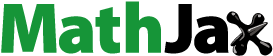
ABSTRACT
In this study, ground wastes of Nettle (Urtica dioica L.) fiber (GWN), which contains cellulose of 52.2 wt%, hemicellulose of 28.9 wt%, and lignin of 18.9 wt%, filled polypropylene (PP) composites were fabricated by using a high-speed kinetic mixer. The effect of filling GWN into PP at different weight fractions on density, crystallization behavior, coefficient of thermal expansion, and thermal stability was investigated. In addition, tensile and flexural tests were performed to determine how the mechanical properties of PP were affected. Morphological observations were conducted using scanning electron microscopy (SEM). The flexural strength values of PP increased by 10%, 15%, and 31% with the addition of 7 wt%, 14 wt%, and 21 wt% GWN, respectively. However tensile strength value of PP decreased slightly with the addition of GWN. 21 wt% GWN addition into PP led to a considerable decrease (about 29%) in the thermal expansion coefficient of PP. The degree of crystallinity of PP was not affected by the addition of GWN.
摘要
在本研究中,使用高速动态混合器制备了荨麻(Urtica dioica L.)纤维(GWN)的研磨废料,该纤维含有52.2 wt%的纤维素、28.9 wt%的半纤维素和18.9 wt%的木质素,填充聚丙烯(PP)复合材料. 研究了在不同重量分数的聚丙烯中填充GWN对密度、结晶行为、热膨胀系数和热稳定性的影响. 此外,还进行了拉伸和弯曲试验,以确定PP的机械性能如何受到影响. 使用扫描电子显微镜(SEM)进行形态学观察. 添加7 wt%、14 wt%和21 wt%的GWN后,PP的弯曲强度值分别增加了10%、15%和31%. 但随着GWN的加入,PP的拉伸强度值略有下降. 向PP中加入21 wt%的GWN导致PP的热膨胀系数显著降低(约29%). GWN的加入对PP的结晶度没有影响.
Introduction
With the increasing concerns about the use of nonrenewable resources all over the world, studies on new environmentally friendly materials have gained momentum as an alternative to traditional materials (Balla et al. Citation2019). Waste recycling, renewability, and sustainability have become one of the most important needs for various industries such as automotive, electrical electronics, household goods, defense, aviation, etc (Balla et al. Citation2019; Tarique et al. Citation2021).
Polymeric materials due to their lightweight, ease of processing, and low cost play an important role in meeting the challenges of the twenty-first century in engineering and high-tech applications. The number of scientific research on the development of polymeric and polymeric-composite materials with desired properties according to the application in which they will be used is quite high (Omrani, Menezes, and Rohatgi Citation2016; Sinha et al. Citation2020). Polymer-based composites reinforced with petroleum based fibers such as carbon, glass, boron, and aramid fibers are highly preferred in engineering applications due to their excellent mechanical properties and structural advantages. In addition, high strength and long fatigue life are important advantages of synthetic fiber-reinforced polymer composites. However, besides such advantages, adverse environmental impact, degradability problem, and low recycling rates make them non-preferable for some applications (Kim, Dutta, and Bhattacharyya Citation2018). For these reasons, environmentally friendly, renewable, and sustainable natural fiber-reinforced composite materials are increasingly being used instead of environmentally harmful synthetic fiber-reinforced composite materials ((Sanjay et al. Citation2018) (Sanjay et al. Citation2019)). Natural fibers provide economic and environmental benefits because they are recyclable, biodegradable, have high specific stiffness and strength values, and are relatively inexpensive compared to synthetic supplements (Balla et al. Citation2019; Kim, Dutta, and Bhattacharyya Citation2018). The production of natural fiber-reinforced polymer-based composites has recently increased, especially in the furniture, automotive, and construction industries (De Rosa, Santulli, and Sarasini Citation2009). Recently, interest in thermoplastic-based natural fiber reinforced composites for high-performance engineering applications has been increasing due to the many advantages of these materials, such as satisfactorily high specific strength and modulus, and low corrosion resistance (Alkbir et al. Citation2016; Balla et al. Citation2019).
