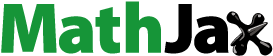
ABSTRACT
In the present era, recycling and reducing environmental pollution are the main objectives of sustainable development. Many researchers are thinking of innovation in the field of composite technology by utilizing waste material. The objective of this work is to check the effect of a human hair (waste material) as fiber on physical and mechanical properties. Tensile, flexural, impact strengths and hardness of human hair based polyester composite were evaluated to assess the possibility of using it as a new material in various engineering applications for longer life. The addition of polyester to the human hair fiber with marble dust adds as filler to increase the Impact strength of fabricated composite. Samples are fabricated by the hand lay-up process (40: 20: 40 matrix, filler and fiber ratio by weight), and the mechanical properties like tensile, flexural, impact using the Universal Testing Machine, Hardness test using Rockwell hardness testing machine, Impact using Izod impact test were all evaluated. It is an eco-friendly, long life and cost effective solution for various applications.
摘要
在当今时代,循环利用和减少环境污染是可持续发展的主要目标. 许多研究人员正在考虑利用废旧材料在复合材料技术领域进行创新. 这项工作的目的是检查作为纤维的人发(废料)对物理和机械财产的影响. 对人发聚酯复合材料的拉伸、弯曲、冲击强度和硬度进行了评估,以评估其在各种工程应用中用作新材料以延长寿命的可能性. 将聚酯添加到人发纤维中,加入大理石粉尘作为填料,以提高制造的复合材料的冲击强度. 样品通过手工叠层工艺制作(40:20:40基体、填料和纤维重量比),并使用通用试验机评估拉伸、弯曲、冲击、洛氏硬度试验机硬度试验、Izod冲击试验冲击等机械财产. 它是一种环保、长寿命和经济高效的解决方案,适用于各种应用.
Introduction
Composite materials have a wide range of applications in the defense, automotive, aerospace, and marine industries. Natural fibers have been studied as reinforcements in composites for many applications over traditional materials because composite materials have low fabrication costs and good mechanical qualities. Vinyl ester, epoxy, and polyester are examples of composites, which are made up of a matrix and reinforcement matrix and have a thermoset property (Abraham et al. Citation2013). The natural fiber is a popular reinforcing material among academics and engineers working in the field of composites because of its biodegradability, low cost, and ease of processing. Advanced composites are employed in a variety of industries, including aerospace, automotive, energy, major sports and recreation, and just about anywhere low weight and other specific qualities are required (Li and Wang Citation2022). They’re quickly becoming a low-cost way to get good structural performance (Lu et al. Citation2022). They are in almost every automobile we drive, as well as all buses and trains, boats, and recreational and sporting equipment like skis and canoes that we use on weekends. Because natural fiber is widely available and has superior mechanical qualities, more study is being conducted on it (Tamrakar et al. Citation2023). Polymer fiber composites have superior qualities than other composite materials, and they are widely used in a variety of applications.
Fly ashes are finely separated residues produced by thermal power plants when pulverized coal is burned. The growth of these coal-fired power stations has raised concerns about the pollution caused by fly ash produced by these units (Mohanty et al. Citation2021). This has sparked worldwide interest in its application. Polyesters, on the other hand, are made from low-cost resin systems and have a low operating service temperature. Furthermore, they have good corrosion resistance and are highly sought after in the market for qualities like as high strength, light weight, and longer service life. Electrical components, sheet molding compound, bulk molding compound, pipes, tanks, ducts, and pultrusion are only a few of the uses (Pan et al. Citation2020). As a result, fly ash particles, which are made up of alumino-silicate-based ceramic spheres, can be used to make light composite materials with low density, as well as to improve a variety of properties such as stiffness, strength, wear resistance, and hardness, which can be used in a variety of new applications. Properties of polyester are mentioned in , (Varga et al. Citation2010). Various studies of the characteristics of fly ash-reinforced polymers have been conducted and are currently being conducted.
Table 1. Properties of unsaturated polyester resin.
