ABSTRACT
Agro waste burning is a serious environmental issue, which results in water and air pollution. The addition of these agro wastes as reinforcements in polymer composites can improve the mechanical properties. The present study involves the fabrication of banana fiber reinforced polyester composites filled with coconut shell filler using the hand layup technique. 30 vol% of banana fibers with 10 mm length is used for fabrication along with coconut shell filler of 1, 3 & 5 vol% in the polyester matrix. The fabricated composites are processed using the XRD, FTIR, TGA, tensile and flexural tests. The maximum tensile and flexural strength of 19.91 MPa and 92.761 MPa is achieved with 3 vol% of coconut shell-filled banana fiber polyester composites. The fiber/matrix debonding, poor interfacial adhesion, and matrix cracks are the important failure mechanisms that are identified using scanning electron microscopy.
摘要
农业废弃物焚烧是一个严重的环境问题,导致水和空气污染. 在聚合物复合材料中添加这些农业废弃物作为增强材料可以改善机械性能.本研究涉及使用手工叠层技术制备填充椰子壳填料的香蕉纤维增强聚酯复合材料. 30体积%长度为10 mm的香蕉纤维与聚酯基质中1、3和5体积%的椰子壳填料一起 用于制造。使用XRD、FTIR、TGA、拉伸和弯曲试验对制备的复合材料进行了处理. 椰子壳填充香蕉纤维聚酯复合材料的最大拉伸强度和弯曲强度分别为19.91MPa和92.761MPa. 纤维/基体脱粘、界面粘合性差和基体裂纹是使用扫描电子显微镜识别的重要失效机制.
Introduction
India is a major agro-based economic country, which contributes to many agricultural production activities in the world. However, there is a little lack of waste management techniques, which results in the burning and landfilling of huge tons of agro-waste. Large volumes of agro wastes are produced annually but are not efficiently reused, recycled, or disposed of. Fabrication of sustainable materials using these agro wastes can be a better practice. Banana fibers (67383 ktons) and coconut shells (726 kton/year) are the major agro wastes generated in India (Dennis et al. Citation2015; Kannan and Thangaraju Citation2021). Both banana fibers and coconut shells can be effectively used as reinforcement in composite production. The addition of agricultural residues as reinforcements in polymer composites reduces the traditional residue management practices (Kannan and Thangaraju Citation2021). Hybrid composites consist of one or more reinforcements in a particular matrix. Reinforcements can be of different forms like two fillers, two fibers, or fibers and fillers. Adding fillers to polymer composites provides improved mechanical properties (Gokul, Ram Prabhu, and Rajasekaran Citation2017; Vigneshwaran et al. Citation2020). The main objective of utilizing the filler material is to improve the mechanical properties and to reduce the overall cost of the compound. For instance, the effect of filler loading on the morphological and mechanical properties of polypropylene composites reinforced with coconut shell filler is investigated by Mark et al. (Citation2019). The usage of the inorganic filler is expensive and hard to process. Also, the inorganic filler with synthetic polymer is very harmful to the environment after their service life. The above difficulties made the researchers turn their focus toward organic fillers as a better replacement for traditional fillers (La Mantia and Morreale Citation2006). Various researchers are exploring plant-based reinforcements in the form of yarns, woven fabrics, strands, fibers, micro fibers, particles and nanoparticles for several applications. The properties of the composites can be controlled and improved by selecting proper manufacturing methods, fibers, matrix, and additives (Ramesh, Palanikumar, and Hemachandra Reddy Citation2017).
Ojha, Raghavendra, and Acharya (Citation2014) investigated the tensile and flexural properties of 0, 5, 10, 15 & 20 wt% of coconut shell reinforced epoxy composites. The maximum tensile and flexural strength obtained using 15 wt% of coconut shell-filled composites are 40.3 MPa and 68.25 MPa, respectively. Hybridization effect of banana fiber and carbon fiber on mechanical and water absorption properties of epoxy composites was investigated by Manickam Ramesh, Palanikumar, and Hemachandra Reddy (Citation2017). Hybrid composites with 80% banana fiber and 20% carbon fiber provide a maximum tensile strength of about 277 MPa. Balaji et al. (Citation2020) evaluated the mechanical properties of hybridized polyester composites with banana and snake grass fibers. Tensile and flexural strength of the hybrid polyester composites are increased with the increase in fiber volume fraction (5, 10, 15, 20, & 25%) and maximum strength attained at 25%.
