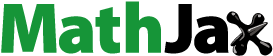
ABSTRACT
The quantity of bottled water and other household packaging materials increases enormously in developing countries like Ethiopia. Most of these materials are packed with polyethylene terephthalate (PET) plastics which results in the mounting of wastes rapidly. Due to their non-biodegradability, PET wastes cause challenges such as landfills, health problems, and a reduction in productivity. PET, a thermoplastic polymer, can be remelted and molded into different products. In this research, the recycled PET is reinforced with natural fibers such as false banana and sisal fibers to produce floor tile composites. The processing steps include a collection of waste PET and natural fibers, cleaning, shredding, treating fibers, composite manufacturing, and characterizing. The use of natural fibers in recycled plastics resulted in the production of cheaper, effective floor tile composites, and a reduction in environmental pollution. The FTIR analysis shows the removal of certain functional groups in chemically treated natural fibers and the occurrence of chemical and mechanical degradations during the recycling process. Natural fibers reinforced composite samples showed about 36% lightness compared to glass fibers reinforced composites and resulted in maximum compression strength of 3.1 MPa. Further study needs to be undertaken to enhance the mechanical properties of such composites in the future.
摘要
在埃塞俄比亚等发展中国家,瓶装水和其他家用包装材料的数量大幅增加. 大多数这些材料都是用聚对苯二甲酸乙二醇酯(PET)塑料包装的,这会导致废物迅速堆积. 由于其不可生物降解性,PET废物带来了诸如填埋场、健康问题和生产率降低等挑战. PET是一种热塑性聚合物,可以重熔并模塑成不同的产品. 在这项研究中,用天然纤维如假香蕉和剑麻纤维增强再生PET,以生产地板砖复合材料. 加工步骤包括收集废PET和天然纤维、清洁、粉碎、处理纤维、复合材料制造和表征. 在再生塑料中使用天然纤维可以生产更便宜、有效的地砖复合材料,并减少环境污染. FTIR分析显示化学处理的天然纤维中某些官能团的去除以及在回收过程中发生的化学和机械降解. 与玻璃纤维增强复合材料相比,天然纤维增强复合样品显示出约36%的轻质度,并产生3.1MPa的最大抗压强度. 未来需要进一步研究以提高此类复合材料的机械性能.
Introduction
There is a continuous increase in the production of plastics in the world today and it is predicted to persist. The progressively growing use of plastics generates enormous amount of non-biodegradable wastes in the environment (Arif et al. Citation2022). As these wastes stay hundreds of years without degradation, they need to be reprocessed or removed before being dumped into landfills (Arif et al. Citation2022). Recycling plastic materials are among the effective means of reducing the environmental pollution caused by these wastes (Qaidi et al. Citation2022). A thermoplastic polymer such as PET can be easily remelted and molded to different useful end products. In addition to sustaining the environment, recycling significantly contributes to the conservation of natural resources as the raw materials are also being significantly exhausted and resulting in high prices (Khalid and Ullah Arif Citation2022). As landfill space runs out, recycling becomes increasingly attractive (Ilyas et al. Citation2018). There is a wider scope of recycling in developing countries due to factors such as lower labor costs, easy to form small-scale recycling activities, almost no laws to control the standards of recycled materials, very low materials and transportation costs, and cheaper entry costs. Thus, as the amount of plastic being consumed increases in developing countries, collecting, sorting, and recycling of plastic wastes become a viable activity (Khalid et al. Citation2022).
To conserve the environment, fast-mounting of plastic wastes needs improved solutions including amendments of legislation all around the world (Arif et al. Citation2022). Recycled PET can be converted to various products such as textile fibers and composite materials typically as a fine aggregate to strengthen concrete and other building materials (Al-Tayeb et al. Citation2022; Jawad et al. Citation2022; Qaidi and Al-Kamaki Citation2020). The recycled PET can be also melted and acts as a binder to the reinforcing fibers. Many fibers have been utilized to reinforce the polymeric matrix. The most common are synthetic fibers such as carbon fibers (Chen et al. Citation2021; Zheng et al. Citation2022), glass fibers (Kaboglu, Eken, and Yurekturk Citation2021), and aramid fibers such as Kevlar (Bessa et al. Citation2022; Wenyu et al. Citation2021). Recently, with advantages of reasonable mechanical properties, low density, environmental benefits, and renewability, natural fibers have been paid more attention in composite applications (Babu et al. Citation2021; Khalid et al. Citation2021). Natural fibers are produced and provided by nature from various parts of the plants, trees, animals, and minerals (Karimah et al. Citation2021). These fibers are abundant and are reasonably cheap making it economically viable for the reinforcement of composites (Karimah et al. Citation2021). Thus, natural fibers are proficient material which would be utilized to replace the synthetic materials and their related products for the applications requiring less weight and energy conservation (Khalid et al. Citation2021). Natural plant fiber composites as environmentally attractive materials have been proven and emerged as an alternative to the glass reinforced composites used in many applications since the 1990s (Sanjay et al. Citation2016). Natural fibers such as flax, hemp, and sisal have been actively used with bio-resins systems to develop various interior components of automotive and aircraft industries (Ho et al. Citation2012).
