fabrics, which had different percentages of alum, gall oak, cochineal, and calcium nitrate were used for dyeings and fixing with guar gum in industrial sample jet dyeing machines. 25 kilograms of bleached cotton fabric was used for each sample dyeing. 500 kilograms of the same bleached cotton fabric was used for industrial-scale dyeing. Dyeing's pH has buffered with citric acid in 6.0–7.0. These dyeing processes were given in .
Table 1. Dyeing parameter, according to the percentages of alum, Ca(NO3)2, gall oak and cochineal.
In addition, the number 3 recipe was selected optimum recipe (). 0.3% cochineal, 0.3% gall oak, 0.03% calcium nitrate, 0.075% alum and 0,03% guar gum were used for sustainable industrial-scale production. Just in time dyeing [extract, complex formation, and dyeing together (synchronous dyeing)] method used in the sample jet dyeing machine and large-scale production. Before an extraction unit was modified to jet dyeing machines for extraction and complex formation. Ground cochineal, gall oak, alum, and calcium nitrate were added to the extraction unit. Together cochineal, gall oak, calcium nitrate, and alum were extracted for 15 minutes at 30°C. The extract was slowly dosage to the dyeing machine. Extraction, formation complex, and dyeing continued simultaneously (as synchronous) throughout the dyeing. As a gradient, extraction and dyeing temperatures increased to 80°C. Then temperature has been decreased to 50°C, and guar gum (0.003 g/L) was added for fixing. Fixing continued at 50°C for another 30 minutes. Then, soup add and the temperature was increased to 60°C. Washing was done for 20 minutes at 60°C. Finally, the dyed cotton fabric was rinsed and dried. The extraction, formation complex, dyeing, and fixing processes are given in .
HPLC analysis (high-performance liquid chromatography)
HPLC instrumentation
Chromatographic measurements were carried out using an Agilent 1200 series system (Agilent Technologies, Hewlett-Packard, Germany). The analytical protocol and elution program are given in the previous studies (Karadag Citation2021). (Karadag, Buyukakinci, and Torgan Citation2022). Gallic acid, carminic acid, ellagic acid, and flavokermesic acid were identified in the dyed fabric ().
Figure 2. (a) Chromatograms of the dyed fabrics, (b) spectra of 6.252 RT (black line) and spectra of gallic acid (red line) (c) spectra of 16.143 RT (black line) and spectra of carminic acid (red line), (d) spectra of 17.402 RT (black line) and spectra of ellagic acid (red line), (e) spectra of 26.039 RT (black line) and spectra of flavokermesic acid (red line).
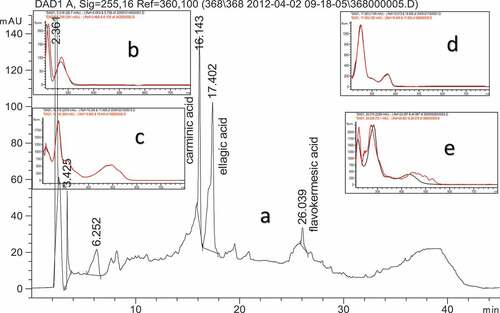
Color measurement
Konica Minolta CM-2300d Software Spectra Magic NX (6500 K, 10°) was used for color measurement (Karadag, Buyukakinci, and Torgan Citation2022). CMC, L*, a*, b*, and K/S values are shown in .
Fastness properties
The washing, rubbing, and light fastnesses of 10 dyed fabrics and large-scale production were determined according to ISO105: C06 (A1S), ISO105-E04, ISO105-X12, and ISO105-B02 standards, respectively. The ISO 105:C06 A1S fastness test was carried out at 40°C for 30 min containing 10 steel balls. The dyed samples were exposed to the light for 48 h from a xenon arc lamp (250 W). The lightfastness, washing, and rubbing values of the dyed fabrics are given in .
Table 2. Fastness properties of cochineal (Dactylopius coccus Costa).
SEM-EDX analysis
The untreated cotton fabric and dyed cotton fabric were analyzed by Scanning Electron Microscope equipped with Energy Dispersive X-ray Spectrometer (SEM-EDX) for surface imaging analysis with a secondary electron (SE) detector. The analytical protocol is given in
the previous study (Karadag Citation2021). Surface images and elemental analysis are given in .
Result and discussion
The coloring compounds of the cochineal are a major quantity of carminic acid and a trace amount flavokermesic acid. The coloring compound (carminic acid) is soluble in the water. But the coloring compound (carminic acid) is more soluble in the alum aqueous solution than in the water.
