ABSTRACT
In the framework of environment-friendly materials, natural fiber polymer matrix composites are in demand in the current years. Natural fiber-reinforced polymer matrix composites (NFRPCs) involved massive attention to the industries and academia due to their excellent strength, modulus of elasticity, and Tribo properties. This article focuses on the application of natural fiber-reinforced composite materials in many engineering systems and the effect of different material parameters – like the length of the fiber, fiber weight fraction, fiber surface treatment, fiber orientation, etc., and different operating parameters – like load, speed, sliding distance, temperature, etc., on the friction and wear behavior of the NFRPCs. The different wear mechanisms and the principle used in wear test rigs are also presented, aiming to showcase a scope of composite as Tribo material and highlight further research directions to accomplish a comprehensive outline on the tribo behavior of various natural fiber-reinforced composite materials.
摘要
在环保材料的框架下,天然纤维聚合物基复合材料是近年来的需求. 天然纤维增强聚合物基复合材料(NFRPC)因其优异的强度、弹性模量和摩擦学性能而受到工业界和学术界的广泛关注. 本文重点介绍了天然纤维增强复合材料在许多工程系统中的应用,以及不同材料参数(如纤维长度、纤维重量分数、纤维表面处理、纤维取向等)和不同操作参数 (如载荷、速度、滑动距离、温度、,等对NFRPC的摩擦和磨损行为的影响. 还介绍了不同的磨损机理和磨损试验台中使用的原理,旨在展示复合材料作为摩擦材料的范围,并强调进一步的研究方向,以全面概述各种天然纤维增强复合材料的摩擦行为.
1. Introduction
Tribology relates to the friction, wear, and lubricating conditions between two matching surfaces. Friction usually produces energy loss, leading to the material removal called wear (Parikh and Gohil Citation2019). Wear and friction are interconnected; however, growing friction does not always produce wear loss (Parikh and Gohil Citation2015). Wear and friction are not always unfavorable; in some cases, it is required for the efficient performance of the elements, this called productive friction and wear. Few unproductive and productive frictions and wear examples are shown in .
One of the main reasons for any engineering part failure is friction and wear between interacting surfaces. Thus, there is a need to study the tribological behavior of the components (Milosevic, Valášek, and Ruggiero Citation2020). Conventional materials are extracted from a lengthy metallurgical process and are limited in nature. Growth in urbanization caused deforestation, which is alarming for the balanced ecosystem. There is an increasing demand for new materials, which can work in severe pressure, temperature, and corrosive conditions. So, there is a need to develop a new material that can cater to all these requirements; this has triggered the concept of composite material (Pachta et al. Citation2014). Composite materials are currently on rise nowadays due to their high strength, low weight, high corrosion resistance, high fatigue strength, etc. (Shahinur and Hasan Citation2020). Polymer composites have huge demand because of their self-lubricating properties, corrosion resistance, and lightweight properties (Periyasamy, Ramamoorthy, and Lavate Citation2019). Nowadays, plant-based natural fibers are in demand in industrial and structural applications because of their ease of accessibility, low cost, less weight, biodegradability, and low density over synthetic fibers (Khot and Kumar Citation2021). Plants, animals are the primary source of natural fibers as it is plotted in according to Saxena et al. (Citation2011).
Many natural fibers polymer composites give compatible properties with synthetic fibers reinforced composites and are used in many engineering systems listed in ; however, natural fibers have certain drawbacks like high moisture absorption – hydrophilic nature, less strength than synthetic fibers, variation in properties based on harvesting place, time and season. These negatively impact the tribo mechanical behavior of the natural fiber polymer composite material (Balla et al. Citation2019; Ruggiero, Valášek, and Müller Citation2016). Surface treatment of fibers or the addition of fillers during composite material manufacturing reduces its hydrophilic nature.
Table 1. Applications of NFRCs.
As such, Tribo tests on natural fiber reinforced, composites are critical for the better performance of tribological systems. Initially, Tribo testing is performed at laboratory level. In this process, a selection of proper geometry, contact surface, load, sliding speed, and contact pressure, wear/friction analysis is carried out. Most common contact configurations include a pin on flat, flat on flat, rotating pin on disc, pin on rotating disc, cylinder on a cylinder, pin on rotating cylinder, etc. (Chand and Fahim Citation2020).
In the present study, the author has focused on tribo behavior of different natural fiber polymer composites and studied the effect of various material parameters like length of the fiber, orientation of fiber, fiber weight fraction, fiber treatment, fiber type, etc., and various operating parameters like speed, temperature, load, sliding distance, etc., on friction and wear behavior of composite material.
2. Tribology in NFRPCs
Tribology relates to the study of wear, friction, and lubrication between two interacting surfaces. Friction is an essential aspect of life. The discovery of fire is due to friction, which has changed human life. We cannot imagine our life without friction. But the friction creates an adverse effect in the machinery lead to wear. Wear is a gradual loss of material from the operating surfaces, which causes vibration, misalignment, noise, dimensional changes, cracks, and finally leads to the failure of parts (Aldousiri, Shalwan, and Chin Citation2013; Basavarajappat Citation2005; Fernández et al. Citation2003). Some most common wear mechanisms are abrasive, adhesive, erosive, and corrosive. A comprehensive view of different wear mechanisms, their application areas, and research on the materials by researchers is listed in .
