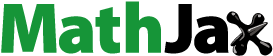
ABSTRACT
In the current work, the experiments on Careya Arborea (CA) fiber have been carried out for physio-chemical properties, thermal properties, and other characteristics. The chemical composition of CA fiber has been identified with rich content of cellulose (71.17%), lignin (14.95%), hemicellulose (27.86%), small amount of wax (0.18%) and ash (0.78%). CA fiber crystallinity index of 85.05% with crystalline size 7.40 nm is seen from XRD analysis. The surface morphology and roughness of the CA fiber have been investigated using scanning electronic microscopy and found an average diameter of 28 nm, Atomic force microscopy (AFM) with an average surface roughness of 33.458 nm and Energy dispersive X-ray micro analyzer to confirm the element configuration. Thermal properties of CA fiber were also measured by Thermogravimetry analysis and Differential scanning calorimeter analysis. The results showed the thermal stability of upto 248°C and degradation temperature of 385°C which is suitable for polymer composite fabrication. The chemical functional groups available in CA fiber were identified by FTIR. The density of the CA fiber was 1140 kg/m3 which is lower than the existing fibers and exhibited respectable tensile properties. The results were compared with latest natural fibers to discern the versatility in various applications such as aerospace, automotive and automobile industries.
摘要
在目前的工作中,对Careya Arborea(CA)纤维的理化性能、热性能和其他特性进行了实验. CA纤维的化学成分中含有丰富的纤维素(71.17%)、木质素(14.95%)、半纤维素(27.86%)、少量蜡(0.18%)和灰分(0.78%). XRD分析表明CA纤维结晶度指数为85.05%,结晶尺寸为7.40 nm. 使用扫描电子显微镜对CA纤维的表面形貌和粗糙度进行了研究,发现平均直径为28 nm,原子力显微镜(AFM)的平均表面粗糙度为33.458 nm,并使用能量色散X射线显微分析仪对元素结构进行了确认. 通过热重分析和差示扫描量热分析测定了CA纤维的热性能. 结果表明,热稳定性高达248°C,降解温度为385°C,适合于聚合物复合材料的制备. 通过FTIR鉴定了CA纤维中可用的化学官能团. CA纤维的密度为1140 kg/m3,低于现有纤维,并表现出良好的拉伸性能. 将结果与最新的天然纤维进行比较,以了解其在航空航天、汽车和汽车工业等各种应用中的多功能性.
1. Introduction
The pollution and global warming levels due to current utilization of non-biodegradable materials, petrochemicals are creating harmful effect on environment. Aesthetics of petrochemical products are more attractive, but they are non-biodegradable. The researchers are looking for alternative materials with green effects (Khalid and Arif Citation2022). Nature is the main source of human life on Earth, and it always gives the solution to the issues. From the past few years, awareness and applications of natural fibers have been exponentially increased due to their suitability and replaceable properties (Khalid et al. Citation2021). Researchers also suggested hybridization of natural materials with polymers for various application of automotive, building construction and aerospace (Arif et al. Citation2022; Jawaid and Abdul Khalil Citation2011; Khalid et al. Citation2021; Lauchlin and Thomas Citation2012; Peças et al. Citation2018). There are many varieties of applications due to their extensive properties such as low density, availability, cost effectiveness, good thermomechanical properties and eco-friendly with environment i.e biodegradable in nature(Madhu et al. Citation2019; Rangappa and Siengchin Citation2022; Sanjay and Siengchin Citation2021; Senthamaraikannan et al. Citation2016). The existing synthetic fibers and polymers are not biodegradable and eco-friendly. To overcome this issue natural fibers are the best possible alternative, and researchers were suggested variety of natural fibers such as hemp, sisal, jute, cocknut, bamboo, banana, palf, and various leaf fibers and root fibers (Indran, Edwin Raj, and Sreenivasan Citation2014; Jayaramudu et al. Citation2011; Maran et al. Citation2020; Nagaraja Setty et al. Citation2020; Sanjay et al. Citation2016; Vinod et al. Citation2020). The identification and extraction of natural fiber are one of the most significant steps in fiber-making process and it was available to plants, trees and different crops, and also can be extracted from bark, stem, root, leaf, seeds and fruits (Darder, Aranda, and Ruiz-Hitzky Citation2007; Sanjay et al. Citation2018). These fibers have their unique dimensions and good surface structure arrangement of the cellulose (Kathiresan et al. Citation2016; Khalid et al. Citation2021). The various natural fibers and their application based on their strength, interfacial bonding and surface roughness properties, and the effectiveness of the composite material depend on the selection of resins and process used (Khalid et al. Citation2021; Manimaran et al. Citation2020; Reddy and Whan Rhim Citation2018; Saravanan and Gnanavel Citation2020). Based on literature and researcher’s data these natural fibers consist of various other elements or constituents like cellulose, hemicellulose, wax, pectin and lignin (Manimaran et al. Citation2019; Sanjay et al. Citation2018, Citation2019). To remove the additional constituents in the fiber and to smoothen the surface of the fiber, various chemical treatments were carried out (Bright et al. Citation2021; De Rosa et al. Citation2011; Hyness et al. Citation2018; Njuguna and Pielichowski Citation2004; Sarikanat et al. Citation2014). Natural fibers were very good to reinforcing with various polymers, so here the understanding of the composite properties was important and as well as a greater number of varieties of fiber exploration are mandatory to create healthy environmental (Kim, Dutta, and Bhattacharyya Citation2018; Manimaran et al. Citation2019). The study aims to understand the various properties of Careya arborea (CA) fiber, and compare CA fibers anatomy, mechanical properties, chemical properties, and thermal properties with the other fibers. According to researcher knowledge, the bark fiber of CA as novel fiber studies for the first time into the literature. From the experimental data it was observed that CA fiber is good reinforcement for the polymer matrix composites.