Many studies have been carried out to improve the mechanical properties of plant fibers such as flax, kenaf, jute, and sisal, which are widely used among natural fiber types, by reinforcing them into polymers (Li et al. Citation2020; Sivakandhan et al. Citation2020). (Lee, Kim, and Yu (Citation2009))examined the mechanical properties of long and short kenaf and jute-reinforced polypropylene composites (Lee, Kim, and Yu Citation2009). Mahesh et al. (Citation2022) investigated the effect of hybrid ramie and sisal fibers on the mechanical properties of polypropylene-based composites. They concluded that ramie and sisal fibers were the potential fibers to improve the mechanical properties of polypropylene composites (Mahesh et al. Citation2022). It is realized that most studies focused on natural filler/fiber polymer composite materials. However, waste-based sources for eco-friendly polymeric composites are also available. It is known that the environmental threat from bio-waste is the generating of methane from such waste decomposing in landfills, which accounted for some of the total greenhouse gas emissions (Ramesh, Palanikumar, and Reddy Citation2017). Most bio-wastes were found to enhance the modulus only without any pre-treatment (Das et al. Citation2022). One of the waste-based sources is the waste of Nettle fiber which is produced on an industrial scale. It is unknown that, in addition, to the increase in modulus of polymers, other properties such as other mechanical, physical, and thermal properties can be enhanced by filling the polymer with the waste of Nettle fiber. Moreover, to our knowledge, the characterization of Nettle fiber wastes-filled polypropylene (PP) composite materials has not been studied in detail. For this reason, the application areas of nettle fiber will be diversified with its use in the automotive sector and white goods products. Among the natural fibers used in polymer composite materials, the interest in nettle fibers will increase. Fisher et al. investigated the properties of nettle-reinforced poly(lactic acid) (PLA) and PP composites produced by compression molding (Fischer, Werwein, and Graupner Citation2012). To the best of our knowledge, ground wastes of Nettle (Urtica dioica L.) fiber-filled PP composite produced by thermo-kinetic mixer was not examined in details. In this study, it was aimed to determine the mechanical, physical, and thermal properties of stinging nettle-reinforced polypropylene (PP) composites and to determine a suitable material for automotive and white goods applications from these composites.
Materials and methods
Materials
Polypropylene (density: 0.9 g/cm3) was supplied from IMS Polymers (LG M 1600), Turkey. Nettle (Urtica dioica L.) fiber waste, which was obtained from the textile industry, was used as reinforcement material in this study. In order to obtain the powder form of Nettle fiber waste (GWN), the waste was ground to pass the sieve size 100 microns by using Blade Grinder.
Determination of chemical composition of GWN
Chemical analysis was performed to evaluate the chemical content of GWN. Fiber samples were oven-dried at 105 °C and then kept in a desiccator prior to chemical analysis processes. The procedure of the processes is given in elsewhere (Kılınç et al. Citation2018).
Preparation of composite
After GWN was dried at 80°C at 2 h, it was added to the mixing bowl in certain proportions (7, 14, 21 wt. % of GWN) and mixed with PP in a Thermo-kinetic mixer (Gelimat) for about 120 seconds. Before molding, the mold was coated with polytetrafluoroethylene (PTFE) fabric to prevent the material from sticking. The prepared mixture was poured into the 20 cm x 20 cm x 3 cm mold. A hot hydraulic press was applied to the sample at 180°C at 60, 90, and 120 bar pressures and for 120, 60, and 30 seconds. Then, a cold hydraulic press was applied at 120 bar pressure for 90 seconds.
Characterization
2.4.1. Density measurement
Density measurement of the specimens was performed according to the ASTM D792–00 using Densimeter MD-300S.
