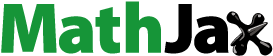
ABSTRACT
The use of natural fibers is a sustainable alternative for developing reinforced-polymer composites. It is believed that the seed flosses of common milkweed, Asclepias Syriraca, may be a promising reinforcing fiber given its uncommon hollow microstructure that is associated with both high specific properties and outstanding insulating capacities. This study presents an overview of the properties of milkweed floss and its potential use in reinforced-polymer composites. Milkweed flosses from Quebec were analyzed to determine their overall dimensions, density, porosity, coefficient of acoustic absorption, thermal conductivity, thermal resistance, and elastic modulus. In parallel, a portion of milkweed fibers was treated with acetone to modify their surface, and the properties of the treated fibers were measured and compared against the characteristics of the original fibers. Infrared spectroscopy was employed to assess differences between the chemical groups on the surface of treated and native fibers. The treatment with acetone removed fatty acids, waxes, and free sugars from the fibers’ surface. The acetone treatment did not affect the fibers’ microstructure nor their acoustic absorption capacity. The acetone-treated fibers showed greater thermal resistance and a higher thermal conductivity than native milkweed floss. The elastic modulus of milkweed decreased by nearly 49% after the acetone treatment.
摘要
使用天然纤维是开发增强聚合物复合材料的可持续选择. 据信,普通马利筋(Asclepias Syrraca)的种子浮渣可能是一种有前途的增强纤维,因为其罕见的中空微结构与高比性能和出色的绝缘能力有关. 本研究综述了马利筋松的性能及其在增强聚合物复合材料中的潜在应用. 分析了魁北克省的麋鹿绒,以确定其总体尺寸、密度、孔隙率、吸声系数、导热系数、热阻和弹性模量. 同时,用丙酮处理一部分马利筋纤维以改性其表面,并测量经处理纤维的性能,并与原始纤维的特性进行比较. 红外光谱法用于评估经处理的纤维和天然纤维表面化学基团之间的差异. 丙酮处理去除了纤维表面的脂肪酸、蜡和游离糖. 丙酮处理不会影响纤维的微观结构和吸声能力. 丙酮处理的纤维显示出比天然马利筋松更高的耐热性和更高的导热性. 丙酮处理后马利筋的弹性模量降低了近49%.
Introduction
The application of fiber-reinforced polymer composites (FRPC) has gained wide acceptance in sectors like transportation, construction, and defense due to their increased mechanical resistance and barrier properties (Astrom Citation2018; Chung Citation2010). FRPCs are mainly made by the combination of synthetic polymers and technical fibers, which raises environmental concerns about the mass production of FRPCs, mainly because of the large amounts of energy and nonrenewable resources used in their fabrication and the low biodegradability and the difficulties to recycle or repurpose their constituting elements (Dorigato Citation2021; Khalid et al. Citation2022; Pickering, Efendy, and Le Citation2016; Sanjay et al. Citation2019; Sunter et al. Citation2015; Thakur, Thakur, and Kessler Citation2017).
The use of natural fibers and biopolymers has proven to be a sustainable alternative to reduce the environmental impact of producing FRPCs. Long natural fibers like sisal, jute, flax, and bamboo have been successfully used to make FRPCs for construction and the automobile industry, whereas short fibers like cotton and coir have been employed in cushioning materials and personal protection gears. Likewise, the production of FRPCs using biopolymers like polysaccharides, bio-based resins, and polyhydroxyalkanoates is a subject of investigation (Arif et al. Citation2022; Arumugaprabu et al. Citation2022; Ismail, Akpan, and Dhakal Citation2022; Khalid et al. Citation2021, Citation2021; Khalil, Bhat, and Yusra Citation2012; Pickering, Efendy, and Le Citation2016; Sanjay et al. Citation2019; Sengupta Citation2020; Thakur, Thakur, and Kessler Citation2017).
Among natural fibers, milkweed floss (MW) is considered a promising reinforcement for polymer matrices due to its lightweight, high specific properties, and good insulating capacities. MW is a single cell that elongates 20–30 mm from the seeds produced in the follicles, or “seedpods,” of common milkweed, Asclepias Syriaca. They appear as white silky hairs that work as an airfoil for the dispersion of the seeds with the wind when the follicle ripens and splits open. Its low weight results from its hollow structure, with a diameter of 20–50 µm and a wall-thickness of 0.7–1.5 µm. To obtain MW, the seedpods are ground, and the fibers are separated from the ground seeds. shows a mature follicle and a seed with its flosses (Hassanzadeh and Hasani Citation2017; Karthik and Murugan Citation2016a; Ovlaque Citation2019).
The overall chemical composition of MW consists of about 40–45% of cellulose, 35–40% of hemicellulose, and 13–18% of lignin. The fiber’s surface is coated with a thin layer of waxes, lignin, and free sugars that makes up around 2–6% of the total composition of MW and gives it hydrophobicity and good chemical resistance (Ashori and Bahreini Citation2009; Karthik and Murugan Citation2016a; Ovlaque Citation2019; Richard et al. Citation2019).
The mechanical properties of MW vary among studies, owing to differences in the characterization technique as well as the origin of the fibers used in each study (Hassanzadeh and Hasani Citation2017; Karthik and Murugan Citation2016a, Citation2016b; Nourbakhsh, Ashori, and Kouhpayehzadeh Citation2009; Ovlaque Citation2019). Ovlaque (Citation2019) measured the ultimate tensile strength (UTS) and strain at break of MW grown in North America at 341 ± 116 MPa and 3.02% ± 0.99%, respectively.
