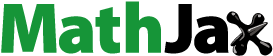
ABSTRACT
Two varieties of jute fiber, tossa (Corchorus olitorius) and white (Corchorus capsularis), were combined with nano-clay (montmorillonite clay) modified polyester to fabricate composites using the hand lay-up method. The goal was to examine the impact of nano-clay on structural, mechanical, and thermal properties. The two types of jute fibers were first treated with NaOH, and the polyester was then modified with montmorillonite nano-clay (1, 2, 3) (wt%). Finally, 30 cm long unidirectional fibers were used to fabricate a composite (fiber volume fraction is 19.3%). Accordingly, the structural (crystallinity), mechanical, and thermal properties of the composite were examined using the XRD, UTM, and TGA apparatus. Regarding crystallinity, treating the tossa jute fiber and its composite with nano-clay demonstrated improved crystallinity indices of 75.24% and 75.52%. The Tossa jute fiber composite treated with 1% nano-clay exhibits an increased tensile strength of 97.8805 MPa, which is 10.92% higher than the treated fiber without NC, and a flexural strength of 159.79 MPa, which is 3.12% higher than the treated fiber without NC). In comparison to white jute composite, the treated tossa jute fiber composite showed improved thermal stability; the addition of 3% nano-clay also demonstrated higher thermal stability. The use of modified polyester in composites along with nano-clay produces better outcomes in every way.
摘要
将两种黄麻纤维tossa(Corchore olitorius)和白色(Corchores capsularis)与纳米粘土(蒙脱石粘土)改性聚酯结合,采用手工铺层法制造复合材料. 目的是研究纳米粘土对结构、机械和热财产的影响. 两种类型的黄麻纤维首先用NaOH处理,然后用蒙脱土纳米粘土(1,2,3)(wt%)对聚酯进行改性。最后,使用30 cm长的单向纤维制造复合材料(纤维体积分数为19.3%). 据此,使用XRD、UTM和TGA仪器检查了复合材料的结构(结晶度)、机械和热财产. 关于结晶度,经处理的黄麻纤维及其与纳米粘土的复合材料的结晶度指数提高了75.24%和75.52%. 用1%纳米粘土处理的Tossa黄麻纤维复合材料的拉伸强度增加了97.8805MPa,比未经NC处理的纤维高10.92%,弯曲强度增加了159.79MPa,比未经过NC处理的光纤高3.12%). 与白黄麻复合材料相比,经处理的tossa黄麻纤维复合材料表现出更好的热稳定性; 3%纳米粘土的加入也显示出较高的热稳定性. 在复合材料中使用改性聚酯和纳米粘土在各个方面都能产生更好的效果.
Introduction
Global awareness of environmental and economic considerations increases the demand for natural fibers, including jute, as they are bio-degradable and nontoxic. Currently, the world is concerned about the use of artificial products, which are non-biodegradable and cause serious pollution problems. Natural fiber-reinforced materials are in demand due to their high strength, eco-friendly, renewable, availability, low cost, and biodegradability compared with synthetic fiber (Gon et al. Citation2013; Kumar et al. Citation2018; Munshi et al. Citation2020; Raghavendra, Shakuntala Ojha, and Pal Citation2014). Natural fiber jute is also important in engineering, textile, technical textile, geo-textile, automobile (Alves et al. Citation2010), and electrical industries (Pandey et al. Citation2010).
Among various lignocellulose fibers, jute is a widely used reinforcement material (Shahinur et al. Citation2022). The jute is a long and coarse fiber. Furthermore, the hydrophilic behavior of jute fibers induces poor interfacial bonding with the hydrophobic resins, which leads to poor mechanical properties. To decrease hydrophilic behavior, moisture absorption and increase surface roughness through surface treatment of jute fibers, appropriate chemicals are used (Gopinath, Kumar, and Elayaperumal Citation2014; Sathishkumar et al. Citation2017). In this context, sodium hydroxide- (NaOH-) treated natural fiber polymer composites showed higher mechanical strength, better thermal stability, and lower water absorption rate due to improved interfacial adhesion between the fiber and matrix (Doan, Brodowsky, and Mäder Citation2012; Londhe, Mache, and Kulkarni Citation2016). Therefore, the selection of chemical treatment is important as alkali treatment for surface modification.