Differential scanning calorimetry (DSC) analysis
DSC measurements of PP and its composites were performed by using DSC Q20 (TA Instruments Inc.). The specimens were heated from 20 to 200°C with a ramp of 10°C/min and kept at 200°C for 1 min. After being cooled to 20°C, the samples were re-heated to 200°C with a heating rate of 10°C under a nitrogen atmosphere.
Thermogravimetric (TG) analysis
TG analyses of PP and PP-GWN composites were conducted by using a thermogravimetric analyzer (TGA-Q50-TA Instruments) at a heating rate of 10 ºC/min under a nitrogen atmosphere between the temperature range of 25 to 800 ºC.
Thermomechanical analysis (TMA)
The thermal expansion coefficients (CTE) of PP and PP-GWN composites were determined by using a thermo-mechanical analyzer (TMA 400-TA Instruments). The analyses were conducted with expansion mode at a constant compression load of 0.02 N. The specimens (10 mm × 5 mm × 3 mm) were heated from −30 to 90°C at a heating rate of 5°C min−1.
Mechanical tests
Tensile tests were performed according to ASTM D638–10 standard, with specimen type I and a crosshead speed of 50 mm/min. Three-point bending test was conducted by using the ASTM D790 standard with a support span of 64 mm and a deformation rate of 2 mm/min.
Scanning electron microscopy (SEM)
The morphological properties of GWN-filled PP composites were examined by using a scanning electron microscope (300 VP FE-SEM, Carl Zeiss AG, Germany) operated at an acceleration voltage of 3 kV. Before analysis, the surface of GWN-filled PP composites was coated with a thin layer of gold via a plasma sputtering system.
Results and discussions
Chemical composition GWN fibers
The chemical composition of the plant fibers is affected by the growing region, part and age of the plant, and extraction technique (Maheshwaran et al. Citation2018). Plant fibers are mainly composed of cellulose, hemicellulose, and lignin. The cellulose and hemicellulose contents of GWN are 52.2 and 28.9%, respectively. The fraction of the rest of the other chemical components including lignin is 18.9%. Hemicellulose can be considered as a compatibilizer between cellulose and lignin. Cellulose consists of helically wound cellulose micro-fibrils bound together with and further embedded in lignin (Arthanarieswaran, Kumaravel, and Saravanakumar Citation2015).
The cellulose contents of some other fibers were listed in ().
Table 1. Cellulose contents of GWN and recently characterized plant fibers.
The cellulose content of GWN is lower than Thespesia populnea, Red banana peduncle, and Dichrostachys Cinerea (Baskaran et al. Citation2018; Ganapathy et al. Citation2019; Manimaran et al. Citation2018). It was comparable with Conium Maculatum, Curcuma longa L., Morus alba L., coir, kapok, and kenaf fibers (Chaiarrekij et al. Citation2012; Esmeraldo et al. Citation2010; Ilangovan et al. Citation2018, 2019 (Seki et al. Citation2018)). Accordingly, it is possible to reveal that GWN can be a candidate to be used as a reinforcement with its cellulose capacity.
Density
The density values of GWN-filled PP composites are given in ().
Table 2. Density of GWN-filled PP composites.
As noticed from (), the density values of the composites were obtained to be higher than the density of the neat PP. As expected, the density of the composites increased with the increase in the weight fraction of the GWN. This is due to the higher density of GWN compared to neat PP. The highest density was found to be 0.98 g/cm3 for PP containing 21 wt.% GWN.
DSC analysis
DSC curves of PP and PP-GWN composites are shown in ().
Melting temperature (Tm) and enthalpy of melting (ΔHm) can be obtained from the DSC curves. DSC data obtained from () are summarized in (). The degree of crystallinity (Xc) of the specimens can be calculated using the following equation Eq.(1) (27).
Table 3. DSC data of PP and its composites.
where ϕPP is the weight fraction of PP in the composite, is the enthalpy of melting of fully crystalline PP, taken as 209 J/g (Kaya et al. Citation2018).
