ABSTRACT
This paper deals with the study of the chemical composition of cow dung and the paper-making from cow dung. With the insight into such data, we considered the effect of cooking temperatures and the potassium hydroxide concentration on paper performance. The relationship between cow dung fiber, such as morphology, chemical composition, crystallization, and chemical state structure, and paper performance were studied. Meanwhile, the mechanical performance of cow dung paper and the degradation of cow dung paper in soil were investigated in this work as well. At 100°C, the residue from cooking cow dung decreased and stabilized. Fiber yield in cow dung peaked at 10% KOH concentration. The lignin-hemicellulose C=O bonds were completely broken making the material softer and looser. At 42 °SR Schopper-Riegler’s Degree (SR) pulping, the polymerization was 1126, and the average fiber length and width were 1245 μm and 18.3 μm. Cow dung paper had the best mechanical performance at 42 °SR of 2.48 KPam2/g burst index, 4.83 mNm2/g tear index, and 26.72 Nm/g tensile index, respectively. This work demonstrates that cellulose fiber, extracted from cow dung, is suitable for paper applications and provides new insight into cow dung recycling.
摘 要
本文研究了牛粪的化学成分及其造纸工艺。通过深入了解这些数据,我们研究了蒸煮温度和氢氧化钾浓度对纸张性能的影响。研究了牛粪纤维的形态、化学成分、结晶和化学状态结构与纸张性能的关系。除此以外,本文还研究了牛粪纸的力学性能和牛粪纸在土壤中的降解过程。蒸煮温度为100°C时,牛粪的残留物质量趋于稳定,牛粪中的纤维产量在10%KOH浓度时达到峰值,木质素半纤维素C=O键完全断裂,使蒸煮后的牛粪更加柔软和松散;当打浆度为42°SR 时,牛粪制浆的聚合度为1126,平均纤维长度和宽度分别为1245 μm和18.3 μm。牛粪纸在42°SR下的力学性能最好,耐破度为2.48 KPm2/g,撕裂指数为4.83 mNm2/g,抗张强度为26.72 Nm/g。这项工作表明,从牛粪中提取的纤维素纤维适用于造纸,并为牛粪回收利用提供了新的思路。
Introduction
With the development of papermaking technology and market segmentation, functional paper-making plays a critical role in this new information age. As the primary raw material, wood accounts for more than 90% of cellulose pulp (Fechter et al. Citation2020). Although many efforts have been paid to improve the efficiency of cellulose extraction from wood, the vast market demands are still a challenge for papermaking (Debnath, Haldar, and Kumar Purkait Citation2021). As a result, the quest for novel raw pulp materials has become a research priority.
In recent years, raw non-wood pulp materials, such as agricultural waste, have attracted attention. The performance of pulp prepared from bagasse is comparable to hardwood pulps. Bagasse has been used in many types of paper preparation, such as writing, printing and wrapping materials, toilet paper, corrugating medium glassine, liner board, and towels (Bian et al. Citation2019; CitationEl-Sayed, El-Sakhawy, and Abdel-Monem El-Sakhawy Citation2020; Rainey et al. Citation2016). Besides, straw fibers have long been considered a suitable alternative to wood due to their narrow and thick-walled shape with a hull or sharp end. Thus, it can make printing and writing paper, glassine and greaseproof paper, duplex and triplex paper, and corrugating medium paper. Not only that, the rice straw (Jahan et al. Citation2016), date palm rachis (Khiari et al. Citation2010), cotton linter (Ateş et al.), Tunisian Alfa stems (Marrakchi et al. Citation2011), Stipagrostis pungens (Ferhi et al. Citation2014), Opuntia ficus-indica (Mannai et al. Citation2016), Luffa Cylindrica (Premalatha et al. Citation2021), the pineapple and flax fibers (Sumesh et al. Citation2022), Phaseolus vulgaris (Babu et al. Citation2022), Citrullus lanatus Climber (Khan et al. Citation2022), Eleusine Indica Grass (Khan et al. Citation2021), the Stem of Momordica CharantiaAnish et al. (Citation2022), and Cortaderia Selloana Grass (Khan et al. Citation2021), can also be used as raw materials for papermaking, especially in areas lacking wood pulp. However, most of these studies focus on annual pure natural herbs. They still need some treatment, cutting, and cooking. The extraction process is complicated and associated with environmental pollution. To expand the sources of additional papermaking materials, it was found that the process of digesting food in livestock stomachs and non-wood fiber pulping are similar. Digestive enzymes and numerous anaerobic microbes break down plant fibers’ hemicellulose and pectin content, resulting in a very high amount of cellulose in herbivorous animal feces (Braun Citation2016; Joblin et al. Citation2002). For this reason, researchers utilized elephant excrement (Saleem, Yaqoob, and Ur Citation2016), kangaroo excrement (Citation2010), and panda excrement (Xiangguo Citation2018) for paper-making and achieved excellent results. These approaches present new ideas for resource exploitation by humans. Cattle dominate the livestock. Cow dung is not only a resource that has not been widely used, but it is also a significant source of pollution in agricultural production (Gupta, Rai Aneja, and Rana Citation2016). The global cattle population was about one billion in 2020, with an annual increase of 989 million yearly (Citation2021). Thus, if cellulose derived from livestock was used to make paper, the economic value of straw could be enhanced while minimizing environmental pollution caused by cow dung.
