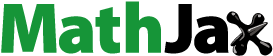
ABSTRACT
This study focuses on the determination of the mechanical characteristics of composites under static and dynamic conditions. The composites are prepared by reinforcing with 3 mm, 7 mm, and 10 mm short-treated coconut tree primary flower leaf stalk fiber (CPFLSF) in the polymer matrix. The 3 mm untreated CPFLSF composite (3UTCPFLSFC) reveals the lowest tensile, flexural, and impact properties, whereas 7 mm Alkali-Treated CPFLSF Composite (7ATCPFLSFC) indicate the maximum tensile strength of 34.31 MPa, tensile modulus of 1.81 GPa, flexural strength of 58.43 MPa, flexural modulus of 3.23 GPa, and impact strength of 8.25 kJ/m2. Dynamic mechanical analysis (DMA) reveals that the 7ATCPFLSFC had enhanced loss and storage modulus compared to untreated and other alkali-treated CPFLSF composites. The maximum decomposition is obtained for 7ATCPFLSFC in the region of 550°C temperature with a residual mass of 18% compared to other compositions. From the water absorption test, it was observed that, when increasing the soaking time of the composites, water intake properties gradually increased in the composite. However, the 7ATCPFLSFC absorbed water, compared to the other composites. A scanning electron microscope confirms better bonding in the composite, fracture of fiber, pull-out, fiber shearing, and tearing in the treated and untreated composites.
HIGHLIGHTS OF RESEARCH
This research work reduces the environmental impact of the processing and use of natural fibers.
Achieve the same performance in light load applications; the content of natural fiber should be higher than that of glass fiber.
This requires a reduction in resin content, leading to a significant reduction in the environmental pollution caused by the polymer. The low density of natural fibers improves efficiency. Therefore, less pollutants are emitted while driving in automotive applications.
At the end of the life of natural fibers, their burning produces energy and carbon. However, the use of fertilizers for the growth of natural fibers can result in higher nitrate and phosphate emissions. This is very dangerous for local water resources
摘要
这项研究的重点是确定复合材料在静态和动态条件下的力学特性. 通过在聚合物基质中用3 mm、7 mm和10 mm的短处理椰子树初级花叶茎纤维(CPFLSF)增强来制备复合材料. 3 mm未处理的CPFLSF复合材料(3UTCPFLSFC)显示出最低的拉伸、弯曲和冲击性能,而7 mm碱处理的CPFL复合材料(7ATCPFLSFC)显示出最大拉伸强度为34.31 MPa,拉伸模量为1.81GPa,弯曲强度为58.43MPa,弯曲模量为3.23GPa,冲击强度为8.25 kJ/m2. 动态力学分析(DMA)表明,与未经处理和其他碱处理的CPFLSF复合材料相比,7ATCPFLSFC具有增强的损耗和储能模量. 7ATCPFLSFC在550°C温度范围内获得最大分解,与其他成分相比,残余质量为18%. 从吸水试验中观察到,随着复合材料浸泡时间的增加,复合材料的吸水性能逐渐增加. 然而,与其他复合材料相比,7ATCPFLSFC吸收的水更少. 扫描电子显微镜证实,在处理和未处理的复合材料中,复合材料中的结合、纤维断裂、拔出、纤维剪切和撕裂更好.
Introduction
Due to rising demand, shortage of raw materials and a high energy price, manufacturing material costs have been growing day by day in the last several years. The use of alternative components in materials today constitutes a worldwide issue from the point of view of energy-saving and conservation of natural resources (Gurunathan, Mohanty, and Nayak Citation2015; Saheb and Jog Citation1999; Satyanarayana, Arizaga, and Wypych Citation2008). For the production of sustainable and environmentally friendly material, a worldwide concern needs considerable research and development effort to explore novel ingredients. To produce sustainable and environmentally sound materials, considerable research and development efforts to explore novel materials and components are necessary (Dahy Citation2019; Zhang, Rong, and Lu Citation2005). Sathishkumar, Navaneethakrishnan, and Shankar (Citation2012) investigated coir/snake grass fibers with varied volume fractions and the usage of stacking patterns in the composite with 25 volume percentage snake grass/coir fiber had maximum flexural strength of 110 MPa and a flexural modulus of 14 GPa were produced. Biswas, Kindo, and Patnaik (Citation2011) investigated the untreated and treated 5 mm, 20 mm, and 30 mm coconut coir fibers used as reinforcement materials in epoxy resin composites, which confirmed that 20 mm coconut coir fiber reinforced epoxy composites have better tensile strength (13.05 MPa), tensile modulus (2.064 GPa), flexural strength (35.42 MPa), and higher impact strength (17.5 kJ/m2). Mechanical properties were tested for fibers from various portions of the coconut palm, and the highest modulus and stress strength for the fibers derived from the petioles bark was 24.7GPa and 191.81MPa (Shanmugam and Thiruchitrambalam Citation2014). The tensile strength findings indicated that the tensile characteristics of coconut tree primary flower leaf stalk fiber (CPFLSF) treated with 6% NaOH were better in the 2008– 2653 MPa range. The work offers a way to produce a polymer matrix composite for the use of light load automobile applications also the alkali treatment and purification procedure improved the cellulose fibrillation process. Both methods have provided the CPFLSF with good tensile and young modules (Silva, Chawla, and de Toledo Filho Citation2008). Other than researchers started their investigation on some of the available lignocelluloses fibers such as Jute, Hemp, Flax, Ramie, Kenaf, Roselle, Mesta, Okra, Kudzu, Rattan, Wisteria, Coir, Kapok, African Oil Palm, Areca, Borassus, Sisal, Banana, Palf, Henequen, Agave, Raphia, Fique, Abaca, Palmyra palm-leaf stalk, Curious, Bamboo, Bagasse, Corn, Sabai, Rape, Esparto, and Canary as well and confirmed that the treated fiber had very good mechanical properties compared to the raw fiber. Due to the advantages, described above the use of fiber composites is finding many applications including aerospace, structure, sports, tools, food housing, maritime, sports, and automotive industries (Li, Tabil, and Panigrahi Citation2007; Mohammed et al. Citation2015; Saheb and Jog Citation1999). The idea of using plant waste (yard cutting) as reinforcement for composite materials was studied in this article and In terms of mechanical characteristics (tensile, flexural, and impact), it was discovered that the rise is more substantial with the inclusion of treated fillers, with tensile strength and modulus increasing by 30% and 34%, respectively, and flexural strength and modulus increasing by 18% and 33% (Shaker et al. Citation2020). 