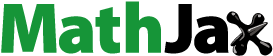
ABSTRACT
The usage of natural fibers is regarded as the most viable solution for controlling the consumption of synthetic materials. However, the low moisture resistance, stiffness and poor adhesion capabilities restrict their use in several advanced composite applications. Hence, different surface treatments are employed to improve the physical characteristics of natural materials. In this study, the effect of chemical treatments (sodium hydroxide, acetic acid, potassium permanganate and bromodecane) on the surface characteristics and the adhesion capabilities of Furcraea foetida (FF) fiber with epoxy material is evaluated. From the study, it is seen that the chemical treatment (CT) eliminates the O-H functional groups and enhances the hydrophobic characteristics in FF fiber. Furthermore, the CT removes the amorphous organic attachments and improves the crystallinity in the fiber. However, no substantial increase in the thermal stability of FF fiber was observed post chemical treatment. The microscopic analysis of chemically treated FF (CTFF) fiber shows the elimination of organic attachments and developed neat uniform surface structure. The NaOH-treated FF fiber exhibited maximum tensile strength (σt: 241.75 MPa). Whereas the acetic acid-treated FF fiber showed maximum tensile modulus (σm: 6.9 GPa) and interfacial shear strength (IFSS: 0.06 MPa) compared to CTFF and untreated FF fiber (UTFF).
摘要
使用天然纤维被认为是控制合成材料消耗的最可行的解决方案. 然而,低防潮性、刚度和较差的附着力限制了它们在几种先进复合材料应用中的使用. 因此,采用不同的表面处理来改善天然材料的物理特性. 在本研究中,评估了化学处理 (氢氧化钠、醋酸、高锰酸钾和溴代甘蔗) 对呋喃草纤维与环氧材料的表面特性和粘附能力的影响. 从研究中可以看出,化学处理 (CT) 消除了FF纤维中的O-H官能团并增强了其疏水特性. 此外,CT去除了非晶有机附着物,提高了纤维的结晶度. 然而,在化学处理后,FF纤维的热稳定性没有显著提高. 化学处理的FF (CTFF) 纤维的微观分析表明,有机附着物被去除,表面结构整齐均匀. NaOH处理的FF纤维表现出最大拉伸强度 (σt:241.75 MPa) . 然而,与CTFF和未经处理的FF纤维 (UTFF) 相比,经醋酸处理的纤维表现出最大拉伸模量 (σm:6.9 GPa) 和界面剪切强度 (IFSS:0.06 MPa) .
Introduction
The consumption of synthetic materials is drastically increasing in various industries with the growing demand and technological advancements. Today, the global production of fiber materials has surpassed 100 Mt (FY 2017) and 65% of which are synthetic fibers (Dhaliwal Citation2019). Synthetic materials are durable, moisture resistant, and have higher strength than natural fibers (Liu et al. Citation2019; Zhang, Zhong, and Ren Citation2017). However, the continuous use of these materials causes health issues in living beings and severely pollutes the environment (Lithner, Larsson, and Dave Citation2011; Rhodes Citation2018). As a result of this pressing issue, various industries are compelled to develop sustainable natural materials to replace synthetic materials in different applications. Also, the use of biobased natural resources in the fabrication of different materials show substantial growth from 12% (FY 2010) to 18% (FY 2020) and it is anticipated to reach 25% in the FY 2030 (Andrew and Dhakal Citation2022; Gurunathan, Mohanty, and Nayak Citation2015). Although natural fibers are considered a prominent reinforcing material, their inhomogeneous properties, hydrophilic nature, and lower mechanical and thermal properties compared to synthetic fibers make them unsuitable in various applications. Therefore, various CT are used to enhance the strength, adhesion capabilities, moisture resistance and TS of bio-fibers (Najeeb et al. Citation2020; Valasek, Muller, and Vladimir Citation2017). Alkaline, Silane, Benzolysation, Acetylization, Permanganate, Peroxide, and so on, are some effective CT used to treat lignocellulosic fibers (Al-Maharma and Al-Huniti Citation2019; Kenned, Sankaranarayanasamy, and Suresh Citation2020).
The alkaline treatment is one of the frequently used CT methods. During the treatment, the OH groups in the fiber surface react and dissolve by transforming into cellulose alkoxides, improving the moisture resistance in fibers (Mishra et al. Citation2001; Verma and Goh Citation2021). Nouri et al. Citation2020 (diss fiber) and Pouriman et al. Citation2017 (salago fiber) observed that fibers treated with 5 Wt.% concentrated NaOH solution improved the moisture resistance, reduced lignin content and improved the TS (up to 80°C) of fibers. Acetalization is also a popular CT that helps improve the dimensional stability in natural fibers (Alvarez and Vazquez Citation2006; Rana et al. Citation1997). The studies conducted by Zaman and Khan Citation2021 (banana/polypropylene), Chung et al. Citation2018 (Kenaf/PLA) and Diharjo et al. Citation2017 (sugar palm/Phenolic) indicate that the acetalization improves the stiffness in the natural fibers thus enhances the mechanical strength in composites. Permanganate treatment is another effective fiber treatment that improves fiber-matrix adhesion. During this treatment, the highly reactive Mn3+ ions react with the OH groups of the fiber and by copolymerization, form cellulose-Mn bonding. This formation of cellulose-Mn improves the σt of the fibers (Kabir et al. Citation2012; Madhu et al. Citation2019).
From the literatures it is evident that CT removes the undesired organic contents such as lignin, hemicellulose, wax, pectin and fills the cracks or micropores on the surface of the bio-fibers (Manalo et al. Citation2015; Sullins et al. Citation2017). This develops a uniform surface and improves the surface roughness, interfacial strength, σt and moisture resistance in fibers (Gokul and Rajasekaran Citation2021; Li, Panigrahi, and Panigrahi Citation2007). However, the effectiveness of any CT depends on the type of chemical and its concentration, reaction time and temperature (Mwaikambo, Tucker, and Clark Citation2007). Therefore, the effect of different CT on the mechanical and morphological properties of newly extracted FF fiber is explored for the first time in this study. The FF fiber is chemically treated with sodium hydroxide (NaOH), acetic acid (CH3COOH), potassium permanganate (KMnO4) and 1-Bromodecane (C10H21Br) chemical solutions and the surface characteristics and adhesion properties of CTFF is evaluated.
