ABSTRACT
Nettle plants are grown naturally as forest weeds in Himalayan region without much explored economic value. The plant remains under-explored as far as extraction of fiber for textile and other industrial applications are concerned. Present study highlights a complete information, starting from fiber extraction, retting, production of blended yarns & fabrics, coloration and products development along with cost analysis. Himalayan nettle plant was considered for fiber extraction through microbial retting, yielded 1.25% dry fiber. Extracted fiber was characterized in details for physical, mechanical, chemical, thermal and morphological properties. Fiber having fineness of 2.2–2.4 tex, tenacity of 10–16 cN/tex, and elongation of 3% was blended with viscose fiber in 100/0, 75/25, 50/50, and 25/75 ratios to produce blended yarns. Those yarns and bleached & dyed yarns were utilized as weft to produce fabric in handloom, keeping cotton yarn as warp. Yarns and fabrics properties were also evaluated in detail. Apparel textile products, like female fashion wear (cost $ 13) and “shawl” (cost $ 39), were produced. The developed products are not only be fashionable apparel but also be fully biodegradable. Research findings advocate that nettle plant may be considered as an untapped potential source for fiber extraction and application in apparel textile.
摘要
在喜马拉雅地区,荨麻植物作为森林杂草自然生长,没有太多的经济价值. 就提取纤维用于纺织和其他工业应用而言,该工厂仍处于探索阶段. 本研究强调了一个完整的信息,从纤维提取、脱胶、生产混纺纱线和织物、着色和产品开发以及成本分析开始. 喜马拉雅荨麻植物被考虑通过微生物脱胶提取纤维,产生1.25%的干纤维. 对提取的纤维进行了物理、机械、化学、热和形态财产的详细表征. 以100/0、75/25、50/50和25/75的比例将纤维细度为2.2-2.4 tex、韧性为10-16 cN/tex和伸长率为3%的粘胶纤维与粘胶纤维共混,以生产混纺纱. 这些纱线以及漂白和染色的纱线被用作纬纱,在手摇织布机中生产织物,保持棉纱作为经纱. 还对纱线和织物的财产进行了详细评估. 生产了服装纺织产品,如女性时装(成本13美元)和“披肩”(成本39美元). 开发的产品不仅是时尚的服装,而且是完全可生物降解的. 研究结果表明,荨麻植物可能被认为是一种尚未开发的纤维提取和应用于服装纺织品的潜在来源.
Introduction
Natural fibers like cotton, silk, wool, flax, ramie and jute, and the man-made fibers like, viscose, cellulose acetate, polyester, acrylic, nylon, and polypropylene are mostly used in the production of apparel, home and technical textiles, and also in making fiber-reinforced composites, either in pure form or in appropriate blends (Chattopadhyay et al. Citation2021; Debnath Citation2016; Jagadeesh et al. Citation2022; Teli, Pandit, and Samanta Citation2015). Both the natural as well as manmade fibers play as a key resource of raw materials to fulfil the demand of textile industry. With recent awareness on eco-sustainability, biodegradability, low density & cost, and easy of availability & processability, the utilization of different natural fibers is gaining considerable attention to develop biodegradable textile products (Vinod et al. Citation2020). Well-explored natural fibers, namely, cotton, silk, wool, jute, flax, ramie, etc. could not meet the demand of total natural fiber for textile, composite and other industrial applications. Thus, the research has been also conducted in the recent past to explore other upcoming natural fibers, obtained from the different plant parts/agro-wastes. In this context, locally available agricultural plants waste (bark or leaf) can be utilized for the extraction of textile-grade fibers, namely, Okra, Banana, Pineapple, Coconut, Cornhusk, and Areca nut husk (Chattopadhyay et al. Citation2020; Gupta, Patra, and Samanta Citation2021; Kambli et al. Citation2018; Sunny and Rajan Citation2021). In this direction, nettle, an important plant, mostly grown naturally in the high altitude of Himalayan region, is now becoming a popular fiber for textile application. Nettle plant is not cultivated for the fiber production, rather it is naturally grown as forest weed without much explored economic value. There are two main nettle fibers producing species, namely, European nettle and Himalayan nettle, the alter is grown as wild in fertile forest soils in altitudes ranging from 1200 to 3000 m. It is a perennial stinging nettle (Urtica dioica L.) plant, which grows on ruderal sites, in gardens, at the edges of forests and in wooded areas of riverine floodplains. All parts of the plants are covered with thorn, like stinging hairs that can cause painful rashes. Fiber is similar to flax, ramie, and hemp, and it can be used to produce a fine cloth. Nettle was used for the production of textiles in central Europe, even before the introduction of cotton. In spite of its potential for textile applications, it lost its popularity, when cotton arrived in the 16th century, due to ease of cotton harvesting and spinning. At present with the advancements in awareness, scientific development, availability of suitable spinning technologies, nettle fiber is once again becoming popular for making apparel, home, and technical textiles.
