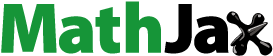
ABSTRACT
In order to revise the problem of inferior hand-feeling of cashmere textile anti-filling finished with “addition” or “subtraction-addition” technology and indicate the effects of graphene distributed state in the surface on antistatic properties of cashmere fibers, A couple of flexible hydrophilic cationic polyurethanes used as a dispersion medium for graphene purposefully are designed and prepared. In addition, the state of polymer coating and graphene on the fiber is effectively controlled by foam micro-coating technology. The admirable pilling resistance, static resistance, and hand-feeling of cashmere textile attributed to two-layer polyurethane membranes realized through “bottom coating (BC)” and “surface coating (SC)” are definite and reliable. The results show that the cashmere textile obtained 1.0% (o.m.f. on mass of fabric) weight gain rate (WGR) under the foam bottom coating process, correspondingly, obtained 3–4% (o.m.f.) weight gain rate (WGR) under traditional dipping process, the pilling resistance grade of cashmere textile is improved to Grade 4–5 from Grade 1–2. The semi-embed state of graphene in the “surface coating” resin film on cashmere surface results in the decrease of static voltage half-life from 180 s to about 2 s. Clearly, the foam microcoating technology scheme of “BC+ SC@graphene” has achieved good expected results.
摘要
为了改善羊绒织物通过“加法”或“减法”技术进行抗起球整理后带来的手感风格差的问题,并指出表面石墨烯分布状态对羊绒纤维抗静电性能的影响,设计并制备了两种用作石墨烯分散介质的柔性亲水性阳离子聚氨酯。此外,聚合物涂层和石墨烯在纤维上的状态由泡沫微涂层技术有效控制. 通过“底部涂层(BC)”和“表面涂层(SC)”实现的两层聚氨酯膜,使羊绒织物具有令人钦佩的抗起球性、抗静电性和手感,这是明确可靠的。 结果表明,在泡沫底涂工艺下,羊绒织物的增重率(WGR)为1.0%(o.m.f.,以织物质量计),相应地,在传统浸渍工艺下,其增重率为3-4%(o.m.f.),羊绒织的抗起球等级从1-2级提高到4-5级。石墨烯在羊绒表面的“表面涂层”树脂膜中的半嵌入状态导致静态电压半衰期从180秒减少到约2秒。显然,“BC+”的泡沫微涂层技术方案SC@graphene“取得了良好的预期结果。
Introduction
It is widely known that static accumulation and pilling are the problems that impute to the compact scale structure and better elasticity of cashmere textile (Hassan and Carr Citation2019; Wang et al. Citation2015; Xu et al. Citation2019). At the same time, it is inevitable that the natural hand-feeling of softness, fluffiness, and elasticity of cashmere fiber will be damaged if we treat cashmere textile by traditional and complicated scales removal (subtraction process), scales covering (addition process) or “subtraction-addition” process, which is far from what consumers expect from cashmere products because of their unacceptable destructive effects on cashmere products (Bhavsar et al. Citation2017; Frunza et al. Citation2018; Li et al. Citation2021). Therefore, the anti-pilling and anti-static finishing technology of cashmere textile have always been a hot topic in related fields (Kaur, Chakraborty, and Dubey Citation2016; McNeil and McCall Citation2011; Periolatto et al. Citation2013).
In recent years, various new technologies have been tried. Mei found that, compared with natural protease, the reducibility protease with disulfide bond will result in relatively less damage to wool fibers and could give them an obvious anti-pilling property (Mei et al. Citation2018). Zhu prepared Engineered Water Nanostructure (EWNS) with the technology of electro-spray high purity water, and EWNS’s strong oxidizing could degrade the warping of the scales of wool fibers, thus reducing the directional friction effect of wool fibers and improving the pilling resistance of woolen knitwear (Zhu, Ding, and Wu Citation2020). While Zhang combined the “subtraction” processes based on biological enzymes and low-temperature plasma to controllably corrode wool scales. The function of “light etching” of plasma made the enzymes more effective in the process of breaking scales, and the felting shrinkage of treated woolen fabrics and their damage is significantly reduced (Jiang et al. Citation2021; Zhang and Wang Citation2015).
In addition, Yu and Eren constructed an even-distributed conductive layer by in-situ polymerization on the surface of wool fibers that are pre-treated with oxygen plasma, which endowed woolen fabrics with excellent conductivity of 11.3 s/cm and better antibacterial performance (Eren et al. Citation2015; Yu et al. Citation2018). In Peng’s research work, supercritical CO2 and polyol are, respectively, employed as a catalyst and reducing agents to in-situ generate silver nanoparticles on the surface of wool fibers, which gives them excellent antistatic and antibacterial properties (Peng et al. Citation2017). While vapor deposition (PECVD) technology was employed by Montarsolo to treat silicon-containing polymers on the surface of wool fibers that were pretreated with plasma. The pilling resistance of the sample was improved by two grades with good washability (Montarsolo et al. Citation2013).
