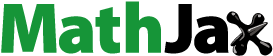
ABSTRACT
Global availability, cost-effectiveness and the excellent crack bridging mechanism offered by the natural fibers played a vital role in the development of sustainable construction. On the other hand, research works in the geopolymer concrete are a significant domain in terms of its zero carbon footprints. Hybridization of natural fibers such as coir and sisal etc, in the geopolymer composite enhanced the ductility and flexural strength of the composite by 37 to 60% than the one developed by synthetic fiber alone. This paper aims to review the reinforcement hybridized effect of natural fiber in the geopolymer concrete development. In case of natural organic fibers, the presence of high polarized hydroxyl groups such as hemicelluloses and lignin reduced the rate of polymerization process and induced porosity. But, the fiber cellulosic content bridges the micro cracks and enhanced the ductility by 60% in the geopolymer composites. Also, the thermal instability and excessive hydrophilic tendency of the natural fibers affects the thermal and workability properties. To overcome these effects, this paper highlights the variation of the behavioral changes by correlating the natural fiber properties and mechanism in order to ensure the development of the most sustainable and eco-friendly natural fiber reinforced geopolymer concrete construction.
摘要
天然纤维提供的全球可用性、成本效益和卓越的裂缝桥接机制在可持续建筑的发展中发挥了至关重要的作用. 另一方面,就其零碳足迹而言,地质聚合物混凝土的研究工作是一个重要领域. 与单独使用合成纤维开发的复合材料相比,在地质聚合物复合材料中混合天然纤维(如椰壳纤维和剑麻纤维等)可提高复合材料的延展性和弯曲强度37%至60%. 本文旨在综述天然纤维在地聚合物混凝土开发中的加固杂交效应. 在天然有机纤维的情况下,高极化羟基(如半纤维素和木质素)的存在降低了聚合过程的速率并诱导了孔隙率. 但是,在地质聚合物复合材料中,纤维纤维素含量桥接了微裂纹,并将延展性提高了60%. 此外,天然纤维的热不稳定性和过度亲水倾向也会影响热性能和加工性能财产. 为了克服这些影响,本文通过关联天然纤维的财产和机理来强调行为变化的变化,以确保发展最可持续、最环保的天然纤维增强土工聚合物混凝土结构.
Introduction
Climate change and the associated hazardous effects such as global warming, drought, severe storms, loss of species, changes in the life cycles are the greatest challenges faced by the human society in this modern era (Castaneda et al. Citation2020). Excessive emissions of green house gases are the root cause of all such disasters. Construction industry alone emits nearly 7% of the total green house gases due to the wide use of cementitious material (de Mendonça Neuba et al. Citation2020). Approximately, a tonne of cement usage is responsible for a tonne of green house gas emission. In order to overcome these effects, in the earlier 1979, Prof. Davidovits invented an inorganic alternative binder system named geopolymer. As the name indicates, geopolymer mainly consist of earthen siliceous material synthesized by activating the alumino-silica minerals such as fly ash, ground granulated blast furnace slag (GGBS) by means of sodium or potassium based alkaline solution. The derived alternative binder system leads to the greener and environmental friendly construction by eliminating 80% of the overall green house gas emitted by the construction industry (Li et al. Citation2022). Recently, the geopolymer composite construction system, are gaining more interest due to the high early strength, extremely better durability and micro structural characteristics than the conventional cement concrete construction (Khan et al. Citation2018b).
Even though the geopolymer composite offered excellent sustainability against vulnerable acidic, sulfate and chloride environments than the conventional cement construction, the lack of flexural strength and the brittle nature of the concrete system acts as a major obstruction for the practical concern (Souza et al. Citation2020). This led to the severe disintegration and the sudden collapse of the structural element without prior warning. Incorporation of fiber in the brittle geopolymer medium resulted in the excellent crack arresting phenomenon and transformed the mode of failure into ductile manner (Aisyah et al. Citation2014). Most of the research works involved in the use of synthetic fibers such as carbon, steel, glass and polypropylene fibers etc., due to the high tensile strength and better compatibility in the geopolymer concrete (Zhang et al. Citation2018). But the material resource exploitation, complexity of production, cost of manufacturing and the increased self weight of the synthetic fibers are the major influencing factor to be considered on the synthetic fiber reinforced geopolymer composites (Maranan et al. Citation2021).
In the recent times, geopolymer concrete researchers shifted their interest on the side of natural fiber reinforced composite due to the eco-friendly, naturally available and simple manufacturing techniques. Korniejenko et al. (Citation2016) reported that the use of natural cotton, sisal and coir fibers resulted in the 26.55%, 14.68% and 1.53% improved compressive strength in the geopolymer composite. Similarly, Ye et al. (Citation2018) concluded that the increase in the addition of cellulose fibers well bridge the micro cracks and resulted in the ductile fracture in the geopolymer composites. However, the poor resistance to moisture absorption, low dimensional stability like shrinkage and swelling, and low fire resistance capacity are considered as the main drawbacks of natural fibers incorporation in the geopolymer composites. This is due to the presence of the high polarized hydroxyl groups in the form of lignin and hemicellulose compound in the natural fibers (Ganesan, Sahana, and Indira Citation2017).
To overcome the constraints of using synthetic and natural fibers, hybridization of the fibers in the geopolymer construction are highly encouraged nowadays. The concept of hybridization is the trend in which the addition of two or more types of fiber in the concrete helps to achieve higher engineering properties since the existence of one fiber allows the effective application of the potential properties of the other fiber (Shah et al. Citation2020). Achieving compatibility between the fibers and the geopolymer matrix is the main parameter to be considered while producing hybridized natural fiber reinforced geopolymer composites. In this review, the role of hybridized natural fiber in the geopolymer concrete was identified and aimed to achieve wide prospect application in structural applications. Most commonly, in construction industry, natural plant fibers were employed due to the complexity of extracting animal fibers. The different types of natural plant fibers with the various source materials used in geopolymer concrete on the mechanical properties like compressive strength, split tensile strength and flexural strength, their toughness, ductility and energy absorption capacity are presented. This review work done on the mechanism involved in the enhancement of mechanical properties in the geopolymer concrete while incorporating natural fibers intended to provide the structural behavior of hybrid fiber reinforced geopolymer concrete in the strength and durability aspects.
