ABSTRACT
The exceptional benefits of natural fibers like high weight ratio, biodegradable and low density increased the usage of natural fibers reinforcement in polymers that has increased in recent years. To enhance bonding strength between polymers and natural fibers, this research paper is focused on the possibility of utilizing epoxy resin and nettle fiber to develop a biocomposite. In addition to that surface modification of nettle fibers has been done using different concentration of NaOH, KOH, and NaHCO3. The treated fibers were then reinforced in the epoxy resin to investigate the influence of chemicals on the mechanical properties of developed composites by performing tensile strength, flexural strength, and impact strength. The investigation results revealed that during the experimental investigation, maximum tensile strength (30.13 MPa), flexural strength (22.36 MPa), and impact strength (9.21 J) were discovered for 5% NaOH. Besides the mechanical testing, the fabricated composites were conventionally drilled to investigate the effect of spindle speed (50–800 rev/min), feed rate (0.125–1.2 mm/min), and drill diameter (4–8 mm). The study suggested increase in delamination factor at a higher feed rate and drill diameter. SEM was done on the drilled hole to observe the delamination damage.
摘要
近年来,随着天然纤维增强剂在聚合物中的应用不断增加,天然纤维的特殊优势,如高重量比、可生物降解和低密度. 为了提高聚合物与天然纤维之间的粘结强度,本研究重点探讨了利用环氧树脂和荨麻纤维开发生物复合材料的可能性. 此外,采用不同浓度的NaOH、KOH和NaHCO3对荨麻纤维进行了表面改性. 然后在环氧树脂中增强处理过的纤维,通过拉伸强度、弯曲强度和冲击强度,研究化学品对开发的复合材料力学性能的影响. 研究结果表明,在实验研究过程中,发现5%氢氧化钠的最大拉伸强度(30.13 MPa)、弯曲强度(22.36 MPa)和冲击强度(9.21 J). 除机械测试外,对所制复合材料进行常规钻孔,以研究主轴转速(50–800转/分)、进给速度(0.125–1.2毫米/分)和钻孔直径(4–8毫米)的影响. 研究表明,在较高的进给速度和钻头直径下,分层系数增加。对钻孔进行扫描电镜观察分层损伤.
Introduction
Over the last few years, the utilization of natural fibers as an alternative for synthetic fibers in composites has increased drastically. The importance of using natural fibers for the development of bio-based composites has increased due to their distinctive properties like nontoxic, biodegradable, nonabrasive, and lightweight (Pankaj, Jawalkar and Kant Citation2021; Jirawattanasomkul et al. Citation2020). Traditionally the development of composites materials was done by reinforcing carbon and glass fibers. However, synthetic fibers have many advantages in terms of mechanical properties, but they show non-biodegradable behavior which in the future creates so many problems by waste generation. So, to deal with such disadvantages, from the past few years, natural fibers like jute, hemp, nettle, kapok and flax has been used as reinforcement member in the developing new composites materials (Jirawattanasomkul et al. Citation2021; Sathishkumar et al. Citation2020). The most popular reason for natural fibers is their renewable and biodegradable behavior. The proper reinforcement of natural fibers requires a thorough study of the chemical composition and surface adhesive bonding of fibers. The primary components of natural fibers are pectin, cellulose, hemicellulose, and lignin. To deliver better bonding between fibers and matrix, surface modification techniques like alkali treatment have to be carried out on the fiber surface. Various engineers, researchers, and scientists have carried out experimental investigations to study the surface modification consequence on mechanical characteristics of composites). The experimental study through various testing methods showed a significant improvement in mechanical and thermal properties of natural fiber added polymer and concrete composites (Jain, Sinha, and Jain Citation2021; Jirawattanasomkul et al. Citation2019).