7% MCC particles are the optimal amount to improve the properties of the composite, and specific load increases of 48%, 52.14%, and 100% in tensile, flexural and toughness were observed in alkali-treated woven jute/epoxy composite, respectively (Rehman et al. Citation2019). Tensile testing of Vernonia fibers showed that the fibers had modulus and strength of 259.6 MPa and 37.75 GPa, respectively, which were superior to cotton, whereas sisal and thermogravimetric analysis showed that Vernonia fibers were showed thermal stability (Shaker et al. Citation2020). Sari et al. (Citation2021) reveal that UV exposure of corn husk fiber polyester composite of density, tensile, and flexural strength decreased compared to before UV exposure, due to the interfacial bond between the resin-corn husk fiber to be not being as much strong Syafri et al. (Citation2021) studied the Nano cellulose from Agave gigantea (AG) fiber treated with alkalization were increased the crystal index and cellulose content by 48.3% and 20.4% compared to raw AG fiber, due to this reason the tensile strength of fiber was improved. Sari et al. (Citation2017) confirmed that when the fiber was arranged in a conventional pattern the absorption coefficient is close to zero; however, the random pattern produced a high absorption coefficient compared to the conventional pattern. Herlina et al. (Citation2018) indicated that NaOH treatment improved the morphology, crystallinity size, cellulose, and thermal–mechanical properties of CHFs significantly. Alkali treatment with NaOH removes hemicellulose and lignin from the fibers, resulting in lower moisture content, more dominant cellulose content, higher crystallinity index, rougher fiber surface, fibrils, smaller lumen size inside the fiber bundles, and decreased fiber diameter. Karimah et al. (Citation2021) revealed the characteristic strands with enticing properties such as lower thickness, lighter weight, biodegradability, good particular quality and modulus, great thermal insulation, good acoustic insulation, and higher electrical resistance can be utilized for different applications such as automotive, building construction, and electronic industries.
Research has shown that not much work attempting to study the behavior of short reinforced CPFLSF polymer composites is found in the literature. This study focused on the static and dynamic mechanical, water, and thermal characteristics of the raw and alkali-treated CPFLSF reinforced polymer composites.
Materials and methods
Materials
The CPFLSF was obtained from the coconut tree leaf stalks (Cocosnucifera L). First, the primary stalks of the leaf were taken from the coconut tree, and thorns were removed and dipped into the water for 4 weeks. Then, a wooden hammer was pounded over the stems, and the fibers were removed from the stems. As indicated in , CPFLSF and extracted fibers were continuously washed, cleaned, and dried in the sunlight for 3 days (Silva, Chawla, and de Toledo Filho Citation2008). The fibers thus obtained are cut to the necessary length (3 mm, 7 mm, and 10 mm) by using a chisel. Chemicals for the production of composites such as unsaturated polyester resin, accelerator (cobalt naphthalene), and catalyst (methyl ethyl ketone peroxide) were purchased from Covai Seenu and Company Coimbatore, India (Belouadah, Rokbi, and Ati Citation2020).
Alkali treatment
The fibers were soaked in a 6% NaOH solution for 30 min. The alkali compounds were removed from the fibers by continually washing them in water. The fibers were cleaned several times with 3% (by weight) hydrochloric acid (HCl) to eliminate any excess moieties on the fiber surface, then washed with distilled water, and dried at room temperature for 2 days (Rehman et al. Citation2019). The cumulative time taken for the alkali treatment process was 45 min. Alkaline treatment modifies the surface of the fiber by removing a certain amount of lignin, hemicellulose, wax, and oil that line the outer surface of the natural fiber. Therefore, alkaline treatment increases the proportion of crystalline cellulose (Muruganrama et al. Citation2020).
Fabrication of CPFLSF reinforced polymer composite
Primarily die sets were cleaned and dried before applying the release agent (silicon). The matrix was prepared by mixing unsaturated polyester along with accelerator and catalyst. The weight percentage of fiber and matrix are set at 30:70 in the manufacturing of composite plates. The CPFLSF were randomly placed in the mold, and the matrix was poured inside the die set and compressed by applying a pressure of 1 ton by hydraulic compression and left for 12 h (Muruganrama et al. Citation2020). The composite plates were removed from the mold after 12 h and post-cured at room temperature (Shaker et al. Citation2020). After that specimens were cut from the composite plates as per ASTM standard and it is shown in .
