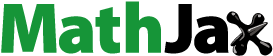
ABSTRACT
Acid hydrolysis is commonly used to extract cellulose nanocrystals (CNC) from natural fibers. This research thus investigates the effect of hydrolysis temperatures and time on the yields of CNC from water hyacinth. The aim is to determine the optimal acid hydrolysis condition for water hyacinth fiber that effectively enhances the CNC yield. The acid hydrolysis temperatures were varied between 50 and 60°C and the hydrolysis time between 15, 30, 60, and 120 min. Prior to the hydrolysis, raw water hyacinth fiber was treated with alkaline and bleached by hydrogen peroxide. The results showed that the optimal hydrolysis condition was 60°C and 30 min, with the crystallinity index of 80%, the crystalline size of 3.91 nm, and the CNC yield of 71.5%. The transmission electron microscopy morphology of CNC from water hyacinth was of whisker shape, with the diameter and length of 10 nm and 200–500 nm. The results also indicated that, unlike the hydrolysis time, the hydrolysis temperature had a negligible effect on the crystallinity index. Besides, under the optimal hydrolysis condition, CNC was of stable aqueous suspension with a zeta potential of −43.21 mV, indicating high physical colloidal stability.
摘要
酸水解通常用于从天然纤维中提取纤维素纳米晶(CNC). 因此,本研究探讨了水解温度和时间对水葫芦CNC产率的影响. 目的是确定有效提高水葫芦纤维CNC得率的最佳酸水解条件. 酸水解温度在50和60°C之间变化,水解时间在15、30、60和120分钟之间. 在水解之前,用水葫芦纤维进行碱性处理并用过氧化氢漂白. 结果表明,最佳水解条件为60℃,30 min,结晶度指数为80%,结晶度为3.91 nm,CNC收率为71.5%. 水葫芦CNC的透射电镜形貌为晶须状,直径为10 nm,长度为200-500 nm. 结果还表明,与水解时间不同,水解温度对结晶度指数的影响可以忽略不计. 此外,在最佳水解条件下,CNC为稳定的水悬浮液,zeta电位为-43.21 mV,表明具有较高的物理胶体稳定性.
Introduction
To reduce reliance on synthetic polymers and promote sustainable development, biodegradable and environmentally-friendly plant-based natural fibers are increasingly adopted as an alternative to synthetic fibers for use as a reinforcing agent in polymer composites (Habibi, Lucia, and Rojas Citation2010; Rasheed, Jawaid, and Parveez Citation2021). The predominant constituents in natural fibers are cellulose, lignin, and hemicellulose. Cellulose is of crystalline structure, while lignin and hemicellulose are of amorphous structure (Mariano, El Kissi, and Dufresne Citation2014; Trache et al. Citation2017). Of particular interest is cellulose which accounts for over 50% of the constituents in natural fibers.
Water hyacinth (Eichhornia crassipes) is a type of lignocellulosic biomass whose cellulose content is as much as 60%, followed by 17% for lignin, 8% for hemicellulose, and 15% for other impurities (Abdel-Fattah and Abdel-Naby Citation2012; Malik Citation2007). The high cellulose content renders water hyacinth an operationally and economically viable feedstock for cellulose nanocrystals. In addition, the use of water hyacinth as the feedstock adds economic value to the plant while tackling the waterway clogging problems.
Cellulose nanocrystals (CNC) are unique nanomaterials derived from the natural polymer, i.e., cellulose (Sundari and Ramesh Citation2012; Taflick et al. Citation2017). The advantages of CNC include excellent mechanical properties (Moon et al. Citation2011), high surface-area-to-volume ratio, lightweight, low density, high hydroxyl groups which make it suitable for a variety of applications, and environmental friendliness (Latif and Mahmood Citation2018). The physical appearance of CNC is of rod-like or ribbon-like particles of 3–50 nm in diameter and 50–1000 nm in length. As a result, CNC can potentially be used in a variety of applications, such as the reinforcing agents in high-performance nanocomposites, filtration media, paints and coatings, and in personal care products, in addition to in biomedical, hygiene, and absorbent products (Mekonnen et al. Citation2019).
Bondeson, Mathew, and Oksman (Citation2006) performed acid hydrolysis using commercial micro cellulose (MCC) using sulfuric acid (H2SO4, 63.5% w/w) at 50°C for 2 h, with the resulting CNC yield of 30%. Hamad and Hu (Citation2010) isolated CNC from commercial MCC using H2SO4 (64% w/w) at 65°C for 25 min. The experiment achieved a CNC yield of 35%. In addition, acid hydrolysis was undertaken with commercial softwood craft pulp using H2SO4 (64% w/w) at 45°C for 25 min, achieving a CNC yield of 32.9% (Hu, Hashaikeh, and Berry Citation2014).