Natural fiber’s limitations such as poor wettability, low fiber matrix bonding, and high water absorption properties play an important role in affecting the overall mechanical behavior of the fabricated composites. To overcome this limitation, many researchers have attempted to elevate the mechanical properties of fabricated composites and found that chemical treatments are an important method to enhance bonding between hydrophilic fibers and hydrophobic matrix (Gholampour and Ozbakkaloglu Citation2020; Pankaj, Kant and Jawalkar Citation2022a; Pankaj, Kant and Jawalkar Citation2022b; Jirawattanasomkul et al. Citation2020). Alkali treatment is one of the popular surface modification techniques to remove impurities and hemicellulose from fiber surface, leading to better interlocking between fiber and matrix material (Maheswari et al. Citation2013). An experimental study of alkali treatment was carried out on bauhinia vahlii fibers to ascertain its outcome on the mechanical properties and furnished that Alkali treatment enhanced the overall strength of the composites (Patel et al. Citation2022). The tensile strength of alkali-treated flax fiber reinforced epoxy was 19.07% more than the untreated fiber-reinforced composites (Ishikawa et al. Citation2014). Improvement in mechanical properties was also observed when Christmas palm fibers treated with KOH were reinforced in the polyester resin. Increase of 60.86% in tensile strength, 50.99% in impact strength, and 49.44% in flexural strength was observed as compared to the untreated fibers (Sundaram and Jayabal Citation2014). Enhancement in impact strength was reported when areca fiber were chemically modified with KOH for 36 hours and then reinforced in the matrix material (Srinivasa and Bharath Citation2013). Enhancement in tensile strength for NaHCO3-treated sisal fibers were observed and significant factors were evaluated by using the Taguchi technique (Kansal et al. Citation2020). The machining behavior of cellulose added fibers is quite different as compared to metals and delamination damage is evolved during the drilling of Composites. The delamination damage is influenced by various machining process parameters like drill bit geometry, drill bit diameter, spindle speed, and feed rate (Lotfi et al. Citation2021). The drilling operations on flax-reinforced epoxy composites were performed in ambient conditions and less thrust force and delamination damage was recorded for the twist drill as compared to coroDrill 854 and coroDrill 856 (Maleki et al. Citation2019a). The optimization of drilling process parameters was conducted while drilling vetiveria zizanioides-based composites. The study suggested minimum delamination damage at intermediate spindle speed and low feed rate (Vinayagamoorthy et al. Citation2018). Limited research work has been reported in the machining of natural fiber-reinforced polymer composites and none has done drilling operations of nettle fiber-based biocomposites. Therefore, this research gap was considered to fill by performing drilling operations on the composite materials reinforced with nettle fibers in epoxy resin.
In the present study, nettle fiber-reinforced epoxy composites were developed and mechanical testing along with delamination factor evaluation was carried out. The fiber content in the fabricated composite was taken as a constant value of 20%. It has been identified from the earlier studies that treatments of natural fibers with NaOH, KOH, and NaHCO3 were effective to enhance the mechanical properties. Limited research work has been reported in the treatment of nettle fibers with NaOH, KOH, and NaHCO3. Three different alkali treatments with NaOH, KOH, and NaHCO3 were successfully implemented on the nettle fibers surface to check the feasibility and enhance the mechanical performance of the composites. Three different concentrations (3%, 6%, and 9%) were selected for each chemical to check the performance of composites at various concentration loads and delamination damage was also studied first time.
Materials and methods
Nettle fiber, polymer, and curing agent
Fibers from plants can be obtained from leaves, stems, and stalk through chemical or mechanical extraction techniques. Plant fibers like nettle, jute, hemp, and flax were traditionally used to make ropes for domestic applications from ancient times. Nettle fiber is considered as the best reinforcement constituent in thermoplastic because of its higher strength as compared to the other plant-based fibers. Many experimental and analytical studies have revealed that the inclusion of nettle fibers as filler members will improve the mechanical performance of the neat polymers. Since these natural fibers are obtained from natural process, so they have inherent moisture quantity. Due to the moisture content natural fibers have poor wettability with polymers, which need to be improved by various chemical techniques (Chaudhary, Bajpai, and Maheshwari Citation2020). Uttarakhand state in India possesses a variable physiographic diversity which makes it fertile land for various fiber plants. Himalayan nettle grows up to a height of 3 m and is found at various places in Uttarakhand state (India). During this study, the carded nettle fibers were obtained from Uttarakhand fiber and bamboo development board, India. Considering the mechanical properties such as high strength, resilience, and toughness; the epoxy resin (LY556) and curing agent (HY559) have been used for the reinforcement of nettle fibers. The cured mixture has good chemical and moisture resistance, with excellent dielectric properties. The curing agent helps to solidify the mixture at room temperature without any external pressure. Its main advantage is its easy bonding ability with synthetic as well as natural fibers. The epoxy resin and hardener were procured from nearly industrial areas. During this study of composite fabrication, high duty silicone spray was used as a releasing agent.
Surface modification of fibers
Surface modification of nettle fibers was performed to enhance the adhesive strength between fibers and epoxy resin. The surface of fibers when get interacted with the chemicals, then the impurities with in them get removed and a good fiber surface is thus created. The fiber surface modifier pallets of Potassium hydroxide (KOH), Sodium hydroxide (NaOH), and Sodium bicarbonate (NaHCO3) were procured in pallet form (Himalaya scientific instruments, Chandigarh) shown in .
Experimental method
The details related to the fabrication and testing executed for the nettle and epoxy-based composites has been discussed ahead in this section.