Natural fibers can be obtained from different parts of the plant like the stem, leaf, seed, and fruit (Chandramohan and Marimuthu Citation2011). Jute is a natural lignocellulosic fiber of two varieties: white jute and tossa jute belong to the Tiliaceae Corchorus family (Duan, Weidong, and Zhaoling Citation2017). shows the differences between tossa and white jute. The mechanical and physical properties of jute are highly inconsistent and depend on its variety, age, fiber extraction method, and geographical area (Babu et al. Citation2020). Although there are variations in chemical composition, physical properties, and mechanical properties of the varieties, it is necessary to investigate whether there are any differences following chemical alteration and their reinforced composite.
Figure 1. Tossa and white jute fruits, leaves and fiber. (Marrot et al. Citation2013; Roy International Jute Study Group, Sudripta 2010).
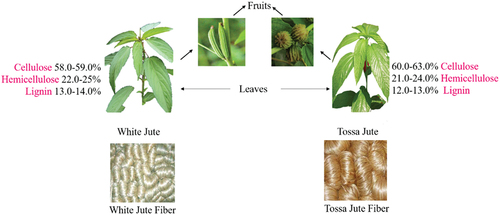
Hemicellulose and lignin are fully amorphous, in contrast to the well-known cellulose structure of the fibers, which has crystalline and amorphous sections. The cellulose crystalline region contains a strong hydroxyl group (Kabir, Citation2013). The amorphous hemicellulose and lignin can be removed by acid and alkali treatments (Corrales et al. Citation2007; B. Wang, Sain, and Oksman Citation2007; Özgür Seydibeyoǧlu and Oksman Citation2008). Therefore, the crystallinity of the two types should be measured following chemical alteration, as this impacts the composite strength. Sayeed and Paharia (Citation2019) showed that NaOH-treated jute fiber reinforced polymer composite showed better mechanical properties. Nano-clay has additional reinforcement to enhance the properties of the composites. Nano-clay also exhibits higher thermal, tensile, flexural, and impact strength (Hossain et al. Citation2011b). Ramakrishnan et al. (Citation2019) used 1 to 7 wt% nano-clay and found better thermal and mechanical properties. Hasan, Sazib Mollik, and Mahbubur Rashid (Citation2018) showed that 5% of the added nano-clay samples showed better thermal stability. The effect of montmorillonite nano-clay addition and chemical treatment on structural, mechanical, and thermal properties of tossa and white jute species reinforced composite is not studied yet. Two varieties of jute fibers are treated with NaOH; thereafter, they are incorporated into the polyester (nano-clay modified) according to hand layup, and their structural, mechanical, and thermal properties are analyzed.
Materials and methods
Materials
Two types of jute species, tossa jute and white jute, were collected from Faridpur regional station, BJRI, Bangladesh. For chemical treatment, NaOH was purchased from Merck, Germany . As a matrix material, an unsaturated polyester resin of orthophthalic grade was used from a local market. The resin (268BQTN™) was supplied by Singapore Highpolymer Chemicals Products Pte Ltd. Methyl Ethyl Ketone Peroxide (MEKP) (Butanox M-50) is used as a hardener supplied by PT. Kawaguchi Kimia, Indonesia. Organically modified montmorillonite clay (nano-clay, Nanomer™® 1.31PS) was procured from Sigma-Aldrich, USA. Milot paper was procured from a local market for quick mold release after curing. The specification of used materials is listed in .
Table 1. Specification of unsaturated polyester resin, catalyst, nano-clay, and NaOH.
Methods
Alkali (NaOH) treatment
The alkaline treatment increases the surface roughness of jute fibers, which results in better mechanical properties and thermal stability (Zafar, Nath Maiti, and Kumar Ghosh Citation2016). According to Dewan et al. (Citation2013) in this experiment, both the tossa and white jute fiber varieties were cut into 30 cm in length and soaked in a 5% (wt% of fiber) NaOH solution at 30°C for 2 hours. The fibers were then washed out several times with distilled water to remove redundant alkali leached in the fiber. The washed fibers were dried at room temperature for 8 hours.