Iyyadurai et al. (Citation2020) examined the mechanical and tribological characteristics of 30 wt% of Cissus quadrangularis fiber with 40 mm length-reinforced epoxy composites filled with carbonized coconut shell filler (2.5, 5, 7.5 & 10 wt%). The composites reinforced with 5 wt % of coconut shell ash provide 22.3% improved tensile strength compared to composites without coconut shell ash. Chun, Husseinsyah, and Osman (Citation2012) evaluated the effect of silane coupling agent and filler content on the thermal properties of coconut shell filler added bio-composite made of polylactic acid. The authors confirmed that the addition of coconut shell particles enhanced the thermal stability of polylactic acid. The total weight loss of biocomposite decreased with filler content at 600º C. Khalil et al. (Citation2017) investigated the effect of coconut shell filler on vinyl ester composites reinforced with kenaf and coconut fibers. They found that incorporation of coconut shell filler at 3 wt% improved the mechanical properties of composites like flexural strength and modulus, tensile strength and modulus and impact strength. The authors suggested that coconut shell fillers can be used as effective fillers in hybrid composites.
Utilization agro wastes as fillers or reinforcements in polymer composites can alleviate the wood shortage in the construction, automobile and packaging applications (Bledzki, Mamun, and Volk Citation2010).
It is clearly understood that natural agro residues have a great impact on polymer composites from the existing state of the art. There is a necessity to develop a new material from agricultural wastes like banana fibers and coconut shell that can be used in structural applications and should hold good mechanical properties. Only few studies addressed the hybridization effect of natural fiber reinforced polymer composites with filler materials. Hence, this work is an attempt to research low-cost value-added composite materials derived from agricultural wastes. The present study involves processing, characterization, and experimentation on the mechanical and thermal properties of banana fibers and coconut shell filler-reinforced polyester composites.
Materials and methodology
Materials
The banana fiber (BF) and coconut shell (CS) fillers are collected from local sources in Tamilnadu, India. The banana fibers are composed of cellulose 63–64 wt %, hemicellulose 19 wt%, and lignin 5 wt% (Prasad, Kumar Agarwal, and Sinha (Citation2016). Properties of banana fibers are listed in . The coconut shell consists of cellulose 36–42%, hemicellulose 41–46%, pectin 3–4% and lignin 0.15–0.25% (Islam et al. Citation2017). Chemical composition of coconut shell filler is illustrated in . Polyester resin, MEKP (methyl ethyl ketone peroxide) catalyst, and cobalt octoate accelerator were supplied by Sakthi fabric, Chennai. Properties of polyester resin are shown in . Detailed methodology of the present study is shown in .
Table 1. Properties of banana fibers Venkateshwaran and ElayaPerumal (Citation2010) (Pothan, Thomas, and Neelakantan Citation1997) (Ramesh et al. Citation2014).
Table 2. Properties of polyester resin (Muhammad Shahroze et al. Citation2018).
Table 3. Chemical composition of coconut shell filler (Sareena, Ramesan, and Purushothaman Citation2012).
Composite processing
30 vol % of banana fibers having 10 mm length were kept in random orientation on the mold of size 300 × 300 * 3 mm. The coconut shell flakes (1, 3 & 5 vol %) were added to the polyester matrix and stirred for approximately 20 minutes to ensure the uniform distribution. After this, the accelerator cobalt octoate and catalysts methyl ethyl ketone peroxide (MEKP) were added each 1% to the mixture as suggested by the supplier. Again, the mixture was stirred continuously for homogenous conditions. The completely dispersed coconut shell flake polyester mixture was poured into the mold to wet the banana fibers throughout the mold. The curing process was performed at room temperature in closed condition for 24 hours. Fabrication of the composites is illustrated in .
Mechanical testing
A Universal Testing machine (TUECN-200, Hitech India) with a maximum capacity of 200 KN and measuring range between 0 and 200 KN was used for conducting the tensile and flexural tests. The tensile test was performed according to the ASTM D 3039 standard with the specimen dimensions of 250 × 25 * 3 mm. The flexural test was performed as per the ASTM D 730 standard for a specimen size of 125 mm × 12.7 mm × 3 mm. Both tensile and flexural tests were operated with 3 mm/min of crosshead travel in UTM. Tensile and flexural specimens before, during and after testing are shown in . The red arrow heads on the figure indicates the direction of the applied load. For each composite composition, five specimens were tested and average values were calculated and reported for tensile and flexural strength. Morphological study and failure fractography were examined using the FEI Quanta 200 FEG scanning electron microscope (SEM) operating at 20 KV.
X-ray diffraction analysis
X-ray diffraction analysis (XRD) was used to detect the crystalline region available in specimens of composites and reinforcements. The XRD spectrum of banana fiber, coconut shell filler, and its composites were detected using a Malvern Panalytical high-resolution X-ray diffractometer with an angle range (5–140 degrees) and a minimum step size of 0.06519. The characterization was performed in a continuous scanning mode of step size 0.04º and operating 2θ range between 10º to 80º for the 50 mg powdered samples.