2. Materials and methodology
2.1 Extraction of careya arborea fiber
Careya arborea (CA) natural cellulose fiber was collected from “Banjeeru village, Meliyaputti mandalam, Srikakulam district of coastal region of Andhra Pradesh, India”. Careya arborea tree is deciduous tree, it can grow up to 10 to 15 m height and it has flowers of light yellow with the combination of red color. The Careya arborea fiber were extracted from the bark of the CA tree, washed with water and the bast strips were retted for 14 days in a container clean water at room temperature. After 14 days, CA fibers were washed eight times and combed and removed the unwanted ingredients from the CA fiber surface. Later, CA fibers were dried in natural sunlight for 60 hours to remove the volatile contended water and dirt. The CA fiber extraction process is shown in .
2.2 Characterization of CA fiber
2.2.1 Tensile and single fiber pull-out tests
The anatomy of the bast fiber of careya arborea had been examined using Radical scientific equipment polarized microscope, Estimation of maximum tensile strength of the CA single fiber measured with the help of Zwickroell Universal testing machine according to ASTM D3822 standard, Tensile strength of CA fiber was tested with 80 mm of gauge length of individual fiber and at the RPM of 5 mm/min is the speed of the crosshead used for the experiment. The experiment was conducted under the ambient conditions at 28 degree C with relative humidity condition of 81%. The CA fiber micro fibrill angle is measured in EquationEquation (1)(1)
(1) (Indran, Edwin Raj, and Sreenivasan Citation2014)
In above equation (ε) represents the total strain or deformation of the CA fiber, here is the fibril angle, Lo is the total gauge length in (mm) and change in length indicating with Δ L. The properties of the fiber may vary with respective the plant age, climatic conditions, fiber extraction method, ambient testing conditions and the irregular diameter of the fiber bundle. The very important aspect is that to findthe appropriate values of the tensile properties with help of statistical analysis. However, many researchers followed the Weibull distribution method to calculate the tensile properties of various natural cellulose fibers, based on this procedure authors carry their analysis using Minitab software (Belouadah, Ati, and Rokbi Citation2015).
2.2.2 Determination of chemical composition of CA fiber
The primary chemical composition (Cellulose, lignin, ash, pectin, hemicellulose, moisture, and wax) of the CA fiber was estimated with help of standard procedural steps (Segal et al. Citation1952) and the main objective of the chemical analysis is to understand the quantitative elemental content percentage of CA fiber. The cellulose content of the CA fiber apprised according to Sanjay et al. (Citation2018)
2.2.3 Fourier transform infrared spectrometer (FTIR)
With the help of SHIMADZU-8400S spectrometer instrument Fourier transform infrared (FTIR) analysis was conducted, the characterization expressed the information about different types of chemical groups and compounds presented in the CA fiber. To perform the FTIR characterization CA fiber converted as power form and it mixed with Potassium bromide with appropriate ratio, then the pellets were prepared by using hydraulic press pellet maker. The FTIR spectra data was recorded in the range of 4000–400 cm−1 with 10 scans per minute and the resolution of 4 cm−1.
2.2.4 X-ray powder diffraction (×RD)
The crystallinity index of CA Fiber calculated with the aid of X-Ray diffraction techniques, and it brings out the complete inculcation of crystallographic, physical properties of the CA fiber. The Powdered CA fiber was analyzed with SHIMADZU XRD 7000, the operating conditions of X-ray tube intensity of Cu wavelength of 0.154 nm. The operating scanning range was 10° to 80° (2 θ) with the step size of 0.02°. Based on X-ray diffraction the crystalline index (CI) in the CA fiber is determined according to peak height techniques given by the Segal analytical equation (Segal et al. Citation1959).
Wherein the above equation, I200 is the Maximum intensity to 58 lattice planes at 2θ angle between 10° to 80° and IAM is the amorphous material phase calculated by height of the maximum peaks no 7, 2θ is the 22.005° (Indran, Edwin Raj, and Sreenivasan Citation2014).
Where the Sherror’s constant (K) = 0.89, wavelength of the radiation (λ) = 1.54178 nm, and β is the full width half maximum in degree according to Bragg angle.
2.2.5 Thermo-gravimetry analysis (TGA)
Thermo-gravimetry analysis (TGA) predicts the thermal degradation of the cellulose fiber weight lossd, analysis carried out using Model SMHADZU-DTG 60 H and this equipment consists of furnace with aluminum crucible slot for sample loading and heating with precision balancing. The temperature of the sample raises progressively for the over a period up to 840.00°C with temperature Ramp of 20.00°C/min. Also, to maintain furnace ambient condition, pure N2 gas was supplied with rate of 20 ml/min (Manimaran et al. Citation2016).
