ABSTRACT
With the advance in wearable electronics, there is increasing demand for conductive fibers that are stable under machine washing. Silk-based conductive fibers in particular have attracted significant attention due to their biocompatibility and excellent mechanical properties. To achieve the machine washability of silk-based conductive fibers, poly(3,4-ethylenedioxythiophene) polystyrene sulfonate (PEDOT:PSS) has been adopted as a conductive functional layer. PEDOT:PSS with ethylene glycol has a negative surface charge that can strongly adhere to the positively charged silk surface, leading to the excellent machine washability of silk-based conductive fibers. Various types of PEDOT:PSS/silk-based conductive fibers have been demonstrated in past research, including those in which different types of materials, such as silver (Ag) nanowires, carbon nanotubes, or manganese dioxide (MnO2), have been inserted to produce a range of electrical and chemical properties that can be used for different applications. In this mini-review, strategies to enhance the stability of silk-based conductive fibers using PEDOT:PSS are discussed. Various types of PEDOT:PSS/silk-based conductive fiber are introduced and research trends and future research directions are discussed.
摘要
随着可穿戴电子技术的进步, 对在机器清洗下稳定的导电纤维的需求日益增加. 特别是基于丝的导电纤维由于其生物相容性和优异的机械性能而引起了极大的关注. 为了实现丝基导电纤维的可机洗性, 已采用聚 (;3,4-亚乙基二氧噻吩) 聚苯乙烯磺酸盐 (PEDOT:PSS) 作为导电功能层. PEDOT:PSS与乙二醇具有负表面电荷, 可强烈粘附在带正电荷的丝绸表面, 从而使丝绸基导电纤维具有优异的机器可洗性. 在过去的研究中已经证明了各种类型的PEDOT:PSS/基于丝的导电纤维, 包括其中插入了不同类型的材料, 如银 (Ag) 纳米线、碳纳米管或二氧化锰 (MnO2), 以产生可用于不同应用的一系列电和化学性质的纤维. 在这篇小综述中, 讨论了使用PEDOT:PSS增强丝基导电纤维稳定性的策略. 介绍了各种类型的PEDOT:PSS/丝基导电纤维, 并讨论了其研究趋势和未来的研究方向.
1 Introduction
The development of 5 G communications and Internet of Things (IoT) networks has facilitated interest in wearable electronic devices (Haghi, Thurow, and Stoll Citation2017; Muhammad et al. Citation2022; Rodrigues et al. Citation2018; Seo et al. Citation2022; Singh, Rana, and Kumar Singh Citation2022; Varghese et al. Citation2022). is the summary of wearable devices in the 5 G era for which conductive fibers are required. The key functions of wearable devices in IoT systems are to collect user information and exchange this data with the controlling platform. Therefore, sensitive sensing performance is critical for next-generation wearable devices, which can be realized by fabricating highly conductive flexible and stretchable interconnecting materials and devices, including flexible printed circuit boards (Kwak et al. Citation2017; Sheng et al. Citation2021; Zhang et al. Citation2021), stretchable conductive composite films (Chen et al. Citation2020; Hwang and Gwang Yun Citation2019; Hwang, Han, and Matteini Citation2022; Shen et al. Citation2020), and conductive fibers (Gao et al. Citation2020; Gibbs and Asada Citation2005; Hansora, Shimpi, and Mishra Citation2015). Conductive fibers are considered particularly important due to the freedom in their structural design, their excellent flexibility, and the seamlessness of their use with the human body (Heo, Faruk Hossain, and Kim Citation2020; Hwang et al. Citation2020; Niu et al. Citation2020). Conductive fibers can be categorized into three main forms: conductive wires, conductive filler and polymer matrix composite fibers, and conductive layer-coated fibers. shows the comparison of each types of fiber in terms of various aspects that need to be considered for reliable conductive fibers. In the , the headings of fabrication, conductivity, flexibility/stretchability/washability, comfort, productivity, and technological maturity indicate technologies used to make conductive fiber, resistance to bending, stretching and washing, seamlessness to human body, efficiency to mass production, and status of technological development, respectively.
Figure 1. Summary of wearable devices in the 5 G era for which conductive fibers are required. Reproduced with permission from ref. (Rodrigues et al. Citation2018).
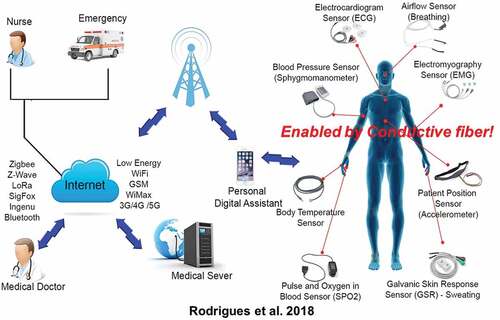
Table 1. Comparison of the performance and properties of different types of conductive fiber.
Conductive wires include metal wires and conducting polymer wires that are produced by extruding conductive material through a hole (Pani, Achilli, and Bonfiglio Citation2018; Zeng et al. Citation2014). Because the entire wire consists of conductive material, it offers excellent electrical conductivity. However, metal wires are susceptible to mechanical deformation and are not comfortable for the human body when used in wearable devices. In contrast to conductive wires, composite fibers are fabricated by mixing conductive fillers such as metal particles or metal nanowires with a polymeric matrix (Lee et al. Citation2015, Citation2015, Citation2019; Lee, Kim, and Hwang Citation2019). The percolating networks formed by the conductive filler in the polymer matrix confer electrical conductivity on the composite fibers. To ensure sufficient conductivity, however, the amount of added filler should exceed the percolation threshold, the point at which nanoparticles or nanowires form enough networks to create a conducting path across the entire area of the composite. This increases the material costs of conductive composite fibers. In addition, it is difficult to prevent voids from forming during the fabrication process, and their inhomogeneous distribution within composite fibers degrades the mechanical properties of these fibers.
Recently, fibers coated with a conductive layer have attracted significant attention for use in wearable devices due to their easy fabrication process and high electrical conductivity (Hwang et al. Citation2020; Kony, Tabor, and Ghosh Citation2019; Pan et al. Citation2020; Wu et al. Citation2016). Conductive layers such as metal thin films (Bard et al. Citation2019; Feng et al. Citation2010; Kony, Tabor, and Ghosh Citation2019), conductive polymer layers (Choi et al. Citation2022; Idumah Citation2022; Kim et al. Citation2003; Lund et al. Citation2020), or metal nanoparticle or nanowire networks (Hong et al. Citation2022, Arat, Jia, and Plentz Citation2022; Qian et al. Citation2022) are employed to cover the surface of the core fiber. Because conductive layer-coated fibers use commercially available fibers as their core, voids are not an issue. In addition, the conductive region is only on the surface of the fiber; thus the material costs are lower when compared to composite fibers. Therefore, conductive layer-coated fibers offer excellent mechanical properties, high electrical conductivity, and low fabrication costs.