Recently, researchers used the kraft pulping method to extract cellulose, lignin, and hemicellulose and obtained useful biological material from cow dung fiber, which fueled the exhaust of researchers, especially in small farms (Puri et al. Citation2020). Indian scholars investigated three types of cow dung and demonstrated the feasibility of paper fabrication from cow dung. However, there was no assessment of the performance of cow dung paper. Furthermore, the article suggests that un-milked and older animals can also find industrial applications, avoiding the need to chop down forests or convert crop straw for papermaking (Fasake and Dashora Citation2020). According to the latest literature, the paper mulching film provides superior environmental conservation and weed control benefits. However, high cost limits its popularity and utilization (Anling et al. Citation2021). If cow dung was the primary raw material for paper mulch production, this would solve the white pollution brought by traditional polyethylene (PE) film while making better use of agricultural waste. Thus, combining farming and animal husbandry to extract fiber and produce cow dung-based paper.
The conventional pulping process is primarily based on NaOH-anthraquinone (Ferhi et al. Citation2014). If recycled improperly, pulping black liquor will cause environmental pollution. By contrast, when KOH is used for pulping, pulping black liquor can be used as liquid fertilizer, avoiding ecological problems while bringing economic benefits (Jahan et al. Citation2016; Kataoka, Del Pilar Hidalgo Falla, and Maria Da Luz Citation2021). Lays Furtado de Medeiros Souza Kataoka studied the efficacy of obtaining cellulosic fibers from jute using KOH. Factors including concentration and reaction time individually significantly affected cellulose yield. (Kataoka, Del Pilar Hidalgo Falla, and Maria Da Luz Citation2021); Erinc Bahcegul considered the production of hemicellulose based films, should govern the pretreatment temperature since it was more responsive to the changes in the pretreatment temperature compared to the cellulosic part that accounts for glucose production. (Bahcegul et al. Citation2012). In this work, cow dung was pulped with KOH solution, and cow dung paper was made. The physical characteristics of cow dung pulp and paper were evaluated using a scanning electron microscope and energy-dispersive X-ray spectroscopy (SEM-EDS), Thermal gravimetric analysis (TGA), Fourier Transform Infrared Spectroscopy (FTIR), X-ray diffraction (XRD), and X-ray photoelectron spectroscopy (XPS). The study’s findings indicated that cow dung-based paper has a wide range of applications.
Experimental
Materials
Cow dung was obtained from Huarui agricultural company, Eco-industrial park, Minle County, Zhangye City, Gansu province, China. The breeds of dairy cows are mostly Holstein and Jersey cows, and the cows were fed with silage corn and high-quality alfalfa. The cow dung was grounded according to the GB 02677.1-1993-T standards, and its 40–60 mesh fractions were selected for chemical composition analysis.
Characterization of the cow dung
The morphology and composition of cow dung and cow dung paper were examined by scanning electron microscope (SEM, FEI Inspect F50) with coupled energy-dispersive X-ray spectroscopy (EDS). The chemical compositions of cow dung were carried out according to standardized methods, as shown in the Supporting information. The surface species and relative thermal stability of the cow dung and cow dung paper were measured by thermal gravimetric analysis (TGA), Fourier Transform Infrared Spectroscopy (FTIR), X-ray diffraction (XRD) and X-ray photoelectron spectroscopy (XPS). Details of these measurements were present in Part 1 of Supporting information.
The optimized process of cow dung paper making
The process of Cow dung paper making is shown in . Pulping of cow dung was carried out by KOH process in electrically heated four lits capacity digesters. The following parameters were held constant to optimize the pulping process and get the optimal pulping temperature: (1) Cow dung to liquor ratio: 1:10, (2) Cooking time: 60 min. Cooking temperatures range from 60°C to 120°C, and KOH concentration changes among 0%, 5%, 10%, and 15%. After cooking, we rinsed the bleaching material many times with distilled water until it reached a neutral pH value. The pulp yield was calculated gravimetrically using the oven-dried weight of residue. The fiber yield was evaluated using the nitric acid-ethanol method. To optimize the pulping process and select the best KOH concentration, the active KOH concentration was varied from 0, 5%, 10%, and 15% on cow dung at 100°C. XRD, TGA, and SR were used to characterize the fibers. To optimize the pulping process and select the best drainage resistance, the active drainage resistance charge was varied from 22°SR, 30.5°SR, 42°SR, 51°SR, 60°SR, and 68°SR on cow dung at 100°C, 10% KOH. The tensile and burst indexes were determined.
