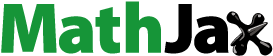
ABSTRACT
Increasing demand for bio-degradable, eco-friendly, and sustainable textile products to confront environmental pollution accelerates the research on natural fibers. Researchers are also in search of novel natural fibers to be used in different textile products. The present study attempts to extract textile-grade novel Bauhinia vahlii fibers (BVFs) from the Bauhinia vahlii (BV) plant bark. Textile grade BVFs were obtained by treating the BV plant bark with 15% (w/w) sodium hydroxide solution (NaOH) at 95°C for 2 h, followed by manual fiber extraction. The extracted BVFs were analyzed for physical, chemical, morphological, structural, mechanical, and thermal characteristics. Fourier transform infrared (FTIR) spectroscopy and chemical analysis revealed that the extracted fiber contains 75.8% holocellulose and 13.7% lignin. The physical analysis demonstrated that BVFs have 10.5% moisture content, 1.47 gm/cm3 fiber density, and 15.77 microns average fiber fineness. X-ray diffraction (×RD) confirmed that BVFs have 56% crystallinity. Thermogravimetric study revealed that the BVFs could be thermally stable up to 233.4°C. Outcomes of all the analyzes indicate that the extracted fiber can be used to convert them into yarn by blending with some short-staple fiber.
摘要
为应对环境污染,人们对可生物降解、环保和可持续的纺织品的需求不断增加,这加速了对天然纤维的研究. 研究人员也在寻找用于不同纺织产品的新型天然纤维. 本研究试图从紫荆(BV)植物树皮中提取纺织级新型紫荆纤维(BVF). 通过在95°C下用15%(w/w)氢氧化钠溶液(NaOH)处理BV植物树皮2小时,然后手动提取纤维,获得纺织级BVF. 对提取的BVF进行物理、化学、形态、结构、机械和热特性分析. 傅里叶变换红外光谱和化学分析表明,提取的纤维含有75.8%的全纤维素和13.7%的木质素. 物理分析表明,BVF的含水量为10.5%,纤维密度为1.47 gm/cm3,平均纤维细度为15.77微米。X射线衍射(XRD)证实BVF具有56%的结晶度. 热重分析表明,BVF的热稳定性可达233.4°C. 所有分析的结果表明,提取的纤维可以通过与一些短纤维混合而转化为纱线.
Introduction
The story of natural fibers used by humans dates back to prehistoric times to endure adverse weather conditions. Until around a century ago, the only fibers used by human beings were natural to beautify the environment and for clothing. Humans made advancements with time in the realm of textiles and developed synthetic fibers. In the last 50 years, the production of synthetic fibers has increased significantly and captured the textile market for their low cost, uniform quality, and excellent durability. However, synthetic fibers are non-biodegradable and provide less comfort compared to natural fibers. Moreover, issues like increasing carbon footprint, climatic changes, and environmental pollution due to manufacturing, usage, and disposal of excessive synthetic textile materials have emerged (Ramasamy and Subramanian Citation2021). Since then, customer demand for biodegradable and sustainable textiles has grown considerably. Manufacturers are thus focusing on products manufactured from bio-based renewable resources, i.e., from natural fibers. Plants are the primary source of natural fibers. Researchers are also working on different natural fiber-based products and searching for novel plant-based natural fibers to neutralize people’s growing concerns about sustainability.
Bauhinia vahlii (BV) is a fast-growing, woody climber of the legume family. It is also among the most abundant Indian bauhinia species, as shown in . Bauhinia recemosa, the other name of the BV plant, is generally found in the world’s warmer regions, mainly in Asia, Africa, and South America (Chauhan and Saklani Citation2013). In India, this plant is native to the sub-Himalayan region as well as Chhattisgarh, Madhya Pradesh, Bihar, Odisha, and West Bengal. Bauhinia vahlii plant leaves are used to make plates and bark to make simple household products by the tribal people of Odisha for their livelihood. Leaves and bark extract of the BV plant have potential antioxidant and antimicrobial properties (Bar and Bar Citation2020).
Lignocellulosic fibers are a naturally occurring composite in which cellulosic fibrils are embedded in the lignin matrix. Besides cellulose, lignin, hemicellulose, pectin, and wax are the other significant components of lignocellulosic fibers (John and Thomas Citation2008). Hemicellulose is highly hydrophilic and undergoes easy dissolution under alkaline conditions. Lignin is considered as a three-dimensional copolymer comprising aliphatic and aromatic compounds. The main problem with lignin chemistry is that it cannot be isolated to its native state. It is entirely amorphous and hydrophobic and becomes soluble under hot alkaline conditions (Olesen and Plackett Citation1999). Conventionally, lignocellulosic and bast fibers were extracted through the water retting process. Dew retting is also an alternative and sustainable way of lignocellulosic fiber extraction. However, due to longer time requirements and water pollution problems in water retting, researchers developed alternative fiber extraction methods, including decortication, post decortication cleaning, enzymatic retting, chemical retting, etc. To get better fiber quality and higher fiber yield, single or multiple methods can be employed to extract the lignocellulosic fiber depending on the fiber type. In the case of fibers having higher lignin content, to scrape away excess lignin from the fiber, degumming is carried out to convert them into a textile-grade fiber. Degumming includes alkali, acid, and emulsion treatments (Kale, Alemayehu, and Gorade Citation2020).