Alkali treatment of nettle fibers
Untreated dried nettle fibers were soaked in NaOH, NaHCO3, and KOH to alter the surface properties. The concentration of each chemical was varied as (3, 6 and 9%). The alkali solutions were prepared by mixing requisite amounts of NaOH, NaHCO3, and KOH in predetermined (100 gm) water. To prepare the alkali solution of 3%; 3 gm of each chemical was diluted in 100 gm of water. The same measured procedure was adopted to prepare alkali solution for 6 and 9%. The nettle fibers were then placed inside each alkali solution for 8 hours and at regular intervals shaking of the mixture was done for uniform treatment. The nettle fiber to alkali solution ratio was kept at 1:15. The chemical treatment performed at various solution concentration is shown in .
Fabrications of composites
Conventional hand layup method of composites fabrication was adopted during this study to develop nettle fiber based polymer sheets. The metallic mold with a dimensions of 250 × 250 x 4 mm was made for the casting of the composites. Teflon sheets with very small thickness was placed at inward surface of the mould for easy removal of the fabricated composites sheets. The fiber weight percentage of the nettle fibers was kept fixed 20% for the fabrication of the composites. The measured amount of epoxy resin and hardener with a ratio of 10:1 was mixed properly to prepare a homogenous mixture. The nettle fibers were then mixed thoroughly with the prepared polymer resins to obtain a homogenous mixture. The inner side of the mould was sprinkled with releasing agent to avoid irregular sticking of the polymer resin with the mould wall. The homogenous mixture of nettle fibers and polymer resin was poured into the mould and weight was placed on the mould to obtain a desired and uniform thickness. The composite casting was allowed to cure at room temperature for 24 hours. After complete curing process, composite sheets were separated from the mould without harming the composites. The prepared composite sheets were then converted into required dimensions according to the ASTM standards. The composite samples for evaluation of delamination factor in drilling operation were prepared in the stainless steel mould with dimensions of 250 × 200 × 6 mm. The same procedure of sample preparation was followed as discussed above.
Mechanical testing and delamination factor determination
The composite samples were tested to find the tensile, flexural, and impact strength. The tensile and flexural strength was tested on the universal testing machine. The composite samples for evaluation of tensile strength were prepared according to ASTM 638 standards. The composite samples with dumbbell shapes were tested two times for each combination to test the repeatability. The average tensile strength of tested samples was reported as the final strength of the composites. The flexural strength of the rectangular composite samples prepared according to the ASTM 790 standard was evaluated successfully three times for each combination. The impact strength of the chemically treated nettle fiber-reinforced composites was evaluated for the samples prepared in compliance with ASTM D 256. The whole experimentation and testing were conducted at ambient temperature. The practical conditions of fiber reinforced polymer composites leading to the generation of delamination damage are shown in . The delamination factor of the drilled holes in the composites samples was evaluated by importing the digital images in the imajeJ software. ImajeJ is a java-based image processing software to edit and analyze the 16 bit integer and 32 bit floating point images. The threshold feature was adjusted in imageJ software to calculate the maximum damaged area. The Procedure adopted to calculate delamination factor is shown in . The drilling operation was performed through stainless steel twist drill in dry conditions. The delamination factor for the evaluation of delamination damage was evaluated through the given equation: Fd = Dmax/D
Figure 4. Procedure adopted to calculate delamination factor (a) Drilling of nettle fiber composite (b) Digital microscopy image of hole (c) Image imported to imageJ software.
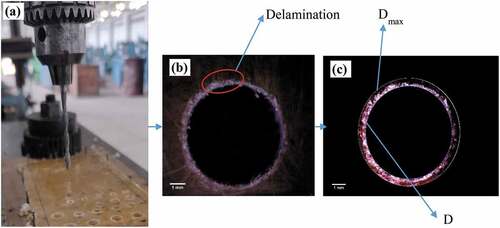
where Dmax is the enlarged diameter due to drilling and D is the nominal diameter.
Results and discussions
Tensile strength of chemically treated composites
The modification of nettle fibers through NaOH, KOH, and NaHCO3 improved the surface qualities of the fibers and improvement in tensile strength of composites was observed as shown in . NaOH concentration of 3, 6, and 9% were used during the treatment of fibers. During the investigation, maximum tensile strength was observed for 6% NaOH concentration. When the chemical concentration was used at a level beyond 6%, decrease in tensile strength was observed.
