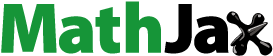
ABSTRACT
The demand for face masks is increasing exponentially due to the coronavirus pandemic and the particulate matter (PM) in the atmosphere. As a result, an enormous number of disposable mask filters have been produced and discarded, contributing to plastic waste. Underprivileged people who cannot afford to purchase commercial face masks have started making fabric masks with waste clothing; however, this material does not effectively filter viruses or PM. Therefore, in this study, a chitosan coating was applied to clothing fabrics to increase their effectiveness as face masks. The improvement in the PM removal efficiency owing to the chitosan polymer was observed for stocking, innerwear, and bamboo materials, but not for cotton. Furthermore, chitosan prepared in the form of a nanowhisker (CsW) achieved a PM 2.5 removal efficiency of 96% in a five-layer cotton fabric. In addition, a commercial biodegradable poly(lactic acid) filter was coated with CsW, which increased the PM 2.5 removal efficiency from 67% to 83%. Additionally, microbial growth was significantly suppressed in the chitosan-coated fabrics, and the degree to which it was suppressed depended on the coating concentration. The study will aid in the utilization of face mask filters that are more sustainable, efficient, and widely accessible.
摘要
由于冠状病毒大流行和大气中的颗粒物 (PM) ,口罩的需求呈指数级增长. 因此,大量的一次性口罩过滤器被生产和丢弃,导致塑料垃圾. 无力购买商业口罩的弱势群体已经开始用废旧衣物制作织物口罩; 然而,这种材料不能有效地过滤病毒或PM. 因此,在本研究中,将壳聚糖涂层应用于服装面料,以提高其作为面罩的有效性. 观察到壳聚糖聚合物对袜子、内衣和竹子材料的PM去除效率有所提高,但对棉花则没有. 此外,以纳米晶须 (CsW) 形式制备的壳聚糖在五层棉织物中实现了96%的PM 2.5去除效率. 此外,商用可生物降解聚乳酸过滤器涂有CsW,这将PM 2.5去除效率从67%提高到83%. 此外,壳聚糖涂层织物中的微生物生长受到显著抑制,其抑制程度取决于涂层浓度. 这项研究将有助于使用更可持续、更高效、更易于使用的面罩过滤器.
Introduction
Currently, there is a large demand for face masks due to the unprecedented coronavirus pandemic (COVID-19) (Siller et al. Citation2021; Worby and Chang Citation2020; Wu et al. Citation2020). In addition, the presence of particulate matter (PM) is the most problematic air pollution issue because it severely impacts the natural environment in various ways as well as the quality of human life (Anderson, Thundiyil, and Stolbach Citation2012; Raaschou-Nielsen et al. Citation2016). PM is classified as PM 2.5 and PM 10 based on the rough particle size (2.5 and 10 µm, respectively) (Ryou, Heo, and Kim Citation2018). Considering these small particle sizes, face masks have become the most effective countermeasures against PM hazards that are available to individuals, and it is important to develop an efficient face mask filter in terms of air permeability and PM removal.
There are two problems associated with the rapidly increasing demand for face masks. The first problem is mask waste. Globally, >12 billion disposable masks have been discarded every month in 2021 due to COVID-19 (Dissanayake et al. Citation2021; Selvaranjan et al. Citation2021; Torres and De-la-Torre Citation2021). This has led to serious environmental issues associated with large volumes of plastic waste (Jang et al. Citation2022). In general, high-performance disposable masks are essential for preventing infectious diseases, and they are usually made of polypropylene. However, these masks are not biodegradable and are not recycled because they are biohazardous. Thus, the masks quickly become waste. Masks made out of cloth are reusable, but they have low filter efficiencies. Therefore, a high-performance reusable mask is needed (Liao et al. Citation2020; Mueller et al. Citation2020; Ullah et al. Citation2020; Zangmeister et al. Citation2021). The second problem pertains to the lower class population, who cannot purchase high-performance masks (Konda et al. Citation2020; Shakya et al. Citation2017). In developing countries, a large number of people cannot afford to buy disposable masks every day. Thus, there is a need to economically increase the performance of masks for the underprivileged.
Chitosan coating can be used to improve the performance of filters made out of clothing fabric. The raw material, chitin, is the most abundant resource in the marine environment, and it has significant potential for various applications due to its bio-regeneration capability, biodegradability, biocompatibility, and antibacterial and hemostatic properties (Tran et al. Citation2019; Hao et al. Citation2020; Ju et al. Citation2021; Saleh et al. Citation2022; Yan and Chen Citation2015; Yu et al. Citation2019; Zhang et al. Citation2021). Chitosan has cationic sites and polar amine groups that attract polar ultrafine PM (e.g., SO42- and NO3-), even in wet conditions (Lee et al. Citation2022). The benefits of a high surface area and low viscosity can be achieved during the coating process by preparing chitosan in the form of a nanowhisker with a short aspect ratio (Kim et al. Citation2019, Citation2021; Vehapi, Yilmaz, and Özçimen Citation2021).