Syafri et al. (Citation2019) extracted CNC from water hyacinth using 5 M of hydrochloric acid (HCl) at 60°C for 20 h. No CNC yield was reported, however. Asrofi et al. (Citation2018), extracted CNC from water hyacinth using 5 M of HCl at 50°C for 12 h, but no CNC yield was reported. Oyeoka et al. (Citation2021) hydrolyzed water hyacinth for CNC using 8.75 mL of H2SO4 (64 wt%) at 45°C for 30 min, achieving a CNC yield of 33.69%. Essentially, the previous studies attempted to isolate CNC under varying experimental conditions, with the CNC yields between 30–34%. However, the CNC yields (30–34%) are economically less attractive for large-scale production. As a result, this study endeavors to determine the optimal acid hydrolysis condition of water hyacinth fiber that effectively enhances the CNC yield.
Specifically, this research investigates the effects of different acid hydrolysis temperatures and times on the yield of cellulose nanocrystals from water hyacinth (WHF-CNC). The hydrolysis temperatures were varied between 50 and 60°C; and the hydrolysis times between 15, 30, 60, and 120 min, given 50% v/v H2SO4. The aim is to determine the optimal acid hydrolysis for water hyacinth fiber that achieves the highest WHF-CNC yield. The study also characterized the chemical composition, crystalline structure (i.e., crystallinity index and crystalline size), and morphology of the experimental water hyacinth fibers. Furthermore, the zeta potential of WHF-CNC was determined. The originality of this research lies in the use of moderate acid concentration (50% v/v H2SO4) and very short hydrolysis time (30 minutes), given the hydrolysis temperature (60°C), to effectively enhance the CNC yield from water hyacinth. Under the optimal hydrolysis condition (50% v/v H2SO4, 30 minutes and 60°C), the CNC yield was 71.5%.
Materials and methods
Experimental materials
In this research, water hyacinth (Eichhornia crassipes) was garnered from a natural waterway in Thailand’s Central province of Pathum Thani, where the aquatic plant is found in abundance. The experimental water hyacinth fibers (WHF) were obtained from the plant stems which are spongy and bulbous stalks containing air-filled tissues that keep the plant afloat. Besides, the stems of water hyacinth contain the highest cellulose content, compared to the plant roots and leaves (Pitaloka, Saputra, and Nasikin Citation2013). Sodium hydroxide (NaOH; 99%, Qrec, New Zealand), hydrogen peroxide (H2O2; 50% v/v, SOLVAY, Thailand), and sulfuric acid (H2SO4; ≥ 98.0%, Anapure, New Zealand) were from Lab Valley Part., Ltd., Thailand. The chemical reagents were used as is.
Preparation of water hyacinth fiber and water hyacinth cellulose nanocrystals
shows the purification and extraction process of raw water hyacinth fiber (WHF-R) for water hyacinth cellulose nanocrystals (WHF-CNC). To obtain WHF-R, fresh stems of water hyacinth were sun-dried for 3 days and then manually cut into small sections of 1 cm in length.
The WHF-R was then boiled in 2 M NaOH solution at 90°C for 60 min and filtered by a No. 18 sieve (1.0 mm openings) and thoroughly washed with deionized (DI) water to remove NaOH. In this research, the alkaline-treated WHF is labeled WHF-A. The WHF-A was subsequently bleached using 0.05 M aqueous NaOH buffer and 10% v/v aqueous H2O2 at 90°C for 120 min with constant mechanical stirring (i.e., first bleaching). The bleached water hyacinth fibers (WHF-B) were then filtered by No. 18 sieve and thoroughly washed with DI water until the pH was 7. To further remove the impurities, the second bleaching was carried out under the same condition and oven-dried at 60°C for 4 h (Thi et al. Citation2017). The alkalization and bleaching were undertaken to remove impurities before process to the hydrolysis (Brito et al. Citation2012; Mueller, Weder, and Foster Citation2014; Shanmugarajah et al. Citation2015).