Fourier transform infrared spectroscopy analysis
A SHIMADZU IRTRACER 100 with wavenumber range (7800–350 cm−1) is utilized to conduct FTIR spectroscopy on the reinforcements and composites to analyze the absorption bands and functional groups present. The FTIR spectra were operated between 500 and 4000 cm−1 at a scanning rate of 4 cm−1 and a resolution of 40 scans.
Thermogravimetric analysis
Thermogravimetric analysis (TGA) was performed in the NETZSCH STA 2500 machine (Temperature range: RT to 1100ºC, Heating rate: 0.001 to 100 K/min, Atmosphere: Vacuum-tight 10–4 mbar). This technique is generally used to calculate the rate and extent of the weight change of the material as a function of time or temperature under a controlled atmosphere. Decomposition, dehydration, or oxidation of materials due to the applied heat helps in the prediction of thermal stability. All the samples are heated in the temperature range of 25 - 600º C at a rate of 20ºC min−1 under a nitrogen atmosphere.
Results and discussion
Reinforcement morphology
Unlike conventional materials, it is necessary to study the surface morphology of natural reinforcements for a brief understanding of failure mechanisms. The banana fiber and coconut shell filler reinforcements are subjected to SEM characterization to analyze their surface topography. reveals the surface textures of banana fibers at 2500 × and 5000 × magnification. It was observed that the bunch of fibrils was twisted throughout its length with dimensional variability. The surfaces of the banana fiber were identified as clear and rough with fibril debris. reveals the topography of coconut shell fillers at 2500 × and 5000 × magnification. The surfaces of the coconut shell filler revealed a flaky texture with rough surface patches. These surfaces of banana fibers and coconut shell filler possessed a high potential for interlocking with the polyester matrix during curing. Strong interlock bonding helps in the provision of maximum mechanical strength for the composites.
X-ray diffraction analysis
The X-ray diffraction patterns of coconut shell, banana fiber, polyester matrix, and their composites are shown in . The banana fiber exhibited three different diffraction peaks 14.73º, 17.71º, and 21.71º, corresponding to the 101, 10–1, and 002 planes. It was clearly evident that the presence of both crystalline and amorphous phases was seen in the banana fiber. The highest peak at 21.7º corresponded to the presence of the cellulose I structure. Similar peaks were identified in the raw banana fiber by Bar et al. (Citation2021). The diffraction peaks of coconut shells at 22.3º, 26.14º, 27.7 º and 31.24º confirmed the presence of hemicellulose, cellulose, and lignin (Balan et al. Citation2017). The major diffraction peaks of the neat polyester, BA/CS 1%, BA/CS 3%, and BA/CS 5% were 19.5º, 20.69 º, 21.17º & 20.58º respectively. The plots of all the composites, including neat polyester, revealed broad peaks and confirmed their amorphous nature. The non-crystalline nature of the composites was identified by the absence of sharp peaks (Neher et al. Citation2014). The crystalline structures of the banana fiber polyester composites were not altered by the filler loading. Also, the crystallinity of the composites was mostly established by the base polymer.
Fourier transform infrared spectroscopy analysis
The FTIR spectrum of the reinforcements and composites is shown in . The stretching vibrations at 3347 cm−1 corresponded to the hydroxyl groups (OH) for the banana fibers. These O-H compounds consist of cellulose, hemicellulose and lignin extracts with aliphatic primary and secondary alcohols (Ibrahim et al. Citation2010). The absorption band of banana fibers at 2916 cm−1 may be attributed to the CH stretching vibrations. The stretching vibrations for the cellulose region at 1640 cm−1 can be represented as a C=O bond of alpha-keto carbonyl. A strong absorption band at 1044 cm−1 refers to the C-O-C pyranose ring (Sheng et al. Citation2014). Similar to the banana fibers, the coconut shell flakes were also found to possess broad peaks at 3100–3700 cm−1 which belonged to the hydroxyl (OH) groups of cellulose, hemicelluloses, and lignin. The stretching band at 1742 cm−1 is related to the carboxyl group (C=O) from hemicellulose. The vibrations at 1599 and 1029 cm−1 were associated with the conjugated C-O group of aromatic skeletal from the lignin and C-O-C groups of the cellulose and lignin carbohydrates (Chun, Husseinsyah, and Nasihah Azizi Citation2013). For polyester, weak and wider peaks between 3400 and 3600 cm−1 refer to the hydroxyl (OH) groups. The vibration band at 1934 cm−1 corresponded to the C-H stretching. An intense peak at 1723 cm−1 was responsible for the carbonyl (C=O) from ester linkage. Small peaks at 1586 cm−1 and 1450–1350 cm−1 are termed as C=C stretching of an aromatic ring, asymmetric, and symmetric CH3 bending, respectively (Reddy et al. Citation2012). The C-H aromatic bands were identified at 698 cm−1 for both composites and neat polyester. The spectra of banana fiber reinforced coconut shell-filled composites were observed to possess similar stretching bands of a neat polyester matrix.