Exploration of hybridized natural fibers on the development of geopolymer concrete
Geopolymers are the chain or network of inorganic molecule in which its chemical composition is similar to Zeolites but with the amorphous microstructure properties. The term Geo polymer was first presented by Prof. Davidovits in the year 1979 to characterize the wide range of binders with the network of molecules linked with the covalent bond. The source material or by-product material for the production of Geopolymer concrete is Fly Ash, GGBS, metakaolin, silica fume, rice husk ash etc. The polymeric reaction occurs with the alkaline activator solution and the by- product or source materials obtained from the geological origin (Marvila et al. Citation2021). Here, the chemical reaction takes place in the form of polymerization process. The polymerization reaction of Geopolymer concrete is a fast chemical reaction in which the silica and alumina minerals creates a three-dimensional polymeric chain or network of tetrahedral formation (Gopalakrishnan and Chinnaraju Citation2019). Generally, the concrete possesses the compressive strength more than 55 MPa by adding novel ingredients such as mineral additives, nano materials and fiber reinforcement etc are termed out to be high strength concrete and geopolymer concrete is also one of the types of high strength concrete in the aspect of compressive strength (Shah et al. Citation2020). To enhance the tensile strength and ductility characteristics of the geopolymer concrete the following fibers were used by various researchers. The various types of fibers are used in the manufacturing of high strength concrete and the major classifications of these fibers are given in .
In the construction of hybridized natural fiber reinforced geopolymer, sisal, cotton, jute, coir, luffa, bamboo and flax fibers were generally employed. By considering the merits and demerits of natural and synthetic fibers, the recent geopolymer research works are focused on the hybridization of synthetic and natural fiber reinforcement on the geopolymer composite construction (Sathiskumar, Naveen, and Satheeshkumar Citation2017). On the whole, it was inferred that each natural fiber has its own unique application on the hybridized fiber reinforced geopolymer construction. The highlights of those merits of each natural fiber on the hybridized fiber reinforced geopolymer concrete is listed in .
Table 1. Role of natural fibers on the properties of geopolymer concrete.
Contribution of natural fiber hybridization on the characteristics of geopolymer composite
Mechanism of attaining stronger and denser geopolymer composite using natural fiber hybridization process
Density of the geopolymer matrix is the main factor which influence the strength attainment phenomenon of the hybridized natural fiber reinforced geopolymer composite. Denser the matrix, higher is the attainment of mechanical strength (Komnitsas et al. Citation2015). The density of fiber reinforced geopolymer composite depends upon the percentage of fiber addition and the specific gravity of the fiber used. Abbas, Singh, and Singh (Citation2021) represented the relationship between the fiber and the density of geopolymer composite by using Eq.1
Vrf is the volume fraction of the fiber reinforcement; γf is the density of fiber; Vrm is the volume fraction of the matrix and γm is the density of the matrix.
To line with this Eq.1, Punurai et al. (Citation2018) reported that the incorporation of basalt fiber in the geopolymer concrete increased the density of the matrix due to the high specific gravity of the basalt fiber. While using hemicelluloses and lignin fibers in the geopolymer concrete, Nedeljkovi et al. (Citation2018) found that the increase in the fiber content resulted in the reduction in the density properties. This is due to the increased porosity of fiber reinforced geopolymer matrix at the time of mixing. Similarly, Poletanovic et al. (Citation2020) reported that the addition 0.5% volume of hemp fiber resulted in the 5% reduction in the density of geopolymers with fly ash and GGBS as solid prime materials. The density reduction in the hemp fiber reinforced geopolymer was attributed by the highly porous fiber-matrix interface. This is due to the accumulation of entrapped air within the concrete. Also, the natural hemp fiber possesses lower density than the other geopolymer ingredients and led to the reduction in the overall density of the hemp fiber reinforced geopolymer matrix. On the other hand, Castaneda et al. (Citation2020) conducted an experimental research by using jute and sisal fiber reinforcement on the geopolymer composite. From the results, it was suggested that the use of 1% weight of jute and sisal fiber in the geopolymer composite increased the density of matrix and the density of the same will be decreased if the fiber addition exceeds beyond 1% by weight of the matrix. The higher compaction employed during the mixing process led to the improvement in the viscosity of the composite due to which the workability of the matrix at fresh state tend to get reduced (Chen et al. Citation2014). The improved viscosity not only reduced the workability but also acted as a major fact for the improvement in the density of the natural fiber reinforced geopolymer composite. However, the increase in the addition of jute and sisal fiber beyond 1% by weight resulted in the reduction in the density characteristics due to the phenomenon named agglomeration. The agglomerated fibers got clustered each other and led to the formation of inter granular pores which attributes to the reduction in the density of the resultant composites. All these conclusions were in line with the equation formed by Abbas et.al (2022) which confirms the variation of natural fiber reinforced geopolymer composite with the volume fraction and specific gravity of the natural fibers. Similarly, the effect of various types of fibers with different volume fractions on the density and other mechanical properties of geopolymer composites were listed in .
Synergetic effect of the hybridized natural fiber on the structural characteristics of the geopolymer composites
The hybridization of natural fibers in the geopolymer medium depends on the synergetic effect between the fibers which caused the enhancement in the structural properties as indicated in . Shah et al. (Citation2020) reported that the strength of the geopolymer concrete was not increased due to the hybridization of natural fiber but the hybridized fiber considerably enhanced the ductility characteristics of the geopolymer beams. On the other hand, Castaneda et al. (Citation2020) reported that hybridization of natural fibers involved in the improvement in both strength and ductility properties than the geopolymer composites with mono fiber addition.
