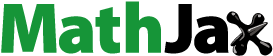
ABSTRACT
Fiber reinforcement is the most common method for modifying polylactic acid (PLA). However, poor compatibility between fibers and PLA, especially at high cellulose contents, can promote cellulose agglomeration in the continuous phase, which damages the mechanical properties of composite materials. To address these issues, bagasse cellulose (BC) was used as a substrate and bifunctional glycidyl methacrylate (GMA) was used as a reactive monomer for graft modification. GMA-modified BC (BC-GMA)/PLA composite materials with different particle sizes were prepared using a blending grafting method, and the influence of the type and content of BC-GMA on the mechanical properties of the composite materials was explored. During the grafting modification of BC, a longer reaction time was found to result in smaller BC particles and a higher degree of grafting. For BC-GMA, the degree of grafting reached 27.02% with a maximum thermal decomposition temperature of 359.31°C. Furthermore, the BC-GMA/PLA composite material had a greater relative crystallinity of PLA, indicating that BC-GMA was evenly dispersed in the continuous phase. This study demonstrates that grafting modification can successfully achieve high cellulose loading in composite materials and thus reduce the production costs of PLA-based packaging materials.
GRAPHICAL ABSTRACT
摘要
纤维增强是改性聚乳酸(PLA)最常用的方法. 然而,纤维与PLA之间的相容性差,特别是在高纤维素含量下,会促进纤维素在连续相中的团聚,从而损害复合材料的机械性能. 为了解决这些问题,甘蔗渣纤维素(BC)被用作基材,双官能甲基丙烯酸缩水甘油酯(GMA)被用作接枝改性的反应性单体. 采用共混接枝法制备了不同粒径的GMA改性BC(BC-GMA)/PLA复合材料,并探讨了BC-GMA的类型和含量对复合材料力学性能的影响. 在BC的接枝改性过程中,发现反应时间越长,BC颗粒越小,接枝程度越高. 对于BC-GMA,接枝率达到27.02%,最高热分解温度为359.31°C. 此外,BC-GMA/PLA复合材料具有更大的PLA相对结晶度,表明BC-GMA在连续相中均匀分散. 这项研究表明,接枝改性可以成功地在复合材料中实现高纤维素负载,从而降低PLA基包装材料的生产成本.
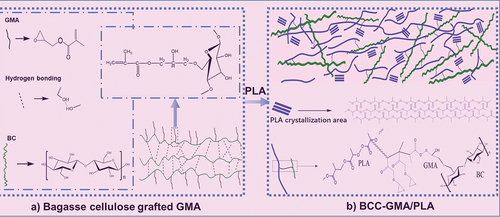
Introduction
Fused deposition modeling (FDM) is a novel material processing method in 3D printing technology (Meng et al. Citation2017;Ngo et al. Citation2018;Patra and Young Citation2016). This rapid prototyping technology is based on the principles of layered processing and layer-by-layer superposition. Polylactic acid (PLA) is widely used in the field of FDM 3D printing because of its good biocompatibility (Liu, Zhang, and Wang Citation2014;Saeidlou et al. Citation2012), biodegradability, small shrinkage, and low warpage (Fernández-Cervantes et al. Citation2019;Haneef et al. Citation2019;Morão and de Bie Citation2019). Nevertheless, PLA has various disadvantages, such as poor toughness, low thermal stability, and poor crystallinity, which limit its application in biomedicine and high-temperature-resistant materials. To overcome these issues, PLA is usually modified by chemical, physical, or surface modification. PLA is obtained by chemical synthesis from crop products, such as corn starch. Based on the underlying principle, PLA synthesis methods can be divided into two categories: direct polymerization (Rahmayetty, Prasetya, and Gozan Citation2017;Yoo, Kim, and Lee Citation2006) and ring-opening polymerization (Li et al. Citation2020;Zhang and Zhang Citation2010). Wang et al. prepared Bi0·5Sb1·5Te3 (BST)/PLA composites with different BST loading rates using the extrusion method (Wang et al. Citation2018). The BST filler, a coupling agent (KH570), and a plasticizer (acetyltributylcitrate) were uniformly dispersed in PLA to obtain a composite with good thermoelectric and mechanical properties. Maurel et al. used graphite/PLA to form filaments and employed FDM to print a negative electrode for a lithium battery (Maurel et al. Citation2018). In addition, carbon black and carbon nanofibers have been used as conductive additives to study the effects of temperature on the electrical conductivity of PLA composites.