After cutting the plant, the bark is removed or directly the plant is retted to get fiber. Nettle fiber possesses characteristics of low density, surface waxiness, biodegradability, and reusability (Brindha, Thilagavathi, and Viju Citation2019). Tensile strength of nettle fiber ranges from 24 to 62 cN/tex, higher than cotton, silk, and wool fibers. It is also finer than many plant fibers, namely, coir, corn-husk, sisal, and banana. Fiber is reported to be white, silky and could produce finer and silkier fabric than flax (Viju and Thilagavathi Citation2019, Citation2022a; Viju, Thilagavathi, and Aarthy Citation2020). Alkali treatment of fiber notably enhances the tensile properties in terms of increase in crystallinity, appearance, tensile strength, and elongation at break (Kumar and Das Citation2017). Fiber has been explored for oil absorbency application, where it was observed to perform better than many other natural fibers (Thilagavathi and Karan Citation2018; Viju and Thilagavathi Citation2021; Viju et al. Citation2019). Oil spill clean-up of nettle fiber after requisite physical/chemical treatment has been also reported (Viju and Thilagavathi Citation2019, Citation2022b; Viju, Thilagavathi, and Aarthy Citation2020). Nettle fiber possesses suitable attributes for its blending with other natural fibers, namely, wool, cotton, ramie, flax, and other fibers (Radhakrishnan1 and Preeti Citation2015).
In this direction, an attempt was made to produce yarn from the 100% nettle fiber, but the yarn quality was not satisfactory (Bodros and Baley Citation2008). Blending with other fibers was found to enhance the spinning performance as well as yarn quality. Organic cotton and bamboo fibers were blended with the nettle fibers for yarn production and optimum results were found in the 50:50 blend ratio (Radhakrishnan1 and Preeti Citation2015). Woven fabrics were developed using nettle/organic cotton and nettle/bamboo fibers blended yarns, in weft direction. Fabric properties were compared with the 100% organic cotton and bamboo fabrics, prepared using same yarn in both the directions. Friction spinning technology was also considered to produce yarns from nettle fiber for producing fashionable upholstery (Shaolin et al. Citation2005). Researchers (Bhardwaj and Pant Citation2014) also reported the preparation of nettle/acrylic blended woven textile. The performance of nettle fiber-based towel was investigated by some workers (Sabir and Unal Citation2017).
Present work describes properties evaluation of nettle fiber in details after microbial retting including fiber yield, followed by the development of nettle/viscose blended yarns in different blend ratios e.g., nettle/viscose 100/0, 75/25, 50/50, and 25/75. The study also reports production of fully biodegradable woven fabric (cotton warp) along with yarns and fabric’s properties evaluation in details. Blended yarn was also bleached with H2O2 and colored with reactive dye in different shades so as to produce apparel textile products with jacquard designs. The novelty of the work is an insight of fiber extraction from green-plant-stem retting as well as ribbon retting along with some anatomical information (plant diameter, thickness of fibrous bark layer), fiber to stalk yield in green and dried plant. It also summarizes a complete information on details fiber’s properties evaluation, development of blended yarns by varying the blend ratios, production of different woven fabrics, coloration of nettle yarn, development of apparel textile products, calculation of different fibers percentage in blended textiles, and cost analysis of products, as shown in .
Materials and methods
Materials
Nettle fiber was extracted from the green plants, received from the Manipur, India, to study the microbial retting and dry fiber yield parameters. Nettle fiber was also procured from the Uttarakhand, India, and its different textile properties were compared with the extracted fiber. Regenerated viscose fiber of fineness − 0.67 tex, staple length − 108 mm, tenacity 28.3 cN/tex, and extension percentage − 22.6 was used for making blended yarns.
Extraction of fiber
Nettle plants collected from the Manipur, India, were cut into the length of 12–15 cm for microbial retting. Retting bath was prepared with tap water and 0.5% di-ammonium phosphate that acts as a growth supplement of bacteria. Pectinolytic bacteria, namely, Lysinibacillus boronitolerans was used as microbial inoculation with 5% in 1:15 liquor ratio at 30–35°C. The cut pieces nettle stem was immersed into the retting bath for 3 to 5 days and observed the possibility of fiber separation from the stem on each day. After 5th day, it was possible to extract fiber properly. Extracted fiber was then washed in fresh water and dried in air, before measurement of fiber properties. Nettle plant stem can be retted to obtain textile fiber using above process or initially ribbon (fibrous layer) can be separated from the bark of stem, then it can be retted following the same process.
Development of nettle/viscose blended yarn, fabric and products
Hand opened fiber was passed through the flax finisher card twice to break the inherent meshy structure of the fiber. Prior to carding process, fiber was subjected to application of oil-in-water emulsion, ensuring 2% oil addition on weight of fiber and stored for 48 hours for conditioning as well as better mechanical processing. Carded slivers were then mixed with viscose top in a drawing machine, adjusting doubling to produce nettle/viscose blended yarns with blend ratio of 100/0, 75:25, 50:50, and 25:75 on weight-to-weight basis. Blended silver of 1st drawing machine was processed through the two sequential drawing machines. Finally, blended yarns of count 82–93 tex were spun in apron draft jute spinning machine with baxter flyer, with 291 twist per meter (TPM). Prior to weaving, warping was conducted in sectional warping followed by beaming process using 60s reed. Woven union fabrics were developed in handloom from the different nettle/viscose fiber blended yarns, used in the weft direction, keeping the 2/60s count cotton yarn as warp without sizing. The complete process of development of blended yarn, fabric and apparel products is shown in . Nettle/viscose (25/75) fibers blended yarn was dyed with reactive dyes in 2% shade in green, orange, and blue colors. Different blended yarns were utilized to produce handloom fabric (shawl) with jacquard design/attachment and other products. In the blended fabric, percentage of cotton fiber (yarn) was measured by unraveling and weighing the warp yarn from the fabric; nettle and viscose fiber content was calculated from the blend percentage.