Materials and experimental details
Furcraea foetida plant and fiber extraction
The fully matured FF plant leaves were identified and were procured locally from the surrounding forest region. The collected FF leaves were needle-shaped with a maximum length up to 1.2 m and a width up to 0.2 m. The FF plant leaves were washed with water and then the clean FF leaves are submerged in a tank filled with water for five days to execute the water retting process (Musio, Mussig, and Amaducci Citation2018; Ruan et al. Citation2015). The decayed leaves were then gently crushed and scraped using a thin metal brush and the fibers are separated from the organic greenish layer of the leaf (Lee et al. Citation2020). Further, the fibers are thoroughly washed in running water to eliminate any attachments of organic elements from the fiber surface. The fibers are then sundried upto 24 hours (Abhishek et al. Citation2022). shows detailed steps involved in the FF fiber extraction process.
Chemical treatment of FF fiber
The FF fibers are chemically treated (CT) with sodium hydroxide (NTFF), acetic acid (ATFF), potassium permanganate (PTFF) and bromodecane (BTFF) solutions. The shows the detailed steps followed during the CT process. The dry FF fiber is immersed in 5 Wt.% concentrated NaOH solution for 3 hours (Valasek et al. Citation2021), 4 Wt.% concentrated acetic acid solution for 2 hours (Oladele et al. Citation2020) and 0.5 Wt.% concentrated KMnO4 solution for 30 minutes individually in separate beakers under normal room conditions. Whereas the bromodecane treatment is conducted by immersing the FF fibers in a chemical solution prepared with 100 ml of 1-bromodecane solution, 0.5 grams of NaOH, 30 ml of acetonitrile (C2H3N) and the solution is diluted with distilled water in a beaker. The reaction between the FF fiber and the prepared solution is carried out by reflux process for 3 hours. The fibers treated with different chemical solutions are washed with distilled water to remove the excess chemical attachments. Finally, the fibers are dried in a hot air oven (Heatron Industrial Heaters) for 2 hours at 80°C.
Physical characterization of UTFF and CTFF fiber
Fourier transform-infrared spectroscopy (FT-IR)
The FT-IR study is conducted to detect the functional groups in the FF fiber. The FT-IR analysis of the UTFF and CTFF fibers is conducted using a spectrophotometer (IR Spirit, Shimadzu, Tokyo, Japan). FF fiber pellets are prepared by mixing them with KBr solution and compressing it under a hydraulic press. The FF fiber pellet is exposed to IR radiation of wavelength varying from 400 cm−1 to 4000 cm−1 and the spectra of the fibers are recorded by 32 scans (da Silva et al. Citation2016; Mahato, Goswami, and Ambarkar Citation2014).
X-ray diffraction (XRD)
The XRD analysis of UTFF and CTFF fiber is conducted using an X-Ray diffractometer (Rigaku Miniflex 600, Akishima, Japan). The experimental trials were conducted with CuKα radiation (λ = 1.5406 nm) at 40 kV and 15 mA in the range of 2θ = 5°- 90°. The crystallinity index (CI) of the FF fibers is calculated based on the Segal empirical model as given in EquationEq. (1)(1)
(1) . Where I200 is the maximum intensity of the crystalline phase peak in 2θ angle between 22° and 23° and IAM is the intensity of the amorphous phase peak in 2θ angle around 16° (D’Almeida, Aquino, and Monteiro Citation2006; Indran, Raj, and Sreenivasan Citation2014; Manimaran et al. Citation2018).
Thermogravimetric analysis (TGA)
The TS of UTFF and CTFF fiber is evaluated using TGA apparatus (TGA 5500, TA Instruments, Delaware, United States). The UTFF and CTFF fiber particles are placed in a platinum crucible individually and gradually heated at a constant heating rate of 10 °C/min up to 700°C in an inert nitrogen gas (20 mL/min) atmosphere. The loss in the mass of the fiber vs heating temperature is plotted in thermograms (Zouari, Devallance, and Marrot Citation2022).
Scanning electron microscopy (SEM) and energy dispersive spectroscopy (EDS)
The surface structures of the UTFF and CTFF are examined by conducting SEM analysis (EVO MA18, Carl Zeiss Ltd., Cambridge, United Kingdom). The SEM test samples of fibers are initially made to undergo a sputtering process to improve the transmittance of electrons. The surface structure of the fibers is evaluated at different surface locations and magnification levels. Also, the atomic and weight percentage of different elements on the surface of the FF fiber is studied by EDS.
Mechanical characterization of UTFF and CTFF fiber
Tensile strength of treated and untreated FF fibers
The σt of UTFF and CTFF fiber is evaluated using a universal testing machine (UTM: ETM-A, Shenzhen WANCE testing machine Co., Ltd., Beijing, China) of 5 kN capacity as per the C1557–20 standard. As shown in , a mounting tab (Mtab) prepared using cardboard material is used to load the fibers safely into the UTM. The fibers by maintaining a gauge length of 50 mm are attached to the Mtab using epoxy adhesive, as shown in . Then the Mtab with the fiber is placed in the test machine and the two supporting sides of the cardboard structure are cut to apply load directly to the fibers, as presented in . The tensile test is performed at crosshead speed of 0.2 mm/min till the fiber reaches the maximum load-bearing capacity and fails (Fidelis et al. Citation2013; Langhorst et al. Citation2021). The σt of the treated and untreated fibers are calculated using EquationEq. (2)(2)
(2) , where Fm and Ac are the maximum force (N) and cross-sectional area (mm2) of FF fiber, respectively.