The main chemical components of natural plant fibers are cellulose, lignin, hemicelluloses, pectin, and rare wax. The components and their percentages vary depending on the type of natural plant fibers (Chokshi et al. Citation2020; Thygesen et al. Citation2011). Natural fiber quality is influenced significantly by the age of the plant, species, growing environment, harvesting, humidity, quality of soil, temperature, and processing steps (Khalid, Ullah Arif, and Al Rashid Citation2022). Thus, it is required to devise methods that improve the consistency of on-field processing and reduce the costs. The properties of commonly used natural fibers are described by many researchers (Bekele, Lemu, and Jiru Citation2022; Sahu and Gupta Citation2020; Widyasanti, Napitupulu, and Thoriq Citation2020). Natural fiber reinforced polymer composites (NFPC) got considerable attention in numerous applications because of the good properties and superior advantages of natural fiber over synthetic fibers in terms of its relatively light weight, low cost, renewable resources, being abundant, flexibility during processing, biodegradability, and minimal health hazards (Ku et al. Citation2011; Shalwan and Yousif Citation2013). Most common attributes of natural fibers are summarized in .
However, natural fibers have drawbacks such as high moisture absorption, weak bindings and difficulty in coupling with polymeric matrix due to difference in chemical structures of fibers and matrix, and ineffectual stress transfer at the interface of the produced composites (Khalid, Arif, et al. Citation2021). These problems are reduced by surface modifications of natural fibers by using specific treatments. Surface modifications of natural fibers result in reduction of moisture absorption and also enhances the incompatibility between the fiber and polymeric matrix (Khalid et al. Citation2021; Varghese and Mittal Citation2017). The study by Kabir et al. concurred that chemical treatment is an important factor that has to be considered when processing natural fibers (Kabir et al. Citation2012). Different chemical treatments help to loosen the hydroxyl groups and reduces the hydrophilic behavior of the natural fibers, which in turn results in improved mechanical strength and dimensional stability of NFPCs (Khalid et al. Citation2021).
Characteristics and performance of NFPCs are affected by several factors. The hydrophilic nature of the natural fiber (Shalwan and Yousif Citation2013) and the fiber loading have great impacts on the composite properties (Norul Izani et al. Citation2013). Several studies reveal that, good properties of NFPCs are attained by high natural fiber loading (Mohammed et al. Citation2015; Shesan et al. Citation2019; Tawakkal, Cran, and Bigger Citation2014). The composition of natural fibers the percentage of cellulose, hemicellulose, lignin, and waxes also affect the properties of resulted composite (Khalid et al. Citation2021). The chosen process techniques and parameters also highly influence and determine the characteristics of produced composites (Ku et al. Citation2011). The suitability, competitiveness, and capabilities of embedding natural fibers in the polymeric matrices were examined by several researchers (Arrakhiz et al. Citation2013; N. Kumar, Bedi, and Singh Citation2021; Neto et al. Citation2021; Pereira et al. Citation2020). Fiber surface modifications effect on manufacturing processes and improving fiber/polymer compatibility were also vastly studied (Latif et al. Citation2019; Mohammed et al. Citation2015; Zwawi Citation2021). The suitability of jute/plastic composites to the eco-design components of automotive industry is investigated and properties such as thermal stability, fiber modification, crystallinity, weathering resistance, and durability were analyzed (Al-Oqla and Sapuan Citation2014).
The mechanical performance of the composites is affected by number of aspects such as orientation of fiber (Şanal and Özyurt Zihnioǧlu Citation2013), length of fibers (Himanshu et al. Citation2015; Prakash et al. Citation2021; Sajin et al. Citation2022), physical properties of fibers (Bénézet et al. Citation2012), volume fraction (Das et al. Citation2018; Prakash et al. Citation2021), interfacial adhesion property of fibers Lee, Khalina, and Hua Lee (Citation2021) and many more. The chemical, physical, or biological approaches of natural fibers surface functionalization could be used to enhance their compatibility with polymeric matrix to produce advanced NFPCs. Most commonly used chemical treatments for plant based-fibers includes alkalization, silanization, acetylation, acrylation, benzoylation, peroxide treatment, maleated coupling treatment, potassium permanganate treatment, acrylonitrile grafting, stearic acid treatment, isocyanate treatment, triazine, sodium chlorite, fungal and enzyme treatment (Tavares et al. Citation2020). As it was mentioned above, the main purpose of surface treatments of natural fibers is to enhance fibre/matrix interfacial bonding and stress transferability of the composites. Taking one of the surface treatments of natural fibers as an example, the alkaline treatment helps to remove the amorphous compounds and increases the crystallinity index of fiber bundles (Venkateshwaran, Elaya Perumal, and Arunsundaranayagam Citation2013; Yiga, Lubwama, and Wilberforce Olupot Citation2021; Zin et al. Citation2018). The appropriate concentration of alkali should be used based on the experiments to have better properties of treated fiber reinforced composites. Low alkali concentration may not fully remove the amorphous components, whereas high alkali concentration may damage the surface of fibers which in turn results in a decrease of mechanical properties. Several researchers have successfully developed polymeric composites reinforced with natural fibers. However, the authors of this study did not find enough studies done on natural fibers reinforced with recycled polymeric composites (NFRPCs) from online literature. Therefore, the possibility of effective NFRPCs production and effects of recyclability on the properties of the resulted composites need further study. Thus, this study is designed to study and evaluate the properties of composite materials developed from natural fibers reinforced recycled PET.