Figure 2. Effect of natural fiber and hybridization effect on the strength and durability characteristics of the geopolymer concrete.
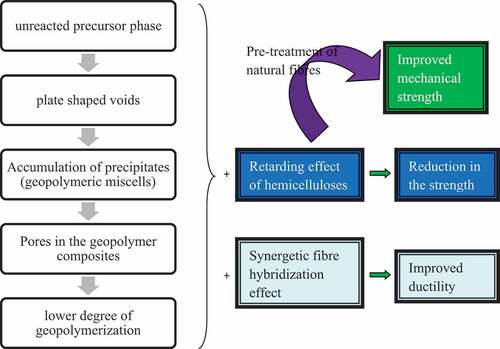
Ye et al. (Citation2018) investigated the hybridized effect of different cellulosic, lignin and hemicellulosic fibers and reported that the addition of mono fiber improved the ultimate strength, crack resistance and strain capacity. But, the hybridized fibers resulted in the excellent impact resistance due to the synergetic effect. From the research work done by Palanisamy and Ramasamy (Citation2020) it was observed that the addition of polypropylene and sisal fiber exhibited huge number of flexural cracks than the counterpart specimens with monofibre addition. This represented the effectiveness of the polypropylene and sisal fiber hybridization in the crack bridging mechanism and the stress redistribution mechanism.
Similarly, Souza et al. (Citation2020) reported that the hybridization of polypropylene, glass and lignin fiber increased the ductility of the geopolymer beams by 24% than the mono fiber reinforced geopolymer composites. The main reason behind this ductility enhancement characteristics were due to the fracture toughness of hybridized fiber composites which resisted the crack growth and improved the ductility properties. On the other hand, Trindade, Borges and da Silva Alves et al. (Citation2019) stated that the hybridization of PVA fiber and Curaua fiber exhibited 47% improved shear strength characteristics than the geopolymer beams with mono Curaua fiber. The effects of natural fiber hybridization effects on the geopolymer composite are represented in . On the whole, it was inferred that some of the fibers such as sisal fiber and caraua fiber contributed to the strength enhancement properties while undergoing hybridization phenomenon. But, hemi cellulosic fibers exhibited improved ductility characteristics and showed marginal improvement in the strength properties (Stalin et al. Citation2021). This is due to the synergetic nature of the hybridized fibers on the geopolymerisation process. So, further studies are required to be done on the applicability of fiber hybridization in the structural behavior of the geopolymer composites.
Mechanical strength
Most of the researchers hybridized steel fiber with the different types of fibers in order to study their strength performance in the high strength concrete (Khan et al. Citation2018). The processing and synthetic parameters involved in the fiber reinforced geopolymerisation process and evaluation tests used in the attainment of high strength were described in . Also, the comparison between the different natural fibers and the corresponding improvement on the mechanical strength of the geopolymer composites was indicated as shown in .
Figure 3. List of synthesis and processing parameters and strength evaluation tests in hybridized natural fiber reinforced geopolymer composites.
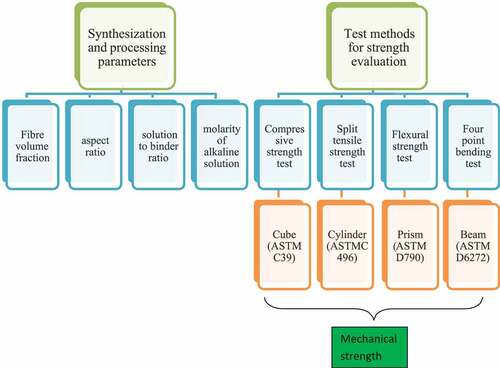
Figure 4. Graphical comparison of the role of natural fiber on the mechanical strength development of geopolymer composites. (a) Compressive strength. (b) Split tensile strength. (c) Flexural strength.
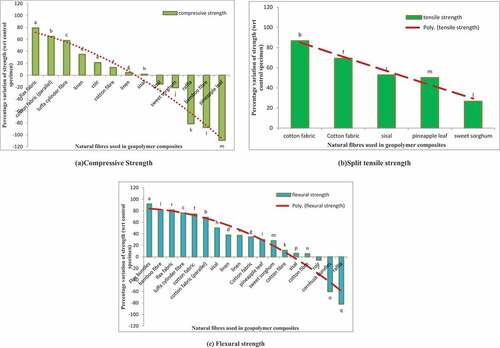
Aisyah et al. (Citation2014) reported that while using mono banana fiber in the high strength concrete, the compressive strength of concrete was significantly reduced due to the increase in the pore volume in the micro structure. Also, the density of the banana fiber is significantly higher than the sisal and polypropylene fibers. It is very difficult for the high density banana fibers to get penetrated into the concrete phase and hence the banana fiber reinforced concrete system showed lower compressive strength. But the hybridization of poly propylene and sisal fibers with banana fibers resulted in the 47% improvement in the compressive strength than the cement concrete due to the uniform dispersion of composite fibers throughout the geopolymer concrete. Similarly, Walbruck et al. (Citation2021) reported that an increased amount of Miscanthus fibers from 30 to 40 wt% leads to a significant increase in the strength from 0.139 to 0.305 MPa as the miscanthus fibers offers better adhesion on the alkaline geopolymer medium.