Rice belongs to family Oryza sativa L. is a staple food for billions of people and one of the world’s most important crops. It covers around 1% of the planet’s surface (Kumar and Sekaran Citation2014). According to statistics, the average annual worldwide rice output was 725 million metric tonnes between 2010 and 2013, with Asia accounting for nearly 90% of total global rice production (Chand, Sharma, and Fahim Citation2010). Rice husk (RH) is a low-cost residue of rice processing that is separated from the rice grain during milling. It is estimated that 0.23 tonnes of RH are created for every tonne of rice produced (Luduena et al. Citation2011). In nations like China, India, Indonesia, Malaysia, and Bangladesh, rice milling is one of the most important businesses (Chen et al. Citation2015). Burning of RH is discouraged, resulting in ash, fumes, and poisonous gases, resulting in considerable air pollution. Furthermore, silica is found naturally in RH and has been employed to improve the mechanical properties of composites (Grimm et al. Citation2021). Every year, 840,000 tonnes of RH are produced in Malaysia’s rice fields, which cover an area of approximately 680,000 hectares (Wang, Wang, and Wang Citation2021). RH is a fibrous cellulose-based substance that comes in a variety of aspect ratios.
RH is made up of 35% cellulose, 25% hemicelluloses, 20% lignin, 3% crude protein, and 17% ash. A range of uses has been proposed in the literature due to its great availability, low bulk density (90–150 kg m3), toughness, abrasiveness in nature, resilience to weathering, and unusual composition. RH could be used as an insulator, in the manufacturing of organic compounds, panel boards and activated carbon, and as a supplemental cementing material. The potential of RH as a source of energy and its financial viability has also been investigated, with promising results (Duy Tran et al. Citation2013). Even though a few of these husk are turned into the aforementioned end goods, the industrial applications of this biomass, like much other agricultural waste, are still limited with little economic value. As a result, it’s critical to find ways to fully exploit the RH, and extensive research is presently being conducted around the world to uncover prospective applications and build commercially viable techniques for these applications.
Marble is a metamorphic rock generated from limestone by geological processes such as heat and pressure in the earth’s crust. In the building and art sectors, marble powder is frequently mixed with cement. Marble has extremely little quartz, with a density of 2.7 g/cm3 (0.2%) and a relative porosity of 0.4%. It is utilized as a building material in architecture, in the arts for sculpting, and for the variety of other purposes (Singh, Srivastava, and Bhunia Citation2017). The term “marble” is used to describe a variety of various stones that may be polished to a high sheen and have diverse compositions, origins, and commercial qualities. Metamorphism of sedimentary carbonate rocks produces marble. The original rock is completely recrystallized into an interlocking mosaic of dolomite crystals or calcite throughout this metamorphic phase. Any fossils and sedimentary textures present in the parent rock are typically destroyed by the heat and pressures required to make marble. Because of its uneven shape and/or smaller size, 30% of the Marble stone is lost to scrap during processing. Every year, millions of tonnes of marble powder are harvested and processed all over the world.
As a result of the massive amounts of marble dust created by these companies, severe environmental damage occurs. During the machining of stones in India, a considerable amount of marble dust is created. When left unchecked, marble dust reduces soil productivity by decreasing porosity and water percolation, as well as contributing to air pollution (Kumar, Patnaik, and Bhat Citation2017). Marble waste (marble dust) deposited in riverbeds, along roadsides, and on undulated open terrain has become a huge environmental concern and a major threat to the local ecosystem. The marble waste particulates dangle in the air around us in dry conditions and tend to be deposited on vegetation, crops, and have a substantial impact on the ecosystem. It also causes a loss in topsoil porosity/permeability, which contributes to waterlogging, as well as a decrease in soil fertility and crop productivity as a result of increased soil alkalinity (Singh, Vyas, and Ahmed Citation2017).
