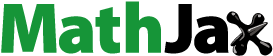
ABSTRACT
This research focuses on developing a new material by reinforcing chemically treated Eleusine Indica (EI) fiber with epoxy resin as matrix. Composites using varying wt% of treated EI fibers were fabricated taking epoxy as matrix. The effect of chemical treatment and fiber loading on various mechanical properties, thermal, and morphology using a scanning electron microscope (SEM) was investigated. From the results obtained, it is obvious that the mechanical and thermal properties of composites reinforced with chemically treated fibers were enhanced due to fiber surface modification which helps in better bonding with matrix. Moreover, the composites with 20 wt% fiber concentration shows good tensile strength, Young’s modulus, impact strength and was found to be 79.31MPa, 3.84 GPa, 32.24 KJ/m2 respectively. At this fiber loading the composites were characterized by Fourier transform infrared spectroscopy (FTIR), X-ray diffraction (XRD), and thermogravimetric (TGA) and compared with untreated fiber reinforced composites and neat epoxy. Finally, the failure analysis of fracture surface due to delimitation, pull-out of the fibers, percentage of voids, and composite fracture has been verified using scanning electron microscope. The findings provide manufacturers and engineers with a general concept of how to employ the composites to make low-weight automotive parts for improved fuel efficiency.
摘要
本研究的重点是开发一种以环氧树脂为基体,通过化学处理的Eleusine Indica(EI)纤维增强的新材料. 以环氧树脂为基体,制备了使用不同重量百分比处理过的EI纤维的复合材料. 利用扫描电子显微镜(SEM)研究了化学处理和纤维负载对各种力学性能、热性能和形态的影响. 从所获得的结果可以看出,由于纤维表面改性有助于更好地与基体结合,化学处理纤维增强的复合材料的机械和热性能得到了提高. 此外,纤维浓度为20 wt%的复合材料显示出良好的拉伸强度、杨氏模量和冲击强度,分别为79.31MPa、3.84GPa和32.24 KJ/m2. 在此纤维负载下,通过傅里叶变换红外光谱(FTIR)、X射线衍射(XRD)、热重分析(TGA)对复合材料进行了表征,并与未处理的纤维增强复合材料和纯环氧树脂进行了比较. 最后,利用扫描电子显微镜验证了断裂表面由于划界、纤维拉出、空隙百分比和复合断裂而导致的失效分析. 研究结果为制造商和工程师提供了如何使用复合材料制造低重量汽车零件以提高燃油效率的一般概念.
Introduction
Due to their inherent qualities, synthetic polymer-based composites have played an increasingly important role in numerous applications such as structural components and vehicle parts in recent decades (Sanjay et al. Citation2019; Vijay et al. Citation2021). Scientists and academics are highly engaged in using bio-based materials to replace and minimize the usage of synthetic materials as a result of increased environmental consciousness and to provide more modern and biodegradable materials for automotive, aerospace, construction, marine, and packaging applications (Vinod et al. Citation2021).
Depending on a number of variables, including the method of extraction, the age of the plant, the portion of the plant from which the fiber is removed, and the geographic region, different plant fibers have different qualities. In addition, components including the fiber type, reinforcing type, orientation, kind of matrix, and catalyst all affect the polymer composite’s characteristics (Binoj et al. Citation2020). In this context, due to their biodegradability, availability, ease of manufacture, low cost, remarkable properties, and lightweight, lignocellulose fiber reinforced polymer composites are recommended (Gurukarthik et al. Citation2019; Manimaran et al. Citation2020; Sanjay and Yogesha Citation2017; Yashas et al. Citation2018). Natural fibers, on the other hand, have issues since their structure is made up of cellulose, hemicelluloses, lignin, pectin, and waxy compounds. These components aid in the absorption of moisture, resulting in composite fracture due to weak fiber-matrix bonding. This is owing to the fact that water molecules can have a physical and chemical effect not only on polymers but also on fibers and the fiber-matrix interface. (Jena et al. Citation2021; Yashas et al. Citation2018) Construction and building, locomotives, furnishings, and the packaging industry all use natural reinforcement-based polymer composites (Bharath et al. Citation2020; Jagadeesh et al. Citation2022; Sanjay and Yogesha Citation2018; Yashas et al. Citation2021). Much effort was given in improving the mechanical performance of this group of materials to expand the capabilities and applications. Chemical modification of fibers results in modifying the fiber surface, which enhances the bonding between a natural fiber and a polymeric matrix (Manimaran et al. Citation2018a; Srisuk et al. Citation2020; Vijay et al. Citation2019). Recently, many researchers reviewed that natural fibers can effectively be used as filler/reinforced material in varieties of thermoplastic and thermoset polymer composites for packaging, constructional, and automotive applications (Jena et al. Citation2022; Nayak and Khuntia Citation2019; Nayak et al. Citation2020). Many natural fibers such as palm, common fig, Carex meyeriana, papaya, Red banana, vetiver grass, Prosopis juliflora, Plassav palm, and Cyperus pangorei were proven to be potential candidates to be used as reinforcement in the polymer matrix for low- and medium-weight-bearing applications (Devi, Bhagawan, and Thomas Citation1996; Eslami-Farsani Citation2017; Jena et al. Citation2021; Manimaran et al. 2018; Mayandi et al. Citation2016; Prithiviraj et al. Citation2016; Rajeshkumar, Hariharan, and Scalici Citation2016; Reddy et al. Citation2016; Saravanakumaar et al. Citation2018; Wang et al. Citation2016).