Carminic acid has formed a complex with aluminum ions. The complex of aluminum-carminic acid formed in the extraction unit. But aluminum-carminic acid complex is not a strong complex. The formed aluminum-carminic acid complex is formed into a new very strong complex with calcium ions (). The complex formed in the extraction unit through dyeing and bound to the cotton fabric during dyeing. Instead of complexes that bind to the cotton fabric, carminic acid continuously dissolves from the cochineal.
Gall oak was dissolved in the extraction unit. The main components of gall oak are gallic acid and ellagic acid. The components are very strong cationic binders in the cotton dyeing process. The natural fixing agent provides the depth of color. This dissolution continues until the complete dissolution of carminic acid from cochineal, and gallic acid and ellagic acid from the gall oak. The maximum amount of dyestuffs was extracted from the cochineal and gall oak by this method.
Carminic acid, flavokermesic acid, gallic acid, and ellagic acid, were detected in the dyed fabric. Carminic acid has five dissociation constants, and the constants values are pKa1:3.39; pKa2:5.78; pKa3: 8.35; pKa4:10.27, and pKa5:11.51. This ligand behaves as a bi-dentate ligand, and the carboxyl and the ortho hydroxy groups of the ligand coordinate with the metal ions (Mihail and Craciun Citation1970). Accordingly, it can be assumed that the coordination of carminic acid with the metal ion occurs via the carboxylic group and the hydroxy group to form complexes. Intrahydrogen bonding between the hydrogen of the carboxylic group and the oxygen of the hydroxy group is expected to take place within the ligand molecule in solution. The low dissociation constant of the carboxylic group in the carminic acid will encourage intrahydrogen bonding, but it is not expected that such bonding will cause significant obstruction to the coordination of the ligand with the metal ion or ions.
Metal (M): Ligand (L) ratio. [M:L (Al: carminic acid)] is 1:2. The carminic acid-aluminum, aluminum-carminic acid-calcium, and structural complexes have been found in various previously published articles (Dapson Citation2007; Gabrielli et al. Citation2018; Šuleková et al. Citation2017).
The carminic acid first dissolves from the cochineal. First, the carminic acid forms a complex with Al3+ ions and after then too strong complex with Ca2+ ions. The coloring compounds were extracted from the dye sources (cochineal and gall oak) and the aluminum-carminic acid-calcium complex () was formed during the dyeing, and the complex was bound to the cotton fabric via gallic acid and ellagic acid during the dyeing (as synchronous). Thus, the complex was formed for a long time (throughout dyeing). The alum-carminic acid-calcium complex and extract of gall oak (gallic acid and ellagic acid) were dosed for a long time. At the same time, both dyeing and complex started at low concentrations and low temperatures. Because the temperature has been increased as a gradient, the complex was slowly formed from the cochineal extraction and the cotton fabric was slowly dyed. This process continues until the dyestuffs are completely dissolving from the cochineal and gall oak.
The dye liquor ratio is too high in traditional dyeing conditions. The dye liquor ratio is not suitable for sustainable and industrial-scale production by nowadays-textile machines. The machine was designed and developed for a low dye liquor ratio. Thus, a low dye liquor ratio provided high dye concentration, low water consumption, low energy consumption, and low wastewater. It is problematic to start dyeing at high dye concentrations and high temperatures. Unevenness dyeing is a very important problem in industrial-scale productions (Karadag Citation2021). Therefore, cotton fabric dyeing started with low aluminum-carminic acid-calcium complex concentration and low temperature. The SEM images and elemental analysis of dyed fabric and undyed fabric are shown in . It was observed that the fibers dyed with aluminum-carminic acid-calcium complex dye retained their structures without any damage after the dyeing processes. 0.02% aluminum and zero calcium were detected in the undyed fabric. But 0.07% aluminum and 0.18% calcium were detected in the dyed fabric. Silicone arises from standard bleaching and the finishing process.
It is normal for the color values to differ depending on the recipe in dyeing. Which color value is better depends on the consumer. That is, the color preference differs from person to person. Therefore, all recipes can be used for industrial dyeing. In the work, guar gum was used as a stabilizer in dyeing cotton fabrics with cochineal. Guar gum, also called guaran, is a galactomannan polysaccharide extracted from guar beans that has thickening and stabilizing properties useful in food, feed, and industrial applications (Thombarea et al. Citation2016).
The color change values of the samples after the washing, light-fastness, and rubbing fastness tests in general, were found to be 4–5 in grayscale rating. The color fastness values of dyed samples to the light of cochineal were found to be 4–5 in blue-scale rating. Fastness values are high in wool and silk dyeings with weld. But generally, the fastness values are low in dyeing the cotton with cochineal. With this method, the fastness values in cotton dyeing were increased. Fastness properties are moderately or low in the cotton dyeing with cochineal (Arroyo-Figueroa et al. Citation2010; Ke, Kundi, and Chowdury Citation2021). The method has increased all fastness properties.