Due to environmental and economic concerns, the usage of polymer-based natural fiber-reinforced composites has risen considerably in recent years in our society. For generating ecofriendly and more effective reinforced composites, various types of natural fibers (plant and animal hair) are employed. Natural fibers, on the other hand, have various drawbacks (varying quality, water sensitivity, etc.) that can reduce the adhesion between the matrix and the fiber. To increase the connection between the matrix and the fiber, physical and chemical treatments are applied (Popescu and Hocker Citation2007). Hair fiber (HF) can be considered as animal fiber within the category of natural fiber or other fibrous materials, which have the benefits of being lightweight, environmentally benign, and low-energy to produce. In most communities, hair fiber is a natural fiber that is considered useless. As a result, it can be found in municipal waste streams in practically every city and village on the planet. Hair is thrown out in nature in rural places or areas with low human density, where it slowly decomposes over several years, finally returning to its basic parts of carbon, nitrogen, and sulfur. It often collects in considerable volumes in solid waste streams and chokes drainage systems in urban areas or areas with high population density, providing a multidimensional challenge (Vishakh et al. Citation2013).
Human hair is a natural fiber made up of keratin, a protein with high sulfur content due to the amino acid cysteine. The majority of HF is made up of 65–95% proteins, with the rest being water and lipid pigment. Cuticle, cortex, and medulla combine to form HF. The cuticle, which covers the hair from the scalp to the ends, is the most valuable component of human hair (Ahmad Citation2014). The cortex takes up the majority of the hair’s surface area (75%). Cortex cells are found in cysteine cross-links and the cell membrane complex (CMC). Each cortical cell has a spindle form with a length of 50–100 m and a diameter of 3 m. The medulla is a narrow cylindrical layer in the center of human hair that has a high lipid rate concentration but low cysteine. Color and shine may be compromised in dehydrated hair. This characteristic is controlled by the cortex (keratin). The cortex’s lengthy chains (keratin) are compressed to form a regular structure, which gives HF its strength. Hair diameter is usually between 50 and 80 m, density is around 1.32 g/cm3, tensile strength is between 150 and 350 MPa, and elongation at break is at 216.9% (Santos et al. Citation2020). Due to its widespread availability in municipal garbage, low density, and low cost, HF is commonly utilized in the manufacture of natural fiber-reinforced composites. It also has outstanding mechanical and water absorption qualities.
Numerous studies have been on the characterization of fly ash, marble dust and rice husk with the polyester and its applications in different field. The present study involves the fabrication and characterization of polyester composite reinforced with the combination of human hair with the fly ash, marble dust and rice husk.
Material and methodology
Material
Rice husk were collected from one Village, near Bhopal, Madhya Pradesh, India. Rice husk was washed, dried, crushed and sieve of size 4.0 mm. The class F-Grade (having higher silica content) fly ash was collected from Coal power plant in Bhopal, India. The marble dust used was collected from a marble processing unit in Bhopal, Madhya Pradesh, India. Human hairs were collected from a nearby barber shop. These fibers were thoroughly cleaned with shampoo and dried in sunlight for few hours. Fibers were cut with the scissor and sieve of above mentioned size, .
Fabrication of composites
The polyester and its hardener (Methyl Ethyl Ketone Peroxide) were mixed in the ratio of 10:1 (mentioned in the catalog) by weight. Human hair were then mixed with fly ash, rice husk and marble dust by percentage weight to prepare different composite samples (Sample 1–4), polyester Neat (Sample 1), polyester + fly ash + human hair in the ratio of 40:20:40 by percentage weight (Sample 2), polyester + rice husk + human hair in the ratio of 40:20:40 by percentage weight (Sample 3), polyester + marble dust + human hair in the ratio of 40:20:40 by percentage weight (Sample 4) by hand lay-up technique. The combination was systematically mixed until uniform dough was formed. The dough was then gradually poured into a square mold of size 170 mm in length, 170 mm in width and 4 mm in thickness. The casting was left for 24 hours and after that composite specimens were taken out from the mold. Specimens of required size were cut for testing their mechanical properties and characterization, .
Mechanical properties of composites
Tensile properties
The tensile strength of composite samples was evaluated using Instron model 3382 testing equipment in accordance with ASTM D 638. Composite samples with dimensions of 150 × 12.99×4 mm were examined in a rectangular shape. At a crosshead speed of 50 mm, samples were tested to failure under stress. For strain measurement, an extensometer was mounted to the gauge part of the sample. Four samples were evaluated to ensure that the results were repeatable ASTM D638–10. Tensile strength and elongation at break were measured.