Significance of the study
The use of renewable resources such as natural fibers in composite materials has been significantly increased due to their economic and environmental advantages. Utilizing these natural fibers as a reinforcement for recycled plastic will have huge benefits in terms of sustainable development. A large number of studies have utilized plastic waste as aggregate or fiber to improve the mechanical properties of composite for building materials such as concrete. To the best knowledge of authors, a little is known about composite materials produced through melting of recycled plastic reinforced with natural fibers. Tile composites produced from manually melted recycled PET reinforced with natural fibers has not been investigated yet and this study will fill the gap within the area.
Materials and methodologies
Materials and equipment’s
To undertake this study the following materials and equipment were used. Natural fibers such as false banana, sisal fibers, shredded PET waste bottles, gypsum, stainless steel melting pot, four partitioned compacting mold, sodium hydroxide (NaOH), blowing fan, charcoal, water, and plastic barrel are used.
The following testing device were used: universal testing machine (WAW-600D) was used to test the compressive strength of the composite and PerkinElmer FTIR instrument was used to test the functional groups.
Methods
The following main procedures are followed in this research:
Fiber extraction
Sisal fibers are extracted from the raw sisal plant mechanically by researchers whereas the false banana fibers are procured from local farmers. After cleaning the impurities, the long fibers are cut into short fibers of about 3–4 cm length by using scissors to imitate the aspect ratio of synthetic fibers like glass fibers as shown in .
Treatment of natural fibers
To illustrate the effect of surface treatment in composites, false banana fibers are treated with NaOH at different concentrations. The surface treatments follow previous researcher steps (Kabir et al. Citation2012; Shalwan and Yousif Citation2013): fibers are pre-cleaned to remove impurities which increase the fiber surface roughness and preventing the ions absorption that remove the OH groups from the fibers surface as shown in equation below.
Collection and cleaning of waste PET
Waste PET bottles are collected from Bahir Dar city, Ethiopia. Then, the bottle covers and tags are removed and cleaned to remove the impurities and any contaminations.
Shredding
Cleaned bottles are shredded by a local shredding machine at Aychew and friends a small-scale enterprise as shown in .
Composite manufacturing
Shredded PET wastes are melted in stainless steel melting pot by continuously blowing the charcoal using electric fan. Charcoal was used in this study due to the absence of alternative methods like a heavy-duty gas or electrical stove and the use of such energy sources is recommended in future studies. After PET completely melts, the gypsum of 22 wt% is added slowly and stirred gently until it is homogenously distributed without agglomerates formation and finally fibers of 3 wt% is introduced in a speedy and gentle mixing until it is uniformly distributed in melted PET matrix. The proportion of gypsum and fibers selected for this study is based on the researcher preliminary study and also referring other’s researcher findings (Turlapati and Vineel Citation2020). The processing parameters such as temperature and time have significant impact on the properties of the produced tiles. High temperature beyond melting temperature and prolonged stay at the melted state lead to low strength tile products due to thermal degradation of PET. Thus, researchers stop blowing the charcoal as soon as the PET completely melts and added fillers and fibers within two minutes to avoid the degradation of both natural fibers and PET. Finally, the melted solution is immediately poured to a four partitioned compacting metal mold of each 20 mm x 20 mm x 30 mm size and pressing it with a high pressure until it solidified for about 5–7 minutes to form floor tile of uniform and flat surface. shows the summary of manufacturing process of NFRPCs.
Compression strength tests
The compressive strengths of floor tile composites produced from fibers reinforced recycled PET are measured by using automatic compression tester machine model 50-C46P02, Italy CONTROLS S.P.A. according to ASTM C469 standard test method as shown in .
Functional group analysis
The functional groups found in composite were analyzed using the PerkinElmer FTIR instrument. FTIR spectrum outputs were obtained in the range of 4000–500 cm−1 using five scans and recorded in the absorbance mode as a function of wavenumber.
Results and discussion
Recycling of plastics have benefits such as decrease of greenhouse gas discharges, energy savings, and nonrenewable sources like oil and gas savings. Furthermore, recycling offers an income for many people and families in emerging countries, both in the form of formal employment or informal economic activities. The previous research work of other researcher shows that recycled PET gives an improved sets of properties when it is reinforced with synthetic fibers than natural fibers. The glass fibers introduced in the polymeric matrix result in better and more consistent performance than other fillers and reinforcements in recycled PET composites (A. Kumar, Bedi, and Singh Citation2021). This is due to the high aspect ratio of the fibres (the diameter is in the range of 10-20 μm and final length of 3 cm), which translates in an excellent reinforcing ability. Accordingly, this study was undertaken to investigate the performance of natural fibers by mimicking the aspect ratio of glass fibers through cutting it to appropriate dimension. Also, the glass fibers reinforced recycled PET composites is produced to compare its properties with that of natural fibers reinforced composites in this study.