Evaluation of physical parameters and chemical composition
Fiber fineness was measured by standard gravimetric method i.e., cut and weigh method. In this process, 2-mm fiber length samples cut from different parts of the sample were mixed and 100 of such samples were weighed. The result was expressed in “Tex” value and average of five such readings was reported. Bundle strength of nettle fiber was measured using a bundle strength tester, which works on the principle of beam balance following the Bureau of Indian Standards (BIS), 1986. Chemical composition of nettle fiber in terms of cellulose, hemi-cellulose, and lignin percentage was measured following the TAPPI (T-203 cm-99), TAPPI (T-223 om-82), and TAPPI (T-222 om-02) methods, respectively (TAPPI test methods). Pectin, fat, and wax percentages were measured by ammonium oxalate and solvent extraction process, respectively. Yarn linear density was measured by gravimetric method. Tensile properties of nettle/viscose fibers blended yarns were measured in Instron Tensile Tester, Model 5567 following IS 1670. Fabrics tensile properties were measured by following the ASTM D1682–1975 method. Dimensional stability of woven fabric was measured following the IS 9: 1982 standard. Bending length and flexural rigidity of the blended fabric samples were measured using a stiffness tester following ASTMD1388 method. Crease recovery angle of the fabrics was evaluated using the Shirley’s crease tester following IS 4681:1968 method. Measurement techniques consist of a circular dial, which carries the clamp for holding the specimen. In center of the dial, there is a knife edge and an index line to measure the recovery angle, where 180° angle signifies full recovery. During the measurement, the specimen size of 4 cm × 1.5 cm is cut by a template and carefully creased by folding the fabric and by placing a weight of 500 gm in the between two glass plates. After 1 min, the weight is removed and the creased fabric is clamped on the instrument. Subsequently, the sample is allowed to recover to the highest extent and the angle is measured from the engraved scale.
Measurement of color parameters
Color parameters, namely, whiteness index (WI- on the “HUNTER” scale), yellowness index (YI- as per ‘ASTM D 1925), L, a*, b*, color saturation strength (c) and hue (h) were measured for the different fibers and fabrics using Spectrascan − 5100 computerized color matching system. Depth of color (shade) of fiber and fabric samples was determined by measuring the color strength (K/S) from the reflectance data using Kubelka – Munk equation. The color strength K/S = (1-R)2/(2 R), where K and S denote the absorption and scattering coefficients, R denotes the reflectance of sample at λmax (wavelength of maximum absorption). Color fastness of the dyed yarn was measured in weather fastness tester following IS:2454: 1985 standard.
SEM surface and cross-sectional morphology
Surface and cross-sectional morphology of nettle and viscose fiber, and nettle/viscose blended yarns were evaluated under scanning electron microscope (SEM, Model: Stereoscan 360, Cambridge Instruments) by typifying the surface at 350–500 ×. Prior to fiber or yarn SEM imaging, samples were coated with conductive metal. The elemental identification along with quantitative estimation of the samples was performed in SEM equipment with energy-dispersive X-ray (EDX) attachment.
Thermal analysis
Thermogravimetric analysis (TGA) of the nettle fiber was carried out on a thermogravimetric analyzer (TA instrument, Model Q-500, USA) over the temperature ranges of 50°C to 550°C in nitrogen atmosphere at 20 mL/min flow rate and at 10°C/min heating rate. Differential scanning calorimetry (DSC) of the nettle fiber was also carried out in the same equipment.
X-Ray diffraction
X-ray crystallinity of the finely powdered nettle fiber was determined in Phillips X-ray diffractometer (Model 1700) with nickel-filtered copper Kα 1.54 A0 radiation. Crystallinity index (CI) was calculated using the following expression: CI = [(It- Ia)/It] × 100, where It is the total intensity of peak at 22.9º and Ia is the amorphous peak intensity at 18.2º (Nam et al. Citation2016). The crystal size (D) was calculated using Debye – Scherrer formula: D= k λ/β cos θ, where K is known as the Scherer’s constant (K = 0.94), λ is the X-ray wavelength (1.54 Å), β is full width at half maximum (FWHM) of the diffraction peak, and θ is the angle of diffraction (Kambli et al. Citation2018).