Static mechanical properties of composites
An instron tensile tester was used to determine the tensile properties of the composites. ASTM: D638 standards was used to test the composites with a crosshead speed of 5 mm/min. Specimens of size 127 mm x 12.7 mm x 3 mm were prepared and then the flexural test for those specimens was conducted as per the ASTM D790–03 (Muruganrama et al. Citation2020), using a Kalpak Universal Testing Machine with a capacity of 20 kN and with a crosshead speed of 2 mm per minute. Composite specimens of size 64 mm x 13 mm x 3 mm and a notch were provided as per ASTM: D256 for impact testing (Rehman et al. Citation2019). In the impact tester, the specimens were fixed and impacted by the cantilever pendulum in a single swing at the notch. For each test, three specimens were tested, and average values were reported (Prades et al. Citation2012; Satyanarayana et al. Citation1982).
Water absorption of composites
The specimens for the water absorption test were cut, and the water absorption test was performed by ASTM D570–99 (Shaker et al. Citation2020) standards. Specimens of 64 mm x 12.7 mm x 3 mm were used for the tests. At regular intervals of time, the immersed specimens were taken out, and their weight was noted. The percentage of water absorption in the composites was calculated (Muruganrama et al. Citation2020).
Where WC = Water absorption of the composites, Wo= Wet weight of the composites, Wt= Initial dry weight of the sample after a specific interval of time in the water.
Dynamic mechanical analysis (DMA)
The DMA analysis was conducted using SII (Inkarp) DMS 6100 make. A frequency of 1 Hz and dual cantilever bending mode was used for the experiment. The specimen sizes of 50 mm x 50 mm x 3 mm were cut from the fabricated composite plates, and the test was conducted at room temperature. A heating rate of 2°C/min is used during the tests (Rehman et al. Citation2019).
Thermo gravimetric analysis (TGA)
The thermal stability of the composites was carried out using ASTM E1131 standard. Composite was analyzed by TGA/DTG using a Perkin Elmer machine in a temperature range of 50°C–750°C at a heating rate of 10°C/min and 20 ml/min nitrogen atmosphere (Rehman et al. Citation2019).
Scanning electron microscope (SEM)
SEM was carried out with SEM JEOL JSM 6390 SEM JEOL at a 10 KV accelerating voltage. After a tensile test, the surface morphology of the cracked surface of the composite material was studied (Rehman et al. Citation2019).
Result and discussions
Tensile properties
The interfacial adhesion between the matrix and fibers is a significant factor, which influences the tensile properties of the composites. The tensile strength and tensile modulus of untreated fiber composites such as 3UTCPFLSFC, 7UTCPFLSFC, 10UTCPFLSFC, and alkali-treated 3ATCPFLSFC, 7ATCPFLSFC, and 10ATCPFLSFC are shown in .
Figure 3. a) tensile strength and b) tensile modulus of 3 mm, 7 mm, and 10 mm UTCPFLSFC and ATCPFLSFC.
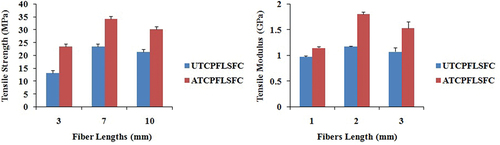
The 7ATCPFLSFC showed 61%, 31%, 37%, and 11% improvement in the tensile strength, and 30%, 35%, 35%, 35%, and 15% in the tensile modulus compared with 3UTCPFLSFC, 7UTCPFLSFC, 10UTCPFLSFC, 3ATCPFLSFC, and 10ATCPFLSFC, respectively. Based on the above results, the tensile strength and tensile modulus of (34.31 MPa & 1.81 GPa) 7ATCPFLSFC are found to be superior in comparison with other composites, which is due to exposure of more surface area of the fiber with the matrix. 3ATCPFLSFC had poor matrix bonding, and small-fiber has many possibilities of being pulled quickly from the composite materials. Due to its increased length, in the case of 10ATCPFLSFC has to lead the reduction adhesion between the fiber and matrix in the composites. However, 7ATCPFLSFC has shown that the seamless stronger bonding between the fiber and matrix has reduced the pullout of fibers from composites during loading (Shaker et al. Citation2020). The tensile properties of untreated composites were reduced due to weak adhesion between the fiber and matrix in the composites. The mechanical properties of the composites were improved by alkali treatment, which eliminates unnecessary excess materials from the fiber and increases the interlocking between the fiber and matrix. Alkali treatment results in defibrillation of fibers and formation of rough surfaces on the fibers producing many pores on the surface of the fibers through which the resin has penetrated the fiber resulting in better fiber matrix adhesion and increased density which has contributed to enhanced properties (Bhuvaneshwaran et al. Citation2021). The good adhesion between the fiber and matrix resulted in improved stress transfer in the composite, due to this reason the tensile load carrying capacity is considerably increased (Rehman et al. Citation2019). Composite strength depends on the load transfer capability, which is mainly attributed to the bonding strength between the fiber and matrix (Shaker et al. Citation2020). A good fiber–matrix adhesion may result in better or improved load transfer, thus leading to higher tensile strength in the case of treated composites (Muruganrama et al. Citation2020).
Flexural properties
The flexural strength and modulus of the treated and untreated composites are shown in , respectively. The 3UTCPFLSFC exhibited a minimum flexural strength of 22.06 MPa and a flexural modulus of 1.20 GPa, whereas 7ATCPFLSFC showed the maximum flexural strength of 58.43 MPa and a flexural modulus of 3.23 GPa.