The WHF-B was subsequently hydrolyzed by using diluted H2SO4 solution (50% v/v) whereby 10 g of dried WHF-B was treated with the H2SO4 solution (1 g/10 ml) and constant magnetic stirring at 500 rpm under variable hydrolysis temperatures (50 and 60°C) and times (15, 30, 60, and 120 min). To stop the reaction, 400 ml of DI water was added to the mixture and centrifuged at 10,000 rpm at 25°C for 10 min (Frontier, PerkinElmer) and the flow birefringence of CNC was determined using cross-polarized light setup. The procedure was repeated until the aqueous CNC suspension was formed, as evidenced by the flow birefringence, as shown in . The aqueous CNC suspension was neutralized by adding 0.05 M NaOH until the pH of the aqueous CNC solution was 7 and centrifuged at 10,000 rpm for 60 min at 10°C.
Characterization of water hyacinth fibers
Microstructure of the experimental water hyacinth fibers
The microstructure of water hyacinth fibers (WHF), including raw WHF, alkaline-treated WHF, and bleached WHF, were characterized by a 50X CU SmartLens. The CU SmartLens is an economical, versatile and reliable microscope that is used with a smartphone to render an enlarged image of a very small object that is too small to be seen by the unaided (Ekgasit et al. Citation2016; Pisantanaroj et al. Citation2020). illustrates the 50X CU SmartLens attached to a smartphone.
Chemical composition of the experimental water hyacinth fibers
The chemical composition of WHF-R, WHF-A, WHF-B, and WHF-CNC were analyzed by Fourier transform infrared spectroscopy (FTIR; Frontier, Perkin Elmer). Prior to the FTIR analysis, samples of WHF-R, WHF-A, WHF-B, and WHF-CNC were oven-dried at 50°C for 1 h for produce dried film. The dried samples were then scanned using the FTIR spectrometer in attenuated total reflectance mode at 4000 to 650 cm −1 wavelength and the spectra recorded in absorption mode. Each WHF sample was scanned 16 times.
Crystallinity index and crystalline size
The crystallinity index and crystalline size of WHF-R, WHF-A, WHF-B, and WHF-CNC were determined by using X-ray diffraction (×RD; SmartLab, Rigaku). Prior to the XRD analysis, samples of WHF-R, WHF-A, WHF-B, and WHF-CNC were oven-dried at 50°C for 1 h before transferring to copper anticathodes operated at 40 kV and 40 mA. The scattered intensity was measured in the 2θ angular domain from 5° to 55° with λ = 1.54 Å. The detector was a linear detector with an angular aperture of 3°. The cellulose crystallinity index (ICr) was calculated based on the XRD patterns and EquationEquation (1)(1)
(1) (Ali et al. Citation2020; Asrofi et al. Citation2017).
where It is the total intensity of the 002 crystalline peak at 22° and Iam is the amorphous intensity at 18°. The crystalline size (τ) was calculated by EquationEquation (2)(2)
(2) .
where k is a form factor (0.9) and β is the full width half maximum (FWHM) of maximum intensity (I002) in radians, and θ is the diffraction angle of the peak (Monshi, Foroughi, and Monshi Citation2012).
Yield of water hyacinth cellulose nanocrystals
The yield of water hyacinth cellulose nanocrystals (WHF-CNC; %) was calculated by EquationEquation (3)(3)
(3) , where WCNC is the dried weight of WHF-CNC and W0 is the weight of water hyacinth fiber after alkaline treatment and bleaching.
Morphology of water hyacinth cellulose nanocrystals
The morphology of WHF-CNC was characterized by transmission electron microscopy (TEM) (Talos, Thermo Scientific). Specifically, TEM was utilized to determine the dimensions (i.e., diameter and length) and the physical appearance of WHF-CNC. Prior to TEM analysis, the WHF-CNC aqueous suspension was diluted with DI water for the WHF-CNC suspension with 0.5 wt%. The diluted WHF-CNC suspension was then deposited on the surface of a carbon grid and coated with a thin carbon film and left to dry at room temperature (25°C). The TEM analysis was carried out with an accelerating voltage of 80 kV.
Zeta potential of water hyacinth cellulose nanocrystals
The zeta potential of WHF-CNC aqueous suspension (0.01 wt%) was determined using a particle analyzer (Delsa Nano C, Beckman Coulter). To mitigate the effect of ionic strength, the WHF-CNC suspension was diluted in an aqueous standard solution with pH 7.
