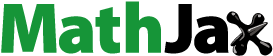
ABSTRACT
In this research, a novel eco-friendly green composite is fabricated by combining a biomatrix composed of a biopolymer, date palm fiber, and a filler obtained from discarded eggshell (ES) waste material. This research aims to check the influent of ES filler on thermal and viscoelasticity properties of bio-epoxy composite with incorporation of 40 wt.% date palm (DP) fiber. Various ES filler ratios, specifically 5 wt.%, 10 wt.%, 15 wt.%, and 20 wt.%, are dispersed into the composite. Thermogravimetric analysis (TGA) and dynamic mechanical analysis (DMA) approach were employed to investigate the properties of fabricated composites as a function of temperature in terms of storage modulus (E′), loss modulus (E′′), Tan delta (Tan δ), glass transition temperature (Tg), and Cole-Cole plot. Overall, incorporating ES filler into the bio-epoxy/DP fiber composites increased E′, E′′, and Tg significantly. ES-filled composites containing 5 and 10 wt.% exhibited properties comparable to 15 wt.% but less than 20 wt.% ES filler. Thermal tests result show that 20 wt.% ES-filled materials outperform their counterparts in terms of heat resistance or thermal stability. The evidence suggests that the embodiment of ES filler in bio-epoxy/DP fiber composites yields enhancements in both thermal and dynamic mechanical properties. This indicates the potential for utilizing ES filler loading in advanced composite applications that prioritize thermal stability and sustainability.
摘要
在这项研究中,通过将由生物聚合物、椰枣纤维和从废弃蛋壳(ES)废料中获得的填料组成的生物基质相结合,制备了一种新型环保绿色复合材料. 本研究旨在考察ES填料对掺入40 wt%的生物环氧复合材料的热性能和粘弹性的影响椰枣(DP)纤维. 各种ES填料比例、特别是5 wt%,10 wt%,15 wt%,和20 wt%,分散到复合材料中. 采用热重分析(TGA)和动态力学分析(DMA)方法,研究了所制备的复合材料的储能模量(E′)、损耗模量(E’′)、Tanδ(Tanδ)、玻璃化转变温度(Tg)和cole-cole图随温度的变化. 总体而言,在生物环氧/DP纤维复合材料中加入ES填料显著提高了E′、E′′和Tg. 含5和10 wt%的ES填充复合材料表现出相当于15 wt%的性能但小于20 wt%ES填料. 热测试结果表明,20 wt%ES填充材料在耐热性或热稳定性方面优于同类材料. 有证据表明,ES填料在生物环氧/DP纤维复合材料中的实施方案提高了热性能和动态力学性能. 这表明在优先考虑热稳定性和可持续性的高级复合材料应用中利用ES填料负载的潜力.
Introduction
The advancement of biobased composites using biopolymer matrix and reinforcement derived from renewable resources has emerged as among the utmost promising areas of study in polymer science (Hanan et al. Citation2023). In this regard, bio-epoxy resins have shown promising viable alternative to synthetic resins in the production of entirely bio-based composite systems. Bio-epoxy resin is a type of environmentally friendly epoxy resin derived primarily from biological resources. It is frequently blended with inorganic fillers or synthetic/natural fibers to enhance processing ease, reduced costs, and improve end-use properties (Vinod, Sanjay, and Siengchin Citation2021, Vinod et al. Citation2022, Thiagamani et al. Citation2019. Coatings, adhesives, composites, laminates, and electronic materials such as potting compounds can all benefit from bio-epoxy. The main issue, however, is that bio-epoxy lacks the properties of synthetic epoxy, making it difficult to develop promising bio-based composites. But somehow, previous research has widely accepted that the properties of bio-based composites can be optimized using different types of reinforcement or filler (Deeraj et al. Citation2021; Lotfi et al. Citation2021; Suriani et al. Citation2021).
Phoenix dactylifera or date palm is the biggest important agricultural crop, abundant in Northern Africa and the Middle East. In Saudi Arabia, alone, around 15,000 tons of date palm stem and leaves are deposited as misuse. Without proper utilization, large amounts of date palm biomass waste accumulate each year. These quantities possess the capability to contribute to the promotion of industrial sustainability through the generation of alternative goods that are both economical and environmentally responsible. The study conducted by Benmansour et al. (Benmansour et al. Citation2014) examined the utilization of date palm fiber as a filler in mortar for its potential application as an insulating medium in buildings. The results of their work indicate that the inclusion of date palm fiber exhibits considerable potential as a viable choice for thermal insulation materials in the construction of buildings. According to the study conducted by Al Oqla et al. (AL-Oqla, Hayajneh, and Al-Shrida Citation2022) the incorporation of date palm fibers into polypropylene composites resulted in an enhancement of their thermal stability. In their study, Amroune et al. (Amroune et al. Citation2021) conducted an investigation into the utilization of date palm fiber as reinforcement in composites. Their findings revealed that the application of chemical treatment to the fibers resulted in a significant enhancement of their tensile strength properties, with improvements of up to threefold. Date palm fiber has been discovered to substantially enhance mechanical properties such as tensile, flexural strength, and impact endurance when used in various composites (Awad et al. Citation2023; Faiad et al. Citation2022; Lahouioui et al. Citation2020). It is gaining popularity as a fiber material to substitute synthetic and other organic fibers owing to its accessibility, lack of expense, low cost of processing, sustainability, and environmental friendliness.