In terms of the application of conductive inorganic materials, Mohammad and Cao-coated fabrics with graphene or its complex with TiO2. Hereby, a continuous functional film was treated on the surface of fibers, which endowed the textile with good antibacterial, antistatic, anti-ultraviolet, and photocatalytic self-cleaning properties (Cao and Wang Citation2017; Shirgholami, Karimi, and Mirjalili Citation2016). Moreover, Kowalczyk deposited graphene on the fiber’s surface by sol-gel technique for the excellent antistatic properties realization (Kowalczyk et al. Citation2017).
For the antistatic effect with better durability, a polymer with good film-forming properties is generally chosen to fix graphene firmly to the surfaace of cashmere fibers (Hu et al. Citation2015; Kim and Lee Citation2017). But the technical scheme will inevitably deteriorate the natural softness and fluffiness of cashmere. Considering that polyurethane resin has excellent film-forming property, excellent elasticity, and softness under a low-temperature environment, the excellent natural style of cashmere textiles can be preserved to the greatest extent by employing it as an adhesion agent for graphene to cashmere fibers.
Obviously, in view of the above technical problems, it is necessary to ensure that the “micro-erosion” of cashmere fibers’ scales is controllable or effectively controls flexible polymer to be distributed on the surface of cashmere fiber continuously, evenly and its membrane should be as thin as possible. Particularly, cationic waterborne polyurethane was specially selected because of its better antistatic property, soft feeling and easy to foam. Of course, graphene fragments with little oxidative damage, which has excellent electrical conductivity, should be semi-embed in the surface coating membrane. So, the foam micro-coating technology is employed in this paper, based on waterborne polyurethanes with different properties and graphene dispersed in “surface coating” membrane, to build functional coating with a hierarchical structure on the surface of cashmere fibers (). And then, the relationship between the pilling resistance, static resistance, comprehensive handle feeling of treated cashmere textile and different coating processing are studied.
Materials and methods
Materials
Cashmere textile (32S/2) was supplied by Hebei qinghe cashmere industrial park and cationic waterborne polyurethane CSPU/CS5 (25 wt.%) was purchased from Guyin new material technology Co., Ltd, Shanghai, China. Graphene dispersion (1 g/L) was provided by XF-nano, Nanjing, China. Lauryl betaine, cationic modified guar gum, acetic acid, hydrochloric acid, and sodium hydroxide all were chemically pure and obtained from Sinopharm chemical reagents Co., Ltd.
Methods
Surface modification of cashmere knitted fabric
Foam micro-coating process: The clean cashmere fabric is dried in a vacuum drying oven at 70°C to constant weight (m1). The foam coating is taken on the dried cashmere fabric by small automatic film coating applicator FA-201/202D (Shanghai Fuan Enterprise, China) and then dried in a vacuum drying oven at 70°C to constant weight (m2).
The “bottom coating (BC)” foaming solution was prepared by mixing CSPU, lauryl betaine and cationic modified guar gum and their concentration is, respectively, controlled as 60 g/L, 7 g/L, and 7 g/L. As well, the “surface coating (SC)” foaming solution was prepared by mixing CS5, laurel betaine, cationic modified guar gum and graphene dispersion and their concentration is, respectively, controlled as 60 g/L, 7 g/L, 7 g/L, and 0.56 g/L.
Addition process: The clean and dried cashmere fabric (m1) is dipped in polymer emulsion (CSPU or CS5 20-80 g/L) at room temperature for 20 min, and then dried at 90°C (m2).
Subtraction-addition process: The commercial cashmere fabric mercerized with protease (m3, pretreated under the conditions of neutral protease 5%, pH6.8–7.2 and room temperature for 30 min) is treated with “addition process” (m4).
The coating weight gain rate (WGR) can be calculated by the equation:
The rationality of BC foaming solution formulation
Cationic polyurethane, foaming agent, and foam stabilizer in BC foaming solution formulation have different affinities to water and air, which probably results in an unstable proportion of polymer in BC foaming solution and BC foam during the continuous foam coating process. A further effect is that the quality of the polymer coating on the surface of the fiber is constantly changing, which makes the coating is unreliable. Therefore, it is very important to find out the reasonable range of BC foaming solution formulation to ensure that the composition of BC foam and BC foaming solution is basically constant during the continuous foam coating process.
According to relevant research results, the concentration of the foaming agent (lauryl betaine) in BC foaming solution is fixed at 7 g/L, the concentrations of BC polyurethane emulsion and foam stabilizer (cationic modified guar gum) are, respectively, 20-100 g/L and 2-10 g/L. The BC foaming solution is continuously foamed, and the foam produced within 10s is intermittently weighed (mf) every 20s spacing interval and the dried foam is weighed (md). The WGR standard deviation of md/mf is calculated according to the following formula, the critical concentrations of polyurethane emulsion and foam stabilizer in BC foaming solution are determined according to the set standard deviation critical value and the figure is drawn according to those critical concentrations. In the formula, mi represents test i and represents the average of multiple tests.