In this new era of biocomposites, various major variants of Mercedes Benz are utilizing natural fiber like jute for their door panels (Koronis, Silva, and Fontul Citation2013; Mantia and Morreale Citation2011; Marsh Citation2003). Flax/sisal fiber reinforced epoxy composites were used for interior design which decreased the weight by almost 20%. Various body parts of Mercedes EvoBus, Travego, and Setra Top-class were fabricated with composite material made of polyester/flax. A reduction of 5% in weight was observed by using polymer composites reinforced with natural fibers in the engines of setra variants (Koronis, Silva, and Fontul Citation2013). It was observed that natural fiber reinforced polymer composites find wide applications in the manufacture of door lining and panels, interiors of various automobile giants. Cotton fibers and wood fibers are used for sound proofing materials and seat backrest respectively. For seat cushioning of cars, coconut fibers are used.
In the present study, composites were fabricated reinforcing chemically treated and untreated Eleusine Indica grass fibers at different wt% of fiber loading (i.e. 5%, 10%, 15%, 20%, and 25 wt %) with epoxy resin and various properties like mechanical, thermal, and morphological properties were evaluated and studied. The chemical composition characteristics were analyzed using FTIR and XRD spectroscopy.
Materials and methods
Fiber extraction
Eleusine indica (EI) grass is also known as the Indian goose grass, yard grass, goose grass, wiregrass, or crowfoot grass. It is a species of grass in the family Poaceae. EI grass has been collected and immersed in distilled water for around 5 days at room temperature. Then, with the help of a wire brush all the fibers were extracted from the grass. The extracted fibers were sun dried for 3 days to eliminate the moisture present. The fibers at this stage were named as untreated EI fibers ().
Surface modification of fibers
Chemical modification of fibers is a common method for modifying the fiber surface which enhances the bonding between a natural fiber and a polymeric matrix. Natural fibers are hydrophilic in nature whereas polymeric matrix is hydrophobic, so it will result in poor fiber/matrix adhesion. Chemical treatment helps in reducing the hemicellulose, lignin, wax, and oils that surround the external surface of the fiber leading to increase in the surface roughness which improves the fiber/matrix bonding (Mohanty, Misra, and Drzal Citation2001). The untreated EI fibers were alkali-treated in 5% sodium hydroxide (NaOH) solution for 1 h at a temperature of 80°C. Then, the fibers were cooled to room temperature and washed in running water to remove any trace of sodium hydroxide solution adhered on the surface of the fibers so that the pH level of fiber is approximately 7 (neutral). Then, they were dried in an oven at a temperature of 60°C for 24 h. NaOH reacts with the hydroxyl group of the natural fibers, removes the hemicellulose, lignin, wax and oils that surround the external surface of the fiber leading to increase in the surface roughness and reduction in the fiber diameter and results in a mercerized cellulose structure which improves interfacial fiber/matrix bonding (Joseph et al. Citation2003).