Campeau, Panneton, and Elkoun (Citation2019) studied the effects of the bulk density and hollow structure of MW on the acoustic absorption capacities of nonwoven mats of MW. They showed that the acoustic absorption improved by increasing the mesoporosity of the samples. The hollow structure of MW did not have any influence on the acoustic insulation. On the other hand, there is no direct measurement of the thermal conductivity of MW, even though this fiber is recognized as a good thermal insulator. Crews et al. (Citation1991) estimated the thermal insulation capacity of MW at 2.24 clo for a jacket filled with a 1-inch layer of fibers. A clo unit is the amount of clothing to keep thermal comfort at a given temperature and airflow.
As with other natural fibers, chemical treatments are an option to modify the properties of MW and improve the incorporation of the fibers into polymer matrices (Jagadeesh et al. Citation2021; Khalid et al. Citation2021; Mayandi et al. Citation2016; Pickering, Efendy, and Le Citation2016; Reddy et al. Citation2010). Ovlaque et al. (Citation2020) investigated the microstructure and mechanical properties of MW following a treatment with NaOH or boiling acetone with epoxy-silane. The mercerization improved the roughness of the fibers but produced the collapse of the hollow structure and a decrease of about 68% of the Young’s modulus of MW. By comparison, the treatment with boiling acetone and epoxy-silane caused a decrease of 30% in the Young’s modulus of the fibers but did not affect the surface or the microstructure of MW.
Even though there are studies on the characteristics of MW, there is a lack of information on some properties of these fibers and their values before and after a chemical treatment (Hassanzadeh and Hasani Citation2017; Karthik and Murugan Citation2016a, Citation2016b; Nourbakhsh, Ashori, and Kouhpayehzadeh Citation2009; Ovlaque Citation2019).
This study evaluates some characteristics of MW before and after a treatment with acetone, including their chemical composition, microstructure, density, porosity, acoustic absorption, thermal conductivity, and thermal and tensile resistances. Later, these properties were analyzed to discuss the potential uses of these fibers in the reinforcement of polymer composites.
Experimental
Materials
A combination of first-class and low-grade MW was supplied by the Monark Cooperative (QC, Canada). Acetone at 99.5% w/w was procured from Sigma Aldrich Canada (Ontario, Canada).
A batch of 15 g of MW fibers was dipped in 250 ml of pure acetone (99.5% w/w) at room temperature for 15 min. The fibers were removed from the solution and let dry at room temperature for 30 min. The fibers were immersed again in 250 ml of fresh acetone at room temperature for 15 min, and then the solution was filtered to recover the fibers. The fibers were dried at 50°C for 24 hours inside a vacuum drying oven (SVAC4, Geneq Inc., Montreal, Canada).
Characterization of milkweed floss
Fourier transform infra-red spectroscopy (FTIR)
Infra-red spectroscopy was employed to assess differences within the chemical groups present in each type of fiber. The spectra of native and acetone-treated MW were obtained using a Mid-IR FT/IR spectrometer (FT/IR 4600, Jasco, Easton, MD, USA). Each spectrum was recorded in ATR mode from 4000 to 400 cm-1 at a resolution of 4 cm−1 using 128 scans per sample.
Microstructural analysis, density, and porosity of milkweed floss
Strands of either native or acetone-treated MW were coated with a thin layer of a gold-platinum alloy, and their microstructure was analyzed in a field emission scanning electron microscope (FE-SEM S-4700, Hitachi, Tokyo, Japan). The diameter (df) and wall-thickness (δ) of the fibers were calculated as the mean value of 100 fibers per specimen.
The true density (ρt) of native and acetone-treated MW was measured in a gas pycnometer (AccuPyc II 1340, Micromeritics, Norcross, GA, USA), using pure helium at 26°C. The apparent density (ρA) of the two types of fibers was calculated using EquationEquation 1,(1)
(1)
where “AApparent” and “AEffective” stand for the apparent and effective cross-sectional area of the fiber, respectively. AApparent was estimated as the average measurement of the cross-sectional area of 100 individual fibers, obtained using SEM images and image analysis software. AEffective was computed using EquationEquation 2.(2)
(2) The porosity of the fibers (θ) was quantified using EquationEquation 3
(3)
(3) ,
Thermo-acoustic insulating properties of milkweed floss
The coefficient of acoustic absorption of both native and acetone-treated MW was evaluated in samples of nonwoven mats of 1-inch thickness and bulk densities (ρ) of 7, 14, 21, and 28 kg/m3. The coefficient of acoustic absorption of the samples was measured from a frequency of 100 to 4300 Hz in an impedance tube with an internal diameter of 44 mm (Mecanum Instruments, Sherbrooke, QC, Canada), operating at 24°C and 25% relative humidity. A grid was placed at one end of the tube to hold the samples in place and to avoid variations in their ρ.
The thermal conductivity of native and acetone-treated MW was evaluated in samples of nonwoven mats containing 7, 14, 21, and 28 kg/m3 of each type of fiber. The nonwoven mats were made by laying individual fibers in the same direction on the surface of a mold of 305 mm x 305 mm (12 × 12 inches) until producing samples of 25.4 mm (1 inch) thickness. The thermal conductivity of each sample was measured at a mean temperature of 24°C using a heat-flow meter (FOX 314, TA instruments, New Castle, DE, USA), in accordance with the ASTM C518 standard.