As can be seen from (), melting temperature does not change considerably upon GWN filling. However, an increase in melting enthalpy was observed. The degree of crystallinity of PP, PP-7GWN, PP-14GWN, and PP-21GWN values were calculated to be 40, 43, 40, and 40% respectively. It is noted that the degree of crystallinity value of the PP-7GWN composite is higher than that of neat PP. The increase in crystallinity in PP-based composites could be due to the nucleating effect of the fillers which could promote crystallization. A similar phenomenon was reported for various fillers resulting in increased crystallinity in PP composites (Altay et al. Citation2018). The degree of supercooling decreased with a filling of 7 and 14 wt. % of GWN, which shows the nucleating agent’s ability (Beck and Ledbetter Citation1965).
TG analysis
TGA curves for PP and PP-GWN composites are given in ().
As can be understood from (), PP-GWN composites display two main weight losses around 250–350°C and 400–500°C due to the degradation of GWN and PP, respectively. Degradation temperatures at different levels of TG weight loss are listed in ().
Table 4. Degradation temperatures at different levels of TG weight loss.
It is presented that the maximum degradation temperatures of PP slightly increased with the addition of GWN. Salemane and Luyt (Citation2006) and Mofokeng et al. (Citation2012) reported similar degradation behavior when PP was filled with wood flour and sisal fiber, respectively. Besides, () indicates that the addition of GWN into PP reduced the thermal stability of PP. It can also be observed that there is an apparent decreasing trend in the thermal stability of the composites with increasing the weight fraction of GWN. T (0 C) at 2 wt.% and T (0 C) at 5 wt.% values decreased with the weight fraction of GWN within the composites. The greatest weight fraction of GWN within PP led to the lowest T (0 C) at 2 wt.%, T (0 C) at 5 wt.%, and T (0 C) at 10 wt.% values.
TMA
Dimensional change versus temperature change for PP and PP-GWN composites are shown in ().
An increasing trend in dimensional change can be realized in the studied temperature range. The coefficient of thermal expansion (CTE) values of PP and PP-GWN composites were obtained in the temperature range (−10) to 50°C and obtained results are given in ().
Table 5. The thermal expansion coefficients of PP and PP-GWN composites.
CTE values of PP, PP-7GWN, PP-14GWN, and PP-21GWN were obtained to be 109, 117, 120, and 77 µm/m 0 C, respectively. It is known that adding fiber to a thermoplastic polymer reduces the thermal expansion of the composite (Bogard et al. Citation2022). The coefficient of thermal expansion of PP-21GWN decreased considerably. The addition of 7% GWN and 14% GWN to PP may not be effective on the coefficient of thermal expansion because of the close CTE values. With the addition of 21 wt.% GWN into PP decreased the CTE value of PP by 29%. It is known that thermoplastic materials are known with high CTE values. Therefore, lower CTE value of PP-21GWN is an advantage for many applications (Atagur et al. Citation2020).
Mechanical properties
The values of tensile and flexural strength of the GWN-loaded PP are given in , respectively.
Tensile strength values of PP, PP-7GWN, PP-14GWN, and PP-21GWN composites were obtained to be 22.05, 20.55, 19.02, and 18.09 MPa, respectively. At the whole weight fraction of GWN, the tensile strength values of GWN-loaded PP composites are lower than that of PP.
The decrements in tensile strength may result from the poor interfacial adhesion between the hydrophobic PP matrix and hydrophilic lignocellulosic GWN filler. Thus, it prevents efficient stress transfer from the PP matrix to GWN particles ((Premalal, Ismail, and Baharin Citation2002) (Ab Ghani and Ahmad Citation2011; Fu et al. Citation2008)). Reductions in the tensile strength may be prevented if a compatibilizer is used to increase the compatibility between the additives and matrix.