Polymeric fibers and natural fibers can be used as the core for conductive layer-coated fibers. Though polymeric fibers offer the benefits of relatively low production costs and the freedom to tune the mechanical properties, the use of natural fibers such as silk or cotton is preferable for next-generation wearable devices because of their eco-friendly characteristics and their ease of production on a mass scale using existing facilities (Lu et al. Citation2022; Mayank, Sethi, and Gudwani Citation2022; Sammi et al. Citation2022). In particular, silk is of the most widely used materials for the core of conductive fibers due to its excellent mechanical reliability and good compatibility with conductive materials. Thus, a number of studies have developed silk-based conductive fibers with good mechanical strength and high electrical conductivity (Darabi et al. Citation2020; Hwang et al. Citation2020; Lund et al. Citation2018; Ryan et al. Citation2017; Seo et al. Citation2022). However, despite the advantages of natural silk-based conductive fibers, one of the difficulties in using them in wearable devices is ensuring that they are washable. The conductive layer on the fiber surface can be easily removed due to mechanical and chemical damage during machine washing, which degrades the electrical conductivity of the conductive fibers and leads to the malfunction of wearable devices.
Therefore, strategies to enhance the washability of conductive fibers are required. Recently, enhanced washability through the use of poly(3,4-ethylenedioxythiophene) polystyrene sulfonate (PEDOT:PSS) on silk fibers has been reported (Lund et al. Citation2018; Ryan et al. Citation2017). The strong electrostatic interaction between PEDOT:PSS and the silk surface results in excellent machine washability. Consequently, a number of studies have sought to optimize the electrical or chemical properties of PEDOT:PSS-coated silk-based conductive fibers using various materials such as silver (Ag) nanowires (Hwang et al. Citation2020), carbon nanotubes (CNTs) (Seo et al. Citation2022), and manganese dioxide (MnO2) (Wang et al. Citation2021). In this review, recent progress on PEDOT:PSS-coated silk-based conductive fibers using different types of functional material to enhance their washability and optimize their electrical or chemical properties are summarized. The advantages and disadvantages of these material systems are discussed and future directions for research on machine-washable silk-based conductive fibers are proposed. This review thus provides a comprehensive overview of the technological trends in PEDOT:PSS-coated conductive silk fibers with the aim to promote the development of next-generation textile-based wearable devices.
1.1 PEDOT:PSS-coated conductive silk yarn
Ryan et al. reported a machine-washable PEDOT:PSS-coated conductive yarn (Ryan et al. Citation2017). , b show photo and cross-sectional SEM image of PEDOT:PSS-coated conductive silk fibers, respectively, which confirmed that the PEDOT:PSS uniformly covered the surface of silk yarns. Machine-washability was enhanced by utilizing the strong electrostatic attraction between PEDOT:PSS and degummed silk yarn. PEDOT:PSS mixed with ethylene glycol (EG) has a relatively low pH of 2, which results in a negative net charge, while silk yarn has a positively charged surface, leading to the strong attraction between PEDOT:PSS and the silk surface. , d present photo of conductive fibers in water and the change in the conductivity of PEDOT:PSS-coated conductive silk fibers over four machine-washing cycles, respectively. In machine-washing tests with commercial detergent at 30°C for 50 min and a 900-rpm spin-drying cycle, the PEDOT:PSS-coated silk yarn did not exhibit any significant change in conductivity even after four washing cycles. shows the bending test results. The PEDOT:PSS-coated silk yarn exhibited good mechanical wear resistance under repeated bending tests over Teflon bars with diameters of 4.5 and 52 mm (). However, the conductivity of the fiber was relatively low at 18 ± 6 S/cm ().
Figure 2. Features of PEDOT:PSS-coated conductive silk fibers fabricated by using a dip coating process. (a) Photo and (b) cross-sectional SEM image of PEDOT:PSS-coated conductive silk fibers. (c) Photo of conductive fibers in water. (d) Change in the conductivity of PEDOT:PSS-coated conductive silk fibers over four machine-washing cycles. (e) Distribution of the conductivity of PEDOT:PSS-coated conductive silk fibers. (f) Change in the resistance of PEDOT:PSS-coated conductive silk fibers over 1000 bending cycles. Reproduced with permission from ref. (Ryan et al. Citation2017).
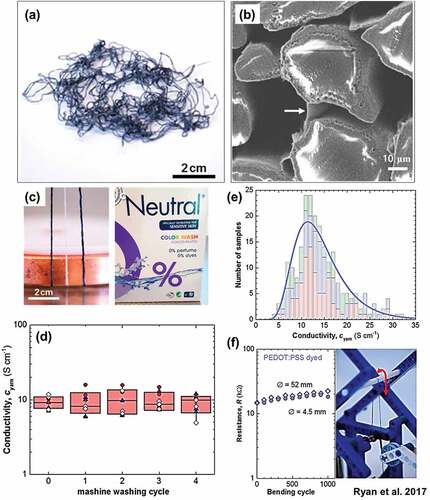
In addition, Lund et al. demonstrated that PEDOT:PSS-coated silk yarn could be mass-produced through a roll-to-roll coating process in which 100 m of conductive yarn was fabricated in a single cycle (Lund et al. Citation2018). presents schematic overview of the roll-to-roll production of PEDOT:PSS-coated silk yarn. The conductive yarns were continuously produced with the total length of 100 m. are the results of bending and machine-washing tests. This PEDOT:PSS-coated silk yarn showed high resistance to machine washing and mechanical deformation, with no significant change in electrical conductivity observed after 15 washing cycles at 30 ºC for 40 min with 20 ml of detergent () and after 1000 bending cycles (). Despite the excellent machine-washability of the PEDOT:PSS-coated silk yarn, however, its electrical conductivity was low at 74 ± 18 S/cm. This is an inherent limitation of PEDOT:PSS, which has intrinsically lower electrical conductivity compared to metallic materials.
Figure 3. Features of PEDOT:PSS-coated conductive silk fibers fabricated through a roll-to-roll process. (a) Schematic overview of the roll-to-roll production of PEDOT:PSS-coated silk fibers. Change in the resistance of PEDOT:PSS-coated silk fibers over (b) 1000 bending cycles and (c) 15 machine-washing cycles. Reproduced with permission from ref. (Lund et al. Citation2020).