2.2.6 Differential scanning calorimeter (DSC)
The DSC analysis on CA fiber was performed on DSC Q20 V24, TA Instruments India, the heating rate was 10°C/min a temperature range from25° to 400°C. The sample loaded in aluminum pans with the ambient nitrogen gas conditions up to heating and melting of the fiber peak.
2.2.7 Surface morphology of CA fiber by scanning electron microscopy
The Scanning electron microscopy (SEM) analysis of CA fibers was performed using HITACHI S-3700N electron microscope examine the surface with Resolution in BSE Imaging in Low vacuum mode at 4.0 nm, electron beam potential (Accelerating voltage) 0.3 to 30kV at ambient room conditions.
2.2.8 Atomic force microscopy (AFM)
Atomic force microscopy (AFM) apprises the characteristics of surface roughness and standard information of average surface roughness-(Ra), Root mean square roughness-(Rq), Different point average surface roughness-(Rz), Skewness-(Rsk), Kurtosis-(Rku) and it shows the maximum peak-to-valley height (Rt). The analysis on CA fiber had been performed in Asylum Research, (USA) MFP-3D BIO AFM equipment.
2.2.9 Energy dispersive X-ray spectroscopy (EDX) analysis
The Energy dispersive X-ray spectroscopy (EDX) analysis assists to identify the consisting elements and chemical composition on surface area of the various fibers and give the information about atomic weight percentage of different elements like C, O, Na, Mg, Al, Si, P, Cl, K, Ca, and S. EDAX analysis done by scanning electron microscope model HITACHI S-3700N.
3. Results and discussion
3.1 Anatomy of careya arborea (CA) fiber
Investigation of the CA bark fiber under the micron radical scientific equipment (Coaxial Binocular Research) microscope identified the microscopic surface structure and clear nomenclature of the fiber. For natural fibers, diameter is critical parameter. The fiber length and fiber diameter may depend on the process which has been followed and applied pressure while extraction process. However, the fibers are circular to explore the mechanical properties like tensile strength and young’s modulus. The major industries like aerospace, marine, textile, and automobile are looking for lightweight materials. So, it is very essential to identify the low-density natural fiber for industrial applications and also, they would biodegradable, sustainable and eco-friendly with environment. Similarly, CA fiber is 1140 kg/m3 which comparatively has less density than existed fibers, such as Banana fiber (1350 kg/m3), coconut sheath fiber (1375 kg/m3) and saisal fiber (1500 kg/m3) (Senthilkumar et al. Citation2018). Primary, thermo-mechanical properties of the natural fibers depend on the chemical properties and elements of the natural fibers presented in . The rich cellulose content (71.17 wt. %) of the CA fiber has enhanced the mechanical properties of the fiber. Other aspect, the percentage of the hemicellulose (27.86 wt. %) is showing impact on mechanical properties. The Rich lignin percentage of CA fiber (14.95 wt. %) is a shielding agent against the biological impact and whereas its low percentage contributes toward structural properties of the CA fiber. The bonding properties of any fiber is very essential, that is decided by wax content in the (0.18 wt. %) CA fiber. The moisture content (9.87 wt.%), Pectin (2.94 wt.%) noticed that in CA fiber, The density of CA fiber is 1140 kg/m3, which confers that CA fiber is suitable for fabricating the lightweight composites and hybrid composites. The diameter of the CA fiber is 28 µm.
Table 1. Comparison of the physical, chemical, crystalline, and thermal properties of CA fiber with other natural fibers.
3.2 Thermal analysis of CA fiber (TGA)
The preparation of the composites and reinforcement of fiber with thermoplastics is challenging task, most of the manufacturing processes involved huge thermal loads and structural loads for manufacturing the composite products. It is the most predominant to know the thermal stability of the CA fiber at various temperatures to understand the suitable thermal stability value to manufacture the composite. The TGA and DTA curves of the CA fiber are represented in . It is showing that mainly how the weight percentage loss with respective temperature, the first phase weight percentage loss 9.131% was resulted at raising temperature to 200°C, During this, phase decomposition takes place for compositions water molecules, hydroxyls, moisture and carboxyl groups (Liu et al. Citation2009) and the second phase degradation of the material started at 200°C to 1000°C with 90.87% of the weight, the major peak indicating decomposition of volatiles, α-cellulose and hemi cellulose decompose at 380°C. However, various natural fiber peaks are considered to compared with CA fiber, Aerial Root Fibers of Ficus amplissima (335°C), Acalypha Indica L (225°C), Vachellia farnesiana (324° C), (Jeyabalaji et al. Citation2021; Ramesh Babu and Rameshkannan Citation2021; Vijay et al. Citation2020). The impact of kinetic activation energy in plant fibers is notable, this factor lies between 60 to 170 kJ/mol. for plant-based natural fibers. The Kinetic activation energy of Careya arborea fiber is 74.62 kJ/mol. This activatio energy is the grater than the Dracaena reflexa 68.784 kJ/mol, Furcraea foetida 65.64 kJ/mol and less than the Prosopis juliflora (76.72 kJ/mol). From this analysis this CA fiber is novel embodiment for reinforcement with available resins.