Fiber analyses
The Kappa values and degree of polymerization (DP) were calculated according to GB/T 1546–1989 and GB/T 1548–1989. The DP is determined by the following formula proposed by Sihtola et al. (Sihtola et al. Citation1963). The pulp’s water retention value (WRV) was determined using the Silvy et al. method (Silvy, Romatier, and Chiodi Citation1968). To measure the drainage capacity of pulp, the SR was determined according to GB/T 3332–1982. More details can be seen in Part 2 of Supporting Information
Paper making process
Optimum conditions for preparing cow dung paper are: (1) Cow dung to liquor ratio: 1:10; (2) Cooking time: 60 min; (3) Cooking temperature: 100°C; (4) KOH concentration :10%; (5) SR: 42 °SR. The diluted pulp suspension concentration is 2 g/L. The prepared hand sheets exhibited a base weight of 60 g/m2, according to ISO 5269–2. Papers were conditioned at 23°C and 50% humidity for 48 h, according to ISO 187. All of the hand sheets tests were based on the following standards: ISO536, ISO 534, ISO 5636–3, ISO 1924–3, ISO 2758, and ISO 1974, to measure the basis weight, thickness, bulk, and permeability, as well as the tensile, burst and tear strengths. The elemental composition and morphology of the cow dung paper were determined by SEM with EDX.
Cow dung paper was buried in the soil and monitored every 30 days to investigate the degrading process. This bioremediation experiment area is located in Hexi arid oasis irrigation area, Zhangye City, Gansu. (100 625′ N, 38 375′ E, 1673 m ASL). The annual radiation temperature is 11.61°C, and the annual average precipitation is 133.1 mm. According to Chinese soil taxonomy, the soil type is Castanea mollissima, which is developed from loess-like parent material, with soil PH value of 8.5 and available water content of 1 mm.
Results and discussion
Characterization of raw materials
The morphology of cleaned cow dung was first measured via Scanning Electron Microscopy (SEM), as shown in . The cleaned cow dung is mainly made up of coarse fibers with diameters of 100–300 μm and lengths of 500–1500 μm. Meanwhile, these natural fibers consist of a series of homogenous tiny fibers, as shown in . Further analysis implies many mesoporous pores on fibers, which are probably extended along these “hollow” fibers, as suggested by . This mesoporosity would increase the roughness of fibers’ surface and enhance water affinity, thus shorting the mixing time. Moreover, this mesoporosity would also facilitate alkaline liquid permeation and increase cooking efficiency, thus enhancing the quality of final products. It is worth mentioning that due to the low conductivity of cleaned-cow dung, the samples were first processed by metal spraying. That is to say, the natural surface of the cleaned-cow dung may not be smooth, as shown in .
shows the chemical analysis of cow dung and a variety of lignocellulosic plants. The results obtained from cow dung were compared with those from other raw materials reported in the literature. The results show that the cellulose content was similar to the ones of Rapeseed Straw (Mousavi et al. Citation2013) and Softwood (Gharehkhani et al. Citation2015), and the content of holocellulose was close to that of Paulownia Fortuna (Rodríguez et al. Citation2008) and Softwood. Lignin content is similar to the ones of Paulownia Fortuna (Gharehkhani et al. Citation2015) and Hardwood (Gharehkhani et al. Citation2015). The ash content is equivalent to the one of Bagasse (Saeed et al. Citation2017); NaOH extract is slightly higher than the one of Cotton cellulose (Rodríguez et al. Citation2008), and hot water extract is slightly lower than the one of Phragmites (Rodríguez et al. Citation2008).
Table 1. Chemical composition of cow dung and other plants.
The thermal stability of the cleaned cow dung was further measured by the thermogravimetric analysis (TGA), as illustrated in . The TGA curve showed two stages of weight loss. The first weight-loss stage was generated from 50°C to 115°C due to the desorption/release of water from the hydrophilic lignocellulosic surface (~10%). From 115°C to 250°C, there is no weight loss or other thermal decomposition. The raw materials showed a novel thermostability and presented a stable stage on the TGA curve. After this stage, a sharp weight loss occurred from 250°C toTo 400°C due to the degradation of the lignocellulosic biomass fractions. At the loss stage, from 400°C to 800°C, the long-chain lignin was further degraded and showed a slow decline in weight. Meanwhile, we also noted that the first two sharply weight-losing stages are commonly coupled with an endothermic peak, as present in , implying that the thermal decomposition process is in an exothermic reaction.
X-ray diffraction was performed on the cleaned-cow dung, as shown in , which presents the XRD measurement for the dried sample of prepared cleaned-cow dung. At present, the XRD diffraction pattern shows significant intensity peaks located at 15°, 21° and 33° (#PDF-00-043-1589). Meanwhile, the relatively high background probably comes from the amorphous glass slide. The degree of crystallinity is about 51.07%. However, many other peaks were also detected, which might have been generated by the corresponding silica. The EDS analysis () revealed that C and O were the most prevalent components of cow dung. It was also found that the mineral elements Si and Ca were present at low concentrations.
Effect of temperature on extraction of cow dung fiber
shows the morphology of cow dung after treatment with potassium hydroxide at various temperatures and concentrations. As shown in , the fiber condition of cow dung steamed at 60°C did not change significantly after 45 min of precipitation and remained clean and visible. In the cow dung fiber cooked at 120°C, however, some fine flocculent fibers emerged above the precipitates. After 45 min of precipitation, the cow dung fibers were shaken to obtain the suspension illustrated in . Cow dung fibers heated at 60°C were the most visible in the suspension. The suspension grew increasingly hazy as the steaming temperature went from 60°C to 120°C, showing that the higher the steaming temperature, the more terrific the dimensional refinement of the cow dung fibers. The refined components of cow dung fiber steadily increased with increasing KOH concentration, as indicated in . This phenomenon is also considerably affected by temperature. The suspension illustrated in show that the size of cow dung fiber changes dramatically with temperature and KOH concentration. The higher the temperature and KOH content after 20 h of drying, the more advanced the refinement and softness of the cow dung fiber are, as shown in .