Cellulose is a linear polymer composed of D-glucose groups (Selvendran Citation1987), each of which is connected by 1,4-β-glycosidic bonds. Furthermore, glucose units C2 and C3 are connected to a secondary hydroxyl group, whereas C6 is connected to a primary hydroxyl group. Owing to the presence of hydroxyl (-OH) groups, the interactions between the adjacent cellulose molecules in the cellulose fibers are relatively stronger. These groups extend from the chain to form molecular hydrogen bonds (Klemm et al. Citation2005). Therefore, cellulose has a stable structure, is highly rigid, and exhibits high performance. However, because of its closed structure, hydrogen bonds are formed between the molecules. As a result, cellulose does not dissolve in water or most organic solvents. At the same time, the poor thermoplasticity of cellulose results in molding and processing difficulties, which, in turn, limit its applicability. Studies have shown that (Rozman, Saad, and Ishak Citation2003), in the presence of peroxides, maleic anhydride (MAH)-treated oil palm silk (empty fruit bunch) and the polypropylene matrix are compounded when melted together because of the grafting reaction between the MAH double bond and the polypropylene chain. This results in significant improvements in the mechanical properties; however, a higher fiber loading rate reduces the performance of the three-dimensional printed part. Modifying plastics with natural fibers to enhance the performance of the plastic matrix and reduce the cost, thereby replacing glass and other synthetic materials (Wambua, Ivens, and Verpoest Citation2003), is a hot topic of research. However, because of the poor compatibility of natural fibers with the polymer matrix and the tendency of cellulose to readily undergo agglomeration, it shows low dispersibility in the polymer matrix, which leads to cellulose/polymer composites exhibiting poor mechanical properties (Pracella et al. Citation2006). The modification of the fiber surfaces with a multifunctional monomer can induce a secondary reaction with the polymer matrix, thereby resulting in the formation of a stable bonding network between the fibers and the polymer. Glycidyl methacrylate (GMA) has attracted significant industrial interest as a monomer containing two functional groups. Such monomers are highly applicable as precursors of functionalized polymers, in which only one group is polymerized (Cardil et al. Citation2022). The epoxy groups can react with many other groups such as hydroxyl and carboxylic acid, while acrylic groups have the ability to graft GMA radicals to polymer chains (Wang, Zhang, and Weng Citation2021). The epoxy groups can react with many other groups, such as hydroxyl and carboxy, and the acrylic groups can graft the GMA radicals onto the polymer chains. GMA-functionalized compatibilizers are being widely used as interfacial modifiers of blends prepared using commercial polymers (e.g., PS, PP, and PE) as well as biopolymers (e.g., PLA, PCL, and PHB) (de Souza Morais et al. Citation2022). Cellulose–poly(GMA) (CPGMA) graft copolymers, which act as intermediates in many synthesis processes, can be directly used or further functionalized through ring opening, thus providing wider application in composite materials, adsorbent materials, drug release, and other functional materials (Pracella et al. Citation2006). A green and effective method for the preparation of CPGMA is vitally important (Guo et al. Citation2020)
In this study, bagasse cellulose (BC) was used as a raw material, PLA as a substrate, and glycidyl methacrylate (GMA) as a reaction monomer. The grafting modification of BC by GMA improved the loading rate of cellulose and reduced the use of PLA, so as to decrease the production cost of composite materials. When a large amount of cellulose is used, the cellulose is more likely to agglomerate in the continuous phase and degrade, the mechanical properties of the composite. However, the GMA-modified BC would weaken the interaction between numerous hydroxyl groups on the cellulose surface and the interface of the composite. Therefore, the mechanical properties (Jamaluddin et al. Citation2021;Lee, Park, and Kim Citation2020;Wu and Chen Citation2020) of the composites can be improved by achieving better compatibility between the two (Jamaluddin et al. Citation2021;Khan et al. Citation2018). The GMA-modified BC (BC-GMA) was effectively wrapped with PLA macromolecules and evenly dispersed in the PLA matrix, which improved the mechanical properties of the composite material. This low-cost BC-GMA/PLA composite exhibited excellent performance. Thus, this work is expected to provide practical guidance for the field of 3D printing materials and PLA-based packaging materials.
Materials and methods
Materials used
Bagasse was supplied by Guangxi Guitang (Group) Co. Ltd., China. Polylactic acid was purchased from Youli (Suzhou) Technology Material Co. Ltd., China. Glycidyl methacrylate (GMA) was obtained from Shanghai Aladdin Industrial Company, China. Acetone was purchased from Sinopharm Chemical Reagent Co. Ltd., China. Triethylamine (TEA) was purchased from Chongqing Chuandong Chemical (Group) Co. Ltd., China, and a 30% hydrogen peroxide solution was supplied by Tianjin Zhiyuan Chemical Reagent Co. Ltd., China. All the other reagents used were of analytical grade.