3.3 Surface morphology of CA fiber (SEM)
The surface morphology of the CA fiber had been measured with the help of scanning electron microscope at different magnifications (100 µm and 30 µm) represented in, to explore the reinforcement and bonding ability of the fiber. indicates the surface morphology of the CA fiber. shows the average diameter of the CA fiber as 28 µm and most of the fiber are spherical in shape. Moreover, this analysis expressed that the fiber surface is hard and it contains small circular pores, these pores increase the surface roughness of the CA fiber and leads toward the bonding strength of the fibers. While manufacturing the composite, roughness factor enhances the bonding between fiber and matrix materials (Belouadah, Ati, and Rokbi Citation2015; Fiore, Scalici, and Valenza Citation2014). shows the surface of CA fiber consisting of some debris, to clean the debris and enhance the bonding stability of the composites, the CA fiber has to undergo with suitable chemical treatment to enhance the properties.
3.4 Atomic force microscopy
(a),(b) & (c) indicaties the 3D, 2D and Line plot of AFM images of the CA fiber. The average roughness value of the CA fiber is (RMS) 43.753 nm which is the greater than the average and root mean square roughness value (39 nm) of the Piliostigmaracemosa fibers, Root fibers of Ficus amplissima (8.225 nm), and less than Cyperus Pangorei fiber (0.625 nm) (Mayandi et al. Citation2016; Ramesh Babu and Rameshkannan Citation2021; Ramkumar and Saravanan Citation2021). The higher roughness value shows the favorable topology and less debris presenting on the top surface layer of the CA fiber. Roughness Skewness (Rsk) and Roughness kurtosis (Rku) are the important parameters to inculcate the porosity of the fiber and nonlinear nature of the CA fiber surface (Manimaran et al. Citation2018). CA fiber shown the value of Skewness Rsk (0.0586 nm) and kurtosis Rku (0.763 nm), since both value of CA fiber is less than 3, in case if it is greater than 3, fiber exhibits the change in surface topological values. The prime value of Rz (286.13), Rt (345.999),Rq (143.172) are stating the surface roughness of the CA fiber.
3.5 Fourier transforms infrared spectroscopy (FTIR)
Essential chemical groups available in the CA fiber had been identified with FTIR spectrum in indicating the FTIR spectra of wavenumber (4000-500 cm−1) of raw CA fiber. At the peak 3430 cm−1, it exhibits the information of O-H stretching strong, broad peak with α-Cellulose, and other medium peak 2906 cm−1 indicating the C=H stretching with alpha cellulose. The other medium peak identified 2351 cm−1 indicating the ≡C-H Stretching with wax content. The other peak 1633 cm−1 reflecting alkene group (C=O) with the availability of lignin, also CA fiber the detected narrow peaks was observed at 1381 cm−1 alkanes group (C=O) with hemicellulose and at fingerprint region a strong peak 1065 cm-1, alcohol (C-O) stretches with lignin. The comparison analysis of peak position, intensities, composition, and functional groups of CA fiber is provided in .
Table 2. Comparison of roughness parameter of careya arboreaya with other natural fiber s available.
3.6 Morphology of careya arborea fiber with X-RD
The X-Ray diffraction (×RD) is most prominent tool to understand the morphology, it determined the difference between amorphous and crystalline structures of the CA fiber. The XRD plot of CA fiber presented in shows the diffraction curve clearly indication of short and sharp peaks denotes that the distribution of the crystalline cellulose through the fiber, that expressing the crystalline nature of the CA fiber. By observing the strongest three peaks of CA fiber at 2θ diffraction angle of 22.0050°, 15.46°, 14.20° these peaks are considering the cellulose-I, amorphous-cellulose, and cellulose-IV fractions in the CA fiber, respectively. The calculate crystallinity index (CI) 85.5% is greater than the aerial root banyan fiber (72.47%), Sansevieria cylindrica (60%), Furcraea foetida (52.6%), and T. Populnea (48.17%) and also, less than Cannabis sativa (88%), (Lim et al. Citation2020; Sreenivasan et al. Citation2011; Vijay et al. Citation2019).The Crystalline size of the CA fiber value was 7.40 nm, comparatively the size indicating that greater than Ficus religiosa root fiber (5.18 nm), Piliostigma racemosa(5.25 nm), Albizia Julibrissin (6.75 nm) and less than aerial root banyan fiber (28.36 nm), (Md et al. Citation2020; Ramesh Babu and Rameshkannan Citation2021; Ramkumar and Saravanan Citation2021). The crystalline size influences the new embodiments of the fiber chemical properties and water absorption properties.
3.7 Differential scanning calorimeter (DSC) analysis
The activation energy is most prominent factor to understand the thermal stability of fiber, it can be calculated using the equation (ln(k2/k1) = Ea/R x (1/T1 - 1/T2)). The estimation of the thermal stability of the CA fiber indicating DSC curve by the . The Kinetic activation energy of Careya arborea fiber is 74.62 kJ/mol. This activation energy is greater than the Dracaena reflexa 68.784 kJ/mol and less than Prosopis juliflora (76.72 kJ/mol).