Single fiber pull-out test
The test samples for single fiber pull-out test are prepared using epoxy (L12) and hardener (K6) mixed in the ratio of 10:1, respectively, and were procured from Atul Pvt. Ltd. Gujarat, India. The single FF fiber of length 50 mm is embedded in the epoxy as shown in the . The sample is then tested using a UTM (ETM-A, Shenzhen WANCE testing machine Co., Ltd., Beijing, China) of 5 kN capacity. The ends of the sample are fixed on the machine’s jaws and tensile load is applied at a crosshead speed of 0.1 mm/min till the fiber fails (Ru et al. Citation2022; Viel et al. Citation2018).
The shear stress in the test sample is evaluated using the EquationEq. (3)(3)
(3) . Where, τ is the interfacial shear stress, Fdebonding (max) is the maximum pull-out load, d is the diameter of the fiber, and Le is the depth of the fiber embedded in the matrix (Thomason and Rudeiros-Fernandez Citation2022).
Results and discussions
Physical properties of UTFF and CTFF fiber
FT-IR analysis of UTFF and CTFF fiber
illustrates the FT-IR spectra of UTFF and CTFF fiber. The carboxyl and OH groups in the natural fibers are found to have hydrogen bonding (HB) interactions (Bakri et al. Citation2016). The peaks centering at 3335 cm−1 show the -OH stretching of the hydroxyl group of cellulose. These hydroxyls groups can be from hemicellulose or lignin content of FF fibers. In CTFFs, the broadness of the peaks was reduced on comparison with the untreated FFs, which indicates a new type of HB interactions between the -OH group of the fibers (Pratiwi et al. Citation2017) and the reactant used in the treatment. Also observed a well resolved sharp peak at around 3740 cm−1 which indicates the residual free – OH groups on the surface of CTFFs. The peaks observed in and around the 2900 cm−1 in untreated and treated FFs are attributed to the C-H stretchings. The observed peak at around 1727 cm−1 in UTFF is the carbonyl (C=O) stretching of ester and carboxyl groups present in hemicellulose (Wan et al. Citation2012). This peak is observed with different intensities after CT, which infers the new interactions (Akhtar et al. Citation2016; Liu and Dai et al. Citation2007; Mwaikambo and Ansell et al. Citation2002) between the carbonyl group and the reagent used in the treatment. A strong absorption peak is observed in all the FFs at around 1032 cm−1 indicate the presence of C-O/C-C stretchings of polysaccharides in cellulose (Dasong and Fan Citation2010; Zhang and Zhang Citation2009). details the observed FT-IR peaks in UTFF and CTFF fibers.
Table 1. FT-IR peaks (cm −1) for UTFF and CTFF fiber.
XRD analysis of UTFF and CTFF fiber
The shows the diffraction peaks of UTFF and CTFF fibers. Two major peaks were observed for UTFF and CTFF fiber, that is, at 2θ = 16° and 22°. The peak at 16° indicates the amorphous region containing organic contents such as hemicellulose and lignin (Anish et al. Citation2022; Vineeth and Senthil Citation2020 and Teklu et al. Citation2022). Whereas the peak at 22° corresponds to the cellulose content in the fiber (Manimaran et al. Citation2018; Patel et al. Citation2020; Senthamaraikannan et al. Citation2016; Sreenivasan et al. Citation2011). The CI of UTFF fiber is calculated to be 54.17% which is comparably better than Grewia tilifolia (41.7%), Lygeumspartum (46.19%) and lesser than Sansevieria cylindrica (60%), Acacia planifrons (65.38%) fibers (Belouadaha et al. Citation2015, Senthamaraikannan et al. Citation2016). The peaks observed in the XRD spectrum for CTFF fibers are slightly higher compared to UTFF fibers. The NTFF fiber showed maximum CI of 63.68% followed by PTFF (60.37%), BTFF (57.61%) and ATFF (54.69%). The CI of NTFF, PTFF, ATFF and BTFF increased by 14.93%, 10.27%, 6.26% and 0.95%, respectively. This increase in the CI is attributed to the elimination of amorphous fiber compounds through acid hydrolysis reaction through the CT (Jabbar et al. Citation2016; Reddy et al. Citation2012). The CI of UTFF and CTFF was found better than hemp, jute, kenaf and sisal fibers as given in .
Table 2. Crystallinity index of different natural fibers.
Thermogravimetric analysis of UTFF and CTFF
The shows TGA curves of the UTFF and CTFF fibers. Both UTFF and CTFFs are showed similar thermal history. A mass loss of about 8% is observed below 200°C due to loss of fiber moisture content. The onset and end set of the thermal degradation in UTFF and CTFF fibers are observed in the temperature range of 250°C to 370°C. In order to find the maximum decomposition temperature, the derivative thermograms are drawn and is given in . The peak value shows the maximum degradation (weight loss >50%) temperature of the samples and are given in . The maximum weight losses are due to the combined thermal degradation of glycosidic bonds of cellulose and the decomposition of hemicellulose content of FF fibers. It is observed that the thermal degradation in the CTFF fibers in the present study are in good agreement with the TGA results of natural fibers reported by Kommula et al. Citation2013 and Madhu et al. Citation2018.
Table 3. Details of different thermal degradation stages.
Microscopic analysis of UTFF and CTFF fiber
The SEM analysis is conducted to understand the structure and topography of the UTFF and CTTFF fiber surfaces. Based on the microscopic observations of FF fibers, the effect of different CT on the adhesion capability of fibers can be predicted. The shows the SEM images of UTFF and CTFF fiber surfaces. The FF fiber is observed to be made up of several microfibers (fibrils), which are closely attached by pectin (Aina et al. Citation2012; Chen et al. Citation2018). The diameter of the UTFF fiber was observed in the range of 176.9–414.8 µm and the diameter of the fibrils ranged from 5.83 µm to 19.90 µm. The surface of untreated FF fiber is covered by a waxy layer and appears to have a smooth surface. Also, undesired organic attachments were observed throughout the fiber surface as seen in . These surface impurities create poor adhesion with matrix phase. The CT of fibers eliminates hemicellulose, lignin, wax and pectin, and so on, undesired attachments and imparts a neat and rough surface structure in fiber (Madhu et al. Citation2018; Vidyashri et al. Citation2019). The BTFF in , shows a clean fiber surface without any impurities. Whereas the NTFF fiber shows higher surface roughness compared to other fibers (Wang, Kabir, and Lau Citation2014). The fibrils in PTFF fiber appear to be slightly detached because of the removal of pectin/lignin from fiber, as seen in . Treating FF fiber with acetic acid enhanced cellulose structures and improved its surface roughness. With the elimination of impurities during the CT, the diameter of fibers and fibrils are observed to slightly reduce. The diameter of the CTFF ranged from 86.13 µm to 278.3 µm and the diameter of the fibrils from 2.64 µm to 13.18 µm.