The chicken eggshell is a residue in aviculture that has recently gained recognition as a significant environmental concern worldwide, especially in countries with a highly developed egg product industry (Owuamanam and Cree Citation2020). ES contains 94-96 wt.% calcite-shaped calcium carbonate (CaCO3), 3-4 wt.% organic content, along with traces of magnesium, phosphorus, and other substances (Kowshik et al. Citation2022; Owuamanam, Soleimani, and Cree Citation2021). Although there is a growing amount of discarded ES leading to land degradation, it is possible to utilize ES as a filler component in composites to modify their mechanical properties. Composites containing ES fillers have been developed using a variety of lab-scale production techniques, including matrix polymer. In a recent study, the incorporation of nano-eggshell particles measuring 50 nm in diameter was investigated in a synthetic epoxy resin. The weight fractions of the nano-eggshell particles used in the study ranged from 1 wt.% to 5 wt.%. The tensile strength exhibited an increase ranging from 7% to 93%, the modulus experienced a rise between 24% and 112%, and the Izod impact energy demonstrated a boost of 5% to 15%. The experimental results indicate that a filler loading of 2 wt.% resulted in the highest values for both tensile strength and impact toughness. Conversely, a filler loading of 5 wt.% yielded the highest tensile modulus (Mohan and Kanny Citation2018). The scholar made a discovery that nano-sized powders, possessing a significant specific surface area and exhibiting stronger bonding with the matrix phase, were found to enhance both tensile strength and impact durability. Additionally, it was observed that the presence of filler nanoparticles with higher stiffness correlated to the matrix material resulted in a proportional escalation in tensile modulus. In a separate study, eggshells with distinct compositions (5, 10, 15, and 20 wt.%) were integrated into a synthetic epoxy matrix through blending (Gbadeyan et al. Citation2020). When compared to pure epoxy resin, the tensile properties and elastic modulus of the composite have improved by 5%, 12%, 36%, and 16%, and by 74%, 63%, 144%, and 130%, respectively. The characteristics are improved due to the proper diffusion of the shell particles inside the epoxy (Azman et al. Citation2020). Due to better loading density and compactness, finer particle size of ES has been found to have a significant beneficial impact on composites material characteristics. Furthermore, the primary element in the composition of ES is CaO, which is helpful in improving the properties of cementitious materials (Yang et al. Citation2022). A larger CaO substance (greater than 90%) ES particles assist expands composite performance.
In general, thermomechanical and viscoelastic of polymer composites are influenced by particle volume, shape, size, surface characteristics, and particle distribution within the matrix (Ameen et al. Citation2021; Furtos et al. Citation2022; Matykiewicz, Sałasińska, and Barczewski Citation2020). To better understand and address problems in these parameters, theoretical, experimental, and degree of interaction between filler and polymer must be learned. While numerous investigations on biomatrix reinforced composites have been conducted in recent years (Hasan et al. Citation2023; Ramlee et al. Citation2022; Sarmin et al. Citation2022; Veerasimman et al. Citation2022), effective distribution of dual bonding filler in biopolymer remains a challenge, and experimental thermomechanical properties are still far below the theoretical value. Furthermore, to the best of our information, hardly a research paper on biomatrix with date palm fiber and a filler derived from discounted eggshell have been published. Hence, this study is conducted to fill in the gap. This current study presents an environmentally friendly and long-lasting developed composite due to the usage of plant fibers and eggshell as reinforcement. Besides, the matrix used was bio-epoxy, which contained 56% plant-based carbon. Consequently, the utilized components were biodegradable and environmentally friendly. Bio-epoxy composites were fabricated using a 40% loading of date palm fibers and varying concentrations (5%, 10%, 15%, and 20%) of ES fillers. The thermogravimetric (TGA) and dynamic mechanical analyzer (DMA) techniques were utilized to investigate the thermal and viscoelastic properties of fabricated composites in terms of storage modulus (E′), loss modulus (E′′), Tan delta (Tan δ), glass transition temperature (Tg), and Cole-Cole plot.
Experimental works
Raw material preparation
In this research, date palm fiber (DP) and eggshell powder were used as reinforcements, and bio-epoxy resin was used as the matrix material. The date palm trees were sourced from Jeddah, Saudi Arabia. The fibers underwent fragmentation, resulting in the production of shorter fibers measuring between 0.8 and 1 mm in length. These fibers possessed a moisture content of 6 to 8% at the time of fabrication. The chemical composition of DP is presented in .
Table 1. Chemical constituent of date palm leaf sheath (DP) fiber.
ES from local eggshell trash was used as a filler. In order to eliminate odors and pollutants from the residual egg and organic membranes, the ES waste underwent a procedure involving the extraction of the inner membrane, followed by a coarse crushing and subsequent rinsing with water. The sample was subsequently subjected to a sun-drying process lasting 8 hours, followed by a subsequent drying step at a temperature of 110°C for a duration of 24 hours in order to eliminate any remaining moisture. Subsequently, the substance was allowed to reach ambient temperature and subsequently pulverized into a fine particulate state using a mortar and pestle. The ES powder was subjected to a precise particle size of 53 µm using a vibrating sieve shaker, after which it collected.
The matrix utilized in this study consisted of a green bio-epoxy polymer, specifically the SR GreenPoxy 56 resin and SD 280 × hardener, which were procured from Sicomin Epoxy Systems in France. It is noteworthy that this polymer acquires a molecular structure derived from plants, accounting for nearly 56% of its composition. presents the desired characteristics of the GreenPoxy 56 resin. The weight ratio of the resin to hardener was 100:37.
Table 2. Bio-epoxy resin type SR GreenPoxy 56 and SD 280× hardener specification.
exhibits the different loadings of DP fiber utilized in bio-epoxy composites. The process of fabricating the composite material is illustrated in . The ES was incorporated into the bio-epoxy matrix. In the formulations, four different weight fractions of the fillers were used as matrix replacements, with loadings of 5, 10, 15, and 20 wt%. For comparison’s sake, a sample without ES filler was made. The necessary quantity of bio-epoxy resin was initially deposited in a beaker, along with the suitable quantity of ES. The combination was evenly mixed for 7 to 10 min. The necessary quantity of hardener was then added and mixed for 3 to 5 min prior to degassing for 15 min. Additionally, the mixture was combined into DP fibers containing a 40 wt.% fiber loading and thoroughly blended for 7–10 min. In the subsequent procedure, the mixture was evenly spread into mold measuring 150 mm in width, 150 mm in length, and 3 mm in thickness. Subsequently, the mold was transferred to the hot press and subjected to a temperature of 110°C for a duration of 10 min, while being subjected to a significant pressure of 2.5 Mpa. showed fabricated bio-epoxy composite with date palm fiber and 20% eggshell filler and the microscopic behaviour at 50x magnification. The sample was post-cured for 3 h before being cut to the standard size for each analysis.