Thermogravimetric analysis
Thermogravimetric analysis is used to detect the thermal stability of the materials with weight loss by heating the sample. reveals a small amount of mass loss present in the range of 25–200 ºC for all the composites and neat polyester. The banana fiber exhibited 11.05% of mass loss at 200 ºC, mainly because of the humidity present in the hydrophilic materials (Mohan and Kanny Citation2017). Weight loss of banana fibers was observed to be 22.43% and 33.10% at 300 ºC and 400 ºC, respectively. The coconut shell filler revealed 4.1%, 17.81% and 33. 64% weight reduction at 200 ºC, 300 ºC, and 400 ºC, respectively. It was identified that the major weight loss occurred between 200 and 400 ºC, mainly due to the decomposition of cellulose, hemicelluloses, and lignin (Balaji et al. Citation2020). Hemicellulose was the early decomposing component, followed by cellulose due to its crystalline nature and the lignin-tough component (Norizan et al. Citation2017). Neat polyester and its composites maintained good stability up to 200 ºC with only 2–3% weight loss. At 300 ºC, both polyester and their composites revealed 8–13% decomposition. From 300 to 400 ºC, all the composites and neat polyester revealed 34% to 51% of major mass loss. The weight loss of polyester matrices and their composites was due to the de-polymerization and breaking of the crosslink chains (Kumari et al. Citation2020). It was identified from the plot that the inclusion of coconut shells in the banana fiber polymer composites provided improvements in thermal stability. The thermal stability of coconut shell flakes was found to be impressive beyond 370 ºC compared to the other curves. The composites with 5 vol% of coconut shell filler gave better thermal stability compared to the other composites.
Tensile strength
The tensile strength of the composites is shown in . From the results, it was observed that the banana fiber composites with 3 vol% of coconut shell-filled composites provided a maximum tensile strength of 19.91 MPa compared to the other composites. The maximum tensile property attained was due to the existence of strong interfacial bonding between the banana fibers and the coconut shell fillers along with the matrix. The performance observed in the current investigation was far superior to the polyester composites reinforced with random oriented Caryota fibers (Vijayakumar and Palanikumar Citation2020). The addition of coconut shell filler provided maximum improvement in the tensile strength of 33.11% and 69.14% compared to the composites without filler and neat polyester. The inclusion of filler particles helped to fill the voids of the composites by settling in the interstitial position between the fibers and matrix. Gradual debonding of banana fibers from the matrix and crack propagation was controlled by the addition of random fibers and fillers during plastic deformation. The strengthening and stiffening characteristics of the composites depend on the uniform dispersion of coconut shell fillers within the polyester resin.
Composites without filler, 1% & 5 vol% of coconut shell filler gave a maximum tensile strength of 14.635 MPa, 16.418 & 15.193 MPa, respectively. It was evident that the increasing filler content strongly influenced the tensile strength of the banana fiber polymer composites. Thus, the hybridization of banana fibers, coconut shell fillers, and polyester matrix generated a durable adhesion inside the processed composites. The present findings also revealed that an increase in filler content beyond 3 vol % revealed a 23.72% decline in tensile strength. This is mainly due to the formation of clusters at a higher volume concentration of the filler material. Stress concentration in agglomerated regions tends to induce crack initiation and propagation, and sudden failure results in low tensile strength. A similar decrement in tensile strength with increasing the filler content was evidenced by Vigneshwaran, Uthayakumar, and Arumugaprabu (Citation2020).
The SEM images of tensile failure specimens of the composites are shown in . River-like markings, fractured fibers, fiber breakage, damaged fiber/matrix interface, and rich matrix region were identified in for the composites without filler. These findings revealed the brittleness of the polyester composites, which was responsible for the low tensile strength of the composites without filler compared to the other composites with filler. Similar findings of river makings and brittle fracture patterns were observed by Mohammadalipour et al. (Citation2018). A bunch of fiber pullouts, strong fiber/matrix bonding, fiber pullout pores, fiber/fibrillation, and filler/matrix debris are revealed in for composites with 1 & 3 vol% of coconut shell filler respectively. Matrix cracks, damaged fiber surface, debris, air bubbles, and voids are captured in ) for composites with 5 vol% of coconut shell filler. A similar type of tensile failure mechanism was identified by Vigneshwaran, Uthayakumar, and Arumugaprabu (Citation2019). Enhanced concentration of coconut shell filler stimulated agglomerations within the composites, which then declined due to fracture toughness. The high filler loading introduced the voids and air bubbles, which functioned as stress concentrators.