Energy dispersive spectroscopy
The EDS helps to identify different elements existing in the FF fiber. The shows the EDS spectrum of UTFF and CTFF fibers. The FF fiber majorly contains carbon and oxygen elements (Du, Yan, and Kortschot Citation2015) followed by minimal percentages of sodium, potassium, chlorine and calcium (White and Brown Citation2010). The percentages of carbon after the CT increased whereas the oxygen content decreased. This is due to the formation of phenolic ether group which were developed by the dilution of hydroxyl groups in the FF fiber (Zhang and Zhang Citation2008; Zhang et al. Citation2018). shows the atomic (At. %) and weight (Wt.%) percentages of elements present in the treated and UTFF fiber.
Table 4. Elements present in the UTFF and CTFF fiber.
Mechanical properties of UTFF and CTFF fiber
Single fiber tensile strength
show the σt and σm of UTFF and CTFF fibers. The CT of FF fiber is observed to increase the tensile properties of UTFF fibers. The observed improvement is due to the elimination of micro-pores, cracks, and other surface impurities from the fiber surface. Also, higher CI and the enhanced C-H bonding in FF fiber as discussed in XRD and FT-IR analysis is responsible for the improvement of tensile properties in CTFF compared to UTFF (Rajeshkumar et al. Citation2021).
The NTFF and ATFF fiber showed maximum σt (241.75 MPa) and σm (6.9 MPa), respectively compared to other CTFF test samples. The NTFF, ATFF, PTFF and BTFF fiber showed an improvement of 29%, 24%, 16% and 15% in σt, respectively, compared to UTFF. The higher deviations in σt and modulus of FF fiber are due to the inhomogeneous nature of natural fibers. compares the tensile properties of UTFF and different untreated natural fibers.
Table 5. Tensile properties of FF fiber compared with different natural fibers.
Interfacial shear strength of UTFF and CTFF fiber
shows the IFSS of the UTFF and CTFF fibers. The ATFF showed maximum IFSS (0.06 MPa) compared to other CTFF fibers. The IFSS in ATFF, NTFF and PTFF fiber improved by 49.2%, 11.5% and 8.4%, respectively, compared to UTFF fiber. However, the IFSS of BTFF fiber decreased by 15.73%. The CT removes the surface impurities and improves the stress transfer ability of the fiber. Also, it improves the aspect ratio and the overall effective fiber area which enhances the adhesion capability of FF fiber (Joseph et al. Citation2003). In addition, the CT removes the hydroxyl groups from the fiber which helps to develops chemical bond and improves the mechanical interlocking between fiber and the matrix (Atiqah et al. Citation2018; Khalit et al. Citation2015; Lee, Khalina, and Lee Citation2021).
Conclusions
In this study, the surface characteristics of a newly extracted fiber from FF plant is improved by treating with different chemical solutions. The FT-IR analysis of UTFF and CTFF fiber indicate the existence of cellulose, hemicellulose, lignin content. The CT is observed to reduce the undesired organic hemicellulose and lignin content from the fiber and enhances its surface characteristics. The XRD study shows that the CT improves the CI of the FF fiber and the NTFF fiber showed maximum CI (63.68%). The improvement in the C.I is due to the removal of amorphous content from the fiber surface. It is evident from the SEM observations that the CT of FF fiber develops uniform fiber surface. The σt of the FF fiber is improved by 29%, 24%, 16% and 15% by treating with sodium hydroxide, acetic acid, potassium permanganate and bromodecane chemical solutions, respectively. Also, the ATFF fiber showed a maximum σm of 6.9 GPa, followed by PTFF, NTFF, UTFF and BTFF fiber. The CT improves the IFSS of FF fiber and the ATFF fiber showed a maximum IFSS of 0.06 MPa compared to other test samples. The NTFF exhibited higher σt and indicate better bonding with polymer materials compared to other CTFF fibers. The NaOH-treated fiber having increased tensile strength can be used as cost effective source of fiber reinforcement in various polymer composite applications. However, a systematic study by varying the concentration of NaOH in the treatment process is required to optimize it for high strength polymer composite applications.
Acknowledgments
The authors would like to acknowledge Manipal Academy of Higher Education, Manipal for providing the instrumental and infrastructural facilities to conduct the experimentations. Also, the authors thank Dr. Hariprasad Uppara, BMS College of Engineering, Bengaluru for his inputs in analysing the XRD results.
Disclosure statement
The authors declare that there is no conflict of interests associated with the research work.
References
- Abhishek, S. M., D. Doreswamy, S. Maddasani, M. Shettar, and R. Shetty. 2022. Processing, characterization of Furcraea foetida (FF) fiber and investigation of physical/mechanical properties of FF/epoxy composite. Polymers 14:1476. doi:10.3390/polym14071476.
- Aina, V. O., M. M. Barau, O. A. Mamman, and A. Zakari. 2012. Extraction and characterization of pectin from peels of lemon (citrus limon), grapefruit (citrus paradisi) and sweet orange (citrus sinensis). British Journal of Pharmacology Toxicology 3:259–17.
