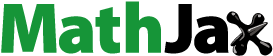
ABSTRACT
Research aims on natural fibers using nano materials according to health studies. In this research, cork powder was used as a raw natural and ecofriendly material which was doped with nano strontium titanate. The composite was extruded by twin screw extruder to obtain composite fibers. The strength of the composites produced was investigated and the results revealed that all samples containing cork with nano particles have better strength, which can be used in textile industry. On the other hand, the composite UV protection was studied and the result showed the final composite has excellent protection against UV transmission which is so important in today’s world. Also, water uptake was investigated and the SEM images proved the distribution of nano particles and cavity forms of cork after extrusion.
摘要
根据健康研究,研究对象是使用纳米材料的天然纤维. 本研究以软木粉为原料,掺入纳米钛酸锶,制成天然环保材料. 通过双螺杆挤出机挤出复合材料,获得复合纤维. 对所制备的复合材料的强度进行了研究,结果表明,所有含有纳米颗粒软木的样品都具有较好的强度,可用于纺织工业. 另一方面,对复合材料的紫外线防护进行了研究,结果表明,最终的复合材料具有优异的防紫外线透射性能,这在当今世界非常重要. 此外,研究了吸水率,SEM图像证明了挤出后软木的纳米颗粒分布和空腔形式.
Introduction
The fabrics and fibers made from cellulose such as viscose, hemp and cotton are wide-spread biopolymers in the world recognized as environmentally friendly materials. This cellulose can be reached from various sources such as plants, wood, bran etc. (Ghiasi, Davodiroknabadi, and Zohoori Citation2021; Kooshamoghadam et al. Citation2021; Liu, Wang, and Chen Citation2020; Yamin, Naddafiun, and Zohoori Citation2021). Hydrogen bonds and hydrophilicity of cellulose are due to the existence of hydroxyl groups, which is the cause of polar surface. On the other hand, these hydrophilic groups of cellulose give special properties to the fibers promoting the nucleation and growth of inorganic phases like doping and mixing cellulosic fiber with nano materials (such as zinc oxide, strontium titanate and titanium dioxide) (Karimi et al. Citation2010). In the last two decades many researchers studied on replacing synthetic fibers and composites with cellulosic ones (Joshi et al. Citation2004; Salasinska and Ryszkowska Citation2015). Dittenber et al. have introduced the use of natural cellulosic fibers/composites with excellent specific mechanical properties, easier to handle and positive economic and environmental outlook instead of synthetic fibers (Dittenber and GangaRao Citation2012).
Cork is one of the natural composites which was used over 5000 years by human. This material is made up of cellulose (and hemicellulose), lignin, suberin, etc. In the history cork has many applications especially in floating apparatuses, as well the elasticity of cork. The cellular structure of cork has penta\hexagonal shape and its lamella is clear under microscope (Castola et al. Citation2005; Silva et al. Citation2005). Due to this structure, cork cells can be filled by gas were the ability of shape recovering after compression can be achieved (Duarte and Bordado Citation2015; Mateus, Bordado, and dos Santos Citation2017). Ihamouchen et al. in their study produced cork fibers and due to the amount of used cork and polymer, collect different mechanical properties (Ihamouchen, Djidjelli, and Boukerrou Citation2021). The other study by Correia demonstrates that using cork fiber has excellent effect on improving mechanical properties such as tensile property (Correia et al. Citation2022). Also, some researches illustrated that cork fibers had good efficiency on reduction of pollutions and this fiber can be used as filtration (Wang et al. Citation2021). In the last two decades, natural fibers\fabrics have gained attention due to their especial properties such as acoustic insulation (Maleksabet and Zohoori Citation2021), availability, recycling possibility, environmental friendly, etc. Therefore, special consideration since few years has been given to use cork as base material in many applications especially in composite industry (Gil Citation2009). Previous studies have shown that using cork fiber as reinforcing composites has caused to reduce some mechanical properties such as tensile property (Moresco et al. Citation2010). However, Fernandes et al. reported that by adding coupling agent improves the tensile strength (Fernandes et al. Citation2010). On the other hand, Abdallah et al. have used several chemical modifications such as sodium hydroxide and silane in order to improve the mechanical properties such as tensile strength (Abdallah et al. Citation2010). So, these methods can be used to improve interfacial composite bonds. Dias et al. reported that cork can be used as coating of fibers and is an interesting alternative bio-sorbent material (Dias et al. Citation2013). An important research on hydrophobicity and hydrophilicity of cork was done. Research by Chanut et al. reported that the contact angle of water on cork was near 90° and due to this test, cork has an intermediate hydrophobic/hydrophilic behavior. Also, Chanut indicated that the chemical composition and specific surface can strengthen either the hydrophilic or the hydrophobic property (Chanut et al. Citation2022).