Physical and chemical analysis
The density of untreated and alkali-treated Eleusine indica grass fibers were measured using densitometer following Archimedes principle. The chemical composition of Eleusine indica grass was analyzed by the ASTM standard methods. In this analysis, the percentage of cellulose, hemicellulose, and lignin was determined using Kushner and Hoffer method. Ash content was estimated by ASTM E1755–01 method. The wax content was assessed by the Conrad method. The moisture content of Eleusine indica grass was determined with the help of an electronic moisture analyzer (Sartorius, model MA45).
As seen from , the cellulose content has increased by 19.78% after chemical treatment whereas the lignin has decreased from 20.12% to 11.65% in treated fiber. As discussed earlier chemical treatment helps in reducing hydrophilic hydroxyl groups and increases the fiber moisture resistance property. It also takes out a certain portion of hemicelluloses, lignin, pectin, wax, and oil covering materials (Li, Tabil, and Panigrahi Citation2007; Mwaikambo, Tucker, and Clark Citation2007). The cross section of untreated fiber was compared with alkali-treated EI fibers for better understanding the effect of chemical modification of fibers. It was clearly observed that after alkali treatment the fiber cross section was decreased which was explained in earlier sections (). The diameter of Eleusine indica grass fibers were found to be 315.4–318.2 μm; 10 fiber samples from untreated and treated fibers were measured in order to obtain the average value of diameter. The density of untreated fiber was found to be 1143 kg/m3, whereas for treated fiber it was reduced to 1027 kg/m3. Reduced density is a good indication of utilizing those lightweight fibers as reinforcement for fabrication of lightweight automobile parts.
Table 1. Chemical composition and density of EI fiber before and after chemical treatment.
Single fiber tensile strength
The mechanical properties such as tensile strength, Young’s modulus, and flexural strength of untreated and alkali-treated EI fibers were performed as per ASTM D3379–75 (ASTM, Citation1975). To hold the specimen a tab was prepared by cutting a cardboard. A slot has been cut in the middle of the tab having length equal to the gage length (50 mm) of the specimen. Servo-hydraulic static testing machine (INSTRON 3382) has been used to perform the test at a load cell of 100 g. A gauge length of 50 mm and crosshead speed of 0.2 mm/min have been maintained.
The chemical composition of natural fibers affects their mechanical characteristics. Through hydrogen bonding, cellulose contributes to the improvement of mechanical characteristics; in contrast, hemicellulose promotes biodegradation and hinders thermal stability and moisture sensitivity (Asim et al. Citation2020). The alkali-treated EI fibers showed highest cellulose content as compared with raw EI fibers. The increase in weight ratio of cellulose is because alkali treatment reduces the hemicellulose, lignin, and wax from the total composition of EI fibers. It is clearly seen that all the mechanical property values are superior in alkali-treated fiber as compared to untreated fibers. The reason is due to the removal of the major parts of lignin, hemicelluloses, and other impurities. When those impurities are removed, the interfibrillar region is likely to be less dense and less rigid, thereby making the fibrils more capable of rearranging themselves along the direction of tensile deformation, resulting in higher tensile strength (Parida, Dash, and Das Citation2015; Shanmugasundaram and Rajendran Citation2016). Removal of above impurities by alkali treatment makes the fiber surface rough which enhances the fiber-matrix bonding when used for composite fabrication. The mechanical properties obtained for untreated fiber are 42.55 MPa tensile strength, 8.35 GPa Young’s modulus, and 22.98 MPa flexural strength, whereas for alkali-treated EI fiber, the tensile strength recorded is 55.21 MPa, Young’s modulus of 10.67 GPa, and flexural strength of 22.98 MPa. Those obtained results is comparable with other natural fibers like Artisdita hystrix (1.57 ± 0.04 GPa Young’s modulus), Manicaria saccifera palm (2.20 ± 0.44 GPa Young’s modulus), and Sansevieria ehrenbergii (1.50–7.67 GPa Young’s modulus), Cordia dichotoma (16.9 ± 1.3 MPa tensile strength), and Napier grass strands (13.15 MPa tensile strength). The results suggested that Eleusine indica grass can be suitable for reinforcement material in polymer composites.