Flexural strength
The flexural strength of the composites is illustrated in . From the results, it was observed that the maximum flexural strength of 92.761 MPa was witnessed in composites with 3 vol % of coconut shell filler. Rigid coconut shell filler stimulated enhanced rigidity with improved interfacial bonding. The addition of coconut shell filler provided a maximum 70% improvement in the flexural strength compared to the composites without filler material. Flexural strength of this banana fiber reinforced coconut shell hybrid composites provide 323% improvement compared to banana fiber reinforced low-density polyethylene composites developed by Prasad, Kumar Agarwal, and Sinha (Citation2016). It was also identified that a higher filler content 5 vol% resulted in a decline of flexural strength about 36% compared to composites with 3 vol% of coconut shell filler. The coconut shell flakes provided strong interlock bonds around the banana fiber with polyester matrix at 3 vol% and weaker adhesion due to an agglomeration at 5 vol %. The addition of filler materials at higher loading resulted in agglomeration, which decreased the flexural strength of the composites as reported by Adediran et al. (Citation2021).
SEM images of flexural fracture specimens of banana fiber composites with different filler contents are shown in . Fractured fiber, matrix crack, fiber peeling, and fiber bending are identified in for composites without filler. The smooth surface of the fiber/matrix interface and river-like markings again proved the brittle fracture of the polyester matrix. Linear and rapid crack propagation resulted in brittle failure of composites without filler, leading to lesser energy dissipation with low flexural strength. Sharp fiber fractures, fiber pores at the cross-section, strong fiber pullout holes, and damaged fibers are observed in , (c,d) and (e,f) for composites with 1 & 3 vol% coconut shell filler, respectively. Similar fracture morphologies were reported by Gokul et al. (Citation2022).
Figure 9. SEM images of flexural fractured specimen (a & b) BF/CS 0 vol%, (c & d) BF/CS 1 vol%, (e & f) BF/CS 3 vol% and (g – i) BF/CS 5 vol%.
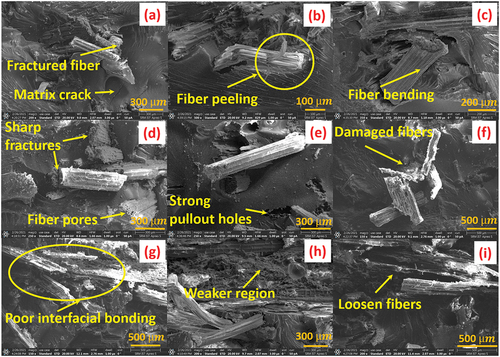
When the coconut shell filler content was increased, more energy was dissipated into the banana fiber polyester composites, resulting in higher flexural strength. The coconut shell filler zones within the processed composites also functioned as barriers, which restricted the rapidly propagating cracks during the flexural testing. Hence, it was proposed that the composites at 3 vol% of coconut shell loading absorbed more fracture and subsequently showed higher bending resistance compared to the other composites. However, a further increase in filler loading reduced the flexural strength of the banana fiber composites. Poor interfacial bonding, weaker region, voids, bubbles, pullout traces, and loosen fibers are captured in ) for composites with 5 vol% of coconut shell filler. A similar interfacial fracture morphology was investigated by Ramli et al. (Citation2020). The agglomeration of coconut shell filler at higher concentrations reduced their effective surface area and cross-linking density between the filler and the polyester matrix. This phenomenon was responsible for weaker interfacial adhesion and cracks initiated in these zones, which determined the permanent failure of the composites.
Conclusion
The influence of coconut shell filler on the tensile, flexural and thermal properties of banana fiber polyester composites was examined in brief. The thermal stability of banana fiber polyester composites is improved by the addition of coconut shell filler loading and confirmed by TGA. The Composite with 5 vol% of filler provides better thermal stability with minimum weight loss 11% at 300 ºC than other composites. The maximum tensile strength was attained at 3 vol% addition of coconut shell filler about 20 MPa. The addition of 3 vol % of coconut shell filler improved the tensile strength up to 33.11% and 69.14% compared to the composites without filler and neat polyester. The maximum flexural strength of the composites was 92.761 MPa which was realized for 3 vol% inclusion of coconut shell filler. At high filler loading, about 5 vol % of the composite’s flexural strength was reduced by 36% due to the agglomerated fillers. The fractured fibers, fiber pullouts, and fiber/matrix debonding were the fundamental failure mechanisms. These types of agro waste-based polymer composites have a great future and potential in the areas of construction, packaging, interior decoration, decorative components, furniture industry, etc. They are also capable of supporting the economy of farmers by reducing the difficulties associated with agricultural waste.