According to (), the flexural strength values for PP, PP-7GWN, PP-14GWN, and PP-21GWN were determined to be about 46.4, 51.1, 53.2, and 61.0 MPa, respectively. The flexural strength values of PP increased by 10%, 15%, and 31% with the addition of 7 wt%, 14 wt%, and 21 wt% GWN, respectively. This indicates that as the weight fraction of GWN was increased, the flexural strength values increased. The highest flexural strength value was achieved at 21 wt.% GWN filling (Fischer, Werwein, and Graupner Citation2012). Fischer, Werwein, and Graupner (Citation2012), obtained that reinforcement by 30 wt-% nettle resulted in a tensile strength 33% lower than PP and a flexural strength 60% below PP, which is due to poor interaction between the nonpolar polymer matrix and the polar nettle fibers (Fischer, Werwein, and Graupner Citation2012). Kumar and Das (Citation2017) showed that the tensile strength, elongation-at-break, Young’s modulus, flexural strength, and impact strength of the biocomposites increased initially with the increase of nettle fiber content and decreased afterward (Kumar and Das Citation2017).
As can be realized from , the tensile and flexural modulus of PP increased with the addition of GWN fillers in the studied concentration range (7–21 wt.%). PP has tensile and flexural moduli of about 745 and 1619 MPa, respectively. Filler loading affects the stiffness properties of the matrix material. The increase in the tensile and flexural modulus of the PP matrix may be due to the higher modulus of the natural fillers. It is well known that the addition of rigid filler is anticipated to increase the tensile and flexural modulus of the composites and yield a greater stiffness the composites. When 21 wt. % GWN was added, and the tensile and flexural moduli increased by about 101% and 123%, respectively (Jamil, Ahmad, and Abdullah Citation2006). Showed that the addition of the filler increases the tensile and flexural moduli of composites. This results from the addition of rigid fillers into the matrix (Jamil, Ahmad, and Abdullah Citation2006).
SEM
GWN at different particle sizes within the PP matrix can be given in
Powder pull-outs can be tracked especially at a higher weight fraction of GWN () This indicates a poor dispersion between PP and GWN particles. However, aggregated filler powder acting as a stress concentrator, which led to drops in tensile strength, is not commonly seen in the SEM images of GWN-added PP composites (Atagür et al. Citation2018; Kaya et al. Citation2018; Maheshwaran et al. Citation2018).
Conclusion
In this study, GWN-filled polypropylene composites at different weight fractures of GWN were manufactured. There were certain effects of GWN on the thermal, mechanical, and physical properties of polypropylene composites. Some specific conclusions could be drawn as follows:
The degree of crystallinity values of 40, 43, 40, and 40% were calculated for PP, PP-7GWN, PP-14GWN, and PP-21GWN composites respectively.
The greatest weight fraction of GWN within PP led to the lowest T(0 C) at 2 wt.% and T(0 C) at 5 wt.%, T(0 C) at 10 wt.% values.
PP-7GWN and PP-14GWN exhibited an increasing trend in CTE values. However, with the addition of 21 wt.% GWN into PP decreased the CTE value of PP by 29%.
The flexural strength value of PP increased by about 10, 15, and 31% with the filling of 7, 14, and 21 wt. % of GWN, respectively.
From the conducted study it can be concluded that GWN as a bio-waste material, without any pre-treatment, enhanced not only modulus values but also improved the coefficient of thermal expansion and flexural strength values of the polymer. GWN’s low cost, biodegradability, and satisfactory performance make it a promising natural fiber to replace synthetic fibers in thermoplastic-based composites for numerous applications.
Highlights
Nettle-reinforced polypropylene composites were prepared from a bio-waste material by using high-speed kinetic mixer.
The effect of filling nettle fiber waste into polypropylene at different weight fractions was investigated in detailed.
Nettle fiber waste as a bio-waste material, without any pre-treatment, enhanced modulus values, coefficient of thermal expansion and flexural strength values of polypropylene.
Ethical approval
We confirm that all the research meets ethical guidelines and adheres to the legal requirements of the study country. The research does not involve any human or animal welfare-related issues.
Disclosure statement
No potential conflict of interest was reported by the authors.