3.8 EDX analysis
represents the EDAX analysis of CA fiber, it is agreed that the existence of the various chemical compositional elements (C, O, Na, Mg, Al, Si, P, Cl, K, Ca, and S). presents the EDX analysis of the CA fiber and which was compared with other available natural fibers Furcra Foetida, Dracana reflexa, Albizia Julibrissin and Ficus amplissima. The Carbon weight percentage of 15.66% of the CA fiber is less than the other fibers in comparison, and identified oxygen is 26.37%, which also less than the compared percentages of the fibers. Also, other elements identified in CA fiber is Al percentage is (3.14%), P percentages (3.33%), Cl percentage (2.21%), K percentage (1.29%) and Ca percentage is (44.53%) the calcium value is greater than all the fibers which are compared in , it shows the impact on elongation properties of the natural fibers.
Table 3. FTIR peak intensity and availability of chemical stretches in the CA fiber.
Table 4. Comparison of weight and atomic percentage of CAF with other natural fibers.
3.9 Single fiber tensile test analysis
The mechanical behavior of Careya arboreaya fiber is shown in . The mechanical properties of the fiber are tensile strength, young’s modulus, and elongation at break of CA fiber investigated for twenty individual fibers. The results listed in clearly indicate the average breaking strength and breaking energy of the CA fiber in two different units of measured. Based on the observations noted that a higher breaking work obviously indicates a stronger fiber as CA fiber material has relatively a very low elongation (average-1.6%) value but good breaking strength.
Table 5. Mechanical properties of the careaya arborea fiber.
4. Conclusions
The microstructural and mechanical properties of the CA fibers were investigated in the current study and were compared with novel fibers of scientific interest. The characterization to evaluate properties such as chemical, mechanical, thermal, and microstructural were investigated and the following conclusion have been discerned.
The chosen fibers have lowest density of 1140 kg/m3 when compared with other novel fibers in the current scientific community and hence are found to be amenable in use with the light-weight applications.
Whereas when compared with the thermoplastics, it has high thermal stability and degradation with an elevated temperature of about 385°C inferred from the DSC investigations and hence they can be used in chemical adhesive-based high temperature applications.
The tailorability of the CA fiber is that surface roughness can be morphed through chemical treatment and the roughness in the current investigation from the AFM is found to be Ra- 33.458 nm. This enables us to use them in the applications toward strong adhesive joint and hence resulting in greater interlaminar shear strength.
The various chemical compositions of the constituents in the current CA fiber has cellulose and hemicellulose indicating higher strength to weight ratio and this is identified from the EDX. Percentage of the lignin and ash is highly appreciable when compared to the other conventional natural fibers. Since low content of the lignin and decent percentage of ash attributed toward better tensile strength.
Finally, during the structure-property correlation, we have identified that the surface roughness and from the arrangement of the constituent elements, it can be conferred that comparative to hydroxyl groups of lignin, the carboxyl group from the ash has enabled a decent mechanical property. This can be conferred from the FTIR and XRD.
Hence it was found that, the current material has excellent amenability toward high strength applications such as aerospace and automotive, at the same time an inclination toward the biomedical applications in areas like bone tissue engineering applications. Hence enabling a suitable platform for sustainable living.
5. Future perspective
Meeting the pace of the identification of new materials is always difficult for the demand, hence there must be always an alternative which is modifying the existing materials to make them versatile for various applications. Similarly, in the current work, we have identified an interesting and novel fiber which has displayed a decent mechanical and structural properties that are suitable for aerospace and automotive applications. This work currently focuses on few microstructural and mechanical properties, however an intuition for the same will be carried out in the future to evaluate the thermal and tribological characteristics. This may allow us to configure various hybrid materials by combining with various materials. However, a more inclination must be given toward processing techniques in a more sustainable way, which is of current scientific interest.
Acknowledgements
The researcher would like to thank the Department of Biosciences and Bioengineering (BSBE), IIT Bombay, Maharashtra, India, and South India Textile Research Association (SITRA) Coimbatore, Tamil Nadu, India, for their continuous support for research.
Disclosure statement
No potential conflict of interest was reported by the author(s).
References
- Arif, Z. U., M. Y. Khalid, M. F. Sheikh, A. Zolfagharian, and M. Bodaghi. 2022. Biopolymeric sustainable materials and their emerging applications. Journal of Environmental Chemical Engineering 10 (4):108159. doi:10.1016/j.jece.2022.108159.
- Belouadah, Z., A. Ati, and M. Rokbi. 2015, August. Characterization of new natural cellulosic fiber from lygeum spartum L. ( Elsevier Ltd) Carbohydrate Polymers 134:429–17. doi:10.1016/j.carbpol.2015.08.024.
- Bright, B. M., B. J. Selvi, S. Abu Hassan, M. Mustapha Jaafar, S. Suchart, S. Mavinkere Rangappa, and B. K. Nagaraj. 2021. Characterization of natural cellulosic fiber from cocos nucifera peduncle for sustainable biocomposites. Journal of Natural Fibers 1–11. Informa UK Limited. October. doi:10.1080/15440478.2021.1982827.