Fabrication of epoxy/EI composites
A mold has been prepared and coated with wax and allowed to dry in sunlight. Wax coating helps in easy removal of the fabricated composite from the mold. All the samples were prepared by hand layout method. The weight % of alkali-treated EI fibers were varied from 5 wt% to 25 wt% with an interval of 5% (i.e. 5%, 10%, 15%, 20%, and 25 wt %). Two-millimeter length of fibers has been taken as reinforcement. To prepare the matrix epoxy resin, the epoxy was mixed with hardener in the ratio of 10:1. To fabricate 5 wt% EI/epoxy composites, 5 wt% of EI fibers were taken and mixed with epoxy resin. Then the mixture of fiber and epoxy was properly stirred with a mechanical stirrer. After stirring it for 5 min the fiber-epoxy mixture was poured in the prepared mold of size 300 × 300 × 5 mm. A 20 kg weight was kept on the mold and left for curing in room temperature for 24 h. In the similar manner all types of composites were fabricated. A control sample containing 20 wt% of untreated EI fiber was also fabricated for comparison purpose.
Characterization and study of properties of epoxy/EI composites
The tensile tests of treated and untreated epoxy/EI composites were performed in servo-hydraulic static testing machine (INSTRON 3382) with a load cell of 5 kN as per ASTM D 638 standard. At each fiber loading 20 samples were tested and the average value was recorded in the table. The obtained results can be seen in . The tests were conducted at a crosshead speed of 2 mm/min at laboratory temperature, and the displacement was measured with a 50 mm extensometer. The flexural tests were conducted on the same machine using three-point bending method at a crosshead speed of 1 mm/min as per ASTM D 790–99 standard. Similar to tensile test, 20 samples were tested and the average value was noted.
Table 2. Mechanical properties of epoxy/EI composite.
Thermal stability of epoxy/EI composites were studied by the use of thermogravimetric analysis (TGA), while the chemical composition characteristics were analyzed using FTIR and XRD spectroscopy. The thermogravimetric analyses (TGA) of epoxy/EI composites in solid form, weighing around 8–10 mg, were performed with the help of Universal V4.5A TA TGA instrument at a heating rate of 10°C min −1. The measurement is taken according to the rate of change of mass with respect to the change in temperature. FTIR of samples were conducted by Nicolet 6700 Thermo Scientific Spectrophotometer in the absorbance range of 4000 and 400 cm −1. All the composites were ground into small pellets and evaluated using ATR mode. ATR method involves pressing the sample against a high-refractive-index prism and measuring the infrared spectrum using infrared light that is totally internally reflected in the prism. For conducting XRD the samples were taken in powdered form. This test method is performed by directing an x-ray beam at a sample and measuring the scattered intensity as a function of the outgoing direction. Once the beam is separated, the scatter, also called a diffraction pattern, indicates the sample’s crystalline structure. XRD was conducted with Mini Flex Diffractometer (Shimadzu, XRD-7000) operating under CuKα radiation at 40 kV and 150 mA in reflection mode, with a step of 0.05°, counting time of 1 s.
The surface morphology of composites was studied by using ZEISS Supra55 SEM to get a clear idea on fiber-matrix adhesion.
Result and discussion
Study of mechanical properties of untreated and treated epoxy/EI composites
presents various mechanical properties (tensile strength, Young’s modulus, elongation at break, and impact strength) of alkali-treated epoxy/EI, untreated epoxy/EI at 20 wt% fiber loading (control sample) and neat epoxy.
From the results, it is observed that all the above properties are higher in treated fiber composites in comparison to untreated fiber composite. Further, these properties of epoxy/EI composites first increase with fiber loadings and then decrease after reaching the optimum weight percentage (i.e. 20 wt %). The untreated composites show poor value as compared to treated composites because of the presence of lignin in the untreated fibers which deteriorates the strength of the composites due to poor fiber-matrix bonding between hydrophilic fibers and hydrophobic matrix.
The maximum value has been obtained at 20 wt% of fiber loading, which gives 79.31 MPa of tensile strength, 3.84 GPa of Young’s modulus and 32.24 kJ/m2 of impact strength. The tensile strength of the treated composites is presented in the form of a graph in .