Table 2. Wear mechanisms.
The majority of the mechanical elements fail due to abrasive and adhesive wear, leading to the shutdown of industry (Hashmi, Dwivedi, and Chand Citation2007). Different wear test rigs used to measure adhesive and abrasive wear with their working principle are shown in .
Table 3. Wear test rigs (Parikh and Gohil (Citation2015)).
The unproductive wear and friction cannot be recovered totally, but choosing the right tribo pair can be reduced to a possible range. Nowadays, composite materials are in demand as Tribo material, which reveals significant wear resistance.
3. Friction and wear of NFRPCs
Tribo behavior of natural fiber reinforced polymer matrix composites has been evaluated by numerous researchers (Goriparthi, Suman, and Rao Citation2012; Nirmal et al. Citation2010; Raghavendra et al. Citation2014; Rodríguez-Tembleque and Aliabadi Citation2014; Shireesha and Nandipati Citation2019; Xess Citation2012; Yallew, Kumar, and Singh Citation2014). Tribological properties of the NFRPCs are affected by various material parameters and operating parameters. An overview based on the literature survey on various plant-based fibers is presented below.
3.1. Jute fiber
Jute fiber is obtained from the bast of the plant (Corchorus capsularis and Corchorus olitorius). Jute polymer composites – Jute/epoxy, jute/polyester, jute/polypropylene – were developed by researchers for different applications like low-cost housing, small fishing boat, etc. As the jute fiber mainly consists of cellulose, surface treatment of the fibers plays a significant role in enhancing the composite material’s performance. The abrasive wear behavior of jute fiber reinforced polyester composites under the effect of coupling agent was studied by Chand and Fahim (Citation2020) and revealed its effect with scanning electron microscopy. The test results showed that the coupling agent enhances the wear resistance of the composite material. Effect of surface treatment and jute fiber orientations on the friction and wear behavior of the material were studied by researchers and revealed its sound effect on the tribo behavior of the material (Acha, Marcovich, and Reboredo Citation2005; Dwivedi and Chand Citation2009). Jute fiber reinforced polyester composites were used in bearing and evaluating the effect of fiber volume fraction and fiber orientation on the tribo behavior of the composite material (El-Sayed et al. Citation1995). The test results revealed that 33% volume fraction of fiber increased the friction coefficient by 14% and reduced the wear rate by 95% for normal fiber orientation.
3.2. Coir fiber
The coir fiber is a fruit fiber obtained from the husk of coconut trees. Coconut is found in many parts of the world; most coir fibers come from India, Sri Lanka, Malaysia, the Philippines, and Indonesia. Due to the increasing demand for coconut products, waste products from the coconut fruit is also increasing. The coir fiber is mainly used for producing ropes, yarns, mats, rugs, etc. However, only a tiny portion of the coconut husk is utilized for total coconut husk production. So, many researchers are working on the tribological and mechanical behavior of the coir fibers to make valuable industrial products (Ayrilmis et al. Citation2011).
Aireddy and Mishra (Citation2011) have studied the erosive and abrasive wear behavior of coir-filled epoxy matrix composites with different impingement angles and various impact velocities for silica of 200 to 600-micron size. Erosive wear is reduced with the increased coir dust. The abrasive wear was studied on a pin on a disc wear tester for different loading conditions. The test results revealed that with increasing fiber concentration, wear resistance of the material increases for higher loading conditions (Yan, Su, and Chouw Citation2015). Many researchers evaluated the result of fiber treatment on the wear performance of coir fiber epoxy composites with varying fiber weight fractions. All the research reach to same conclusion that fiber treatment and fiber weight fraction substantially influence the wear behavior of the composite material (Adeniyi et al. Citation2019; Khan et al. Citation2014; Rao et al. Citation2012; Valášek et al. Citation2018). Yousif (Citation2009) has studied the friction and wear behavior of coir reinforced polyester composites. The test results revealed that weight fraction of fibers has significant effect on the friction and wear behavior of the material.
3.3. Sisal fiber
Sisal fiber is removed from the plant leaves. More commonly found in South America specially in Brazil and North America, particularly in West Indies. The soil rich in magnesium, potassium, nitrogen, and phosphorus is preferred for the sisal. Different types of sisal plants are found across the world. Fibers obtained from the plant depend on the time, place, and season of harvesting. Sisal is one of the most commonly used natural plants, and it is easily cultivated. The fibers have good strength, good elasticity, and good resistance against corrosion; however, they degrade quickly due to their hydrophilic nature when exposed to the environment (Balla et al. Citation2019). The fiber treatment can reduce the hydrophilic effect nature of the fiber. Priyanka (Citation2013) has studied the result of fiber treatment on the composite material’s moisture absorption behavior and mechanical behavior. The author has revealed that the alkaline treatment enhanced the moisture absorption behavior of the material and improved mechanical behavior. Short sisal fiber-reinforced epoxy composites were studied for various loads, sliding distances, and sliding speeds. The test results revealed that all three variables substantially affect the wear behavior of composite material (Maurya, Jha, and Tyagi Citation2017; Vigneshkumar and Rajasekaran Citation2018). Sisal and glass hybrid composites were prepared and evaluated for tribological characterization. These studies revealed the natural fiber as the potential substitute for synthetic fibers in Tribo composites (Aslan, Tufan, and Küçükömeroğlu Citation2018; Gehlen et al. Citation2020). Sisal fibers with diverse shapes, namely undulated, spiral, and straight shapes, were combined with resin to evaluate the effect of different shapes of natural fibers on the composite’s tribological, morphological, and mechanical performance. Friction composites are prepared using binders, reinforcements, fillers, and friction modifiers using the compression molding process. The test results revealed that the helical-shaped sisal fibers showed better tribological behavior than undulated and straight shape fibers (Wu et al. Citation2021).