Thermal and mechanical resistance of milkweed floss
The thermal degradation of native and acetone-treated MW was studied using a thermogravimetric analyzer (Pyris 4000, Perkin-Elmer, Waltham, MA, USA). The pyrolysis of the fibers was analyzed from 30°C to 500°C, at a heating rate of 5°C/min and using a gas flow of 20 ml of N2 per minute. Samples of about 20 mg in weight were used for this analysis.
The force at break (FBreak), strain at break (ε), tensile strength (σ), and elastic modulus (E) of native and acetone-treated MW were evaluated according to the standard ASTM D3822 using a universal testing machine (Z050, Zwick/Roell, Baden-Wuerttemberg, Germany), equipped with a load cell of 5 N, operating at a rate of extension of 1 mm/min and a gauge length of 10 mm. The fibers’ σ and E were estimated using the AApparent the hollow fibers. Samples of 100 fibers were used to calculate the values for the mean mechanical properties of each type of fiber.
Results and discussion
FTIR
presents the spectra of both native and acetone-treated MW. The peaks at 3000 and 2965 cm−1 disappeared in the spectrum of the acetone-treated fibers when compared with the spectrum of native MW. These peaks have been associated with the stretching of O-H and C-H in lignin and waxes in MW, respectively (Richard et al. Citation2019). Likewise, the spectrum of the acetone-treated fibers exhibited a lower intensity for the peak at 1735 cm−1, which has been associated with the stretching of C=O groups in lignin and hemicellulose in MW (Karthik and Murugan Citation2013; Richard et al. Citation2019).
In the fingerprint region of the spectra (1450 cm−1 to 400 cm−1), the signals of the peaks at 1371 and 1240 cm−1 were weaker in the spectrum of acetone-treated MW when compared with the spectrum of native MW. These two peaks have been related to the bending of C-H groups in aliphatic compounds and waxes and the stretching of C-O and C=O groups in aromatic rings, respectively (Karthik and Murugan Citation2013; Richard et al. Citation2019).
The differences in the spectra of native and acetone-treated MW fibers suggested that the acetone treatment removed part of the waxes, lignin, and hemicellulose on the fiber’s surface. The development of peaks at 2925 and 1318 cm−1 in the spectra of acetone-treated MW revealed the presence of remaining wax and aliphatic compounds, respectively. Moreover, the weak peaks at 1603, 1508, and 1425 cm−1 indicated the existence of leftover lignin on the treated fibers.
Microstructural analysis
presents images of the microstructure of native and acetone-treated MW.
Figure 3. Microstructure of native milkweed floss at a) 100× and b) 2000× magnifications. Microstructure of acetone-treated milkweed floss at c) 100× and d) 2000× magnifications.
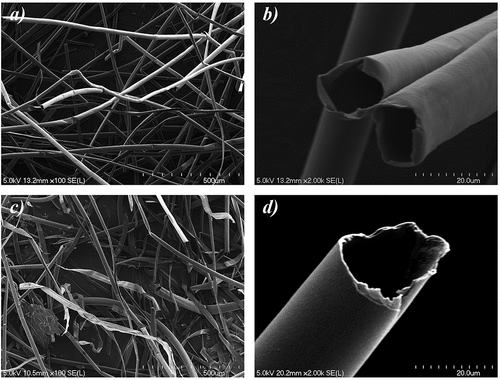
show the microstructure of native MW at different magnifications. Native MW has a mean df and δ of 22.9 ± 4.5 μm and 0.82 ± 0.27 μm, respectively. Native MW’s df and δ displayed a coefficient of standard deviation (COD) of 19.6% and 32.2%, respectively, meaning that there is a greater variation in the fiber’s δ than in its df. The overall size of MW’s circular cross-sectional area is 329.3 ± 60.0 μm, where the hollow portion accounts for nearly 93% of this area. (b) shows that the fiber’s wall is divided into three layers. These layers include the fibers’ inner wall, outer wall, and a middle layer that corresponds to the microfibrils (Bakhtiari et al. Citation2015; Hassanzadeh and Hasani Citation2017; Richard et al. Citation2019).
The surface of the fibers is covered by narrow folds and striae that have been associated with the layer of waxes and free sugars on MW’s surface (Richard et al. Citation2019). Twists or bends were observed along the surface of some fibers. A few other fibers exhibited a ribbon-like shape resulting from the collapse of their cross-section. These deformations could be caused by the mechanical stresses applied during the sample’s preparation.
present the images of acetone-treated MW at 100× and 2000× magnifications, respectively. The non-collapsed treated fibers have the same mean dimensions as native MW, including df, δ, and cross-sectional area. Besides, (d) shows the three sections of the treated fibers’ wall. When compared with native MW, either a larger number of acetone-treated fibers present bents or their cross-section completely collapsed. These observations suggest that the acetone treatment may have induced the deformation of MW’s hollow structure. Richard et al. (Citation2019) and Ovlaque et al. (Citation2020) found a similar behavior when treating MW with NaOH. Ovlaque et al. (Citation2020) reported that those defects improved the interlocking between MW and a matrix of polylactic acid (PLA).
The treated fibers did not exhibit the narrow folds and striae attributed to the presence of waxes and free sugars on the fibers’ surface, which supports the results from the FTIR analysis. A similar observation was reported by Richard et al. (Citation2019) after removing the waxes and free sugars from Mw’s surface using boiling ethanol and chloroform.