Initial attempts have been made to extract the BVFs from the BV plant bark for fiber-reinforced composite. Kumar et al. (Citation2021) manually extracted the fiber bundles from the BV plant bark and treated them with 5% NaOH solution for 8 h at ambient temperature for surface modification. Bauhinia vahlii mat reinforced composite was developed from the treated fiber strand. Stalin and Ramkumar (Citation2015) have prepared Bauhinia recemosa fiber-reinforced polyester composites from the dried and staple Bauhinia recemosa plant bark of 30 mm in length. Ray et al. (Citation2020) have also extracted BV fiber strands by hammering the BV bark, followed by surface modification. Till now, BVFs have been extracted in significantly coarser fiber strand form and used for making fiber-reinforced composite only. According to the available literature, no effort has been made to extract textile-grade BV fibers. There is a huge scope to explore this fiber further for use in textile products. The present study focuses on the extraction and characterization of textile-grade BVFs fiber from BV bark. Characterization of the fiber includes physical, chemical, morphological, structural, mechanical, and thermal analysis.
Material and methods
Materials
Bauhinia vahlii plant bark was supplied by District Rural Development Agency, Mayurbhanj, Odisha, India. Sodium hydroxide and acetic acid are used of Rankem, Maharashtra, India.
Fiber extraction process
To extract BV bast fiber, at first barks were sliced into 30–40 centimeters in length. Bark pieces were manually cleaned to remove the immature and woody parts, followed by dipping them into the water for 1 day at ambient temperature to soften the bark structure. Soft bark samples were treated with 15% (w/w) NaOH solution at around 95°C for 2 h to remove the lignin and other contaminants. Causticized samples were washed and passed through the padding mangle at a pressure of 3 bar to squeeze out the gummy substances from the bark. The squeezing process was repeated twice, followed by washing at 100°C for 30 min. The washed bark samples were neutralized with acetic acid. The final removal of leftover gummy substances from the bark was carried out by scraping with a teaspoon or simple knife. At this stage, the presence of impurities and gummy substances was minimal. The fiber layers were separated manually from the processed bark. Dried fiber layers were cut into a length of approximately 5 cm, and further fiber strands were separated in a width-wise direction. The extracted fiber was further opened by hand carding. The process sequence of fiber extraction is shown in .
Figure 2. Stepwise extraction process of BVFs: (a) collected BV bark, (b) treating with NaOH solution at 95°C, (c) removal of the gummy substance by scraping with a simple knife, (d) separation of fiber layers, (e) fiber layer cut into smaller pieces, (f) manually extracted fiber, (g) hand carding of the fiber, and (h) final fiber after hand carding.
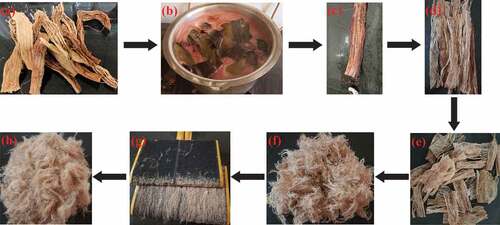
Physical property analysis
Mean fiber length was determined by randomly selecting 100 fibers from a tuft of BV fiber sample. Each fiber sample was straightened and the length was measured using a measuring scale. Mean fiber length, standard deviation (SD), and coefficient of variation (CV) were calculated from the measured fiber length. The fineness of the BVFs was determined utilizing an optical fiber diameter analyzer (OFDA 4000, BSC Electronics, Australia). The density of the BVFs (ρf) was quantified according to the ASTM-D3800–99 method using the below equation (Tamanna et al. Citation2021). A tuft of BVFs was weighed in air and subsequently in methanol using a 0.5 mm diameter copper suspension wire:
where W1, W2, W3, and W4 are the weight of copper wire in the air, copper wire in liquid up to the immersion point, fiber tuft along with copper wire in the air, and fiber tuft along with suspension wire in liquid, respectively. The specific density of methanol (ρl) is 0.79 g/ml.
Morphological characterization
A SEM (Zeiss, EVO 50) at different magnification levels was operated at 20 kv accelerating voltage to examine surface morphology and cross-sectional view of BVFs. For cross-sectional view, fibers were inserted inside a cork with the help of a sharp needle. Then, the cork and the fibers were finely sliced perpendicular to the axis of the fibers using a sharp blade. A thin layer of gold coating was applied to the fiber sample to avoid the accumulation of electrical charges.
Fourier transform-infrared analysis
The FTIR spectra of the BVFs were captured on a thermo FTIR (model Nicolet iS-50) from 400 to 4000 cm−1 wavenumber to detect the functional group present in the fiber. A KBr pallet was prepared by mixing and compressing one part of finely chopped BVFs powder with nine parts of KBr, and it was used for FTIR analysis.