Figure 1. Schematic diagram of preparation and fabrication process of bio-epoxy composite with date palm fiber and eggshell filler.
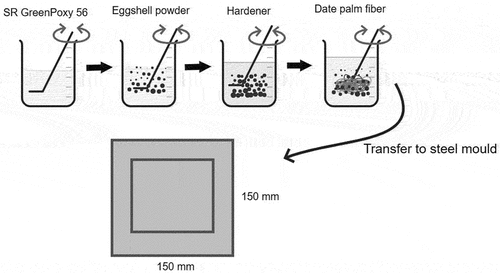
Figure 2. Diagram of fabricated bio-epoxy composite with date palm fiber and eggshell filler; SEM image at 50× magnification.
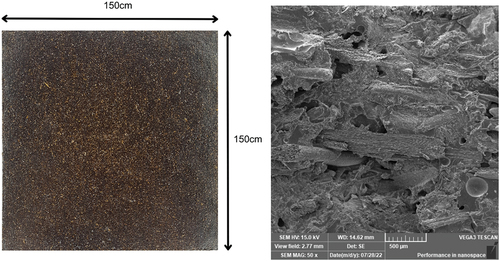
Table 3. Formulations of filler (ES and DP) in the bio-epoxy composites.
Characterization
Dynamic Mechanical Analysis (DMA)
The viscoelastic properties of composite samples were investigated using a dynamic mechanical analyzer DMA Q-800 (TA Instruments, USA) at INTROP, UPM. The samples were evaluated in agreement with ASTM D4065 (D4065 Citation2020) and measured 60 mm in length, 12.5 mm in width, and 3 mm in thickness. In a nitrogen atmosphere, the three-point bending mode was used with temperatures ranging from 30°C to 150°C and a heating rate of 10°C/min. The frequency of the oscillation was set to 1 Hz.
According to DMA analysis, for any material sequence, the complex modulus is a vital distinguishing feature that changes as the material changes, as shown in EquationEquation 1.(1)
(1)
The material response DP fibers and ES filler composites were accessed under these conditions. As shown in EquationEquation 2(2)
(2) , the storage and loss modulus, two critical components of this time-dependent distinguishing feature, were also retrieved to temperature.
The product of these two quantities, =
and
=
, yields an estimate of elastic retrieval of distortion energy and heat dissipation. Alternatively, measurements of the material’s stiffness and damping capability were performed. The loss factor was then calculated as a function of temperature to investigate energy dissipation and deformation energy storage per cycle, as shown in EquationEquation 3.
(3)
(3)
Thermogravimetric Analysis (TGA)
The thermal stability of the composite was investigated using thermogravimetric analysis (TGA) in accordance with ASTM E1131–03 (E1131–03 Citation2020). TGA was carried out, which generally entails measuring the polymer mass as a temperature function or time by subjecting the sample exposed to a regulated temperature programmed in a controlled environment. Polymers begin to lose mass in an oxidative environment, although mass growth can be observed prior to breakdown at gradual heating rates.
All measurements were taken with a Mettler TGA Q 500 TA (USA) at the INTROP, UPM Laboratory of Bio-composites. To avoid oxidation, the TGA was measured in a nitrogen atmosphere at a flow rate of 50 ml/min. The weighed composite samples (40 mg to 45 mg) were placed in an alumina and warmed to different temperatures ranging from 30°C to 800°C at a rate of 10°C/min.
Results and discussions
Storage modulus (E’)
The effect of ES particles corporation on the E’ values of bioepoexy/DP fiber composites at a frequency of 1 Hz is shown in . The graph demonstrates that DP composites have the lowest E’ values, which denotes a low level of stiffness. However, throughout the temperature range investigated, all ES-filled composites exhibit significant improvement in storage modulus (E’). The improvement in stiffness observed in these composites are attributed to the high stiffness of the ES filler, which can efficiently limit the agitation of bio-epoxy polymeric structure brought on by the optimal and well distributed filler in the epoxy matrix. also shows that the E′ tends to turn out to be wider in the glassy zone due to the constituents’ proximity, tight packing, and frosted condition, ensuing in a steep storage modulus value below Tg. A sharp drop in the E′ curves between 80 and 100°C also indicates a change from glass to rubber. Even though the E′ values in the rubbery zone decrease as temperature rises, the components of composites lose their tight packing due to increased molecular mobility. The observed trend is also consistent with other research studies in which insignificant changes in modulus are attended in the rubbery region (Balaji et al. Citation2022; Hanan et al. Citation2023; Ismail et al. Citation2023; Saba et al. Citation2016).
Figure 3. Effect of eggshell filler loading in bio-epoxy/date palm fiber composite on storage modulus value.
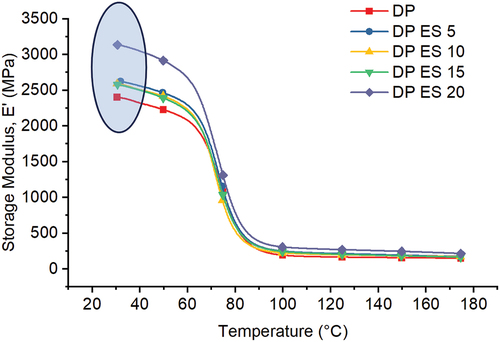
The concurrent improvement of E’ value to ES-filled composites attributes to physical interaction via ionic bonds amid surface carboxyl groups of ES filler and polar groups of bio-epoxy matrix. In comparison to 5 wt.%, 10 wt.%, and 15 wt.% filler loading, 20 wt.% ES filler loading composites have the highest storage modulus value. DP ES 20 has the maximum E′ rate in mutually the glassy and rubbery regions, indicating perfect uniform distribution, diffusion, and great physical interaction between them and the bio-epoxy matrix. Similar findings have been observed in other investigations, where the storage modulus is increased by incorporating an ideal loading ratio of powdered olive tree leaves and pineapple leaf fiber in the epoxy matrix (Senthilkumar et al. Citation2022). In other agreement with da Silva et al. (da Silva et al. Citation2022), the storage modulus of the epoxy composite reinforced kenaf fiber increased with the increment kenaf fiber loading.