Sample preparation
Graft modification of BC
To accurately determine the sizes of the different BC samples(see supplementary materials for pretreatment and composition analysis of bagasse fibers, the solid–liquid ratio was set to 1:5 and the samples were added to a mixed solution of GMA and TEA (3:7, v/v). To prevent the free radical polymerization of GMA during the reaction, hydroquinone (2% of the mass of GMA) was added to the mixture (Rozman et al. Citation1997). The reaction was performed at 90°C for 1–4 h to obtain the grafted product, which was washed with acetone thrice. Finally, Soxhlet extraction was performed for 4 h to remove the residual solvent and the unreacted reagents and allow for the homopolymerization of GMA. The obtained product was kept in a vacuum drying oven at 60°C for 2 h until its weight stabilized. The samples obtained were labeled BC-GMA (i.e., BCA-GMA, BCB-GMA, and BCC-GMA).
Preparation of BC-GMA/PLA composite
BC-GMA and PLA were placed in a vacuum drying oven at 60°C for 2 h. They were then removed and sealed in a drying dish for later use. Next, BC-GMA and 3% tert-butyl peroxybenzoate (TBPB) were added to PLA. The mixture was stirred evenly and placed in a twin-screw mixing extruder, which was rotated at 30 rpm at approximately 165°C for a cyclic reaction for 4 min. The extrusion molding process yielded BC-GMA/PLA, which was sealed and stored for later use.
Testing and characterization
Material characterization
BC was also characterized by FT-IR (TENSOR II, Bruker, Germany). An X-ray photoelectron spectrometer was used to evaluate the modified BC samples. The surface microstructures of the graft-modified BC and BC-GMA/PLA binary composite samples were characterized using a SEM system (F16502, Phenom, the Netherlands). A thermogravimetric analyzer (Discovery TGA 55,, TA Instrument, USA) was used to analyze the thermal stability of the graft-modified BC and BC-GMA/PLA composite samples. An electronic universal material testing machine (INSTRON-3367, Instrom Company, USA) was used to evaluate the mechanical properties of the BC-GMA/PLA binary composite samples. An X-ray photoelectron spectrometer (ESCALAB 250×I+, Thermo Fisher Scientific, USA) was used to evaluate the modified BC samples. A differential scanning calorimeter(TA-25, TA Instruments, USA) was used to characterize the BC-GMA/PLA binary composite samples. A dynamic mechanical analyzer (DMA, 0850–00278, TA Instrument, USA) was used to characterize the BC-GMA/PLA binary composite samples. (See supplementary materials for specific test parameters)
Grafting rate
The extent of the graft modification reaction can be quantitatively analyzed based on the increase in the mass of cellulose after the reaction. The BC samples of different sizes were vacuum-dried at 60°C for 2 h, and 1 g of each BC sample was accurately weighed; the control error was 0.001 g. Next, the samples were heated at 90°C for 1, 2, 3, and 4 h and washed with acetone. After 4 h of extraction, the samples were placed in a vacuum drying oven at 60°C and dried for 2 h. Three samples were analyzed from each group, and the average value was calculated,
where WPG is the percentage increase in the mass (%), m0 is the mass of BC before the reaction (g), and m1 is the mass of BC after the reaction (g).
Results and discussion
FT-IR analysis
compares the FT-IR spectra of bagasse before and after pretreatment. The absorption peak at 3650–600 cm−1 is related to the stretching vibrations of O – H bonds, whereas that at 3000–800 cm−1 is related to the stretching vibrations of methyl and methylene groups. The peaks at 1603, 1513, and 461 cm−1 are ascribable to the vibrations of the benzene ring skeleton of lignin (Zhu, Zhu, and Wu Citation2012). The peak at 252 cm−1 is caused by the vibrations of the C–O–C structure in guaiac lignin (Khan, Ashraf, and Malhotra Citation2004), and that at 34 cm−1 is caused by the vibrations of the C – H bonds in lignin. Moreover, the absorption peak at 736 cm−1 is related to the stretching vibrations of the polyxylose carbonyl groups of hemicellulose, whereas those at approximately 897, 1160, and 890 cm−1 are characteristic of cellulose (Zhang et al. Citation2019). After the pretreatment, the absorption peaks related to lignin weakened and that at 736 cm−1 disappeared, indicating that the contents of lignin and hemicellulose in bagasse greatly decreased while the proportion of cellulose significantly increased. After BC was grafted with GMA, new absorption peaks appeared at approximately 1720 and 14 cm−1, which are related to the stretching vibrations of C=O bonds and the vibrations of epoxy groups (Du Citation2018). The characteristic peak at 634 cm−1 can be ascribed to the stretching vibrations of C=C bonds in GMA, indicating that GMA was successfully grafted onto BC (the mechanism is shown in). XPS also confirmed the same results (see Fig. S-1 and Fig. S-2).