Thus the tensile strength was minimum in the case of 9% NaOH concentration. This decrease in tensile strength was due to the damage in the fiber surface when using an excessive amount of alkali solution. The tensile strength of 6% NaOH was 16.33% more than that of 3% NaOH. Similar results for mechanical properties enhancement and decrease with NaOH treatment in jute fiber composites were observed (Siddika et al. Citation2014). Significant improvement in tensile strength of green composites was observed when rice husk and jute fibers treated with acrylic acid and NaOH were reinforced in unsaturated polyester resin (Chanda et al. Citation2015). Thus, the results obtained due to NaOH treatment were in agreement with the study conducted by many researchers. The SEM images of nettle fibers without treatment and with NaOH solution (6%) treatment are shown in . Potassium hydroxide has been used as a chemical for the treatment of nettle fibers to remove the lignin containing elements such as pectin and wax. The treatment of the fibers was done by varying the solution concentration as 3, 6, and 9%. This treatment acts as a cleaning element to remove the surface impurities of the fibers. The tensile strength of fabricated composites was higher for KOH treatment at 6% solution concentration because of the better adhesive strength and better stress distribution. Besides this, a decrease in tensile strength beyond 6% KOH concentration was observed during the investigation since a higher content of KOH concentration removed the higher contents of cellulose and made fiber brittle and stiff (Vignesh Citation2018). The improvement in tensile strength of composites was noticed when NaHCO3 treated fibers were reinforced with epoxy resin. As compared to the NaOH treatment (6%) fibers, the tensile strength observed for NaHCO3 treatment at 6% concentration was 10% lower. The overall effect of this chemical treatment was to increase the tensile strength, but it was significant up to 6% concentration value beyond which it decreased. A similar effect of NaHCO3 treatment on tensile strength of composites was reported when treated flax, jute, and sisal fibers were reinforced in epoxy resins (Fiore, Sanfilippo, and Calabrese Citation2019).
Flexural strength of chemically treated composites
The NaOH solution was found to be quite effective in improving the flexural strength of nettle fiber-based composites. The maximum flexural strength was observed for the 6% NaOH fiber treatment. The flexural strength for various treated fibers reinforced in epoxy resin is shown in . During the treatment, strong inter- and intramolecular bonds are formed when the hydroxyl group of fibers interacts with the chemical used. There is a change of monolithic crystalline structure of cellulose into different polymorphous forms when alkali treatment of fibers is done (Marques et al. Citation2015). The flexural strength of 6% NaOH was 22.18% more than that of 3% NaOH. When this study was compared with another similar study, then it has been found that fragrant screwpine fibers treated with NaOH performed very well in terms of flexural strength when reinforced in unsaturated polyester (Selvan and Athijayamani Citation2016). The flexural strength obtained during this investigation is lower than the basalt fiber-based composites, but benefits of partial biodegradability and sustainability have been achieved (Pithalis, Raj, and Sathish Citation2021). The average flexural strength observed during this experimental investigation was quite comparable and in agreement with the banana and flax-reinforced epoxy hybrid composites. It can be predicted through the tensile strength results that during the chemical treatment with KOH, a chemical reaction may have occurred, which could have led to increased tensile strength. Similarly, enhanced flexural strength for nettle fiber-based composites was observed when it was treated with KOH. The fracture of the composites under bending load occurs due to the simultaneously tensile and compression at the bottom and top surface. The crack propagation initiates either at the top surface or surface area near to loading nose. A similar study has been carried out in the treatment of pineapple fibers through KOH at various concentrations and improvement in the flexural strength of the composites was noticed (Senthilkumar et al. Citation2019). The SEM images of nettle fibers without treatment and with KOH solution (6%) treatment are shown in . During the investigation, significant improvement in flexural strength of composites was observed when nettle fibers were treated with NaOH and KOH. The same pattern in flexural strength improvement was observed when nettle fibers were treated with NaHCO3. The use of NaHCO3 beyond 6% was not desirable in terms of flexural strength in developed composite, as a higher concentration of chemical concentration and soaking time leads to degradation of surface properties of fibers (Fiore and Calabrese Citation2019).
Impact strength of chemically treated composites
The effect of the NaOH treatment on impact strength is illustrated in . From the experimental results, it is worth noticing that various chemical treatments were useful to enhance the impact strength of composites as found in the case of tensile and flexural strength. The maximum impact strength was observed as 9.21J for NaOH with a 6% concentration. It is clear from that surface treatment has a negative as well as a positive effect on the impact strength of the composites. We cannot achieve higher impact strength (either lower or higher level) through chemical concentrations. During the investigation, 6% of NaOH was found to be the best alkali solution to achieve the highest impact strength. The impact strength mainly depends upon the energy absorbed by the fiber to stop crack propagation and the presence of micro-cracks due to poor interfacial bonding between fiber and polymer matrix. The impact strength of NaOH-treated Acacia leucophloea fiber-based composites enhanced drastically and thermal performance enhancement was also noticed (Arthanarieswaran et al. Citation2016). The impact strength results obtained for KOH-treated fibers increased due to the good interfacial strength and low fiber pull out. The results for impact strength are shown in and a similar trend of decrease in impact strength beyond 6% had also been also observed. The impact strength of the developed composites was better than the Vetiveria zizanioides-reinforced polyester composites (Vinayagamoorthy Citation2017). The modification of nettle fibers through NaHCO3 improved the surface qualities of the fibers and an improvement in the impact strength of composites was also observed. NaHCO3 concentration of 3, 6 and 9% was used for the treatment of fibers. During the investigation, maximum impact strength was observed for 6% NaOH concentration when various treatments were examined. When the chemical concentration was used at a level beyond 6%, a decrease in impact strength was observed. Thus the impact strength was minimum for 9% NaOHCO3. This decrease in tensile strength was due to the damage in the fiber surface when using an excessive amount of alkali solution. The impact strength of 6% NaHCO3 was 23.43% more than that of 3% NaHCO3. Similar enhancement in impact strength was reported when woven jute fibers treated with sodium bicarbonate were reinforced in epoxy resin (Yadav and Gupta Citation2019). The SEM images of nettle fibers without treatment and with NaHCO3 solution treatment are shown in .