Figure 4. a) flexural strength and b) flexural modulus of 3 mm, 7 mm, and 10 mm UTCPFLSFC and ATCPFLSFC.
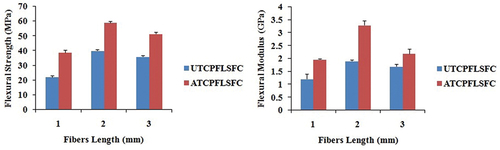
However, the flexural strength of 7ATCPFLSF composite increased by 62%, 26%, 38%, 34%, and 12% and flexural modulus increased by 51%, 15%, 31%, and 10% compared to 3UTCPFLSFC, 7UTCPFLSFC, 10UTCPFLSFC, 3ATCPFLSFC, and 10ATCPFLSFC, respectively. When the load is applied vertically to the horizontal axis of the composite, the inter-laminar forces control the flexural strength and flexural modulus. The chemical treatment of the fibers resulted in good bonding between the matrix and fiber. This has provided the high strength and rigidity of the composites. Therefore, the alkali-treated fiber has good adhesion properties resulting in maximum flexural strength (Rehman et al. Citation2019). With an incremental increase in the length of the fiber from 3 to 7 mm, the potential of bending resistance was seen to increase. However, the resistance to multidirectional forces reduces, as the fiber length is greater than 7 mm. The optimum length of 7 mm fiber in the composite provided the composites greater rigidity and thereby improved mechanical properties (Muruganrama et al. Citation2020). However, in the case of 3 mm fiber, the bond with the matrix is poor, because of its very shorter length. In the case of any load, the 3 mm fiber in the matrix has poor load–displacement (Bisanda and Martin Citation1992).
Impact properties
Before the final failure occurs, the total energy dissipated in the material is the ability of the material to resist the sudden impact load. shows the impact strength of the treated and untreated composites.
The impact strength of the composites was found to be improved, which was due to the effect of alkali treatment and fiber length. The bonding strength between the fiber and the matrix is specifically related to the impact properties of fiber-reinforced polymer composites. The impact strength of 3.99 kJ/m2 for 3UTCPFLSC is the lowest, and the 7ATCPFLSFC composite had the highest impact strength of 8.25 kJ/m2. The 7ATCPFLSFC composites had an increase in impact strength by 51.6%, 15.7%, 31%, 20.7%, and 10.7% compared to 3UTCPFLSFC, 7UTCPLSFC, 10UTCPFLSFC, 3ATCPFLSFC, and 10ATCPFLSFC, respectively. The 7ATCPFLSFC absorbed more energy, which is due to good interlocking between the matrix and the fiber and better load transfer due to alkali treatment on the fiber surface that has stopped the propagation of crack during the impact test (Belouadah, Rokbi, and Ati Citation2020; Bhuvaneshwaran et al. Citation2021). shows the mechanical properties of short ATCPFLSF composites with different natural fiber composites, and shows the Mechanical Properties of CPFLSF Composite with Neat resin.
Table 1. Mechanical properties of short ATCPFLSF composites with different natural fiber composites.
Table 2. Mechanical properties of CPFLSF composites with neat resin.
The 7ATCPFLSFC sample exceeds the other natural fiber composites. The low cost, lightweight, bio-based polymer composites have gained more attention due to their renewability and biodegradability. Moreover, 7ATCPFLSFC has shown that the mechanical properties of natural fiber composites are similar or even better than jute, straw, sisal, banana, coir, hemp, and kenaf fiber-reinforced composites.
Water absorption properties
The water absorption characteristics of the composite were measured at an interval of 30 min up to 180 min. shows the weight of the composites and percentage due to moisture absorption and found that the amount of water absorbed in 7ATCPFLSFC is very low (Bhuvaneshwaran et al. Citation2021).
Figure 6. a) water absorption weight and b) water absorption weight percentage of 3 mm, 7 mm, and 10 mm UTCPFLSFC and ATCPFLSFC for every 30 minutes.
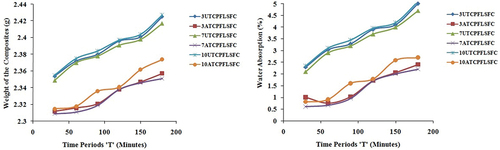
The percentage increase in weight is found by using Equationequation (1)(1)
(1) . For all variances, compared to the initial weight, the composite weight considerably increased after every 30-min interval of time. The 7ATCPFLSFC showed a maximum moisture absorption compared to the 3UTCPFLSFC. The surface area interaction of fiber will be more in the case of longer fiber and also a large amount of pectin, lignin, and hemicelluloses, which are the primary water-holding molecules in the untreated fibers is the reason for higher moisture absorption in any composites (Bhuvaneshwaran et al. Citation2021). This indicates the reason, the longer fiber composites absorb more water than the others. In treated fibers, the lignin, pectin, and hemicellulose contents are removed by the alkali solution, and hence the moisture absorption in treated fibers will be comparatively low compared to the untreated fibers (Muruganrama et al. Citation2020).