X-ray diffraction analysis
The crystallinity index (CI) of BVFs was estimated using an X-ray diffractometer (×’pert PRO, PANalytical) with a scanning velocity of 2 degrees/minute and an X-ray of 0.154 nm wavelength. Finely crushed BVFs powder was used for the analysis. The crystallinity index of BVFs was computed using the area method as per the equation below (Ling et al. Citation2019):
OriginPro software was used to measure the area underneath the crystalline peak region (ACrystalline) and total area (ATotal) beneath the X-ray spectra. The interplanar spacing of BVFs was estimated at various lattice planes employing Bragg’s equation (Kumar and Das Citation2016):
where dhkl stands for an interplanar distance of hkl crystallographic planes, θ signifies Bragg’s angle, λ symbolizes the X-ray wavelength, and n defines the diffraction order. The crystallite size (CS) of the BVFs was determined using Scherrer’s equation (Elenga et al. Citation2009):
where K is Scherrer’s constant having a value of 0.89, β stands for peak’s full-width at half-maximum in radian.
Chemical analysis
Bauhinia vahlii fiber was analyzed to determine their chemical components, using the process mentioned by Sengupta, Mazumdar, and Macmillan (Citation1958). The acid-insoluble klason lignin was quantified using the TAPPI method (T 222 om-06). Pectin was isolated from the BVFs by treating the fiber with ethylene diamine tetraacetic acid at boiling temperature for 45 min (Wang et al. Citation2015). The moisture content percentage of BVFs was calculated using the below formula (Sathishkumar et al. Citation2013):
Mechanical characterization
The tensile strength and breaking elongation of BVFs were measured using a tensile tester (Vibrodyn 500, Lenzing Instruments) as per the standard (ASTM D3822-01) with a gauge length and crosshead speed of 10 mm and 0.1 mm/minute, respectively. Twenty fibers were tested, having a fiber length of 25–30 mm, and their diameter was assessed in three distinct places using digital projection of paramount (Bar et al. Citation2021).
Thermogravimetric analysis
The thermal properties of the BVFs were studied by thermogravimetric (TG) and derivative thermogravimetric (DTG) assessment using a simultaneous thermal analyzer SDT650. The test was carried out for BVFs from ambient temperature to 750°C with a 10°C per minute scanning rate. OriginPro software calculated initial and maximum decomposition temperatures, weight loss percentage, and ash content. The kinetic activation energy (Ea) of BVFs was calculated according to the Broido’s equation as mentioned below (Md et al. Citation2022):
where y represents normalized weight [ratio of weight at any temperature to initial weight], R is the gas constant (8.314 J/mol K), T is the temperature in Kelvin, and K is the constant of the reaction rate.
Results and discussion
Physical property analysis
Fiber length and fineness are the two important characteristics of any staple fiber for their spinnability. The lengths of BVFs vary from 9 to 32 mm, with an average value of 20.05 mm. The average length of BVFs is slightly shorter than the cotton (20–35 mm) fiber (Wang and Wang Citation2009). depicts the distribution of fibers length of randomly selected 100 BV fibers. The SD and CV of the measured fibers are 5.67 mm and 28.28%, respectively. demonstrates the distribution of BV fibers’ fineness. The fineness of 95% BV fibers ranges from 4 to 34 microns, with an average fiber fineness of 15.77 microns comparable to the cotton fiber (12–38 microns). Only 5% of fibers are coarser than 33.57 microns. The calculated spin fineness of BVFs is below 25.6 microns, with 91.8% of fibers falling within this limit. The comfort factor of the BVFs as per the mean fiber fineness is 93.8%, as quantified using an optical fiber diameter analyzer. The average aspect ratio of BVFs is 1271, more than the minimum fiber length to diameter ratio required to convert the fibers into yarn. The density of BVFs is 1.47 gm/cm3 as determined using Archimedes’ buoyancy method. It is very close to that of other cellulosic fibers, such as cotton, jute, hemp, flax, sisal, and nettle. Comparative data of fiber fineness and fiber density are tabulated in .
Table 1. Properties of BVFs in comparison to other natural cellulosic fibers.
Morphological characteristics
depicts a SEM image of BV fibers extracted with 15% NaOH at 1500X magnification. The causticizing process removed a considerable amount of lignin and pectin from the fiber matrix, enabling the fibers’ separation, as seen in the image (Kumar and Das Citation2016). Though the maximum impurities have already been removed from the fiber surface, surface roughness, and fragmented impurities can still be visible. Further removal of lignin and other contaminants may cause structural damage to the fiber (Kumar and Das Citation2016). Fiber surface roughness reduces the fiber-to-fiber slippage in the yarn due to better mechanical interlocking and enhances the yarn’s mechanical characteristics (Yao and Chen Citation2013). depicts a cross-sectional view of the extracted BV fibers. Fiber cross-sections range from circular to flat oval. An eye-shaped lumen can be seen in a few fiber samples. The shape factor (q) of the BVFs was calculated by implementing the below equation (Neckář and Das Citation2012):
where p stands for perimeter and d symbolizes the equivalent diameter of the fiber. The value of p and d was measured using MIPAR image analysis software. The shape factor of the BVFs is 0.1232. In the case of circular, square, hexagonal, or triangular cross-sections, the shape factor will be 0.0, 0.1281, 0.1547, or 0.2858, respectively (Kumar and Das Citation2016).