Results and discussion
Fiber extraction and properties
Retting of green-nettle-plant-stem was conducted to obtain textile fiber after defoliation and cutting approximately 6 inch stem at the bottom part of the plant. The process was carried our using a pectinolytic bacteria (Lysinibacillus boronitolerans), keeping the green stem to water ratio of 1:15 at 30–35°C along with addition of 0.5% di-ammonium phosphate that acts as a growth supplement of bacteria, as shown in . In retting process, as the fiber bundle is obtained from the bark of the plant, thus, the extracted fiber may be called as “bast fiber.” Nettle plant stem can be retted to obtain textile fiber using above process or first ribbon (fibrous layer of thickness 1.22 mm) can be extracted from the bark of the stem, then it can be retted following the same process. In green-plant-stem-retting after 3 days, fiber was tried to extract, but it did not show satisfactory extraction process. It was observed that fiber could be properly extracted after five days of microbial retting. From , it can be seen that the green plant stem consists of approximately 76.5% wet-stick and 18.3% wet fibrous layer (ratio 4.18:1), whereas this proportion becomes 19.3% and 4.6% (ratio 4.19 : 1) after drying of both the components. The average thickness of the fibrous layer attached to the green plant stick, from where the fiber bundle could be extracted, is 1.22 mm, whereas diameter of the plant stem is 13.7 mm. Average yield of dry fiber after microbial retting of green plant stem is 1.25%. Ribbon retting process yields little more dry fiber percentage. Different parameters of plant, fibrous layer thickness, and fiber yield are tabulated in . In anatomical section, the diameter of plant was found to vary from 5.7 to 28.7 mm (average 13.7 mm) considering the bottom to top part of the plant and also variation in plant-to-plant. The plant stem outline is wavy in nature owing to the presence of ridges and furrows, as reported by Singh and Kali (Citation2019). Cortical region could be differentiated from outer side to single layer epidermis with the presence of cellulosic wall. The stinging hairs followed by 3 to 4 layered collenchymatous hypodermal region and toward inner side parenchymatous cortex were present. The stele was present below the endodermis, where 12–16 vascular bundles are arranged in a ring, that exhibits endarch, conjoint, collateral, and open condition. Vascular bundles encircle parenchymatous pith in the center. In the transverse section of stem, fibro-vascular bundles range 12–20 in number.
Table 1. Different parameters of nettle plant, fibrous layer, and yield.
From the gravimetric fineness value (), it can be seen that both the extracted and procured fibers have almost similar fineness of value (2.2 to 2.4 tex). It is also observed that fiber breaking load as well as tenacity values of the procured fiber is higher than the microbial extracted fiber. However, elongation percentage remained similar. Furthermore, it can be seen that except initial modulus, other fiber parameters, namely, tenacity, total energy, tensile strain, and specific work of rupture are higher in the procured fiber.
Table 2. Fineness and strength (single fiber and bundle of fibers) properties of nettle fibers.
Since the nettle fiber procured from Uttarakhand, India, exhibits better fineness and mechanical properties along with availability in a large quantity, this fiber () was considered for further processing i.e., production of blended yarns with viscose, development of union fabrics and product development. Fiber length distribution was studied by taking 100 individual fibers, randomly from the bulk sample, as shown in . Nettle fiber has a wide range of length variation, ranging from 28 cm to 70 cm with an average fiber length of 41 cm with CV of 22%. Similarly, diameter of 100 fiber samples was measured by optical microscope technique; it shows that the fiber diameter ranges from 71 to 93 µm, with an average value of 84 µm (co-efficient of variation, CV − 21%). Fiber shows two XRD peak at 2θ values of 14.7º and 22.9º with crystallinity index (CI) of 75. Higher the crystallinity index value signifies a well-order structure/arrangement of cellulose macro-molecular polymer chains in the fiber structure. With increasing the CI value, fiber properties like strength, tenacity, and density are expected to increase. The CI value of nettle fiber is higher than the sisal fiber (0.60), and a little lower than the jute, flax, and hemp fibers (0.78–88) (Celino et al. Citation2013). The uniformity in crystal size was measured in terms of full width at half maximum (FWHM), which shows the values of 0.358 and 0.977 for their corresponding 2θ values of 14.7 and 22.9. Crystal size of the nettle fiber is calculated to be 1.6 nm and 4.2 nm for the 2θ values of 14.7 and 22.9, respectively.
Color parameters of fiber
Different color attributes of the various fibers, namely, nettle, viscose, and cotton (yarn) were measured and depicted in . Whiteness index (WI) of nettle fiber (WI: 61) is better than many similar ligno-cellulosic fibers like jute (WI: 50.3) and banana (WI: 53.8) (Chattopadhyay et al. Citation2020). Cotton shows higher whiteness index value of 73 due to the absence of lignin. On the other hand, regenerated viscose rayon, being a pure cellulosic fiber showed highest whiteness index of 86. The value of a* (red for +Ve and green for -Ve) slowly reduce from nettle to viscose, as fiber becomes whiter in appearance. Yellowness index (YI) also follows a similar trend, where YI values decrease from 24.6 to 14.4 for the nettle to viscose fibers. Similar result is also visible for b* value (yellow for +Ve and blue for -Ve). Due to darker color of nettle fiber, it reflects less amount of incident light during the spectroscopic color measurement, thus exhibited highest K/S value of 0.94. Viscose being the whitest fibers among the three, reflects highest amount of light (61.5%), resulting lowest K/S value of 0.12. The cotton fiber showed results in between.
Table 3. Spectroscopic color parameters of different fibers.