Dynamic mechanical analysis (DMA)
Storage modulus (E’)
The storage modulus (E’) was found higher for 7ATCPFLSFC (1247 MPa) within the glassy temperature region compared to 3UTCPFLSFC (967 Mpa), 7UTCPFLSFC (1089 MPa), 10UTCPFLSFC (1023 MPa), 3ATCPFLSFC (1110 MPa), and 10ATCPFLSFC (1183 MPa). The different concentrations of NaOH treatment alter the physical and chemical properties of CPFLSF and the decreased mobility of the polymer particles, which actuates superior stress exchange that results in positive interfacial bonding between fiber and matrix. It was observed that the storage modulus increased in all the treated fiber composites compared to untreated composite and has also shown the same trend before and after the transition region (Shaker et al. Citation2020). shows the progressive fall of storage modulus with an increase in temperature that was observed in all the cases. The stiffness of the fiber decreased due to an increase in temperature and thus the storage modulus was observed to be reduced in the composites (Kumar et al. Citation2014).
Loss modulus (E’’)
Loss modulus (E’’) is the measure of heat energy dissipated as heat per cycle of viscous deformation of the material (Thirumurugan et al. Citation2019). The variation of loss modulus (E’’) with the change in temperature due to different treatments on the fibers is shown in . Due to the need for heat dissipation within the material, the least loss modulus of 112.4 MPa was observed for 3UTCPFLSFC at a temperature region of 60ºC to 80ºC. In the smooth transition region, the 7ATCPFLSFC appears the most extreme loss modulus of 231.4 MPa. This is due to alkali treatment that has resulted in the removal of impurities from the fiber surface and also change the fiber smooth surface into a rough surface (Rehman et al. Citation2019). It can moreover be observed that the modulus curve broadens, which may be due to the type of fiber treatments and the physical state of the matrix encompassing the fibers to the others (Shaker et al. Citation2020).
Damping factor (Tan δ)
The damping factor (Tan δ) is determined by the ratio of loss modulus (E’) and storage modulus (E’’). The damping factor (Tan δ) measured with the temperature of different composites is shown in . Consolidation of fibers in a composite system influences the damping behavior of the composites, which is due to shear stretch concentrations within the fibers alongside visco-elastic vitality scattering within the matrix (Rehman et al. Citation2019). The composite good fiber/matrix attachment decreases the mobility of the polymer chains in this way reducing the damping factor (0.188) to represent that the particular composite has good load-bearing capacity. The 7ATCPFLSFC composite has a low damping factor compared to 3UTCPFLSFC,7UTCPFLSFC, 10UTCPFLSFC, 3ATCPFLSFC, and 10ATCPFLSFC. The results demonstrate that the good interfacial holding between 7ATCPFLSF composite and polyester decreases the damping of the composites (Rehman et al. Citation2019).
Thermo gravimetric analysis
The TGA of untreated and alkali-treated CPFLSF-reinforced polymer composites is shown in . From 30°C to 600°C and 0–180 minutes, a single-stage thermal degradation takes place in the composites. Moreover, similar decomposition behavior was observed in all composites. From the four-stage of decomposition, the least temperatures that contributed toward the decomposing of the remaining mass of 7.42%, 9.55%, 11.23%, 13.67%, 18.36%, 15.93% for 3UTCPFLSFC, 7UTCPFLSFC, 10UTCPFLSFC, 3ATCPFLSFC, 7ATCPFLSFC, and 10ATCPFLSFC, respectively. The decomposition from 150°C to 200°C is the first stage in composites. At this stage, the evaporation of moisture and removal of the solvent takes place in the composite and no thermal decomposition happened (Rehman et al. Citation2019). The decomposition of composites from 270°C to 320°C is the second stage (Shaker et al. Citation2020). This stage indicates the decomposition of molecules like fats and waxes that were removed due to alkali treatment (Muruganrama et al. Citation2020). The next stage of decomposition happened from 380°C to 440°C, which is the third stage (Muruganrama et al. Citation2020). At this stage, the lignin, hemicelluloses, and celluloses are decomposed, and as well as the soft segment and volatilization of the composite are degraded (Rehman et al. Citation2019). The fourth stage of decomposition happened between the temperatures of 480°C to 520°C within the composites (Bhuvaneshwaran et al. Citation2021). At this stage, the fibers at the side polymer composites are degraded. From and over 520°C, the weight loss of all treated composites appears to be less than that of untreated composites (Muruganrama et al. Citation2020). The sharp drop observed between 40°C and 100°C corresponds to the change from glass to rubbery transition (Gu Citation2009). The changes in molecular mobility due to an increase in length leading to better wetting between the fiber, matrix, and interfacial bonding as the temperature is increased can be attributed to this behavior in all the composites (Mohanty, Verma, and Nayak Citation2006; Ray et al. Citation2002). The storage modulus fall as the temperature is increased is observed for all the cases. Similar behavior of fall in storage modulus was reported in (Jawaid et al. Citation2013).
Figure 9. a) thermo gravimetric analysis curve and b)differential thermogravimetric analysis curve of 3 mm, 7 mm, and 10 mm UTCPFLSFC and ATCPFLSFC.