Fourier transform-infrared analysis
As illustrated in , the FTIR spectrum helps identify the functional groups present in the BVFs. Stretching of the aromatic ring of lignin is seen at around 3650–4000 cm−1, which validates the existence of lignin in the BVFs (Ray et al. Citation2020). A broad and deep absorbance peak that appeared at 3342 cm−1 corresponds to O–H bond stretching and confirms the presence of α–cellulose (Hyness et al. Citation2018; Vijay et al. Citation2021). Another absorbance peak observed at 2900 cm−1 is characteristic of the stretching vibration of the C–H bond, which strengthens the presence of cellulose and hemicellulose in the BVFs (Vijay et al. Citation2021). A narrow peak spotted at 1634 cm−1 is linked to the vibration of absorbed water in cellulose as well as C=O stretching of lignin (Hyness et al. Citation2018). The peak that appeared at 1427 cm−1 is connected to the CH2 symmetric bending of cellulose (Chand and Fahim Citation2008). The peak at 1370 and 1316 cm−1 are linked to –CH bending vibration and C–O stretching of aromatic rings of cellulose polysaccharides, respectively (Zhuang et al. Citation2020). Peak noticed at 1204 cm−1 is assigned to –COO vibration of the acetyl group of hemicellulose (Reddy et al. Citation2013). The peak noticed at 1110 cm−1 is attributed to in-plane deformation of the aromatic C–H bond within lignin (Zhuang et al. Citation2020). An intense absorbance peak observed at 1058 cm−1 and a small peak at 1036 cm−1 represented symmetric C–O-H stretching of lignin (Maheshwaran et al. Citation2018). The infra-red absorption bands at 1162 and 898 cm−1 are attributed to C–O–C stretching at β-(1–4)-glycosidic linkages of cellulose and hemicellulose (Baskaran et al. Citation2018). The Fourier transform-infrared spectrum of BVFs confirms that the fiber contains cellulose, hemicellulose, and lignin.
X-ray diffraction analysis
An X-ray diffractogram of BVFs is illustrated in . X-ray diffraction pattern of BVFs shows two major diffraction peaks at 2θ of about 15.23° and 22.79°Correspond to (1 0 1) and (0 0 2) crystal lattice plane sequentially (Bar et al. Citation2021). The broad peak detected at 2θ = 15.23° confirms the presence of hemicellulose, lignin, pectin, and amorphous cellulose (Baskaran et al. Citation2018). The sharp peak observed at 2θ = 22.79°Characterizes the lattice plane of cellulose I (Vijay et al. Citation2021). The crystalline region of BVFs is lying in-between 2θ = 19.65° to 25.21° and 2θ = 13.17° to 17.97°. The crystallinity index of BVFs is estimated as 56%, which is very close to the cotton fiber. The crystallinity index of BVFs is compared with other natural cellulosic fibers used in conventional textile materials and is tabulated in . The interplanar or lattice plane spacing in the above-mentioned diffraction peaks is computed using Bragg’s equation and determined to be 0.58 and 0.39 nm sequentially. The crystal lattice planes are very close and tightly packed at 2θ of 22.79°Compared to 15.23° (Kumar and Das Citation2016). The crystallite sizes of the BVFs determined against (1 0 1) and (0 0 2) crystal lattice planes are 3.85 and 2.56 nm, respectively. The average crystallite size of BVFs is 3.2 nm, smaller than the Indian cotton fiber of 5.5 nm, cornstalk fiber of 3.8 nm, ramie of 16 nm (Elenga et al. Citation2009), and jute of 3.58 nm (Wang et al. Citation2019). However, it is slightly larger than that of flax 2.8 nm (Tamanna et al. Citation2021). The average crystallite size of BVFs is close to the other conventional natural cellulosic fibers used to produce yarns and fabrics. Fibers having equivalent crystallinity and lower crystallite size increase the chemical reactivity as well as moisture absorption capacity due to its larger total surface area compared to bigger crystallite sizes (Elenga et al. Citation2009).
Chemical analysis
The physical properties of any fiber depend on its chemical constituents. Further, the chemical composition of lignocellulosic fiber is affected not only by the kind of plant but also on the geographical location and climatic condition where the plant grows, the plant’s age, and the fiber extraction method (Baskaran et al. Citation2018). Bauhinia vahlii fiber was extracted with 15% NaOH solution containing 75.8% holocellulose, of which 65.2% was α-cellulose and 10.6% hemicellulose. The α-cellulose content of BVFs is very much comparable with other lignocellulosic fibers, whereas hemicellulose content is lower than that of flax, jute, hemp, and sisal. Bauhinia vahlii fiber also contained 13.7% acid insoluble klason lignin, which is also lower than the flax, jute, and kenaf fiber, as concluded in . Bauhinia vahlii fiber also contained 1.8% pectin. The moisture content of the BVFs is measured as 10.5%, which is higher than the cotton fiber and at par with other natural cellulosic fibers, also tabulated in . The lower crystallinity and crystallite size of BVFs enhance the moisture absorption in the fiber (Elenga et al. Citation2009).
Table 2. Chemical composition of BVFs in comparison to other natural cellulosic fibers.