Fiber chemical properties
Elemental chemical composition of nettle fiber was studied by energy-dispersive X-ray-analysis (EDX). shows several peaks, corresponding to the various elements at different energy levels. As EDX technique cannot detect the hydrogen atom, the peaks only for carbon and oxygen are present. Fiber contains carbon (49.21%) and oxygen (45.63%) almost in equal quantity, as far as their atomic percentage is concerned (). Some other minerals like calcium, silicone, magnesium, etc are also present in minor quantity (2.62%) that might have come in the process of fiber retting and/or present in the plant body. Similar results were also observed in other plant fibers (Kambli et al. Citation2018; Roy, Samanta, and Patra Citation2019). The presence of small quantity of nitrogen and fluorine in the elemental analysis might has appeared due to the presence of other aromatic molecules in the plant/fiber, in addition to cellulose, hemi-cellulose, and lignin. Chemical composition of nettle fiber in terms of cellulose, hemi-cellulose, and lignin content was measured following different TAPPI methods. It shows the presence of 71.4% cellulose, 16.7% hemicellulose, and 4.5% lignin. Furthermore, the fiber contains 2.3% pectin, and 2.8% fat & wax.
Table 4. EDX elemental percentage in the nettle fiber.
Fiber morphology
shows the SEM surface as well as cross-sectional morphology of the nettle fiber. All the fiber cross-sections look like elliptical in nature. Nettle being a plant fiber, unlike other similar fibers, the characteristic lumen is marginally visible in the fiber cross-section. It may also be noted that the breadth or diameter of the fiber varies notably due to variation in fiber to fiber or in the top to bottom part of the fiber. The measurable diameter of fiber is in the range of 62 to 100 µm. Fiber looks like tape/ribbon like surface with the tentative length-to-breadth ratio (aspect ratio) is more than 5000, considering the average fiber diameter of 78 µm. The small variation in fiber diameter obtained from the SEM and optical microscope images is due to difference in their working principle. In the surface morphology several serrated features are visible. It indicates that surface is not smooth and it may be useful, where adhesion property is important. shows the surface morphology of the regenerated rayon fiber (viscose). As it is produced by wet-coagulation process, fiber seems to be much uniform in diameter along with presence characteristic serrated surface features.
Fiber thermal properties
Thermal analysis like, thermogravimetric analysis (TGA) and differential scanning calorimetry (DSC) were performed to understand the thermal stability of this under-explored natural fiber. Thermal stability of any textile fiber is important prior to any chemical processing such as, bleaching, dyeing and various functional finishing either in pure form or suitable blends, where the sample would be subjected to elevated temperature ranges for a certain duration. It also depicts flammability/thermal stability properties of the fiber. .a shows the thermogravimetric analysis (TGA) curve of nettle fiber in nitrogen atmosphere. The TGA curve depicts three stages of mass loss. In the initial stage at temperature below 200°C, mass loss of around 11.2% occurred mainly due to the removal of bound and unbound absorbed moisture from the fiber. Pyrolysis of ligno-cellulosic polymer occurred in the temperature range 250–384°C with signature of mass loss of around 58%. Major mass loss happened at around 348°C. Above 384°C, dehydration and char formation occurred and the residual mass of 20% at temperature of 548°C is a clearly indication of higher thermal stability of the fiber. In this temperature zone, there is an around 10.8% loss in fiber mass. In the DSC a sharp endothermal peak can be seen in the temperature range of 50–160°C, correspond to the heat of evaporation of water molecules absorbed in the fiber (.b). A similar observation is also made in TGA analysis. The curve exhibits another endothermic peak at around 350–383°C with a peak at 369°C, corresponds to depolymerization of cellulose with the formation of flammable gases like, pyroglucosan and levoglucosan. At this stage, pyrolytic degradation takes place with a rapid cleavage of the glucosidic bond. The TGA and DSC analysis show, the nettle fiber is reasonably thermally stable, similar to other plant-based ligno-cellulosic fibers viz., jute, flax and banana.
Nettle/Viscose blended yarn properties
Nettle fiber was blended with viscose fiber with blend ratios of 100/0, 75/25, 50/50 and 25/75 in first drawing machine for intimate mixing of these two fibers. shows images of the developed yarns. Tensile parameters of blended yarn namely tensile strain, tenacity, initial modulus and work-of-rupture were measured and compared with 100% nettle yarn. From the , it can be seen that tenacity pure nettle yarn is highest (10.9 cN/tex), however it reduced notably with the introduction of flexible (fine) viscose fiber in the yarn structure. Effect of presence of viscose fiber is more clearly visible for initial modulus value, where it reduced gradually from 554 cN/tex to 271 cN/tex. The incorporation of 25%, 50% and 75% viscose fiber in the blended yarn reduced the initial modulus by 30%, 44% and 51%, respectively. The distribution/presence of nettle and viscose fibers in the 50/50 blended yarn is shown in , where viscose fibers are noticed mostly at the inner part of the yarn due to migration from surface toward the core. It might be due to lower initial modulus (885 cN/tex) and lower fineness (0.67 tex) of viscose fiber in comparison of nettle fiber 1823 cN/tex and 2.2 tex, respectively (Hearle Citation2001; Roy and Roy Citation2005). Presence of viscose fiber thus reduces the hardness/rigidity of the yarns, which is use full for apparel textile. Tensile strain varies in the yarn samples within 2.06% − 4.20%, due to low extension percentage of nettle fiber<3%. Highest tensile strain value was noted in nettle/viscose (25/75) blended yarn due to higher extension percentage (22.6%) of viscose fiber (Roy and Roy Citation2005). As expected, cotton yarn showed higher elongation percentage (6.26%), tenacity (13.1 cN/tex) and work of rupture (4.16 m2/s2) than the blended yarns.