- Darder, M., P. Aranda, and E. Ruiz-Hitzky. 2007. Bionanocomposites: A new concept of ecological, bioinspired, and functional hybrid materials. Advanced Materials 19 (10):1309–19. doi:10.1002/adma.200602328.
- De Rosa, I. M., J. M. Kenny, M. Maniruzzaman, M. Moniruzzaman, M. Monti, D. Puglia, C. Santulli, and F. Sarasini. 2011. Effect of chemical treatments on the mechanical and thermal behaviour of okra (abelmoschus esculentus) fibres. Composites Science and Technology 71(2):246–54. Elsevier Ltd. doi:10.1016/j.compscitech.2010.11.023.
- Fiore, V., T. Scalici, and A. Valenza. 2014. Characterization of a new natural fiber from arundo donax l. as potential reinforcement of polymer composites. Carbohydrate Polymers 106 (1):77–83. doi:10.1016/j.carbpol.2014.02.016.
- Hyness, N. R. J., N. J. Vignesh, P. Senthamaraikannan, S. S. Saravanakumar, and M. R. Sanjay. 2018. Characterization of new natural cellulosic fiber from heteropogon contortus plant. Journal of Natural Fibers Taylor & Francis. 15 (1):146–53. doi:10.1080/15440478.2017.1321516.
- Indran, S., R. Edwin Raj, and V. S. Sreenivasan. 2014, September. Characterization of new natural cellulosic fiber from cissus quadrangularis root. ( Elsevier Ltd) Carbohydrate Polymers 110:423–29. doi:10.1016/j.carbpol.2014.04.051.
- Jawaid, M., and H. P. S. Abdul Khalil. 2011. Cellulosic/Synthetic fibre reinforced polymer hybrid composites: a review. Carbohydrate Polymers Elsevier Ltd. 86 (1):1–18. doi:10.1016/j.carbpol.2011.04.043.
- Jayaramudu, J., A. Maity, E. R. Sadiku, B. R. Guduri, A. Varada Rajulu, C. V. V. Ramana, and R. Li. 2011. Structure and properties of new natural cellulose fabrics from cordia dichotoma. Carbohydrate Polymers 86 (4):1623–29. doi:10.1016/j.carbpol.2011.06.071.
- Jeyabalaji, V., G. R. Kannan, P. Ganeshan, K. Raja, B. NagarajaGanesh, and P. Raju. 2021. Extraction and characterization studies of cellulose derived from the roots of acalypha indica L. Journal of Natural Fibers. Bellwether Publishing, Ltd.113. doi:10.1080/15440478.2020.1867942.
- Kathiresan, M., P. Pandiarajan, P. Senthamaraikannan, and S. S. Saravanakumar. 2016. Physicochemical properties of new cellulosic artisdita hystrix leaf fiber. International Journal of Polymer Analysis and Characterization 21 (8):663–68. doi:10.1080/1023666X.2016.1194636.
- Khalid, M. Y., and Z. U. Arif. 2022. Novel biopolymer-based sustainable composites for food packaging applications: a narrative review. Food Packaging and Shelf Life. Elsevier Ltd. doi:10.1016/j.fpsl.2022.100892.
- Khalid, M. Y., Z. U. Arif, M. F. Sheikh, and M. A. Nasir. 2021. Mechanical characterization of glass and jute fiber-based hybrid composites fabricated through compression molding technique. International Journal of Material Forming 14(5):1085–95. Springer-Verlag Italia s.r.l. doi:10.1007/s12289-021-01624-w.
- Khalid, M. Y., A. A. Rashid, Z. U. Arif, W. Ahmed, and H. Arshad. 2021.Recent advances in nanocellulose-based different biomaterials: types, properties, and emerging applications. Journal of Materials Research and Technology. Elsevier Editora Ltda14: 2601–23.doi: 10.1016/j.jmrt.2021.07.128.
- Khalid, M. Y., A. A. Rashid, Z. U. Arif, W. Ahmed, H. Arshad, and A. A. Zaidi. 2021. Natural fiber reinforced composites: sustainable materials for emerging applications. Results in Engineering. Elsevier B.V. doi:10.1016/j.rineng.2021.100263.
- Khalid, M. Y., A. A. Rashid, Z. U. Arif, N. Akram, H. Arshad, and F. P. G. Márquez. 2021. Characterization of failure strain in fiber reinforced composites: under on-axis and off-axis loading. Crystals 11(2):1–11. MDPI AG. doi:10.3390/cryst11020216.
- Kim, N. K., S. Dutta, and D. Bhattacharyya. 2018. A review of flammability of natural fibre reinforced polymeric composites. Composites Science and Technology 162:64–78. Elsevier Ltd. doi:10.1016/j.compscitech.2018.04.016.
- Lauchlin, A. R. M. C., and N. L. Thomas. 2012. Chapter 13: biodegradable polymer nanocomposites. In Book : Advances in polymer nanocomposites.
- Lim, C. J., M. Arumugam, C. Kiang Lim, and G. Cheng Lian Ee. 2020. Mercerizing extraction and physicochemical characterizations of lignocellulosic fiber from the leaf waste of mikania micrantha kunth ex H.B.K. Journal of Natural Fibers 17(5):726–37. Taylor and Francis Inc. doi:10.1080/15440478.2018.1527742.