Density and porosity of milkweed floss
displays the values of ρt, ρA, and θ for native and acetone-treated MW. MW’s ρt and ρA increased slightly after the treatment with acetone, possibly because of the removal of low-density components such as waxes and free sugars. The native MW’s ρt was higher than the value reported elsewhere, at 1.48 ± 0.02 g/cm3 (Karthik and Murugan Citation2016a; Ovlaque Citation2019). The native MW’s ρA was close to the value reported in the literature of about 0.3 g/cm3 for non-collapsed MA and other natural hollow fibers like kapok (Meiwu, Hong, and Weidong Citation2010; Ovlaque Citation2019; Zheng and Wang Citation2014).
Table 1. True density (ρt), apparent density (ρA), and porosity (θ) of native and acetone-treated milkweed floss.
The results of θ showed that MW’s lumen represents around 82% of the fiber’s volume. These measurements were higher than the values of MW’s θ reported elsewhere, ranging from 76% to 80% (Campeau, Panneton, and Elkoun Citation2019; Ovlaque Citation2019). The lower θ in the treated fibers may be explained by the decrease in their lumen volume due to the partial collapse of the cross-section of some fibers.
MW’s ρt, meaning the density of its fiber wall, approached the value of density for other natural fibers such as cotton or pure cellulose, at 1.52 g/cm3 and 1.60 g/cm3, respectively (Bakhtiari et al. Citation2015; Biagiotti, Puglia, and Kenny Citation2004; Moon et al. Citation2011).
Coefficient of acoustic absorption
shows the coefficient of acoustic absorption vs frequency for samples made of native or acetone-treated MW with different fiber contents or ρ. Besides, presents the mean value of the coefficient of acoustic absorption for each sample.
Figure 4. Coefficient of acoustic absorption vs frequency for samples with a fiber content (bulk density, ρ) of 7, 14, 21, and 28 kg/m3 of a) native milkweed floss or b) acetone-treated milkweed floss.
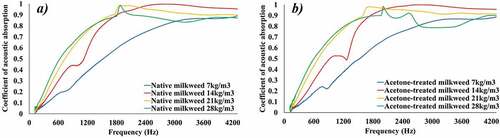
Table 2. Mean coefficient of acoustic absorption for samples with different contents (bulk density, ρ) of native or acetone-treated milkweed floss.
The overall coefficient of acoustic absorption for the two types of fibers improved by increasing the samples’ ρ, just right up until a value of ρ of 21 kg/m3. A further increase in ρ lowered the acoustic insulation capacity of the samples because of a decrease in their mesoporosity and, consequently, an increase in their air flow resistivity (Campeau, Panneton, and Elkoun Citation2019). The peaks in the samples’ coefficient of acoustic absorption were the result of the fibers’ resonance at different wavelengths, whereas the valleys in the coefficient of acoustic absorption were generated by the quarter-wavelength resonance of the samples (Allard and Atalla Citation2009; Cao et al. Citation2018; Crocker Citation2008; Dahl, Rice, and Groesbeck Citation1990; Sarli et al. Citation2021).
The values in indicated that samples with the same ρ had comparable values of coefficient of acoustic absorption independent of the type of fibers they were made of. Therefore, the variations in the microstructure produced by the acetone treatment did not modify the coefficient of acoustic absorption of MW. A similar conclusion was made by Campeau, Panneton, and Elkoun (Citation2019) who noticed that the hollow structure of MW does not influence its acoustic insulating properties.
Ergo, it may be critical to maintain MW’s mesoporous structure but not its hollow structure when using this fiber to improve the acoustic insulation of polymer matrix.
Thermal conductivity
presents the thermal conductivities of samples made of native or acetone-treated MW with different fiber contents or ρ. The results of thermal conductivity for native MW were lower than the value reported by Crews et al. (Citation1991), at 2.24 clo, which is equivalent to 73.15 mW/m K.
Figure 5. Thermal conductivity for samples with different content (bulk density, ρ) of native or acetone-treated milkweed floss.
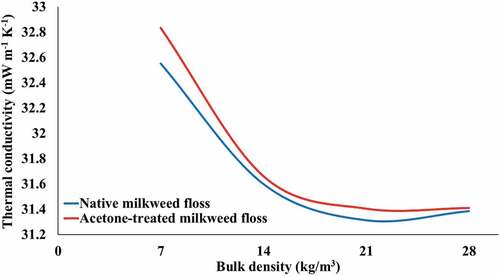
The thermal conductivity decreased with the increase in the samples’ ρ, right up to a value of ρ of 21 kg/m3. The plateau in thermal conductivity may have resulted from the increasing contact between fibers and the decrease in the samples’ θ at large values of ρ. A closer contact between fibers favors heat transfer via conductivity, whereas a decrease in the samples’ θ implies a drop in the volume of air in their structure (Çengel and Ghajar Citation2015).
The thermal conductivity of samples with the same ρ was higher in the samples made of acetone treated fibers when compared with the samples made of native MW. The lower θ, higher exposure of polar groups, and greater contact between fibers may explain the higher thermal conductivity of the samples made of treated fibers. The bends and defects in some of the treated fibers may have acted as contact nodes between fibers that improved the heat transfer via conduction in the samples (Bakhtiari et al. Citation2015; Ovlaque Citation2019; Richard et al. Citation2019; Çengel and Ghajar Citation2015). Likewise, removing the coating layer may have exposed some of the polar groups on the fibers’ surface. This phenomenon has been associated with an increase in the thermal conductivity of fibers (Agrawal et al. Citation2000; Dong et al. Citation2021; Mark Citation2007).