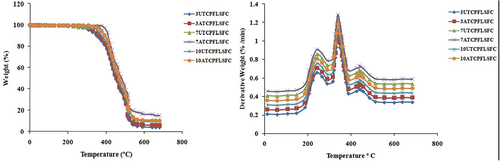
The DTG curves of untreated and treated CPFLSF composites are shown in . Based on the endothermic and exothermic reactions at distinct temperatures, the decomposition of composites takes place. At the temperature between 30°C and 700°C, weight loss takes place. In relation with increased NaOH percentage in CPFLSF, the temperature extends of 370°C, 375°C, 382°C, 391°C, 400°C, and 405°C (Muruganrama et al. Citation2020) for 3UTCPFLSFC, 3ATCPFLSFC, 7UTCPFLSFC, 10UTCPFLSFC, 10ATCPFLSFC, and 7ATCPFLSFC have been noticed. At temperatures over 590°C, the treated composite exhibited major degradation with more weight loss (Shaker et al. Citation2020). The FTIR Spectroscopy of both raw and alkali (6% NaOH) is shown in . The fiber shows well-defined groups at around 3550, 2960, 2460, 1850, 1300, 750 cm−1. Alkaline treatment modifies the surface of the fiber and removes a certain amount of lignin and hemicellulose confirmed by FTIR analysis. The cellulose and hemicelluloses C-H stretching vibrations have a peak at 2400–2800 cm−1. The signal at 1800 cm−1 is related to the lignin compound C = O stretching alphaketo carboxylic acid. The peak at 1500 cm−1 connected to lignin’s C = C aromatic ring. The band around 3332 cm-1 is narrower and has a higher intensity for cellulose, which demonstrated that the extracted cellulose contained more –OH groups than in the untreated sample. The band at 2901 cm-1 relates to the stretching of C-H bonds, and the one at 3332 cm-1 to the stretching of H-bonded OH groups.
Scanning electron microscope
The morphology of the fractured surfaces of 3UTCPFLSFC, 3ATCPFLSFC, 7UTCPFLSFC, 7ATCPFLSFC, 10UTCPFLSFC, and 10ATCPFLSFC subjected to tensile loads are shown in . In 3UTCPFLSFC and 3ATCPFLSFC, the fiber pullout occurred to a greater extent compared to that of 7ATCPFLSFC. This is due to better adhesion between the matrix and the fiber. The de-bonding between fiber and matrix was visible in 3UTCPFLSCF composite and 3ATCPFLSFC. The effect of individual fiber tensile properties is presented because of pores and pits. Due to low interfacial strength, the stress transfer efficiency is much less compared to that of composites reinforced with alkali-treated fibers, which in turn has resulted in very low mechanical properties for the untreated fiber-reinforced composites. This was due to the presence of wax, moisture content, hemicelluloses, and lignin fiber. The alkali treatment improves the characteristics of the fiber (Belouadah, Rokbi, and Ati Citation2020). This results in an increase of mechanical properties on 7ATCPFLSFC. It is also clear from SEM images that only a little evidence of fiber fracture is visible in the composite, which indicates that alkali treatments led to good interfacial adhesion between the fiber and matrix leading to better stress transfer efficiency with increased mechanical properties compared to those of the 3UTCPFLSFC and 3ATCPFLSFC (Belouadah, Rokbi, and Ati Citation2020). The fiber breakage and very little pullout from the resin prove that 7ATCPFLSFChas good mechanical properties (Rehman et al. Citation2019). The alkali treatment has resulted in better interfacial adhesion. It almost resists the heavy tensile load. The fiber pull-out length is considerably shorter which can be seen, where the failure of the composites had occurred due to fiber shearing and not due to interfacial failure. This led to better stress transfer between the fiber and matrix and also increased the mechanical properties compared to untreated fiber composites (Belouadah, Rokbi, and Ati Citation2020). All of these factors contributed to the improvement of the mechanical properties of the composites. The 7ATCPFLSFC has good bonding compared to other types of composites. Due to this, debonding occurs at the fiber–matrix interface and also results in the formation of cracks (Belouadah, Rokbi, and Ati Citation2020). Alkali treatment modifies the fiber surface resulting in positive penetration of resin inside the fibers due to which better interlocking of fibers with matrix occurs. This in turn has to lead to lesser removal of material compared to untreated fiber composites (Rehman et al. Citation2019). All this proves that, when compared to 3UTCPFLSFC, 3ATCPFLSFC, and 7UTCPFLSFC, 7ATCPFLSFC has better Mechanical and Physical properties. Moreover, 10UTCPFLSFC and 10ATCPFLSFC exhibit more fiber pullouts. Because the longer fibers are easier to break than the shorter fiber, because the longer fiber had a longer perpendicular distance in loading condition, compared to the smaller fibers (Rehman et al. Citation2019). So to break a smaller fiber more force is required to cover a smaller perpendicular distance and to gain a sufficient amount of torque, which is quite hard but in the case of longer fiber, less force is required to gain a sufficient amount of torque because of the longer perpendicular distance (Bisanda and Martin Citation1992). In this case, the 10UTCPFLSFC and 10ATCPFLSFC have a poor bond between the matrix and the fiber, there occurred weak reinforcement so that the fiber gets easily broken and pulled out (Belouadah, Rokbi, and Ati Citation2020). Due to the larger fiber matrix, the fiber forms a cluster than the continuous selection, the resin did not spread all over the composites and results in pores and discontinuous arrangement of the fiber in the matrix of the composites (Mahalingam Citation2022; Muruganrama et al. Citation2020).