Figure 4. The morphology of cow dung after treatment with KOH at different temperatures and concentrations (a~l), the influence of temperature on cow dung residue % (n), the influence of temperature on cow dung fiber (o).

As shown in , the residue quality of the reaction decreases as the temperature rises during the cooking of cow dung. This is due to the fact that as the temperature rises, the collision between molecules becomes more intense, and the reactivity increases significantly, resulting in the hydrolysis of non-fiber materials (such as crude lignin fat and crude protein, etc.). However, when the cooking temperature exceeds 100°C, the residue after the reaction tends to be stable. () displays the residual content after cooking at various temperatures and KOH concentrations. The residual content at cooking temperatures of 100°C and 120°C are comparable. As a result, from the standpoint of energy consumption, 100°C was chosen as the best reaction temperature to extract cow dung fiber.
Table 2. The residual content after cooking at different temperatures and concentrations of KOt.
Effect of KOH concentration on yield of cow dung fiber
The cellulose content of the cooking residue was tested using the nitric acid ethanol technique. The cellulose content in cow dung varied with KOH concentration at the same temperature, as illustrated in . When the KOH concentration was between 0 and 10%, the cellulose content rose with the increase of KOH concentration, indicating positively linked treads of the cellulose content. When the KOH concentration reached 10%, the highest value of cellulose content was observed. When the KOH concentration exceeds 10%, the cellulose content decreases. These results demonstrated that 10% of KOH is the best compromise between hemicellulose and lignin in the residue and KOH concentration. When the KOH concentration reaches 10%, the hemicellulose and lignin in the cooking waste are destroyed, and the lye begins to break down cellulose. illustrates the fiber yield after incubation at various temperatures and KOH concentrations. The best reaction temperature is 100°C with a KOH concentration of 10% chosen for economic gain.
Table 3. Fiber yield after cooking at different temperatures and concentrations of KOH.
FTIR and XRD further investigated the effect of KOH concentration on the surface functional group of cow dung fibers. As presented in , the FTIR spectra present a peak around 3400 cm−1, which can be indexed to O-H groups. This indicated that cellulose exists in cow dung fibers. The stretch vibration of approximately 2920 cm−1 is a typical band of cellulose and hemicellulose components, further confirming the existence of cellulose (Jaramillo-Quiceno et al. Citation2018). Moreover, we also noted that the signal of carbonyl stretching (1730 cm−1) is enhanced with increased KOH concentration, bringing evidence of hemicellulose and lignin in cow dung fibers. Additionally, all spectra present a broad peak at 1050 cm-1, which can be indexed to C-H glycosidic bonds stretching, indicating that the amorphous constituents have been removed, and the cellulose is exposed at the surface of cow dung fibers, this is consistent with the study of Nikonenko et al (Nikonenko et al. Citation2000). Anyhow, in cow dung fibers, the bands between 1520 and 1690 cm−1 appeared in all samples, indicating that the C=O and C=C are stable in samples and that KOH has little effect on the structure of cow dung fibers when KOH concentration is below 15%. In addition, the XRD results showed that the characteristic peak at 22° decreased with the increase of KOH concentration, implying that the amorphous carbon was removed, which is consistent with FTIR (). The cow dung before and after cooking with lye were beaten, and the SR was tested every two minutes. The curves of beating time and SR are shown in . The SR of cow dung cooked with KOH solution improved significantly in the same beating time as cow dung cooked without treatment, but SR of cow dung cooked with 10% KOH solution and cow dung cooked with 15% KOH solution exhibited little difference. The maximum SR of untreated cow dung after 60 min of beating was 29°SR, while the maximum SR of the KOH-treated cow dung was 59°SR. As a result, the KOH cooking treatment significantly enhanced the cow dung SR.
Figure 5. The FTIR (a), XRD (b), and SR (c) spectra of cow dung fibers processed at different KOH concentrations.
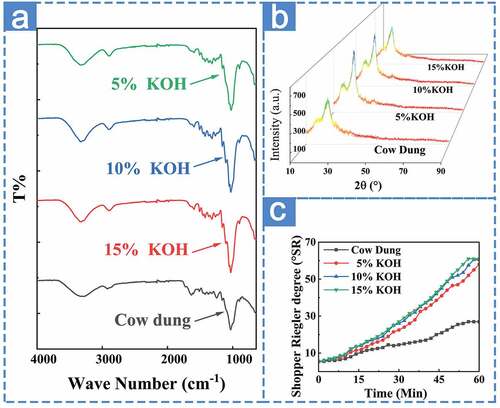
We further considered the stability of cow dung fibers with the increase in KOH concentration. As presented in , TG and DTG were performed on every KOH-treated cow dung fiber. It shows that cow dung fibers’ decomposition behavior differs depending on KOH concentration. Due to the fiber being exposed to air, the samples quickly absorb the species in the air. The first thermal decomposition peak, which appeared below 100°C for all samples, can be indexed to moisture and adsorbates loss. The second weight-loss peak appeared at 316°C, indicating the thermal decomposition of the cellulose of cow dung fibers. This temperature is slightly lower than standard cellulose extracted from other fibers, indicating that the cow digested fibers are less stable than other types. Meanwhile, with the increasing KOH concentration, the second decomposition temperature of cow dung fibers has increased with increasing KOH concentration, implying that the lignin, hemicellulose and crude protein have been removed. Moreover, when the KOH concentration is higher than 10%, the third decomposition peak, ranging from 400°C to 500°C, disappears, suggesting that lignin, hemicellulose, crude protein, and crude fat have been removed during the cooking process.