Tensile strength
The tensile property of fibers mainly depends on their chemical components and their percentage. For natural cellulosic fibers, cellulose microfibrils act as a load-bearing component and give structural integrity to the fiber. The strength of a fiber depends on its microfibril angle as well as its orientation in the cell wall (Petroudy Citation2017). The microfibril angle (α) is derived by applying the global deformation (ε) equation (Maheshwaran et al. Citation2018).
L0 is the gauge length in mm, and ΔL is the breaking elongation in mm. The microfibril angle of BVFs varies from 12.43° to 20.41°, which is higher than other natural cellulosic fibers like jute (8.1°), ramie (8°), flax (5°), hemp (6.2°), and very similar to sisal (10°–25°), cotton (14.6°–23.8°) (Maheshwaran et al. Citation2018; Petroudy Citation2017). The fiber sample mounted for testing and the tensile strength–elongation curve of BVFs is shown in . It was observed from the tensile strength-elongation graph that the curve is slightly concave to the elongation axis, like the other natural cellulosic fibers. The tensile strength and elongation have a linear relationship (Eyupoglu Citation2022). The average breaking strength of BVFs is 187 Mpa. The tensile strength of BVFs is a little less compared to other natural cellulosic fibers due to their very fine mesh structure and higher microfibril angle. The higher microfibril angle also indicates that the BVFs is less stiff than the jute and flax fiber (Petroudy Citation2017). The breaking elongation of BVFs varies from 2.4% to 6.7%, with an average breaking elongation of 4.4%, which is higher than the flax, jute, hemp, sisal, and kenaf fiber and lower than cotton fiber. compares tensile strength and breaking elongation of BVFs with other fibers.
Thermogravimetric analysis
Thermogravimetric and derivative thermogravimetric curves were derived from the thermal study of BVFs from ambient temperature to 750°C, as illustrated in . Thermogravimetric analysis curve of BVFs exhibits multiple phases of degradation with an increase in temperature. In the first phase of degradation, two small endothermic peaks are seen in the DTG curve at 59°C and 151°C, which is attributed to the evaporation of moisture and elimination of structurally bound water molecules in the fiber (Alwani et al. Citation2014; Legrand et al. Citation2020). Till 159°C, 9.83% weight loss is observed. From 159°C to 233.4°C, the BVFs is thermally stable, having a minimal weight loss of 0.55%. Textile materials manufactured from BVFs can be processed or ironed at this temperature. In the second phase of degradation, which starts from 233.4°C, weight loss of 62.05% is noticed, which refers to the disintegration of hemicellulose, glycosidic linkages of cellulose, cellulose I, and α-cellulose (Belouadah, Ati, and Rokbi Citation2015). A deep endothermic peak at 368°C is attributed to the higher decomposition rate. The decomposition rate is reduced in the third phase of degradation, which ranges from 385°C to 696°C with 11.92% weight loss, which is associated with the decomposition of residual cellulose, lignin, and aromatics contained in BVFs (Legrand et al. Citation2020). The endothermic peak observed at 491°C links to maximal lignin degradation and thermal depolymerization of wax (Maheshwaran et al. Citation2018). Lignin decomposes slowly compared to cellulose and hemicellulose over a broad range of temperatures owing to several functional groups having varied thermal stabilities present in the fiber (Brebu and Vasile Citation2010). At 740°C, char content is 15.65%. The minimum energy required for the degradation of the fiber at a certain temperature is known as kinetic activation energy (Ea). The Ea of BVFs is 96.18 KJ/mol, as calculated from the Broido’s plot shown in . The Ea of BVFs is within the range that of the other natural fibers (60–170 KJ/mol) (Md et al. Citation2022).
Conclusion
Successful extraction of BVFs has been accomplished from the BV plant bark using 15% NaOH solution at 95°C. The morphological study reveals that the fiber surface has natural roughness, and the cross-sectional view varies from circular to flat oval. The fineness and the density of the BVFs are very close to the cotton fiber, and the average fiber length is slightly shorter than the cotton fiber. The FTIR and the chemical analysis have confirmed that extracted BVFs are rich in cellulose content. X-ray analysis of BVFs is exposed that it has 56% crystallinity, and the crystallite size of BVFs is smaller than the cotton fiber, which enhances its moisture absorption capacity as well as its reactivity. The thermogravimetric analysis proclaimed that BVFs is thermostable up to 233.4°C, and physical and chemical processing of this fiber can be done up to this temperature. The average tensile strength of the BVFs is 187 Mpa with 4.4% average breaking elongation. Findings of all the analyzes suggest that the extracted fiber can be used to convert them into yarn by blending with some short-staple cellulosic fiber-like cotton with a lower blend ratio keeping tensile strength into consideration.
Highlights
Textile-grade novel Bauhinia Vahlii fiber (BVFs) were extracted by treating the Bauhinia Vahlii plant bark with 15% (w/w) sodium hydroxide solution at 95°C for 2 h with a 1:40 material to liquor ratio, followed by manual extraction of the fiber.