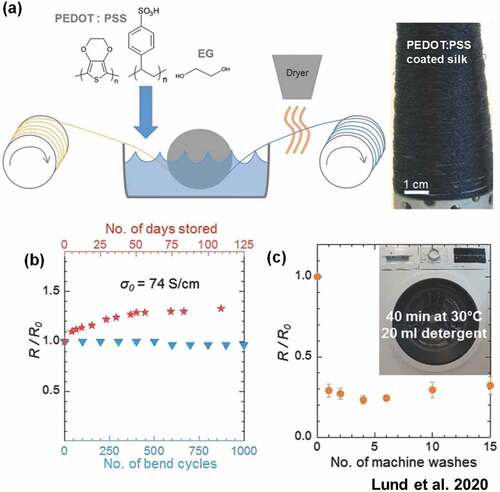
1.2 PEDOT:PSS/Ag nanowire-coated conductive silk yarn
To resolve the conductivity issue, Hwang et al. proposed an integrated system of Ag nanowires and PEDOT:PSS for the conducting layer of silk yarn (Hwang et al. Citation2020). Ag nanowires with an aspect ratio greater than 1,000 were used to form a percolated network structure through which electrical current can flow. Because of their high electrical conductivity of Ag (62.1 × 108 S/cm), Ag nanowire networks tend to exhibit much higher conductivity than electrodes consisting of CNTs, graphene, or PEDOTO:PSS (Lee et al. Citation2008). In addition, Ag nanowire networks are beneficial for releasing the strain imposed by stretching the network without severe stress localization (An et al. Citation2017; Hwang et al. Citation2014; Kim et al. Citation2019; Lee, Kim, and Hwang Citation2019; Park et al. Citation2019; Seo and Hwang Citation2019). Therefore, Ag nanowire networks have been widely used as the conducting layer of stretchable or flexible electrodes. However, Ag nanowires weakly bind to the substrate through physisorption, thus they are not strongly resistant to external mechanical damage. Therefore, to use Ag nanowires in conductive silk yarn, the poor machine washability arising from the weak adhesion of Ag nanowires to the silk surface must be solved.
shows schematic description of the preparation of conductive silk yarn with an Ag nanowire/PEDOT:PSS composite coating. Sequential dip coating was used by Hwang et al. to fabricate PEDOT:PSS-coated silk yarn, with Ag nanowires and PEDOT:PSS sequentially coated onto silk yarn followed by a drying process (Hwang et al. Citation2020). Pre-washed silk yarn was dipped in a Ag nanowire solution followed by drying at 180 ºC for 5 min, during which Ag nanowires attached themselves to the silk surface. The Ag nanowire-coated silk yarn was then dipped in a PEDOT:PSS solution. As described in Section 2.1, the PEDOT:PSS was strongly bound to the silk surface through electrostatic attraction while holding the Ag nanowires between the two. presents the SEM images of each layer that confirmed the reliable coating of Ag nanowires and PEDOT:PSS on silk surface. In this structure, the PEDOT:PSS layer protects the Ag nanowires from external damage from machine washing or mechanical wear. , f are the results of machine washing and bending tests. The PEDOT:PSS/Ag nanowire-coated silk yarn thus demonstrated excellent machine washability, with only a two-fold increase in resistance after 10 washing cycles at 30 ºC for 20 min with detergent, while silk yarn covered only with Ag nanowires completely lost its electrical conductivity after a single washing cycle (). To demonstrate its wear resistance, the PEDOT:PSS/Ag nanowire-coated silk yarn was subjected to 300,000 cycles of bending at a radius of 1.5 mm. Only a 30% increase in resistance was observed for the PEDOT:PSS/Ag nanowire-coated silk yarn while the Ag nanowire-coated silk yarn experienced an increase in resistance of over 1000% (). The PEDOT:PSS coating was thus confirmed to successfully protect Ag nanowires from delamination due to external forces, thus maintaining the excellent electrical conductivity of the yarn even after multiple machine washing and bending cycles.
Figure 4. Features of Ag nanowire/pedot:pss-coated conductive silk yarns fabricated by using a dip coating process. (a) Schematic description of the preparation of conductive silk yarn with an Ag nanowire/PEDOT:PSS composite coating. (b) Top view and (c, d) cross-sectional SEM images of individual filaments that make up the conductive silk yarn. Normalized change in the resistance of silk yarn with AgNW and AgNW/PEDOT:PSS coatings as a function of the number of (e) machine-washing cycles and (f) bending cycles. R0 is the initial resistance before testing, and R is the resistance measured after the washing/bending/tensile tests. Reproduced with permission from ref. (Hwang et al. Citation2020).
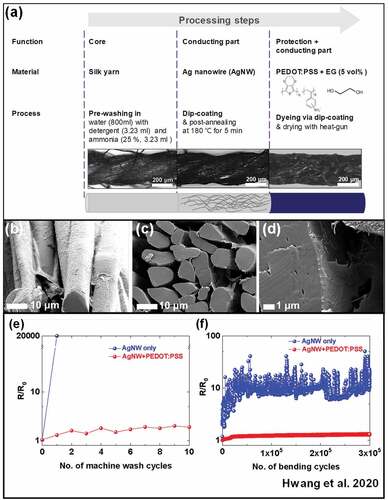
More importantly, in this work by Hwang et al., the electrical conductivity of conductive fibers was greatly enhanced by adding Ag nanowires to PEDOT:PSS-coated conductive silk fibers. shows the change in electrical conductivity as a function of dip-coating cycles. The metallic Ag nanowires, which have a high intrinsic electrical conductivity, formed a percolation network on the silk surface during the dip-coating process, and the electrical conductivity of the silk yarn was able to be controlled by changing the number of times it was dipped into the Ag nanowire solution. In particular, conductivity of 284 S/cm was achieved using seven coats of Ag nanowires (). The subsequent PEDOT:PSS coating enhanced the electrical conductivity of the conductive silk yarn further because it filled the vacant areas between individual nanowires, providing additional paths for the flow of current. Thus, the conductivity of the Ag nanowire-coated silk yarn increased to 320 S/cm. It should be noted that drying at a relatively high temperature of 180 ºC was required to achieve the optimal electrical conductivity. shows the change in the electrical conductivity as a function of the post-annealing time at 180°C. The synthesized Ag nanowires were covered with a thin polyvinylpyrrolidone (PVP) layer, which hindered current flow, leading to a high junction resistance within the Ag nanowire networks. However, the PVP layer was able to be removed using post-thermal annealing at 180 ºC, thus optimizing the electrical conductivity after each coating of Ag nanowires (). At annealing temperatures higher than 180 ºC, sintering of the Ag nanowires occurred, reducing their surface energy and breaking the nanowire networks, thus reducing the electrical conductivity as shown in (Hwang et al. Citation2017).
Figure 5. Factors affecting the electrical conductivity of Ag nanowire/pedot:pss-coated conductive silk yarns. (a) Electrical conductivity of silk yarn as a function of the number of dip-coating cycles in a Ag nanowire solution. (b) Normalized conductivity of the silk yarn after two (black), three (red), and four (blue) dipping cycles as a function of the post-annealing time at 180°C. σ0 indicates the initial conductivity before annealing. Reproduced with permission from ref (Hwang et al. Citation2020). (c) SEM images of Ag nanowires after annealing at 380 ºC for 20 min. Reproduced with permission from ref. (Hwang et al. Citation2017).