Characterization of untreated and treated epoxy/EI composites
The TGA and DTG graph of treated and untreated epoxy/EI composite at 20 wt% fiber loading were presented in . A three-stage degradation process was observed from the graph for both the composites. The initial degradation starts at an early temperature of 30°C for untreated and 40°C for treated composite. An initial weight loss below 155°C can be seen in the TGA graph. This initial drop (4.6% for untreated composite and 6.5% for treated fiber composite) is due to the evaporation of moisture content surrounding the composite surface, moisture absorbed inside the sample (Nayak and Khuntia Citation2019). The maximum degradation in terms of maximum weight loss (2nd stage) can be observed over 240°C for untreated composite (50.25% weight loss) and 265°C for treated composites (43.2% weight loss) which involves synchronous multi-processes such as dehydration, depolymerization, and decomposition of composite. It is observed that the untreated composite has been degraded at a temperature of 410°C (end temperature) whereas the treated composites degrades at a temperature of 530°C (end temperature) in the final stage of degradation which indicated a good thermal stability of treated fiber composites. DTG curves exhibited maximum decomposition rates at DTGmax = 294°C and 311°C for the untreated and treated composite samples, respectively.
shows the FTIR spectrum of treated and untreated epoxy/EI composite at 20 wt% fiber loading. In the spectrum of untreated composite, the broad band at 3397 cm−1 attributed to the symmetrical stretching vibration of – OH group (Bhargav et al. Citation2009; Pradyot et al. Citation2010) which is observed to more stretch as compared to treated composite. This may be due to the presence of water molecules in untreated fibers in the composites. It also indicates the compatibility between EI fibers and epoxy in composite caused by the bonding formation of epoxy matrix with treated fibers formed through the interaction between hydroxy alcohol and phenolic. The band at 2882 cm−1 is more pronounced in treated composites as compared with untreated composite which is due to C – H symmetrical stretching. The wave number at 1735 cm−1 is for H – C – H bending. Various new peaks are observed between 1000 and 1500 cm−1 in treated composites which may be due to active participation of treated fibers as reinforcement in matrix. The peak 1100 cm−1 is stretched more in untreated composite as compared with treated composite, which corresponds to C–H wagging (Pradyot et al. Citation2010). The graph also shows that the number of functional groups has reduced in epoxy composite with treated EI fibers compared with untreated EI fiber composite. Furthermore, it illustrates that the compatibility has been achieved after chemical treatment of fibers. shows the wave numbers and their respective bonding.
Table 3. Wave number with their respective bonding.
The XRD of treated and untreated epoxy/EI composites at 20 wt% fiber loading is shown in and explained. The sharp XRD peak at 18.6° may be due to the crystallinity peak of untreated fibers present in the composite, whereas in the case of treated composite, there is a slight right shift of peaks at 2θ values of 19.5°. A broad peak around 30° in untreated composite shows the amorphous region which may be due to reinforcement of untreated fibers. The same peak has been removed in treated fiber composite showing an increase in crystalline part. It is expected that chemical treatment of fibers removes the amorphous part and increase the crystalline part of the composite. Further, it is also observed that there is no change in the peak at 2Ɵ value of 42°. Hence, it may be concluded that by reinforcing alkali-treated fibers has enhanced fiber-matrix bonding. The reason may be due to removal of amorphous parts from the fiber surface which makes the fiber surface rough for better adhesion with matrix.
shows the SEM images of 20 wt% treated and untreated fiber reinforced composite to have a clear idea about the fiber matrix bonding. In , poor fiber-matrix bonding is visible with detached fibers seen on the surface. Moreover, fibers debonding with some cracks are also observed which clearly explains the poor bonding in untreated 20 wt% fiber loading composite. But in , it is clearly visible that the fibers are closely packed with the matrix showing enhanced fiber-matrix bonding in treated 20 wt% of fiber loading composite (highest mechanical properties were obtained earlier). The reason behind poor fiber-matrix bonding in untreated composite is the hydrophilic nature of the natural fibers due to the presence of lignin and waxy material that leads to fiber detachment and cracks in the fabricated composites. As discussed earlier, chemical treatment removes the unwanted materials like lignin and waxy materials which enhances the quality of the fiber and thus showing a better fiber-matrix bonding in treated composites.
Conclusion
In the present research, composites taking epoxy resin as matrix and alkali-treated Eleusine Indica grass fibers as reinforcement were fabricated and various properties were evaluated and highlighted. As obvious, treated composites reveal enhanced properties as compared with untreated composites. From the test values it has been observed that tensile strength of the composite initially increases with the increase of fiber content and decreases afterward. A fiber loading of 20 wt% was considered as optimum for fabrication of composites as it shows highest mechanical properties (i.e. 79.31 MPa of tensile strength, 3.84 GPa of Young’s modulus, and 32.24 KJ/m2 of impact strength) as compared with other fabricated composites. TGA revealed that better thermal stability of treated composites has been achieved as compared with untreated composites. The chemical composition characteristics were analyzed using FTIR and XRD spectroscopy. Thus, it may be concluded that Eleusine Indica grass fiber composites were found to be a good potential candidate for automobile industries for fabricating interior door panel and dash board.