Highlights
Hybrid composites were developed using agro waste banana fiber and coconut shell filler.
Effects of coconut shell filler on tensile, flexural and thermal properties of banana fiber reinforced polyester composites are evaluated.
Maximum mechanical strength attained at 3 vol% of coconut shell filler composites.
Thermal stability of the composites increased with 5 vol% of filler addition.
Higher filler loading results in the formation of agglomeration.
Abbreviations
BF | = | Banana Fibers |
CS | = | Coconut Shell |
NP | = | Neat Polyester |
UTM | = | Universal Testing Machine |
ASTM | = | American Society for Testing and Materials |
XRD | = | X-ray Diffraction analysis |
FTIR | = | Fourier Transform Infrared spectroscopy |
TGA | = | Thermo gravimetric analysis |
SEM | = | Scanning Electron Microscopy |
Acknowledgement
We acknowledge (i) Centre for Composites and Advanced Materials, (ii) Strength of Materials Laboratory, Department of Mechanical Engineering, SRMIST. (iii) Nanotechnology Research Centre (NRC), and (iv) SRM Central Instrumentation Facility, SRMIST for providing the research facilities.
Disclosure statement
No potential conflict of interest was reported by the author(s)
References
- Adediran, A. A., A. A. Akinwande, O. A. Balogun, O. S. Olasoju, and O. S. Adesina. 2021. Experimental evaluation of bamboo fiber/particulate coconut shell hybrid PVC composite. Scientific reports 11:1 11 (1):1–14. doi:10.1038/s41598-021-85038-3.
- Balaji, A., R. Purushothaman, R. Udhayasankar, S. Vijayaraj, and B. Karthikeyan. 2020. Study on mechanical, thermal and morphological properties of banana fiber-reinforced epoxy composites. Journal of Bio- and Tribo-Corrosion 6 (2):60. doi:10.1007/s40735-020-00357-8.
- Balaji, D., M. Ramesh, T. Kannan, S. Deepan, V. Bhuvaneswari, and L. Rajeshkumar. 2020. Experimental investigation on mechanical properties of banana/snake grass fiber reinforced hybrid composites. Materials Today: Proceedings 42 (xxxx):350–55. doi:10.1016/j.matpr.2020.09.548.
- Balan, A. K., S. Mottakkunnu Parambil, S. Vakyath, J. Thulissery Velayudhan, S. Naduparambath, and P. Etathil. 2017. Coconut shell powder reinforced thermoplastic polyurethane/natural rubber blend-composites: Effect of silane coupling agents on the mechanical and thermal properties of the composites. Journal of Materials Science 52:11 52 (11):6712–25. doi:10.1007/S10853-017-0907-Y.
- Bar, M., H. Belay, A. Ramasamy, A. Das, and P. Ouagne. 2021. Refining of banana fiber for load bearing application through emulsion treatment and its comparison with other traditional methods. Journal of Natural Fibers 19:5956–73. doi:10.1080/15440478.2021.1902901.
- Bledzki, A. K., A. A. Mamun, and J. Volk. 2010. Barley husk and coconut shell reinforced polypropylene composites: The effect of fibre physical, chemical and surface properties. Composites Science and Technology 70 (5):840–46. doi:10.1016/j.compscitech.2010.01.022.
- Chun, K. S., S. Husseinsyah, and F. Nasihah Azizi. 2013. Characterization and properties of recycled polypropylene/coconut shell powder composites: Effect of sodium dodecyl sulfate modification. Polymer-Plastics Technology and Engineering 52 (3):287–94. doi:10.1080/03602559.2012.749282.
- Chun, K. S., S. Husseinsyah, and H. Osman. 2012. Mechanical and thermal properties of coconut shell powder filled polylactic acid biocomposites: Effects of the filler content and silane coupling agent. Journal of Polymer Research 19:5. doi:10.1007/s10965-012-9859-8.
- Dennis, C., P. Joshi, L. Diels, P. M. Sarma, and D. Pant. 2015. Agriculture biomass in India: Part 1. estimation and characterization. Resources Conservation and Recycling 102 (July):39–48. doi:10.1016/j.resconrec.2015.06.003.