Performance and structural characterization
FTIR
FTIR was measured using a Nicolet iS5 infrared spectrometer (Thermo Scientific, USA) by potassium bromide tablet method at 25°C and the test range is 400–4000 cm−1. The test resolution is 4 cm−1 and the scanning times are 32.
XRD
TD-3300 ×-ray diffractometer (Rigaku, Japan) is employed in supramolecular structure analysis. Scan range 10–800, test voltage 40kV, test current 40 mA and Copper target. Interavale used in the scan of the samples is 0.04°.
SEM
Joel-2100F transmission electron microscope (JEOL, Japan) is employed in fabric surface morphology analysis with an accelerating voltage of 10 kV. All samples were ion-sputtered with a thin layer of gold to enhance the conductivity before observations.
TEM
S-4800 scanning electron microscope (HITACHI, Japan) is employed in surface morphology analysis. The cashmere fibers treated by different finishing technology are gilded and observed.
Emulsion conductivity and particle size
ZS90 nanoparticle size and Zeta potentiometer (Malvern, U.K) is employed in hydro-dispersion electric properties analysis. The electrokinetic potential of the polymer emulsion and graphene dispersion was tested under different pH conditions adjusted with 1 mol/L hydrochloric acid or NaOH. The 1 wt.%-emulsion was used in particle size characterization of the polymer emulsion, and that the emulsion was subjected to ultrasonication for 30 min at 25°C before the measurement.
Acid and water resistance
An appropriate amount of polymer emulsion was dried at room temperature for 24 h and then heated at 80°C for 30 min, baked at 140°C for 5 min to obtain a polymer membrane of about 20 × 20 × 1 mm. Finally, the film was kept in the dryer for 24 h. Then, the polymer membrane is immersed in water or acid solution (0.1 mol/L acetic acid) at 25 ± 1°C for 24, 48, and 72 h. The immersion resistance can be calculated by Eq:
where m5 is the polymer weight before immersing in water or acid solution, m6 is the polymer weight after immersing in water or acid solution.
Pilling resistance
The pilling resistance of treated cashmere fabrics was evaluated according to the standard method (GB/T4802.3–2008) at room temperature and 65% relative humidity.
Static resistance
FY342E-II fabric inductive electrometer is employed in static resistance analysis according to standard method (GB/T12703.1–2008). The clean cashmere fabric is treated with polymer emulsion under the following conditions: bath ratio of 1:20, 5% (o.m.f., on mass of fabric) polymer emulsion.
Comprehensive hand-feeling
The treated cashmere fabric is moistened for 24 h at 20°C and RH65%. The softness, elasticity, fluffiness, and drape styles of cashmere fabric are evaluated by subjective touch evaluation method.
Results and discussion
Structure of cationic polyurethanes for BC and SC
Generally, cationic waterborne polyurethane is very suitable for textile functional finishing processing because of its strong adhesion, soft feeling, and antibacterial and antistatic properties (Dong, Xin, and Luo Citation2018; Lü et al. Citation2020; Naz et al. Citation2018). According to the different requirements of antipilling and anti-static finishing to BC and SC polymer, two cationic waterborne polyurethanes were specially designed and prepared.
According to , better film-forming ability is very important for BC polymer to cover the scales of cashmere fiber, which is indispensable for pilling resistance of treated cashmere textile based on coating process. So, a higher proportion of branched polyether structure R0 is specially introduced into the BC polyurethane (Sukhawipat et al. Citation2020). R0 is a trifunctional polyether with a molecular weight of 3300.
According to , the SC polyurethane is designed to endow static resistance and excellent hand-feeling to treated cashmere textile and to fix graphene on its surface. Therefore, in this study, polyethylene glycol and quaternary ammonium groups, whose hydrophilicity is better, are introduced into the molecular structure of the SC polyurethane to improve the moisture absorption (moisture regain performance) performance of the fabric, so that charge release ability of fabric will be better.
In addition, polysiloxane and active groups (alkoxy silane) are, respectively, introduced into the molecular skeleton and tails of BC and SC polyurethanes in order to improve their hand-feeling and film-forming ability (Sukhawipat et al. Citation2020).
In , the medium-strength absorption peak at 3440 cm−1 is attributed to the stretching vibration of N-H in the carbamate groups, and the absorption peaks at 2918 cm−1, 2925 cm−1 and 1150–1465 cm−1 are, respectively, caused by the stretching vibration and bending vibration of C-H groups in the polymers. The absorption peaks near 1677 cm−1 and 1577 cm−1, 1595 cm−1 and 1705 cm−1 can be attributed to the stretching vibration of C=O and bending vibration of N-H in carbamate groups, respectively. The absorption peaks at 1112 cm−1 and 1120 cm−1 are attributed to the stretching vibration of C-O-C and Si-O-Si in polyether and polysiloxane chain segments.