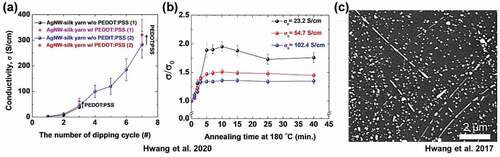
Darabi et al. also demonstrated that an integrated PEDOT:PSS and Ag nanowire structure is suitable for cellulose yarn (Darabi et al. Citation2020). , b shows schematic description of roll-to-roll production process for PEDOT:PSS/AgNW-coated cellulose yarn and (b) photo of produced fiber. They produced ultra-long (>100 m) PEDOT:PSS/Ag nanowire-coated cellulose yarn using a roll-to-roll dip-coating process () that achieved an electrical conductivity of 181 S/cm. , d are the results of machine-washing and bending tests. The surface of cellulose has a net positive charge similar to silk yarn, thus electrostatic attraction enhances the adhesion between the negatively charged PEDOT:PSS and the cellulose surface. Due to this mechanism, the PEDOT:PSS/Ag nanowire-coated cellulose yarn did not experience any significant change in conductivity after 10 machine-washing cycles at 30 ºC and 800 rpm (). Furthermore, the PEDOT:PSS/Ag nanowire coated cellulose yarn was subjected to 1000 bending cycles, and no change in resistance was observed (). This reliable and mass-producible PEDOT:PSS/Ag nanowire-coated cellulose yarn with high electrical conductivity thus has the potential to be used in a range of next-generation textile-based wearable devices.
Figure 6. Features of Ag nanowire/pedot:pss-coated conductive silk yarns fabricated by using a roll-to-roll process. (a) Schematic description of roll-to-roll production process for PEDOT:PSS/AgNW-coated cellulose yarn and (b) photo of produced fiber. Change in the resistance of PEDOT:PSS/AgNW-coated cellulose yarn as a function of the number of (c) machine-washing cycles and (d) bending cycles. R0 is the initial resistance before testing, and R is the resistance measured after the washing/bending/tensile tests. Reproduced with permission from ref. (Darabi et al. Citation2020).
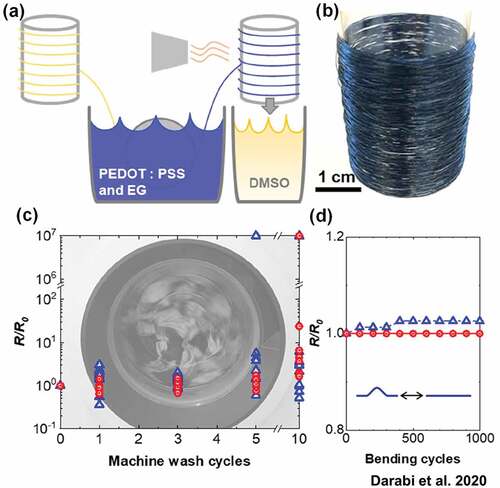
1.3 PEDOT:PSS/Ag nanowire/carbon nanotube-coated conductive silk yarn
With the addition of CNTs, conductive silk yarn can exhibit strong electrochemical properties that can be used for wearable supercapacitor applications. Seo et al. demonstrated washable PEDOT:PSS/Ag nanowire/CNT-coated conductive silk yarn for wearable supercapacitors (Seo et al. Citation2022). present schematic illustration of the fabrication process for conductive silk yarn with a Ag nanowire/CNT/PEDOT:PSS composite coating and corresponding SEM images of coating steps of Ag nanowire, CNT and PEDOT:PSS layers, respectively. Silk yarn was sequentially dip-coated in Ag nanowires, CNTs, and PEDOT:PSS. The PVP layer on the Ag nanowires formed hydrogen bonds with the silk surface and the defects in the CNTs (Lee et al. Citation2016); thus, Ag nanowires can stick to the silk surface during the sequential dipping process to make PEDOT:PSS/Ag nanowire/CNT-coated conductive silk yarn. shows the results of washing and bending tests, respectively. The PEDOT:PSS/Ag nanowire/CNT-coated conductive silk yarn was stable under washing at 30 ºC and 300 rpm with a detergent for 100 min (), exhibiting a conductivity of 280 S/cm. In addition, bending tests revealed that PEDOT:PSS/Ag nanowire/CNT-coated conductive silk yarn had a less than 10% increase in resistance even after 300,000 bending cycles with a bending radius of 1.5 mm, while Ag nanowire/CNT-coated conductive yarn without a PEDOT:PSS layer experienced a 1000% increase in resistance (). At the low pH (≈2) of the PEDOT:PSS, the silk surface have a net positive charge (isoelectric point pH ≈ 4), which results in the electrostatic attraction to the negatively charged sulfonate groups of PEDOT:PSS (Hwang et al. Citation2020). The Ag nanowires and CNTs were located between the PEDOT:PSS and silk surface that were strongly bound together through the electrostatic interaction. Therefore, the top layer, i.e. PEDOT:PSS, could be stable from washing or bending, which protected the Ag nanowires and CNT.
Figure 7. Features of Ag nanowire/CNT/PEDOT:PSS-coated conductive silk yarns fabricated by using a roll-to-roll process. (a) Schematic illustration of the fabrication process for conductive silk yarn with a Ag nanowire/CNT/PEDOT:PSS composite coating, and SEM images taken of (b) bare silk and (c) Ag nanowire-coated, (d) Ag nanowire/CNT-coated, and (e) Ag nanowire/CNT/PEDOT:PSS-coated silk fibers. Normalized change in the resistance of fiber electrodes as a function of (f) the dipping time in water and (g) the number of bending cycles. Reproduced with permission from ref. (Seo, Ha, et al. Citation2022).
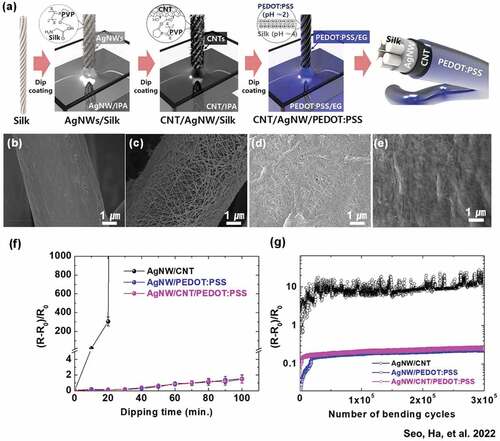
An integrated system of PEDOT:PSS, Ag nanowires, and CNTs is also beneficial for electrochemical applications because each component has obvious advantages. Ag nanowires confer high electrical conductivity on the conductive fibers, thus acting as an excellent current collector in a supercapacitor. CNTs are widely used as active materials in supercapacitors because of their ability to produce a high power density through the formation of an electrical double layer (EDL) structure. However, supercapacitors using CNTs suffer from a low energy density caused by non-Faradic reactions. PEDOT:PSS is a pseudocapacitor material that has a higher theoretical specific capacitance than that of EDL materials, and it offers a high energy density by storing electrical energy through Faradic reactions. Therefore, the combination of Ag nanowires, CNTs, and PEDOT:PSS is expected to take advantage of the excellent current collection properties of Ag nanowires, the high power density of CNTs, and the high energy density of PEDOT:PSS.