As for the coefficient of acoustic absorption, maintaining the mesoporous structure of MW may be a critical factor for improving the thermal insulation capacity of polymer matrices reinforced with this type of fiber. Besides, it may be a better option to use native MW instead of acetone-treated fibers for improving the thermal insulating capacity of polymer composites.
Thermo-gravimetric analysis
shows the results of the thermogravimetric analysis (TGA) and the differential TGA (δTGA) for native and acetone-treated MW.
Figure 6. a) Thermogravimetric analysis (TGA) and b) differential TGA (δTGA) for native and acetone-treated milkweed floss.

Two peaks of weight loss were identified in the ΔTGA of native MW. The first peak, ranging from 40°C to 110°C, corresponded to the evaporation of water on the surface of MW and in the bulk structure of the samples (Gu, Hessley, and Pan Citation1992; Karthik and Murugan Citation2013, Citation2016a). The sample lost about 3.7% of its weight at these temperatures. The second peak spanned from 190°C to 360°C, having its maximum rate of degradation at 316°C. The weight loss during this event could be attributed to the combined pyrolysis of hemicellulose, free sugars, low-molecular weight lignin, and cellulose (Gu, Hessley, and Pan Citation1992; Karthik and Murugan Citation2016a; Khalid et al. Citation2021; Kim and Agblevor Citation2014; Ovlaque Citation2019). The sample lost about 67.4% of its weight during the second thermal event.
It has been reported that the pyrolysis of hemicellulose occurs between 220°C and 315°C. Lignin degrades at a slow rate from 160°C to 900°C, with a peak of maximum degradation close to 360°C. The pyrolysis of cellulose starts at a temperature above 300°C, just like it was observed in the present study. Kim and Agblevor (Citation2014) reported that the temperature of maximum degradation of cellulose in MW was 296°C, which is significantly lower than the temperatures of maximum degradation of cellulose reported elsewhere (Gu, Hessley, and Pan Citation1992; Ovlaque Citation2019; Yang et al. Citation2007).
Two thermal events were identified in the ΔTGA of acetone-treated MW. The first event took place from 60°C to 120°C, and it corresponded to the evaporation of water in the sample (Gu, Hessley, and Pan Citation1992; Karthik and Murugan Citation2013, Citation2016a). The sample lost 1.5% of its weight over this event, which was less than the weight loss of native MW at these temperatures. This result suggested that the treated fibers had a lower moisture content than the native ones, which agrees with the observations made after treating natural fibers with chemical agents like NaOH, benzoyl chloride, and acetic anhydride (Jagadeesh et al. Citation2021; Khalid et al. Citation2021)
The second thermal event for acetone-treated MW came about from 190°C to beyond 360°C, with its maximum value at 333°C. The weight loss below 300°C may be attributed to the pyrolysis of leftover hemicellulose and low-molecular weight lignin, whereas cellulose and lignin with high-molecular weight degraded above 300°C (Gu, Hessley, and Pan Citation1992; Ovlaque Citation2019; Yang et al. Citation2007). Gu, Hessley, and Pan (Citation1992) found that the maximum degradation of isolated cellulose occurred at a temperature close to 330°C, which agrees with the peak of maximum degradation of acetone-treated MW in the present study. The treated fibers lost 62.2% of their weight during the second thermal event.
Both types of fibers showed a similar onset temperature of degradation; however, the differences in the thermal behavior between native and acetone-treated MW may be explained by the variation in the concentration of hemicellulose and lignin in each type of fiber. Native MW degrades at lower temperatures than the acetone-treated fibers because of its larger proportion of fast degradable components such as waxes, sugars, and low-molecular-weight compounds. In contrast, the higher proportion of cellulose and high-molecular-weight compounds in the treated fibers may explain their greater thermal resistance when compared with native MW (Mayandi et al. Citation2016; Ovlaque Citation2019; Reddy et al. Citation2010; Richard et al. Citation2019). As a result, polymers reinforced with acetone-treated MW may exhibit greater thermal resistance than native MW-reinforced composites.
Mechanical characterization
shows the histograms of FBreak and E for native and acetone-treated MW. displays the FBreak, ε, σ, E, and specific modulus (E/ρA) of native and acetone-treated MW. presents the strain–stress curve for native and acetone-treated MW.
Figure 7. Histograms of breaking force (FBreak) for a) and b) native and acetone-treated milkweed floss, respectively. Histograms of elastic modulus (E) for c) and d) native and acetone-treated milkweed floss, respectively.
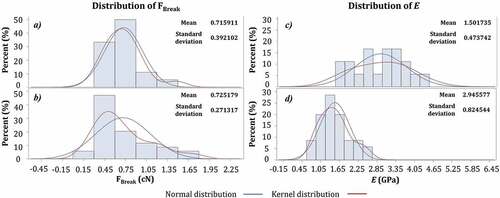
Table 3. Force at break (FBreak), strain at break (ε), tensile strength (σ), elastic modulus (E), and specific modulus (E/ρA) of native and acetone-treated milkweed floss.
The histogram of FBreak for the native MW () displayed a normal distribution, with a mean of 0.72 ± 0.27 cN. The acetone-treated MW FBreak () showed an asymmetric distribution skewed to the right with a mean value of 0.71 ± 0.39 cN. Both types of fibers had comparable values of mean FBreak, yet the values of the standard deviation indicated that there was a greater variability in FBreak for the treated fibers than in the native ones. The presence of bends and crimps may have acted as stress concentration zones in the treated fibers, increasing the variability of their FBreak.