Properties of cationic bottom coating and surface coating polyurethane
According to , the average particle size of cationic BC polyurethane emulsion is 75.8 nm and its particle size distribution is unimodal, while the average particle size of cationic SC polyurethane emulsion is 127.5 nm and its particle size distribution takes on a bimodal distribution. In fact, the average particle size of the both polyurethane emulsions is sufficiently small. Obviously, their molecular weight are small enough, which makes them can be emulsified easily, because their molecular chains are active-caped by amino silane coupling agent. Of course, the hydrophilicity of polyether chains in their molecular structures is also very conducive to the formation of stable emulsion (Fang et al. Citation2019; Feng et al. Citation2022).
It should be noted that the chemical structure of SC polyurethane is linear on which hydrophilic polyether and hydrophobic polysiloxane are simultaneously distributed. The amphipathic linear macromolecule usually has strong water absorption, which will result in higher emulsion viscosity during the beginning of the emulsification process (Wang et al. Citation2014; Zhang et al. Citation2021). That is why the particle size distribution of SC polyurethane takes on bimodal distribution though its hydrophilicity is better than that of BC polyurethane (Cintora et al. Citation2021).
It’s necessary for BC and SC polyurethane membranes to ensure their excellent performance of soaking resistance, which supports the cashmere textiles coated with them show a desirable durability of pilling/static resistance. Of course, acid resistance is usually poor for cationic waterborne polyurethane, so it deserves more attention (Zhu et al. Citation2019).
According to , the WGRs of BC and SC membranes that have been immersed in water for 24, 48, 72hrs are 11.3, 12.5, 12.7% and 17.1, 17.7, 20.0%, respectively. And the WGRs in the acid of them are 17.5, 18.8, 19.1% and 18.0, 20.2, 22.5%, respectively.
Generally, both the BC and SC polyurethane membranes show good water and acid resistance. This is because both of them possess a cross-linked structure derived from active-capped groups based on amino triethoxysilane coupling agent and intramolecular crosslinking structure based on tri-branched polyether structure R0.
Of course, the tertiary amine groups in the polymer have higher ionization degrees under acidic conditions, which results in the acid resistance of the BC membrane being obviously weaker than its water resistance. However, the quaternary ammonium in the molecular structure of the SC membrane is not sensitive to acid, which renders the difference in its water resistance and the acid resistance inconspicuous. Of course, the poor water-resistance of the SC membrane is still because of the stronger hydrophilicity of quaternary ammonium and polyethylene glycol chains existed in its molecular structure.
According to the and , the BC polyurethane shows better film-forming ability and water/acid resistance and the SC polyurethanes shows better antistatic performance, which comes from the chemical structure they were designed for. According to , the static voltage half-life period of cashmere treated by CSPU or CS5 was reduced from 174.9s to 26.1s or 11.8s. Distinctly, the hydrophilic cationic polyurethanes (CSPU or CS5) modified by polysiloxane we prepared possess the antistatic function because of their moisture absorption ability which is derived from the hydrophilicity of the polyether chains in their macromolecules.
Table 1. The static resistance of BC and SC membranes.
Actually, the CSPU with better membrane-forming performance is specially designed for BC whose soft segments domain is composed of branched polyether and ethylene oxide/propylene oxide random block copolymer. On the contrary, the surface coating resin CS5 is designed one that with better hydrophilicity containing the linear polyether, for the enhanced moisture regains, composed of polyethylene glycol. Therefore, the surface coating resin could endow the fibers with better hygroscopic properties and antistatic performance.
Structure and properties of graphene dispersion
Relevant studies have shown that cellulose nanocrystals have low density, high specific surface area and abundant hydroxyl groups, which makes it very convenient and efficient to prepare cellulose nanocrystals/graphene by ultrasonic stripping in aqueous system (Carrasco et al. Citation2014).
According to , the crystallinity of the graphite powder is very strong, it has a sharp diffraction peak at 2θ = 26.8° (Oliveira et al. Citation2022). When graphene is prepared by ultrasonic stripping, the intensity of crystallization diffraction peak of graphite powder decreases gradually with the ratio of cellulose nanocrystalline CNC to graphite powder increases, that is, the higher the ratio of CNC is, the higher efficiency of graphite powder peeled is, which signifies a lower and lower degree of crystallization of graphite powder (Nayak and Debata Citation2013).
Figure 3. (a) X-ray diffraction spectrum of CNC-graphene, (b) Effect of pH on Zeta potential of cationic foaming solution.