Results and discussion
Microstructure of WHF-R, WHF-A, and WHF-B
are the photograph images of WHF-R, WHF-A, and WHF-B, respectively. In , the color of WHF-R is brown and changed to light brown following the alkalization. depicts the alkaline-treated WHF (WHF-A), while shows the bleached WHF (WHF-B), and the color of the bleached WHF is white. The changes in color were attributed to the removal of non-cellulosic materials (i.e., hemicelluloses and lignin) and other impurities (i.e., pectin and wax) following the chemical treatment (alkalization and bleaching).
respectively show the microstructure of WHF-R, WHF-A, and WHF-B by using the 50X CU SmartLens microscope. In , the WHF-R were bundled together and the fibers are thick and rough. Following the alkalinization (WHF-A), the fibers became unbundled, thinner, and smoother, as shown in . In , bleaching further thinned out the fibers, resulting in the microfibers (WHF-B). The smoother and thinner fibers were attributable to the removal of non-cellulosic components and other impurities, including pectin and wax which serve as the protective layer of WHF.
FTIR chemical composition analysis
respectively show the FTIR spectra of WHF-R, WHF-A, WHF-B, and WHF-CNC. Specifically, in , the peaks at 1731 cm−1 and 1242 cm−1 were characteristic of carbonyl stretching in hemicellulose; and CO stretching in lignin and hemicellulose, respectively. However, both peaks (at 1731 cm−1 and 1242 cm−1) disappeared following the alkalization and bleaching, as shown in , indicating that the alkalization and bleaching effectively removed lignin and hemicellulose. Meanwhile, WHF-CNC exhibited a strong band at 3337 cm−1 (), which belongs to the stretching vibration of the O-H group. tabulates the FTIR characteristic peaks of the experimental water hyacinth fibers (WHF-R, WHF-A, WHF-B, WHF-CNC), which are consistent with Asrofi et al. (Citation2018); Jonoobi et al. (Citation2009).
Table 1. The characteristic FTIR absorption bands of the experimental WHF.
XRD crystalline structure of cellulose
illustrate the XRD spectra of WHF-R, WHF-A, WHF-B, and WHF-CNC, respectively. By comparison, the intensity and sharpness of the peaks of WHF-R, WHF-A, and WHF-B () were substantially lower than those of WHF-CNC (). Specifically, the alkalization, bleaching and acid hydrolysis effectively removed the amorphous domains in the raw water hyacinth fiber (WHF-R).
In , the two dominant peaks (2θ) at 16° and 22° were associated with the crystalline structure of cellulose type I, consisting of the intra- and intermolecular hydrogen bonds by the hydroxyl groups (Kouadri and Satha Citation2018; Kwak et al. Citation2018). The hydrogen bonds restricted the movement of the cellulosic chains, giving rise to crystallinity as the cellulosic chains were aligned closer together. The low crystallinity index of WHF-R (38%) could be attributed to high content of amorphous components, e.g., hemicellulose, lignin, and pectin (). The crystallinity index increased with further chemical treatments (i.e., alkalization, bleaching and acid hydrolysis) as the amorphous components were removed (Chandra, George, and Narayanankutty Citation2016).
Table 2. Crystallinity index and crystalline size of WHF-R, WHF-A, WHF-B, and WHF-CNC.
tabulates the crystallinity index and crystalline size of WHF-R, WHF-A, WHF-B, and WHF-CNC. The crystallinity index of WHF-R, WHF-A, WHF-B, and WHF-CNC were 38%, 42%, 60%, and 76–85%, respectively. The crystallinity index of WHF-CNC varied in accordance with different hydrolysis temperatures (50 and 60°C) and times (15, 30, 60, 120 min). The lower crystallinity index of WHF-R, WHF-A and WHF-B, compared to that of WHF-CNC, was attributable to the residual amorphous components, e.g., lignin and hemicellulose.
As seen in , the crystalline size and the crystallinity index were positively correlated. Besides, the crystalline size of WHF-R increased from 2.21 nm to between 3.91–4.12 nm for WHF-CNC. Essentially, the chemical treatment (i.e., alkalization, bleaching, and acid hydrolysis) improved the crystalline size of cellulose as the amorphous domains were removed (Jonoobi et al. Citation2009). Alkalization and bleaching removed hemicelluloses and lignin (i.e., the amorphous components) and realigned the crystalline domains. After alkalization and bleaching, the remaining randomly-oriented amorphous domains were readily removed by acid hydrolysis as the hydronium ions efficiently penetrated into the amorphous domains, resulting in the hydrolytic cleavage of glycosidic bonds of cellulose and larger crystalline size
Effects of hydrolysis temperature and time on the crystallinity index and crystalline size of WHF-CNC
compares the color of WHF-CNC after 48 h under different hydrolysis times (15, 30, 60, and 120 min), given the hydrolysis temperatures of 50 and 60°C. At 50°C, the color of WHF-CNC changed from white to yellowish as the hydrolysis time increased from 15 to 120 min. At 60°C, the color of WHF-CNC changed from white to light brown as the hydrolysis time increased from 15 to 120 min. The acid-hydrolyzed WHF-CNC was of colloidal aqueous suspension.