The floor tile composites, shown in , produced from recycled PET filled with gypsum of about 22 wt% and reinforced from untreated and treated natural fibers of about 3 wt% show low weight compared to that of glass fibers reinforced composites of similar fibers content. Thus, the comparative advantages of using the lignocellulosic fibers are their lower density and costs as well as renewability, biodegradability, recyclability and neutrality with respect to CO2 emission which is responsible for global warming. Floor tile composites produced from natural fibers resulted in lower costs of 15.8% compared to that of glass fibers reinforced tiles of similar fibers ratio. shows the mean weight of chemical treated as well as untreated false banana fibers and sisal fibers reinforced composites have almost similar weight of about 1.4 kg whereas floor tiles weighing about 1.9 kg is produced with glass fibers reinforcement. This result mainly due to the lightweight properties of natural fibers and certain degradation occurring during the composite processing at high temperatures.
The lignocellulosic fibers have limited application in high-temperature engineering composites due to their restricted thermal resistance. As limited works are available to analyze the feasibility of lignocellulosic fibers at high temperature, this study is devoted to consider the effectiveness of false banana fibers and sisal fibers reinforcement in the melted recycled PET. A thermogravimetric analysis of sisal fibers studied by Dantas et al (Dantas et al. Citation2019) shows a first mass loss event around 100°C and a second main degradation event of the fibers between 200°C and 400°C. As it was shown by this study, the major thermal loss of sisal fibers occurred mainly above 300°C. This implies that sisal fibers and false banana fibers which have almost similar properties could be successfully used to reinforce polyethylene terephthalate at its melting temperature of about 260°C in this study.
In order to improve the adhesion and compatibility of false banana fibers to the PET matrix, raw fibers were chemically treated with sodium hydroxide. The reaction of cellulose in false banana fibers is confirmed by FTIR spectrum analysis of the raw and treated false banana fibers reinforced composite as shown in , respectively. The FTIR spectrum shows that there is a difference between the non-treated and treated false banana fibers reinforced composite. Some of the functional groups have been removed from the treated false banana fibers. This could be due to the reduction in molecular weight or reduction of the chain length due to the reduction of wax, hemicellulose, pectin, lignin, and other water-soluble components during the treatment of false banana fibers and thermal degradation. The FTIR spectrum of the nontreated false banana fibers-based composite shows the absorption band in the region of 3435 cm−1, 1733 cm−1 and 2901 cm−1 due to O-H stretching vibration, C=O stretching vibration and C-H stretching vibration respectively. These absorption bands are due to the hydroxyl group in cellulose, carbonyl group of acetyl ester in hemicellulose and carbonyl aldehyde in lignin . On the other hand, the characteristic peak at 1733 cm−1 and other peaks i.e., 1428 cm−1 and 1248 cm−1 were completely disappeared upon chemical treatment with sodium hydroxide.
The FTIR spectrum of the sisal fibers reinforced recycled PET composite is shown in . Throughout the recycling process, there is both chemical and mechanical degradations. This affects the mechanical properties and chemical resistance as well as melt viscosity of recycled PET which is less than that of virgin PET. The factors that cause a reduction in the physical, mechanical, chemical, and rheological properties of recycled PET will also affect the brittleness of the recycled polymer. These factors also make recycled PET lose its melting elasticity behavior.
Even though the floor tiles composite manufactured from natural fibers prevails in lightness, the compression test result shows relatively poor compressive strength compared to that of the glass fibers reinforced composites. shows the average value of compression strength of sodium hydroxide treated and untreated false banana fibers, sisal fibers, and glass fibers reinforced tile composites. As it can be seen from the graph, the surface modification of false banana fibers by sodium hydroxide improved the compression strength compared to that of untreated false banana fibers.
Figure 10. Compression strength of untreated and sodium hydroxide treated false banana fibers, sisal fibers, and glass fibers reinforced recycled PET floor tile composites.
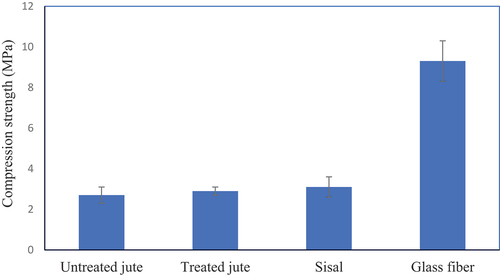
The compression strength of NaOH treated false banana fibers reinforced floor tile composites value was improved to about 2.9 MPa from 2.7 MPa of untreated false banana fibers. Relative to false banana fibers, sisal fibers reinforced recycled PET composites shows relatively higher compression strength of 3.1 MPa which is about 15% more than the results obtained by untreated false banana fibers. Generally, this study reveals that the compression strength of glass fibers reinforced recycled PET composites is almost thrice of the sisal fibers and false banana fibers reinforced recycled PET composites.
Thus, the decrease in compression strength of natural fibers reinforced recycled PET composites could be due to relatively low mechanical strength of natural fibers and possible thermal deterioration of the natural fibers at the melting temperature of recycled PET. However, the floor tiles produced from natural fibers reinforced recycled PET composites fulfill the compression strength criteria and can be used as potential candidate materials due to its lightweight, economic, and conserve environment. Comparison of compressive strength of floor tiles composites produced in this study and other researchers is demonstrated in .
Table 1. Comparison of different floor tile composites.