Composite fabrication process
There are different methods of composite fabrication. Hot press, injection molding, extrusion, and hand lay-up techniques are the most widely used (Fazlar et al. Citation2020; Sayeed et al. Citation2021; Sweety, Hasan, and Julfikar Citation2021). Therefore, among them, fabrication technique selection is an important issue (Sayeed, Abu, and Haider Citation2020). The hand layup method was used to prepare jute fiber reinforced modified polyester composite. Two stainless steel plates of square shape, each having dimensions 300 mm × 300 mm × 3 mm, were used as molds to fabricate samples of the same size, and thickness varies between 3 and 3.2 mm. Nano-clay at a different weight percentage of matrix weight (1%, 2%, and 3%) was added slowly to the unsaturated polyester resin, and then agitation was done mechanically for 2 hours. The modified polyester and catalyst (MEKP) ratio was 1:0.01. For defect-free composite fabrication, care was taken to avoid the formation of bubbles. The subsequent fabrication process consisted of first putting a Milot paper on the surface of a stainless-steel plate, which was coated with a layer of catalyzed resin. The reinforcing tossa and white jute fiber were placed on the sticky surface individually and saturated with more resin. Catalyzed resin coating was poured on the top to ensure good surface finishing. The top was then covered with a Milot paper, and the total system was manually rolled with a steel rod roller. Then, another stainless-steel plate and 10 lb weight were placed on the system, which creates 494.41 Pa pressure on the system for better curing and thickness control. It was left for 24 hours to cure at room temperature. Fiber volume fraction of both treated and untreated raw jute fibers was 19.3% for each specimen. Test samples were properly prepared according to ASTM specifications to perform tests. The composite fabrication process is given in . show the samples for tensile and flexural strength tests.
X-ray diffraction analysis
In this study, Rigaku SmartLab SE’s XRD system was utilized to determine the crystallinity of jute fiber and nano-clay-modified composite. Jute fiber’s crystalline phases were identified and measured using X-ray diffraction (XRD), a technique that tracks the diffraction of X-rays after they interact with the sample. The sample was target with Cu-kα radiation (wavelength of the incident ray, λ = 1.544 A). The scattered radiation was detected in a 2θ (angle between the incident and reflected beam) range of the axis (10–80°), and the rotation of the detector was 2°/min. The voltage and current were 40 kV and 30 mA, respectively. The XRD deconvolution method was used to determine the relative crystallinity index (CI) (Park et al. Citation2010). The Gaussian function was used in Origin Pro 9.0 software to measure the peak areas. CI was measured using Equationequation (1)(1)
(1) (Correia and Sanches Valera Citation2019).
where Ac is the sum of the peak areas corresponding to the crystalline structure and At is the total area of the XRD curve.
Mechanical properties
Tensile and flexural properties of jute-polyester composites with nano-clay were conducted using Instron Universal Testing Machine. For the tensile test, specimens were prepared using a CNC router machine with dimensions of 165 mm × 12.7 mm × 3.2 mm according to ASTM D 638–03. In flexural testing, three-point bending was performed at room temperature on a specimen of 127 mm × 12.7 mm × 3.2 mm and span length of 60 mm according to the dimensions of ASTM D 790–03. Five samples from each category were tested to obtain the average result. The strain rate was 0.001 mm/mm per second and 0.0026 mm/mm per second for tensile and flexural tests, respectively.
Thermo-gravimetric (TGA) analysis
To identify composites with improved thermal stability, thermo-gravimetric analysis (TGA) was carried out with nano-clay loaded for both tossa and white jute fiber-reinforced composites using ELTRA thermostep, thermo-gravimetric analyzer. Chemically treated jute fiber of both varieties of nano-clay modified polyester composites were subjected to TGA with high purity nitrogen under a constant rate of 5 ml/min, sample purge flow of 60 ml/mm, and balance purge flow of 40 ml/mm. Thermal decomposition for each sample occurred in a programmed temperature range of 30–600°C. Three samples from different parts of the fabricated composites for each category were tested.
Results and discussions
Effect of two jute varieties on the crystallinity
The crystallinity of natural fiber composites represents their strength and rigidity. Tossa jute’s determined crystallinity value is slightly higher than that of the white jute variety. Natural plant fibers are less crystalline compared to crystal materials, and the positions of peaks are a function of the source of the natural plant fiber. Tossa and white fibers have slightly different chemical compositions, and this is reflected in their crystallinities as well. Clearly Resolve Deflected peaks for two varieties are of different numbers according to raw material (jute and nano-clay modified jute polyester composite). The diffraction patterns of both treated and untreated tossa and white fiber are shown in .