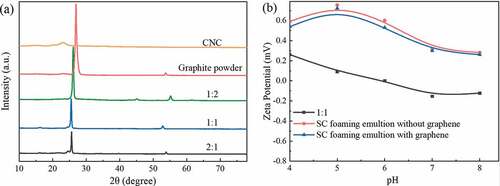
It can be seen from that the electrokinetic potential of the self-made graphene dispersion is almost zero within the range of pH5–8, which indicates that the graphene prepared under the ratio of CNC to graphite powder is 1:1 has almost no oxidation damage, which will surely benefit to its electrical conductivity (Ma et al. Citation2011). The electrokinetic potential of SC foaming solution (CS5 60 g/L, laurel betaine 7 g/L, cationic modified guar gum 7 g/L, and graphene dispersion 0 or 0.56 g/L) shows weak positive and almost no difference regardless of whether graphene is dispersed in SC foaming solution or not, which demonstrates that self-made graphene has complete ring-structure (Barany, Kartel,’ and Meszaros Citation2014).
Microcoating finish of cashmere fabric based on BC and SC polyurethanes
Anti-pilling finishing of cashmere textile based on BC
As analyzed in the preface of this paper, it is necessary to continuously cover the surface of cashmere fiber with a polymer membrane to endow the pilling resistance to cashmere textiles. At the same time, we must try to avoid “bonding” the fiber and yarn together to ensure that the soft and fluffy style of cashmere textiles are not harmed (Hassan and Carr Citation2019). So, the “Foam micro – coating finishing (F),” “Dipping addition finishing (D)” and “Dipping subtraction/addition finishing (DSA)” are employed in cashmere textile coating in order to find out a better coating scheme.
It can be seen from , for the pilling resistance and hand-feeling of treated cashmere textile, a thin membrane covering on its surface by “Foam micro-coating finishing (Process F)” based on BC polyurethane is much better than that by “Dipping addition finishing (Process D)” or “Dipping subtraction/addition finishing (Process DSA).” It is worth emphasizing that, for the treated cashmere textile, the pilling resistance based on WGR 0.5 ~ 1% by Process F is almost equal to that based on WGR 2% by Process DSA. For Process D, it does not even endow good pilling resistance to the treated cashmere textile.
Table 2. BC technologies and its performance evaluation (Pilling resistance).
In Process F, due to the high viscosity and low permeability of the BC foam, the majority of BC foam can be effectively controlled on the surface of the fibers rather than in the gaps of textile or yarns. However, for Process D and DSA, the BC polyurethane emulsion will inevitably be distributed in the gaps between yarn and fiber more, resulting in the “bonding” of yarn and fiber. Sequentially, not only the rough feeling and worse elasticity of treated cashmere textile are unavoidable, but also accompanied by poor pilling resistance due to less polymer adsorption on the fibers’ surface. Compared with Process DSA, the surface of cashmere fiber in Process D has stronger hydrophobicity, which is against the adsorption of BC emulsion to cashmere fibers. So, the majority of BC emulsion will exist in the fabric gaps, and of course, it is difficult to obtain a good hand-feeling and pilling resistance for Process D.
The above analysis and discussion can be primely verified in .
Unquestionably, the distribution of the BC polymer on the surface of cashmere fiber has an important effect on its pilling resistance. However, the content of polyurethane in BC foaming solution and in BC foam, during the continuous foam coating process, maybe significantly changed because of its unsuited affinity to water and air, which surely result in an unreliable coating effect.
In order to define the rationality of BC foaming solution scheme, the concentration of BC polymer and foam stabilizer in the BC foaming solution is set as independent variables, and the WGR standard deviation of ≤ 0.2%, 0.2 ~ 0.4% and ≥ 0.4% are, respectively, set as the critical value of “stable zone,” “transition zone” and “unstable zone” of BC foaming solution.
According to , the reasonable concentration of foam stabilizer should be in positive proportion to the concentration of BC polyurethane when the latter concentration is lower than 20 g/L or more than 80 g/L. And the relationship between them is nonlinear when the concentration of BC polyurethane is 20–80 g/L.
Morphology of BC membrane on cashmere fiber surface
The morphologies of BC membrane on the surface of cashmere fiber treated by different processes clearly support the relevant analysis and views mentioned in this paper (). As expected, the fiber’s scales are not only fully covered after Process F but also their structure is clear and intact.
Surface coating and antistatic finishing of cashmere textile
The surface coating is designed for antistatic properties of cashmere textile. In addition, in order to enhance the antistatic effect of SC membrane, we also mixed graphene in SC foaming solution.
Considering that the state of graphene in the SC membrane may affect its function, the experiments about SC are specially designed (). Among them, “CHF” means foaming SC (CS5 0 g/L, graphene dispersion, lauryl betaine 7 g/L, cationic modified guar gum 7 g/L), “CFF” means foaming SC (CS5 60 g/L, graphene dispersion, lauryl betaine 7 g/L, cationic modified guar gum 7 g/L) and “CFD” means dipping SC (CS5 60 g/L, graphene dispersion).
Table 3. SC technologies and its performance evaluation (Static resistance).