Additional information
Funding
References
- Ab Ghani, M. H., and S. Ahmad. 2011. The comparison of water absorption analysis between counterrotating and corotating twin-screw extruders with different antioxidants content in wood plastic composites. Advances in Materials Science and Engineering 1–13. doi:10.1155/2011/406284.
- Alkbir, M. F. M., S. M. Sapuan, A. A. Nuraini, and M. R. Ishak. 2016. Fibre properties and crashworthiness parameters of natural fibre-reinforced composite structure: A literature review. Composite Structures 148:59–73. doi:10.1016/j.compstruct.2016.01.098.
- Altay, L., M. Atagur, O. Akyuz, Y. Seki, I. Sen, M. Sarikanat, and K. Sever. 2018. Manufacturing of recycled carbon fiber reinforced polypropylene composites by high speed thermo‐kinetic mixing for lightweight applications. Polymer Composites 39 (10):3656–65. doi:10.1002/pc.24394.
- Arthanarieswaran, V. P., A. Kumaravel, and S. S. Saravanakumar. 2015. Characterization of new natural cellulosic fiber from Acacia leucophloea bark. International Journal of Polymer Analysis and Characterization 20 (4):367–76. doi:10.1080/1023666X.2015.1018737.
- Atagür, M., M. Sarikanat, T. Uysalman, O. Polat, İ. Y. Elbeyli, Y. Seki, and K. Sever. 2018. Mechanical, thermal, and viscoelastic investigations on expanded perlite–filled high-density polyethylene composite. Journal of Elastomers & Plastics 50 (8):747–61. doi:10.1177/0095244318765045.
- Atagur, M., Y. Seki, O. Oncu, K. Sever, Y. Seki, M. Sarikanat, and L. Altay. 2020. Evaluating of reinforcing effect of ceratonia siliqua for polypropylene: Tensile, flexural and other properties. Polymer Testing 89:106607. doi:10.1016/j.polymertesting.2020.106607.
- Atagur, M., Y. Seki, Y. Pasaoglu, K. Sever, Y. Seki, M. Sarikanat, and L. Altay. 2020. Mechanical and thermal properties of Carpinus betulus fiber filled polypropylene composites. Polymer Composites 41 (5):1925–35. doi:10.1002/pc.25508.
- Balla, V. K., K. H. Kate, J. Satyavolu, P. Singh, and J. G. D. Tadimeti. 2019. Additive manufacturing of natural fiber reinforced polymer composites: Processing and prospects. Composites Part B: Engineering 174:106956. doi:10.1016/j.compositesb.2019.106956.
- Baskaran, P. G., M. Kathiresan, P. Senthamaraikannan, and S. S. Saravanakumar. 2018. Characterization of new natural cellulosic fiber from the bark of dichrostachys cinerea. Journal of Natural Fibers 15 (1):62–68. doi:10.1080/15440478.2017.1304314.
- Beck, H. N., and H. D. Ledbetter. 1965. DTA study of heterogeneous nucleation of crystallization in polypropylene. Journal of Applied Polymer Science 9 (6):2131–42. doi:10.1002/app.1965.070090610.
- Bogard, F., T. Bach, B. Abbes, C. Bliard, C. Maalouf, V. Bogard, F. Beaumount, and G. Polidori. 2022. A comparative review of nettle and ramie fiber and their use in biocomposites, particularly with a PLA matrix. Journal of Natural Fibers 19:8205–29. doi:10.1080/15440478.2021.1961341.
- Chaiarrekij, S., A. Apirakchaiskul, K. Suvarnakich, and S. Kiatkamjornwong. 2012. Kapok I: Characteristcs of kapok fiber as a potential pulp source for papermaking. BioResources 7 (1):0475–88.
- Das, O., K. Babu, V. Shanmugam, K. Sykam, M. Tebyetekerwa, R. E. Neisiany, and S. Ramakrishna. 2022. Natural and industrial wastes for sustainable and renewable polymer composites. Renewable and Sustainable Energy Reviews 158:112054. doi:10.1016/j.rser.2021.112054.