From , the peaks at 2θ = 15.6° (101), 17.1° (10), 33.5° (002), and 35° (040) are for the crystallinity nature of the fiber. represents the CIs of fibers and composites. indicates that, in comparison to white jute fiber, tossa jute fiber has higher intensity and narrower peaks. Moreover, from it is clear that treated fibers of both varieties show narrower and higher peaks compared to untreated jute fibers. Similar results were published by Mwaikambo and Ansell (Citation2002), W. Ming Wang et al. (Citation2009) and Zafar, Nath Maiti, and Kumar Ghosh (Citation2016).
Table 2. Crystallinity index of untreated, treated tossa and white fiber.
XRD patterns for both varieties, treated and untreated fiber composites with (3%) nano-clay and without nano-clay, are shown in , accordingly.
From it is clear that the peaks of treated fiber composites are higher and narrower compared to untreated fiber composites. the peaks of the tossa fiber composite are higher and narrower compared to the white fiber composite. Peaks near 2θ = 24° and 44° are for crystalline properties of composites. The crystallinity index is measured according to Equationequation 1(1)
(1) . presents that the crystallinity of untreated fiber composites is lower compared to treated fiber composites. Imposing nano-clay in composites increases crystallinity. Hasan, Sazib Mollik, and Mahbubur Rashid (Citation2018), Hossain et al. (Citation2011a) showed that jute composite with nano-clay shows better crystallinity which is similar to our results.
Table 3. Crystallinity index of different tossa composite and white composite.
Tensile properties analysis
The composites were prepared using treated and untreated fibers of both jute varieties to assess the impact of nano-clay. Five samples from each category (without nano-clay and with 1%, 2%, and 3% nano-clay) were subjected to tensile tests. The stress–strain curve of one sample from each category is shown in (tossa) and (white). (tossa) and (white) represent the average tensile strength of five samples from each category.
For tossa and white fiber, according to , composite made of treated fiber exhibits greater tensile strength than an untreated fiber composite. Additionally, composite with 1% nano-clay exhibits better tensile strength for both tossa and white fiber. The Tossa fiber composite has higher tensile strength than the white fiber composite in the variety comparison.
We have discovered a tensile strength of 72.55 ± 15.5 MPa for a composite made of 19.3% (fiber volume fraction) untreated fiber, whereasBhowmick (Citation2015) discovered a tensile strength of 80 ± 13.39 MPa for a composite built of 25% fiber. Due to the inherent variation of single jute fiber and the composites are fabricated by the hand lay-up method, the distribution of fibers in the matrix was not perfectly uniform and parallel to each other, tensile strength varies. Ramakrishnan et al. (Citation2019) found 103.05 MPa tensile strength for a composite made of 5% nano-clay and 20% fiber of 30 mm length and epoxy resin, whereas we found 97.88 MPa tensile strength for a composite made of 1% nano-clay and 19.3% (fiber volume fraction) fiber of 30 cm length and polyester resin. Here, the difference is due to fiber length and orientation and matrix material.
Flexural properties analysis
display the flexural load vs. deflection for both tossa and white fiber composites. illustrate variations in flexural strength for both variants of untreated and treated fiber with and without nano-clay.
As shown in , for tossa and white fiber, a composite composed of treated fiber has a higher flexural strength than one produced of an untreated fiber. Furthermore, the flexural strength for both tossa and white is improved in the composite with 1% nano-clay. In a variety of comparisons, white fiber composite is less flexural-stable than tossa fiber composite.
Hasan and Sazib Mollik (Citation2015) used a hand lay-up method to test a jute fiber polyester composite containing (1–3)% nano-clay. They discovered that adding 1% nano-clay improved the composite’s flexural strength while adding more nano-clay reduced it. We get 17.49% higher flexural strength than Hasan and Sazib Mollik (Citation2015).
Thermo-gravimetric analysis
TGA analysis was performed to investigate the thermal stability of prepared composites with and without nano-clay. For tossa and white jute fiber composites, depict the temperature vs. percentage of remaining weight.