Figure 11. SEM cross-sectional image of the 50/50 nettle/viscose blended yarn (red circle -nettle fiber).
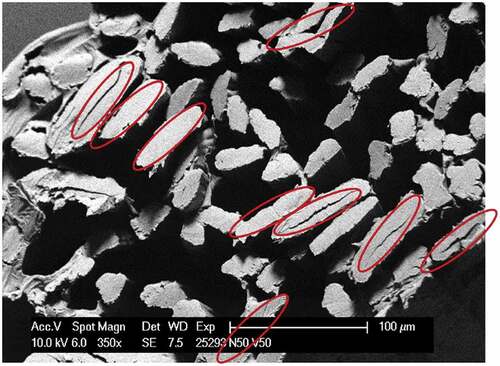
Table 5. Properties of different nettle/viscose fiber blended yarns.
Nettle/Viscose blended fabric properties
(a) Color parameters of fabric samples
Different color parameters of the four different nettle/viscose fibers blended fabrics were evaluated. It can be seen from the that with increase in viscose fiber in the blended yarn as well as in the developed union fabric, WI value increases linearly from 64 to 71 i.e., 10% increase in WI value. The WI values (64–71) in all the four fabrics are much higher than the whiteness index value of nettle fiber (61) as depicted in . This has occurred due to introduction of viscose fiber in the blended yarn in concurrence with use of cotton yarn in the warp direction and those fibers (viscose and cotton) possess higher whiteness index values of 86 and 73, respectively. Maximum measured whiteness value of 71 in the blended fabrics was more than nettle fiber and less than cotton or viscose fibers. Due to increase in whiteness index and L* value in concurrent with increase in reflectance %, the color strength (K/S) decrease gradually from 0.72, 0.66, 0.61, and 0.46 in the blended fabrics with 100%, 75%, 50%, and 25% nettle fiber. Yellowness index value does not change much with the introduction of viscose fiber in the blended fabrics, thus b* value also does not change notably.
Table 6. Spectroscopic color parameters in the nettle/viscose blended union fabrics.
(b) Fabric physical properties
It can be seen from the that areal density of the fabric varies in the range of 135 to 152 g/m2, with highest value in the 100% nettle fabric. The 100% nettle fabric also showed highest thickness of 0.71 mm, due to higher count of 100%, while the remaining samples possess thickness of 0.55 mm. Ends per inch remains almost similar, as all the fabrics were developed from the same warp beam. As viscose fiber is more flexible due to its lower fineness, the bending length reduces marginally with the introduction of viscose fiber in the blended fabrics, resulting 6.8% reduction in blending length along weft direction (N25/V75). This leads to reduction in flexural rigidity of the samples from 854 to 689 (19%), 649 (24%), and 637 (25.4%) in the 75/25, 50/50, and 25/75 nettle/viscose blended fabrics. Similar results were also measured in the warp direction for all the union fabrics. Bending modulus in warp and weft direction also followed similar trend like flexural rigidity. The measured higher bending and flexural rigidity in weft direction of the fabric would help to provide better draping attribute of the garments and also the product does not become very limp due to use of fine cotton yarn in the warp. Nettle/viscose (25/75) blended fabric shows best crease recovery angle both in warp and weft direction.
Table 7. Different physical properties of the nettle/viscose fiber blended union fabrics.
(c) Fabric mechanical properties
From the , it can be seen that tenacity of the 100% nettle fabric in weft direction is highest, possibly due to higher yarn strength as depicted in . It reduces with the increase of viscose fiber in the blended fabrics. The 50/50 and 25/75 nettle/viscose blended fabrics show comparable properties in the weft direction. Fabric tenacity in the warp direction improved a little (15.6%) in the blended textiles. However, tenacity in the weft direction decreases with increase in viscose fiber in the blended fabrics.
Table 8. Mechanical properties of the different nettle/viscose blended union fabrics.
Fabric elongation percentage in the weft direction enhances from 2.84% in 100% nettle yarn to 3.57%, 4.02%, and 5.05% in the blended fabrics with the presence of 25%, 50%, and 75% viscose fiber in blended yarn. The reason may be due to gradual increase of viscose fiber in the blend fabric/yarn, which has high elongation percentage of 22.6% (Roy and Roy Citation2005) in comparison with 2.6% of nettle fiber. Initial modulus in the warp and weft direction in the blended fabrics was found to reduce, which implies that fabric becomes softer and more flexible. These results are well in agreement with the reduction in blending length and flexural rigidity owing to incorporation of softer/finer viscose fiber () and lower yarn initial modulus (). shows the percentage of different fibers in the blended textiles. It can be seen from that the weight percentage for nettle fiber varies from 16.9% in nettle/viscose (N25/V75) to maximum 67.22% in 100% nettle fabric, whereas weight of viscose fiber varies from 16.83% in N75/V25 to 50.68% in the N25/V75 fabric.