- De Rosa, I. M., C. Santulli, and F. Sarasini. 2009. Acoustic emission for monitoring the mechanical behaviour of natural fibre composites: A literature review. Composites Part A, Applied Science and Manufacturing 40 (9):1456–69. doi:10.1016/j.compositesa.2009.04.030.
- Esmeraldo, M. A., A. C. Gomes, J. E. Freitas, P. B. Fechine, A. S. Sombra, E. Corradini, and S. E. Mazzetto. 2010. Dwarf-green coconut fibers: A versatile natural renewable raw bioresource. Treatment, morphology, and physicochemical properties. Bioresources 5 (4):2478–501.
- Fischer, H., E. Werwein, and N. Graupner. 2012. Nettle fibre (urtica dioica L.) reinforced poly(lactic acid): A first approach. Journal of Composite Materials 46 (24):3077–87. doi:10.1177/0021998311435676.
- Fu, S. Y., X. Q. Feng, B. Lauke, and Y. W. Mai. 2008. Effects of particle size, particle/matrix interface adhesion and particle loading on mechanical properties of particulate–polymer composites. Composites Part B: Engineering 39 (6):933–61. doi:10.1016/j.compositesb.2008.01.002.
- Ganapathy, T., R. Sathiskumar, P. Senthamaraikannan, S. S. Saravanakumar, and A. Khan. 2019. Characterization of raw and alkali treated new natural cellulosic fibres extracted from the aerial roots of banyan tree. International Journal of Biological Macromolecules 138:573–81. doi:10.1016/j.ijbiomac.2019.07.136.
- Ilangovan, M., V. Guna, C. Hu, G. S. Nagananda, and N. Reddy. 2018. Curcuma longa L. plant residue as a source for natural cellulose fibers with antimicrobial activity. Industrial Crops and Products 112:556–60. doi:10.1016/j.indcrop.2017.12.042.
- Jamil, M. S., I. Ahmad, and I. Abdullah. 2006. Effects of rice husk filler on the mechanical and thermal properties of liquid natural rubber compatibilized high-density polyethylene/natural rubber blends. Journal of Polymer Research 13 (4):315–21. doi:10.1007/s10965-005-9040-8.
- Kaya, N., M. Atagur, O. Akyuz, Y. Seki, M. Sarikanat, M. Sutcu, and K. Sever. 2018. Fabrication and characterization of olive pomace filled PP composites. Composites Part B: Engineering 150:277–83. doi:10.1016/j.compositesb.2017.08.017.
- Kılınç, A. Ç., S. Köktaş, M. Atagür, and M. Ö. Seydibeyoglu. 2018. Effect of extraction methods on the properties of althea officinalis L. fibers. Journal of Natural Fibers 15 (3):325–36. doi:10.1080/15440478.2017.1325813.
- Kim, N. K., S. Dutta, and D. Bhattacharyya. 2018. A review of flammability of natural fibre reinforced polymeric composites. Composites Science and Technology 162:64–78. doi:10.1016/j.compscitech.2018.04.016.
- Kumar, N., and D. Das. 2017. Fibrous biocomposites from nettle (Girardinia diversifolia) and poly(lactic acid) fibers for automotive dashboard panel application. Composites Part B: Engineering 130:54–63. doi:10.1016/j.compositesb.2017.07.059.
- Lee, B. H., H. J. Kim, and W. R. Yu. 2009. Fabrication of long and discontinuous natural fiber reinforced polypropylene biocomposites and their mechanical properties. Fibers and Polymers 10 (1):83–90. doi:10.1007/s12221-009-0083-z.
- Li, Q., Y. Li, H. Ma, S. Cai, and X. Huang. 2020. Effect of processing temperature on the static and dynamic mechanical properties and failure mechanisms of flax fiber reinforced composites. Composites Communications 20:100343. doi:10.1016/j.coco.2020.04.009.
- Mahesh, A., B. M. Rudresh, and H. N. Reddappa. 2022. Potential of natural fibers in the modification of mechanical behavior of polypropylene hybrid composites. Materials Today: Proceedings, Bengaluru, India, 54: 131–36.