Flexural strength
Composite samples were subjected to a three-point bending test by ASTM D 790. The Instron Machine Model 3382 was used to examine the flexural properties of composite materials. At room temperature, rectangular samples with dimensions of 80 × 10×4 mm3 were examined at a cross head speed of 3 mm/min. For the flexural test, the support span was 64 mm. As a result, each type of sample received an average of five specimens ASTM D790–10.
The ability of a material to endure bending forces applied perpendicular to its longitudinal axis is known as flexural strength. The stresses caused by the flexural load are a mix of compressive and tensile stresses.
Impact strength
The overall toughness of polymeric materials is directly proportional to their impact characteristics. The ability of a polymer to absorb applied energy is characterized as toughness. The area under the stress-strain curve is proportional to a material’s toughness. The toughness of a substance is proportional to its impact strength, and vice versa.
Izod impact of rectangular samples with dimensions of 67 × 10×3.5 mm was examined using an Izod impact tester on a Tinius Olsen impact 104 machine. Five specimens were tested for each component, and the average data was presented. ASTM D 256–10 was used to determine all of the samples.
Hardness rockwell tester
ASTM D 785 was used to conduct the hardness test. The resistance of a substance to deformation, particularly persistent distortion by indentation or scratching, is characterized as hardness. After allowing for elastic recovery of the test specimen, the Rockwell hardness test evaluates the hardness of polymers. This test aids in determining the material’s visco-elastic properties. The penetration of a specific type of indenter when pressed into the material under specific conditions is the basis for this test method.
Water uptake
For the water uptake test, all of the aforementioned constructed composite samples were sliced to a tiny size 10 × 2×0.2 cm. For various periods, the composite samples were immersed in a flask containing 500 ml of distilled water at room temperature (10 min, 30 min, 2 h, 12 h, and 24 h). Tissue paper was used to extract the samples from the flask. The beginning and final weights were used to calculate the composites water uptake. The following equation was used to calculate the water uptake (Sahadat Hossain, Chowdhury, and Khan Citation2017).
Water uptake =
x 100
Scanning electron microscopy
Fiber – matrix adhesion, fiber dispersion in polymer matrix, surface roughness, adhesive failure, fractured surfaces, networks, and phase boundaries in blends are just a few of the polymers and composites studies and applications where SEM has been applied. The scanning electron microscope (SEM) is commonly used to obtain information about the structure of composites. The methodology for using SEMs to analyze fractures in polymeric composites is still being debated. Many authors prefer to employ conductive sputter coating rather than low-voltage or variable-pressure approaches because it preserves the original surfaces. The morphology of the polymer composites can be seen using a scanning electron microscope (SEM). The electron beam interacts with the surface region during the “scanning” process, generating secondary electrons from the composite. There is also the possibility of back scattering of the incident electrons. The secondary or back-scattered electrons’ intensity is measured and compared to that of the scanned electron beam. On the screen, a contrasting picture of the composite’s surface is displayed.
Scanning electron microscopy (SEM) was used to investigate the fracture surface of the composite following the tensile test (model: Phenom Pro). The samples were fixed on a carbon tap and gold-coated for 20 seconds. All of the photos were taken at a voltage of 5 KV.
Results
Mechanical properties of hair fiber composite samples
The effects of fiber in different samples of composite loading on different mechanical properties i.e. tensile strength, tensile modulus, flexural strength, flexural modulus, impact and hardness are shown in . The average values of the experimental results are taken for different mechanical tests. The experimental results show that the tensile and flexural properties of composite of fly ash, rice husk and marble dust composites are increased with the addition of hair fiber as compared to the neat sample. It was found that, all the mechanical properties were increased by the addition of hair fiber in each sample and it was also noted that after adding up of hair fiber impact strength was tremendously increased . The mechanical properties of composite of fly ash, marble dust and rice husk with polyester are reported by other studies mentioned in (Arjmandi et al. Citation2015; Kumar Nayak and Satapathy Citation2021). Uncertainty is presented in all values as a variation on the third digit after decimal.
Figure 3. Effect of fiber loading on (a) tensile strength (b) flexural strength (c) flexural modulus (d) hardness (e) impact strength of different samples of hair-fiber composite: Sample 1(neat), Sample 2(polyester + fly ash + hair fiber), Sample 3(polyester + rice husk + hair fiber) and Sample 4(polyester + marble dust + hair fiber).