3.4. Sugar cane fiber
Sugarcane is commonly found in tropical areas, and the fibers remain as residue after extracting juice from the stalks of sugarcane. Because of its low cost, it is usually used as fuel to produce energy, and nowadays, it is more commonly used as filler to produce composite materials. Various chemical treatments like silane and alkaline treatment modify the fiber’s surface for proper adhesion with the matrix material and improve mechanical strength, acoustic properties, and aging properties of the composite material. Sugarcane ash as filler material in concrete gives thermal stability to the structure at elevated temperatures (Devadiga, Bhat, and Mahesha Citation2020). The wear rate of sugarcane fiber polyester composites was evaluated for different fiber lengths and compared with the glass fiber composite. A dry sliding wear test was performed at a speed of 2.5 m/s, 2.25 km sliding distance, and ambient temperature conditions. The wear resistance of chopped sugar cane fibers reinforced composites plotted for various loading conditions compared with chopped glass fiber polyester composites (CGRP) is shown in .
Figure 3. Wear behavior of glass and sugarcane fiber composites (El-Tayeb Citation2008).

The test results revealed higher wear resistance and a higher coefficient of friction for composites reinforced with sugarcane fiber than for those reinforced with glass fiber. Therefore, the composite reinforced with sugarcane fiber is a more promising material than the one reinforced with glass fiber (El-Tayeb Citation2008). Wear behavior of chopped sugarcane fiber polyester composites (C-SCRP) with varying fiber length was evaluated. Less abrasive wear was observed for small fiber length (1 mm), and higher wear was observed with the increasing length of the fiber. Advanced optimization techniques are used to determine the optimum fiber length for abrasive wear conditions. The suggested best size of the fiber length is 7–8 mm for minimum abrasive wear (Mahapatra and Chaturvedi Citation2009). Fiber orientation plays a vital role in controlling the wear of the material. indicates the influence of normal orientation (NO), antiparallel orientation (APO), and parallel orientation (PO) of unidirectional sugarcane fiber/polyester composite on the abrasive wear behavior. The wear rate was evaluated for 150, 180, 320, and 400 grit sizes and revealed that wear rate is strongly affected by load and grit size and increased with growing load and grit size (Mishra and Acharya Citation2010).
Figure 4. Influence of Fiber orientation on wear performance of sugarcane composites (Mishra and Acharya Citation2010).
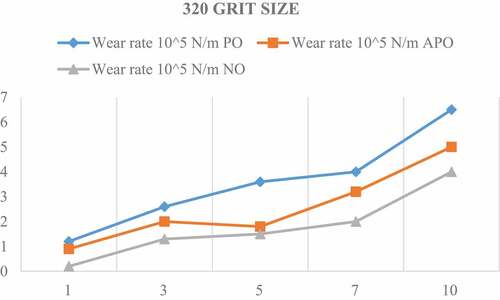
3.5. Cotton fiber
Cotton belongs to the genus Gossypium, sub-tribe Hibisceae family Malvaceae and it is a vital farming crop. It is most commonly used in clothing and has high demand worldwide. Also, its strength and easy blending characteristics with the other fibers make it more favorable for fibers to produce composite materials.
Graphite, fly ash, and SiC fillers with varying weight fractions (0, 3, 5 wt. percentage) were used with cotton fiber reinforced polyester composites for evaluating composite friction properties. The experiments results revealed that the different weight concentration of fillers has a significant effect on the friction behavior of the material. As the weight fraction of SiC is increased from 3% to 5%, coefficient of friction increased due to more uniform distribution of fillers gave good adhesion, shown in ; on the other hand, the increasing weight fraction of fly ash from 3% to 5% and graphite fillers from 3% to 5% reduce the coefficient of friction. The higher weight fraction of fillers showed a more uniform fillers distribution in (Parikh and Gohil Citation2021).
Figure 5. SEM Image of A) Graphite B) SiC C) Flyash filled cotton fiber reinforced polyester composites (Parikh and Gohil Citation2021).