- Maheshwaran, M. V., N. R. J. Hyness, P. Senthamaraikannan, S. S. Saravanakumar, and M. R. Sanjay. 2018. Characterization of natural cellulosic fiber from epipremnum aureum stem. Journal of Natural Fibers 15 (6):789–98. doi:10.1080/15440478.2017.1364205.
- Manimaran, P., M. R. Sanjay, P. Senthamaraikannan, M. Jawaid, S. S. Saravanakumar, and R. George. 2018. Synthesis and characterization of cellulosic fiber from red banana peduncle as reinforcement for potential applications. Journal of Natural Fibers 768–80. doi:10.1080/15440478.2018.1434851.
- Mofokeng, J. P., A. S. Luyt, T. Tábi, and J. Kovács. 2012. Comparison of injection moulded, natural fibre-reinforced composites with PP and PLA as matrices. Journal of Thermoplastic Composite Materials 25 (8):927–48.
- Omrani, E., P. L. Menezes, and P. K. Rohatgi. 2016. State of the art on tribological behavior of polymer matrix composites reinforced with natural fibers in the green materials world. Engineering Science and Technology, an International Journal 19 (2):717–36. doi:10.1016/j.jestch.2015.10.007.
- Premalal, H. G., H. Ismail, and A. Baharin. 2002. Comparison of the mechanical properties of rice husk powder filled polypropylene composites with talc filled polypropylene composites. Polymer testing 21 (7):833–39. doi:10.1016/S0142-9418(02)00018-1.
- Ramesh, M., K. Palanikumar, and K. H. Reddy. 2017. Plant fibre based bio-composites: Sustainable and renewable green materials. Renewable and Sustainable Energy Reviews 79:558–84. doi:10.1016/j.rser.2017.05.094.
- Salemane, M. G., and A. S. Luyt. 2006. Thermal and mechanical properties of polypropylene-wood powder composites. J Appl Polym 100:4173–80.
- Sanjay, M. R., P. Madhu, M. Jawaid, P. Senthamaraikannan, S. Senthil, and S. Pradeep. 2018. Characterization and properties of natural fiber polymer composites: A comprehensive review. Journal of Cleaner Production 172:566–81. doi:10.1016/j.jclepro.2017.10.101.
- Sanjay, M. R., S. Siengchin, J. Parameswaranpillai, M. Jawaid, C. I. Pruncu, and A. Khan. 2019. A comprehensive review of techniques for natural fibers as reinforcement in composites: Preparation, processing and characterization. Carbohydrate Polymers 207:108–21. doi:10.1016/j.carbpol.2018.11.083.
- Seki, Y., A. Ç. Kılınç, R. Dalmis, M. Atagür, S. Köktaş, A. A. Göktaş, and A. B. Önay. 2018. Surface modification of new cellulose fiber extracted from conium maculatum plant: A comparative study. Cellulose 25 (6):3267–80. doi:10.1007/s10570-018-1797-0.
- Sinha, R. K., K. Sridhar, R. Purohit, and R. K. Malviya. 2020. Effect of nano SiO2 on properties of natural fiber reinforced epoxy hybrid composite: A review. Materials Today: Proceedings, U.P., India, 26: 3183–86.
- Sivakandhan, C., G. Murali, N. Tamiloli, and L. Ravikumar. 2020. Studies on mechanical properties of sisal and jute fiber hybrid sandwich composite. Materials Today: Proceedings, Tiruchirappalli, India, 21: 404–07.
- Tarique, J., S. M. Sapuan, A. Khalina, S. F. K. Sherwani, J. Yusuf, and R. A. Ilyas. 2021. Recent developments in sustainable arrowroot (maranta arundinacea linn) starch biopolymers, fibres, biopolymer composites and their potential industrial applications: A review. Journal of Materials Research and Technology 13:1191–219. doi:10.1016/j.jmrt.2021.05.047.