Disclosure statement
The authors declare that they have no known competing financial interests or personal relationships that could have appeared to influence the work reported in this paper.
References
- Asim, M., M. T. Paridah, M. Chandrasekar, R. M. Shahroze, M. Jawaid, M. Nasir, and R. Siakeng. 2020. Thermal stability of natural fibers and their polymer composites. Iranian Polymer Journal 29 (7):625–12. doi:10.1007/s13726-020-00824-6.
- ASTM D3379-75, 1975. “Standard Test Method for Tensile Strength and Young’s Modulus for High Modulus Single Filament Fibers,” ASTM Standards.
- Bharath, K. N., P. Madhu, T. G. Gowda, A. Verma, M. R. Sanjay, and S. Siengchin. 2020. A novel approach for development of printed circuit board from biofiber based composites. Polymer Composites 41 (11):4550–58. doi:10.1002/pc.25732.
- Bhargav, P. B., V. M. Mohan, A. K. Sharma, and V. V. R. N. Rao. 2009. Investigations on electrical properties of (Pva:Naf) polymer electrolytes for electrochemical cell applications. Current Applied Physics 9 (1):165–71. doi:10.1016/j.cap.2008.01.006.
- Binoj, J. S., R. E. Raj, S. A. Hassan, M. Mariatti, S. Siengchin, and M. R. Sanjay. 2020. Characterization of discarded fruit waste as substitute for harmful synthetic fiber-reinforced polymer composites. Journal of Material Science 55 (20):8513–25. doi:10.1007/s10853-020-04620-8.
- Devi, L. U. M. A., S. S. Bhagawan, and S. Thomas. 1996. Mechanical Properties of Pineapple Leaf Fiber-Reinforced polyester composites. Journal of Applied Polymer Science 64 (9):1739–48. doi:10.1002/(SICI)1097-4628(19970531)64:9<1739:AID-APP10>3.0.CO;2-T.
- Eslami-Farsani, R. 2017. Effect of fiber treatment on the mechanical properties of date palm fiber reinforced PP/EPDM composites. Advanced Composite Materials 24 (1):27–40. doi:10.1080/09243046.2013.871177.
- Gurukarthik, B., D. Prince Winston, P. SenthamaraiKannan, S. S. Saravanakumar, and M. R. Sanjay. 2019. Study on characterization and physicochemical properties of new natural fiber from Phaseolus vulgaris. Journal of Natural Fibers 16 (7):1035–42. doi:10.1080/15440478.2018.1448318.
- Jagadeesh, P. K., M. Puttegowda, Y. G. T. Girijappa, S. M. Rangappa, and S. Siengchin. 2022. Carbon fiber reinforced areca/sisal hybrid composites for railway interior applications: Mechanical and morphological properties. Polymer Composites 43 (1):160–72. doi:10.1002/pc.26364.
- Jena, P. K., J. R. Mohanty, S. Nayak, K. R. Panda, R. Sahu, and S. K. Khuntia. 2022. Utilization of chemically modified novel Urena lobata fibers as reinforcement in polymer composites – an experimental study. Journal of Natural Fibers 19 (7):2479–89. doi:10.1080/15440478.2020.1818352.
- Jena, P. K., P. Samal, S. Nayak, J. R. Behera, S. K. Khuntia, J. Mohapatra, S. D. Mohanty, and C. Malla. 2021. Experimental Investigation on the mechanical, thermal, and morphological behaviour of prosopisjuliflora bark reinforced epoxy polymer composite. Journal of Natural Fibers 19 (14):8593–603. doi:10.1080/15440478.2021.1964144.
- Joseph, P. V., K. Joseph, S. Thomas, C. K. S. Pillai, V. S. Prasad, and G. Groennick. 2003. The thermal and crystallization studies of short sisal fibre reinforced polypropylene composites. Compos Part A Applied Science and Manufacturing 34 (3):253–66. doi:10.1016/S1359-835X(02)00185-9.