shows that, for the same fiber size, the degree of grafting of GMA onto BC-GMA increased with the reaction time (Abdelwahab and Shukry Citation2015;Sharif et al. Citation2013;Tyagi, Tomar, and Singh Citation2009). This is because a longer reaction time increased the contact time between GMA and BC, thus enhancing the strength of the reaction. In addition, for the same reaction time, the degree of grafting of small-sized BC (BCC) was greater than those of the large-sized BC samples (BCA and BCB). For reaction times of 1–2 h, the grafting degrees of BCA-GMA and BCB-GMA were similar. Finally, the grafting degree of BCC-GMA was as high as 27.02% for a reaction time of 4 h. These results suggest that the degree of cellulose grafting is affected by the reaction time and cellulose fiber size (see Fig. S-3). The larger the specific surface area of cellulose, the greater the number of hydroxyl groups exposed. Hence, the epoxy groups of GMA are more likely to undergo ring-opening reactions, resulting in an increased reaction strength. In the same manner, an increase in the reaction time also increased the degree of grafting of BC onto GMA.
TGA analysis
As shown in, the thermal degradation process of the samples can be divided into three stages. The temperature corresponding to 5% weight loss (T95%), 10% weight loss (T90%) and the temperature at the maximum degradation rate (Tmax). In the first stage, at temperatures lower than 163.71°C, the weight loss of the samples is mainly caused by the evaporation of internal moisture. The second stage of weight loss in the temperature range of 163.71–387.12°C is related to the thermal degradation of the samples. BF undergoes chemical and physical processes such as decomposition, depolymerization, oxidation, and hydrolysis. In the final (third) stage of weight loss at temperatures higher than 387.12°C, cellulose is gradually carbonized, and the mass loss is small. The onset of BF is 187.81°C. At this temperature, BF undergoes preliminary thermal degradation, and its mass starts to decrease. From 247.51°C onward, the mass of BF decreases rapidly. The T50% of BF is 301.73°C. At this temperature, the sample undergoes obvious quality loss, indicating that the main components in BF have begun to decompose. In the third weight loss stage of BF (Tmax = 340.27°C), the mass loss rate is the highest. BF also shows weight loss peaks in its DTG curve, indicating that BF contains a variety of substances. However, the mass of BF does not decrease at temperatures higher than 631.52°C, and the mass residual rate is 2.10%. The onset of BC is 219.68°C, and its mass begins to reduce rapidly from 278.60°C onward. For BC, T50% is 340.48°C and Tmax is 343.75°C. When BC is heated to 559.39°C or higher, no further decrease in mass occurs and the mass residual rate is 3.61%. The DTG curve of BF shows two weight loss peaks (at 302.73 and 340.27°C), whereas that of BC after the pretreatment has a single peak (at 343.75°C). The decomposition temperature of hemicellulose is 302.73°C (Yang et al. Citation2020). Moreover, the decomposition of lignin occurs throughout the thermal decomposition process. The pretreatment slightly increases the thermal decomposition temperature of cellulose because hemicellulose is amorphous, and the thermal decomposition temperature of hemicellulose is lower than that of cellulose. After the removal of a large amount of hemicellulose, the crystallinity of BC increases and its thermal stability improves. The main component of BC obtained after the alkali treatment of BF is cellulose (see Table S-1). The initial decomposition temperature of BCC-GMA is 202.42°C, and its maximum decomposition temperature is 359.31°C. After BCC is modified with GMA, its thermal stability improves. This may be because the surface of BC is wrapped with GMA, and the ring opening of the epoxy groups of GMA results in reactions with the –OH groups, leading to the formation of new –OH groups. The epoxy groups continue to react with the –OH groups. In addition, hydrogen bond formation between the hydroxyl groups hinders the thermal movement of the BC-GMA molecular chains, thus increasing the thermal decomposition temperature. The thermal decomposition temperature of PLA is 206.56°C, and the Tmax of PLA is 359.46°C. The T5%, T50%, and Tmax of the 30% BCC-GMA/PLA composite are 329.41, 356.45, and 358.31°C, respectively. The increase of temperature at the maximum thermal degradation rate of the composite is because the addition of BCC-GMA induces the crystallization of the PLA phase in the blend system, which will hinder the thermal movement of the PLA molecular chain and increase the energy required for the thermal decomposition of PLA, so the thermal stability of the composite is improved (Han et al. Citation2019;Wang, Zeng, and Li Citation2011). Further, DSC and DMA tests were carried out to analyze the Tg, Xc, storage modulus and loss factor of the material (see Fig. S-4 and Fig. S-5). In general, compared with unmodified fibers, graft copolymerization reduces the thermal stability and broadens the decomposition window (Guo et al. Citation2020).