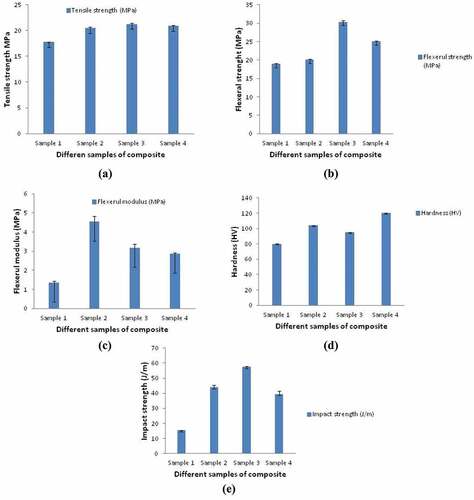
Table 2. Mechanical properties of composites of fly ash, rice husk and marble dust with polyester.
Water uptake
depicts the water absorption characteristics of various hair fiber-reinforced composite samples. The absorption of water in composites increases with the addition of hair fiber and can increase with time. The water absorption of composites is determined by the fiber surface and the matrix-fiber bonding. Because of its hydrophobic nature, hair fiber composites have a lower absorption percentage than other natural fibers. The addition of hair fiber enhances the roughness on the composite surface, which raises the percent gain in water absorption.
Scanning electron microscopy analysis of hair-fiber composite samples
SEM is used to evaluate the morphology of the various composite samples. As shown in , SEM micrographs of Sample 1, a neat and hair fiber samples with fly ash, rice husk, and marble dust, reveal the morphology of the samples (A-D). Because amino acids and cuticles are present, the fiber’s surface is smooth. depicts the sample without hair fiber, while depicts the sample with hair fiber (B-D). To increase the connection between the matrix and the fiber, the fiber surface is more porous and holes are visible on the fiber surface. Hair fiber increases the holes on the surface of the composites, which increases fiber locking with the matrix and improves the composites’ mechanical properties.
Discussion
Natural fiber reinforced polymer composites and natural-based resins are increasingly being used to replace conventional synthetic polymer or glass fiber reinforced materials. For their interior components, the automotive and aerospace industries have been actively producing various types of natural fiber, primarily hemp, flax, and sisal, as well as bioresins systems (He et al. Citation2012). Natural fiber composites are appealing for a variety of applications due to their high specific characteristics and affordable pricing. Natural fibers are increasingly being used in a variety of industries, including autos, furniture, packaging, and construction. This is owing to its advantages over synthetic fibers, which include low cost, low weight, reduced damage to processing equipment, improved surface polish of molded components composites, good relative mechanical qualities, and abundant and renewable resources (Ramesh et al. Citation2014). Natural fibers are utilized in a variety of applications, including construction materials, particle boards, insulation boards, human and animal feed, cosmetics, pharmaceuticals, and biopolymers and fine chemicals.
Various scientists have reported on the mechanical properties of polyester composites including fly ash, rice husk, and marble dust. Fly ash, rice husk, and marble dust were added to polyester composites to improve their qualities (Pan and Zhong Citation2015). Hair fiber-reinforced composites mechanical characteristics and water absorption were here studied in relation to fiber loading. The addition of hair fibers improves mechanical qualities such as tensile strength, flexural strength and modulus, impact strength, and hardness. The testing results suggest that the tensile, flexural, and hardness properties of hair fiber reinforced composites were improved, while the impact strength was significantly raised when compared to neat, Sample 1. We noted in this study that after adding hair fiber, the mechanical parameters (tensile strength and flexural stiffness) improved.
The water absorption of composites is determined by the fiber surface and the matrix-fiber bonding. Because hair fiber enhances the roughness on the sample surface, the percent gain of water absorption increases with its participation. An SEM morphological analysis can quickly confirm the effect of fiber modification while also improving the interlocking between the matrix and the fiber. Hair fiber-reinforced polymer composites can be developed using waste hair fiber as a resource.