Delamination damage evaluation
One factor at a time approach-based experiments were conducted on nettle/epoxy fiber-based composites to study the delamination factor. The composites subjected to drilling operation were prepared according to the conventional hand layup method. Each experiment was repeated two times. The diameter of the drilled hole was measured on a digital microscope and images were imported to imageJ software to evaluate the diameter of the damaged hole. During the initial stage, one parameter at a time was varied in order to predict its influence and quantify the response parameter named delamination factor. In this course of study, trial experiments were performed on nettle fiber-based epoxy composites under the three conditions (Drill diameter: 4 mm, feed: 0.125 mm/rev, spindle speed: 50, 200, 400, 600, and 800 rev/min) (Drill diameter: 6 mm, spindle speed: 800 rpm, feed: 0.125, 0.212, 0.3, 0.5, 0.8, and 1.2 mm/rev) (Feed .125 mm/rev, spindle speed: 800 rev/min and drill diameter: 4, 6, and 8 mm). The fiber breakage, matrix breakage and fiber matrix debonding are the major factors to decide the finishing of the drilled holes in fiber reinforced polymer composites. Delamination occurs at both ends of the drilled hole i.e. at entry and exit. The delamination damage is more prominent at the exit of the hole therefore, delamination factor evaluation at the exit was carried out. The delamination damage induced during the drilling leads to failure of the part during the assembly and reduces the overall strength of the structure. This defect acts as a stress concentrator and localized crack propagation and failure occurs at these sites. The exit delamination damage of drilled holes occurs due to the fiber pull out. The exit delamination damage for nettle/epoxy composites showing the fiber pull out at drilling conditions of spindle speed 50 rpm, drill diameter 4 mm and feed .125 mm/rev is shown in . Influence of the cutting condition of spindle speed, feed rate, and drill diameter is presented in the graphical form in . From , it is clear that when spindle speed increases the delamination factor decreases. This graph is plotted for the cutting conditions of; Drill diameter: 4 mm, feed rate: 0.125 mm/rev, spindle speed: 50, 200, 400, 600, and 800 rev/min. From , it can be concluded that delamination factor increases with an increase of drill diameter and feed rate. represent the influence of feed rate on delamination factor for the drilling conditions of; Drill diameter: 6 mm, spindle speed: 800 rpm, feed rate: 0.125, 0.212, 0.3, 0.5, 0.8, and 1.2 mm/rev. represent the influence of feed rate on delamination factor for the drilling conditions of; Feed rate 0.125 mm/rev, spindle speed: 800 rev/min, and drill diameter: 4, 6, and 8 mm. The straightforward method of finding the drill quality performed by drilling operation is investigating the delamination damage which is one of the major issue while machining cellulose fiber-reinforced polymer composites (Maleki et al. Citation2019b). It has been observed during investigation
that the values of delamination factor were higher at lower feed rates. High temperature generates at the contact area of the drill bit and workpiece due to prolonged interaction time at lower and intermediate feed rates. This causes enhanced material damage around the drilled hole due to bending, pushing, and displacement of material without generating a perfect hole. This delamination damage can be minimized by reducing the heat generation, perhaps attained by enhancing the feed rate. Drilling fibrous composites at higher feed rates reduce the interaction time between tool and workpiece due to rapid relative movement. Thus, heat generation can be lowered by machining this way. Higher strengths are maintained at the kerf wall due to less softening of material at low feed rates (Geng et al. Citation2019). The material removal is controlled by the conversion of bending forces into shear forces. Complete shearing and fracture occur at a higher feed rate due to higher shear stress with quick crack generation and propagation (Bhattacharyya and Horrigan Citation1998). The delamination factor was observed to be increased with the rise in drill diameter and decreased with rising in spindle speed. This was due to the increase in thrust force while drilling natural fiber-based composites (Debnath, Singh, and Dvivedi Citation2014). One-way ANOVA study has been carried out on spindle speed, feed rate, and drill diameter at 6 level, 6 level, and 3 level, respectively, to find the significance of these factors. In this research article, S/N ratio (signal-to-noise ratio) concept has been used because it covers both the mean and standard deviation for each experiment. The number of experiments are two (2) for each trial. Experiments which have highest S/N ratio may be considered the best among all. One-way ANOVA has also been performed on the data to check the significant of the process parameters. The S/N ratio and ANOVA table for different parameters are shown in . Lower is the better quality characteristics S/N ratio formulae have been used in this work and the formula is as follows. It was concluded from the experimentation that drilling operation performed on nettle fiber-based composite at higher or moderate spindle speed, small drill diameter, and low feed rate would generate better quality holes. Therefore, the selection of drilling process parameters while machining natural fiber-reinforced polymer composites are important because these factors decide the quality and efficacy of the drilling operations. It is clear from the image that drilled surface is not good and fibers protruding are clearly noticed. The cutting forces generated during the drilling hole in natural fiber-reinforced polymer induce small pits and rough surfaces. The SEM image for the top surface (drilled hole edge) is shown in .