- Koronis, G., A. Silva, and M. Fontul. 2013. Green composites: A review of adequate materials for automotive applications. Composites: Part B 44 (1):120–27. doi:10.1016/j.compositesb.2012.07.004.
- Li, X., L. G. Tabil, and S. Panigrahi. 2007. Chemical treatment of natural fibre for use in natural fibre-reinforced composites: A review. Polymer Environment 15 (1):25–33. doi:10.1007/s10924-006-0042-3.
- Manimaran, P., M. R. Sanjay, P. Senthamaraikannan, M. Jawaid, S. S. Saravanakumar, and R. George. 2018a. Synthesis and characterization of cellulosic fiber from red banana peduncle as reinforcement for potential applications. Journal of Natural Fibers 16 (5):768–80. doi:https://doi.org/10.1080/15440478.2018.1434851.
- Manimaran, P., M. R. Sanjay, P. Senthamaraikannan, B. Yogesha, C. Barile, and S. Siengchin. 2020. A new study on characterization of Pithecellobium dulce fiber as composite reinforcement for light-weight applications. Journal of Natural Fibers 17 (3):359–70. doi:10.1080/15440478.2018.1492491.
- Manimaran, P., P. Senthamaraikannan, K. Murugananthan, and M. R. Sanjay. 2018b. Physicochemical properties of new cellulosic fibers from Azadirachta indica plant. Journal of Natural Fibers 15 (1):29–38. doi:10.1080/15440478.2017.1302388.
- Mantia, F. P. L., and M. Morreale. 2011. Green composites: A brief review. Composite Part A: Applied Science and Manufacturing 42 (6):579–88. doi:10.1016/j.compositesa.2011.01.017.
- Marsh, G. 2003. Next step for automobile materials. Materials Today 6 (4):36–43. doi:10.1016/S1369-7021(03)00429-2.
- Mayandi, K., N. Rajini, P. Pitchipoo, J. T. W. Jappes, and A. V. Rajulu. 2016. Extraction and characterization of new natural lignocellulosic fiber Cyperus pangorei. International Journal of Polymer Analysis and Characterization 21 (2):175–83. doi:10.1080/1023666X.2016.1132064.
- Mohanty, A. K., M. Misra, and L. T. Drzal. 2001. Surface modifications of natural fibers and performance of the resulting biocomposites: An Overview. Composite Interfaces 8 (5):313–43. doi:10.1163/156855401753255422.
- Mwaikambo, L. Y., N. Tucker, and A. J. Clark. 2007. Mechanical properties of hemp fibre reinforced euphorbia composites. Macromolecular Materials and Engineering 292 (9):993–1000. doi:10.1002/mame.200700092.
- Nayak, S., and S. K. Khuntia. 2019. Development and study of properties of moringa oleifera fruit fibers/polyethylene terephthalate composites for packaging applications. Composites Communications 15:113–19. doi:10.1016/j.coco.2019.07.008.
- Nayak, S., S. K. Khuntia, S. D. Mohanty, and J. Mohapatra. 2020. Investigation and fabrication of thermo-mechanical properties of ceiba pentandra bark Fiber/Poly (Vinyl) alcohol composites for automobile dash board and door panel applications. Journal of Natural Fibers 19 (2):1–13. doi:10.1080/15440478.2020.1745124.
- Parida, C., S. K. Dash, and S. C. Das. 2015. Effect of fiber treatment and fiber loading on mechanical properties of luffa resorcinol composites. Indian Journal of Materials Science 25:1–6. doi:10.1155/2015/658064.
- Pradyot, N., S. K. Deb, S. Manna, U. De, and S. Tarafdar. 2010. Effect of gamma irradiation on a polymer electrolyte: Variation in crystallinity, viscosity and ion-conductivity with dose. Nuclear Instruments and Methods in Physics Research Section B 268 (1):73–78. doi:10.1016/j.nimb.2009.09.063.
- Prithiviraj, M., R. Muralikannan, P. Senthamaraikannan, and S. S. Saravanakumar. 2016. Characterization of new natural cellulosic fiber from the Perotis indica plant. International Journal of Polymer Analysis and Characterization 21 (8):669–74. doi:10.1080/1023666X.2016.1202466.