There are three significant regions of weight loss due to the temperature rise. The initial weight loss of composites at low temperatures is due to moisture removal. The maximum weight loss due to degradation and volatilization of polyester and nano-clay along with jute fibers present in composites. Finally, at the end of the decomposition at around 600°C, the ash content remained (Hasan, Sazib Mollik, and Mahbubur Rashid Citation2018). The thermal stability of every type of sample has not changed significantly, as shown by .
The Tossa jute composite showed better thermal stability than the white fiber composite, according to . The composite of nano-clay-modified polyester showed slightly improved thermal stability. From , the composite of treated tossa fiber with 3% nano-clay lost 75% of its weight at 422°C, whereas without nano-clay, the temperature was 416°C.
Table 4. Thermo gravimetric data for tossa and white jute composite after treatment.
According to Hasan, Sazib Mollik, and Mahbubur Rashid (Citation2018) the composite with 5% nano-clay showed a final breakdown between 416°C and 460°C, while we discovered that the 3% nano-clay composite showed a final decomposition between 420°C and 500°C.
Conclusions
The composites of both varieties were fabricated using the hand lay-up technique for treated and untreated fibers with and without nano-clay. After that, the structural, tensile, flexural, and thermal properties were examined. These properties were tested to determine how the addition of nano-clay and NaOH treatment affected the unidirectional single-fiber polyester composite. As a structural property, the crystallinity index was determined. Treated tossa jute fiber and its composite with nano-clay showed increased crystallinity indices of 75.24% and 75.52%. The tossa jute fiber composite treated with 1% nano-clay exhibits increased tensile (97.8805 MPa) and flexural strength (159.97 MPa). The thermal stability of the treated tossa jute fiber composite and the addition of 3% nano-clay were both higher than that of the white jute composite, respectively. Composites that incorporate modified polyester with nano-clay get better results overall. So we can conclude that nano-clay modified polyester composite was found mechanically stronger and thermally stable that can be safely utilized in the automobile sector, railway wagon interiors, kitchen cabinets, and school furniture in place of non-degradable plastic and plastic-based composites. We believe that this is the direction to head toward better materials.
Highlights
The importance of this article is associated with which varieties of jute fibers are suitable for reinforced nano-clay modified polyester composites.
This article also reveals the crystallinity index of both jute fiber varieties and their composites, which will help to choose better crystalline fibers and composites on purpose.
The result of tossa reinforced nano-clay modified polyester composite shows higher tensile and flexural strength compared to white reinforced nano-clay modified polyester composites.
TGA result of 3% nano-clay loaded treated tossa fiber reinforced polyester composite showed better thermal stability.
Ethical approval
I confirm that all the research meets ethical guidelines and adheres to the legal requirements of the study country.
Acknowledgments
The authors would like to thank Professor Dr. Md. Abu Hasan Bhuiyan, Pro Vice-Chancellor of UITS and also thank Md. Moslem Uddin, Director of Technology Wing of BJRI for technical support. The authors would also like to thank the BJRI staff for their assistance during the field data collection and characterization of jute fibers.
Disclosure statement
No potential conflict of interest was reported by the author(s).
Additional information
Funding
References
- Alves, C., P. M. C. Ferrão, A. J. Silva, L. G. Reis, M. Freitas, L. B. Rodrigues, and D. E. Alves. 2010. Ecodesign of automotive components making use of natural jute fiber composites. Journal of Cleaner Production 18 (4):313–15. doi:10.1016/j.jclepro.2009.10.022.
- Babu, B. G., D. Princewinston, S. S. Saravanakumar, P. V. A. B. Anish Khan, S. Indran, and D. Divya. May 2020. Investigation on the physicochemical and mechanical properties of novel alkali-treated Phaseolus vulgaris fibers. Journal of Natural Fibers 19(2):1–12. doi: 10.1080/15440478.2020.1761930.
- Bhowmick, M. 2015. Mechanical properties of unidirectional jute-polyester composite. Journal of Textile Science & Engineering 05 (04):04. doi:10.4172/2165-8064.1000207.
- Chandramohan, D., and K. Marimuthu. January 2011. A review on natural fibers. International Journal of Research and Reviews in Applied Sciences 8:194–206.
- Corrales, F., F. Vilaseca, M. Llop, J. Gironès, J. A. Méndez, and P. Mutjè. 2007. Chemical modification of jute fibers for the production of green-composites. Journal of Hazardous Materials 144 (3):730–35. doi:10.1016/j.jhazmat.2007.01.103.