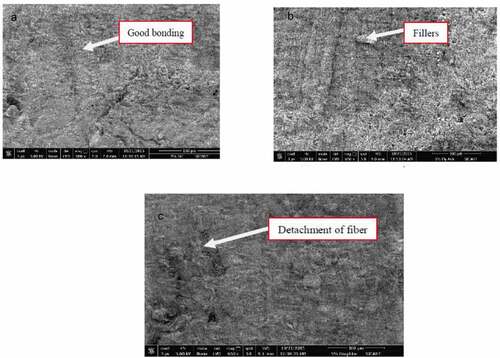
3.6. Banana fiber
Tropical plant banana belongs to the genus Musa, family Musaceae. Mainly four types of Musa varieties are cultivated for the fruits – Sentuluvan, Aethalpalal, Rasagatali, and Palayannkottai. Sentuluvan is red and produces red-brown fibers mainly cultivated from southern India. Banana natural fibers are used for making household products like bags, bins, mats, etc. Banana fibers contain 9% lignin, 43.46% cellulose, 38.54% hemicellulose, and exhibit a tensile strength of 142.9 MPa (Jústiz-Smith, Virgo, and Buchanan Citation2008). The studies revealed that when the polymers are reinforced with banana fibers, it improves the mechanical and tribo properties of the polymers (Asabe Popat and Bhosale Citation2017; Idicula et al. Citation2005; Joseph et al. Citation2002; Sapuan et al. Citation2006; Thwe and Liao Citation2002; Zhu et al. Citation1994). Rahul et al. (Citation2017) has revealed that when epoxy is reinforced with banana fibers wear resistance of the epoxy increases. Also, adding the nano fillers like silica and clay further increase the wear resistance of the banana fiber epoxy composites. There is still a vast scope of work in the tribology of banana fiber polymer composites.
3.7. Hybrid/Fillers filled composite
Bio-degradable fibers spectrum is increasing globally in a wide range of applications in many engineering disciplines. Researchers have combined two or more fibers/added fillers to develop more versatile composite materials. The work done by researchers is listed in .
Table 4. Summary of hybrid plant-based fiber reinforced polymer composites.
summarizes the tribological characterization of natural fiber polymer matrix composites (NFRPCs) found in scientific works.
Table 5. Summary – tribological characterization of NFRPCs.
4. Summary
Many plant-based natural fibers (like jute, cotton, coir, sugarcane, banana, sisal), animal fibers, and mineral fibers are used in the different matrices to create an eco-friendly composite material. Plant-based natural fiber polymer composites are getting the attention of several engineering fields, automobile research, and fundamental research. Tribological performance of natural fiber polymer composites is a novel research field as its application directly affects the performance of parts.
Different researchers’ work has been reviewed, and a few points summarized:
The vast scope of FRP composites as Tribo material, without lubricating conditions because of its self-lubricating nature.
The reinforcement of natural fibers in the polymers enhances the wear performance of the polymer matrix composites.
Research reveals the sound effect of material parameters like fiber length, the weight fraction of fiber, fiber surface treatment, fiber arrangement, fillers concentration, etc., on the wear behavior of the composite material. Functioning parameters like load, speed, sliding distance, temperature, etc., also revealed a significant effect on tribo behavior of the NFRPCs.
Tribo – Mechanical properties of natural fibers has revealed that few fiber reinforced composite materials are likely to substitute the synthetic material; however, the evaluation of the tribological and mechanical properties of different composite materials using varying operating parameters allows to achieve a more global and useful overall view of the tribological performance of these materials.
The future scope for further study in the context of tribology of NFRPCs should be underlined in this way: Detailed investigation on tribo behavior of natural fiber polymer composites by changing various material parameters and operating parameters. Development and Tribological characterization of totally environment-friendly biocomposite. Tribological characterization of composites under both dry and wet conditions.
Highlights
A comprehensive discussion on the scope of Natural Fiber Reinforced Polymer Composites as Tribo Material.
An overview of different wear test rigs for Tribo testing.
Emerging applications of Natural Fibers are also analyzed to reduce carbon foot print.
Disclosure statement
No potential conflict of interest was reported by the author.
References
- Acha, B. A., N. E. Marcovich, and M. M. Reboredo. 2005. Physical and mechanical characterization of jute fabric composites. Journal of Applied Polymer Science 98 (2):639–15. doi:10.1002/app.22083.
- Adeniyi, A. G., D. V. Onifade, J. O. Ighalo, and A. S. Adeoye. 2019. A review of coir fiber-reinforced polymer composites. Composites Part B: Engineering 176:107305. doi:10.1016/j.compositesb.2019.107305.
- Aireddy, H., and S. C. Mishra. 2011. Tribological behavior and mechanical properties of Bio-waste reinforced polymer matrix composites. Journal of Metallurgy and Materials Science 53 (2):139–52.
- Ajay, G., and C. Navin. 2007. Abrasive wear behavior of bamboo powder-filled polyester composite. Bioresource Technology 7:693–98.
- Aldousiri, B., A. Shalwan, and C. W. Chin. 2013. A review on tribological behavior of polymeric composites and future reinforcements. Advances in Materials Science and Engineering 2013:1–8. doi:10.1155/2013/645923.
- Arjmandi, R., A. Hassan, K. Majeed, and Z. Zakaria. 2015. Rice husk-filled polymer composites. International Journal of Polymer Science 2015:1–32. doi:10.1155/2015/501471.
- Asabe Popat, B., and S. B. Bhosale. 2017. Development and analysis of natural banana fiber composite. International Journal on Recent and Innovation Trends in Computing and Communication 5 (6):1384–86.
- Aslan, M. U. S. T. A. F. A., M. Tufan, and T. E. V. F. İ. K. Küçükömeroğlu. 2018. Tribological and mechanical performance of sisal-filled waste carbon and glass fibre hybrid composites. Composites Part B: Engineering 140:241–49. doi:10.1016/j.compositesb.2017.12.039.