Effect of SR on mechanical properties of cow dung paper
The SR has a significant effect on the mechanical characteristics of paper. Therefore, it is critical to choose a suitable SR. In this study, cow dung fibers were selected after steaming with a solution containing 10% KOH, and six degrees of beating, 22°SR, 30.5°SR, 42°SR, 51°SR, 60°SR, and 68°SR, were chosen for paper making. The tensile strength achieved is displayed in , and the burst strength is presented in . The tensile strengths and burst strength were 14.22 N and 81.89 kgP, 18.92 N and 98.76 kgP, 24.92 N and 140.04 kgP, 33.59 N and 148.97 kgP when SR was at 22°SR, 30.5°SR, 42°SR, 51°SR, respectively. At this moment, the tensile strength and burst strength rise as the SR rises. This phenomenon occurs when shear and friction damage the primary wall of cow dung fiber, causing water absorption, swelling, and fine fibrillation to rise substantially faster, increasing the inter-fiber bonding force. When the SR exceeded 51 °SR, the tensile strength and burst strength started to decrease, and when the SR was 60 °SR, the Tensile strength and Burst index were 29.55 N and 132.30 kgP, respectively, and when the SR was 68°SR, the Tensile strength and Burst index were 28.06 N and 111.02 kgP. The Tensile strength and Burst strength decrease with the increase of SR. While the binding force of fibers improves with continuous pounding, the binding force between fibers grows slowly. In contrast, the average fiber length decreases tensile and burst strength. However, during testing, it was shown during testing that increasing the SR from 42°SR to 51°SR resulted in little change in tensile and burst strength while increasing the SR from 42°SR to 51°SR increased the time and energy consumption considerably. Therefore, a pulp with an SR of 42° was selected for the final paper manufacturing.
Pulp and paper characterization
The morphological properties of the obtained pulp fibers are shown in . The length of the cow dung fiber is 730 μm (arithmetic mean), and the width is 17.6 μm (arithmetic mean). These results show that the fiber is close to fibers obtained from some annual plants in terms of morphology. Cow dung has a much higher WRV value (144%) than unrefined softwood hardwood pulp (90%-100%). This value shows that the fibers have high flexibility. Consequently, the resulting paper has strong mechanical properties. The pulp’s degree of polymerization (DPv), around 1127, is suited for paper applications and indicates that suitable pulping conditions were applied. The SR of produced pulp is around 40°SR. These values are similar to those of other non-woody and annual plants of the same species.
Table 4. Main properties of the pulp.
To evaluate the cow dung paper, the morphological SEM examination was carried out on the cow dung paper (their surface and cross-sectional views are shown in ). Upon the surface of the sheet surface, the fibers were long and expanded, well-spaced and homogeneous, and securely connected together in a crisscross pattern. () Many thick fibers are visible on the paper’s surface, as well as a homogeneous distribution of delicate components over the paper’s surface. The EDS analysis revealed that C and O were the most prevalent components of this material, as expected. It was also found that the mineral elements Si and Ca were present in low concentrations. As shown in , the primary constituents of cow dung paper were based on C and O. However, compared to the raw material of cow dung, the amounts of Si and Ca have been significantly reduced.
Figure 8. The micrograph of a cow dung paper: longitudinal section (a) and surface (b) of cow dung paper, the EDS (c) spectrum of cow dung paper.
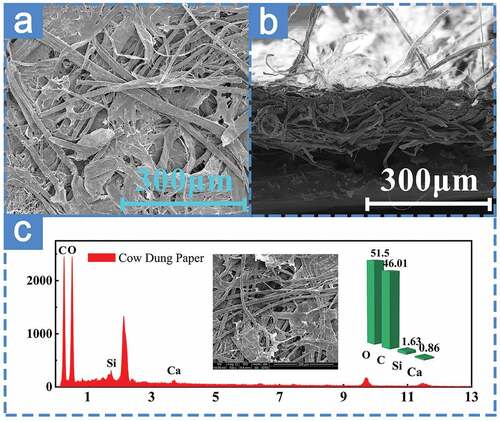
XPS has been performed to characterize the surface species and the residues further. shows the full spectrum of cow dung fibers, which exhibited O1s, Ca2p, C1s, and Si 2p peaks, in agreement with FTIR results. The high-resolution spectrum () of K 2p presents a feeble peak at 296.2 eV, implying that K has been completely removed during the rinsing process, which is essential for decreasing the soil alkalization induced by paper mulch. The fitting of O1s peaks presents an O0 peak at 530.9 eV, indicating that O2 is adsorbed on the surface of cow dung fibers (), which is consistent with the DTA results. Meanwhile, we also note that the Si and Ca are present at the surface of fibers as Si0 and Ca2+ (), which are probably induced by the straw knots, which are easily enriched by Ca and Si elements. Although cows have digested the fibers, these indigestible masses are also present in significant amounts. The C1s have been further considered in this work. As presented in , the fitting results show two peaks at 285.1 eV and 282.9 eV, attributed to C-C and C-H, suggesting that organic matter is stable in fibers. Note that the C1s spectrum also corrected the XPS data. The structural and mechanical properties of the cow dung paper made from cow dung were determined and compared to those of paper made from Wheat straw, Corn stalk, Rice straw, and Cotton stalk (see ).
