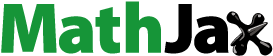
ABSTRACT
Natural fiber-reinforced two hybrid composites: “Jute and betel nut husk (BNH)” and “Human hair, Jute and BNH,” are fabricated by the hand lay-up method using 50:50 and 33.33:33.33:33.33 fiber ratio by weight, respectively. The 3 to 4 mm long fibers and 20% fiber loading by volume are used to fabricate the composites. The mechanical properties such as tensile, flexural, impact strength, and hardness of composites are evaluated by tests as per ASTM standards and compared. This study revealed that human hair-embedded (with hair – WH) composite is remarkably stronger than non-embedded ones (without hair – WoH). In human hair-embedded (WH) composites, the tensile, flexural, and impact strength are found more than 75% higher, and the hardness is found 19% higher than non-embedded ones (WoH). The bonding between fibers and matrix, voids, microcracks, and fracture of the composites are also investigated by SEM (Scanning Electron Microscopy). It revealed that human hair-embedded composites have stronger bonding, fewer voids and microcracks, and outstanding energy absorption capacity, strength, and hardness. This study expands the scope of human hair to strengthen natural fiber-reinforced composites as a low-cost constituent and application of human hair-embedded composites in different engineering fields, ultimately reducing environmental pollution and greenhouse effects.
摘要
天然纤维增强的两种混杂复合材料: “黄麻和槟榔壳(BNH)”和“人发、黄麻和BNH”,分别采用50:50和33.33:33.33:33.33纤维重量比的手工叠层法制造. 使用3至4 mm长的纤维和按体积计20%的纤维负载来制造复合材料. 根据ASTM标准通过测试评估并比较复合材料的机械性能,如拉伸、弯曲、冲击强度和硬度. 这项研究表明,嵌入毛发(含毛发WH)的复合材料明显强于未嵌入毛发(无毛发WoH). 在人头发嵌入(WH)复合材料中,发现拉伸、弯曲和冲击强度比未嵌入的高75%以上,硬度比未嵌入(WoH)高19%. 还通过SEM(扫描电子显微镜)研究了纤维与基体之间的结合、孔隙、微裂纹和复合材料的断裂. 研究表明,人发嵌入复合材料具有更强的结合力、更少的空隙和微裂纹,以及出色的能量吸收能力、强度和硬度. 这项研究扩大了人类毛发的范围,以强化天然纤维增强复合材料,作为一种低成本的成分,并将人类毛发嵌入复合材料应用于不同的工程领域,最终减少环境污染和温室效应.
Introduction
Plant-based fibers such as jute, banana, sisal, hemp, coir, pineapple, betel nut, bamboo, palm, etc. (Rahman et al. Citation2020; Verma, Singh, and Sharma Citation2016) are the most popular to the researchers to fabricate polymer composites. It has remarkable properties such as 100% biodegradability, environmentally friendly, low cost and density, high specific strength, and plenty of availability (Rahman et al. Citation2020; Venkateshappa et al. Citation2010). To reduce environmental pollution, researchers are trying to replace synthetic fiber-based composites with natural fiber-based composites (Khan, Srivastava, and Gupta Citation2018). Besides plant-based fiber, animal-based fiber such as human hair, sheep wool, horse and cow hair, silk, bird feathers, etc., is getting researcher’s attention (Kumar, Singh, and Ranjan Citation2019; Manivannan et al. Citation2019; Oladele and Agbeboh Citation2017). The animal-based fiber-reinforced polymer composites have higher mechanical strength than plant-based fiber-reinforced composites (Kumar, Singh, and Ranjan Citation2019). Animal hairs are slowly biodegradable, treated as biological waste, and disposed of by burying and burning (Gupta Citation2014; Rao, Divakara, and Eshwara Prasad Citation2018; Selvakumar and Meenakshisundaram Citation2019). Consequently, it contributes to environmental pollution. Human hair has high tensile strength (Gupta Citation2014; Rao, Divakara, and Eshwara Prasad Citation2018) equivalent to copper wire (Kumar et al. Citation2015; Selvakumar and Meenakshisundaram Citation2019), noble insulation property and high friction coefficient (Gupta Citation2014), low cost and weight, and abundantly available (Kumar et al. Citation2015; Rao, Divakara, and Eshwara Prasad Citation2018). Therefore, researchers are trying to use animal-based fibers such as human hair to reinforce polymer composites besides plant-based fibers.