- Ayrilmis, N., S. Jarusombuti, V. Fueangvivat, P. Bauchongkol, and R. H. White. 2011. Coir fiber reinforced polypropylene composite panel for automotive interior applications. Fibers and Polymers 12 (7):919–26. doi:10.1007/s12221-011-0919-1.
- Balla, V. K., K. H. Kate, J. Satyavolu, P. Singh, and J. G. D. Tadimeti. 2019. Additive manufacturing of natural fiber reinforced polymer composites: Processing and prospects. Composites Part B: Engineering 174:106956. doi:10.1016/j.compositesb.2019.106956.
- Basavarajappat, S. 2005. Wear studies on metal matrix composites: A Taguchi approach. Journal of Materials Science and Technology 21 (6):845–50.
- Boggarapu, V., R. Gujjala, and S. Ojha. 2020. A critical review on erosion wear characteristics of polymer matrix composites. Materials Research Express 7 (2):022002. doi:10.1088/2053-1591/ab6e7b.
- Boopathi, L., P. S. Sampath, and K. Mylsamy. 2012. Influence of fiber length in the wear behavior of Borassus fruit fiber reinforced epoxy composites. International Journal of Engineering Science and Technology 4 (9):4119–29.
- Chand, N., and M. Fahim.2020. Tribology of natural fiber polymer composites. Cambridge, United Kingdom: Elsevier, Woodhead publishing. eBook. ISBN: 9780128190739.
- Chaudhary, V., P. K. Bajpai, and S. Maheshwari. 2018. An investigation of the wear and dynamic mechanical behavior of jute/hemp/flax reinforced composites and their hybrids for tribological applications. Fibers and Polymers 19 (2):403–15. doi:10.1007/s12221-018-7759-6.
- Chin, C. W., and B. F. Yousif. 2009. Potential of kenaf fibers as reinforcement for tribological applications. Wear 267 (9–10):1550–57. doi:10.1016/j.wear.2009.06.002.
- Chin, C. W., and F. Yousif. 2010. Influence of particle size, applied load, and fiber orientation on 3B-A wear and frictional behavior of epoxy composite based on kenaf fibers. Proceedings of the Institution of Mechanical Engineers, Part J: Journal of Engineering Tribology 224 (5):481–89. doi:10.1243/13506501JET667.
- Das, S., Y. L. Saraswathi, and D. P. Mondal. 2006. Erosive–corrosive wear of Aluminium alloy composites: Influence of slurry composition and speed. Wear 261 (2):180–90. doi:10.1016/j.wear.2005.09.013.
- Das, S., A. K. Singha, A. Chaudhuri, and P. K. Ganguly. 2019. Lengthwise jute fiber properties variation and its effect on jute–polyester composite. The Journal of the Textile Institute 110 (12):1695–702. doi:10.1080/00405000.2019.1613735.
- Deo, C., and S. K. Acharya. 2010. Effects of fiber content on abrasive wear of Lantana Camara fiber reinforced polymer matrix composite. Indian Journal of Engineering and Material Science 17:219–23.
- Devadiga, D. G., K. S. Bhat, and G. T. Mahesha. 2020. Sugarcane bagasse fiber-reinforced composites: Recent advances and applications. Cogent Engineering 7 (1):1823159. doi:10.1080/23311916.2020.1823159.
- Dwivedi, U. K., and N. Chand. 2009. Influence of fiber orientation on friction and sliding wear behavior of jute fiber reinforced polyester composite. Applied Composite Materials 16 (2):93–100. doi:10.1007/S10443-008-9079-X.
- El-Sayed, A. A., M. G. El-Sherbiny, A. S. Abo-El-Ezz, and G. A. Aggag. 1995. Friction and wear properties of polymeric composite materials for bearing applications. Wear 184 (1):45–53. doi:10.1016/0043-1648(94)06546-2.
- El-Tayeb, N. S. M. 2008. A study on the potential of sugarcane fibers/polyester composite for tribological applications. Wear 265 (1–2):223–35. doi:10.1016/j.wear.2007.10.006.
- Fernández, J. E., M. Del Rocı́o Fernández, R. V. Diaz, and R. T. Navarro. 2003. Abrasive wear analysis using factorial experiment design. Wear 255 (1–6):38–43. doi:10.1016/S0043-1648(03)00103-0.
- Gehlen, G. S., P. D. Neis, L. Y. de Barros, J. C. Poletto, M. Ebeling, N. F. Ferreira, and C. C. Angrizani. 2020. Tribological behavior of glass/sisal fiber reinforced polyester composites. Polymer Composites 41 (1):112–20. doi:10.1002/pc.25350.
- Goriparthi, B. K., K. N. S. Suman, and N. M. Rao. 2012. Effect of fiber surface treatments on mechanical and abrasive wear performance of polylactide/jute composites. Composites Part A, Applied Science and Manufacturing 43 (10):1800–08. doi:10.1016/j.compositesa.2012.05.007.
- Goutianos, S., T. Peijs, B. Nystrom, and M. Skrifvars. 2006. Development of flax fiber-based textile reinforcements for composite applications. Applied Composite Materials 13 (4):199–215. doi:10.1007/s10443-006-9010-2.
- Gupta, M. K., and R. K. Srivastava. 2016. Tribological and dynamic mechanical analysis of epoxy-based hybrid sisal/jute composite. Indian Journal of Engineering and Material Science 23:37–44.