SEM analysis
As shown in , the surfaces of BF are covered by many impurities, as are the cellulose fibers. Moreover, the sample surface is very rough and consists of many fragments, which were probably formed as the cell wall structure was destroyed by the mechanical force of the pulverizer. After the alkali treatment and bleaching, the impurities that originally wrapped the cellulose disappeared, and the cellulose was fully exposed. It can be seen from that BC has a “striped” appearance and that the stripes are arranged in a crisscross pattern (Pracella et al. Citation2006). shows that the surface of BCC is relatively rough, consisting of “dulls and verticals,” with many small fragments attached. These features were formed by the shredding of the fine cellulose through the combined action of the alkali treatment and mechanical force. shows that the surface of BCC-GMA is covered by an “oily” substance. In addition, the entire surface is smooth, and the previously observed “gullies” are completely filled. Moreover, there is adhesion between the cellulose fibers. This is because the cellulose is grafted with GMA, which reduces the polarity of the cellulose. As a result, the intermolecular hydrogen bonds are weakened, and the hydroxyl groups of cellulose are replaced by GMA. Thus, the compatibility between cellulose fibers has been improved, which is consistent with the results reported by Pracella (Pracella et al. Citation2006). The partial magnified image of BCC-GMA in the upper right corner of clearly shows the apparent morphology of BCC modified by GMA. When 10% BCC-GMA was added (), it was distributed widely in the PLA matrix because the cellulose content was low and all the cellulose could be completely wrapped with PLA. However, a few holes can be observed in the sample. These holes are due to delamination, which occurs when the material breaks. With an increase in the BCC-GMA content, the amount of pores formed upon fracture of the composite material gradually increased. When the BCC-GMA content was 30%, the number of pores increased, and the BCC-GMA fibers were broken or pulled out perpendicular to the stretching direction (). In addition, as shown in, when the BCC-GMA content was 50%, BCC-GMA and PLA exhibited a certain degree of phase separation. The use of excessive BCC-GMA can cause agglomeration, leading to stress concentration during stretching and tensile strength measurements of the composite material (), which could decrease the stretching performance.
Tensile properties analysis
Overall, as the fiber size of BC-GMA decreases, the tensile strength of the BC-GMA/PLA composites gradually increases and the elastic modulus gradually decreases (). The tensile strength, elastic modulus, and elongation at break of 10% BCB/PLA are 37.82 MPa, 2287.91 MPa, and 2.23%, respectively. In contrast, for 10% BCA-GMA/PLA and 10% BCB-GMA/PLA, the tensile strength and elongation at break are significantly higher, whereas the elastic modulus is slightly reduced. shows that when the amount of BCC-GMA added is 10%, the tensile strength of the composite material is 43.94 MPa, the elastic modulus is 2000.89 MPa, and the elongation at break is 4.03%. However, when the amount of BCC-GMA added is increased to 50%, the tensile strength is slightly elevated to 45.12 MPa, the modulus of elasticity increases to 3233.29 MPa, and the elongation at break decreases significantly to 1.93% (Wang Citation2012). This is because, on the one hand, PLA can combine with the primary free radicals generated by TBPB in the molten state to form a PLA macroinitiator and react with the long chains of the BCC-GMA macromolecules in the molten state. During melt mixing, the epoxy group in BC-GMA reacts with the hydroxyl group of BC, and the other end reacts with the carboxyl group of PLA (Han et al. Citation2021;Robledo-Ortíz et al. Citation2021) Consequentiy, BC-GMA strengthens the linkage between BC and PLA, which improves the compatibility between BCC-GMA and PLA (see for the reaction mechanism). On the other hand, GMA wraps BC and forms a “shell–core” structure in the PLA matrix. In other words, GMA shows strong adhesion to BC. The contact area between the GMA in the outer layer and the base PLA increases, thus increasing the compatibility with PLA. When the material is subjected to an external force, the resulting stress is transferred along the PLA molecular chain to the wrapped BC. As a result, the material shows increased toughness. As the content of BCC-GMA is increased, the concentration of BCC-GMA in the system increases. In the later stage of the reaction, owing to steric hindrance, the free space for the movement of the PLA and BCC macromolecular chains is limited. Hence, the probability of effective collisions is greatly reduced, and the reaction cannot proceed readily. The molecular chains of BCC-GMA may become entangled and agglomerate with each other, which would have an adverse effect on the tensile properties of the composite material. Therefore, the use of excessive BCC-GMA decreases the tensile performance of the composite material.
3D printing physical image
FDM printing has advantages for manufacturing multi-functional 3D printing parts, while PLA cannot meet the requirements for 3D printing consumables in some fields due to its poor toughness. Therefore, it is a trend for the future development of FDM to increase the toughness of modified PLA. In this paper, BC was grafted to improve the mechanical properties of the composites by increasing the compatibility of BC and PLA. BCC-GMA/PLA composite was prepared into a 3D printing filament with a diameter of 1.5 mm, and the blended filament was printed into flowers, Chinese knots, whistles, Yuantong, filter channels, hubs and bearings, respectively, with an FDM printer, as shown in . The surface of the printed matter is smooth without warping. BCC-GMA/PLA composites are expected to be widely used in 3D field.