The treatment with acetone caused an increase of 87% in MW’s ε. A similar behavior has been observed when treating MW and other natural fibers with NaOH (Karthik and Murugan Citation2013, Citation2016b; Moon et al. Citation2011; Ovlaque Citation2019). The increase in MW’s ε may be attributed to changes in the fibers’ shape and chemical composition. The mechanical stretching of the twists on the surface of the acetone-treated fibers may have contributed to magnifying the values of ε (Ban et al. Citation2016; Singha and Singha Citation2013). Also, the removal of lignin and hemicellulose that bind cellulose may have resulted in higher rates of mobility and displacement of the microfibrils in MW.
The histogram of E evidenced the decrease in the tensile properties of MW after the treatment with acetone. The native MW’s E () displayed a bimodal distribution with its two peaks at around 3.20 ± 0.82 GPa and 2.60 ± 0.82 GPa, and its mean at 2.94 ± 0.82 GPa. The acetone-treated MW’s E () displayed a close to normal distribution, with its mean at 1.50 ± 0.47 GPa.
The acetone-treated fibers had an E 49% lower than native MW. Ovlaque et al. (Citation2020) observed a decrease of nearly 30% in MW’s E after a treatment with pure boiling acetone and epoxy-silanol. They attributed the decrease of E in the treated fibers to the higher plasticity of their cellulosic wall and the changes in their shape from a straight cylinder to a spring-like configuration. Furthermore, these authors observed a greater improvement in the E of PLA/MW composites when using the treated fibers instead of the native ones, notwithstanding the decrease in the E of the treated fibers.
Conclusions
The spectroscopic analysis indicated that the treatment with acetone removed part of the lignin, hemicellulose, and free sugars from milkweed floss (MW). Likewise, the absence of folds and striae on the surface of the treated MW may be evidence of the removal of their coating layer.
The treatment with acetone did not affect MW’s length or wall thickness. However, this treatment produced the partial collapse of some fibers and the formation of defects along their surface, leading to a slight decrease in MW’s porosity (θ).
The real and apparent densities of MW increased by 1.05% and 3.28%, respectively, after the acetone treatment because of the partial removal of low-density compounds. Likewise, the removal of these compounds slowed down the rates of thermal degradation of MW.
The thermal conductivity of MW increased after the acetone treatment because of the lower θ, increased contact between fibers, and the greater exposure of polar group on the treated fibers. The acetone treatment did not affect the acoustic absorption capacity of MW.
The acoustic absorption and thermal insulating capacities of MW improved with the increase in bulk density (ρ), up to a value of ρ of 21 kg/m3. A further increase in the ρ lowered the insulation capacities of the samples due to a decrease in their mesoporosity and volume of air.
There was no significant difference in the mean tensile strength (σ) of MW before and after the acetone treatment. However, the treated fibers showed a greater variability in their σ due to the asymmetric occurrence of bends and defects after the chemical treatment. Likewise, the stiffness of MW decreased by 49% after the acetone treatment due to a higher mobility of its cellulose microfibrils and the partial removal of linking agents such as lignin and hemicellulose.
This research presents a description of some attributes of MW that could make it an effective fiber for the reinforcement of polymer composites or thermo-acoustic insulation, but further investigation is needed to understand the factors influencing MW’s thermal conductivity and its chemical composition after the treatment with acetone.
Prior studies have demonstrated the reinforcing capacity of MW in thermoplastics. It may be worthwhile investigating the use of MW alone or in conjunction with other fibers in the reinforcement of thermoset composites.
Highlights
This study focused on the characterization of native and acetone-treated milkweed floss and their potential uses as reinforcement in polymer composites.
The properties of native and acetone-treated milkweed floss were studied, including their microstructure, thermo-acoustic insulating capacities, and thermal and mechanical resistances.
When comparing the two types of fibers, the treated fibers showed higher density, thermal conductivity, and thermal resistance than native milkweed floss. Conversely, the treatment with acetone decreased the porosity and mechanical properties of milkweed.
The treatment with acetone did not affect the acoustic absorption capacity of milkweed.
Disclosure statement
No potential conflict of interest was reported by the authors.
References
- Agrawal, R., N. S. Saxena, M. S. Sreekala, and S. Thomas. 2000. Effect of treatment on the thermal conductivity and thermal diffusivity of oil-palm-fiber-reinforced phenol formaldehyde composites. Journal of Polymer Science Part B, Polymer Physics 38 (7):916–14. doi:10.1002/SICI1099-04882000040138:7<916:AID-POLB2>3.0.CO;2-0.
- Allard, J. -F., and N. Atalla. 2009. Propagation of sound in porous media: Modelling sound absorbing materials. 2nd ed. John Wiley and Sons:Chichester.
- Arif, Z. U., M. Y. Khalid, M. F. Sheikh, A. Zolfagharian, and M. Bodaghi. 2022. Biopolymeric sustainable materials and their emerging applications. Journal of Environmental Chemical Engineering 10 (4). doi:10.1016/j.jece.2022.108159.
- Arumugaprabu, V., R. D. J. Johnson, M. Uthayakumar, and P. Sivaranjana. 2022. Polymer-based composites; design, manufacturing, and applications. 1st ed. CRC Press:Boca Raton.
- Ashori, A., and Z. Bahreini. 2009. Evaluation of calotropis gigantea as a promising raw material for fiber-reinforced composite. Journal of Composite Materials 43 (11):1297–304. doi:10.1177/0021998308104526.