Conclusion
Cochineal dye insect was used in the industrial-scale sample jet dyeing machines for cotton fabric dyeing. Ten dyeing recipes were created using 0.025%, 0.05%, 0.075%, 0.10%,0.125%, 0.15%, 0.175%,0.20%,0.225, and 0.25 proportions of alum; 0.1%, 0.2%, 0.3%, 0.4%, 0.5%, 0.6%, 0.7%,0.8%, 0.9% and 0.1.0% proportions of gall oak; 0.01%, 0.02%, 0.03%, 0.04%, 0.05%, 0.06%, 0.07, 0.08%, 0.09%, and 1.0% proportions of calcium nitrate mordant and 0.1%, 0.02%, 0.3%, 0.4%, and 0.5% proportions of cochineal dye insect in different combinations (). All the cochineal recipes have features that can be used for pink and red dyeings. However, in industrial-scale dyeing, the selected optimum recipe (0.3% cochineal, 0.3% gall oak, 0.03 calcium nitrate, and 0.075% alum) was used.
Considering the Ca-carminic acid-Al [Ca(C22H20O13)2Al] reaction, alum and calcium mordant percentages were calculated according to carminic acid (15% – % 30) content in the cochineal ( dyeing numbers 3 and 11). The calculation was made without taking kermesic acid into account. Because the amount of kermesic acid is negligible.
This recipe has preferred because it is more economical in large-scale production. The color values and fastness (washing, light, and rubbing) tests of all recipes are very good for natural pink dyes in cotton dyeing. Less quantity cochineal, less quantity gall oak, less quantity calcium salt, and less quantity alum were used and more color yield was obtained. Gall oak is a good cationic agent and guar gum is a good stabilizer for cochineal dyed cotton fabrics. If an extraction unit is added to a jet dyeing machine or any dyeing machine, natural dyes can also be used for sustainable industrial-scale such as synthetic dyes.
Color is relative and each consumer’s and each fashion clothing industry’s color preference is different. Thus, each of these ten cochineal dyeing recipes can be used for pink colors.
Dyeing proceeds in a controlled manner by just in time dyeing method. A complex is formed with alum and calcium as much as the amount of extract (carminic acid). They formed complex bonds to the cotton fabric. This cycle goes on continuously until the extract (carminic acid) runs out. Since the initial and all during, dyeing the dye concentration is very low in this method, unevenness does not occur in dyeing.
Based on this dyeing method, it will shed light on more controlled dyeings with new algorithms so that natural dyeing can be much more used in industrial dyeing.
Disclosure statement
No potential conflict of interest was reported by the author(s).
References
- Adeel, S., M. Hussaan, F. Rehman, N. Habib, M. Salman, S. Naz, N. Amin, and N. Akhtar. 2019. Microwave-assisted sustainable dyeing of wool fabric using cochineal-based carminic acid as natural colorant. Journal of Natural Fibers 16 (7):1026–11. 10.1080/15440478.2018.1448317.
- Amin, N., F. Rehman, S. Adeel, T. Ahamd, M. Muneer, and A. Haji. 2020. Sustainable application of cochineal-based anthraquinone dye for the coloration of bio-mordanted silk fabric. Environmental Science and Pollution Research 27 (7):6851–60. 10.1007/s11356-019-06868-3.
- Arroyo-Figueroa, G., G. M. L. Ruiz-Aguilar, G. Cuevas-Rodriguezc, and G. Gonzalez-Sanchez. 2010. Cotton fabric dyeing with cochineal extract: Influence of mordant concentration, Coloration Technology. Color Technologies 127:46. 10.1111/j.1478-4408.2010.00276.x.
- Benli, H 2020 . Coloration of cotton and wool fabric by using bio-based red beetroot (Beta Vulgaris L. Journal of Natural Fibers in Press. doi:10.1080/15440478.2020.1848725.
- Blyskal, B. 2015. Fungal deterioration of a woolen textile dyed with cochineal. Journal of Cultural Heritage 16 (1):32–39. 10.1016/j.culher.2014.01.008.
- Borges, M. E., R. L. Tejera, L. Diaz, P. Esparza, and E. Ibanez. 2012. Natural dyes extraction from cochineal (Dactylopis coccus). New extraction methods. Food Chemistry 132 (4):1855–60. 10.1016/j.foodchem.2011.12.018.