Conclusion
In this study, the pretreatment of BF with sodium hydroxide solution and hydrogen peroxide solution to obtain BC increased the cellulose content from 45.46% to 82.16%. FTIR and XPS analyses confirmed the successful formation of the grafted product BC-GMA through the ring-opening polymerization reaction of the epoxy groups in GMA with the hydroxyl groups in BC. The graft rate of BC-GMA depended on both the reaction time and the BC particle size. The longer the reaction time resulted in smaller BC particles, the higher the degree of reaction is. The effects of different types of BC-GMA and the BCC-GMA content on the properties of BC-GMA/PLA composites were investigated. BC-GMA formed macromolecular chains with PLA under the action of the initiator, which acted as lubricants in the system and promoted the crystallization of PLA. Thus, the relative crystallinity of PLA in the BC-GMA/PLA composites was relatively high. Thus, thermal stability of the composites was improved.
Highlights
Using GMA to graft bagasse cellulose to improve the compatibility between polylactic acid composites and fibers
The BC-GMA/PLA composite material was prepared using the principle of blending and grafting reaction
The mechanical properties of BC-GMA/PLA composites are much greater than the original composites without compatibilization and modification
Author statement
Yanan Wang contributed to conceptualization, writing-review and wditing, writing-original draft, and project administration; Hao Xu contributed to investigation, software, investigation, funding acquisition, and supervision; Lijie Huang contributed to methodology, formal analysis, and visualization; Zhehao Wei contributed to validation; Xiaoxue Hancontributed to validation; QI Mo contributed to software; Xiyue Wang contributed to formal analysis and investigation; Yishan Li contributed to formal analysis;
Supplemental Material
Download MS Word (48.7 KB)Acknowledgment
The work was supported by the Guangxi Natural Science Foundation under Grant [Grant No. GXNSFAA297042], Guangxi Bossco Environmental Protection Technology (Bossco) under Grant [No.AA17129006], and Guangxi Key Laboratory of Clean Pulp & Papermaking and Pollution Control under Grant [2021KF53].
Disclosure statement
No potential conflict of interest was reported by the authors.
Supplementary material
Supplemental data for this article can be accessed online at https://doi.org/10.1080/15440478.2022.2164822
Additional information
Funding
References
- Abdelwahab, N. A., and N. Shukry. 2015. Synthesis, characterization and antimicrobial properties of grafted sugarcane bagasse/silver nanocomposites. Carbohydrate Polymers 115:276–14. doi:10.1016/j.carbpol.2014.08.052.
- Cardil, A., M. Palenzuela, J. F. Vega, and M. E. G. Mosquera. 2022. Rheology of poly(glycidyl methacrylate) macromolecular nano assemblies. Polymers 14 (3):455. doi:10.3390/polym14030455.
- de Souza Morais, D. D., C. B. Luna, E. B. Bezerra, D. C. de França, E. M. Araújo, E. P. Do Nascimento, A. D. de Oliveira, and T. J. de Mélo. 2022. Performance of poly(caprolactone) (pcl) as an impact modifier for polystyrene (ps): Effect of functionalized compatibilizers with maleic anhydride and glycidyl methacrylate. Sustainability 14 (15):9254. doi:10.3390/su14159254.
- Du, S. 2018. Study on the synthesis and separation of glycidyl methacrylate. M.D diss., Tianjing University.
- Fernández-Cervantes, I., M. A. Morales, R. Agustín-Serrano, M. Cardenas-García, P. V. Pérez-Luna, B. L. Arroyo-Reyes, and A. Maldonado-García. 2019. Polylactic acid/sodium alginate/hydroxyapatite composite scaffolds with trabecular tissue morphology designed by a bone remodeling model using 3d printing. Journal of Materials Science 54 (13):9478–96. doi:10.1007/s10853-019-03537-1.
- Guo, L., A. Meng, L. Wang, J. Huang, X. Wang, H. Ren, H. Zhai, and M. Ek. 2020. Improving the compatibility, surface strength, and dimensional stability of cellulosic fibers using glycidyl methacrylate grafting. Journal of Materials Science 55 (27):12906–20. doi:10.1007/s10853-020-04932-9.
- Han, S., Y. Li, M. He, and G. Tian. 2019. Advances in heat-resistant modification of poly(lactic acid)-based composites. Engineering Plastics Applications 47 (04):143–47. doi:10.1080/14658011.2018.1447338.
- Han, X., L. Huang, Z. Wei, Y. Wang, H. Chen, C. Huang, and S. Su. 2021. Technology and mechanism of enhanced compatibilization of polylactic acid-grafted glycidyl methacrylate. Industrial Crops and Products 172:114065. doi:10.1016/j.indcrop.2021.114065.