In this study, we present a sustainable method for improving the filter performance of cloth masks using chitosan, which is a bio-renewable polymer (). We found that as more fabric layers were stacked, the base PM removal efficiency increased. In most cases, regardless of the fabric type, the coating of chitosan materials increased the removal efficiency by approximately 10% in one-layer fabrics. In addition, the process of coating in the nanowhisker form increased the removal efficiency by 20% or more. Moreover, the coating demonstrated antibacterial properties, and therefore it was effective as biodegradable filters.
Experimental
Dip-coating procedure and measurement of PM
Fabrics with a size of 5 cmⅹ5 cm were prepared, dip-coated in a chitosan solution (1 wt%) and chitosan nanowhisker (CsW) solution (0.2 wt%) for 5 min, and dried for 24 h under ambient conditions (Figure S1). The method for measuring the filter efficiency was as follows: small circular pieces of paper with a diameter of 5 mm were obtained using a fixed paper punch and burned to generate PM. As shown in Figure S2, the paper was burned in a closed PM source chamber, and the amount of PM generated was controlled by the number of pieces of paper (Choi et al. Citation2021). The PM was then transported by the air compressor, and the velocity of the air (approximately 1–2 m/s) passing through the filter was adjusted by changing the pressure of the compressed air. The number of PMs was counted by a particle counter (DT-9881 M, CEM Instruments, China), and the removal efficiency was calculated by comparing the number of detected particles in the presence and absence of a filter. The relative humidity during the test was approximately 15%, and the pressure drop (ΔP) was measured using a pressure and flow meter (DT-8920, CEM Instruments, China) (Kim et al. Citation2019; Li et al. Citation2020).
Chemical and morphological characterization
Surface images of the non-coated and chitosan-coated fabrics were obtained using a scanning electron microscope (SEM; Tescan MIRA3, Czech Republic) with a beam intensity of 3 kV. To confirm the presence of the coating in the fabrics, the attenuated total reflection Fourier transform infrared (ATR-FTIR; Nicolet iS50, Thermo, USA) spectra were measured, and 128 scans were collected to ensure that each sample had high-resolution data.
Assessment of the antibacterial activity of the coated fabrics
The antibacterial properties of the coated fabric samples were evaluated with a quantitative method (AATCC-100) using Staphylococcus aureus (S. aureus) ATCC 25,923 (gram-positive) and Escherichia coli (E. coli) ATCC 25,922 (gram-negative) as reference bacterial strains (Mohiti-Asli, Pourdeyhimi, and Loboa Citation2014; Rajendran et al. Citation2013).
An inoculum containing 100 mL of nutrient broth (NB) was incubated for 24 h at 37 ± 1°C. Then, each fabric specimen, which was 4.8 ± 0.1 cm in diameter, was inoculated with 1 ± 0.1 mL of the diluted bacterial suspension. The specimens were then incubated for 24 h at 37°C ±1°C. After incubation, the specimens were placed in jars containing 100 mL of phosphate buffer solution, and the jars were shaken vigorously for 1 min. After serial dilution, 0.1 mL of the diluted solution was transferred to NB agar plates. After 24 h of incubation at 37 ± 1°C, the number of living bacteria was determined by counting the colonies. The antibacterial treatment efficiency was calculated using the relation
where R is the percentage reduction, A is the number of bacteria on the control fabric, and B is the number of bacteria on the coated fabric. All experiments were conducted in triplicates to ensure reproducibility.
Results and discussion
To prepare effective face mask filters with clothing fabrics, commonly available fabrics, including stockings, innerwear, bamboo, and cotton, were acquired. Dipping solutions were prepared by dissolving the chitosan polymer with a molecular weight of 50,000–190,000 g/mol in deionized (DI) water at a concentration of 1 wt%, and by dispersing CsW with a diameter of 40 nm and a length of approximately 300 nm in DI water at a concentration of 0.2 wt% (Figure S3). After immersing the fabrics in these solutions for 5 min and drying them for one day, the PM removal efficiency and pressure drop before and after the coating were compared.
The presence of the chitosan coating in the fabrics was determined by identifying the characteristic peaks of chitosan in the ATR-FTIR spectra (). In all four fabrics, the characteristic stretching vibrations of chitosan, including the O-H, N-H, amide I, amide II, and C-O vibrations, were observed. This confirmed that the coating process was successful (Dahmane et al. Citation2014; Fernandes Queiroz et al. Citation2015).
Figure 2. ATR-FTIR spectra before (black lines) and after (red lines) the chitosan coating of (a) stockings, (b) innerwear, (c) bamboo, and (d) cotton.