Loss modulus (E’’)
shows the accumulated DMA curves of E′′ against temperature of bio-epoxy/DP fiber and ES-filled composites. The loss modulus plot exhibits a similar pattern to the E’ plot, indicating that the inclusion of ES particles in bio-epoxy/DP improves the loss modulus.
Figure 4. Effect of eggshell filler loading in bio-epoxy/date palm fiber composite on loss modulus value.
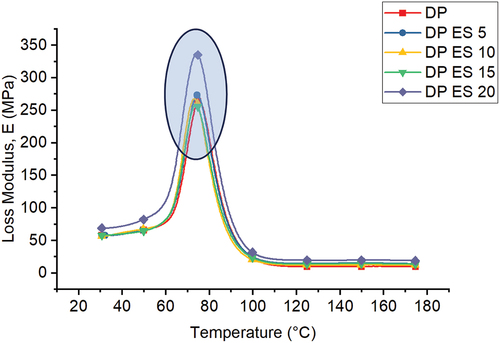
The E” peak height for DP composites is reduced in , however the accumulation of ES particles into the bio-epoxy matrix raises the E’’ peak rates. Interestingly, higher E” peak heights are detected for DP ES 20 compared to the other bio-epoxy composites, highlighting improved diffusion and no visible agglomeration in the bio-epoxy matrix. The agglomeration causes non-homogeneous distribution and a two-phase system in the polymer, resulting in a decrease in the peak height of E.” Other researchers reported comparable trends and conclusions (Khan et al. Citation2022; Uppin et al. Citation2022). Above Tg, all ES-filled composites have a higher E′′ value than bio-epoxy/DP composites. The DP ES 20 composite has the highest E′′ max peak, followed by the DP ES 5, DP ES 10, and DP ES 15 composites. also depicts the composites with the highest E′′ peak height, indicating that they may have the highest tensile properties of any composite. Furthermore, the addition of stiff filler (ES) to the bio-epoxy/DP composites improve their complex modulus (E*). The addition of ES filler causes an expansion in both the E′ and E′′ values.
Damping factor (Tan δ)
Tan δ is a damping factor measurement that also identifies a system’s elastic or viscous properties, and its peak height is related to the internal energy dissipation of the matrix/filler interphase (Wang et al. Citation2022). depicts the Tan δ of bio-epoxy/DP and ES filled composites. The figure reveals that damping factor raises with temperature and attains its peak in the transition zone, preceded by a decrement in the rubbery region for all types of composites. The damping factor graph clearly shows that due to frozen polymeric chains at this point, all composites have minimum values below Tg, ensuing in a higher degree of molecular maneuverability at higher Tan δ peak values.
Figure 5. Influence of eggshell filler loading in bio-epoxy/date palm fiber composite on damping factor.
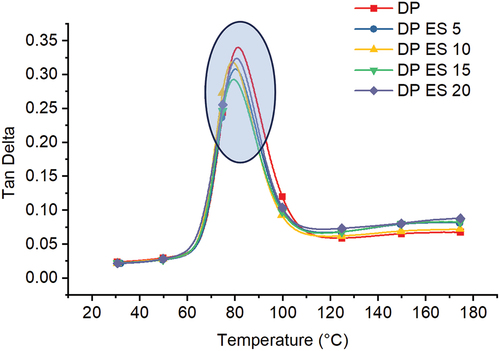
The DP composite clearly has the greatest maximum value (0.34), indicating a greater degree of molecular movement. It is also observed from , the Tan δ peak height of the ES filled bio-epoxy composites is relatively lower, as the incorporation of ES powder significantly lessens the viscoelastic damping factor of the bio-epoxy matrix. The decline in the intensity of the Tan δ peaks recommends that the addition of ES filler slows down the energy dissipation process, demonstrates good scattering in the matrix and efficiently preventing polymer change. When the ES filler loading is increased to 15 wt.%, there is a further decrease in Tan δ, but when the ES filler loading is increased to 20 wt.%, there is an increase in Tan δ rather than a further decrease. Thus, among the 5,10,15, and 20 wt.% ES filler loadings, the 15 wt.% ES has the minimum Tan δ, pursued by the 5 wt.% ES filler loading. When the ES loading is increased from 15 wt.% to 20 wt.%, agglomeration occurs, increasing the available space for the polymer network to transition or rotate, thereby boosting viscoelastic damping behavior. The outcomes obtained are consistent along with previous study discoveries (Chandrika et al. Citation2022; Samal et al. Citation2023).
Glass transition (Tg)
shows the peak height of the Tan δ curve as well as the Tg values. The DP composite clearly has a reduction Tg compared to the remainder of the ES-filled bio-epoxy composites attained from E”. Even though the identified value is quite significant compared with several other published studies conducted, the reduced Tg value (81.05°C) for DP composite is attributable to the availability of certain agile and movable bio-epoxy polymer network within the bio-epoxy matrix (Matykiewicz, Sałasińska, and Barczewski Citation2020; Mohan and Kanny Citation2018). The sample without eggshell filler has the highest value of Tan δ as measured by the DMA plots. The respective residue values for the composites ranged between 19.95 and 34.48. The values of this parameter rise as the percentage of eggshell filler in the prepared compositions increases. The addition of ES particles to the bio-epoxy matrix behaves as a stumbling block, increasing the variability of the filled bio-epoxy composites’ cross-linked composition. Elevated heterogeneity reduces voids, thus limiting bio-epoxy polymer evolution within the ES-filled composites.