- Gokul, K., T. Ram Prabhu, and T. Rajasekaran. 2017. Processing and evaluation of mechanical properties of sugarcane fiber reinforced natural composites. Transactions of the Indian Institute of Metals 70 (10):2537–46. doi:10.1007/s12666-017-1116-8.
- Gokul, K., R. Thangaraju, P. Kayaroganam, and J. Paulo Davim. 2022. The combined effect of banana fiber and fly ash reinforcements on the mechanical behavior of polyester composites. Journal of Natural Fibers 19:1–20. January. doi: 10.1080/15440478.2022.2025977.
- Ibrahim, M. M., A. Dufresne, W. K. El-Zawawy, and F. A. Agblevor. 2010. Banana fibers and microfibrils as lignocellulosic reinforcements in polymer composites. Carbohydrate Polymers 81 (4):811–19. doi:10.1016/j.carbpol.2010.03.057.
- Islam, M., S. C. D. Tangimul, J. Saha, M. T. I. Debasree Paul, M. Rahman, M. Ahmad Khan, and M. A. Khan. 2017. Effect of coconut shell powder as filler on the mechanical properties of coir-polyester composites. Chemical and Materials Engineering 5 (4):75–82. doi:10.13189/CME.2017.050401.
- Iyyadurai, J., S. Gandhi Veeramalai Chinnasamy, S. Basavarajappa, S. Indran, D. Divya, Y. Liu, M. R. Sanjay, and S. Siengchin. 2020. Tribo-mechanical characterization of carbonized coconut shell micro particle reinforced with cissus quadrangularis stem fiber/epoxy novel composite for structural application. Journal of Natural Fibers 19:2963–79. doi:10.1080/15440478.2020.1838988.
- Kannan, G., and R. Thangaraju. 2021. Recent progress on natural lignocellulosic fiber reinforced polymer composites: A review. Journal of Natural Fibers. doi:10.1080/15440478.2021.1944425.
- Khalil, A. H. P. S., M. Masri, C. K. Saurabh, M. R. N. Fazita, A. A. Azniwati, N. A. Sri Aprilia, E. Rosamah, and R. Dungani. 2017. Incorporation of coconut shell based nanoparticles in kenaf/coconut fibres reinforced vinyl ester composites. Materials Research Express 4:3. doi:10.1088/2053-1591/aa62ec.
- Kumari, S., R. Kumar, B. Rai, S. Sirohi, and G. Kumar. 2020. Study on the modification of polyester resin bamboo fiber-based composite with euphorbia coagulum and their effect on mechanical and thermal properties. Journal of Composite Materials 54 (24):3473–80. doi:10.1177/0021998320916542.
- La Mantia, F. P., and M. Morreale. 2006. Mechanical properties of recycled polyethylene ecocomposites filled with natural organic fillers. Polymer Engineering & Science 46 (9):1131–39. doi:10.1002/PEN.20561.
- Mark, U. C., I. C. Madufor, H. C. Obasi, and U. Mark. 2019. Influence of filler loading on the mechanical and morphological properties of carbonized coconut shell particles reinforced polypropylene composites. Journal of Composite Materials 54 (3):397–407. doi:10.1177/0021998319856070.
- Mohammadalipour, M., M. Masoomi, M. Ahmadi, and Z. Kazemi. 2018. The effect of simultaneous fiber surface treatment and matrix modification on mechanical properties of unidirectional ultra-high molecular weight polyethylene fiber/epoxy/nanoclay nanocomposites. Journal of Composite Materials 52 (21):2961–72. doi:10.1177/0021998318755542.
- Mohan, T. P., and K. Kanny. 2017. Mechanical and thermal properties of nanoclay-treated banana fibers. Journal of Natural Fibers 14 (5):718–26. doi:10.1080/15440478.2016.1277819.
- Muhammad Shahroze, R., M. Ridzwan Ishak, M. Sapuan Salit, Z. Leman, M. Asim, and M. Chandrasekar. 2018. Effect of organo-modified nanoclay on the mechanical properties of sugar palm fiber-reinforced polyester composites | Shahroze | BioResources.”|“effect of Organo-Modified Nanoclay on the Mechanical Properties of Sugar Palm Fiber-Reinforced Polyester Composites | Shahroze | BioResources.”|“effect of Organo-Modified Nanoclay on the Mechanical Properties of Sugar Palm Fiber-Reinforced Polyester Composites | Shahroze | BioResources. https://ojs.cnr.ncsu.edu/index.php/BioRes/article/view/BioRes_13_4_7430_Shahroze_Organo_Modified_Nanoclay_Composites/6319.