- Akhtar, M. N., A. B. Sulong, M. K. F. Radzi, N. F. Ismail, M. R. Raza, N. Muhamad, and M. A. Khan. 2016. Influence of alkaline treatment and fibre loading on the physical and mechanical properties of kenaf/polypropylene composites for variety of applications. Progress in Natural Science: Materials International 26 (6):657–64. doi:10.1016/j.pnsc.2016.12.004.
- Al-Maharma, A., and N. Al-Huniti. 2019. Critical review of the parameters affecting the effectiveness of moisture absorption treatments used for natural composites. Journal of Composite Science 3 (1):27. doi:10.3390/jcs3010027.
- Alvarez, V. A., and A. Vazquez. 2006. Influence of fiber chemical modification procedure on the mechanical properties and water absorption of MaterBi-Y/sisal fiber composites. Composites Part A: Applied Science and Manufacturing 37:1672–80. doi:10.1016/j.compositesa.2005.10.005.
- Andrew, J. J., and H. N. Dhakal. 2022. Sustainable biobased composites for advanced applications: Recent trends and future opportunities–a critical review. Composites Part C: Open Access 7:100220. doi:10.1016/j.jcomc.2021.100220.
- Anish, K., R. Vijay, D. S. Lenin, M. R. Sanjay, S. Suchart, J. Mohammad, A. A. Khalid, and M. A. Abdullah 2022 . Extraction and characterization of natural fibers from Citrullus lanatus climber. Journal of Natural Fibers 19 (2):621–29. doi:10.1080/15440478.2020.1758281.
- Atiqah, A., M. Jawaid, M. R. Ishak, and S. M. Sapuan. 2018. Effect of alkali and silane treatments on mechanical and interfacial bonding strength of sugar palm fibers with thermoplastic polyurethane. Journal of Natural Fibers 15 (2):251–61. doi:10.1080/15440478.2017.1325427.
- Bakri, M. K. B., E. Jayamani, S. Hamdan, M. E. Rahman, K. H. Soon, and A. Kakar. 2016. Fundamental study on the effect of alkaline treatment on natural fibres structures and behaviors. Journal of Engineering and Applied Science 11 (14):8759–63.
- Belouadah Z, Ati A and Rokbi M. (2015). Characterization of new natural cellulosic fiber from Lygeum spartum L. Carbohydrate Polymers, 134 429–437. 10.1016/j.carbpol.2015.08.024
- Chen, Y., N. Su, K. Zhang, S. Zhu, Z. Zhu, W. Qin, Y. Yang, Y. Shi, S. Fan, Z. Wang, et al. 2018. Effect of fiber surface treatment on structure, moisture absorption and mechanical properties of luffa sponge fiber bundles. Industrial Crops and Products 123:341–52. doi:10.1016/j.indcrop.2018.06.079.
- Chung, T. J., J. W. Park, H. J. Lee, H. J. Kwon, H. J. Kim, Y. K. Lee, and T. W. Tze. 2018. The improvement of mechanical properties, thermal stability, and water absorption resistance of an eco-friendly PLA/kenaf biocomposite using acetylation. Applied Science 8:376. doi:10.3390/app8030376.
- D’Almeida, J. R. M., R. C. M. P. Aquino, and S. N. Monteiro. 2006. Tensile mechanical properties, morphological aspects and chemical characterization of piassava (Attala funifera) fibers. Composites Part A: Applied Science and Manufacturing. 37:1473–1479.
- da Silva, I. L. A., A. B. Bevitori, L. A. Rohen, M. F. Muylaert, B. F. de Oliveira, and S. N. Monteiro. 2016. Characterization by Fourier transform infrared (FTIR) analysis for natural jute fiber. Materials Science Forum 869:283–87. https://doi.org/10.4028/www.scientific.net/MSF.869.283.
- Dasong, D., and M. Fan. 2010. Characteristic and performance of elementary hemp fibre. Materials Sciences and Applications 1 (06):336. doi:10.4236/msa.2010.16049.
- Dhaliwal, J. S. 2019. Natural fibers: Applications. Generation, Development and Modifications of Natural Fibers 2:1–23.
- Diharjo, K., P. Andy, A. Robbi, A. Gundhi, S. B. Herru, and F. Yohanes. 2017. Effect of acetylation treatment and soaking time to bending strength of sugar palm fiber composite. AIP Conference Proceedings 1788 (1):030049.
- Dittenber, D. B., and H. V. S. GangaRao. 2012. Critical review of recent publications on use of natural composites in infrastructure. Composites Part A, Applied Science and Manufacturing 43 (8):1419–29. doi:10.1016/j.compositesa.2011.11.019.
- Du, Y., N. Yan, and M. T. Kortschot. 2015. The use of ramie fibers as reinforcements in composites. Biofiber Reinforcements in Composite Materials 15:104–37.
- Fidelis, M. E. A., T. V. C. Pereira, O. D. F. M. Gomes, F. S. de Andrade, and F. R. D. Toledo. 2013. The effect of fiber morphology on the tensile strength of natural fibers. Journal of Material Research and Technology 2 (2):149–57. doi:10.1016/j.jmrt.2013.02.003.
- Gokul, K., and T. Rajasekaran. 2021. Recent progress on natural lignocellulosic fiber reinforced polymer composites: A review. Journal of Natural Fibers 21 (7):1–32. doi:10.1080/15440478.2021.1944425.
- Goulart, S. A. S., T. A. Oliveira, A. Teixeira, and P. C. Mileo. 2011. Mechanical behaviour of polypropylene reinforced palm fibers composites. Procedia Engineering 10:2034–39. doi:10.1016/j.proeng.2011.04.337.
- Gurunathan, T., S. Mohanty, and S. K. Nayak. 2015. A review of the recent developments in biocomposites based on natural fibres and their application perspectives. Composites Part A, Applied Science and Manufacturing 77:1–25. doi:10.1016/j.compositesa.2015.06.007.
- Indran, S., R. E. Raj, and V. S. Sreenivasan. 2014. Characterization of new natural cellulosic fiber from cissus quadrangularis root. Carbohydrate Polymers 110:423–29. doi:10.1016/j.carbpol.2014.04.051.