Figure 7. Color of WHF-CNC suspension after 48 h, given the hydrolysis temperatures of 50 and 60°C: (a) 15 min, (b) 30 min, (c) 60 min, (d) 120 min.
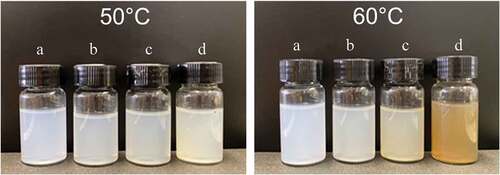
For the hydrolysis temperature above 60°C, the color of WHF-CNC became dark brown, indicating that WHF-CNC was transformed into glucose. On the other hand, if the hydrolysis temperature was below 50°C, no cellulose nanocrystals were formed. In addition, the excessively lengthy hydrolysis time (i.e., over 120 min) resulted in carbonization and the transformation of WHF-CNC into glucose. No cellulose nanocrystals were formed for the hydrolysis time shorter than 15 min.
shows the crystallinity index of WHF-CNC under variable hydrolysis times (15, 30, 60, 120 min), given the hydrolysis temperatures of 50 and 60°C. At 50°C, the initial crystallinity index of 60% at t = 0 rapidly increased with increase in the hydrolysis time and gradually decreased after 30 min. The crystallinity index of WHF-CNC was around 70% after 120 min. Meanwhile, at 60°C, the initial crystallinity index of 60% rapidly increased with increase in the hydrolysis time and steadily decreased after 15 min, achieving the crystallinity index of 76% at 120 min of hydrolysis time.
Figure 8. The crystallinity index of WHF-CNC under variable hydrolysis times given the hydrolysis temperatures of 50 and 60°C.
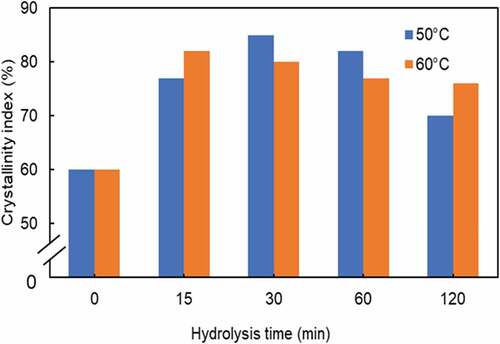
compares the crystalline size of WHF-CNC under variable hydrolysis times, given the hydrolysis temperatures of 50 and 60°C. The crystalline size of WHF-CNC under both hydrolysis temperatures (50 and 60°C) followed the similar pattern. Specifically, the crystalline size increased rapidly during the first 15 min and gradually decreased with increase in the hydrolysis time, suggesting that acid hydrolysis promotes the growth of crystalline size.
The yield of WHF-CNC
compares the yield of WHF-CNC (%) under variable hydrolysis times, given the hydrolysis temperatures of 50 and 60°C. Overall, the yield of WHF-CNC was positively correlated with the hydrolysis temperature and time. At 50°C, the hydrolysis time had less effect on the WHF-CNC yield, compared to that at 60°C. Specifically, at 60°C, the WHF-CNC yield steadily increased with increase in the hydrolysis time but decreased after 60 min. The highest WHF-CNC yield of 85.3% was achieved under 60°C and 60 min.
Figure 10. The yield of WHF-CNC under variable hydrolysis times given the hydrolysis temperatures of 50 and 60°C.
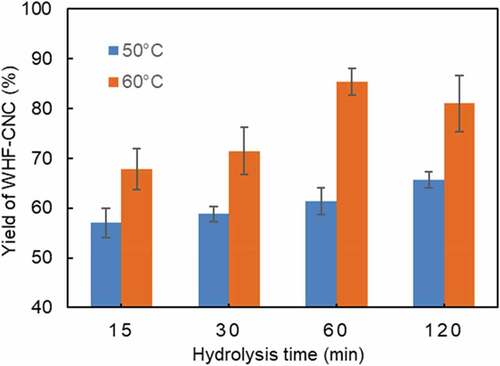
Despite the highest WHF-CNC yield (85.3%), the aqueous suspension of WHF-CNC was unstable and precipitated after 96 h. The instability could be attributed to acid hydrolysis as cellulose was transformed into glucose. As a result, the optimal hydrolysis condition (in terms of the hydrolysis temperature and time) for stable WHF-CNC aqueous suspension were 60°C and 30 min, with the WHF-CNC yield of 71.5%. In comparison, the yield was substantially higher than that of eucalyptus-based CNC (30%) (Bondeson, Mathew, and Oksman Citation2006) and kraft pulp-based CNC (48.2%) (Hu, Hashaikeh, and Berry Citation2014).