- Liu, D., G. Han, J. Huang, and Y. Zhang. 2009. Composition and structure study of natural nelumbo nucifera fiber. Carbohydrate Polymers 75 (1):39–43. doi:10.1016/j.carbpol.2008.06.003.
- Madhu, P., M. R. Sanjay, P. Senthamaraikannan, S. Pradeep, S. S. Saravanakumar, and B. Yogesha. 2019. A review on synthesis and characterization of commercially available natural fibers: part-I. Journal of Natural Fibers Taylor and Francis Inc. 16 (8):1132–44. doi:10.1080/15440478.2018.1453433.
- Manimaran, P., M. R. Sanjay, P. Senthamaraikannan, M. Jawaid, S. S. Saravanakumar, and R. George. 2019. Synthesis and characterization of cellulosic fiber from red banana peduncle as reinforcement for potential applications. Journal of Natural Fibers 16(5):768–80. Taylor & Francis. doi:10.1080/15440478.2018.1434851.
- Manimaran, P., S. S. Saravanakumar, N. K. Mithun, and P. Senthamaraikannan. 2016. Physicochemical properties of new cellulosic fibers from the bark of acacia arabica. International Journal of Polymer Analysis and Characterization 21(6):548–53. Taylor and Francis Inc. doi:10.1080/1023666X.2016.1177699.
- Manimaran, P., S. P. Saravanan, M. R. Sanjay, M. Jawaid, S. Siengchin, and V. Fiore. 2020. New lignocellulosic aristida adscensionis fibers as novel reinforcement for composite materials: extraction, characterization and weibull distribution analysis. Journal of Polymers and the Environment Springer US. 28 (3):803–11. doi:10.1007/s10924-019-01640-7.
- Manimaran, P., S. P. Saravanan, M. R. Sanjay, S. Siengchin, M. Jawaid, and A. Khan. 2019. Characterization of new cellulosic fiber: dracaena reflexa as a reinforcement for polymer composite structures. Journal of Materials Research and Technology Elsevier Editora Ltda. 8 (2):1952–63. doi:10.1016/j.jmrt.2018.12.015.
- Manimaran, P., P. Senthamaraikannan, K. Murugananthan, and M. R. Sanjay. 2018. Physicochemical properties of new cellulosic fibers from azadirachta indica plant. Journal of Natural Fibers Taylor and Francis Inc. 15 (1):29–38. doi:10.1080/15440478.2017.1302388.
- Manimaran, P., P. Senthamaraikannan, M. R. Sanjay, M. K. Marichelvam, and M. Jawaid. 2018, February. Study on characterization of furcraea foetida new natural fiber as composite reinforcement for lightweight applications. ( Elsevier Ltd) Carbohydrate Polymers 181:650–58. doi: 10.1016/j.carbpol.2017.11.099.
- Maran, M., R. Kumar, P. Senthamaraikannan, S. S. Saravanakumar, S. Nagarajan, M. R. Sanjay, and S. Siengchin. 2020. Suitability Evaluation of sida mysorensis plant fiber as reinforcement in polymer composite. Journal of Natural Fibers Journal of Natural Fibers Taylor and Francis Inc. 19 (5):1–11. doi:10.1080/15440478.2020.1787920.
- Mayandi, K., N. Rajini, P. Pitchipoo, J. T. W. Jappes, and A. Varada Rajulu. 2016. Extraction and characterization of new natural lignocellulosic fiber cyperus pangorei. International Journal of Polymer Analysis and Characterization Taylor and Francis Inc. 21 (2):175–83. doi:10.1080/1023666X.2016.1132064.
- Md, J. S., S. Madhu, S. Chakravarthy K, and J. Siva Naga Raju. 2020. Characterization of natural cellulose fibers from the stem of albizia julibrissin as reinforcement for polymer composites. Journal of Natural Fibers Taylor and Francis Inc. 19 (6):2204–17. doi:10.1080/15440478.2020.1807440.
- Nagaraja Setty, S., V. Kumar, G. Goud, S. Peramanahalli Chikkegowda, and S. Mavinkere Rangappa. 2020. Characterization of chemically treated limonia acidissima (wood apple) shell powder: physicochemical, thermal, and morphological properties.Journal of Natural Fibers. Bellwether Publishing, Ltd.19 (11):4093–104. doi:10.1080/15440478.2020.1853925.
- Njuguna, J., and K. Pielichowski. 2004. Polymer nanocomposites for aerospace applications: fabrication. Advanced Engineering Materials 6 (4):193–203. doi:10.1002/adem.200305111.
- Peças, P., H. Carvalho, H. Salman, and M. Leite. 2018. Natural fibre composites and their applications: a review. Journal of Composites Science 2(4). doi:10.3390/jcs2040066. MDPI AG.
- Ramesh Babu, S., and G. Rameshkannan. 2021. Aerial root fibres of ficus amplissima as a possible reinforcement in fibre-reinforced plastics for lightweight applications: physicochemical, thermal, crystallographic, and surface morphological behaviours. Journal of Natural 1–16. Fibers Taylor and Francis Ltd. doi:10.1080/15440478.2021.1958422.