The average fineness and the density of the BVFs are 15.77 microns and 1.47 gm/cm3, respectively. The mean fiber length of BVFs is 20.05 mm. BVFs contain 65.2% cellulose, 10.6% hemicellulose, 13.7% lignin, and 10.5% moisture. The average tensile strength of the BVFs is 187 Mpa with a 4.4% average breaking elongation.
BVFs have 56% crystallinity. The average crystallite size is 2 nm, smaller than the cotton fiber’s, enhancing moisture absorption capacity and reactivity.
BVFs are thermally stable up to 233.4°C.
Findings of all the analyzes suggest that the extracted fiber can be used to convert them into yarn by blending with some short-staple cellulosic fiber like cotton with a lower blend ratio keeping the fiber length and tensile strength into consideration. Introduction
Ethical approval
This article does not contain any studies with human or animal subjects. Hence, ethical approval is not applicable.
Acknowledgment
The authors want to thank the CRF, IIT Delhi, for extending their support in material testing.
Disclosure statement
No potential conflict of interest was reported by the authors.
Additional information
Funding
References
- Alwani, M. S. Alwani, H. P. S. A. Khalil, O. Sulaiman, M. N. Islam, and R. Dungani. 2014. An approach to using agricultural waste fibres in biocomposites application: Thermogravimetric analysis and activation energy study. BioResources 9 (1):218–16. doi:10.15376/biores.9.1.218-230.
- Amutha, V., and B. Senthilkumar. 2021. Physical, chemical, thermal, and surface morphological properties of the bark fiber extracted from Acacia concinna plant. Journal of Natural Fibers 18 (11):1661–74. doi:10.1080/15440478.2019.1697986.
- Bar, G., and M. Bar. 2020. Dyeing and flame-retardant finishing of silk fabric: An ecofriendly approach. SN Applied Sciences 2 (3):3. doi:10.1007/s42452-020-2114-8.
- Bar, M., H. Belay, A. Ramasamy, A. Das, and P. Ouagne. 2021. Refining of banana fiber for load bearing application through emulsion treatment and its comparison with other traditional methods. Journal of Natural Fibers 1–18. doi:10.1080/15440478.2021.1902901.
- Baskaran, P. G., M. Kathiresan, P. Senthamaraikannan, and S. S. Saravanakumar. 2018. Characterization of new natural cellulosic fibre from the bark of Dichrostachys cinerea. Journal of Natural Fibers 15 (1):62–68. doi:10.1080/15440478.2017.1304314.
- Belouadah, Z., A. Ati, and M. Rokbi. 2015. Characterization of new natural cellulosic fiber from Lygeum Spartum L. Carbohydrate Polymers 134 (10):429–37. doi:10.1016/j.carbpol.2015.08.024.
- Brebu, M., and C. Vasile. 2010. Thermal degradation of lignin – a review. Cellulose Chemistry and Technology 44 (9):353–63.
- Chand, N., and M. Fahim. ed., 2008. Natural fibers and their composites. in Tribology of Natural Fiber and Polymer Composites 1–58. Woodhead Publishing. doi:10.1533/9781845695057.1.
- Chauhan, R., and S. Saklani. 2013. Bauhinia Vahlii: Plant to be explored. International Research Journal of Pharmacy 4 (8):5–9. doi:10.7897/2230-8407.04802.
- Elenga, R. G., G. F. Dirras, J. G. Maniongui, P. Djemia, and M. P. Biget. 2009. On the microstructure and physical properties of untreated raffia textilis fiber. Composites Part A Applied Science and Manufacturing 40 (4):418–22. doi:10.1016/j.compositesa.2009.01.001.
- Eyupoglu, S. 2021. Characterization of a Novel Cellulosic Fiber from Brassica oleracea Var. Italic Stem. Journal of Natural Fibers 1–11. doi:10.1080/15440478.2021.1950098.
- Eyupoglu, S. 2022. Characterization of New Cellulosic Fibers Obtained from Zingiber Officinale. Journal of Natural Fibers 19 (4):1287–96. doi:10.1080/15440478.2020.1764452.
- Eyupoglu, S., and C. Eyupoglu. 2022. Investigation of a New Natural Cellulosic Fiber Extracted from Beetroot Plant. Journal of Natural Fibers 1–12. doi:10.1080/15440478.2022.2108956.
- Eyupoglu, S., and N. Merdan. 2021a. Physicochemical Properties of New Plant Based Fiber from Lavender Stem. Journal of Natural Fibers 1–11. doi:10.1080/15440478.2021.1982816.
- Eyupoglu, S., and N. Merdan. 2021b. Investigation of the characteristic and sound absorption properties of a new cellulose-based fiber from Alcea rose L. plant. Journal of Natural Fibers 1–12. doi:10.1080/15440478.2021.1993481.
- Gopi Krishna, M., C. Kailasanathan, and B. NagarajaGanesh. 2022. Physico-chemical and morphological characterization of cellulose fibers extracted from Sansevieria roxburghiana Schult. & Schult. F leaves. Journal of Natural Fibers 19 (9):3300–16. doi:10.1080/15440478.2020.1843102.
- Hyness, N. R. J., N. J. Vignesh, P. Senthamaraikannan, S. S. Saravanakumar, and M. R. Sanjay. 2018. Characterization of new natural cellulosic fiber from Heteropogon contortus plant. Journal of Natural Fibers 15 (1):146–53. doi:10.1080/15440478.2017.1321516.