Furthermore, the flow birefringence was carried out under a cross-polarized light setup to determine the cellulose nanocrystals in the WHF-CNC aqueous suspension. illustrate the WHF-CNC aqueous suspension, given the optimal hydrolysis condition, under normal light and cross-polarized light setup, respectively.
TEM morphology of WHF-CNC
depicts the TEM morphology of WHF-CNC under the optimal hydrolysis condition. The WHF-CNC was of whisker shape as the acid hydrolysis destroyed the amorphous domains of cellulosic microfibrils while retaining the straight crystalline domains (Brito et al. Citation2012; Mueller, Weder, and Foster Citation2014; Shanmugarajah et al. Citation2015). The diameter and length of acid-hydrolyzed WHF-CNC were 10 nm and 200–500 nm (Asrofi et al. Citation2018; Mohan et al. Citation2021) with an aspect ratio of 10–20.
The zeta potential of WHF-CNC
The zeta potential of WHF-CNC was −43.21 mV, indicating the high stability of the aqueous suspension for an extended time period, given that a zeta potential below −30 mV or above 30 mV represents high physical colloidal stability (Joseph and Singhvi Citation2019). In this research, the negative zeta potential (−43.21 mV) was attributable to the insertion of H2SO4-induced charged sulfate ester groups onto the CNC surface.
Conclusions
Water hyacinth can be used to produce CNCs as a source of cellulose with high yield and shorter time in well-defined structure. This research investigated the effects of variable hydrolysis temperatures and times on the yields of cellulose nanocrystals from water hyacinth. The experimental results showed that acid hydrolysis increased the crystallinity index as the amorphous domains were effectively removed. The crystalline size was positively correlated with the crystallinity index. The optimal hydrolysis condition was 60°C for the hydrolysis temperature and 30 min for the hydrolysis time, with the crystallinity index of 80%, the crystalline size of 3.91 nm, and the WHF-CNC yield of 71.5%. The WHF-CNC was of whisker shape, with the diameter and length of 10 nm and 200–500 nm. Besides, under the optimal hydrolysis condition, the WHF-CNC was of stable aqueous suspension with a zeta potential of −43.21 mV. Essentially, the WHF-CNC could potentially be adopted as a reinforcing agent in bio-nanocomposites. Furthermore, subsequent research would investigate the physical, mechanical and chemical properties of WHF-CNC in various applications.
Highlights
This paper revealed the well-defined cellulose nanocrystals (CNC) and their colloidal suspension obtained by acid hydrolysis from renewable natural resources and abundant cellulose.
In this paper, we report on a new technique of cellulose nanocrystal production from water hyacinth fiber that achieves the highest CNC yield in a shorter time with high colloidal stability without precipitation. Even though the typical CNC is studied by many researchers but the yield of production is relatively low (about 30-34%).
Economic preparation (high yield and short time) is necessary for large-scale production.
The water hyacinth is a plant often found in abundance in natural waterways in tropical countries and is regarded as a severe problem. If we can turn it into a value-added CNC, we can help the reduction of natural waterways waste.
Author contributions
Conceptualization, P.P., W.A., and S.E.; Methodology, P.P., W.A., and S.E.; Validation W.A.; Writing-review and editing, P.P. and W.A. All authors have read and agreed to the published version of the manuscript.
Disclosure statement
No potential conflict of interest was reported by the author(s).
Additional information
Funding
References
- Abdel-Fattah, A. F., and M. A. Abdel-Naby. 2012. Pretreatment and enzymic saccharification of water hyacinth cellulose. Carbohydrate Polymers 87 (3):2109–14. doi:10.1016/j.carbpol.2011.10.033.
- Ali, J. B., A. Danladi, M. M. Bukhari, B. B. Nyakuma, P. Mamza, Z. B. Mohamad, A. B. Musa, and I. M. Inuwa. 2020. Extraction and characterization of cellulose nanofibres and cellulose nanocrystals from Sammaz-14 maize cobs. Journal of Natural Fibers 19 (7):1–16. doi:10.1080/15440478.2020.1856279.