- Jabbar, J. I. M., B. M. Wiener, J. Kale, U. Ali, U. Ali, and S. Rwawiire. 2016. Rwawiire, S. nanocellulose coated woven jute/green epoxy composites: Characterization of mechanical and dynamic mechanical behavior. Composite Structures 161:340–49. doi:10.1016/j.compstruct.2016.11.062.
- Joseph, P. V. J., S. K. Joseph, C. K. S. Thomas, G. Prasad, V. S. Groeninckx, G. Groeninckx, and M. Sarkissova. 2003. Composite part A: Applied. Science Manufacturing 34 (3):253–66. doi:10.1016/S1359-835X(02)00185-9.
- Kabir, M. M., H. Wang, K. T. Lau, and F. Cardona. 2012. Chemical treatments on plant-based natural fibre reinforced polymer composites: An overview. Composites Part B: Engineering 43 (7):2883–92. doi:10.1016/j.compositesb.2012.04.053.
- Kenned, J. J., K. Sankaranarayanasamy, and K. S. Suresh. 2020. Chemical, biological, and nanoclay treatments for natural plant fiber-reinforced polymer composites: A review. Polymers and Polymer Composites 29 (7):1011–38. doi:10.1177/0967391120942419.
- Khalit, M., H. Anuar, N. Shaffiar, I. Yaacob, and S. Sapuan. 2015. Matrix cracking in reinforced polymer nanocomposites: A review. Journal of Advanced Science 11:13–36.
- Kommula, V. P., K. O. Reddy, M. Shukla, T. Marwala, and A. V. Rajulu. 2013. Physico-chemical, tensile, and thermal characterization of Napier grass (native African) fiber strands. International Journal of Polymer Analysis and Characterization 18 (4):303–14. doi:10.1080/1023666X.2013.784935.
- Langhorst, A., M. Ravandi, D. Mielewski, and M. Banu. 2021. Technical agave fiber tensile performance: The effects of fiber heat-treatment. Industrial Crops and Products 171:113832. doi:10.1016/j.indcrop.2021.113832.
- Lee, C. H., A. Khalina, and S. H. Lee. 2021. Importance of interfacial adhesion condition on characterization of plant-fiber-reinforced polymer composites: A review. Polymers 13 (3):438. doi:10.3390/polym13030438.
- Lee, C. H., A. Khalina, S. H. Lee, and L. A. Ming. 2020. Comprehensive review on bast fibre retting process for optimal performance in fibre-reinforced polymer composites. Advances in Material Science and Engineering 19 (12):27. doi:10.1155/2020/6074063.
- Li, L. G. T., S. Panigrahi, and S. Panigrahi. 2007. Chemical treatments of natural fiber for use in natural fiber-reinforced composites: A review. Journal of Polymers and the Environment 15 (1):25–33. doi:10.1007/s10924-006-0042-3.
- Lithner, D., A. Larsson, and G. Dave. 2011. Environmental and health hazard ranking and assessment of plastic polymers based on chemical composition. The Science of the Total Environment 409 (18):3309–24. doi:10.1016/j.scitotenv.2011.04.038.
- Liu, X. Y., and G. C. Dai. 2007. Surface modification and micromechanical properties of jute fibre mat reinforced polypropylene composites. Express Polymer Letters 1 (5):299–307. doi:10.3144/expresspolymlett.2007.43.
- Liu, Y., J. Xie, N. Wu, Y. Ma, C. Menon, and J. Tong. 2019. Characterization of natural cellulose fiber from corn stalk waste subjected to different surface treatments. Cellulose 26:4707–19. doi:10.1007/s10570-019-02429-6.
- Madhu, P., M. R. Sanjay, S. Pradeep, K. S. Bhat, B. Yogesha, and S. Siengchin. 2019. Characterization of cellulosic fibre from phoenix pusilla leaves as potential reinforcement for polymeric composites. Journal of Materials Research and Technology 8 (3):2597–604. doi:10.1016/j.jmrt.2019.03.006.
- Madhu, P., M. R. Sanjay, P. Senthamaraikannan, S. Pradeep, S. Siengchin, M. Jawaid, and M. Kathiresan. 2018. Effect of various chemical treatments of Prosopis juliflora fibers as composite reinforcement: Physicochemical, thermal, mechanical, and morphological properties. Journal of Natural Fibers 17 (6):833–44. doi:10.1080/15440478.2018.1534191.
- Mahato, K., S. Goswami, and A. Ambarkar. 2014. Morphology and mechanical properties of sisal fibre/vinyl ester composites. Fibers and Polymers 15 (6):1310–20. doi:10.1007/s12221-014-1310-9.
- Manalo, A. C., E. Wani, N. A. Zukarnain, W. Karunasena, and K. T. Lau. 2015. Effects of alkali treatment and elevated temperature on the mechanical properties of bamboo fibre–polyester composites. Composites Part B: Engineering 80:73–83. doi:10.1016/j.compositesb.2015.05.033.
- Manimaran, P., P. Senthamaraikannan, M. R. Sanjay, M. K. Marichelvam, and M. Jawaid. 2018. Study on characterization of Furcraea foetida new natural fiber as composite reinforcement for lightweight applications. Carbohydrate Polymers 181:650–58. doi:10.1016/j.carbpol.2017.11.099.
- Mishra, S., M. Misra, S. S. Tripathy, S. K. Nayak, and A. K. Mohanty. 2001. Potentiality of pineapple leaf fibre as reinforcement in palf-polyester composite: Surface modification and mechanical performance. Journal of Reinforced Plastics and Composites 20 (4):321–34. doi:10.1177/073168401772678779.
- Musio, S., J. Mussig, and S. Amaducci. 2018. Optimizing hemp fiber production for high performance composite applications. Frontiers in Plant Science 9:1702. doi:10.3389/fpls.2018.01702.
- Mwaikambo, L. Y., and M. P. Ansell. 2002. Chemical modification of hemp, sisal, jute, and kapok fibres by alkalization. Journal of Applied Polymer Science 84 (12):222–34. doi:10.1002/app.10460.