Table 4. Peak height and Tg of Tan δ curve and residue at 700°C for bio-epoxy/DP composites and all ES filler loading composites.
Cole-Cole
The Cole-Cole plot is a practical and effective tool for understanding how loss modulus (E′′) and storage modulus (E′) relate to one another (Saba et al. Citation2017). The plotted curves indicate a homogeneous polymeric system by their smooth, semicircular arc. Furthermore, flawed, or random shape denotes intersection impacts and heterogeneous phase or nonlinear distribution in the polymer network. reveals the Cole-Cole outline at which the E” values are shown graphically as a function of E’ for bio-epoxy composites/DP fiber and ES filled composites.
Figure 6. Effect of eggshell filler loading in bio-epoxy/date palm fiber composite on Cole-Cole plot.
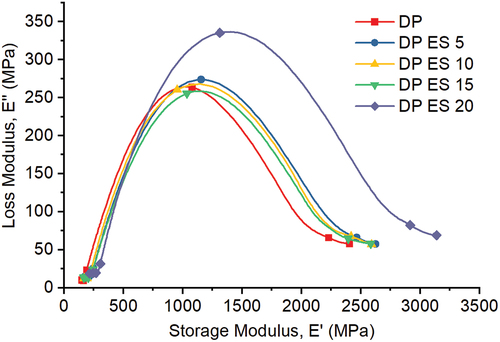
shows that the semicircular and smooth arcs of bio-epoxy/DP and bio-epoxy/DP with ES-filled composites are almost identical, indicating perfect diffusion of DP fiber and ES filler loading in the bio-epoxy matrix. The accumulation of ES filler into microscopic particles creates a system that allows for perfect and homogeneous scattering with good engagement at the interface between bio-epoxy, DP fiber, and ES filler. All of this results in semicircular and smooth arcs in Cole-Cole plots (). Other researchers have expressed similar views (Ameen et al. Citation2021; Amroune et al. Citation2021; Saba et al. Citation2017). Cole-cole regulates the greater E,’ E” and Tg, superior tensile strength, and flawless interfacial interaction among the polymer and the 20 wt.% ES filler.
Thermogravimetric analysis
depicts the thermograms of varying ES filler loadings (5 wt.%, 10 wt.%, 15 wt.%, and 20 wt.%) in bio-epoxy/DP fiber composites. Three degrading regions are used to explain thermal stability: introductory degradation climate, primary degradation climate, and ultimate degradation climate (Hanan et al. Citation2023; Malik et al. Citation2022; Wang et al. Citation2022). The first stage, which occurs at temperatures ranging from 100 to 200°C, involves the thermal degradation of all bio-epoxy/DP fiber composites owing to the evaporation of supplementary alcoholic groups and the condensation weak water molecules from the surface of the composites.
Figure 7. Effect of eggshell filler loading on thermal degradation of bio-epoxy/date palm fiber composite.
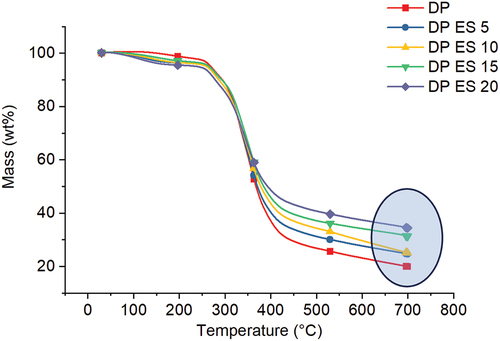
The primary decomposition phase occurs after 300°C () due to pyrolysis and degradation of the aromatic group of the bio-epoxy as well as the aliphatic amine hardener due to the low breaking energy of the C-N bond (Ismail et al. Citation2023). This is primarily due to the decomposition of natural chemicals found in ES particles. The final phase occurs above 400°C. At this final stage, the hydrogen bonds in the bio-epoxy network are totally broken, resulting in complete degradation or decomposition, which can be substantiated by the quantity of char production. DP composites have the lowest thermal stability compared to DPES 5, DPES 10, and DPES 15 composites.
Agreeing to the TGA graph, the general degradation temperature for all bio-epoxy/DP fiber composites happens between 350°C and 450°C. The composites’ degradation temperature rises as the ES filler content raised from 5 wt.% to 20 wt.%, and the main degradation peak temperature is lifted to a greater temperature, which significantly decelerates the level of degradation of the fabricated composites. Thermal stability is found to be increased with 20 wt.% ES filler loadings when compared to 5 wt.%, 10 wt.%, and 15 wt.%. The increased thermal stability of DPES 20 composites over DPES 5, DPES 10, and DPES 15 predicts that the mobility of bio-epoxy polymer chains will be restricted, decomposition will be suppressed, and the dissemination of ES microstructure particles in the bio-epoxy matrix will be homogeneous. Comparable arguments have been presented for nanocellulose composites made from sugarcane bagasse and poly(vinyl alcohol) (Mandal and Chakrabarty Citation2014).
demonstrates the derivative of the mass loss per unit temperature as a function of temperature for different ES filler loading bio-epoxy composites (5 wt.%, 10 wt.%, 15 wt.%, and 20 wt.%). The derivative of mass loss for DPES 20 is smaller, indicating that it has greater thermal stability than DP, DPES 5, DPES 10, and DPES 15. The DTG curve demonstrates that the addition of ES filler increases the transition temperature of DP composites from 300°C to a comparatively higher temperature, which is the temperature at which the composites decompose indicating these composites can be applied in high temperature conditions. DPES 5 composites have the lowest derivative moss loss among the ES-filled composites, indicating that they have a higher thermal stability. Elevated thermal constancy is ascribed to the DP fiber and ES particles being highly cross-linked with bio-epoxy and natural chemicals present in the composites.