- Asrofi, M., H. Abral, A. Kasim, and A. Pratoto. 2017. XRD and FTIR studies of nanocrystalline cellulose from water Hyacinth (Eichornia crassipes) fiber. Journal of Metastable and Nanocrystalline Materials 29:9–16. https://doi.org/10.4028/www.scientific.net/JMNM.29.9.
- Asrofi, M., H. Abral, A. Kasim, A. Pratoto, M. Mahardika, J.-W. Park, and H.-J. Kim. 2018. Isolation of nanocellulose from water hyacinth fiber (WHF) produced via digester-sonication and its characterization. Fibers and Polymers 19 (8):1618–25. doi:10.1007/s12221-018-7953-1.
- Bondeson, D., A. Mathew, and K. Oksman. 2006. Optimization of the isolation of nanocrystals from microcrystalline cellulose by acid hydrolysis. Cellulose 13 (2):171–80. doi:10.1007/s10570-006-9061-4.
- Brito, B. S., F. V. Pereira, J.-L. Putaux, and B. Jean. 2012. Preparation, morphology and structure of cellulose nanocrystals from bamboo fibers. Cellulose 19 (5):1527–36. doi:10.1007/s10570-012-9738-9.
- Chandra, J., N. George, and S. K. Narayanankutty. 2016. Isolation and characterization of cellulose nanofibrils from arecanut husk fibre. Carbohydrate Polymers 142:158–66. doi:10.1016/j.carbpol.2016.01.015.
- Ekgasit, S., N. Kaewmanee, P. Jangtawee, C. Thammacharoen, and M. Donphoongpri. 2016. Elastomeric PDMS planoconvex lenses fabricated by a confined sessile drop technique. ACS Applied Materials & Interfaces 8 (31):20474–82. doi:10.1021/acsami.6b06305.
- Habibi, Y., L. A. Lucia, and O. J. Rojas. 2010. Cellulose nanocrystals: Chemistry, self-assembly, and applications. Chemical Reviews 110 (6):3479–500. doi:10.1021/cr900339w.
- Hamad, W. Y., and T. Q. Hu. 2010. Structure–process–yield interrelations in nanocrystalline cellulose extraction. The Canadian Journal of Chemical Engineering 88 (3):392–402.
- Hu, T. Q., R. Hashaikeh, and R. M. Berry. 2014. Isolation of a novel, crystalline cellulose material from the spent liquor of cellulose nanocrystals (CNCs). Cellulose 21 (5):3217–29. doi:10.1007/s10570-014-0350-z.
- Jonoobi, M., J. Harun, M. Mishra, and K. Oksman. 2009. Chemical composition, crystallinity and thermal degradation of bleached and unbleached kenaf bast (Hibiscus cannabinus) pulp and nanofiber. BioResources 4 (2):626–39.
- Joseph, E., and G. Singhvi. 2019. Multifunctional nanocrystals for cancer therapy: A potential nanocarrier. Nanomaterials for Drug Delivery and Therapy 91–116.
- Kouadri, I., and H. Satha. 2018. Extraction and characterization of cellulose and cellulose nanofibers from Citrullus colocynthis seeds. Industrial Crops and Products 124:787–96. doi:10.1016/j.indcrop.2018.08.051.
- Kwak, H. W., H. Lee, M. E. Lee, and H.-J. Jin. 2018. Facile and green fabrication of silk sericin films reinforced with bamboo-derived cellulose nanofibrils. Journal of Cleaner Production 200 (5):1034–42. doi:10.1016/j.juro.2018.05.156.
- Latif, M. H. A., and Y. F. Mahmood. 2018. Isolation and characterization of microcrystalline cellulose and preparation of nano-crystalline cellulose from tropical water hyacinth. Ibn AL-Haitham Journal for Pure and Applied Science 31 (1):180–88. doi:10.30526/31.1.1865.
- Malik, A. 2007. Environmental challenge vis a vis opportunity: The case of water hyacinth. Environment International 33 (1):122–38. doi:10.1016/j.envint.2006.08.004.
- Mariano, M., N. El Kissi, and A. Dufresne. 2014. Cellulose nanocrystals and related nanocomposites: Review of some properties and challenges. Journal of Polymer Science: Part B, Polymer Physics 52 (12):791–806. doi:10.1002/polb.23490.