According to Khan et al. (Citation2018a) two phenomena could be observed in respect of compressive strength due to the addition of fibers. The first one is an increase in the compressive strength when the capacity of the fibers to prevent cracks overshadows the effect of the induced porosity through the fibers. In contrast, a decrease in compressive strength could be observed when the increase in porosity dominates. As an evident to this conclusion, Korniejenko et al. (Citation2016) reported that when the geopolymer composites were reinforced with different amounts of cotton fibers ranging from 0 to 1 wt%, it was observed that geopolymer composites reinforced with 0.5 wt% cotton had the highest compressive strength. Due to the hybrid fiber reinforcement, higher loads are transferred from the geopolymer matrix to the fiber reinforcements. On the other hand, Wongsa et al. (Citation2020) reported that in addition to the fiber content, the fiber size and the amount of added admixture showed a significant influence on the compressive strength. While comparing the results for the thermal conductivity, the increase of fiber size from 125 to 250 μm led to a porous microstructure. This induced the higher amount of parenchyma of the fibers which is responsible for the reduction in compressive strength from 0.350 to 0.085 MPa.
Poletanovic et al. (Citation2020) reported that the addition of 1% hemp fibers by volume tend to reduce the flexural strength of the fly ash based geopolymer composite by 21% than their counterpart without fibers. But, the addition of 1% volume of hemp fiber in the GGBS based geopolymer composite exhibited insignificant reduction in the flexural strength. From this finding, it was inferred that GGBS based binders exhibited improved density and compatibility on the hemp fiber reinforcement than the fly ash binders and enables the GGBS based geopolymer concrete to maintain the flexural strength. But, the research work carried out by Alomayri et al. (Citation2013) and Alomayri et al. (Citation2014) reported that the geopolymer composite having cotton fabrics exhibited improved flexural strength than the plain geopolymer. The ability of the cotton fabrics to bridge the cracks irrespective of the orientation, resulted in the efficient stress transfer at the ITZ which enhanced the flexural strength. Due to this effect, the increase in the addition of fiber content resulted in the significant improvement in the flexural strength. As an evident to this conclusion, the flexural strength of the cotton fiber reinforced geopolymer composite increased from 12 to 31.7 MPa while increasing the fiber content respectively from 3.6% to 8.3% by weight. Due to the light weight properties of cotton fabrics, inclusion of several layers of such fiber enables the geopolymer composite to resist shear deformation. Also, the efficient stress transfer achieved between the fiber and binder interface resulted in the improved flexural strength.
Durability
Ductility and energy absorption capacity
The addition of fibers in the concrete reduces the propagation of cracks in the concrete thereby changes the behavior of concrete from brittle to ductile in nature (Ma, Awang, and Omar Citation2018). Poletanovic et al. (Citation2020) reported that during the post peak stage, no deformation capacity was observed on the plain geopolymer concrete. After reaching the ultimate point, a sudden drop was observed in the post peak region. This indicates the weak energy absorption capacity of the plain geopolymer concrete. On the other hand, the geopolymer composite reinforced with hemp fibers undergoes large deflection under the same load. Higher the fiber addition, higher will be deflection capacity. To line with these conclusion Assaedi, Shaikh, and Low (Citation2021) reported that plain geopolymer with nano clay exhibited zero values of toughness due to their extreme brittleness. On the other hand, the geopolymer composite with flax fiber reinforcement showed higher toughness due to the capability of these fibers to resist the load. Also, the flax fiber reinforcement caused the geopolymer composite to develop network of cracks during the loading process and transformed the mode of failure into ductile manner. It was emphasized that the application of natural fiber in the geopolymer concrete resulted in the improved fracture toughness and energy absorption capacity. Similarly, Alomayri et al. (Citation2013) found that the geopolymer composite having 0.5% cotton fibers resulted in 60% improved toughness than the plain geopolymer. Further addition of cotton fiber led to the non uniform distribution in the matrix and this effect attributed to the decrease in the toughness of the geopolymer composites.
Chemical resistance
To explore the impermeable properties of geopolymer concrete with bar chip fibers, Ramli, Kwan, and Abas (Citation2013) carried out the durability research work by immersing the concrete in the seawater conditions for 180 to 546 days. It was observed that the chloride ion permeability of geopolymer concrete with bar chip fiber was lesser than the counterpart specimen with 0% fiber reinforcement. The bar chip fibers involved in the process of minimizing the crack orientation by constraining the specimens from volume expansions and reduced the rate of permeation. Guo and Xiong (Citation2021) carried out a research work by employing polypropylene, basalt and steel fiber and studied the effect of fiber reinforcement under the sulfate and freezing thawing cycles for 28 days. The results indicated that the fiber reinforcement in the geopolymer concrete reduced the rate of mass loss by 4% than the control specimen. But, still few research works were done in the field of fiber reinforced geopolymer concrete under chemical resistance and more studies are required to be carried out to evaluate the chemical durability of the natural fiber reinforced geopolymer concrete.
Performance of natural fiber reinforced composite under elevated temperature
The thermal instability and resultant the strength reduction were occurred in the geopolymer composites due to the dehydration and evaporation of the water from the matrix. The employment of suitable fibers with required volume fraction enhanced the thermal and residual properties of the geopolymer concrete (Kong, Sanjayan, and Sagoe-Crentsil Citation2007). The inclusion of fibers preserved the structural and mechanical integrity of the geopolymer composite under high temperatures. The fine and homogeneous distribution of crystalline fibrous materials contributed positively on the mechanical strength (Ali et al. Citation2019). Nkwaju et al. (Citation2019) reported that the use of natural fiber in the geopolymer composite enhanced the material insulation properties. While using bagasse fibers the thermal conductivity of the geopolymer composite reduced from 0.77 to 0.55 W/m K. This is due to the lower thermal conductivity of the bagasse fibers than the other geopolymeric binders. Also, the inclusion of bagasse fiber increased the porosity at the fiber-binder interface which reduced the thermal conductivity of the composites. Due to the lower thermal conductivity of the bagasse fibers, it is highly preferable for the insulating applications.