In the work by Seo et al, a supercapacitor based on the PEDOT:PSS/Ag nanowire/CNT-coated conductive silk yarn was fabricated using a hydrogel electrolyte. shows the electrochemical properties of Ag nanowire/CNT/PEDOT:PSS and Ag nanowire/PEDOT:PSS conductive silk yarn electrodes. Polyacrylamide (PAAm)-based hydrogel was poured into the container, where the conductive fibers were free-standing, which was then UV-cured to form solid-state supercapacitor. The ternary PEDOT:PSS/Ag nanowire/CNT system generated a better electrochemical performance than did binary- or single-component systems (). The volumetric power and energy density of the supercapacitor produced using PEDOT:PSS/Ag nanowire/CNT-coated conductive silk yarn were 8 − 19 mWh cm−3 and 8 − 13 W cm−3, respectively, higher than previously reported results for supercapacitors using other types of material (). In addition, the supercapacitor using PEDOT:PSS/Ag nanowire/CNT-coated conductive silk yarn was stable under mechanical deformation, with the specific capacitance maintained at 94% and 93% after 90° bending and 20% stretching tests, respectively ().
Figure 8. Electrochemical properties of Ag nanowire/CNT/PEDOT:PSS and Ag nanowire/PEDOT:PSS conductive silk yarn electrodes: (a) charge−discharge cycles, (b) cyclic voltammetry, (c) volumetric capacitance, and (d) electrical impedance testing. (e) Electrochemical performance evaluated using a Ragone plot. (f) Normalized change in the capacitance of a planar-type supercapacitor in response to mechanical bending. Changes in the discharge time of a planar-type supercapacitor in response to (g) mechanical bending and (h) mechanical stretching. Reproduced with permission from ref. (Wang et al. Citation2021).
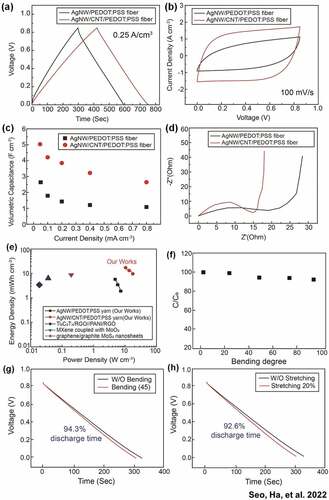
1.4 PEDOT:PSS/MnO2-coated conductive silk yarn
Wang et al. reported the development of PEDOT:PSS/MnO2-coated conductive silk fibers for wearable sensors (Wang et al. Citation2021). Silk was dipped in potassium permanganate (KMnO4) followed by rinsing in water and drying in an oven, which led to a MnO2 layer forming on the silk surface. presents schematic illustration of the preparation process for conductive silk fibers. The MnO2-coated silk fibers were then immersed in a mixed solution of 3,4-ethylenedioxythiophene (EDOT), ammonium persulfate ((NH₄)₂S₂O₈), and sulfuric acid (H2SO4), which produced PEDOT:PSS/MnO2-coated conductive silk fibers through an in-situ polymerization reaction (). shows the results of washing tests. The resistivity of the PEDOT:PSS/MnO2-coated silk fibers was 1.5 Ω·cm, and they were also washable in water, leading to only a 2.5-fold increase in resistance even after eight washing cycles. presents the results of washing tests in different solvents. They were stable in the presence of various chemicals, with less than a two-fold increase in resistance observed when soaking the fibers in sodium chloride (NaCl), ethanol, and N-methylpyrrolidone (NMP) solutions for 30 h (). These results confirmed that a PEDOT:PSS coating can enhance the washability of conductive fibers in both water and various organic solvents such as ethanol and NMP.
Figure 9. Features of PEDOT:PSS/MnO2-coated conductive silk yarns fabricated by using a roll-to-roll process. (a) Schematic illustration of the preparation process for conductive silk fibers. Relative resistance of PEDOT/silk fibers (b) under eight washing cycles and (c) with different solvents. (d) Sensitivity of PEDOT/silk fibers to temperature in the range of 293.15–323.15 K (during the heating and cooling process). (e) Photograph of an LED integrated with PEDOT/silk fibers. Reproduced with permission from ref. (Wang et al. Citation2021).
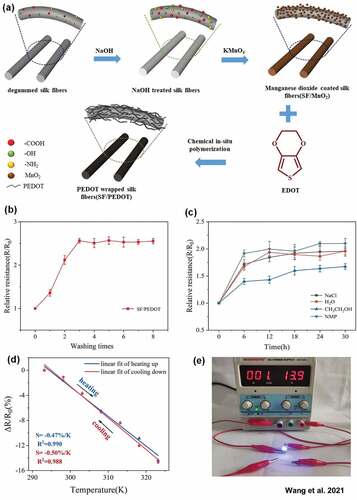
The purpose of the MnO2 coating is to confer sensing properties on the conductive silk fibers. MnO2 is a naturally abundant substance that is widely used as a sensing material due to its cost-effectiveness and low toxicity. In addition, its excellent physical and chemical properties allow MnO2 to be used in various types of device, such as catalytic and electrochemical devices (Dey et al. Citation2018; Ma et al. Citation2020; Yuan et al. Citation2020). shows the sensitivity of the conductive fibers to the temperature difference. Wang et al. employed MnO2 in a wearable temperature sensing system. PEDOT:PSS/MnO2-coated conductive silk fibers exhibited an excellent thermal sensitivity with an error of only −0.47%/K when used in a temperature sensor, compared to 0.61%/℃ for a PEDOT: PSS-CNT temperature sensor and 0.634%/℃ for a reduced graphene oxide (rGO)/polyethylene terephthalate (PET) temperature sensor (Cui, Robles Poblete, and Zhu Citation2019; Honda et al. Citation2014; Liu et al. Citation2018). Furthermore, the conductive fiber successfully contributed to the operation of LED lights as shown in . This illustrated that PEDOT:PSS-based conductive fibers can be used in various sensing devices by combining them with appropriate functional materials such as MnO2.
The performance and main functionality of the PEDOT:PSS/silk-based conductive fibers are summarized in . A negatively charged PEDOT:PSS solution with EG strongly adheres to the positively charged silk surface. Thus, most silk fibers with a PEDOT:PSS layer exhibit excellent stability under the repeated cycles of machine washing. However, silk-based-based conductive fibers coated with PEDOT:PSS only have a relatively low electrical conductivity of 74 S/cm (). To improve the conductivity of PEDOT:PSS-coated conductive silk fibers, Ag nanowires have been inserted between the PEDOT:PSS layer and silk surface. Metallic Ag nanowire-coated silk fibers have a high electrical conductivity, while excellent machine-washability was maintained by the PEDOT:PSS layer. By adopting other functional materials such as CNT or MnO2, PEDOT:PSS-coated conductive silk fibers offer excellent functionality and machine-washability. In particular, PEDOT:PSS/CNT/Ag nanowire-coated conductive silk fibers exhibit good electrochemical performance, while PEDOT:PSS/MnO2/Ag nanowire-coated conductive silk fibers have a high sensitivity to changes in temperature.