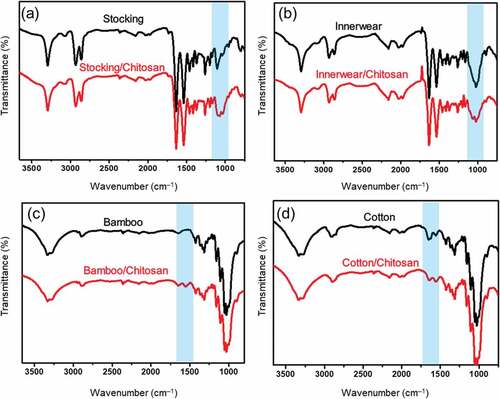
and Table S1 show the PM removal efficiency and pressure drop before and after the chitosan was coated onto the fabrics. The more layers in the fabric, the higher the base removal efficiency. The PM 2.5 removal efficiency of the stocking increased from 42.1% for a single layer (one-layer) to 80.4% for 10 layers, that of the innerwear increased from 44.5% to 82.0%, and that of the bamboo increased from 43.0% to 89.3%. As the fabric thickness increased, the length of the path through which the PM passed increased, which in turn improved the removal efficiency (Hasolli, Park, and Rhee Citation2013; Riefler et al. Citation2018). Accordingly, the 2–3 Pa pressure drop in the one-layer fabric increased to 17–27 Pa in the 10-layer fabric. For reference, the pressure drop of a dental KF-AD-grade mask filter is 12 Pa, and that of a KF-94-grade filter is 58 Pa.
Figure 3. Effect of chitosan coating on the PM removal efficiency for (a) stockings, (b) innerwear, (c) bamboo, and (d) cotton.
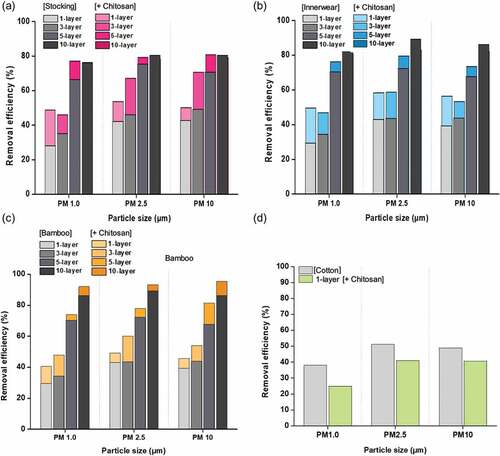
After the fabrics were coated with chitosan, the PM removal efficiencies of most of them improved. This was because the permanent dipoles exhibited by the amine groups on the surface of the chitosan captured ultrafine PM (e.g., nitrogen and sulfur oxides) (Abbas et al. Citation2021; Gao and Zhang Citation2020; Li et al. Citation2011). In the case of the one-layer stockings, the PM 1.0 removal efficiency increased by 20.8% (from 28.0% to 48.8%), and the PM 10 removal efficiency increased by 7.5% (from 42.7% to 50.2%). The incremental effect of the chitosan gradually decreased as more layers were stacked: the chitosan offered only a 4% (from 75.3% to 79.3%) improvement relative to the PM 2.5 removal efficiency of the five-layer fabric, and there was almost no change in the 10-layer fabric. Thus, the improvement in the PM removal efficiency via the electrostatic attraction of chitosan is more effective when the fabric is thin. This is because, when the fabric is thick, the effect of the longer path through which the air passes is more significant than the effect of the chitosan. This phenomenon was also observed for the innerwear and bamboo fabrics. The improvement in the PM 1.0 removal efficiency in the one-layer fabric was 16.9% for the innerwear and 9.6% for the bamboo, which was smaller than that exhibited by the stockings. The maximum increase achieved by the chitosan coating was 91.8% for PM 10 removal efficiency of the 10-layer bamboo fabric. For the cotton fabric, the PM removal efficiency and pressure drop decreased after chitosan coating, regardless of the particle size ().
Based on the SEM images before and after chitosan coating (), no noticeable changes were observed in the stocking, innerwear, and bamboo fabrics. However, in the cotton fabric, the gaps between the fibers were found to be wider. Because both bamboo and cotton fabrics are made of cellulose fibers, the difference in these results indicates that the effect of the chitosan coating on the fabric is influenced not only by the materials, but also by the post-treatment or weaving methods (Choi et al. Citation2021; Dennis Citation1974; Konda et al. Citation2020).
Figure 4. SEM images before (left panels) and after (right panels) chitosan coating of (a) stockings, (b) innerwear, (c) bamboo, and (d) cotton.
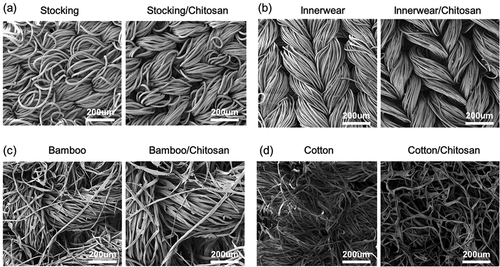
Compared to the single chitosan polymer chain, CsW has a lower viscosity and higher surface area, which is expected to have a positive effect on the improvement in the PM filter efficiency, as demonstrated by the experimental data ( and Table S2) (Choi et al. Citation2021; Nguyen et al. Citation2021; Sivanesan et al. Citation2021; Thuy et al. Citation2021). In the case of the one-layer stocking fabric, the PM 1.0 removal efficiency increased by 25.4% after CsW was applied, achieving a higher removal efficiency of 53.4% compared to that with chitosan coating (the PM 1.0 removal efficiency increased by 20.8% to achieve an overall removal efficiency of 48.8%). For the five-layer fabric, the PM 2.5 removal efficiency was 84.9%, and the PM 10 removal efficiency was 89.4%, which was 5.6% and 8.6% higher, respectively, than that when coated with chitosan. This was also observed for the innerwear and bamboo fabrics: the PM 1.0 removal efficiency of the one-layer fabric improved by 21.3% for the innerwear and 26.7% for the bamboo.