- Haneef, I. N. H. M., Y. F. Buys, N. M. Shaffiar, S. I. S. Shaharuddin, and M. K. Nor Khairusshima. 2019. Miscibility, mechanical, and thermal properties of polylactic acid/polypropylene carbonate (pla/ppc) blends prepared by melt-mixing method. Materials Today: Proceedings 17:534–42. doi:10.1016/j.matpr.2019.06.332.
- Jamaluddin, N., Y. I. Hsu, T. A. Asoh, and H. Uyama. 2021. Effects of acid-anhydride-modified cellulose nanofiber on poly(lactic acid) composite films. Nanomaterials 11 (3):3. doi:10.3390/nano11030753.
- Khan, B. A., H. Na, V. Chevali, P. Warner, J. Zhu, and H. Wang. 2018. Glycidyl methacrylate-compatibilized poly(lactic acid)/hemp hurd biocomposites: Processing, crystallization, and thermo-mechanical response. Journal of Materials Science & Technology 34 (2):387–97. doi:10.1016/j.jmst.2017.03.004.
- Khan, M. A., S. M. Ashraf, and V. P. Malhotra. 2004. Development and characterization of a wood adhesive using bagasse lignin. International Journal of Adhesion and Adhesives 24 (6):485–93. doi:10.1016/j.ijadhadh.2004.01.003.
- Klemm, D., B. Heublein, H. P. Fink, and A. Bohn. 2005. Cellulose: Fascinating biopolymer and sustainable raw material. Angewandte Chemie-International Edition 44 (22):3358–93. doi:10.1002/anie.200460587.
- Lee, J. H., S. H. Park, and S. H. Kim. 2020. Surface alkylation of cellulose nanocrystals to enhance their compatibility with polylactide. Polymers 12 (1):1. doi:10.3390/polym12010178.
- Li, G., M. Zhao, F. Xu, B. Yang, X. Li, X. Meng, L. Teng, F. Sun, and Y. Li. 2020. Synthesis and biological application of polylactic acid. Molecules 25 (21):5023. doi:10.3390/molecules25215023.
- Liu, G., X. Zhang, and D. Wang. 2014. Tailoring crystallization: Towards high-performance poly(lactic acid). Advanced Materials 26 (40):6905–11. doi:10.1002/adma.201305413.
- Maurel, A., M. Courty, B. Fleutot, H. Tortajada, K. Prashantha, M. Armand, S. Grugeon, S. Panier, and L. Dupont. 2018. Highly loaded graphite-polylactic acid composite-based filaments for lithium-ion battery three-dimensional printing. Chemistry of Materials 30 (21):7484–93. doi:10.1021/acs.chemmater.8b02062.
- Meng, S., H. He, Y. Jia, P. Yu, B. Huang, and J. Chen. 2017. Effect of nanoparticles on the mechanical properties of acrylonitrile–butadiene–styrene specimens fabricated by fused deposition modeling. Journal of Applied Polymer Science 134 (7):7. doi:10.1002/app.44470.
- Morão, A., and F. de Bie. 2019. Life cycle impact assessment of polylactic acid (pla) produced from sugarcane in thailand. Journal of Polymers and the Environment 27 (11):2523–39. doi:10.1007/s10924-019-01525-9.
- Ngo, T. D., A. Kashani, G. Imbalzano, K. T. Q. Nguyen, and D. Hui. 2018. Additive manufacturing (3d printing): A review of materials, methods, applications and challenges. Composites Part B: Engineering 143:172–96. doi:10.1016/j.compositesb.2018.02.012.
- Patra, S., and V. Young. 2016. A review of 3d printing techniques and the future in biofabrication of bioprinted tissue. Cell Biochemistry and Biophysics 74 (2):93–98. doi:10.1007/s12013-016-0730-0.
- Pracella, M., D. Chionna, I. Anguillesi, Z. Kulinski, and E. Piorkowska. 2006. Functionalization, compatibilization and properties of polypropylene composites with hemp fibres. Composites Science and Technology 66 (13):2218–30. doi:10.1016/j.compscitech.2005.12.006.
- Rahmayetty, S., B. Prasetya, and M. Gozan. 2017. Synthesis and characterization of l-lactide and polylactic acid (pla) from l-lactic acid for biomedical applications. In Biomedical engineering’s recent progress in biomaterials, drugs development, and medical devices, vol 1817. Aip conference proceedings, ed. Y. Whulanza, S. Supriadi, and M. Sahlan. February 21. doi:10.1063/1.4976761.