This study investigates the effect of human hair on the mechanical properties of natural fiber-reinforced hybrid polyester composites. In this regard, natural fiber-reinforced two polyester composites: “Jute and betel nut husk (BNH)” and “Human hair, Jute and BNH” are fabricated by hand lay-up method using 50:50 and 33.33:33.33:33.33 fiber ratio by weight, respectively. The 3 to 4 mm long fibers with 20% fiber loading by volume are used to make the composites. The mechanical properties such as tensile strength, modulus of elasticity and toughness, flexural strength and modulus, and hardness of the composites are evaluated by tests as per ASTM standards and compared. Besides, the surface morphology and bonding between the fibers and matrix are examined by Scanning Electron Microscopy (SEM) and compared.
Some studies are reported about animal hair-reinforced polymer composites and the prospect of human hair in reinforcing the composite materials. Researchers Kumar, Singh, and Ranjan (Citation2019) investigated the mechanical properties of horsehair-reinforced polypropylene composites. Manivannan et al. (Citation2019) and Oladele and Agbeboh (Citation2017) studied sheep wool and cow hair-reinforced polyester composites, respectively. They evaluated the effect of fiber loading on the mechanical strength of the composites. Kumar et al. (Citation2015) studied the impact of adding 1.5% human hair by weight to the M-40 Grade cement and found that the compressive, flexural, and split tensile strength of the cement increased by 7.22% to 8.18%, 23.56% to 27.60%, and 17.26% to 26.60%, respectively. Nanda and Satapathy (Citation2017) and Verma and Singh (Citation2019) worked on human hair-reinforced epoxy and polymer composites, respectively. They found that the mechanical strength of both composites increased appreciably due to the addition of human hair. Selvakumar and Meenakshisundaram (Citation2019) also studied jute and human hair-reinforced hybrid polymer composites. They revealed that the tensile and flexural strength and viscoelastic behavior of the composite were enhanced by adding human hair. Besides those noteworthy studies, Gupta (Citation2014) and Yang et al. (Citation2017) revealed the prospects of human hair as a potential and natural ecological fiber to reinforce polymer composites. Due to the favorable mechanical and thermophysical properties, researchers are still interested in incorporating human hair in the natural fiber-reinforced composites to enrich mechanical strength and thermal properties. However, those studies are not related to the effect of human hair on the mechanical properties of natural fiber-reinforced hybrid polyester composites.
To achieve the objective of this study, natural fiber-reinforced two hybrid polyester composites: embedded (with hair – WH) and non-embedded (without hair – WoH) human hair are fabricated by the hand lay-up method. The effects of human hair embedded in natural fiber-reinforced composites are investigated by evaluating mechanical properties through tests as per ASTM standards. The surface morphology, such as bonding between fibers and matrix, voids, microcracks, crack propagation, and fiber agglomeration in the fabricated composites, is also investigated by SEM.
Materials and fabrication process
Three natural fibers: human hair, jute, and betel nut husk (BNH) fiber, are used to fabricate the composites with 20% fiber loading by volume. The solution of polyester and Methyl Ethyl Ketone Peroxide (MKEP) is used as a matrix. The NaOH solution is used to treat the fibers since it brings softness and smoothness to the fibers (Rahman et al. Citation2020) and improves the bonding between the matrix and fibers (Lazim et al. Citation2014; Muralidhar et al. Citation2019). The morphological images of the treated and untreated fibers are obtained by Scanning Electron Microscopy (SEM), as shown in , The following procedure and process are used to extract and treat the fibers.
Figure 1. Morphological investigation of treated and untreated fibers: (a) human hair, (b) jute fiber, and (c) BNH fiber.
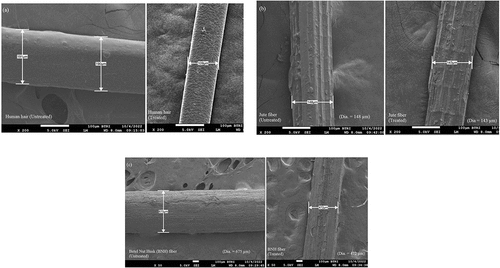
Human hair
Asian male hair is used in this study to fabricate the composites, which are collected from the local salons. The dirt particles are removed from the hair by hand stretching and then soaked in the 10% NaOH solution for 2 hours. After that, the hair is washed in distilled water and dried at room temperature. Human hair is greasier and oilier than other natural fibers since people use different types of oil, gel, and color in their hair. However, it depends on ethnicity, culture, and geographical location. Therefore, the 10% NaOH solution is used in this study to remove the oily and greasy matter from the human hair and to achieve appropriate bonding with the matrix.
Jute fiber
The jute fibers used in this study are collected locally. First, the dirt particles are removed from the fibers with a comb and then soaked in the 2% NaOH solution for 4 hours. After that, jute fibers are washed with clean water and dried in sunlight.