As seen from , the floor tiles produced from natural fibers reinforced recycled PET composites have comparative compressive strength and/or better strengths than the reference composites in certain cases.
Conclusion
Composite materials used for floor tiles were developed successfully using sisal fibers and false banana fibers of 3 wt% as reinforcement in melted recycled PET matrix where 22 wt% of gypsum added as fillers improved shrinkage on molding. The statistical results of floor tile composites produced from natural fibers showed lightweight and low compressive strength compared to synthetic fibers reinforced composites of the same composition. Chemical treatment of natural fibers resulted in the removal of certain functional groups due to the reduction of non-cellulosic components such as hemicellulose, wax, pectin and lignin. The FTIR analysis demonstrated the occurrence of chemical and mechanical degradations during the recycling process. Natural fibers developed floor tile composites showed about 36% lightness compared to glass fibers composites, whereas sisal fibers reinforced recycled PET composites had recorded maximum compressive strength of about 3.1 MPa. The comparison of compressive strength between this study and reference studies undertaken on the floor tile composites demonstrated it was within the given ranges. The results obtained in this study confirm that the natural fibers such as false banana and sisal fibers could be used to produce lightweight and relatively low compressive strength composites with melted PET wastes. Therefore, reinforcing the recycled plastics with natural fibers at relatively low temperature make them suitable for infrastructure applications like floor tile composites. However, further research needs to be undertaken to enhance the mechanical performance of the floor tile composites. Authors would like to recommend to use a heavy-duty gas or electrical stove energy source with certain automation to enhance the results obtained in this study and conserve the environment further.
Highlights
As polyethylene terephthalate prolongs in the environment for hundred years without degradation its recycling will contribute to the conservation of the environment.
Natural fibers are viable for the reinforcement of recycled PET composites due to their abundance, renewability, degradability, low density and low cost.
Floor tile composites were successfully produced by reinforcing the recycled PET with false banana and sisal fibers and using gypsum as filler.
The produced floor tile composites resulted in 36% lightness compared to the glass fibers composites with the same proportion, and a compressive strength of up to 3.1 MPa.
Acknowledgements
The authors would like to thank Ethiopian Institute of Textile and Fashion Technology (EiTEX), Bahir Dar University for supporting this study.
Disclosure statement
No potential conflict of interest was reported by the author(s).
Additional information
Funding
References
- Al-Oqla, F. M., and S. M. Sapuan. 2014. Natural fiber reinforced polymer composites in industrial applications: Feasibility of date palm fibers for sustainable automotive industry. Journal of Cleaner Production 66:347–14. doi:10.1016/j.jclepro.2013.10.050.
- Al-Tayeb, M. M., Y. I. A. Aisheh, S. M. A. Qaidi, and B. A. Tayeh. 2022. Experimental and simulation study on the impact resistance of concrete to replace high amounts of fine aggregate with plastic waste. Case Studies in Construction Materials 17 (June):e01324. doi:10.1016/j.cscm.2022.e01324.
- Arif, Z. U., M. Yasir Khalid, W. Ahmed, H. Arshad, and S. Ullah. 2022. Recycling of the glass/carbon fibre reinforced polymer composites: A step towards the circular economy. Polymer-Plastics Technology and Materials 61 (7):761–88. doi:10.1080/25740881.2021.2015781.
- Arif, Z. U., M. Yasir Khalid, R. Noroozi, A. Sadeghianmaryan, M. Jalalvand, and M. Hossain. 2022. Recent Advances in 3D-printed polylactide and polycaprolactone-based biomaterials for tissue engineering applications. International Journal of Biological Macromolecules 218:930–68. doi:10.1016/j.ijbiomac.2022.07.140.
- Arrakhiz, F. Z., M. El Achaby, M. Malha, M. O. Bensalah, O. Fassi-Fehri, R. Bouhfid, K. Benmoussa, and A. Qaiss. 2013. Mechanical and thermal properties of natural fibers reinforced polymer composites: Doum/low density polyethylene. Materials & Design 43:200–05. doi:10.1016/j.matdes.2012.06.056.
- Babu, T. N., S. Shyam, S. Kaul, and D. Rama Prabha. 2021. Natural fibre composites – an alternative to plastics in the automotive industry: A review. Proceedings of the Institution of Mechanical Engineers, Part L: Journal of Materials: Design and Applications 236 (2):237–66. doi:10.1177/14644207211041622.
- Bekele, A. E., H. G. Lemu, and M. G. Jiru. 2022. Experimental study of physical, chemical and mechanical properties of enset and sisal fibers. Polymer testing 106 (November 2021):107453. doi:10.1016/j.polymertesting.2021.107453.
- Bénézet, J. C., A. Stanojlovic-Davidovic, A. Bergeret, L. Ferry, and A. Crespy. 2012. Mechanical and physical properties of expanded starch, reinforced by natural fibres. Industrial Crops and Products 37 (1):435–40. doi:10.1016/j.indcrop.2011.07.001.
- Bessa, W., D. Trache, M. Derradji, and A. Fouzi Tarchoun. 2022. Kevlar fabric reinforced polybenzoxazine composites filled with silane treated microcrystalline cellulose in the interlayers: The next generation of multi-layered armor panels. Defence Technology 18 (11):2000–07. doi:10.1016/j.dt.2021.10.005.