- Robledo-Ortíz, J., M. González-López, A. Campo, L. Peponi, R. González-Nuez, D. Rodrigue, and A. Pérez-Fonseca. 2021. Fiber-matrix interface improvement via glycidyl methacrylate compatibilization for rotomolded poly(lactic acid)/agave fiber biocomposites. Journal of Composite Materials 55 (2):201–12. doi:10.1177/0021998320946821.
- Rozman, H. D., R. N. Kumar, H. Khalil, A. Abusamah, R. Abu, and H. Ismail. 1997. Fibre activation with glycidyl methacrylate and subsequent copolymerization with diallyl phthalate. European Polymer Journal 33 (8):1213–18. doi:10.1016/s0014-3057(97)00008-6.
- Rozman, H. D., M. J. Saad, and Z. A. M. Ishak. 2003. Flexural and impact properties of oil palm empty fruit bunch (efb)-polypropylene composites - the effect of maleic anhydride chemical modification of efb. Polymer Testing 22 (3):335–41. doi:10.1016/s0142-9418(02)00109-5.
- Saeidlou, S., M. A. Huneault, H. Li, and C. B. Park. 2012. Poly(lactic acid) crystallization. Progress in Polymer Science 37 (12):1657–77. doi:10.1016/j.progpolymsci.2012.07.005.
- Selvendran, R. R. 1987. Chemistry of plant cell walls and dietary fibre. Scandinavian Journal of Gastroenterology Supplement 22 (Sup129):33–41. doi:10.3109/00365528709095848.
- Sharif, J., S. F. Mohamad, N. A. Fatimah Othman, N. A. Bakaruddin, H. N. Osman, and O. Güven. 2013. Graft copolymerization of glycidyl methacrylate onto delignified kenaf fibers through pre-irradiation technique. Radiation Physics and Chemistry 91:125–31. doi:10.1016/j.radphyschem.2013.05.035.
- Tyagi, C., L. K. Tomar, and H. Singh. 2009. Surface modification of cellulose filter paper by glycidyl methacrylate grafting for biomolecule immobilization: Influence of grafting parameters and urease immobilization. Journal of Applied Polymer Science 111 (3):1381–90. doi:10.1002/app.28933.
- Wambua, P., J. Ivens, and I. Verpoest. 2003. Natural fibres: Can they replace glass in fibre reinforced plastics? Composites Science and Technology 63 (9):1259–64. doi:10.1016/s0266-3538(03)00096-4.
- Wang, B. Y. 2012. Research on interface modification technology and performance of wood- plastic composites. M. D. diss., Hangzhou Normal University.
- Wang, J., H. Li, R. Liu, L. Li, Y. H. Lin, and C. W. Nan. 2018. Thermoelectric and mechanical properties of pla/bi0.5sb1.5te3 composite wires used for 3d printing. Composites Science and Technology 157:1–9. doi:10.1016/j.compscitech.2018.01.013.
- Wang, L., Z. Zeng, and Y. Li. 2011. Green synthesis, characterization and thermal degradation kinetics analysis of pla/mmt-htcc nanocomposites. China Plastics 25 (06):42–48. doi:10.19491/j.issn.1001-9278.2011.06.009.
- Wang, N., C. Zhang, and Y. Weng. 2021. Enhancing gas barrier performance of polylactic acid/lignin composite films through cooperative effect of compatibilization and nucleation. Journal of Applied Polymer Science 138 (15):50199. doi:10.1002/app.50199.
- Wu, W., and F. Chen. 2020. Coupling agent-modified corn stalk cellulose/used rubber powder composites. Journal of Rubber Research 23 (3):237–43. doi:10.1007/s42464-020-00053-9.
- Yang, H., Q. Chen, H. Zhao, H. Gu, J. Yan, and H. Lin. 2020. Study on preparation and performance of bagasse hollow cellulose membrane. Biomass Chemical Engineering 54 (02):6–14. doi:10.1016/j.ceramint.2018.07.063.
- Yoo, D. K., D. Kim, and D. S. Lee. 2006. Synthesis of lactide from oligomeric pla: Effects of temperature, pressure, and catalyst. Macromolecular Research 14 (5):510–16. doi:10.1007/bf03218717.
- Zhang, L., J. Liu, Y. You, Y. Liu, X. Sun, X. Tan, X. Pei, X. Luo, and Q. Li. 2019. Study on preparation of super absorbent resin from bagasse fiber. Journal of Sichuan University Natural Science Edition 56 (3):523–30.
- Zhang, N., and J. Zhang. 2010. Recent progress in study of biomacromolecular material polylactic. Journal of Hebei Polytechnic University 32 (03):116–20.
- Zhu, Z., M. Zhu, and Z. Wu. 2012. Pretreatment of sugarcane bagasse with nh4oh-h2o2 and ionic liquid for efficient hydrolysis and bioethanol production. Bioresource Technology 119:199–207. doi:10.1016/j.biortech.2012.05.111.