Figure 5. Effect of CsW coating on the PM removal efficiency for (a) stockings, (b) innerwear, (c) bamboo, and (d) cotton.
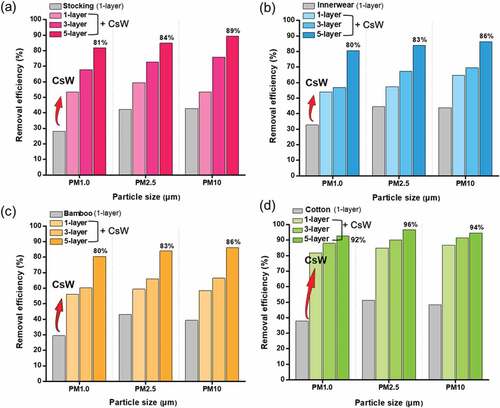
For the bamboo, the effect of the CsW was much greater than that of the chitosan. This effect was surprisingly more significant in the cotton fabric: the PM 1.0 removal efficiency of the one-layer fabric increased by 43.8% (from 38.0% before coating; to 81.8% after coating). The CsW coating on the five-layer fabric achieved a PM 2.5 removal efficiency of 96.6%, which is equal to the efficiency (96%) of a commercial dental mask filter.
The SEM images taken before and after the CsW coating (shown in ), indicated that the fabric fibers underwent no changes. However, numerous nanoscale objects of nano dimensions were present on the fibers (Choi et al. Citation2021; Mostafa and Ameen Citation2022). The durability of face masks in regards to wash fastness is crucial, hence, the filtering efficiency after multiple washing cycles was examined. The three-layer and five-layer fabrics that were coated with chitosan and CsW were washed using DI water up to five times. As the washing cycles increased, the PM filter efficiencies decreased gradually. However, it’s noteworthy that even after five washing cycles, the efficiency level remained above 80% of the original efficiency, and mostly showed better filtering efficiency compared to uncoated fabrics (Table S3 and S4).
Figure 6. SEM images before (left panels) and after (right panels) CsW coating for (a) stockings, (b) innerwear, (c) bamboo, and (d) cotton.
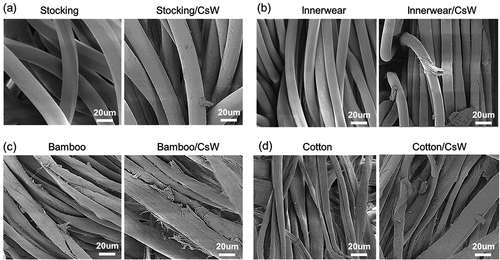
Because environmental pollution caused by disposable face masks has become serious, efforts should be made to research and develop filters using biodegradable materials and expand the corresponding market (Babaahmadi et al. Citation2021; Wang et al. Citation2022). Therefore, poly(lactic acid) (PLA)-based filters that were commercially available in Korea were purchased and coated with chitosan and CsW to investigate the PM removal efficiency before and after coating (). The chitosan coating improved the PM removal efficiencies by only 1–7%, while the CsW coating improved the PM removal efficiencies by 14–26%. In particular, the PM 10 removal efficiency increased from 61% to 87%. This difference in improvement is attributed to the high viscosity of chitosan, which hinders effective dispersion through fabric fibers. In contrast, the permanent electrostatic attraction of CsW, enabled by its low viscosity and high surface area, facilitates effective PM removal, as evident from the SEM images ().
Figure 7. (a) Effect of chitosan coating of PLA filter on the PM removal efficiency. (b) SEM images of fabrics before coating, (c) after chitosan coating, and (d) after CsW coating.