Some researches were done in order to improve the cork property (Filipe-Ribeiro, Cosme, and Nunes Citation2019; Gil Citation2015). One of the method is modifying the surface of cork with nano materials. Surface modification is very helpful in order to enhance cork properties but its major problem is that it is a temporary method (Abdallah et al. Citation2010). Nowadays a wide range of these nano particles are been used in composites which give special properties to final products (Aalipourmohammadi, Davodiroknabadi, and Nazari Citation2021; Avazpour, Karimi, and Zohoori Citation2017; Bekrani, Zohoori, and Davodiroknabadi Citation2020; Daneshian, Nayebzadeh, and Davodiroknabadi Citation2021; Zare et al. Citation2021; Zohoori et al. Citation2021). One of these nano materials is strontium titanate been active under UV irradiation due to its wide band gap (Zohoori, Karimi, and Nazari Citation2014). The perovskite oxides such as SrTiO3 have ABO3 formula. In this formula A is rare earth metal and B is transition metal. A has a large ionic radius and B has the small ionic radius. Using SrTiO3 instead of SrO and TiO2 has proved better: Sr in SrTiO3 give more ionic properties and the titanium of SrTiO3 is morecovalent (Karimi and Zohoori Citation2013; Karimi, Zohoori, and Yazdanshenas Citation2014).
The novelty of this paper is to produce a composite which is almost ecofriendly and used as different applications such as cosmetics, clothes (especially pregnancy cloths due to its UV protection) and to improve the mechanical properties of composites. Additionally, using nano material in natural fibers aims to enhance some properties and using common technology like extrusion the cork fiber.
Materials and methods
In this research cork powder was purchased from S. Paio Oleiros, Portugal. The particle size of cork powder was less than 500 μm and its specific weight was about 160 kg/m3. Nano strontium titanate powder (SrTiO3) with particle size of <100 nm and density of 4.81 g/cm3 was provided by Sigma Aldrich.
Twin Screw Extruder (Brabender, Germany) was used for the formation of composite fibers. The morphology of produced composite fibers was studied by scanning electron microscopy (SEM-MIRA3-TESCAN), in this case all samples were covered by gold film. An Instron universal testing machine (Z020, Germany) was used to measure the tensile property of produced composites. Perkin Elmer Lambda UV-vis spectrophotometer apparatus was used in order to investigate the UV-transmittance.
In order to stabilize the moisture content of purchased cork powder, it was dried at 75°C for a day in an oven. Then the cork and nano powders (in different percentages) were extruded in twin screw extruder. The screw speed was 40 rpm and the temperature was kept at 145°C. Finally, the extruded composites was cooled in air and the composite fibers was obtained. The specification of samples is illustrated in .
Table 1. Specification of samples and water uptake.
Results and discussion
Water uptake
ASTM D570 was used to investigate the produced water uptake. In this method the composites were soaked in distilled water. Then the soaked composites were dried in an oven at 40°C for one day. The composites were weighed (m0) and immersed again in distilled water at room temperature for another one day and dried with absorbent paper and again weighed (m1). Mass variation (Δm) was evaluated by EquationEquation (1)(1)
(1) as follows:
Five samples of each produced code were tested and the results of water uptake are presented in . As shown, the produced cork fiber has higher water uptake due to its hydroxyl groups of polysaccharides. But the samples containing nano particles have less water uptake based on their reaction with cork and lower concentration of OH groups of cork. Of course, the water uptake of CS1, CS2 and CS3 is not too rare, and good results for many applications. shows the graph of the water uptake after five days. As it was shown, after five days, there is no significant increase/decrease in water uptake due to the saturation state. Izzat et.al used this method in order to investigate the water uptake of produced PCL/HA fibers (Izzat et al. Citation2014). By comparing the results of these two studies, we come to conclusion that after long time the PCL/HA start to degrade and CS1–3 saturated, so the hydrophobic/hydrophilic groups have important role in water uptake.