Micro structural properties
In the micro structure of the natural fiber reinforced geopolymer composites, the significant influencing factor to be emphasized is its interfacial transition zone (ITZ). Because of the relatively higher aspect ratio and larger surface contact of the natural fibers than the other geopolymer ingredients, the ITZ of the natural fiber reinforced geopolymer concrete is a critical factor to be considered in the micro structural study than the plain geopolymer. The properties of these ITZ are highly influenced by the solution to binder ratio, nature of the fiber and the inclusion of the additives. Under the application of external pull, the resistance offered by the ITZ between the fiber and the geopolymer was activated by means of adhesive chemical binding mechanism (Abdollahnejad et al. Citation2018). At this phase, the fiber and the matrix deformations are fully compatible and confirm the ITZ not to get damaged. Upon the continuous application of external loading, the quality of the ITZ bonding purely depends on the composite behavior between the type of natural fiber and the geopolymeric materials. Masi et al. (Citation2015) reported that the inclusion of synthetic fiber led to the better improvement in mechanical strength of the geopolymer composite than the one with natural fibers. As an evident of this, the SEM results indicate that the PVA fiber was totally covered with geopolymeric products a.
Also, the longitudinal striations on the PVA surface resulted in the increased bonding between the geopolymer paste and fiber. But, the smooth surface of the basalt fiber resulted in a weak bonding of fiber with the surrounding geopolymer paste. As a result of this phenomenon, no geopolymer products were observed around the pulled out basalt fiber as shown in c. On the other hand, Castaneda et al. (Citation2020) reported that the addition of jute and sisal fiber in the geopolymer composite showed a better strength performance than the plain geopolymer concrete. The sufficient fiber-geopolymer interactions enhanced the energy absorption mechanism starting from fiber pull out, debonding and up to the stress transfer phenomenon. This efficient stress transferring mechanism of the sisal and jute fiber resulted in the improved mechanical strength of the geopolymer composites.
Effectiveness of natural fiber pre-treatment techniques on the geopolymer composites
Eventhough the use of natural fibers in the geopolymer composites offered numerous benefits, some limitations exist as obstruction for the practical use. Ye et al. (Citation2018) insisted that the presence of non-cellulosic organic compounds in the natural fibers such as lignin, hemicellulose, etc, are sensitive to the alkaline medium of the geopolymer composites. The compatibility of natural fibers with the geopolymer composite is highly affected by the degradation of these non-cellulosic compounds. The presence of hemi cellulose induced the formation of carboxylic acids and reduced the rate of geopolymerisation process. Also, these hemicelluloses and lignin in geopolymer composite attributed to the formation of porous microstructure which resulted in the reduced density and brittle fracture. This attributed to the corresponding reduction in the strength characteristics of the natural fiber reinforced geopolymer concrete. To overcome this limitations, Lazorenko et al. (Citation2021) employed mercerization with 5% sodium hydroxide and ultrasonic treatment on the flax fibers and used in the geopolymer composites. The prescribed pre-treatment technique effectively extracted the non-cellulosic compounds from the natural fiber and resulted in the improved ITZ and mechanical strength of the flax fiber reinforced geopolymer composites. Similarly, Alshaaer et al. (Citation2017) carried out a research on the micro structural characteristics of geopolymer concrete reinforced with luffa fibers having the various length ranging from 100 to 400 µm. It was observed that the luffa fibers are filled with fibrous vascular fibrils of 10 µm diameter and plant tissue resins. During the geopolymerisation process, the hemicelluloses and lignin existed in the luffa fibers are significantly consumed. This resulted in the reduction of hydroxyl groups and the increase in the surface roughness. Due to this effect, the hydrophilic nature of the luffa fiber was highly reduced and enabled the water to make strong bond between the fiber and the geopolymer binder. At the time of geopolymerisation process, the fiber bundle broke down into small filaments. This reduced the diameter of the luffa fiber and increased the aspect ratio. The increased aspect ratio attributed to the improved adhesion at the fiber-binder interfaces which increased the mechanical strength. Only few research studies were carried out on the assessment of natural fiber pre-treatment techniques and the associated changes in the durability characteristics of the geopolymer concrete with natural fiber reinforcement. Still further pre-treatment techniques are required to be developed for the successful and effective application of natural fiber hybridization in the development of durable and eco-friendly geopolymer construction.
Limitations of the natural fiber hybridizations and research scope
Most of the research works are conducted by implementing steel fibers as main reinforcement and other smaller fractions of fibers such as coir, kenaf, banana and polypropylene fibers as supporting reinforcements to attain the flexibility, ductility, energy absorption and other unique desired features. This is due to the higher tensile strength and Youngs modulus offered by the steel fibers. At the same time, the hybridization of two or more natural fibers such as kenaf and banana fibers resulted in the porous micro structure with more swelling ability which affects their durability characteristics Narayanan Sivakumaresa Chockalingam and Merina Rymond (Citation2021). While comparing the costs of various natural fibers used in the geopolymer composite, it was observed that the market price of each fiber depends upon the source material and processing cost as compared in .
Figure 6. Comparison of the market price of the various natural fiber employed on the geopolymer composites.
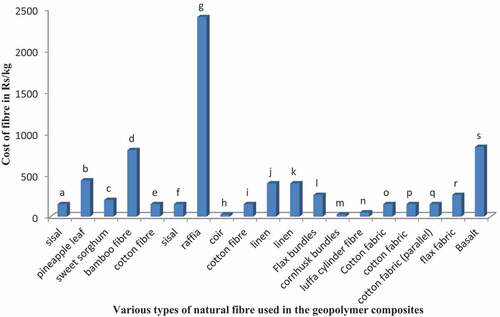
Some of the fibers such as raffia, bamboo and basalt fibers are highly beneficial for the improvement of flexural strength but has high material cost. So a cost effective method of deriving these fibers are the most required field of research on the development of cost effective natural fiber hybridized geopolymer composites. The research in the hybridization of natural fibers in geopolymer concrete is very limited and more natural hybrid combinations have to be analyzed for the future geopolymer construction. The hybridization of various combinations of synthetic and natural fibers are required to be analyzed in order to understand its performance in structures. Also, the effectiveness of the different pre-treatment techniques such as chemical, thermal and oxidation process etc, of the natural fiber has to be explored on the various micro structural and durability aspects of the natural fiber hybridized geopolymer composites.