BNH fiber
The ripe betel nuts are kept damp for 14 days to start the retting process. Then, BNH fibers are extracted manually by separating the betel nut from the shell. Only fine fibers from the inner fibrous part of the shell are extracted and washed in clean water. Fibers dried in the sunlight for three days, soaked in the 5% NaOH solution for 4 hours, and dried again in the sunlight for 48 hours.
Matrix
The unsaturated polyester and organic compound MKEP with 97% and 3% ratio by weight, respectively, are used as a matrix to fabricate the composites. MKEP accelerates the hardening of unsaturated polyester and initiates the bonding between polyester and fibers (Rahman et al. Citation2020). The mechanical properties of human hair, BNH and jute fibers, and unsaturated polyester found in the literature are shown in .
Table 1. Mechanical properties of human hair, BNH and jute fiber.
Fabrication of composites
The composites are fabricated by the hand lay-up method using 3 to 4 mm of human hair, jute, and BNH fiber. Natural fiber-reinforced two hybrid polyester composites: “Jute and BNH” and “Human hair, Jute and BNH” fibers, are fabricated with 50:50 and 33.33:33.33:33.33 fiber ratio by weight, respectively, and 20% fiber loading by volume. The 15.25 cm x 12.7 cm composite sheets are fabricated using molds. First, the dried and treated BNH and jute fibers are cut into 3–4 mm pieces and mixed homogeneously in a blending machine. The weight and volume fraction of the polyester and fibers are ensured by weighing. A glass sheet is laid on the flat surface, and a cleaned malleate paper is attached on top of it. PVC sheets are used around the mold to protect the polyester resin from escaping. The solution of unsaturated polyester and MKEP is poured into the mold. Then, the mixture of fibers is spread out uniformly over the mold. The stacks of fibers and polyester are poked with sharp needles to remove the trapped air and ensure resin flow from top to bottom. Another malleate paper is placed at the top of the fibers stacks and pressed gently by a roller to set the fibers in the polyester resin and remove air bubbles. The top malleate paper is covered by another glass sheet under a pressure of 10.13 kPa for 24 hours. The resin is cured entirely within 24 hours and then carefully removed from the mold. The same procedure is followed to fabricate the “Human hair, Jute, and BNH” fiber-reinforced hybrid polyester composites. The thickness of the composite sheets varies from 4.1–4.22 mm and 3.1–3.26 mm, for “Jute and BNH” and “Human hair, Jute and BNH” fiber-reinforced composite, respectively. Since composite sheets are fabricated by the hand lay-up method, a slight variation in thickness is unavoidable. However, it does not affect the evaluation of mechanical properties of the composites.
Experiment
The mechanical properties of the “Jute and BNH” fiber-reinforced polyester composites with embedded (WH) and non-embedded (WoH) human hair are investigated by tests as per ASTM standards. The property characterization, including tensile, flexural, and impact strength, as well as hardness, is evaluated by testing. The bonding between fiber and matrix is investigated by SEM. The specimens are obtained from the fabricated composite sheets by cutting as per the required size and dimensions.
Tensile strength
The tensile strength of the fabricated composites is determined by the test as per ASTM D638–14 standards. For each composite, three dog-bone-shaped specimens are tested in the Hounsfield UTM (System ID 3369J8567, max capacity of 50 kN). Tensile force is applied to the specimens at a 2 mm/min strain rate until failure. The length of the narrow section of the dog-bone-shaped specimen was 25 mm. The specimens and their tensile tests are shown in .
Flexural strength
The flexural strength of the composites is determined by three-point bending test as per ASTM-D790-00 standards using Hounsfield H10KS UTM. The length of the specimens between the support spans was 52.4 mm and 51.2 mm for the “Jute and BNH” and “Human hair, Jute and BNH” fiber-reinforced composites, respectively. Bending load is applied to the specimens at a rate of 2.0 mm/min until failure. The bending test and failure mode of the specimens are shown in .
Figure 3. Bending test: (a) specimens of jute and BNH fibers composites and (b) failure mode of specimens; (c) specimens of human hair, jute and BNH fibers composites and (d) failure mode of specimens; (e) Hounsfield H10KS UTM (range 10 kN).
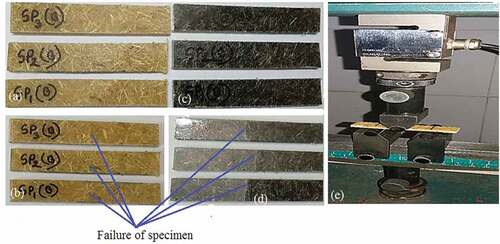
The following two equations are used to find the flexural strength and modulus of the fabricated composites,
where, E = Flexural modulus, σ = Flexural strength, L = Distance between support spans, w = Width of beam specimen, t = Thickness of beam specimen, I = Moment of inertia of the beam specimen, δ = Mid-span deflection and P = Applied force to the specimens. The value of is found from the slope of the force vs. deflection graph. The bending strength (σ) of the composites is calculated using the highest value of “P” of the respective graph.