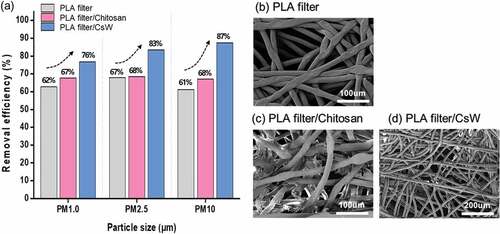
The interiors of mask filters, which have large surface areas, are inevitably exposed to moisture, providing an environment for rapid bacterial growth. To prevent this, the antibacterial effect of the fabrics coated with chitosan was determined using two types of bacteria: E. coli (gram-negative) and S. aureus (gram-positive). AATCC 100, the most widely used international standard, was used to measure the antibacterial effect of the fabrics (). To mimic how a sweat-stained T-shirt left at room temperature for a long time develops an odor as microorganisms reproduce, the non-coated fabric and chitosan-coated fabrics were inoculated with a certain amount of microbial samples and incubated at 37°C for 24 h. The number of living microorganisms in the fabrics was then counted (). As a result, compared to the untreated non-coated fabric, the fabrics coated with 1 wt% chitosan achieved an antibacterial effect of~50% against S. aureus and~25% against E. coli (). When the chitosan coating concentration was increased from 1 to 3 wt%, the microbial growth inhibition increased to almost 100% against both S. aureus and E. coli. The antibacterial and antifungal effects resulting from the structural and physicochemical properties of chitosan are already well understood. For pH < 6, the quaternary ammonium groups (R-NH3+) of chitosan combine with the polyamines of the bacterial cell wall to induce cell hydrolysis or change cell wall permeability in order to facilitate microbial death (Chen and Cooper Citation2002; Kong et al. Citation2008; Vishu Kumar et al. Citation2005). At pH > 6, the unprotonated amino groups in chitosan transfer their lone pair of electrons to metal ions (Ca2+ and Mg2+) present on the bacterial surface for chelation, which suppresses the production of toxins and the overall growth of the microorganisms (Chung et al. Citation2003; Kong et al. Citation2010). In addition, in the case of low-molecular weight chitosan, cell death is promoted via penetration through the cell, which affects mRNA synthesis, protein synthesis, and mitochondrial functions (Kong et al. Citation2010; Rabea et al. Citation2003). Therefore, it was confirmed that coating fabrics with chitosan not only improve the PM removal efficiency, but also imparts antibacterial effects (Gomes et al. Citation2020).
Figure 8. Antibacterial effect of chitosan-coated fabrics. (a) Diagram of the experimental process of antimicrobial fabric test (AATCC 100). (b) Images of colonies on agar plates transferred from non-coated fabric and chitosan-coated fabric (3 wt%). (c) Microbial growth inhibition of S. aureus and E. coli on fabric samples coated with different concentrations of chitosan solutions (1 and 3 wt%). The data (n = 3) represents the mean ± standard deviation.
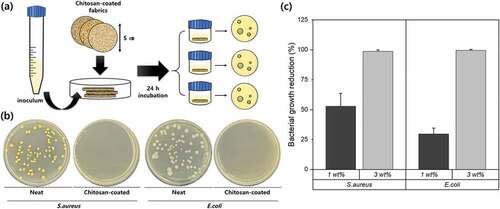
Conclusions
In summary, we investigated the applicability of fabrics as face mask filter materials by dip-coating fabrics into chitosan materials. As more fabric layers were stacked, the base PM removal efficiency increased. Regardless of the fabric type, most of the fabrics exhibited a higher removal efficiency after they were coated with chitosan. Generally, based on the one-layer fabric, the removal efficiency improved by approximately 10% after chitosan coating and by 20% or more after CsW coating. For cotton fabric, the removal efficiency decreased after chitosan coating, but increased by 40% after CsW coating, achieving a PM 2.5 removal efficiency of 96% in the five-layer fabric. The chitosan was also effective in commercial biodegradable filter materials, as the PM 2.5 removal efficiency improved from 67% to 83% after CsW coating. This demonstrates the possibility of improving the marketability of biodegradable filter products. Coating the fabrics with chitosan, a common antibacterial substance, greatly suppressed microbial growth in the fabrics and improved mask hygiene. We expect the results presented in this study to inspire resource recycling and the development of low-cost chitosan-coated fabric face masks that can be used as effective personal protective equipment.
Consent for publication
All authors have given approval to the final version of the manuscript.
Highlights
Dip-coating fabrics into chitosan materials for face mask filter materials.
Removal efficiency improves by 10% after chitosan coating and by 20% after nanowhisker coating.
Five-layered cotton fabric achieves PM 2.5 removal efficiency of 96%.
Coated fabrics suppress microbial growth improving mask hygiene.
Supplemental Material
Download MS Word (1.2 MB)Acknowledgements
We are thankful to Prof. Sejin Choi at Pusan National University for a fruitful discussion.
Disclosure statement
No potential conflict of interest was reported by the authors.
Data availability statement
Data are available upon reasonable request.
Supplemental data
Supplemental data for this article can be accessed online at https://doi.org/10.1080/15440478.2023.2187507
Additional information
Funding
References
- Abbas, W. A., B. S. Shaheen, L. G. Ghanem, I. M. Badawy, M. M. Abodouh, S. M. Abdou, S. Zada, and N. K. Allam. 2021. Cost-effective face mask filter based on hybrid composite nanofibrous layers with high filtration efficiency. Langmuir 37:7492–13. doi:10.1021/acs.langmuir.1c00926.
- Anderson, J. O., J. G. Thundiyil, and A. Stolbach. 2012. Clearing the air: A review of the effects of particulate matter air pollution on human health. Journal of Medical Toxicology 8:166–75. doi:10.1007/s13181-011-0203-1.
- Babaahmadi, V., H. Amid, M. Naeimirad, and S. Ramakrishna. 2021. Biodegradable and multifunctional surgical face masks: A brief review on demands during COVID-19 pandemic, recent developments, and future perspectives. The Science of the Total Environment 798:149233. doi:10.1016/j.scitotenv.2021.149233.