Table 9. Percentage of cotton (warp), nettle and viscose fiber in the blended textiles.
Coloration of nettle/viscose yarn and product development
Among all the different nettle/viscose blended fabrics, the N25/V75 blended fabric showed better physical and mechanical properties (lower value) as far as their bending length, flexural rigidity, and initial modulus are concerned. Lower values of such parameters along with higher crease recovery angle and acceptable tenacity ensure the requisite flexibility of fabric to be used for apparel textile manufacturing. Thus, the nettle/viscose (25/75) blended yarn was dyed with reactive dyes (2% shade) in three different colors, namely, green, orange and blue, and utilized as weft to produce “shawl” in handloom with jacquard design (). Similarly, the above undyed (natural color) yarn was used in the weft direction to develop plain weave union fabric (cotton warp) and the same was used to produce female wear. The cost of female wear and shawl is estimated to be $ 13 and $ 39, respectively. The dyed yarns showed the color fastness rating of 4–5. Dimensional stability of woven fabric shows the shrinkage of 1.6% and 2.5% in the warp and weft directions, respectively. In addition to apparel wear, nettle fiber-based pure or blended yarns may also be used in making home textile/furnishing and handicraft items.
Conclusions
It is possible to extract 1.25–1.81% dry fiber on weight of green nettle plant by microbial retting of stem or ribbon. Physical, chemical, mechanical, and thermal properties were evaluated in details to find out suitable textile applications. Nettle fiber from Uttarakhand, Himalayan origin was blended with viscose fiber in four different blend ratios, namely, 100/0, 75/25, 50/50, and 25/75. Blending of viscose fiber reduces the initial modulus, for yarn: from 554 to 271 cN/tex and for fabric: from 416 to 224 N/mm2. Viscose fiber improves the suppleness of blended yarns and fabrics, as observed from the reduced flexural rigidity and initial modulus. A similar improvement was also noticed for WI color value in the blended fabrics. However, tenacity in blended yarn and fabric reduced marginally due to introduction of viscose fiber in the structure. The nettle/viscose (25/75) blended fabric showed overall satisfactory properties, thus considered for successive coloration and apparel products development. The study postulated that nettle plant may be considered as a potential fiber-yielding plant for extraction of fiber to be used in apparel textile manufacturing. It also includes a complete process i.e., from fiber extraction to fashionable products development along with cost analysis.
Highlights
Nettle plant, an underexplored forest resources, has huge potential for application in apparel textile.
Study reports a complete information from fiber extraction to fashionable apparel production.
Nettle/viscose blended yarns with ratios of 100/0, 75/25, 50/50, and 25/75 produced and used as weft yarn.
Performance-related physical, optical, and mechanical properties of fabrics reported in details.
Fully biodegradable female wear (cost $ 13) and shawl (cost $ 39) developed using natural, bleached, and dyed yarns.
Acknowledgements
Authors would like to acknowledge the Director, ICAR-NINFET for various research supports.
Disclosure statement
No potential conflict of interest was reported by the authors.
References
- Bhardwaj, S., and S. Pant. 2014. Properties of nettle-acrylic blended yarn. Journal of the Textile Association 75 (1):28–17.
- Bodros, E., and C. Baley. 2008. Study of the tensile properties of stinging nettle fibers (Urtica Dioica). Materials Letters 62 (14):2143–45. doi:10.1016/j.matlet.2007.11.034.
- Brindha, R., G. Thilagavathi, and S. Viju. 2019. Development of nettle–polypropylene-blended needle-punched nonwoven fabrics for oil spill cleanup applications. Journal of Natural Fibers 17 (10):1439–53. doi:10.1080/15440478.2019.1578717.
- Celino, A., S. Freour, F. Jacquemin, and P. Casari. 2013. Characterization and modeling of the moisture diffusion behavior of natural fibers. Journal of Applied Polymer Science 130 (1):297–306. doi:10.1002/app.39148.
- Chattopadhyay, S. N., N. C. Pan, A. N. Roy, and K. K. Samanta. 2020. Pretreatment of jute and banana fibre – its effect on blended yarn and fabric. Journal of Natural Fibres 17 (1):75–83. doi:10.1080/15440478.2018.1469450.
- Chattopadhyay, S. N., N. C. Pan, A. N. Roy, K. K. Samanta, and A. Khan. 2021. Hybrid bleaching of jute yarn using hydrogen peroxide and peracetic acid. Indian Journal of Fibre & Textile Research 46:78–82.
- Debnath, S. 2016. Natural fibres for sustainable development in fashion industry. In Sustainable fibres for fashion industry. environmental footprints and Eco-design of products and processes, ed. S. Muthu and M. Gardetti, 89–108. Singapore: Springer. doi:10.1007/978-981-10-0522-04.
- Gupta, P. K., S. Patra, and K. K. Samanta. 2021. Potential of Okra for application in textiles: A review. Journal of Natural Fibres 18 (11):1788–800. doi:10.1080/15440478.2019.1697997.
- Hearle, J. W. S. 2001. Physical structure and fibre properties. In Regenerated cellulose fibres, ed. C. Woodings, 99–232. Cambridge: CRC press and Woodhead publishing.