Firstly, whatever which kind of SC technique is adopted, the contribution of graphene to the static resistance of cashmere will be inapparent when its concentration is above 0.56 g/L. Secondly, though cashmere shows the best static resistance because graphene is fully exposed in CHF (), the graphene existing on its surface is easily washed off. Graphene in CFD is almost completely covered by a membrane (), which results in the inhibition of graphene conductivity and the worst static resistance. For CFF, graphene can be dispersed on the surface of SC foam, and the thickness of the membrane is not enough to completely wrap graphene, so the graphene is semi-embed in the SC membrane (), so the treated cashmere textile shows the best antistatic performance.
Actually, for CFF and CHF, the antistatic properties of treated cashmere are almost indistinguishable when the concentration of graphene dispersion is 0.5 ~ 0.9 g/L. According to , it is very important, comprehensively consider the antistatic performance of cashmere textile and its durability, to ensure graphene is fixed by SC membrane in the form of semi-exposed. The hydrophilic polyethylene glycol segments and quaternary ammonium groups distributed in the molecule of SC can achieve a permanent antistatic effect by improving the hydrophilicity of cashmere fabric, but the reduction of the resistivity of the fabric is not efficient. When graphene is complete covered by resin, its excellent electrical conductivity will be distinctly discounted, although graphene has excellent electrical conductivity (Su et al. Citation2020). Therefore, the dispersion of graphene on the surface of the fabric is particularly important.
Conclusions
The “bottom coating” water-based polymer with excellent film formation performance and the “surface coating” water-based polymer with better moisture absorption performance are designed and prepared. The anti-pilling and anti-static bi-functional finishing of cashmere textile is realized through the construction of hierarchical coating based on cationic waterborne polyurethane modified with polysiloxane.
The bi-functional ultra-thin composite membrane with anti-pilling and anti-static functions is constructed on the surface of cashmere fibers by “foam micro-coating” technique. “Welding together” between the common structures of anti-static “surface coating” membrane and anti-pilling “bottom coating” membrane enable the former better durability and washing resistance.
Dispersing graphene on the surface of functional hydrophilic polyurethane foam and ensuring the graphene is fixed on the surface of the polyurethane membrane with a semi-exposed state is very important for the antistatic performance and durability of the treated fabric.
The anti-pilling performance of cashmere textile can be improved from Grade 2 ~ 3 to Grade 4 ~ 5 with a bottom coating WGR (weight gain rate) of<1% with the maintenance of soft hand feeling. And tiny amounts of graphene semi-embed in the surface coating membrane can reduce the static voltage half-life of cashmere textile from 180 s to about 2 s.
Supplemental Material
Download Zip (699.6 KB)Acknowledgment
This work was supported by the Hebei Province Key R&D Program, Project Number: 18211407D; Science and Technology Bureau Foundation of Jingzhou, Project Number: 2022AA13; Guiding Project of Hubei Provincial Department of Education, Project Number: B2021102.
Disclosure statement
No potential conflict of interest was reported by the authors.
Supplementary material
Supplemental data for this article can be accessed online at https://doi.org/10.1080/15440478.2023.2181910
Additional information
Funding
References
- Barany, S., N. Kartel’, and R. Meszaros. 2014. Electrokinetic potential of multilayer carbon nanotubes in aqueous solutions of electrolytes and surfactants. Colloid Journal 76 (5):509–14. doi:10.1134/s1061933x14050020.
- Bhavsar, P. S., M. Zoccola, A. Patrucco, A. Montarsolo, R. Mossotti, M. Giansetti, G. Rovero, S. S. Maier, A. Muresan, and C. Tonin. 2017. Superheated water hydrolyzed Keratin: A new application as a foaming agent in foam dyeing of cotton and wool fabrics. ACS Sustainable Chemistry & Engineering 5 (10):9150–59. doi:10.1021/acssuschemeng.7b02064.
- Cao, J., and C. Wang. 2017. Multifunctional surface modification of silk fabric via graphene oxide repeatedly coating and chemical reduction method. Applied Surface Science 405:380–88. doi:10.1016/j.apsusc.2017.02.017.
- Carrasco, P. M., S. Montes, I. García, M. Borghei, H. Jiang, I. Odriozola, G. Cabañero, and V. Ruiz. 2014. High-concentration aqueous dispersions of graphene produced by exfoliation of graphite using cellulose nanocrystals. Carbon 70:157–63. doi:10.1016/j.carbon.2013.12.086.
- Cintora, A., F. Käfer, C. Yuan, and C. K. Ober. 2021. Effect of monomer hydrophilicity on ARGET–ATRP kinetics in aqueous mini‐emulsion polymerization. Journal of Polymer Science 60 (4):666–73. doi:10.1002/pol.20210658.
- Dong, C., W. Xin, and Y. Luo. 2018. Synthesis and application of a cationic waterborne polyurethane fixative using quaternary ammonium diol as a chain extender. RSC Advances 8 (73):42041–48. doi:10.1039/c8ra09123d.
- Eren, E., L. Oksuz, A. I. Komur, F. Bozduman, N. N. Maslakci, and A. U. Oksuz. 2015. Atmospheric pressure plasma treatment of wool fabric structures. Journal of Electrostatics 77:69–75. doi:10.1016/j.elstat.2015.07.004.