Conclusions
Bio-composites based on bio-epoxy reinforced with DP fibers and ES filler were successfully fabricated and their thermomechanical and viscoelastic properties were investigated. The results revealed that the addition of ES particles significantly altered the dynamic properties of the bio-epoxy/DP fiber composites. The addition of 20 wt.% ES filler improved the storage modulus (E′) and loss modulus (E”) of bio-epoxy/DP fiber composites. When compared to plain composites, ES-filled composites had a significant decrease in damping factor. Tg values derived from Tan peaks and loss modulus (E′′) values showed a significant progress in all bio-epoxy/DP fiber composites. The Cole-Cole plot clearly showed semicircular and smooth arcs indicating system homogeneity moreover, uniform fiber/matrix bonding in bio-epoxy/DP fiber composites. Thus, the use of ES filler can provide a favorable and advanced platform for other natural fillers. Generally, we conclude that the combination produces eco-friendly composites with acceptable thermal stability, dynamic modulus and damping properties. The improvements of the bio-epoxy/DP fiber composites indicate a significant potential in innovative light weight engineering material such as aircraft, high rises, bridges, boats, reservoirs, and pressure vessels where renewable resources and excellent performance are needed.
Highlights
Eggshell can improve both the thermal and dynamic mechanical properties of bioepoxy/DP fiber composites.
ES-filled composites with 5 and 10% wt ES filler exhibited properties comparable to 15% w ES filler, but less than 20% wt ES filler.
The addition of eggshell filler improved the storage modulus (E′) and loss modulus (E”) of bioepoxy/DP fiber composites.
The incorporation of eggshell filler contributed to the hardness and stiffness of bioepoxy/DP fiber composites.
Author’s contribution
Data curation, Sarmin SN and Jawaid M, Balbir Singh: Formal analysis, Sarmin SN, Ismail AS and Jawaid M; Funding acquisition, Jawaid M, Foud H, M. Hashem; Project administration, Foud H, Balbir singh, and Jawaid M; Writing – original draft, Sarmin SN, and Jawaid M; Writing – review & editing, Sarmin SN, Salim N, Jawaid M, B. Singh, M. Hashem, H. Fouad, and Dhakal HN. All authors have read and agreed to the published version of the manuscript.
Declarations
We confirm that this work is original and has not been published elsewhere, nor is it currently under consideration for publication elsewhere.
Human and animal rights
We declare that there are no animal studies or human participant involvement in the study.
Acknowledgments
The authors would like thank the King Saud University, Riyadh for providing the funding support for this research work using Researchers Supporting Project number (RSPD2023R680), King Saud University, Riyadh, Saudi Arabia.
Disclosure statement
No potential conflict of interest was reported by the author(s).
Additional information
Funding
References
- AL-Oqla, F. M., M. T. Hayajneh, and M. A. M. Al-Shrida. 2022. “Mechanical Performance, Thermal Stability and Morphological Analysis of Date Palm Fiber Reinforced Polypropylene Composites Toward Functional Bio-Products.” Cellulose 29 (6): 3293–14. https://doi.org/10.1007/s10570-022-04498-6.
- Ameen, F., M. Atif, K. Mahmood, and U. F. Yousuf. 2021. “Qualitative and Quantitative Impact of Filler on Thermomechanical Properties of Epoxy Composites.” Polymers for Advanced Technologies 32 (8): 2813–2828. https://doi.org/10.1002/pat.5304.
- Amroune, S., A. Bezazi, A. Dufresne, F. Scarpa, and A. Imad. 2021. “Investigation of the Date Palm Fiber for Green Composites Reinforcement: Thermo-Physical and Mechanical Properties of the Fiber.” Journal of Natural Fibers 18 (5): 717–734. https://doi.org/10.1080/15440478.2019.1645791.
- Awad, S., T. Hamouda, M. Midani, E. Katsou, and M. Fan. 2023. “Polylactic Acid (PLA) Reinforced with Date Palm Sheath Fiber Bio-Composites: Evaluation of Fiber Density, Geometry, and Content on the Physical and Mechanical Properties.” Journal of Natural Fibers 20 (1). https://doi.org/10.1080/15440478.2022.2143979.
- Azman, N. A. N., M. R. Islam, M. Parimalam, N. M. Rashidi, and M. Mupit. 2020. “Mechanical, Structural, Thermal and Morphological Properties of Epoxy Composites Filled with Chicken Eggshell and Inorganic CaCo3 Particles.” Polymer Bulletin 77 (2): 805–821. https://doi.org/10.1007/s00289-019-02779-y.
- Balaji, N., J. S. P. Kumar, G. Ramesh, V. Dhinakaran, N. Gobu, and T. Maridurai. 2022. “Investigation on DMA, Fatigue and Creep Behaviour of Rice Husk Ash Biosilica-Prickly Pear Short Fibre-Reinforced Epoxy Resin Composite.” Silicon 14 (18): 12773–12779. https://doi.org/10.1007/s12633-022-01981-4.
- Benmansour, N., B. Agoudjil, A. Gherabli, A. Kareche, and A. Boudenne. 2014. “Thermal and Mechanical Performance of Natural Mortar Reinforced with Date Palm Fibers for Use as Insulating Materials in Building.” Energy and Buildings 81:6. https://doi.org/10.1016/j.enbuild.2014.05.032.
- Chandrika, V. S., A. Anamika, C. Jeeva, B. Perumal, S. S. Kumar, J. F. Roseline, and I. K. Raghavan. 2022. “Natural Fiber Incorporated Polymer Matrix Composites for Electronic Circuit Board Applications.” Advances in Materials Science and Engineering 2022:9. https://doi.org/10.1155/2022/3035169.
- D4065, A. 2020. “Standard Practice for Plastics: Dynamic Mechanical Properties: Determination and Report of Procedures.” ASTM International (ASTM). 4065–01.