- Chen, A. Y., S. Baehr, A. Turner, Z. Zhang, and G. X. Gu. 2021. Carbon-fiber reinforced polymer composites: A comparison of manufacturing methods on mechanical properties. International Journal of Lightweight Materials and Manufacture 4 (4):468–79. doi:10.1016/j.ijlmm.2021.04.001.
- Chokshi, S., V. Parmar, P. Gohil, and V. Chaudhary. 2020. Chemical composition and mechanical properties of natural fibers. Journal of Natural Fibers 17 (00):1–12. doi:10.1080/15440478.2020.1848738.
- Dantas, L. G., L. Aparecida, C. De Motta, D. Pasquini, and F. De Engenharia Civil. 2019. Surface esterification of sisal fibres for use as reinforcement in cementitious matrix. 22 (4):e20180585. doi:10.1590/1980-5373-mr-2018-0585.
- Das, S. C., D. Paul, M. Muhammad Fahad, G. M. S. R. Mithun Kumer Das, M. Ahmad Khan, and M. A. Khan. 2018. Effect of fiber loading on the dynamic mechanical properties of jute fiber reinforced polypropylene composites. Advances in Chemical Engineering and Science 08 (04):215–24. doi:10.4236/aces.2018.84015.
- Himanshu, B., M. K. Gupta, P. Shandilya, and R. K. Srivastava. 2015. Effect of fibre length on mechanical properties of randomly oriented short jute fibre reinforced epoxy composite. Materials Today: Proceedings 2 (4–5):1193–99. doi:10.1016/j.matpr.2015.07.031.
- Ho, M. P., H. Wang, J. Hee Lee, H. Chun Kit, K. Tak Lau, J. Leng, and D. Hui. 2012. Critical factors on manufacturing processes of natural fibre composites. Composites Part B: Engineering 43 (8):3549–62. doi:10.1016/j.compositesb.2011.10.001.
- Ilyas, M., W. Ahmad, H. Khan, S. Yousaf, K. Khan, and S. Nazir. 2018. Plastic waste as a significant threat to environment - a systematic literature review. Reviews on Environmental Health 33 (4):383–406. doi:10.1515/reveh-2017-0035.
- Jawad, A., A. Majdi, A. Babeker Elhag, A. Farouk Deifalla, M. Soomro, H. F. Isleem, and S. Qaidi. 2022. A step towards sustainable concrete with substitution of plastic waste in concrete: Overview on mechanical, durability and microstructure analysis. Crystals 12 (7):944. doi:10.3390/cryst12070944.
- Kabir, M. M., H. Wang, K. T. Lau, and F. Cardona. 2012. Chemical treatments on plant-based natural fibre reinforced polymer composites: An overview. Composites Part B: Engineering 43 (7):2883–92. doi:10.1016/j.compositesb.2012.04.053.
- Kaboglu, C., T. Y. Eken, and Y. Yurekturk. 2021. Impact performances and failure modes of glass fiber reinforced polymers in different curvatures and stacking sequences. Journal of Composite Materials 56 (7):1123–38. doi:10.1177/00219983211059096.
- Karimah, A., M. Rasyidur Ridho, S. Sofyan Munawar, D. Sudarwoko Adi, R. D. Ismadi, B. Subiyanto, W. Fatriasari, A. Fudholi, and A. Fudholi. 2021. A review on natural fibers for development of eco-friendly bio-composite: Characteristics, and utilizations. Journal of Materials Research and Technology 13:2442–58. doi:10.1016/j.jmrt.2021.06.014.
- Khalid, M. Y., A. Al Rashid, Z. Ullah Arif, W. Ahmed, and H. Arshad. 2021. Recent advances in nanocellulose-based different biomaterials: Types, properties, and emerging applications. Journal of Materials Research and Technology 14:2601–23. doi:10.1016/j.jmrt.2021.07.128.
- Khalid, M. Y., A. Al Rashid, Z. Ullah Arif, W. Ahmed, H. Arshad, and A. Ali Zaidi. 2021. Natural fiber reinforced composites: Sustainable materials for emerging applications. Results in Engineering 11:100263. doi:10.1016/j.rineng.2021.100263.
- Khalid, M. Y., A. Al Rashid, Z. Ullah Arif, M. Fahad Sheikh, H. Arshad, and M. Ali Nasir. 2021. Tensile strength evaluation of glass/jute fibers reinforced composites: An experimental and numerical approach. Results in Engineering 10 (December 2020):100232. doi:10.1016/j.rineng.2021.100232.
- Khalid, M. Y., R. Imran, Z. Ullah Arif, N. Akram, H. Arshad, A. Al Rashid, and F. Pedro García Márquez. 2021. Developments in chemical treatments, manufacturing techniques and potential applications of natural-fibers-based biodegradable composites. Coatings 11 (3):1–18. doi:10.3390/coatings11030293.
- Khalid, M. Y., and Z. Ullah Arif. 2022. Novel biopolymer-based sustainable composites for food packaging applications: A narrative review. Food Packaging and Shelf Life 33:100892. doi:10.1016/j.fpsl.2022.100892.