- Chen, C. Z., and S. L. Cooper. 2002. Interactions between dendrimer biocides and bacterial membranes. Biomaterials 23:3359–68. doi:10.1016/S0142-9612(02)00036-4.
- Choi, S., H. Jeon, M. Jang, H. Kim, G. Shin, J. M. Koo, M. Lee, H. K. Sung, Y. Eom, H. S. Yang, et al. 2021. Biodegradable, efficient, and breathable multi-use face mask filter. Advanced Science. 8 (6):2003155. doi:10.1002/advs.202003155.
- Chung, Y. C., H. L. Wang, Y. M. Chen, and S. L. Li. 2003. Effect of abiotic factors on the antibacterial activity of chitosan against waterborne pathogens. Bioresource Technology 88 (3):179–84. doi:10.1016/S0960-8524(03)00002-6.
- Dahmane, E. M., M. Taourirte, N. Eladlani, and M. Rhazi. 2014. Extraction and characterization of chitin and chitosan from Parapenaeus longirostris from Moroccan local sources. International Journal of Polymer Analysis and Characterization 19:342–51. doi:10.1080/1023666X.2014.902577.
- Dennis, R. 1974. Collection efficiency as a function of particle size, shape and density: Theory and experience. Journal of the Air Pollution Control Association 24:1156–63. doi:10.1080/00022470.1974.10470029.
- Dissanayake, J., C. Torres-Quiroz, J. Mahato, and J. Park. 2021. Facemasks: A looming microplastic crisis. International Journal of Environment Research Public Health 18 (13):7068. doi:10.3390/ijerph18137068.
- Fernandes Queiroz, M., K. R. T. Melo, D. A. Sabry, G. L. Sassaki, and H. A. O. Rocha. 2015. Does the use of chitosan contribute to oxalate kidney stone formation? Marine Drugs 13 (1):141–58. doi:10.3390/md13010141.
- Gao, Y., and J. Zhang. 2020. Chitosan modified zeolite molecular sieve particles as a filter for ammonium nitrogen removal from water. International Journal of Molecular Sciences 21:2383. doi:10.3390/ijms21072383.
- Gomes, L. P., S. I. Anjo, B. Manadas, A. V. Coelho, and V. M. F. Paschoalin. 2020. Proteomic analyses reveal new insights on the antimicrobial mechanisms of chitosan biopolymers and their nanosized particles against Escherichia coli. International Journal Molecular Sciences 21 (1):225. doi:10.3390/ijms21010225.
- Hao, L. T., Y. Eom, T. H. Tran, J. M. Koo, J. Jegal, S. Y. Hwang, D. X. Oh, and J. Park. 2020. Rediscovery of nylon upgraded by interactive biorenewable nano-fillers. Nanoscale 12:2393–405. doi:10.1039/C9NR08091K.
- Hasolli, N., Y. O. Park, and Y. W. Rhee. 2013. Experimental study on filtration performance of flat sheet multiple-layer depth filter media for intake air filtration. Aerosol Science and Technology 47:1334–41. doi:10.1080/02786826.2013.842281.
- Jang, M., H. Yang, S. A. Park, H. K. Sung, J. M. Koo, S. Y. Hwang, H. Jeon, D. X. Oh, and J. Park. 2022. Analysis of volatile organic compounds produced during incineration of non-degradable and biodegradable plastics. Chemosphere 303:134946. doi:10.1016/j.chemosphere.2022.134946.
- Ju, S., G. Shin, M. Lee, J. M. Koo, H. Jeon, Y. S. Ok, D. S. Hwang, S. Y. Hwang, D. X. Oh, and J. Park. 2021. Biodegradable chito-beads replacing non-biodegradable microplastics for cosmetics. Green Chemistry 23:6953–65. doi:10.1039/D1GC01588E.
- Kim, H., M. S. Shin, H. Jeon, J. M. Koo, Y. Eom, S. Choi, G. Shin, D. X. Oh, S. Y. Hwang, and J. Park. 2021. Highly reinforced poly(butylene succinate) nanocomposites prepared from chitosan nanowhiskers by in-situ polymerization. International Journal of Biological Macromolecules 173:128–35. doi:10.1016/j.ijbiomac.2021.01.102.
- Kim, T., T. H. Tran, S. Y. Hwang, J. Park, D. X. Oh, and B. S. Kim. 2019. Crab-on-a-tree: All biorenewable, optical and radio frequency transparent barrier nanocoating for food packaging. ACS Nano 13 (4):3796–805. doi:10.1021/acsnano.8b08522.
- Konda, A., A. Prakash, G. A. Moss, M. Schmoldt, G. D. Grant, and S. Guha. 2020. Aerosol filtration efficiency of common fabrics used in respiratory cloth masks. ACS Nano 14:6339–47. doi:10.1021/acsnano.0c03252.
- Kong, M., X. G. Chen, C. S. Liu, C. G. Liu, X. H. Meng, and L. J. Yu. 2008. Antibacterial mechanism of chitosan microspheres in a solid dispersing system against E. coli. Colloids and Surfaces B, Biointerfaces 65 (2):197–202. doi:10.1016/j.colsurfb.2008.04.003.