Conclusions
The coconut tree primary flower leaf stalk fiber was extracted from the coconut tree and investigated for static, dynamic mechanical, water, thermal properties, and scanning electron microscopy. The tensile strength, flexural strength, and impact strength of randomly distributed 7ATCPFLSFC improved by 61.43%, 62.24%, and 51.6%, respectively, compared with 3UTCPFLSFC. Dynamic mechanical analysis, a maximum storage modulus (E’) of 1247MPa and a loss modulus (E’’) of 231.4 MPa were recorded for 7ATCPFLSFC. The alkali treatment reduced the water absorption in the composites. 7ATCPFLSFC exhibited the least water absorption compared to the 3TCPFLSFC. Thermal properties of the treated and untreated composite showed similar decomposition in all stages. However, the 7ATCPFLSFC shows the maximum thermal decomposition with a residual mass of 18%. The SEM image of the 7ATCPFLSFC fractured surface after tensile loading showed evidence of less fiber pullout and less fracture. This can be attributed to better mechanical properties in static and dynamic loading conditions. Research results imply that the CPFLSF may be employed as a possible strengthening agent to the polymer matrix for the production of wall roof applications and industrial components.
Disclosure statement
No potential conflict of interest was reported by the author(s).
Additional information
Funding
References
- Belouadah, Z., M. Rokbi, and A. Ati. 2020. Manufacturing and characterization of new composite based on epoxy resin and lygeum spartum L. plant. Journal of Natural Fibers 19 (11):1–16. doi:10.1080/15440478.2020.1856273.
- Bhuvaneshwaran, M., S. P. Pavayee Subramani, S. K. Palaniappan, S. K. Pal, and S. Balu. 2021. Natural cellulosic fiber from coccinia indica stem for polymer composites: Extraction and characterization. Journal of Natural Fibers 18 (5):644–52. doi:10.1080/15440478.2019.1642826.
- Bisanda, E. T. N., and P. A. Martin. 1992. Properties of sisal-CNSL composites. Journal of Materials Science 27:1690–700. doi:10.1007/BF00542934.
- Biswas, S., S. Kindo, and A. Patnaik. 2011. Effect of fiber length on mechanical behavior of coir fiber reinforced epoxy composites. Fibers and Polymers 12 (1):73–78. doi:10.1007/s12221-011-0073-9.
- Dahy, H. 2019. Natural fibre-reinforced polymer composites (NFRP) fabricated from lignocellulosic fibres for future sustainable architectural applications, case studies: Segmented-shell construction, acoustic panels, and furniture. Sensors 19 (3):738. doi:10.3390/s19030738.
- Gu, H. 2009. Dynamic mechanical analysis of the seawater treated glass/polyester composites. Materials & Design 30 (7):2774–77. doi:10.1016/j.matdes.2008.09.029.
- Gurunathan, T., S. Mohanty, and S. K. Nayak. 2015. A review of the recent developments in biocomposites based on natural fibres and their application perspectives. Composites Part A, Applied Science and Manufacturing 77 (77):1–25. doi:10.1016/j.compositesa.2015.06.007.
- Herlina, S. N., I. N. G. Wardana, Y. S. Irawan, and E. Siswanto. 2018. Characterization of the chemical, physical, and mechanical properties of NaOH-treated natural cellulosic fibers from corn husks. Journal of Natural Fibers 15 (4):545–58. doi:10.1080/15440478.2017.1349707.
- Jawaid, M., H. P. S. Abdul Khalil, A. Hassan, R. Dungani, and A. Hadiyane. 2013. Effect of jute fibre loading on tensile and dynamic mechanical properties of oil palm epoxy composites. Composites Part B: Engineering 45 (1):619–24. doi:10.1016/j.compositesb.2012.04.068.
- Karimah, A., M. R. Ridho, S. S. Munawar, Y. Amin, R. Damayanti, M. A. Rahandi Lubis, A. P. Wulandari, A. H. Iswanto, and A. Fudholi. 2021. A comprehensive review on natural fibers: Technological and socio-economical aspects. Polymers 13 (24):4280. doi:10.3390/polym13244280.
- Kumar, S. M., D. Suresh, and K. Subramanian. 2014. Studies on mechanical, thermal and dynamic mechanical properties of untreated (raw) and treated coconut sheath fiber reinforced epoxy composites. Materials & Design 59:63–69. doi:10.1016/j.matdes.2014.02.013.
- Li, X., L. G. Tabil, and S. Panigrahi. 2007. Chemical treatments of natural fiber for use in natural fiber-reinforced composites: A review. Journal of Polymers and the Environment 15 (1):25–33. doi:10.1007/s10924-006-0042-3.
- Mahalingam, J. 2022. Mechanical, thermal, and water absorption properties of hybrid short coconut tree primary flower leaf stalk fiber/glass fiber-reinforced unsaturated polyester composites for biomedical applications. Biomass Conversion and Biorefinery 1–12. doi:10.1007/s13399-022-02958-4.
- Mohammed, L., M. Nm Ansari, G. Pua, M. Jawaid, and M. Saiful Islam. 2015. A review on natural fiber reinforced polymer composite and its applications. International Journal of Polymer Science. 1–15. doi:10.1002/SICI1098-232919992418:4<351:AID-ADV6>3.0.CO;2-X
- Mohanty, S., S. K. Verma, and S. K. Nayak. 2006. Dynamic mechanical and thermal properties of MAPE treated jute/HDPE composites. Composites Science and Technology 66 (3–4):538–47. doi:10.1016/j.compscitech.2005.06.014.
- Mulinari, D. R., C. A. R. P. Baptista, J. V. C. Souza, and H. J. C. Voorwald. 2011. Mechanical properties of coconut fibers reinforced polyester composites. Procedia Engineering 10:2074–79. doi:10.1016/j.proeng.2011.04.343.