- Khalid, M. Y., Z. Ullah Arif, W. Ahmed, and H. Arshad. 2022. Recent trends in recycling and reusing techniques of different plastic polymers and their composite materials. Sustainable Materials and Technologies 31:e00382. doi:10.1016/j.susmat.2021.e00382.
- Khalid, M. Y., Z. Ullah Arif, and A. Al Rashid. 2022. Investigation of tensile and flexural behavior of green composites along with their impact response at different energies. International Journal of Precision Engineering and Manufacturing - Green Technology 9 (5):1399–410. doi:10.1007/s40684-021-00385-w.
- Khalid, M. Y., Z. Ullah Arif, M. Fahad Sheikh, and M. Ali Nasir. 2021. Mechanical characterization of glass and jute fiber-based hybrid composites fabricated through compression molding technique. International Journal of Material Forming 14 (5):1085–95. doi:10.1007/s12289-021-01624-w.
- Kumar, A., R. Bedi, and B. Singh. 2021. Composite materials based on recycled polyethylene terephthalate and their properties – a comprehensive review. Composites Part B 219:108928. doi:10.1016/j.compositesb.2021.108928.
- Ku, H., H. Wang, N. Pattarachaiyakoop, and M. Trada. 2011. A review on the tensile properties of natural fiber reinforced polymer composites. Composites Part B: Engineering 42 (4):856–73. doi:10.1016/j.compositesb.2011.01.010.
- Latif, R., S. Wakeel, N. Zaman Khan, A. Noor Siddiquee, S. Lal Verma, and Z. Akhtar Khan. 2019. Surface treatments of plant fibers and their effects on mechanical properties of fiber-reinforced composites: A review. Journal of Reinforced Plastics and Composites 38 (1):15–30. doi:10.1177/0731684418802022.
- Lee, C. H., A. Khalina, and S. Hua Lee. 2021. Importance of interfacial adhesion condition on characterization of plant-fiber-reinforced polymer composites: A review. Polymers 13 (3):1–22. doi:10.3390/polym13030438.
- Linda Bih, N., A. Aboubakar Mahamat, J. Bidossèssi Hounkpè, P. Azikiwe Onwualu, and E. E. Boakye. 2021. The Effect of Polymer Waste Addition on the Compressive Strength and Water Absorption of Geopolymer Ceramics. Applied Sciences 11 (8):3540. doi:10.3390/app11083540.
- Mohammed, L., M. N. Ansari, G. Pua, M. Jawaid, and M. S. Islam. 2015. A review on natural fiber reinforced polymer composite and its applications. International Journal of Polymer Science 2015:243947. doi:10.1155/2015/243947.
- Neto, J. S. S., H. F. M. de Queiroz, R. A. A. Aguiar, and M. D. Banea. 2021. A review on the thermal characterisation of natural and hybrid fiber composites. Polymers 13 (24):4425. doi:10.3390/polym13244425.
- Norul Izani, M. A., M. T. Paridah, U. M. K. Anwar, M. Y. Mohd nor, and P. S. H’Ng. 2013. Effects of fiber treatment on morphology, tensile and thermogravimetric analysis of oil palm empty fruit bunches fibers. Composites Part B: Engineering 45 (1):1251–57. doi:10.1016/j.compositesb.2012.07.027.
- Omosebi, T. O., and N. F. Abass. 2021. Polymer tiles from polyethylene terephthalate (PET) wastes and fly ash: mechanical properties and durability. F1000Res 10:1139. doi:10.12688/f1000research.53514.1.
- Pereira, A. L., M. D. Banea, J. S. S. Neto, and D. K. K. Cavalcanti. 2020. Mechanical and thermal characterization of natural intralaminar hybrid composites based on sisal. Polymers 12 (4):866. doi:10.3390/POLYM12040866.
- Prakash, K. B., Y. A. Fageehi, R. Saminathan, P. M. Kumar, S. Saravanakumar, R. Subbiah, B. Arulmurugan, and S. Rajkumar. 2021. Influence of fiber volume and fiber length on thermal and flexural properties of a hybrid natural polymer composite prepared with banana stem, pineapple leaf, and S-glass. Advances in Materials Science and Engineering 2021: 6329400. doi: 10.1155/2021/6329400.
- Qaidi, S., and Y. Al-Kamaki. 2020. State-of-the-art review: Concrete made of recycled waste pet as fine aggregate. The Journal of the University of Duhok 23 (2):412–29. doi:10.26682/csjuod.2020.23.2.34.
- Qaidi, S., Y. S. S. Al-Kamaki, R. Al-Mahaidi, A. S. Mohammed, H. Unis Ahmed, O. Zaid, F. Althoey, J. Ahmad, H. F. Isleem, and I. Bennetts. 2022. Investigation of the effectiveness of CFRP strengthening of concrete made with recycled waste PET fine plastic aggregate. PLoS ONE 17 (7):1–27. doi:10.1371/journal.pone.0269664.
- Sahu, P., and M. K. Gupta. 2020. A review on the properties of natural fibres and its bio-composites: Effect of alkali treatment. Proceedings of the Institution of Mechanical Engineers, Part L: Journal of Materials: Design and Applications 234 (1):198–217. doi:10.1177/1464420719875163.