SEM analysis and ashing test
The produced composite morphology diameter variation and distribution of nano particle in composites are shown in . As shown, the diameter of nano particles is about 35 nm while the diameter of composite fiber is about 125 μm. On the other hand, the mean diameter of cork cells is about 500 nm. By close observation at SEM image(right), we come to conclusion that the nano particles of SrTiO3 is distributed without any aggregation or agglomeration. These images revealed that the produce cork composite despite the spinning process has many cells. It is important to note that in SEM the nano particles of SrTiO3 are distributes inside the cells, which maybe the cause to increase some physical or chemical properties of composites.
Another test for proving the existence of used nano particle is the ashing method. In this test, five samples of each composite weighted (m1), burned in a stove at 560°C. Then the remained ash was weighed again (m2) and compared with the raw sample (the sample without nano particle). The difference between m1 and m2 shows the used amount of nano particle. The results revealed that the used and remained nano SrTiO3 had one thousandth of a gram variation. This difference is negligible and ashing test has proved that approximately all used nano particles are presented in the produced sample, and its good distribution proved by SEM.
Tensile analysis
shows the tensile force of produced composites with/without nano particle. As shown in , the addition of nano SrTiO3 causes the increase of tensile force. By doping the cork fiber with nano SrTiO3 in concentration of 1.5% and 2%, composite strength enhances to some extent, with approximately the same strength percentage. But by increasing the amount of nano SrTiO3 to 2.5%, the strength of produced composites enhances significantly. This phenomenon can be introduced due to the reaction between hydroxyl groups of cork and functional group of nano particles. In this case, the cross-links of nano particle and cellulose part of cork improve the strength of produced composites. This phenomenon was sen in other researches such as doping cotton fibers with nano particles which was done by Karimi et. al (Karimi et al. Citation2010), or a research by Kooshamoghadam which demonstrate that using nano particles in finishing of fibers have direct effect on tensile of samples (Kooshamoghadam et al. Citation2021).
Ultra-violet protection
Nowadays most people know that UV irradiation is the reason of many diseases and can lead to cancer. One of the best ways to protect skin from ultra-violet spectra is by using UV protection fiber/fabric. So, the amount of fiber/fabric UV transmittance is important. In this research, the diagram of UV transmission prepared in the wavelength range of 200-400 nm (). As shown, the produced cork fiber without nano particle has a high transmittance while the samples containing nano particles have lower UV transmittance. This can be introduced due to the synergetic UV absorption of nano SrTiO3. From , by increasing the amount of nano particle, the UV transmittance is reduced. This means that using nano particles in cork fiber gives significant UV protection. By comparison of other researches which was introduced in introduction, it is clearly demonstrated that wide band gap of some nano particle such as nano SrTiO3 caused to activate the material under UV irradiation and reduce the transmission of ultraviolet waves.
Conclusion
The aim of this study has revealed a simple and cost effective way to produce and use an ecofriendly composite with improved properties. Cork powder with nano strontium titanate were extruded in twin screw extruder. Three percentages of nano material were used (1.5%, 2%, 2.5%) and the produced composite compared with each other. The strength of samples enhances due to the presence of nano material, to have enough strength in order to be used in textile industry, but the water uptake has a slight decrease. The important property improved was UV blocking. By using nano strontium titanate, the UV transmission decreased significantly which is very important for us nowadays. On the other hand, the SEM images showed that the produced composite keep its cavity form of cork so that the final produce can keep in the heat.
Highlights
Simple and cost effective way to produce cork fiber with nano strontium titanate which can be used as ecofriendly composite.
Enhancing strength of produced fiber.
Loading UV blocking property to produced fiber.
Ethical approval
We confirm that all the research meets ethical guidelines and adheres to the legal requirements of the study country. The research does not involve any human or animal welfare related issues.
Acknowledgments
We do not express our acknowledgments to anyone.
Disclosure statement
No potential conflict of interest was reported by the authors.
Additional information
Funding
References
- Aalipourmohammadi, M., A. Davodiroknabadi, and A. Nazari. 2021. Homogeneous coatings of titanium dioxide nanoparticles on corona-treated cotton fabric for enhanced self-cleaning and antibacterial properties. AUTEX Research Journal 21 (1):101. doi:10.2478/aut-2019-0058.
- Abdallah, F., R. Cheikh, M. Baklouti, Z. Denchev, and A. Cunha. 2010. Effect of surface treatment in cork reinforced composites. Journal of Polymer Research - J POLYM RES 17:519. doi:10.1007/s10965-009-9339-y.