Figure 9. The XPS spectra of cow dung fibers. a) full spectrum, b) K 2p regions, c) O 1s regions, d) Si 2p regions, e) Ca 2p regions, f) C 1s regions.
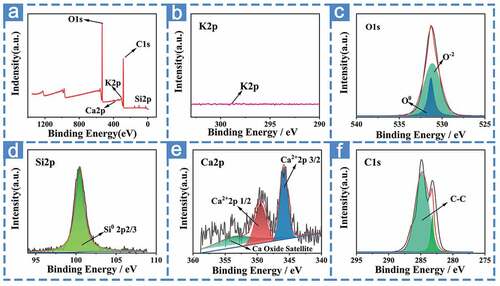
Table 5. Paper properties made from cow dung and some other sources of agricultural waste.
The cow dung paper was buried in the soil for degradation testing, and samples were collected every 30 days, as illustrated in . There was no discernible change in the cow dung paper after 30 days, and the paper could be felt to become brittle when gathered, making it easier to break than in the initial stage, as illustrated in . Mildew patches occurred on cow dung paper after 60 days, as illustrated in . Cow dung paper was more brittle and easily breakable. A substantial quantity of mildew occurred on the cow dung paper after 90 days, which might have been damaged by a gentle touch during collection, as illustrated in . Cow dung paper has no longer been collected after 120 days. Cow dung paper degrades in around 120 days, showing a solid degradation performance.
Conclusion
This study utilized cow dung for papermaking and revealed the effects of KOH concentration and temperature on the treatment of cow dung. The physical property analysis shows that KOH concentration and temperature played an essential role in cow dung fiber’s morphology, chemical composition, crystallization, and chemical state structure, with a significant effect on the final paper performance. The comparative study presents that the residue from cooking cow dung decreased and stabilized at 100°C and achieved a fiber yield peak at 10% KOH concentration. Microscopic morphology analysis demonstrated that the average fiber length and width of pulp were 1245 μm and 18.3 μm. The results of the analysis of the paper show that the mechanical properties of cow dung paper depend heavily on the SR. Under 10% KOH, T = 100°C, T = 60 min, 42°SR. The cow dung paper showed an optimum performance of burst index 2.48 KPam2/g, tear index 4.83 mNm2/g, and tensile index 26.72 Nm/g. In addition, the degradation performance of the cow dung paper was also considered. After 120 days, the cow dung paper was degraded completely, reflecting an application potential on mulching film. This work demonstrates that cellulose fiber, extracted from cow dung, is suitable for paper applications and provides new insight into cow dung recycling.
Highlights
The role of temperature and KOH concentration on pulping of cow dung fibers was studied.
The highest cow dung fiber yield of 42% is obtained with 10% KOH concentration at 100℃.
The best cow dung paper, prepared at 42° SR, shows the highest tensile properties and burst index of 4.36 m·Nm2/g and 2.48 KPa·m2/g, respectively.
The cow dung paper can be completely degraded within 100 days.
Supplemental Material
Download Zip (159.1 KB)Disclosure statement
No potential conflict of interest was reported by the authors.
Supplementary material
Supplemental data for this article can be accessed online at https://doi.org/10.1080/15440478.2022.2164546
Additional information
Funding
References
- Anish, K., D. L. S. Vijay Raghunathan, M. R. Sanjay, S. Siengchin, M. Jawaid, A. A. Khalid, and M. A. Abdullah. 2022. Extraction and characterization of cellulose fibers from the stem of momordica charantia. Journal of Natural Fibers 19 (6):2232–15. doi:10.1080/15440478.2020.1807442.
- Anling, L., J. Zhang, S. Ren, Y. Zhang, and F. Zhang. 2021. Research progress on preparation and field application of paper mulch. Environmental Technology & Innovation 24 (November):101949. doi:10.1016/j.eti.2021.101949.
- Artist Finds His Niche - Turning Poo into Paper. 2010. Stuff. https://www.stuff.co.nz/oddstuff/3673024/Artist-finds-his-niche-turning-poo-into-paper.
- Babu, B., D. Gurukarthik, S. S. Princewinston, Saravanakumar, P. V. Anish Khan, S. Aravind Bhaskar, Indran, and D. Divya. 2022. Investigation on the physicochemical and mechanical properties of novel alkali-treated Phaseolus vulgaris fibers. Journal of Natural Fibers 19 (2):770–81. doi:10.1080/15440478.2020.1761930.