- Kong, M., X. G. Chen, K. Xing, and H. J. Park. 2010. Antimicrobial properties of chitosan and mode of action: A state of the art review. International Journal of Food Microbiology 144:51–63. doi:10.1016/j.ijfoodmicro.2010.09.012.
- Lee, S., L. T. Hao, J. Park, D. X. Oh, and D. S. Hwang. 2022. Nanochitin and nanochitosan: Chitin nanostructure engineering with multiscale properties for biomedical and environmental applications. Advanced Materials 34 (4):2203325. doi:10.1002/adma.202203325.
- Liao, L., W. Xiao, M. Zhao, X. Yu, H. Wang, Q. Wang, S. Chu, and Y. Cui. 2020. Can N95 respirators be reused after disinfection? How many times? ACS Nano 14:6348–56. doi:10.1021/acsnano.0c03597.
- Li, T. T., Y. Fan, X. Cen, Y. Wang, B. C. Shiu, H. T. Ren, H. K. Peng, Q. Jiang, C. W. Lou, and J. H. Lin. 2020. Polypropylene/Polyvinyl alcohol/metal-organic framework-based melt-blown electrospun composite membranes for highly efficient filtration of PM2.5. Nanomaterials 10 (10):2025. doi:10.3390/nano10102025.
- Li, X., P. Wu, G. F. Gao, and S. Cheng. 2011. Carbohydrate-functionalized chitosan fiber for influenza virus capture. Biomacromolecules 12:3962–69. doi:10.1021/bm200970x.
- Mohiti-Asli, M., B. Pourdeyhimi, and E. G. Loboa. 2014. Novel, silver-ion-releasing nanofibrous scaffolds exhibit excellent antibacterial efficacy without the use of silver nanoparticles. Acta Biomaterialia 10:2096–104. doi:10.1016/j.actbio.2013.12.024.
- Mostafa, K. M., and H. A. Ameen. 2022. Rendering viscose fabrics dye-able with basic and acid dyes using citric acid and chitosan nano particles based finishing formulation. Journal of Natural Fibers 19 (16):13167–79. doi:10.1080/15440478.2022.2086661.
- Mueller, A. V., M. J. Eden, J. M. Oakes, C. Bellini, and L. A. Fernandez. 2020. Quantitative method for comparative assessment of particle removal efficiency of fabric masks as alternatives to standard surgical masks for PPE. Matter 3:950–62. doi:10.1016/j.matt.2020.07.006.
- Nguyen, H. L., T. H. Tran, L. T. Hao, H. Jeon, J. M. Koo, G. Shin, D. S. Hwang, S. Y. Hwang, J. Park, and D. X. Oh. 2021. Biorenewable, transparent, and oxygen/moisture barrier nanocellulose/nanochitin-based coating on polypropylene for food packaging applications. Carbohydrate Polymers 271:118421. doi:10.1016/j.carbpol.2021.118421.
- Raaschou-Nielsen, O., R. Beelen, M. Wang, G. Hoek, Z. J. Andersen, B. Hoffmann, M. Stafoggia, E. Samoli, G. Weinmayr, K. Dimakopoulou, et al. 2016. Particulate matter air pollution components and risk for lung cancer. Environment International 87:66–73. doi:10.1016/j.envint.2015.11.007.
- Rabea, E. I., M. E. T. Badawy, C. V. Stevens, G. Smagghe, and W. Steurbaut. 2003. Chitosan as antimicrobial agent: Applications and mode of action. Biomacromolecules 4 (6):1457–65. doi:10.1021/bm034130m.
- Rajendran, R., R. Radhai, T. M. Kotresh, and E. Csiszar. 2013. Development of antimicrobial cotton fabrics using herb loaded nanoparticles. Carbohydrate Polymers 91:613–17. doi:10.1016/j.carbpol.2012.08.064.
- Riefler, N., M. Ulrich, M. Morshäuser, and U. Fritsching. 2018. Particle penetration in fiber filters. Particuology 40:70–79. doi:10.1016/j.partic.2017.11.008.
- Ryou, H. G., J. Heo, and S. Y. Kim. 2018. Source apportionment of PM10 and PM2.5 air pollution, and possible impacts of study characteristics in South Korea. Environmental Pollution 240:963–72. doi:10.1016/j.envpol.2018.03.066.
- Saleh, R. I., M. Kim, S. Y. Baek, and C. Cha. 2022. Chitosan-functionalized silica nanoparticles as a multifunctional coating material for improved water repellency, antimicrobial activity and mechanical strength of degradable bioplastics. Cellulose 29:7691–701. doi:10.1007/s10570-022-04745-w.
- Selvaranjan, K., S. Navaratnam, P. Rajeev, and N. Ravintherakumaran. 2021. Environmental challenges induced by extensive use of face masks during COVID-19: A review and potential solutions. Environmental Challenges 3:100039. doi:10.1016/j.envc.2021.100039.