Table 2. Summary of various PEDOT:PSS/silk-based conductive fibers.
2 Summary
In summary, various types of silk-based conductive fibers that employ PEDOT:PSS as an adhesion promoter to enhance their machine-washability have been introduced. The PEDOT:PSS coating significantly improved the machine-washability due to the strong electrostatic attraction force between the PEDOT:PSS and silk surface. The excellent adhesion properties of PEDOT:PSS to silk surface also secured the mechanical stabilities of the silk-based conductive fibers under repeated deformation. More importantly, the functionalities of the conductive fibers such as high electrical conductivity, electrochemical property or thermal sensitivity can be obtained by incorporating with the various nanomaterials including Ag nanowire, CNT or MnO2. Despite the recent progress in PEDOT:PSS/silk-based conductive fibers, there is still significant room for the development of other variations of these fibers. By inserting different types of functional materials between the silk core and PEDOT:PSS layer, various types of conductive fibers with excellent machine-washability can be fabricated (Lou Citation2005; Pei, Zhang, and Chen Citation2019; Shahzad et al. Citation2019), further expanding the textile-based wearable device industry.
Highlights
Strategies to enhance the stability of silk-based conductive fibers utilizing PEDOT:PSS are discussed.
Various types of PEDOT:PSS/silk-based conductive fiber are reviewed.
Research trend and future research direction of PEDOT:PSS/silk-based conductive fiber are discussed.
Disclosure statement
No potential conflict of interest was reported by the author(s).
Additional information
Funding
References
- An, C.-H., S. Kim, H.-J. Lee, and B. Hwang. 2017. Facile patterning using dry film photo-resists for flexible electronics: Ag nanowire networks and carbon nanotube networks. Journal of Materials Chemistry C 5 (19):4804–17. doi:10.1039/C7TC00885F.
- Arat, R., G. Jia, and J. Plentz. 2022.Wet chemical method for highly flexible and conductive fabrics for smart textile applications. The Journal of the Textile Institute 1: 1–6.doi: 10.1080/00405000.2022.2061760
- Bard, S., F. Schönl, M. Demleitner, and V. Altstädt. 2019. Copper and Nickel Coating of Carbon Fiber for Thermally and Electrically Conductive Fiber Reinforced Composites. Polymers 11 (5):823. doi:10.3390/polym11050823.
- Chen, J., H. Li, L. Zhang, C. Du, T. Fang, and J. Hu. 2020. Direct Reduction of Graphene Oxide/Nanofibrillated Cellulose Composite Film and its Electrical Conductivity Research. Scientific Reports 10 (1):3124. doi:10.1038/s41598-020-59918-z.
- Choi, S.-M., E.-J. Shin, Z. Sun-Mi, K.-M. Rao, Y.-J. Seok, S.-Y. Won, and S.-S. Han. 2022. Revised Manuscript with Corrections: Polyurethane-Based Conductive Composites: From Synthesis to Applications. International Journal of Molecular Sciences 23 (4):1938. doi:10.3390/ijms23041938.
- Cui, Z., F. Robles Poblete, and Y. Zhu. 2019. Tailoring the Temperature Coefficient of Resistance of Silver Nanowire Nanocomposites and their Application as Stretchable Temperature Sensors. ACS Applied Materials & Interfaces 11 (19):17836–42. doi:10.1021/acsami.9b04045.
- Darabi, S., M. Hummel, S. Rantasalo, M. Rissanen, I. Öberg Månsson, H. Hilke, B. Hwang, M. Skrifvars, M. M. Hamedi, H. Sixta, et al. 2020. Green Conducting Cellulose Yarns for Machine-Sewn Electronic Textiles. ACS Applied Materials & Interfaces 12 (50):56403–12. doi:10.1021/acsami.0c15399.
- Dey, G., L. Yang, K.-B. Lee, and L. Wang. 2018. Characterizing Molecular Adsorption on Biodegradable MnO2 Nanoscaffolds. The Journal of Physical Chemistry C 122 (50):29017–27. doi:10.1021/acs.jpcc.8b09562.
- Feng, Y., H. Zhang, Y. L. Li, and C. F. Rao. 2010. Temperature Sensing of Metal-Coated Fiber Bragg Grating. IEEE/ASME Transactions on Mechatronics 15 (4):511–19. doi:10.1109/TMECH.2010.2047111.
- Gao, Q., M. Wang, X. Kang, C. Zhu, and M. Ge. 2020. Continuous wet-spinning of flexible and water-stable conductive PEDOT: PSS/PVA composite fibers for wearable sensors. Composites Communications 17:134–40. doi:10.1016/j.coco.2019.12.001.
- Gibbs, P. T., and H. Asada. 2005. Wearable Conductive Fiber Sensors for Multi-Axis Human Joint Angle Measurements. Journal of Neuroengineering and Rehabilitation 2 (1):7. doi:10.1186/1743-0003-2-7.
- Haghi, M., K. Thurow, and R. Stoll. 2017. Wearable Devices in Medical Internet of Things: Scientific Research and Commercially Available Devices. Hir 23 (1):4–15. doi:10.4258/hir.2017.23.1.4.
- Hansora, D. P., N. G. Shimpi, and S. Mishra. 2015. Performance of hybrid nanostructured conductive cotton materials as wearable devices: An overview of materials, fabrication, properties and applications. RSC advances 5 (130):107716–70. doi:10.1039/C5RA16478H.
- Heo, J. S., M. Faruk Hossain, and I. Kim. 2020. Challenges in Design and Fabrication of Flexible/Stretchable Carbon- and Textile-Based Wearable Sensors for Health Monitoring: A Critical Review. Sensors 20 (14):3927. doi:10.3390/s20143927.
- Honda, W., S. Harada, T. Arie, S. Akita, and K. Takei. 2014. Wearable, Human-Interactive, Health-Monitoring, Wireless Devices Fabricated by Macroscale Printing Techniques. Advanced Functional Materials 24 (22):3299–304. doi:10.1002/adfm.201303874.
- Hong, X., W. Zhao, R. Yu, Q. Wang, F. Zeng, Y. Tao, Z. Jin, and C. Zhu. 2022. Multifunctional silver nanowire coated fabric capable of electrothermal, resistance temperature-sensitivity, electromagnetic interference shielding, and strain sensing. Journal of Industrial Textiles 0(0): 15280837221076029. doi:10.1177/15280837221076029.
- Hwang, B., Y. An, H. Lee, E. Lee, S. Becker, Y.-H. Kim, and H. Kim. 2017. Highly Flexible and Transparent Ag Nanowire Electrode Encapsulated with Ultra-Thin Al2O3: Thermal, Ambient, and Mechanical Stabilities. Scientific reports 7 (1):41336. doi:10.1038/srep41336.