Conclusion
Natural fiber composites are one of the emerging fields in material science that is gaining attention for usage in a variety of applications, according to the findings of this study. The hand layup technique was used to create natural composites from fly ash, rice husk, and marble dust, as well as hair fiber reinforced polyester composites. Based on the above-mentioned mechanical property test findings, it was concluded that the inclusion of hair fiber content improves all mechanical properties.
Highlights
A composite is effectively made from waste human hair fibers, which are widely available on the market as a waste human byproduct.
Human hair fibers were mixed with a fraction of fly ash, marble dust, and rice husk in this investigation, and the mechanical properties were assessed.
Composites reinforced with human hair perform best in terms of mechanical properties such as flexural strength, tensile strength, and impact strength.
Human hair is a non-biodegradable substance that is causing an environmental problem, its use as a fibro reinforcing material can help to mitigate the situation.
Disclosure statement
No potential conflict of interest was reported by the authors.
References
- Abraham, E., B. Deepa, L. A. Pothen, J. Cintil, S. Thomasc, M. J. Johnd, R. Anandjiwala, and S. S. Narine. 2013. Environmental friendly method for the extraction of coir fibre and isolation of nanofibre. Carbohydrate Polymer 15:1477–11. doi:10.1016/j.carbpol.2012.10.056.
- Ahmad, S. 2014. Preparation of eco-friendly natural hair fiber reinforced polymeric composite (FRPC) material by using of polypropylene and fly ash: A review. International Journal of Scientific & Engineering Research 5:969.
- Arjmandi, R., A. Hassan, K. Majeed, and Z. Zakaria. 2015. Rice husk filled polymer composites. International Journal of Polymer Science ID:501471. doi:10.1155/2015/501471.
- Chand, N., P. Sharma, and M. Fahim. 2010. Tribology of maleic anhydride modified rice-husk filled polyvinylchloride. Wear 269; 11:847–53. doi:10.1016/j.wear.2010.08.014.
- Chen, R. S., M. H. Ab Ghani, M. N. Salleh, S. Ahmad, and M. A. Tarawneh. 2015. Mechanical, water absorption, and morphology of recycled polymer blend rice husk flour biocomposites. Journal of Applied Polymer Science 8:1–12. doi:10.1002/app.41494.
- Duy Tran, T., M. Dang Nguyen, C. N. H. Thuc, H. H. Thuc, and T. Dang Tan. 2013. Study of mechanical properties of composite material based on polypropylene and Vietnamese rice husk filler. Journal of Chemistry ID 752924:6. doi:10.1155/2013/752924.
- Grimm, A. M., L. Y. Dorsch, G. H. Kloess, D. Enke, and A. Roppertz. 2021. Transition metal promoted combustion of rice husk and rice straw towards an energy optimized synthesis of biogenic silica. Biomass & bioenergy 155:106282. doi:10.1016/j.biombioe.2021.106282.
- He, L., X. Li, W. Li, J. Yuan, and H. Zhou. 2012. A method for determining reactive hydroxyl groups in natural fibers: Application to ramie fiber and its modification. Carbohydrate Research 348:95–98. doi:10.1016/j.carres.2011.10.035.
- Kumar Nayak, S., and A. Satapathy. 2021. Development and characterization of polymer-based composites filled with micro-sized waste marble dust. Polymer and Polymer Composites 29:497–508. doi:10.1177/0967391120926066.
- Kumar, S. R., A. Patnaik, and I. K. Bhat. 2017. Development and characterization of marble dust-filled dental composite. Journal of Composite Material 15:1997–2008. doi:10.1177/0021998316666334.
- Kumar, K. P., and A. S. J. Sekaran. 2014. Some natural fibers used in polymer composites and their extraction processes: A review. Journal of Reinforced Plastics and Composites 33:1879–92. doi:10.1177/0731684414548612.
- Li, Y., and L. Wang. 2022. Investigation of interfacial structure and dynamic mechanical behavior of titanium alloy laminated composites. Journal of Materials Research and Technology 21:5111–20. doi:10.1016/j.jmrt.2022.11.101.
- Luduena, L., D. Fasce, V. A. Alvarez, and P. M. Stefani. 2011. Nanocel- lulose from rice husk following alkaline treatment to remove silica. Bio Resources 6; 2:1440–53. doi:10.15376/biores.6.2.1440-1453.