Conclusion
As the density and hydrophilic properties of the natural fibers affect the workability properties of the natural fiber hybridized geopolymer composites, the pre-drying and sodium hydroxide immersion techniques are essential for the natural fiber before applying in the geopolymer composites.
While assessing the hybridization of basalt and steel fiber, it was inferred that limiting the total volume of fiber addition within 1% resulted in the 37.14% improved tensile strength.
The increase in the aspect ratio of the luffa fibers and the consumption of hemicellulosic and lignin in the geopolymerisation process significantly reduced the hydroxyl groups and increased the surface roughness. Also, the improved fiber binder interaction resulted in the increased mechanical strength.
The hybridization of coconut coir fiber with PVA fiber induced 60% improved impact resistance characteristics in the geopolymer concrete medium and exhibited ductile mode of deformation.
The thermal conductivity of bagasse fibers are significantly lower than the other geopolymeric binders and led to the better thermal insulation phenomenon inside the geopolymer composites.
The hybridized synthetic and natural fibers enhanced the mechanical and durability characteristics of concrete than the mono fiber application. This review will pave a new way of developing natural fiber hybridized with synthetic fibers at the specific volume fraction resulted in the more durable, high strength geopolymer concrete construction.
Highlights
Behavioral characterization of natural fiber hybridized geopolymer concrete elements
Exploration of fiber hybridization on the concrete properties
Comparative review on the combined synthetic and natural fiber effect
Disclosure statement
No potential conflict of interest was reported by the authors.
References
- Abbass, M., D. Singh, and G. Singh. 2021. Properties of hybrid geopolymer concrete prepared using rice husk ash, fly ash and GGBS with coconut fiber. Materials Today Proceedings. doi: 10.1016/j.matpr.2021.01.390.
- Abdollahnejad, Z., M. Mastali, T. Luukkonen, P. Kinnunen, and M. Illikainen. 2018. Fiber-reinforced one-part alkali-activated slag/ceramic binders. Ceramics International 44 (8):8963–18. doi:10.1016/j.ceramint.2018.02.097.
- Aisyah, H. A., P. M. Tahir, S. M. Sapuan, R. A. Ilyas, A. Khalina, N. M. Nurazzi, S. H. Lee, and C. H. Lee. 2021. A comprehensive review on advanced sustainable woven natural fibre polymer composites. Polymers 13. doi:10.3390/polym13030471.
- Ali, A., M. Uysal, A. Yılmaz, M. M. Al-Mashhadani, O. Canpolat, F. Şahin, and Y. Aygörmez. 2019. Influence of wetting-drying curing system on the performance of fiber reinforced metakaolin-based geopolymer composites. Construction and Building Materials 225:909–26. doi:10.1016/j.conbuildmat.2019.07.235.
- Alomayri, T., H. Assaedi, F. U. A. Shaikh, and I. M. Low. 2014. Effect of water absorption on the mechanical properties of cotton fabric-reinforced geopolymer composites. Journal of Asian Ceramic Societies 2 (3):223–30. doi:10.1016/j.jascer.2014.05.005.
- Alomayri, T., and I. M. Low. 2013. Synthesis and characterization of mechanical properties in cotton fiber-reinforced geopolymer composites. Journal of Asian Ceramic Societies 1 (1):30–34. doi:10.1016/j.jascer.2013.01.002.
- Alomayri, T., F. U. A. Shaikh, and I. M. Low. 2013. Characterisation of cotton fibre-reinforced geopolymer composites. Composites Part B: Engineering 50:1–6. doi:10.1016/j.compositesb.2013.01.013.
- Alomayri, T., F. U. A. Shaikh, and I. M. Low. 2014. Effect of fabric orientation on mechanical properties of cotton fabric reinforced geopolymer composites. Materials & Design 57:360–65. doi:10.1016/j.matdes.2014.01.036.
- Alshaaer, F. R. M., S. Mallouh, J. Al-Kafawein, Y. Al-Faiyz, T. Fahmya, and A. Kallel. 2017. Fabrication, microstructural and mechanical characterization of Luffa Cylindrical Fibre - Reinforced geopolymer composite. Applied Clay Science 143:125–33. doi:10.1016/j.clay.2017.03.030.
- Assaedi, H., F. U. A. Shaikh, and I. M. Low. 2016. Characterizations of flax fabric reinforced nanoclay-geopolymer composites. Composites Part B: Engineering 95:412–22. doi:10.1016/j.compositesb.2016.04.007.
- Castaneda, D., G. Silva, J. Salirrosas, S. Kim, B. Bertolotti, J. Nakamatsu, and R. Aguilar. 2020. Production of a lightweight masonry block using alkaline activated natural pozzolana and natural fibers. Construction and Building Materials 253:199143. doi:10.1016/j.conbuildmat.2020.119143.
- Chen, R., S. Ahmari, and L. Zhang. 2014. Utilization of sweet sorghum fiber to reinforce fly ash-based geopolymer. Journal of Materials Science 49 (6):2548–58. doi:10.1007/s10853-013-7950-0.
- Chen, K., W. Dazhi, L. Xia, Q. Cai, and Z. Zhang. 2021. Geopolymer concrete durability subjected to aggressive environments – a review of influence factors and comparison with ordinary Portland cement. Construction and Building Materials 279:122496. doi:10.1016/j.conbuildmat.2021.122496.
- Correia, E., S. Torres, M. Alexandre, K. Gomes, N. Barbosa, and S. Barros. 2013. Mechanical performance of natural fibers reinforced geopolymer composites. Materials Science Forum 758:139–45. doi:10.4028/0000www.scientific.net/MSF.758.139.