- Dapson, R. 2007. The history, chemistry and modes of action of carmine and related dyes. Biotechnic & Histochemistry 82 (4–5):173–87. 10.1080/10520290701704188.
- Deveoğlu, O., G. Erkan, E. Torgan, and R. Karadag. 2013. The evaluation of procedures for dyeing silk with buckthorn and Walloon oak on the basis of colour changes and fastness characteristics. Coloration Technology 129 (3):223–31. 10.1111/cote.12023.
- Gabrielli, L., D. Origgi, G. Zampella, L. Bertini, S. Bonetti, G. Vaccaro, F. Meinardi, R. Simonutti, and L. Cipolla. 2018. Towards hydrophobic carminic acid derivatives and their incorporation in polyacrylates. Royal Society Open Science 1–11. 10.1098/rsos.172399
- Kahraman, N., and R. Karadag. 2017. Characterization of sixteenth to nineteenth century ottoman silk brocades by scanning electron microscopy–energy dispersive x-ray spectroscopy and high-performance liquid chromatography. Analytical Letters 50 (10):1553–67. 10.1080/00032719.2016.1236264.
- Karadag, R. 2021. Sustainable and mass production of cotton dyeing with natural dye (weld) in the textile industry. Journal of Natural Fibers 1–11. in press 10.1080/15440478.2021.2002781
- Karadag, R., B. Y. Buyukakinci, and E. Torgan. 2022. Extraction and natural cotton dyeing of valonia oak and anatolian buckthorn by microwave irradiation. Journal of Natural Fibers 19 (1):159–72. 10.1080/15440478.2020.1731907.
- Karadag, R., T. Torgan, T. Taskopru, and Y. Yıldız. 2015. Characterization of dyestuffs and metals from selected 16–17th-century ottoman silk brocades by RP-HPLC-DAD and FESEM-EDX. Journal of Liquid Chromatography & Related Technologies 38 (5):591–99. 10.1080/10826076.2014.922476.
- Karapanagiotis, I., and R. Karadag. 2015. Dyes in post-byzantine and ottoman textiles: a comparative hplc study. Mediterranean Archaeology and Archaeometry 15(1):177–89. dio.org. doi:10.5281/zenodo.15052.
- Karapanagiotis, I., A. Lakka, L. Valianou, and Y. Chryssoulakis. 2008. High-performance liquid chromatographic determination of colouring matters in historical garments from the holy mountain of athos. Microchimica Acta 160(4):477–83. Dio.org. doi:10.1007/s00604-007-0774-4.
- Katarzyna, L., W. Katarzyna, B. Wileńska, Jarosz, and M. Jarosz. 2015. Identification of unknown colorants in pre-Columbian textiles dyed with American cochineal (Dactylopius coccus Costa) using high-performance liquid chromatography and tandem mass spectrometry. Analytical and Bioanalytical Chemistry 407(3):855–67. dio.org. doi:10.1007/s00216-014-8107-y.
- Ke, G., Z. Kundi, and C. H. Chowdury. 2021. Dyeing of cochineal natural dye on cotton fabrics treated with oxidant and chitosan. Journal of Natural Fibers 18 (3):317–29. 10.1080/15440478.2019.1623742.
- Kyung-Hee, P., K. Tae-Young, H. Shin, K. Hyun-Seok, L. Suk-Ho, S. Yong-Min, K. Jung-Hun, and L. Jae-Wook. 2014. Light harvesting over a wide range of wavelength using natural dyes of gardenia and cochineal for dye-sensitized solar cells. Spectrochimica Acta. Part A, Molecular and Biomolecular Spectroscopy 128:868–73. doi:10.1016/j.saa.2014.03.016.
- Mihail, N., and C. Craciun. 1970. Effect of cochenille on Jensen tumors. Naturwessenschaften 57 (10):500–06. doi:10.1007/BF00593091.
- Şahinbaşkan, B. Y., R. Karadag, and E. Torgan. 2018. Dyeing of silk fabric with natural dyes extracted from cochineal (Dactylopius coccus Costa) and gall oak (Quercus infectoria Olivier). Journal of Natural Fibers 15 (4):559–74. doi:10.1080/15440478.2017.1349708.
- Šuleková, M., M. Smrčová, A. Hudák, M. Heželová, and M. Fedorová. 2017. Organic colouring agents in the pharmaceutical industry. Folia Veterinaria 61 (3):32–46. 10.1515/fv-2017-0025.
- Thombarea, N., U. Jha, S. Mishra, and M. Z. Siddiqui. 2016. Guar gum as a promising starting material for diverse applications: A review. International Journal of Biological Macromolecules 88:361–72. doi:10.1016/j.ijbiomac.2016.04.001.