- da Silva, T. T., P. H. P. M. D. Silveira, A. B. H. D. S. Figueiredo, S. N. Monteiro, M. P. Ribeiro, L. D. M. Neuba, N. T. Simonassi, F. D. C. Garcia Filho, and L. F. C. Nascimento. 2022. “Dynamic Mechanical Analysis and Ballistic Performance of Kenaf Fiber-Reinforced Epoxy Composites.” Polymers 14 (17): 3629. https://doi.org/10.3390/polym14173629.
- Deeraj, B. D. S., K. Joseph, J. S. Jayan, and A. Saritha. 2021. “Dynamic Mechanical Performance of Natural Fiber Reinforced Composites: A Brief Review.” Applied Science and Engineering Progress 14 (4): 614–23.
- E1131-03, A. 2020. “Standard Test Method for Compositional Analysis by Thermogravimetry.” ASTM International (ASTM), March 15, 2020.
- Faiad, A., M. Alsmari, M. M. Ahmed, M. L. Bouazizi, B. Alzahrani, and H. Alrobei. 2022. “Date Palm Tree Waste Recycling: Treatment and Processing for Potential Engineering Applications.” Sustainability 14 (3): 1134. https://doi.org/10.3390/su14031134.
- Furtos, G., L. Molnar, L. Silaghi-Dumitrescu, P. Pascuta, and K. Korniejenko. 2022. “Mechanical and Thermal Properties of Wood Fiber Reinforced Geopolymer Composites.” Journal of Natural Fibers 19 (13): 6676–6691. https://doi.org/10.1080/15440478.2021.1929655.
- Gbadeyan, O. K., S. Adali, G. Bright, B. Sithole, and O. Awogbemi. 2020. “Studies on the Mechanical and Absorption Properties of Achatina Fulica Snail and Eggshells Reinforced Composite Materials.” Composite Structures 239:239. https://doi.org/10.1016/j.compstruct.2020.112043.
- Hanan, F., T. Khan, M. Jawaid, M. T. H. Sultan, T. Sebaey, B. Singh, and S. N. Sarmin. 2023. “Thermal Characterization of Epoxy Bilayer Hybrid Composites Reinforced with Kenaf and Oil Palm Fibers.” Polymer Composites 44 (1): 444–452. https://doi.org/10.1002/pc.27108.
- Hasan, K. F., S. Chen, G. Török, L. Xiaoyi, P. G. Horváth, and T. Alpár. 2023. “Natural/Synthetic Polymer Hybrid Composites in Automotive Applications.” In Green Hybrid Composite in Engineering and Non-Engineering Applications, edited by T. Khan and M. Jawaid, 25. Singapore: Springer Nature.
- Ismail, A. S., M. Jawaid, N. H. Hamid, R. Yahaya, A. Hassan, and S. N. Sarmin. 2023. “Physical, Structural and Thermal Properties of Bio-Phenolic/epoxy Polymers Blends.” Materials Today Communications 34:105455. https://doi.org/10.1016/j.mtcomm.2023.105455.
- Khan, F. M., A. H. Shah, S. Wang, S. Mehmood, J. Wang, W. Liu, and X. Xu. 2022. “A Comprehensive Review on Epoxy Biocomposites Based on Natural Fibers and Bio-Fillers: Challenges, Recent Developments and Applications.” Advanced Fiber Materials 4 (4): 683–704. https://doi.org/10.1007/s42765-022-00143-w.
- Kowshik, S., S. Sharma, M. Shettar, P. Hiremath, and A. Upadhyaya. 2022. “Investigation on the Effects of Uncarbonised, Carbonised and Hybrid Eggshell Filler Addition on the Mechanical Properties of Glass Fibre/Polyester Composites.” Engineered Science 18:10. https://dx.doi.org/10.30919/es8d679.
- Lahouioui, M., R. Ben Arfi, M. Fois, L. Ibos, and A. Ghorbal. 2020. “Investigation of Fiber Surface Treatment Effect on Thermal, Mechanical and Acoustical Properties of Date Palm Fiber-Reinforced Cementitious Composites.” Waste and Biomass Valorization 11 (8): 4441–4455. https://doi.org/10.1007/s12649-019-00745-3.
- Lotfi, A., H. Li, D. V. Dao, and G. Prusty. 2021. “Natural fiber–reinforced composites: A review on material, manufacturing, and machinability.” Journal of Thermoplastic Composite Materials 34 (2): 238–284. https://doi.org/10.1177/0892705719844546.
- Malik, K., F. Ahmad, N. A. Yunus, E. Gunister, T. Nakato, E. Mouri, and S. Ali. 2022. “A Review of Flax Fiber Reinforced Thermoset Polymer Composites: Thermal-Physical Properties, Improvements and Application.” Journal of Natural Fibers 19 (15): 10412–10430. https://doi.org/10.1080/15440478.2021.1993507.
- Mandal, A., and D. Chakrabarty. 2014. “Studies on the Mechanical, Thermal, Morphological and Barrier Properties of Nanocomposites Based on Poly (Vinyl Alcohol) and Nanocellulose from Sugarcane Bagasse.” Journal of Industrial & Engineering Chemistry 20 (2): 462–473. https://doi.org/10.1016/j.jiec.2013.05.003.
- Matykiewicz, D., K. Sałasińska, and M. Barczewski. 2020. “The Effect of Poly (Vinyl Chloride) Powder Addition on the Thermomechanical Properties of Epoxy Composites Reinforced with Basalt Fiber.” Materials & Design 13 (16): 3611. https://doi.org/10.3390/ma13163611.
- Mohan, T. P., and K. Kanny. 2018. “Thermal, Mechanical and Physical Properties of Nanoegg Shell Particle-Filled Epoxy Nanocomposites.” Journal of Composite Materials 52 (29): 3989–4000. https://doi.org/10.1177/0021998318773445.