- Mwaikambo, L. Y., N. Tucker, and A. J. Clark. 2007. Mechanical properties of hemp-fibre reinforced euphorbia composites. Macromolecular Materials and Engineering 292 (9):993–1000. doi:10.1002/mame.200700092.
- Naidu, A. L., V. Jagadeesh, and M. R. Bahubalendruni. 2017. A review on chemical and physical properties of natural fiber reinforced composites. Journal of Advanced Research in Engineering and Technology 8 (1):56–68.
- Najeeb, M., M. Sultan, Y. Andou, A. Shah, K. Eksiler, M. Jawaid, and A. Ariffin. 2020. Characterization of silane treated Malaysian Yankee pineapple AC6 leaf fiber (PALF) towards industrial applications. Journal of Material Research and Technology 9:3128–39. doi:10.1016/j.jmrt.2020.01.058.
- Nouri, M., M. Tahlaiti, F. Grondin, and R. Belarbi. 2020. The influence of chemical and thermal treatments on the diss fiber hygroscopic behaviors. Journal of Natural Fibers 20 (12):1–14. doi:10.1080/15440478.2020.1848733.
- Oladele, I. O., O. S. Michael, A. A. Adediran, O. P. Balogun, and F. O. Ajagbe. 2020. Acetylation treatment for the batch processing of natural fibers: Effects on constituents, tensile properties and surface morphology of selected plant stem fibers. Fibers 8 (12):73. doi:10.3390/fib8120073.
- Omrani, E., P. L. Menezes, and P. K. Rohatgi. 2016. State of the art on tribological behavior of polymer matrix composites reinforced with natural fibers in the green materials world. Engineering Science and Technology, an International Journal 19 (2):717–36. doi:10.1016/j.jestch.2015.10.007.
- Patel, U., R. Ray, A. Mohapatra, S. N. Das, and H. C. Das. 2020. Effect of different chemical treatments on surface morphology, thermal and tensile strength of bauhinia vahlii (BV) stem fibers. Journal of Natural Fibers 1 (19):1–12. doi:10.1080/15440478.2020.1739591.
- Pouriman, M., A. R. Caparanga, M. Ebrahimi, and A. Dahresobh. 2017. Characterization of untreated and alkaline-treated salago fibers (genus wikstroemia spp.). Journal of Natural Fibers 15 (2):296–307. doi:10.1080/15440478.2017.1329105.
- Pratiwi, H. 2017. The alkali treatment parameters using Taguchi model in order to obtain the optimum tensile strength of single kenaf fibre. Angkasa: Jurnal Ilmiah Bidang Teknologi 7 (2):49–58. doi:10.28989/angkasa.v7i2.148.
- Rajeshkumar, G., V. Hariharan, G. L. Devnani, M. J. Prakash, M. R. Sanjay, S. Siengchin, N. A. Al‐dhabi, and K. Ponmurugan. 2021. Cellulose fiber from date palm petioles as potential reinforcement for polymer composites: Physicochemical and structural properties. Polymer Composites 42 (8):3943–53. doi:10.1002/pc.26106.
- Rana, A. K., R. K. Basak, B. C. Mitra, M. Lawther, and A. N. Banerjee. 1997. Studies of acetylation of jute using simplified procedure and its characterization. Journal of Applied Polymer Science 64 (8):1517–23. doi:10.1002/(SICI)1097-4628(19970523)64:8<1517:AID-APP9>3.0.CO;2-K.
- Rao, K. M. M., and K. M. Rao. 2007. Extraction and tensile properties of natural fibers: Vakka, date and bamboo. Composite Structures 77 (3):288–95. doi:10.1016/j.compstruct.2005.07.023.
- Reddy, O., M. Shukla, U. Maheswari, and V. Rajulu. 2012. Mechanical and physical characterization of sodium hydroxide treated Borassus fruit fibers. Journal of Forestry Research 23 (4):667–74. doi:10.1007/s11676-012-0308-7.
- Rhodes, C. J. 2018. Plastic pollution and potential solutions. Science Progress 101 (3):207–60. doi:10.3184/003685018X15294876706211.
- Ruan, P., V. Raghavan, Y. Gariepy, and J. Du. 2015. Characterization of flax water retting of different durations in laboratory condition and evaluation of its fiber properties. BioResources 10 (2):3553–63. doi:10.15376/biores.10.2.3553-3563.
- Ru, S., C. Zhao, S. Yang, and D. Liang. 2022. Effect of coir fiber surface treatment on interfacial properties of reinforced epoxy resin composite. Polymers 14 (17):3488. doi:10.3390/polym14173488.
- Senthamaraikannan, P., S. S. Saravanakumar, V. P. Arthanarieswaran, and P. Sugumaran. 2016. Physico-Chemical properties of new cellulosic fibers from the bark of acacia planifrons. International Journal of Polymer Analysis and Characterization 21 (3):207–13. doi:10.1080/1023666X.2016.1133138.
- Sreenivasan, V. S., S. Somasundaram, D. Ravindran, V. Manikandan, and R. Narayanasamy. 2011. Microstructural, physico-chemical and mechanical characterisation of sansevieria cylindrica fibres–an exploratory investigation. Materials & Design 32 (1):453–61. doi:10.1016/j.matdes.2010.06.004.
- Sullins, T., S. Pillay, A. Komus, and H. Ning. 2017. Hemp fiber reinforced polypropylene composites: The effects of material treatments. Composites Part B: Engineering 114:15–22. doi:10.1016/j.compositesb.2017.02.001.
- Syazwani, N. S., M. E. Efzan, C. K. Kok, and M. J. Nurhidayatullaili. 2022. Analysis on extracted jute cellulose nanofibers by Fourier transform infrared and X-Ray diffraction. Journal of Building Engineering 48:103744. doi:10.1016/j.jobe.2021.103744.