- Correia, C. A., and T. Sanches Valera. 2019. Cellulose nanocrystals and jute fiber-reinforced natural rubber composites: cure characteristics and mechanical properties. Materials Research 22 (suppl 1):1–9. doi:10.1590/1980-5373-mr-2019-0192.
- Dewan, M. W., M. Kamal Hossain, M. Hosur, and S. Jeelani. 2013. Thermomechanical properties of alkali treated jute-polyester/nanoclay biocomposites fabricated by VARTM process. Journal of Applied Polymer Science 128 (6):4110–23. doi:10.1002/app.38641.
- Doan, T. T. L., H. Brodowsky, and E. Mäder. 2012. Jute fibre/epoxy composites: Surface properties and interfacial adhesion. Composites Science and Technology 72 (10):1160–66. doi:10.1016/j.compscitech.2012.03.025.
- Duan, L., Y. Weidong, and L. Zhaoling. 2017. Analysis of structural changes in jute fibers after peracetic acid treatment. Journal of Engineered Fibers and Fabrics 12 (1):33–42. doi:10.1177/155892501701200104.
- Fazlar, R., A. Eiamin, M. Rakib Hasan, M. M. H. Shariful Islam, M. A. Gafur, and S. A. Dhar. 2020. Effect of fiber loading and orientation on mechanical and thermal properties of jute-polyester laminated composite. Journal of Natural Fibers 00 (00):1–15.
- Gon, D., K. Das, P. Paul, and S. Maity. 2013. Jute composites as wood substitute. International Journal of Textile Science 1 (6):84–93. doi:10.5923/j.textile.20120106.05.
- Gopinath, A., M. S. Kumar, and A. Elayaperumal. 2014. Experimental Investigations on mechanical properties of jute fiber reinforced composites with polyester and epoxy resin matrices. Procedia Engineering 97:2052–63. doi:10.1016/j.proeng.2014.12.448.
- Hasan, M. H., and M. Sazib Mollik. 2015. “Mechanical performance of montmorillonite dispersed jute reinforced composite.” 4th International Conference on Material Science and Engineering Technology, Singapore, 30: 7–10.
- Hasan, M. H., M. Sazib Mollik, and M. Mahbubur Rashid. 2018. Effect of nanoclay on thermal behavior of jute reinforced composite. International Journal of Advanced Manufacturing Technology 94 (5–8):1863–71. doi:10.1007/s00170-017-0883-z.
- Hossain, M. K., M. W. Dewan, M. Hosur, and S. Jeelani. 2011a. Effect of surface treatment and nanoclay on thermal and mechanical performances of jute fabric/biopol ‘green’ composites. Journal of Reinforced Plastics and Composites 30 (22):1841–56. doi:10.1177/0731684411430426.
- Hossain, M. K., M. W. Dewan, M. Hosur, and S. Jeelani. 2011b. Mechanical performances of surface modified jute fiber reinforced biopol nanophased green composites. Composites Part B: Engineering 42 (6):1701–07. doi:10.1016/j.compositesb.2011.03.010.
- Kabir, M. M. 2013. Mechanical and thermal properties of jute fibre reinforced composites. Journal of Multifunctional Composites 1 (1). doi:10.12783/issn.2168-4286/1.1/kabir.
- Kumar, V. K., K. J. Gokuleshwar, S. Ranganathan, and C. Thiagarajan. 2018. Fabrication and mechanical property study on glass/sisal/banana natural fibres. International Journal of Pure and Applied Mathematics 119 (12):15637–45.
- Londhe, R., A. Mache, and A. Kulkarni. 2016. An experimental study on moisture absorption for jute-epoxy composite with coatings exposed to different ph media. Perspectives in Science 8:580–82. doi:10.1016/j.pisc.2016.06.026.
- Marrot, L., A. Lefeuvre, B. Pontoire, A. Bourmaud, and C. Baley. 2013. Analysis of the hemp fiber mechanical properties and their scattering (Fedora 17). Industrial Crops and Products 51:317–27. doi:10.1016/j.indcrop.2013.09.026.
- Munshi, R., S. Sharar Alam, M. Merajul Haque, and A. Shufian. 2020. An experimental study of physical, mechanical, and thermal properties of rattan-bamboo fiber reinforced hybrid polyester Laminated Composite. Journal of Natural Fibers 00 (00):1–15.