- Neher, B., M. A. Gafur, M. A. Al-Mansur, M. M. R. Bhuiyan, M. R. Qadir, and F. Ahmed. 2014. Investigation of the surface morphology and structural characterization of palm fiber reinforced acrylonitrile butadiene styrene (PF-ABS) composites. Materials Sciences and Applications 05 (06):378–86. doi:10.4236/msa.2014.56043.
- Norizan, M. N., K. Abdan, M. Sapuan Salit, and R. Mohamed. 2017. Physical, mechanical and thermal properties of sugar palm yarn fibre loading on reinforced unsaturated polyester composites. Journal of Physical Science 28 (3):115–36. doi:10.21315/JPS2017.28.3.8.
- Ojha, S., G. Raghavendra, and S. K. Acharya. 2014. A comparative investigation of bio waste filler (wood apple-coconut) reinforced polymer composites. Polymer Composites 35 (1):180–85. doi:10.1002/PC.22648.
- Pothan, L. A., S. Thomas, and N. R. Neelakantan. 1997. Short banana fiber reinforced polyester composites: Mechanical, failure and aging characteristics. Journal of Reinforced Plastics and Composites 16 (8):744–65. doi:10.1177/073168449701600806.
- Prasad, N., V. Kumar Agarwal, and S. Sinha. 2016. Banana fiber reinforced low-density polyethylene composites: Effect of chemical treatment and compatibilizer addition. Iranian Polymer Journal (English Edition) 25 (3):229–41. doi:10.1007/s13726-016-0416-x.
- Ramesh, M., K. Palanikumar, and K. Hemachandra Reddy. 2017. Plant fibre based bio-composites: Sustainable and renewable green materials. Renewable and Sustainable Energy Reviews 79 (May):558–84. doi:10.1016/j.rser.2017.05.094.
- Ramesh, M., T. Sri Ananda Atreya, U. S. Aswin, H. Eashwar, and C. Deepa. 2014. Processing and mechanical property evaluation of banana fiber reinforced polymer composites. Procedia Engineering 97:563–72. proeng.12.284.
- Ramli, W. M. A. W., M. S. Abdul Majid, M. J. M. Ridzuan, M. T. H. Sultan, N. A. M. Amin, and A. G. Gibson. 2020. The effect of nanomodified epoxy on the tensile and flexural properties of Napier fiber reinforced composites. Polymer Composites 41 (3):824–37. doi:10.1002/PC.25413.
- Reddy, K. O., C. U. M. Mukul Shukla, A. Varada Rajulu, and A. V. Rajulu. 2012. Evaluation of mechanical behavior of chemically modified borassus fruit short fiber/unsaturated polyester composites. Journal of Composite Materials 46 (23):2987–98. doi:10.1177/0021998312454032.
- Sareena, C., M. T. Ramesan, and E. Purushothaman. 2012. Utilization of coconut shell powder as a novel filler in natural rubber. Journal of Reinforced Plastics and Composites 31 (8):533–47. doi:10.1177/0731684412439116.
- Sheng, Z., J. Gao, Z. Jin, H. Dai, L. Zheng, and B. Wang. 2014. Effect of steam explosion on degumming efficiency and physicochemical characteristics of banana fiber. Journal of Applied Polymer Science 131:16. doi:10.1002/APP.40598.
- Venkateshwaran, N., and A. Elayaperumal. 2010. Banana fiber reinforced polymer composites - a review. Journal of Reinforced Plastics and Composites 29 (15):2387–96. doi:10.1177/0731684409360578.
- Vigneshwaran, S., R. Sundarakannan, K. M. John, R. Deepak Joel Johnson, K. Arun Prasath, S. Ajith, V. Arumugaprabu, and M. Uthayakumar. 2020. Recent advancement in the natural fiber polymer composites: A comprehensive review. Journal of Cleaner Production 124109. doi:10.1016/j.jclepro.2020.124109.
- Vigneshwaran, S., M. Uthayakumar, and V. Arumugaprabu. 2019. Development and sustainability of industrial waste-based red mud hybrid composites. Journal of Cleaner Production 230 (September):862–68. doi:10.1016/j.jclepro.2019.05.131.
- Vigneshwaran, S., M. Uthayakumar, and V. Arumugaprabu. 2020. Potential use of industrial waste-red mud in developing hybrid composites: A waste management approach. Journal of Cleaner Production 276 (December):124278. doi:10.1016/j.jclepro.2020.124278.
- Vijayakumar, S., and K. Palanikumar. 2020. Evaluation on mechanical properties of randomly oriented caryota fiber reinforced polymer composites. Journal of Materials Research and Technology 9 (4):7915–25. doi:10.1016/J.JMRT.2020.05.005.