- Hwang, B., and T. Gwang Yun. 2019. Stretchable and patchable composite electrode with trimethylolpropane formal acrylate-based polymer. Composites Part B: Engineering 163:185–92. doi:10.1016/j.compositesb.2018.11.009.
- Hwang, B., Y. Han, and P. Matteini. 2022. Bending fatigue behavior of Ag nanowire/Cu thin-film hybrid interconnects for wearable electronics. Facta Universitatis, Series: Mechanical Engineering. doi:10.22190/FUME220730040H.
- Hwang, B., A. Lund, Y. Tian, S. Darabi, and C. Müller. 2020. Machine-Washable Conductive Silk Yarns with a Composite Coating of Ag Nanowires and PEDOT:PSS. ACS Applied Materials & Interfaces 12 (24):27537–44. doi:10.1021/acsami.0c04316.
- Hwang, B., H.-A.S Shin, T. Kim, Y.-C. Joo, and S. Min Han. 2014. Highly Reliable Ag Nanowire Flexible Transparent Electrode with Mechanically Welded Junctions. Small 10 (16):3397–404. doi:10.1002/smll.201303906.
- Idumah, C. I. 2022. Recent advancements in conducting polymer bionanocomposites and hydrogels for biomedical applications. International Journal of Polymeric Materials and Polymeric Biomaterials 71 (7):513–30. doi:10.1080/00914037.2020.1857384.
- Kim, S., J. Kim, D. Kim, B. Kim, H. Chae, H. Yi, and B. Hwang. 2019. High-Performance Transparent Quantum Dot Light-Emitting Diode with Patchable Transparent Electrodes. ACS Applied Materials & Interfaces 11 (29):26333–38. doi:10.1021/acsami.9b05969.
- Kim, H. K., M. Sun Kim, S. Yeon Chun, Y. Heum Park, B. Soo Jeon, J. Young Lee, Y. Ki Hong, J. Joo, and S. Hun Kim. 2003. Characteristics of electrically conducting polymer-coated textiles. Molecular Crystals and Liquid Crystals 405 (1):161–69. doi:10.1080/15421400390263550.
- Kony, C., J. Tabor, and T. K. Ghosh. 2019. Electrically Conductive Coatings for Fiber-Based E-Textiles. Fibers 7 (6):51. doi:10.3390/fib7060051.
- Kwak, Y. H., W. Kim, K. Bum Park, K. Kim, and S. Seo. 2017. Flexible heartbeat sensor for wearable device. Biosensors & bioelectronics 94:250–55. doi:10.1016/j.bios.2017.03.016.
- Lee, Y., S. Bae, B. Hwang, M. Schroeder, Y. Lee, and S. Baik. 2019. Considerably improved water and oil washability of highly conductive stretchable fibers by chemical functionalization with fluorinated silane. Journal of Materials Chemistry C 7 (39):12297–305. doi:10.1039/C9TC03944A.
- Lee, J.-Y., S. T. Connor, Y. Cui, and P. Peumans. 2008. Solution-Processed Metal Nanowire Mesh Transparent Electrodes. Nano letters 8 (2):689–92. doi:10.1021/nl073296g.
- Lee, T.-W., M. Han, S.-E. Lee, and Y. Gyu Jeong. 2016. Electrically conductive and strong cellulose-based composite fibers reinforced with multiwalled carbon nanotube containing multiple hydrogen bonding moiety. Composites Science and Technology 123:57–64. doi:10.1016/j.compscitech.2015.12.006.
- Lee, C., H. Kim, and B. Hwang. 2019. Fracture behavior of metal oxide/silver nanowire composite electrodes under cyclic bending. Journal of Alloys and Compounds 773:361–66. doi:10.1016/j.jallcom.2018.09.212.
- Lee, J., H. Kwon, J. Seo, S. Shin, J. Hoon Koo, C. Pang, S. Son, J. Hyung Kim, Y. Hoon Jang, D. Eun Kim, et al. 2015. Conductive Fiber-Based Ultrasensitive Textile Pressure Sensor for Wearable Electronics. Advanced Materials 27 (15):2433–39. doi:10.1002/adma.201500009.
- Lee, S., S. Shin, S. Lee, J. Seo, J. Lee, S. Son, H. Jin Cho, H. Algadi, S. Al-Sayari, D. Eun Kim, et al. 2015. Ag Nanowire Reinforced Highly Stretchable Conductive Fibers for Wearable Electronics. Advanced Functional Materials 25 (21):3114–21. doi:10.1002/adfm.201500628.
- Liu, G., Q. Tan, H. Kou, L. Zhang, J. Wang, W. Lv, H. Dong, and J. Xiong. 2018. A Flexible Temperature Sensor Based on Reduced Graphene Oxide for Robot Skin Used in Internet of Things. Sensors 18 (5):1400. doi:10.3390/s18051400.
- Lou, C.-W. 2005. Process of Complex Core Spun Yarn Containing a Metal Wire. Textile Research Journal 75 (6):466–73. doi:10.1177/0040517505053871.
- Lu, L., W. Fan, S. Ge, R. Keey Liew, Y. Shi, H. Dou, S. Wang, and S. Shiung Lam. 2022. Progress in recycling and valorization of waste silk. The Science of the Total Environment 830:154812. doi:10.1016/j.scitotenv.2022.154812.
- Lund, A., S. Darabi, S. Hultmark, J. D. Ryan, B. Andersson, A. Ström, and C. Müller. 2018. Roll-to-Roll Dyed Conducting Silk Yarns: A Versatile Material for E-Textile Devices. Advanced Materials Technologies 3 (12):1800251. doi:10.1002/admt.201800251.
- Lund, A., Y. Tian, S. Darabi, and C. Müller. 2020. A polymer-based textile thermoelectric generator for wearable energy harvesting. Journal of Power Sources 480:228836. doi:10.1016/j.jpowsour.2020.228836.
- Mayank, A. B., V. Sethi, and H. Gudwani. 2022. Spider-silk composite material for aerospace application. Acta astronautica 193:704–09. doi:10.1016/j.actaastro.2021.08.013.
- Ma, J., Y. Zhang, M. Yuan, and C. Nan. 2020. Li Ion Exchanged α-MnO2 Nanowires as Efficient Catalysts for Li-O2 Batteries. Chemical Research in Chinese Universities 36 (6):1261–64. doi:10.1007/s40242-020-0077-3.
- Muhammad, A., Z. Hassan, S. M. Mohammad, S. Rajamanickam, S. Mohammed Abed, and M. G. B. Ashiq. 2022. Realization of UV-C absorption in ZnO nanostructures using fluorine and silver co-doping. Colloid and Interface Science Communications 47:100588. doi:10.1016/j.colcom.2022.100588.