- Mekonnen, T. H., T. Ah-Leung, S. Hojabr, and R. Berry. 2019. Investigation of the co-coagulation of natural rubber latex and cellulose nanocrystals aqueous dispersion. Colloids and Surfaces: A, Physicochemical and Engineering Aspects 583:123949. doi:10.1016/j.colsurfa.2019.123949.
- Mohan, T., C. J. Chirayil, C. Nagaraj, M. Bračič, T. A. Steindorfer, I. Krupa, M. A. A. A. Maadeed, R. Kargl, S. Thomas, and K. Stana Kleinschek. 2021. Anticoagulant activity of cellulose nanocrystals from isora plant fibers assembled on cellulose and SiO2 substrates via a layer-by-layer approach. Polymers 13 (6):939. doi:10.3390/polym13060939.
- Monshi, A., M. R. Foroughi, and M. R. Monshi. 2012. Modified Scherrer equation to estimate more accurately nano-crystallite size using XRD. World Journal of Nano Science and Engineering 02 (3):154–60. doi:10.4236/wjnse.2012.23020.
- Moon, R. J., A. Martini, J. Nairn, J. Simonsen, and J. Youngblood. 2011. Cellulose nanomaterials review: Structure, properties and nanocomposites. Chemical Society Reviews 40 (7):3941–94. doi:10.1039/c0cs00108b.
- Mueller, S., C. Weder, and E. J. Foster. 2014. Isolation of cellulose nanocrystals from pseudostems of banana plants. RSC Advances 4 (2):907–15. doi:10.1039/C3RA46390G.
- Oyeoka, H. C., C. M. Ewulonu, I. C. Nwuzor, C. M. Obele, and J. T. Nwabanne. 2021. Packaging and degradability properties of polyvinyl alcohol/gelatin nanocomposite films filled water hyacinth cellulose nanocrystals. Journal of Bioresources and Bioproducts 6 (2):168–85. doi:10.1016/j.jobab.2021.02.009.
- Pisantanaroj, P., P. Tanpisuth, P. Sinchavanwat, S. Phasuk, P. Phienphanich, P. Jangtawee, K. Yakoompai, M. Donphoongpi, S. Ekgasit, and C. Tantibundhit. 2020. Automated firearm classification from bullet markings using deep learning. IEEE Access 8:78236–51.
- Pitaloka, A. B., A. H. Saputra, and M. Nasikin. 2013. Water hyacinth for superabsorbent polymer material. World Applied Sciences Journal 22 (5):747–54.
- Rasheed, M., M. Jawaid, and B. Parveez. 2021. Bamboo fiber based cellulose nanocrystals/poly (Lactic acid)/poly (butylene succinate) nanocomposites: Morphological, mechanical and thermal properties. Polymers 13 (7):1076. doi:10.3390/polym13071076.
- Shanmugarajah, B., P. L. Kiew, I. M. L. Chew, T. S. Y. Choong, and K. W. Tan. 2015. Isolation of nanocrystalline cellulose (NCC) from palm oil empty fruit bunch (EFB): Preliminary result on FTIR and DLS analysis. Chemical Engineering Transactions 45:1705–10.
- Sundari, M. T., and A. Ramesh. 2012. Isolation and characterization of cellulose nanofibers from the aquatic weed water hyacinth—eichhornia crassipes. Carbohydrate Polymers 87 (2):1701–05.
- Syafri, E., E. Yulianti, M. Asrofi, H. Abral, S. Sapuan, R. Ilyas, and A. Fudholi. 2019. Effect of sonication time on the thermal stability, moisture absorption, and biodegradation of water hyacinth (Eichhornia crassipes) nanocellulose-filled bengkuang (Pachyrhizus erosus) starch biocomposites. Journal of Materials Research and Technology 8 (6):6223–31.
- Taflick, T., L. A. Schwendler, S. M. Rosa, C. I. Bica, and S. M. Nachtigall. 2017. Cellulose nanocrystals from acacia bark–influence of solvent extraction. International Journal of Biological Macromolecules 101:553–61.
- Thi, B. T. N., L. H. Thanh, T. P. Lan, N. D. Thuy, and Y.-H. Ju. 2017. Comparison of some pretreatment methods on cellulose recovery from water hyacinth (Eichhornia crassipe). Journal of Clean Energy Technologies 5 (4):274–79.
- Trache, D., M. H. Hussin, M. M. Haafiz, and V. K. Thakur. 2017. Recent progress in cellulose nanocrystals: Sources and production. Nanoscale 9 (5):1763–86.