- Jawaid, M., L. K. Kian, H. Fouad, N. Saba, O. Y. Alothman, and M. Hashem. 2021. New cellulosic fibers from washingtonia tree agro-wastes: Structural, morphological, and thermal properties. Journal of Natural Fibers 1–11. doi:10.1080/15440478.2021.1875374.
- John, M., and S. Thomas. 2008. Biofibres and biocomposites. Carbohydrate Polymers 71 (3):343–64. doi:10.1016/j.carbpol.2007.05.040.
- Kale, R. D., T. G. Alemayehu, and V. G. Gorade. 2020. Extraction and characterization of lignocellulosic fibers from Girardinia bullosa (steudel) wedd. (Ethiopian kusha plant). Journal of Natural Fibers 17 (6):906–20. doi:10.1080/15440478.2018.1539940.
- Khan, A., V. Raghunathan, D. L. Singaravelu, M. R. Sanjay, S. Siengchin, M. Jawaid, K. A. Alamry, and A. M. Asiri. 2022. Extraction and characterization of cellulose fibers from the stem of momordica charantia. Journal of Natural Fibers 19 (6):2232–42. doi:10.1080/15440478.2020.1807442.
- Kumar, N., and D. Das. 2016. Alkali treatment on nettle fibers. The Journal of the Textile Institute 108 (8):1461–67. doi:10.1080/00405000.2016.1257346.
- Kumar, S., V. K. Patel, K. K. S. Mer, B. Gangil, T. Singh, and G. Fekete. 2021. Himalayan natural fiber-reinforced epoxy composites: Effect of Grewia optiva/Bauhinia vahlii fibers on physico-mechanical and dry sliding wear behavior. Journal of Natural Fibers 18 (2):192–202. doi:10.1080/15440478.2019.1612814.
- Kumar, R., S. Sivaganesan, P. Senthamaraikannan, S. S. Saravanakumar, A. Khan, S. A. A. Daniel, and L. Loganathan. 2022. Characterization of new cellulosic fiber from the bark of Acacia nilotica L. plant. Journal of Natural Fibers 19 (1):199–208. doi:10.1080/15440478.2020.1738305.
- Legrand, N. B. R., M. Lucien, O. Pierre, B. E. Fabien, N. P. Marcel, and A. A. Jean. 2020. Physico-chemical and thermal characterization of a lignocellulosic fiber, extracted from the bast of cola lepidota stem. Journal of Minerals and Materials Characterization and Engineering 8 (5):377–92. doi:10.4236/jmmce.2020.85024.
- Ling, Z. Ling, T. Wang, M. Makarem, M. Santiago Cintrón, H. N. Cheng, X. Kang, M. Bacher, A. Potthast, T. Rosenau, et al. 2019. Effects of ball milling on the structure of cotton cellulose. Cellulose. 26(1):305–28. doi:10.1007/s10570-018-02230-x.
- Maheshwaran, M. V., N. R. J. Hyness, P. Senthamaraikannan, S. S. Saravanakumar, and M. R. Sanjay. 2018. Characterization of natural cellulosic fiber from epipremnum aureum stem. Journal of Natural Fibers 15 (6):789–98. doi:10.1080/15440478.2017.1364205.
- Md, J. S., S. Madhu, K. Chakravarthy, and J. S. N. Raju. 2022. “Characterization of natural cellulose fibers from the stem of Albizia Julibrissin as reinforcement for polymer composites. Journal of Natural Fibers 19 (6):2204–17. doi:10.1080/15440478.2020.1807440.
- Mewoli, A. E., C. Segovia, F. B. Ebanda, A. Ateba, P. M. A. Noah, B. Ndiwe, and A. E. Njom. 2020. Physical-chemical and mechanical characterization of the bast fibers of Triumfetta cordifolia A. rich. from the equatorial region of cameroon. Journal of Minerals and Materials Characterization and Engineering 8 (4):163–76. doi:10.4236/jmmce.2020.84011.
- Moshi, A. A. M., D. Ravindran, S. R. S. Bharathi, V. Suganthan, and G. K. S. Singh. 2019. “Characterization of new natural cellulosic fibers – a comprehensive review”. IOP Conference Series: Materials Science and Engineering, Kanchipuram, India, 574:1–11 doi:10.1088/1757-899X/574/1/012013.
- Neckář, B., and D. Das, ed. 2012. Theory of structure and mechanics of fibrous assemblies: Basic properties of single fibers and fibrous assemblies 1–28. New Delhi: Woodhead Publishing India Pvt. Ltd. doi:10.1201/9780367805548.
- Olesen, P. O., and D. V. Plackett. 1999. Perspectives on the performance of natural plant fibres. The Natural Fibres Performance Forum, Copenhagen, Denmark, May 27-28.
- Petroudy, S. R. D. 2017. Physical and mechanical properties of natural fibers. In Book advanced high strength natural fibre composites in construction, ed. M. Fan and F. Fu, 59–83. Woodhead Publishing. doi: 10.1016/B978-0-08-100411-1.00003-0.