- Astrom, B. T. 2018. Manufacturing of polymer composites. 2nd ed. Routledge:Boca Raton.
- Bakhtiari, M., H. Hasani, M. Zarrebini, and S. Hassanzadeh. 2015. Investigation of the thermal comfort properties of knitted fabric produced from estabragh (milkweed)-cotton blended yarns. The Journal of the Textile Institute 106 (1):47–56. doi:10.1080/00405000.2014.902167.
- Ban, E., V. H. Barocas, M. S. Shephard, and C. R. Picu. 2016. Effect of fiber crimp on the elasticity of random fiber networks with and without embedding matrices. Journal of Applied Mechanics 83 (4):410081–87. doi:10.1115/1.4032465.
- Biagiotti, J., D. Puglia, and J. M. Kenny. 2004. A review on natural fibre-based composites. Part I: Structure, processing, and properties of vegetable fibres. Journal of Natural Fibers 1 (2):37–68. doi:10.1300/J395v01n02_04.
- Campeau, S., R. Panneton, and S. Elkoun. 2019. Experimental validation of an acoustical micro-macro model for random hollow fibre structures. Acta Acustica United with Acustica 105 (1):240–47. doi:10.3813/AAA.919305.
- Cao, L., Q. Fu, Y. Si, B. Ding, and J. Yu. 2018. Porous materials for sound absorption. Composites Communications 10:25–35. doi:10.1016/j.coco.2018.05.001.
- Çengel, Y. A., and A. J. Ghajar. 2015. Heat and mass transfer. Fundamentals and applications. 5th ed. McGraw-Hill:New York.
- Chung, D. 2010. Composite materials science and applications. 2nd ed. Springer:New Yor.
- Crews, P. C., S. A. Sievert, L. T. Woeppel, and E. A. McCullough. 1991. Evaluation of milkweed floss as an insulative fill material. Textile Research Journal 61 (4):203–10. doi:10.1177/004051759106100403.
- Crocker, M. J. 2008. Handbook of noise and vibration control handbook of noise and vibration control. 1st ed. John Willey & Sons:New Jersey.
- Dahl, M. D., E. J. Rice, and D. E. Groesbeck. 1990. Effects of fiber motion on the acoustical behaviour of an anisotropic, flexible fibrous material. The Journal of the Acoustical Society of America 87 (1):54–66. doi:10.1121/1.398968.
- Dong, B. X., C. Nowak, J. W. Onorato, T. Ma, J. Niklas, O. G. Poluektov, G. Grocke, M. F. DiTusa, F. A. Escobedo, C. K. Luscombe, et al. 2021. Complex relationship between side-chain polarity, conductivity, and thermal stability in molecularly doped conjugated polymers. Chemistry of Materials. 33(2):741–53. doi:10.1021/acs.chemmater.0c04153.
- Dorigato, A. 2021. Recycling of polymer blends. Advanced Industrial and Engineering Polymer Research 4 (2):53–69. doi:10.1016/j.aiepr.2021.02.005.
- Gu, P., R. K. Hessley, and W. -P. Pan. 1992. Thermal characterization analysis of milkweed floss. Journal of Analytical and Applied Pyrolysis 24 (2):147–61. doi:10.1016/0165-2370(92)85026-H.
- Hassanzadeh, S., and H. Hasani. 2017. A review on milkweed fiber properties as a high-potential raw material in textile applications. Journal of Industrial Textiles 46:1412–36. doi:10.1177/1528083715620398.
- Ismail, S. O., E. Akpan, and H. N. Dhakal. 2022. Review on natural plant fibres and their hybrid composites for structural applications: Recent trends and future perspectives. Composites Part C 9:100322. doi:10.1016/j.jcomc.2022.100322.
- Jagadeesh, P., M. Puttegowda, S. M. Rangappa, and S. Siengchin. 2021. A review on extraction, chemical treatment, characterization of natural fibers and its composites for potential applications. Polymer Composites 42 (12):6239–64. doi:10.1002/pc.26312.
- Karthik, T., and R. Murugan. 2013. Characterization and analysis of ligno-cellulosic seed fiber from pergularia daemia plant for textile applications. Fiber and Polymers 14 (3):465–72. doi:10.1007/s12221-013-0465-0.
- Karthik, T., and R. Murugan. 2016a. Milkweed - a potential sustainable natural fibre crop. In Environmental footprints and eco-design of products and processes, ed. S. S. Muthu, 111–46. 1st ed. Berlin: Springer-Verlag.
- Karthik, T., and R. Murugan. 2016b. Spinnability of cotton/milkweed blends on ring, compact and rotor spinning systmes. Indian Journal of Fiber and Textile Research 41:26–32.
- Khalid, M. Y., A. Al Rashid, Z. U. Arif, W. Ahmed, H. Arshad, and A. A. Zaidi. 2021. Natural fiber reinforced composites: Sustainable materials for emerging applications. Results in Engineering 11. doi:10.1016/j.rineng.2021.100263.
- Khalid, M. Y., A. Al Rashid, Z. U. Arif, M. F. Sheikh, H. Arshad, and M. Ali Nasir. 2021. Tensile strength evaluation of glass/jute fibers reinforced composites: An experimental and numerical approach. Results in Engineering 10. doi:10.1016/j.rineng.2021.100232.
- Khalid, M. Y., Z. U. Arif, W. Ahmed, and H. Arshad. 2022. Recent trends in recycling and reusing techniques of different plastic polymers and their composite materials. Sustainable Materials and Technologies 31. doi:10.1016/j.susmat.2021.e00382.