- Fang, C., S. Pan, Z. Wang, X. Zhou, W. Lei, and Y. Cheng. 2019. Synthesis of waterborne polyurethane using snow as dispersant: Structures and properties controlled by polyols utilization. Journal of Materials Science & Technology 35 (7):1491–98. doi:10.1016/j.jmst.2019.03.017.
- Feng, X. -J., Y. -J. Tang, Y. Yang, G. Wang, P. Mei, and L. Lai. 2022. Relationship between the dynamic interfacial activity and demulsification performance of hyperbranched poly(amido amine) polyethers. Colloids and Surfaces A, Physicochemical and Engineering Aspects 633:127869. doi:10.1016/j.colsurfa.2021.127869.
- Frunza, L., L. Diamandescu, I. Zgura, S. Frunza, C. P. Ganea, C. C. Negrila, M. Enculescu, and M. Birzu. 2018. Photocatalytic activity of wool fabrics deposited at low temperature with ZnO or TiO2 nanoparticles: Methylene blue degradation as a test reaction. Catalysis Today 306:251–59. doi:10.1016/j.cattod.2017.02.044.
- Hassan, M. M., and C. M. Carr. 2019. A review of the sustainable methods in imparting shrink resistance to wool fabrics. Journal of Advanced Research 18:39–60. doi:10.1016/j.jare.2019.01.014.
- Hu, X., M. Tian, L. Qu, S. Zhu, and G. Han. 2015. Multifunctional cotton fabrics with graphene/polyurethane coatings with far-infrared emission, electrical conductivity, and ultraviolet-blocking properties. Carbon 95:625–33. doi:10.1016/j.carbon.2015.08.099.
- Jiang, Z., Y. Zhang, Q. Wang, P. Wang, Y. Yu, M. Zhou, and E. Li. 2021. Thiol-based ionic liquid: an efficient approach for improving Hydrophilic performance of wool. Journal of Natural Fibers 19 (14):1–12. doi:10.1080/15440478.2021.1993403.
- Kaur, A., J. N. Chakraborty, and K. K. Dubey. 2016. Enzymatic functionalization of wool for felting shrink-resistance. Journal of Natural Fibers 13 (4):437–50. doi:10.1080/15440478.2015.1043686.
- Kim, H., and S. Lee. 2017. Electrical properties of graphene/waterborne polyurethane composite films. Fibers and Polymers 18 (7):1304–13. doi:10.1007/s12221-017-7142-7.
- Kowalczyk, D., W. Fortuniak, U. Mizerska, I. Kaminska, T. Makowski, S. Brzezinski, and E. Piorkowska. 2017. Modification of cotton fabric with graphene and reduced graphene oxide using sol–gel method. Cellulose 24 (9):4057–68. doi:10.1007/s10570-017-1389-4.
- Li, Y., J. Noro, J. Li, C. Silva, J. Su, and A. Cavaco-Paulo. 2021. Grafting of Poly(tyrosine) by Laccase improves the tensile strength and anti-shrinkage of wool. Journal of Natural Fibers 19 (15):1–13. doi:10.1080/15440478.2021.2002785.
- Lü, Z., Y. Yi, C. Zhang, K. Lü, H. Feng, and Y. Zhang. 2020. Synthesis of castor oil-based cationic waterborne polyurethane emulsion and its application. Journal of Wuhan University of Technology-Materials Science Education 35 (4):832–40. doi:10.1007/s11595-020-2327-0.
- Ma, P. -C., N. A. Siddiqui, E. Mäder, and J. -K. Kim. 2011. Correlation between electrokinetic potential, dispersibility, surface chemistry and energy of carbon nanotubes. Composites Science and Technology 71 (14):1644–51. doi:10.1016/j.compscitech.2011.07.014.
- McNeil, S. J., and R. A. McCall. 2011. Ultrasound for wool dyeing and finishing. Ultrasonics Sonochemistry 18 (1):401–06. doi:10.1016/j.ultsonch.2010.07.007.
- Mei, J., N. Zhang, Y. Yu, Q. Wang, J. Yuan, P. Wang, L. Cui, and X. Fan. 2018. A novel “trifunctional protease” with reducibility, hydrolysis, and localization used for wool anti-felting treatment. Applied Microbiology and Biotechnology 102 (21):9159–70. doi:10.1007/s00253-018-9276-y.
- Montarsolo, A., R. Mossotti, R. Innocenti, and E. Vassallo. 2013. A study on washing resistance of pp-HMDSO films deposited on wool fabrics for anti-pilling purposes. Surface & Coatings Technology 224:109–13. doi:10.1016/j.surfcoat.2013.03.007.
- Nayak, D., and M. Debata. 2013. Effect of composition and milling time on mechanical and wear performance of copper–graphite composites processed by powder metallurgy route. Powder Metallurgy 57 (4):265–73. doi:10.1179/1743290113y.0000000080.