Impact strength
The impact strength is the energy required to fracture the composites under impact load. It is evaluated as per ASTM D4812 standards using an Izod Impact Tester (QPI-IC-21J). Rectangular specimens of 64.0 mm x 12.9 mm are used in the tests without notches, which allow specimens to fracture through its weak-strength zone instead of a predefined location. Specimens are held vertically by clamping the anvil, as shown in . During free fall, the striker of the pendulum hits the specimens in a direction perpendicular to the longitudinal axis. The impact energy is determined based on the per unit width of the specimens and by taking the average of three. The impact test and failure mode of the specimens are shown in .
Hardness test
The 12 mm x 12 mm specimens are used to test the hardness of the composites. Hardness is determined in the Shore-D scale by the Durometer as per ASTM D2240 standards. The higher number represents the higher hardness in the Shore-D scale.
Void calculation
Composites are primarily composed of liquid resins and reinforcement fibers. During resins solidification, the air bubbles are trapped in the composites and create voids (Cilley, Roylance, and Schneider Citation1974; Saman Citation2020). It represents the weaker bonding between the fibers and matrix interfaces; and reduces the mechanical strength and fatigue life of composites significantly (Saman Citation2020). In this study, composites are fabricated by hand lay-up methods, and checking void content is vital. The voids in the composites can be characterized by density measurement technique, microscopic imaging, radiography, ultrasound, etc. (Saman Citation2020). In this study, the void contents are determined by the density measurement technique. The theoretical value of density of the fibers, matrix, and hardeners is used in the calculation, and the result is justified by Scanning Electron Microscopy (SEM). The following equations are used to calculate the voids in the composites (Nanda and Satapathy Citation2017).
where and
is weight fractions of the fibers and matrix.
,
and
are the density of the fibers, matrix, and composites, respectively.
and
are the actual density and volume fraction of voids in composites. The actual density,
is calculated based on the volume and weights of fibers and the matrix used to fabricate the composites.
Results and discussion
Tensile strength
The stress-strain curves of the fabricated composites are shown in , and a magnified view of the initial stage of tensile loading is shown in . The modulus of elasticity and toughness are determined from the slope and area under the same stress-strain curve, respectively. The tensile strength of the composites is determined from the highest point of the respective stress-strain curve. The modulus of elasticity (E), tensile strength (σut), and modulus of toughness (Gt) of the “Jute and BNH” fiber-reinforced polyester (WoH) composites are found 0.61 GPa, 9.68 MPa, and 85 kJ/m3, respectively. However, for “Human hair, Jute and BNH” fiber-reinforced polyester (WH) composite, those values are found 1.07 GPa, 22.05 MPa, and 269.33 kJ/m3, respectively, shown in .
Figure 5. (a) Stress-strain curves of jute and BNH (WoH), and human hair, jute and BNH (WH) fibers reinforced polyester composites, and (b) stress-strain curves at initial stage of loading.
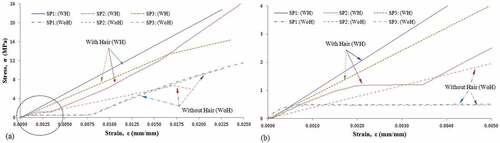
Figure 6. (a) Modulus of elasticity (E), (b) tensile strength (σut) and (c) modulus of toughness (Gt).