- Avazpour, S., L. Karimi, and S. Zohoori. 2017. Simultaneous coloration and functional finishing of cotton fabric using Ag/ZnO nanocomposite. Coloration Technology 133 (5):423. doi:10.1111/cote.12296.
- Bekrani, M., S. Zohoori, and A. Davodiroknabadi. 2020. Producing multifunctional cotton fabrics using nano CeO doped with nano TiO and ZnO. AUTEX Research Journal 20 (1):78. doi:10.2478/aut-2019-0057.
- Castola, V., B. Marongiu, A. Bighellia, C. Floris, A. Laı̈, and J. Casanovaa. 2005. Extractives of cork (Quercus suber L.): Chemical composition of dichloromethane and supercritical CO2 extracts. Industrial Crops and Products 21 (1):65. doi:10.1016/j.indcrop.2003.12.007.
- Chanut, J., Y. Wang, I. Cin, E. Ferret, R. Gougeon, J. Bellat, and T. Karbowiak. 2022. Surface properties of cork: Is cork a hydrophobic material? Journal of Colloid and Interface Science 608:416. doi:10.1016/j.jcis.2021.09.140.
- Correia, J., G. Serra, R. AlvesdeSousa, A. Pereira, and F. Fernandes. 2022. Expanded (Black) cork for the development of an eco-friendly surfboard: environmental impact and mechanical properties. Sustainability 14:2. doi:10.3390/su14020668.
- Daneshian, H., S. Nayebzadeh, and A. Davodiroknabadi. 2021. Improvement of physical properties of viscose using nano GeO as doping material. AUTEX Research Journal 22 (2):243. doi:10.2478/aut-2021-0002.
- Dias, A. N., V. Simão, J. Merib, and E. Carasek. 2013. Cork as a new (green) coating for solid-phase microextraction: Determination of polycyclic aromatic hydrocarbons in water samples by gas chromatography–mass spectrometry. Analytica chimica acta 772:33. doi:10.1016/j.aca.2013.02.021.
- Dittenber, D. B., and H. V. S. GangaRao. 2012. Critical review of recent publications on use of natural composites in infrastructure. Composites: Part A, Applied Science and Manufacturing 43 (8):1419. doi:10.1016/j.compositesa.2011.11.019.
- Duarte, A. P., and J. C. Bordado. 2015. Cork – a renewable raw material: Forecast of industrial potential and development priorities. Frontiers in Materials 2:1. doi:10.3389/fmats.2015.00002.
- Fernandes, E. M., V. Correlo, J. Chagas, J. Mano, and R. Reis. 2010. Cork based composites using polyolefin’s as matrix: Morphology and mechanical performance. Composites Science and Technology 70 (16):2310. doi:10.1016/j.compscitech.2010.09.010.
- Filipe-Ribeiro, L. S., F. Cosme, and F. M. Nunes. 2019. A simple method to improve cork powder waste adsorption properties: Valorization as a new sustainable wine fining agent. ACS Sustainable Chemistry & Engineering 7 (1):1105. doi:10.1021/acssuschemeng.8b04775.
- Ghiasi, Y., A. Davodiroknabadi, and S. Zohoori. 2021. Electrospinning of wheat bran cellulose/TiO2/ZnO nanofibre and investigating the UV blocking and bactericidal properties. Bulletin of Materials Science 44 (2):89. doi:10.1007/s12034-021-02406-5.
- Gil, L. 2009. Cork composites: A review. Materials 2 (3):776–8. doi:10.3390/ma2030776.
- Gil, L. 2015. New cork-based materials and applications. Materials 8 (2):625. doi:10.3390/ma8020625.
- Ihamouchen, C., H. Djidjelli, and A. Boukerrou. 2021. Development and characterization of a new cork-based material. Materials Today 36:34–40. doi:10.1016/j.matpr.2020.05.092.
- Izzat, M., N. Sultana, C. Csci, and S. Hamdan. 2014. Bioactivity Assessment of Poly(ɛ -caprolactone)/hydroxyapatite electrospun fibers for bone tissue engineering application. Journal of Nanomaterials 8:1–6. doi:10.1155/2014/573238.
- Joshi, S. V., L. T. Drzal, A. K. Mohanty, and S. Arorac. 2004. Are natural fiber composites environmentally superior to glass fiber reinforced composites? Composites: Part A, Applied Science and Manufacturing 35 (3):371. doi:10.1016/j.compositesa.2003.09.016.