Table 1. S/N ratio and ANOVA results for variable speeds at constant drill diameter and feed rate.
Table 2. S/N ratio and ANOVA results for variable feed rate at constant drill diameter and spindle speed.
Table 3. S/N ratio and ANOVA results for variable drill diameter at constant spindle speed and feed rate.
Conclusions
Composite sheets reinforced with treated nettle fibers were successfully fabricated and tested for mechanical properties and machining behavior especially focused on drilling. The composites samples for various testing operations were fabricated through the easiest composites fabrication technique i.e. hand layup method. The comparative analysis of chemical treatments (NaOH, KOH, NaHCO3) on mechanical properties of nettle fiber-based composites has been reported first time. The drilling behaviour of nettle fibers composites has been not reported yet. The following significant detail outcomes of the experimental investigation are discussed below.
The mechanical properties evaluated for the sustainable and partially biodegradable composite materials were found to be highest at the 5% solution concentration for NaOH, KOH and NaHCO3.
Mechanical properties evaluated for the NaOH solution treated nettle fiber-based composites showed the maximum tensile strength of 30.13 MPa, the flexural strength of 22.36 MPa and Impact strength of 9.21 J.
The SEM images observed for the chemically treated fibers showed cleaned surfaces as compared to the untreated fibers.
The delamination factor was observed to decrease at higher spindle speed (800 rev/min) because less time was available for interaction between tool and fibers.
During the drilling operations on nettle fiber-reinforced polymer composites, it was observed that the feed rate and drill diameter both increased the delamination with the increasing value of any of these parameters.
The ANOVA approach was incorporated in this research work and feed rate along with spindle speed showed significant contribution to delamination damage.
The delamination damage observed through SEM images showed the presence of flaws and geometric irregularities, which reduce the overall life of the structural members while working under harsh and cyclic loading conditions.
Hence, the results shows that nettle fiber composites should be chemically treated prior to their reinforcement in polymers to enhance mechanical properties. The nettle fibers have emerged as a good reinforcing elements for light weight polymeric applications.
Highlights
Mechanical and machining behavior of eco-friendly chemically treated nettle fiber-reinforced epoxy composites.
The mechanical properties enhancement of biocomposites occurs when chemical-treated nettle fibers are reinforced in the epoxy resin.
The natural fiber composites faces problem of delamination damage when machined with conventional drilling method.
Increase in feed rate and drill diameter are responsible for increased delamination damage among nettle fiber-reinforced epoxy composites.
Compliance with ethical standards
Yes.
Consent to participate
Yes. All equally participated.
Consent for publication
Yes granted.
Acknowledgements
The authors thank Punjab Engineering College for valuable support for the examination and experimental investigation.
Disclosure statement
No potential conflict of interest was reported by the author(s).
References
- Arthanarieswaran, V. P., A. Kumaravel, M. Kathirselvam, and S. S. Saravanakumar. 2016. Mechanical and thermal properties of acacia leucophloea fiber/epoxy composites: influence of fiber loading and alkali treatment. International Journal of Polymer Analysis and Characterization 21 (7):571–390. doi:10.1080/1023666X.2016.1183279.
- Bhattacharyya, D., and D. P. W. Horrigan. 1998. A study of hole drilling in kevlar composites. Composites Science and Technology 58 (2):267–83. doi:10.1016/S0266-3538(97)00127-9.
- Chanda, A. K., A. Hazra, M. P. Kumar, S. Neogi, and S. Neogi. 2015. Chemical treatments of rice husk filler and jute fiber for the use in green composites. Fibers and Polymers 16 (4):902–10. doi:10.1007/s12221-015-0902-3.
- Chaudhary, V., P. K. Bajpai, and S. Maheshwari. 2020. Effect of moisture absorption on the mechanical performance of natural fiber reinforced woven hybrid bio-composites. Journal of Natural Fibers 17 (1):84–100. doi:10.1080/15440478.2018.1469451.