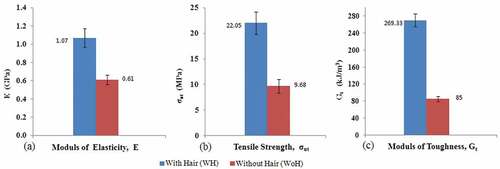
It is observed that the “Jute and BNH” fiber-reinforced (WoH) composite takes a while to pick up the tensile load by the specimens. It takes longer to transfer load from the fibers to the matrix and vice versa. However, in the “Human hair, Jute and BNH” fiber-reinforced (WH) composite, the tensile load transfers immediately and uniformly throughout the specimen. It picks up the tensile load quickly, even at the initial stage. The stress-strain curves of human hair-embedded (WH) composites are found much stiffer than the non-embedded ones (WoH). Due to the addition of human hair in the “Jute and BNH” fiber-reinforced polyester composites, mechanical strengths such as E, σut, and Gt are increased by 75.4%, 127.8%, and 217.8%, respectively, though fiber loading remains the same. Human hair has a high coefficient of friction and hydrophobic characteristics (Gupta Citation2014; Tang et al. Citation2016; Velasco et al. Citation2009), which improves the interlocking and binding between the fibers and matrix, as well as better stress distribution at the interfaces (Kumar et al. Citation2015; Selvakumar and Meenakshisundaram Citation2019). In addition, human hair helps to control micro-cracking and brings ductility to the composites (Kumar et al. Citation2015). Moreover, it has higher tensile strength than other natural fibers and offers resistance to stretching (Gupta Citation2014; Velasco et al. Citation2009). Therefore, in this study, the tensile strength of the human hair-embedded (WH) composites are found much higher than the non-embedded ones (WoH). The mechanical properties of the fabricated composites are shown in . This study agrees with the investigations of Selvakumar and Meenakshisundaram (Citation2019), where the tensile strength of jute (25% by volume) and human hair (0% by volume) reinforced epoxy composites is found 16 MPa, and for 0% jute and 25% human hair by volume is found 23.5 MPa. Due to the addition of hair, the tensile strength of the composites is increased by 46.88%. In the study by Nanda and Satapathy (Citation2017), the tensile strength of short human hair reinforced epoxy composites is also improved by 95.38% (from 65 MPa to 127 MPa) for raising the hair weight fraction from 0 to 8%. This study’s results are consistent with Selvakumar and Meenakshisundaram (Citation2019) and Nanda and Satapathy (Citation2017) investigations. Since the composites in this study are fabricated by the hand lay-up method, the variation of tensile strength between the specimens is unavoidable and expected.
Table 2. Mechanical Properties of the Fabricated Composites.
Flexural strength
The flexural load vs. deflection curves of the fabricated composites are shown in . It is found stiffer for the “Human hair, Jute and BNH” fiber-reinforced (WH) composites than the “Jute and BNH” fiber-reinforced (WoH) composites. At the initial loading stage, the human hair-embedded (WH) composites pick up the load quickly due to the better bonding and load distribution at the fiber and matrix interfaces. The flexural strength and modulus for the “Jute and BNH” fiber-reinforced composites (WoH) are found 31.82 MPa and 1.82 GPa, respectively. However, it is found 58.99 MPa and 4.25 GPa for the human hair-embedded (WH) composites, respectively, as shown in . Due to the adding human hair in the composites, flexural strength and modulus are increased by 85% and 133%, respectively, though the fiber loading remains the same.
Figure 7. (a) Flexural load-deflection curves of jute and BNH (WoH) and human hair, jute and BNH (WH) fibers reinforced polyester composites, and (b) flexural load-deflection curves at initial stage of loading.
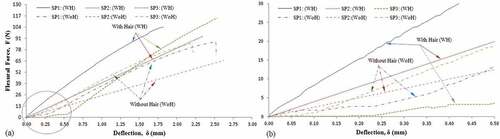
Human hair enhances the compressive strength and fracture-resilience of composites (Gupta Citation2014) and bonding between the fiber and matrix interfaces (Selvakumar and Meenakshisundaram Citation2019). In this study, the tensile strength of the human hair-embedded composites (WH) is also found higher than the non-embedded one (WoH). As a result, the flexural strength and flexural modulus of the human hair-embedded (WH) composites are increased remarkably compared to the non-embedded ones (WoH). In the study of Nanda and Satapathy (Citation2017), the flexural strength of short human hair reinforced epoxy composites is increased by 82.76% (from 58 MPa to 106 MPa) due to the increasing hair weight fraction of composites from 0% to 8%. Kumar et al. (Citation2015) also found that the flexural strength of human hair-reinforced concrete increased by 23.62% (from 4.53 MPa to 5.60 MPa) due to the addition of human hair from 0 to 1.5% by weight. Although the mechanical properties of the same composites with identical fibers, fiber ratio, and matrix are not available, this study’s results are consistent with the investigations of Nanda and Satapathy (Citation2017) and Kumar et al. (Citation2015). Since the hand lay-up method is used in this study to fabricate the composites, the variation of flexural strength between the specimens is inevitable and likely.
Impact strength
The impact strength of the “Human hair, Jute and BNH” and “Jute and BNH” fiber-reinforced composites is found 0.0187 J/mm and 0.0086 J/mm, respectively, as shown in . It is found 117% higher in human hair-embedded composites (WH) than the non-embedded ones (WoH). Human hair enhances bonding at the fiber-matrix interfaces, micro-cracking control (Kumar et al. Citation2015), compressive strength, and fracture resilience (Gupta Citation2014) of the composites. Therefore, the energy absorption capacity of hair-embedded composites (WH) is much higher than the non-embedded ones (WoH), which is expected and justified. In the study of Selvakumar and Meenakshisundaram (Citation2019), the impact strength of the human hair reinforced epoxy composites is improved tremendously (from 0.3 to 4.25 joules) due to the increasing human hair content from 0% to 25% by volume. Verma and Singh (Citation2019) also found that the impact strength of the composites increased significantly for adding human hair. The impact test results of this study agree with the investigations of Selvakumar and Meenakshisundaram (Citation2019) and Verma and Singh (Citation2019).