- Niu, L., X. Miao, G. Jiang, A. Wan, Y. Li, and Q. Liu. 2020. Biomechanical energy harvest based on textiles used in self-powering clothing. Journal of Engineered Fibers and Fabrics 15:1558925020967352. doi:10.1177/1558925020967352.
- Pani, D., A. Achilli, and A. Bonfiglio. 2018. Survey on Textile Electrode Technologies for Electrocardiographic (ECG) Monitoring, from Metal Wires to Polymers. Advanced Materials Technologies 3 (10):1800008. doi:10.1002/admt.201800008.
- Pan, W., J. Wang, L. Yong-Ping, X.-B. Sun, J.-P. Wang, X.-X. Wang, J. Zhang, H.-D. You, Y. Gui-Feng, and Y.-Z. Long. 2020. Facile Preparation of Highly Stretchable TPU/Ag Nanowire Strain Sensor with Spring-Like Configuration. Polymers 12 (2):339. doi:10.3390/polym12020339.
- Park, M., W. Kim, B. Hwang, and S. Min Han. 2019. Effect of varying the density of Ag nanowire networks on their reliability during bending fatigue. Scripta materialia 161:70–73. doi:10.1016/j.scriptamat.2018.10.017.
- Pei, Z., Y. Zhang, and G. Chen. 2019. A core-spun yarn containing a metal wire manufactured by a modified vortex spinning system. Textile Research Journal 89 (1):113–18. doi:10.1177/0040517517736477.
- Qian, L., D. He, H. Qin, X. Cao, J. Huang, and J. Li. 2022. Chitosan fabrics with synergy of silver nanoparticles and silver nanowires for enhanced conductivity and antibacterial activity. Journal of Industrial Textiles 51 (1_suppl):1279S–95S. doi:10.1177/15280837221101650.
- Rodrigues, J. J. P. C., D. B. De Rezende Segundo, H. A. Junqueira, M. H. Sabino, R. M. Prince, J. Al-Muhtadi, and V. H. C. De Albuquerque. 2018. Enabling Technologies for the Internet of Health Things. IEEE Access 6:13129–41. doi:10.1109/ACCESS.2017.2789329.
- Ryan, J. D., D. Alemu Mengistie, R. Gabrielsson, A. Lund, and C. Müller. 2017. Machine-Washable PEDOT:PSS Dyed Silk Yarns for Electronic Textiles. ACS Applied Materials & Interfaces 9 (10):9045–50. doi:10.1021/acsami.7b00530.
- Sammi, A., S. M. Divya, R. Kumar, and P. Chandra. 2022. Nano-bio-engineered silk matrix based devices for molecular bioanalysis. Biotechnology and Bioengineering 119 (3):784–806. doi:10.1002/bit.28021.
- Seo, Y., H. Ha, J. Young Cheong, M. Leem, S. Darabi, P. Matteini, C. Müller, T. Gwang Yun, and B. Hwang. 2022. Highly Reliable Yarn-Type Supercapacitor Using Conductive Silk Yarns with Multilayered Active Materials. Journal of Natural Fibers 19 (3):835–46. doi:10.1080/15440478.2021.1993509.
- Seo, Y., and B. Hwang. 2019. Mulberry-paper-based composites for flexible electronics and energy storage devices. Cellulose 26 (16):8867–75. doi:10.1007/s10570-019-02686-5.
- Seo, Y., S. Ko, H. Ha, N. Qaiser, M. Leem, S. Jo Yoo, J. Hyeon Jeong, K. Lee, and B. Hwang. 2022. Stretchable carbonyl iron powder/polydimethylsiloxane composites for noise suppression in gigahertz bandwidth. Composites Science and Technology 218:109150. doi:10.1016/j.compscitech.2021.109150.
- Shahzad, A., A. Rasheed, Z. Khaliq, M. Bilal Qadir, M. Qamar Khan, S. Talha Ali Hamdani, Z. Ali, A. Afzal, M. Irfan, M. Shafiq, et al. 2019. Processing of metallic fiber hybrid spun yarns for better electrical conductivity. Materials and Manufacturing Processes 34 (9):1008–15. doi:10.1080/10426914.2019.1594270.
- Sheng, J., H. Li, S. Shen, R. Ming, B. Sun, J. Wang, D. Zhang, and Y. Tang. 2021. Investigation on Chemical Etching Process of FPCB with 18 μm Line Pitch. IEEE Access 9:50872–79. doi:10.1109/ACCESS.2021.3069284.
- Shen, Y., Y. Wang, Z. Luo, and B. Wang. 2020. Durable, Sensitive, and Wide-Range Wearable Pressure Sensors Based on Wavy-Structured Flexible Conductive Composite Film. Macromolecular Materials and Engineering 305 (8):2000206. doi:10.1002/mame.202000206.
- Singh, M., S. Rana, and A. Kumar Singh. 2022. Advanced nanomaterials utilized as top transparent electrodes in semi-transparent photovoltaic. Colloid and Interface Science Communications 46:100563. doi:10.1016/j.colcom.2021.100563.
- Varghese, R., S. Salvi, P. Sood, J. Karsiya, and D. Kumar. 2022. Carbon nanotubes in COVID-19: A critical review and prospects. Colloid and Interface Science Communications 46:100544. doi:10.1016/j.colcom.2021.100544.
- Wang, Y., X. Ai, S. Lu, T. Xing, N. Qi, and G. Chen. 2021. Fabrication of a type of silk/PEDOT conductive fibers for wearable sensor. Colloids and Surfaces: A, Physicochemical and Engineering Aspects 625:126909. doi:10.1016/j.colsurfa.2021.126909.
- Wu, C., T. Whan Kim, F. Li, and T. Guo. 2016. Wearable Electricity Generators Fabricated Utilizing Transparent Electronic Textiles Based on Polyester/Ag Nanowires/Graphene Core–Shell Nanocomposites. ACS Nano 10 (7):6449–57. doi:10.1021/acsnano.5b08137.
- Yuan, R., Z. Jiang, Z. Wang, S. Gao, Z. Liu, M. Li, and G. Boczkaj. 2020. Hierarchical MnO2 nanoflowers blooming on 3D nickel foam: A novel micro-macro catalyst for peroxymonosulfate activation. Journal of Colloid and Interface Science 571:142–54. doi:10.1016/j.jcis.2020.03.041.
- Zeng, W., L. Shu, Q. Li, S. Chen, F. Wang, and X.-M. Tao. 2014. Fiber-Based Wearable Electronics: A Review of Materials, Fabrication, Devices, and Applications. Advanced Materials 26 (31):5310–36. doi:10.1002/adma.201400633.
- Zhang, H., R. He, H. Liu, Y. Niu, Z. Li, F. Han, J. Li, X. Zhang, and F. Xu. 2021. A fully integrated wearable electronic device with breathable and washable properties for long-term health monitoring. Sensors and Actuators: A, Physical 322:112611. doi:10.1016/j.sna.2021.112611.