- Owuamanam, S., and D. Cree. 2020. “Progress of Bio-Calcium Carbonate Waste Eggshell and Seashell Fillers in Polymer Composites: A Review.” Journal of Composites Science 4 (2): 70. https://doi.org/10.3390/jcs4020070.
- Owuamanam, S., M. Soleimani, and D. E. Cree. 2021. “Fabrication and characterization of bio-epoxy eggshell composites.” Applied Mechanics 2 (4): 694–713. https://doi.org/10.3390/applmech2040040.
- Ramlee, N. A., M. Jawaid, E. S. Zainudin, S. A. K. Yamani, S. Alamery, H. Fouad, C. Santulli, and S. N. Sarmin. 2022. “Thermal and Acoustic Properties of Silane and Hydrogen Peroxide Treated Oil Palm/Bagasse Fiber Based Biophenolic Hybrid Composites.” Polymer Composites 43 (9): 5954–5966. https://doi.org/10.1002/pc.26871.
- Saba, N., M. T. Paridah, K. Abdan, and N. A. Ibrahim. 2016. “Dynamic mechanical properties of oil palm nano filler/kenaf/epoxy hybrid nanocomposites.” Construction and Building Materials 124:5. https://doi.org/10.1016/j.conbuildmat.2016.07.059.
- Saba, N., A. Safwan, M. L. Sanyang, F. Mohammad, M. Pervaiz, M. Jawaid, O. Y. Alothman, and M. Sain. 2017. “Thermal and Dynamic Mechanical Properties of Cellulose Nanofibers Reinforced Epoxy Composites.” International Journal of Biological Macromolecules 102:16. https://doi.org/10.1016/j.ijbiomac.2017.04.074.
- Samal, A., S. Kumar, M. Bhargava, and B. S. Roy. 2023. “Fabrication and Characterization of Banana Pseudostem Fibre Reinforced Epoxy Hybrid Composite Using Al2O3 as Filler.” Journal of Bionic Engineering 20 (4): 1737–1746. https://doi.org/10.1007/s42235-023-00331-3.
- Sarmin, S. N., M. Jawaid, S. A. Awad, N. Saba, H. Fouad, O. Y. Alothman, and M. Sain. 2022. “Olive Fiber Reinforced Epoxy Composites: Dimensional Stability, and Mechanical Properties.” Polymer Composites 43 (1): 358–365. https://doi.org/10.1002/pc.26380.
- Senthilkumar, K., M. Chandrasekar, O. Y. Alothman, H. Fouad, M. Jawaid, and M. A. Azeem. 2022. “Flexural, Impact and Dynamic Mechanical Analysis of Hybrid Composites: Olive Tree Leaves Powder/Pineapple Leaf Fibre/Epoxy Matrix.” Journal of Materials Research and Technology 21:11. https://doi.org/10.1016/j.jmrt.2022.11.036.
- Suriani, M. J., H. Z. Rapi, R. A. Ilyas, M. Petrů, and S. M. Sapuan. 2021. “Delamination and Manufacturing Defects in Natural Fiber-Reinforced Hybrid Composite: A Review.” Polymers 13 (8): 1323. https://doi.org/10.3390/polym13081323.
- Thiagamani, S. M. K., S. Krishnasamy, C. Muthukumar, J. Tengsuthiwat, R. Nagarajan, S. Siengchin, and S. O. Ismail. 2019. “Investigation into Mechanical, Absorption and Swelling Behaviour of Hemp/Sisal Fibre Reinforced Bio-Epoxy Hybrid Composites: Effects of Stacking Sequences.” International Journal of Biological Macromolecules 140:10. https://doi.org/10.1016/j.ijbiomac.2019.08.166.
- Uppin, V. S., P. S. Gouda, M. I. Kittur, A. Andriyana, B. C. Ang, B. Parveez, I. A. Badruddin, S. Javed, and S. Kamangar. 2022. “Mechanical Response of Glass–Epoxy Composites with Graphene Oxide Nanoparticles.” Materials & Design 15 (23): 8545. https://doi.org/10.3390/ma15238545.
- Veerasimman, A., V. Shanmugam, S. Rajendran, D. J. Johnson, A. Subbiah, J. Koilpichai, and U. Marimuthu. 2022. “Thermal Properties of Natural Fiber Sisal Based Hybrid Composites–A Brief Review.” Journal of Natural Fibers 19 (12): 4696–4706. https://doi.org/10.1080/15440478.2020.1870619.
- Vinod, A., M. R. Sanjay, and S. Siengchin. 2021. “Fatigue and Thermo-Mechanical Properties of Chemically Treated Morinda Citrifolia Fiber-Reinforced Bio-Epoxy Composite: A Sustainable Green Material for Cleaner Production.” Journal of Cleaner Production 326:129411. https://doi.org/10.1016/j.jclepro.2021.129411.
- Vinod, A., J. Tengsuthiwat, Y. Gowda, R. Vijay, M. R. Sanjay, S. Siengchin, and H. N. Dhakal. 2022. “Jute/Hemp Bio-Epoxy Hybrid Bio-Composites: Influence of Stacking Sequence on Adhesion of Fiber-Matrix.” International Journal of Adhesion and Adhesives 113:113. https://doi.org/10.1016/j.ijadhadh.2021.103050.
- Wang, F., J. Liao, C. Huang, H. Yu, J. Yan, and H. Li. 2022. “Study on the Damping Dynamics Characteristics of a Viscoelastic Damping Material.” Processes 10 (4): 635. https://doi.org/10.3390/pr10040635.
- Yang, D., J. Zhao, W. Ahmad, M. N. Amin, F. Aslam, K. Khan, and A. Ahmad. 2022. “Potential Use of Waste Eggshells in Cement-Based Materials: A Bibliographic Analysis and Review of the Material Properties.” Construction and Building Materials 344:128143. https://doi.org/10.1016/j.conbuildmat.2022.128143.