- Jagadeesh, P., M. Puttegowda, Y. G. T. Girijappa, S. M. Rangappa, and S. Siengchin. 2022. Effect of natural filler materials on fiber reinforced hybrid polymer composites: An overview. Journal of Natural Fibers 19 (11):4132–47. doi:10.1080/15440478.2020.1854145.
- Kambli, N. D., K. K. Samanta, S. Basak, S. K. Chattopadhyay, P. G. Patil, and R. R. Deshmukh. 2018. Characterization of the corn husk fibre and improvement in its thermal stability by banana pseudostem sap. Cellulose 25 (9):5241–57. doi:10.1007/s10570-018-1931-z.
- Kumar, N., and D. Das. 2017. Alkali treatment on nettle fibers: Part I: Investigation of chemical, structural, physical, and mechanical characteristics of alkali-treated nettle fibers. The Journal of the Textile Institute 108 (8):1461–67. doi:10.1080/00405000.2016.1257346.
- Nam, S., A. D. French, B. D. Condon, and M. Concha. 2016. Segal crystallinity index revisited by the simulation of X-raydiffraction patterns of cotton cellulose Iβ and cellulose II. Carbohydrate Polymers 135:1–9. doi:10.1016/j.carbpol.2015.08.035.
- Radhakrishnan1, S., and A. Preeti. 2015. Development of fabric from Girardina Diversifolia stem fibres and its blends. International Journal of Innovative Research in Science, Engineering and Technology 4 (11):10499–506. doi:10.15680/IJIRSET.2015.0411023.
- Roy, A. N., and P. Roy. 2005. Jute-viscose blended needle punched nonwovens - stress decay & cycling loading. Man-Made Textiles in India 48 (4):161–66.
- Roy, A. N., K. K. Samanta, and K. Patra. 2019. Physico-chemical properties of black yak fibre and its modification for blending with jute fibre. Journal of Natural Fibres 16 (2):225–36. doi:10.1080/15440478.2017.1414652.
- Sabir, E. C., and B. Z. Unal. 2017. The using of nettle fiber in towel production and investigation of the performance properties. Journal of Natural Fibers 14 (6):781–87. doi:10.1080/15440478.2017.1279102.
- Shaolin, X., S. Hong, H. Fengli, X. Aiming, and S. Xiaoyin. 2005. Technology research on friction spinning nettle core-spun yarn. Cotton Textile Technology 9:13–15.
- Singh, M., and G. Kali. 2019. Study on morpho-anatomical and histo-chemical charaterisation of stinging nettle, Urtica dioica L in Uttarakhand, India. Journal of Pharmacognosy and Phytochemistry 8 (3):4325–31.
- Sunny, G., and T. P. Rajan. 2021. Review on areca nut fiber and its implementation in sustainable products development. Journal of Natural Fibers 19 (12):1–15. doi:10.1080/15440478.2020.1870623.
- TAPPI test methods. Atlanta USA. Vol. 1. https://www.tappi.org
- Teli, M. D., P. Pandit, and K. K. Samanta. 2015. Application of atmospheric pressure plasma technology on textile. Journal of the Textile Association 75 (6):422–27.
- Thilagavathi, G., and C. P. Karan. 2018. Investigations on oil sorption capacity of nettle fibrous assembly and 100% nettle and nettle/kapok blended needle-punched nonwovens. Journal of Industrial Textile 49 (4):415–30. doi:10.1177/1528083718787532.
- Viju, S., and G. Thilagavathi. 2019. Oil spill cleanup by bonded nettle fibrous mat. Journal of the Institution of Engineers (India) 100 (1):93–100. doi:10.1007/s40034-018-0131-6.
- Viju, S., and G. Thilagavathi. 2021. Effect of alkali treatment of nettle fibers on oil absorbency. Journal of Natural Fibers 18 (12):2092–101. doi:10.1080/15440478.2020.1723776.
- Viju, S., and G. Thilagavathi. 2022a. Comfort characteristics of nettle Nonwoven fabrics. Journal of Natural Fibers 19 (4):1490–97. doi:10.1080/15440478.2020.1779899.
- Viju, S., and G. Thilagavathi. 2022b. Hot water treatment on Nettle fibers: An environment-friendly/Economical process for the production of oil sorbent. Journal of Natural Fibers 19 (2):761–69. doi:10.1080/15440478.2020.1761929.
- Viju, S., G. Thilagavathi, and S. Aarthy. 2020. Effect of hydrochloric acid treated nettle fibre on oil absorbency. Indian Journal of Fibre & Textile Research 45 (3):332–37.
- Viju, S., G. Thilagavathi, B. Vignesh, and R. Brindha. 2019. Oil sorption behaviour of acetylated nettle fiber. The Journal of the Textile Institute 110 (10):1415–23. doi:10.1080/00405000.2019.1603184.
- Vinod, A., M. R. Sanjay, S. Suchart, and P. Jyotishkumar. 2020. Renewable and sustainable biobased materials: An assessment on biofibers, biofilms, biopolymers and biocomposites. Journal of Cleaner Production 258:120978. doi:10.1016/j.jclepro.2020.120978.