- Mwaikambo, L. Y., and M. P. Ansell. 2002. Chemical modification of hemp, sisal, jute, and kapok fibers by alkalization. Journal of Applied Polymer Science 84 (12):2222–34. doi:10.1002/app.10460.
- Özgür Seydibeyoǧlu, M., and K. Oksman. 2008. Novel nanocomposites based on polyurethane and micro fibrillated cellulose. Composites Science and Technology 68 (3–4):908–14. doi:10.1016/j.compscitech.2007.08.008.
- Pandey, J. K., S. H. Ahn, C. S. Lee, A. K. Mohanty, and M. Misra. 2010. Recent advances in the application of natural fiber based composites. Macromolecular Materials and Engineering 295 (11):975–89. doi:10.1002/mame.201000095.
- Park, S., J. O. Baker, M. E. Himmel, P. A. Parilla, and D. K. Johnson. 2010. Cellulose crystallinity index: measurement techniques and their impact on interpreting cellulase performance. Biotechnology for Biofuels 3 (1):10. doi:10.1186/1754-6834-3-10.
- Raghavendra, G., S. K. A. Shakuntala Ojha, and S. K. Pal. 2014. Mechanical properties of woven jute–glass hybrid-reinforced epoxy composite. Journal of Composite Materials 48 (28):3445–55. doi:10.1177/0021998313501924.
- Ramakrishnan, S., K. Krishnamurthy, R. Rajasekar, and G. Rajeshkumar. 2019. An experimental study on the effect of nano-clay addition on mechanical and water absorption behaviour of jute fibre reinforced epoxy composites. Journal of Industrial Textiles 49 (5):597–620. doi:10.1177/1528083718792915.
- Roy International Jute Study Group., Sudripta. 2010. Jute Basics. Dhaka: International Jute Study Group.
- Sathishkumar, S., A. V. Suresh, M. Nagamadhu, and M. Krishna. 2017. The effect of alkaline treatment on their properties of jute fiber mat and its vinyl ester composites. Materials Today: Proceedings 4 (2):3371–79. doi:10.1016/j.matpr.2017.02.225.
- Sayeed, M. M. A., S. M. S. Abu, and J. Haider. 2020. Opportunities with renewable jute fiber composites to reduce eco-impact of nonrenewable polymers. In In, ed. S. Hashmi and I. A. B. T, 810–21. Oxford: Elsevier.
- Sayeed, M. M. A., S. M. S. Abu, J. Haider, M. M. Habib, and B. T. Anubhav. 2021. Re-use of plastic products–materials perspective. Reference Module in Materials Science and Materials Engineering Malik In Elsevier 3:652–661.
- Sayeed, M. M. A., and A. Paharia. 2019. Optimisation of the surface treatment of jute fibres for natural fibre reinforced polymer composites using Weibull analysis. The Journal of the Textile Institute 110 (11):1588–95. doi:10.1080/00405000.2019.1610998.
- Shahinur, S., M. M. A. Sayeed, M. Hasan, A. Sadat, M. Sayem, J. Haider, and S. Ura. 2022. Current development and future perspective on natural jute fibers and their biocomposites. Polymers 14 (7):1445. doi:10.3390/polym14071445.
- Sweety, S., M. Hasan, and B. T. Julfikar. 2021. Effect of processing techniques and characteristics of plastic products. Reference Module in Materials Science and Materials Engineering Haider in Elsevier 3:225–233.
- Wang, B., M. Sain, and K. Oksman. 2007. Study of structural morphology of hemp fiber from the micro to the nanoscale. Applied Composite Materials 14 (2):89. doi:10.1007/s10443-006-9032-9.
- Wang, W. M., Z. Sheng Cai, J. Y. Yu, and Z. Peng Xia. 2009. Changes in composition, structure, and properties of jute fibers after chemical treatments. Fibers and Polymers 10 (6):776–80. doi:10.1007/s12221-009-0776-3.
- Zafar, M. T., S. Nath Maiti, and A. Kumar Ghosh. 2016. Effect of surface treatment of jute fibers on the interfacial adhesion in poly(lactic acid)/jute fiber biocomposites. Fibers and Polymers 17 (2):266–74. doi:10.1007/s12221-016-5781-8.