Hardness test
The hardness of the fabricated composites is measured in the Shore-D scale. It is found 69.3 and 58.3 for “Human hair, Jute and BNH” and “Jute and BNH” fiber-reinforced composites, respectively, as shown in . Human hair increases the spalling and stretching resistance of the composites (Kumar et al. Citation2015). In addition, its hydrophobic nature improves the bonding and interlocking between the fiber and matrix interfaces (Selvakumar and Meenakshisundaram Citation2019). Therefore, the hardness of the human hair-embedded composites (WH) is found much higher than the non-embedded ones (WoH). It is logical and indicates the appropriateness of this study. Verma and Singh (Citation2019) revealed that the hardness of epoxy-based composites increased for adding human hair. In addition, there is a linear relationship between hardness and compressive strength. The mechanical properties of composites with identical fibers, fiber ratio, and matrix as of this study are not available. However, research by Nanda and Satapathy (Citation2017) and Kumar et al. (Citation2015) shows that adding human hair increases the compressive strength of the composites, which is in line with the results of this study. Since the hardness of composites with human hair increases by 18.87% in this investigation.
Void content
The void content is measured 0.21% in the “Human hair, Jute and BNH” fiber-reinforced (WH) composites and 0.56% in the “Jute and BNH” fiber-reinforced (WoH) composites. Due to hydrophobic characteristics, human hair increases the bonding and interlocking at the matrix and fibers interfaces (Selvakumar and Meenakshisundaram Citation2019). As a result, human hair-embedded (WH) composite has fewer voids, strong bonding, and higher mechanical strength such as tensile, flexural, impact, and hardness than the non-embedded ones (WoH), as shown in . Since Liquid Composite Molding (LCM) is used to fabricate most composites, the void in the composites can be reduced by controlling pressure, temperature, resin viscosity, and curing time (Cilley, Roylance, and Schneider Citation1974). Composites are fabricated by the hand lay-up method; some voids in both (WH and WoH) composites are unavoidable. However, it is found insignificant and within the acceptable limits (7% to 8%) of polyester composites (Hamdan et al. Citation2019; Shah et al. Citation2012). In the study of Nanda and Satapathy (Citation2017), the void contents of short human hair reinforced epoxy composites are found 0.9% and 1.9% for the 0% and 8% human hair content by weight, respectively. However, in this study, the void contents found 0.21% in the human hair-embedded (WH) composites and 0.56% in the non-embedded ones (WoH), which indicates the achievement of strong bonding between the fibers and matrix and appropriateness of this study.
Morphological analysis of composites
The surface morphology, such as bonding between fibers and matrix, voids, microcracks, crack propagation, and fiber agglomeration in composites, are investigated by Scanning Electron Microscopy (SEM). The surface characteristics and internal structure of the tensile fractured specimens are shown in . The fibers are identified in the composites by investigating the SEM image. The “Jute and BNH” fiber-reinforced (WoH) composites, shown in , have more microcracks and voids than the “Human hair, Jute, and BNH” fiber-reinforced (WH) composites, shown in . The BNH fiber has more cracks than the jute fiber and human hair since it has the lowest tensile strength, which reveals the appropriateness of this study. The bonding and interlocking between the polyester and human hair are found more robust than the jute and BNH fiber. It happened due to the hydrophilic nature and high friction coefficient of human hair. Therefore, the mechanical properties, such as tensile and flexural strength, modulus of elasticity, modulus of toughness, impact strength, and surface hardness, are higher in the human hair-embedded (WH) composites than the non-embedded ones (WoH). The investigation of SEM images of the composites confirms the accuracy of this study. It also agrees with the experimental findings of Selvakumar and Meenakshisundaram (Citation2019).
Conclusion
This study revealed that the mechanical properties of human hair-embedded natural fiber-reinforced composites (with hair – WH) are remarkably higher than the non-embedded ones (without hair – WoH); even fiber loading remains the same, as shown in . The SEM images revealed that bonding in the hair-embedded (WH) composites is more robust, with fewer voids and cracks than non-embedded ones (WoH). The strength of a particular natural fiber-reinforced polymer composite can be enhanced significantly by adding human hair. Therefore, the wood and synthetic fiber-based composites can be replaced by human hair-embedded natural fiber-reinforced composites, which will reduce the pollution and greenhouse effect. This study expands the scope of human hair as a low-cost composites constituent and the application of human hair-embedded composites in different engineering fields such as automobiles, aerospace, home building, furniture, boats, etc. Since human hair-embedded composites have high energy absorption capacity, strength, and hardness, it could be used in the automobile to fabricate door panels, seat backs, dashboards, linings, IC engine covers and insulation, roof covers, cargo floor trays; the non-structural and secondary structure of aircraft, interior partitions, and insulation panels in home building, boat construction, etc. In addition, there is scope to investigate thermal and fatigue analysis of the human hair-embedded natural fiber-reinforced composites, which will widen its application further.