- da Silva Alves, L. C., R. A. dos Reis Ferreira, L. Bellini Machado, and L. A. de Castro Motta. 2019. Optimization of metakaolin-based geopolymer reinforced with sisal fibers using response surface methology. Industrial Crops and Products 139:111551. doi:10.1016/j.indcrop.2019.111551.
- de Mendonça Neuba, L., R. F. Pereira Junio, M. P. Ribeiro, A. T. Souza, E. de Sousa Lima, F. D. C. Garcia Filho, A.B. -H.D.S. Figueiredo, F. D. O. Braga, A. R. G. D. Azevedo, and S. N. Monteiro. 2020. Promising mechanical, thermal, and ballistic properties of novel epoxy composites reinforced with cyperus malaccensis sedge fiber. Polymers 12 (8):1776. doi:10.3390/polym12081776.
- Ganesan, N., R. Sahana, and P. V. Indira. 2017. Effect of hybrid fibers on tension stiffening of reinforced geopolymer concrete. Advances in Concrete Construction 5 (1):75–86. doi:10.12989/acc.2017.5.1.75.
- Gopalakrishnan, R., and K. Chinnaraju. 2019. Durability of ambient cured alumina silicate concrete based on slag/fly ash blends against sulfate environment. Construction and Building Materials 204:70–83. doi:10.1016/j.conbuildmat.2019.01.153.
- Guo, X., and G. Xiong. 2021. Resistance of fiber-reinforced fly ash-steel slag based geopolymer mortar to sulfate attack and drying-wetting cycles. Construction and Building Materials 269:121326. doi:10.1016/j.conbuildmat.2020.121326.
- Khan, M. Z. N., Y. Hao, H. Hao, and F. U. A. Shaikh. 2017. Mechanical properties of ambient cured high strength hybrid steel and synthetic fibers reinforced geopolymer composites. Cement and Concrete Composites 85:133–52. doi:10.1016/j.cemconcomp.2017.10.011.
- Khan, M. Z. N., Y. Hao, H. Hao, F. UAShaikh, and K. Liu. 2018a. Experimental evaluation of quasi static and dynamic compressive properties of ambient cured high strength plain and fibers reinforced geopolymer composites. Construction and Building Materials 166:482–99. doi:10.1016/j.conbuildmat.2018.01.166.
- Khan, M. Z. N., Y. Hao, H. Hao, F. UAShaikh, and K. Liu. 2018b. Mechanical properties of ambient cured high strength plain and hybrid fibers reinforced geopolymer composites from triaxial compressive tests. Construction and Building Materials 185:338–53. doi:10.1016/j.conbuildmat.2018.07.092.
- Komnitsas, K., D. Zaharaki, A. Vlachou, G. Bartzas, and M. Galetakis. 2015. Effect of synthesis parameters on the quality of construction and demolition wastes (CDW) geopolymers. Advanced Powder Technology 26 (2):368–76. doi:10.1016/j.apt.2014.11.012.
- Kong, D., J. Sanjayan, and K. Sagoe-Crentsil. 2007. Comparative performance of geopolymers made with metakaolin and fly ash after exposure to elevated temperatures. Cement and Concrete Research 37 (12):1583–89. doi:10.1016/j.cemconres.2007.08.021.
- Korniejenko, K., E. Froczek, E. Pytlak, and M. Adamski. 2016. Mechanical properties of geopolymer composites reinforced with natural fibers. Procedia Engineering 151:388–93. doi:10.1016/j.proeng.2016.07.395.
- Korniejenko, K., M. Łach, M. Hebdowsk-Krupa, and J. Mikuł. 2018. The mechanical properties of flax and hemp fibers reinforced geopolymer composites. In IOP Conference Series Materials Science and Engineering, Blansko-Cezkovice, 379: 012023.
- Lazorenko, G., A. Kasprzhitskii, V. Yavna, V. Mischinenko, A. Kukharskii, and A. Kruglikov. 2020. Effect of pre-treatment of flax tows on mechanical properties and microstructure of natural fiber reinforced geopolymer composites. Environmental Technology and Innovation 20:101105. doi:10.1016/j.eti.2020.101105.
- Li, W., E. D. Shumuye, T. Shiying, Z. Wang, and K. Zerfu. 2022. Eco-friendly fibre reinforced geopolymer concrete a critical review on the microstructure and long-term durability properties. Case Studies in Construction Materials 16:894. doi:10.1016/j.cscm.2022.e00894.
- Ma, C. -K., A. Z. Awang, and W. Omar. 2018. Structural and material performance of geopolymer concrete: A review. Construction and Building Materials 186:90–102. doi:10.1016/j.conbuildmat.2018.07.111.
- Maranan, G. B., A. C. Manalo, B. Benmokrane, W. Karunasena, P. Mendis, and T. Q. Nguyen. 2019. Flexural behaviour of geopolymer concrete beams longitudinally reinforced with GFRP and steel hybrid reinforcements. Engineering Structures 182:141–52. doi:10.1016/j.engstruct.2018.12.073.
- Marvila, M. T., H. A. Rocha, A. R. G. de Azevedo, H. A. Colorado, J. F. Zapata, and C. Maurício Fontes Vieira. 2021. Use of natural vegetable fibers in cementitious composites concepts and applications. Innovative Infrastructure Solutions 6 (3):180. doi:10.1007/s41062-021-00551-8.
- Masi, G., W. D. A. Rickard, M. Chiara, and A. Van Riessen. 2015. The effect of organic and inorganic fibres on the mechanical and thermal properties of aluminate activated geopolymers. Composites Part B: Engineering 76:218–28. doi:10.1016/j.compositesb.2015.02.023.
- Mastali, M., Z. Abdollahnejad, and F. Pacheco-Torgal. 2018. Carbon dioxide sequestration of fly ash alkaline-based mortars containing recycled aggregates and reinforced by hemp fibres. Construction and Building Materials 160:48–56. doi:10.1016/j.conbuildmat.2017.11.044.