- Rajeshkumar, G., G. L. Devnani, J. P. Maran, M. R. Sanjay, S. Siengchin, N. A. Al-Dhabi, and K. Ponmurugan. 2021. Characterization of novel natural cellulosic fibers from purple bauhinia for potential reinforcement in polymer composites. Cellulose 28 (9):5373–85. doi:10.1007/s10570-021-03919-2.
- Raju, J. S. N., M. V. Depoures, J. Shariff, and S. Chakravarthy. 2021. Characterization of natural cellulosic fibers from stem of symphirema involucratum plant. Journal of Natural Fibers 1–16. doi:10.1080/15440478.2021.1875376.
- Ramasamy, R., and R. B. Subramanian. 2021. Synthetic textile and microfiber pollution: A review on mitigation strategies. Environmental Science and Pollution Research 28 (31):41596–611. doi:10.1007/s11356-021-14763-z.
- Ray, R., S. N. Das, A. Mohapatra, and H. C. Das. 2020. Comprehensive characterization of a novel natural Bauhinia Vahlii stem fiber. Polymer Composites 41 (9):3807–16. doi:10.1002/pc.25678.
- Reddy, K. O., K. R. N. Reddy, J. Zhang, J. Zhang, and A. V. Rajulu. 2013. Effect of alkali treatment on the properties of Century fiber. Journal of Natural Fibers 10 (3):282–96. doi:10.1080/15440478.2013.800812.
- Reddy, N., and Y. Yang. 2008. Characterizing natural cellulose fibers from velvet leaf (Abutilon theophrasti) stems. Bioresource Technology 99 (7):2449–54. doi:10.1016/j.biortech.2007.04.065.
- Sathishkumar, T. P., P. Navaneethakrishnan, S. Shankar, and R. Rajasekara. 2013. Characterization of new cellulose Sansevieria ehrenbergii fibers for polymer composites. Composite Interfaces 20 (8):575–93. doi:10.1080/15685543.2013.816652.
- Sengupta, A. B., S. K. Mazumdar, and N. G. Macmillan. 1958. Isolation of jute holocellulose by the action of sodium chlorite. Indian Journal of Applied Chemistry 21:105–10.
- Sreenivas, H. T., N. Krishnamurthy, and G. R. Arpitha. 2020. A comprehensive review on light weight kenaf fiber for automobiles. International Journal of Lightweight Materials and Manufacture 3 (4):328–37. doi:10.1016/j.ijlmm.2020.05.003.
- Stalin, B., and R. Ramkumar. 2015. Mechanical properties of Bauhinia racemosa fiber reinforced with polymer composites. International Journal of Applied Engineering Research 10 (51):701–05.
- Stevulova, N., J. Cigasova, P. Purcz, I. Schwarzova, F. Kacik, and A. Geffert. 2015. Water absorption behavior of hemp hurds composites. Materials 8 (5):2243–57. doi:10.3390/ma8052243.
- Tamanna, T. A., S. A. Belal, M. A. H. Shibly, and A. N. Khan. 2021. Characterization of a new natural fiber extracted from Corypha taliera fruit. Scientific reports 11 (1):1–12. doi:10.1038/s41598-021-87128-8.
- Vijay, R., J. D. J. Dhilip, S. Gowtham, S. Harikrishnan, B. Chandru, M. Amarnath, and A. Khan. 2022. Characterization of natural cellulose fiber from the barks of vachellia farnesiana. Journal of Natural Fibers 19 (4):1343–52. doi:10.1080/15440478.2020.1764457.
- Vijay, R., D. L. Singaravelu, A. Vinod, M. R. Sanjay, and S. Siengchin. 2021. Characterization of alkali-treated and untreated natural fibers from the stem of Parthenium hysterophorus. Journal of Natural Fibers 18 (1):80–90. doi:10.1080/15440478.2019.1612308.
- Wang, L., X. Liu, X. Zheng, and Y. Tian. 2015. Extraction of pectin from flax fiber by chemical means. International Journal of Clothing Science and Technology 27 (3):390–96. doi:10.1108/IJCST-03-2014-0037.
- Wang, L., and X. Wang. 2009. Effect of structure–property relationships on fatigue failure in natural fibres. In Fatigue failure of textile fibres, ed. M. Miraftab, 95–132. Woodhead Publishing. doi: 10.1533/9781845695729.2.95.
- Wang, X., L. Wang, W. Ji, Q. Hao, G. Zhang, and Q. Meng. 2019. Characterization of KH-560-modified jute fabric/epoxy laminated composites: Surface structure, and thermal and mechanical properties. Polymers 11 (5):769. doi:10.3390/polym11050769.
- Yao, Y., and S. Chen. 2013. The effects of fiber’s surface roughness on the mechanical properties of fiber-reinforced polymer composites. Journal of Composite Materials 47 (23):2909–23. doi:10.1177/0021998312459871.
- Zhuang, J., M. Li, Y. Pu, A. J. Ragauskas, and C. G. Yoo. 2020. Observation of potential contaminants in processed biomass using Fourier transform infrared spectroscopy. Applied Sciences 10 (12):1–13. doi:10.3390/app10124345.