Highlights
Two unique hybrid polyester composites with identical fiber loading are fabricated by the hand lay-up method – the first one with jute and BNH fibers and the second one with human hair, jute, and BNH fibers.
Tensile, flexural and impact strengths, and hardness are significantly higher in the human hair-embedded composites than in the non-embedded ones.
Human hair-embedded composites have stronger bonding, fewervoids and microcracks, and higher energy absorption capacity than non-embedded ones.
The strength of natural fiber-reinforced polymer composites could be enhanced significantly by adding human hair as a low-cost constituent, which will reduce environmental pollution and greenhouse effects.
Thermal and fatigue analysis of the human hair-embedded natural fiber-reinforced composites will widen its application.
Acknowledgements
The authors want to thank for financing and supporting this work in all respect from the Department of Mechanical and Production Engineering (MPE) of Ahsanullah University of Science and Technology (AUST), Tejgaon Industrial Area, Dhaka, Bangladesh.
Disclosure statement
No potential conflict of interest was reported by the author(s).
References
- Binoj, J. S., R. E. Raj, V. S. Sreenivasan, and G. R. Thusnavis. 2016. Morphological, physical, mechanical, chemical and thermal characterization of sustainable Indian areca fruit husk fibers (areca catechu l.) as potential alternate for hazardous synthetic fibers. Journal of Bionic Engineering 13 (1):156–14. doi:10.1016/S1672-6529(14)60170-0.
- Cilley, E., D. Roylance, and N. Schneider. 1974. “Methods of fiber and void measurement in graphite/epoxy composites.” In Composite Materials: Testing and Design (Third Conference), ASTM STP, Philadelphia, 546:237–49.
- Gupta, A. 2014. Human hair ‘waste’ and Its utilization: Gaps and possibilities. Journal of Waste Management 2014:1–17. doi:10.1155/2014/498018.
- Hamdan, M., M. Hazim, J. Parlaungan Siregar, S. Thomas, M. John Jacob, J. Jaafar, and C. Tezara. 2019. Mechanical performance of hybrid woven jute–roselle-reinforced polyester composites. Polymers and Polymer Composites 27 (7):407–18. doi:10.1177/0967391119847552.
- Khan, M. Z. R., S. K. Srivastava, and M. K. Gupta. 2018. Tensile and Flexural Properties of Natural Fiber Reinforced Polymer Composites: A Review. Journal of Reinforced Plastics and Composites 37 (24):1435–55. doi:10.1177/0731684418799528.
- Kumar, T. N., K. Goutami, J. Aditya, K. Kavya, and V. R. Mahendar, Dr. R. C. Reddy, and S. Kaushik. 2015. An experimental study on mechanical properties of human hair fibre reinforced concrete (M-40 grade). IOSR Journal of Mechanical and Civil Engineering (IOSR-JMCE) 12 (4):65–75. Dr. doi:10.4028/scientific.net/AMM.405-408.2767.
- Kumar, N., A. Singh, and R. Ranjan. 2019. “Fabrication and mechanical characterization of horse hair (HH) reinforced polypropylene (PP) composites.” Materials Today: Proceedings 19: 622–25. doi:10.1016/j.matpr.2019.08.078.
- Lazim, Y., S. Mohd Salit, E. Syams Zainudin, M. Mustapha, and M. Jawaid. 2014. Effect of alkali treatment on the physical, mechanical, and Morphological properties of waste betel nut (areca catechu) husk fibre. BioResources 9 (4):7721–36. doi:10.15376/biores.9.4.7721-7736.
- Mangalgiri, P. D. 1999. Composite materials for aerospace applications. Bulletin of Materials Science 22 (3):657–64. doi:10.1007/BF02749982.
- Manivannan, J., S. Rajesh, K. Mayandi, N. Rajini, S. O. Ismail, F. Mohammad, M. Kitek Kuzman, and A.A.L. Hamad. 2020. Animal fiber characterization and fiber loading effect on mechanical behaviors of sheep wool fiber reinforced polyester composites. Journal of Natural Fibers (11):1–17. doi:10.1080/15440478.2020.1848743.