- Karimi, L., M. Mirjalili, M. Yazdanshenas, and A. Nazari. 2010. Effect of nano TiO2 on self-cleaning property of cross-linking cotton fabric with succinic acid under UV irradiation. Photochemistry and Photobiology 86 (5):1030. doi:10.1111/j.1751-1097.2010.00756.x.
- Karimi, L., and S. Zohoori. 2013. Superior photocatalytic degradation of azo dyes in aqueous solutions using TiO2/SrTiO3 nanocomposite. Journal of Nanostructure in Chemistry 3. doi:10.1186/2193-8865-3-32.
- Karimi, L., S. Zohoori, and M. E. Yazdanshenas. 2014. Photocatalytic degradation of azo dyes in aqueous solutions under UV irradiation using nano-strontium titanate as the nanophotocatalyst. Journal of Saudi Chemical Society 18 (5):581. doi:10.1016/j.jscs.2011.11.010.
- Kooshamoghadam, N., S. Zohoori, M. Bekrani, S. Shahsavari, and R. Talebikatieklahijany. 2021. Enhancing physical properties of viscose by preparing viscose/keratin/nano ZnO composite fabric. Journal of Natural Fibers 19 (13):1–8. doi:10.1080/15440478.2020.1870631.
- Liu, F., S. Wang, and S. Chen. 2020. Adsorption behavior of Au(III) and Pd(II) on persimmon tannin functionalized viscose fiber and the mechanism. International Journal of Biological Macromolecules 152:1242. doi:10.1016/j.ijbiomac.2019.10.221.
- Maleksabet, F., and S. Zohoori. 2021. Surface modification of wool: Superior sound absorption and water resistance. Journal of Natural Fibers 19:1–7. doi:10.1080/15440478.2021.1958419.
- Mateus, M. M., J. M. Bordado, and R. G. dos Santos. 2017. Ultimate use of Cork – Unorthodox and innovative applications. Ciência & Tecnologia dos Materiais 29 (2):65. doi:10.1016/j.ctmat.2016.03.005.
- Moresco, M., S. Rosa, E. Santos, and S. Nachtigall. 2010. Agrofillers in Polypropylene composites: A relationship between the density and the mechanical properties. Journal of Applied Polymer Science 117:400. doi:10.1002/app.31602.
- Salasinska, K., and J. Ryszkowska. 2015. The effect of filler chemical constitution and morphological properties on the mechanical properties of natural fiber composites. Composite Interfaces 22 (1):39. doi:10.1080/15685543.2015.984521.
- Silva, S. P., M. A. Sabino, E. M. Fernandes, V. M. Correlo, L. F. Boesel, and R. L. Reis. 2005. Cork: Properties, capabilities and applications. International Materials Reviews 50 (6):345. doi:10.1179/174328005X41168.
- Wang, Q., Z. Lai, C. Luo, J. Zhang, X. Cao, J. Liu, and J. Mu. 2021. Honeycomb-like activated carbon with microporous nanosheets structure prepared from waste biomass cork for highly efficient dye wastewater treatment. Journal of Hazardous Materials 416:125896. doi:10.1016/j.jhazmat.2021.125896.
- Yamin, F., F. Naddafiun, and S. Zohoori. 2021. Electrospinning of eucalyptus cellulose nano fiber and improving its properties by doping nano materials. Journal of Natural Fibers 19:1–10. doi:10.1080/15440478.2021.1932675.
- Zare, H., S. Nayebzadeh, A. Davodiroknabadi, and S. Hataminasab. 2021. Fabrication of multifunctional nano gelatin/zinc oxide composite fibers. AUTEX Research Journal 21 (4):403. doi:10.2478/aut-2020-0046.
- Zohoori, S., L. Karimi, and A. Nazari. 2014. Photocatalytic self-cleaning synergism optimization of cotton fabric using nano SrTiO3 and nano TiO2. Fibres & Textiles in Eastern Europe 22:91.
- Zohoori, S., S. Shahsavari, M. Sabzali, S. Hosseini, R. Talebikatieklahijany, and Z. Morshedzadeh. 2021. Reinforcing of viscose fabric using nano web of palm-cellulose carbon mesoporous nanoparticle composite. Journal of Natural Fibers 19:1–9. doi:10.1080/15440478.2021.1975600.