- Lu, J., J. PengGuan, H. Wang, R. Dang, M. Fan, S. QingZhu, and X. Shen. 2022. Investigation on compressive and impact performance of GO-modified hollow glass beads/epoxy resin composites in simulated deep-sea environment. Composites Science and Technology 227:109608. doi:10.1016/j.compscitech.2022.109608.
- Mohanty, S., N. Roy, S. Prasad Singh, and P. Sihag. 2021. Strength and durability of flyash, GGBS and cement clinker stabilized dispersive soil. Cold Regions Science and Technology (191):103358. doi:10.1016/j.coldregions.2021.103358.
- Pan, J., T. Nie, B. Vaziri Hassas, M. Rezaee, Z. Wen, and C. Zhou. 2020. Recovery of rare earth elements from coal fly ash by integrated physical separation and acid leaching. Chemosphere 248:126112. doi:10.1016/j.chemosphere.2020.126112.
- Pan, Y., and Z. Zhong. 2015. A micromechanical model for the mechanical degradation of natural fiber reinforced composites induced by moisture absorption. Mechanics of Materials 85:7–15. doi:10.1016/j.mechmat.2015.02.001.
- Popescu, C., and H. Hocker. 2007. Hair the most sophisticated biological composite material. CChemical Society Reviews 37:1282–91. doi:10.1039/b604537p.
- Ramesh, M., T. S. A. Atreya, U. S. Aswin, H. Eashwar, and C. Deepa. 2014. Processing and mechanical property evaluation of banana fiber reinforced polymer composites. Procedia Engineering 97:563–72. doi:10.1016/j.proeng.2014.12.284.
- Sahadat Hossain, M., A. M. S. Chowdhury, and R. A. Khan. 2017. Effect of disaccharide, gamma radiation and temperature on the physico-mechanical properties of jute fabrics reinforced unsaturated polyester resin-based composite. Radiation Effects and Defects in Solids 172; 5–6:517–30. doi:10.1080/10420150.2017.1351442.
- Santos, F. D., M. A. M. Taguba, A. R. Alzona, R. C. S. Basada, J. M. A. Elbit, G. L. Nones, K. P. M. Olido, and E. U. G. Ramos. 2020. Optimization of the compressive strength of hair fiber reinforced concrete using central composite design. IOP Conference Series Material Science Engginering 771:1. doi:10.1088/1757-899X/771/1/012059.
- Singh, M., A. Srivastava, and D. Bhunia. 2017. An investigation on effect of partial replacement of cement by waste marble slurry. Construction Building Materials 134:471–88. doi:10.1016/j.conbuildmat.2016.12.155.
- Singh, Y., A. K. Vyas, and K. I. S. Ahmed. 2017. Compressive strength evaluation of mortars containing ISF slag and marble powder. Material Today Proceeding 4:9635–39. doi:10.1016/j.matpr.2017.06.239.
- Tamrakar, S., R. Couvreur, D. Mielewski, J. W. Gillespie, and A. Kiziltas. 2023. Effects of recycling and hygrothermal environment on mechanical properties of thermoplastic composites. Polymer Degradation and Stability 207:110233. doi:10.1016/j.polymdegradstab.2022.110233.
- Varga, C., N. Miskolczi, L. Bartha, and G. Lipóczi. 2010. Improving the mechanical properties of glass-fibre-reinforced polyester composites by modification of fibre surface. Materials & Design 31; 1:185–93. doi:10.1016/j.matdes.2009.06.034.
- Vishakh, R., M. Arvind, T. Mahesh, and T. R. Tephly. 2013. Formate assay in body fluids: Application in methanol poisoning. International Journal for Technological Research in Engineering 13:26–30. doi:10.1016/0006-2944(75)90147-7.
- Wang, H., M. Wang, and J. Wang. 2021. Nickel silicate hydroxide on hierarchically porous carbon derived from rice husks as high-performance electrode material for super capacitors. International Journal of Hydrogen Energy 46:35351–64. doi:10.1016/j.ijhydene.2021.08.062.