- Bahcegul, E., H. Ezgi Toraman, N. Ozkan, and U. Bakir. 2012. Evaluation of Alkaline pretreatment temperature on a multi-product basis for the co-production of glucose and hemicellulose based films from lignocellulosic biomass. Bioresource Technology 103 (1):440–45. doi:10.1016/j.biortech.2011.09.138.
- Bian, H., Y. Gao, J. Luo, L. Jiao, W. Weibing, G. Fang, and H. Dai. 2019. Lignocellulosic Nanofibrils produced using wheat straw and their pulping solid residue: from agricultural waste to cellulose nanomaterials. Waste Management 91 (May):1–8. doi:10.1016/j.wasman.2019.04.052.
- Braun, U. 2016. Ultrasonographic Examination of the Reticulum, Rumen, Omasum, Abomasum, and Liver in Calves. The Veterinary Clinics of North America Food Animal Practice 32 (1):85–107. doi:10.1016/j.cvfa.2015.09.011.
- “Cattle/Cow Population Worldwide 2012-2021.” 2021. Statista. Accessed December 5. https://www.statista.com/statistics/263979/global-cattle-population-since-1990/.
- Debnath, B., D. Haldar, and M. Kumar Purkait. 2021. A critical review on the techniques used for the synthesis and applications of crystalline cellulose derived from agricultural wastes and forest residues. Carbohydrate Polymers 273 (December):118537. doi:10.1016/j.carbpol.2021.118537.
- El-Sayed, E. S. A., M. El-Sakhawy, and M. Abdel-Monem El-Sakhawy. 2020. Non-wood fibers as raw material for pulp and paper industry. Nordic Pulp & Paper Research Journal 35 (2):215–30. De Gruyter. doi:10.1515/npprj-2019-0064.
- Fasake, V., and K. Dashora. 2020. Characterization and morphology of natural dung polymer for potential industrial application as bio-based fillers. Polymers 12 (12):3030. doi:10.3390/polym12123030.
- Fechter, C., S. Fischer, F. Reimann, H. Brelid, and T. Heinze. 2020. Influence of pulp characteristics on the properties of Alkali cellulose. Cellulose 27 (12):7227–41. doi:10.1007/s10570-020-03151-4.
- Ferdous, T., M. A. Quaiyyum, S. Bashar, and M. S. Jahan. 2020. Anatomical, morphological and chemical characteristics of kaun straw (Seetaria-ltalika). Nordic Pulp & Paper Research Journal 35:288–298. doi:10.1515/npprj-2019-0057.
- Ferhi, F., S. Das, Y. Moussaoui, E. Elaloui, and J. G. Yanez. 2014. Paper from Stipagrostis Pungens. Industrial Crops and Products 59:59. doi:10.1016/j.indcrop.2014.05.015.
- Gharehkhani, S., E. Sadeghinezhad, S. N. Kazi, H. Yarmand, A. Badarudin, M. R. Safaei, and M. N. M. Zubir. 2015. Basic effects of pulp refining on fiber properties—A review. Carbohydrate Polymers 115:115. doi:10.1016/j.carbpol.2014.08.047.
- Gupta, K. K., K. Rai Aneja, and D. Rana. 2016. Current status of cow dung as a bioresource for sustainable development. Bioresources and Bioprocessing 3 (1):28. doi:10.1186/s40643-016-0105-9.
- Jahan, M. S., F. Haris, M. M. Rahman, P. Rani Samaddar, and S. Sutradhar. 2016. Potassium Hydroxide pulping of rice straw in biorefinery initiatives. Bioresource Technology 219 (November):445–50. doi:10.1016/j.biortech.2016.08.008.
- Jaramillo-Quiceno, J. Natalia, V. R. Manuel, M. Edith, C. Cadena, A. Restrepo-Osorio, and J. Felipe Santa. 2018. Improvement of mechanical properties of pineapple leaf fibers by mercerization process. Fibers and Polymers 19 (12):2604–11. doi:10.1007/s12221-018-8522-3.
- Joblin, K. N., H. Matsui, G. E. Naylor, and K. Ushida. 2002. Degradation of fresh ryegrass by methanogenic co-cultures of ruminal fungi grown in the presence or absence of Fibrobacter Succinogenes. Current microbiology 45 (1):46–53. doi:10.1007/s00284-001-0078-5.
- Kataoka, L. F. D. M. S., M. Del Pilar Hidalgo Falla, and S. Maria Da Luz. June 2021. The Influence of Potassium Hydroxide Concentration and reaction time on the extraction cellulosic jute fibers. Journal of Natural Fibers 19(13):1–13. doi: 10.1080/15440478.2021.1934934.
- Khan, A., R. Vijay, D. Lenin Singaravelu, M. R. Sanjay, S. Siengchin, M. Jawaid, A. A. Khalid, and M. A. Abdullah. 2022. Extraction and characterization of natural fibers from Citrullus Lanatus climber. Journal of Natural Fibers 19 (2):621–29. doi:10.1080/15440478.2020.1758281.
- Khan, A., R. Vijay, D. Lenin Singaravelu, M. R. Sanjay, S. Siengchin, F. Verpoort, K. Ahmad Alamry, and M. A. Abdullah. 2021. Characterization of natural fibers from Cortaderia Selloana Grass (Pampas) as reinforcement material for the production of the composites. Journal of Natural Fibers 18 (11):1893–901. doi:10.1080/15440478.2019.1709110.