- Shakya, K. M., A. Noyes, R. Kallin, and R. E. Peltier. 2017. Evaluating the efficacy of cloth facemasks in reducing particulate matter exposure. Journal of Exposure Science & Environmental Epidemiology 27:352–57. doi:10.1038/jes.2016.42.
- Siller, P., J. Reissner, S. Hansen, M. Kühl, A. Bartel, D. Schmelzeisen, T. Gries, U. Roesler, and A. Friese. 2021. Innovative textiles used in face masks: Filtration efficiency and self-disinfecting properties against Coronaviruses. Nanomaterials 11:2088. doi:10.3390/nano11082088.
- Sivanesan, I., M. Muthu, J. Gopal, N. Hasan, S. Kashif Ali, J. Shin, and J. W. Oh. 2021. Nanochitosan: Commemorating the metamorphosis of an exoskeletal waste to a versatile nutraceutical. Nanomaterials 11 (3):821. doi:10.3390/nano11030821.
- Thuy, V. T. T., L. T. Hao, H. Jeon, J. M. Koo, J. Park, E. S. Lee, S. Y. Hwang, S. Choi, J. Park, and D. X. Oh. 2021. Sustainable, self-cleaning, transparent, and moisture/oxygen-barrier coating films for food packaging. Green Chemistry 23 (7):2658–67. doi:10.1039/D0GC03647A.
- Torres, F. G., and G. E. De-la-Torre. 2021. Face mask waste generation and management during the COVID-19 pandemic: An overview and the Peruvian case. The Science of the Total Environment 786:147628. doi:10.1016/j.scitotenv.2021.147628.
- Tran, T. H., H. L. Nguyen, D. S. Hwang, J. Y. Lee, H. G. Cha, J. M. Koo, S. Y. Hwang, J. Park, and D. X. Oh. 2019. Five different chitin nanomaterials from identical source with different advantageous functions and performances. Carbohydrate Polymers 205:392–400. doi:10.1016/j.carbpol.2018.10.089.
- Ullah, S., A. Ullah, J. Lee, Y. Jeong, M. Hashmi, C. Zhu, K. I. Joo, H. J. Cha, and I. S. Kim. 2020. Reusability comparison of melt-blown vs nanofiber face mask filters for use in the coronavirus pandemic. Acs Applied Nano Materials 3:7231–41. doi:10.1021/acsanm.0c01562.
- Vehapi, M., A. Yilmaz, and D. Özçimen. 2021. Fabrication of oregano-olive oil loaded PVA/chitosan nanoparticles via electrospraying method. Journal of Natural Fibers 18:1359–73. doi:10.1080/15440478.2020.1774463.
- Vishu Kumar, A. B., M. C. Varadaraj, L. R. Gowda, and R. N. Tharanathan. 2005. Characterization of chito-oligosaccharides prepared by chitosanolysis with the aid of papain and Pronase, and their bactericidal action against Bacillus cereus and Escherichia coli. The Biochemical Journal 391:167–75. doi:10.1042/bj20050093.
- Wang, L., Y. Gao, J. Xiong, W. Shao, C. Cui, N. Sun, Y. Zhang, S. Chang, P. Han, F. Liu, et al. 2022. Biodegradable and high-performance multiscale structured nanofiber membrane as mask filter media via poly(lactic acid) electrospinning. Journal of Colloid and Interface Science 606:961–70. doi:10.1016/j.jcis.2021.08.079.
- Worby, C. J., and H. H. Chang. 2020. Face mask use in the general population and optimal resource allocation during the COVID-19 pandemic. Nature Communications 11 (1):4049. doi:10.1038/s41467-020-17922-x.
- Wu, H. L., J. Huang, C. J. P. Zhang, Z. He, and W. K. Ming. 2020. Facemask shortage and the novel coronavirus disease (COVID-19) outbreak: Reflections on public health measures. EClinicalMedicine 21:100329. doi:10.1016/j.eclinm.2020.100329.
- Yan, N., and X. Chen. 2015. Sustainability: Don’t waste seafood waste. Nature 524 (7564):155–57. doi:10.1038/524155a.
- Yu, H. S., H. Park, T. H. Tran, S. Y. Hwang, K. Na, E. S. Lee, K. T. Oh, D. X. Oh, and J. Park. 2019. Poisonous caterpillar-inspired chitosan nanofiber enabling dual photothermal and photodynamic tumor ablation. Pharmaceutics 11:258. doi:10.3390/pharmaceutics11060258.
- Zangmeister, C. D., J. G. Radney, M. E. Staymates, E. P. Vicenzi, and J. L. Weaver. 2021. Hydration of hydrophilic cloth face masks enhances the filtration of nanoparticles. Acs Applied Nano Materials 4:2694–701. doi:10.1021/acsanm.0c03319.
- Zhang, Y., M. Zhao, Q. Cheng, C. Wang, H. Li, X. Han, Z. Fan, G. Su, D. Pan, and Z. Li. 2021. Research progress of adsorption and removal of heavy metals by chitosan and its derivatives: A review. Chemosphere 279:130927. doi:10.1016/j.chemosphere.2021.130927.