- Ramkumar, R., and P. Saravanan. 2021. Characterization of the cellulose fibers extracted from the bark of piliostigma racemosa. Journal of Natural Fibers 1–15. Bellwether Publishing, Ltd. doi:10.1080/15440478.2021.1875356.
- Rangappa, S. M., and S. Siengchin. 2022. Moving towards biofiber-based composites: knowledge gaps and insights. Express Polymer Letters. BME-PT and GTE. doi:10.3144/expresspolymlett.2022.33.
- Reddy, J. P., and J. Whan Rhim. 2018. Extraction and characterization of cellulose microfibers from agricultural wastes of onion and garlic. Journal of Natural Fibers 15(4):465–73. Taylor & Francis. doi:10.1080/15440478.2014.945227.
- Sanjay, M. R., G. R. Arpitha, L. Laxmana Naik, K. Gopalakrishna, and B. Yogesha. 2016. Applications of natural fibers and its composites: an overview. Natural Resources 07 (03):108–14. doi:10.4236/nr.2016.73011.
- Sanjay, M. R., P. Madhu, M. Jawaid, P. Senthamaraikannan, S. Senthil, and S. Pradeep. 2018.Characterization and properties of natural fiber polymer composites: a comprehensive review. Journal of Cleaner Production 172: 566–81.doi: 10.1016/j.jclepro.2017.10.101.
- Sanjay, M. R., and S. Siengchin. 2021. Editorial corner – a personal view exploring the applicability of natural fibers for the development of biocomposites. Express Polymer Letters. BME-PT and GTE. doi:10.3144/expresspolymlett.2021.17.
- Sanjay, M. R., S. Siengchin, J. Parameswaranpillai, M. Jawaid, C. Iulian Pruncu, and A. Khan. 2019. A comprehensive review of techniques for natural fibers as reinforcement in composites: preparation, processing and characterization. Carbohydrate Polymers 207 October2018):108–21. doi:10.1016/j.carbpol.2018.11.083
- Saravanan, R., and C. Gnanavel. 2020. “Synthesis and characterization of treated banana fibers and selected jute fiber based hybrid composites.” Materials Today: Proceedings 21 ( xxxx). Elsevier Ltd: 988–92. doi:10.1016/j.matpr.2019.09.143.
- Sarikanat, M., Y. Seki, K. Sever, and C. Durmuşkahya. 2014. Determination of properties of althaea officinalis l. (marshmallow) fibres as a potential plant fibre in polymeric composite materials. Composites Part B: Engineering 57:180–86. Elsevier Ltd. doi:10.1016/j.compositesb.2013.09.041.
- Segal, L., J. J. Creely, A. E. Martin, and C. M. Conrad. 1952. Opportunity for new developments in all phases of textile manufacturing. ’ literature cited an empirical method for estimating the degree of crystallinity of native cellulose using the x-ray diffractometer. Apparel Manufacturing 43.
- Segal, L., J. J. Creely, A. E. Martin Jr, and C. M. Conrad. 1959. An empirical method for estimating the degree of crystallinity of native cellulose using the x-ray diffractometer. Textile Research Journal 29 (10):786–94. doi:10.1177/004051755902901003.
- Senthamaraikannan, P., S. S. Saravanakumar, V. P. Arthanarieswaran, and P. Sugumaran. 2016. Physico-chemical properties of new cellulosic fibers from the bark of acacia planifrons. International Journal of Polymer Analysis and Characterization 21 (3):207–13. doi:10.1080/1023666X.2016.1133138.
- Senthilkumar, K., I. Siva, N. Rajini, J. T. W. Jappes, and S. Siengchin. 2018. Mechanical characteristics of tri-layer eco-friendly polymer composites for interior parts of aerospace application. In Sustainable composites for aerospace applications, 35–53. Elsevier. doi:10.1016/B978-0-08-102131-6.00003-7.
- Sreenivasan, V. S., S. Somasundaram, D. Ravindran, V. Manikandan, and R. Narayanasamy. 2011. Microstructural, physico-chemical and mechanical characterisation of sansevieria cylindrica fibres - an exploratory investigation. Materials & Design 32 (1):453–61. doi:10.1016/j.matdes.2010.06.004.
- Vijay, R., J. D. James Dhilip, S. Gowtham, S. Harikrishnan, B. Chandru, M. Amarnath, and A. Khan. 2020. Characterization of natural cellulose fiber from the barks of vachellia farnesiana. Journal of Natural Fibers Taylor and Francis Inc. doi:10.1080/15440478.2020.1764457.
- Vijay, R., D. L. Singaravelu, A. Vinod, M. R. Sanjay, S. Siengchin, M. Jawaid, A. Khan, and J. Parameswaranpillai. 2019, March. Characterization of raw and alkali treated new natural cellulosic fibers from tridax procumbens. ( Elsevier B.V.) International Journal of Biological Macromolecules 125:99–108. doi:10.1016/j.ijbiomac.2018.12.056.
- Vinod, A., M. R. Sanjay, S. Suchart, and P. Jyotishkumar. 2020. Renewable and sustainable biobased materials: an assessment on biofibers, biofilms, biopolymers and biocomposites. Journal of Cleaner Production 258. doi:10.1016/j.jclepro.2020.120978.