- Khan, A., R. Vijay, D. Lenin Singaravelu, M. R. Sanjay, S. Siengchin, F. Verpoort, A. A. Khalid, and A. M. Asiri. 2021. Extraction and characterization of natural fiber from eleusine indica grass as reinforcement of sustainable fiber reinforced polymer composites. Journal of Natural Fibers 18 (11):1742–50. doi:10.1080/15440478.2019.1697993.
- Khiari, R., M. F. Mhenni, M. N. Belgacem, and E. Mauret. 2010. Chemical composition and pulping of date palm rachis and posidonia oceanica – a comparison with other wood and non-wood fibre sources. Bioresource Technology 101 (2):101. doi:10.1016/j.biortech.2009.08.079.
- Mannai, F., M. Ammar, E. E. José Garrido Yanez, and Y. Moussaoui. 2016. Cellulose fiber from Tunisian Barbary Fig “Opuntia ficus-indica” for papermaking. Cellulose 23 (3):2061–72. doi:10.1007/s10570-016-0899-9.
- Marrakchi, Z., R. Khiari, H. Oueslati, É. Mauret, and F. Mhenni. 2011. Pulping and papermaking properties of tunisian alfa stems (Stipa Tenacissima)—Effects of refining process. Industrial Crops and Products 34 (3):1572–82. doi:10.1016/j.indcrop.2011.05.022.
- Mousavi, S. M. M., S. Z. Hosseini, H. Resalati, S. Mahdavi, and E. R. Garmaroody. 2013. Papermaking potential of rapeseed straw, a new agricultural-based fiber source. Journal of Cleaner Production 52:52. doi:10.1016/j.jclepro.2013.02.016.
- Moussaoui, Y., F. Ferhi, E. Elaloui, R. Ben Salem, and M. N. Belgacem. 2011. Utilisation of Astragalus armatus roots in papermaking. Bioresour 6:4969–4978. doi:10.15376/BIORES.6.4.4969-4978.
- Nikonenko, N. A., D. K. Buslov, N. I. Sushko, and R. G. Zhbankov. 2000. Investigation of Stretching Vibrations of Glycosidic Linkages in Disaccharides and Polysaccharides with Use of IR Spectra Deconvolution. Biopolymers 57 (4):257–62. doi:10.1002/1097-0282(2000)57:4<257:AID-BIP7>3.0.CO;2-3.
- Premalatha, N., S. S. Saravanakumar, M. R. Sanjay, S. Siengchin, and A. Khan. 2021. Structural and Thermal Properties of Chemically Modified Luffa Cylindrica Fibers. Journal of Natural Fibers 18 (7):1038–44. doi:10.1080/15440478.2019.1678546.
- Puri, S., S. Sharma, A. Kumari, M. Sharma, U. Sharma, and S. Kumar. November 2020. Extraction of Lignocellulosic Constituents from Cow Dung: Preparation and Characterisation of Nanocellulose. Biomass Conversion and Biorefinery 13(1):311–20. doi: 10.1007/s13399-020-01119-9.
- Rainey, T. J., and G. Covey. 2016. Pulp and Paper Production from Sugarcane Bagasse. In Sugarcane-Based Biofuels and Bioproducts, ed. I. M. O’Hara and S. G. Mundree, 259–80. Hoboken, NJ, USA: John Wiley & Sons, Inc. doi:10.1002/9781118719862.ch10.
- Rodríguez, A., L. Serrano, A. Moral, A. Pérez, and L. Jiménez. 2008. Use of High-Boiling Point Organic Solvents for Pulping Oil Palm Empty Fruit Bunches. Bioresource Technology 99 (6):1743–49. doi:10.1016/j.biortech.2007.03.050.
- Saeed, H. A. M., Y. Liu, L. Lucia, and H. Chen. 2017. Evaluation of Sudanese Sorghum and Bagasse as a Pulp and Paper Feedstock. Bioresources 12 (3):5212–22. doi:10.15376/biores.12.3.5212-5222.
- Saleem, M., N. Yaqoob, and R. I. Ur-. 2016. Eco-Friendly Bleaching of Soda-AQ Chemical Elephant Dung Pulp. IRA-International Journal of Applied Sciences (ISSN 2455-4499) 4 (1). doi:10.21013/jas.v4.n1.p4.
- Sihtola, H., B. Kyrklund, L. Laamanen, and I. Palenius. 1963. Comparison and conversion of viscosity and DP values determined by different methods. Pap Puu 4 225–232 .
- Silvy, J., G. Romatier, and R. Chiodi. 1968. Méthodes Pratiques de Contrôle Du Raffinage. Revue ATIP 22 31–53.
- Sumesh, K., V. Kavimani, G. Rajeshkumar, S. Indran, and A. Khan. 2022. Mechanical, water absorption and wear characteristics of novel polymeric composites: Impact of hybrid natural fibers and oil cake filler addition. Journal of Industrial Textiles 51 (4_suppl):5910S–37S. doi:10.1177/1528083720971344.
- Xiangguo, C. 2018. ‘Panda poop paper’ – win-win for recycling. Energy Conservation & Environmental Protection 01:46–47.