- Debnath, K., I. Singh, and A. Dvivedi. 2014. Drilling characteristics of sisal fiber-reinforced epoxy and polypropylene composites. Materials and Manufacturing Processes 29 (11):1401–09. doi:10.1080/10426914.2014.941870.
- Fiore, V., and L. Calabrese. 2019. Effect of stacking sequence and sodium bicarbonate treatment on quasi-static and dynamic mechanical properties of flax/jute epoxy-based composites. Materials 12 (2):1363. doi:10.3390/ma12091363.
- Fiore, V., C. Sanfilippo, and L. Calabrese. 2019. Influence of sodium bicarbonate treatment on the aging resistance of natural fiber reinforced polymer composites under marine environment. Polymer Testing 80:106100. doi:10.1016/j.polymertesting.2019.106100.
- Geng, D., Y. Liu, Z. Shao, Z. Lu, J. Cai, X. Li, X. Jiang, and D. Zhang. 2019. Delamination formation, evaluation and suppression during drilling of composite laminates: A review. Composite Structures 216:168–86. doi:10.1016/j.compstruct.2019.02.099.
- Gholampour, A., and T. Ozbakkaloglu. 2020. A review of natural fiber composites: properties, modification and processing techniques, characterization, applications. Journal of Materials Science 55 (3):829–92. doi:10.1007/s10853-019-03990-y.
- Ishikawa, H., H. Takagi, A. N. Nakagaito, M. Yasuzawa, H. Genta, and H. Saito. 2014. Effect of surface treatments on the mechanical properties of natural fiber textile composites made by VaRTM method. Composite Interfaces 21 (4):329–36. doi:10.1080/15685543.2013.876322.
- Jain, J., S. Sinha, and S. Jain. 2021. Compendious characterization of chemically treated natural fiber from pineapple leaves for reinforcement in polymer composites. Journal of Natural Fibers 18 (6):845–56. doi:10.1080/15440478.2019.1658256.
- Pankaj, Jawalkar, C. S., and S. Kant. 2021. Critical review on chemical treatment of natural fibers to enhance mechanical properties of bio composites. Silicon 14 (10):1–22. doi:10.1007/s12633-021-01194-1.
- Jirawattanasomkul, T., S. Likitlersuang, N. Wuttiwannasak, T. Ueda, D. Zhang, and M. Shono. 2020. Structural behaviour of pre-damaged reinforced concrete beams strengthened with natural fibre reinforced polymer composites. Composite Structures 244:112309. doi:10.1016/j.compstruct.2020.112309.
- Jirawattanasomkul, T., S. Likitlersuang, N. Wuttiwannasak, T. Ueda, D. Zhang, and T. Voravutvityaru. 2020. Effects of heat treatment on mechanical properties of jute fiber–reinforced polymer composites for concrete confinement. Journal of Materials in Civil Engineering 32 (12):04020363. doi:10.1061/(ASCE)MT.1943-5533.0003456.
- Jirawattanasomkul, T., H. Minakawa, S. Likitlersuang, T. Ueda, J. G. Dai, N. Wuttiwannasak, and N. Kongwang. 2021. Use of water hyacinth waste to produce fibre-reinforced polymer composites for concrete confinement: mechanical performance and environmental assessment. Journal of Cleaner Production 292:126041. doi:10.1016/j.jclepro.2021.126041.
- Jirawattanasomkul, T., T. Ueda, S. Likitlersuang, D. Zhang, N. Hanwiboonwat, N. Wuttiwannasak, and K. Horsangchai. 2019. Effect of natural fibre reinforced polymers on confined compressive strength of concrete. Construction and Building Materials 223:156–64. doi:10.1016/j.conbuildmat.2019.06.217.
- Kansal, S., A. S. Verma, S. Kant, and Pankaj2020. Parametric study of sisal-epoxy resin composite treated in sodium bicarbonate solution using Taguchi orthogonal array. International Journal of Materials Engineering Innovation. 11 (3):264–74. doi:10.1504/IJMATEI.2020.108886.
- Pankaj, Kant, S., and C. S. Jawalka. 2022a. Study on mechanical properties and delamination factor evaluation of chemically treated nettle fiber reinforced polymer composites. Preprint version. doi:10.21203/rs.3.rs-1189002/v1.
- Pankaj, Kant, S., and C. S. Jawalkar. 2022b. Comparative modal analysis of cantilever beam made of biocomposites using finite element analysis. Materials Today: Proceedings. 49 (2022):2330–34. doi:10.1016/j.matpr.2021.09.351.
- Lotfi, A., H. Li, D. V. Dao, and G. Prusty. 2021. Natural fiber–reinforced composites: A review on material, manufacturing, and machinability. Journal of Thermoplastic Composite Materials 34 (2):238–84. doi:10.1177/0892705719844546.