- Muruganrama, T., J. Mahalingam, S. Dharmalingam, and S. Natarajan. 2020. Investigation of static and dynamic mechanical properties of short palmyra palm leaf stalk fiber (PPLSF) reinforced polymer composites. Journal of Natural Fibers 19 (5):1–17. doi:10.1080/15440478.2020.1840478.
- Prades, A., R. R. Ablan Assa, M. Dornier, J. Pierre Pain, and R. Boulanger. 2012. Characterisation of the volatile profile of coconut water from five varieties using an optimised HS-SPME-GC analysis. Journal of the Science of Food and Agriculture 92:2471–78. doi:10.1002/jsfa.5655.
- Ray, D., B. K. Sarkar, S. Das, and A. K. Rana. 2002. Dynamic mechanical and thermal analysis of vinylester-resin-matrix composites reinforced with untreated and alkali-treated jute fibers. Composites Science and Technology 62 (7–8):911–17. doi:10.1016/S0266-3538(02)00005-2.
- Rehman, M. M., M. Zeeshan, K. Shaker, and Y. Nawab. 2019. Effect of micro-crystalline cellulose particles on mechanical properties of alkaline treated jute fabric reinforced green epoxy composite. Cellulose 26 (17):9057–69. doi:10.1007/s10570-019-02679-4.
- Saheb, D. N., and J. P. Jog. 1999. Natural fiber polymer composites: A review. Advances in polymer technology. Journal of the Polymer Processing Institute 18:351–63.
- Sari, N. H., R. A. Ilyas, E. Syafri, and S. Indran. 2021. Characterization of the density and mechanical properties of corn husk fiber reinforced polyester composites after exposure to ultraviolet light. Functional Composites and Structures 3 (3):034001. doi:10.1088/2631-6331/ac0ed3.
- Sari, N. H., I. N. Wardana, Y. S. Irawan, and E. Siswanto. 2017. Corn husk fiber-polyester composites as sound absorber: Nonacoustical and acoustical properties. Advances in Acoustics and Vibration 2017:1–7. doi:10.1155/2017/4319389.
- Sathishkumar, T. P., P. Navaneethakrishnan, and S. Shankar. 2012. Tensile and flexural properties of snake grass natural fiber reinforced isophthalic polyester composites. Composites Science and Technology 72 (10):1183–90. doi:10.1016/j.compscitech.2012.04.001.
- Satyanarayana, K. G., G. G. Arizaga, and F. Wypych. 2008. Biodegradable composites based on lignocellulosic fibers-an overview. Progress in Polymer Science 34 (9):982–1021. doi:10.1016/j.progpolymsci.2008.12.002.
- Satyanarayana, K. G., C. K. S. Pillai, K. Sukumaran, S. G. K. Pillai, P. K. Rohatgi, and K. Vijayan. 1982. Structure property studies of fibres from various parts of the coconut tree. Journal of Materials Science 17 (8):2453–62. doi:10.1007/BF00543759.
- Shaker, K., R. M. Ullah Khan, M. Jabbar, M. Umair, A. Tariq, M. Kashif, and Y. Nawab. 2020. Extraction and characterization of novel fibers from Vernonia elaeagnifolia as a potential textile fiber. Industrial Crops and Products 250 (152):112518. doi:10.1016/j.indcrop.2020.112518.
- Shaker, K., M. Umair, S. Shahid, M. Jabbar, R. M. Waseem Ullah Khan, M. Zeeshan, and Y. Nawab. 2020. Cellulosic fillers extracted from argyreia speciose waste: A potential reinforcement for composites to enhance properties. Journal of Natural Fibers 19 (11):1–13. doi:10.1080/15440478.2020.1856271.
- Shanmugam, D., and M. Thiruchitrambalam. 2014. Influence of alkali treatment and layering pattern on the tensile and flexural properties of palmyra palm leaf stalk fiber (PPLSF)/jute fiber polyester hybrid composites. Composite Interfaces 21 (1):3–12. doi:10.1080/15685543.2013.830513.
- Silva, D. A., N. Chawla, and R. D. de Toledo Filho. 2008. Tensile behavior of high performance natural (sisal) fibers. Composites Science and Technology 68 (15–16):3438–43. doi:10.1016/j.compscitech.2008.10.001.
- Syafri, E., N. H. Sari, M. Mahardika, P. Amanda, and R. A. Ilyas. 2021. Isolation and characterization of cellulose nanofibers from agave gigantea by chemical-mechanical treatment. International Journal of Biological Macromolecules 200 (25):333. doi:10.1016/j.ijbiomac.2021.12.111.
- Thirumurugan, R., M. Jayaraj, D. Shanmugam, and T. Ramkumar. 2019. Characterization of new natural cellulosic fiber from coconut tree primary flower leaf stalk fiber (CPFLSF). Journal of Natural Fibers 18 (11):1–13. doi:10.1080/15440478.2019.1701608.
- Venkataswamy, M. A., C. K. S. Pillai, V. S. Prasad, and K. G. Satyanarayana. 1987. Effect of weathering on the mechanical properties of midribs of coconut leaves. Journal of Materials Science 22 (9):3167–72. doi:10.1007/BF01161178.
- Zhang, M. Q., M. Z. Rong, and X. Lu. 2005. Fully biodegradable natural fiber composites from renewable resources: All-plant fiber composites. Composites Science and Technology 65:15–16. doi:10.1016/j.compscitech.2005.06.018.