- Hashmi, S. A. R., U. K. Dwivedi, and N. Chand. 2007. Graphite modified cotton fiber reinforced polyester composites under sliding wear conditions. Wear 262 (11–12):1426–32. doi:10.1016/j.wear.2007.01.014.
- Huang, K., L. Q. N. Tran, W. S. Teo, and H. P. Lee. 2018. Vibroacoustic behavior and noise control of flax fiber-reinforced polypropylene composites. Journal of Natural Fibers 16 (5):729–43. doi:10.1080/15440478.2018.1433096.
- Idicula, M., N. R. Neelakantan, Z. Oommen, K. Joseph, and S. Thomas. 2005. A study of the mechanical properties of randomly oriented short banana and sisal hybrid fiber reinforced polyester composites. Journal of Applied Polymer Science 96 (5):1699–709. doi:10.1002/app.21636.
- Jollivet, T., C. Peyrac, and F. Lefebvre. 2013. Damage of composite materials. Procedia Engineering 66:746–58. doi:10.1016/j.proeng.2013.12.128.
- Joseph, S., M. S. Sreekala, Z. Oommen, P. Koshy, and S. Thomas. 2002. A comparison of the mechanical properties of phenol formaldehyde composites reinforced with banana fibers and glass fibers. Composites Science and Technology 62 (14):1857–68. doi:10.1016/S0266-3538(02)00098-2.
- Jústiz-Smith, N. G., G. J. Virgo, and V. E. Buchanan. 2008. Potential of Jamaican banana, coconut coir and bagasse fibers as composite materials. Materials Characterization 59 (9):1273–78. doi:10.1016/j.matchar.2007.10.011.
- Kamath, M. G. 2004. Processing and Evaluation of Cotton-based Composites for Automotive and Other Applications. Master Thesis. University of Tennessee. https://trace.tennessee.edu/utk_gradthes/2261
- Kamath, M. G., G. S. Bhat, D. V. Parikh, and D. Mueller. 2005. Cotton fiber nonwovens for automotive composites. Journal of Engineered Fibers and Fabrics 14 (1):34–40. doi:10.1177/1558925005os-1400105.
- Khan, A., M. A. Ahmad, S. Joshi, and S. A. Al Said. 2014. Abrasive wear behavior of chemically treated coir fiber-filled epoxy polymer composites. American Journal of Mechanical Engineering and Automation 1 (1):1–5.
- Khan, J. A., and M. A. Khan. 2014. The use of jute fibers as reinforcements in composites. Biofiber Reinforcements in composite materials, Cambridge, UK: Elsevier, Woodhead Publishing. EBook. ISBN: 9781782421276.
- Khot, M. B., and M. P. Kumar. 2021. Effect of tool material on thrust force and delamination in the drilling of coconut leaf sheath fiber reinforced polymer composites. Materials Today: Proceedings 47 (16):5715–21. doi:10.1016/j.matpr.2021.05.061.
- Kranthi, G., R. Nayak, S. Biswas, and A. Satapathy 2010. Wear performance evaluation of pinewood dust-filled epoxy composites. Proceedings of the International Conference on Advancements in Polymeric Materials APM, Cipet, Bhubaneswar.
- Kumar, V., N. Mohan, and A. K. Bongale. 2019. Fabrication and tribological investigation of coconut coir/banana fiber/glass fiber reinforced hybrid polymer matrix composites-A Taguchi’s approach. Materials Research Express 6 (10):105345. doi:10.1088/2053-1591/ab3d4a.
- Mahapatra, S. S., and V. Chaturvedi. 2009. Modeling and analysis of abrasive wear performance of composites using Taguchi approach. International Journal of Engineering, Science and Technology 1 (1):123–35. doi:10.4314/ijest.v1i1.58072.
- Maurya, H. O., K. Jha, and Y. K. Tyagi. 2017. Tribological behavior of short sisal fiber reinforced epoxy composite. Polymers and Polymer Composites 25 (3):215–20. doi:10.1177/096739111702500306.
- Mendoza, J. C., E. E. Vera Cardenas, R. Lewis, W. Mai, E. O. Avila Davila, A. I. Martinez-Perez, and M. Moreno Rios. 2021. Water jet erosion performance of carbon fiber and glass fiber reinforced polymers. Polymers 13 (17):2933. doi:10.3390/polym13172933.
- Milosevic, M., P. Valášek, and A. Ruggiero. 2020. Tribology of natural fibers composite materials: An overview. Lubricants 8 (4):42. doi:10.3390/lubricants8040042.
- Mishra, P., and S. K. Acharya. 2010. Anisotropy abrasive wear behavior of bagasse fiber-reinforced polymer composite. International Journal of Engineering, Science and Technology 2 (11). doi: 10.4314/ijest.v2i11.64558.
- Mishra, A. K., R. Sheokand, and R. K. Srivastava. 2012. Tribological behavior of Al-6061/sic metal matrix composite by Taguchi’s techniques. International Journal of Scientific and Research Publications 2 (10):1–8. doi:10.15373/22778179/OCT2013/37.
- Munde, Y. S., R. B. Ingle, and I. Siva. 2018. Investigation to appraise the vibration and damping characteristics of coir fiber reinforced polypropylene composites. Advances in Materials and Processing Technologies 4 (4):639–50. doi:10.1080/2374068X.2018.1488798.