- Maheswari, C. U., K. O. Reddy, E. Muzenda, M. Shukla, and A. V. Rajulu. 2013. Mechanical properties and chemical resistance of short tamarind fiber/unsaturated polyester composites: influence of fiber modification and fiber content. International Journal of Polymer Analysis and Characterization 18 (7):520–33. doi:10.1080/1023666X.2013.816073.
- Maleki, H. R., M. Hamedi, M. Kubouchi, and Y. Arao. 2019a. Experimental investigation on drilling of natural flax fiber-reinforced composites. Materials and Manufacturing Processes 34 (3):283–92. doi:10.1080/10426914.2018.1532584.
- Maleki, H. R., M. Hamedi, M. Kubouchi, and Y. Arao. 2019b. Experimental study on drilling of jute fiber reinforced polymer composites. Journal of Composite Materials 53 (3):283–95. doi:10.1177/0021998318782376.
- Marques, M. D. F. V., R. P. Melo, R. D. S. Araujo, J. D. N. Lunz, and V. D. O. Aguiar. 2015. Improvement of mechanical properties of natural fiber–polypropylene composites using successive alkaline treatments. Journal of Applied Polymer Science 132 (12):20015. doi:10.1002/app.41710.
- Patel, U., R. Ray, A. Mohapatra, S. N. Das, and H. C. Das. 2022. Effect of different chemical treatments on surface morphology, thermal and tensile strength of bauhinia vahlii (BV) stem fibers. Journal of Natural Fibers 19 (1):280–91. doi:10.1080/15440478.2020.1739591.
- Pithalis, N. E., J. B. Raj, and S. Sathish. 2021. Tensile and flexural behaviour of basalt composites with silicone carbide fillers. Silicon 14 (4):1–11. doi:10.1007/s12633-021-00978-9.
- Sathishkumar, G. K., M. Ibrahim, M. M. Akheel, G. Rajkumar, B. Gopinath, R. Karpagam, P. Karthik, M. M. Charles, G. Gautham, and G. G. Shankar. 2020. Synthesis and mechanical properties of natural fiber reinforced epoxy/polyester/polypropylene composites: A review. Journal of Natural Fibers 19 (10):1–24. doi:10.1080/15440478.2020.1848723.
- Selvan, M. G. A., and A. Athijayamani. 2016. Mechanical properties of fragrant screwpine fiber reinforced unsaturated polyester composite: effect of fiber length, fiber treatment and water absorption. Fibers and Polymers 17 (1):104–16. doi:10.1007/s12221-016-5593-x.
- Senthilkumar, K., N. Rajini, N. Saba, M. Chandrasekar, M. Jawaid, and S. Siengchin. 2019. Effect of alkali treatment on mechanical and morphological properties of pineapple leaf fibre/polyester composites. Journal of Polymers and the Environment 27 (6):1191–201. doi:10.1007/s10924-019-01418-x.
- Siddika, S., F. Mansura, M. Hasan, and A. Hassan. 2014. Effect of reinforcement and chemical treatment of fiber on the properties of jute-coir fiber reinforced hybrid polypropylene composites. Fibers and Polymers 15 (5):1023–28. doi:10.1007/s12221-014-1023-0.
- Srinivasa, C. V., and K. N. Bharath. 2013. Effect of alkali treatment on impact behavior of areca fibers reinforced polymer composites. Fiber Composites 1 (2):2013.
- Sundaram, S. K., and S. Jayabal. 2014. Mechanical properties of potassium hydroxide-pretreated Christmas palm fiber-reinforced polyester composites: Characterization study, modeling and optimization. Journal of Polymer Engineering 34 (9):839–49. doi:10.1515/polyeng-2014-0084.
- Vignesh, K. 2018. Mercerization treatment parameter effect on coir fiber reinforced polymer matrix composite. Materials Research Express 5 (7):075303. doi:10.1088/2053-1591/aad034.
- Vinayagamoorthy, R. 2017. Influence of fiber surface modifications on the mechanical behavior of Vetiveria zizanioides reinforced polymer composites. Journal of Natural Fibers 16 (2):163–74. doi:10.1080/15440478.2017.1410513.
- Vinayagamoorthy, R., I. V. Manoj, G. N. Kumar, I. S. Chand, G. V. S. C. Kumar, and K. S. Kumar. 2018. A central composite design based fuzzy logic for optimization of drilling parameters on natural fiber reinforced composite. Journal of Mechanical Science and Technology 32 (5):2011–20. doi:10.1007/s12206-018-0409-0.
- Yadav, A., and M. K. Gupta. 2019. Development and characterization of jute composites for sustainable product: Effect of chemical treatments and polymer coating. Materials Research Express 7 (1):015306. doi:10.1088/2053-1591/ab5bd9.