- Muralidhar, N., V. A. Kaliveeran, V. Arumugam, I. Srinivasula Reddy. 2019. A study on areca nut husk fibre extraction, composite panel preparation and mechanical characteristics of the composites. Journal of the Institution of Engineers (India): Series D:135–45. doi:10.1007/s40033-019-00186-1.
- Nanda, B. P., and A. Satapathy. 2017. “Processing and characterization of epoxy composites reinforced with short human hair.” In IOP Conference Series: Materials Science and Engineering, 178:012012. doi:10.1088/1757-899X/178/1/012012.
- Oladele, I. O., and N. I. Agbeboh. 2017. Development of mathematical models and estimation for the mechanical properties of organic fiber reinforced polyester composites. Fibers and Polymers 18 (7):1336–45. doi:10.1007/s12221-017-1064-2.
- Rahman, F., M. Ashabul Eiamin, M. Rakib Hasan, M. M. H. Md Shariful Islam, M. A. Gafur, and S. A. Dhar. 2020. Effect of fiber loading and orientation on mechanical and thermal properties of jute-polyester laminated composite. Journal of Natural Fibers 1–15. doi:10.1080/15440478.2020.1788485.
- Rao, P., C. U. K. Divakara, and K. Eshwara Prasad. 2018. Tensile studies on random oriented human hair fiber reinforced polyester composites. Journal of Mechanical Engineering 47 (1):37–44. doi:10.3329/jme.v47i1.35357.
- Rowell, R. M. 2008. Natural Fibres: Types and Properties. Properties and Performance of Natural-Fibre Composites 3–66. doi:10.1533/9781845694593.1.3
- Saman, F. 2020. Void content computation using optical microscopy for carbon fiber composites. KTH School of Engineering Sciences, Stockhom, Sweden.
- Saxena, M., A. Pappu, R. Haque, and A. Sharma. 2011. Sisal fiber based polymer composites and their applications. Cellulose Fibers: Bio- and Nano-Polymer Composites: Green chemistry and technology, 589–659.
- Selvakumar, K., and O. Meenakshisundaram. 2019. Mechanical and dynamic mechanical analysis of jute and human hair-reinforced polymer composites. Polymer Composites 40 (3):1132–41. doi:10.1002/pc.24818.
- Shah, D. U., P. J. Schubel, P. Licence, and M. J. Clifford. 2012. Determining the minimum, critical and maximum fibre content for twisted yarn reinforced plant fibre composites. Composites Science and Technology 72(15): doi:10.1016/j.compscitech.2012.08.005. Elsevier Ltd: 1909–1917.
- Tang, W., S. G. Zhang, J. K. Zhang, S. Chen, H. Zhu, and S. R. Ge. 2016. Ageing effects on the diameter, nanomechanical properties and tactile perception of human hair. International Journal of Cosmetic Science 38 (2):155–63. doi:10.1111/ics.12269.
- Trade, I. 2021. MEKP Catalyst in Rajajinagar Industrial Town. Aryan Composites Private Limited. Available: https://www.tradeindia.com/products/mekp-catalyst-c4745312.html.
- Velasco, M. V. R., T. Cristina de Sá Dias, A. Zanardi de Freitas, N. D. Vieira Júnior, C. Aparecida Sales DeOliveira Pinto, T. M. Kaneko, and A. R. Baby. 2009. Hair fiber characteristics and methods to evaluate hair physical and mechanical properties. Brazilian Journal of Pharmaceutical Sciences 45 (1):153–62. doi:10.1590/S1984-82502009000100019.
- Venkateshappa, S. C., B. Bennehalli, M. Gadde Kenchappa, and R. Patel Gowda Ranganagowda. 2010. Flexural behaviour of areca fibers composites. BioResources 5 (3):1846–58. doi:10.15376/biores.5.3.1846-1858.
- Verma, A., and V. K. Singh. 2019. Mechanical, microstructural and thermal characterization of epoxy-based human hair-reinforced composites. Journal of Testing and Evaluation 47 (2):1193–215. doi:10.1520/JTE20170063.
- Verma, A., V. K. Singh, and A. Sharma. 2016. Human Hair: A biodegradable composite fiber–a review. International Journal of Waste Resources 6 (2). doi: 10.4172/2252-5211.1000206.
- Yang, Y., W. Yang, B. Wang, and M. André Meyers. 2017. Structure and mechanical behavior of human hair. Materials Science and Engineering: C 73:152–63. doi:10.1016/j.msec.2016.12.008.
- Yusriah, L., S. M. Sapuan, E. S. Zainudin, and M. Mariatti. 2014. Characterization of Physical, mechanical, thermal and morphological properties of agro-waste betel nut (areca catechu) husk fibre. Journal of Cleaner Production 72:174–80. doi:10.1016/j.jclepro.2014.02.025.