- Sajin, J. B., R. Christu Paul, J. S. Binoj, B. Brailson Mansingh, M. Gerald Arul Selvan, R. S. R. I. Kheng Lim Goh, and M. S. Senthil Saravanan. 2022. Impact of fiber length on mechanical, morphological and thermal analysis of chemical treated jute fiber polymer composites for sustainable applications. Current Research in Green and Sustainable Chemistry 5 (November 2021):100241. doi:10.1016/j.crgsc.2021.100241.
- Şanal, I., and N. Özyurt Zihnioǧlu. 2013. To what extent does the fiber orientation affect mechanical performance? Construction and Building Materials 44:671–81. doi:10.1016/j.conbuildmat.2013.03.079.
- Sanjay, M. R., G. R. Arpitha, L. Laxmana Naik, K. Gopalakrishna, and B. Yogesha. 2016. Applications of natural fibers and its composites: An overview. Natural Resources 07 (03):108–14. doi:10.4236/nr.2016.73011.
- Shalwan, A., and B. F. Yousif. 2013. In state of Art: Mechanical and tribological behaviour of polymeric composites based on natural fibres. Materials & Design 48:14–24. doi:10.1016/j.matdes.2012.07.014.
- Shesan, J., A. C. S. Owonubi, A. G. Chioma, R. Neerish, and S. E. Rotimi. 2019. Improving the mechanical properties of natural fiber composites for structural and biomedical applications. Renewable and Sustainable Composites 1–27. doi:10.5772/intechopen.85252.
- Tavares, T. D., J. C. Antunes, F. Ferreira, and H. P. Felgueiras. 2020. Biofunctionalization of natural fiber-reinforced biocomposites for biomedical applications. Biomolecules 10 (1):148. doi:10.3390/biom10010148.
- Tawakkal, I. S. M. A., M. J. Cran, and S. W. Bigger. 2014. Effect of kenaf fibre loading and thymol concentration on the mechanical and thermal properties of PLA/kenaf/thymol composites. Industrial Crops and Products 61:74–83. doi:10.1016/j.indcrop.2014.06.032.
- Thygesen, A., B. Madsen, A. Belinda Bjerre, and H. Lilholt. 2011. Cellulosic fibers: Effect of processing on fiber bundle strength. Journal of Natural Fibers 8 (3):161–75. doi:10.1080/15440478.2011.602236.
- Turlapati, V. V., and C. Vineel. 2020. A comparative study on performance of synthetic and natural fibers on compressive and flexural strength of concrete. Advanced Engineering Forum 36 (June):97–113. https://doi.org/10.4028/scientific.net/AEF.36.97.
- Varela, B. D., J. L. Quito, and N. C. Piaza. 2015. Flexural and Compressive Strength of Concrete Tiles with Different Levels of Partial Substitution of Pulverized Solid Waste Materials for Gravel. OALib 02 (01):1–10. doi:10.4236/oalib.1101187.
- Varghese, A. M., and V. Mittal. 2017. Surface modification of natural fibers. Biodegradable and Biocompatible Polymer Composites: Processing, Properties and Applications Elsevier Ltd. doi:10.1016/B978-0-08-100970-3.00005-5.
- Venkateshwaran, N., A. Elaya Perumal, and D. Arunsundaranayagam. 2013. Fiber surface treatment and its effect on mechanical and visco-elastic behaviour of banana/epoxy composite. Materials & Design 47:151–59. doi:10.1016/j.matdes.2012.12.001.
- Wenyu, L., W. Yu, B. Zhang, X. Dou, X. Han, and H. Cai. 2021. Kevlar fibers reinforced straw wastes-polyethylene composites: combining toughness, strength and self-extinguishing capabilities. Composites Part B: Engineering 223 (April):109117. doi:10.1016/j.compositesb.2021.109117.
- Widyasanti, A., L. O. B. Napitupulu, and A. Thoriq. 2020. Physical and mechanical properties of natural fiber from sansevieria trifasciata and agave sisalana. IOP Conference Series: Earth and Environmental Science 462 (1):012032. doi:10.1088/1755-1315/462/1/012032.
- Yiga, V. A., M. Lubwama, and P. Wilberforce Olupot. 2021. Effect of alkaline surface modification and carbonization on biochemical properties of rice and coffee husks for use in briquettes and fiber-reinforced plastics. Journal of Natural Fibers 18 (4):620–29. doi:10.1080/15440478.2019.1642824.
- Zheng, H., W. Zhang, B. Li, J. Zhu, C. Wang, G. Song, G. Wu, X. Yang, Y. Huang, and L. Ma. 2022. Recent advances of interphases in carbon fiber-reinforced polymer composites: A review. Composites Part B: Engineering 233:109639. doi:10.1016/j.compositesb.2022.109639.
- Zin, M. H., K. Abdan, N. Mazlan, E. S. Zainudin, and K. E. Liew. 2018. The effects of alkali treatment on the mechanical and chemical properties of pineapple leaf fibres (PALF) and adhesion to epoxy resin. IOP Conference Series: Materials Science and Engineering 368 (1):012035. doi:10.1088/1757-899X/368/1/012035.
- Zwawi, M. 2021. A review on natural fiber bio-composites, surface modifications and applications. Molecules 26 (2):404. doi:10.3390/molecules26020404.