- Khalid, M. Y., R. Imran, Z. U. Arif, N. Akram, H. Arshad, A. Al Rashid, and F. P. G. Márquez. 2021. Developments in chemical treatments, manufacturing techniques and potential applications of natural-fibers-based biodegradable composites. Coatings 11 (3):293–311. doi:10.3390/coatings11030293.
- Khalil, H. P. S. A., A. H. Bhat, and A. F. I. Yusra. 2012. Green composites from sustainable cellulose nanofibrils: A review. Carbohydrate Polymers 87 (2):963–79. doi:10.1016/j.carbpol.2011.08.078.
- Kim, S. S., and F. A. Agblevor. 2014. Thermogravimetric analysis and fast pyrolysis of milkweed. Bioresource Technology 169:367–73. doi:10.1016/j.biortech.2014.06.079.
- Mark, J. E. 2007. Physical Properties of Polymers Handbook. 2nd ed. Springer US:New York.
- Mayandi, K., N. Rajini, P. Pitchipoo, J. T. W. Jappes, and A. V. Rajulu. 2016. Extraction and characterization of new natural lignocellulosic fiber Cyperus pangorei. International Journal of Polymer Analysis and Characterization 21 (2):175–83. doi:10.1080/1023666X.2016.1132064.
- Meiwu, S., X. Hong, and Y. Weidong. 2010. The fine structure of the kapok fiber. Textile Research Journal 80 (2):159–65. doi:10.1177/0040517508095594.
- Moon, R. J., A. Martini, J. Nairn, J. Simonsen, and J. Youngblood. 2011. Cellulose nanomaterials review: Structure, properties, and nanocomposites. Chemical Society Reviews 40 (7):3941–94. doi:10.1039/c0cs00108b.
- Nourbakhsh, A., A. Ashori, and M. Kouhpayehzadeh. 2009. Giant milkweed (calotropis persica) fibers - a potential reinforcement agent for thermoplastics composites. Journal of Reinforced Plastics and Composites 28 (17):2143–49. doi:10.1177/0731684408091902.
- Ovlaque, P. 2019. Valorization de la fibre d’asclépiade pour le renforcement de matrices organiques. PhD dissertation, Université de Sherbrooke.
- Ovlaque, P., M. Foruzanmehr, S. Elkoun, and M. Robert. 2020. Milkweed floss fiber/PLA composites: Effect of alkaline and epoxy-silanol surface treatment on their mechanical properties. Composite Interfaces 6 (5):495–513. doi:10.1080/09276440.2019.1655316.
- Pickering, K. L., M. G. A. Efendy, and T. M. Le. 2016. “A review of recent developments in natural fibre composites and their mechanical performance. Composites, Part A, Applied Science and Manufacturing 83:98–112. doi:10.1016/j.compositesa.2015.08.038.
- Reddy, K. O., G. S. Reddy, C. U. Maheswari, A. V. Rajulu, and K. M. Rao. 2010. Structural characterization of coconut tree leaf sheath fiber reinforcement. Journal of Forestry Research 21:53–58. doi:10.1007/s11676-010-0008-0.
- Richard, C., P. Cousin, M. Foruzanmehr, S. Elkoun, and M. Robert. 2019. Characterization of components of milkweed floss fiber. Separation Science and Technology 54 (18):3091–99. doi:10.1080/01496395.2018.1556691.
- Sanjay, M. R., S. Siengchin, J. Parameswaranpillai, M. Jawaid, C. I. Pruncu, and A. Khan. 2019. A comprehensive review of techniques for natural fibers as reinforcement in composites: Preparation, processing and characterization. Carbohydrate Polymers 207 (1):108–21. doi:10.1016/j.carbpol.2018.11.083.
- Sarli, M. A., M. Hasanzadeh, M. A. Sarli, A. T. Özgüney, D. Duran, and H. A. Yilmaz. 2021. On the acoustic energy absorption properties of nonwoven layers produced from blend of estabragh and wool fibers. In XVth International İzmir Textile and Apparel Symposium, Bornova, Turkey, 340–47.
- Sengupta, S. 2020. Development of jute fabric for jute-polyester biocomposite considering structure–property relationship. Journal of Natural Fibers 19 (5):1864–78. doi:10.1080/15440478.2020.1788495.
- Singha, K., and M. Singha. 2013. Fiber crimp distribution in nonwoven structure. Frontiers in Science 1:14–21. 2013.
- Sunter, D. A., W. R. M. Iii, J. W. Cresko, and H. P. H. Liddell. 2015. The manufacturing energy intensity of carbon fiber reinforced composites and its effect on life cycle energy use for vehicle door lightweighting. In 20th International Conference on Composite Materials, Copenhagen, Denmark.
- Thakur, V. K., M. K. Thakur, and M. R. Kessler. 2017. Handbook of Composites from Renewable Resources: Functionalization. 4th ed. John Willey & Sons:Chichester.
- Yang, H., R. Yan, H. Chen, D. H. Lee, and C. Zheng. 2007. Characteristics of hemicellulose, cellulose, and lignin pyrolysis. Fuel 86 (12–13):1781–88. doi:10.1016/j.fuel.2006.12.013.
- Zheng, Y., and A. Wang. 2014. Kapok fiber: Structure and properties. In Biomass and Bioenergy: Processing and Properties, ed. K. Hakeem, M. Jawaid, and U. Rashid, 101–10. 1st ed. Cham: Springer.