- Naz, F., M. Zuber, K. Mehmood Zia, M. Salman, J. Chakraborty, I. Nath, and F. Verpoort. 2018. Synthesis and characterization of chitosan-based waterborne polyurethane for textile finishes. Carbohydrate Polymers 200:54–62. doi:10.1016/j.carbpol.2018.07.076.
- Oliveira, E. V., F. A. Costa, R. A. Raimundo, C. S. Lourenço, M. A. Morales, S. N. Mathaudhu, and U. U. Gomes. 2022. Effect of milling time in characteristics of the powder Cu-5wt.%graphite. Advanced Powder Technology 33 (1):103360. doi:10.1016/j.apt.2021.11.012.
- Peng, L., R. Guo, J. Lan, S. Jiang, C. Li, and Z. Zhang. 2017. Synthesis of silver nanoparticles on wool fabric in supercritical carbon dioxide. Materials Express 7 (5):405–10. doi:10.1166/mex.2017.1386.
- Periolatto, M., F. Ferrero, C. Vineis, and F. Rombaldoni. 2013. Multifunctional finishing of wool fabrics by chitosan UV-grafting: An approach. Carbohydrate Polymers 98 (1):624–29. doi:10.1016/j.carbpol.2013.06.054.
- Shirgholami, M. A., L. Karimi, and M. Mirjalili. 2016. Multifunctional modification of wool fabric using graphene/TiO2 nanocomposite. Fibers and Polymers 17 (2):220–28. doi:10.1007/s12221-016-5838-8.
- Su, M., X. Chen, L. Zhang, and J. Min. 2020. Synthesis of active graphene with para-ester on cotton fabrics for antistatic properties. Nanomaterials (Basel) 10 (6):1147. doi:10.3390/nano10061147.
- Sukhawipat, N., W. Raksanak, E. Kalkornsurapranee, A. Saetung, and N. Saetung. 2020. A new hybrid waterborne polyurethane coating synthesized from natural rubber and rubber seed oil with grafted acrylate. Progress in Organic Coatings 141:105554. doi:10.1016/j.porgcoat.2020.105554.
- Sukhawipat, N., N. Saetung, P. Pasetto, J. -F. Pilard, S. Bistac, and A. Saetung. 2020. A novel high adhesion cationic waterborne polyurethane for green coating applications. Progress in Organic Coatings 148:105854. doi:10.1016/j.porgcoat.2020.105854.
- Wang, C. X., M. Du, J. C. Lv, Q. Q. Zhou, D. W. Gao, G. L. Liu, L. M. Jin, Y. Ren, and J. H. Liu. 2015. Effect of wetting pretreatment on structure and properties of plasma induced chitosan grafted wool fabric. Fibers and Polymers 16 (2):404–12. doi:10.1007/s12221-015-0404-3.
- Wang, G., X. Li, Z. Du, E. Li, and P. Li. 2014. Butynediol-ethoxylate based trisiloxane: Structural characterization and physico-chemical properties in water. Journal of Molecular Liquids 197:197–203. doi:10.1016/j.molliq.2014.04.033.
- Xu, L., N. Zhang, Q. Wang, J. Yuan, Y. Yu, P. Wang, and X. Fan. 2019. Eco-friendly grafting of chitosan as a biopolymer onto wool fabrics using Horseradish Peroxidase. Fibers and Polymers 20 (2):261–70. doi:10.1007/s12221-019-8546-3.
- Yu, J., Z. Pang, J. Zhang, H. Zhou, and Q. Wei. 2018. Conductivity and antibacterial properties of wool fabrics finished by polyaniline/chitosan. Colloids and Surfaces A, Physicochemical and Engineering Aspects 548:117–24. doi:10.1016/j.colsurfa.2018.03.065.
- Zhang, M., B. Ning, Y. Bai, X. Tai, and G. Wang. 2021. Solution properties of mixed system containing butynediol-ethoxylate polysiloxanes and polyether trisiloxane surfactant. Colloid and Interface Science Communications 41:100367. doi:10.1016/j.colcom.2021.100367.
- Zhang, R., and A. Wang. 2015. Modification of wool by air plasma and enzymes as a cleaner and environmentally friendly process. Journal of Cleaner Production 87:961–65. doi:10.1016/j.jclepro.2014.10.004.
- Zhu, L., X. Ding, and X. Wu. 2020. A novel method for improving the anti-pilling property of knitted wool fabric with engineered water nanostructures. Journal of Materials Research and Technology 9 (3):3649–58. doi:10.1016/j.jmrt.2020.01.102.
- Zhu, J., Z. Wu, D. Xiong, L. Pan, and Y. Liu. 2019. Preparation and properties of a novel low crystallinity cross-linked network waterborne polyurethane for water-based ink. Progress in Organic Coatings 133:161–68. doi:10.1016/j.porgcoat.2019.04.033.