- Teixeira, F. P., O. D. F. M. Gomes, and S. F. de Andrade. 2019. Degradation mechanisms of Curaua. Hemp, and Sisal Fibers Exposed to Elevated Temperatures BioResourses 14 (1):1494–511. doi:10.15376/biores.14.1.1494-1511.
- Teklu, T. 2021. Characterization of physico-chemical, thermal, and mechanical properties of Ethiopian sisal fibers. Journal of Natural Fibers 21 (2):1–12.
- Teklu T. (2022). Characterization of Physico-chemical, Thermal, and Mechanical Properties of Ethiopian Sisal Fibers. Journal of Natural Fibers, 19(10), 3825–3836. 10.1080/15440478.2020.1848730
- Thomason, J. L., and J. L. Rudeiros-Fernandez. 2022. Characterization of interfacial strength in natural fibre–polyolefin composites at different temperatures. Composite Interfaces 29 (2):175–96. doi:10.1080/09276440.2021.1913901.
- Totong, T. W., M. Wardiningsih, W. Al-Ayyuby, R. Wanti, and R. Rudy. 2021. Extraction and characterization of natural fiber from Furcraea Foetida leaves as an alternative material for textile applications. Journal of Natural Fibers 21 (4):1–12. doi:10.1080/15440478.2021.1904477.
- Tuerxun, D., T. Pulingam, N. I. Nordin, Y. W. Chen, J. B. Kamaldin, N. B. M. Julkapli, H. V. Lee, B. F. Leo, and M. R. B. Johan. 2019. Synthesis, characterization and cytotoxicity studies of nanocrystalline cellulose from the production waste of rubber-wood and kenaf-bast fibers. European Polymer Journal 116:352–60. doi:10.1016/j.eurpolymj.2019.04.021.
- Valasek, P., M. Muller, V. Sleger, V. Kolar, M. Hromasova, R. D’Amato, and A. Ruggiero. 2021. Influence of alkali treatment on the microstructure and mechanical properties of coir and abaca fibers. Materials 14 (10):2636. doi:10.3390/ma14102636.
- Valasek, P., M. Muller, and S. Vladimir. 2017. Influence of plasma treatment on mechanical properties of cellulose-based fibres and their interfacial interaction in composite systems. BioResources 12 (3):5449–61. doi:10.15376/biores.12.3.5449-5461.
- Verma, D., and K. L. Goh. 2021. Effect of mercerization/Alkali surface treatment of natural fibres and their utilization in polymer composites: Mechanical and morphological studies. Journal of Composite Science 5:175. doi:10.3390/jcs5070175.
- Vidyashri, V., H. Lewis, P. Narayanasamy, G. T. Mahesha, and K. S. Bhat. 2019. Preparation of chemically treated sugarcane bagasse fiber reinforced epoxy composites and their characterization. Cogent Engineering 6 (1):1708644. doi:10.1080/23311916.2019.1708644.
- Viel, Q., A. Esposito, J. M. Saiter, C. Santulli, and J. A. Turner. 2018. Interfacial characterization by pull-out test of bamboo fibers embedded in poly (lactic acid). Fibers 6 (1):1–7. doi:10.3390/fib6010007.
- Vineeth, K. V., and K. S. Senthil. 2020. Characterization of various properties of chemically treated allium sativum fiber for brake pad application. Journal of Natural Fibers 2 (19):1–14. doi:10.1080/15440478.2020.1745130.
- Wang, H., M. M. Kabir, and K. T. Lau. 2014. Hemp reinforced composites with alkalization and acetylation fibre treatments. Polymers and Polymer Compos 22 (3):247–52. doi:10.1177/096739111402200304.
- Wan, O. W. N., M. Jawaid, A. Almasri, K. H. P. S. Abdul, S. Suhaili, and A. R. Mohamed. 2012. Cell wall morphology, chemical and thermal analysis of cultivated pineapple leaf fibres for industrial applications. Journal of Polymers and the Environment 20 (2):404–11. doi:10.1007/s10924-011-0380-7.
- White, P. J., and P. Brown. 2010. Plant nutrition for sustainable development and global health. Annals of Botany 105 (7):1073–80. doi:10.1093/aob/mcq085.
- Yasin, P., M. Venkataramana, and S. K. Kudari. 2020. Physio-mechanical properties and thermal analysis of Furcraea Foetida Mediopicta (ffm) fibers: Its potential application as reinforcement in making of composites. International Conference on Emerging Trends in Engineering (ICETE), Springer: Berlin, Germany 2:492–500.
- Zaman, H. U., and R. A. Khan. 2021. Acetylation used for natural fiber/polymer composites. Journal of Thermoplastic Composite Materials 34 (1):3–23. doi:10.1177/0892705719838000.
- Zeriouh, A., and L. Belbirl. 1995. Thermal decomposition of a Moroccan wood under a nitrogen atmosphere. Thermochimica Acta 258:243–48. doi:10.1016/0040-6031(94)02246-K.
- Zhang, W., L. Li, W. Ou, L. Song, and Q. Zhang. 2018. Hydrophobic modification of hemp powders for their application in the stabilization of Pickering emulsions. Cellulose 25 (7):4107–20. doi:10.1007/s10570-018-1848-6.
- Zhang, J. C., and H. Zhang. 2008. Structure and performance of China hemp fiber and process technology. Chinese Polymer Bulletin 12:44–51.
- Zhang, H., and L. M. Zhang. 2009. Structure and properties of hemp fabric treated with chitosan and dyed with mixed epoxy‐modified silicone oil. Journal of Applied Polymer Science 114 (3):1377–83. doi:10.1002/app.30607.
- Zhang, L., J. Zhong, and X. Ren. 2017. Natural fiber-based biocomposites. Green Biocomposites Springer International Publishing Springer International Publishing 16 (10):31–70.
- Zouari, M., D. B. Devallance, and L. Marrot. 2022. Effect of biochar addition on mechanical properties, thermal stability, and water resistance of hemp-polylactic acid (PLA) composites. Materials 15 (6):2271. doi:10.3390/ma15062271.