- Munium, A., and R. M. Algbory. 2011. Wear rate behavior of carbon/epoxy composite materials at different working conditions. The Iraqi Journal for Mechanical and Material Engineering 11 (3):475–85.
- Narish, S., B. F. Yousif, and D. Rilling. 2011. Adhesive wear of thermoplastic composite based on kenaf fibers. Proceedings of the Institution of Mechanical Engineers, Part J: Journal of Engineering Tribology 225 (2):101–09. doi:10.1177/2041305X10394053.
- Nirmal, U., J. Hashim, and K. O. Low. 2012. Adhesive wear and frictional performance of bamboo fibers reinforced epoxy composite. Tribology International 47:122–33. doi:10.1016/j.triboint.2011.10.012.
- Nirmal, U., B. F. Yousif, D. Rilling, and P. V. Brevern. 2010. Effect of betelnut fibers treatment and contact conditions on adhesive wear and frictional performance of polyester composites. Wear 268 (11–12):1354–70. doi:10.1016/j.wear.2010.02.004.
- Nordin, N. A., F. M. Yussof, S. Kasolang, Z. Salleh, and M. A. Ahmad. 2013. Wear rate of natural fiber: Long kenaf composite. Procedia Engineering 68:145–51. doi:10.1016/j.proeng.2013.12.160.
- Pachta, V., M. Stefanidou, S. Konopisi, and I. Papayianni. 2014. Technological evolution of historic structural mortars. Journal of Civil Engineering and Architecture 8 (7):846–54. doi:10.17265/1934-7359/2014.07.005.
- Parikh, H. H., and P. P. Gohil. 2015. Composites as TRIBO materials in engineering systems: Significance and applications. Processing Techniques and Tribological Behavior of Composite Materials. ACME Book Series: IGI Global doi:10.4018/978-1-4666-7530-8.ch007.
- Parikh, H. H., and P. P. Gohil. 2017. Experimental investigation and prediction of wear behavior of cotton fiber polyester composites. Friction 5 (2):183–93. doi:10.1007/s40544-017-0145-y.
- Parikh, H. H., and P. P. Gohil. 2019. Experimental determination of tribo behavior of fiber-reinforced composites and its prediction with artificial neural networks. In Durability and life prediction in biocomposites, fibre-reinforced composites and hybrid composites. Cambridge, United States: Woodhead Publishing. doi:10.1016/B978-0-08-102290-0.00013-1.
- Parikh, H., and P. Gohil. 2021. Experimental evaluation and estimation of frictional behavior of polymer matrix composites. Journal of Computational and Applied Research in Mechanical Engineering 10 (2):473–83. doi:10.22061/jcarme.2019.4329.1527.
- Periyasamy, A. P., S. K. Ramamoorthy, and S. S. Lavate. 2019. Eco-friendly Denim Processing. In Handbook of Ecomaterials, L. Martínez, O. Kharissova, and B. Kharisov. ed., Cham: Springer. doi:10.1007/978-3-319-68255-6_102.
- Phillips, S., and L. Lessard. 2012. Application of natural fiber composites to musical instrument top plates. Journal of Composite Materials 46 (2):145–54. doi:10.1177/0021998311410497.
- Priyanka, S. P. 2013. Effect of water absorption on an interface and tensile properties of banana fiber reinforced functionalized Polypropylene (BF/CFPP) composites developed by Palsule process. Applied Polymer Composites 1 (2):103–13.
- Raghavendra, G., S. Ojha, S. K. Acharya, and S. K. Pal. 2014. Jute fiber reinforced epoxy composites and comparison with the glass and neat epoxy composites. Journal of Composite Materials 48 (20):2537–47. doi:10.1177/0021998313499955.
- Rahul, K., M. H. Shetty, M. N. Karthik, B. Pavana Kumara, K. P. D’souza, and D. Loyd. 2017. Processing and characterization of banana fiber reinforced polymer nanocomposite. Nanoscience and Nanotechnology 7 (2):34–37. doi:10.5923/j.nn.20170702.02.
- Rajeev, V. R., D. K. Dwivedi, and S. C. Jain. 2010. Dry reciprocating wear of Al-Si–SiC composites: A statistical analysis. Tribology International 43 (8):1532–41. doi:10.1016/j.triboint.2010.02.014.
- Rao, C. C., S. Madhusudan, G. Raghavendra, and E. V. Rao. 2012. Investigation in to wear behavior of coir fiber reinforced epoxy composites with the Taguchi method. International Journal of Engineering Research and Applications 2:2248–9622.
- Rodríguez-Tembleque, L., and M. H. Aliabadi. 2014. Friction and wear modelling in fiber-reinforced composites. Computer Modelling in Engineering and Sciences 102:183–210.
- Ruggiero, A., P. Valášek, and M. Müller. 2016. The exploitation of waste date seeds of Phoenix dactylifera in polymeric particle biocomposite: Investigation on adhesion, cohesion and wear. Composites Part B: Engineering 104:9–16. doi:10.1016/j.compositesb.2016.08.014.
- Sapuan, S. M., A. Leenie, M. Harimi, and Y. K. Beng. 2006. Mechanical properties of woven banana fiber reinforced epoxy composites. Materials & Design 27 (8):689–93. doi:10.1016/j.matdes.2004.12.016.