- Narayanan Sivakumaresa Chockalingam, L., and N. Merina Rymond. 2021. Strength and durability characteristics of coir, kenaf and polypropylene fibers reinforced high performance concrete. Journal of Natural Fibers 19 (13):6692–700. doi:10.1080/15440478.2021.1929656.
- Nedeljkovi, M., M. Lukovi, K. Van Breugel, D. Hordijk, and G. Ye. 2018. Development and application of an environmentally friendly ductile alkali-activated composite. Journal of Cleaner Production 180:524–38. doi:10.1016/j.jclepro.2018.01.162.
- Nkwaju, R. Y., J. N. Y. Djobo, J. N. F. Nouping, P. W. M. Huisken, J. G. N. Deutou, and L. Courard. 2019. Iron-rich laterite-bagasse fi bers based geopolymer composite mechanical, durability and insulating properties. Applied Clay Science 183:105333. doi:10.1016/j.clay.2019.105333.
- Palanisamy, E., and M. Ramasamy. 2020. Dependency of sisal and banana fiber on mechanical and durability properties of polypropylene hybrid fiber reinforced concrete. Journal of Natural Fibers 19 (8):3147–57. doi:10.1080/15440478.2020.1840477.
- Palanisamy, P., and P. Suresh Kumar. 2018. Effect of molarity in geo polymer earth brick reinforced with fibrous coir wastes using sandy soil and quarry dust as fine aggregate. (Case Study) Case Studies in Construction Materials 8:347–58. doi:10.1016/j.cscm.2018.01.009.
- Poletanovic, B., J. Dragas, I. Ignjatovic, M. Komljenovic, and I. Merta. 2020. Physical and mechanical properties of hemp fibre reinforced alkali-activated fly ash and fly ash/slag mortars. Construction and Building Materials 259:119677. doi:10.1016/j.conbuildmat.2020.119677.
- Punurai, W., W. Kroehong, A. Saptamongkol, and P. Chindaprasirt. 2018. Mechanical properties, microstructure and drying shrinkage of hybrid fly ash-basalt fibers geopolymer paste. Construction and Building Materials 186:62–70. doi:10.1016/j.conbuildmat.2018.07.115.
- Ramli, M., W. H. Kwan, and N. F. Abas. 2013. Application of non-corrosive barchip fibres for high strength concrete enhancements in aggressive environments. Composites Part B: Engineering 53:134–44. doi:10.1016/j.compositesb.2013.04.012.
- Ribeiro, S., A. Ruy, G. S. R. Marilene, and K. Sankar. 2016. Geopolymer-bamboo composite – a novel sustainable construction material. Construction and Building Materials 123:501–07. doi:10.1016/j.conbuildmat.2016.07.037.
- Sathiskumar, T. P., J. Naveen, and S. Satheeshkumar. 2017. Hybrid fiber reinforced polymer composites – a review. Journal of Reinforced Plastics and Composites 33:454–71. doi:10.1177/0731684413516393.
- Shah, I., L. Jing, Z. Ming Fei, Y. Sheng Yuan, M. Umar Farooq, and N. Kanjana. 2020. A review on chemical modification by using sodium hydroxide (NaOH) to investigate the mechanical properties of sisal, coir and hemp fiber reinforced concrete composites. Journal of Natural Fibers 19 (13):5133–51. doi:10.1080/15440478.2021.1875359.
- Simonovaa, H., B. Kucharczykova, L. Topolar, Z. Kersner, I. Merta, J. Dragas, I. Ignjatovic, M. Komljenovic, and V. Nikoli. 2018. Crack initiation of selected geopolymer mortars with hemp fibers. Procedia Structural Integrity 13:578–83. doi:10.1016/j.prostr.2018.12.095.
- Souza, A. T., R. F. P. Junio, L. D. M. Neuba, V. S. Candido, A. C. R. da Silva, A. R. G. de Azevedo, S. N. Monteiro, and L. F. C. Nascimento. 2020. Caranan fiber from mauritiella armata palm tree as novel reinforcement for epoxy composites. Polymers 12 (9):2037. doi:10.3390/polym12092037.
- Stalin, A., S. Mothilal, V. Vignesh, K. J. Nagarajan, and T. Karthick. 2021. Mechanical properties of typha angustata/vetiver/banana fiber mat reinforced vinyl ester hybrid composites. Journal of Natural Fibers 19 (13):5227–38. doi:10.1080/15440478.2021.1875366.
- Trindade, A. C. C., P. H. R. Borges, and F. de Andrade Silva. 2018. Mechanical behavior of strain-hardening geopolymer composites reinforced with natural and PVA fibers. Materials Today Proceedings. doi: 10.1016/j.matpr.2019.02.017.
- Walbruck, K., L. Drewler, S. Witzleben, and D. Stephan. 2021. Factors influencing thermal conductivity and compressive strength of natural fiber-reinforced geopolymer foams. Open Ceramics 5:100. doi:10.1016/j.oceram.2021.100065.
- Wongsa, A., R. K. Wong, S. Naenudon, V. Sata, and P. Chindaprasit. 2020. Natural fibers reinforced high calcium fly ash geopolymer mortar. Construction and Building Materials 241:118143. doi:10.1016/j.conbuildmat.2020.118143.
- Ye, H., Y. Zhang, Z. Yu, and J. Mu. 2018. Effects of cellulose, hemicellulose, and lignin on the morphology and mechanical properties of metakaolin-based geopolymer. Construction and Building Materials 173:10–16. doi:10.1016/j.conbuildmat.2018.04.028.
- Zhang, H., P. K. Sarker, Q. Wang, B. He, and Z. Jianga. 2021. Strength and toughness of ambient-cured geopolymer concrete containing virgin and recycled fibres in mono and hybrid combinations. Construction and Building Materials 304:124649. doi:10.1016/j.conbuildmat.2021.124649.