- Rajeshkumar, G., V. Hariharan, and T. Scalici. 2016. Effect of NaOH treatment on properties of phoenix Sp. Fiber. Journal of Natural Fibers 13 (6):702–13.
- Reddy, K. O., C. Uma Maheswari, E. Muzenda, M. Shukla, and A. V. Rajulu. 2016. Extraction and characterization of cellulose from pretreated ficus (peepal tree) leaf fibers. Journal of Natural Fibers 13 (1):54–64. doi:10.1080/15440478.2014.984055.
- Sanjay, M. R., S. Siengchin, M. Jawaid, J. K. Parameswaranpillai, C. I. Pruncu, and A. Khan. 2019. A comprehensive review of techniques for natural fibers as reinforcement in composites: Preparation, processing and characterization. Carbohydrate Polymer 207:108–21. doi:10.1016/j.carbpol.2018.11.083.
- Sanjay, M. R., and B. Yogesha. 2017. Studies on natural/glass fiber reinforced polymer hybrid composites: An evolution. Materials Today Proceedings 4 (2):2739–47. doi:10.1016/j.matpr.2017.02.151.
- Sanjay, M. R., and B. Yogesha. 2018. Studies on hybridization effect of jute/kenaf/e-glass woven fabric epoxy composites for potential applications: Effect of laminate stacking sequences. Journal of Industrial Textiles 47 (7):1830–48. doi:10.1177/1528083717710713.
- Saravanakumaar, A., A. Senthilkumar, S. S. Saravanakumar, M. R. Sanjay, and A. Khan. 2018. Impact of alkali treatment on physico-chemical, thermal, structural and tensile properties of Carica papaya bark fibers. International Journal of Polymer Analysis and Characterization 23 (6):529–36. doi:10.1080/1023666X.2018.1501931.
- Shanmugasundaram, N., and I. Rajendran. 2016. Characterization of raw and alkali treated mulberry fibers as potential reinforcement in polymer composites. Journal of Reinforced Plastics and Composites 35 (7):601–14. doi:10.1177/0731684415625822.
- Srisuk, R., L. Techawinyutham, S. Mavinkere Rangappa, S. Siengchin, and R. Dangtungee. 2020. Development of master batch for composites using bamboo charcoal powders in poly(lactic) acid. Polymer Composites 41 (12):5082–95. doi:https://doi.org/10.1002/pc.25776.
- Vijay, R., D. Lenin Singaravelu, A. Vinod, M. R. Sanjay, S. Siengchin, M. Jawaid, A. Khan, and J. Parameswaranpillai. 2019. Characterization of raw and alkali treated new natural cellulosic fibers from Tridax procumbens. International Journal of Biological Macromolecules 125:99–108. doi:10.1016/j.ijbiomac.2018.12.056.
- Vijay, R., A. Vinod, D. L. Singaravelu, M. R. Sanjay, and S. Siengchin. 2021. Characterization of chemical treated and untreated natural fibers from Pennisetum orientale grass- a potential reinforcement for lightweight polymeric applications. International Journal of Lightweight Materials and Manufacture 4 (1):43–49. doi:10.1016/j.ijlmm.2020.06.008.
- Vinod, A., M. R. Sanjay, S. Siengchin, and S. Fischer. 2021. Fully bio-based agro-waste soy stem fiber reinforced bio-epoxy composites for lightweight structural applications: Influence of surface modification techniques. Construction and Building Materials 303:124509. doi:10.1016/j.conbuildmat.2021.124509.
- Wang, C., S. Bai, X. Yue, Z. Ren, and C. Fiber. 2016. Extraction and performance characterization of the carexmeyeriana fiber. Journal of Natural Fibers 13 (6):759–68.
- Yashas, G. T. G., V. Kushvaha, M. R. Sanjay, and S. Siengchin. 2021. A new study on flax-basalt-carbon fiber reinforced epoxy/bioepoxy hybrid composites. Polymer Composites 42 (4):1891–900. doi:10.1002/pc.25944.
- Yashas, G. T. G., M. R. Sanjay, K. Subrahmanya Bhat, P. Madhu, P. Senthamaraikannan, B. Ogesha, and D. Pham. 2018. Polymer matrix-natural fiber composites: An overview. Cogent Engineering 5 (1):1446667. doi:10.1080/23311916.2018.1446667.