- Saxena, M., A. Pappu, A. Sharma, R. Haque, and S. Wankhede. 2011. Composite materials from natural resources: Recent trends and future potentials. Advances in Composite Materials- Analysis of Natural and Man-Made Materials. doi:10.5772/18264.
- Shahinur, S., and M. Hasan. 2020. Natural fiber and synthetic fiber composites: Comparison of properties, performance, cost and environmental benefits. Encyclopedia of Renewable and Sustainable Materials 2:794–802.
- Shahzad, A. 2012. Hemp fiber and its composites–a review. Journal of Composite Materials 46 (8):973–86. doi:10.1177/0021998311413623.
- Shireesha, Y., and G. Nandipati 2019. State of the art review on natural fibers. Materials Today: Proceedings 18:15–24. DOI: 10.1016/j.matpr.2019.06.272.
- Singh, N., B. F. Yousif, and D. Rilling. 2011. Tribological characteristics of sustainable fiber-reinforced thermoplastic composites under wet adhesive wear. Tribology Transactions 54 (5):736–48. doi:10.1080/10402004.2011.597544.
- Suresha, B. 2006. The role of fillers on friction and slide wear characteristics in glass-epoxy composite systems. Journal of Minerals and Materials Characterization and Engineering 5 (01):87. doi:10.4236/jmmce.2006.51006.
- Suresha, B., S. Seetharamu, and P. S. Kumaran. 2009. Investigations on the influence of graphite filler on dry sliding wear and abrasive wear behavior of carbon fabric reinforced epoxy composites. Wear 267 (9–10):1405–14. doi:10.1016/j.wear.2009.01.026.
- Thomas, B., M. Hadfield, and S. Austen. 2009. Experimental wear modeling of lifeboat slipway launches. Tribology International 42 (11–12):1706–14. doi:10.1016/j.triboint.2009.04.043.
- Thwe, M. M., and K. Liao. 2002. Effects of environmental aging on the mechanical properties of bamboo–glass fiber reinforced polymer matrix hybrid composites. Composites Part A, Applied Science and Manufacturing 33 (1):43–52. doi:10.1016/S1359-835X(01)00071-9.
- Valášek, P., R. D’amato, M. Müller, and A. Ruggiero. 2018. Mechanical properties and abrasive wear of white/brown coir epoxy composites. Composites Part B: Engineering 146:88–97. doi:10.1016/j.compositesb.2018.04.003.
- Verma, D., P. C. Gope, A. Shandilya, A. Gupta, and M. K. Maheshwari. 2013. Coir fiber reinforcement and application in polymer composites. Journal of Materials Environmental Science 4 (2):263–76.
- Vigneshkumar, S., and T. Rajasekaran. 2018. Experimental analysis on tribological behavior of fiber-reinforced composites. IOP Conference Series: Materials Science and Engineering 402 (1):012198. doi:10.1088/1757-899X/402/1/012198.
- Wu, S., J. Zhao, M. Guo, J. Zhuang, and Q. Wu. 2021. Effect of fiber shape on the tribological, mechanical, and morphological behaviors of sisal fiber-reinforced resin-based friction materials: helical, undulated, and straight shapes. Materials 14 (18):5410. doi:10.3390/ma14185410.
- Xess, P. A. 2012. Erosion wears behavior of bamboo fiber-based hybrid composites. Master Dissertation. National Institute of Technology - Rourkela.
- Yallew, T. B., P. Kumar, and I. Singh. 2014. Sliding wear properties of jute fabric reinforced polypropylene composites. Procedia Engineering 97:402–11. doi:10.1016/j.proeng.2014.12.264.
- Yan, L., S. Su, and N. Chouw. 2015. Microstructure, flexural properties and durability of coir fiber reinforced concrete beams externally strengthened with flax FRP composites. Composites Part B: Engineering 80:343–54. doi:10.1016/j.compositesb.2015.06.011.
- Yousif, B. F. 2009. Frictional and wear performance of polyester composites based on coir fibers. Proceedings of the Institution of Mechanical Engineers, Part J: Journal of Engineering Tribology 223 (1):51–59. doi:10.1243/13506501JET455.
- Yousif, B. F., and N. S. M. El-Tayeb. 2009. Mechanical and wear properties of oil palm and glass fibers reinforced polyester composites. International Journal of Precision Technology 1 (2):213–22. doi:10.1504/IJPTECH.2009.026380.
- Yousif, B. F., and N. S. M. El-Tayeb. 2010. Wet adhesive wear characteristics of untreated oil palm fiber-reinforced polyester and treated oil palm fiber-reinforced polyester composites using the pin-on-disc and block-on-ring techniques. Proceedings of the Institution of Mechanical Engineers, Part J: Journal of Engineering Tribology 224 (2):123–31. doi:10.1243/13506501JET655.
- Yousif, B. F., S. T. Lau, and S. McWilliam. 2010. Polyester composite based on betelnut fiber for tribological applications. Tribology International 43 (1–2):503–11. doi:10.1016/j.triboint.2009.08.006.
- Zhu, W. H., B. C. Tobias, R. S. P. Coutts, and G. Langfors. 1994. Air-cured banana-fiber-reinforced cement composites. Cement and Concrete Composites 16 (1):3–8. doi:10.1016/0958-9465(94)90024-8.